GCr9物料平衡计算
物料平衡计算公式
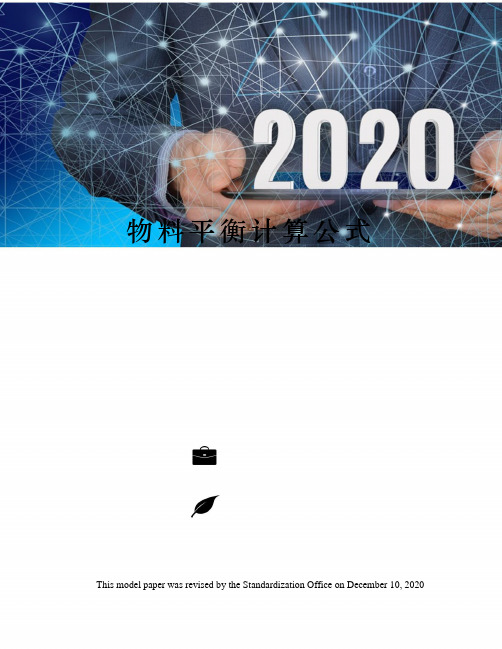
物料平衡计算公式This model paper was revised by the Standardization Office on December 10, 2020物料平衡计算公式:每片主药含量理论片重=测得颗粒主药百分含量1.原辅料粉碎、过筛的物料平衡物料平衡范围: %~100 %物料平衡= %100⨯+ac b a-粉筛前重量(kg) b-粉筛后重量(kg) c-不可利用物料量(kg)2.制粒工序的物料平衡物料平衡范围: %~ %制粒工序的物料平衡=a d cb ++×100% 制粒工序的收率=ab ×100% a-制粒前所有原辅料总重(kg) b-干颗粒总重(kg)c-尾料总重(kg) d-取样量(kg)3.压片工序的物料平衡范围: %~ %压片工序的物料平衡=ad c b ++×100% 压片工序的收率=ab ×100%a-接收颗粒重量(kg) b-片子重量(kg)c-取样重量(kg) d-尾料重量(kg)4.包衣工序的物料平衡包衣工序的物料平衡范围: %~ %包衣工序的物料平衡 = b a ed c +++包衣工序的收率 = b a c+a-素片重量(kg) b-包衣剂重量(kg) c-糖衣片重量(kg) d-尾料重量(kg) e-取样量(kg)5.内包装工序物料平衡内包装工序物料平衡范围: %~ %包材物料平衡=%100⨯++++A a dc b Ba- PTP 领用量(kg) b- PTP 剩余量(kg) A- PVC领用量(kg) B- PVC 剩余量(kg) c-使用量(kg) d-废料量(kg)片剂物料平衡=%100⨯++a dc ba :领用量(Kg)b :产出量(Kg)c :取样量(Kg)d :废料量(Kg)6.外包装工序的物料平衡包装材料的物料平衡范围:100%包装材料物料平衡=%100⨯+++ea d cb e-上批结存 a-领用量 b-使用量 c-剩余量 d-残损量7.生产成品率成品率范围:90%~102%片剂收率= %100⨯++a dc ba-计划产量 b-入库量 c-留样量 d-取样量 1.粉碎过筛和称配岗位物料平衡检查:配料量╳100% 粉碎过筛后原辅料总重(物料平衡范围应控制在~%)2.制粒干燥、整粒总混岗位物料平衡检查:总混后重量+不良品╳100%干颗粒净重+润滑剂+崩解剂(物料平衡范围应控制在~%)3.充填抛光岗位物料平衡检查:胶囊总重+细粉+不良品+废胶囊壳重量╳100%颗粒总重+胶囊壳重量(物料平衡范围应控制在~%)4.铝塑内包岗位物料平衡检查:(成品板总重/平均每板重量+不良品)×规格(粒/板)╳100%胶囊领用量/平均胶囊重(物料平衡范围应控制在~%)5.总物料平衡检查:成品产量╳100%理论产量(物料平衡范围应控制在97~100%)。
物料平衡计算公式
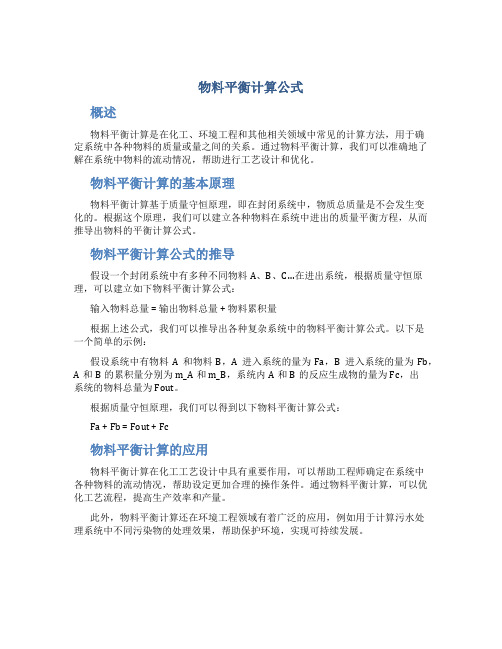
物料平衡计算公式概述物料平衡计算是在化工、环境工程和其他相关领域中常见的计算方法,用于确定系统中各种物料的质量或量之间的关系。
通过物料平衡计算,我们可以准确地了解在系统中物料的流动情况,帮助进行工艺设计和优化。
物料平衡计算的基本原理物料平衡计算基于质量守恒原理,即在封闭系统中,物质总质量是不会发生变化的。
根据这个原理,我们可以建立各种物料在系统中进出的质量平衡方程,从而推导出物料的平衡计算公式。
物料平衡计算公式的推导假设一个封闭系统中有多种不同物料A、B、C…在进出系统,根据质量守恒原理,可以建立如下物料平衡计算公式:输入物料总量 = 输出物料总量 + 物料累积量根据上述公式,我们可以推导出各种复杂系统中的物料平衡计算公式。
以下是一个简单的示例:假设系统中有物料A和物料B,A进入系统的量为Fa,B进入系统的量为Fb,A和B的累积量分别为m_A和m_B,系统内A和B的反应生成物的量为Fc,出系统的物料总量为Fout。
根据质量守恒原理,我们可以得到以下物料平衡计算公式:Fa + Fb = Fout + Fc物料平衡计算的应用物料平衡计算在化工工艺设计中具有重要作用,可以帮助工程师确定在系统中各种物料的流动情况,帮助设定更加合理的操作条件。
通过物料平衡计算,可以优化工艺流程,提高生产效率和产量。
此外,物料平衡计算还在环境工程领域有着广泛的应用,例如用于计算污水处理系统中不同污染物的处理效果,帮助保护环境,实现可持续发展。
结论物料平衡计算是化工、环境工程等领域中的重要计算方法,通过建立质量守恒原理的物料平衡计算公式,可以准确地描述物料在系统中的流动情况。
合理应用物料平衡计算,有助于工程师优化工艺流程,提高生产效率,保护环境,推动可持续发展。
物料平衡计算公式:
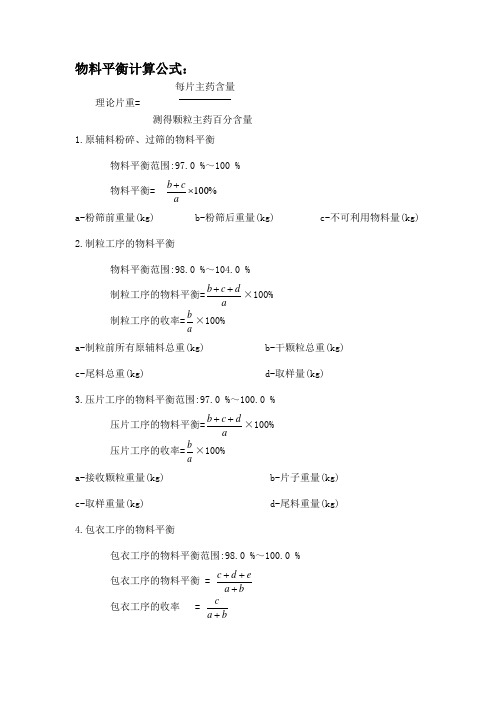
物料平衡计算公式:每片主药含量理论片重=测得颗粒主药百分含量1.原辅料粉碎、过筛的物料平衡物料平衡范围:97.0 %~100 %物料平衡= %100⨯+ac b a-粉筛前重量(kg) b-粉筛后重量(kg) c-不可利用物料量(kg)2.制粒工序的物料平衡物料平衡范围:98.0 %~104.0 %制粒工序的物料平衡=a d cb ++×100% 制粒工序的收率=ab ×100% a-制粒前所有原辅料总重(kg) b-干颗粒总重(kg)c-尾料总重(kg) d-取样量(kg)3.压片工序的物料平衡范围:97.0 %~100.0 %压片工序的物料平衡=a d cb ++×100% 压片工序的收率=ab ×100% a-接收颗粒重量(kg) b-片子重量(kg)c-取样重量(kg) d-尾料重量(kg)4.包衣工序的物料平衡包衣工序的物料平衡范围:98.0 %~100.0 %包衣工序的物料平衡 =ba e d c +++ 包衣工序的收率 =b ac +a-素片重量(kg) b-包衣剂重量(kg) c-糖衣片重量(kg) d-尾料重量(kg) e-取样量(kg)5.内包装工序物料平衡内包装工序物料平衡范围:99.5 %~100.0 %包材物料平衡=%100⨯++++Aa d cb B a- PTP 领用量(kg) b- PTP 剩余量(kg) A- PVC 领用量(kg) B- PVC 剩余量(kg) c-使用量(kg) d-废料量(kg)片剂物料平衡=%100⨯++ad c b a :领用量(Kg) b :产出量(Kg)c :取样量(Kg)d :废料量(Kg)6.外包装工序的物料平衡包装材料的物料平衡范围:100%包装材料物料平衡=%100⨯+++ea d cb e-上批结存 a-领用量 b-使用量 c-剩余量 d-残损量7.生产成品率成品率范围:90%~102%片剂收率= %100⨯++ad c b a-计划产量 b-入库量 c-留样量 d-取样量1.粉碎过筛和称配岗位物料平衡检查:配料量╳100%粉碎过筛后原辅料总重(物料平衡范围应控制在99.8~100.2%)2.制粒干燥、整粒总混岗位物料平衡检查:总混后重量+不良品╳100%干颗粒净重+润滑剂+崩解剂(物料平衡范围应控制在99.0~100.0%)3.充填抛光岗位物料平衡检查:胶囊总重+细粉+不良品+废胶囊壳重量╳100%颗粒总重+胶囊壳重量(物料平衡范围应控制在96.0~101.0%)4.铝塑内包岗位物料平衡检查:(成品板总重/平均每板重量+不良品)×规格(粒/板)╳100%胶囊领用量/平均胶囊重(物料平衡范围应控制在98.0~101.0%)5.总物料平衡检查:成品产量╳100%理论产量(物料平衡范围应控制在97~100%)。
(完整版)物料平衡计算公式:
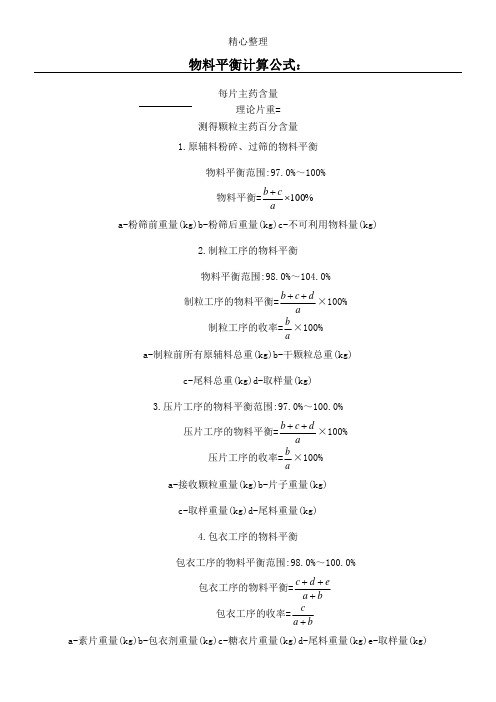
物料平衡计算公式:
每片主药含量
理论片重=
测得颗粒主药百分含量
1.原辅料粉碎、过筛的物料平衡
物料平衡范围:97.0%~100% +c b
c-取样重量(kg)d-尾料重量(kg)
4.包衣工序的物料平衡
包衣工序的物料平衡范围:98.0%~100.0%
包衣工序的物料平衡=b
a e d c +++ 包衣工序的收率=b
a c + a-素片重量(kg)b-包衣剂重量(kg)c-糖衣片重量(kg)d-尾料重量(kg)e-取样量(kg)
5.内包装工序物料平衡
内包装工序物料平衡范围:99.5%~100.0%
包材物料平衡=%100⨯++++A
a d c
b B a-PTP 领用量(kg)b-PTP 剩余量(kg)A-PVC 领用量(kg)
B-PVC 剩余量(kg)c-使用量(kg)d-废料量(kg)
片剂物料平衡=%100⨯++d c b
粉碎过筛后原辅料总重
(物料平衡范围应控制在99.8~100.2%)
2.制粒干燥、整粒总混岗位物料平衡检查:
总混后重量+不良品
╳100%
干颗粒净重+润滑剂+崩解剂
(物料平衡范围应控制在99.0~100.0%)
3.充填抛光岗位物料平衡检查:
胶囊总重+细粉+不良品+废胶囊壳重量
╳100%
颗粒总重+胶囊壳重量
(物料平衡范围应控制在96.0~101.0%)
4.铝塑内包岗位物料平衡检查:
(成品板总重/平均每板重量+不良品)×规格(粒/板)
╳100%。
3.3.3物料平衡计算的方法和步骤
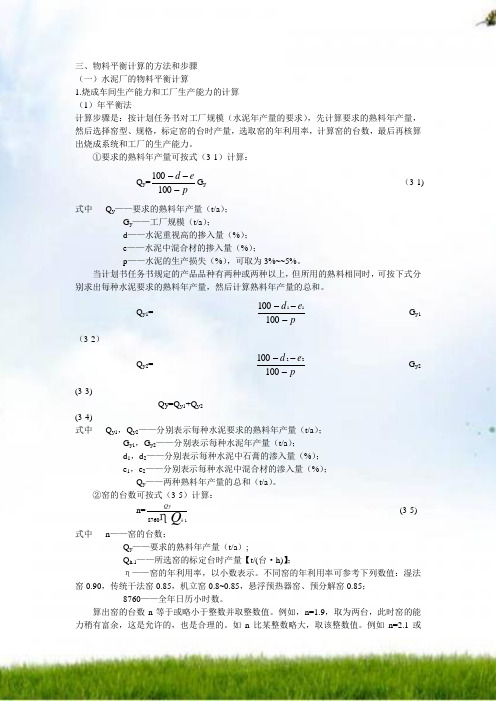
三、物料平衡计算的方法和步骤 (一)水泥厂的物料平衡计算1.烧成车间生产能力和工厂生产能力的计算 (1)年平衡法计算步骤是:按计划任务书对工厂规模(水泥年产量的要求),先计算要求的熟料年产量,然后选择窑型、规格,标定窑的台时产量,选取窑的年利用率,计算窑的台数,最后再核算出烧成系统和工厂的生产能力。
①要求的熟料年产量可按式(3-1)计算: Q y =ped ---100100G y (3-1)式中 Q y ——要求的熟料年产量(t/a );G y ——工厂规模(t/a );d ——水泥重视高的掺入量(%);e ——水泥中混合材的掺入量(%); p ——水泥的生产损失(%),可取为3%~~5%。
当计划书任务书规定的产品品种有两种或两种以上,但所用的熟料相同时,可按下式分别求出每种水泥要求的熟料年产量,然后计算熟料年产量的总和。
Q y1=pe d ---10010011G y1(3-2)Q y2=pe d ---10010022G y2(3-3)Qy=Q y1+Q y2(3-4)式中 Q y1,Q y2——分别表示每种水泥要求的熟料年产量(t/a );G y1,G y2——分别表示每种水泥年产量(t/a ); d 1,d 2——分别表示每种水泥中石膏的渗入量(%); e 1,e 2——分别表示每种水泥中混合材的渗入量(%); Q y ——两种熟料年产量的总和(t/a )。
②窑的台数可按式(3-5)计算:n=1.8760h QQyη (3-5)式中 n ——窑的台数;Q y ——要求的熟料年产量(t/a );Q h.1——所选窑的标定台时产量【t/(台·h)】;η——窑的年利用率,以小数表示。
不同窑的年利用率可参考下列数值:湿法窑0.90,传统干法窑0.85,机立窑0.8~0.85,悬浮预热器窑、预分解窑0.85;8760——全年日历小时数。
算出窑的台数n 等于或略小于整数并取整数值。
例如,n=1.9,取为两台,此时窑的能力稍有富余,这是允许的,也是合理的。
物料平衡计算的技巧和步骤
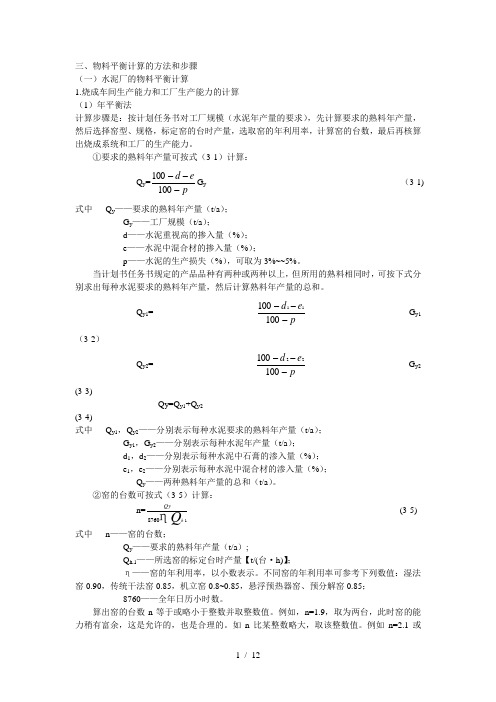
三、物料平衡计算的方法和步骤 (一)水泥厂的物料平衡计算1.烧成车间生产能力和工厂生产能力的计算 (1)年平衡法计算步骤是:按计划任务书对工厂规模(水泥年产量的要求),先计算要求的熟料年产量,然后选择窑型、规格,标定窑的台时产量,选取窑的年利用率,计算窑的台数,最后再核算出烧成系统和工厂的生产能力。
①要求的熟料年产量可按式(3-1)计算: Q y =ped ---100100G y (3-1)式中 Q y ——要求的熟料年产量(t/a );G y ——工厂规模(t/a );d ——水泥重视高的掺入量(%);e ——水泥中混合材的掺入量(%); p ——水泥的生产损失(%),可取为3%~~5%。
当计划书任务书规定的产品品种有两种或两种以上,但所用的熟料相同时,可按下式分别求出每种水泥要求的熟料年产量,然后计算熟料年产量的总和。
Q y1=pe d ---10010011G y1(3-2)Q y2=pe d ---10010022G y2(3-3)Qy=Q y1+Q y2(3-4)式中 Q y1,Q y2——分别表示每种水泥要求的熟料年产量(t/a );G y1,G y2——分别表示每种水泥年产量(t/a ); d 1,d 2——分别表示每种水泥中石膏的渗入量(%); e 1,e 2——分别表示每种水泥中混合材的渗入量(%); Q y ——两种熟料年产量的总和(t/a )。
②窑的台数可按式(3-5)计算:n=1.8760h QQyη (3-5)式中 n ——窑的台数;Q y ——要求的熟料年产量(t/a );Q h.1——所选窑的标定台时产量【t/(台·h)】;η——窑的年利用率,以小数表示。
不同窑的年利用率可参考下列数值:湿法窑0.90,传统干法窑0.85,机立窑0.8~0.85,悬浮预热器窑、预分解窑0.85;8760——全年日历小时数。
算出窑的台数n 等于或略小于整数并取整数值。
例如,n=1.9,取为两台,此时窑的能力稍有富余,这是允许的,也是合理的。
物料平衡计算公式:教学文案
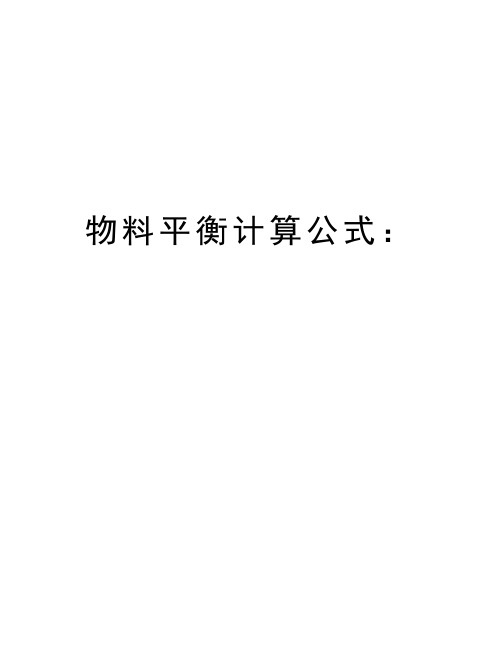
物料平衡计算公式:物料平衡计算公式:每片主药含量理论片重=测得颗粒主药百分含量1.原辅料粉碎、过筛的物料平衡物料平衡范围:97.0 %~100 %物料平衡= %100⨯+ac b a-粉筛前重量(kg) b-粉筛后重量(kg) c-不可利用物料量(kg)2.制粒工序的物料平衡物料平衡范围:98.0 %~104.0 %制粒工序的物料平衡=a d cb ++×100% 制粒工序的收率=ab ×100% a-制粒前所有原辅料总重(kg) b-干颗粒总重(kg)c-尾料总重(kg) d-取样量(kg)3.压片工序的物料平衡范围:97.0 %~100.0 %压片工序的物料平衡=a d cb ++×100% 压片工序的收率=ab ×100% a-接收颗粒重量(kg) b-片子重量(kg)c-取样重量(kg) d-尾料重量(kg)4.包衣工序的物料平衡包衣工序的物料平衡范围:98.0 %~100.0 %包衣工序的物料平衡 =ba e d c +++ 包衣工序的收率 =b ac +a-素片重量(kg) b-包衣剂重量(kg) c-糖衣片重量(kg) d-尾料重量(kg) e-取样量(kg)5.内包装工序物料平衡内包装工序物料平衡范围:99.5 %~100.0 %包材物料平衡=%100⨯++++Aa d cb B a- PTP 领用量(kg) b- PTP 剩余量(kg) A- PVC 领用量(kg)B- PVC 剩余量(kg) c-使用量(kg) d-废料量(kg)片剂物料平衡=%100⨯++ad c b a :领用量(Kg) b :产出量(Kg)c :取样量(Kg)d :废料量(Kg)6.外包装工序的物料平衡包装材料的物料平衡范围:100%包装材料物料平衡=%100⨯+++ea d cb e-上批结存 a-领用量 b-使用量 c-剩余量 d-残损量7.生产成品率成品率范围:90%~102%片剂收率= %100⨯++ad c b a-计划产量 b-入库量 c-留样量 d-取样量1.粉碎过筛和称配岗位物料平衡检查:配料量╳100%粉碎过筛后原辅料总重(物料平衡范围应控制在99.8~100.2%)2.制粒干燥、整粒总混岗位物料平衡检查:总混后重量+不良品╳100%干颗粒净重+润滑剂+崩解剂(物料平衡范围应控制在99.0~100.0%)3.充填抛光岗位物料平衡检查:胶囊总重+细粉+不良品+废胶囊壳重量╳100%颗粒总重+胶囊壳重量(物料平衡范围应控制在96.0~101.0%)4.铝塑内包岗位物料平衡检查:(成品板总重/平均每板重量+不良品)×规格(粒/板)╳100%胶囊领用量/平均胶囊重(物料平衡范围应控制在98.0~101.0%)5.总物料平衡检查:成品产量╳100%理论产量(物料平衡范围应控制在97~100%)。
物料平衡计算的技巧和步骤
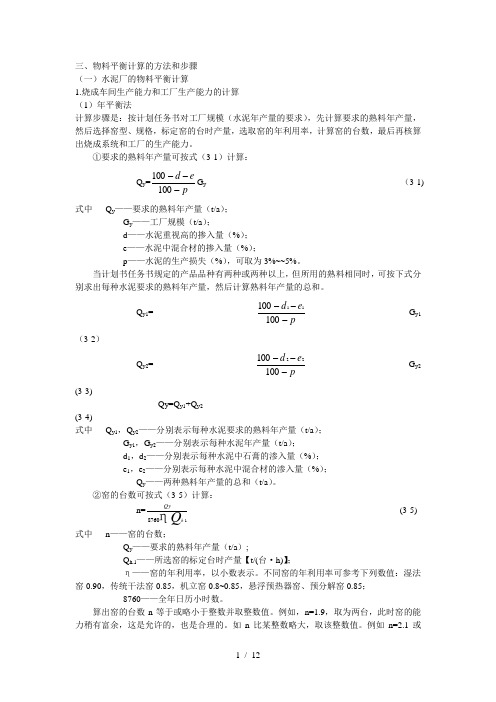
三、物料平衡计算的方法和步骤 (一)水泥厂的物料平衡计算1.烧成车间生产能力和工厂生产能力的计算 (1)年平衡法计算步骤是:按计划任务书对工厂规模(水泥年产量的要求),先计算要求的熟料年产量,然后选择窑型、规格,标定窑的台时产量,选取窑的年利用率,计算窑的台数,最后再核算出烧成系统和工厂的生产能力。
①要求的熟料年产量可按式(3-1)计算: Q y =ped ---100100G y (3-1)式中 Q y ——要求的熟料年产量(t/a );G y ——工厂规模(t/a );d ——水泥重视高的掺入量(%);e ——水泥中混合材的掺入量(%); p ——水泥的生产损失(%),可取为3%~~5%。
当计划书任务书规定的产品品种有两种或两种以上,但所用的熟料相同时,可按下式分别求出每种水泥要求的熟料年产量,然后计算熟料年产量的总和。
Q y1=pe d ---10010011G y1(3-2)Q y2=pe d ---10010022G y2(3-3)Qy=Q y1+Q y2(3-4)式中 Q y1,Q y2——分别表示每种水泥要求的熟料年产量(t/a );G y1,G y2——分别表示每种水泥年产量(t/a ); d 1,d 2——分别表示每种水泥中石膏的渗入量(%); e 1,e 2——分别表示每种水泥中混合材的渗入量(%); Q y ——两种熟料年产量的总和(t/a )。
②窑的台数可按式(3-5)计算:n=1.8760h QQyη (3-5)式中 n ——窑的台数;Q y ——要求的熟料年产量(t/a );Q h.1——所选窑的标定台时产量【t/(台·h)】;η——窑的年利用率,以小数表示。
不同窑的年利用率可参考下列数值:湿法窑0.90,传统干法窑0.85,机立窑0.8~0.85,悬浮预热器窑、预分解窑0.85;8760——全年日历小时数。
算出窑的台数n 等于或略小于整数并取整数值。
例如,n=1.9,取为两台,此时窑的能力稍有富余,这是允许的,也是合理的。
物料平衡计算公式
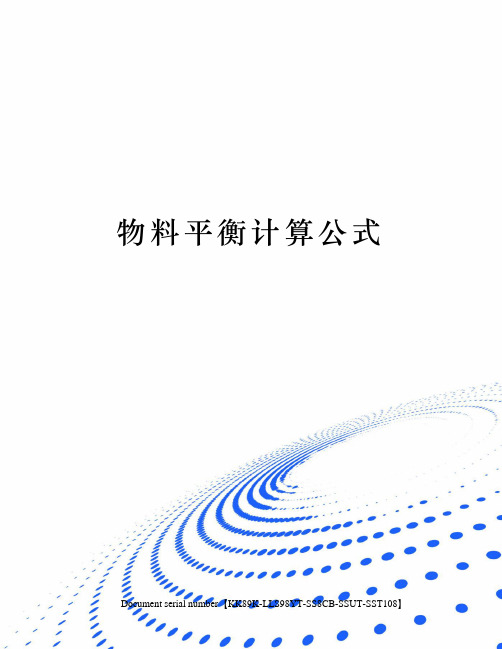
物料平衡计算公式 Document serial number【KK89K-LLS98YT-SS8CB-SSUT-SST108】物料平衡计算公式:每片主药含量理论片重=测得颗粒主药百分含量1.原辅料粉碎、过筛的物料平衡物料平衡范围:97.0%~100%物料平衡=%100⨯+ac b a-粉筛前重量(kg)b-粉筛后重量(kg)c-不可利用物料量(kg)2.制粒工序的物料平衡物料平衡范围:98.0%~104.0%制粒工序的物料平衡=a d cb ++×100% 制粒工序的收率=ab ×100% a-制粒前所有原辅料总重(kg)b-干颗粒总重(kg)c-尾料总重(kg)d-取样量(kg)3.压片工序的物料平衡范围:97.0%~100.0%压片工序的物料平衡=a d cb ++×100% 压片工序的收率=ab ×100% a-接收颗粒重量(kg)b-片子重量(kg)c-取样重量(kg)d-尾料重量(kg)4.包衣工序的物料平衡包衣工序的物料平衡范围:98.0%~100.0%包衣工序的物料平衡=b a e dc +++ 包衣工序的收率=ba c + a-素片重量(kg)b-包衣剂重量(kg)c-糖衣片重量(kg)d-尾料重量(kg)e-取样量(kg)5.内包装工序物料平衡内包装工序物料平衡范围:99.5%~100.0%包材物料平衡=%100⨯++++Aa d cb B a-PTP 领用量(kg)b-PTP 剩余量(kg)A-PVC 领用量(kg) B-PVC 剩余量(kg)c-使用量(kg)d-废料量(kg)片剂物料平衡=%100⨯++ad c b a :领用量(Kg)b :产出量(Kg)c :取样量(Kg)d :废料量(Kg)6.外包装工序的物料平衡包装材料的物料平衡范围:100%包装材料物料平衡=%100⨯+++ea d cb e-上批结存a-领用量b-使用量c-剩余量d-残损量7.生产成品率成品率范围:90%~102%片剂收率=%100⨯++ad c b a-计划产量b-入库量c-留样量d-取样量1.粉碎过筛和称配岗位物料平衡检查:配料量╳100%粉碎过筛后原辅料总重(物料平衡范围应控制在99.8~100.2%)2.制粒干燥、整粒总混岗位物料平衡检查:总混后重量+不良品╳100%干颗粒净重+润滑剂+崩解剂(物料平衡范围应控制在99.0~100.0%)3.充填抛光岗位物料平衡检查:胶囊总重+细粉+不良品+废胶囊壳重量╳100%颗粒总重+胶囊壳重量(物料平衡范围应控制在96.0~101.0%)4.铝塑内包岗位物料平衡检查:(成品板总重/平均每板重量+不良品)×规格(粒/板)╳100%胶囊领用量/平均胶囊重(物料平衡范围应控制在98.0~101.0%)5.总物料平衡检查:成品产量╳100%理论产量(物料平衡范围应控制在97~100%)。
炼钢过程中的物料平衡与热平衡计算
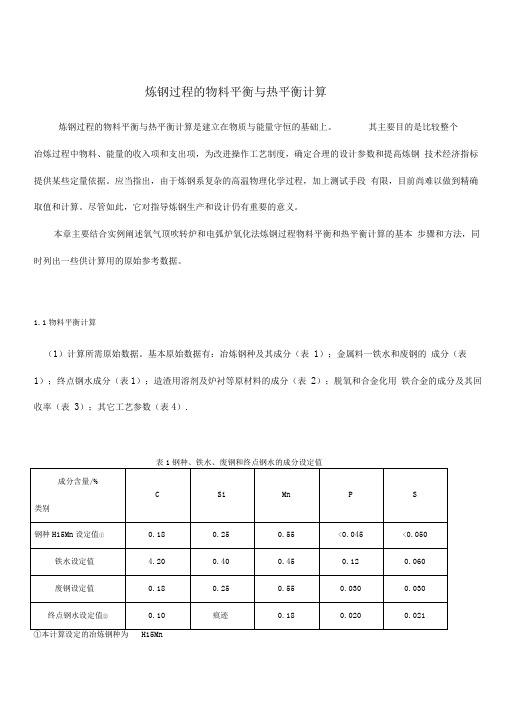
炼钢过程的物料平衡与热平衡计算炼钢过程的物料平衡与热平衡计算是建立在物质与能量守恒的基础上。
其主要目的是比较整个冶炼过程中物料、能量的收入项和支出项,为改进操作工艺制度,确定合理的设计参数和提高炼钢技术经济指标提供某些定量依据。
应当指出,由于炼钢系复杂的高温物理化学过程,加上测试手段有限,目前尚难以做到精确取值和计算。
尽管如此,它对指导炼钢生产和设计仍有重要的意义。
本章主要结合实例阐述氧气顶吹转炉和电弧炉氧化法炼钢过程物料平衡和热平衡计算的基本步骤和方法,同时列出一些供计算用的原始参考数据。
1.1物料平衡计算(1)计算所需原始数据。
基本原始数据有:冶炼钢种及其成分(表1);金属料一铁水和废钢的成分(表1);终点钢水成分(表1);造渣用溶剂及炉衬等原材料的成分(表2);脱氧和合金化用铁合金的成分及其回收率(表3);其它工艺参数(表4).钢种、铁水、废钢和终点钢水的成分设定值表②[C ]和[Si ]按实际生产情况选取;[Mn ]、[P ]和[S ]分别按铁水中相应成分含量的 30%、10%和60%留在钢水中设表原材料成分表铁合金成分(分子)及其回收率(分母)①与氧生产 2表4其它工艺参数设定值(2)物料平衡基本项目收入项有:铁水、废钢、溶剂(石灰、萤石、轻烧白云石)、氧气、炉衬蚀损、铁合金。
支出项有:钢水、炉渣、烟尘、渣中铁珠、炉气、喷溅。
(3)计算步骤。
以100kg铁水为基础进行计算。
第一步:计算脱氧和合金化前的总渣量及其成分。
总渣量包括铁水中元素氧化、炉衬蚀损和加入溶剂的成渣量。
其各项成渣量分别列于表5、6和7 总渣量及其成分如表8所示。
第二步:计算氧气消耗量。
氧气实际消耗量系消耗项目与供入项目之差,详见表9。
表5铁水中元素的氧化产物及其成渣量① 由还原出的氧量,消耗的量表6炉衬蚀损的成渣量表加入溶剂的成渣量①石灰加入量计算如下:由表可知,渣中已含渣中已含(Si02)=0.857+0.009+0.028+0.022=0.914kg.因设定的终渣碱度 R=3.5 ;故石灰加入量为[R D w (SiO 2)— B w (CaO )]/[w (CaO 石灰)一R X w (SiO 2 石灰)]=2.738/ (88.00% — 3.5 X2.50% ) =3.45kg ②为(石灰中CaO 含量)一(石灰中 S T CaS 自耗的CaO 量)。
物料平衡计算公式:
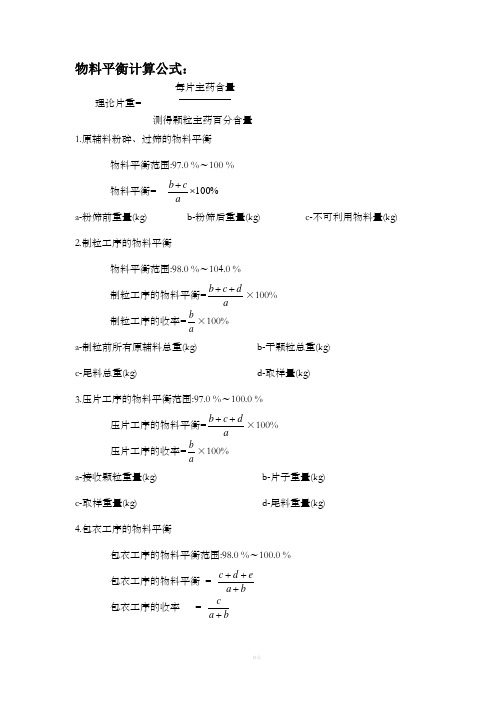
物料平衡计算公式:每片主药含量理论片重=测得颗粒主药百分含量1.原辅料粉碎、过筛的物料平衡物料平衡范围:97.0 %~100 %物料平衡= %100⨯+ac b a-粉筛前重量(kg) b-粉筛后重量(kg) c-不可利用物料量(kg)2.制粒工序的物料平衡物料平衡范围:98.0 %~104.0 %制粒工序的物料平衡=a d cb ++×100% 制粒工序的收率=ab ×100% a-制粒前所有原辅料总重(kg) b-干颗粒总重(kg)c-尾料总重(kg) d-取样量(kg)3.压片工序的物料平衡范围:97.0 %~100.0 %压片工序的物料平衡=a d cb ++×100% 压片工序的收率=ab ×100% a-接收颗粒重量(kg) b-片子重量(kg)c-取样重量(kg) d-尾料重量(kg)4.包衣工序的物料平衡包衣工序的物料平衡范围:98.0 %~100.0 %包衣工序的物料平衡 =ba e d c +++ 包衣工序的收率 =b ac +a-素片重量(kg) b-包衣剂重量(kg) c-糖衣片重量(kg) d-尾料重量(kg) e-取样量(kg)5.内包装工序物料平衡内包装工序物料平衡范围:99.5 %~100.0 %包材物料平衡=%100⨯++++Aa d cb B a- PTP 领用量(kg) b- PTP 剩余量(kg) A- PVC 领用量(kg) B- PVC 剩余量(kg) c-使用量(kg) d-废料量(kg)片剂物料平衡=%100⨯++ad c b a :领用量(Kg) b :产出量(Kg)c :取样量(Kg)d :废料量(Kg)6.外包装工序的物料平衡包装材料的物料平衡范围:100%包装材料物料平衡=%100⨯+++ea d cb e-上批结存 a-领用量 b-使用量 c-剩余量 d-残损量7.生产成品率成品率范围:90%~102%片剂收率= %100⨯++ad c b a-计划产量 b-入库量 c-留样量 d-取样量1.粉碎过筛和称配岗位物料平衡检查:配料量╳100%粉碎过筛后原辅料总重(物料平衡范围应控制在99.8~100.2%)2.制粒干燥、整粒总混岗位物料平衡检查:总混后重量+不良品╳100%干颗粒净重+润滑剂+崩解剂(物料平衡范围应控制在99.0~100.0%)3.充填抛光岗位物料平衡检查:胶囊总重+细粉+不良品+废胶囊壳重量╳100%颗粒总重+胶囊壳重量(物料平衡范围应控制在96.0~101.0%)4.铝塑内包岗位物料平衡检查:(成品板总重/平均每板重量+不良品)×规格(粒/板)╳100%胶囊领用量/平均胶囊重(物料平衡范围应控制在98.0~101.0%)5.总物料平衡检查:成品产量╳100%理论产量(物料平衡范围应控制在97~100%)。
物料平衡计算公式
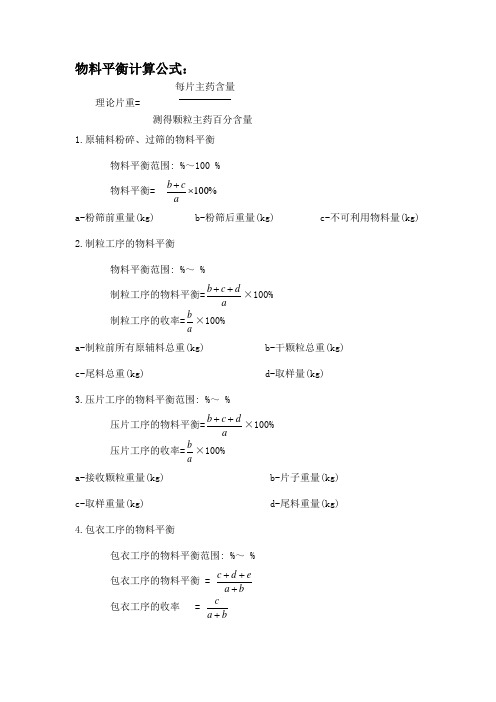
物料平衡计算公式:每片主药含量理论片重=测得颗粒主药百分含量1.原辅料粉碎、过筛的物料平衡物料平衡范围: %~100 %物料平衡= %100⨯+ac b a-粉筛前重量(kg) b-粉筛后重量(kg) c-不可利用物料量(kg)2.制粒工序的物料平衡物料平衡范围: %~ %制粒工序的物料平衡=a d cb ++×100% 制粒工序的收率=ab ×100% a-制粒前所有原辅料总重(kg) b-干颗粒总重(kg)c-尾料总重(kg) d-取样量(kg)3.压片工序的物料平衡范围: %~ %压片工序的物料平衡=a d cb ++×100% 压片工序的收率=ab ×100% a-接收颗粒重量(kg) b-片子重量(kg)c-取样重量(kg) d-尾料重量(kg)4.包衣工序的物料平衡包衣工序的物料平衡范围: %~ %包衣工序的物料平衡 =ba e d c +++ 包衣工序的收率 =b ac +a-素片重量(kg) b-包衣剂重量(kg) c-糖衣片重量(kg) d-尾料重量(kg) e-取样量(kg)5.内包装工序物料平衡内包装工序物料平衡范围: %~ %包材物料平衡=%100⨯++++Aa d cb B a- PTP 领用量(kg) b- PTP 剩余量(kg) A- PVC 领用量(kg) B- PVC 剩余量(kg) c-使用量(kg) d-废料量(kg)片剂物料平衡=%100⨯++ad c b a :领用量(Kg) b :产出量(Kg)c :取样量(Kg)d :废料量(Kg)6.外包装工序的物料平衡包装材料的物料平衡范围:100%包装材料物料平衡=%100⨯+++ea d cb e-上批结存 a-领用量 b-使用量 c-剩余量 d-残损量7.生产成品率成品率范围:90%~102%片剂收率= %100⨯++ad c b a-计划产量 b-入库量 c-留样量 d-取样量1.粉碎过筛和称配岗位物料平衡检查:配料量╳100%粉碎过筛后原辅料总重(物料平衡范围应控制在~%)2.制粒干燥、整粒总混岗位物料平衡检查:总混后重量+不良品╳100%干颗粒净重+润滑剂+崩解剂(物料平衡范围应控制在~%)3.充填抛光岗位物料平衡检查:胶囊总重+细粉+不良品+废胶囊壳重量╳100%颗粒总重+胶囊壳重量(物料平衡范围应控制在~%)4.铝塑内包岗位物料平衡检查:(成品板总重/平均每板重量+不良品)×规格(粒/板)╳100%胶囊领用量/平均胶囊重(物料平衡范围应控制在~%)5.总物料平衡检查:成品产量╳100%理论产量(物料平衡范围应控制在97~100%)。
物料平衡计算
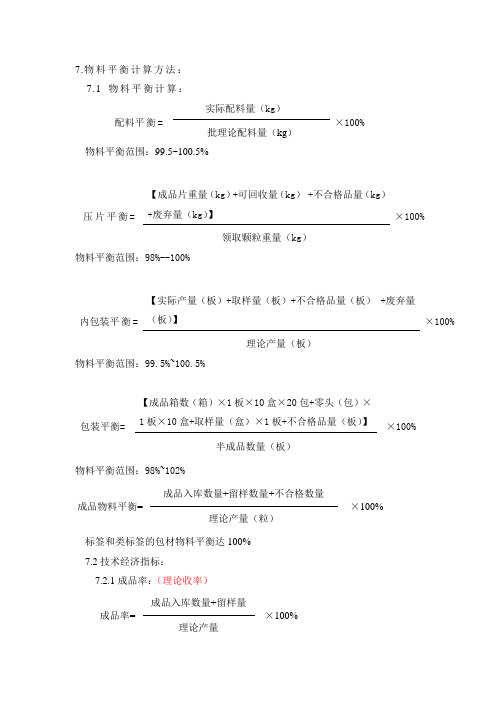
7.物料平衡计算方法:
7.1 物料平衡计算:
配料平衡= 实际配料量(kg)
×100% 批理论配料量(kg)
物料平衡范围:99.5~100.5%
压片平衡= 【成品片重量(kg)+可回收量(kg) +不合格品量(kg)
+废弃量(kg)】×100%
领取颗粒重量(kg)
物料平衡范围:98%--100%
内包装平衡= 【实际产量(板)+取样量(板)+不合格品量(板) +废弃量
(板)】×100%
理论产量(板)
物料平衡范围:99.5%~100.5%
包装平衡= 【成品箱数(箱)×1板×10盒×20包+零头(包)×
1板×10盒+取样量(盒)×1板+不合格品量(板)】
×100%
半成品数量(板)
物料平衡范围:98%~102%
成品物料平衡= 成品入库数量+留样数量+不合格数量
×100% 理论产量(粒)
标签和类标签的包材物料平衡达100% 7.2技术经济指标:
7.2.1成品率:(理论收率)
成品率= 成品入库数量+留样量
×100% 理论产量
7.2.2成本:
成本=
车间成本(元)
成品与入库数量(片)7.2.3一次合格率:
一次合格率= 一次合格品数
×100% 成品数。
GCr9物料平衡计算
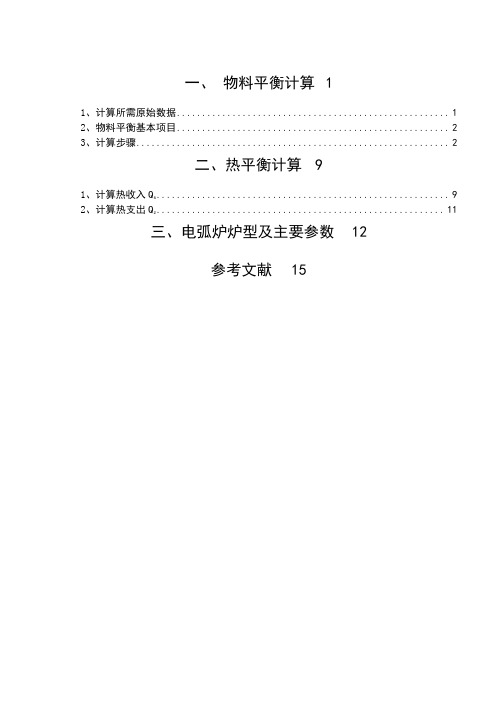
一、物料平衡计算 11、计算所需原始数据 (1)2、物料平衡基本项目 (2)3、计算步骤 (2)二、热平衡计算91、计算热收入Q s (9)2、计算热支出Q z (11)三、电弧炉炉型及主要参数12参考文献15一、物料平衡计算1、计算所需原始数据基本原始数据:冶炼钢种及成分(见表1);原材料成分(见2);炉料中元素烧损率(见表3);其他数据(见表4)注:分母系计算时的设定值,取其成分中限。
①按末期含量比规格下限低0.03%~0.10%(取0.06%)确定(一般不低于0.03%的脱碳量);②按末期含量0.015%来确定2、物料平衡基本项目收入项有:废钢、生铁、焦炭、石灰、电极、炉衬镁砖、炉顶高铝砖、火砖块、氧气和空气。
支出项有:钢水、炉渣、炉气、挥发的铁、焦炭中挥发分。
3、计算步骤以100kg金属炉料(废钢+生铁)为基础,按工艺阶段分为熔化期和氧化期分别进行计算,然后汇总成物料平衡表。
第一步:熔化期计算。
(1)确定物料消耗量:1)金属炉料配入量。
废钢和生铁按75kg和25kg搭配,不足碳量用焦炭来配。
其结果列于表5。
①碳烧损率25%。
2)其他原材料消耗量。
为了提前造渣脱磷,先加入一部分石灰(20kg/t(金属料))和矿石(10kg/t(金属料))。
炉顶、炉衬和电极消耗量见表4。
(2)确定氧气和空气消耗量:耗氧项包括炉料中元素的氧化,焦炭和电极中碳的氧化;而矿石则带来部分氧,石灰中CaO被自身S还原出部分氧。
详见表6。
*令铁烧损率为2%,其中80%生成Fe2O3挥发掉成为烟尘的一部分;20%成渣。
在这20%中,按3:1的比例分别生成(FeO)和(Fe2O3)。
如表4中所述,应由氧气供给的氧为50%,即3.142×50%=1.571,空气应供氧1.571-0.270=1.301kg,由此可求出氧气与空气的实际消耗量如表7(3)确定炉渣量:炉渣源于炉料中Si、Mn、P、Fe等元素的氧化产物,炉顶和炉衬的蚀损,焦炭和电极中的灰分,以及加入的各种熔剂。
物料平衡计算公式
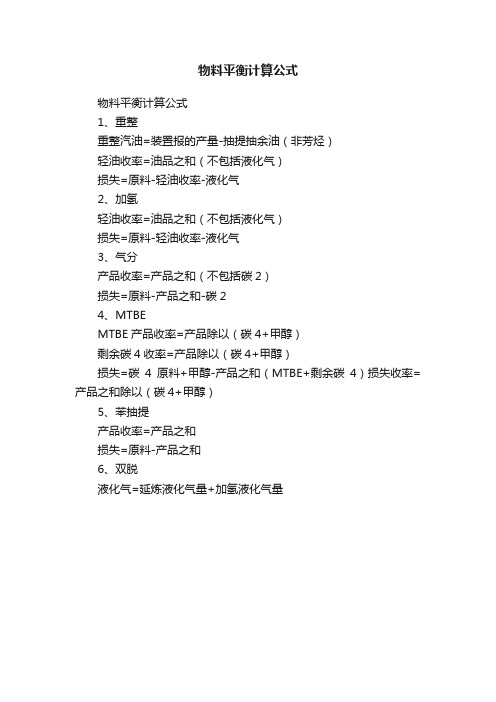
物料平衡计算公式
物料平衡计算公式
1、重整
重整汽油=装置报的产量-抽提抽余油(非芳烃)
轻油收率=油品之和(不包括液化气)
损失=原料-轻油收率-液化气
2、加氢
轻油收率=油品之和(不包括液化气)
损失=原料-轻油收率-液化气
3、气分
产品收率=产品之和(不包括碳2)
损失=原料-产品之和-碳2
4、MTBE
MTBE产品收率=产品除以(碳4+甲醇)
剩余碳4收率=产品除以(碳4+甲醇)
损失=碳4原料+甲醇-产品之和(MTBE+剩余碳4)损失收率=产品之和除以(碳4+甲醇)
5、苯抽提
产品收率=产品之和
损失=原料-产品之和
6、双脱
液化气=延炼液化气量+加氢液化气量。
物料平衡计算公式:
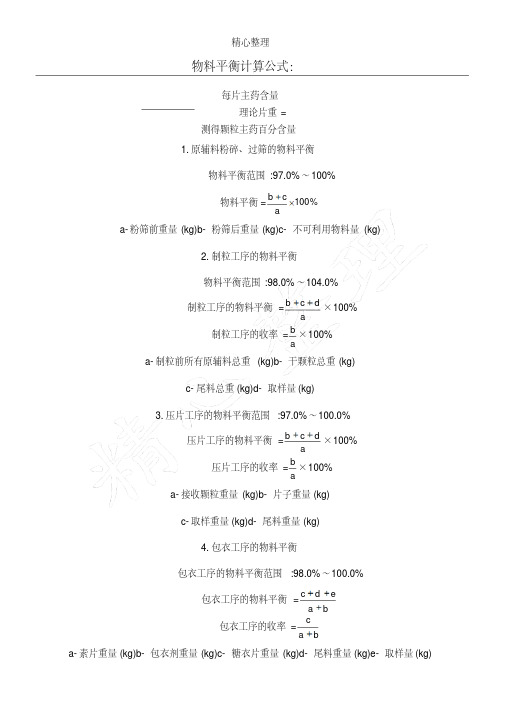
精心整理
物料平衡计算公式:
每片主药含量
理论片重=
测得颗粒主药百分含量
1.原辅料粉碎、过筛的物料平衡
物料平衡范围:97.0%~100%
物料平衡=%
100a c b
a-粉筛前重量(kg)b-粉筛后重量(kg)c-不可利用物料量(kg)
2.制粒工序的物料平衡
物料平衡范围:98.0%~104.0%
制粒工序的物料平衡=a d c b
×100% 制粒工序的收率=a b
×100%
a-制粒前所有原辅料总重(kg)b-干颗粒总重(kg)
c-尾料总重(kg)d-取样量(kg)
3.压片工序的物料平衡范围:97.0%~100.0%
压片工序的物料平衡=a d c b
×100% 压片工序的收率=a b
×100%
a-接收颗粒重量(kg)b-片子重量(kg)
c-取样重量(kg)d-尾料重量(kg)
4.包衣工序的物料平衡
包衣工序的物料平衡范围:98.0%~100.0%
包衣工序的物料平衡=
b a e d
c 包衣工序的收率=b a
c
a-素片重量(kg)b-包衣剂重量(kg)c-糖衣片重量(kg)d-尾料重量(kg)e-取样量(kg)。
炼钢物料平衡热平衡计算概述

炼钢物料平衡热平衡计算概述炼钢是一项涉及到复杂物料流动和能量转化的工艺过程。
热平衡计算是炼钢过程中的重要一环,它可用于评估和优化炼钢装置的热能利用效率。
炼钢物料平衡热平衡计算主要包括两个方面:物料平衡计算和热平衡计算。
物料平衡计算是指通过对炼钢装置中各个系统和设备中原料、中间产品和产出物料的流量进行测量和计算,以确定物料流动的平衡状况。
这一步骤通常包括测量和计算进料的质量和流量、测量和计算产出物料的质量和流量以及收集和记录其他与物料平衡相关的数据。
物料平衡计算可帮助工程师了解炼钢过程中原料的利用率和产出物料的损耗情况,从而评估和改进炼钢装置的运行效果。
热平衡计算是指通过对炼钢装置中的热流量进行测量和计算,以确定能量的平衡状况。
在炼钢过程中,燃料燃烧产生的热能被用于加热冷却液、回收热能或用于其他工艺用途。
热平衡计算可以帮助工程师了解炼钢装置中热能的利用率和能量总和的平衡状况,从而优化能源利用,降低能源消耗。
物料平衡和热平衡的计算是相互关联的,彼此影响。
在炼钢过程中,物料的流动和能量的转化是紧密联系的。
例如,在高炉冶炼过程中,铁矿石和焦炭作为原料进入高炉,燃烧产生的热能用于冶炼和预热原料。
热平衡计算可以帮助确定燃烧的热能是否能满足冶炼的要求,物料平衡计算可以帮助确定原料的利用率和产出物料的质量。
总之,炼钢物料平衡热平衡计算是炼钢过程中的关键一环,它可用于评估和优化炼钢装置的热能利用效率。
通过物料平衡计算可以了解原料的利用率和产出物料的损耗情况,通过热平衡计算可以了解炼钢装置中热能的利用率和能量平衡情况。
这两个计算相互关联,彼此影响,共同为炼钢过程的优化提供依据。
炼钢物料平衡热平衡计算是炼钢过程中的重要环节,其目的是评估和优化炼钢装置的热能利用效率。
通过进行物料平衡计算和热平衡计算,可以对炼钢过程中的物料流动和能量转化进行有效控制和管理,从而提高生产效率和降低能耗。
物料平衡计算是通过对炼钢装置中的原料、中间产品和产出物料的流量进行测量和计算,以确定物料流动的平衡状况。
物料平衡怎么计算?
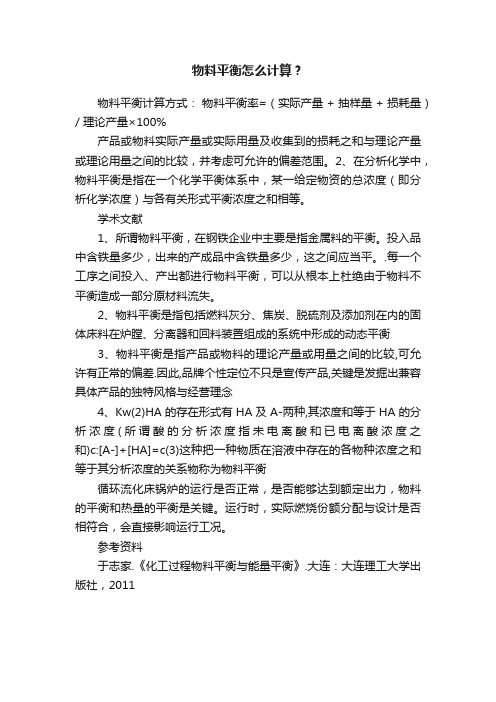
物料平衡怎么计算?
物料平衡计算方式:物料平衡率=(实际产量 + 抽样量 + 损耗量)/ 理论产量×100%
产品或物料实际产量或实际用量及收集到的损耗之和与理论产量或理论用量之间的比较,并考虑可允许的偏差范围。
2、在分析化学中,物料平衡是指在一个化学平衡体系中,某一给定物资的总浓度(即分析化学浓度)与各有关形式平衡浓度之和相等。
学术文献
1、所谓物料平衡,在钢铁企业中主要是指金属料的平衡。
投入品中含铁量多少,出来的产成品中含铁量多少,这之间应当平。
.每一个工序之间投入、产出都进行物料平衡,可以从根本上杜绝由于物料不平衡造成一部分原材料流失。
2、物料平衡是指包括燃料灰分、焦炭、脱硫剂及添加剂在内的固体床料在炉膛、分离器和回料装置组成的系统中形成的动态平衡
3、物料平衡是指产品或物料的理论产量或用量之间的比较,可允许有正常的偏差.因此,品牌个性定位不只是宣传产品,关键是发掘出兼容具体产品的独特风格与经营理念
4、Kw(2)HA的存在形式有HA及A-两种,其浓度和等于HA的分析浓度(所谓酸的分析浓度指未电离酸和已电离酸浓度之和)c:[A-]+[HA]=c(3)这种把一种物质在溶液中存在的各物种浓度之和等于其分析浓度的关系物称为物料平衡
循环流化床锅炉的运行是否正常,是否能够达到额定出力,物料的平衡和热量的平衡是关键。
运行时,实际燃烧份额分配与设计是否相符合,会直接影响运行工况。
参考资料
于志家.《化工过程物料平衡与能量平衡》.大连:大连理工大学出版社,2011。
3.3.3物料平衡计算的方法和步骤

3.3.3物料平衡计算的方法和步骤三、物料平衡计算的方法和步骤(一)水泥厂的物料平衡计算1.烧成车间生产能力和工厂生产能力的计算(1)年平衡法计算步骤是:按计划任务书对工厂规模(水泥年产量的要求),先计算要求的熟料年产量,然后选择窑型、规格,标定窑的台时产量,选取窑的年利用率,计算窑的台数,最后再核算出烧成系统和工厂的生产能力。
①要求的熟料年产量可按式(3-1)计算: Q y =pe d ---100100G y (3-1)式中 Q y ——要求的熟料年产量(t/a );G y ——工厂规模(t/a );d ——水泥重视高的掺入量(%);e ——水泥中混合材的掺入量(%);p ——水泥的生产损失(%),可取为3%~~5%。
当计划书任务书规定的产品品种有两种或两种以上,但所用的熟料相同时,可按下式分别求出每种水泥要求的熟料年产量,然后计算熟料年产量的总和。
Q y1=pe d ---10010011G y1(3-2)Q y2=p e d ---10010022G y2(3-3)Qy=Q y1+Q y2(3-4)式中Q y1,Q y2——分别表示每种水泥要求的熟料年产量(t/a );G y1,G y2——分别表示每种水泥年产量(t/a ); d 1,d 2——分别表示每种水泥中石膏的渗入量(%);e 1,e 2——分别表示每种水泥中混合材的渗入量(%);Q y ——两种熟料年产量的总和(t/a )。
②窑的台数可按式(3-5)计算:n=1.8760h QQyη (3-5)式中 n ——窑的台数;Q y ——要求的熟料年产量(t/a );Q h.1——所选窑的标定台时产量【t/(台·h)】;η——窑的年利用率,以小数表示。
不同窑的年利用率可参考下列数值:湿法窑0.90,传统干法窑0.85,机立窑0.8~0.85,悬浮预热器窑、预分解窑0.85;8760——全年日历小时数。
算出窑的台数n 等于或略小于整数并取整数值。
- 1、下载文档前请自行甄别文档内容的完整性,平台不提供额外的编辑、内容补充、找答案等附加服务。
- 2、"仅部分预览"的文档,不可在线预览部分如存在完整性等问题,可反馈申请退款(可完整预览的文档不适用该条件!)。
- 3、如文档侵犯您的权益,请联系客服反馈,我们会尽快为您处理(人工客服工作时间:9:00-18:30)。
一、物料平衡计算 (1)1、计算所需原始数据 (1)2、物料平衡基本项目 (2)3、计算步骤 (2)二、热平衡计算 (9)1、计算热收入Q s (9)2、计算热支出Q z (11)三、电弧炉炉型及主要参数 (12)参考文献 (15)一、物料平衡计算1、计算所需原始数据基本原始数据:冶炼钢种及成分(见表1);原材料成分(见2);炉料中元素烧损率(见表3);其他数据(见表4)表1 冶炼钢种及其成分钢种成分(%)备注C Si Mn P S Cr FeGCr9 1.00~1.10/1.050.15~0.35/0.250.20~0.40 ≤0.027 ≤0.020 0.90~1.20余量氧化法注:分母系计算时的设定值,取其成分中限。
表2 原材料成分(%)名称C Si Mn P S Cr Al Fe H2O灰分挥发分碳素废钢0.18 0.25 0.55 0.030 0.030 余量炼钢生铁 4.20 0.80 0.60 0.200 0.035 余量焦炭81.50 0.58 12.40 5.52 电极99.00 1.00名称CaO SiO2MgO Al2O3CaF2Fe2O3CO2H2O P2O5S石灰88.00 2.50 2.60 1.50 0.50 4.64 0.10 0.10 0.06铁矿石 1.30 5.75 0.30 1.45 89.77 1.20 0.15 0.08火砖块0.55 60.80 0.60 36.80 1.25高铝砖 1.25 6.40 0.12 91.35 0.88镁砂 4.10 3.65 89.50 0.85 1.90焦炭灰分 4.40 49.70 0.95 26.25 18.55 0.15电极灰分8.90 57.80 0.10 33.10表3 炉料中元素烧损率成分C Si Mn P S烧损率(%)熔化期25~40,取30 70~95,取 8560~70,取6540~50,取45可以忽略氧化期0.06①全部烧损20 0.015②25~30,取27①按末期含量比规格下限低0.03%~0.10%(取0.06%)确定(一般不低于0.03%的脱碳量);②按末期含量0.015%来确定表4 其他数据名称参数配碳量比钢种规格中限高0.70%,即达1.75%熔化期脱碳量30%,即1.75×30%=0.51kg电极消耗量熔化期3Kg/t;氧化期1 Kg/t炉顶高铝砖消耗量熔化期占0.75 Kg/t,氧化期0.525 Kg/t炉衬镁砖消耗量熔化期2 Kg/t;氧化期1.5 Kg/t熔化期和氧化期所需要氧量50%来自氧气,其余50%来自矿石和空气氧气纯度和利用率99%,余者为N2,氧利用率90%焦炭中碳的回收率75%(系指配料用焦炭)碳氧化产物均按70%生成CO,30%生成CO2考虑2、物料平衡基本项目收入项有:废钢、生铁、焦炭、石灰、电极、炉衬镁砖、炉顶高铝砖、火砖块、氧气和空气。
支出项有:钢水、炉渣、炉气、挥发的铁、焦炭中挥发分。
3、计算步骤以100kg金属炉料(废钢+生铁)为基础,按工艺阶段分为熔化期和氧化期分别进行计算,然后汇总成物料平衡表。
第一步:熔化期计算。
(1)确定物料消耗量:1)金属炉料配入量。
废钢和生铁按75kg和25kg搭配,不足碳量用焦炭来配。
其结果列于表5。
表5 炉料配入量名称用量(kg)配料成分(kg)C Si Mn P S Fe废钢75.000 0.135 0.188 0.413 0.023 0.023 74.218 生铁25.000 1.050 0.200 0.150 0.050 0.009 23.541 焦炭0.924 0.565①合计100.924 1.750 0.388 0.563 0.073 0.032 97.759 ①碳烧损率25%。
2)其他原材料消耗量。
为了提前造渣脱磷,先加入一部分石灰(20kg/t(金属料))和矿石(10kg/t(金属料))。
炉顶、炉衬和电极消耗量见表4。
(2)确定氧气和空气消耗量:耗氧项包括炉料中元素的氧化,焦炭和电极中碳的氧化;而矿石则带来部分氧,石灰中CaO被自身S还原出部分氧。
详见表6。
表6 净耗氧量的计算项目名称元素反应产物元素氧化量(kg)耗氧量(kg)供氧量(kg)耗氧项炉料中元素的氧化CSiMnPFe〔C〕→{CO}〔C〕→{CO2}〔Si〕→(SiO2)〔Mn〕→(MnO)〔P〕→(P2O5)〔Fe〕→(FeO)*〔Fe〕→(Fe2O3)*1.750×30%×70%=0.3681.750×30%×30%=0.1580.388×85%=0.3300.563×65%=0.3660.073×45%=0.03397.759×2%×15%=0.29397.759×2%×85%=1.6620.4910.4210.4430.1060.0430.0840.712合计 3.210 2.300 焦炭中碳的氧化电极中碳的氧化CC(C)→{CO}(C)→{CO2}(C)→{CO}(C)→{CO2}0.924×81.5%×25%×70%=0.1320.924×81.5%×25%×30%=0.0570.4×75%×99%×70%=0.2080.4×75%×99%×30%=0.0890.1760.1520.2770.237合计 3.142供氧项矿石石灰Fe2O3SFe2O3 =2Fe+3/2O2CaO+S=CaS+O0.2690.0006合计0.270 净耗氧量 2.872 *令铁烧损率为2%,其中80%生成Fe2O3挥发掉成为烟尘的一部分;20%成渣。
在这20%中,按3:1的比例分别生成(FeO)和(Fe2O3)。
如表4中所述,应由氧气供给的氧为50%,即3.142×50%=1.571,空气应供氧1.571-0.270=1.301kg,由此可求出氧气与空气的实际消耗量如表7表7 氧气与空气实际消耗量氧气(kg)空气(kg)带入O2带入N2带入O2带入N21.571/90%=1.746 1.746/99%×1%=0.018 1.301 1.301×(77/23)=4.356∑=1.746+0.018=1.764 ∑=1.301+4.356=5.657 上述1)+2)便是熔化期的物料收入量。
(3)确定炉渣量:炉渣源于炉料中Si、Mn、P、Fe等元素的氧化产物,炉顶和炉衬的蚀损,焦炭和电极中的灰分,以及加入的各种熔剂。
结果见表8。
表8熔化期炉渣量的确定名称消耗量(kg)成渣组分(kg)CaO SiO2MgO Al2O3MnO FeO Fe2O3P2O5CaS合计炉料SiMnPFe0.3300.3660.0330.3910.7070.4720.377 0.1400.0760.7070.4720.0760.517炉顶炉衬焦炭电极石灰矿石0.0750.2000.9240.3002.0001.0000.0010.0080.005略1.7580.0130.0040.0070.0570.0020.0500.058略0.1790.001略0.0520.0030.0690.0020.0300.0010.0300.0150.0010.0040.0210.010余量0.002 0.0020.0750.2000.1140.0031.904合计 1.785 0.885 0.235 0.147 0.472 0.377 0.176 0.080 0.004 4.161 百分比42.90 21.27 5.65 3.53 11.34 9.06 4.23 1.92 0.10 100.00①Fe的消耗量,按表6中注释97.759×25%×20%=0.391②石灰中氧化钙的计算,石灰中自身S还原消耗0.002kgCa③矿石中的Fe2O3假设全部还原,还原得到的铁为1.000×0.8977×112/160=0.628kg(4)确定金属量:金属量Q i=金属炉料重+矿石带入的铁量-炉料中C、Si、Mn、P和Fe的烧损量+焦炭配入的碳量=100+0.628-3.210+0.565=97.983kg。
(5)确定炉气量:炉气来源于炉料以及焦炭和电极中碳的氧化物CO和CO2,氧气带入的N2,物料中的H2O及其反应产物,游离O2及其反应产物,石灰的烧减(CO2),焦炭的挥发分。
计算结果列于表9。
表9 炉气量计算项目气态产物(kg)CO CO2N2H2O H2挥发物合计炉料中C的氧化焦炭带入电极带入石灰带入矿石带入氧气带入空气带入游离O2参与反应CO+1/2O2=CO2 H2O参与反应H2O+CO=H2+CO20.8590.3080.485-0.301-0.1200.5790.2090.3260.0930.4800.1890.0184.3560.0050.0020.0120.058*-0.077 0.0090.0511.4380.5730.8110.0950.0120.0184.4140.179合计1.231 1.876 4.374 0 0.009 0.051 7.540 质量分数/% 16.33 24.88 58.01 0 0.12 0.68 100.00*计算条件:常温(20℃)、常压(0.1MPa)下空气相对湿度为70%,20℃的饱和蒸汽压为0.0023MPa。
先求湿空气体积 4.396×(273+20)/273×0.1/(0.1-0.0023)=4.829 m3再算空气含水量 4.725×0.0119=0.058kg(6)确定铁的挥发量:有表6中设定,铁的挥发量为:97.949×2%×80%=1.564kg。
上述(3)+(4)+(5)+(6)便是熔化期的物料支出量。
由此可列出熔化期物料平衡表10。
表10 熔化期物料平衡表收入支出项目质量(kg) % 项目质量(kg) %废钢75.000 67.01 金属97.983 88.08生铁25.000 22.34 炉渣 4.161 3.74焦炭0.924 0.83 炉气7.540 6.78电极0.300 0.27 铁的挥发 1.564 1.41矿石 1.000 0.89石灰 2.000 1.79炉顶0.075 0.07炉衬0.200 0.18氧气 1.764 1.58空气 5.657 5.05合计111.920 100.00 合计111.248 100.00注:计算误差=(111.920-111.248)/111.920×100%=0.60%。