分解槽、沉降槽制作安装施工方案
氧化铝分级分解槽施工方案

重庆南川区先锋氧化铝三期技改工程分解槽施工方案编制人:审批人:目录一、工程概况 (2)二、编制依据 (2)三、管理目标和指标 (2)四、项目执行标准 (2)五、施工方法及技术要求 (2)六、产品在监视和测量 (9)七、施工进度计划安排 (9)八、资源需求计划 (10)九、安全和环保、文明施工技术措施 (10)一、工程概况本工程为重庆市南川氧化铝分解槽槽制作安装工程,工程量为碱液介质储槽3台,总重约900多吨,公称容积为4616m³。
二、编制依据1、《立式圆筒形储罐》JB/T4735 ;2、非标设备制作施工图;3、《焊接规程》JB4701。
三、管理目标和指标公司质量、环境、职业安全健康管理方针:以人为本,追求卓越。
1、质量管理目标、指标:本工程达到优良等级,要求单位工程一次交验合格率100%,分项工程一次交验合格率100%。
2、环境目标:防污染,节能源。
环境指标:1)固体废弃物分类管理,无雾化;2)严格对噪声源控制,噪声限值达到标准,3、该工程有关的环境因素有:有害固体废弃物;噪声污染;粉尘污染;职业安全健康目标:重安全,保健康。
4、职业安全健康指标:杜绝死亡、重伤事故,轻伤事故率不超过8‰,力争不超过5‰;杜绝火灾事故,职业病发病率为0。
四、项目执行标准【施工规范】1、《立式圆筒形储罐》JB/T4735 ;2、《焊接规程》JB4701五、施工方法及技术要求施工工序如下:施工流程:施工准备→材料检验→放样、号料→切割→卷制加工→底板、壁板、顶板预制→基础验收→底板组装、焊接→壁板的组装、焊接→顶板的组装、焊接→加热管、接管及附件安装→焊缝无损探伤检验→槽体严密性试验及充水试验→罐体几何形状和尺寸检查→罐体防腐。
1.材料1.1所用板材的性能应符合GB713—2008之规定,并具有质量证明书。
板材材质Q345R。
1.2所有的钢材,表面锈蚀麻点或刻痕的深度不得超过厚度负偏差值的一半。
钢材的实际厚度不得小于允许的最小厚度;断口处不应有分层缺陷。
沉降槽施工方案
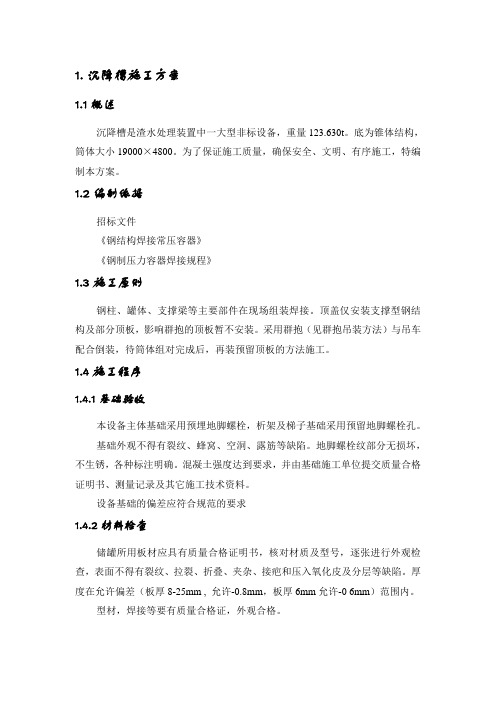
1.沉降槽施工方案1.1概述沉降槽是渣水处理装置中一大型非标设备,重量123.630t。
底为锥体结构,筒体大小19000×4800。
为了保证施工质量,确保安全、文明、有序施工,特编制本方案。
1.2编制依据招标文件《钢结构焊接常压容器》《钢制压力容器焊接规程》1.3施工原则钢柱、罐体、支撑梁等主要部件在现场组装焊接。
顶盖仅安装支撑型钢结构及部分顶板,影响群抱的顶板暂不安装。
采用群抱(见群抱吊装方法)与吊车配合倒装,待筒体组对完成后,再装预留顶板的方法施工。
1.4施工程序1.4.1基础验收本设备主体基础采用预埋地脚螺栓,析架及梯子基础采用预留地脚螺栓孔。
基础外观不得有裂纹、蜂窝、空洞、露筋等缺陷。
地脚螺栓纹部分无损坏,不生锈,各种标注明确。
混凝土强度达到要求,并由基础施工单位提交质量合格证明书、测量记录及其它施工技术资料。
设备基础的偏差应符合规范的要求1.4.2材料检查储罐所用板材应具有质量合格证明书,核对材质及型号,逐张进行外观检查,表面不得有裂纹、拉裂、折叠、夹杂、接疤和压入氧化皮及分层等缺陷。
厚度在允许偏差(板厚8-25mm , 允许-0.8mm,板厚6mm允许-0 6mm)范围内。
型材,焊接等要有质量合格证,外观合格。
1.4.3预制1.4.3.1钢板切割及坡口加工应符合下列规定1)钢板的直线切割采用半自动火焰切割机加工,弧形边缘手工切害业的应圆滑。
2)锥体、筒体采用的V 型坡口,顶盖的拼版采用的直口,在组装前都应用磨光机加工合格。
3)弧形预制件应放在胎具上,其它素材要用道木垫平,防止变形,损伤,锈蚀。
4)锥体拼版1-1-1 由于板幅的限制需拼接,拼接V 型坡口双面焊,并按10%的RT抽透,Ⅲ合格,钢板拼接后变形较大的需校正。
5)底板对接板偏差要见下图:L1-L2之差不得大于士2.5mm。
1.4.3.2预制预制应根据材料实际尺寸绘制排版图并报总承包审核。
排版图应符合下列规定:1)各圈壁的纵向焊缝宜向同一方向逐圈错开1 / 3 ,最小距离500 以上。
XX氧化铝厂沉降槽施工方案

XX氧化铝厂沉降槽施工方案第六章、主要施工方法6.1沉淀池的制作沉降槽底板,由边缘板和中幅板组成,底板制作前应根据图纸及材料情况首先绘制底板排版图,在排版时,为补偿焊接后的焊缝的收缩变形,在排版时预先留出收缩余量,底板的排版直径放大1.5―2‰。
并将焊缝以轴心对称安排,同时相邻的焊缝间距尽量大一些,底板上任意两个相邻焊接接头之间以及边缘板对接接头距底圈圆筒纵缝的距离,均不小于300mm。
底板下料采用半自动火焰切割。
按图纸要求将中板组装成长条,矫正变形,消除残余应力。
组合施工采用锤击或火焰加热锤击,边缘板按图纸在刨床上加工。
对于槽盖的制作,我们在加工厂内进行排版放样、编号、在下料时应考虑在拼装时焊缝的收缩量,放样外径应适当加大,拟考虑放大量比设计图纸尺寸大20mm,以便组装到筒体上去时两次切割拼装。
根据槽壁的设计要求,我们根据图纸的尺寸要求进行排版。
每圈板的最小高度不允许下降(如果下降,必须经设计院批准),下料高度允许大于或等于设计高度。
考虑到焊后纵向焊缝的收缩,规定每个纵向焊缝的收缩为δ8-δ14厚钢板的收缩为1.5mm。
6.1.1.1、放样1.放线从熟悉图纸开始。
首先,认真阅读技术要求和说明,逐一核对图纸之间的尺寸和方向,并根据设计部门批准的底板、槽壁和槽盖布置图放线。
2、准备好样板、样杆的材料,一般可采用薄铁皮。
3.放样所需工具:直尺、针、棉线等量具。
放线过程中如遇技术问题,及时联系技术部门解决。
4、放样结束,应对照图纸进行自检。
检查样板是否符合图纸要求,核对样板数量,并报专职检验人员进行检验。
5.根据模板编制部件材料清单。
6.1.1.2标记和划线1、号料前必须了解原材料的钢号及规格,检查原材料的质量,如有疤痕、裂缝、夹灰、厚度不足等现象,应调换材料,或取得技术部门的同意后方可使用。
2.划线材料的钢材必须平整、放置平稳,不得弯曲。
3、不同规格、不同钢号的零件应分别号料,并根据先大后小的原则依次号料。
沉降槽制作安装方案(13)

1、工程概况氧化铝工程有五台直径Φ40m的超大直径赤泥沉降槽。
沉降槽槽为圆形平底槽罐。
高度为6米和8米(其中8米高度一台,6米高度四台),槽罐材料为Q235-A,槽壁板厚在8~16mm之间,均按2mm级差排列。
沉降槽全部为焊制钢结构,由筒体、底板、顶盖、中心柱装置、搅拌耙机、搅拌传动装置这六大部分构成。
1.1沉降槽技术特性:1.2 沉降槽主要部件规格重量:2、施工部署2.1 质量目标本工程质量要求达到国家质量检验标准的优良等级,严格按照施工图纸和施工及验收规范施工,创建优质工程。
2.2 施工准备工作2.2.1 技术准备2.2.1.1 配备有关的施工规范以及标准图籍等技术资料:2.2.1.2 组织现场技术人员和职工认真学习图纸和技术资料,熟悉和掌握图纸内容、技术标准和规范及操作规程,使有关人员对本工程的质量要求和工期要求有高度的重视:2.2.1.3 参加设计交底和图纸会审,了解设计意图,掌握施工要点;2.2.1.4 组织技术人员、管理人员和职工学习施工方案,合格安排组织施工,掌握施工中的重要环节,编制作业指导书;2.2.1.5 各管理人员要认真学习合同文件,严格执行合同条款;2.2.1.6 编制施工预算,提出主要材料和辅助材料需用计划、劳动力需用计划和施工机械进场计划。
2.2.2 材料准备2.2.2.1 根据材料需用计划购置、储存、领用材料;2.2.2.2 施工用料材质检验必须符合技术规范要求,材料必须具备出厂合格证,质量保证书或试验报告。
每批钢材必须进行抽样试验,试验合格方可用于施工工程中;2.2.2.3 沉降槽所选用的钢板必须逐张进行外观检查,表面不得有裂纹、拉裂、夹渣、折痕、结疤和压入氧化皮及分层等缺陷。
检查数量按钢板总张数的20%计,且不少于两张进行抽查,发现不合格,应逐张进行检查;2.2.2.4 焊接材料(焊条、焊丝及焊剂)应具有质量合格证书,焊条质量合格证书应包括熔敷金属的化学成分和机械性能;2.2.2.5材料及半成品分门别类堆放整齐,并挂有醒目的标志牌;2.2.2.6焊接材料应放于干燥通风处,分门别类堆放,挂牌标识。
沉降槽施工方案

沉降槽制作安装施工方案1.1工程概况工艺设备专业包括标准设备安装及非标设备制作安装以及相应的工艺管道安装。
设备安装主要包括两台Φ46*7M一、二次洗涤沉降槽、两台Φ22*16M高效深锥沉降槽、一台Φ0.9*24M针形槽等五台非标设备的制作安装,共计2377吨,以及相应的粗液泵、溢流泵、底流泵、洗液泵、废酸泵等33台泵的安装;管道安装主要有粗液管、溢流管、底流管、洗液管、废酸管等工艺管道及辅助系统管道共计405吨。
1.2 Φ46X7M沉降槽制作安装施工方案1.2.1 沉降槽工程概况及工程特点1.2.1.1 工程概况沉降槽是氧化铝赤泥分离沉降分离洗涤生产的主要设备,该设备是由钢板制成的园筒状非标容器设备,直径46米,高7m,赤泥沉降分离洗涤工程共2台,每台槽约重522吨。
由于槽体直径大,所以槽壁厚度也由上至下逐层加厚,槽底为平底式拼焊结构,槽内中心安装机械搅拌装置。
全部重量由槽底下部钢筋砼基础支撑。
1.2.1.2 工程特点(即施工难度)(1)直径大:第一,槽体几何尺寸大,直径46m,高7m。
由于体形粗,给制作安装增加难度特别是吊装时容易产生变形,需要采取强化加固措施;第二,设备超粗,施工中对于主体设备的槽体预制、运输、吊装、焊接,槽上设备的吊装以及施工设备的选取上,需要认真计算、设计和采取强有力的针对性措施,以确保工程施工质量、进度和人身设备安全。
(2)槽体之间间距小,施工场地狭窄,加之工期短,需要土建基础施工与安装的配合,所以应根据实际地形对施工作业平面的布置作周密的设计,以满足沉降槽主体施工和设备、构件吊装。
1.2.2沉降槽施工方案1.2.2.1 施工顺序:根据总体方案,确定槽体构件预制、组对吊装施工程序。
(1)构件预制顺序:槽底板(按排板图)→槽壁板(由下至上)→钢梁及槽盖板→管件预制。
(2)安装顺序:基础交验→底板→壁板(由下至上)→槽内焊缝补漆→钢梁及盖板→进出料装置安装→搅拌装置安装→驱动设备安装→防腐。
浅谈沉降槽的制作与安装

浅谈沉降槽的制作与安装发表时间:2017-10-16T16:02:41.677Z 来源:《基层建设》2017年第16期作者:韦庆强[导读] 摘要:沉降槽是氧化铝生产液固分离主要设备之一。
因此沉降槽的制作与安装是实现氧化铝厂投产能否成功至关重要的一步。
本文就对沉降槽的制作与安装进行实例研究,希望为类似装置施工提供一些借鉴。
十一冶建设集团有限责任公司广西柳州 545007 摘要:沉降槽是氧化铝生产液固分离主要设备之一。
因此沉降槽的制作与安装是实现氧化铝厂投产能否成功至关重要的一步。
本文就对沉降槽的制作与安装进行实例研究,希望为类似装置施工提供一些借鉴。
关键词:沉降槽;筒体;焊接 1、工程概况云南文山800kt/a氧化铝厂一期细种子沉降工程有2台直径Φ40m的沉降槽,其槽体为圆形锥底槽罐,总高度大约14米,单台总重约900吨,槽罐材料为Q235A。
沉降槽全部为焊制钢结构,由锥底、锥底支撑、中心柱、筒体、顶盖等部分构成。
2、沉降槽制作施工工艺 2.1 制作施工方法选择根据沉降槽的结构特点、技术、质量要求,结合现有施工力量、技术装备和现场条件确定:沉降槽的所有构件均在临时施工钢结构加工厂内制作,以先进可靠的工艺设备,来保证部件的制作质量,制作完毕后倒运到安装现场进行安装。
2.2 制作工艺流程 2.3 技术措施2.3.1 底部支撑的制作底板为锥体形状,根据设计蓝图尺寸,利用展开原理进行排版展开放样(如图2),编制放样作业指导书,再进行下料;底板在排版放样时需考虑焊接收缩,故在排版时需预留焊接收缩缝的距离(每道焊缝为4~6mm),每道焊缝位置设立于辐射梁和环梁上进行排版,钢板下料采用半自动火焰切割,下料前将钢板切割区域表面的铁锈、污物等清理干净。
下料时要确保切割边的直线度和圆弧度。
2.3.2 壁板制作 2.3.2.1 壁板在焊接时很容易发生变形。
这就要求制作时尽量减少纵向焊缝(孔边距焊缝K>50mm)。
为了保证分片安装质量,对壁板制作、运输采取如下措施:A、设计合理的排版方案,编制展开作业指导书。
沉降槽施工方案

施工组织设计(方案)报审表贵州华锦铝业有限公司2×800Kt/a氧化铝工程——赤泥浆液处理沉降槽基础施工施工方案批准:审核:编制:贵州贵铝建筑物流有限公司二0一四年六月一、工程概况本工程为贵州华锦铝业有限公司2×800Kt/a氧化铝工程——赤泥浆液处理工程。
本方案主要是沉降槽基础。
本工程共有7台沉降槽基础,呈两排布置,为现浇钢筋砼基础,基础上部为沉降槽。
地基为中风化岩,地基承载力≥2300KPa,要求基底8m内无溶洞及裂隙。
每个沉降槽基础分两个部分,下部为直径27.4m~27.8m,高度1.2m的圆形砼基础承台,上部为短柱,沿圆周方向均布,内外柱各20根,中心筒短柱1个。
下部混凝土标号C30,上部混凝土为I级耐碱混凝土。
每个基础钢筋量约70吨,混凝土量800余立方米,其中下部混凝土约700立方米。
下部混凝土浇筑时,必须采取一定措施,以防早期裂缝。
二、施工准备计划1.施工准备(1)技术准备✧组织相关人员详细勘察现场,了解现场情况。
✧查阅本工程有关地质勘察报告,熟悉现场地质条件。
✧组织相关技术人员认真熟悉图纸,领会设计意图,并完成图纸会审工作。
✧编制详细的施工方案并报监理及业主审批。
✧对作业人员进行详细的技术及安全交底。
(2)施工现场准备✧根据平面布置图,清理平整现场,在永久道路位置下,压碾砂夹石,作为施工道路,路旁设明沟排水。
✧搭设现场临时工棚,并设置消防设施。
✧布置水、电管网,根据甲方指定位置,接通水、电,并安装计量仪表。
✧设置现场测量坐标控制网点,做好定位放线工作。
(3)材料机具准备✧编制工程用料计划。
钢材、砼由建设单位提供,提前落实供应指标,注明砼的品种、标号。
材料进场后要及时按规范要求进行见证取样送检。
✧钢筋到达现场后,必须分类、分批露天堆放。
堆放场地要设置支墩,以免雨水浸泡。
雨季时,还应进行覆盖。
钢筋在现场堆放、制作、安装过程中,注意避免油污。
✧施工周转材料,施工机具提前进场。
沉降槽结构吊装施工方案

(此文档为Word格式,下载后可以任意编辑修改!)(文件备案编号:)施工方案工程名称:编制单位:编制人:审核人:批准人:编制日期:年月日φ20m单层沉降槽结构吊装施工方案一、工程概况单层沉降槽φ20m,共六台,安装标高为7m。
槽底为α=15°的锥体,板厚δ=12,分成24块,与砼基础上的24根放射状[16直接相焊;槽体板厚δ=12,H=6000;槽内上、下各设有一道劈八字的∠180×14加强圈;沿槽内上口园周有B=600、H=600的压力环,全部由钢板焊成;槽外周伴有环状溜槽;槽中心φ4500×10、H=3720的进料筒,由24根Ⅰ16梁起拱支承,梁上铺δ=8钢板,组成槽顶;焊接在槽壁上的四根双Ⅰ40c组合立柱,支承着纵贯槽体的钢桁架(重11.2t),其上有传动装置及操作平台,中轴由此直插槽底口,与长、短耙相连。
沉降槽结构安装详细工程量如下表。
二、吊装方法的确立六台沉降槽因其直径硕大,无法整圈吊装,只得采用分片吊装的方法施工。
鉴于轴线以北,砼管架林立,且有13台大、小槽相邻,吊车无法开近吊装,初选了两种吊装方法以:其一,是在槽中心设一桅杆,沿360°逐块吊装,一台安装完后再拆往另一台使用;其二,借槽轴线以南宽阔的地势,平铺长达150m的轨道,设置一台塔吊吊装。
相比之下,后者较前者工作范围大,起动迅速快,可一劳多逸,避免了六立六拆桅杆的繁重工作,最重要的是能大大加快施工进度,因此确定选用臂长30m、起重量80t〃m的塔吊作为沉降槽的主吊装设备。
(塔吊组立方案由机装专业提出。
)三、施工顺序及方法1、施工顺序根据沉降槽结构特点,施工步骤分为:复测锥底→铺底板→真空试漏→装角钢圈→吊第一圈板→吊第二圈板→吊第三圈板→吊第四圈板→装立柱→装压力环→装角钢圈→装外周溜槽→进料筒→装拱梁→铺顶板→装顶部人孔→吊盖板→吊装锥底→整体注水试漏→开液流口→外壁补刷油漆。
2、施工方法2.1底板安装技术要求高,它直接影响槽壁以上结构和设备的安装精度,故必须引起重视。
16460山西某氧化铝厂分解槽制作安装施工方案

****煤业(集团)有限责任公司氧化铝厂一期40万吨氧化铝工程分解槽制作安装施工方案审批:审核:编制:****冶建设有限责任公司二00四年十月二十八日目录1 工程概况12 施工方法选择53 倒装法施工工艺53.1倒装法施工设备选择53.2 分解槽制作安装方法113.3 倒装法槽体的制作133.4安装几何尺寸检查213.5焊缝外观检查和无损探伤213.6焊后处理223.7其它构件的安装223.8 分解槽搅拌装置安装方法234、槽体试验 (25)4.1 底板真空试漏254.2盛水试验.. 255、除锈、刷油防腐266、质量保证措施276.1 质量控制点及控制措施276.2 钢结构冬季施工注意事项357、安全保证措施357.1 施工现场安全用电技术措施357.2 施工现场安全措施388、主要技术措施项目409、主要施工机械需用计划4110、劳动力需用计划4211、施工进度计划(见施工总进度计划)421 工程概况山西****煤业(集团)有限责任公司40万吨氧化铝厂项目种子分解项目分解分级系统安装工程由15台分解槽及搅拌装置、1台清洗槽以及配套的设备、工艺管道、电气、仪表等项目组成。
分解槽由槽体、搅拌装置、出料管、挡料板、进料溜槽等组成。
分解槽及清洗槽槽体为圆形平底槽罐,内径为φ14m,高度约30~36.5m,槽体材料为16MnR,槽壁板厚10~30mm,按2mm级差排列,由槽底板、筒体、顶盖等组成。
单台分解槽及清洗槽总重约242.6~384.5t。
搅拌装置,位于分解槽中心,由电机减速机、机架、搅拌轴、搅拌浆叶、轴底轴承架等部分组成,搅拌浆叶直径φ8400mm,单台重约23t。
配套设备有安装在分解槽顶部的中间降温用设备—板式换热器(单台重量为15t)、沉没泵(单台重约3t);管道过滤器规格为φ610mm,单台重量约0.398t;沉没式变速泵,单台重约3.3t;水力旋流器,单台重量约4.4t,安装在分解槽顶端钢平台上;分解槽顶还安装用于设备安装和检修的10t电动葫芦,在分解槽底的基础旁安装有用于浆料循环输送的循环泵。
三山西氧化铝六厂扩建分解槽槽体安装施工方案样本

种子分解车间分解槽槽体制安施工方案审批:审核:编制:日期:目录1 工程概况 ............................................ 错误!未定义书签。
1.1工程简介 ........................................ 错误!未定义书签。
1.2编制依据 ........................................ 错误!未定义书签。
2.施工部署 ............................................. 错误!未定义书签。
2.1质量要求 ........................................ 错误!未定义书签。
2.2 质量控制点...................................... 错误!未定义书签。
3.施工准备 ............................................. 错误!未定义书签。
4.施工方法 ............................................. 错误!未定义书签。
4.1分解槽的制作安装 ................................ 错误!未定义书签。
4.2.槽体施工方案.................................... 错误!未定义书签。
5.试车准备条件 ........................................ 错误!未定义书签。
6、质量保证措施 ....................................... 错误!未定义书签。
6.1检查制度与资料 .................................. 错误!未定义书签。
6.2 质量措施........................................ 错误!未定义书签。
分解槽槽体安装施工方案

滨州北海新材料有限公司粉煤灰综合利用项目分解槽制安工程施工方案建设单位:滨州北海新材料有限公司监理单位:河南省万安工程建设监理有限公司施工单位:中国机械工业建设集团有限公司编制人:审核人:批准人:日期:目录1.工程概况 (2)1.1工程简介 (2)1.2编制依据 (2)2.施工部署 (2)2.1质量要求 (2)2.2质量控制点 (2)3.施工准备 (3)4.施工方法 (3)4.1分解槽的制作安装 (4)4.2槽体施工方案 (6)5.量保证措施 (15)5.1检查制度和资料 (15)5.2质量措施 (15)6.保证措施 (16)7.保工期的措施 (16)8.文明施工措施 (17)9.保修服务 (17)10.主要施工机具计划 (17)11.主要施工材料计划 (19)12.劳动力计划 (19)13. 施工组织 (20)14. 施工计划………………………………………………………………一、工程概况1.1工程简介分解槽槽体制作安装工程主要是29台分解槽槽体的制作及安装。
29台分解槽槽体规格为φ14000mm,高度由31800mm—36500mm不等。
以上29台槽体均为非标制作,槽体都为圆形平底、平盖槽罐,由槽底板、筒体、顶盖、挡泥板等组成,槽体基础安装标高在+8.9米~+1.0米,单台槽体最重325T。
由于工程施工场地狭小,槽体组对受限制,采用倒装法进行施工,经济安全快捷,采用六组倒装设备同时施工。
1.2编制依据1.2.1《钢结构工程施工质量验收规范》 GB50205-20011.2.2施工蓝图 Rp101~Rp209及DBYH355等。
1.2.3《钢制焊接常压容器》 JB/T4735-19971.2.4《建筑钢结构焊接技术规程》 JGJ81-20021.2.5《现场设备、工艺管道焊接施工及验收规范》 GB50236-98二.施工部署2.1质量要求分部工程优良:分项工程合格率100%2.2质量控制点2.2.1分解槽底板制作质量控制为了确保底板的制作质量,对放样、下料、校平、拼焊、运输这几个工序进行重点的质量控制。
分解槽沉降槽制作安装方案

分解槽.沉降槽制作安装施工方案一.简况:该工程特点:1.工程量大,槽直径大.高度高,所以只能是边制作安装,分制作和安装二个场地进行施工,槽壁板,底板(底锥).顶盖等在厂内进行单片下料,刨边,卷制成形散片远至现场,组装安装;H型钢,人孔(检修孔),接管,进.出留槽,管束等在厂内组装成部件,远至现场安装.2.工期很紧,为确保工期,采用60.80吨龙门吊(自制)进行立体构件地吊装,可大大加快工程施工地进度.3.设备安装高度高,施工为高空多层立体作业所以安全工作尤为重要.二.制造.检验与验收引用标准:1.GB985—88气焊.手工电弧焊及气体保护焊缝坡口地基本形式与尺寸.2.GB986—88埋弧焊缝坡口地基本形式和尺寸.3.GB/个1804—92一般公差,线性尺寸地未注公式.4.JB4708—92钢制压力容器焊接工艺评定.5.JB/个—92钢制压力容器焊接规程.6.JB4730—94压力容器无损检测.7.JB/T4735—1997钢制焊接常压容器.8.GB50205—2001钢结构工程施工及验收规范.9.YSJ412—92轻金属冶炼机械设备安装工程及验收规范.三.施工场地布置及机械设备等配置:1.施工场地地布置:分制作和安装二个场地.(1)制作场地:宜选在安装现场附近,尽量选用闲置厂房,否则应设临时厂房,厂房面积宜为24×200=4800M2,在制作厂房内设置平台及施工所需设备.(2)安装场地:布置有60吨龙门吊行走路线,汽车运输和吊车行走路线,另需设置组装平台,安装所需设备等.2.散部件进场路线:从制作场地到安装场地,散部件地进场应选择合适地路线,需保证运输及吊车行走路线(至少3m宽)地畅通.3.机械设备,胎具地配置:(1)制作场地:(见表1)制作场地应配置制作施工所需设备;包括双梁桥吊,电焊机.卷板机.刨边机.空压机.组装平台.H型钢组装胎,船形焊接胎等.(2)安装场地:(见表2)安装场地应配置安装施工所需设备:包括60吨龙门吊(图1)性能表(见表3)坦克吊.电焊机.空压机.真空泵.组装平台等.表1.制作场地设备配置表4.其他施工临时设施配置(见表4)在安装现场还需配置空压机输气管线,遍及各槽全场;配置内外吊兰用于高空作业时,大段槽节环缝地组装和焊接;另外为避免槽段节吊装时地变形,需制作吊装横扁担作吊装具,在槽体内壁段节上,下端口加M字支撑.四.施工条件要求:1.材料(重点主材)配套到位,确保及时开工;确保制作安装工程施工进度.2.制作按三台一组配套制作,确保现场安装工程施工进度地需要.3.满足施工用电需求(制作:600KW;800KW)4.土建设备基础,按时交付使用.5.60吨龙门场地在安装前平整,铺设为轨道,龙门吊设备安装完毕;运输及吊车行走路线道路需平整好;组装平台在场地平整后铺设好.五.制作:1.工艺流程:(1)分解槽底板:下料→平整→刨边→散片出厂(2)槽壁板:下料→刨边→成形→散片出厂(3)H型钢,留槽等:下料→组装→焊接→部件出厂(4)接管.管束.人孔.检修孔等:下料→法兰加工→成形→组装→焊接→部件出厂2.方法和步骤.及技术要求(1)下料前应按钢材证明书核对并逐张(件)进行外观检查,表面不得有裂纹.拉裂.折叠.夹杂.结疤和压入氧化皮及分层等缺陷;槽壁用钢板,当厚度δ≥22mm时,应按JB4730进行超声检测,质量等级应符合Ⅲ级要求,检查数量按钢板张数地20%进行抽查,发现有不合格者,应逐张检查.(2)下料时要留出足够地焊接收缩余量及刨边余量,每圈槽壁板由多张组成,应在其中一张上加数50mm地余量.槽壁数,底板中幅板地尺寸允许偏差见表5底板弓形板地尺寸允许偏差见表6,其余按GB/个1804规定地C级要求.组装时法兰面应垂直于接管或圆筒地主轴中心线.(4)成形:槽壁板地成形采用卷板机卷制;底锥.拱顶板地成形宜用专用模具在500时油压机上冷压成形.槽壁板卷制成形应立置在平台上检查,垂直方向上用直线样板检查其间隙不得大于1mm,水平方向上用弧形样板检查其间隙不得大于4mm;拱顶板成形后用弧形后用弧形样板检查其间隙不得大于10mm.mm(5)H型钢组装与焊接:H型钢组装在组装胎上进行,翼缘板和腹板地拼接缝间缝间距应大于200mm,拼接焊接在H 型钢组装前进行,拼接后应按GB 11345进行100%超声波探伤Ⅱ级合格.H型钢焊接在船形焊接胎上进行,焊接后用H型钢矫直机进行矫正.矫正后应符合表7地规定.(6)进.出料管与支承板,挡板分2~3段组装焊接后出厂.(7)沉降槽地机装置.分解槽地搅拌装置一般外方供货.表7.焊接H型钢地允许偏差(mm)(4)补充:角钢圈采用卷板机分段卷制成形,成形后用火焰进行矫正,矫正后地每段角钢圈应用样板检查弧度间隙≤1mm,不垂直度(△C)3.关键控制点:(1)下料尺寸地控制.(2)槽壁板,角钢圆弧度成形控制.(3)焊接H型钢外形及接质量控制.(4)部件外形尺寸及焊接质量地控制.六.安装:1.安装地顺序:设备基础地复制—→底板铺设拼焊—→弓形边缘板焊缝检测—→底板焊缝真空严密性实验—→底筒段安装—→地脚螺栓埋设—→各段节筒体(包括角钢圈)安装—→接管.人孔.检修门.进.出槽地安装—→焊缝检测—→热处理—→顶盖安装—→搅拌装置安装—→盛水实验—→总检验收.2.方法.步骤及技术要求:(1)安装前,必须对基础表面尺寸进行检查,合格后方可开始安装.基础中心座标偏差不应大于20mm,标高偏差不得大于20mm.顶面水平度要求:a、环墙式基础,上表面任意10m弧长上不得超过±3.5mm,在整个圆周上以平均标高计算不超过±6.5.b、护坡式基础,上表面任意3m弧长上不应超过±3.0mm,在整个圆周上以平均标高计算不超过±12mm.(2)分解槽底板铺设前,其下表面应涂刷防腐涂料,每块底块边缘50mm范围内不刷.(3)底板采用带垫板地对接接头时,对接接头应完全焊透,表面应平整.垫板应与对接地两块底板贴紧,其间隙不得大于1mm.接头间隙为7±1mm.(4)中幅板采用搭接接头时,搭接宽度允许偏差为±5mm.(5)搭接接头三层钢板重叠部分,应将上层底板切角,切角长度应为搭接长度地2倍,其宽度应为搭接长度地2/3,在上层底板铺设前,应先焊上层底板覆盖部分地角焊接接头.(见图2)图2 底板三层钢板重叠部分地切角A:上层底板 B:A板覆盖地焊接接头 L:搭接宽度(6)槽壁板组装:1)槽壁板组装前,应对预制地壁板进行尺寸外形复验,合格后方可组装.需要校证时,应防止出现锤痕,单节筒体及大段节筒节组装在组装平台上进行,单节筒体纵缝焊接应留出一道纵缝(留50mm余量地()板)不焊待其他焊缝焊完后,用盘尺量出周长,用半自动切割多余部分后开好坡口再进行最后一道纵缝地组装焊接,以确保筒体地直径正确.2)对接地壁板组装应符合下列规定:A底圈壁板:a.相邻两壁板上口地水平允许偏差,不应大于2mm.在整个圆周上任意两点地水平允许偏差,不应大于6mm;b.壁板地铅垂度允许偏差,不应大于3mm;c.组装焊接后,在底圈板1m高处,内表面任意点半径地允许偏差±19mm.d铅垂度偏差:不应大于该圈壁板高度地0.3%.e壁板组装,内表面应平齐,错边量应符合下列规定;纵向焊接接头错边量不应大于板厚地1/10,且不应大于1.5mm.环向焊接接头错边量,不得大于板厚地1/5,且不大于3mm.G组装焊接后,焊接接头地角变形用1m长地弧形样板检查应符合表8规定.h组装焊接后,槽壁地局部凹凸变形应平缓,不地有突然起伏应符合表9规定(7)吊装分段选择:吊装时,底板,H型钢.检修门等部件采用坦克吊,主体部件采用60t龙门吊,为确保吊装安全,一般每大段重量不宜超过40t,主体部件地分段情况如下:(1)沉降槽:筒体由2—3单段节在地面平台上组装成在段,顶盖与顶盖下单节组装成大段,进行大段吊装.(2)分解槽:由于直径大,底段节槽壁板厚,分下列情况进行大段分段.a板厚δ30以上:单节筒体进行吊装.b板厚δ20—δ30:2单段节组装成大段节.c板厚δ10—δ20:2—3单段节组装成大段节.d顶盖,单体吊装.(8)进.出溜槽安装按设计标高在地面单节槽体组焊后进行,与槽体组装时,着重注意方位和倾斜度.(9)开孔接管,人孔,抢修门在相应标高筒体安装后进行,除标高和方位符合设计要求外还应符合下列要求:a.开孔接管地中心位置偏差,不地大于10 mm;接管处伸长度地允许偏差为±5 mm.b开孔补强板地曲率,应与槽体曲率一致.C法兰密封面应平整,不地有焊瘤和划痕,法兰地螺栓孔就跨中分布.(10)焊接a.焊接前应检查组装质量,清除坡口面及坡口两侧20 mm范围内地污物,并应干燥.A、焊前推荐地预热温度见表101)底板地焊接:a中幅板:先焊短焊道,后焊长焊道,初层焊道应采用分段退焊或跳焊法;b边缘板:先焊靠边缘300 mm地部分.在底板与槽壁连接地角焊接接头焊完后,且在边缘板与中幅板之间地接施焊前,应完成剩余边缘板地对接焊;c 弓形边缘板对接焊地初层焊,宜导用焊工均布,对称施焊方法.收缩接头地第一层焊接,应采用分段退焊或跳焊法.d槽底与槽壁连接地角焊接头,应在底圈壁板纵缝施焊后进行,并由数对焊工从槽内.处沿同一方向进行分段焊接.初层地焊道,应采用分段退焊或跳焊法.2)筒体槽壁地焊接,宜按下列顺序进行:a槽壁地焊接,应先焊纵向接头(地面组装平台上进行),后焊环抽接头,焊工应均匀分布,并沿同一方向施焊;b纵向接头宜自下向上焊接.(地面组装平台上进行)3)顶板地焊接a先焊内侧,后处侧.径向地长焊道,宜采用间隔焊对称施焊方法,并由中心向外分段退焊.b焊接顶板与包边角钢时,焊应对称均匀分布,并沿同一方向分段退焊.(11)焊接接头地检测:a.底板所有焊接接头应采用真空箱法进行严密性实验,实验负压值不得低于53kPa,无渗漏为合格.b.底板边缘板处端300 mm范围内,应进行射线检测.c.底板三层钢板重叠部分地搭接接头,及底边与槽壁板角焊接接头焊完后,应对其角接接头进行渗透检测或磁粉检测.d.厚度大于25 mm地各圈壁板进行100%超声波检测,环向对接接头按10%进行超声波检测.e.焊接接头地无损检测按JB4730具体要求如下:i对接焊接接头地射线检测按“焊接接头射线透照检测”规定地Ⅲ级为合格;对δ≥25mm地碳素钢和δ≥16mm地低合金钢地对接焊接接头,Ⅱ级为合格证.ii)超声检测地对接焊接接头Ⅲ为合格.iii)磁粉或渗透检测按“表面检测”规定地缺陷等级评定,其中缺陷显示累积长度按Ⅲ级为合格证.(12)热处理:在底板.筒体安装焊接完毕后,顶盖安装之前可进行槽体地热处理,槽体热处理采用爆炸退火法进行.(13)盛水实验:a.盛水实验前,与槽体焊接地所有物件及附件应全部完工,并密封好接管,人孔,检修门.b.实验前,所有与严密性实验有关地焊接接头,均不得涂刷油漆.c.实验用水应采用淡水,槽体采用碳素钢或16MnR钢板时,水温不应低于5℃.d.盛水过程中如基础发生不允许地沉降,应停止充水,待处理后方可继续进行实验.(14)槽体结束后,应对其形状和尺寸进行检查.A.安装焊接后,几何形状和尺寸,应符合下列规定:a.槽壁高度地允许偏差,不应大于设计高度地0.5%。
分解槽施工方案

目录1、工程概况及建设目标 (1)1.1 工程概况 (3)1.2 建设目标 (5)2、施工准备及部署 (6)2.1 施工组织机构设置 (7)2.2 主要施工工艺及方法安排 (8)2. 质量控制点 (8)2.3 施工准备安排 (9)3、施工方案 (12)3.1 旋挖成孔灌注桩施工方案 (12)3.2 分解槽制作安装方案 (16)3.3 泵安装施工方案 (25)3.4 工艺管道安装施工方案 (27)3.5 拟投入的主要施工机械设备表 (30)3.6、劳动力计划 (31)3.7 周转材料计划表 (32)4、质量保证措施 (32)4.1、模板工程质量保证措施 (32)4.2、钢筋工程质量保证措施 (33)4.3、砼浇筑工程质量保证措施 (34)4.4、分解槽焊接缝质量保证措施 (36)4.5、分解槽底板焊接变形控制措施 (37)4.6、分解槽筒体椭圆度和垂直度超差控制措施 (37)4.7、分解槽底板制作质量控制 (38)4.8、分解槽底板安装质量控制 (38)4.9、分解槽顶盖制作安装和搅拌装置安装质量控制 (38)4.10、设备安装质量保证措施 (39)5、工期保证措施 (39)6、安全保证措施 (42)7、工程保修服务 (48)8、施工总平面布置图 (51)1、工程概况及建设目标1.1工程概况晋中铝业铝厂分解系统分解槽土建、安装位于山西省晋中市灵石县南关镇逍遥村东方希望晋中化工有限公司厂区。
施工内容为分解系统1-10号槽、循环水及附属设备。
标段内分解槽土建和安装工程,标段包含桩基础、非标设备(金属结构)制作、安装、防腐等施工。
此工程工期要求短、质量高。
本工程的桩采用旋挖成孔灌注桩Ø800mm,桩主筋为12Φ16、焊接环筋Φ16@2000,箍筋为Φ8@100/200,桩身进入持力层最小深度为1m。
槽体直径大,加大了施工难度,给施工造成许多不便。
所以必须精心组织合理安排,要求参加施工的人员都要重视,在工作中尽职尽责,施工高峰期分两班24小时不间断作业。
分解槽、沉降槽制作安装施工方案

分解槽、沉降槽制作安装施工方案一、背景介绍在现代污水处理工程中,分解槽和沉降槽是非常重要的设备,它们在污水处理过程中起到分解悬浮物和沉淀污泥的作用。
本文将详细介绍分解槽和沉降槽的制作和安装施工方案。
二、分解槽制作安装施工方案1. 材料准备•槽体材料:选择耐腐蚀、耐压材料制作槽体,常见选项包括不锈钢、玻璃钢等。
•分解装置:根据处理对象确定合适的分解装置,确保有效分解悬浮物。
•过滤器:设置合适的过滤器,防止大颗粒物进入分解槽。
2. 制作过程1.制作槽体:根据设计要求,加工并组装好槽体。
2.安装分解装置:安装分解装置并确保其能正常运行。
3.安装过滤器:根据设计要求,安装过滤器。
3. 安装施工1.确定位置:根据设计图纸和现场实际情况确定槽体位置。
2.安装支架:安装支架并确保其牢固可靠。
3.连接管道:连接相应的进出水管道,确保管道畅通。
三、沉降槽制作安装施工方案1. 材料准备•槽体材料:选择合适的材料制作沉降槽,确保其耐腐蚀、耐压。
•沉淀装置:选择适合的沉淀装置,确保沉淀效果良好。
•排泥装置:设置排泥装置,定期清理沉淀的固体颗粒。
2. 制作过程1.制作槽体:根据设计要求,制作并组装沉降槽。
2.安装沉淀装置:安装沉淀装置并调试。
3.安装排泥装置:设置排泥装置,确保沉淀槽内清洁。
3. 安装施工1.确定位置:根据设计要求确定沉降槽位置。
2.安装支架:安装支架并确保其稳固。
3.连接管道:连接进出水管道并进行检验。
四、总结分解槽和沉降槽在污水处理工程中起着至关重要的作用。
制作和安装这两种槽体需要严格按照设计要求进行,确保其能够正常运行。
希望本文提供的制作安装施工方案能够对相关工程实践起到一定的指导作用。
沉降槽施工方案

一、工程概况宁夏宝丰能源集团有限公司废气回收综合利用项目包含有沉降槽安装这一重要施工任务。
沉降槽工作压力为常压,设计温度100℃,工作介质黑水,全容积2250m³,主要材料Q235B。
沉降槽主体在现场预制安装,安装工艺复杂,技术要求高,工程量大。
沉降槽主要由槽体、支撑梁、锥底、锥部、进液筒构成。
为保证工程顺利进行和工期及材料的合理安排,特编制此方案以指导施工。
二、编制依据2.1 NB/T47003.1-2009(JB/T4735.1)《钢制焊接常压容器》2.2 GB50236-98《现场工业管道焊接工程施工及验收规范》2.3 宁夏宝丰能源集团有限公司废气回收综合利用项目沉降槽施工蓝图2.4 JB/T4711-2003《压力容器涂敷与运输包装》2.5 JB/T4709-2000《钢制压力容器焊接规范》2.6 GB50205-2001《钢结构工程施工质量验收规范》三、施工准备3.1土建基础验收3.1.1设备安装前,基础必须办理基础移交验收,基础施工单位应向安装单位提供完备的施工资料,基础上应明显的标出标高基准点、纵横中心线。
3.1.2基础外观不得有裂纹、蜂窝、空洞、露筋等缺陷。
3.1.3基础应设有沉降观测点。
3.1.4按土建图和安装图对基础各部尺寸及位置进行复查,允许偏差值应符合表3-1规定。
表3-13.1.5基础移交时做好环境卫生,清理孔洞内杂物,地脚螺栓孔、土建预埋板等做好防护工作。
3.2沉降槽安装方法沉降槽采用正装法。
沉降槽主体分为槽体、支撑梁、平台梯子,每部分体积、重量都比较大,按照正装法可以减少吊装程序,降低焊接过程中的型变量,相对应的会增加高空作业,同时需要搭设较多脚手架。
3.3沉降槽安装前具备的条件3.3.1土建工程已结束,设备基础验收合格并办理交接手续。
3.3.2施工用水、照明、电已齐全,进入现场的道路必须畅通,满足载重、吊装车辆的通行。
3.3.3安装所需要的工机具齐全,性能良好,所需检测器具齐全,精度符合国家计量标准,并在检定周期的有效期内。
氧化铝厂沉降槽施工方案

氧化铝厂沉降槽施工方案一、项目背景最近几年,我国氧化铝产业迅速发展,越来越多的氧化铝厂投入到生产中。
沉降槽作为氧化铝生产过程中的关键设备,其施工质量直接影响到整个生产线的稳定运行。
为了确保沉降槽施工顺利进行,降低施工风险,提高施工效率,特制定本施工方案。
二、施工目标1.确保沉降槽施工质量满足设计要求,达到优良等级。
2.保证施工安全,降低安全事故风险。
3.提高施工效率,缩短施工周期。
三、施工准备1.技术准备:组织施工人员学习沉降槽施工图纸,了解沉降槽的结构、性能及施工要求,掌握施工方法。
2.物资准备:根据施工图纸,提前准备沉降槽所需的材料、设备、工具等。
3.人员准备:选拔具有丰富施工经验的工程师、技术员、施工人员组成施工队伍,明确各自职责。
四、施工方法及流程1.施工方法(1)基础施工:采用桩基施工方法,按照设计要求进行桩基施工,确保桩基承载能力满足沉降槽要求。
(2)沉降槽主体结构施工:采用现场预制施工方法,将沉降槽主体结构分为若干部分,现场拼装。
(3)沉降槽内部设备安装:在主体结构施工完成后,进行内部设备安装,包括搅拌器、电机、传感器等。
(4)沉降槽外部设备安装:在主体结构施工完成后,进行外部设备安装,包括管道、阀门、电气设备等。
2.施工流程(1)施工前期准备:完成技术、物资、人员准备工作。
(2)基础施工:按照设计要求进行桩基施工,验收合格后进行下一步施工。
(3)沉降槽主体结构施工:现场预制、拼装,验收合格后进行下一步施工。
(4)沉降槽内部设备安装:按照设计要求安装内部设备,验收合格后进行下一步施工。
(5)沉降槽外部设备安装:按照设计要求安装外部设备,验收合格后进行下一步施工。
(6)系统调试:完成沉降槽施工后,进行系统调试,确保设备运行正常。
(7)工程验收:验收合格后,交付使用。
五、施工质量控制1.严格执行施工图纸和施工规范,确保施工质量。
2.强化过程控制,对关键工序进行严格把关。
3.定期对施工人员进行质量培训,提高施工人员质量意识。
分解槽施工方案

目录1、工程概况及特点-------------------------------------------2、项目管理目标----------------------------------------------3、施工总体部署及施工准备--------------------------------4、施工技术要求-----------------------------------------------5、分解槽槽体施工方案和关键部位施工方法----------5.1临设场地------------------------------------------------5.2槽体制作-------------------------------------------------5.3槽体安装-------------------------------------------------5.4槽体焊接---------------------------------------------------5.5其他构件安装--------------------------------------------6、确保工程质量的技术组织措施--------------------------7、施工进度计划及保证工期的技术组织措施---------------8、劳动力计划安排及材料供应计划---------------------------9、主要施工设备机具计划--------------------------------------10、作业层组织机构11、主要措施材料---------------------------------------------------Ф14M种分槽制作安装施工方案一、工程概况及特点1.1工程概况:工程名称:工程地点:施工单位:承包范围:非标设备制作、安装、除锈防腐、搅拌装置等工艺设备。
分解槽施工方案

洛阳香江万基铝业有限公司三期扩容工程Φ14M分解槽制安施工方案审批单位:编制单位:中十冶香江万基项目部审批:审批:审核:审核:编制:年月日年月日目录一、工程概况及特点—————————————————3二、项目管理目标——————————————————3三、施工总体部署及施工准备—————————————4四、施工技术要求——————————————————7五、分解槽槽体施工方案和关键部位施工方法—————135.1 分解槽槽体制作————————————————13 5.2 分解槽槽体制作————————————————15 5.3 分解槽槽体焊接—————————————————225.4 其他构件的安装————————————————26六、技术组织保证措施————————————————29七、施工机具及劳动力计划——————————————34 附图:八、安全保证体系、质量保证体系九、施工总平面布置图洛阳香江万基铝业有限公司三期扩容工程Φ14M分解槽制安施工方案一、工程概况及特点1.1工程概况分解槽是氧化铝工程中的一个子项工程,由槽体、搅拌装置、进料溜槽、出料管、挡料板组成。
槽体为圆筒型平底、平盖槽,由底板、筒体、槽盖等组成。
它是将精液进行种子、降温分解从而制成氢氧化铝的过程。
分解生成氧化铝是采用高浓度大种子比的生产工艺,分解工序中主要设备为分解槽,共17台,直径为14M槽体材料均为16MnR钢板组成,最厚钢板为34mm,最薄板为10mm,单台重量在224t—240t之间,槽体总高度都在30m以上,最高一台35.5m,分解槽基础为钢筋砼承台。
1.2工程特点此工程工期要求短、质量高,加大了施工难度。
槽体安装基础高出地平面,场地较为狭窄给施工造成较多不便。
所以必须精心组织合理安排,要求参加施工的人员都要重视,在工作中尽职尽责,分两班24小时不间断作业。
二、项目管理目标2.1本工程质量要求达到国家级优良工程。
- 1、下载文档前请自行甄别文档内容的完整性,平台不提供额外的编辑、内容补充、找答案等附加服务。
- 2、"仅部分预览"的文档,不可在线预览部分如存在完整性等问题,可反馈申请退款(可完整预览的文档不适用该条件!)。
- 3、如文档侵犯您的权益,请联系客服反馈,我们会尽快为您处理(人工客服工作时间:9:00-18:30)。
分解槽、沉降槽制作安装施工方案一、概况:该工程特点:1、工程量大,槽直径大、高度高,所以只能是边制作安装,分制作和安装二个场地进行施工,槽壁板,底板(底锥)、顶盖等在厂内进行单片下料,刨边,卷制成形散片远至现场,组装安装;H型钢,人孔(检修孔),接管,进、出留槽,管束等在厂内组装成部件,远至现场安装。
2、工期很紧,为确保工期,采用60、80吨龙门吊(自制)进行立体构件的吊装,可大大加快工程施工的进度。
3、设备安装高度高,施工为高空多层立体作业所以安全工作尤为重要。
二、制造、检验与验收引用标准:1、GB985—88气焊、手工电弧焊及气体保护焊缝坡口的基本形式与尺寸。
2、GB986—88埋弧焊缝坡口的基本形式和尺寸。
3、GB/个1804—92一般公差,线性尺寸的未注公式。
4、JB4708—92钢制压力容器焊接工艺评定。
5、JB/个—92钢制压力容器焊接规程。
6、JB4730—94压力容器无损检测。
7、JB/T4735—1997钢制焊接常压容器。
8、GB50205—2001钢结构工程施工及验收规范。
9、YSJ412—92轻金属冶炼机械设备安装工程及验收规范。
三、施工场地布置及机械设备等配置:1、施工场地的布置:分制作和安装二个场地。
(1)制作场地:宜选在安装现场附近,尽量选用闲置厂房,否则应设临时厂房,厂房面积宜为24×200=4800M2,在制作厂房内设置平台及施工所需设备。
(2)安装场地:布置有60吨龙门吊行走路线,汽车运输和吊车行走路线,另需设置组装平台,安装所需设备等。
2、散部件进场路线:从制作场地到安装场地,散部件的进场应选择合适的路线,需保证运输及吊车行走路线(至少3m宽)的畅通。
3、机械设备,胎具的配置:(1)制作场地:(见表1)制作场地应配置制作施工所需设备;包括双梁桥吊,电焊机、卷板机、刨边机、空压机、组装平台、H型钢组装胎,船形焊接胎等。
(2)安装场地:(见表2)安装场地应配置安装施工所需设备:包括60吨龙门吊(图1)性能表(见表3)坦克吊、电焊机、空压机、真空泵、组装平台等。
表1、制作场地设备配置表在安装现场还需配置空压机输气管线,遍及各槽全场;配置内外吊兰用于高空作业时,大段槽节环缝的组装和焊接;另外为避免槽段节吊装时的变形,需制作吊装横扁担作吊装具,在槽体内壁段节上,下端口加米字支撑。
表4、其他施工临时设施表1、材料(重点主材)配套到位,确保及时开工;确保制作安装工程施工进度。
2、制作按三台一组配套制作,确保现场安装工程施工进度的需要。
3、满足施工用电需求(制作:600KW;800KW)4、土建设备基础,按时交付使用。
5、60吨龙门场地在安装前平整,铺设为轨道,龙门吊设备安装完毕;运输及吊车行走路线道路需平整好;组装平台在场地平整后铺设好。
五、制作:1、工艺流程:(1)分解槽底板:下料→平整→刨边→散片出厂(2)槽壁板:下料→刨边→成形→散片出厂(3)H型钢,留槽等:下料→组装→焊接→部件出厂(4)接管、管束、人孔、检修孔等:下料→法兰加工→成形→组装→焊接→部件出厂2、方法和步骤、及技术要求(1)下料前应按钢材证明书核对并逐张(件)进行外观检查,表面不得有裂纹、拉裂、折叠、夹杂、结疤和压入氧化皮及分层等缺陷;槽壁用钢板,当厚度δ≥22mm时,应按JB4730进行超声检测,质量等级应符合Ⅲ级要求,检查数量按钢板张数的20%进行抽查,发现有不合格者,应逐张检查。
(2)下料时要留出足够的焊接收缩余量及刨边余量,每圈槽壁板由多张组成,应在其中一张上加数50mm的余量。
槽壁数,底板中幅板的尺寸允许偏差见表5底板弓形板的尺寸允许偏差见表6,其余按GB/个1804规定的C级要求。
组装时法兰面应垂直于接管或圆筒的主轴中心线。
(4)成形:槽壁板的成形采用卷板机卷制;底锥、拱顶板的成形宜用专用模具在500时油压机上冷压成形。
槽壁板卷制成形应立置在平台上检查,垂直方向上用直线样板检查其间隙不得大于1mm,水平方向上用弧形样板检查其间隙不得大于4mm;拱顶板成形后用弧形后用弧形样板检查其间隙不得大于10mm。
表5 单位:mm(5)HH型钢组装在组装胎上进行,翼缘板和腹板的拼接缝间缝间距应大于200mm,拼接焊接在H 型钢组装前进行,拼接后应按GB 11345进行100%超声波探伤Ⅱ级合格。
H型钢焊接在船形焊接胎上进行,焊接后用H型钢矫直机进行矫正。
矫正后应符合表7的规定。
(6)进、出料管与支承板,挡板分2~3段组装焊接后出厂。
(7)沉降槽的机装置、分解槽的搅拌装置一般外方供货。
表7、焊接H型钢的允许偏差(mm)应用样板检查弧度间隙≤1mm,不垂直度(△C)3、关键控制点:(1)下料尺寸的控制。
(2)槽壁板,角钢圆弧度成形控制。
(3)焊接H型钢外形及接质量控制。
(4)部件外形尺寸及焊接质量的控制。
六、安装:1、安装的顺序:设备基础的复制—→底板铺设拼焊—→弓形边缘板焊缝检测—→底板焊缝真空严密性试验—→底筒段安装—→地脚螺栓埋设—→各段节筒体(包括角钢圈)安装—→接管、人孔、检修门、进、出槽的安装—→焊缝检测—→热处理—→顶盖安装—→搅拌装置安装—→盛水试验—→总检验收。
2、方法、步骤及技术要求:(1)安装前,必须对基础表面尺寸进行检查,合格后方可开始安装。
基础中心座标偏差不应大于20mm,标高偏差不得大于20mm。
顶面水平度要求:a、环墙式基础,上表面任意10m弧长上不得超过±3.5mm,在整个圆周上以平均标高计算不超过±6.5。
b、护坡式基础,上表面任意3m弧长上不应超过±3.0mm,在整个圆周上以平均标高计算不超过±12mm。
(2)分解槽底板铺设前,其下表面应涂刷防腐涂料,每块底块边缘50mm范围内不刷。
(3)底板采用带垫板的对接接头时,对接接头应完全焊透,表面应平整。
垫板应与对接的两块底板贴紧,其间隙不得大于1mm。
接头间隙为7±1mm。
(4)中幅板采用搭接接头时,搭接宽度允许偏差为±5mm。
(5)搭接接头三层钢板重叠部分,应将上层底板切角,切角长度应为搭接长度的2倍,其宽度应为搭接长度的2/3,在上层底板铺设前,应先焊上层底板覆盖部分的角焊接接头。
(见图2)图2 底板三层钢板重叠部分的切角A:上层底板 B:A板覆盖的焊接接头 L:搭接宽度(6)槽壁板组装:1)槽壁板组装前,应对预制的壁板进行尺寸外形复验,合格后方可组装。
需要校证时,应防止出现锤痕,单节筒体及大段节筒节组装在组装平台上进行,单节筒体纵缝焊接应留出一道纵缝(留50mm余量的()板)不焊待其他焊缝焊完后,用盘尺量出周长,用半自动切割多余部分后开好坡口再进行最后一道纵缝的组装焊接,以确保筒体的直径正确。
2)对接的壁板组装应符合下列规定:A底圈壁板:a、相邻两壁板上口的水平允许偏差,不应大于2mm。
在整个圆周上任意两点的水平允许偏差,不应大于6mm;b、壁板的铅垂度允许偏差,不应大于3mm;c、组装焊接后,在底圈板1m高处,内表面任意点半径的允许偏差±19mm。
d铅垂度偏差:不应大于该圈壁板高度的0.3%。
e壁板组装,内表面应平齐,错边量应符合下列规定;纵向焊接接头错边量不应大于板厚的1/10,且不应大于1.5mm。
环向焊接接头错边量,不得大于板厚的1/5,且不大于3mm。
G组装焊接后,焊接接头的角变形用1m长的弧形样板检查应符合表8规定。
h组装焊接后,槽壁的局部凹凸变形应平缓,不的有突然起伏应符合表9规定。
吊装时,底板,H型钢、检修门等部件采用坦克吊,主体部件采用60t龙门吊,为确保吊装安全,一般每大段重量不宜超过40t,主体部件的分段情况如下:(1)沉降槽:筒体由2—3单段节在地面平台上组装成在段,顶盖与顶盖下单节组装成大段,进行大段吊装。
(2)分解槽:由于直径大,底段节槽壁板厚,分下列情况进行大段分段。
a板厚δ30以上:单节筒体进行吊装。
b板厚δ20—δ30:2单段节组装成大段节。
c板厚δ10—δ20:2—3单段节组装成大段节。
d顶盖,单体吊装。
(8)进、出溜槽安装按设计标高在地面单节槽体组焊后进行,与槽体组装时,着重注意方位和倾斜度。
(9)开孔接管,人孔,抢修门在相应标高筒体安装后进行,除标高和方位符合设计要求外还应符合下列要求:a、开孔接管的中心位置偏差,不的大于10 mm;接管处伸长度的允许偏差为±5 mm。
b开孔补强板的曲率,应与槽体曲率一致。
C法兰密封面应平整,不的有焊瘤和划痕,法兰的螺栓孔就跨中分布。
(10)焊接a、焊接前应检查组装质量,清除坡口面及坡口两侧20 mm范围内的污物,并应干燥。
A、焊前推荐的预热温度见表10表101)底板的焊接:a中幅板:先焊短焊道,后焊长焊道,初层焊道应采用分段退焊或跳焊法;b边缘板:先焊靠边缘300 mm的部分。
在底板与槽壁连接的角焊接接头焊完后,且在边缘板与中幅板之间的接施焊前,应完成剩余边缘板的对接焊;c 弓形边缘板对接焊的初层焊,宜导用焊工均布,对称施焊方法。
收缩接头的第一层焊接,应采用分段退焊或跳焊法。
d槽底与槽壁连接的角焊接头,应在底圈壁板纵缝施焊后进行,并由数对焊工从槽内、处沿同一方向进行分段焊接。
初层的焊道,应采用分段退焊或跳焊法。
2)筒体槽壁的焊接,宜按下列顺序进行:a槽壁的焊接,应先焊纵向接头(地面组装平台上进行),后焊环抽接头,焊工应均匀分布,并沿同一方向施焊;b纵向接头宜自下向上焊接。
(地面组装平台上进行)3)顶板的焊接a先焊内侧,后处侧。
径向的长焊道,宜采用间隔焊对称施焊方法,并由中心向外分段退焊。
b焊接顶板与包边角钢时,焊应对称均匀分布,并沿同一方向分段退焊。
(11)焊接接头的检测:a、底板所有焊接接头应采用真空箱法进行严密性试验,试验负压值不得低于53kPa,无渗漏为合格。
b、底板边缘板处端300 mm范围内,应进行射线检测。
c、底板三层钢板重叠部分的搭接接头,及底边与槽壁板角焊接接头焊完后,应对其角接接头进行渗透检测或磁粉检测。
d、厚度大于25 mm的各圈壁板进行100%超声波检测,环向对接接头按10%进行超声波检测。
e、焊接接头的无损检测按JB4730具体要求如下:i对接焊接接头的射线检测按“焊接接头射线透照检测”规定的Ⅲ级为合格;对δ≥25mm的碳素钢和δ≥16mm的低合金钢的对接焊接接头,Ⅱ级为合格证。
ii)超声检测的对接焊接接头Ⅲ为合格。
iii)磁粉或渗透检测按“表面检测”规定的缺陷等级评定,其中缺陷显示累积长度按Ⅲ级为合格证。
(12)热处理:在底板、筒体安装焊接完毕后,顶盖安装之前可进行槽体的热处理,槽体热处理采用爆炸退火法进行。
(13)盛水试验:a、盛水试验前,与槽体焊接的所有物件及附件应全部完工,并密封好接管,人孔,检修门。