复杂钣金零件渐进成形方法
探究复杂钣金零件的工序形状设计技术
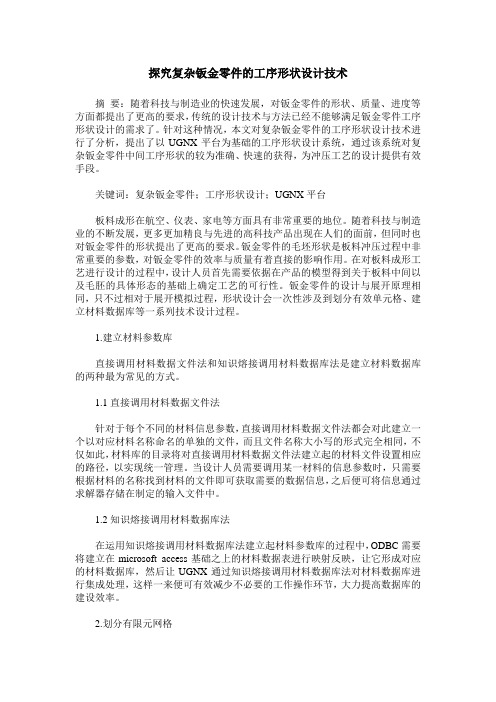
探究复杂钣金零件的工序形状设计技术摘要:随着科技与制造业的快速发展,对钣金零件的形状、质量、进度等方面都提出了更高的要求,传统的设计技术与方法已经不能够满足钣金零件工序形状设计的需求了。
针对这种情况,本文对复杂钣金零件的工序形状设计技术进行了分析,提出了以UGNX平台为基础的工序形状设计系统,通过该系统对复杂钣金零件中间工序形状的较为准确、快速的获得,为冲压工艺的设计提供有效手段。
关键词:复杂钣金零件;工序形状设计;UGNX平台板料成形在航空、仪表、家电等方面具有非常重要的地位。
随着科技与制造业的不断发展,更多更加精良与先进的高科技产品出现在人们的面前,但同时也对钣金零件的形状提出了更高的要求。
钣金零件的毛坯形状是板料冲压过程中非常重要的参数,对钣金零件的效率与质量有着直接的影响作用。
在对板料成形工艺进行设计的过程中,设计人员首先需要依据在产品的模型得到关于板料中间以及毛胚的具体形态的基础上确定工艺的可行性。
钣金零件的设计与展开原理相同,只不过相对于展开模拟过程,形状设计会一次性涉及到划分有效单元格、建立材料数据库等一系列技术设计过程。
1.建立材料参数库直接调用材料数据文件法和知识熔接调用材料数据库法是建立材料数据库的两种最为常见的方式。
1.1直接调用材料数据文件法针对于每个不同的材料信息参数,直接调用材料数据文件法都会对此建立一个以对应材料名称命名的单独的文件,而且文件名称大小写的形式完全相同,不仅如此,材料库的目录将对直接调用材料数据文件法建立起的材料文件设置相应的路径,以实现统一管理。
当设计人员需要调用某一材料的信息参数时,只需要根据材料的名称找到材料的文件即可获取需要的数据信息,之后便可将信息通过求解器存储在制定的输入文件中。
1.2知识熔接调用材料数据库法在运用知识熔接调用材料数据库法建立起材料参数库的过程中,ODBC需要将建立在microsoft access基础之上的材料数据表进行映射反映,让它形成对应的材料数据库,然后让UGNX通过知识熔接调用材料数据库法对材料数据库进行集成处理,这样一来便可有效减少不必要的工作操作环节,大力提高数据库的建设效率。
金属板材的数控单点渐进成形技术
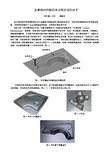
金属板材的数控单点渐进成形技术
华中理工大学 莫健华
本次深圳培训班讲课的亮点在于金属板材的数控单点渐进成形技术。
该技术获得国家自然科学基金资助、科技部科技型中小企业创新基金的资助,并获得中国发明专利。
该技术是一种无模具成形方法。
其基本原理是引入快速成形制造技术“分层制造(Layered
Manufacturing )”的思想,将复杂的三维数字模型沿高度方向分层,形成一系列断面二维数据,并根据这些断面轮廓数据,从顶层开始逐层对板材进行局部的塑性加工。
加工过程是:在计算机控制下,安装在三轴联动的数控成形机床上的成形压头,先走到模型的顶部设定位置,即加工轨迹的起点,对板材压下设定的压下量,然后按照第一层断面轮廓,以走等高线的方式,对板材施行渐进塑性加工。
在模型顶部板材加工面形成第一层轮廓曲面后,成形压头再压下一个设定高度,沿第二层断面轮廓运动,并形成第二层轮廓曲面。
如此重复直到整个工件成形完毕(图1)。
这种成形技术很适合汽车新车型开发时,用于快速制造概念车的覆盖件。
也适合航空业中飞行器的开发和制造;其他壳形件的快速制造。
图2、3、4是用该技术加工的工件。
成形压头 加工轨迹 成形部分 板料
图1 汽车覆盖件的渐进成形模拟图
图2 汽车门外覆盖件 图3 工艺品 图4 汽车翼子板覆盖件。
金属板材数控渐进成形加工轨迹交互修改及优化分析

金属板材数控渐进成形加工轨迹交互修改及优化分析通过CAD模型,能够直接驱动金属板材数控渐进成型技术,来设计完成柔性快速一体化的制造与加工。
这种技术在提升加工效率上必然会发挥巨大的作用,对此,文章对相关方面的内容进行了论述。
标签:金属板材;数控渐成形;加工轨迹;交互修改优化1 加工原理分析沿着z轴方向将复杂的三维形状离散化处理,就是将多个二维断面层分解出来,在二维断面层上,塑性加工其局部。
图1为基本的加工原理图。
在一个支撑模型9上放置被加工板材3,在板材周围通过压板4在托板5上将材料夹紧,可以顺着导柱6自由上下滑动托板。
在三轴联动的数控无模成形机上固定该装置,加工的过程中,首先在指定的位置控制成形工具头,将压下量设定在板材下,之后在控制系统的作用下,在第一层截面轮廊规定下,通过等高线的形式,渐进塑性加工板材。
在第一层截面轮廊形成之后,将高度在成形工具头压下设定出来,再依据下一层截面轮廊的规定去运动,从而将这一层的轮廊构造出来。
多次这样操作,直到加工完成整个工件为止。
加工轨迹与工艺规划是这些塑性加工成型的重点。
工件的成型精度不仅会直接受到它的影响,同时,不恰当的轨迹与工艺会直接造成加工受阻。
2 具体的修改和优化对策分析2.1 优化改造CAM/CAD软件生成加工轨迹通过图2中所示的工艺路线,对板材数控渐进成型过程进行改进与优化,首先,在工艺要求的基础上,将零件的CAD模型在通用的CAM/CAD软件中构建起来,再从CAD模型着手,将工艺模型制作出来,并且在此基础上构成加工轨迹和支撑模型,之后加工模板,使其成为需要的模型。
然而,在成形的时候,垂直部分的板材变形或者工件的尖角处,因为超过了相应的塑性变形极限,这样塌陷和破裂问题极易发生。
所以,需要根据实际情况认真的修改这些部位的加工轨迹。
但是,在加工修改这些加工轨迹的时候,一定要转换到过去的三维模型中。
再将加工轨迹重新生成出来,比如图2中的第一种方法。
一般的时候,是通过多个细小的面片缝合而得到CAD模型中的复杂曲面,因此,在进行修改的时候就会面临很多的困难。
金属板材智能渐进成形关键技术及其应用

金属板材智能渐进成形关键技术及其应用
本项目为了克服难成形金属板材(如,AZ系列镁合金、TC系列钛合金等)室温成形性能较差、成形效率较低、成形质量较差等问题,提出了一种油浴辅助加热渐进成形新技术,将难成形金属板材的优异机械性能和渐进成形技术的先进性有机结合在一起,并对油浴辅助加热渐进成形新技术的微观成形机制、成形零件缺陷形态及其形成原因和解决措施、渐进成形工艺及渐进成形设备改进等多个方面进行了理论分析和实验研究。
该项目采用机器视觉技术和模糊识别处理技术实时监测并记录渐进成形过程中已经成形表面的变形情况,识别金属板材数控渐进成形零件的表面质量、尺寸误差、壁厚误差、破裂和回弹等缺陷状况,建立缺陷形态预估模型,提高成形零件质量。
该项目采用人工智能技术建立工艺参数修正及优化模型,动态在线规划工艺参数及刀具路径,优化工艺过程,缩短成形时间,提高成形效率。
该项目很好的解决了航空航天、交通运输及医疗器件等产业中单件、小批量个性化定制及产品开发试制中的高费用问题,并增加高端制造装备的科技附加值。
推广应用该项技术,能够在不增加设备投入的情况下,极大地提高难成形金属板材的成形性能、成形质量和成形效率,对促进渐进成形技术的进步和成形零部件生产制造都具有十分重大的现实意义。
金属板材三点渐进成形技术基础研究

(5)实验研究了工艺参数对三点渐进成形质量的影响,归纳了工艺参数选取的一般原则。基于离散定义域内线性插值,实现了等高线加工轨迹规划。
利用实验研究了进给量、工具头等对几何轮廓和表面质量的影响。基于目标曲面的数学描述,利用法向渐变屈服的变形映射关系,建立了板厚计算的全新表达形式。
通过锥台件在几何精度主应变、板厚及表面质量等方面的理论研究、数值分析和实验结果的比较,验证了本文所做的理论分析及方法的正确性。最后,探讨了椭球面件、凹凸特征件等复杂零件的成形实验和方法。
(4)研究并建立了基于LS-DYNA的三点渐进成形数值分析方法,并以此为基础探讨了其变形机理和特点。基于增量理论和塑性势关联算法,实现了锥台件成形的有限元模拟。
锥台件的仿真结果验证了所提等效加工层模型、法向屈服变形算法和平面应变等力学特征的正确性,证实了三点渐进成形精度高、局部变形范围小、变形控制有效。探讨了其变形主要模式是弯曲、挤压和剪切的联合作用,分析了其根本原因在于对顶式辅助工具头和支撑工具头的引入。
(2)研究并探讨了三点渐进成形等效加工层的塑性变形力学特征。利用薄膜分析理论和平面应变条件,建立了描述变形规律的力学方程,求解了等效虚拟应力应变,分析了其变形状态和变形方式,为理解其变形机理本质和指导路径规划、工艺参数设计提供了理论依据。
(3)研究了基于法向渐变屈服的三点渐进成形变形基本算法。通过分析初始板材到目标形状映射的变形轨迹,求解了变形过程中的分层塑性位移,计算了任一节点的变形过程及历史位移等信息,为预测几何形状和板材减薄提供了基础依据。
刍议拉形与渐进成形在钣金零件快速制造中的复合运用
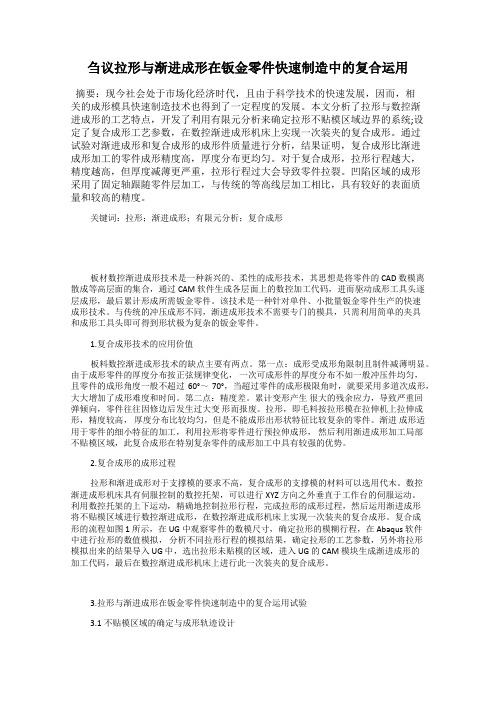
刍议拉形与渐进成形在钣金零件快速制造中的复合运用摘要:现今社会处于市场化经济时代,且由于科学技术的快速发展,因而,相关的成形模具快速制造技术也得到了一定程度的发展。
本文分析了拉形与数控渐进成形的工艺特点,开发了利用有限元分析来确定拉形不贴模区域边界的系统;设定了复合成形工艺参数,在数控渐进成形机床上实现一次装夹的复合成形。
通过试验对渐进成形和复合成形的成形件质量进行分析,结果证明,复合成形比渐进成形加工的零件成形精度高,厚度分布更均匀。
对于复合成形,拉形行程越大,精度越高,但厚度减薄更严重,拉形行程过大会导致零件拉裂。
凹陷区域的成形采用了固定轴跟随零件层加工,与传统的等高线层加工相比,具有较好的表面质量和较高的精度。
关键词:拉形;渐进成形;有限元分析;复合成形板材数控渐进成形技术是一种新兴的、柔性的成形技术,其思想是将零件的 CAD 数模离散成等高层面的集合,通过 CAM 软件生成各层面上的数控加工代码,进而驱动成形工具头逐层成形,最后累计形成所需钣金零件。
该技术是一种针对单件、小批量钣金零件生产的快速成形技术。
与传统的冲压成形不同,渐进成形技术不需要专门的模具,只需利用简单的夹具和成形工具头即可得到形状极为复杂的钣金零件。
1.复合成形技术的应用价值板料数控渐进成形技术的缺点主要有两点。
第一点:成形受成形角限制且制件减薄明显。
由于成形零件的厚度分布按正弦规律变化,一次可成形件的厚度分布不如一般冲压件均匀,且零件的成形角度一般不超过60°~70°,当超过零件的成形极限角时,就要采用多道次成形,大大增加了成形难度和时间。
第二点:精度差。
累计变形产生很大的残余应力,导致严重回弹倾向,零件往往因修边后发生过大变形而报废。
拉形,即毛料按拉形模在拉伸机上拉伸成形,精度较高,厚度分布比较均匀,但是不能成形出形状特征比较复杂的零件。
渐进成形适用于零件的细小特征的加工,利用拉形将零件进行预拉伸成形,然后利用渐进成形加工局部不贴模区域,此复合成形在特别复杂零件的成形加工中具有较强的优势。
渐进成形技术

工作原理
类型
渐进成形分为负成形(NIF)与正成形( PIF)。 1、负成形可以成形一些形状比较简单的 零件,它不需要支撑模型,只需要简单的夹具 即可。板料由夹具夹紧,然后成形压头按设定 好的程序实现分层加工,每加工一层,成形压 头便下降一定距离,进行第二层的加工,如此 直至结束,在加工过程中夹具夹紧板料始终不 动。
负成形
负成形方法中,需要支撑模型,支撑 模型的轮廓形状要与所成形的零件的形状一致 ,在加工中起到支撑的作用,这种支撑模型与 冲压成形中的模具有很大差别,它的精度要求 不是很高,并且材料的选择上比较灵活。在这 种成形方法中,首先要加工支撑模型,支撑模 型加工完毕后再放上板料,与负成形所不同的 是正成形中成形压头每走完一层的路径,托板 都要带动板料与成形压头共同向下移动相同距 离。数控成形装置主要由成形压头、导向装置 (导柱、导套)、顶支撑模型、托板、夹具组 成。
特点、优势
研究现状
问题: 1、破裂(成形角大到一定角度就会发生); 2、零件精度及回弹。 考虑: 1、从影响成形极限角的因素(板料厚度、 压头直径、模型形状)考虑改进; 2、通过优化压头路径可以提高表面光洁度 ,减小回弹,提高零件精度。
发展前景
目前渐进成形技术在工业领域还没有得到 大规模应用,技术手段和工艺方面还有待继续 深入研究。国内外学者在应用方面也做了很多 的探索。 该方法实现了复杂形状的成形,并且经济 快捷,对于传统的冲压等板材成形方法也是很 大的补充。
正成形
正成形示意图
产品
本田S800跑车引擎盖 金属面具
特点、优势
1、实现柔性制造。不需要专用模具,与传统成形 方法相比,可节省巨额的模具制造费用,对航空航天 领域等多种小批量产品,家用电器等新产品的开发及 汽车新型车试制等具有较大的经济价值和发展前景。 2、重复性好。由数控机床控制成形压头的运动, 可以保证成形零件的重复性好,可控制金属流动。 3、具备快速成形技术和塑性加工技术的优点。 可以极大降低产品的制造成本并缩短开发级制造周期 。 4、实现数字化分层局部制造。可以把形状复杂 的零件分成一系列的二维层进行加工,便于成形且修 改方便。
金属板材渐进成形工具头运动策略与成形质量分析
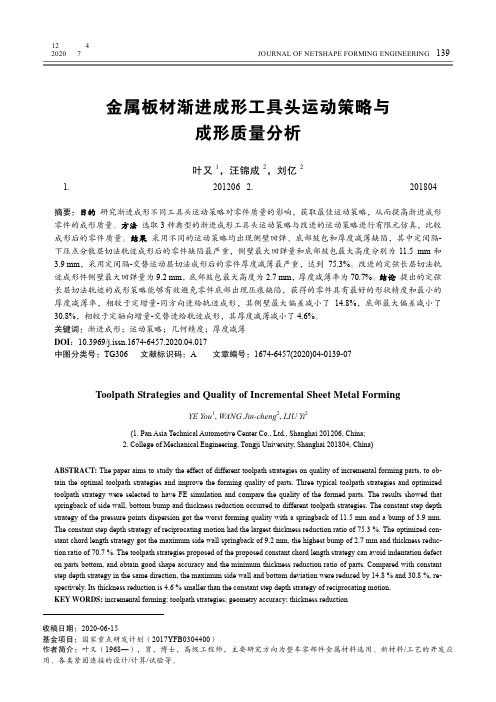
第12卷第4期精密成形工程2020年7月JOURNAL OF NETSHAPE FORMING ENGINEERING139金属板材渐进成形工具头运动策略与成形质量分析叶又1,汪锦成2,刘亿2(1. 泛亚汽车技术中心有限公司,上海 201206;2. 同济大学机械与能源工程学院,上海 201804)摘要:目的研究渐进成形不同工具头运动策略对零件质量的影响,获取最佳运动策略,从而提高渐进成形零件的成形质量。
方法选取3种典型的渐进成形工具头运动策略与改进的运动策略进行有限元仿真,比较成形后的零件质量。
结果采用不同的运动策略均出现侧壁回弹、底部鼓包和厚度减薄缺陷,其中定间隔-下压点分散层切法轨迹成形后的零件缺陷最严重,侧壁最大回弹量和底部鼓包最大高度分别为11.5 mm和3.9 mm,采用定间隔-交替运动层切法成形后的零件厚度减薄最严重,达到75.3%。
改进的定弦长层切法轨迹成形件侧壁最大回弹量为9.2 mm,底部鼓包最大高度为2.7 mm,厚度减薄率为70.7%。
结论提出的定弦长层切法轨迹的成形策略能够有效避免零件底部出现压痕缺陷,获得的零件具有最好的形状精度和最小的厚度减薄率,相较于定增量-同方向进给轨迹成形,其侧壁最大偏差减小了14.8%,底部最大偏差减小了30.8%,相较于定轴向增量-交替进给轨迹成形,其厚度减薄减小了4.6%。
关键词:渐进成形;运动策略;几何精度;厚度减薄DOI:10.3969/j.issn.1674-6457.2020.04.017中图分类号:TG306 文献标识码:A 文章编号:1674-6457(2020)04-0139-07Toolpath Strategies and Quality of Incremental Sheet Metal FormingYE You1, WANG Jin-cheng2, LIU Yi2(1. Pan Asia Technical Automotive Center Co., Ltd., Shanghai 201206, China;2. College of Mechanical Engineering, Tongji University, Shanghai 201804, China)ABSTRACT: The paper aims to study the effect of different toolpath strategies on quality of incremental forming parts, to ob-tain the optimal toolpath strategies and improve the forming quality of parts. Three typical toolpath strategies and optimized toolpath strategy were selected to have FE simulation and compare the quality of the formed parts. The results showed that springback of side wall, bottom bump and thickness reduction occurred to different toolpath strategies. The constant step depth strategy of the pressure points dispersion got the worst forming quality with a springback of 11.5 mm and a bump of 3.9 mm.The constant step depth strategy of reciprocating motion had the largest thickness reduction ratio of 75.3 %. The optimized con-stant chord length strategy got the maximum side wall springback of 9.2 mm, the highest bump of 2.7 mm and thickness reduc-tion ratio of 70.7 %. The toolpath strategies proposed of the proposed constant chord length strategy can avoid indentation defect on parts bottom, and obtain good shape accuracy and the minimum thickness reduction ratio of parts. Compared with constant step depth strategy in the same direction, the maximum side wall and bottom deviation were reduced by 14.8 % and 30.8 %, re-spectively. Its thickness reduction is 4.6 % smaller than the constant step depth strategy of reciprocating motion.KEY WORDS: incremental forming; toolpath strategies; geometry accuracy; thickness reduction收稿日期:2020-06-15基金项目:国家重点研发计划(2017YFB0304400)作者简介:叶又(1968—),男,博士,高级工程师,主要研究方向为整车零部件金属材料选用、新材料/工艺的开发应140精密成形工程 2020年7月工业4.0对全球制造业产生了巨大的影响,传统的大批量生产模式正逐渐向大规模定制转变,新的工业浪潮对按需生产和柔性制造提出了更高的需求[1]。
渐进成形技术

正成形
正成形示意图
产品
本田S800跑车引擎盖 金属面具
特点、优势
1、实现柔性制造。不需要专用模具,与传统成形 方法相比,可节省巨额的模具制造费用,对航空航天 领域等多种小批量产品,家用电器等新产品的开发及 汽车新型车试制等具有较大的经济价值和发展前景。 2、重复性好。由数控机床控制成形压头的运动, 可以保证成形零件的重复性好,可控制金属流动。 3、具备快速成形技术和塑性加工技术的优点。 可以极大降低产品的制造成本并缩短开发级制造周期 。 4、实现数字化分层局部制造。可以把形状复杂 的零件分成一系列的二维层进行加工,便于成形且修 改方便。
特点、优势
研究现状
问题: 1、破裂(成形角大到一定角度就会发生); 2、零件精度及回弹。 考虑: 1、从影响成形极限角的因素(板料厚度、 压头直径、模型形状)考虑改进; 2、通过优化压头路径可以提高表面光洁度 ,减小回弹,提高零件精度。
发展前景
目前渐进成形技术在工业领域还没有得到 大规模应用,技术手段和工艺方面还有待继续 深入研究。国内外学者在应用方面也做了很多 的探索。 该方法实现了复杂形状的成形,并且经济 快捷,对于传统的冲压等板材成形方法也是很 大的补充。
负成形
负成形示意图
负成形机床
正成形
2、 正成形方法中,需要支撑模型,支撑 模型的轮廓形状要与所成形的零件的形状一致 ,在加工中起到支撑的作用,这种支撑模型与 冲压成形中的模具有很大差别,它的精度要求 不是很高,并且材料的选择上比较灵活。在这 种成形方法中,首先要加工支撑模型,支撑模 型加工完毕后再放上板料,与负成形所不同的 是正成形中成形压头每走完一层的路径,托板 都要带动板料与成形压头共同向下移动相同距 离。数控成形装置主要由成形压头、导向装置 (导柱、导套)、顶支撑模型、托板、夹具组 成。
钣金加工零件有哪些成型方法
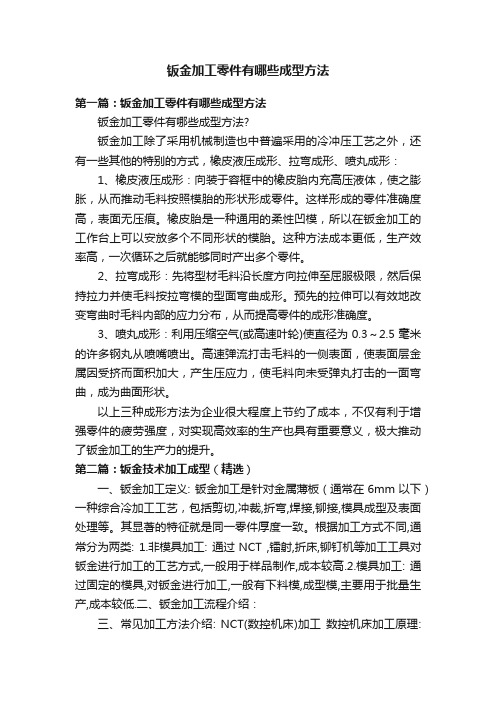
钣金加工零件有哪些成型方法第一篇:钣金加工零件有哪些成型方法钣金加工零件有哪些成型方法?钣金加工除了采用机械制造也中普遍采用的冷冲压工艺之外,还有一些其他的特别的方式,橡皮液压成形、拉弯成形、喷丸成形:1、橡皮液压成形:向装于容框中的橡皮胎内充高压液体,使之膨胀,从而推动毛料按照模胎的形状形成零件。
这样形成的零件准确度高,表面无压痕。
橡皮胎是一种通用的柔性凹模,所以在钣金加工的工作台上可以安放多个不同形状的模胎。
这种方法成本更低,生产效率高,一次循环之后就能够同时产出多个零件。
2、拉弯成形:先将型材毛料沿长度方向拉伸至屈服极限,然后保持拉力并使毛料按拉弯模的型面弯曲成形。
预先的拉伸可以有效地改变弯曲时毛料内部的应力分布,从而提高零件的成形准确度。
3、喷丸成形:利用压缩空气(或高速叶轮)使直径为0.3~2.5毫米的许多钢丸从喷嘴喷出。
高速弹流打击毛料的一侧表面,使表面层金属因受挤而面积加大,产生压应力,使毛料向未受弹丸打击的一面弯曲,成为曲面形状。
以上三种成形方法为企业很大程度上节约了成本,不仅有利于增强零件的疲劳强度,对实现高效率的生产也具有重要意义,极大推动了钣金加工的生产力的提升。
第二篇:钣金技术加工成型(精选)一、钣金加工定义: 钣金加工是针对金属薄板(通常在6mm以下)一种综合冷加工工艺,包括剪切,冲裁,折弯,焊接,铆接,模具成型及表面处理等。
其显著的特征就是同一零件厚度一致。
根据加工方式不同,通常分为两类: 1.非模具加工: 通过NCT ,镭射,折床,铆钉机等加工工具对钣金进行加工的工艺方式,一般用于样品制作,成本较高.2.模具加工: 通过固定的模具,对钣金进行加工,一般有下料模,成型模,主要用于批量生产,成本较低.二、钣金加工流程介绍:三、常见加工方法介绍: NCT(数控机床)加工数控机床加工原理:数控机床是一种能够适应产品频繁变化的柔性自动化机床,加工过程所需的各种操作和步骤以及刀具与工件之间的相对位移量都用数字化的代号来表示,通过控制介质(如纸带或磁盘)将数字信息送入专用的或通用的计算器,计算器对输入的信息进行处理和运算,发出各种指令来控制机床的伺服系统或其它执行组件,使机床自动加工出所需要的工件或产品.数控机床常见用途: 下料,冲网孔,冲凸包,切边,打凸点,压筋,压线,抽孔数控机床的加工精度: +/-0.1mm NCT(数控冲床)加工的工艺处理及注意事项: 1.在距边缘的距离小于料厚时,冲方孔会导致边缘被翻起,方孔越大翻边越明显,此时常常考虑LASER二次切割.2.NCT冲压的孔与孔之间,孔与边缘之间的距离不应过小,其允许值如表;材料冲圆孔冲方孔硬钢 0.5t 0.4t 软钢,黄铜 0.35t 0.3t 铝 0.3t 0.28t NCT冲压的最小孔径如表: 材料冲圆孔冲方孔硬钢1.3T 1.0T 软钢,黄铜1.0T 0.7T 铝0.8T 0.6T 注:T表示料厚3.抽孔:NCT抽孔离边缘最小距离为3T,两个抽孔之间的最小距离为6T,抽孔离折弯边(内)的最小安全距离为3T+R,如偏小则须压线处理.4.经现场测试,NCT冲半剪凸点的高度不超过0.6T,如大于0.6T则极易脱落.镭射加工镭射加工原理: Laser是由Light Amplification by Stimulated Emission of Radiation的前缀缩写而成.原意为光线受激发放大,一般译为激光(也称激光).激光切割是由电子放电作为供给能源,通过He、N2、CO2等混合气体为激发媒介,利用反射镜组聚焦产生激光光束,从而对材料进行切割.在由程控的伺服电机驱动下,切割头按照预定路线运动,从而切割出各种形状的工件。
渐进码塑性压缩成形汽车车身板件的研究

渐进码塑性压缩成形汽车车身板件的研究渐进码塑性压缩成形(Progressive Die Plastic Compression Molding)是一种汽车车身板件加工和制造的方法,它通过利用连续进行的变形工序,将一张平面金属片逐步压缩成需要的形状。
这种技术在汽车制造业中得到广泛应用,其研究和发展也成为当前热门的领域。
本文将探讨渐进码塑性压缩成形汽车车身板件的研究,并分析该技术对汽车工业的影响。
第一部分:渐进码塑性压缩成形的原理和工艺渐进码塑性压缩成形技术的核心是渐进码模具。
该模具由一系列连续排列的工位组成,每个工位都有特定功能,可以完成金属板件的压缩、切割、弯曲等操作。
工件必须通过模具的每个工位,才能达到最终所需的形状。
在渐进码塑性压缩成形过程中,金属板材先经过装夹工位,固定在模具上。
模具随着机床的运动逐渐将金属板塑性变形到需求的形状,并通过剪裁、冲孔等工序进行后续处理。
这种连续变形过程能够有效提高生产效率和精度,并且减少了人工操作的需求。
第二部分:渐进码塑性压缩成形在汽车车身板件制造中的应用渐进码塑性压缩成形技术在汽车制造业中得到广泛应用,特别是在汽车车身板件的制造过程中。
以前,车身板件的制造通常需要多次操作和多个模具,而渐进码塑性压缩成形技术使得整个过程变得更加高效和精确。
通过渐进码模具的连续工序,可以在一个模具内完成多个操作,如切割、折弯、冲孔等。
这不仅提高了生产效率,还减少了所需设备和工艺的数量。
与传统的车身板件制造相比,这种技术可以减少成本和制造周期。
此外,渐进码塑性压缩成形还可以实现更复杂形状的车身板件制造。
与传统的液压成形相比,该技术具有更好的形状控制能力。
通过调整模具的设计和控制工艺参数,可以实现更高的精度和一致性。
这对于汽车制造商来说,意味着他们可以生产出更符合设计要求的车身板件,提升整体质量和竞争力。
第三部分:渐进码塑性压缩成形对汽车工业的影响渐进码塑性压缩成形技术的广泛应用,对汽车工业产生了积极的影响。
金属板料渐进成形工艺过程有限元模拟

金属板料渐进成形工艺过程有限元模拟作者:华中科技大学李迎浩莫键华摘要:本文介绍了金属板料分层渐进成形过程有限元模拟。
在金属板料渐进成形过程中,材料的弹塑性变形十分复杂,影响成形过程的因素很多,同时各个工艺参数对成形过程的影响又很难确定。
为此根据金属板料分层渐进成形为多工步成形的技术特点,建立一种有限元模拟方案,对板料渐进成形过程进行模拟分析。
关键词:分层成形;渐进成形;有限元模拟1.前言板料零件数控渐进成形工艺是一种通过数字控制设备,采用预先编制好的控制程序逐点成形板料零件的柔性加工工艺。
该工艺不需要专用模具,成形极限较大,重复性好,可控制金属流动,能加工出形状复杂的自由曲面,适合于航天、汽车工业等的小批量、多品种、形状复杂的板料零件加工,有着十分诱人的发展前景。
但是迄今为止,国际上对数控渐进成形工艺的研究也只处于探索阶段,理论方面的分析较少且不成熟,对于该工艺的成形和控制方面还有待于发展完善。
随着有限元分析技术的飞速发展以及计算机性能的不断提高,一个融入了计算机图形学、数值方法、塑性成形理论与工艺等各类技术的模拟软件系统已逐渐成为板料数控渐进成形研究及成形优化的强有力的工具。
本文就引入有限元模拟技术对板料零件数控渐进成形工艺的成形过程进行模拟方面的探讨。
2.金属板料数控渐进成形原理板料零件数控渐进成形的加工过程如图1所示。
数控成形系统主要由工具头(成形工具)、导向装置、芯模和机床本体组成。
工具头在数控系统的控制下进行运动,芯模起支撑板料的作用,对于形状复杂的零件,该芯模可以制成简单的模具,有利于板料的成形。
成形时,首先将被加工的板料置于一个通用芯模上,在托板四周用压板夹紧板料,该托板可沿导柱上下滑动。
然后将该装置固定在三轴联动的数控成形机上,加工时,成形工具先走到指定位置,并对板料压下设定压下量,然后根据控制系统的指令,按照第一层轮廓的要求,以走等高线的方式,对板料进行单点渐进塑性加工,如图1b所示。
大型铝合金曲面零件电磁渐进成形线圈结构优化设计
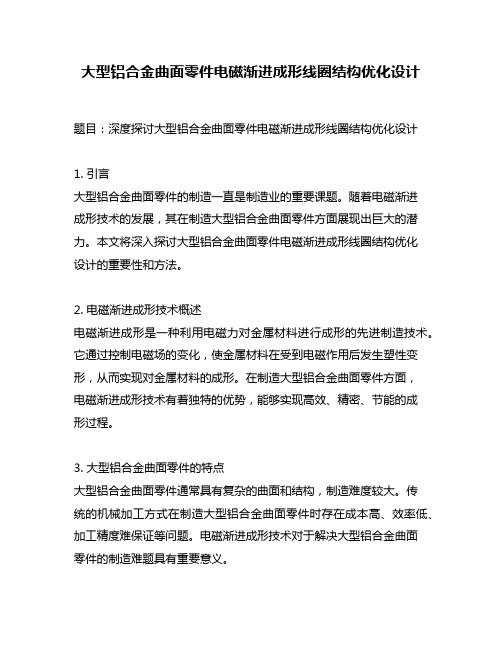
大型铝合金曲面零件电磁渐进成形线圈结构优化设计题目:深度探讨大型铝合金曲面零件电磁渐进成形线圈结构优化设计1. 引言大型铝合金曲面零件的制造一直是制造业的重要课题。
随着电磁渐进成形技术的发展,其在制造大型铝合金曲面零件方面展现出巨大的潜力。
本文将深入探讨大型铝合金曲面零件电磁渐进成形线圈结构优化设计的重要性和方法。
2. 电磁渐进成形技术概述电磁渐进成形是一种利用电磁力对金属材料进行成形的先进制造技术。
它通过控制电磁场的变化,使金属材料在受到电磁作用后发生塑性变形,从而实现对金属材料的成形。
在制造大型铝合金曲面零件方面,电磁渐进成形技术有着独特的优势,能够实现高效、精密、节能的成形过程。
3. 大型铝合金曲面零件的特点大型铝合金曲面零件通常具有复杂的曲面和结构,制造难度较大。
传统的机械加工方式在制造大型铝合金曲面零件时存在成本高、效率低、加工精度难保证等问题。
电磁渐进成形技术对于解决大型铝合金曲面零件的制造难题具有重要意义。
4. 电磁渐进成形线圈结构的优化设计在大型铝合金曲面零件的电磁渐进成形中,线圈结构的设计是至关重要的。
线圈结构的优化设计,能够有效改善电磁场的分布和作用效果,从而提高对铝合金材料的成形控制能力。
优化设计应考虑线圈的布局、尺寸、形状、绕组方式等因素,以确保电磁作用对铝合金曲面的成形具有精准、高效的影响。
5. 个人观点和理解在我看来,大型铝合金曲面零件电磁渐进成形线圈结构的优化设计需要综合考虑材料特性、成形工艺和实际应用需求。
结合数值模拟和实验验证,不断完善线圈结构的设计,是实现大型铝合金曲面零件电磁渐进成形高质量、高效率制造的关键。
6. 总结通过对大型铝合金曲面零件电磁渐进成形线圈结构优化设计的深度探讨,我们可以看到其在大型铝合金曲面零件制造中的重要作用。
优化设计能够提高电磁成形的精度和效率,为制造业的发展带来新的机遇和挑战。
相信随着技术的不断进步,大型铝合金曲面零件的制造将迎来更加璀璨的未来。
- 1、下载文档前请自行甄别文档内容的完整性,平台不提供额外的编辑、内容补充、找答案等附加服务。
- 2、"仅部分预览"的文档,不可在线预览部分如存在完整性等问题,可反馈申请退款(可完整预览的文档不适用该条件!)。
- 3、如文档侵犯您的权益,请联系客服反馈,我们会尽快为您处理(人工客服工作时间:9:00-18:30)。
0 前言
1 渐进成形分类及特点
传统的钣金加工工艺是先设计、制造模具,然 后用模具加工出产品。它是一种适合品种单一、大 批量、产品更新换代时间长的生产方式[1-2];所需的 模具设计制造周期长、费用高,难以适应小批量、 多品种和样品试制的需要。
为了适应市场的需要,各种无模成形方法不断 涌现出来,如成形锤渐进成形、喷丸成形、无模多 点成形、激光热应力成形、旋压成形、CNC 高压水 喷射成形和金属板料单点渐进成形等。近年来,国 内外愈来愈多的学者致力于金属板料单点渐进成形 技术的研究。渐进成形技术是根据工件形状的几何 信息,在数控设备上控制成形工具头沿特定轨迹对 板料进行局部的塑性加工,使板料逐渐成形为所需 工件。渐进成形不需要专用的模具,重复性好,可 控制金属流动,能加工出形状复杂的工件,对于飞 机等多种小批量产品、家用电器等新产品的开发以 及汽车新型样车试制等具有较大的经济价值和广阔 的发展前景。
(2) UG 软件可以生成用于渐进成形的三轴加工 代码,不能完全符合渐进成形正成形过程的要求, 必须通过转换程序对 UG 软件产生的加工代码进行 转换,使托板带动板料实现随着加工工具逐层下降 的功能。
(3) 渐进成形正成形中定位精度非常重要,如 果定位精度误差达到一定程度,就会导致板料的贴 模性不好,从而严重影响成形的质量,甚至不能够 成功成形出零件。
第 43 卷第 12 期 2007 年 12 月
机械工程学报
CHINESE JOURNAL OF MECHANICAL ENGINEERING
Vol.43 No.12 Dec. 2 0 0 7
复杂钣金零件渐进成形方法
崔 震 1 高 霖 1 陆启建 2
(1. 南京航空航天大学机电学院 南京 210016; 2. 南京四开电子企业有限公司 南京 210016)
图 1 渐进成形(负成形)及板料成形角原理示意图
形状复杂的零件要用正成形的方法。在正成形 方法中,需要支撑模型,支撑模型的形状要与所成 形的零件的形状一致,这种支撑模型与冲压成形中 的模具有很大差别,支撑模型的精度要求不是很高, 并且材料的选择比较灵活。在这种成形方法中,首 先加工支撑模型,支撑模型加工完毕后再放上板料, 以后的加工步骤与负成形基本相同,所不同的是正 成形中成形工具头每走完一层的路径,托板都要带
待
加
托
工
板
板
料
装
夹
支
板 料 夹 紧
装 置
撑 模 型 的 虎 钳
图 6 试验设计的装夹装置
调入加工程序进行渐进成形。试验中使用普通 润滑油,使用的 LY12M 板料的实际厚度为 0.923 mm,板料尺寸为 290 mm × 180 mm,待加工的人面 部模型的尺寸:长度为 168 mm、宽度为 96 mm、 高度为 27 mm。按此加工两个人面部零件,为了证 明定位精度对零件加工结果的影响,零件 1 有比较 高的定位精度,并特意在零件 2 定位时故意向 x 轴 负方向移动 1 mm,两个零件的其他加工方法完全相 同。最终成形的人面部零件 1 与零件 2 如图 7 所示。
摘要:以复杂钣金零件-人面部模型零件为例,论述基于 UG 软件的建模及建模过程中应注意的问题、支撑模型 的制作及其加工代码的生成、适用于渐进成形正成形过程的加工代码生成处理过程,给出加工代码的详细信息, 成功加工出质量较高的人面部模型。人面部模型渐进成形试验结果表明,利用渐进成形正成形方法可以成形出形 状复杂的钣金零件,生产小批量复杂零件可以节省时间与费用;UG 生成的三轴数控加工代码需要通过处理才能 应用于渐进成形正成形过程;复杂钣金件渐进成形过程中定位精度非常重要,定位精度高的零件厚度分布符合 δ = δ0 cosθ 的规律,并可以成功成形出设计的零件,定位精度误差较大时零件厚度分布不均匀,成形工具头与板 料的过度挤压侧板料厚度变薄急剧从而引起零件的过早破裂。 关键词:渐进成形 钣金件 数控技术 中图分类号:TG386
表 1 支撑模型加工程序信息
加工参数名称
操作类型
操作方法 刀具 每一刀全局 深度 a/mm 剪切速度 f/(mm·min–1) 加工余量 a′/mm 加工时间
粗加工信息 型腔铣 CAVITY_ MILL/ mill_contour 粗加工 MILL_ROUGH 直径 8 mm 平头刀
1.5
1 500
图 3 传统成形方法与渐进成形方法的成形极限曲线
2 人面部模型渐进成形试验过程
人面部模型是相对较为复杂的零件,在成形人 面部模型的过程中,采用以下步骤:建模及生成加 工代码、制造支撑模型、加工人面部模型。 2.1 建模及生成加工代码
渐进成形中,板料的厚度变化遵循如下规律: δ = δ0 cosθ [6]( δ0 为板料的初始厚度),θ 称为板料 成形角(图 1)。每种材料有其相对应的最大成形角 度,称为成形极限角。试验用的 LY12M 材料的成 形极限角在 65º~70º[7]之间,超过此角度材料在成 形过程中极易出现裂纹等失效形式,因此在建模时 必须考虑这一点。用于加工成形的零件其板料成形 角度尽量控制在成形极限角度之内,对于某些要求
此 处 破 裂
图 10 零件 2 破裂示意图
图 11 零件 2 非挤压侧板料实际厚度与理论厚度比较图
(1) 渐进成形正成形方法可以成形形状复杂的 钣金零件,成形只需要简单的支撑模型,成形出的 零件精度较高,表面质量较好,对于小批量零件花 费时间少,节省资金,可以满足产品不断创新设计、 多品种、小批量的要求。
参考文献
[1] 松原茂夫. 数值控制逐次成形法[J]. 塑性と加工, 1994 (11):1 258-1 263.
板料成形前
板料成形后
图 2 渐进成形(正成形)原理示意图
1.2 渐进成形方法的特点 渐进成形过程中板料的成形能力有所提高,从
成形极限图上可以看出(图 3),成形极限可以用 εmax + εmin 表示[5],因此,渐进成形中板料可以有更 大的变形量。渐进成形的缺点主要是成形效率较低, 成形单个零件所需要的相对时间比较长,因此如何 提高其成形效率也是其是否能够得以广泛应用的一 个很重要的前提。
图 7 最终成形的人面部零件 1 与零件 2
3 渐进成形试验结果分析
图 5 加工完的支撑模型
加工完毕后固定在原位以方便进行下面的试 验。由于进行模型加工与渐进成形加工的主轴不相
零件 1 原点定位精度比较高,可以成功地成形 出需要的零件,零件的表面质量比较好,对零件的 一个断面进行厚度分析(图 8、9),可以看出,材料 的厚度基本符合 δ = δ0 cosθ 的规律,并且在 x 轴的 正负对称方向厚度变薄一致。
本文在对金属板料数控单点渐进成形技术进行 了一些研究的基础上,利用现有的资源,将计算机、 数控成形机床以及成形工具、结构简单的夹具组成 一个数控成形系统,采用预先编制好的控制程序逐 点进行板料零件的加工,成功成形出人面部形状的 钣金零件。
20061213 收到初稿,20070820 收到修改稿
1.1 渐进成形的分类 渐进成形分为负成形与正成形[3]。负成形可以
2360
机械工程学报
第 43 卷第 12 期期
动板料与成形工具头共同向下移动相同距离。渐进 成形(正成形)原理示意图如图 2 所示。
导柱
托 板 逐 层 下 降
夹板 托板
支撑模型 支架
成形工具头 板料
角度大于成形极限角的特征,则尽可能减小其高度, 特别是零件如果有直壁部分,其直壁部分一般不能 超过 8 mm[8]。用于本次试验成形的人面部模型在除 下巴部分以外的地方最大角度控制在 56º以内,在 理论上是完全能够成功成形的。下巴部分的角度为 90º,因此在生成加工代码时使下巴部分的加工深度 最大为 5 mm。试验中使用的建模软件是 UG NX3, 并使用它的 CAM 模块生成加工代码,由 UG NX3 曲面建模功能建立的模型如图 4。
图 4 待加工的人面部支撑模型与 最终要应该省时、 经济、实用,试验中采用代木作为支撑模型,在加 工人面部模型之前首先要在机床上加工出支撑模 型。考虑到板料的厚度,直接对建立的人面部模型 向内偏置一个板料厚度,用于生成支撑模型的加工 代码模型,然后生成加工代码。加工支撑模型的程 序只需要三轴的加工程序即可,具体加工信息如表 1 所示。
0.5 58′13′′
精加工信息 等高线加工 ZLEVEL_ PROFILE / mill_contour 精加工 MILL_FINISH
直径 6 mm 球头刀
0.1
1 500
0 63′45′′
然后生成用于人面部渐进成形加工的刀具轨 迹。渐进成形的刀具轨迹的产生思想是模拟模型的 精加工,即加工余量设为零。UG 中的 CAM 模块没 有专门用于模拟板料挤压成形的刀轨,根据渐进成 形的过程特点要求程序要按照层加工进行,只有加 工完上一层后才能进入下一层进行加工,因此在加 工选项里面要选择“层优先”,这与铣削加工的深度
首先加工支撑模型,将代木装夹到机床夹具 上面,进行粗、精加工,加工完的支撑模型如图 5 所示。
同,因此在换刀后有一个重新定位的问题,要使渐 进成形刀具非常准确地找到先前加工的刀具原点, 并且要在 z 轴方向上向上移动一个板料厚度的距 离。如果存在误差,在渐进成形过程中成形工具在 某些地方过度挤压板料;如果支撑模型的硬度比较 高,成形工具、板料、支撑模型之间的力会非常大, 对板料的成形性能影响也很大,而在有的地方板料 与支撑模型之间的贴合程度就很小。定位了加工程 序的原点后,升起托板,把板料装夹到托板上。图 6 为试验设计的装夹装置。
2380
机械工程学报
第 43 卷第 12 期期
图 8 厚度分析图
图 12 零件 2 过度挤压侧板料实际厚度与理论厚度比较图
4 结论
图 9 零件 1 实际厚度与理论厚度分布比较示意图
对于零件 2,从图 10~12 可以看出,由于定位 误差的原因,根本不能成形出设计的人面部零件, 对于没有受到挤压的一侧,由于板料的贴模性不好, 材料变薄与 δ = δ0 cosθ 有较大误差,并在有的地方 材料发生堆积,使板料的厚度不但没有减薄,反而 有所加厚;板料在过度挤压侧材料变薄严重,并很 快发生了破裂。