化肥挤压造粒技术
国外造粒技术

国外造粒技术国外造粒技术主要指的是颗粒制备技术,广泛应用于制药、食品、化工等领域,用于将粉状物料通过一系列工艺步骤转化为颗粒状的成品。
以下是一些常见的国外造粒技术:滚动造粒(Roller Compaction):利用辊式压缩机将粉末物料通过辊的挤压和研磨,形成一定大小的颗粒。
这是一种常见的制药造粒技术,有助于提高药品的流动性和可压缩性。
湿造粒(Wet Granulation):将粉末物料与一定量的液体(通常是水或有机溶剂)混合,形成湿团,然后通过造粒机或挤压机制成颗粒。
湿造粒可用于制备可溶性或可压缩的颗粒。
喷雾造粒(Spray Granulation):将液体溶液通过喷雾喷嘴喷雾成小滴,与粉末物料混合,形成颗粒。
这种方法常用于制备微胶囊、肥料和颗粒涂层等。
热熔造粒(Hot Melt Granulation):利用热熔物料形成颗粒,通常涉及加热和混合,然后通过挤压或切割形成颗粒。
这种技术常用于制备热熔药物或塑料颗粒。
冷冻干燥造粒(Freeze Granulation):利用冷冻干燥技术,在低温下冷冻物料,然后通过升温干燥形成颗粒。
这种方法通常用于制备温敏物质,如生物药物。
挤压造粒(Extrusion/Spheronization):通过挤压将湿的或干燥的粉末物料通过孔板挤压成长条形的颗粒,然后通过切割或球化形成颗粒。
旋转床造粒(Rotary Drum Granulation):利用旋转床将物料喷雾成小滴,与床内颗粒碰撞形成颗粒。
常用于化肥制造。
这些造粒技术可以根据不同的物料性质、工艺需求和最终产品的特性选择使用。
它们在提高产品质量、可流动性、溶解性等方面发挥着关键作用。
复合肥生产挤压工艺流程

复合肥生产挤压工艺流程1.预处理原料,在混合桶中加入尿素、磷酸二铵、钾肥和微量元素。
Pre-process the raw materials, adding urea, ammonium phosphate, potash fertilizer and trace elements to the mixing tank.2.搅拌混合原料,确保各种营养物质均匀分布。
Stir and mix the raw materials to ensure evendistribution of nutrients.3.加入粘结剂,以便于挤压成型。
Add binder to facilitate extrusion molding.4.将混合物送入挤压机中进行挤压成型。
Send the mixture to the extruder for extrusion molding.5.切割成合适的长度,形成颗粒状的复合肥。
Cut into appropriate lengths to form granular compound fertilizer.6.进行颗粒的再处理,使其表面光滑。
Reprocess the particles to make the surface smooth.7.对复合肥颗粒进行干燥,去除多余的水分。
Dry the compound fertilizer particles to remove excess moisture.8.进行包装,标明产品信息。
Packaging and labeling of the product.9.对成品进行质量检测,确保符合标准。
Quality testing of finished products to ensure compliance with standards.10.成品入库,等待发货。
Finished products are stored in the warehouse awaiting shipment.。
年产1万吨有机肥造粒技术方案
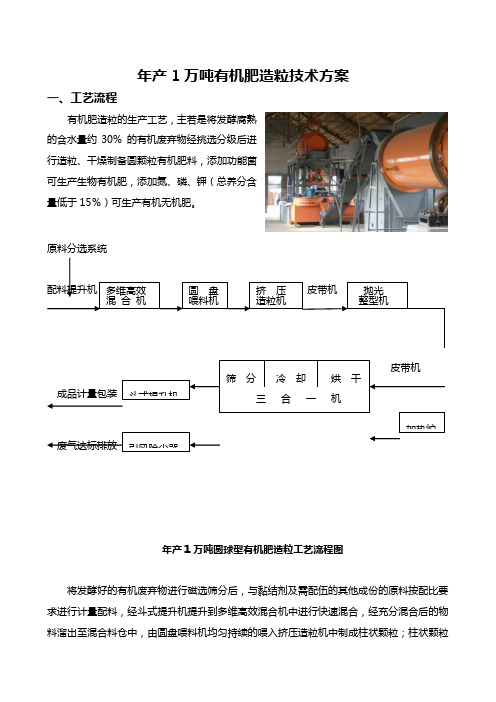
年产1万吨有机肥造粒技术方案一、工艺流程有机肥造粒的生产工艺,主若是将发酵腐熟的含水量约30% 的有机废弃物经挑选分级后进行造粒、干燥制备圆颗粒有机肥料,添加功能菌可生产生物有机肥,添加氮、磷、钾(总养分含量低于15%)可生产有机无机肥。
原料分选系统配料提升机 皮带机皮带机成品计量包装废气达标排放年产1万吨圆球型有机肥造粒工艺流程图将发酵好的有机废弃物进行磁选筛分后,与黏结剂及需配伍的其他成份的原料按配比要求进行计量配料,经斗式提升机提升到多维高效混合机中进行快速混合,经充分混合后的物料溜出至混合料仓中,由圆盘喂料机均匀持续的喂入挤压造粒机中制成柱状颗粒;柱状颗粒多维高效混 合 机 圆 盘 喂料机挤 压 造粒机抛光 整型机筛 分 冷 却 烘 干三 合 一 机加热炉斗式提升机 引风除尘器(直径和长度相等)经圆颗粒抛光整形机抛光整形成球状颗粒,由皮带机送入烘干、冷却、筛分机(三合一机型),颗粒在烘干冷却筛分机的前段进行低温大风量烘干(≤65℃),然后进入冷却段进行风冷,充分冷却后的物料进入安装在筒体尾端的筛网将粉料及大颗粒筛出,从头返回混合造粒系统;成品颗粒由提升机输送到成品料仓,经包装系统计量、包装入库。
二、工艺特点(一)、采纳挤压造粒、抛光整型新工艺可生产“圆球型”纯有机肥、有机无机肥、生物有机肥。
工艺流程短,运行费用低,生产的有机肥颗粒均匀圆整、表面滑腻、抗压强度高,流动性好,微生物菌成活率>90%,成粒率85-95%,颗粒直径-4 mm。
(二)、挤压造粒、抛光整型新工艺具有较强的原料适应性,可完全解决圆盘或转鼓等传统造粒工艺难以解决的关键性技术难题:一、经发酵后的有机物料不需进行前期烘干、粉碎处置即可直接用于造粒。
圆盘或转鼓等传统造粒工艺对原料细度要求较高,即80%以上的物料细度应达到80目以上,因此需对其进行粉碎处置,由于发酵后的有机物料含水分较高,粉碎前需对其烘干至含水分13 %以下才能知足粉碎条件,设备投资大,运行费用高。
挤压造粒生产复混肥技术方案

挤压造粒生产复混肥技术方案1、生产方法的特点及描述挤压造粒是一种较新的干法造粒生产复合肥料的工艺。
挤压造粒在肥料领域最早应用于氯化钾的造粒,由于氯化钾物理化学性质的特殊性,国外用于掺混肥料(BB肥)所需的颗粒状(1-4mm)氯化钾基本都采用挤压法生产。
近年来,挤压造粒用于生产复混肥料在国外得到了较快的发展。
挤压造粒的形式可以有对辊式和轮辗式两种,对辊式挤压是先压成大块,再破碎成颗粒,这样装置的能力大、颗粒强度高、能耗低,对辊挤压在国外使用广泛。
而轮辗式是将物料在压模盘中直接挤压成园柱条形,再切断成柱形颗粒,国内目前采用的挤压造粒方法多是轮辗造粒法,由于其生产规模小,单台机器最大只能达3-5吨/小时,且造粒强度有限、模具易损坏,生产的是园柱形颗粒,流动性差,国内发展较缓慢。
在国外已淘汰了轮辗造粒工艺。
本报告所论述的挤压造粒指对辊式挤压造粒。
对辊式挤压造粒的工艺原理是:干物料在压力作用下团聚成致密坚硬的大块(饼料),称为挤压过程;饼料再被破碎筛分后成为颗粒料称为造粒过程。
挤压的作用一是将颗粒间的空气挤掉,另外是使颗粒间距达到足够近,以产生如范德华力、吸附力、晶桥及内嵌连接等吸引力。
挤压造粒的颗粒主要是靠分子之间的作用力形成的颗粒强度。
挤压造粒生产复混肥料主要有以下的工艺特点:低能耗挤压造粒是物料在常温下进行造粒,与其它方法相比,不需要燃油、燃气等干燥措施。
生产仅需耗电和极少量的冷却水(用于辊轴冷却),每吨产品仅耗电约30kwh。
无需另外添加粘合剂国内常用的复混肥生产方法是蒸汽造粒。
水蒸汽在物料分子间凝结、结晶后,在造粒过程中起粘合剂的作用。
但在干燥过程中又必须将颗粒内部和表面的水赶出来,否则化肥在贮存过程中易粘结、结块。
而干法造粒不需另外的添加剂,只需利用物料本身的分子间力,简化了流程、降低了能耗。
投资较低由于省去了干燥过程,同时返料比低(占挤压机总进料量的35%左右),工艺流程简单,投资较低。
据IFDC(国际肥料发展中心)在1987年的曾经进行过详细的研究,证明在发展中国家,对一套新建复肥装置来说,挤压造粒在经济上要优于蒸汽造粒和化学造粒或料浆造粒。
肥料造粒方法

肥料造粒方法一、引言肥料是农业生产中必不可少的物质,它能为作物提供养分,改善土壤质量,提高农产品的产量和质量。
肥料造粒方法是将散装肥料通过一系列工艺加工成颗粒状的形式,以便于储存、运输和施用。
本文将介绍常见的肥料造粒方法,包括湿法造粒和干法造粒两种主要工艺,并对每种工艺进行详细解析。
二、湿法造粒湿法造粒是将散装肥料与添加剂混合后加入湿法造粒机中,在机器内部形成颗粒状,并通过干燥设备使其固化成型。
下面将介绍湿法造粒的几种常见方法。
1. 挤压造粒法挤压造粒法是利用挤压力将混合好的湿性原料通过模具挤压成型。
这种方法适用于有一定塑性的原料,如有机肥、复合肥等。
其步骤包括:原料混合→进料→挤出→切割→干燥→筛分→包装。
2. 滚球造粒法滚球造粒法是将混合好的原料通过滚筒机进行滚动,使其形成颗粒状。
这种方法适用于一些湿性较高的原料,如尿素、硝酸铵等。
其步骤包括:原料混合→进料→滚动→干燥→筛分→包装。
3. 喷雾造粒法喷雾造粒法是将混合好的原料通过喷雾器喷洒成小颗粒,并在空气中进行干燥和固化。
这种方法适用于一些具有良好流动性的原料,如复合肥、微生物菌剂等。
其步骤包括:原料混合→喷雾→干燥→筛分→包装。
三、干法造粒干法造粒是将散装肥料通过机械力或压力形成颗粒状,无需添加水或其他溶剂。
下面将介绍干法造粒的几种常见方法。
1. 压片造粒法压片造粒法是利用机械设备对散装肥料进行压制,使其形成颗粒状。
这种方法适用于一些具有较高硬度的原料,如复合肥、尿素等。
其步骤包括:原料混合→进料→压制→破碎→筛分→包装。
2. 旋转造粒法旋转造粒法是将散装肥料放入旋转造粒机内,通过离心力和摩擦力使其形成颗粒状。
这种方法适用于一些较小颗粒的原料,如微生物菌剂、微量元素等。
其步骤包括:原料混合→进料→旋转→干燥→筛分→包装。
3. 振动造粒法振动造粒法是通过振动设备对散装肥料进行振动和压实,使其形成颗粒状。
这种方法适用于一些具有较好流动性的原料,如微生物菌剂、有机肥等。
挤压机造粒带的生产工艺

挤压机造粒带的生产工艺
挤压机造粒带的生产工艺主要包括以下几个步骤:
1. 原料准备:选择适合造粒的原料,如聚合物树脂、颜料、添加剂等,并按照一定比例混合。
2. 制备混合料:将经过原料准备的材料送入混合设备中进行充分混合,确保各种原料均匀分散。
3. 进料预热:将混合料送入预热机中进行加热处理,使其达到适宜的温度,提高材料的塑性和流动性。
4. 挤出造粒:将预热后的混合料送入挤压机中,通过螺杆的旋转和高温下的压力,使混合料在挤出机筒中挤压和加热,形成熔体。
5. 造粒带成型:将熔融的材料经过挤压机机头的模具,在模具中的出口处通过特定形状的孔口挤出,形成具有特定形状和尺寸的条状产物,即造粒带。
6. 冷却定型:造粒带从挤出机出口后,经过冷却水槽或冷却辊进行迅速冷却,使其固化成为带状固体。
7. 剪切切割:通过特定的设备和刀具将造粒带切割成所需的长度,完成最终的
制品。
8. 包装与存储:对制成的造粒带进行包装,然后存放在干燥、防潮的环境中,以保证其质量和性能。
以上是一般挤压机造粒带的常见生产工艺流程,具体的工艺步骤和参数还需要根据不同材料和产品要求进行调整和优化。
化肥挤压造粒技术

化肥挤压造粒技术复合肥料的常规造粒工艺是采用湿法,该法需先把湿的单一原料混合,然后再干燥,能耗较高。
大部分的能量都用于干燥系统,只有一小部分用于超大颗粒的破碎和产品的运输。
对于湿法工艺,干燥过程非常关键,因为需将颗粒内部的水份干燥出来,否则水会在贮存过程中迁移到颗粒表面,产生结块。
同时,多孔状的颗粒物料在造粒过程中因重结晶而结壳,这也有碍于造粒。
因此,干燥过程十分缓慢,而且操作不便。
干粉状物料的直接挤压造粒则避免了干燥这一昂贵的过程。
因而降低了能耗和生产成本,干法造粒过程一般是:先在辊压机中将物料挤压成致密的大块,然后经常规的破碎筛分后得到产品。
筛分后的超大颗粒则循环回破碎机,不合格的小颗粒则回到挤压机中。
有时根据需要产品还经过进一步处理,如产品颗粒的圆整,用农药包裹或用缓释剂包裹,以改善缓释性能。
化肥混合物的结块性能随着以下因素而不同,即:物料的物理化学性能、混合的方法、最终产品的贮存条件。
因为破碎强度与单位体积的晶桥数量有关,它随颗粒体积增大而增加。
因此,粒状肥料与粉状肥料相比一般不易结块,如果造粒过程是通过干法(即没有液体粘合剂)时,更不易结块。
化肥的挤压/造粒工艺由其他的文章专述。
Koeppern公司制造的最大的化肥造粒设备之一,也是挤压成型造粒最先进的设备之一,辊轴的宽度达到1000 mm,直径为1000mm,有四个螺旋给料机,辊轴间的最大压力约在6800 KN,根据设计轴承寿命和辊轴速度(6000-9000 KN),辊轴转速约12转/分。
该设备能力约50-80 t/h的化肥原料,挤压的波浪形大块的厚度约为14~16 mm,当然,较小直径和宽度辊轴的辊压机,带有一个螺旋或重力给料器,及可调节的辊轴转速及板块厚度,其能力比较小。
还有更大的设备可处理100 t/h的钾肥,这些机器的设计原则基本相同,都有专利设计的、高强的、预制的框架,上有控制浮动辊轴的水力加压系统;自调整带并自动润滑的辊轴轴承;双倍输出功率的轴承减速箱;其上有浮动的齿轮、联轴节和垫片,以允许辊轴从框架上水平卸出,设备上还有计时系统,这对于成型非常重要。
挤压造粒

挤压造粒生产方法的特点及描述挤压造粒是一种较新的干法造粒生产复合肥料的工艺。
挤压造粒在肥料领域最早应用于氯化钾的造粒,由于氯化钾物理化学性质的特殊性,国外用于掺混肥料(BB肥)所需的颗粒状(1-4mm)氯化钾基本都采用挤压法生产。
近年来,挤压造粒用于生产复混肥料在国外得到了较快的发展。
挤压造粒的形式可以有对辊式和轮辗式两种,对辊式挤压是先压成大块,再破碎成颗粒,这样装置的能力大、颗粒强度高、能耗低,对辊挤压在国外使用广泛。
而轮辗式是将物料在压模盘中直接挤压成园柱条形,再切断成柱形颗粒,国内目前采用的挤压造粒方法多是轮辗造粒法,由于其生产规模小,单台机器最大只能达3-5吨/小时,且造粒强度有限、模具易损坏,生产的是园柱形颗粒,流动性差,国内发展较缓慢。
在国外已淘汰了轮辗造粒工艺。
本报告所论述的挤压造粒指对辊式挤压造粒。
对辊式挤压造粒的工艺原理是:干物料在压力作用下团聚成致密坚硬的大块(饼料),称为挤压过程饼料再被破碎筛分后成为颗粒料称为造粒过程。
挤压的作用一是将颗粒间的空气挤掉,另外是使颗粒间距达到足够近,以产生如范德华力、吸附力、晶桥及内嵌连接等吸引力。
挤压造粒的颗粒主要是靠分子之间的作用力形成的颗粒强度。
挤压造粒生产复混肥料主要有以下的工艺特点:低能耗挤压造粒是物料在常温下进行造粒,与其它方法相比,不需要燃油、燃气等干燥措施。
生产仅需耗电和极少量的冷却水(用于辊轴冷却),每吨产品仅耗电约30kwh。
无需另外添加粘合剂国内常用的复混肥生产方法是蒸汽造粒。
水蒸汽在物料分子间凝结、结晶后,在造粒过程中起粘合剂的作用。
但在干燥过程中又必须将颗粒内部和表面的水赶出来,否则化肥在贮存过程中易粘结、结块。
而干法造粒不需另外的添加剂,只需利用物料本身的分子间力,简化了流程、降低了能耗。
投资较低由于省去了干燥过程,同时返料比低(占挤压机总进料量的35%左右),工艺流程简单,投资较低。
据IFDC(国际肥料发展中心)在1987年的曾经进行过详细的研究,证明在发展中国家,对一套新建复肥装置来说,挤压造粒在经济上要优于蒸汽造粒和化学造粒或料浆造粒。
挤压造粒生产硫酸钾镁肥的生产技术
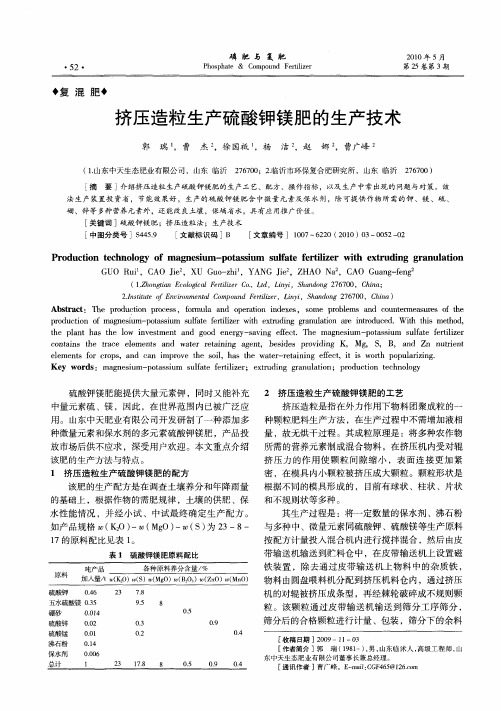
按配方计量投入混合机 内进行搅拌混合 ,然后由皮 带输 送机输 送 到贮 料仓 中 ,在 皮带 输送 机上 设置 磁
铁装 置 ,除去 通 过 皮带 输 送 机上 物 料 中的杂 质 铁 , 物料 由圆盘喂料 机分 配 到挤 压机 料仓 内 ,通 过挤 压 机 的对 辊被 挤压 成条 型 ,再 经棘 轮破 碎成 不规 则颗
对 策 :更换 箩底 或 固定 挂钩 ;及 时更 换棘 轮 轴
硫酸 钾 、硫酸 镁 、微量 元 素 、保水 剂及 填料 均 承或齿 轮 。 按配 方要求 进行 配 比。工艺 指标 为 :轧辊 转 速 ( 交 6 挤压 造粒 生产 硫 酸钾镁 肥 的特点
换 )l、2 、2 、3 / i,蓄能器 预加 压 力 5~8 6 0 4 0r mn
硼 、锌等 多种营养元素外,还能改 良土壤 ,保墒省水 ,具有应 用推广价值。
[ 关键词 ] 酸钾镁肥 ;挤 压造粒法;生产技术 硫 [ 中图分类号 ]¥ 4 . 4 59 [ 文献标识码 ] B [ 文章编号 ] 10 —6 2 2 1 0 —05 — 2 0 7 20( 0 0) 3 0 2 0
Ke r ma n su poa sum ul t friie ; x r d n g a lto y wo ds: g e i m— t s i s f e e t z r e t i g r nu ai n; p o u to tc noo y a l u r d c in e h l g
粒 。该颗粒通过皮带输送机输送到筛分工序筛分 , 筛分后的合格颗粒进行计量 、包装 ,筛分下的余料
[ 收稿 日期 ]2 0 0 9一l —0 1 3 [ 作者简介 ]郭 瑞 ( 9 1 男 , 18 一), 山东临沭人 , 高级工 程师 , 山 东中天生态肥业有 限公司董事长兼总经理。 [ 通讯作者 ]曹广峰 。E ma : G 4 5 2 . m — i C F 6 @16e l o
复肥挤压造粒技术在华南区域的应用控导

0前言现在,我国复合(混)肥料的造粒很多都是采用滚筒造粒法(包括硫酸法、喷浆法等),高含量的复合(混)肥料则用高塔造粒法,这些造粒工艺也叫湿法造粒工艺或化学造粒法。
这些造粒工艺的缺点就是能耗高,很多能量都是用在对复合(混)肥料颗粒的干燥上,在烘干和冷却过程中还产生大量的废气和粉尘,对环境造成不利影响。
挤压造粒法是一种在整个造粒生产过程中不用加水,也没有烘干冷却工序的新的生产复合(混)肥料工艺。
挤压造粒工艺法因其环保、耗能低、投入较少、占用场地小等优点,已成为复合(混)肥造粒技术的发展潮流,但在发展和推广使用过程中也遇到一些问题,也凸显出这种造粒工艺的缺点。
因挤压造粒去掉了干燥工序,所以对原料的水分要求比较严格,原料水分偏高就会造成挤压出来的颗粒强度低、容易粉化等一系列问题。
我国华南区域天气的特点是3~4月是回南天,5~9月是湿热天气,10~次年2月是比较干燥的天气。
在华南区域用挤压造粒法生产高氮、含硝态氮或加入易吸潮原料的复合(混)肥产品时,生产过程将会遇到一系列问题,甚至无法进行生产。
本文主要针对华南区域天气的特点,对挤压造粒的工艺及设备进行改进,以达到使生产顺利进行的目的。
1复合(混)肥挤压造粒法的主要工艺流程1.1简介挤压造粒系统由4个部分组成,每部分都有各自的设备(如图1所示),分别如下:①计量、混合;②挤压、破碎;③筛分、整形;④成品包装。
物料在各工序均由皮带输送来完成。
1.2主要工艺流程(1)计量、混合。
各种原材料按照配方的投料量,计量好后从投料口投入,尿素等其他颗粒较大或结块的原材料要经过投料口的粉碎机投入,各原料由输送皮带输送到混合搅拌机进行混合。
(2)挤压、破碎。
混合好后的物料由输送带输送到喂料搅拌机,搅拌机通过搅拌将物料不断地刮到挤压机进行挤压。
挤压成型的物料片进到挤压轴下部的破碎装置进行破碎。
(3)筛分、整形。
破碎成小颗粒后的物料通过输送带进入到圆筒形筛分机,粉粒和小颗粒及大颗粒通过回料皮带重新进入喂料搅拌机与新料混合再次挤压,适合的颗粒则进入成品皮带被输送到成品储料斗等待包装。
挤压造粒无烘干生产硫酸钾镁肥的工艺[发明专利]
![挤压造粒无烘干生产硫酸钾镁肥的工艺[发明专利]](https://img.taocdn.com/s3/m/7e126f42d1f34693dbef3ee1.png)
专利名称:挤压造粒无烘干生产硫酸钾镁肥的工艺专利类型:发明专利
发明人:郭瑞
申请号:CN200810016920.7
申请日:20080617
公开号:CN101298393A
公开日:
20081105
专利内容由知识产权出版社提供
摘要:本发明涉及一种挤压造粒无烘干生产硫酸钾镁肥的工艺,其特点在于:将硫酸钾、五水硫酸镁、保水剂以及中、微量元素按照46∶35∶0.6∶18.4的重量份数混合,充分均匀搅拌后,送至加料斗,然后经轧片、切碎、整粒、筛分后包装成品。
所述的中、微量元素包括:沸石粉、硼砂、硫酸锌、硫酸铜、硫酸亚铁,它们按照10-20∶1-3∶1-2.5∶0.1-1.5∶0.1-1的重量份数比混合均匀。
本发明采用挤压造粒工艺,并且添加抗旱保水促生长剂,生产的多元素硫酸钾镁保水肥产品,养分释放缓慢、肥料利用率高、缓解资源紧张,且减少土壤养分流失,保护地下水环境,安全环保。
在整个生产过程中,无水分引入,无烘干过程,减少了烘干、冷却过程中的电耗、煤耗,在生产过程中无三废污染物排放。
申请人:郭瑞
地址:276700 山东省临沭县金星集团公司家属院
国籍:CN
更多信息请下载全文后查看。
复合肥挤压工艺流程

复合肥挤压工艺流程复合肥挤压可是个挺有趣的过程呢。
一、原料准备。
这就像是做饭之前得把食材都准备好一样。
复合肥挤压得先有各种原料。
这些原料呀,那可都是经过精心挑选的。
有氮元素相关的原料,就像尿素啦,它可是给植物提供氮营养的小能手。
还有磷元素的原料,磷能让植物根系长得壮壮的。
钾元素的原料也不能少,就像氯化钾之类的,它能让植物的枝干更挺拔。
这些原料呢,要按照一定的比例混合在一起。
这个比例可是很关键的,就像是调鸡尾酒,比例不对,味道就全变了。
二、混合搅拌。
原料准备好之后就要混合搅拌啦。
把各种原料都放到一个大大的搅拌设备里。
这个搅拌设备就像一个超级大的搅拌机,一开启,里面的原料就像在开舞会一样,转呀转呀。
搅拌的目的就是要让这些原料混合得非常均匀。
如果混合不均匀,那生产出来的复合肥可就有问题啦。
有的地方营养成分多,有的地方营养成分少,植物用了这样的复合肥就像人吃饭吃不均衡一样,会长不好的。
而且搅拌的时候也不能太暴力,要是把原料都给搅得太碎了,也不行。
要刚刚好,让它们能够和谐地待在一起。
三、挤压成型。
混合均匀之后就到了挤压成型的阶段啦。
这时候会用到专门的挤压设备。
这个设备有点像一个超级大力士,把混合好的原料用力地挤压。
原料在这个设备里就像被挤牙膏一样,一点点地被挤出来。
不过这个过程可不像我们挤牙膏那么简单轻松。
挤压的力度要控制得非常好。
如果力度小了,复合肥就不能成型,可能就松松散散的。
要是力度太大了,又可能会把复合肥挤得太硬,不利于后面的使用。
在挤压的过程中,还可以根据需要调整复合肥的形状呢。
可以是圆形的颗粒,就像小珠子一样,也可以是方形的小块块,可有意思啦。
四、干燥处理。
挤压成型后的复合肥可不能就这么直接用,因为它还含有一些水分呢。
就像刚洗过澡的小宠物,得把身上的水弄干才行。
所以要进行干燥处理。
干燥的时候也有讲究的。
温度不能太高,要是太高了,可能会把复合肥里的营养成分给破坏掉。
就像烤蛋糕,温度太高,蛋糕就烤糊了。
一种肥料的挤压造粒系统
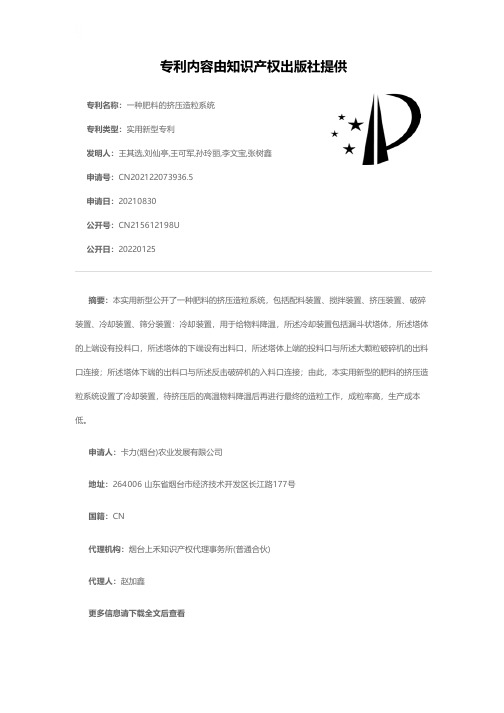
专利名称:一种肥料的挤压造粒系统
专利类型:实用新型专利
发明人:王其选,刘仙亭,王可军,孙玲丽,李文宝,张树鑫申请号:CN202122073936.5
申请日:20210830
公开号:CN215612198U
公开日:
20220125
专利内容由知识产权出版社提供
摘要:本实用新型公开了一种肥料的挤压造粒系统,包括配料装置、搅拌装置、挤压装置、破碎装置、冷却装置、筛分装置:冷却装置,用于给物料降温,所述冷却装置包括漏斗状塔体,所述塔体的上端设有投料口,所述塔体的下端设有出料口,所述塔体上端的投料口与所述大颗粒破碎机的出料口连接;所述塔体下端的出料口与所述反击破碎机的入料口连接;由此,本实用新型的肥料的挤压造粒系统设置了冷却装置,待挤压后的高温物料降温后再进行最终的造粒工作,成粒率高,生产成本低。
申请人:卡力(烟台)农业发展有限公司
地址:264006 山东省烟台市经济技术开发区长江路177号
国籍:CN
代理机构:烟台上禾知识产权代理事务所(普通合伙)
代理人:赵加鑫
更多信息请下载全文后查看。
挤压造粒肥 环评报告

挤压造粒肥环评报告挤压造粒肥环评报告一、引言挤压造粒肥是一种通过将有机废弃物挤压成粒状形成的有机肥料。
本文将对挤压造粒肥的环境影响进行评估和分析,以确保其生产和使用过程不对环境造成负面影响。
二、挤压造粒肥的生产过程挤压造粒肥的生产过程主要包括废弃物收集、挤压造粒、干燥和包装等环节。
废弃物收集阶段需要合理规划和管理,以确保废弃物来源的合法合规。
挤压造粒过程需要使用专用设备,通过挤压力将废弃物压缩成颗粒状,并添加适量的添加剂。
干燥环节主要是将造粒后的肥料进行干燥处理,以保证其质量和储存稳定性。
最后,将干燥后的肥料进行包装,以便储运和销售。
三、挤压造粒肥的环境影响1. 废弃物收集环节:在废弃物收集过程中,需要合理选择收集点和收集车辆,以减少交通拥堵和噪音污染。
同时,要避免废弃物的二次污染和恶臭扩散。
2. 挤压造粒环节:挤压造粒过程中,需要使用挤压机和添加剂。
挤压机的运行会产生噪音和震动,需要采取隔音和减震措施,以减少对周边居民的影响。
添加剂的选择应符合环保要求,不得含有有害物质。
3. 干燥环节:干燥过程中需要使用燃气或电力设备,应确保设备的排放符合环保标准,避免大气污染。
同时,要合理利用余热,减少能源浪费。
4. 包装环节:包装材料应选择可降解或可回收利用的材料,减少对环境的污染。
四、挤压造粒肥的环境风险评估1. 噪音污染:挤压机和干燥设备的运行会产生噪音,可能对周边居民和生态环境造成负面影响。
应采取隔音和减震措施,确保噪音在规定范围内。
2. 挤压机挤压过程中产生的振动可能对设备和建筑物造成损坏,需采取减震措施,确保设备和建筑物的安全稳定。
3. 废气排放:干燥过程中的燃气排放可能对大气环境造成污染。
应确保燃气设备的排放符合国家标准,并进行排气处理,减少对大气的影响。
4. 废水处理:挤压造粒过程中可能会产生废水,应建立废水处理系统,确保废水的排放符合国家标准,避免对水环境造成污染。
五、挤压造粒肥的环境保护措施1. 废弃物收集:合理选择收集点和收集车辆,加强废弃物分类和转运管理,避免二次污染和恶臭扩散。
- 1、下载文档前请自行甄别文档内容的完整性,平台不提供额外的编辑、内容补充、找答案等附加服务。
- 2、"仅部分预览"的文档,不可在线预览部分如存在完整性等问题,可反馈申请退款(可完整预览的文档不适用该条件!)。
- 3、如文档侵犯您的权益,请联系客服反馈,我们会尽快为您处理(人工客服工作时间:9:00-18:30)。
化肥挤压造粒技术
复合肥料的常规造粒工艺是采用湿法,该法需先把湿的单一原料混合,然后再干燥,能耗较高。
大部分的能量都用于干燥系统,只有一小部分用于超大颗粒的破碎和产品的运输。
对于湿法工艺,干燥过程非常关键,因为需将颗粒内部的水份干燥出来,否则水会在贮存过程中迁移到颗粒表面,产生结块。
同时,多孔状的颗粒物料在造粒过程中因重结晶而结壳,这也有碍于造粒。
因此,干燥过程十分缓慢,而且操作不便。
干粉状物料的直接挤压造粒则避免了干燥这一昂贵的过程。
因而降低了能耗和生产成本,干法造粒过程一般是:先在辊压机中将物料挤压成致密的大块,然后经常规的破碎筛分后得到产品。
筛分后的超大颗粒则循环回破碎机,不合格的小颗粒则回到挤压机中。
有时根据需要产品还经过进一步处理,如产品颗粒的圆整,用农药包裹或用缓释剂包裹,以改善缓释性能。
化肥混合物的结块性能随着以下因素而不同,即:物料的物理化学性能、混合的方法、最终产品的贮存条件。
因为破碎强度与单位体积的晶桥数量有关,它随颗粒体积增大而增加。
因此,粒状肥料与粉状肥料相比一般不易结块,如果造粒过程是通过干法(即没有液体粘合剂)时,更不易结块。
化肥的挤压/造粒工艺由其他的文章专述。
Koeppern公司制造的最大的化肥造粒设备之一,也是挤压成型造粒最先进的设备之一,辊轴的宽度达到1000 mm,直径为1000 mm,
有四个螺旋给料机,辊轴间的最大压力约在6800 KN,根据设计轴承寿命和辊轴速度(6000-9000 KN),辊轴转速约12转/分。
该设备能力约50-80 t/h的化肥原料,挤压的波浪形大块的厚度约为14~16 mm,当然,较小直径和宽度辊轴的辊压机,带有一个螺旋或重力给料器,及可调节的辊轴转速及板块厚度,其能力比较小。
还有更大的设备可处理100 t/h的钾肥,这些机器的设计原则基本相同,都有专利设计的、高强的、预制的框架,上有控制浮动辊轴的水力加压系统;自调整带并自动润滑的辊轴轴承;双倍输出功率的轴承减速箱;其上有浮动的齿轮、联轴节和垫片,以允许辊轴从框架上水平卸出,设备上还有计时系统,这对于成型非常重要。
辊轴的中心有内部齿轮和驱动轴颈,由高强度铸钢制造,压块设备(环或模块)有不同的方式与轴心结合,如带或不带有销的热烧嵌或夹紧方式。
压模通过切削、轧制、磨削、电化学洗削。
其它可选择的机器性能包括辊轴和其它关键部分的水冷、辊轴室(如粉尘)及不同操作条件的电控系统。
挤压后的物料必须破碎到一定的颗粒范围,破碎设备的性能很重要,因为一般合格产品颗粒的比例往往是决定一套装置是否成功运行的关键。
挤压物料的打片、磨碎和优化,是根据粘合后的固体物料经破碎后的要求而不同。
挤压后的大片,内部含有不同密度和强度的区域,其特性由原料决定。
有一些产品,如钾肥,其大片很快就有高强度和脆性,而其它大部分化肥,如含磷肥料和有机成分的NPK复合肥,它们产生的大片在贮存中通过化学反应发生硬化,因此,为得到较窄的颗粒分布范围和较高的产量,必须选择不同的打片方法和设备。
由于颗粒肥料在运输、贮存、施用时不能产生过多的细粉,高强度和脆性大片在破碎时,要采用较强的冲击力以破坏颗粒中较软的部分,这时可采用冲击磨。
如果挤压后的物料较软或是塑性的,需采用其它磨机,如带有沟绞的滚压机、配合或交错盘、不同形状的螺纹。
因为在打片和研磨阶段,循环回路的细粉量必须最少,颗粒形状也应尽量呈圆形或方形,所以造粒设备的选择和优化对每套化肥挤压/造粒装置是非常重要的,为了提高产量,可采用二级或更高级的造粒系统。
在辅助设备中最重要的是筛分,因为其在很大程度上决定了产品的实际产量和质量。
筛分设备必须有精确的分离效果,使筛上不留有产品颗粒,并且产品中没有超大颗粒和不合格的细粉。
为了达到些目的,一般使用多级筛,而且带有振动框架的筛则己被振动的筛所取代。
大部分挤压能量都转化为潜热,因此使许多肥料产生塑性和粘性,这些物料会粘结在筛子和运输设备上,而且使物料的流动性变差。
在装置设计时需考虑这些特性和条件,一般在理论上完全解决这些问题几乎是不可能的,所以只有通过试验装置上的测试或通过经验解决。
这也表明对每套装置的设计必须适应特定的肥料配方和当地条件。
然而,化肥挤压造粒装置的最大特点是许多参数都可以调整,这就可适应很大的原料范围。
虽然许多常规化肥装置仍在采用湿法造粒流程生产类似球形的
颗粒化肥,挤压造粒流程具有许多优势,其中重要的有:低能耗
无需液体粘合剂
可采用很宽颗粒分布范围的原料
进料组成灵活
能力适用范围广,大型或小型装置均适用
因此,该技术己越来越引起人们的兴趣,许多国家在建设新装置时,均在考虑干法挤压造粒工艺。