车架检验标准汇总
二手车技术鉴定--车身骨架的检查
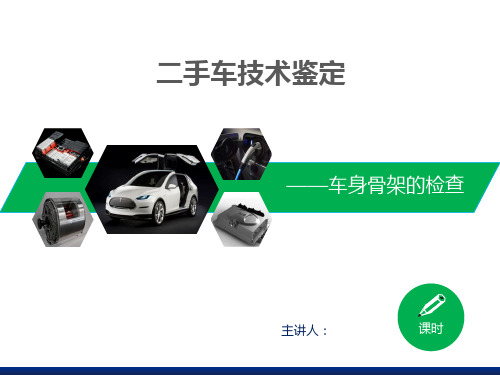
车身骨架的检查
结构性损伤具有以下特征:
1.经过撞击,损伤到发动机舱和驾驶舱的车辆 2.后翼子板撞击损伤超过其三分之一的车辆 3.纵梁有焊接、切割、整形、变形的车辆 4.减振器座有焊接、切割、整形、变形的车辆 5.ABC柱有焊接、切割、整形、变形的车辆 6.因撞击造成汽车安全气囊弹出的车辆 7.其它不可拆卸部份有严重的焊接、切割、整形、变形的车辆 8.车身经水浸泡超过车身二分之一,或积水进入驾驶舱的车辆 9.车身经火焚烧超过0.5平方米,经修复仍存在安全隐患的车辆
二、A、B、C柱的检查
如果拧动过会在螺丝或螺母上留下痕迹(如图所示)
二、A车 门就是更换过的,可 能是因为需要钣金喷 漆而拆卸。还通过检 查车门胶条来判断车 门是否更换过,正常 情况下,原车门都是 由机器打胶条,所以 会非常平整、顺畅, 而后换的车门都是由 人工打的,看上去会 非常不均匀,摸起来 也会稍软一些。
二、A、B、C柱的检查
二、A、B、C柱的检查
除了检查A柱上的焊点外,还要检查柱子上的螺丝是否拧动过, 拧动过的螺丝会在螺丝头或螺冒上留有痕迹(如图所示2-71所示), 顺便检查车门是否拆装更换过,也是判断A柱是否发生过事故的依据 之一
二、A、B、C柱的检查
首先,应立刻打开车门,检查车门合页及固定螺丝(如 图所示)。
二、A、B、C柱的检查
二、A、B、C柱的检查
1. A柱及车门的检查
二、A、B、C柱的检查
二、A、B、C柱的检查
使用漆膜厚度仪检查A柱
二、A、B、C柱的检查
• 有些严重事故的车辆,单看门框上的焊点可能判断不出是 否是事故车,因为A柱变形严重,A柱可能更换了新件。那 这些车又应该怎样检查呢
• 一是要重点检查A柱切割的位置,因为切割后一定要焊接 ,在焊接的地方肯定留下痕迹。二是检查A柱相邻部位翼 子板内衬。多部位结合检查,肯定会发现事故修复的痕迹
车架品质知识点总结
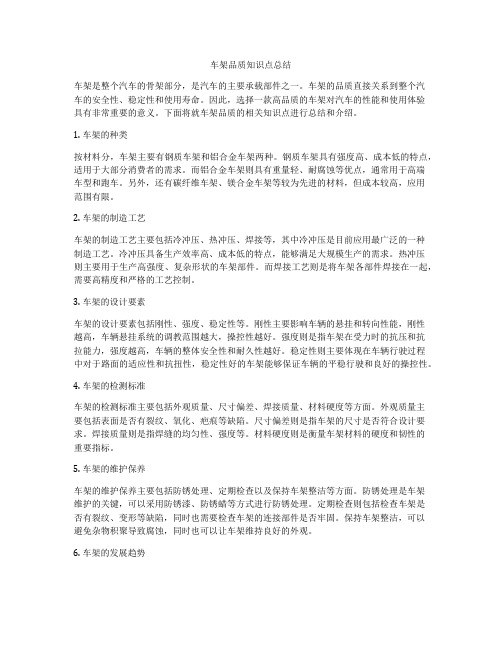
车架品质知识点总结车架是整个汽车的骨架部分,是汽车的主要承载部件之一。
车架的品质直接关系到整个汽车的安全性、稳定性和使用寿命。
因此,选择一款高品质的车架对汽车的性能和使用体验具有非常重要的意义。
下面将就车架品质的相关知识点进行总结和介绍。
1. 车架的种类按材料分,车架主要有钢质车架和铝合金车架两种。
钢质车架具有强度高、成本低的特点,适用于大部分消费者的需求。
而铝合金车架则具有重量轻、耐腐蚀等优点,通常用于高端车型和跑车。
另外,还有碳纤维车架、镁合金车架等较为先进的材料,但成本较高,应用范围有限。
2. 车架的制造工艺车架的制造工艺主要包括冷冲压、热冲压、焊接等,其中冷冲压是目前应用最广泛的一种制造工艺。
冷冲压具备生产效率高、成本低的特点,能够满足大规模生产的需求。
热冲压则主要用于生产高强度、复杂形状的车架部件。
而焊接工艺则是将车架各部件焊接在一起,需要高精度和严格的工艺控制。
3. 车架的设计要素车架的设计要素包括刚性、强度、稳定性等。
刚性主要影响车辆的悬挂和转向性能,刚性越高,车辆悬挂系统的调教范围越大,操控性越好。
强度则是指车架在受力时的抗压和抗拉能力,强度越高,车辆的整体安全性和耐久性越好。
稳定性则主要体现在车辆行驶过程中对于路面的适应性和抗扭性,稳定性好的车架能够保证车辆的平稳行驶和良好的操控性。
4. 车架的检测标准车架的检测标准主要包括外观质量、尺寸偏差、焊接质量、材料硬度等方面。
外观质量主要包括表面是否有裂纹、氧化、疤痕等缺陷。
尺寸偏差则是指车架的尺寸是否符合设计要求。
焊接质量则是指焊缝的均匀性、强度等。
材料硬度则是衡量车架材料的硬度和韧性的重要指标。
5. 车架的维护保养车架的维护保养主要包括防锈处理、定期检查以及保持车架整洁等方面。
防锈处理是车架维护的关键,可以采用防锈漆、防锈蜡等方式进行防锈处理。
定期检查则包括检查车架是否有裂纹、变形等缺陷,同时也需要检查车架的连接部件是否牢固。
保持车架整洁,可以避免杂物积聚导致腐蚀,同时也可以让车架维持良好的外观。
车架检验标准

一、外观质量1、车架各部位不应有锐边、毛刺。
2、车架外表面不应有明显的划伤、碰伤、压瘪等现象。
3、车架贴花表面应平整,不应有明显的皱花、错花、大面积坏花、歪花、散花、气泡等现象。
4、车架的硬印号码应清晰、永久、唯一。
5、车架焊缝应均匀不应有漏焊、焊渣等现象。
二、装配尺寸1、前管两端孔ФXX+00.084;2、电源锁支架位置按模具定好型;e) 平叉开档尺寸XX+2.20。
三、车架立管平行度:车架立管轴线应在车架中心基准面上,其公差值为1.8㎜。
四、车架平、立叉对称度:车架平、立叉应对称于车架中心基准面,其公差值为6㎜。
五、车架平叉开口垂直度:车架左右平叉接片开口连线应与车架中心基准面垂直,其公差值为1.2㎜。
六、检验规则1、批次确定:以每交货批为一批次。
2、进厂验收项目按产品标准QB1880-2008中7.3条规定执行。
3、进厂验收检验项目按GB/T2828.1-2003标准中规定的二次正常抽样方案。
检查水平为一般检查水平(I),B类接收质量限AQL=4.0,C类接收质量限AQL=6.5。
4、批质量以每百单位产品不合格品数计算。
检查项目、检查水平、不合格分类、接收质量限(AQL)见《车架质量特性检查表》。
5、需要时,进厂验收项目可以到生产厂进行验收检验。
6、进厂验收项目检验后应作好记录,质检部负责保存记录,保存期限为二年。
7、经检验合格的产品办理入库手续;检验不合格,按不合格品管理办理规定处理。
8 外观、焊接质量用目视法进行检验。
8.1、尺寸检验使用专用、通用量具进行检测。
8.2、ФXX+00.084专用量具或游标卡尺测定;8.3、其余尺寸用游标卡尺或卷尺测定。
车架质量特性检查表。
摩托车车架检验规程附表

项目
标准要求
试验方法
检测设备
备注
1
表面质量
焊缝应平整、均匀,不应有烧穿构件、虚焊、漏焊、裂纹、夹渣、气孔、焊瘤等缺陷。
漆层应均匀,不应有流痕、缺漆、起泡、脱落、漏底、起皱和麻点等缺陷。
目测
2
形位公差
车架尾部对称度
偏差不大于2mm
将专用轴套装配在车头管两安装钢腕的内孔中,然后将标准轴穿过两专用轴套
刀片、粘贴胶带
5
车架强度
与顾客提供的样品进行比较,若顾客无样件提供的由供需双方协商确定。
当有质量争议时进行
编制(日期):审核(日期):批准(日期):
附表
使用各种专用工具对整个车架进行全部试装,试装进程中不能敲、撬,要自然。
各专用配件
4
漆层性能
抗冲击强度
≥50㎏f·s/c㎡
按GB/T1732-1993《漆膜耐冲击测定法》的规定测定
冲击试验器
漆膜硬度
≥2H
按GB/T6739-1996《涂膜硬度铅笔测定法》的规定测定
中华绘图铅笔2H
漆膜附着力
0-1级
按GB/T9286-1998《色漆和清漆漆膜的划格试验》的规定试验
选择合适的垫铁,使车架中心基准面与平台平行
用高度尺测量车架尾部、底部中心相对于车架中心基准之差
专用轴套、垫铁、标准轴、高度游标卡尺
车架底部对称度(含大撑支架、左右边管、底部弯管等)
各零部件
详见《车架检验指导书》的规定
试装
专用检具
3
整车的装配性
车架各零部件的孔位要能与各装配件的孔位对齐,能够自然方便地安装。各塑料件之间的间隙不大于1mm。
车载支架成品检验规范

1.目的为规范成品入库及出货检验标准,确保所出货产品符合客户的需求,杜绝不良品接收及流出,不断的提升产品品质,提高客户的满意度,特制定此检验标准。
2.范围2.1适用于本公司所有充电器产品。
3.定义3.1缺陷级别定义3.2检验面定义A 面:直接看到的区域,如充电器顶部面。
B 面:不在直视范围,但暴露在外的面,如两侧面等。
C 面:正常使用时看不到的面,如充电器底面。
3.3抽样标准3.3.1依据MIL-STD-105E正常检验单次抽样3.3.2检验水准:一般特性采用II级水准;特殊特性采用S-2级水准3.3.3允收水平:CR缺陷:AQL=0 ; MAJ缺陷:AQL=0.65 ; MIN缺陷:AQL=1.04.权责4.1.品质部:负责成品检验标准的制定及执行,异常信息的反馈及改善措施有效性验证;4.2.研发部:对品质部分析处理检验中发现的重大结构、性能或工艺性异常,给予技术支援协同处理,并完善修改相关技术性文件;5.作业内容:5.1检验条件(如下图):5.1.1照明条件:600~1000LUX日光灯;5.1.2观察角度:被检测面与视线在45°范围内旋转,转动15°范围;5.1.3观测距离:距被测物表面距离为300~350mm;5.1.4观察时间:5~10秒钟;5.1.5视力:裸视或矫正视力在 1.0以上且无色盲。
序号检验项目检验标准检验方法检验工具AQL 备注1 包装外箱1.核对订单号、产品型号(SKU)、箱唛、数量是否一致。
目视/ MIN检验测量时参考产品图纸、标准样品、限度样品、SIP等作业。
2.无变形,划痕,破损。
目视/ MIN3.无潮湿,严重脏污。
目视/ MIN4.颜色,字样,要符合设计要求。
目视/ MIN5.无(设计指定贴附)之外的其它标示标贴。
目视/ MIN6.外箱尺寸管理:外径尺寸、内径尺寸、壁厚尺寸符合标准规格值要求,外箱毛重和净重与实际重量误差≤0.2kg。
测量标尺/电子秤MIN6.参考文件6.1《产品检验控制程序》6.2《不合格品控制程程序》6.3《样品承认书》。
车架检验标准汇总
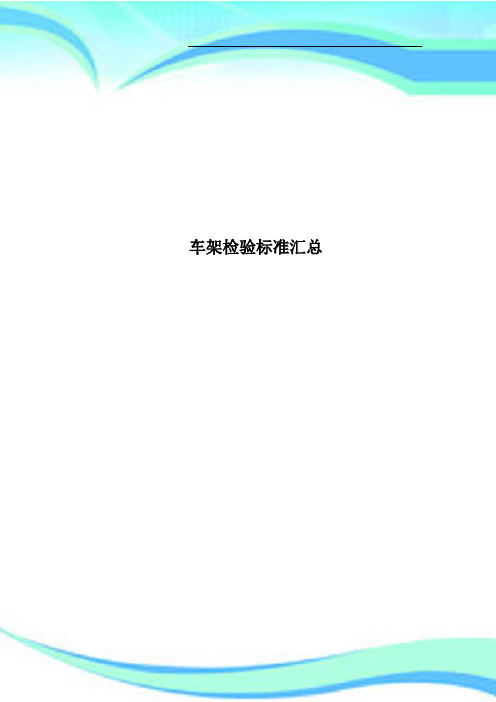
悍马车架检验标准11
悍马二代车架检验标准ﻩ13
世纪凌鹰车架检验标准15
B公主车架检验标准ﻩ16
圆梦车架检验标准ﻩ18
760车架检验标准20
小王子车架检验标准ﻩ21
小旋风车架检验标准ﻩ23
爱虎车架检验标准24
小雨点车架检验标准ﻩ25
中华海棠车架检验标准27
小帅哥车架检验标准29
小帅哥(电摩)车架检验标准…………………………………………………………………..40
风暴阳光(电摩)车架检验标准………………………………………………………………..41
五羊公主(助力车)车架检验标准…………………………………………………………….42
凌鹰(助力车)车架检验标准…………………………………………………………………..43
2.4.3车架上、下、立管直线度
车架上、下、立管直线度在300mm内,公差值为1mm。
2.4.4车架立管轴线与车架尾部中心线误差不大于3mm。
2.4.5车架中心线与平叉固定板中心线垂直度不大于2 mm。
2.4.6车架中心线与中轴中心线垂直度不大于2mm。
2.4.7中轴与平叉中心线平行度误差不大于2 mm。
2.通用技术要求
2.1外观质量
2.1.1车架各部位不得有锐边,毛刺。
2.1.2车架外表面不得有明显的划伤,碰伤,变形。
2.1.3对于外露车架其表面漆膜应符合QB/T1218标准(正视面不得有龟裂和明显的流疤,集结的沙粒,皱皮,漏漆等缺陷)。
2.2焊接要求
2.2.1各焊接处不得有漏焊,焊缝不规范,不充分及长度不够(在重点部位不得缺少3mm)等现象,安装塑件的固定片不得缺焊50%以上。
3.4各焊接处必须符合焊接要求,焊缝不得小于两工件的2/3,焊缝需平整、均匀,不得有焊缝不规范、不充分、长度不够、跑偏等现象。
挂车质量检验规范

挂车质量检验规范挂车质量检验规范一、引言挂车作为一种特殊的道路车辆,在运输行业起着重要的作用。
为了确保挂车的质量安全和道路行驶的安全性,需要对挂车进行质量检验。
本详细介绍了挂车质量检验的规范,包括检验原则、检验内容、检验方法等,旨在提供一个全面的参考指南。
二、检验原则1. 安全性原则:挂车的构造、材料、创造工艺等应符合相关安全标准,确保车辆在行驶过程中具备良好的安全性。
2. 可靠性原则:挂车的各个部件及系统应具备可靠性,能够经受长期使用和道路的各种复杂环境。
3. 经济性原则:挂车的创造成本、使用成本和维修成本应在合理范围内,以实现经济效益。
三、检验内容1. 车身结构检验:(1) 车架结构检验:检查挂车车架的创造工艺和材料,确保车架具备足够的强度和刚度。
(2) 车身外观检验:检查挂车外观的整体质量和工艺,包括车身平整度、涂装质量等。
2. 箱体检验:(1) 箱体结构检验:检查挂车箱体的创造工艺和材料,确保箱体具备足够的刚度和密封性。
(2) 箱体内部检验:检查挂车箱体内部的装备设施,包括货物固定装置、防滑设施等。
3. 制动系统检验:(1) 制动力检验:检查挂车制动系统的制动力是否符合标准要求,确保制动性能良好。
(2) 制动灵敏度检验:检查挂车制动系统的灵敏度是否符合标准要求,确保操作方便准确。
4. 灯光系统检验:(1) 示廓灯检验:检查挂车示廓灯的亮度和位置是否符合标准要求,确保夜间行驶的安全性。
(2) 制动灯检验:检查挂车制动灯的亮度和位置是否符合标准要求,确保其他车辆能够准确识别制动情况。
(3) 转向灯检验:检查挂车转向灯的亮度和位置是否符合标准要求,确保转向行驶时的安全性。
5. 悬挂系统检验:(1) 悬挂装置检验:检查挂车的悬挂装置是否符合标准要求,确保车辆悬挂系统具备良好的稳定性和舒适性。
(2) 后桥检验:检查挂车后桥的创造工艺和材料,确保后桥具备足够的强度和可靠性。
6. 轮胎系统检验:(1) 轮胎磨损检验:检查挂车轮胎的磨损情况,确保轮胎具备良好的抓地力和耐久性。
Q YD 007 车架标准

T 80备案号:浙江雅迪机车有限公司企业标准Q/YD 007—2011代替Q/YD 007—2010两轮车车架2011-04-18发布 2011-04-20实施浙江雅迪机车有限公司发布前言本标准由浙江雅迪机车有限公司提出。
本标准起草单位:浙江雅迪机车有限公司技术与产品规划部。
本标准主要起草人:邹万福本标准所代替的历次版本发布情况为:——Q/YD 007—2010两轮车车架1 范围本标准规定了摩托车和轻便摩托车(以下简称:摩托车)、电动摩托车和电动轻便摩托车(以下简称:电摩车)车架的术语和定义、要求、试验方法、检验规则、标志、包装与运输、贮存。
本标准适用于摩托车和电摩车车架(以下简称:车架);也适用于电动自行车和汽油机助力自行车车架。
2 规范性引用文件下列文件中的条款通过本标准的引用而成为本标准的条款。
凡是注日期的引用文件,其随后所有的修改单(不包括勘误的内容)或修订版均不适用于本标准,然而,鼓励根据本标准达成协议的各方研究是否可使用这些文件的最新版本。
凡是不注日期的引用文件,其最新版本适用于本标准。
GB/T 700碳素结构钢GB/T 1732—1993漆膜耐冲击性测定法GB/T 1733—1993漆膜耐水性测定法GB/T 1771—2007色漆和清漆耐中性盐雾性能的测定GB/T 1184—1996 形状和位置公差未注公差值GB/T 1804—2000 一般公差未注公差的线性和角度尺寸的公差GB/T 2828.1—2003计数抽样检验程序第1部分:按接收质量限(AQL)检索的逐批检验抽样计划GB/T 4955—2005金属覆盖层覆盖层厚度测量阳极溶解库伦法GB/T 5270—2005金属机体上的金属覆盖层电沉积和化学沉积层附着强度试验方法评述GB/T 6461—2002 金属机体上金属和其他无机覆盖层经腐蚀试验后的试样和试件的评级GB/T 6728—2002结构用冷弯空心型钢尺寸、外形、重量及允许偏差GB/T 6739—2006色漆和清漆铅笔法测定漆膜硬度GB/T 8162—2008结构用无缝钢管GB/T 9286—1998色漆和清漆漆膜的划格试验GB/T 9790—1998金属覆盖层及其他有关覆盖层维氏和努氏显微硬度试验GB/T 10125—1997人造气氛腐蚀试验盐雾试验GB/T 12467.1—2009金属材料熔焊质量要求第1部分:质量要求相应等级的选择准则GB/T 12467.2—2009金属材料熔焊质量要求第2部分:完整质量要求GB/T 12467.3—2009金属材料熔焊质量要求第3部分:一般质量要求GB/T 12467.4—2009金属材料熔焊质量要求第4部分:基本质量要求GB/T 13452.2—2008 色漆和清漆漆膜厚度的测定GB/T 13793—2008直缝电焊钢管GB/T 15367—2008 摩托车和轻便车两轮车和三轮车零部件名称GB/T 19804—2005 焊接结构的一般尺寸公差和形位公差QC/T 819—2009 两轮摩托车和两轮轻便摩托车车架QB 1880—2008 自行车车架3 术语和定义下列术语和定义适用于本标准3.1 两轮车装有一个驱动轮和一个从动轮,一般可用于公路或城市道路上行驶的车辆。
底盘主要零部件检验与车架检验要点
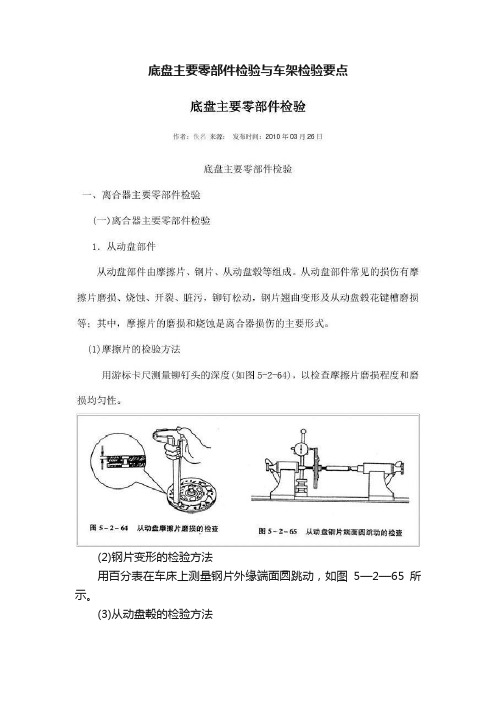
底盘主要零部件检验与车架检验要点(2)钢片变形的检验方法用百分表在车床上测量钢片外缘端面圆跳动,如图5—2—65所示。
(3)从动盘毂的检验方法用百分表或样板规检查花键槽的磨损量。
用百分表检查花键槽磨损量的具体方法是:把变速器第l轴的花键端插入从动盘毂的花键槽中,将百分表触头接触第l轴齿轮的齿面,再扳动第1轴,观察百分表指针的摆动值。
根据该摆动值,换算出花键啮合间隙,进而获得花键齿的磨损量。
(4)从动盘总成的检验方法1)用游标卡尺测量从动盘总成的厚度。
2)用游标卡尺测量铆钉埋人深度。
3)用塞尺检查摩擦片和钢片的铆接紧度:0.1mm的塞尺一般不应插入两者之间(应无间隙)。
4)用钢直尺和塞尺俭查摩擦片表面的平面度,其值一般应≤0.50mm2.压盘压盘的损伤主要发生在与从动盘接触的表面上,表现为工作平面擦伤、烧蚀、磨损、变形和裂纹;双片离台器中间压盘能损伤还有传动销孔或传力槽的磨损。
压盘的检验方法是:①检视压盘工作平面是否有沟槽,沟槽深度一般应≤O.5 mm。
②用平面度检验仪,平板和塞尺检查压盘工作平面的平面度。
③在静平衡装置上对压盘进行静平衡。
3.压紧弹簧压紧弹簧的常见损伤是弹簧的永久变形和弹力减弱,有时也会出现磨损和断裂等损伤。
压紧弹簧的检验方法是:用离合器弹簧弹力检验仪或在平板上用高度游标卡尺测量其自由长度、压缩长度和相应的压力;对膜片弹簧,还应测量其内端的磨损深度,其内端应在一个平面上,相差一般应≤0.5mm。
(二)离合器装配后的检验1)用高度游标卡尺和直尺测量离台器分离杠杆端面至飞轮表面的距离,同时检查4个分离杠杆端面的高度差。
如东风EQ1090E规定分离杠杆内端至减振器盘后平面的距离为32.4mm,各杠杆高度差不大于0.2mm。
2)在动平衡试验台上对装配在一起的离合器总成、曲轴与飞轮进行动平衡试验。
3)用直尺测量离合器踏板的自由行程。
二、变速器主要零部件检验(一)变速器主要零部件检验1.变速器壳体与盖变速器壳体与盖的常见损伤是变形、裂纹、轴承孔磨损和螺纹损坏等。
车架布纹外观检验标准
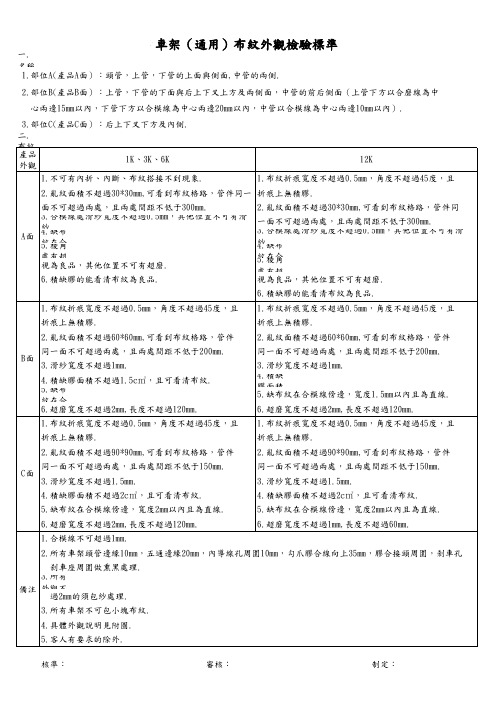
一.名稱定義
二.布紋檢驗標準
.長度不超過60mm 2mm ,超
核準: 審核:制定:200mm...
45度,且車架(通用)布紋外觀檢驗標準
3.部位C(產品C 面):后上下叉下方及內側.
1.部位A(產品A 面):頭管,上管,下管的上面與側面,中管的兩側.
心兩邊15mm 以內,下管下方以合模線為中心兩邊20mm 以內,中管以合模線為中心兩邊10mm 以內).
2.部位B(產品B 面):上管,下管的下面與后上下叉上方及兩側面,中管的前后側面(上管下方以合磨線為中45度,且45度,且150mm...
A 面:車架的上下管兩側,頭管的外側,中管的兩側(如上圖)
B 面:中心兩邊20mm 以內,后上下叉上方及兩側面
上管下方以合磨線為中心兩邊30mm 以內,下管下方以合模線為中心兩邊40mm 以內,中管以合磨線為更多免费资料下载请进: 車架左側面(A 面)車架右側面(A 面)車架上管上側(
A 面)車架下管上側(A 面)
車架上管下側(B 面)車架下管下側(B 面)
30mm 40mm
20mm
車架中管合模線周圍20mm 以內(B 面)后上下叉上方及兩側面(B 面)。
电动自行车检验标准
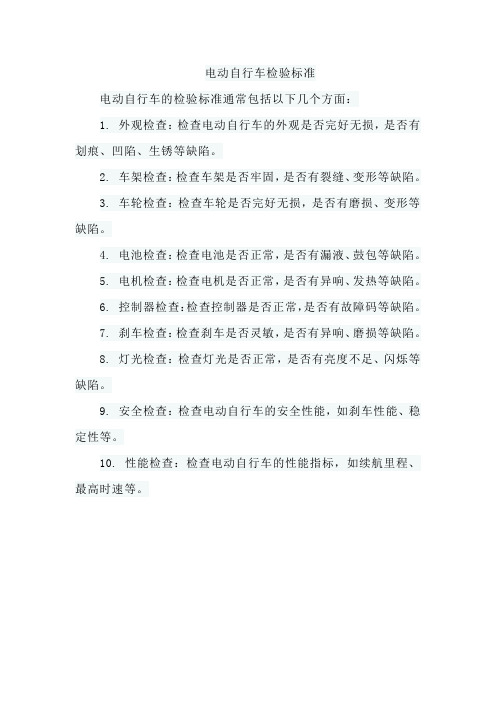
电动自行车检验标准
电动自行车的检验标准通常包括以下几个方面:
1. 外观检查:检查电动自行车的外观是否完好无损,是否有划痕、凹陷、生锈等缺陷。
2. 车架检查:检查车架是否牢固,是否有裂缝、变形等缺陷。
3. 车轮检查:检查车轮是否完好无损,是否有磨损、变形等缺陷。
4. 电池检查:检查电池是否正常,是否有漏液、鼓包等缺陷。
5. 电机检查:检查电机是否正常,是否有异响、发热等缺陷。
6. 控制器检查:检查控制器是否正常,是否有故障码等缺陷。
7. 刹车检查:检查刹车是否灵敏,是否有异响、磨损等缺陷。
8. 灯光检查:检查灯光是否正常,是否有亮度不足、闪烁等缺陷。
9. 安全检查:检查电动自行车的安全性能,如刹车性能、稳定性等。
10. 性能检查:检查电动自行车的性能指标,如续航里程、最高时速等。
车架车厢检验规范
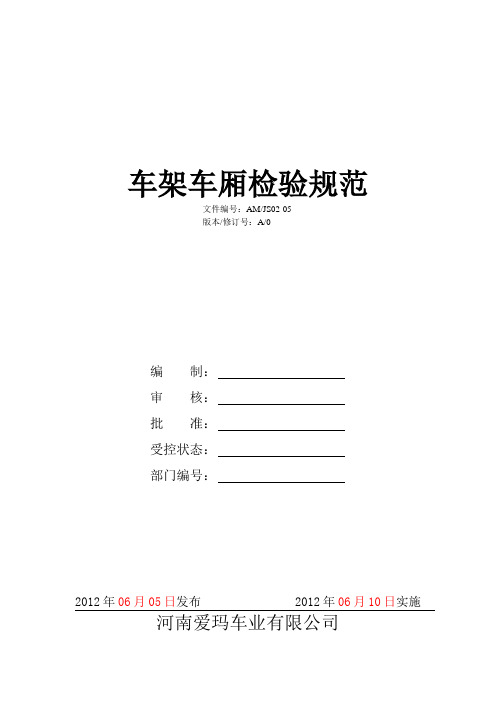
车架车厢检验规范
文件编号:AM/JS02-05
版本/修订号:A/0
编制:
审核:
批准:
受控状态:
部门编号:
2012年06月05日发布 2012年06月10日实施河南爱玛车业有限公司
车架车厢检验规范
1.检验分类
进厂检验为关键零部件进厂时由本公司检验员实施的检验工作。
出厂检验为企业生产最终产品按国家/行业、内部规定的频率对该部件进行的质量确认。
2.检验的项目
对于进厂检验项目和出厂检验按附表A中的规定进行。
3.检验的频率
按照附表A的规定执行。
4.检验的实施者
检验一般由本公司质量检验部门实施。
5.检验方法
按照附表A的规定执行。
6.抽样比例和接收准则
根据检验检测的性质(破坏性检验等)、工作难易程度、质量特性的重要度对检测项目做A、B、C等三个等级的划分。
注:
1.如该项目为验证供方检测报告,除有特殊说明外,其检验周期为1次/年。
2.可以认可第三方提供的检测报告。
3.外形尺寸检验如无特殊说明,计量单位为mm。
附表A:进厂与出厂检验项目。
车架实物与标准评价
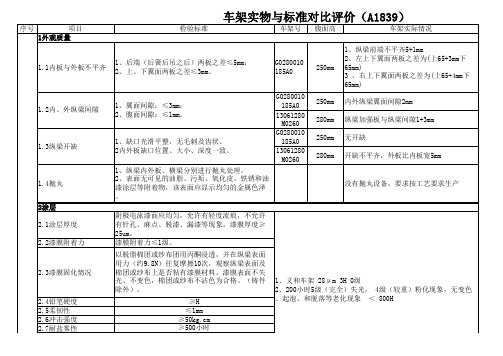
113-138 106-130 160-195 178-218 247-290 265-311 380-437 397-457 486-548 540-596
64-96 61-92 99-149 103-154 148-222 162-243 190-285 224-336 304-456 310-465
2.8人工老化 2.9抗石击性 3直线度
氙灯人工老化500h,漆膜抛光后,失光率≤30%。 ≤2级 G0280010 185A0 车架总长度≤5000mm时,直线度误差:≤3mm; 车架总长度>5000mm时,直线度误差:≤6mm 13061280 M0260 G0280010 185A0 车架总成左、右纵梁上翼面的平面度误差:≤4mm 13061280 M0260 G0280010 185A0 250mm 280mm 250mm 280mm 直线度公差3mm,车架总长度<5000mm 直线度公差3mm,车架总长度>5000mm 平面度公差4mm(左右纵梁) 平面度公差4mm(左右纵梁) 前吊耳支架(左):90°±18′+2.°2′ 后板簧支架(左):90°±18′+3°22′ 左纵梁:90°±30′+1°30′ 右纵梁:90°±30′+2°30′ 前吊耳支架(左):90°±18′+1°32′ 后板簧支架(右):90°±18′+1°12′ 左纵梁:90°±30′+1°30′ 右纵梁:90°±30′-10′ 公差1mm 左右公差2mm 前端车架宽:860﹢2mm 平衡悬挂梁:860+3mm 副板簧支架:860+3mm 车架尾端:860+2mm 前端车架宽:800﹣1mm 平衡悬挂梁:800mm 副板簧支架:800﹣4mm 车架尾端:800mm
车架检验规范(轻型电动车)
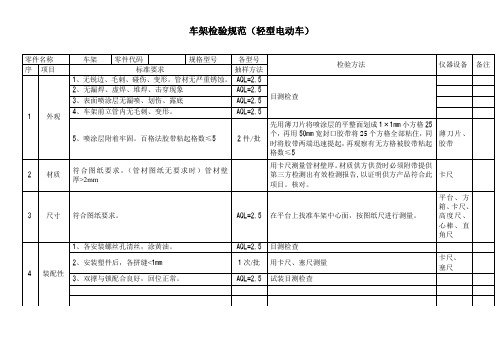
3
尺寸
符合图纸要求。
AQL=2.5
在平台上找准车架中心面,按图纸尺进行测量。
平台、方箱、卡尺、高度尺、心棒、直角尺
4
装配性
1、各安装螺丝孔清丝,涂黄油。
AQL=2.5
目测检查
2、安装塑件后,各拼缝<1mm
1次/批
用卡尺、塞尺测量
卡尺、
塞尺
3、双撑与锁配合良好,回位正常。
AQL=2.5
试装目测检查
平台、卡尺、高度尺、心棒、直角尺
编制/日期
校对/日期
标准化/日期
审核/日期
批准/日期
车架检验规范(轻型电动车)
零件名称
车架
零件代码
规格型号
各型号
检验方法
仪器设备
备注
序
项目
标准要求
抽样方法
1
外观
1、无锐边、毛刺、碰伤、变形。管材无严重锈蚀。
AQL=2.5
目测检查
2、无漏焊、虚焊、堆焊、击穿现象
AQL=2.5
3、表面喷涂层无漏喷、划伤、露底
AQL=2.5
4、车架前立管内无毛刺、变形。
AQL=2.5
5、喷涂层附着牢固。百格法胶带粘起格数≤5
2件/批
先用薄刀片将喷涂层的平整面划成1×1mm小方格25个,再用50mm宽封口胶带将25个方格全部粘住,同时将胶带两端迅速提起,再观察有无方格被胶带粘起格数≤5
薄刀片、胶带
2
材质
符合图纸要求,(管材图纸无要求时)管材壁厚>2mm
用卡尺测量管材壁厚。材质供方供货时必须附带提供第三方检测出有效检测报告,以证明供方产品符合此项目。核对。
试装。并检查转动灵活性。
电动车车架

××××股份有限公司企业标准电动车车架前言车架是电动车上的一个重要部件,其质量的好坏直接关系到用户人身安全。
目前尚无相关国家标准、行业标准,为统一本公司对车架的要求,结合本公司实际而制定本标准。
电动车车架1范围本标准规定了电动车用车架的整体结构形式、材料、规格、部件技术要求、部件焊接、表面涂装、车架检测及包装运输要求。
本标准适用于电动自行车车架、电动摩托车各型车架的设计、制造。
本标准中未涉及的部分按车型实际需要设计,同减震器、平叉、前叉连接部分的设计应满足该部品的设计标准需要。
2 规范性引用文件下列文件中的条款通过本标准的引用而成为本标准的条款,凡是注日期的引用文件,其随后所有的修改单(不包括勘误表)或修订版均不适用于本标准,然而,鼓励根据本标准达成协议的各方研究是否可使用这些文件的最新版本。
凡是不注日期的引用文件,其最新版本适用于本标准。
GB/T 196-2003 普通螺纹基本尺寸GB/T 197-2003 普通螺纹公差GB/T 700-2008 碳素结构钢GB/T 6739-2006 色漆和清漆铅笔法测定漆膜硬度GB/T 9286-1998 色漆和清漆漆膜的划格试验GB/T 13793-1992 直缝电焊钢管3 车架的结构形式3.1 总则车架的结构形式应能满足其功能(装配性等)、性能(刚度、强度等)和商品性的需要,符合国家相关法规和安全性的要求,本标准只对关重部位结构形式做总括性要求,具体结构设计按车型需要进行。
3.2 前立管部位结构形式3.2.1 电动摩托车的前立管部位的结构形式采用无缝钢管扩口形式,同主管连接处的下端以加强板连接见图1。
3.2.2 豪华款电动车的前立管部位的结构形式可采用高频焊管焊接结构、无缝钢管上下缩口结构和电动摩托车的前立管结构形式。
采用高频焊管焊接结构时,同主管连接处的上端和下端都必须有加强板1 连接,总长度不得超过280mm,见图2;长度超过280mm的需采用缩口形式或3.2.1电摩款的形式见图3。
摩托车货架检验指导书

摩托车货架检验指导书摘要:一、引言二、摩托车货架检验标准1.材料要求2.设计要求3.制造要求4.安全性能要求三、检验流程1.检验准备2.现场检验3.检验结果处理4.检验周期四、常见问题及解决方案1.材料不合格2.设计缺陷3.制造质量问题4.安全性能不足五、结论正文:一、引言摩托车货架作为摩托车的重要组成部分,其质量直接影响到驾驶员和乘客的安全。
为了确保摩托车货架的质量,我国制定了严格的检验指导书。
本文将对摩托车货架的检验标准、检验流程以及常见问题进行详细解析,以指导企业和检验人员正确开展摩托车货架检验。
二、摩托车货架检验标准1.材料要求摩托车货架应采用符合国家标准的材料,具有足够的强度、耐腐蚀性和耐磨性。
常见的材料有钢铁、不锈钢、铝合金等。
检验时,需对材料的牌号、规格、力学性能等进行核实。
2.设计要求摩托车货架设计应符合国家相关法规和标准,如GB/T 1416-2009《摩托车车架》、GB 16151-2009《摩托车乘员扶手》等。
设计要求包括结构合理、安装方便、稳定可靠、美观大方等。
3.制造要求摩托车货架的制造应严格按照设计图纸和工艺要求进行,确保产品尺寸、形状和表面质量满足标准。
检验时,应对制造过程进行现场监督,确保产品质量。
4.安全性能要求摩托车货架的安全性能是检验的重要指标。
检验项目包括静态承载能力、动态承载能力、抗风性能、稳定性、刚度等。
安全性能不合格的货架严禁上市销售。
三、检验流程1.检验准备检验前,应制定详细的检验计划,明确检验项目、检验标准、检验人员和检验设备。
同时,对检验人员开展培训,确保他们熟悉检验标准和检验方法。
2.现场检验现场检验分为原材料检验、制造过程检验和成品检验。
检验人员应按照检验计划,对每个环节进行严格把关,确保货架质量。
3.检验结果处理检验完成后,检验人员应对检验数据进行整理、分析,形成检验报告。
对于不合格的项目,应提出整改要求,并督促企业及时整改。
4.检验周期摩托车货架的检验周期应根据产品类型、风险等级等因素确定。
载货汽车车架总成检验评价办法
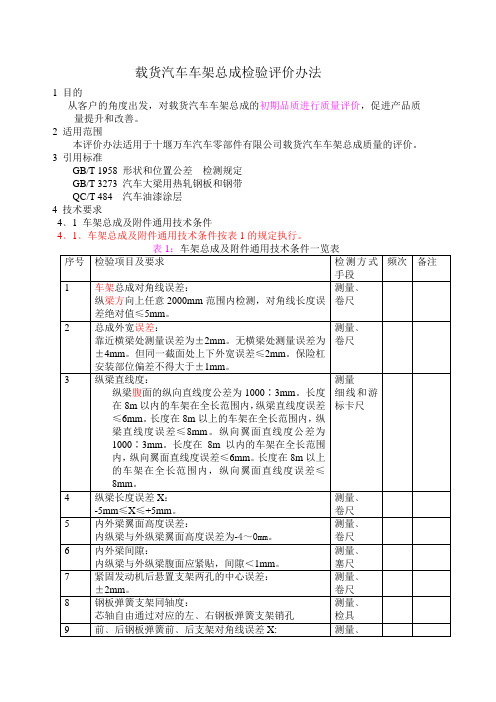
载货汽车车架总成检验评价办法1 目的从客户的角度出发,对载货汽车车架总成的初期品质进行质量评价,促进产品质量提升和改善。
2 适用范围本评价办法适用于十堰万车汽车零部件有限公司载货汽车车架总成质量的评价。
3 引用标准GB/T 1958 形状和位置公差检测规定GB/T 3273 汽车大梁用热轧钢板和钢带QC/T 484 汽车油漆涂层4 技术要求4﹑1 车架总成及附件通用技术条件4﹑1﹑车架总成及附件通用技术条件按表1的规定执行。
表1:车架总成及附件通用技术条件一览表序号检验项目及要求检测方式手段频次备注1 车架总成对角线误差:纵梁方向上任意2000mm范围内检测,对角线长度误差绝对值≤5mm。
测量﹑卷尺2 总成外宽误差:靠近横梁处测量误差为±2mm。
无横梁处测量误差为±4mm。
但同一截面处上下外宽误差≤2mm。
保险杠安装部位偏差不得大于±1mm。
测量﹑卷尺3 纵梁直线度:纵梁腹面的纵向直线度公差为1000∶3mm。
长度在8m以内的车架在全长范围内,纵梁直线度误差≤6mm。
长度在8m以上的车架在全长范围内,纵梁直线度误差≤8mm。
纵向翼面直线度公差为1000∶3mm。
长度在8m以内的车架在全长范围内,纵向翼面直线度误差≤6mm。
长度在8m以上的车架在全长范围内,纵向翼面直线度误差≤8mm。
测量细线和游标卡尺4 纵梁长度误差X:-5mm≤X≤+5mm。
测量﹑卷尺5 内外梁翼面高度误差:内纵梁与外纵梁翼面高度误差为-4~0mm。
测量﹑卷尺6 内外梁间隙:内纵梁与外纵梁腹面应紧贴,间隙<1mm。
测量﹑塞尺7 紧固发动机后悬置支架两孔的中心误差:±2mm。
测量﹑卷尺8 钢板弹簧支架同轴度:芯轴自由通过对应的左﹑右钢板弹簧支架销孔测量﹑检具9 前﹑后钢板弹簧前﹑后支架对角线误差X: 测量﹑-2mm≤X≤+2mm。
卷尺10 左纵梁上前簧前支架到后簧前支架的距离与右纵梁上前簧前支架到后簧前支架的距离的误差≤5mm。
- 1、下载文档前请自行甄别文档内容的完整性,平台不提供额外的编辑、内容补充、找答案等附加服务。
- 2、"仅部分预览"的文档,不可在线预览部分如存在完整性等问题,可反馈申请退款(可完整预览的文档不适用该条件!)。
- 3、如文档侵犯您的权益,请联系客服反馈,我们会尽快为您处理(人工客服工作时间:9:00-18:30)。
车架检验标准1. 适用范围1.1本标准适用丁无锡市志达车业有限公司车架外购配件入厂时的检验。
1.2对丁不同款式的车架,可根据本标准附件《各型车架检验标准汇总》的具体要求进行检验。
2. 通用技术要求2.1外观质量2.1.1车架各部位不得有锐边,毛刺。
2.1.2车架外表面不得有明显的划伤,碰伤,变形。
2.1.3对丁外露车架其表面漆膜应符合QB/T1218标准(正视面不得有龟裂和明显的流疤,集结的沙粒,皱皮,漏漆等缺陷)。
2.2焊接要求2.2.1各焊接处不得有漏焊,焊缝不规范,不充分及长度不够(在重点部位不得缺少3mm)等现象,安装塑件的固定片不得缺焊50%以上。
2.2.2焊接面不得处丁不合理受力状态,不得产生不能复原的变形。
2.2.3不允许有虚焊,虚堆。
2.2.4焊接应该米用二氧化碳保护焊和氯弧焊。
2.4精度要求2.4.1车架立管平行度车架立管轴线应在车架中心基准面上,其公差值为 1.8mm.2.4.2车架中接头垂直度车架中接头轴线与车架中心基准面应垂直,公差值为2mm。
2.4.3车架上、下、立管直线度车架上、下、立管直线度在300mm内,公差值为1mm。
2.4.4车架立管轴线与车架尾部中心线误差不大丁 3 mm。
2.4.5车架中心线与平义固定板中心线垂直度不大丁 2 mm。
2.4.6车架中心线与中轴中心线垂直度不大丁2 mm。
2.4.7中轴与平义中心线平行度误差不大丁2 mm。
2.5对丁具体的车型,如果出现与通用标准不符的情况,应该以具体款式的要求为准。
可参加本标准附件的要求进行。
3. 检验规则3.1采用GB2828标准一次抽样,达到技术要求为合格品4. 关丁材料的通用要求:4.1车架的钢管材料:为Q195 (GB/T—700)。
4.2凡是使用钢板制造的车架附件,应该符合冷轧钢板GB 708- 88的要求。
4.3偏撑、中撑弹簧材料:弹黄钢65Mn。
4.4偏撑、中撑轴为35#钢;调质,HB= 180〜220。
4.5平义轴为35#钢;调质,HB= 180〜220。
4.6所有的标准件,必须符合相关的国家标准的要求。
【附件】各型车架检验标准汇总目录万华600车架检验标准 (5)风暴600车架检验标准 (7)B09车架检验标准 (8)悍马车架检验标准 (9)悍马二代车架检验标准 (11)世纪凌鹰车架检验标准 (13)B公主车架检验标准 (14)圆梦车架检验标准 (16)760车架检验标准 (18)小王子车架检验标准 (19)小旋风车架检验标准 (21)爱虎车架检验标准 (22)小雨点车架检验标准 (23)中华海棠车架检验标准 (25)小帅哥车架检验标准 (27)风度车架检验标准 (30)巡洋舰车架检验标准 (31)神行天下车架检验标准.............................................................. ..32时空之恋车架检验标准.............................................................. ..33玉娇龙车架检验标准................................................................ ..34麦莎一号车架检验标准.............................................................. ..35太空一号车架检验标准.............................................................. ..36劲豹车架检验标准.................................................................. ..37凌鹰5代(电摩)车架检验标准...................................................... ..38五羊公主(电摩)车架检验标准...................................................... ..39小帅哥(电摩)车架检验标准........................................................ ..40风暴阳光(电摩)车架检验标准...................................................... ..41五羊公主(助力车)车架检验标准..................................................... .42凌鹰(助力车)车架检验标准........................................................ ..43小帅哥(助力车)车架检验标准...................................................... ..44 B09 (助力车)车架检验标准 (45)风暴阳光(助力车)车架检验标准.................................................... ..46精品文档16AH风行3+1车架检验标准一. 基本要求1.1对厂家定期进行原材料质量抽查一次。
车架所用材料:冲压件应用GB/T708冷轧板,厚度必须符合以下要求:1.2每501只抽取1只做振动疲劳试验1次,在某一批次停产15天以上,再次供货时随机抽检1只做振动试验,雨天送货时必须将车架盖好。
二. 检验过程2.1资料收取①收取厂家每批次购进原材料材质报告,材料Q195 (GB/T ---700)。
②收取厂家成品车架出厂检验合格证。
2.2外观要求①车架不得有水渍,以防锈蚀。
②车架各丝孔、丝杆必须回丝,抹有黄油。
③车架各部位不得有锐边、毛刺。
④车架烤漆必须平滑、光亮,不得有流疤、焊渣、砂粒、麻点、皱皮、漏漆等现象。
⑤车架表面不得有明显划伤、碰伤、变形、裂纹、锈蚀等现象。
⑥车架构件尺寸更准确,管件弯曲拉伸不得超出2mm,不得有起皱、凹凸现象。
2.3焊接要求3.1焊接应用二氧化碳保护焊。
3.2车架各部件位置准确、合理、摆放工整,符合车架的设计要求。
3.3焊接面不得处丁不合理受力状态,不得出现原始变形而乂不能复原的变形现象。
3.4各焊接处必须符合焊接要求,焊缝不得小丁两工件的2/3,焊缝需平整、均匀,不得有焊缝不规范、不充分、长度不够、跑偏等现象。
3.5不允许有虚焊、堆焊、漏焊、填补、少件等现象。
三. 检验要求1. 车架号码应为电脑打码,位置为挡风杠向上80mm-180mm之间大梁上号码盖2. 对车架各装配点、各部份垂直度等,按10-20%上平台进行检测。
各部份精度要求如下:头管直线度不大丁1mm,后尾中心线偏差5mm,衣架支架垂直度2mm,平■行度1.5mm,左右偏差2mm,电池盒支架1.5mm,中接头纵横面2mm,中撑孔纵横面1.5mm。
3. 对车架各装配点进行试装,以检测零部件装配点的准确性,配合效果等,试装可根据情况需要进行部分试装或者完全试装。
各部分尺寸如下:头管外径①34mm、内径①30-0.05,管壁厚度2mm、长280mm,衣架装配点185X 175mm,电池底托尺寸320X 320X 345X 345,中接头开档225mm,平■义挂耳开档101mm,中撑装配点开档40mm,后减挂耳开档不大丁22mm,前义限位宽26mm。
4. 车架称重:每100只车架抽样2只称重量,并且与车架样品质量进行对比四. 平■义检验1. 外观、焊接与车架相同。
2. 尺寸要求:两壁管应为40mmX 20mm,扁管壁厚2mm平义孔中心345mm,平义开档160mm,平义护板120mm,平义后减螺丝M10X 1.25 X20X 35mm3. 精度要求:1. 平义垂直度;平义轴孔与连接片开口处不得大丁 1.5mm。
2. 平义平行度;平义轴孔与平义连接垂直,其开口处平■行度不大丁 1.5mm。
3. 平义对称度;平义连接片左右对称度不大丁 1.6mm。
五. 平■义轴检验1材料;35#钢。
2. 外观要求;①镀锌(光亮锌)不得漏镀、锈蚀等现象。
②不得有不圆、弯曲、砂眼、气孔等现象。
③螺纹不得有碰伤、变形或螺距与螺帽不符现象。
④轴孔与螺帽要符合装配尺寸要求。
3. 平义轴尺寸要求;M1次1 x 120mm销孔①3mnffi离117,螺母为花螺母厚度12mm槽深4mm下面厚度8mm六. 中撑检验1. 外观焊接与车架相同。
2. 尺寸要求;中撑腿管①16mm,壁厚1.8mm,中撑高190mm,装配点开档40-0.5mm,撑起时与地面后火角为80°,中撑挂钩钏钉距离120mm3. 精度要求;左右高低不得超差2mm两腿平行度不大丁4mm七. 偏撑检验1. 外观焊接与车架相同。
2. 技术要求;①偏撑头两孔需同心。
②偏撑头丝牙与偏撑丝杆是否匹配。
③偏撑头槽与偏撑连接片是否匹配。
④偏撑螺丝限位台阶是否合适,装配偏撑是否卡死。
⑤单撑撑起车体与地面斜角800。
3. 尺寸要求;偏撑管①16,壁厚1.5mm单撑长130mm单撑头槽宽6mm螺纹孔M歆1.25, 台阶孔①12,螺丝M软1.25 x 15X台阶①10X 10mm两钏钉距离95mm八. 弹簧检验1. 材质:弹簧钢65Mn.2. 外观①光亮锌;②不得有松紧、变形现象。
③钢丝直径是否达到要求。
④弹簧精度是否达到要求。
⑤弹簧长度是否达到要求。
⑥弹簧开口方向是否达到要求。
3. 尺寸中、偏撑弹簧要求如下:①拉黄。
②中撑长100mm,单撑簧长75mm。
③钢丝粗2.5mm④弹簧外径15mm ⑤弹黄匝数16匝。
云燕三号车架检验标准一. 基本要求1. 对厂家定期1周进行原材料质量抽查一次,落实所用材料是否符合要求,管材钢号Q195光亮管。
头管①34mm< 2.0mm大梁管:55X 35X 2.0椭圆管,后立管38X 2.0mm平又管22X2.0mm®管,上边管19X 1.8mm冲压小件应用冷轧板,厚度符合下列要求;平义连接片5mm电池底托架铁板3mm后泥瓦支架2mm2. 每501只车架抽取1只做振动试验1次,在某一批次停产15天以上,再次供货时随机抽查1只做振动试验。
3. 雨天送货车架必须盖好。
二. 检验过程1. 资料收取;①收取厂家每批次购进原材料材质报告,材料光亮管Q195。
②收取厂家成品车架出厂检验合格证。
2. 外观要求;①车架不得有水渍,以防锈蚀。
②车架各部位不得有锐边、毛刺。
③车架上下不得有流疤、焊渣、麻点、凹凸不平、严重划痕、变形、裂纹等现象。