主梁结构件制造工艺
桥式起重机主梁制造工艺与焊接工艺

桥式起重机主梁制造工艺与焊接工艺设计报告团队成员:..................................................专业班级:...............指导教师:....................1前言桥式起重机是横架于车间、仓库和料场上空进行物料吊运的起重设备。
由于它的两端坐落在高大的水泥柱或者金属支架上,形状似桥。
桥式起重机的桥架沿铺设在两侧高架上的轨道纵向运行,可以充分利用桥架下面的空间吊运物料,不受地面设备的阻碍。
在室内外工矿企业、钢铁化工、铁路交通、港口码头以及物流周转等部门和场所均得到广泛的运用,是使用范围最广、数量最多的一种起重机械。
本文主要介绍了跨度21m,起重量50t 的通用桥式起重机箱型梁的设计生产过程。
所选用的钢材为Q345。
2桥梁的总体结构主梁为双梁模型,结构简图如下:主梁 主梁是桥式起重机桥架中主要受力元件,由左右两块腹板,上下两块盖板以及若干大、小隔板及加强筋板组成。
主要技术要求有:主梁上拱度:当受载后,可抵消按主梁刚度条件产生的下挠变形,避免承载小车爬坡。
主梁旁变:在制造桥架时,走台侧焊后有拉深残余应力,当运输及使用过程中残余应力释放后,导致两主梁向内旁弯;而且主梁在水平惯性载荷作用下,按刚度条件允许有一定侧向弯曲,两者叠加会造成大弯曲变形。
腹板波浪变形:受压区07.0δ<,受拉区02.1δ<,规定较低的波浪变形对于提高起重机的稳定性和寿命是有利的。
上盖板水平度250/b c ≤,腹板垂直度250/0h h ≤,b 为盖板宽度,h0为上下盖板之间的高度。
端梁 端梁是桥式起重机桥架组成部分之一,一般采用箱型结构,并在水平面内与主梁刚性连接,端梁按受载情况可分下述两类:(1)、端梁受有主梁的最大支承压力,即端梁上作用有垂直载荷。
(2)、端梁没有垂直载荷,端梁只起联系主梁的作用。
3主梁的尺寸及校核主梁截面图:尺寸:一、箱型主梁截面的主要几何尺寸 起重机的跨度L L=S -b 式中:S=21m ;b=1500mm(无通道); b=2000mm(有通道);L=19.5m 中部高度h 101161→=L h 即:1212mm ≤h ≤1950mm h=1300mm端梁连接处高度h 1 h h 5.01==1h 650mm梯形高度C C=(0.1~0.2)L C=2.925m 端梁宽度C0 C0=288.5mmC0=288.5mm 腹板的壁间距b 00.2~5.1601~50100=≥b hL bb0=800mm腹板厚度δ0 m m 60=δδ0=6mm 盖板宽度bmm b b )20(200++=δb=852mm大隔板间距a 大 靠近端梁处a 大`=h=1300mm 梁中处a 大=1.5h=1950mma 大`=h=1300mma 大=1.5h=1950mm 小隔板高度h 232h h =h2=433.3mm小隔板间距a 小 靠近端梁处a 小`=0.5h= 650mm 梁中处a 小=0.5h=650mm a 小`=0.5h= 650mm a 小=0.5h=650mm 纵向加筋角钢h3h h 25.03=h3=325mm盖板厚1δ 2δ 根据实际情况确定盖板厚1δ 2δ1δ=2δ=10mm主梁的受力分析(1)载荷的计算a) 由活动载荷引起的弯矩和剪力的计算:设小车轮距m b 21=,则m b 121=当活动载荷21P P =,即小车自重和起重载荷作用在一个主梁上的两个车轮的轮压相同,其合力在21b 处,合力t Gq G K P P R II x II 35.3225.622.2221=+=ψ+=+=进行受力分析可知:∑=0F ∑=0BM则LRb x L F A )2(1--=对LRb x L F A )2(1--=进行求导,则L R F A -='\,即A F 为减函数,则有 当10b L x -〈〈时,.5170〈〈x 即,则有 当0=x 时t L R b x L 69.305.1935.32)15.19()2(F Q 1A max=⨯-=--==活对LRx b x L x F A )2(1--=进行求导,则有)22(1\x b L L R F A --='小车自重 2t 2t 桥梁自重11t11t载荷组合II主梁载荷小车载荷起重载荷t G K q II 1.12111.1=⨯= t Gx K II 2.221.1=⨯= t G q II 5.625025.1=⨯=ψ当4b 21-=L x 时,即25.94225.194b 21=-=-=L x ,x F A 取得极大值,所以 m t L Rx b x L ⋅=⨯⨯--=--==95.1415.1925.935.32)125.95.19()2(x F M 1A max 活同理,当L x b L 〈〈-1时,即17.5<x<19.5当x=17.5时,t L R x L 6.615.19235.32).5175.19(2)(Q max =⨯⨯-=-=活m t L Rx x L ⋅=⨯⨯⨯-=-==17.2925.195.1735.32)5.175.19(2)(x F M A max 活b) 由固定荷载引起的弯矩和剪力的计算:均布荷载,如图所示:距支点A 距离为x 的截面上的固定均布载荷引起的剪力和弯矩分别为t G K qL F F q II B A 05.62111.122=⨯==== m N L G K q q II 6205.05.19111.1=⨯==当x=0时 t 05.6qx -F Q A max ==均2qx -x F M 2A =均,对其进行求导,qx -F A \='均M 令0\='均M ,则x=9.75m ,此时均M 取得最大值,即m t ⋅=⨯-⨯==49.29275.90.620575.905.62qx -x F M 22A max 均 通过对剪力图和弯矩图的分析得出垂直方向的最大剪力和弯矩由于活动载荷和均布载荷引起的最大剪力都是在X=0处产生 所以:Q ⊥max =Q 活max + Q 均max =30.69t+6.05t=36.74t由于活动载荷和均布载荷引起的最大弯矩不在同一处产生,所以不能直接加减求得 故:M ⊥max =2(L-x-b 1/2)Rx /L -q.x ^2/2、M ⊥max '=0 x=(2RL-b 1)/(4R+q.L)=8.46m故在x=8.46m 处取得最大弯矩M ⊥max =259.62t ·m计算水平方向的弯矩时,可以认为桥架是一个超静定刚架结构,最大弯矩为)23(24)21(42maxγγl l q l l F M sh sh sh -+-= 其中'233*38yy gJ J K B c l ++=γ可简化计算,令 Q shmax =0.1 Q ⊥max =3.674tM shmax=0.1 M ⊥max =25.962t ·m(2)强度的计算尺寸确定后惯性矩的 计算4233210131300009186.02102128010852210852122128062121)22(2122)2(121m h b b h I x =⎪⎭⎫ ⎝⎛+⨯⨯⨯+⨯⨯+⨯⨯⨯=+++=δδδδ442332000030031003525.0)26800(6128026128061852102121]2/)[(2122)2(121m mm b h h b I Y =+⨯⨯⨯+⨯⨯+⨯⨯⨯=+++=δδδδ 3301413.0650.0009186.02m m h I W x x === 33008275.0426.0003525.02/m m b I W y y=== 由max max sh M M 和⊥产生的主梁跨中截面的正应力分别为MPa W M x 74.18301413.062.259max ===⊥⊥σ M P aW M y sh sh 374.31008275.0962.25max max ===σ 故水平和垂直弯矩同时作用时,在主梁上下盖中引起最大正应力为MPa sh 114.215374.3174.183max =+=+=⊥σσσ经过查参考资料《优质碳素结构钢》-低碳合金钢的力学性能和对比,取Q345比较合适,则许用应力为:Mpa Mpa s114.2152305.13455.1][=>===σσσ故选用Q345钢,强度符合要求。
市政桥梁钢箱梁制造工艺及质量控制措施

市政桥梁钢箱梁制造工艺及质量控制措施发布时间:2022-08-09T06:29:49.657Z 来源:《工程管理前沿》2022年7期作者:李加福[导读] 近年来,钢箱梁桥因其抗风性能好、施工速度快而迅速得到推广。
在钢箱梁构件制造过程中,由于工艺管理水平及桥梁李加福(云南楚山工程管理有限公司云南玉溪 653100)摘要:近年来,钢箱梁桥因其抗风性能好、施工速度快而迅速得到推广。
在钢箱梁构件制造过程中,由于工艺管理水平及桥梁制造经验的差异,导致钢箱梁构件制造质量与效率存在较大差异。
本文结合元江县跨江大桥,对市政桥梁钢箱梁制造工艺和质量控制措施进行阐述。
关键词:钢箱梁;焊接;制造工艺;质量控制引言:随着我国钢铁行业去产能力度的不断加大,钢铁行业的发展速度也在不断加快。
“十三五”期间,国家加大基础设施投资、交通建设投资,进一步推动了公路桥梁钢结构的应用。
根据兰格钢铁研究中心的测算,每增加10%公路钢结构桥梁的用钢量就会增加8.36×106 t,我国钢结构桥梁发展势头迅猛。
一、工程概况元江县跨江大桥是一座独塔单柱斜拉桥(70+130)。
主桥采用塔墩梁固结体系,主梁采用钢—混凝土组合结构,采用边跨混凝士箱梁和主跨钢箱梁。
斜拉索按扇形布置,采用平行双索面,索面横桥间距1.5米,钢箱梁侧标准索距11.5米。
桥梁平面为直线,纵坡为单向纵坡,坡度为0.9%,全桥均为双向2%。
主桥桥型(立面)布置见图1。
主要工作包括:制造、运输、桥位安装、环缝焊接、防腐(底漆、中间漆、面漆)。
二、钢箱梁加工制造重点、难点本桥是一座钢箱形梁斜拉桥,梁段间的连接除了采用螺栓连接的顶板加劲肋外,其它都是焊接的,其制造的重点和难点如下:1)控制顶板 U肋制孔精度;2)控制 U形肋条的位置精度;3)控制 U形肋条的焊接质量;4)控制钢箱梁的整体焊接变形;5)控制梁段端口外形尺寸;6)梁段装配的焊接质量;7)控制锚拉板的制造和安装精度。
37--斜拉桥主梁(悬臂拼装法)施工工艺

37 斜拉桥主梁(悬臂拼装法)施工工艺37.1 适用范围本工艺适用于桥梁工程、斜拉桥钢主梁(钢—混凝土结合梁)采用悬臂拼装、高强螺栓连接或焊接施工工艺。
37.2 施工准备37.2.1 材料要求1 钢箱梁所用钢板、型钢,其质量应符合《桥梁用结构钢》GB/T714等现行国家产品标准的规定。
钢铸件的品种、规格、性能等应符合现行国家产品标准和设计要求。
钢箱梁用进口钢材其质量应符合设计要求和合同规定标准的要求。
钢箱梁用焊接材料(焊条、焊丝、焊剂及气体保护焊所用氢气、二氧化碳气体等)的质量应符合现行国家产品标准的要求。
钢箱梁用涂装材料、连接紧固件和剪力钉等材料应符合设计要求和国家现行标准规定。
2 钢主梁施工所用的吊装体系材料等应符合施工组织设计规定。
3 拉索及其锚具应委托专业单位制作,严格按照国家或部颁的行业标准、规定及设计的特殊要求进行生产,并应进行检查和验收。
在工艺更新或确有必要时,可考虑进行拉索的疲劳性能、静载性能试验。
对高强钢丝拉索,在工厂制作时应按1.2~1.4倍设计索力对拉索进行预张拉检验,合格后方可出厂。
锚具的动、静载性能应与锚具所对应的拉索相匹配。
锚环、锚板、螺母和垫块等主要受力件的半成品在热处理后应进行超声波探伤,探伤合格的方可进入下一道工序。
拉索成品、锚具交货时应提供下列资料:产品质量保证书、产品批号、设计索号及型号、生产日期、数量、长度、重量、产品出厂检验报告及有关数据。
37.2.2 机具设备1 运梁车辆:轴线车、拖车、炮车等。
运梁车辆应根据钢箱梁长度、重量及几何尺寸以及运输线路现况条件选用,其载重能力及技术性能必须满足运输梁板的要求。
2 钢箱梁吊装设备:龙门吊、汽车吊、履带吊、塔吊、桥面吊机、卷扬机等。
3 拉索安装设备:索盘支架、滚筒(滚轮)、导向轮、卷扬机、塔吊等拉索安装设备。
4 检测仪器设备:全站仪、经纬仪、水准仪、传感器、振动频率测力计等。
5 工具:撬杠、扳手、扭矩扳手、钢尺、直尺等。
航空发动机吊具技术分析

SCIENCE & TECHNOLOGY INFORMATION科技资讯航空发动机吊具技术分析满达 王歆童 张海幸 刘超超中国航发沈阳发动机研究所 辽宁沈阳 110015摘要: 在航空发动机整机试验过程中,需要进行航空发动机的起吊和装卸。
作为航空发动机在试车台安装的工具,航空发动机吊具的重要性不容忽视。
航空发动机吊具的设计方法,包括航空发动机吊具的组成、关键部件的设计及结构强度计算方法。
而航空发动机吊具的检验方法和负载试验方法,能确保设计的航空发动机吊具工作的稳定性。
关键词: 航空发动机吊具 吊具设计 吊具负载试验 吊具使用及维护中图分类号: V262.4文献标识码: A文章编号: 1672-3791(2024)01-0071-03航空发动机吊具是航空领域中航空发动机与试车台组装拆卸过程中使用的专业设备。
由于社会发展、科技进步和军事储备水平的提升,国内航空事业快速发展,各型号的飞机种类不断扩大,航空发动机的型号和种类也在不断增加,各试验台对发动机吊具的需求也日益剧增。
吊具设计应满足被吊物吊装要求,如质量要求、重心要求等,同时还应保证起吊工作的安全性和设计时应具备足够的强度[1]。
对于航空发动机吊具,还需开展出厂前必要的检验及负载试验,确保航空发动机吊具工作的可靠性。
航空发动机吊具已成为航空发动机试验中配套设备设计的关键技术之一。
因此,发动机吊具的设计、检验、操作、维护以及保养就显得格外重要。
本文将从航空发动机吊具设计技术、负载试验、吊具检验方法、使用及保养维护方法进行介绍。
1 航空发动机吊具设计技术1.1 航空发动机吊具组成根据航空发动机结构特点和吊具设计要求,为方便加工、安装等工艺性,吊具通常采用模块化设计。
主要由主梁组合件、吊挂、丝杠传动机构、吊绳吊点组件和其他附件组成,吊具结构如图1所示。
该型吊具具有以下优点:(1)采用连续调节式可调吊挂点,保证重心精确调节的需要;(2)采用组合式吊绳吊点结构,可以针对不同型号快速组合,并保留一定对未来新型号发动机的拓展能力;(3)具有良好的型号适应能力和经济效益,可以推广应用于试车台、外场等,提高外场工装通用性和维护便利性。
起重机桥架的制造工艺

起重机桥架的制造一、起重机箱形主梁制造工艺(一)进厂原材料复检1.入库前应进行质量证明书检查2.实物检查3.理化性能测试(二)主梁、支腿等重要零部件所用的材料的要求:1.A1~A6级起重机,当板厚大于20mm时,钢材牌号应不低于Q235-B;对A7~A8级起重机,钢材牌号应不低于Q235-C。
2.环境温度-20℃~-25℃,或环境温度低于-25℃时,应选用Q235-D或16Mn,且要求在-20℃时的冲击功不小于27J。
3.严禁在低温下使用沸腾钢。
这是因为①沸腾钢脱氧不完全,氧能使钢变脆;②内部杂质较高,成份偏析较大,因而冲击值较低;③冷脆倾向和时效敏感性较大;④焊接性较差。
(五)钢材预处理热轧钢材表面通常有一层氧化皮,呈灰黑色,覆盖于钢材表面,应进行除锈喷丸等预处理,并进行防锈处理。
通常采用的防锈底漆有703环氧脂铁红和无机硅酸锌底漆等。
锈是一种有氧化物和水分子的物质。
锈和氧化物的危害有减弱结构件的承载能力,降低结构的涂漆质量,影响乙块火焰切割和焊接质量等。
(四)主梁的拼接与组装1.盖板与腹板的拼接2.腹板下料主梁成拱最常用的方法是腹板下料成拱法。
腹板的拱形可采用二次抛物线形或正弦曲线形。
腹板上拱值规定为0.9~1.4S/1000,考虑气割、焊接电流、焊接速度、操作者技术程度等因素影响,多取 1.4S/1000。
腹板下料有三种方法:(1)腹板拱度曲线直接号料法(2)样板号料法3.盖板、腹板对接焊缝焊接(1)开坡口盖板、腹板对接焊缝要求焊透,采取开坡口的方法,以增加熔深。
板厚δ时就要开坡口。
mm>6(2)板件拼接间隙和定位焊①板件拼接间隙过大,焊接时易产生烧穿、焊缝成形不佳的缺陷,同时焊接变形也较大。
②定位焊的技术要求盖板、腹板定位焊前要检查一下板边的直线度和预拱值,可用拉粉线或钢丝线测量。
定位焊焊肉要比正式焊缝小,焊缝质量同正式焊缝,不得存在夹渣、裂纹、未焊透等缺陷,定位焊的间距,在根据拼接钢板定型的条件凭经验确定,通常长为20~40mm焊缝,间距在70~150mm范围内。
主梁和次梁介绍
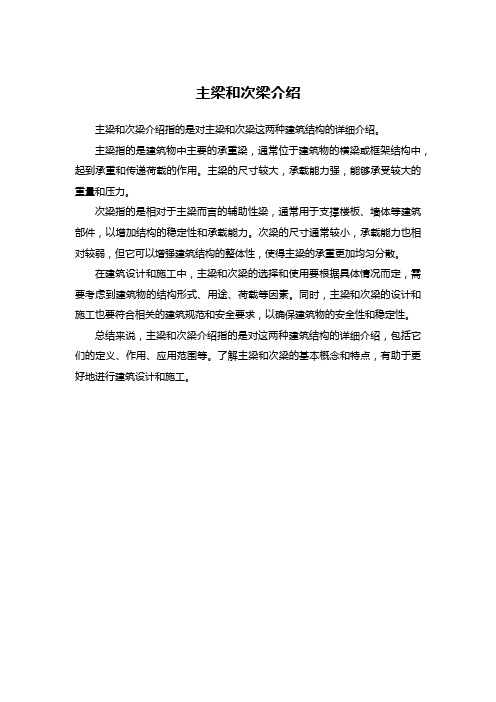
主梁和次梁介绍
主梁和次梁介绍指的是对主梁和次梁这两种建筑结构的详细介绍。
主梁指的是建筑物中主要的承重梁,通常位于建筑物的横梁或框架结构中,起到承重和传递荷载的作用。
主梁的尺寸较大,承载能力强,能够承受较大的重量和压力。
次梁指的是相对于主梁而言的辅助性梁,通常用于支撑楼板、墙体等建筑部件,以增加结构的稳定性和承载能力。
次梁的尺寸通常较小,承载能力也相对较弱,但它可以增强建筑结构的整体性,使得主梁的承重更加均匀分散。
在建筑设计和施工中,主梁和次梁的选择和使用要根据具体情况而定,需要考虑到建筑物的结构形式、用途、荷载等因素。
同时,主梁和次梁的设计和施工也要符合相关的建筑规范和安全要求,以确保建筑物的安全性和稳定性。
总结来说,主梁和次梁介绍指的是对这两种建筑结构的详细介绍,包括它们的定义、作用、应用范围等。
了解主梁和次梁的基本概念和特点,有助于更好地进行建筑设计和施工。
沪通长江大桥超长双整体节点箱形弦杆制造关键技术研究
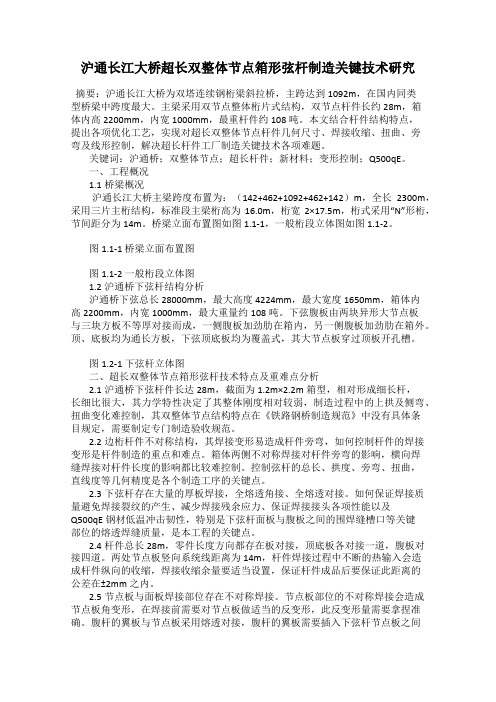
沪通长江大桥超长双整体节点箱形弦杆制造关键技术研究摘要:沪通长江大桥为双塔连续钢桁梁斜拉桥,主跨达到1092m,在国内同类型桥梁中跨度最大。
主梁采用双节点整体桁片式结构,双节点杆件长约28m,箱体内高2200mm,内宽1000mm,最重杆件约108吨。
本文结合杆件结构特点,提出各项优化工艺,实现对超长双整体节点杆件几何尺寸、焊接收缩、扭曲、旁弯及线形控制,解决超长杆件工厂制造关键技术各项难题。
关键词:沪通桥;双整体节点;超长杆件;新材料;变形控制;Q500qE。
一、工程概况1.1桥梁概况沪通长江大桥主梁跨度布置为:(142+462+1092+462+142)m,全长2300m,采用三片主桁结构,标准段主梁桁高为16.0m,桁宽2×17.5m,桁式采用“N”形桁,节间距分为14m。
桥梁立面布置图如图1.1-1,一般桁段立体图如图1.1-2。
图1.1-1 桥梁立面布置图图1.1-2 一般桁段立体图1.2沪通桥下弦杆结构分析沪通桥下弦总长28000mm,最大高度4224mm,最大宽度1650mm,箱体内高2200mm,内宽1000mm,最大重量约108吨。
下弦腹板由两块异形大节点板与三块方板不等厚对接而成,一侧腹板加劲肋在箱内,另一侧腹板加劲肋在箱外。
顶、底板均为通长方板,下弦顶底板均为覆盖式,其大节点板穿过顶板开孔槽。
图1.2-1 下弦杆立体图二、超长双整体节点箱形弦杆技术特点及重难点分析2.1沪通桥下弦杆件长达28m,截面为1.2m×2.2m箱型,相对形成细长杆,长细比很大,其力学特性决定了其整体刚度相对较弱,制造过程中的上拱及侧弯、扭曲变化难控制,其双整体节点结构特点在《铁路钢桥制造规范》中没有具体条目规定,需要制定专门制造验收规范。
2.2边桁杆件不对称结构,其焊接变形易造成杆件旁弯,如何控制杆件的焊接变形是杆件制造的重点和难点。
箱体两侧不对称焊接对杆件旁弯的影响,横向焊缝焊接对杆件长度的影响都比较难控制。
《焊接结构》课程设计说明、课程内容

《焊接结构》课程设计说明一、课程基本信息课程名称:焊接结构学时:60授课对象:焊接专业学分:2课程性质:专业必修课二、课程定位《焊接结构》是焊接技术专业的一门主干专业课程,主要介绍焊接结构生产及现场管理方面的知识,要求具备一定的管理水平,又有较强的焊接结构现场生产实践性。
本课程采用“项目导向、任务驱动”理论实践一体化的教学方法,不单独开设实验课程,强调围绕企业生产为主,积累经验,学会在生产现场进行独立分析、创新设计各种焊接辅助设备,主要内容包括:引导项目:焊接结构(梁、柱、桁架、支架)的生产与管理,主导项目:焊接接头的质量控制(包括变形与应力控制);焊接接头的结构设计;焊接结构件的装配、定位、检测、焊接的全过程;焊接工艺的审定;典型案例的分析等。
通过对焊接结构件的生产管理,学会钢结构类、承压类设备的焊接设计、焊接工艺思路与程序,注重焊前准备、焊接过程控制、焊后检测等环节,生产中体现各种准备要素(包括相应文件资料),焊接结构生产的装配与焊接之间的关系,保证学生的实际动手能力三、课程设计1.能力目标(1)熟悉焊接结构课程的主题框架(2)能对焊缝、焊接接头的各种类型进行优势比较(3)熟悉焊接梁、柱、桁架等结构件的生产流程(4)熟悉焊接生产中注意的问题(焊接应力与变形)进行分析与控制(5)熟悉焊接结构件生产的装配、定位、检测要求(6)熟悉焊接工艺性审查的主要内容2、知识目标(1)熟悉各种焊接接头、基本符号、各种焊缝特点的基本知识(2)掌握焊接结构生产的工作流程与步骤(3)掌握控制焊接应力与变形的方法,了解形成的主要原因(4)熟悉焊接结构件装配、定位器的使用3、态度目标(1)具有勤奋学习的态度,良好的职业道德和爱岗敬业精神(2)具有认真、严谨、耐心、细致的工作作风4、工作目标能进行焊接生产项目的管理,利用各种知识形成体系,具备生产中设计简单夹具、定位机构、旋转机构的能力,对各种焊缝、焊接接头的布局能严格按照工艺要求进行合理的装配—焊接的顺序选择,熟悉承压类设备焊缝的代码编号,焊接工艺编码语言,能根据焊接装配图纸掌握焊缝、焊接位置的全局关系。
浅谈大型桥式起重机的主梁制造与焊接工艺
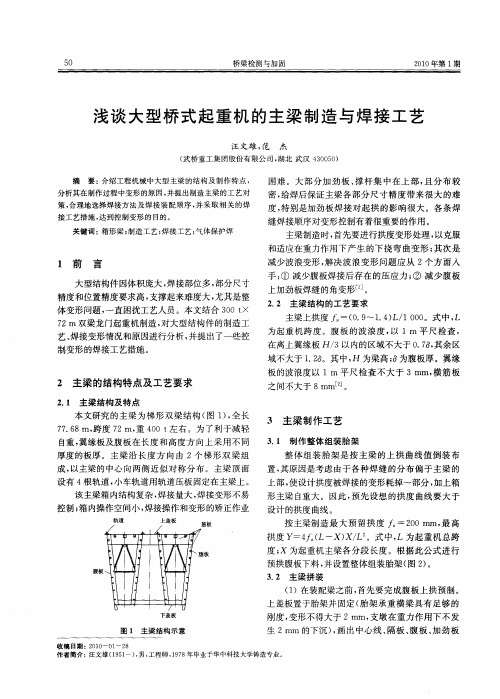
主梁 上拱度 厂一(. ~14L/ 0 。式 中 , a 09 . ) 100 L 为起 重 机 跨度 。腹 板 的波 浪 度 , 11 平 尺 检 查 , 以 I T 在 离上翼缘 板 H/ S以内的区域 不大于 0 7 , . 其余 区 域 不大 于 12 。其 中 , 为梁 高 ; . H 为腹板厚 。翼缘
制变 形 的焊 接工艺措 施 。
板的波浪度以 1 平尺检查不大于 3m 横筋板 m m,
2 主梁的结构特点及工艺要求
2 1 主梁结构 及特 点 .
之 间不大 于 8mmL 。 2 j
本 文研究 的主梁 为 梯 形 双 梁结 构 ( 1 , 长 图 )全 7.8m, 76 跨度 7 重 40t 右 。为 了利 于减 轻 2m, 0 左 自重 , 缘板及 腹板 在 长度 和 高 度方 向上采 用 不 同 翼 厚 度 的板 厚 。主 梁 沿 长 度 方 向 由 2个 梯 形 双 梁组 成, 以主梁 的 中心 向两 侧 近似 对 称 分 布 。主梁 顶 面 设 有 4根轨道 , 小车轨 道用轨 道压板 固定在 主梁上 。
5 0
桥梁检测与加 固
21 0 0年第 1 期
浅 谈 大型 桥 式起 重 机 的主梁 制造 与焊 接 工 艺
汪 文雄 , 范 杰
( 武桥重工集 团股份有限公司 , 湖北 武汉 40 5) 3 O 0
摘
要: 介绍工程机械 中大 型主梁的结构及制作特点 ,
困难 。大 部 分 加 劲 板 、 杆 集 中在 上 部 , 分 布 较 撑 且
该 主梁箱 内结构 复杂 , 接量大 , 焊 焊接 变形不 易
3 主梁制作工艺
LD主梁结构工艺要求

与d面沿水平方向的平行度不大于0.6mm(见图二)
新疆有色全鑫建设 有限公司
工艺附图
产品型号
产品名称
LD10
部件图号
共15页
单梁桥式起重机
部件名称
主梁
第4页
新疆有色全鑫建设 有限公司
工艺附图
产品型号 产品名称
LD10
部件图号
共15页
单梁桥式起重机
部件名称
一、跨度w13.5m的主梁的组装与焊接
1、焊接工字钢下加强板注意对接焊缝应避开跨中及
工子钢拼接处尺寸不小于200mm予制上拱度。
2、将工字钢吊放在平台上,工字钢下面放置垫铁,并 用压板将工字钢紧固在平台上。
3、在工字钢上划隔板安装线。
4、点焊隔板在工字钢上,用直角尺控制垂直。并使每 块隔板边缘在同一条基准线上。
13、交检:按蓝图及各项技术要求检查
装配 部门
设备及工艺装备
辅助材料
工时 定额
(分)
料,接板宽度应>100mm。
2、对于跨度<13.5m的10LD主梁腹板应按下料、矫平、
折弯的顺序完成,对于跨度》13.5m的10LD主梁腹
板,需接长,接宽时,在拼接后经过打磨矫平后方可 号料,接板宽度应>100mm。
装配 部门
设备及工艺装备
辅助材料
工时 定额
(分)
3工字钢矫直。最大波浪度用1m钢板尺检查不大于
4、 主梁腹板的垂直偏斜值hwH/150,(H为腹板高度) (见图五)
5、 主梁上盖板和工字钢的水平偏斜值bwB/150(B为 宽度)(见图六)
6、 箱型梁中心对工字钢中心的偏移不大于2mm
7、对跨度 梁纵向
起重机焊接结构件制造工艺设计规范流程

一、材料预处理1、原材料装卸货和转移时必须采用专用吊具:配备吊梁的专用吊卡、夹鉗、板钩或者磁铁。
在任何情况下都禁止钢丝绳直接接触钢板进行吊运。
原材料水平或者垂直码(堆)放时必须垫实靠牢,使其处于不受力的自然状态。
暂缓不用的原材料须采取有效的防护措施,远离热源和潮湿处搁置,并用明显记号标明材质和规格型号。
2、所有钢板、重要部位的型材以及氧化锈蚀较重的型材须进行双面抛丸、喷沙或者喷丸处理,使其金属表面呈均匀的近白色。
表面处理完毕后即将喷刷薄层(干燥时间不得超过4min ) 的硅酸锌防锈底漆。
禁止使用在气割和焊接过程中会释放出对人体有害气体的防锈油漆。
3、小吨位起重机主梁用钢板优先选用卷板,卷板在开卷矫平机上矫平。
4、钢板厚度6≤14mm、1m 波浪度>3mm 和厚度6>14mm、1m 波浪度> 2mm 的板材必须进行矫正整形处理。
整形方法为:机床整形或者人工冷作整形。
人工整形时禁止直接锤击原材料,必须在其上垫6>8mm 的击打垫板。
不允许火焰整形。
5、型材的初始弯曲程度为: 1m 直线度> 1mm 的必须进行矫直处理。
矫直方法为:型钢矫直机滚压或者油压机顶压。
较大规格型材在征得质量负责人允许后允许火焰矫直。
6、润滑和液压油路的钢管进行酸洗处理。
处理后即将在管外壁喷刷防锈底漆,漆后油封二口以防止内壁再次氧化。
有色金属管和橡胶管须经压风吹净其内壁,然后封堵二口待用。
二、原材料下料1、创造负责人须对采购部门提出钢板供应尺寸(主要针对主梁腹板)的要求,以达到科学合理的拼料。
在选择原材料下料时,起重机桥架用材处于最优先地位,以做到主梁、端梁上的钢板拼接焊缝离主梁中心越远越好、焊缝数量越少越好。
2、原材料下料必须有整体下料的概念,主梁、端梁、走台、小车架要统筹考虑,画好经讨论的排料图再行下料。
下料规则为:先下大料再下小料,先大再小先长后短相互套料,使整台行车的材料利用率达到 95%以上。
3、厚度6≤12mm 的钢板用剪床进行直线形下料。
浅谈电动葫芦门式起重机(箱型)主梁制作技术
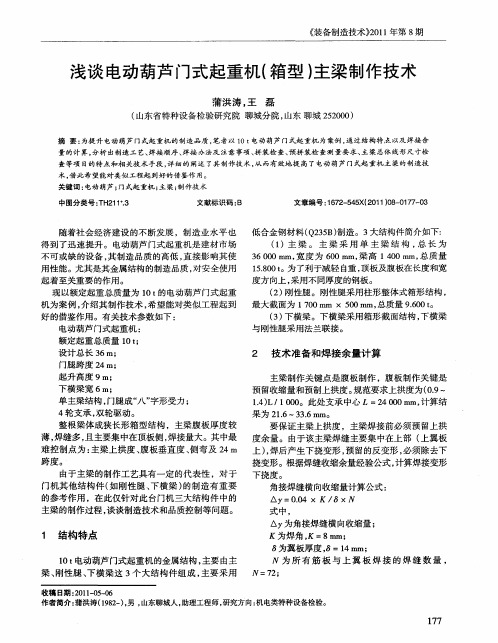
随着 社 会 经 济 建设 的不 断 发 展 ,制 造 业 水 平 也 低合金钢材料 ( 25 ) Q 3 B 制造。3 大结构件简介如下: 得 到 了 迅 速提 升 。 电动 葫芦 门式 起 重机 是 建 材 市 场
不可或缺的设备 , 其制造 品质 的高低 , 直接影响其使 用性能。尤其是其金属结构 的制造 品质 , 对安全使用 起 着 至关 重要 的作 用 。 现 以额定 起 重 总质 量 为 1 的 电动葫 芦 门式起 重 0t 机为案例 , 介绍其制作技术 , 望能对类似工程起到 希 好 的借鉴作用 。有关技术参数如下 : 电动 葫芦 门式起 重机 : 额 定 起重 总 质量 1 ; 0t 设 计 总长 3 6m; 门腿 跨度 2 4m; 起 升 高度 9m; 下横 梁 宽 6m; 单 主梁结 构 , 门腿 成 “ ” 八 字形 受力 ; 4 轮支承 , 双轮驱动 。 整根梁体成狭长形箱型结构 ,主梁腹 板厚度较 薄, 焊缝多 , 且主要集中在顶板侧 , 焊接量大。其 中最 难控制点 为 : 主梁上拱度 、 腹板垂直度 、 侧弯及 2 4m 跨度。 由于主梁 的制作工艺具有一定 的代表性 ,对于 门机其 他结构件 ( 如刚性腿 、 下横梁 ) 的制造有 重要 的参考作用 ,在此仅针对此台门机三大结 构件中的 主梁的制作过程 , 谈谈制造技术和品质控制等 问题。
( )主 梁 。 主 梁 采 用 单 主 梁 结 构 , 长 为 1 总 3 0 宽 度 为 60mm, 高 1 0 i, 质 量 600mm, 0 梁 0ml 总 4 l 1.0 。为 了利 于减 轻 自重 , 板 及腹 板在 长度 和宽 580t 顶 度方 向上 , 用不 同厚 度 的钢板 。 采 () 2 刚性腿。刚性腿采用柱形整体式箱形结构 , 最 大 截 面为 l 0 m × 5 0m 总质量 960t 0m 7 0 m, .0 。 () 3 下横梁。下横梁采用箱形截面结构 , 下横梁 与 刚性腿 采 用法 兰联 接 。
钢结构制造工程施工工序

钢结构制造工程施工工序
钢结构制造工程施工工序主要包括以下几个方面:
一、基础工程阶段
在钢结构制造工程的施工工序中,基础工程是至关重要的一环。
首
先需要对工程现场进行勘察设计,明确地基的尺寸和深度。
接着进行
基坑的挖掘和土方的回填,确保基础牢固。
最后进行基础的浇筑,保
证基础的稳固。
二、主体结构制作
主体结构制作是钢结构制造的核心环节。
首先进行结构设计和计算,确定各个构件的材料和尺寸。
然后进行焊接和切割,加工各种构件,
包括梁、柱等。
最后进行组装,将各个构件连接在一起,组成整体的
主体结构。
三、防火涂料处理
钢结构需要进行防火处理,以提高其防火性能。
首先进行表面处理,清除表面的油污和锈蚀。
然后进行涂料处理,将防火涂料均匀地涂抹
在钢结构表面。
最后进行烘烤处理,确保防火涂料牢固。
四、安装验收
在钢结构制造工程施工工序的最后阶段,需要进行安装和验收工作。
首先进行吊装和安装,将主体结构吊装至设计位置,并进行连接。
然
后进行质量验收,检查各个构件的焊接和连接是否合格。
最后进行安全验收,确保钢结构的安全性能。
综上所述,钢结构制造工程施工工序包括基础工程阶段、主体结构制作、防火涂料处理和安装验收。
每个环节都至关重要,需要严格按照流程进行,以确保工程的质量和安全性。
希望以上内容能够对您有所帮助。
钢结构制造施工工序

钢结构制造施工工序钢结构制造施工工序包括设计、加工、安装等多个环节,下面将详细介绍这些工序。
1. 设计在进行钢结构制造施工之前,首先需要进行设计。
设计师需要根据建筑师或者工程师提供的建筑图纸,结构计算书等资料进行设计。
设计要考虑结构强度、稳定性、承重能力等因素,确保结构安全可靠。
2. 钢材采购设计确定后,接下来是采购所需的钢材。
根据设计的要求和结构的实际情况,选择合适的型号、规格的钢材。
在选择钢材时,要考虑质量、价格、运输等因素,确保钢材符合要求。
3. 钢材加工采购回来的钢材需要进行加工,包括切割、焊接、打磨等操作。
这些加工工序需要在工厂或者加工车间完成,确保加工的精度和质量。
4. 防腐处理对于钢结构,防腐处理非常重要。
在加工完钢材之后,需要进行表面处理,通常是喷涂防锈漆或者热浸镀锌等方式,增加钢结构的耐腐蚀能力。
5. 运输和现场施工加工完成的钢结构件需要进行运输和现场安装。
运输过程中需要注意保护钢结构件,避免损坏。
在现场施工时,需要按照设计要求,进行配合安装工序,确保结构的稳固和安全。
6. 焊接和校正在现场安装过程中,需要进行钢结构的焊接和校正。
焊接要求操作人员具备相应的技术和证书,确保焊接质量。
校正则是对安装后的钢结构进行检查,调整,保证结构的垂直度,水平度等。
7. 质检和验收最后,钢结构制造施工工序中的最后一步是质检和验收。
质检人员需要对钢结构的各个环节进行检查,确保符合相关标准和要求。
验收人员根据质检报告进行验收,确保钢结构安全可靠。
通过以上工序,钢结构制造施工顺利进行,确保建筑的安全性和稳定性。
起重机焊接结构件制造工艺规程
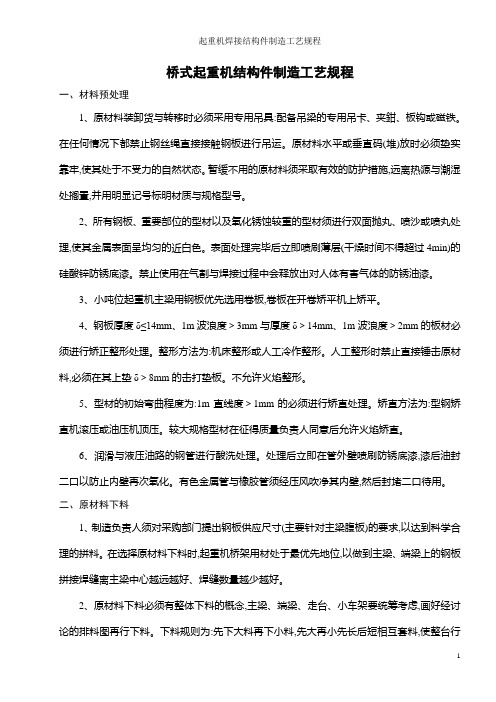
桥式起重机结构件制造工艺规程一、材料预处理1、原材料装卸货与转移时必须采用专用吊具:配备吊梁的专用吊卡、夹鉗、板钩或磁铁。
在任何情况下都禁止钢丝绳直接接触钢板进行吊运。
原材料水平或垂直码(堆)放时必须垫实靠牢,使其处于不受力的自然状态。
暂缓不用的原材料须采取有效的防护措施,远离热源与潮湿处搁置,并用明显记号标明材质与规格型号。
2、所有钢板、重要部位的型材以及氧化锈蚀较重的型材须进行双面抛丸、喷沙或喷丸处理,使其金属表面呈均匀的近白色。
表面处理完毕后立即喷刷薄层(干燥时间不得超过4min)的硅酸锌防锈底漆。
禁止使用在气割与焊接过程中会释放出对人体有害气体的防锈油漆。
3、小吨位起重机主梁用钢板优先选用卷板,卷板在开卷矫平机上矫平。
4、钢板厚度δ≤14mm、1m波浪度>3mm与厚度δ>14mm、1m波浪度>2mm的板材必须进行矫正整形处理。
整形方法为:机床整形或人工冷作整形。
人工整形时禁止直接锤击原材料,必须在其上垫δ>8mm的击打垫板。
不允许火焰整形。
5、型材的初始弯曲程度为:1m直线度>1mm的必须进行矫直处理。
矫直方法为:型钢矫直机滚压或油压机顶压。
较大规格型材在征得质量负责人同意后允许火焰矫直。
6、润滑与液压油路的钢管进行酸洗处理。
处理后立即在管外壁喷刷防锈底漆,漆后油封二口以防止内壁再次氧化。
有色金属管与橡胶管须经压风吹净其内壁,然后封堵二口待用。
二、原材料下料1、制造负责人须对采购部门提出钢板供应尺寸(主要针对主梁腹板)的要求,以达到科学合理的拼料。
在选择原材料下料时,起重机桥架用材处于最优先地位,以做到主梁、端梁上的钢板拼接焊缝离主梁中心越远越好、焊缝数量越少越好。
2、原材料下料必须有整体下料的概念,主梁、端梁、走台、小车架要统筹考虑,画好经讨论的排料图再行下料。
下料规则为:先下大料再下小料,先大再小先长后短相互套料,使整台行车的材料利用率达到95%以上。
3、厚度δ≤12mm的钢板用剪床进行直线形下料。
165t铸造吊主梁产生裂纹原因简析及处理办法初探
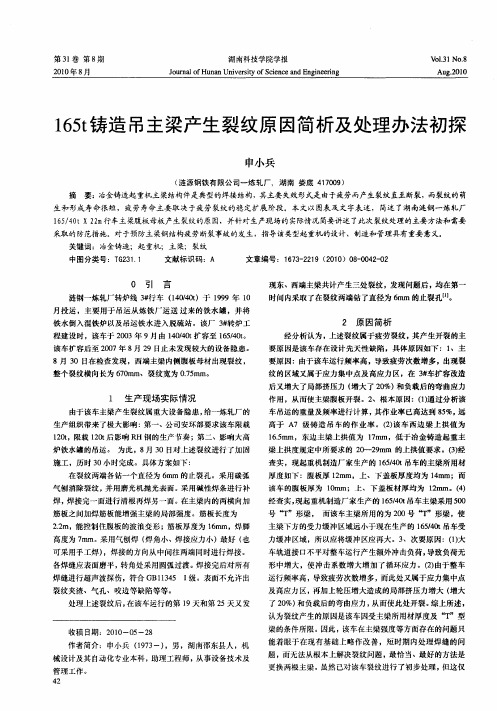
第 3卷 第8 l 期
2 1年 8 00 月
湖 南科 技学 院 学报
J u n l f n nUn v ri f ce c dEn i e r g o r a o Hu a i e st o in ea gn e i y S n n
Vb .1No 8 1 . 3 Au .0 0 g2 1
整个裂纹横向长为 6 0 m、裂纹宽为 07 m 7m . m。 5
l 生产现场 实际情 况
由于该车主梁产生裂纹属重大设备 隐患 , 给一炼轧厂 的 生产组织带来了极大影响 : 第一、公司安环部 要求该车限载 10 ,限载 10 后影响 R 2t 2t H钢的生产节奏 ; 第二、影响大高 炉铁水罐的 吊运。 为此,8月 3 0日对上述裂纹进行了加固
现东、西端主梁共计产 生三处裂纹 ,发现问题后 ,均在第一 时间内采取 了在裂纹两端钻 了直径为 6 m 的止裂孔Ⅲ。 m
2 原 因简析
经分析认为 , 上述裂纹属于疲劳裂纹 , 其产生开裂的主
要原 因是该车存在设计先天性缺陷 ,具体原 因如下 :1 、主
要原因 :由于该车运行频率高,导致疲劳次数增多 ,出现裂 纹 的区域又属于应力集 中点及高应力区,在 3 车扩容改造 # 后又增大了局部挤压力 ( 增大 了 2 %) 负载后的弯曲应力 O 和
TSG特种设备安全技术规范TSGQ00022008

资料的检验时必须按此要求检查;安装过程的监督检验也要按
此要求检验;
6、主要受力结构件有主梁、端梁、小车架、吊具横梁,
而不是制造监督检验中所说的只有主梁。
第九条 制造单位向用户提供的产品质量证明书,至少 包括以下内容: (一)产品合格证; (二)产品技术特征,包括主要参数、工作级别、主要结构 型式、工作机构主要特性、适用工作环境、依据标准; (三)主要受力结构件材料,包括材料标准、牌号、规格、 制造单位、材料标志、制造日期,以及材料化学成分、材料 力学性能; (四)主要零部件,包括所配套的零部件的名称、零部件号、 型号规格、制造单位、制造日期、产品编号,以及外构件合 格证明; (五)安全保护装置,包括所配套的安全保护装置的名称、 装置号、型号规格、制造单位、制造日期、产品编号、外构 件合格证明,以及型式试验报告或者型式试验合格证; (六)出厂检验报告,包括整机检查、主要尺寸测量; (七)铭牌实物复印件(如拓印件)。
本规程适用的起重机,包括通用桥式起重机、
电站桥式起重机、防爆桥式起重机、绝缘桥式起重 机、冶金桥式起重机、架桥机、电动单梁起重机、 电动单梁悬挂起重机、电动葫芦桥式起重机和防爆 梁式起重机等。
要点:1、规定了适用的起重机类型1个:桥 式起重机;品种(型式)有10个;型号多种。
2、规定了适用的环节有7个,即设计、 制造、安装、改造、维修、使用、检测检 验,该7个环节均要执行此规程,和以往的 关于起重机的规定有所不同的是该规程含 盖设计环节,但是他不含盖监督管理环节, 因为他是安全技术监察规程,所以不含监 督管理环节。
果按照375号文件中的11条生产的,那么必须进行单独认证,型号为QDY,产
桥式起重机主梁焊接工艺及防变形控制方法

桥式起重机主梁焊接工艺及防变形控制方法摘要:本文介绍了桥式起重机主梁的制造工艺以及在焊接过程中防止焊接变形的措施,对箱形主梁焊接工艺的分析等做了详细的叙述。
关键词:桥式起重机,主梁,焊接工艺,焊接变形,箱形梁前言桥式起重机是工业生产中常见的起吊设备之一,它是由起重小车在高架轨道上运行的桥架型起重机,一般由起重小车、桥架运行机构、桥架金属结构组成。
其桥架沿铺设在两侧高架上的轨道纵向运行,起重小车沿铺设在桥架上的轨道横向运行,构成一矩形的工作范围,就可以充分利用桥架下面的空间吊运物料,不受地面设备的阻碍。
箱形主梁,是起重机最重要的承载构件,其制造品质直接关系到起重机的承载能力。
桥式起重机主梁在制造过程中,容易出现焊接变形,影响生产和装配。
研究其焊接特性及制造工艺,对实现主梁制造的系列化、提高起重机质量、促进产品的技术进步有着积极的作用。
1.主梁结构分析主梁上包括了上拱的起始点、跨距、跨距中心、轮架支承等桥架的基准点线。
而桥架的技术参数,如桥架的水平度、对角线、主梁的上拱度、旁弯、大车轨距、小车轨距、轨道的偏心度、直线度以及同一断面差等都是以主梁头部的轮架中心为基准的。
桥架总装是以主梁头部为基准面划出基准点线,找正配装端梁来完成的。
单根主梁制造时,从预制上拱到最后的交验,也全部是以主梁头部为基准的。
因此,主梁结构的焊接是起重机制造过程的一个重要环节。
1.1桥式起重机及箱形主梁截面4089d4df29198bbc7dd924c862d3d49a4089d4df29198bbc7dd924c862d3d49a1.2材料箱型主梁材质采用Q235-B成分及力学性能须符合《低合金高强度结构钢》的规定。
对于厚度≥4 0mm的钢板,足Z向性能要求,达到Z15焊材的选用:主基本上为Q235-B钢,手工焊接时采用E4316焊条,自动焊时采用H08A焊丝、HJ431焊剂,CO2气体保护焊接时采用ER50-6焊丝。
焊条,焊丝,焊剂和焊接保护气体,所有焊接材料必须符合设计要求及规范要求。
- 1、下载文档前请自行甄别文档内容的完整性,平台不提供额外的编辑、内容补充、找答案等附加服务。
- 2、"仅部分预览"的文档,不可在线预览部分如存在完整性等问题,可反馈申请退款(可完整预览的文档不适用该条件!)。
- 3、如文档侵犯您的权益,请联系客服反馈,我们会尽快为您处理(人工客服工作时间:9:00-18:30)。
主梁结构件制造工艺1. 主梁工艺概述:1.1 结构的基本形式:窄翼缘板通用桥式起重机的主梁,主要是由上下盖板、两块腹板、大小筋板和工艺角钢(板条)等板、型材焊接而成的正(偏)轨箱形结构。
1.2 主梁制造要点:主梁制成后要有一定的上拱度和一定的水平外旁弯。
在制作过程中应通过腹板下料预制上拱度,并在组装焊接过程加以控制而达到其要求。
2. 工艺技术要求:为了确保主梁生产质量,建立主梁生产工序质量停检点制度。
见表1。
表1 主梁生产工序质量停检点2.1 下料及拼板要求:2.1.1 主梁的受拉盖板在跨中央左右各1m的范围内不得有对接焊缝(即各盖腹板的对接焊缝不允许在此处)。
2.1.2 主梁盖板和腹板的对接焊缝必须至少相互错开200mm。
两腹板(或两盖板)的对接焊缝允许在同一截面上。
2.1.3 横向拼接宽度应大于300mm。
2.1.4 纵向拼接长度应大于1000mm。
2.1.5 拼接焊缝要离开变截面处100mm以上。
或按图样及工艺技术特殊要求来进行拼板。
2.1.6 小筋板与上盖板、腹板的对接焊缝,工作级别A6以下的应错开50mm 以上,工作级别A6或A6以上的应错开100mm以上。
2.1.7 大筋板与上下盖板、腹板的对接焊缝应错开100mm以上(工作级别小于A6)。
工作级别A6和A6以上的应错开150mm以上。
标准型的主梁两端(上盖板内侧,距腹板的边缘100处),各增加一块补强板。
尺寸为:6×梁内宽度×(100~200或为梁内小筋板的高度的一半)。
2.1.9 加强圈可采用拼接制成,但接口处焊缝必须与所相关的腹板或筋板的焊缝错100mm以上。
2.1.10 若图样中下盖板两端在主梁变截面处有厚度减薄的要求,下料时均统一按下盖板中间部分的厚度下料。
2.1.11 筋板的拼接筋板是否可以拼接,首先应按图纸要求。
如图中无特别要求时,则可按如下要求进行:工作级别A6以下(包括A6)的筋板可以拼接,但是焊缝必须保证焊透,同时要求对接焊缝离圆角10mm以上,拼接后筋板的外形尺寸要求参照公司通用技术规范《钢材表面预处理、下料工艺守则》中剪切下料偏差执行。
工作级别A7(包括A7)以上的可以采用数控整体下料。
2.1.12 筋板倒角倒角形式可圆角、斜角、弧角及不规则角。
选择的大小要保证焊缝定位焊后,焊工施焊时焊条或焊嘴通过筋板下焊缝连续焊接不受影响。
(当δ≤12mm时,剪切倒角小,圆角半径或斜角直边不大于25mm;当δ〉12mm 时,圆角半径或斜角直边推荐在25~45mm内,用气割倒圆角要画好线,尺寸可稍微放大,控制倒角速度;非重要构件的小筋板,边长一般在100mm以下,可不必专门标注倒角。
2.1.13 工艺余量主梁盖板、腹板下料时要留有工艺余量:主要是指为满足主梁最后的交检尺寸长度的准确及保证焊接构件的焊缝收缩量(0.5/1000~1/1000),而在跨度S尺寸的基础上而多加的二次下料的余量(待装配时再割除)。
其余量值按下表2选取:表2:2.1.14 腹板上拱余量(F下)按表3规定选取。
上拱值与跨度中心板厚、焊脚、工艺规范参数的大小及焊接工艺方法、焊接顺序等因素有关。
因此,在制造过程中也必须注意上述因素, 最终使产品的跨中上拱度达到公司的检验标准(若合同有特别要求时,应按合同要求执行)。
2.1.15 同一用户、同一型号的产品的预拱度值应一致,最后检查验收也应符合同一标准。
2.2 装配焊接∏型梁装配焊接∏型梁,有以上盖板为基准面和以腹板为基准面两种组装方法。
以上盖板为基准面进行装配的工艺过程如下:2.2.1 划线将上盖板平铺在平台或地面上,先划出跨度中心、盖板中心、两侧腹板及各筋板的位置等线;并要求其粉线<0.75 mm、石笔线<0.5 mm粗细。
筋板位置划线应考虑主梁纵向焊接收缩量(0.5/1000—1/1000),避免累积而造成筋板最终在焊完后错位。
2.2.2 组装各筋板装配定位焊大小筋板,保证其与盖板的垂直度,筋板与盖板间应贴紧,间隙≤0.5mm,筋板侧向位置偏差保证筋板中心线与盖板中心线偏离≤0.5mm,筋板沿盖板纵向位置偏离划线≤2mm,筋板纵向前后倾斜<10mm。
筋板侧向与盖板的垂直度以内侧(无走台侧)为基准a≤2H/1000;如超差,可采取筋板下垫铁丝或锤打筋板一角延展方法调整。
自检符合要求后,方可定位焊筋板。
2.2.3 焊接各筋板与上盖板的角焊缝为了保证预制旁弯,焊接方向从无走台侧向有走台侧焊接。
焊后要修整上盖板与筋板焊接变形。
使焊缝处不得向主梁内部凹陷,且使大筋板与上盖板保持垂直。
)及Π形梁装配下盖板后的拱度值表3:5~100t腹板的下料(F下注:1.斜线下为50t的拱度值。
2.表内数值为参考值。
2.2.2 组装各筋板装配定位焊大小筋板,保证其与盖板的垂直度,筋板与盖板间应贴紧,间隙≤0.5mm,筋板侧向位置偏差保证筋板中心线与盖板中心线偏离≤0.5mm,筋板沿盖板纵向位置偏离划线≤2mm,筋板纵向前后倾斜<10mm。
筋板侧向与盖板的垂直度以内侧(无走台侧)为基准a≤2H/1000;如超差,可采取筋板下垫铁丝或锤打筋板一角延展方法调整。
自检符合要求后,方可定位焊筋板。
2.2.3 焊接各筋板与上盖板的角焊缝为了保证预制旁弯,焊接方向从无走台侧向有走台侧焊接。
焊后要修整上盖板与筋板焊接变形。
使焊缝处不得向主梁内部凹陷,且使大筋板与上盖板保持垂直。
2.2.4组装腹板根据一台起重机两根主梁的四张腹板实测拱度值,确定配对和吊放部位(拱度值偏高者应放在主梁内侧)腹板吊装前划好中心点。
腹板配对方法:例如5t、22.5m跨度的主梁腹板下料拱度值F=70mm,四张腹板(a、b、c、下d)下料后的实测拱度分别为:Fa=73mm. Fb=66mm. Fc=70mm.Fd=67mm,则应a与c配成一根梁,b与d配成一根梁,这样可减小或避免一根主梁两腹板高低差过大。
2.2.4.1 将腹板平铺在平台或地面上,划出跨中心线,筋板、加强角钢(工艺板条)等位置线。
加强角钢与工艺板条等纵向加筋线要与腹板的上拱线一致也带有拱度。
2.2.4.2 以腹板为基准面,按放线位置和图样要求装配定位并焊接加强角钢(或板条),注意角钢或板条与腹板间要贴紧,间隙≤0.5mm。
或将加强角钢(板条)先装配焊接在筋板的角钢(穿孔)相关位置(要保证筋板外缘直线性),再组装定位焊两侧腹板。
加强角钢是否先与腹板焊接、还是在组成∏型梁后焊接,应视其主梁的结构尺寸大小(组成∏型梁后焊工能否便于施焊)、便于控制腹板的波浪变形等情况来定。
原则是应在组成∏型梁后焊接或先只焊角钢与腹板的靠近上盖板侧焊缝。
且必须按图中规定的焊缝要求进行焊接,不得随意改变焊缝尺寸,不得用大直径焊条及大电流,重点是控制腹板的波浪变形。
同时对于图中纵向加筋是断开时也要将其两端用连接板与大筋板焊接上,连接板应与纵向加筋等强,并与腹板贴紧,间隙≤0.5mm。
2.2.4.3 装配定位焊腹板将一腹板吊装在上盖板(筋板)上进行组装,使腹板的跨中心线与盖板上的跨中心线对准后由跨中向两端定位焊接腹板(装配中必须随时使腹板与筋板靠严后再进行定位焊)。
具体方法是:从中间向一端,用加垫、撬、打揳等方法,将上盖板撬起与腹板接触,间隙≤0.5mm,并用撬杠将腹板与筋板靠紧,间隙≤0.5mm,然后定位焊于盖板、筋板上。
一端定位焊好后再由中间向另一端用同样方法进行装配定位焊。
然后再以同一方法组装另一腹板。
2.2.5 有关工艺板条的规定当腹板用普板或卷板材料(板厚为6mm)时,为控制腹板的波浪变形,在小筋板或角钢至腹板下沿的尺寸大于650mm(普板)或500mm(卷板)时可加工艺板条。
2.2.5.1 必须是6~8mm板厚的边角余料剪切制成(或利用现有废条料)。
2.2.5.2 工艺板条的宽度60mm,长度拼接接头为对接焊缝(不得搭接)。
2.2.5.3 工艺板条应穿过筋板(不能断开);工艺板条与腹板对接焊缝相交时,应在工艺板条上割出圆弧缺口避开焊缝,以保证其直线度。
其装配定位、焊接等与2.2.4.2加强角钢的要求相同。
工艺板条与腹板的焊接的焊脚尽量小些(≤4mm),A6以下(包括A6)为交错断续焊缝100(300);A7(包括A7)以上为连续焊缝。
2.2.6 焊接∏型梁内缝:2.2.6.1 将∏型梁无走台侧朝下垫平放在平台上。
2.2.6.2 ∏型梁两相邻大筋板构成的格,按焊工平均分开,最好每人一格,依焊接方向和次序进行焊接,为使受热均匀,焊接时尽量同时焊接。
人少时可采用分中反方向焊接法或分段焊接法以减少变形。
2.2.6.3 焊完一面翻转后,用同样方法焊接另一面(走台侧)。
2.2.7 ∏型梁的综合检查:2.2.7.1检测∏型梁跨中的上拱度和每大筋板处的上拱度值。
2.2.7.2 检测∏型梁的旁弯大小,使其水平弯曲控制在f=L/1500~L/2500范围内。
2.2.7.3 检测每大筋板处腹板倾斜值。
2.2.7.4 检测跨中大筋板处(如跨中无大筋板可在跨中左右筋板处)和两端长筋处上盖板的水平倾斜值。
将测量值用石笔记在上盖板和腹板上作为调整的依据2.3 装配下盖板2.3.1 将下盖板放在平台上,划出跨中心线及∏型梁(两腹板)的位置线。
组装下盖板前应做到:2.3.1.1 ∏型梁与下盖板的旁弯方向和大小要相一致;如果∏型梁与下盖板的旁弯方向相反,不能与下盖板组装,必须进行调整(允许用火焰矫正的方法调整)。
2.3.1.2 ∏型梁腹板如有较大凹陷波浪,可将∏型梁凹陷部分进行火焰矫正。
2.3.1.3 将∏型梁吊放在下盖板上,使∏型梁的中心线与下盖板的中心线重合,支垫处下盖板两边的边缘要相等。
也可将∏型梁根据拱度要求垫好后吊放下盖板。
2.3.2 组装定位焊下盖板2.3.2.1 由跨中开始,两边同时施工,使用撬杠将下盖板顶起,两边盖板边缘距腹板距离要相等,保证腹板与盖板间装配线偏离划线最大距离≤1mm,盖板与腹板间隙≤1mm,斜面处间隙<2mm后,方可定位焊。
2.3.2.2 四条纵向角焊缝的定位焊可采用手工电弧焊,焊角K为4mm,定位焊缝长30~40mm,定位焊间距<400mm。
2.3.3 箱型梁的综合检查(组装定位焊下盖板后、在焊接四条纵焊缝前的检查):检查主梁上拱度及旁弯;检查主梁大筋板处腹板倾斜≤H/250,盖板跨中大筋板处(无大筋板为跨中近处两大筋板)和两端大筋板处倾斜≤B/250。
2.4 主梁翼缘四条主焊缝的焊接2.4.1 将主梁侧放垫平,进行埋弧自动焊接。
2.4.2 焊接顺序:原则上是:先焊下翼缘,后焊上翼缘焊缝;先焊无走台侧,后焊有走台侧(指埋弧焊);如拱度水平弯曲异常,可随时调整焊接顺序。
2.4.3 四条主焊缝的焊接方向应一致。
2.5 主梁端部的焊接:2.5.1 斜稍焊缝,在主梁放倒后手工焊接。