最新模流分析解析(详细)-by-heyy
模流分析解读和提升
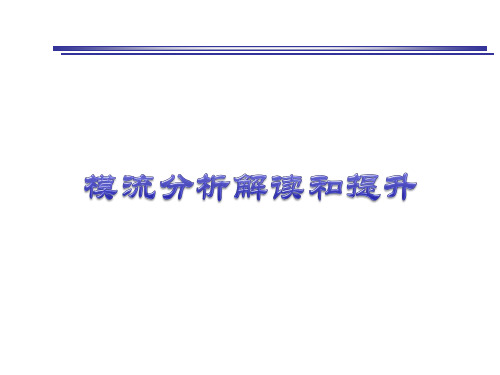
低温部位
滞留现象
温度结果
色差线:当温度梯度过大时则会出现色差线
熔接痕结果
4. Weld lines 熔接线:两股或两股以上的料流汇合时会形成熔 接线,对制品的外观和强度造成影响。
判断熔接线好坏的依据是: a 形成熔接线的时间,早比迟好 b 形成熔接线的流动前沿温度,高比低好; c 两股或多股料流汇合时的夹角越大越好; d 形成熔接线处的剪切应力,小于材料的允许值为好。
减少不均匀冷却的方法: 解决不均匀的冷却问题主要是解决型腔与型芯表面温差问题,可通 过增加冷却水路,修改水路位置,选用温度较低的冷却水,选用热 传导率高的镶件来移走型芯的热量等,来降低 两边的温差。
翘曲分析结果
冷却不均 总体方向变形
冷却不均 Z方向变形
冷却不均 X方向变形
冷却不均 Y方向变形
翘曲分析结果
流前温度低于转换温度,则塑胶冷凝不再流动
14
流动前沿温度结果
制品局部骨位料厚为0.8mm, 造成流动前沿温度范围超过 20℃,并有严重的滞留现象, 导致了制品的缺胶。
缺胶部位
流动前沿温度
最低150℃,如 图中蓝色部位
流动前沿温度结果
此处的料厚最薄为0.3mm, 流动前沿温度最低为151.8 虽未造成制品的缺胶,但有 严重的滞留现象,造成制品 填充困难
a Deflection, orientation effects:X Component X方向变形结果 b Deflection, orientation effects:Y Component Y方向变形结果 c Deflection, orientation effects:Z Component Z方向变形结果
Deflection, all effects:Deflection 变形结果可分为3个方向察看 结果: a Deflection, all effects:X Component X方向变形结果 b Deflection, all effects:Y Component Y方向变形结果 c Deflection, all effects:Z Component Z方向变形结果
模流分析报告解析共32页文档
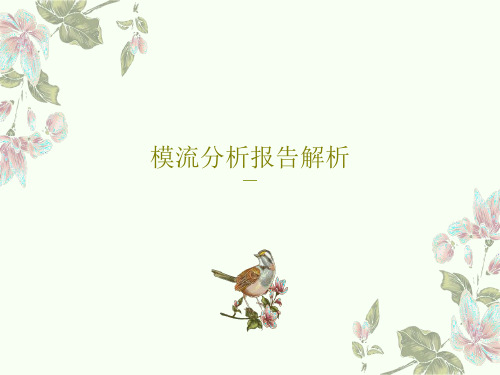
自由边界
单元匹配
Moldflow网格质量检查报告
不好的有限元网格: 1)影响计算精度。 2)错误的计算结果。 3)计算无法进行。
网格大小对计算精度的影响 5
How To Review Mold flow Report/如何检查模流分析报告
分析输入——定义浇口类型
侧浇口(Gate) 热浇道(Hot Drop) 潜伏式浇口(Sub) 直接浇口(Sprue) 香蕉型 (Cashew) 阀式(Valve)
注意:
零件内部的最大剪切应力不应该超过材料 的许可值。
影响: 如果零件内部的最大剪切应力超过材料的许可值, 可能导致一系列的表面缺陷。
14
How To Review Mold flow Report/如何检查模流分析报告
把有限分析结果按照客户需求已报告的方式提供给客户。由于有限元分析不可避免的存在一些 误差,需要在分析报告中对分析结果进行评估。
2
How To Review Mold flow Report/如何检查模流分析报告
Moldflow的计算方式
•模具内熔体的前端不断前移来连接各节点。 •熔体不断填充相邻的节点,直到零件上所有的节点都被 填充。 •熔体和模具接触时会形成一个凝结层。
Frozen Layer
Fountain Flow Region
nodes
3
elements
How To Review Mold flow Report/如何检查模流分析报告
Moldflow中的前处理
• 目前主流的模流分析软件是Moldflow,该软件只接受三角形单元以及四面体单元。 • 高质量的有限元网格是有限元分析精度的保障。 • 对于注塑件,在Moldflow主要有以下三种网格划分方式:中性面、双面流、3D实体。
模流分析报告课件
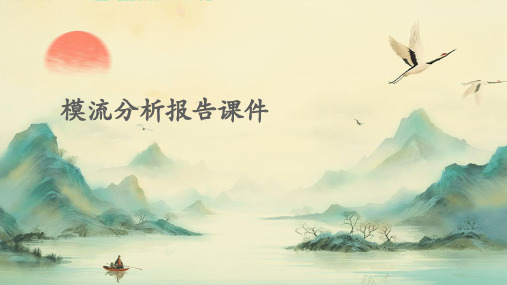
THANKS
感谢观看
模流分析报告课件
• 引言 • 模流分析基本概念 • 模流分析的方法和技术 • 模流分析的应用案例 • 模流分析的未来发展 • 结论
01
引言
目的和背景
目的
模流分析是产品设计和制造过程中的关键环节,它有助于预测产品在真实环境下的性能表现,从而优化设计方案, 提高产品质量。本报告旨在全面介绍模流分析的基本概念、方法和应用,为相关人员提供有益的参考和指导。
边界元法
总结词
边界元法是一种数值分析方法,通过将问题转化为边界积分方程,然后对方程进行离散化求解。
详细描述
边界元法主要应用于求解偏微分方程和积分方程,其基本思想是将微分方程或积分方程转化为边界积 分方程,然后选取适当的离散点或离散元,对方程进行离散化求解。该方法具有较高的精度和计算效 率。
有限差分法
复合材料
随着复合材料的广泛应用,模流分析 需要考虑材料的多层结构和各层之间 的界面效应,以更准确地预测材料的 流动和变形行为。
生物材料
在医疗器械和生物工程领域,生物材 料的模流分析将涉及更复杂的生物化 学和生理学机制,需要开发更为精细 的模型和算法。
高性能计算在模流分析中的应用
计算资源的提升
随着计算技术的不断发展,高性能计 算平台能够提供更高的计算能力和更 快的计算速度,使得大规模、高精度 模流分析成为可能。
后处理
对模拟结果进行可视化处 理和分析,提供优化建议。
模流分析的限制和挑战
限制
模流分析的准确性受到多种因素 的影响,如模型简化程度、边界 条件设置、材料属性等,因此需 要谨慎处理。
挑战
随着产品复杂度的增加,模流分 析的难度也在不断提高,需要更 高的计算资源和更精确的模型来 模拟更复杂的流动行为。
模流分析

217283CAE小百科系列~連載八一:模流分析的應用(充填)Moldex-FLOW是Moldex的流動分析模組,主要可用來模擬分析熱塑性塑料射出成型中的充填或填模(Filling)過程。
在理論模型方面,假設塑料熔膠是非彈性非牛頓流體(Inelastic Non-Newtonian Fluid),其黏度可用冪次率(Power-Law)流體及其修正式來描述,黏度考慮為溫度及剪切率的函數,如下圖所示。
塑料比容為溫度與壓力函數;熱物性質僅為溫度函數;假設塑件為薄件(厚度與長/寬度比超過1:10),因此可用GHS(Generalized Hele-Shaw)流動模式來描述塑料流動。
數值解法採用混合有限元素法(Finite Element Method)與差分法(Finite Difference Method)分別求解流動平面方向與厚度方向變量。
Moldex-FLOW的應用可列舉部分如下:1。
可於設計階段評估不同設計方案的可行性(Feasibility)與成型性(Moldability),作為修改設計與產品肉厚分布的參考,避免潛在成型問題如短射(Short Shot)及包封(Air Trap)等。
2。
可協助設計人員評估不同設計參數變更對產品成型性的影響,以進行必要的設計變更(Design Revision)甚至優化(Optimize)設計。
3。
可協助模具設計人員評估所需鎖模力大小,以修改模具設計,決定模穴數目或是成型機台。
4。
可協助模具設計人員進行流道設計,決定流道與澆口尺寸以避免壓力損耗過大及噴流(Jetting)發生,同時平衡流動使鎖模力得以降低,塑件品質得以控制。
5。
可協助模具設計人員決定澆口數目、種類與進澆位置,以避免包封、縫合線(Welding Line) 與流痕(Flow Mark),避免燒焦劣化(Burning and Degradation),以確保產品表面性質。
6。
可協助成型人員對製程進行故障排除(Trouble-Shooting),找出造成成型問題的可能原因與可能的解決之道,避免成型困難。
模流分析实验报告(3篇)
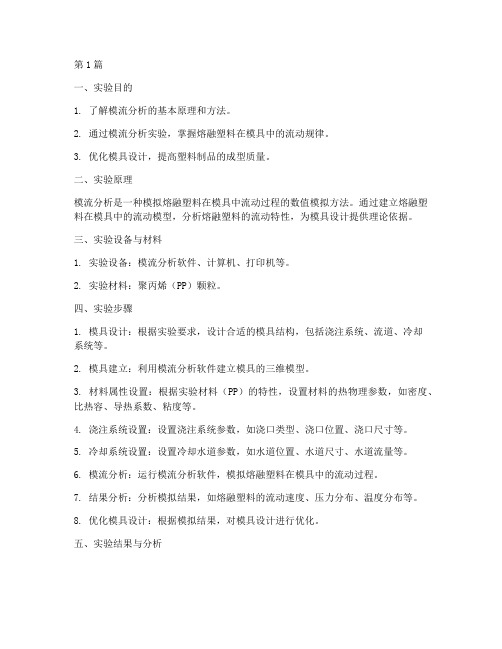
第1篇一、实验目的1. 了解模流分析的基本原理和方法。
2. 通过模流分析实验,掌握熔融塑料在模具中的流动规律。
3. 优化模具设计,提高塑料制品的成型质量。
二、实验原理模流分析是一种模拟熔融塑料在模具中流动过程的数值模拟方法。
通过建立熔融塑料在模具中的流动模型,分析熔融塑料的流动特性,为模具设计提供理论依据。
三、实验设备与材料1. 实验设备:模流分析软件、计算机、打印机等。
2. 实验材料:聚丙烯(PP)颗粒。
四、实验步骤1. 模具设计:根据实验要求,设计合适的模具结构,包括浇注系统、流道、冷却系统等。
2. 模具建立:利用模流分析软件建立模具的三维模型。
3. 材料属性设置:根据实验材料(PP)的特性,设置材料的热物理参数,如密度、比热容、导热系数、粘度等。
4. 浇注系统设置:设置浇注系统参数,如浇口类型、浇口位置、浇口尺寸等。
5. 冷却系统设置:设置冷却水道参数,如水道位置、水道尺寸、水道流量等。
6. 模流分析:运行模流分析软件,模拟熔融塑料在模具中的流动过程。
7. 结果分析:分析模拟结果,如熔融塑料的流动速度、压力分布、温度分布等。
8. 优化模具设计:根据模拟结果,对模具设计进行优化。
五、实验结果与分析1. 熔融塑料的流动速度:在模具入口处,熔融塑料的流动速度较大,随着流动距离的增加,流动速度逐渐减小。
在模具的狭窄部位,流动速度较大,而在宽大部位,流动速度较小。
2. 压力分布:在模具的狭窄部位,压力较大,而在宽大部位,压力较小。
在浇口处,压力最大。
3. 温度分布:在模具的冷却水道附近,温度较低,而在模具的加热部位,温度较高。
4. 优化模具设计:根据模拟结果,对模具设计进行优化,如调整浇口位置、改变冷却水道尺寸等。
六、实验结论1. 模流分析实验能够有效地模拟熔融塑料在模具中的流动过程,为模具设计提供理论依据。
2. 通过对模拟结果的分析,可以优化模具设计,提高塑料制品的成型质量。
3. 模流分析实验有助于缩短新产品开发周期,降低产品开发成本。
模流分析报告解读范例(一)2024
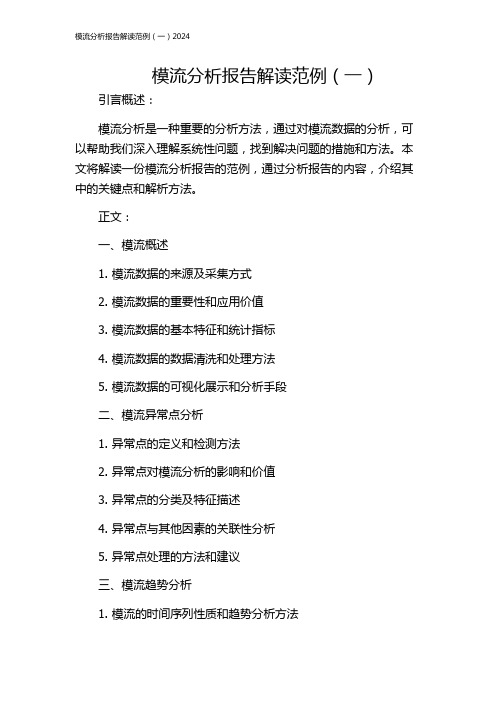
模流分析报告解读范例(一)引言概述:模流分析是一种重要的分析方法,通过对模流数据的分析,可以帮助我们深入理解系统性问题,找到解决问题的措施和方法。
本文将解读一份模流分析报告的范例,通过分析报告的内容,介绍其中的关键点和解析方法。
正文:一、模流概述1. 模流数据的来源及采集方式2. 模流数据的重要性和应用价值3. 模流数据的基本特征和统计指标4. 模流数据的数据清洗和处理方法5. 模流数据的可视化展示和分析手段二、模流异常点分析1. 异常点的定义和检测方法2. 异常点对模流分析的影响和价值3. 异常点的分类及特征描述4. 异常点与其他因素的关联性分析5. 异常点处理的方法和建议三、模流趋势分析1. 模流的时间序列性质和趋势分析方法2. 模流趋势分析的技术指标和模型3. 模流趋势分析的预测和预警方法4. 模流趋势分析在系统优化中的应用5. 模流趋势分析的误差估计和检验方法四、模流关联性分析1. 模流关联性的定义和度量方法2. 模流关联性分析的相关因素选取3. 模流关联性分析的统计检验方法4. 模流关联性的时间和空间特征5. 模流关联性分析的实践案例五、模流变化模式分析1. 模流变化模式的分类和描述方法2. 模流变化模式的驱动因素分析3. 模流变化模式的模型建立和验证方法4. 模流变化模式的周期性分析和控制方法5. 模流变化模式分析的实际应用案例总结:通过对这份模流分析报告的解读,我们了解了模流分析的基本概念和方法。
在实际应用中,模流分析可以帮助我们深入了解系统问题并提出针对性的措施。
在模流分析过程中,我们需要关注异常点、趋势分析、关联性分析和变化模式等方面,以全面把握模流数据的特征和规律。
希望本文的范例可以帮助读者更好地理解和应用模流分析方法。
模流分析报告解析
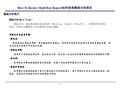
最大锁模力
注意: 最大锁模力不应该超过用于生产该零件 的注塑机的最大锁模力。
影响: 最大锁模力如果超过用于生产该零件的注塑机的最 大锁模力,可能在零件上产生飞边。
19
How To Review Mold flow Report/如何检查模流分析报告
保压分析——体积收缩
注意:
影响:
How To Review Mold flow Report/如何检查模流分析报告
冷却分析——冷却液雷诺数
注意: 为了保证冷却系统产生湍流,最小雷诺数应该大于 10,000。
影响: 当雷诺数低于10000时, 就不能确保冷却液的流动状 态为湍流。而如果达不到湍流的要求,系统的热传导 效率就会下降。
•定义冷却系统尺寸 •定义冷却液类型
•在Moldflow中做出冷却系统
冷却系统
6
How To Review Mold flow Report/如何检查模流分析报告
分析输入——定义注塑参数
7
How To Review Mold flow Report/如何检查模流分析报告
分析输入——定义材料参数
声明: 以下内容是以Darren May的报告为基础。
elements
2
How To Review Mold flow Report/如何检查模流分析报告
Moldflow中的前处理
• 目前主流的模流分析软件是Moldflow,该软件只接受三角形单元以及四面体单元。 • 高质量的有限元网格是有限元分析精度的保障。 • 对于注塑件,在Moldflow主要有以下三种网格划分方式:中性面、双面流、3D实体。 零件 中性面 双面流 3D实体
26
How To Review Mold flow Report/如何检查模流分析报告
什麼是模流分析

什麼是模流分析以下簡單介紹模流CAE的起源與歷史﹐冀能幫助工程人員有不同角度的省思與瞭解。
各領域的CAE應用功能不盡相同,早期主要是用在結構體強度計算與航太工業上。
但應用於塑膠射出與塑膠模具工業的CAE在台灣我們稱為模流分析,這最早是由原文MOLDFLOW直譯而來。
MOLDFLOW是由此領域的先驅Mr. Colin Austin在澳洲墨爾本創立﹐早期(1970~)只有簡單的2D流動分析功能,並僅能提供數據透過越洋電話對客戶服務﹐但這對當時的技術層次來說仍有相當的助益﹔之後開發各階段分析模組, 逐步建立今日完整的分析功能。
同一年代﹐美國Cornell大學也成立了CIMP研究專案,由華裔教授所領導﹐針對塑膠射出加工做系統理論研討,產品名為C-MOLD。
自1980年代起,隨著理論基礎日趨完備,數值計算與電腦設備的發展迅速,眾多同類型的CAE軟體漸漸在各國出現﹐功能也不再侷限於流動現象探討。
約1985年工研院也曾有過相似研發,1990年起清華大學化工系張榮語老師也完成CAE-MOLD軟體提供會員使用,目前則由科盛公司代理銷售。
MOLDFLOW公司創辦人Colin Austin是個機械工程師﹐1970年前後在英國塑膠橡膠研究協會工作。
1971年移民澳洲﹐擔任一家射出機製造廠的研發部門主管﹔在當時﹐塑膠材料在應用上仍被視做一種相當新穎的物料﹐具備了一些奇異的特性。
但在塑膠加工領域工作了幾年後﹐他開始對一般塑膠產品的不良物性感到疑慮﹐一般的塑膠製品並沒有達到物品的適用標準﹐相反的﹐塑膠已逐漸成為'便宜'、'低品質'的同義字﹔但他卻發現﹐多數主要不良品質的成因卻是因為不當成品設計與不良加工條件所造成的﹐所以他開始省思﹐產品設計本身需同時考慮成型階段﹐才是成功最重要的關鍵。
他開始花費大量時間在研究塑膠流動的文獻上﹐但發現這些理論並不能合理解釋他在工廠現場所看到的許多問題﹔因此他開始換角度去思考這些問題﹐將射出機台視為一整組加工程序﹐螺桿正是能量的傳遞機構﹐而模具內部的流動形態﹐才是決定成品品質的最主要因素。
模流分析
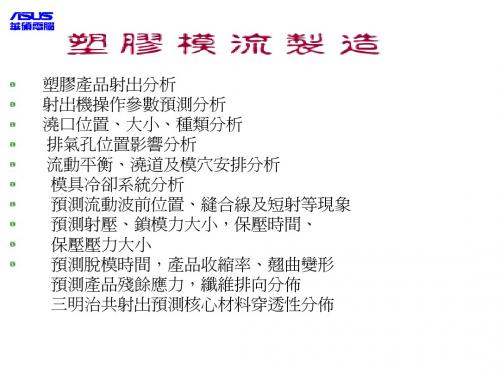
•降低鎖模力傳統射出時高保壓壓力需要高鎖模力,以防止塑料溢出(Flashing),但GIM所需之保 壓壓力不高,通常可降低鎖模力需求達25~60%左右。
•減少流道長度-
•氣體流通管道之較大厚度設計,可引導幫助塑料流通,便不需要特 別的外在流道設計,進而減低模具加工成本,及控制縫合線位置等 。
•應用於厚度變化大之成品厚部可利用以為Gal Channel。 •其他..... MF/GAS是針對GIM成型方式所寫的流動/保壓分析軟體,主要功能在於 預測塑料與氣體之充填流動/保壓行為,包括塑料的流動時間、溫度分 佈、壓力分佈、流動剪力、氣體的充填時間、位置、成品肉厚百分比 ..... MF/GAS分析對象泛包括所有商用氣體射出程序,分為體積控制(如 Cinpres I & II)與壓力控制(如Battenfeld)及其他相似技術,如 Krauss,Klockner,Gain...。
1. • • • • • • •
不同需求提供不同的分析功能模組: MF/Flow流動充填分析:塑料流動充填保壓 MF/Cool模具冷卻分析:模具冷卻水道及溫度變化 MF/Warp翹曲變形分析:成品不同因素影響的變形翹曲預估 MF/Stress塑膠應力分析:塑膠成品線性及非線性應力應變分析 MF/Fiber玻纖配向性分析:內含玻璃纖維流動型態及強度影響 MF/GAS 氣輔中空成型分析:結合流動冷卻的中空氣輔成型 MF/Tset 熱固性分析:IC封裝分析 l MF/Optim 最佳化成型分析: 最佳成型條件分析
GIM的好處 •減少殘留應力、降低翹曲問題傳統射出成型,需要足夠的高壓以推動塑料由主澆道流至最外圍區域;此高壓會造 成高流動剪力,殘存後則會造成成品變形。GIM中形成中空之氣體流通管道(Gas Channel)則能有效傳遞壓力,降低內應力,便減少成品發生翹曲的問題。 •消除凹陷痕跡傳統射出成品會在厚部區域如肋部(Rib & Boss)背後,形成凹陷痕跡(Sink Mark),這 是由於物料產生收縮不均的結果。但GIM則可藉由中空之氣體管道施壓,促使成 品收縮時由內部向外進行,則固化後在外觀上便不會有此痕跡。
模流分析
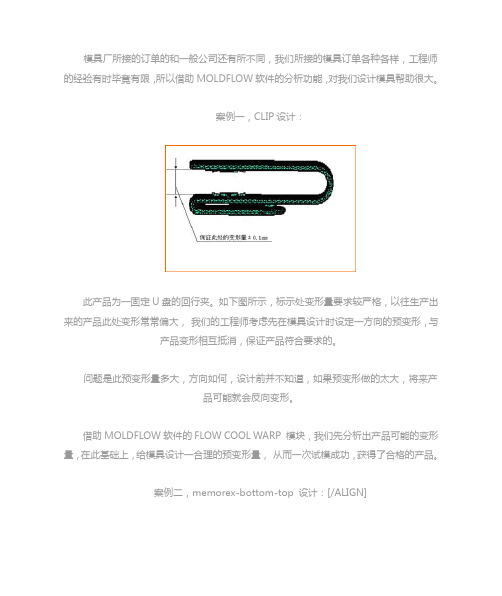
模具厂所接的订单的和一般公司还有所不同,我们所接的模具订单各种各样,工程师的经验有时毕竟有限,所以借助MOLDFLOW软件的分析功能,对我们设计模具帮助很大。
案例一,CLIP设计:此产品为一固定U盘的回行夹。
如下图所示,标示处变形量要求较严格,以往生产出来的产品此处变形常常偏大,我们的工程师考虑先在模具设计时设定一方向的预变形,与产品变形相互抵消,保证产品符合要求的。
问题是此预变形量多大,方向如何,设计前并不知道,如果预变形做的太大,将来产品可能就会反向变形。
借助MOLDFLOW软件的FLOW COOL WARP 模块,我们先分析出产品可能的变形量,在此基础上,给模具设计一合理的预变形量,从而一次试模成功,获得了合格的产品。
案例二,memorex-bottom-top 设计:[/ALIGN]此套模具为2+2 模穴,设计为自然平衡流道,如果不经过分析,模具设计者很难想到要在标示处加强排气,只能等试模时才能发现问题,必然会提高整个产品上市周期。
经过MOLDFLOW 软件的FLOW 模块分析后,我们在模具设计前就已经知道此问题,所以模具设计时特意在此处加强排气,保证一次试模成功。
还有一些案例解决流道平衡的问题,一模多腔的设计,通过控制流道尺寸,保证流动平衡,从而控制产品品质。
避免由于流动不平衡带来过保压现象,导致产品翘曲变形。
同时优化流道尺寸设计还有一个很大的益处就是减小循环周期。
因为很多情况下,产品最后凝固在流道处,如果流道尺寸偏大,必然提高整个循环周期,同时还会产生较多的废料。
电池盖部件是我们运用MOLDFLOW软件的又一成功案例。
此产品是薄壁件,难以填充。
在分析之前,解决它的方法是加大注射压力,提高注射速度,强制成型。
这样一方面机器磨损较大,另外高压高速注射后的产品内部残余应力较大,产品品质仍然无法保证。
采用MOLDFLOW分析后,采用局部加厚的方法,改善了产品的流动,从而使公司可以利用较小的压力和较低的注射速度成型。
模流分析

非流動溫度:
非流動溫度:此溫度也是與壓力狀態有關
黏度:
• 黏度可以視作在壓力推動下﹐塑膠流體流動的能力。黏度大﹐不易流動﹐黏度小 則容易流動。黏度與溫度、剪率、壓力有關﹐一般說來溫度升高﹐剪率變大時﹐ 黏度會變小﹐容易流動。壓力大時則黏度變大﹐但確實數據關係仍待個別研究。 • 通常實驗室等級使用的流變儀只能測取較低剪率範圍的黏度﹐因此實用的實驗操 作是在射出機台前加一方形狹縫模口﹐在七個不同剪率範圍與四種溫度下量取完 整黏度數據。
Extensional Viscosity 拉伸黏度
• Extensional pressure losses occur when a material flows from a large cross-section to a small cross-section (eg. from the barrel through the nozzle). • Extensional viscosity data is required to simulate these pressure losses. • It is particularly important for accurate injection pressure predictions. • As well as the standard set of tests required for the simulation software, Moldflow also commercially offers these following tests upon special request: • Pressure dependent viscosity • Effect of moisture on viscosity • Effect of colorant on shrinkage • Effect of cooling rates on the No-flow temperature • Effect of pressure on thermal conductivity • Extended low and high shear rates on viscosity testing • Thermal conductivity, specific heat and melt density as a function of temperature
模流分析解析(详细)_by_heyy

模流分析解析(详细)_by_heyyAMI 分析详解7.1.11.直浇口直浇口直接由主流道进入型腔。
2.侧浇口侧浇口是叫口中最简单又最常用的浇口。
侧浇口的深度尺寸的微小变化可使塑料熔体的流量发生较大变化。
3 . 护耳式浇口使用侧浇口对于某些开阔的型腔,可能会产生喷射呵蛇形流等现象。
护耳式浇口可将喷射、气纹控制在护耳上,需要的话,可用后加工手段去除护耳,使制品外观保持良好,常应用于高透明度平板类制件。
4 . 环形浇口根据制件的几何形状可以分为对称和不对称两种类型。
当需要设置多个浇口时,对称形状的制件要遵循每个浇口流长相等和填充体积相等的原则;不对称形状的制件由于本身就不能达到自然平衡,所以每个浇口的填充体积和压力降都不尽相同。
不对称形状的制件可能需要较多的浇口数目以获得平衡流动或者产生何莉莉的熔接线位置,同时降低注塑压力。
5 . 隔膜浇口通常在环状制件的内径中设置浇口,该制件通常具有薄壁区域。
7.1.3 分析结果解释1 . 浇口位置日志浇口位置日志给出了分析的一些日志,其中一条主要信息是给出了最佳浇口位置的节点。
2 . 流动阻力指示器表示熔体的流动前沿离不同浇口位置的流动阻力。
流动阻力的值从0到1的变化,阻值越高表明熔体流动越困难。
3 . 浇口匹配性表示浇口位置合理性的因子分布图,因子值越小,浇口位于这个位置的成型合理性越小。
7.2充填分析(必须)1 . 充填时间充填时间显示了熔体填充随时间的变化而变化情况。
从充填时间可以看出产品的填充是否平衡。
产品的两个末端的充填时间为****和****,V/P差相差10M,效果好。
(必须)2 . 速度\压力切换时的压力V\P转换时刻压力属于单组数据,通常,V\P转换时刻压力在整个注塑周期中时最高的,此时的压力大小和分布可以在图中读出,同时,未填充区域在图中以灰色显示。
(必须)3 . 流动前沿温度流动前沿温度是指熔体充填前沿中间层的温度,是熔体达到某节点的瞬时温度。
如何看懂一份模流分析报告
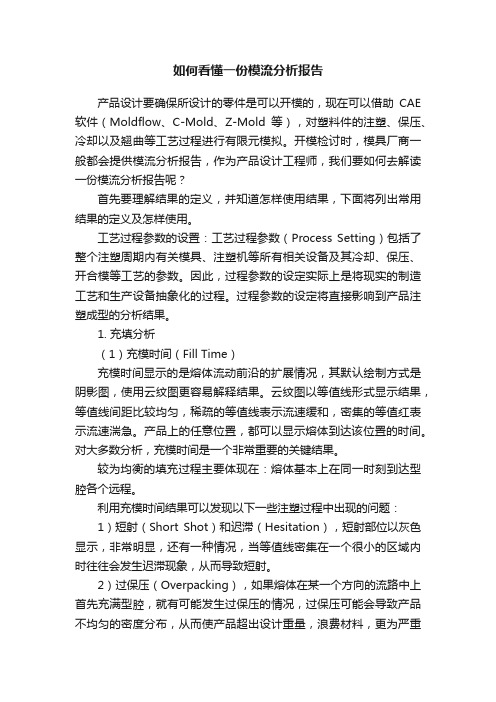
如何看懂一份模流分析报告产品设计要确保所设计的零件是可以开模的,现在可以借助CAE 软件(Moldflow、C-Mold、Z-Mold等),对塑料件的注塑、保压、冷却以及翘曲等工艺过程进行有限元模拟。
开模检讨时,模具厂商一般都会提供模流分析报告,作为产品设计工程师,我们要如何去解读一份模流分析报告呢?首先要理解结果的定义,并知道怎样使用结果,下面将列出常用结果的定义及怎样使用。
工艺过程参数的设置:工艺过程参数(Process Setting)包括了整个注塑周期内有关模具、注塑机等所有相关设备及其冷却、保压、开合模等工艺的参数。
因此,过程参数的设定实际上是将现实的制造工艺和生产设备抽象化的过程。
过程参数的设定将直接影响到产品注塑成型的分析结果。
1. 充填分析(1)充模时间(Fill Time)充模时间显示的是熔体流动前沿的扩展情况,其默认绘制方式是阴影图,使用云纹图更容易解释结果。
云纹图以等值线形式显示结果,等值线间距比较均匀,稀疏的等值线表示流速缓和,密集的等值红表示流速湍急。
产品上的任意位置,都可以显示熔体到达该位置的时间。
对大多数分析,充模时间是一个非常重要的关键结果。
较为均衡的填充过程主要体现在:熔体基本上在同一时刻到达型腔各个远程。
利用充模时间结果可以发现以下一些注塑过程中出现的问题:1)短射(Short Shot)和迟滞(Hesitation),短射部位以灰色显示,非常明显,还有一种情况,当等值线密集在一个很小的区域内时往往会发生迟滞现象,从而导致短射。
2)过保压(Overpacking),如果熔体在某一个方向的流路中上首先充满型腔,就有可能发生过保压的情况,过保压可能会导致产品不均匀的密度分布,从而使产品超出设计重量,浪费材料,更为严重的是导致翘曲发生。
(2)熔接线(Weld lines)当两股熔体的流动前沿汇集到一起,或一股流动前沿分开后又合到一起时,就会产生熔接线,如熔体沿一个孔流动。
最新模流分析报告范本PPT课件

充填的最大壓力為130.58Mpa 成品內部壓力分布為0~98.88M 流道壓力損失為31.70Mpa.
[8/12]
塑模一部設計處
——关于签单之后
1. 签单客户不要提前离开 2. 业务员与客户聚会 3. 陪客户回家 4. 第二天带小礼品去客户家回访
如何做:
全力拜访 量中取质
从我们的“A类客户”中筛选客 户
邀约的准备
1、工具的准备 2、话术准备
第一步: 吸引其注意力
告诉你一个好消息,我们公司定于 6月28日在公司举办一次高端客户联谊 会,本次客户联谊会只针对日益成熟 的现代家庭。机会难得!而且会上还 有众多的抽奖机会。
语气:不卑不亢 态度:诚恳热情 形象:专业干练
拒绝处理
1、我很忙,我没有时间参加。
其实张先生我知道向您这样的成功人 士都很忙,但我们每天忙忙碌碌又都是为 了什么?无非是多赚一点钱,让自己和家 人能够生活的更加幸福!公司举办的是家 庭理财联谊会,就是请专家来教我们安全 有效的家庭理财方法,这样的机会您要是 错过了那将是多么可惜的事情。您可以先 去听听,就算中途有事,又没规定说中途 不可离开。
模流分析报告范本
成型材料
黏度(viscosity) 流體流動阻力的度量。黏度越高,流動阻力越大,流動越困難。 對一般熱塑性塑料,黏度是塑料成分、溫度、壓力及剪切率的函 數。就溫度效應而言,熱塑性塑料的黏度一般隨溫度升高而有降 低的情形。就剪切率(shear rate)的效應而言,剪切率越高,代表 加工變形速率越大,由於高分子鏈被排向的結果,使大部份的塑 料具有黏度隨剪切率升高而下降的切變致稀性(shear-thinning)。
模流分析报告解析(一)2024
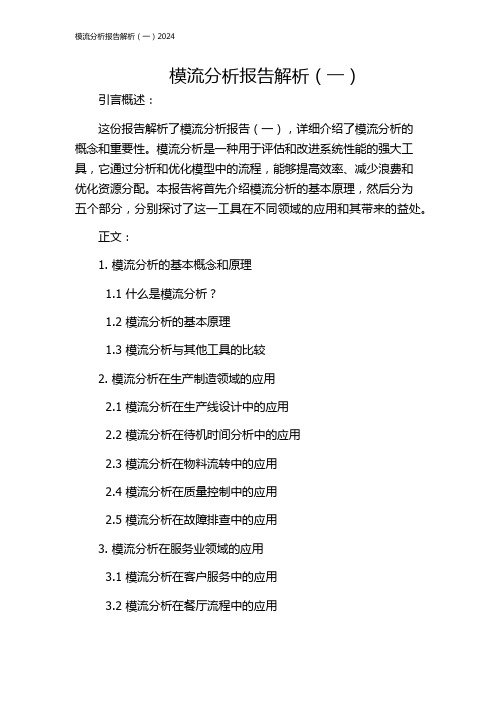
模流分析报告解析(一)引言概述:这份报告解析了模流分析报告(一),详细介绍了模流分析的概念和重要性。
模流分析是一种用于评估和改进系统性能的强大工具,它通过分析和优化模型中的流程,能够提高效率、减少浪费和优化资源分配。
本报告将首先介绍模流分析的基本原理,然后分为五个部分,分别探讨了这一工具在不同领域的应用和其带来的益处。
正文:1. 模流分析的基本概念和原理1.1 什么是模流分析?1.2 模流分析的基本原理1.3 模流分析与其他工具的比较2. 模流分析在生产制造领域的应用2.1 模流分析在生产线设计中的应用2.2 模流分析在待机时间分析中的应用2.3 模流分析在物料流转中的应用2.4 模流分析在质量控制中的应用2.5 模流分析在故障排查中的应用3. 模流分析在服务业领域的应用3.1 模流分析在客户服务中的应用3.2 模流分析在餐厅流程中的应用3.3 模流分析在物流配送中的应用3.4 模流分析在医疗服务中的应用3.5 模流分析在售后服务中的应用4. 模流分析在软件开发领域的应用4.1 模流分析在软件需求分析中的应用4.2 模流分析在系统架构设计中的应用4.3 模流分析在软件测试中的应用4.4 模流分析在性能优化中的应用4.5 模流分析在用户体验改进中的应用5. 模流分析的优势和局限性5.1 模流分析的优势5.2 模流分析的局限性总结:这份报告解析了模流分析报告(一),介绍了模流分析的基本概念和原理。
随后,详细讨论了该工具在不同领域的应用,包括生产制造、服务业和软件开发领域。
最后,总结了模流分析的优势和局限性。
通过本报告的解析,我们可以深入了解模流分析及其在各个领域的益处,希望能够为读者提供思路和相关应用场景的参考。
- 1、下载文档前请自行甄别文档内容的完整性,平台不提供额外的编辑、内容补充、找答案等附加服务。
- 2、"仅部分预览"的文档,不可在线预览部分如存在完整性等问题,可反馈申请退款(可完整预览的文档不适用该条件!)。
- 3、如文档侵犯您的权益,请联系客服反馈,我们会尽快为您处理(人工客服工作时间:9:00-18:30)。
AMI 分析详解7.1.11.直浇口直浇口直接由主流道进入型腔。
2.侧浇口侧浇口是叫口中最简单又最常用的浇口。
侧浇口的深度尺寸的微小变化可使塑料熔体的流量发生较大变化。
3 . 护耳式浇口使用侧浇口对于某些开阔的型腔,可能会产生喷射呵蛇形流等现象。
护耳式浇口可将喷射、气纹控制在护耳上,需要的话,可用后加工手段去除护耳,使制品外观保持良好,常应用于高透明度平板类制件。
4 . 环形浇口根据制件的几何形状可以分为对称和不对称两种类型。
当需要设置多个浇口时,对称形状的制件要遵循每个浇口流长相等和填充体积相等的原则;不对称形状的制件由于本身就不能达到自然平衡,所以每个浇口的填充体积和压力降都不尽相同。
不对称形状的制件可能需要较多的浇口数目以获得平衡流动或者产生何莉莉的熔接线位置,同时降低注塑压力。
5 . 隔膜浇口通常在环状制件的内径中设置浇口,该制件通常具有薄壁区域。
7.1.3 分析结果解释1 . 浇口位置日志浇口位置日志给出了分析的一些日志,其中一条主要信息是给出了最佳浇口位置的节点。
2 . 流动阻力指示器表示熔体的流动前沿离不同浇口位置的流动阻力。
流动阻力的值从0到1的变化,阻值越高表明熔体流动越困难。
3 . 浇口匹配性表示浇口位置合理性的因子分布图,因子值越小,浇口位于这个位置的成型合理性越小。
7.2充填分析(必须)1 . 充填时间充填时间显示了熔体填充随时间的变化而变化情况。
从充填时间可以看出产品的填充是否平衡。
产品的两个末端的充填时间为****和****,相差****,效果****。
(必须)2 . 速度\压力切换时的压力V\P转换时刻压力属于单组数据,通常,V\P转换时刻压力在整个注塑周期中时最高的,此时的压力大小和分布可以在图中读出,同时,未填充区域在图中以灰色显示。
(必须)3 . 流动前沿温度流动前沿温度是指熔体充填前沿中间层的温度,是熔体达到某节点的瞬时温度。
此温度要求分布均匀。
4 . 总体温度是中间结果数据,在静止状态时,是简单平均温度,在流动状态时,是考虑剪切速率的加权平均温度。
温度分布应该均匀,防止引起翘曲。
此例中,*******总体的最高温度不应该超过塑料的降解温度。
(必须)5 . 剪切速率,体积实质整个截面的剪切速率,这是一个中间结果数据,用户可以动态查看随时间变化的体积剪切速率。
如果该剪切速率过大时,熔体可能发生降解等缺陷。
可以看到本案例中的最大剪切发生在(浇口)处,达到了*****,但还是比使用的成型材料的最大剪切速度*******低,不会引起分解。
6 . 注射位置处压力,XY图从图中可以看出注射压力随时间的变化情况。
熔体在进入型腔后,压力持续增高,在达到最高点***后,进行V\P转换,完成最后的填充。
查看这张XY图,目的是要检查注射压力是否出现突变,如果存在突变,说明充模突遇阻力(可能是壁厚的突变造成的),应该相应调整充模速度,避免充模的不平衡。
7 . 达到定出温度的时间是一个单组数据,代表的是熔体从填充完成开始,到凝固至定出温度的时间。
这个时间可以提供给用户作为参考冷却时间。
这里计算的凝固时间,并没有考虑冷却系统的作用,精确的凝固时间可以在冷却分析中得到。
在这个结果中,用户还应该观察浇口附近的凝固时间,这个时间对于后面的表压设置帮助很大。
8 . 冻结层因子冻结层因子是指实时冻结层厚度占整个厚度的百分比。
显然,冷凝层因子最大值是1,表示制品界面已完全冻结。
观察冷凝层因子随时间的变化的情况,可以预判最早凝固的区域,这对于用户确定冷却时间和保压时间是很有好处的。
9 . %射出重量,XY图%射出重量,XY图的结果表达的是实时注射量占全部注射量的百分比随时间变化的情况。
全部注射量的计算是根据材料室温时的密度乘以网络体积得到的。
用户可以判断结束保压是否会影响到注射量。
(必须)10 . 气穴气穴的结果清晰明了的表明了气穴形成的位置。
通常,困气的位置是在两股料流汇合形成包风的地方或者型腔的边角处。
困气所带来的反作用力会影响熔体顺利填充,另外,空气被快速压缩时,温度会急剧上升,可能烧焦塑件。
11 . 平均速度平均速度是指熔体各处实时的流动速率和方向,是个中间数据结果,用户可以点击动画播放按钮,观察各个时刻熔体的平均速度。
通过平均速度结果,用户可以调整模具设计或注塑工艺设置,避免填充的不平衡。
(必须)12 . 锁模力,XY图锁模力,XY图示表示锁模力随时间变化的情况,计算的依据是塑件及流道在分模面上的投影面积乘以注塑压力。
一般地,锁模力应该小于注塑机最大锁模力的80%。
在使用AMI计算锁模力时,必须注意将塑件的开合模方向与系统的Z向相符。
13 . 充填区域充填区域的结果可以观察流经某一区域的材料是来源于哪一个浇口,来自同一浇口的材料流经的区域颜色相同。
在此案例中,采用一模两腔,设置有两个浇口,因此两个产品的颜色分别为红色和蓝色。
14 . 心部取向心部取向结果描述了分子在三角形单元心部的取向,其一般(无纤维填充)与熔体流动方向垂直。
对于没有纤维填充物的聚合物来说,取向方向的线性收缩比垂直于取向方向的线性收缩要大。
15 . 表层取向表层取向的结果描述的是三角形单元的表面的分子取向,且与心部取向方向不同。
分子取向应该近似沿着一条直线方向。
当考虑产品某个区域的力学性能的时候,表层取向的结果就比较有用了,因为取向方向具有更高的冲击强度和拉伸强度。
16 . 压力压力是一个时间数据,代表了从填充开始到填充结束的压力变化的全过程。
实际上,这个压力结果包含了速度\压力切换时的压力的结果,也包含了填充结束时的压力的结果。
17 . 充填结束时的压力充填结束时的压力的结果为单组数据,表示在填充结束时的注塑压力,相当于压力在1.491秒时的数据。
18 . 推荐的螺杆速度,XY图推荐的螺杆速度,XY图,XY图示AMI基于熔体前沿温度一致的原则而给出的随行程变化的螺杆速度。
用户在设置注塑参数时,可以参考该曲线设置螺杆速度,使得在整个冲模过程注塑机很难达到无极调速,而且调速的段数也是有限的,用户应该结合实际情况和生产经验,参考该曲线,设置合适的螺杆速度。
(必须)19 . 壁上剪切应力充模过程中,熔体在接触到冷型腔避时,迅速冷却,形成冻结层,该冻结层与中间流动的熔体形成一个界面,这个界面的剪切应力最高,称为壁上剪切应力。
壁上剪切应力属于中间数据,用户可以观察大壁上剪切应力随时间变化的情况。
充填过程中,壁上剪切应力应小于材料的许用剪切应力。
20 . 料流量料流量主要用于多浇口或多型腔的浇注系统的流动平衡。
在此案例中,对应位置处的流量基本上一样,说明流动平衡。
(必须)21 . 熔接痕熔接痕时塑料制品常见的缺陷,通常出现在两股料流汇合的地方,出现熔接痕并不能判定制品不合格,应该结合熔接痕处的熔体前沿温度及压力,分析熔接痕的相对质量。
7.3Fill+Pack 流动分析目的:进行流动分析时为了获得最佳保压阶段设置,从而尽可能地降低由保压引起的制品收缩、翘曲等质量缺陷。
1 . 冻结层因子通过动画的形式观察冻结层的变化,找出浇口完全冻结的时间。
在此案例中,当浇口的冻结层因子为1时,时间为****妙。
如果直到压力释放之后浇口或制件都没有冻结,那么应该需要延长保压时间。
2 . 第一主方向上的型腔内残余应力制品在顶出时,取向方向上的残余应力。
残余应力的存在,可能导致制品翘曲或开裂,使用AMI分析、对比注塑方案时,应该尽量减少残余应力值。
3 . 第二主方向上的型腔内残余应力第二主方向上的型腔内残余应力显示的是垂直于取向方向的残余应力。
4 . 缩痕,指数缩痕指数表示制品可能出现缩痕的地方,通常由缩痕所在面的另一面的特征引起的。
在壁厚较厚的地方和对面有筋肋等特征时,容易出现缩痕。
缩痕指数的大小表示了可能出现缩痕的可能性的大小。
保压压力的大小对缩痕指数的大小有着直接影响。
5 . 体积收缩率体积收缩率表示了每个单元相对于自身原始体积的收缩率。
体积收缩率时中间数据结果。
对于各向同性的材料来说,三个方向上的线性收缩率大约等于1/3体积收缩率。
如果体积收缩率出现负值,表明有过保压产生,制品将出模膨胀。
(必须)6 . 顶出时的体积收缩率在顶出时制件的体积收缩率,给出收缩率分析结果,帮助制定拔模角度等(必须)7 . 推荐的螺杆速度:XY图,可得出螺杆的行程,试模时,可对螺杆进行定义。
7.3Cool(冷却分析)目的:判断制件冷却效果的优劣,根据冷却效果计算出冷却时间的长短,确定成型周期所用的时间。
在获得均匀冷却的基础上优化冷却管道的布局,尽量缩短冷却时间,从而缩短单个制品的成型周期,提高生产率,降低生产成本。
(必须)1 . 冷却回路介质温度冷却回路介质温度显示了冷却剂在流经冷却回路后温度升高的情况。
一般地,冷却剂温升不要超过2℃。
此例中,冷却水路的进出口温度升高非常小,效果很明显。
2 . 回路流动速率回路流动速率描述的是冷却剂在回路中的流动速率,由于本例中没有并联回路,故每处的流动速率时一致的。
在并联回路中,这个结果非常有用,可以观察每一条回路的流速。
3 . 回路雷诺数冷却剂的流动状态有层流和湍流之分,在湍流时传热效率高,衡量层流和湍流的判断依据就是雷诺数。
当冷却剂的雷诺数在10000 以上时,可以认为是完全的湍流状态,因此AMI推荐冷却回路雷诺数应在10000以上。
值得注意的是,AMI流动速率计算只保证冷却剂入口处的雷诺数符合设定的值,因此在有并联的冷却回路中,要注意检测回路处雷诺数大于10000,否则必须在冷却剂属性设定中提高入口雷诺数。
(必须)4 . 回路管壁温度回路管壁温度显示了冷却回路中模具管道表面的温度。
该温度与冷却剂入口温度之差不应该超过5℃。
如果局部模具表面温度太高,表明该处需要加强冷却。
本案例中温度分布均匀,与冷却剂入口的温差不超过*℃。
5 . 表面温度,冷流道表面温度,冷流道表示与模具表面接触的冷流道的平均速度。
使用此信息,可以观察是否存在热点或冷点,用于调整冷却系统的布局。
6 . 表示制品到达顶出要求所需要的时间。
制品上的不同部位的顶出时间的差距应不明显,否则就说明有热点。
可能需要修改制品壁厚或是重新调整冷却系统布局。
在此案例中,制品凸起部位顶出时间明显,需要修改壁厚。
7 . 达到顶出温度的时间(冷流道)达到顶出温度的时间(冷流道)描述的是冷流道达到顶出要求所需要的时间。
此信息应该结合达到顶出额为年度的时间,制品的结果,确保冷流道冷却在制品冷却之后。
8 . 最高温度,制品塑件在冷却结束时,不仅各处温度不同,而且在厚度方向上也是不同的。
一般地,塑件截面中温度最高的位置应该在截面的中部,这个结果就是描述塑件截面的最高温度。
9 . 最高温度,冷流道最高温度,冷流道显示了穿过冷流道温度曲线的最大温度,在冷却结束时得出。