焦化分馏塔底循环油系统结焦及堵塞
分析分馏塔底结焦的原因--王平)

分馏塔底结焦原因的分析焦化车间王平摘要:重点分析了广州炼油化工股份有限公司延迟焦化分馏塔底结焦的原因,主要从焦炭塔的操作、分馏塔的操作和其他方面对分馏塔底结焦的原因进行了详细的分析。
关键词:焦炭塔油气线速蒸发段安全空高循环油循环比分馏塔是焦化装置的重要的生产设备之一,焦化装置的汽油、柴油、蜡油主要在分馏塔里生成,而分馏塔底结焦严重会造成以下结果:1、分馏塔底温度太高,造成分馏塔内气液两相不平衡,破坏了分馏塔内的物料平衡。
2、蒸发段温度太高,引起分馏塔冲塔,造成产品质量不合格。
3、P1109AB不上量,则循环油上、下返塔量被中断,整个分馏塔的热平衡被打破,分馏塔馏出产品质量不合格。
4、分馏塔底液面太高,使系统憋压,会造成管线破裂而导致火灾的发生。
分馏塔底结焦的原因很多,焦炭塔操作和分馏塔的操作等都会对分馏塔底结焦都会产生重要的影响。
而影响分馏塔底结焦的原因有很多,针对广石化目前分馏塔结焦严重的原因可分为以下三个方面分析:(1)焦炭塔的操作1、消泡剂注入时间偏短,注入量偏小。
注入消泡剂的目的是为了降低泡沫层的高度,而注入消泡剂太小,会造成泡沫层偏高,严重时会造成焦炭塔冲塔,进而携带焦粉进入分馏塔,造成分馏塔底结焦。
广石化规定消泡剂注入的时间为:a、当14:00信号(B点)不起时,统一在14:00之前起时,按B点起的时间注入。
b、当B点信号在14:00之前起时,按B点之前起时,按B点起的时间注入。
广石化消泡剂停注时间为:切四通阀后半小时。
消泡剂注入量为:为每小时半格,即0.5cm。
2、生焦层高度的影响。
焦炭塔总高由焦炭塔高度、泡沫层高度及空间高度三个部分组成,其中焦炭塔高度与泡沫层高度之和为生焦高度。
空间高度又被称为安全高度,国内一般取6-8m,因此,焦炭塔生焦高度极限为22-24m。
焦炭塔空高太大,则焦炭塔的利用率降低,焦炭产率下降,焦炭塔空高太小,则焦炭塔内生焦层会偏高,泡沫层也会偏高,结果会造成焦炭塔再生焦末期和换塔时会造成焦炭塔内焦粉带入分馏塔。
催化裂化装置反应分馏系统结焦问题解决方案

催化裂化装置反应分馏系统结焦问题解决方案张金堂(扬州工业职业技术学院,江苏扬州225000)摘要:在对近年来中国石油地区代表性公司催化装置结焦情况总结分析的基础上,结合国内外学术理论研究成果,提出了对结焦问题“防”与“治”的一系列措施。
并在中石油某地区公司开展应用,效果良好。
关键词:化裂化;流化;剂油比Solving Scheme of Coke Deposition inthe Reaction-fractionation System of RFCC UnitGUO Da-peng,WANXiao-Nan(PetroChina Fushun Petrochemical Company,Liaoning Fushun l 13008,China) Abstract:Based on analysis of coking situations in RFCC units of some refiners,combing with national and international academic research achievements,a series of measures to prevent from and solve eoking problems were put forward.And these measures have been applied in some refiners,and good resulm have been gained.Key words:Catalytic Cracking:Fluidization: Catalyst to oil ratio近年来为了提高效益,将催化裂化装置原料由传统的常压渣油、蜡油催化原料向重质和劣质化方向发展,在保证汽柴比等主要指标的同时尽可能多的获取化工原料是催化装置未来的发展方向。
催化裂化装置发展潜力很大。
但反应分馏系统结焦、衬里开裂脱落、滑阀故障、烟气轮机磨损等问题影响着催化裂化装置的安全、稳定、长周期运行,造成装置非计划停工,给企业带来巨大的经济损失。
延迟焦化装置分馏塔底结焦原因分析及优化

延迟焦化装置分馏塔底结焦原因分析及优化摘要:延迟焦化装置是以加工减压渣油为主要原料,延迟焦化装置主要由加热炉、焦炭塔、分馏塔等主要设备组成。
其中分馏塔的作用是根据进料中各组分存在不同的挥发度,将焦炭塔反应来的高温油气进行多次冷凝和气化,分别从侧线及顶部馏出蜡油、柴油、汽油、富气等产品,是延迟焦化装置非常关键的生产设备。
分馏塔底易结焦一直是制约延迟焦化装置安全、平稳、满负荷、长周期运行的主要因素。
关键词:延迟焦化减压渣油加热炉焦炭塔分馏塔一、前言天津分公司炼油部1#延迟焦化装置最初设计原料参照辽河渣油由中石化北京设计院总承包,中石化第四建设公司承建,为两炉四塔的生产模式。
装置始建于1996年,初始设计规模为100万吨/年,加工原料为大港原油的减压渣油。
2005年装置进行了扩能改造,规模提高到120万吨/年,同时进行了部分材料升级,以适应加工含硫原油的减压渣油。
2008年随着炼油部加工高硫劣质原油,装置加工规模按照90万吨/年重新进行了设计改造。
主要产品为干气、液态烃、汽油、柴油、蜡油、石油焦。
装置包括两大部分。
第一部分为焦化部分,包括焦化、分馏、密闭放空、污油回炼、污泥回炼、冷切焦水处理,水力出焦和焦炭装卸等;第二部分为焦化气压缩,汽柴油两级吸收和稳定等。
装置在2010年4月份进行了焦炭塔整体更换及其转油线震动问题进行了改造,检修开工后,为响应公司增效益、降成本的目标,炼油部进行加工高硫油,操作条件更加苛刻,装置焦炭塔顶油气管线在这次运行周期内,经常出现结焦的情况,影响装置平稳运行。
同时在2012年8月装置停工检修期间,通过对分馏塔底的查看,发现积焦情况比较严重,底循和辐射抽出口亦有不同程度的结焦。
这是造成装置生产期间底循泵无法正常运转、辐射泵抽出量过小的直接原因,严重者有可能导致分馏塔底系统瘫痪。
可见,如何防止分馏塔底积焦意义十分重大。
二、分馏塔底结焦的原因分析经过查阅相关资料[1],并结合装置运行和大修期间发现的结焦情况的分析及操作经验的积累和丰富,我们得出分馏塔底结焦的原因有以下几点:1.焦炭塔顶油气线速过高,造成焦炭塔顶油气携带焦粉至分馏塔底。
焦化分馏塔底循环油系统结焦及堵塞

焦化分馏塔底循环油系统结焦及堵塞原因分析及预防措施郭小安(中国石油大庆石化公司炼油厂延迟焦化车间,大庆163714)摘要针对焦化分馏塔底循环油系统结焦和堵塞问题进行了分析,并对换热器E1105CD 进行了检修,由于分馏塔底过滤器无法检修,车间对分馏及焦炭塔系统采取了相应的操作调整,对实现装置长周期运行提供了有力保障。
关键词:循环油结焦堵塞预防措施1 前言大庆石化公司延迟焦化装置于2008年9月建成投产,设计加工能力为120万吨/年,采用一炉两塔的工艺路线和“可灵活调节循环比”流程[1],该流程在常规的流程基础上,增加循环油抽出设施,循环比的调节直接采用循环油与减压渣油混合的方式,反应油气热量采用循环油中段回流方式取走。
由于取消了反应油气在塔内直接与减压渣油换热的流程,不但循环比可以灵活调节,而且可以大大降低在低循环比下分馏塔下部的结焦倾向。
同时,由于进料的减压渣油不直接与含有焦粉的反应油气接触,辐射进料泵的焦粉含量可以大幅度减少,因而可以减缓辐射进料泵的磨损,延长辐射进料泵的使用寿命。
此流程和原料进分馏塔底预热的老流程相比,其优点是生产方案调整灵活,加热炉和分馏塔底结焦倾向小,其缺点是分馏塔底焦粉置换量小,大部分焦粉在循环油系统中,很容易造成循环油系统被焦粉堵塞问题[2]。
图1-1 焦化分馏塔底循环油系统流程图2 基本情况介绍及存在问题2.1 分馏塔底过滤器检修情况2011年7月检修期间对分馏塔底过滤器进行检修,发现堵塞非常严重,几乎被堵死。
检修期间由于焦炭塔油气入分馏塔口法兰未进行拆卸,导致油气线清焦时产生的大量小焦块进入分馏塔底,这样就加速了循环油系统的堵塞。
2011年8月底分馏塔底泵频繁发生抽空后,对塔底过滤器和泵入口过滤器分别进行了清焦。
2.2 换热器检修前后对比焦化车间原料-循环油换热器E1105A~D自焦化装置2008年开工至2011年未进行检修,已累计运行3年。
2011年11月对换热器E1105AB进行切除过程中,发现管程入口阀不严,无法进行检修,副线阀开度约6扣左右,随后车间对换热器E1105CD进行了检修,检修前后运行参数及照片见。
防止炼厂焦化装置分馏塔结焦的有效措施研究

防止炼厂焦化装置分馏塔结焦的有效措施研究发布时间:2021-11-16T08:01:26.078Z 来源:《中国科技人才》2021年第22期作者:张轩荣[导读] 炼厂中延迟焦化装置的重要性毋庸置疑,而要保持装置的长周期安全稳定运行,减少降低分馏塔底结焦很关键。
本文在对延迟焦化装置分馏塔底系统结焦问题进行现象判断和原因分析基础上,从流程设计、生产控制和设备运行等几个方面提出了防止分馏塔结焦的具体措施。
中国石油辽河石化分公司辽宁盘锦 124000摘要:炼厂中延迟焦化装置的重要性毋庸置疑,而要保持装置的长周期安全稳定运行,减少降低分馏塔底结焦很关键。
本文在对延迟焦化装置分馏塔底系统结焦问题进行现象判断和原因分析基础上,从流程设计、生产控制和设备运行等几个方面提出了防止分馏塔结焦的具体措施。
关键词:延迟焦化装置;分馏塔结焦;防止措施引言随着原油变重、含硫量增高,减压渣油性质更趋于劣化后,焦化装置的原料性质适应性广、操作加工费用低和产品分布灵活可调等优势更加彰显,在炼厂总流程的排定以及生产计划的设置中作用也将更加突出。
但由于原料性质变差、工艺设计不合理和操做不当,常会导致焦炭塔油气中焦粉携带量增加,影响分馏塔操作,进而造成分馏塔底结焦加剧,装置被迫停工。
据不完全统计,分馏塔底系统结焦导致非计划停工占延迟焦化装置非计划停工总的次数50%以上,有的装置连续发生该部位严重结焦导致装置非计划停工。
本文从流程设计、生产控制和设备运行等几个方面分析分馏塔结焦的原因,并提出相应的解决办法。
1分馏塔底结焦原因分析和现象延迟焦化装置的结焦部位主要发生在大油气线、加热炉炉管和分馏塔底部。
原料性质变化、焦炭塔非正常操作、分馏塔底温度过高、介质在分馏塔底停留时间太长等都会导致分馏塔塔底结焦,而分馏塔底系统结焦主要集中在塔体下段、人字塔板上和循环油过滤器等三个部位。
分馏塔底系统结焦以后,一般会出现分馏塔底过滤器前后压差增大、堵塞,甚至分馏塔底部结满厚厚一层焦,堵塞循环油下流通道,循换油泵不停发生抽空不上量。
某重油催化裂化装置结焦原因分析及其预防应对策略

某重油催化裂化装置结焦原因分析及其预防应对策略本文以某石化公司1.2Mt/年重油催化装置为例,就其运行过程中出现的装置提升管、沉降器、分馏塔底和油浆循环系统结焦问题进行了原因分析,并提出了针对性的预防应对措施。
标签:重油催化裂化装置;结焦原因;预防应对措施1.装置结焦概况该装置开工运行两个月后由于分馏塔底结焦,油浆泵出现抽空,经反复调节无效后,装置被迫停工。
停工检查发现:(1)分馏塔底严重结焦,塔底几乎全部充满了焦碳,只有油气入口处和靠近分馏塔搅拌蒸汽入口处的塔壁有空隙。
分馏塔板一层焦厚300-400mm,二层200-300mm,多块塔板被压弯变形,还有两块板脱落。
(2)油浆循环下返塔、油浆回炼线、提升管喷嘴预热线及反应集合管处分馏塔底补油线被堵塞,堵塞物为黑色半固状体。
经做苯溶解和苯不溶物灼烧后,Al2O3含量分析结果为苯溶物49%,苯不溶物为51%,Al2O3含量为4.3%(m),推算结果约含催化剂15%左右。
(3)油浆/原料换热器堵塞严重,且油浆系统调节阀磨损严重。
(4)装置停工检修期间检查发现提升管喷嘴上方1m处有大量硬质焦块,该部位人孔全部堵死。
沉降器顶有大量焦块,防焦蒸汽环管大部分被埋死。
沉降器旋分器升气管外壁有大量硬质焦块。
2.结焦原因分析2.1分馏塔底与油浆系统结焦导致分馏塔底与油浆系统结焦的因素较多,其中油浆的化学组成、分馏塔底和油浆系统的操作条件(如:分馏塔底液面、温度、催化剂固体含量、工艺管线和换热器管束流速等)是主要原因,此外,还与事故状态下的应急处理方式、分馏塔底结构形式等有关。
为提高装置负荷将部分性质恶劣的原料油大量供给重催,为提高装置轻质油收率,采取油浆部分回炼,直接导致油浆性质恶化,油浆比重长期在 1.05~1.1g/cm3运行;操作上,分馏塔底温度控制过高,油浆泵单台运行,循环量只有350t/h,油浆循环系统流速只有不足1.0m/s;为降低能耗,大量限制反应系统各部蒸汽,低负荷运行时沉降器旋分器偏离允许运行工况,导致油浆固含长期超标,这都加剧了分馏塔底与油浆系统结焦的速度。
焦化分馏塔底结焦原因分析与控制

焦化分馏塔底结焦原因分析与控制作者:王蕴超来源:《中国化工贸易·上旬刊》2019年第02期摘要:分馏塔底结焦问题的有效控制,一方面能够降低对塔底循环泵运行的损害,使循环泵等设备能够长期保持运行状态;另一方面,更能够解决过滤器频繁堵塞塔底循环系统的问题,以便持续保障分馏塔生产安全性。
本文基于分馏塔底结焦原因展开分析,在明确控制措施同时,期望为后续分馏塔装置的使用提供良好参照。
关键词:分馏塔;底部结焦;原因分析;控制对策1 分馏塔底结焦原因分析1.1 空塔气流速度偏高首先,在炉内蒸汽排除时,设计人员并未根据标准值选择适宜的汽封装置,导致介质流量高于设计标准值,如此便极易使炉内热量流失。
其次,在焦炭塔设备更换后,在小吹气阀使用期间,吹扫阀也在同时使用,如此塔内气流速度大幅度增加,极易使分馏塔底温度降低,从而呈现结焦问题。
1.2 消泡剂层厚升高根据以往调查资料可知,消泡剂在每个结焦周期中添加的数量是一定的,但基于部分设备存在的问题,经常会使得消泡剂添加量存在一定浮动性,不但极易使得消泡剂注入不均匀,使其消泡性能难以得到发挥,同时焦化反应环境温度的降低,同样会使得消泡剂反应不彻底,促使消泡剂层厚变高。
1.3 分馏塔与焦炭塔操作不平稳根据分馏塔与焦炭塔操作资料可知,部分分馏塔在蒸发段温度下限设置期间,为避免蒸发段温度不低于控制标准,操作人员有可能会关小或关闭循环油上流调节阀,如此便极易造成上流循环油流量过低,致使在塔底部位出现结焦现象。
与此同时,操作人员为确保装置液体收率达标,通常也会对蒸发段的温度进行调节,以便维持能耗最低的循环比,但根据实际情况可知,多数情况温度调节并不及时,致使回流量呈现波动性,在部分冷却时段便极易在塔底结焦。
另外,在分馏塔与焦炭塔生产期间,因为急冷油切换时间的缩短,使得老塔温度普遍呈现下降速度过快的情况,当临近标准值时,新塔油气温度通常还有下降空间,如此便极易使老塔底部出现结焦状况。
延迟焦化运行常见问题

2.3确定最佳的急冷油注入位置
在早期的设计中,一 般在大油气线出口加 三条急冷油注入线, 管径大多是DN25,斜 插入大油气线中,如 图所示:
• 经过各炼厂焦化装置长 期的经验总结,提出了 一系列行之有效的方法。 如在油气管线上加法兰, 当油气管线结焦时可以 拆掉清焦。有的在油气 出口管线上加过滤器。 还有一种比较好的注入 方法,将急冷油注入油 气刚出焦炭塔的根部, 而且急冷油管线也增大 到DN40,有的采用斜插 式注入,有的采用内置 环行喷雾管注入,均可 有效的防止了油气线结 焦。见图
1.3 加热炉出口温度
加热炉出口温度是焦化反应最关键的操作参数,它 直接影响到焦炭塔内泡沫层的高度。炉出口温度越高,焦 化反应越剧烈,深度越深,泡沫层的高度越低。反之,泡 沫层的高度就越高,易雾沫夹带,使泡沫状焦粉带入油气 管线而引起结焦。图-3表示三种减压渣油炉出口温度与 泡沫层高度的关系。
1.4 加热炉炉管注汽(注水)量
2、掺炼催化油浆使分馏塔底循环过滤器堵塞
• 催化油浆中的催化剂固体粉末除在原料换热器内沉积外, 另一重要沉积点为焦化分馏塔底,由于底循环运转的作用, 该固体粉末最终沉积在底循环过滤器内。自从2003年10 月份掺炼油浆以来,焦化分馏塔底循环过滤器经常堵塞, 导致底循环泵提不起量,常常用蒸汽反吹扫,仍难以奏效, 只好拆开清理,仅11月份就拆开清理3次,拆开后发现过 滤器内含较多焦粉与催化剂粉末混合后的粉状、块状物, 堵塞严重。而在第一开工周期期间(该期间基本未掺炼催 化油浆)该过滤器未曾因堵塞拆开清理过,这进一步验证 了大比例掺炼油浆是导致底循环过滤器堵塞的主要原因。
1.6 焦粉(或泡沫)的夹带
焦炭塔焦粉(或泡沫)的夹带量大小主要与塔内的油 气线速及安全空高有关,在确定焦炭塔直径时一般按 小于允许线速度计算,当装置处理能力提高时,油气 线速增大,容易导致焦粉和泡沫不能沉降而带到油气 线内,导致管线内结焦。
焦化分馏塔底抽出线结焦分析及减缓措施

焦化分馏塔底抽出线结焦分析及减缓措施摘要:延迟焦化分馏塔底抽出线结焦是焦化装置普遍存在的一个问题,通过综合当前国内延迟焦化方面的工艺进展及对焦化装置分馏塔底抽出线结焦情况分析,得到影响分馏塔底抽出线结焦的主要因素有辐射注汽量、冷焦吹汽量、消泡剂的作用、焦炭塔平稳操作以及分馏塔底温度等,同时提出了减缓结焦的措施。
关键词:延迟焦化结焦分馏塔底抽出线兰州石化公司炼油厂1.2Mt/a延迟焦化装置,于2005年6月实现投料试车一次成功。
生产过程中发现分馏塔底抽出线结焦严重,在每一个生产周期后期很难建立塔底循环,导致分馏塔底开始结焦,给正常生产带来严重影响。
1、分馏塔底抽出线结焦影响因素分析1.1 辐射注汽量的影响注汽量的大小与原料性质、循环比和处理量等有关,对于新装置,为避免炉管结焦,注汽量较大,但这样加速了油气携带焦粉,增加了焦粉进入分馏塔趋势;另外,为保持辐射炉管内一定的介质流速,当处理量大时就可适当减少注汽量,当处理量小时可适当增大注汽量。
1.2 冷焦小吹汽量的影响焦炭塔在切塔后老塔进行冷焦处理时,由于生焦上部有一定高度的泡沫层和软焦层,如果冷焦时小吹汽量过大,就会有部分泡沫层通过大油气线进入分馏塔底部,加之这时急冷油又切换去了生产塔,不能有效地抑制焦粉和泡沫层进入大油气线和分馏塔。
因此冷焦时吹汽量控制要合理,尤其是高负荷生产和焦炭塔的生焦高度比较高时,应尽量减小小吹汽时蒸汽在塔内的线速。
1.3消泡剂的作用为了降低焦炭塔内泡沫层的高度,防止焦粉通过大油气线携带进入分馏塔底部引起分馏塔底抽出线结焦,一般都要在焦炭塔顶注入消泡剂。
但对消泡剂的加入比例还需要作进一步探索,以节约成本,增加效益。
1.4 焦炭塔平稳操作焦炭塔平稳操作至关重要。
切塔过程中,要通过压缩机控制好系统压力,如果操作不当就会有大量压力损失,会加重焦炭塔内的泡沫生成,打乱分馏塔的温度和压力分布,从而发生泡沫失控导致泡沫溢出,引发焦炭塔冲塔,将大量焦粒带入分馏塔底部,堵塞分馏塔底抽出线。
催化裂化油浆系统结焦原因及解决措施
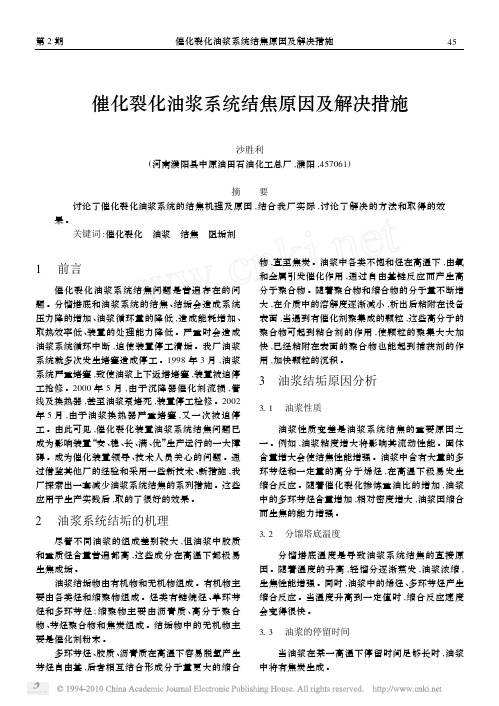
汽油
( %) 481 66 48122
液化气 总液收率
( %) 191 42 191 88
( %) 851 60 851 88
备注 :反应温度 、处理量等保持不变 ;数据采用平均值 。
由表 1 可以看出 ,塔底温度的不同对产品收率无 明显影响 。
41 3 控制停留时间
蒸汽量 (t/ h)
使用前
275 31 6
使用后 241 10
从表 2 可以看出 ,当油浆注入阻垢剂后 ,换热效 果随之明显好转 ,油浆返塔温度降低 ,蒸汽量增加 。
通过采取以上措施 ,保证了装置的长周期平稳 运行 ,降低了工人的劳动强度 。避免了因油浆系统 堵塞而导致的停工抢修事件的发生 。
催化油浆结焦 、结垢是越来越普遍的现象 ,也是 一个原因较复杂的问题 。各炼厂应根据自己的实际 情况 ,分析原因 ,找出适合自身的工艺操作条件 ,以 取得较好的阻垢效果 。
41 5 添加阻垢剂
选用合适的油浆阻垢剂 ,从装置投用起连续注 入 ,防止油浆中不溶物附着在换热器的管壁 。
我厂使用的阻垢剂型号是 SF22 ,使用的效果可 以从表 2 中看出 ,表中的数据为当催化裂化油浆系 统发生结垢时 ,加入阻垢剂 ,油浆系统部分条件的变 化。
表 2 阻垢剂的使用效果
项目 油浆返塔温度 ( ℃)
多环芳烃 、胶质 、沥青质在高温下容易脱氢产生 芳烃自由基 ,后者相互结合形成分子量更大的缩合
物 ,直至焦炭 。油浆中各类不饱和烃在高温下 ,由氧 和金属引发催化作用 ,通过自由基链反应而产生高 分子聚合物 。随着聚合物和缩合物的分子量不断增 大 ,在介质中的溶解度逐渐减小 ,析出后粘附在设备 表面 ,当遇到有催化剂聚集成的颗粒 ,这些高分子的 聚合物可起到粘合剂的作用 ,使颗粒的聚集大大加 快 ,已经粘附在表面的聚合物也能起到捕获剂的作 用 ,加快颗粒的沉积 。
关于油浆结焦问题的分析

关于油浆结焦问题的分析分馏系统结焦原因分析及对策$ b" W, x* L& X& W近年来,随着进口原油的增多,渣油掺炼比的不断提高,装置原料向劣质化和重质化方向发展,油浆在分馏塔底的停留时间长,在换热设备中的线速度低,油浆中固体物、芳烃含量高,油浆系统结焦问题越来越突出。
因此对影响装置分馏系统结焦的原因及相应对策探讨。
7 u4 }- p$ M: r(1)分馏塔底温度3 g6 {' ^9 V. a3 s2 ?- ]油浆性质随掺炼重油的比例和分馏塔底温度的变化而变化,塔底温度过高,即使停留时间较短,也易造成分馏塔底结焦,所以选择适当的塔底温度非常重要。
在投用清洗过的换热器时,保持油浆的循环量,将分馏塔底温度由原来的355℃~360℃,下调到345℃~350℃,并连续注入阻垢剂以防止油浆中的不溶物粘在管壁上。
在使用下返塔油浆作急冷油降低塔底温度的同时,必要时可直接把回炼油注入分馏塔底。
分馏塔底打急冷油的目的有两个:一是可以降低分馏塔底温度,减少油浆高温聚合生焦;二是可以对塔底油浆起搅拌作用,防止形成流动死区,防止催化剂颗粒沉积,堵塞塔底油浆滤焦器。
( J. ^0 D/ t, T, _(2)油浆在分馏塔底的停留时间& C5 h2 g! _( B. I+ R油浆在塔底停留时间长短取决于塔底液面的高低和油浆循环量的大小。
装置在油浆循环量正常的情况下,油浆在分馏塔底的停留时间控制在5min~6min比较适宜。
通过调节反应深度和塔底温度,将分馏塔底液面控制在50%左右,以不超过60%为宜。
控制适当的液面,可以避免因液面过低,造成油浆泵抽空,使得分馏塔热量过剩,从而破坏整个分馏塔的热平衡;也可以避免液面过高,使得油浆在高温的情况下,因停留时间过长而发生结焦。
1 M: v/ s: J0 P/ Q; v另外,在油浆蒸发器处的三通阀应尽可能全走冷流,以保证换热器管束内的油浆保持较高的流速,同时,在油浆泵流量最大的前提下,向油浆系统连续注入阻垢剂,保证油浆在换热器管束内壁上不粘结,避免油浆蒸发器堵塞,确保油浆系统稳定的、较高的循环量以及较短的停留时间。
浅析延迟焦化装置分馏塔底结焦原因及措施
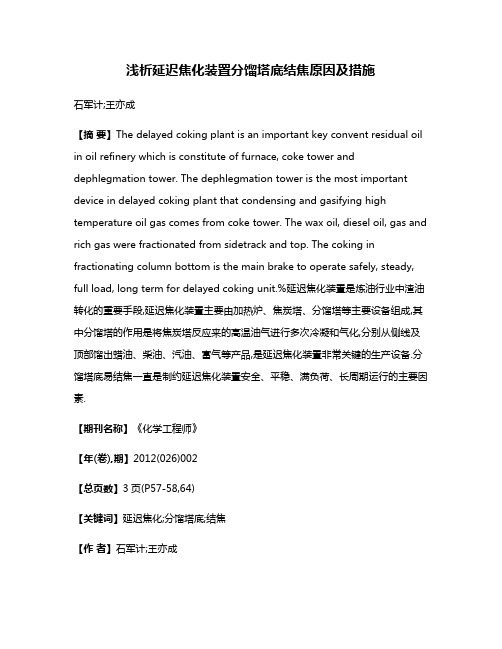
浅析延迟焦化装置分馏塔底结焦原因及措施石军计;王亦成【摘要】The delayed coking plant is an important key convent residual oil in oil refinery which is constitute of furnace, coke tower and dephlegmation tower. The dephlegmation tower is the most important device in delayed coking plant that condensing and gasifying high temperature oil gas comes from coke tower. The wax oil, diesel oil, gas and rich gas were fractionated from sidetrack and top. The coking in fractionating column bottom is the main brake to operate safely, steady, full load, long term for delayed coking unit.%延迟焦化装置是炼油行业中渣油转化的重要手段,延迟焦化装置主要由加热炉、焦炭塔、分馏塔等主要设备组成,其中分馏塔的作用是将焦炭塔反应来的高温油气进行多次冷凝和气化,分别从侧线及顶部馏出蜡油、柴油、汽油、富气等产品,是延迟焦化装置非常关键的生产设备.分馏塔底易结焦一直是制约延迟焦化装置安全、平稳、满负荷、长周期运行的主要因素.【期刊名称】《化学工程师》【年(卷),期】2012(026)002【总页数】3页(P57-58,64)【关键词】延迟焦化;分馏塔底;结焦【作者】石军计;王亦成【作者单位】玉门油田炼化总厂重油车间;玉门油田炼化总厂常减压车间,甘肃玉门735200【正文语种】中文【中图分类】TE9621 延迟焦化装置概况玉门炼化延迟焦化装置加工能力为30万t·a-1,自1993年建成投产,至今运行近19年,近年来我厂延迟焦化装置一直处于高负荷运行,延迟焦化装置现面临着全厂重油平衡的巨大压力。
催化裂化装置反应分馏系统结焦问题解决方案

催化裂化装置反应分馏系统结焦问题解决方案集团企业公司编码:(LL3698-KKI1269-TM2483-LUI12689-ITT289-催化裂化装置反应分馏系统结焦问题解决方案摘要:在对近年来中国石油地区代表性公司催化装置结焦情况总结分析的基础上,结合国内外学术理论研究成果,提出了对结焦问题“防”与“治”的一系列措施。
并在中石油某地区公司开展应用,效果良好。
关键词:化裂化;流化;剂油比SolvingSchemeofCokeDepositionintheReaction-fractionationSystemofRFCCUnitGUODa-peng,WANXiao-Nan(PetroChinaFushunPetrochemicalCompany,LiaoningFushunl13008,China)Abstract:BasedonanalysisofcokingsituationsinRFCCunitsofsomerefiners,combingwithnationalandinternationalacademicresearchachievements ,aseriesofmeasurestopreventfromandsolveeokingproblemswereputforward.Andthesemeasureshavebeenappliedinsomerefiners,andgoodresulmhavebeengained.Keywords:CatalyticCracking:Fluidization:Catalysttooilratio近年来为了提高效益,将催化裂化装置原料由传统的常压渣油、蜡油催化原料向重质和劣质化方向发展,在保证汽柴比等主要指标的同时尽可能多的获取化工原料是催化装置未来的发展方向。
催化裂化装置发展潜力很大。
但反应分馏系统结焦、衬里开裂脱落、滑阀故障、烟气轮机磨损等问题影响着催化裂化装置的安全、稳定、长周期运行,造成装置非计划停工,给企业带来巨大的经济损失。
延迟焦化装置分馏塔底结焦的原因及优化措施
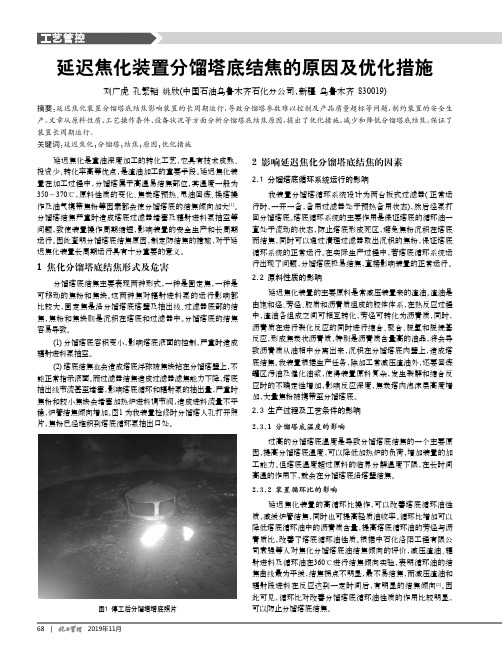
2 影响延迟焦化分馏塔底结焦的因素2.1 分馏塔底循环系统运行的影响我装置分馏塔循环系统设计为两台板式过滤器(正常运行时,一开一备,备用过滤器处于预热备用状态),然后经泵打回分馏塔底。
塔底循环系统的主要作用是保证塔底的循环油一直处于流动的状态,防止塔底形成死区,避免焦粉沉积在塔底而结焦,同时可以通过清理过滤器取出沉积的焦粉,保证塔底循环系统的正常运行。
在实际生产过程中,若塔底循环系统运行出现了问题,分馏塔底极易结焦,直接影响装置的正常运行。
2.2 原料性质的影响延迟焦化装置的主要原料是常减压装置来的渣油。
渣油是由饱和烃、芳烃、胶质和沥青质组成的胶体体系,在热反应过程中,渣油各组成之间可相互转化,芳烃可转化为沥青质,同时,沥青质在进行裂化反应的同时进行缩合、聚合、脱氢和脱烷基反应,形成焦炭状沥青质,特别是沥青质含量高的油品,将会导致沥青质从油相中分离出来,沉积在分馏塔底内壁上,造成塔底结焦。
我装置根据生产任务,除加工常减压渣油外,还要回炼罐区污油及催化油浆,使得装置原料复杂,发生裂解和缩合反应时的不确定性增加,影响反应深度,焦炭塔内泡沫层高度增加,大量焦粉被携带至分馏塔底。
2.3 生产过程及工艺条件的影响2.3.1 分馏塔底温度的影响过高的分馏塔底温度是导致分馏塔底结焦的一个主要原因,提高分馏塔底温度,可以降低加热炉的负荷,增加装置的加工能力。
但塔底温度超过原料的临界分解温度下限,在长时间高温的作用下,就会在分馏塔底沿塔壁结焦。
2.3.2 装置循环比的影响延迟焦化装置的高循环比操作,可以改善塔底循环油性质,减缓炉管结焦,同时也可提高轻质油收率。
循环比增加可以降低塔底循环油中的沥青质含量,提高塔底循环油的芳烃与沥青质比,改善了塔底循环油性质。
根据中石化洛阳工程有限公司袁强等人对焦化分馏塔底油结焦倾向的评价,减压渣油、辐射进料及循环油在360℃进行结焦倾向实验,表明循环油的结焦曲线最为平缓,结焦拐点不明显,最不易结焦,而减压渣油和辐射段进料在反应达到一定时间后,有明显的结焦倾向[2]。
重油催化裂化装置分馏塔塔盘堵塞原因及对策分析

重油催化裂化装置分馏塔塔盘堵塞原因及对策分析发布时间:2023-02-17T06:57:10.325Z 来源:《科学与技术》2022年19期作者:蔡子君[导读] 随着我国对汽油需求的不断提高,对于重油的催化裂化装置方面需要不断提高重视,在对于重油催化裂化方面一般分为汽油和轻质柴油两种类型。
蔡子君中国石油天然气集团有限公司辽河石化公司辽宁省盘锦市 124022摘要:随着我国对汽油需求的不断提高,对于重油的催化裂化装置方面需要不断提高重视,在对于重油催化裂化方面一般分为汽油和轻质柴油两种类型。
需要加大在此方面的重视力度,目前我国在重油催化裂化装置工作方面取得了巨大成就,但是在此过程中仍然出现分馏塔塔盘的堵塞现象,这会直接影响到工作效率以及工作人员的安全问题,因此需要加强对该装置中分馏塔塔盘堵塞的原因进行重点分析,并重点总结其解决对策,希望本文可以对重油催化裂化装置分馏塔塔盘堵塞问题的解决提供有效参考。
关键词:重油催化裂化装置;分馏塔塔盘堵塞;原因对策一、重油的催化裂化主要馏程炼油厂一般采用催化裂化装置对重质油轻质化进行二次加工,通过各个化学反应,最终形成市场上的柴油、汽油、液化气等,在进行对重油的催化裂化方面,需要加强企业储存和恢复活性功能。
通过对重油的雾化为催化裂化催化剂反应提供高温场所,然后对其进行油气分离,最后需要对混合油器进行分馏,在重油的催化裂化流程中,通过预热将重油加热至雾状,然后将重油与蒸汽混合放入提升反应器中,通过高温催化裂化催化剂对雾化中油进行物理化学变化,在物理变化方面形成气化,化学反应是在催化剂的作用下液化形成小分子物质,将这些小分子物质与结焦催化剂进行分离,从而形成混合油气,并放入分馏塔进行分流,一些失活的催化剂将会进行回收并恢复活性。
二、重油催化裂化装置分塔塔盘堵塞原因分馏塔塔盘阻塞一般分为结盐阻塞和结焦阻塞,根据分馏塔分流原理,重油的分流过程主要通过物质对温度的变化而进行分层,在此过程中一些原油的性质及质量不断下降,也使用了诸多的油田助剂品种,分馏塔塔盘阻塞的可能性逐步增高,其不仅会影响到整个重油裂化催化工作的效率,更会加大安全隐患的风险,因此需要加强对其原因的分析。
延迟焦化分馏塔底结焦的原因及优化

山 东 化 工 SHAND0NG CHEMICAL INDUSTRY
2016年第 45卷
2.3 焦 炭塔 的影 响
2.3.1 切 换 、吹 汽 等 情 况 切换是焦炭塔一个生焦周期 的结 束 ,也 是冷焦步 骤的开
始 。切换过程势必会引起焦炭塔压力 的波动 ,高层 的粉焦会 因为压力波动被携 带人 大油 汽管线 进入 分馏塔 。切换后 为 了避免塔底堵塞结焦并 回收塔 中残余 油气 ,会采取小 吹汽操 作 。控制小吹气量继续将油气 吹至分 馏塔 ,其量过小 就起不 到作用 ,而过大 ,会将泡沫焦粉带入 焦炭塔 ,甚至堵塞 大油汽
塔顶温度上升过慢 ;(3)系统压力波 动大 ;(4)炉 出 口温 度过 低 ;(5)拿油 带水 ;(6)焦层过高 。
2.4 分 馏塔 底部 操作 的影 响 分馏塔提馏段 的作用是将进入该 段 的轻组 分逐渐蒸 出 ,
同时把上升 蒸气 中的重 组分 冷凝 逐 步下 来 ,液 相重 组分 提 浓 ,在塔底设定 再沸器为提馏段提供汽 相 回流 。焦粉 的进入 使分馏塔底部 的生 产出现异 常 ,分馏塔底 为避免结焦 会进行 塔底油循环 J,由底循泵抽 出经 过滤器 后返塔 ,此举 为增强
热管作为传热元 件 ,可 以单根使用 ,也可 以组合使用 ,根 据现场 的条件 ,配以相应的流通结构组合成 各种形式 的换热 器 ,碳 钢 一水热 管空气预热器具有热效率 高、阻力 损失小 、结 构紧凑 、工作 可 靠 和维 护费 用少 等 诸多 优点 且 管 内工 质无 毒 、无 害 、无腐蚀 、造 价低 。通过 近一 年来 的使 用证 明 :若 管 内工质 250℃(或烟气温度 s280℃),使用钢 一水热 管空 气预热器不易发 生高 温传 热性能 失效 等问题 。扰流子 空气 预热器 在 280~450℃温度 范 围内使 用安全 系数很 高 ,造价 低 ,但 其传热速率较之碳钢 一水热管空 气预热器传 热速率偏
100万t-年催化裂化分馏塔底结焦及油浆系统堵塞的探讨

100万t/年催化裂化分馏塔底结焦及油浆系统堵塞的探讨摘要防止油浆系统结焦,堵塞是催裂化长周期运行的关键之一,一般与分馏塔底油浆的组成、温度、催化剂含量及塔底停留时间等因素有关。
延安炼油厂100万吨/年催化裂化采取了加阻垢剂、优化操作、改进工艺流程等新措施。
解决油浆系统堵塞问题,同时减缓了分馏塔结焦。
关键词催化裂化;分馏塔底;油浆系统;结焦;阻塞中图分类号te966 文献标识码a 文章编号1674-6708(2012)71-0011-020 引言催化裂化油浆系统堵塞,结焦直接影响装置的长周期运行,催化原料重质化是造成分馏塔结焦的根本原因,油浆流速低和高的固含量是造成油浆系统堵塞的主要原因,提高塔底温度,增加油浆回炼,都会造成油浆变重,稠环芳烃增加,随着超稳沸石催化剂的使用,使一部分原本可生焦的中、重芳烃不形成焦而以稠环芳烃成焦碳前身的形式积聚在油浆中,使分馏塔结焦日趋严重。
油浆系统的低流速和高固含量会造成催剂在换热器沉积,降低换热面积,最后造成换热器堵死。
延安炼油厂100万吨侔催裂化在检修时发现分馏塔底结焦严重,尤其在2006年检修中发现分馏塔软焦(前身物)和硬焦多达十几吨(见图1)。
塔底结焦的水平高度已与防涡齐平,使油浆抽出口流动区域仅形成一个圆状环隙,油浆蒸汽发生器3、4两台因油浆流速低,在运行一年后即被堵死。
图1在开工后,我们采取了防焦措施优化了操作,改进了工艺流程,加注了阻垢剂,装运得置了650天后,在2008年检修中发现油浆系统结焦较以前大为减轻,但分馏塔底结焦情况仍较为严重。
1 结焦问题分析1.1 塔底结焦与油浆性质的关系油浆中所含胶质、沥青质和多环芳烃最易结焦,因此,塔底油浆系统结焦倾向与自身组成有十分重要的关系,油浆的多环芳烃含量、密度、粘度的增大都会引起结焦趋势的增加,油浆中催化剂形成了结焦的核心,所以固含量的增大也是结焦趋势增加的一个原因。
延安炼油厂油浆性质(见表1)较好,故塔底结焦中软焦层较厚。
分馏塔底结焦的处理措施

分馏塔底结焦的处理措施发布时间:2023-01-11T07:35:36.116Z 来源:《中国科技信息》2022年第33卷16期作者:张毅[导读] 延迟焦化装置是炼油行业中渣油转换的重要手段,延迟焦化装置主要由加热炉、焦炭塔、分馏塔等主要设备组成,张毅中石油云南石化有限公司生产四部摘要:延迟焦化装置是炼油行业中渣油转换的重要手段,延迟焦化装置主要由加热炉、焦炭塔、分馏塔等主要设备组成,其中分馏塔的作用是将焦炭塔反应来的高温油气进行多次冷凝和汽化,分别从侧线及顶部馏出蜡油、柴油、汽油、富气等产品,是延迟焦化装置非常关键的生产设备,减少分馏塔底结焦直接关系着装置的长周期运行、安全生产和炼厂重油平衡。
关键词:延迟焦化分馏塔结焦延迟焦化装置为炼厂重要的重油加工装置,分馏塔底结焦一直是制约延迟焦化装置安全、平稳、满负荷、长周期的主要因素。
分馏塔底结焦严重时会造成塔底泵抽空,炉管结焦等一系列问题,从工艺技术及对焦化装置分馏塔底抽出线结焦情况分析,得到影响分馏塔底抽出线结焦的主要因素有:原料性质变化、辐射注汽量大小、冷焦时吹气量及其时间、消泡剂的注入情况、急冷油的选择及注入方式,焦炭塔平稳操作以及分馏塔底温度等。
分馏塔易结焦的部位为分馏塔底,如何防止分馏塔底结焦是保证分馏塔长周期操作的关键。
分馏塔底结焦一般有两种形态,一种是固定在塔壁上的焦炭,一种是可移动的焦粉和焦粒,前者是沿分馏塔底壁和过滤器结的焦,后者主要是沉积在塔底和过滤器中。
在塔底结的焦可使分馏塔底容积变小,导致辐射泵上量不好,还会造成塔底浮球液位计不能正常指示液面;过滤器结焦使过滤器滤焦能力下降,导致分馏塔底抽出线节流甚至堵塞,影响辐射泵上量;焦粉和焦粒都会造成加热炉辐射流控阀堵塞,影响加热炉进料的平稳性,加快炉管结焦。
1. 分馏塔底结焦的现象特征:(1)焦块或焦粉堵塞辐射泵入口过滤器,造成分馏塔底泵抽空;(2)分馏塔底壁上结焦,致使装置的处理量减小;(3)分馏塔底液位假显示,导致操作难度加大;(4)分馏塔底结焦造成分馏塔馏出产品质量不合格;(5)分馏塔底温度过高,加剧了结焦的倾向;(6)分馏塔底过滤器堵塞,导致辐射流量计波动较大,炉出口温度波动频繁。
油浆系统结焦原因及控制对策
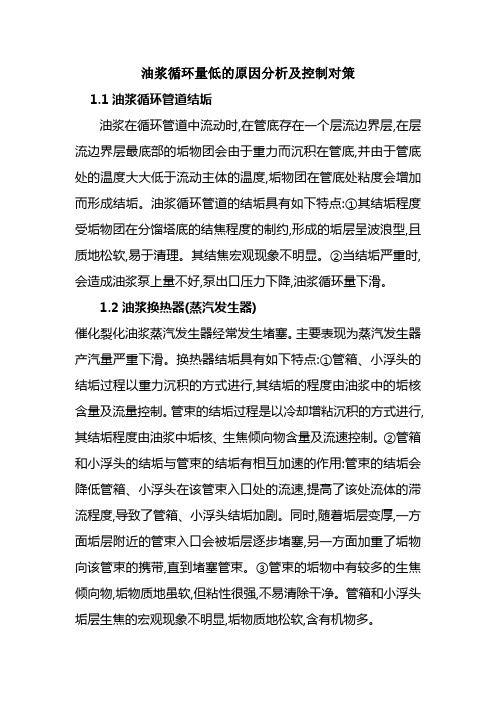
油浆循环量低的原因分析及控制对策1.1油浆循环管道结垢油浆在循环管道中流动时,在管底存在一个层流边界层,在层流边界层最底部的垢物团会由于重力而沉积在管底,并由于管底处的温度大大低于流动主体的温度,垢物团在管底处粘度会增加而形成结垢。
油浆循环管道的结垢具有如下特点:①其结垢程度受垢物团在分馏塔底的结焦程度的制约,形成的垢层呈波浪型,且质地松软,易于清理。
其结焦宏观现象不明显。
②当结垢严重时,会造成油浆泵上量不好,泵出口压力下降,油浆循环量下滑。
1.2油浆换热器(蒸汽发生器)催化裂化油浆蒸汽发生器经常发生堵塞。
主要表现为蒸汽发生器产汽量严重下滑。
换热器结垢具有如下特点:①管箱、小浮头的结垢过程以重力沉积的方式进行,其结垢的程度由油浆中的垢核含量及流量控制。
管束的结垢过程是以冷却增粘沉积的方式进行,其结垢程度由油浆中垢核、生焦倾向物含量及流速控制。
②管箱和小浮头的结垢与管束的结垢有相互加速的作用:管束的结垢会降低管箱、小浮头在该管束入口处的流速,提高了该处流体的滞流程度,导致了管箱、小浮头结垢加剧。
同时,随着垢层变厚,一方面垢层附近的管束入口会被垢层逐步堵塞,另一方面加重了垢物向该管束的携带,直到堵塞管束。
③管束的垢物中有较多的生焦倾向物,垢物质地虽软,但粘性很强,不易清除干净。
管箱和小浮头垢层生焦的宏观现象不明显,垢物质地松软,含有机物多。
1.3 分馏塔底油浆在分馏系统的流动中,随着垢物团的增长,在重力和粘性力的作用下,垢物团会落入液相慢流区并沉积在器壁上。
分馏塔塔径较大,塔底维持稳定的液面,因此油浆在塔底具有最长的停留时间。
并且油浆在塔底流动的线速并不均一,在塔的底部存在缓流区和死区,在塔壁存在滞流边界层,这些为垢物团的重力沉积创造了必要条件。
循环油浆在脱过热段与反应油气(有来自大油气管道的碎焦)进行传热和洗涤的结果造成在塔底油浆具有全塔最高的液相温度以及最高的垢核浓度。
塔底油浆主体温度高,垢物团上的生焦倾向物的热聚反应就会加剧,循环油浆在塔底液面高,停留时间延长,也会发生更多的热缩合反应。
- 1、下载文档前请自行甄别文档内容的完整性,平台不提供额外的编辑、内容补充、找答案等附加服务。
- 2、"仅部分预览"的文档,不可在线预览部分如存在完整性等问题,可反馈申请退款(可完整预览的文档不适用该条件!)。
- 3、如文档侵犯您的权益,请联系客服反馈,我们会尽快为您处理(人工客服工作时间:9:00-18:30)。
焦化分馏塔底循环油系统结焦及堵塞原因分析及预防措施郭小安(中国石油大庆石化公司炼油厂延迟焦化车间,大庆163714)摘要针对焦化分馏塔底循环油系统结焦和堵塞问题进行了分析,并对换热器E1105CD 进行了检修,由于分馏塔底过滤器无法检修,车间对分馏及焦炭塔系统采取了相应的操作调整,对实现装置长周期运行提供了有力保障。
关键词:循环油结焦堵塞预防措施1 前言大庆石化公司延迟焦化装置于2008年9月建成投产,设计加工能力为120万吨/年,采用一炉两塔的工艺路线和“可灵活调节循环比”流程[1],该流程在常规的流程基础上,增加循环油抽出设施,循环比的调节直接采用循环油与减压渣油混合的方式,反应油气热量采用循环油中段回流方式取走。
由于取消了反应油气在塔内直接与减压渣油换热的流程,不但循环比可以灵活调节,而且可以大大降低在低循环比下分馏塔下部的结焦倾向。
同时,由于进料的减压渣油不直接与含有焦粉的反应油气接触,辐射进料泵的焦粉含量可以大幅度减少,因而可以减缓辐射进料泵的磨损,延长辐射进料泵的使用寿命。
此流程和原料进分馏塔底预热的老流程相比,其优点是生产方案调整灵活,加热炉和分馏塔底结焦倾向小,其缺点是分馏塔底焦粉置换量小,大部分焦粉在循环油系统中,很容易造成循环油系统被焦粉堵塞问题[2]。
图1-1 焦化分馏塔底循环油系统流程图2 基本情况介绍及存在问题2.1 分馏塔底过滤器检修情况2011年7月检修期间对分馏塔底过滤器进行检修,发现堵塞非常严重,几乎被堵死。
检修期间由于焦炭塔油气入分馏塔口法兰未进行拆卸,导致油气线清焦时产生的大量小焦块进入分馏塔底,这样就加速了循环油系统的堵塞。
2011年8月底分馏塔底泵频繁发生抽空后,对塔底过滤器和泵入口过滤器分别进行了清焦。
2.2 换热器检修前后对比焦化车间原料-循环油换热器E1105A~D自焦化装置2008年开工至2011年未进行检修,已累计运行3年。
2011年11月对换热器E1105AB进行切除过程中,发现管程入口阀不严,无法进行检修,副线阀开度约6扣左右,随后车间对换热器E1105CD进行了检修,检修前后运行参数及照片见。
表2-1 E1105A~D运行数据对比情况图2-1 E1105CD检修图片车间通过对堵塞换热器的焦块进行分析,发现堵塞换热器管束的焦块有一部分为质地较密的焦块;还有一部分为质地松散且内部含有油迹的结焦物,为后进入分馏塔底的泡沫层物质和焦粉聚结的结焦物。
2.3 存在问题⑴2012年2月初分馏塔底泵又出现抽空现象,由于分馏塔底过滤器出入口阀(均2道阀门)被焦块卡住无法关闭,过滤器堵塞后无法清焦,车间被迫打开塔底过滤器副线,并定期对泵入口过滤器进行清理。
⑵分馏塔底过滤器副线打开后,导致换热器E1105A~D管程堵塞更加严重,由于东北地区气候影响,换热器无法检修,只能维持生产。
为了保证塔底循环油量,车间只能打开E1105A~D管程副线阀,导致分馏塔底循环油与渣油换热量减少,塔底循环油的冷却温度进一步升高,分馏塔底温度升高,从而导致分馏塔底容易发生结焦。
目前分馏塔底热偶已经出现结焦,结焦前热偶温度为363℃,结焦后热偶温度仅为274℃。
⑶打开E1105A~D管程副线阀后,原料与循环油换热量减少,原料进加热炉入口温度也降低,加热炉热负荷增加,瓦斯消耗增大,炉管表面温度升高,严重影响装置的长周期生产。
加热炉进料温度由310℃降至285℃。
加热炉热负荷增加量=160000kg/h×(310-285)℃×3.071kj/kg.℃=1.228×107kj/h,焦化自产瓦斯热值为 4.8294×104kj/kg,加热炉多消耗瓦斯=1.228×107kj/h÷4.8294×104kj/kg=254.28kg/h,影响加热炉瓦斯消耗多增加=254.28kg/h÷160000kg/h×950(系数)=1.51kg.oil/t。
3 原因分析3.1 分馏塔底是整个分馏塔焦粉聚集的地方,循环油的作用就是洗涤油气中携带的焦粉,因此分馏塔底循环油中不可避免的带有焦粉,这些焦粉在换热器内发生沉降,经过长时间的积累后导致管束堵塞。
3.2 通过检修过滤器及换热器,发现焦炭塔油气线内的结焦物质、分馏塔底部和人之挡板上的结焦与堵塞换热器的焦块质地相似,这三处的结焦也都是由于油温过高而形成结焦物质。
由于焦炭塔切塔、污油回炼等操作,造成油气线温度大幅度变化,使部分结焦脱落进入分馏塔底循环油系统。
3.3 2011年装置检修期间对焦炭塔挥发线进行了清焦,由于油气线分馏塔入口段未进行拆卸,导致清焦时产生的小焦块进入分馏塔底部,这样就加速了循环油系统的堵塞。
4 预防措施焦化装置作为重油加工装置,结焦和焦粉是最大的生产隐患,焦炭塔顶油气携带焦粉至分馏系统是不可避免的,而分馏塔底温度过高又能引发结焦,关键是如何防止和控制结焦发生,一方面防止分馏塔底结焦,另一方面防止焦炭塔油气携带焦粉到分馏系统[3]。
4.1 优化分馏系统操作⑴控制分馏塔底焦粉量严格控制分馏塔底循环油上回流量来保证分馏塔人字挡板的洗涤效果和防止循环油上回流分布器偏流,一般循环油上回流量控制在40~60t/h。
根据分馏塔进料量的大小对循环油上回流量进行相应的调整,焦粉基本被洗涤到分馏塔底循环油系统,通过分馏塔底循环油过滤器取出。
⑵防止分馏塔底器壁或人字挡板结焦严格控制分馏塔底循环油下回流量来保证分馏塔底温度,一般循环油下回流量控制在20~40t/h,分馏塔底液相温度控制在365℃以内,气相温度控制在370℃以内,防止分馏塔底器壁结焦。
控制分馏塔底上下循环油回流总量在60t/h以上,确保循环油在人字挡板上分布均匀,以防止换热段人字挡板干板结焦。
另外,通过循环油搅拌线,保证分馏塔底循环油的搅动状态防止分馏塔底聚结生焦。
⑶控制装置大循环比降低焦化循环油在分馏塔底的停留时间也有利于减少结焦,原因是停留时间长,芳烃热聚合反应生成焦炭的可能性就大,而且胶质沥青质等高沸点大分子的物质在塔底结焦的机会就会增加。
因此需要加大分馏塔底循环油的抽出量,减少塔底油的停留时间。
对于“可灵活调节循环比”的焦化装置,适当的循环比还可以提高分馏塔底焦粉的抽出,减缓分馏塔底结焦,目前我装置油量控制在26t/h,循环比控制在0.2左右。
4.2 优化焦炭塔系统操作减少焦炭塔油气焦粉携带有利于减缓分馏塔底结焦,原因是沉积到分馏塔底的焦粉颗粒对焦化循环油具有吸附作用,加速形成焦粉,因此减少焦粉携带对分馏塔底的长周期运行运行具有重要意义。
⑴控制焦炭塔压力在焦炭塔切塔后,老塔小吹汽期间的压力控制是非常重要的,老塔顶压力一旦出现大幅度下降,在焦炭塔生焦末期没有来得及进行生焦反应的泡沫层物质由于二次汽化进入大油气线管线和分馏塔,并在大油气管线和分馏塔底聚结生焦,会导致循环油换热器堵塞或分馏塔底泵抽空等事故。
我装置在切塔后老塔压力控制上采取利用预热瓦斯阀控制的方法,焦炭塔切换同时联系现场操作人员,关小老塔瓦斯阀控制老塔压力,使老塔压力与切塔前保持一致(控制在切塔前老塔压力±0.003MPa)。
焦炭塔预热期间生产塔压力也要进行控制,预热期间预热塔的瓦斯阀每次开关不要大于10%,现场要留人保证预热塔瓦斯阀少开勤开,同时与主操及时联系,主操根据焦炭塔压力控制情况及时联系外操调整预热阀的开度,确保预热期间生产塔的压力控制平稳。
通过对焦炭塔压力的控制,在2011年检修过程中分馏塔内焦粉明显减少,说明有效地降低了焦粉或泡沫层物质向后路的携带。
⑵控制焦炭塔油气线速首先控制加热炉注汽量。
加热炉炉管注汽是国内延迟焦化装置普遍采用的防止炉管结焦的重要手段之一,在实际生产过程中,根据渣油在炉管内线速度来确定注气量,在保证渣油经过炉管过程中不结焦的最低线速度的情况下,所需要的注气量即是最小注汽量。
我车间加热炉注汽量控制在加热炉进料量的1.2%左右。
其次控制焦炭塔小量吹汽量。
焦炭塔小量吹汽目的是为了汽提回收焦炭塔中的残余油气,小吹汽量控制的是否合适对于装置长周期运行也有很大影响。
小量吹汽过大会大幅增加焦炭塔油气线速,势必造成大量未反应的泡沫层物质和焦粉被携带到后路系统中。
经过反复摸索,我装置目前小量吹汽量控制在3t/h左右,时间约为1h。
4.3 控制系统压力平稳,防止焦炭塔冲塔焦炭塔切塔、改放空过程中,要通过压缩机对系统压力进行控制,如果操作不当,压力波动较大,会加重焦炭塔内的泡沫产生,从而导致泡沫失控并溢出,引发焦炭塔冲塔,将大量焦粒带入油气线中,造成油气线严重结焦。
因此,焦炭塔吹汽、冷焦过程也应缓慢进行,避免给汽、给水速度过快,将泡沫带入油气线中,从而减缓油气线结焦速度。
4.4 控制好原料性质和处理量原料组成偏轻或者加工量过高,都会造成焦炭塔内油气线速过高,因此当原料组分变轻时要适当降低装置加工量,根据装置的实际情况控制合理的加工量,以确保焦炭塔线速不过高。
6 结论车间对循环油系统存在的问题进行了处理,并对分馏和焦炭塔各种操作进行了相应的调整。
通过控制分馏塔底上、下回流量、温度和循环比的大小,以及对加热炉注汽量和焦炭塔操作及系统压力的控制进行了优化和调整,延缓了分馏塔底循环油系统堵塞和结焦的速度,力争保证装置实现4年一检修的目的。
参考文献[1] 李和杰,徐江华,甘丽琳等.延迟焦化装置的大型化扩能改造设计.炼油技术和工程.2003,33(8):5-9[2] 瞿国华,延迟焦化工艺与工程[M].北京:中国石化出版社,2008,475-476[3] 瞿滨,延迟焦化装置技术问答[M].北京:中国石化出版社,2007,96-100Abstract Coking fractionator cycle oil system coking and plugging problems, and the heat exchanger E1105CD maintenance workshop on the fractionation and coke drum system, fractionation bottom filter can not overhaul of operations to adjust to the realizationthe device long period to run provided a strong guarantee.Key Words:Circulating oil;coking;block;precaution作者:郭小安(1981-),男,助理工程师,2006年毕业于宁夏大学化学工程与工艺专业,本科,现从事延迟焦化装置技术管理工作,已发表论文2篇。