设备完好率、设备利用率、设备故障率、设备开动率、OEE、MTTR,MTTF,MTBF
企业常用12个设备管理指标计算方法

企业常用12个设备管理指标计算方法企业常用12个设备管理指标计算方法1.可动率:设备可动率有多种计算方法,一般倾向于在工作时间内,设备开动时间与应开动时间的比值的计算方法。
也就是说,要想使机器设备运转的时候,能够达到运转状态的比值。
高可动率是精益生产中流程化生产的基本要求之一。
可动率低意味着设备的稳定性差,易发生故障。
为保证高效率、高品质,流程化与连续性,必须做好设备TPM,使设备始终处于良好状态。
2.利用率:设备利用率是指每年设备实际使用时间占计划用时的百分比,是指设备的使用效率,是反映设备工作状态及生产效率的技术经济指标。
设备利用率=每小时实际产量/每小时理论产量设备利用率=每班次(天)实际开机时数/每班次(天)应开机时数×100%设备利用率=某抽样时刻的开机台数/设备总台数×100%3.设备完好率:指企业中技术性能完好设备台数占全部设备台数的比重。
企业在实际使用中,可以只计算比较重要的设备,是反映企业设备技术状况和评价设备管理工作水平的一个重要指标。
设备完好率=完好设备总台数/全部设备的台数×100%4.MTBF:即平均故障间隔时间或称为平均无故障工作时间,它是表示设备信赖性的指标,MTBF越长表示可靠性越高。
MTBF=总运转时数/故障停机次数5.MTTR:即平均修理时间,表示设备保养性的指标,MTTR越短表示易恢复性越好,同时也体现出维修队伍的能力与水平,它包括确认失效发生所必须的时间以及维护所需要的时间。
MTTR=总停机时间/故障停机次数6.维修费用率:维修费用率是同期内企业的全部维修费用占总生产费用的百分率,是反映维修效率的经济型指标。
维修费用率=全部维修费用/总生产费用×100%7.万元产值维修费:为更直接地反映企业维修的效果和扩大可比性,往往用万元产值的维修费用含量作为考核指标。
万元产值维修费=维修费用总额/以万元计的总产值8.设备故障率:指在一段时间内(年或月)设备的故障停机时间与此期间内的计划开机时间的百分比。
设备管理的11个指标

设备管理的11个指标在企业里,用于度量设备管理好坏的指标很多。
例如设备的完好率,设备的可用率,设备综合效率,设备完全有效生产率,设备故障率,平均故障间隔期,平均修理时间,设备备件库存周转率,备件资金率,维修费用率,检修质量一次合格率,返修率等等。
不同的指标用于度量不同的管理方向。
一、设备管理的指标评价1、设备的完好率在这些指标里用得最多,但其对管理的促进作用有限。
所谓的完好率,是在检查期间,完好设备与设备总台数的比例(设备完好率=完好设备数/设备总数)很多工厂的指标可以达到95%以上。
理由很简单,在检查的那一刻,如果设备是运转的,没出故障,就算是完好的,于是这个指标就很好看。
很好看就意味着没有多少可提升的空间了,就意味着没有什么可改善的了,也就意味着很难进步了。
为此,不少企业提出对此指标的定义进行改造,例如提出每月8日,18日,28日检查三次,取其完好率的平均值作为本月的完好率。
这当然比检查一次要好,但仍然是点状反映出的完好率。
后来有人提出以完好的台时数比上日历工作台时数,完好台时数等于日历工作台时减去故障及其修理的总台时数。
这个指标要真实多。
当然又遇到统计的工作量增加和统计的真实性,遇到预防性维修台时是否扣除的争论。
完好率这一指标是否有效反映设备管理状况,这要看如何应用,仁者见仁,智者见智。
2、设备的故障率这个指标容易混淆,存在两种定义:(1)如果是故障频率则是故障次数与设备实际开动台时的比值(故障频率=故障停机次数/设备实际开动台数);(2)如果是故障停机率,则是故障停机台时与设备实际开动台时加上故障停机台时的比值(故障停机率=故障停机台时/(设备实际开动台时+故障停机台时))显然,故障停机率比较能够真实的反映设备状态。
3、设备的可用率在西方国家采用较多,而在我国有计划时间利用率(计划时间利用率=实际工作时间/计划工作时间)和日历时间利用率(日历时间利用率=实际工作时间/日历时间)两个不同提法。
衡量设备运行状态的几个主要技术经济指标

衡量设备运行状态的几个主要技术经济指标市场经济化的企业生产是以追求经济效益为主要目的的,所谓企业经济效益,就是以尽可能少的劳动消耗,尽可能少的投入来生产出尽可能多的产品,来获得尽可能大的收益,以满足企业生存和社会发展需要。
企业的任何活动都离不开这个主题。
工业企业的生产经营是个复杂性的统一体。
企业效益的好坏也与生产中的各个因素息息相关。
设备是企业的主要技术装备,设备的构成、使用维护的技术经济效果、运行状态的好坏直接影响产品成本、产品质量和企业的竞争力。
因此,衡量设备的运行情况,考核和分析设备管理的相关经济技术指标。
对提高工业企业的经济效益有着十分重要的意义。
下面介绍几个主要设备管理的技术经济指标。
1.设备完好率设备完好率,指的是完好的生产设备在全部生产设备中的比重,它是反映企业设备技术状况和评价设备管理工作水平的一个重要指标。
2.设备可利用率设备可利用率又称有效利用率,它主要反映生产设备在数量、时间、能力等方面的利用程度。
一般包括实有设备安装率、已安装设备利用率、设备制度台时利用率、设备计划台时利用率、设备负荷率和设备综合利用率等指标。
由上面指标计算式可以看出,要提高设备综合利用率,设备实际开动台时数和设备的实际生产量是企业要提高的两个重要参数。
而这两参数的大小又是与设备在运行过程中实际状态相关联的,它直接取决于工业企业在生产过程中对设备维护管理水平的高低。
3.设备大修完成指标大修的指标主要反映企业的生产管理与维修技术水平。
通过与历年的情况对比,有助于企业改进管理,提高经济效益。
4.设备事故率设备事故率又称为设备事故频率,它是反映某一部门发生设备事故频繁程度的一个指标。
5.设备新度它主要反映设备在提取折旧后的新旧程度。
设备管理的11个指标

设备管理的11个指标在企业里,用于度量设备管理好坏的指标很多。
例如设备的完好率,设备的可用率,设备综合效率,设备完全有效生产率,设备故障率,平均故障间隔期,平均修理时间,设备备件库存周转率,备件资金率,维修费用率,检修质量一次合格率,返修率等等。
不同的指标用于度量不同的管理方向。
设备的完好率在这些指标里用得最多,但其对管理的促进作用有限。
所谓的完好率,是在检查期间,完好设备与设备总台数的比例(设备完好率=完好设备数/设备总数)很多工厂的指标可以达到95%以上。
理由很简单,在检查的那一刻,如果设备是运转的,没出故障,就算是完好的,于是这个指标就很好看。
很好看就意味着没有多少可提升的空间了,就意味着没有什么可改善的了,也就意味着很难进步了。
为此,不少企业提出对此指标的定义进行改造,例如提出每月8日,18日,28日检查三次,取其完好率的平均值作为本月的完好率。
这当然比检查一次要好,但仍然是点状反映出的完好率。
后来有人提出以完好的台时数比上日历工作台时数,完好台时数等于日历工作台时减去故障及其修理的总台时数。
这个指标要真实多。
当然又遇到统计的工作量增加和统计的真实性,遇到预防性维修台时是否扣除的争论。
完好率这一指标是否有效反映设备管理状况,这要看如何应用,仁者见仁,智者见智。
设备的故障率这个指标容易混淆,存在两种定义:1.如果是故障频率则是故障次数与设备实际开动台时的比值(故障频率=故障停机次数/设备实际开动台数);2.如果是故障停机率,则是故障停机台时与设备实际开动台时加上故障停机台时的比值(故障停机率=故障停机台时/(设备实际开动台时+故障停机台时))显然,故障停机率比较能够真实的反映设备状态。
设备的可用率设备可用率在西方国家采用较多,而在我国有计划时间利用率(计划时间利用率=实际工作时间/计划工作时间)和日历时间利用率(日历时间利用率=实际工作时间/日历时间)两个不同提法。
按照定义,西方定义的可用率实际上是日历时间利用率。
设备管理统计数据公式
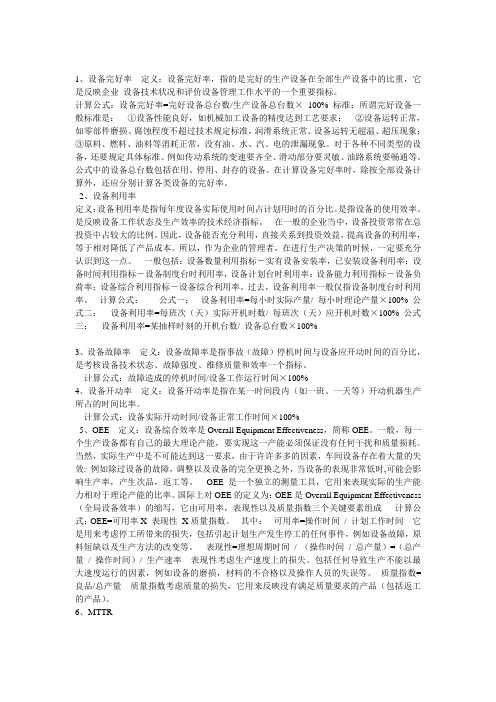
1、设备完好率定义:设备完好率,指的是完好的生产设备在全部生产设备中的比重,它是反映企业设备技术状况和评价设备管理工作水平的一个重要指标。
计算公式:设备完好率=完好设备总台数/生产设备总台数×100% 标准:所谓完好设备一般标准是:①设备性能良好,如机械加工设备的精度达到工艺要求;②设备运转正常,如零部件磨损、腐蚀程度不超过技术规定标准,润滑系统正常、设备运转无超温、超压现象;③原料、燃料、油料等消耗正常,没有油、水、汽、电的泄漏现象。
对于各种不同类型的设备,还要规定具体标准。
例如传动系统的变速要齐全、滑动部分要灵敏、油路系统要畅通等。
公式中的设备总台数包括在用、停用、封存的设备。
在计算设备完好率时,除按全部设备计算外,还应分别计算各类设备的完好率。
2、设备利用率定义:设备利用率是指每年度设备实际使用时间占计划用时的百分比。
是指设备的使用效率。
是反映设备工作状态及生产效率的技术经济指标。
在一般的企业当中,设备投资常常在总投资中占较大的比例。
因此,设备能否充分利用,直接关系到投资效益,提高设备的利用率,等于相对降低了产品成本。
所以,作为企业的管理者,在进行生产决策的时候,一定要充分认识到这一点。
一般包括:设备数量利用指标―实有设备安装率,已安装设备利用率;设备时间利用指标―设备制度台时利用率,设备计划台时利用率;设备能力利用指标―设备负荷率;设备综合利用指标―设备综合利用率。
过去,设备利用率一般仅指设备制度台时利用率。
计算公式:公式一:设备利用率=每小时实际产量/ 每小时理论产量×100% 公式二:设备利用率=每班次(天)实际开机时数/ 每班次(天)应开机时数×100% 公式三:设备利用率=某抽样时刻的开机台数/ 设备总台数×100%3、设备故障率定义:设备故障率是指事故(故障)停机时间与设备应开动时间的百分比,是考核设备技术状态、故障强度、维修质量和效率一个指标。
设备考核指标定义
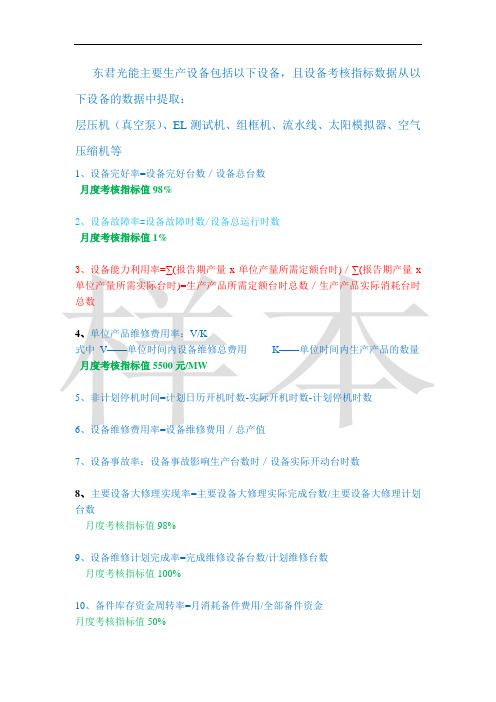
东君光能主要生产设备包括以下设备,且设备考核指标数据从以下设备的数据中提取:
层压机(真空泵)、EL测试机、组框机、流水线、太阳模拟器、空气压缩机等
1、设备完好率=设备完好台数/设备总台数
月度考核指标值98%
2、设备故障率=设备故障时数/设备总运行时数
月度考核指标值1%
3、设备能力利用率=∑(报告期产量x单位产量所需定额台时)/∑(报告期产量x 单位产量所需实际台时)=生产产品所需定额台时总数/生产产品实际消耗台时总数
4、单位产品维修费用率:V/K
式中V——单位时间内设备维修总费用 K——单位时间内生产产品的数量月度考核指标值5500元/MW
5、非计划停机时间=计划日历开机时数-实际开机时数-计划停机时数
6、设备维修费用率=设备维修费用/总产值
7、设备事故率:设备事故影响生产台数时/设备实际开动台时数
8、主要设备大修理实现率=主要设备大修理实际完成台数/主要设备大修理计划台数
月度考核指标值98%
9、设备维修计划完成率=完成维修设备台数/计划维修台数
月度考核指标值100%
10、备件库存资金周转率=月消耗备件费用/全部备件资金
月度考核指标值50%。
度量设备管理好坏的六个评价指标
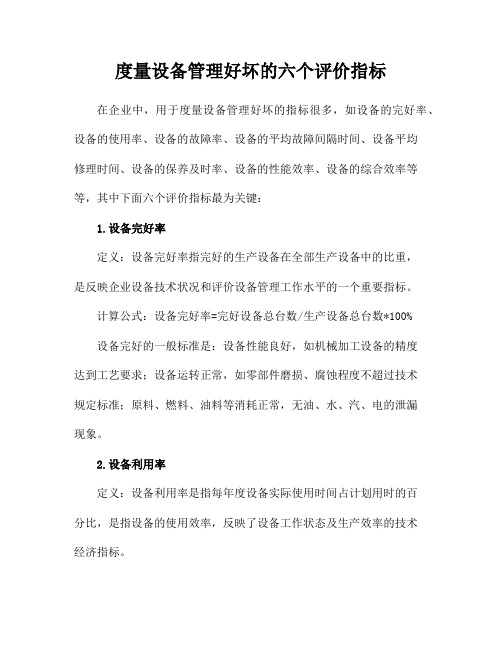
度量设备管理好坏的六个评价指标在企业中,用于度量设备管理好坏的指标很多,如设备的完好率、设备的使用率、设备的故障率、设备的平均故障间隔时间、设备平均修理时间、设备的保养及时率、设备的性能效率、设备的综合效率等等,其中下面六个评价指标最为关键:1.设备完好率定义:设备完好率指完好的生产设备在全部生产设备中的比重,是反映企业设备技术状况和评价设备管理工作水平的一个重要指标。
计算公式:设备完好率=完好设备总台数/生产设备总台数*100%设备完好的一般标准是:设备性能良好,如机械加工设备的精度达到工艺要求;设备运转正常,如零部件磨损、腐蚀程度不超过技术规定标准;原料、燃料、油料等消耗正常,无油、水、汽、电的泄漏现象。
2.设备利用率定义:设备利用率是指每年度设备实际使用时间占计划用时的百分比,是指设备的使用效率,反映了设备工作状态及生产效率的技术经济指标。
计算公式一:设备利用率=每小时实际产量/每小时理论产量*100% 计算公式二:设备利用率=(每班次(天)实际开机时数 )/每班次(天)应开机时数*100%计算公式三:设备利用率=某抽样时刻的开机台数/设备总台数*100%进行设备利用率的统计可依据生产报表分析进行,也可以采取实际统计的办法。
对于时产量固定的或产量容易计算的,可采用公式一;对于产量可变或设备较小的,可采用公式二、公式三。
3.设备平均故障间隔时间(MTBF)定义:设备平均故障间隔时间,英文全称Mean Time BetweenFailure,缩写为MTBF,是指可修复产品两次相邻故障之间的评价时间,是衡量产品的可靠性指标。
计算公式:MTBF=(∑▒〖(downtime-uptime)〗)/(failure times)对于一个简单的可维护的设备,MTBF = MTTF + MTTR。
因为MTTR通常远小于MTTF,所以MTBF近似等于MTTF,通常由MTTF替代。
MTBF用于可维护性和不可维护的系统。
设备管理的量化指标
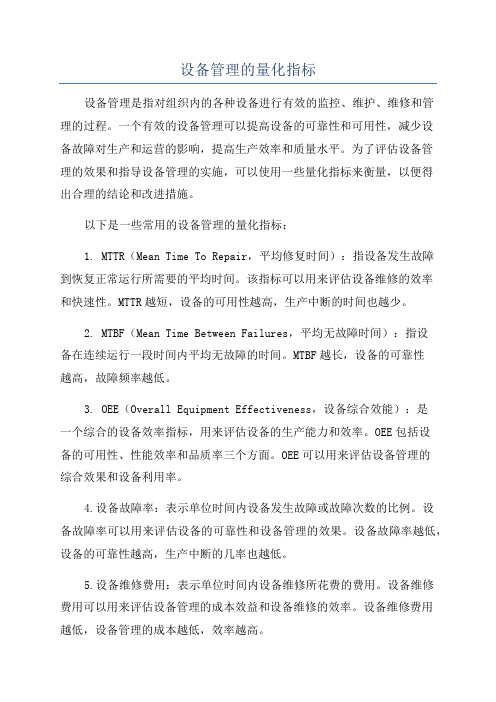
设备管理的量化指标设备管理是指对组织内的各种设备进行有效的监控、维护、维修和管理的过程。
一个有效的设备管理可以提高设备的可靠性和可用性,减少设备故障对生产和运营的影响,提高生产效率和质量水平。
为了评估设备管理的效果和指导设备管理的实施,可以使用一些量化指标来衡量,以便得出合理的结论和改进措施。
以下是一些常用的设备管理的量化指标:1. MTTR(Mean Time To Repair,平均修复时间):指设备发生故障到恢复正常运行所需要的平均时间。
该指标可以用来评估设备维修的效率和快速性。
MTTR越短,设备的可用性越高,生产中断的时间也越少。
2. MTBF(Mean Time Between Failures,平均无故障时间):指设备在连续运行一段时间内平均无故障的时间。
MTBF越长,设备的可靠性越高,故障频率越低。
3. OEE(Overall Equipment Effectiveness,设备综合效能):是一个综合的设备效率指标,用来评估设备的生产能力和效率。
OEE包括设备的可用性、性能效率和品质率三个方面。
OEE可以用来评估设备管理的综合效果和设备利用率。
4.设备故障率:表示单位时间内设备发生故障或故障次数的比例。
设备故障率可以用来评估设备的可靠性和设备管理的效果。
设备故障率越低,设备的可靠性越高,生产中断的几率也越低。
5.设备维修费用:表示单位时间内设备维修所花费的费用。
设备维修费用可以用来评估设备管理的成本效益和设备维修的效率。
设备维修费用越低,设备管理的成本越低,效率越高。
6.设备使用率:表示设备在单位时间内的利用率,即设备的运行时间与总时间的比率。
设备使用率可以用来评估设备管理的效果和生产计划的合理性。
设备使用率越高,设备的利用效率越高,生产能力也越大。
7.维修时间比例:表示设备维修所占的时间比例,即设备维修时间与总时间的比率。
维修时间比例可以用来评估设备管理的效果和设备维修的效率。
维修时间比例越低,设备的可用性越高,生产效率也越高。
- 1、下载文档前请自行甄别文档内容的完整性,平台不提供额外的编辑、内容补充、找答案等附加服务。
- 2、"仅部分预览"的文档,不可在线预览部分如存在完整性等问题,可反馈申请退款(可完整预览的文档不适用该条件!)。
- 3、如文档侵犯您的权益,请联系客服反馈,我们会尽快为您处理(人工客服工作时间:9:00-18:30)。
定义:设备完好率,指的是完好的生产设备在全部生产设备中的比重,它是反映企业设备技术状况和评价设备管理工作水平的一个重要指标。
计算公式:设备完好率=完好设备总台数/生产设备总台数× 100%
标准:所谓完好设备一般标准是:
①设备性能良好,如机械加工设备的精度达到工艺要求;
②设备运转正常,如零部件磨损、腐蚀程度不超过技术规定标准,润滑
系统正常、设备运转无超温、超压现象;
③原料、燃料、油料等消耗正常,没有油、水、汽、电的泄漏现象。
对于各
种不同类型的设备,还要规定具体标准。
例如传动系统的变速要齐全、滑动部分要灵敏、油路系统要畅通等。
公式中的设备总台数包括在用、停用、封存的设备。
在计算设备完好率时,除按全部设备计算外,还应分别计算各类设备的完好率。
2、设备利用率
定义:设备利用率是指每年度设备实际使用时间占计划用时的百分比。
是指设备的使用效率。
是反映设备工作状态及生产效率的技术经济指标。
在一般的企业当中,设备投资常常在总投资中占较大的比例。
因此,设备能否充分利用,直接关系到投资效益,提高设备的利用率,等于相对降低了产品成本。
所以,作为企业的管理者,在进行生产决策的时候,一定要充分认识到这一点。
一般包括:设备数量利用指标―实有设备安装率,已安装设备利用率;设备时间利用指标―设备制度台时利用率,设备计划台时利用率;设备能力利用指标―设备负荷率;设备综合利用指标―设备综合利用率。
过去,设备利用率一般仅指设备制度台时利用率。
计算公式:
公式一:
设备利用率=每小时实际产量/ 每小时理论产量×100%
公式二:
设备利用率=每班次(天)实际开机时数/ 每班次(天)应开机时数×100%
公式三:
设备利用率=某抽样时刻的开机台数/ 设备总台数×100%
定义:设备故障率是指事故(故障)停机时间与设备应开动时间的百分比,是考核设备技术状态、故障强度、维修质量和效率一个指标。
计算公式:故障造成的停机时间/设备工作运行时间×100%
4、设备开动率
定义:设备开动率是指在某一时间段内(如一班、一天等)开动机器生产所占的时间比率。
计算公式:设备实际开动时间/设备正常工作时间×100%
5、OEE
定义:设备综合效率是Overall Equipment Effectiveness,简称OEE。
一般,每一个生产设备都有自己的最大理论产能,要实现这一产能必须保证没有任何干扰和质量损耗。
当然,实际生产中是不可能达到这一要求,由于许许多多的因素,车间设备存在着大量的失效: 例如除过设备的故障,调整以及设备的完全更换之外,当设备的表现非常低时,可能会影响生产率,产生次品,返工等。
OEE是一个独立的测量工具,它用来表现实际的生产能力相对于理论产能的比率。
国际上对OEE的定义为:OEE是Overall Equipment Effectiveness (全局设备效率)的缩写,它由可用率,表现性以及质量指数三个关键要素组成
计算公式:OEE=可用率X 表现性 X质量指数。
其中:
可用率=操作时间 / 计划工作时间
它是用来考虑停工所带来的损失,包括引起计划生产发生停工的任何事件,例如设备故障,原料短缺以及生产方法的改变等。
表现性=理想周期时间 / (操作时间 / 总产量)=(总产量 / 操作时间)/ 生产速率
表现性考虑生产速度上的损失。
包括任何导致生产不能以最大速度运行的因素,例如设备的磨损,材料的不合格以及操作人员的失误等。
质量指数=良品/总产量
质量指数考虑质量的损失,它用来反映没有满足质量要求的产品(包括返工的产品)。
6、MTTR
定义:MTTR(mean time to restoration,即平均修复时间),是指可修复产品的平均修复时间,就是从出现故障到修复中间的这段时间。
MTTR越短表示易恢复性越好。
它包括确认失效发生所必需的时间,以及维护所需要的时间。
MTTR也必须包含获得配件的时间,维修团队的响应时间,记录所有任务的时间,还有将设备重新投入使用的时间。
7、MTBF
定义:全称是Mean Time Between Failure,即平均无故障工作时间。
就是从新的产品在规定的工作环境条件下开始工作到出现第一个故障的时间的平均值。
MTBF越长表示可靠性越高正确工作能力越强。
8、MTTF
定义:全称是Mean Time To Failure,即平均失效时间。
系统平均能够正常运行多长时间,才发生一次故障。
系统的可靠性越高,平均无故障时间越长。