无铆钉铆接的工艺研究
Attexor无铆钉铆接介绍

常见问题与解答
问题二:不同厚薄尺寸之间出力有多大 的差异?
答案: 如果一个料层的厚度是另一个的两倍,那么当厚
层处于冲床面上时,切变强度可能要高出30%-60%
常见问题与解答
问题三:抗拉抗剪力之间的关系?
答案: 抗拉力比抗剪力低30%左右。
常见问题与解答
问题四:如果紧挨着一个铆点安排其它 铆点,可以认为总的强度是简单的叠加 吗?
大行程
大喉深及大喉高 大压力(30吨)外型
成功案例
非标钣金无铆自动线加工专机
各行业应用案例
车库门
脚手架
门框
通风管
太阳能工程
通风过滤板
各行业应用案例
烤箱门
洗衣机
电极
隔热装置
车窗机械装置
汽车装配
无铆钉铆接类型 方形
圆形
无铆钉铆接原理
无铆钉铆接原理
对某一特定材质的工件, 通过对铆孔底板厚度St 以及铆孔直径D的测量, 通过查找标准参数表对 应数据,就可以方便地 计算出当前工件铆孔的 各种抗拉、抗剪等技术 参数。
气气管管
分分体体式式气气 液液增增力力缸缸
吊吊臂臂系系统统
便便携携式式无无 铆铆工工具具
夹夹具具
板板材材
便携式工具各种应用场景
便携式工具规格参数表 FS系列
IP系列
便携式工具规格参数表 PASS系列
供系统集成及自动化用途的设备
分体式气液增力缸 无铆非标应用案例 机器人集成用C型钳
大行程、大喉深、大压力型号的外观
瑞士
无铆钉铆接系统简介
装配连接完美解决方案系列之无铆钉铆接(三) 2013年12月13日 第四稿
瑞士Attexor(ACS)
多点无铆钉铆接机原理

多点无铆钉铆接机原理引言:多点无铆钉铆接机是一种用于连接金属零部件的先进设备,它通过无需铆钉的方式,实现了高效、可靠的金属零部件的连接。
本文将详细介绍多点无铆钉铆接机的原理及其工作过程。
一、多点无铆钉铆接机的原理多点无铆钉铆接机是利用高速旋转的工具头在金属表面上形成一系列微小凸起,然后将另一金属部件放置在这些凸起上,通过高压力和高温使两者紧密连接的一种技术。
其原理主要包括以下几个方面:1. 高速旋转工具头:多点无铆钉铆接机的核心部件是高速旋转的工具头,工具头上装有多个凸起。
当工具头高速旋转时,凸起在金属表面形成一系列微小凹陷。
2. 压力和温度:在工具头旋转的同时,多点无铆钉铆接机会施加高压力和高温,使工具头上的凸起与另一金属部件接触并形成永久连接。
高压力可以确保连接的牢固性,高温则有助于金属的塑性变形,使连接更加牢固。
3. 材料选择:多点无铆钉铆接机适用于连接各种金属材料,如铝、钢、铜等。
不同的金属材料需要不同的压力和温度来实现连接,因此在使用多点无铆钉铆接机时需要根据具体材料进行调整。
二、多点无铆钉铆接机的工作过程多点无铆钉铆接机的工作过程简单明了,如下所示:1. 准备工作:首先,需要准备好待连接的金属零部件,并确定好连接的位置和方向。
2. 调整参数:根据待连接的金属材料,通过调整多点无铆钉铆接机的参数,如压力和温度,以及工具头的旋转速度等,来适配不同材料的连接需求。
3. 开始铆接:将待连接的金属零部件放置在多点无铆钉铆接机的工作台上,并将工具头对准连接位置。
然后,启动多点无铆钉铆接机,工具头开始高速旋转。
4. 连接完成:当工具头旋转时,在金属表面形成一系列微小凹陷,然后将另一金属部件放置在这些凹陷上。
同时,多点无铆钉铆接机施加高压力和高温,使两者紧密连接。
经过一段时间后,连接完成。
三、多点无铆钉铆接机的优势与应用多点无铆钉铆接机具有以下优势:1. 高效率:多点无铆钉铆接机的工作速度快,一次可以完成多个铆接点的连接,大大提高了生产效率。
无铆铆接工艺

无铆铆接工艺无铆铆接工艺是一种常用的连接技术,它通过压制、焊接或粘接等方式将两个或多个零件连接在一起。
相比传统的铆接工艺,无铆铆接工艺具有更多的优点和应用领域。
本文将从原理、应用和优点三个方面阐述无铆铆接工艺的相关知识。
无铆铆接工艺的原理是利用高温或高压的作用下,使两个或多个零件之间的分子间力增大,从而实现零件的连接。
无铆铆接工艺可以分为热压焊接、超声波焊接和粘接三种主要类型。
首先是热压焊接,它是利用高温将待连接的零件加热到一定温度,然后施加压力使其接触面之间的分子间力增加,最终实现连接。
热压焊接广泛应用于金属零件的连接,如汽车制造、航空航天等领域。
其次是超声波焊接,它利用超声波振动产生的高频振动能量,将零件接触面之间的分子间力增加,实现连接。
超声波焊接常用于塑料、橡胶等材料的连接,如电子产品的外壳、医疗器械的组装等。
最后是粘接,它是通过使用粘接剂将待连接的零件粘合在一起。
粘接工艺可以连接不同材料的零件,如金属与塑料、金属与玻璃等。
粘接具有连接强度高、密封性好、工艺简单等优点,广泛应用于船舶、建筑等领域。
无铆铆接工艺具有许多优点,首先是工艺简单,不需要大量的设备和专业的操作人员。
其次是连接强度高,可以满足各种工况下的使用要求。
此外,无铆铆接工艺还可以连接不同材料的零件,具有较好的适应性。
无铆铆接工艺在许多领域都得到了广泛的应用。
在汽车制造领域,无铆铆接工艺可以用于车身焊接、底盘连接等。
在航空航天领域,无铆铆接工艺可以用于航空发动机零件的连接。
在电子产品制造领域,无铆铆接工艺可以用于外壳的组装等。
无铆铆接工艺是一种重要的连接技术,具有工艺简单、连接强度高、适应性强等优点。
它在汽车制造、航空航天、电子产品制造等领域都得到了广泛的应用。
随着科技的不断进步和创新,无铆铆接工艺将会有更广阔的发展空间。
无铆连接工艺过程
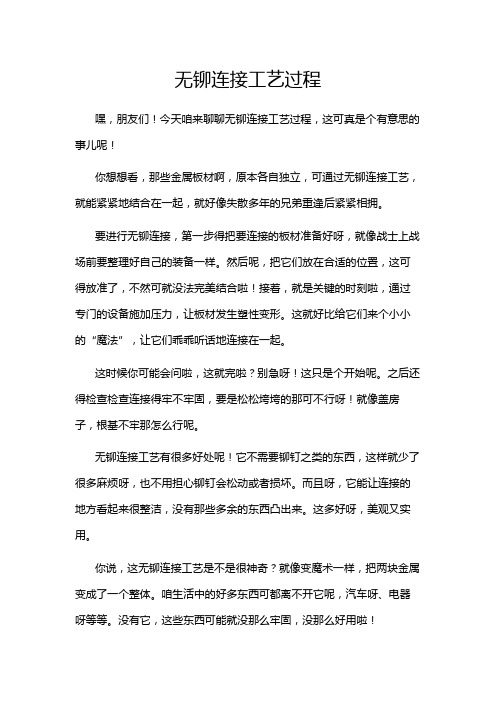
无铆连接工艺过程
嘿,朋友们!今天咱来聊聊无铆连接工艺过程,这可真是个有意思的事儿呢!
你想想看,那些金属板材啊,原本各自独立,可通过无铆连接工艺,就能紧紧地结合在一起,就好像失散多年的兄弟重逢后紧紧相拥。
要进行无铆连接,第一步得把要连接的板材准备好呀,就像战士上战场前要整理好自己的装备一样。
然后呢,把它们放在合适的位置,这可得放准了,不然可就没法完美结合啦!接着,就是关键的时刻啦,通过专门的设备施加压力,让板材发生塑性变形。
这就好比给它们来个小小的“魔法”,让它们乖乖听话地连接在一起。
这时候你可能会问啦,这就完啦?别急呀!这只是个开始呢。
之后还得检查检查连接得牢不牢固,要是松松垮垮的那可不行呀!就像盖房子,根基不牢那怎么行呢。
无铆连接工艺有很多好处呢!它不需要铆钉之类的东西,这样就少了很多麻烦呀,也不用担心铆钉会松动或者损坏。
而且呀,它能让连接的地方看起来很整洁,没有那些多余的东西凸出来。
这多好呀,美观又实用。
你说,这无铆连接工艺是不是很神奇?就像变魔术一样,把两块金属变成了一个整体。
咱生活中的好多东西可都离不开它呢,汽车呀、电器呀等等。
没有它,这些东西可能就没那么牢固,没那么好用啦!
你再想想,如果没有无铆连接工艺,那得用多少铆钉呀,多浪费材料呀,还不环保呢!所以说呀,这个工艺可真是太重要啦!
在这个科技不断进步的时代,无铆连接工艺也在不断发展和完善呢。
说不定以后会变得更加厉害,能连接更复杂的东西,让我们的生活变得更加美好。
总之呢,无铆连接工艺就是这么一个神奇又实用的东西,咱可得好好了解了解它,说不定哪天咱自己也能用上呢!你说是不是呀?
原创不易,请尊重原创,谢谢!。
无铆钉铆接机工作原理

无铆钉铆接机工作原理无铆钉连接工艺的原理:即通过使用专门的连接模具,在一个冲压过程中,利用材料自身的可塑性,在挤压处形成一个相互镶嵌的圆点或者矩形点,由此将2层或多层板件连接起来。
无铆连接技术包括铆接设备和铆接模具两大类。
1)设备分铆接专机和铆接手钳两大类a、铆接专机分为:落地型铆接设备、手持型铆接手钳、铆接单元组合模块b、铆接手钳分为:增压式手钳2)模具分圆形模具和矩形模具。
圆形模具形成圆形的连接点,外形美观,内应力均布。
主要适用于软质材料或薄型材料的连接。
矩形模具形成的矩形点连接复合了切割和变形的工艺过程。
主要适用于硬质材料或不锈钢板件的连接,板厚差异较大的组合材料。
无铆连接与传统工艺(焊接、粘胶、拉铆)相比较,具有以下优点:1)低能耗。
无铆连接不需要消耗原料和辅材,耗用的成本只有点焊的50%左右。
传统工艺成本高、耗材多。
2)价格便宜耐用,结构简单,便于维护。
跟传统设备价格差不多。
传统设备易老化,不便维护3)连接处外形美观,不需要表面处理。
焊接表面有疤痕,需要作(打磨、抛光等)表面处理。
粘胶连接是使用一种强度很高的粘胶,工件腐蚀较严重。
4)连接强度高,连接点质量可以无损伤检测。
5)无铆钉连接模具使用寿命长。
平均使用次数达10万~30万次。
6)工艺简单,不需要预先或事后处理(如冲孔、表面处理)。
7)解决了传统工艺不能对铝、镁、钛等金属材质进行连接的难题。
8)表面有镀层或漆层的工件表面不会损坏,可以对多层或有夹层的材料进行连接。
传统工艺会破坏表面镀层。
9)工作效率高,工作中没有噪音,没有烟尘污染,环境环保。
焊接工艺噪音大、有烟、火花、尘排放。
这种工艺由于低成本、操作简单、连接处质量佳,在国际市场倍受青睐。
我国已广泛应用在家电行业:(如海尔、美的、富士康、艾美特等)、汽车行业(长春一汽、上海大众、比亚迪、奇瑞等),但大多数中小型企业还未认识到,这需要我们不断努力的去推广!使无铆钉连接技术在市场迅速普及!森拓。
无铆钉铆接工艺

无铆钉铆接工艺哎呀,说起无铆钉铆接工艺,这玩意儿可真是个技术活儿。
记得有一次,我去了一家制造厂参观,他们那儿就用了这种工艺。
你可能会问,这无铆钉铆接是个啥玩意儿?别急,听我慢慢道来。
那天,我走进车间,看到工人们正在忙活。
他们手里拿着一些金属片,看起来像是什么机器的外壳。
我好奇地凑过去,只见他们把两块金属片叠在一起,然后放到一个机器下面。
那机器看起来挺复杂的,有点像是科幻电影里的那种高科技设备。
工人们告诉我,他们正在做的就是无铆钉铆接。
原来,这种工艺不需要用到铆钉,而是通过机器的压力,让两块金属片紧紧地贴合在一起。
我心想,这可比用铆钉简单多了,而且看起来还挺结实的。
他们让我看那个机器的工作原理。
机器的一端有个压力装置,当启动机器后,压力装置就会把金属片紧紧地压在一起。
我看着那两块金属片,它们在压力的作用下,慢慢地贴合,然后“啪”的一声,就紧紧地连在一起了。
我凑近一看,那接缝处平滑得就像是天生的一样,一点缝隙都没有。
工人们还告诉我,这种工艺的好处可多了。
首先,它不需要铆钉,这样就减少了材料的浪费。
其次,因为接缝处没有铆钉,所以金属片的强度反而更高。
最后,这种工艺还提高了生产效率,因为不需要一个一个地打铆钉,节省了不少时间。
我看着那些工人,他们的动作熟练而迅速,就像是在跳一支舞。
他们的眼神专注,每一个动作都那么精准。
我不禁感叹,这无铆钉铆接工艺,真是个了不起的技术。
参观结束后,我走出车间,心里还在想着那无铆钉铆接的神奇之处。
你看,这技术就像是生活中的小细节,虽然不起眼,但却能带来意想不到的效果。
就像我们生活中的点点滴滴,看似平凡,却构成了我们丰富多彩的生活。
所以,下次你看到那些精致的金属制品,不妨想想,它们背后可能就有着无铆钉铆接工艺的功劳。
这种工艺,就像生活中的小确幸,虽然不显眼,但却让人心生敬意。
无铆钉铆接的工艺研究

无铆钉铆接的工艺研究无铆钉铆接是一种常见的连接技术,适用于各种材料和各种结构形式的连接。
本文将从工艺原理、优缺点、应用领域和发展趋势等方面对无铆钉铆接进行研究。
无铆钉铆接的工艺原理主要包括:连杆的原理和材料变形原理。
在使用无铆钉铆接时,要将铆接件的两个相对位置的部件夹适当压力下进行一定的材料变形,从而使相应的塑性变形量足够大,以满足连接件的要求。
通常在操作重型铆钉时,铆钉材料由初始形状的管状件制得,或由宽松螺母或厚垫圈制得。
无铆钉铆接的优点主要有以下几个方面:1. 具有较高的强度和连接刚度,能够承受较大的载荷。
2. 简化了制造过程,降低了成本,提高了效率。
3. 可以应用于多种材料和结构形式的连接,具有比较广泛的适用性。
4. 铆接后的连接件不易发生松动和断裂,具有较高的可靠性和耐用性。
然而,无铆钉铆接也存在一些缺点:1. 铆接连接的设计和制造难度较大,需要严格控制铆接件的尺寸和材料特性。
2. 铆接过程中产生的热量容易使材料发生变形和变硬,从而影响连接质量。
3. 铆接后的连接处可能会产生较大的应力集中,如果设计不合理或制造不精确,容易导致连接失效。
无铆钉铆接广泛应用于航空航天、汽车、船舶、电子等领域的连接工艺中。
例如,飞机、汽车和船舶等航空航天和交通工具中的铆接连接通常要求具有较高的强度和可靠性,并能承受较大的载荷和冲击;而电子设备中的铆接连接则要求具有良好的导电性和散热性。
无铆钉铆接的发展趋势主要表现在以下几个方面:1. 研发更高强度和更可靠的无铆钉铆接件,以满足对连接质量和使用寿命的更高要求。
2. 进一步降低制造成本,提高生产效率,加强质量控制,确保连接质量。
3. 改进铆接工艺和设备,提高自动化程度和生产效率,减少人工操作对质量的影响。
4. 探索无铆钉铆接在新材料和新结构形式上的应用,如复合材料和3D打印技术等。
总之,无铆钉铆接是一种重要的连接技术,在多个领域都有广泛的应用和发展。
未来,随着材料科学和工艺技术的不断进步,无铆钉铆接将会得到进一步的发展和完善。
无钉铆接工艺

无钉铆接工艺无钉铆接工艺是一种常用的连接技术,用于连接两个或多个材料,特别适用于连接薄板材料。
它的优点是连接强度高、连接稳定、操作简便、成本低廉等。
无钉铆接工艺的基本原理是利用压力将铆钉穿透被连接材料,并在另一侧形成铆头,以实现材料的连接。
与传统的铆接方法相比,无钉铆接工艺无需使用钉子,因此可以避免钉子在连接过程中对材料造成的损伤。
无钉铆接工艺有多种形式,其中较常见的是压铆和冲压铆接。
压铆是通过压力将铆钉穿透被连接材料,并在另一侧形成铆头,实现连接。
冲压铆接则是在压力的作用下,将铆钉的底部冲击到被连接材料中,形成连接。
无钉铆接工艺适用于各种材料的连接,如金属材料、塑料材料和复合材料等。
在金属材料的连接中,无钉铆接工艺可以实现高强度的连接,而且不会对材料造成热影响区和变形。
在使用无钉铆接工艺进行连接时,需要注意以下几点。
首先,要选择合适的铆钉和被连接材料。
铆钉的长度和直径应根据被连接材料的厚度和类型来确定。
其次,要确保铆钉和被连接材料的表面清洁,以保证连接的质量。
此外,还需要控制好连接的压力和速度,以避免过度压力或过快速度对材料的损伤。
无钉铆接工艺在实际应用中具有广泛的用途。
在汽车制造、航空航天、电子设备和家电等领域,无钉铆接工艺被广泛应用于材料的连接。
它不仅可以提高产品的质量和可靠性,还可以减少生产成本和加工时间。
无钉铆接工艺是一种简便、高效、经济的连接技术。
它具有许多优点,适用于各种材料的连接。
在实际应用中,我们可以根据具体的需求选择合适的无钉铆接工艺,并注意控制好连接的质量和速度,以确保连接的稳定性和可靠性。
无钉铆接工艺的发展将进一步推动各个行业的发展,并为我们的生活带来更多便利。
- 1、下载文档前请自行甄别文档内容的完整性,平台不提供额外的编辑、内容补充、找答案等附加服务。
- 2、"仅部分预览"的文档,不可在线预览部分如存在完整性等问题,可反馈申请退款(可完整预览的文档不适用该条件!)。
- 3、如文档侵犯您的权益,请联系客服反馈,我们会尽快为您处理(人工客服工作时间:9:00-18:30)。
华东交通大学硕士学位论文无铆钉铆接的工艺研究姓名:陈兴茂申请学位级别:硕士专业:机械制造及其自动化指导教师:黄志超20080418无铆钉铆接的工艺研究摘要随着家电及汽车等机械行业的发展和竞争的加剧,这些领域越来越追求加工制造的自动化及高效、快捷性,家电和汽车等机械产品中有不少板料连接件,而无铆钉铆接很适合实现自动化,以提高制造的高效、快捷性,降低生产成本,降低劳动强度。
而且无铆钉铆接疲劳强度比点焊高,对于汽车等处于振动工况的机械产品是一个必备的优点。
要提高汽车的经济性,可以采用铝镁合金等轻型材料,常用的点焊难于连接,而无铆钉铆接能进行较好连接。
本文首先利用DEFORM-2D有限元软件建立无铆钉铆接有限元模型,对铆接过程进行有限元模拟,分析铆接成形过程中的五个阶段。
对模拟过程的应力应变进行了分析,结果表明应力应变主要集中在凸模下面板料及上板料嵌入下板料的镶嵌部分。
研究了铆接成形过程中的载荷-行程变化趋势。
其次对不同厚度板料的组合进行模拟,对模拟结果分析,得到影响铆接接头性能主要工艺参数:凸模和凹模形状及尺寸,被铆接的上、下板料的厚度,上、下板料的材料,被铆接板料的机械性能等;并提出制定工艺时的注意事项。
最后分析了凹模深度、凹模环形凹槽深度、凸模圆角大小、上下层板料放置顺序(包括厚度不同和材料不同)对无铆钉铆接接头性能的影响。
提出在此情况下凸模和凹模形状的设计原则,为实际设计模具提供了参考。
利用多种组合的有限元模拟结果和实验结果,对上、下板料厚度改变情况下铆接接头性能缺陷进行分析和提出解决方案,对无铆钉铆接工艺的制定具有一定的指导意义。
关键词:有限元模拟,无铆钉铆接,DEFORMSTUDY OF CLINCHING TECHNOLOGYABSTRACTWith the development and intense competition of machinery industry, such as household appliances and automotive industries.It demands to manufacture more automationally and efficiently.There are a lot of metal sheets connectors in the household electrical appliances, vehicles, and other machinery products, clinching is very suitable to achieve efficient manufacture, lower production costs, and less labor intensity. There is higher fatigue strength of clinching than the spot welding.It is a definite advantage to have the high fatigue shength for the automotive and other mechanical products that serve in the vibration condition. To improve the economics, lightweight materials such as aluminium-magnesium alloy are used in automotive industry, and the common spot welding is difficult to connect them, clinching is the better choice.Firstly, finite element model of clinching is established on DEFORM-2D software. The finite element simulation of the clinching process is carried out, and five stages of forming process of the riveting are analyzed. Distribution of stress and strain during forming process are analyzed.The results show that stress and strain are mainly concentrated on the sheet under the punch and the mosaic part that the upper sheet embedded into the bottom sheet. This paper has studied trendency of the load-stroke curve.Secondly, the specimens with different thickness sheets (upper sheet and lower sheet) are simulated, and the simulation results are analyzed. The main technology parameters which influence the performance of riveted joint are obtained, these parameters are the shape and size of punch and concave mold, the thickness of the upper sheet and bottom sheet,the material of the sheets,the mechanical properties of the riveted metal sheet,and so on. And the attention matters of the technology are proposed.Finally, the effect of the depth of the concave mold, the groove depth of the ring in the concave mold, punch fillet size and laying order of the matal sheets (different thickness and different material) that influence joint performance of clinching are analyzed. Moreover, the principles of designing punch and concave mold shape are proposed. This can provide some references for mold design.Making use of the finite element simulation results and the experiment results of the many kinds of combinations, the performance flaws and the solutions of clinching are forecasted. This can provide certain references to the practical application of clinching.Key Words:numerical simulation, clinching, DEFORM独创性声明本人郑重声明:所呈交的学位论文是我个人在导师指导下进行的研究工作及取得的研究成果。
尽我所知,除了文中特别加以标注和致谢的地方外,论文中不包含其他人已经发表和撰写的研究成果,也不包含为获得华东交通大学或其他教育机构的学位或证书所使用过的材料。
与我一同工作的同志对本研究所做的任何贡献均已在论文中作了明确的说明并表示了谢意。
本人签名_______________日期____________关于论文使用授权的说明本人完全了解华东交通大学有关保留、使用学位论文的规定,即:学校有权保留送交论文的复印件,允许论文被查阅和借阅。
学校可以公布论文的全部或部分内容,可以采用影印、缩印或其他复制手段保存论文。
保密的论文在解密后遵守此规定,本论文无保密内容。
本人签名____________导师签名__________日期___________第一章绪论1.1 引言随着机械工业的发展,对机械产品的经济性得到越来越高的关注,对机械产品的工艺性也要求可靠、高效、快捷、可实现自动化等等。
相应的机械产品如汽车中板料连接的经济性、高效和自动化等工艺性能也得到越来越高的重视。
由于当代机械产品的生产往往是大规模大批量,因为这样才能取得规模效应,才能取得较好的经济比较效益,要大批大量生产机械产品,就要实现机械化、自动化的生产,这样才能实现产品的快捷生产。
而且实现机械化、自动化能实现质量的稳定、可靠和减轻劳动强度。
板料的连接也不例外,实现机械化、自动化也很有现实及长远意义。
而且据研究表明,当整车质量减轻10%时,燃油经济性提高3.8%,加速时间减少8%,制动距离减少5%,转向力减小6%,CO排放减少4.5%,轮胎寿命提高7% [1,33]。
实现汽车的轻量化就可以大量采用轻金属,而在汽车中有大量的板料连接件,如汽车覆盖件、座椅、内饰件等,这些都可以采用铝合金或铝镁合金等材料。
点焊对于黑色金属之间的连接是可靠的,可以实现大批量生产,故现在点焊连接法广泛应用于这些黑色金属板料的连接,但对于那些铝合金或铝镁合金材料的连接是很困难的。
为了连接点焊不能或难于连接的那些轻金属材料,以及实现板料连接的快速性、自动化等,无铆钉铆接技术得到越来越多的关注。
而且无铆钉铆接可以和粘接联合使用形成高强度、高刚度的连接,无铆钉铆接还可以不破坏镀层或存在夹层的板料,不发热,不发光,铆接设备和模具可以重复使用,只要设备、模具设计和使用得当,它们可以有很高的使用寿命,特别是对于铝合金或铝镁合金等轻金属材料。
无铆钉铆接还不需要辅助材料,故工艺也很经济,没有废料、没有废渣、没有废气等产生,故还很环保。
无铆钉铆接(TOX连接)的连接强度可进行无损检测,这是无铆钉连接所独具的质量检测方法,完全适应了现代化工业对连接加工过程自动化的要求。