注塑工艺参数管理规程及配套文件
注塑成型管理规范

注塑成型管理规范一、引言注塑成型是一种常见的塑料加工工艺,广泛应用于制造各种塑料制品。
为了确保注塑成型过程的质量和效率,制定一套科学合理的管理规范是非常重要的。
本文将详细介绍注塑成型管理规范的相关内容,包括设备管理、原料管理、工艺参数控制、质量控制和安全管理等方面。
二、设备管理1. 设备选型:根据产品要求和生产能力需求,选择适当的注塑成型设备,包括注塑机、模具、辅助设备等。
2. 设备维护:定期对注塑成型设备进行检查和维护,确保设备的正常运行。
包括清洁设备、润滑部件、更换易损件等。
3. 设备校准:定期对注塑成型设备进行校准,确保设备的精度和稳定性。
包括温度控制、压力控制等参数的校准。
三、原料管理1. 原料选型:根据产品要求和生产工艺,选择适当的塑料原料,并确保原料的质量符合要求。
2. 原料存储:对原料进行分类、标识和储存,防止受潮、受污染或变质。
原料库应保持干燥、通风和整洁。
3. 原料检验:对每批原料进行检验,包括外观检查、物理性能测试和化学成分分析等。
四、工艺参数控制1. 注塑温度:根据塑料的熔融温度范围和产品要求,设置合适的注塑温度。
确保塑料能够完全熔化,同时避免热分解或过热。
2. 注射压力:根据产品的尺寸和结构,设置合适的注射压力。
确保塑料能够充分填充模具腔体,并保持一定的压力保持时间。
3. 注射速度:根据产品的尺寸和结构,设置合适的注射速度。
确保塑料能够均匀地充填模具腔体,避免产生气泡或短充问题。
4. 冷却时间:根据产品的尺寸和结构,设置合适的冷却时间。
确保产品能够充分冷却固化,避免变形或收缩问题。
五、质量控制1. 模具检验:对每个新模具进行全面检查和试模,确保模具的质量和性能符合要求。
包括尺寸检查、表面质量检查和模具寿命试验等。
2. 首件检验:在正式生产前,对首件进行全面检验,包括尺寸、外观、物理性能等。
确保首件符合产品要求,并进行记录。
3. 在线检验:在生产过程中,对注塑成型产品进行定期的检验和抽样检验,包括尺寸、外观、物理性能等。
注塑成型管理规范

注塑成型管理规范注塑成型是一种常见的制造工艺,广泛应用于塑料制品的生产中。
为了确保注塑成型过程的顺利进行和产品质量的稳定,需要遵循一定的管理规范。
本文将从五个方面介绍注塑成型管理规范。
一、原料管理1.1 选择合格的原料:在注塑成型过程中,原料的质量直接影响产品的质量。
因此,必须选择符合要求的原料,避免使用劣质原料。
1.2 严格控制原料配比:根据产品的要求,精确控制原料的配比,确保产品的性能稳定。
1.3 做好原料的存储和保管工作:保持原料的干燥和清洁,避免受潮和污染,确保原料的质量。
二、模具管理2.1 定期检查模具:定期检查模具的磨损和损坏情况,及时进行维护和更换,确保模具的正常使用。
2.2 控制模具温度:根据产品的要求,控制模具的温度,避免温度过高或过低影响产品的成型质量。
2.3 做好模具的保养工作:定期清洁和润滑模具,延长模具的使用寿命,提高生产效率。
三、注塑机管理3.1 定期维护注塑机:定期对注塑机进行维护保养,保持设备的正常运转,避免因设备故障造成生产中断。
3.2 控制注塑机的参数:根据产品的要求,合理设置注塑机的参数,确保产品的尺寸精度和表面质量。
3.3 做好注塑机的清洁工作:定期清洁注塑机的内部和外部,避免污垢影响产品的质量。
四、生产过程管理4.1 严格执行生产工艺:根据产品的工艺要求,严格执行生产工艺流程,确保产品的质量稳定。
4.2 定期检查产品质量:定期对产品进行抽检和检测,及时发现问题并进行处理,避免次品流入市场。
4.3 做好生产记录和追溯工作:做好生产记录和产品追溯工作,方便对产品进行质量追溯和问题排查。
五、员工管理5.1 培训员工技能:定期组织员工进行相关技能培训,提高员工的操作技能和质量意识。
5.2 建立奖惩制度:建立奖惩制度,激励员工提高生产效率和质量水平,同时惩罚违规行为。
5.3 加强团队合作:鼓励员工之间相互合作,形成良好的团队氛围,共同为产品质量的提升而努力。
总结:注塑成型管理规范是确保产品质量和生产效率的重要保障,只有严格遵循管理规范,才能生产出高质量的注塑成型产品。
注塑工艺规程

编号: SCK02 -2013 受控状态注塑作业指导书编制: 陈新龙审核: 何月华批准: 何大牛版本号: A/0分发号:淮安市淮安区荣昌塑料制品厂发布日期:2013-09-01 实施日期:2013-09-01注塑工序生产和质量工艺规程一、工作流程和要求1、领料按厂部下达的生产单,做好不同型号、规格的材料配色等准备工作。
2、生产计划按序号、型号、数量和交货日期做好生产计划的合理按排。
3、操作要密切注意安全操作,严格按设备操作规程作业,避免一切故障。
4、注塑注塑工艺要求严密,时间、温度、压力与产品质量有密切相关要严格按工艺标准作业,生产时应注意使用相应要求的模具和材料,并注意控制回料的比例,经选配的各种材料加工成型后,其色彩、强度应同样品一致。
5、首检当首批产品注出及时进行首检,检验颜色是否符合样品和色标,不符合时应及时作好调整,质量标准以实物装配为准是否合适,二者合格后才能批量生产。
6、检验经检验,颜色符合样品,尺寸经实物装配验证,合格的进行入库。
7、记录完成本班工作后,清理工作周围的废品、次品及环境卫生,做好相关记录和产品标识及交接班工作。
二、质量要求1、外形尺寸:注塑件不得发生变形,对有公差配合部分严格与产品图纸一致,。
按相应产品装配要求,通过装配试验应合格。
2、外观:注塑件应有一定的光亮度,不得出现划痕、飞边、射纹、熔痕、等明显缺陷。
对某些受模具技术局限的产品允许有轻微的缩影。
透明件应无气泡。
3、色泽:色泽均匀纯正、无色差,颜色与样品色版相一致。
三、工艺参数表(材料PA66)1、尼龙PA66的干燥温度℃ 130-135 时间3-4小时2、注塑工序见作业供应流程参数表3、软化时间4小时温度95℃。
注塑成型管理规范

注塑成型管理规范引言概述:注塑成型是一种常见的制造工艺,广泛应用于各个行业。
为了确保注塑成型过程的质量和效率,制定一套管理规范是必要的。
本文将详细阐述注塑成型管理规范的五个部分。
一、设备管理1.1 设备选型:根据产品的要求和生产量确定合适的注塑成型设备。
考虑设备的尺寸、注射压力、射出容量等因素。
1.2 设备维护:定期检查设备的润滑情况、冷却系统、温度控制等,确保设备的正常运行。
1.3 设备清洁:每日结束生产后,对注塑成型设备进行清洁,清除残留物和杂质,防止对下一次生产造成污染。
二、原料管理2.1 原料选择:根据产品的要求选择合适的注塑原料,考虑原料的流动性、耐热性、耐腐蚀性等因素。
2.2 原料贮存:将原料存放在干燥、阴凉、通风的地方,避免潮湿和阳光直射,防止原料变质。
2.3 原料检验:对每批原料进行检验,包括外观、密度、熔融指数等指标,确保原料的质量符合要求。
三、工艺参数控制3.1 温度控制:根据不同的原料和产品要求,合理设置注塑成型的温度参数,包括模具温度、熔融温度、冷却时间等。
3.2 压力控制:根据产品的尺寸和结构,调整注射压力和保压时间,确保产品的密实度和尺寸精度。
3.3 注塑速度控制:根据产品的形状和结构,控制注塑机的射出速度,避免产生气泡、短射等缺陷。
四、模具管理4.1 模具维护:定期检查模具的磨损情况,及时更换损坏的部件,保证模具的精度和寿命。
4.2 模具清洁:每次模具更换后,对模具进行清洁,清除残留物和杂质,防止对下一次生产造成污染。
4.3 模具存储:将闲置的模具存放在干燥、阴凉的地方,避免受潮和变形,定期进行保养和检查。
五、质量控制5.1 检测方法:制定合适的检测方法和标准,对注塑成型产品进行尺寸、外观、物理性能等方面的检测。
5.2 不良品处理:对于出现的不良品,及时进行分类和处理,找出问题的原因并采取相应的改进措施。
5.3 记录和分析:对每批生产的产品进行记录和分析,包括生产参数、质量指标等,为后续的质量改进提供依据。
注塑工艺管理规定

注塑工艺管理规定引言概述:注塑工艺是一种通用的塑料加工方法,广泛应用于制造各种塑料产品。
为了确保注塑工艺的高效、稳定和可靠,注塑工艺管理规定起到了关键的作用。
本文将详细介绍注塑工艺管理规定的内容和要点。
正文内容:一、注塑工艺参数设置1.熔融温度控制:- 确定合适的熔融温度,以保证塑料材料完全熔化,并避免过热引起材料变质。
- 根据不同的塑料材料,设置相应的熔融温度范围。
- 定期检查和校准熔融温度控制装置,确保其准确性和稳定性。
2.注射速度控制:- 注射速度的控制对产品的质量和尺寸稳定性有着重要影响。
- 根据产品的形状和尺寸,选择合适的注射速度。
- 注意控制注射速度的变化范围,避免突变引起的质量问题。
3.注射压力控制:- 根据模具结构和塑料材料的特性,设置适当的注射压力。
- 注意控制注射压力的稳定性,以保证产品不会因为注射压力过高而产生翘曲或变形等问题。
4.冷却时间控制:- 合理的冷却时间是保证产品尺寸和性能稳定的关键。
- 根据产品的材料和形状,确定适当的冷却时间。
- 在生产过程中,及时调整冷却时间以适应环境温度和产品质量需求的变化。
5.模具温度控制:- 模具温度的控制对注塑工艺的稳定性和产品质量有重要影响。
- 根据塑料材料的熔融温度和产品要求,设置合适的模具温度。
- 定期检查和校准模具温度控制装置,确保其稳定性和准确性。
二、工艺优化与改进1.工艺优化:- 对于现有的注塑工艺,通过分析生产数据和实际情况,发现并解决工艺中存在的问题,以提高产品质量和生产效率。
- 运用工艺改进的方法,包括设计实验、模拟仿真和实际生产验证,逐步优化工艺参数。
2.材料优化:- 选择合适的塑料材料,根据产品要求进行材料的筛选和测试。
- 与材料供应商合作,了解不同塑料材料的性能特点和应用范围,选择最适合的材料。
3.模具优化:- 对于模具结构和设计存在的问题,进行优化和改进,以提高产品的尺寸稳定性和生产效率。
- 使用先进的模具制造技术,提高模具的加工精度和耐磨性。
注塑工艺参数管理规程及配套文件

1.0目的制定本指导书的目的,是对注塑工艺参数在设置、变更和记录、监督过程中可以标准化操作的部分进行规范,提高工艺参数的稳定性和再现性,减少注塑车间在换模、换料的生产切换过程中材料的损耗与工时的浪费,达到提高生产效率、稳定产品品质的目的。
2.0范围适用注塑车间注塑机工艺参数的设置与管理3.0职责3.1调机员:正确的使用标准成型工艺,并对存在的问题及时向领班反馈,配合领班完成对异常情况的处理。
3.2领班:正确的使用标准成型工艺,当因机器、模具、材料、运水等原因原标准成型工艺参数不适用时,根据实际情况作出相应改变以保证生产的进行并配合在工艺改变后IPQC的品质确认工作。
并将工艺变更情况向主管汇报。
3.3主管:发布和认可标准成型工艺,确认工艺变更的正确性并完成相应记录。
对不正确的工艺进行修改并将原因告示领班和技术员,确保生产是在正常和经济的状态下进行。
4.0标准成型工艺参数的设置和调整的一般原理和注意事项4.1设置成型参数的一般原理和注意事项。
4.1.1合模参数的设定。
合模一般分为四段。
4.1.1.1慢速开始:为使机器平稳启动、合模应以慢速开始。
4.1.1.2快速到位:动模板在合模油缸推动下快速运动,以缩短工作周期。
4.1.1.3低压保护:油缸低压低速运动,以保护模具安全。
对于三板模或有斜顶、铲机结构的模具,动、定模接触时应适当降低速度和压力。
4.1.1.4高压合模:以所需的合模力锁紧模具。
应选用最低而又不使成品产生毛边的合模力,既能提高效率又能延长机器模具寿命。
4.1.2开模参数的设定。
开模一般分为三段。
4.1.2.1慢速开模:为不使产品撕裂、变形,应以慢速开模开始。
4.1.2.2快速到位:模具一经打开,应转为快速开模到位,以缩短工作周期。
但对于三板模具、有斜顶滑块的模具,在动、定模分离时应适当设定速度和压力,减轻对模具和机器的冲击和降低噪音。
4.1.2.3慢速终止:将到终点时,为防止惯性产生冲击,应由中速转为慢速终止。
注塑成型管理规范

注塑成型管理规范一、引言注塑成型是一种常见的塑料加工技术,广泛应用于各个行业。
为了确保注塑成型过程的质量和效率,制定一套科学的管理规范是非常重要的。
本文旨在提供一套注塑成型管理规范,以指导企业进行注塑成型工艺的优化和管理。
二、注塑成型工艺参数的设定1. 温度控制- 熔融温度:根据塑料材料的熔融指标和产品要求,确定合适的熔融温度范围。
- 注射温度:根据塑料材料的注射指标和产品要求,确定合适的注射温度范围。
- 模具温度:根据产品要求,确定合适的模具温度范围,以保证产品的质量和表面光洁度。
2. 压力控制- 注射压力:根据产品的尺寸、结构和塑料材料的流动性,确定合适的注射压力范围。
- 保压压力:根据产品的尺寸、结构和塑料材料的收缩性,确定合适的保压压力范围,以保证产品的尺寸稳定性和密度。
3. 注塑速度控制- 注射速度:根据产品的尺寸、结构和塑料材料的流动性,确定合适的注射速度范围。
- 保压速度:根据产品的尺寸、结构和塑料材料的收缩性,确定合适的保压速度范围,以保证产品的尺寸稳定性和密度。
4. 冷却时间控制- 模具冷却时间:根据产品的尺寸、结构和塑料材料的收缩性,确定合适的模具冷却时间,以保证产品的尺寸稳定性和表面质量。
三、注塑成型设备的维护与保养1. 注塑机的维护与保养- 定期检查注塑机的润滑系统,确保润滑油的充足和质量。
- 定期清洁注塑机的进料口、喷嘴和模具,防止杂质进入注塑机。
- 定期检查注塑机的电气系统,确保电源稳定和线路连接良好。
2. 模具的维护与保养- 定期清洗模具的表面,防止残留物影响产品的表面质量。
- 定期检查模具的冷却系统,确保冷却水的流通畅通。
- 定期检查模具的开合机构和导向系统,确保正常运行和定位准确。
3. 辅助设备的维护与保养- 定期清洗和更换冷却塔的冷却水,确保冷却效果良好。
- 定期检查和清洁热流道系统,确保热流道的流通畅通。
四、注塑成型品质控制1. 原材料控制- 严格选择符合产品要求的塑料原料,并建立供应商管理体系,确保原材料的质量稳定性。
注塑工艺调校及参数管理作业指导书
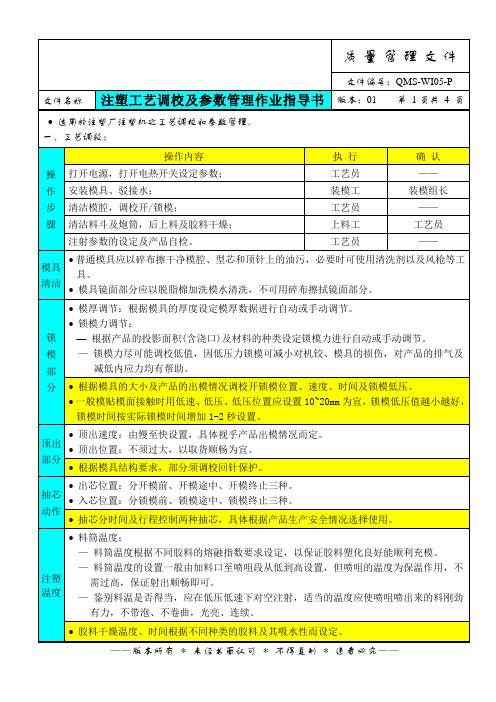
东 江 机 械 制 模 厂 东 江 塑 胶 制 品 有 限 公 司 东 江 塑 胶 制 品 (深 圳 )有 限 公 司
文件名称
质量管理文件
文件编号:QMS-WI05-P 版本:01 第 4 页共 4 页
注塑工艺调校及参数管理作业指导书
生产的注塑参数由工艺员(工艺技工)设定,必要时注塑科文参与设定。 第一次生产时由技术员取出该产品试样用<注塑工艺咭>参考调校参数。 品质合格后工艺员(工艺技工)填写生产的<注塑工艺咭>并经注塑科文审批后摆放机位,< 注塑工艺咭>需按顺序填上编号。 量 产 注 塑 参 数 试样的<注塑工艺咭>取回注塑办公室存档。 当第二次以上生产并于相同的机型生产时,由工艺员(工艺技工) (必要时可注塑科文)到 过往生产的<注塑工艺咭>参考调校参数。 调校的参数与旧参数相差不大时,仍可将旧<注塑工艺咭>摆于机位使用,但需将超差的参 数于变更栏说明及确认,并于再生产栏填写再生产日期及确认。 调校的参数与旧参数相差较大时,时需从新填写<注塑工艺咭>并经注塑科文审批后摆于机 位使用,旧<注塑工艺咭>需取回注塑车间办公室存档。 生产过程中,因品质等问题而变更注塑参数时,胶料干燥温度相差±10℃,其它温度相差 ±5℃以上或其它相差±5%以上时,而修正<注塑工艺咭>,并重新确认。 任何的注塑生产机位必须有<注塑工艺咭>支持,当生产完毕时需将<注塑工艺咭>取回注塑 车间办公室存档。 工艺技工对生产中难以调校的制品或达不到品质要求的制品,以及生产中其它疑难问题; — 当凭自己经验和技术难以解决时,不能盲目进行,应将此情况及时告知注塑科文,共同协商 解决。 — 接到疑难问题时,注塑科文首先要认真分析原因,制定改善对策,如不能改善,应及时上报。 — 技术主管针对下属提出的问题,应及时召集工艺工程师等相关人员,制订改善措施。如与其 它部门有关系的,应及时联络沟通,制定改善措施达成共识后及时上报。
- 1、下载文档前请自行甄别文档内容的完整性,平台不提供额外的编辑、内容补充、找答案等附加服务。
- 2、"仅部分预览"的文档,不可在线预览部分如存在完整性等问题,可反馈申请退款(可完整预览的文档不适用该条件!)。
- 3、如文档侵犯您的权益,请联系客服反馈,我们会尽快为您处理(人工客服工作时间:9:00-18:30)。
1.0目的制定本指导书的目的,是对注塑工艺参数在设置、变更和记录、监督过程中可以标准化操作的部分进行规范,提高工艺参数的稳定性和再现性,减少注塑车间在换模、换料的生产切换过程中材料的损耗与工时的浪费,达到提高生产效率、稳定产品品质的目的。
2.0范围适用注塑车间注塑机工艺参数的设置与管理3.0职责3.1调机员:正确的使用标准成型工艺,并对存在的问题及时向领班反馈,配合领班完成对异常情况的处理。
3.2领班:正确的使用标准成型工艺,当因机器、模具、材料、运水等原因原标准成型工艺参数不适用时,根据实际情况作出相应改变以保证生产的进行并配合在工艺改变后IPQC的品质确认工作。
并将工艺变更情况向主管汇报。
3.3主管:发布和认可标准成型工艺,确认工艺变更的正确性并完成相应记录。
对不正确的工艺进行修改并将原因告示领班和技术员,确保生产是在正常和经济的状态下进行。
4.0标准成型工艺参数的设置和调整的一般原理和注意事项4.1设置成型参数的一般原理和注意事项。
4.1.1合模参数的设定。
合模一般分为四段。
4.1.1.1慢速开始:为使机器平稳启动、合模应以慢速开始。
4.1.1.2快速到位:动模板在合模油缸推动下快速运动,以缩短工作周期。
4.1.1.3低压保护:油缸低压低速运动,以保护模具安全。
对于三板模或有斜顶、铲机结构的模具,动、定模接触时应适当降低速度和压力。
4.1.1.4高压合模:以所需的合模力锁紧模具。
应选用最低而又不使成品产生毛边的合模力,既能提高效率又能延长机器模具寿命。
4.1.2开模参数的设定。
开模一般分为三段。
4.1.2.1慢速开模:为不使产品撕裂、变形,应以慢速开模开始。
4.1.2.2快速到位:模具一经打开,应转为快速开模到位,以缩短工作周期。
但对于三板模具、有斜顶滑块的模具,在动、定模分离时应适当设定速度和压力,减轻对模具和机器的冲击和降低噪音。
4.1.2.3慢速终止:将到终点时,为防止惯性产生冲击,应由中速转为慢速终止。
4.1.3顶出和顶退参数的设置。
要注意提高生产效率、保护模具和降低噪音。
4.1.3.1顶出应选用能使模具顶出机构正稳运动的最高速度。
必须保证产品不能出现变形、白化、撕裂等顶出动作导致的缺陷。
4.1.3.2顶退应选用能使顶出机构平稳复位的较低压力和较高速度。
4.1.4熔胶温度的设置。
熔胶温度通常包括料筒温度和热流道温度两部分。
4.1.4.1熔胶温度设定的范围,应当高于塑料的熔点或软化温度,低于塑料的分解温度。
4.1.4.2需注意设定温度与实际温度之间的差异。
必要时可通过目视检查塑料的熔融状态或热电偶温度计检查。
4.1.5计量、背压和熔胶速度。
在塑料熔融、塑化过程中,熔料不断移向料筒前端(计量室内),且越来越多,逐渐形成一个压力,推动螺杆向后退。
为了阻止螺杆后退过快,确保熔料均匀压实,需要给螺杆提供一个反方向的压力,这个反方向阻止螺杆后退的压力称背压。
螺杆的转速即为熔胶速度。
螺杆后移的距离即为计量。
4.1.5.1注塑机不用于加工小于其注塑容量10%或大于其注塑容量70%的产品;4.1.5.2熔胶压力和熔胶速度要设置恰当,计量时间(熔胶时间)不大于最短冷却周期。
4.1.5.3当得知模取重量,可根据公式估算计量行程LL=Si=ViD2=m÷ρ0.785×D2L:计量行程Si:推进容量D:螺杆直径M:质量ρ:密度4.1.6填充参数的设置。
在高压合模完成后开始,注射油缸推动螺杆前进,把螺杆前熔融的塑料注入模腔。
在保证成品没有气痕、烧焦等缺陷的前提下,应尽可能提高填充速度。
4.1.6.1必须采用多级注射工艺。
操作上以三级注塑工艺设置为基础,需要时设置为四级、五级或更多级别的填充工艺。
4.1.6.2三级填充的设置要领为:第一级低速通过浇口,消除膨大效应和熔体破裂导致的缺陷,第二级快速,提高生产效率;第三级低速,避免因模具排气不良导致的缺陷。
操作中需根据实际情况灵活调整。
4.1.7保压参数的设置。
模腔填充完毕,熔体停止高速流动遇冷收缩定型。
保压的作用是保持一定的压力将熔体经过尚未凝固的浇口不断填充冷却定型时材料体积收缩形成的凹陷或空洞,使成品脱模时饱满。
4.1.7.1保压亦可分为多级设置不同级别的保压压力和保压时间。
通过目视检查或尺寸测量成品来衡量保压设置是否合适。
4.1.7.2使用高分度电子秤称量成品重量。
在保压压力一定按1或0.5秒间隔递增设置保压时间,或保压时间一定按10%或5%间隔递增设置保压压力。
通过测量每个参数的成品平均重量,可评估最佳保压压力和保压时间的设置值。
该方法也可用于评估保压速度的设置。
4.1.7.3薄壁产品填充完毕即已凝固,可不用保压。
4.1.8填充/保压切换模式。
熔体填充模腔完毕停止快速流动即进入收缩定型阶段。
注塑机注射系统由填充却换为保压的模式通常有四种:位置/时间切换模式、时间切换模式、压力切换模式、位置切换模式。
4.1.8.1必须优先使用“位置/时间”切换模式。
4.1.8.2“位置/时间”切换模式下,最佳位置参数的设置要领是:寻找产品投影面填充完成99%~100%,产品重量填充到95%~99%的位置点,在该位置连续成型3~5模产品,如果成型出来的产品重量稳定,该位置就是最佳切换位置。
4.1.9冷却时间:指模腔内成品冷却定型所需要的时间,从保压结束开始计算到模具开模为止结束。
在满足以下两点要求时应设置最短冷却时间以提高生产效率:4.1.9.1必须需保证产品脱模、取出顺利,没有白化、顶高、变形,产品能满足测量、试装需求。
4.1.9.2必须保证模具温度稳定,能连续生产。
4.1.10模具冷却系统的温度控制。
熔融态的塑料被高压注入模腔,在模腔内释放热量冷却到热变形温度以下固化成型。
该过程是由熔料和模具的温差实现的。
由于不同的成型材料要求不同的模具温度(模具温度应低于塑件热变形温度),若模腔表面温度异常,都会影响塑件的变形、尺寸精度、力学性能和外观等质量指标,以及影响生产效率。
模具的常用冷却介质是水和油,介质流动的通道通常叫“水道”、“水路”、“运水”。
常用制冷设备是水塔和恒温机(加热或制冷)4.1.10.1在串联或并联模具水路和制冷设备时,要注意均匀有效。
均匀是进出水管的方向和位置要搭配恰当使模具能均匀散热;有效是指尽少串联水路,尽量避免因一点受阻影响整组串联水路。
下图示意了3路运水的不同联接方式,其右边优于左边,下边的优于上边。
(水路连接示意图)4.1.10.2对于特殊产品或特殊模具,可通过局部制冷或局部加温实现生产目的。
4.2注塑成型工艺参数的管理流程。
4.2.1试产工艺参数的设置与标准化。
4.2.1.1试产时,调机员、领班需根据材料、模具、产品、机器的特点,设置相应的工艺参数。
参数内容需符合“使用多级注射工艺”和“优先选用位置/时间切换模式”两项原则。
所成型的产品满足品质要求,且维持较低的工艺不良率。
4.2.1.2试产结束时,调机员、领班填写《注塑成型工艺参数表》,并附上完整的走胶板、完整的成型样板(含水口),一并交主管审核。
审核后发行的参数即为“S”版参数,供后续试产或量产参考。
4.2.2量产工艺参数的设置。
4.2.2.1在开机前,技术员、领班按照工艺参表数据输入参数,并确认模具水路连接是否正确,阀门是否打开。
4.2.2.2将保压时间设置为“0”,开机成型3~5模产品,检查保压切换位置是否偏移。
若出现偏移,微调直至找准切换点,然后输入参数表记录的保压时间。
4.2.2.3产品经自检合格,在成型5模产品后,取1模产品送IPQC做首件检查。
根据IPQC反馈对参数微调,直到首件检查合格方可开机生产。
4.2.3标准成型参数的微调原则。
《注塑成型工艺参数表》记录的数据大体分为两部分内容。
一部分是与模具开合、顶针进退等辅助动作有关的,主要影响生产效率;第二部分是与温度、射出、保压有关的参数,与产品品质密切相关。
4.2.3.1对第一部分主要影响生产效率的参数,在调整上以符合一般操作要求和不影响生产效率为准绳。
4.2.3.2第二部分参数的调整要求参照下面表格。
对于已经通过首件检验的产品,工艺参数即使在表格允许范围内调整,也必须通知IPQC。
4.2.4临时成型工艺参数的设置。
由于机器、模具、材料、辅助设备故障、设计变更等原因,导致按标准工艺参数生产的产品无法满足品质要求,或制程中产品出现超过5%的工艺不良,技术员、领班有义务设置临时成型工艺参数对成型工艺进行改进,确保生产顺利进行。
4.2.4.1 在只能使用临时工艺参数生产产品时需将情况告知主管。
主管需主持调查变异的原因并提出纠正预防措施。
4.2.4.2 临时工艺参数若属于对原有工艺的改进与补充,参照本节第一条试产参数管理,发行新的标准工艺参数。
5.0 参考文件NPC 注塑成型机《产品使用说明书》《注塑成型工艺参数表》《常用注塑材料特性一览表》6.0流程图 试产准备试产工艺设置确认量产工艺设置确认 临时工艺设置工艺标准化 ORNG NG。