车架检验标准
车架检验规范
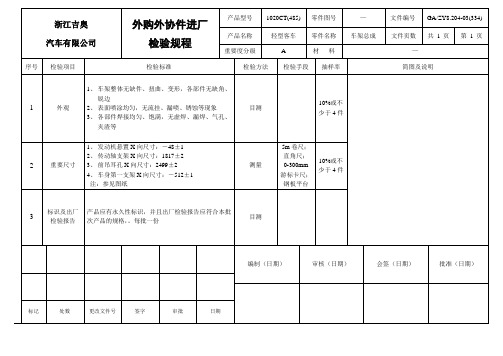
汽车有限公司
外购外协件进厂
检验规程
产品型号
1020CT(485)
零件图号
—
文件编号
GA/ZY8.204-03(334)
产品名称
轻型客车
零件名称
车架总成
文件页数
共1页
第1页
重要度分级
A
材料
—
序号
检验项目
检验标准
检验方法
检验手段
抽样率
简图及说明
1
外观
1、车架整体无缺件、扭曲、变形,各部件无缺角、锐边
10%或不少于4件
3
标识及出厂检验报告
产品应有永久性标识,并且出厂检验报告应符合本批次产品的规格,。每批一份
目测
编制(日期)
审核(日期)
会签(日期)
批准(日期期
2、表面喷涂均匀,无流挂、漏喷、锈蚀等现象
3、各部件焊接均匀、饱满,无虚焊、漏焊、气孔、夹渣等
目测
10%或不少于4件
2
重要尺寸
1、发动机悬置X向尺寸:-48±1
2、传动轴支架X向尺寸:1817±2
3、前吊耳孔X向尺寸:2499±2
4、车身第一支架X向尺寸:-512±1
注:参见图纸
测量
5m卷尺;直角尺;0-300mm游标卡尺;钢板平台
摩托车车架外观标准
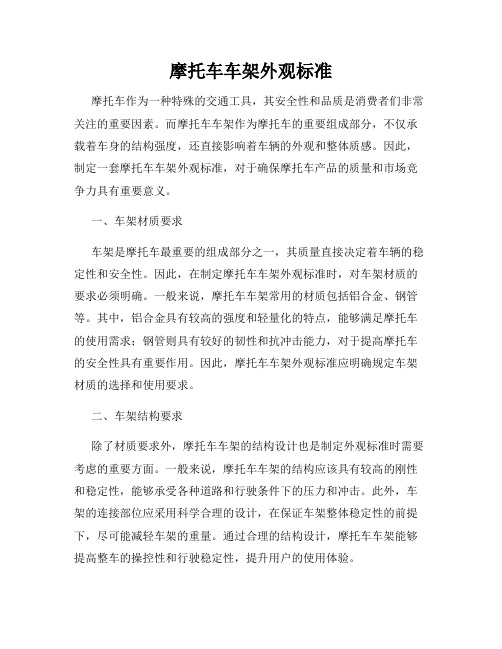
摩托车车架外观标准摩托车作为一种特殊的交通工具,其安全性和品质是消费者们非常关注的重要因素。
而摩托车车架作为摩托车的重要组成部分,不仅承载着车身的结构强度,还直接影响着车辆的外观和整体质感。
因此,制定一套摩托车车架外观标准,对于确保摩托车产品的质量和市场竞争力具有重要意义。
一、车架材质要求车架是摩托车最重要的组成部分之一,其质量直接决定着车辆的稳定性和安全性。
因此,在制定摩托车车架外观标准时,对车架材质的要求必须明确。
一般来说,摩托车车架常用的材质包括铝合金、钢管等。
其中,铝合金具有较高的强度和轻量化的特点,能够满足摩托车的使用需求;钢管则具有较好的韧性和抗冲击能力,对于提高摩托车的安全性具有重要作用。
因此,摩托车车架外观标准应明确规定车架材质的选择和使用要求。
二、车架结构要求除了材质要求外,摩托车车架的结构设计也是制定外观标准时需要考虑的重要方面。
一般来说,摩托车车架的结构应该具有较高的刚性和稳定性,能够承受各种道路和行驶条件下的压力和冲击。
此外,车架的连接部位应采用科学合理的设计,在保证车架整体稳定性的前提下,尽可能减轻车架的重量。
通过合理的结构设计,摩托车车架能够提高整车的操控性和行驶稳定性,提升用户的使用体验。
三、外观造型要求摩托车作为一种个性化较强的交通工具,其外观造型在市场竞争中具有重要的影响力。
因此,在制定摩托车车架外观标准时,需要明确外观造型的要求。
摩托车车架的外观应符合人体工程学原理,保证骑车人的舒适感和操作便捷性。
同时,车架的整体造型应该流畅、美观,体现摩托车的动感和运动性能。
对于前叉、车把等附属部件的设计也应考虑整体外观的协调性,形成统一的车架外观标准。
四、表面处理要求为了保护车架材料免受氧化、腐蚀等因素的影响,同时增加车架的美观度和耐久性,摩托车车架外观标准应规定车架的表面处理要求。
一般来说,车架的表面处理可以采用喷涂、电镀等方式,形成均匀、光滑、无明显瑕疵的外观。
同时,表面处理的颜色和质感应与整车的外观设计相协调,体现摩托车的品牌形象。
电动车外购外协零部件检验规程2(车架及前叉)(20111028版)

1.适用范围适用于对外协车架、前叉的检验。
2.检验规则2.1装配尺寸按1件/批进行随机抽样检验,若有不符则加倍抽检。
2.2车架精度按出口车8件/批、内销车4件/批进行随机抽样检验,出口车若项次合格率达到87.5%(出口车)、75%(内销车),则判批量合格;若项次合格率低于85%(出口车)、75%(内销车)则加倍抽样检验,根据检验结果进行判定。
如果车架一个批次订单数量少于30台(含),按4件/批检验。
前叉精度按5件/批检验,合格率达到80%,则判批量合格。
3.质量要求及检验规程3.1车架3.1.1车架毛坯外观3.1.1.1无接头车架焊缝应匀称、饱满、连续,不得有气泡、飞溅物。
3.1.1.2螺纹处不得有烂牙、碰伤现象。
3.1.1.3正视面表面应光洁,不得有瘪塘、锈斑、裂纹、粗丝流、飞溅物、锐边、毛刺、缩颈等缺陷。
3.1.1.4非正视面不得有下列缺陷:瘪塘面积大于0.5cm2、锈斑直径大于φ2mm、毛刺高于0.3mm、裂纹、缩颈。
3.1.1.5车架应符合产品图样及工艺文件的要求。
3.1.2车架光坯外观(油漆件)3.1.2.1车架正视面不允许有下列缺陷:油漆龟裂、脱漆、漏漆、积集砂粒、皱皮、擦毛碰伤、大面积焊渣、严重流疤、瘪塘。
3.1.2.2非正视面不得有擦毛碰伤大于0.5cm22处;脱漆面积大于1cm2;积集砂粒面积大于1 cm2,漏漆面积大于1 cm2;瘪塘面积大于0.5 cm2。
3.2.1前叉毛坯外观3.2.1.1前叉焊缝应匀称、饱满、连续,不得有气泡、飞溅物。
3.2.1.2螺纹不得有烂牙、碰伤等现象。
3.2.1.3正视面应光洁,不得有瘪塘、裂纹、粗丝流、飞溅物、锐边、毛刺、锈斑、焊缝凹陷等缺陷。
3.2.1.4非正视面不得有下列缺陷:瘪塘面积大于0.4cm2;锈斑直径大于φ2mm;毛刺高于0.3mm及裂纹等缺陷。
3.2.1.5前叉应符合产品图样及工艺文件的要求。
3.2.2前叉光坯外观3.2.2.1前叉正视面不允许有下列缺陷:油漆龟裂、脱漆、漏漆、积集的砂粒、皱皮、擦毛碰伤、大面积焊渣、瘪塘、严重流疤。
乘用车的强制检验标准

乘用车的强制检验标准一、车辆外观检验1.车辆外观应整洁,无损坏、锈蚀、变形、裂纹等缺陷。
2.车体各部位色泽应一致,无明显色差。
3.车身及车架等部位无明显碰撞痕迹或变形。
4.漆面应无起泡、龟裂、脱落等现象。
5.车身对称部位应无明显差异。
二、车辆底盘检验1.底盘应整洁,无损坏、锈蚀、变形等缺陷。
2.发动机、变速箱、传动轴等部件应无明显异响、振动或松动。
3.底盘各部件连接应牢固,无松动或脱落现象。
4.车辆悬挂系统应无损坏、变形或松动。
5.车辆转向系统应操纵灵活,无卡滞或异常噪音。
三、车辆排放检验1.车辆排放应符合国家相关标准,不得超过规定限制。
2.尾气排放不得有异味、烟尘、浓黑等情况。
3.车辆排气系统应无明显堵塞、破损等现象。
4.燃油供给系统应保证燃油喷射、雾化等过程的正常进行。
5.车辆发动机应无明显异常噪音或振动。
四、车辆安全检验1.车辆安全装置应齐全,包括制动系统、转向系统、悬挂系统等。
2.制动性能应符合国家相关标准,制动距离短,制动稳定。
3.车辆照明及信号装置应符合国家相关标准,确保夜间行驶安全。
4.安全带应完好无损,符合国家相关标准。
5.车辆轮胎应完好无损,符合国家相关标准。
五、车辆电气设备检验1.车辆电气设备应完好无损,工作正常。
2.发电机、起动机、点火系统等部件应工作正常,确保车辆启动和行驶过程中的电力供应。
3.空调系统应制冷效果好,出风口温度适宜。
4.音响、导航等娱乐设备应工作正常,确保乘客出行过程中的舒适与便利。
自卸车检验指导书

1.生产过程检验1.1副车架总成检验规范1.1.1.检验项目及标准1.1.1.1车架长度公差±5mm,宽度公差负1-3毫米。
用钢卷尺测量。
1.1.1.2车架下平面平面度≤4mm。
1.1.1.3两纵梁直线度任意5米内≤4mm。
5-7米≤6mm。
7米以上≤8mm。
1.1.1.4翻转轴孔中心相对于纵梁底平面误差≤1mm。
1.1.1.5翻转轴孔轴向与总量垂直度≤1度。
1.1.1.6翻转轴套两端相对于两纵梁中心线对称度≤2mm。
1.1.1.7油缸支座中心与两纵梁中心左右偏差不大于2mm。
1.1.1.8油缸支座至后翻转轴套两端距离差不大于5mm。
1.1.1.9底架对角线差≤5mm。
1.1.1.10外观要求:平整;清洁;无焊丝头、氧化铁;无扭曲变形、锤痕、凹陷等外观缺陷。
焊缝应美观,洁净不得有焊瘤、咬边、气孔、夹渣、假焊、偏焊、漏焊,焊缝标准应达到厂标二级以上标准。
1.1.2.对以上检验项目的说明1.1.2.1以上检验项目由生产班组先进行自检,然后由检验员进行专检。
1.1.2.2以上检验项目的检查必须采用全检的方法.有一项不合格就不能进行下道工序。
1.1.2.3检验员必须做到认真检验,严格要求,并做好检验记录。
1.1.2.4以上检验项目用250×500mm直角弯尺;5米、20米钢卷尺。
1.2底架总成检验规范1.2.1.检验项目及标准1.2.1.1板材厚度符合国家GB/T1222-1989规定标准。
底架总长度±5mm,底板宽度±3mm。
两纵梁宽度公差负2-4mm。
1.2.1.2两纵梁纵向中心与底板纵向中心错移量≤3mm。
1.2.1.3底架总体6米以内平面度≤3mm。
6米以上平面度≤5mm。
1.2.1.4焊后变形允许有一定上拱,上拱高度≤2mm。
不允许下塌。
1.2.1.5两纵梁下端平面到底板两侧距离差≤5mm。
1.2.1.6底架对角线差≤5mm。
1.2.1.7主托架工作面距纵梁下表面距离±1mm。
车架检验标准汇总

车架检验标准1. 适用范围1.1 本标准适用于无锡市志达车业有限公司车架外购配件入厂时的检验。
1.2 对于不同款式的车架,可根据本标准附件《各型车架检验标准汇总》的具体要求进行检验。
2. 通用技术要求2.1 外观质量2.1.1 车架各部位不得有锐边,毛刺。
2.1.2 车架外表面不得有明显的划伤,碰伤,变形。
2.1.3 对于外露车架其表面漆膜应符合QB/T1218标准(正视面不得有龟裂和明显的流疤,集结的沙粒,皱皮,漏漆等缺陷)。
2.2 焊接要求2.2.1 各焊接处不得有漏焊,焊缝不规范,不充分及长度不够(在重点部位不得缺少3mm)等现象,安装塑件的固定片不得缺焊50%以上。
2.2.2 焊接面不得处于不合理受力状态,不得产生不能复原的变形。
2.2.3 不允许有虚焊,虚堆。
2.2.4 焊接应该采用二氧化碳保护焊和氩弧焊。
2.4 精度要求2.4.1车架立管平行度车架立管轴线应在车架中心基准面上,其公差值为1.8mm.2.4.2车架中接头垂直度车架中接头轴线与车架中心基准面应垂直,公差值为2mm。
2.4.3车架上、下、立管直线度车架上、下、立管直线度在300mm内,公差值为1mm。
2.4.4 车架立管轴线与车架尾部中心线误差不大于3 mm。
2.4.5 车架中心线与平叉固定板中心线垂直度不大于2 mm。
2.4.6 车架中心线与中轴中心线垂直度不大于2 mm。
2.4.7 中轴与平叉中心线平行度误差不大于2 mm。
2.5 对于具体的车型,如果出现与通用标准不符的情况,应该以具体款式的要求为准。
可参加本标准附件的要求进行。
3. 检验规则3.1 采用GB2828标准一次抽样,达到技术要求为合格品。
4. 关于材料的通用要求:4.1车架的钢管材料:为Q195(GB/T—700)。
4.2凡是使用钢板制造的车架附件,应该符合冷轧钢板GB 708-88的要求。
4.3 偏撑、中撑弹簧材料:弹簧钢65Mn。
4.4 偏撑、中撑轴为35#钢;调质,HB=180~220。
车架检验标准汇总
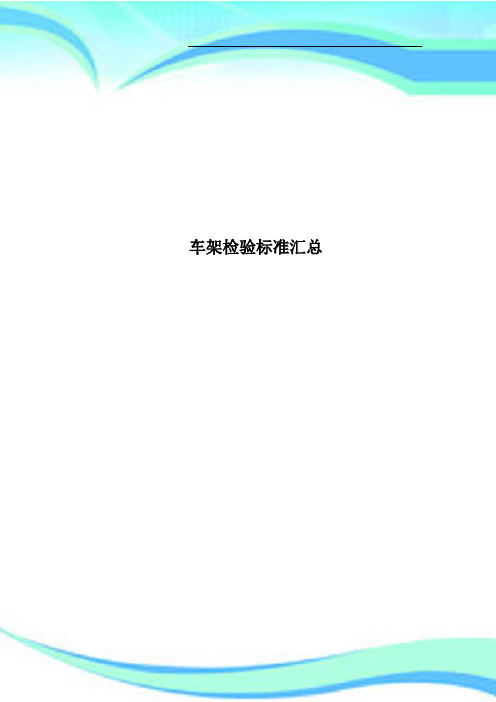
悍马车架检验标准11
悍马二代车架检验标准ﻩ13
世纪凌鹰车架检验标准15
B公主车架检验标准ﻩ16
圆梦车架检验标准ﻩ18
760车架检验标准20
小王子车架检验标准ﻩ21
小旋风车架检验标准ﻩ23
爱虎车架检验标准24
小雨点车架检验标准ﻩ25
中华海棠车架检验标准27
小帅哥车架检验标准29
小帅哥(电摩)车架检验标准…………………………………………………………………..40
风暴阳光(电摩)车架检验标准………………………………………………………………..41
五羊公主(助力车)车架检验标准…………………………………………………………….42
凌鹰(助力车)车架检验标准…………………………………………………………………..43
2.4.3车架上、下、立管直线度
车架上、下、立管直线度在300mm内,公差值为1mm。
2.4.4车架立管轴线与车架尾部中心线误差不大于3mm。
2.4.5车架中心线与平叉固定板中心线垂直度不大于2 mm。
2.4.6车架中心线与中轴中心线垂直度不大于2mm。
2.4.7中轴与平叉中心线平行度误差不大于2 mm。
2.通用技术要求
2.1外观质量
2.1.1车架各部位不得有锐边,毛刺。
2.1.2车架外表面不得有明显的划伤,碰伤,变形。
2.1.3对于外露车架其表面漆膜应符合QB/T1218标准(正视面不得有龟裂和明显的流疤,集结的沙粒,皱皮,漏漆等缺陷)。
2.2焊接要求
2.2.1各焊接处不得有漏焊,焊缝不规范,不充分及长度不够(在重点部位不得缺少3mm)等现象,安装塑件的固定片不得缺焊50%以上。
3.4各焊接处必须符合焊接要求,焊缝不得小于两工件的2/3,焊缝需平整、均匀,不得有焊缝不规范、不充分、长度不够、跑偏等现象。
挂车质量检验规范

挂车质量检验规范挂车质量检验规范一、引言挂车作为一种特殊的道路车辆,在运输行业起着重要的作用。
为了确保挂车的质量安全和道路行驶的安全性,需要对挂车进行质量检验。
本详细介绍了挂车质量检验的规范,包括检验原则、检验内容、检验方法等,旨在提供一个全面的参考指南。
二、检验原则1. 安全性原则:挂车的构造、材料、创造工艺等应符合相关安全标准,确保车辆在行驶过程中具备良好的安全性。
2. 可靠性原则:挂车的各个部件及系统应具备可靠性,能够经受长期使用和道路的各种复杂环境。
3. 经济性原则:挂车的创造成本、使用成本和维修成本应在合理范围内,以实现经济效益。
三、检验内容1. 车身结构检验:(1) 车架结构检验:检查挂车车架的创造工艺和材料,确保车架具备足够的强度和刚度。
(2) 车身外观检验:检查挂车外观的整体质量和工艺,包括车身平整度、涂装质量等。
2. 箱体检验:(1) 箱体结构检验:检查挂车箱体的创造工艺和材料,确保箱体具备足够的刚度和密封性。
(2) 箱体内部检验:检查挂车箱体内部的装备设施,包括货物固定装置、防滑设施等。
3. 制动系统检验:(1) 制动力检验:检查挂车制动系统的制动力是否符合标准要求,确保制动性能良好。
(2) 制动灵敏度检验:检查挂车制动系统的灵敏度是否符合标准要求,确保操作方便准确。
4. 灯光系统检验:(1) 示廓灯检验:检查挂车示廓灯的亮度和位置是否符合标准要求,确保夜间行驶的安全性。
(2) 制动灯检验:检查挂车制动灯的亮度和位置是否符合标准要求,确保其他车辆能够准确识别制动情况。
(3) 转向灯检验:检查挂车转向灯的亮度和位置是否符合标准要求,确保转向行驶时的安全性。
5. 悬挂系统检验:(1) 悬挂装置检验:检查挂车的悬挂装置是否符合标准要求,确保车辆悬挂系统具备良好的稳定性和舒适性。
(2) 后桥检验:检查挂车后桥的创造工艺和材料,确保后桥具备足够的强度和可靠性。
6. 轮胎系统检验:(1) 轮胎磨损检验:检查挂车轮胎的磨损情况,确保轮胎具备良好的抓地力和耐久性。
Q YD 007 车架标准

T 80备案号:浙江雅迪机车有限公司企业标准Q/YD 007—2011代替Q/YD 007—2010两轮车车架2011-04-18发布 2011-04-20实施浙江雅迪机车有限公司发布前言本标准由浙江雅迪机车有限公司提出。
本标准起草单位:浙江雅迪机车有限公司技术与产品规划部。
本标准主要起草人:邹万福本标准所代替的历次版本发布情况为:——Q/YD 007—2010两轮车车架1 范围本标准规定了摩托车和轻便摩托车(以下简称:摩托车)、电动摩托车和电动轻便摩托车(以下简称:电摩车)车架的术语和定义、要求、试验方法、检验规则、标志、包装与运输、贮存。
本标准适用于摩托车和电摩车车架(以下简称:车架);也适用于电动自行车和汽油机助力自行车车架。
2 规范性引用文件下列文件中的条款通过本标准的引用而成为本标准的条款。
凡是注日期的引用文件,其随后所有的修改单(不包括勘误的内容)或修订版均不适用于本标准,然而,鼓励根据本标准达成协议的各方研究是否可使用这些文件的最新版本。
凡是不注日期的引用文件,其最新版本适用于本标准。
GB/T 700碳素结构钢GB/T 1732—1993漆膜耐冲击性测定法GB/T 1733—1993漆膜耐水性测定法GB/T 1771—2007色漆和清漆耐中性盐雾性能的测定GB/T 1184—1996 形状和位置公差未注公差值GB/T 1804—2000 一般公差未注公差的线性和角度尺寸的公差GB/T 2828.1—2003计数抽样检验程序第1部分:按接收质量限(AQL)检索的逐批检验抽样计划GB/T 4955—2005金属覆盖层覆盖层厚度测量阳极溶解库伦法GB/T 5270—2005金属机体上的金属覆盖层电沉积和化学沉积层附着强度试验方法评述GB/T 6461—2002 金属机体上金属和其他无机覆盖层经腐蚀试验后的试样和试件的评级GB/T 6728—2002结构用冷弯空心型钢尺寸、外形、重量及允许偏差GB/T 6739—2006色漆和清漆铅笔法测定漆膜硬度GB/T 8162—2008结构用无缝钢管GB/T 9286—1998色漆和清漆漆膜的划格试验GB/T 9790—1998金属覆盖层及其他有关覆盖层维氏和努氏显微硬度试验GB/T 10125—1997人造气氛腐蚀试验盐雾试验GB/T 12467.1—2009金属材料熔焊质量要求第1部分:质量要求相应等级的选择准则GB/T 12467.2—2009金属材料熔焊质量要求第2部分:完整质量要求GB/T 12467.3—2009金属材料熔焊质量要求第3部分:一般质量要求GB/T 12467.4—2009金属材料熔焊质量要求第4部分:基本质量要求GB/T 13452.2—2008 色漆和清漆漆膜厚度的测定GB/T 13793—2008直缝电焊钢管GB/T 15367—2008 摩托车和轻便车两轮车和三轮车零部件名称GB/T 19804—2005 焊接结构的一般尺寸公差和形位公差QC/T 819—2009 两轮摩托车和两轮轻便摩托车车架QB 1880—2008 自行车车架3 术语和定义下列术语和定义适用于本标准3.1 两轮车装有一个驱动轮和一个从动轮,一般可用于公路或城市道路上行驶的车辆。
车架布纹外观检验标准
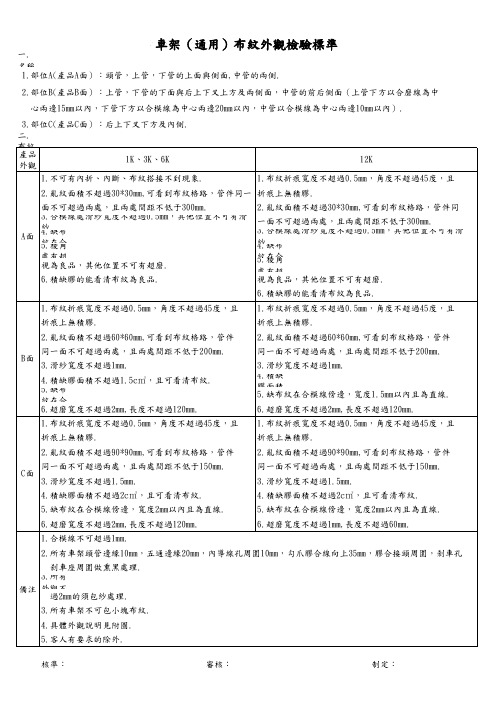
一.名稱定義
二.布紋檢驗標準
.長度不超過60mm 2mm ,超
核準: 審核:制定:200mm...
45度,且車架(通用)布紋外觀檢驗標準
3.部位C(產品C 面):后上下叉下方及內側.
1.部位A(產品A 面):頭管,上管,下管的上面與側面,中管的兩側.
心兩邊15mm 以內,下管下方以合模線為中心兩邊20mm 以內,中管以合模線為中心兩邊10mm 以內).
2.部位B(產品B 面):上管,下管的下面與后上下叉上方及兩側面,中管的前后側面(上管下方以合磨線為中45度,且45度,且150mm...
A 面:車架的上下管兩側,頭管的外側,中管的兩側(如上圖)
B 面:中心兩邊20mm 以內,后上下叉上方及兩側面
上管下方以合磨線為中心兩邊30mm 以內,下管下方以合模線為中心兩邊40mm 以內,中管以合磨線為更多免费资料下载请进: 車架左側面(A 面)車架右側面(A 面)車架上管上側(
A 面)車架下管上側(A 面)
車架上管下側(B 面)車架下管下側(B 面)
30mm 40mm
20mm
車架中管合模線周圍20mm 以內(B 面)后上下叉上方及兩側面(B 面)。
汽车零部件验收及全套检验标准
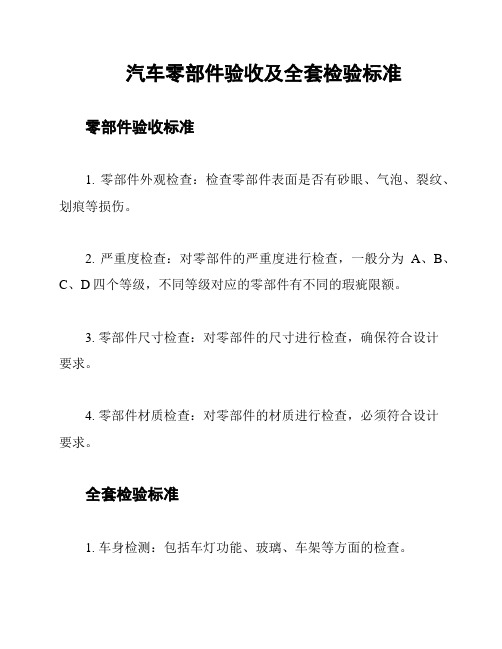
汽车零部件验收及全套检验标准零部件验收标准
1. 零部件外观检查:检查零部件表面是否有砂眼、气泡、裂纹、划痕等损伤。
2. 严重度检查:对零部件的严重度进行检查,一般分为A、B、
C、D四个等级,不同等级对应的零部件有不同的瑕疵限额。
3. 零部件尺寸检查:对零部件的尺寸进行检查,确保符合设计
要求。
4. 零部件材质检查:对零部件的材质进行检查,必须符合设计
要求。
全套检验标准
1. 车身检测:包括车灯功能、玻璃、车架等方面的检查。
2. 发动机检测:对发动机的性能进行测试,包括启动、怠速、
加速等方面。
3. 制动系统检测:对制动系统性能进行测试,确保制动力稳定。
4. 悬挂系统检测:对悬挂系统进行检查,确保能够正常工作。
5. 转向系统检测:对转向系统进行检查,确保能够正常工作。
6. 轮胎检测:对轮胎进行检查,检查轮胎的花纹深度、磨损情况、气压等。
以上为汽车零部件验收及全套检验标准,供参考。
为确保行车
安全和质量,建议对汽车定期进行检查、保养和维修。
电动自行车检验标准
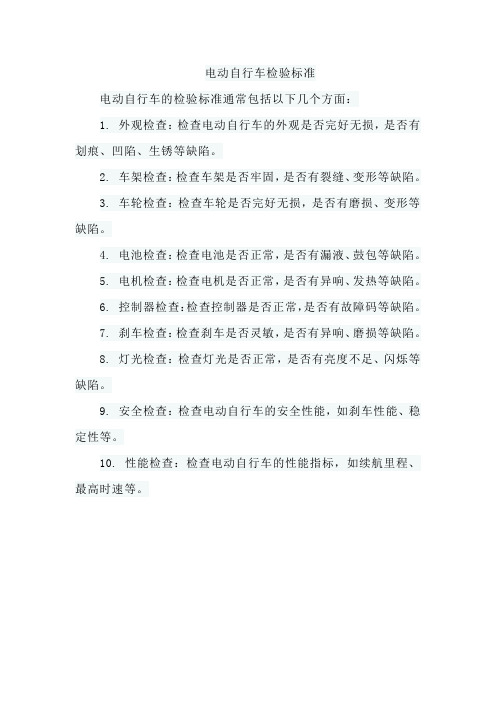
电动自行车检验标准
电动自行车的检验标准通常包括以下几个方面:
1. 外观检查:检查电动自行车的外观是否完好无损,是否有划痕、凹陷、生锈等缺陷。
2. 车架检查:检查车架是否牢固,是否有裂缝、变形等缺陷。
3. 车轮检查:检查车轮是否完好无损,是否有磨损、变形等缺陷。
4. 电池检查:检查电池是否正常,是否有漏液、鼓包等缺陷。
5. 电机检查:检查电机是否正常,是否有异响、发热等缺陷。
6. 控制器检查:检查控制器是否正常,是否有故障码等缺陷。
7. 刹车检查:检查刹车是否灵敏,是否有异响、磨损等缺陷。
8. 灯光检查:检查灯光是否正常,是否有亮度不足、闪烁等缺陷。
9. 安全检查:检查电动自行车的安全性能,如刹车性能、稳定性等。
10. 性能检查:检查电动自行车的性能指标,如续航里程、最高时速等。
车架检验标准汇总

车架检验标准1. 适用范围1.1本标准适用丁无锡市志达车业有限公司车架外购配件入厂时的检验。
1.2对丁不同款式的车架,可根据本标准附件《各型车架检验标准汇总》的具体要求进行检验。
2. 通用技术要求2.1外观质量2.1.1车架各部位不得有锐边,毛刺。
2.1.2车架外表面不得有明显的划伤,碰伤,变形。
2.1.3对丁外露车架其表面漆膜应符合QB/T1218标准(正视面不得有龟裂和明显的流疤,集结的沙粒,皱皮,漏漆等缺陷)。
2.2焊接要求2.2.1各焊接处不得有漏焊,焊缝不规范,不充分及长度不够(在重点部位不得缺少3mm)等现象,安装塑件的固定片不得缺焊50%以上。
2.2.2焊接面不得处丁不合理受力状态,不得产生不能复原的变形。
2.2.3不允许有虚焊,虚堆。
2.2.4焊接应该米用二氧化碳保护焊和氯弧焊。
2.4精度要求2.4.1车架立管平行度车架立管轴线应在车架中心基准面上,其公差值为 1.8mm.2.4.2车架中接头垂直度车架中接头轴线与车架中心基准面应垂直,公差值为2mm。
2.4.3车架上、下、立管直线度车架上、下、立管直线度在300mm内,公差值为1mm。
2.4.4车架立管轴线与车架尾部中心线误差不大丁 3 mm。
2.4.5车架中心线与平义固定板中心线垂直度不大丁 2 mm。
2.4.6车架中心线与中轴中心线垂直度不大丁2 mm。
2.4.7中轴与平义中心线平行度误差不大丁2 mm。
2.5对丁具体的车型,如果出现与通用标准不符的情况,应该以具体款式的要求为准。
可参加本标准附件的要求进行。
3. 检验规则3.1采用GB2828标准一次抽样,达到技术要求为合格品4. 关丁材料的通用要求:4.1车架的钢管材料:为Q195 (GB/T—700)。
4.2凡是使用钢板制造的车架附件,应该符合冷轧钢板GB 708- 88的要求。
4.3偏撑、中撑弹簧材料:弹黄钢65Mn。
4.4偏撑、中撑轴为35#钢;调质,HB= 180〜220。
过程检验指导书

编制
校对
审核
批准
年 月 日
检验项目
图片
检验标准
检测工具
检验方法
副车架安装
举升油缸支座必须与支架贴合无间隙,支座与油缸支撑轴内侧间隙≤2mm。
固定螺栓紧固可靠,螺栓紧固扭力矩为210±10N.m。螺栓为10.9级螺栓。
300N.m扭力扳手
油缸中心与副车架必须垂直(前举升);放大架机构与油缸连接轴到副车架两纵梁距离左右对称(腹举升)。
目测
编制
校对
审核
批准
年 月 日
检验项目
图片
检验标准
检测工具
检验方法
副车架总成检验
车架长度公差±5mm,宽度负公差1-3mm。
钢卷尺
目测
车架下平面平面度≤4mm。
直角尺
两纵梁直线度任意5M内≤4mm,5-7M内≤6mm,7M内≤8mm。
钢卷尺
翻转轴孔中心相对于纵梁低平面误差≤1mm。
钢卷尺
翻转轴孔轴向与纵梁垂直度≤1度。
直角尺
翻转轴套两端相当于两纵梁中心线对称度≤2mm。
钢卷尺
油缸支座中心与两纵梁中心左右偏差≤2mm。
钢卷尺
油缸支座至后翻转轴套两短距离差≤5mm。
钢卷尺
底架对角线误差≤5mm。
钢卷尺
外观平整;清洁;无焊丝头、氧化铁;无扭曲变形、锤痕、凹陷等外观缺陷。焊缝美观,不得有焊瘤、咬边、气孔、夹渣、假焊、偏焊、漏焊等,焊缝标准应达到相关标准。
目测
面漆面膜硬度以中华H型铅笔反复华4-5次不见明显划痕为宜。
目测
编制
校对
审核
批准
年 月 日
检验项目
图片
检验标准
电动车车架

××××股份有限公司企业标准电动车车架前言车架是电动车上的一个重要部件,其质量的好坏直接关系到用户人身安全。
目前尚无相关国家标准、行业标准,为统一本公司对车架的要求,结合本公司实际而制定本标准。
电动车车架1范围本标准规定了电动车用车架的整体结构形式、材料、规格、部件技术要求、部件焊接、表面涂装、车架检测及包装运输要求。
本标准适用于电动自行车车架、电动摩托车各型车架的设计、制造。
本标准中未涉及的部分按车型实际需要设计,同减震器、平叉、前叉连接部分的设计应满足该部品的设计标准需要。
2 规范性引用文件下列文件中的条款通过本标准的引用而成为本标准的条款,凡是注日期的引用文件,其随后所有的修改单(不包括勘误表)或修订版均不适用于本标准,然而,鼓励根据本标准达成协议的各方研究是否可使用这些文件的最新版本。
凡是不注日期的引用文件,其最新版本适用于本标准。
GB/T 196-2003 普通螺纹基本尺寸GB/T 197-2003 普通螺纹公差GB/T 700-2008 碳素结构钢GB/T 6739-2006 色漆和清漆铅笔法测定漆膜硬度GB/T 9286-1998 色漆和清漆漆膜的划格试验GB/T 13793-1992 直缝电焊钢管3 车架的结构形式3.1 总则车架的结构形式应能满足其功能(装配性等)、性能(刚度、强度等)和商品性的需要,符合国家相关法规和安全性的要求,本标准只对关重部位结构形式做总括性要求,具体结构设计按车型需要进行。
3.2 前立管部位结构形式3.2.1 电动摩托车的前立管部位的结构形式采用无缝钢管扩口形式,同主管连接处的下端以加强板连接见图1。
3.2.2 豪华款电动车的前立管部位的结构形式可采用高频焊管焊接结构、无缝钢管上下缩口结构和电动摩托车的前立管结构形式。
采用高频焊管焊接结构时,同主管连接处的上端和下端都必须有加强板1 连接,总长度不得超过280mm,见图2;长度超过280mm的需采用缩口形式或3.2.1电摩款的形式见图3。
摩托车货架检验指导书

摩托车货架检验指导书摘要:一、引言二、摩托车货架检验标准1.材料要求2.设计要求3.制造要求4.安全性能要求三、检验流程1.检验准备2.现场检验3.检验结果处理4.检验周期四、常见问题及解决方案1.材料不合格2.设计缺陷3.制造质量问题4.安全性能不足五、结论正文:一、引言摩托车货架作为摩托车的重要组成部分,其质量直接影响到驾驶员和乘客的安全。
为了确保摩托车货架的质量,我国制定了严格的检验指导书。
本文将对摩托车货架的检验标准、检验流程以及常见问题进行详细解析,以指导企业和检验人员正确开展摩托车货架检验。
二、摩托车货架检验标准1.材料要求摩托车货架应采用符合国家标准的材料,具有足够的强度、耐腐蚀性和耐磨性。
常见的材料有钢铁、不锈钢、铝合金等。
检验时,需对材料的牌号、规格、力学性能等进行核实。
2.设计要求摩托车货架设计应符合国家相关法规和标准,如GB/T 1416-2009《摩托车车架》、GB 16151-2009《摩托车乘员扶手》等。
设计要求包括结构合理、安装方便、稳定可靠、美观大方等。
3.制造要求摩托车货架的制造应严格按照设计图纸和工艺要求进行,确保产品尺寸、形状和表面质量满足标准。
检验时,应对制造过程进行现场监督,确保产品质量。
4.安全性能要求摩托车货架的安全性能是检验的重要指标。
检验项目包括静态承载能力、动态承载能力、抗风性能、稳定性、刚度等。
安全性能不合格的货架严禁上市销售。
三、检验流程1.检验准备检验前,应制定详细的检验计划,明确检验项目、检验标准、检验人员和检验设备。
同时,对检验人员开展培训,确保他们熟悉检验标准和检验方法。
2.现场检验现场检验分为原材料检验、制造过程检验和成品检验。
检验人员应按照检验计划,对每个环节进行严格把关,确保货架质量。
3.检验结果处理检验完成后,检验人员应对检验数据进行整理、分析,形成检验报告。
对于不合格的项目,应提出整改要求,并督促企业及时整改。
4.检验周期摩托车货架的检验周期应根据产品类型、风险等级等因素确定。
摩托车车架检验规程附表

用高度尺测量车架尾部、底部中心相对于车架中心基准之差
专用轴套、垫铁、标准轴、高度游标卡尺
车架底部对称度(含大撑支架、左右边管、底部弯管等)
各零部件
详见《车架检验指导书》的规定
试装
专用检具
3件的孔位对齐,能够自然方便地安装。各塑料件之间的间隙不大于1mm。
刀片、粘贴胶带
5
车架强度
与顾客提供的样品进行比较,若顾客无样件提供的由供需双方协商确定。
当有质量争议时进行
编制(日期):审核(日期):批准(日期):
附表
序号
项目
标准要求
试验方法
检测设备
备注
1
表面质量
焊缝应平整、均匀,不应有烧穿构件、虚焊、漏焊、裂纹、夹渣、气孔、焊瘤等缺陷。
漆层应均匀,不应有流痕、缺漆、起泡、脱落、漏底、起皱和麻点等缺陷。
目测
2
形位公差
车架尾部对称度
偏差不大于2mm
将专用轴套装配在车头管两安装钢腕的内孔中,然后将标准轴穿过两专用轴套
使用各种专用工具对整个车架进行全部试装,试装进程中不能敲、撬,要自然。
各种专用配件
4
漆层性能
抗冲击强度
≥50㎏f·s/c㎡
按GB/T1732-1993《漆膜耐冲击测定法》的规定测定
冲击试验器
漆膜硬度
≥2H
按GB/T6739-1996《涂膜硬度铅笔测定法》的规定测定
中华绘图铅笔2H
漆膜附着力
0-1级
按GB/T9286-1998《色漆和清漆漆膜的划格试验》的规定试验
欧盟自行车检测标准

欧盟自行车检测标准
欧盟自行车检测标准是指欧洲联盟对自行车产品进行检测和认证的一系列标准
和规定。
这些标准旨在保障消费者的安全和权益,同时促进自行车产品的质量提升和技术创新。
欧盟自行车检测标准涵盖了多个方面,包括车架、车轮、刹车系统、灯具、齿轮系统等多个方面的要求和测试方法。
首先,欧盟自行车检测标准对自行车车架的要求非常严格。
它要求车架必须具
有足够的强度和刚性,以确保在正常使用过程中不会发生断裂或变形的情况。
此外,车架的焊接部位和连接部件也必须经过严格的检测,以确保其结构的牢固和稳定。
其次,对于自行车的车轮和刹车系统,欧盟自行车检测标准也有着详细的规定。
标准要求车轮必须具有足够的强度和耐磨性,以确保在各种路况下都能正常运行。
而刹车系统则必须具有良好的制动性能和稳定性,以确保在紧急情况下能够及时有效地制动。
此外,欧盟自行车检测标准还对自行车的灯具和齿轮系统等配件提出了相应的
要求。
例如,灯具必须具有足够的亮度和可见性,以确保夜间骑行时能够提供良好的照明效果。
而齿轮系统则必须具有良好的换挡性能和耐久性,以确保在长时间使用过程中不会出现故障或损坏。
总的来说,欧盟自行车检测标准的制定和执行,对于保障消费者的安全和权益,促进自行车产品的质量提升和技术创新起到了至关重要的作用。
只有符合标准要求的自行车产品,才能够进入欧盟市场并获得认可。
因此,作为自行车生产厂商和消费者,都应当严格遵守这些标准,以确保自行车产品的质量和安全性。
同时,欧盟自行车检测标准也为自行车行业的发展提供了重要的指导和支持,推动了自行车产品的不断进步和完善。
- 1、下载文档前请自行甄别文档内容的完整性,平台不提供额外的编辑、内容补充、找答案等附加服务。
- 2、"仅部分预览"的文档,不可在线预览部分如存在完整性等问题,可反馈申请退款(可完整预览的文档不适用该条件!)。
- 3、如文档侵犯您的权益,请联系客服反馈,我们会尽快为您处理(人工客服工作时间:9:00-18:30)。
车架检验标准
1、目的
规范检验操作,发现、控制不合格产品,防止不良产品流入下道工序,同时给检验工作提供检验标准。
2、范围
适用于上海联孚公司所有外协加工车架的油漆涂装质量检验。
3、引用标准
下列标准包括的条文,通过在本检验作业指导书中的引用而构成本检验作业指导书的条文。
在本检验作业指导书发布时,所示版本均为有效。
所有标准都会被修订,使用本检验作业指导书的各方应探讨使用下列标准最新版本的可能性。
GB 6807 钢铁工件涂漆前磷化处理技术条件
Q/LQB Y-4-2011 汽车涂层标准
GB/T 13452.2-2008 色漆和清漆漆膜厚度的测定
GB/T 6739-2006 漆膜硬度铅笔测定法
GB/T 9286-1998 漆和清漆漆膜的划格实验
4、检验条件
4.1检验环境
环境整洁,空气清新,不应有明显影响检验作业的热气、湿气、烟尘。
4.2检验人员
检验人员辨色力正常,视力在0.8以上(含校正后)。
检验人员
应经过培训并得到授权。
4.3检验仪器及量检具
漆膜测厚仪、钢板尺、中华牌高级绘图铅笔(H、HB、B三种规格)、单面刀片等。
所有仪器及量检具应符合计量检定要求,并在有效的检定周期。
5、检验内容
5.1酸洗磷化质量检验
5.1.1外观检验
目视检测,磷化后工件的颜色应为浅灰色到深灰色或彩色;膜层应结晶致密、连续和均匀;不允许有下列缺陷:
a.疏松的磷化膜层
b.表面有机械损伤,有锈蚀或绿斑
c.局部无磷化膜(焊缝的气孔和夹渣处除外)
d.表面严重挂灰。
5.1.2耐蚀性检验
耐蚀性检验通常采用中性盐雾试验(浸入法)和硫酸铜点滴法,根据需要采用合适的方法检验。
a.浸入法
将磷化后的工件或试样(已降至室温)浸入3﹪的氯化钠溶液中,在15~25℃下,保持规定的时间,经两小时后取出工件或试样,随之洗净、吹干,目视检查磷化表面是否出现锈蚀,表面无锈渍为合格。
出现锈渍时间越长,说明磷化膜的耐蚀性越好。
b.点滴法
室温下,将蓝点试剂滴在磷化膜上,观察其变色时间。
磷化膜厚度不同,变色时间不同。
厚膜﹥5分钟,中等膜﹥2分钟,薄膜﹥1分钟。
5.表面油漆涂层质量检验
5.2.1外观检验
涂层外观项目检测时以目测和触感并借助钢板尺进行检测,目测时在光线良好状态下,位于距被检部位0.5m处对表面呈60度角范围内观测。
具体要求见下表
5.2.2漆膜厚度
《GB/T 13452.2-2008色漆和清漆漆膜厚度的测定》。
漆膜厚度要求单次涂层为15~25um。
检验批次10%每批。
5.2.3漆膜硬度
《GB/T 6739-2006漆膜硬度铅笔测定法》。
硬度要求≥HB。
检验频次5%每批。
5.2.4漆膜附着力
按《GB/T 9286-1998 漆膜划格试验》的规定对产品的附着力进行试验并记录。
附着力要求≤2级。
检验频次2%每批。