SMT设备性能参数对生产基本的工艺要求
SMT生产品质控制工艺标准及流程
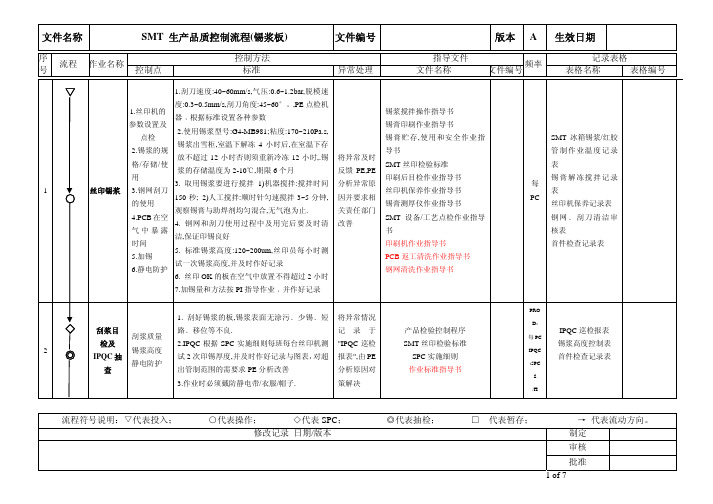
流程符号说明:▽代表投入;○代表操作;◇代表SPC;◎代表抽检;□代表暂存;→代表流动方向。
修改记录日期/版本制定
审核
流程符号说明:▽代表投入;○代表操作;◇代表SPC;◎代表抽检;□代表暂存;→代表流动方向。
修改记录日期/版本制定
审核
流程符号说明:▽代表投入;○代表操作;◇代表SPC;◎代表抽检;□代表暂存;→代表流动方向。
修改记录日期/版本制定
审核
流程符号说明:▽代表投入;○代表操作;◇代表SPC;◎代表抽检;□代表暂存;→代表流动方向。
修改记录日期/版本制定
审核
流程符号说明:▽代表投入;○代表操作;◇代表SPC;◎代表抽检;□代表暂存;→代表流动方向。
修改记录日期/版本制定
审核。
smt焊接工艺技术指标
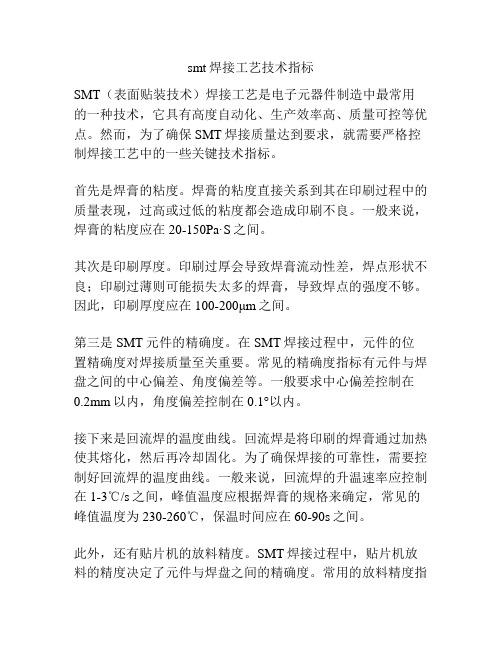
smt焊接工艺技术指标SMT(表面贴装技术)焊接工艺是电子元器件制造中最常用的一种技术,它具有高度自动化、生产效率高、质量可控等优点。
然而,为了确保SMT焊接质量达到要求,就需要严格控制焊接工艺中的一些关键技术指标。
首先是焊膏的粘度。
焊膏的粘度直接关系到其在印刷过程中的质量表现,过高或过低的粘度都会造成印刷不良。
一般来说,焊膏的粘度应在20-150Pa·S之间。
其次是印刷厚度。
印刷过厚会导致焊膏流动性差,焊点形状不良;印刷过薄则可能损失太多的焊膏,导致焊点的强度不够。
因此,印刷厚度应在100-200μm之间。
第三是SMT元件的精确度。
在SMT焊接过程中,元件的位置精确度对焊接质量至关重要。
常见的精确度指标有元件与焊盘之间的中心偏差、角度偏差等。
一般要求中心偏差控制在0.2mm以内,角度偏差控制在0.1°以内。
接下来是回流焊的温度曲线。
回流焊是将印刷的焊膏通过加热使其熔化,然后再冷却固化。
为了确保焊接的可靠性,需要控制好回流焊的温度曲线。
一般来说,回流焊的升温速率应控制在1-3℃/s之间,峰值温度应根据焊膏的规格来确定,常见的峰值温度为230-260℃,保温时间应在60-90s之间。
此外,还有贴片机的放料精度。
SMT焊接过程中,贴片机放料的精度决定了元件与焊盘之间的精确度。
常用的放料精度指标有X轴、Y轴方向的偏差。
一般要求X轴、Y轴方向的偏差控制在±0.05mm以内。
最后是可靠性测试。
在SMT焊接工艺中,可靠性测试是评估焊接质量是否达到要求的重要指标之一。
常见的可靠性测试有剪切力测试、耐热性测试、振动测试、冷热冲击测试等。
通过可靠性测试,可以评估焊接过程中是否存在缺陷或潜在问题。
综上所述,SMT焊接工艺技术指标是确保SMT焊接质量达到要求的重要因素。
在实际生产中,需要控制好焊膏的粘度、印刷厚度、元件的精确度、回流焊的温度曲线、贴片机的放料精度等。
通过严格控制这些指标,可以保证焊接质量的可靠性和稳定性。
SMT贴片标准及工艺标准

印刷工艺
印刷机选择
锡膏选择
印刷精度
根据产品要求选择合适 的印刷机,确保印刷质
量。
根据产品特性选择合适 的锡膏,保证焊接质量。
印刷精度要求高,误差 需控制在一定范围内。
印刷质量检测
印刷完成后需进行质量 检测,确保无缺陷。
贴片工艺
贴片设备选择
根据产品要求选择合适的贴片 设备,确保贴片精度。
元件选择与准备
焊点完整性
焊点外观
焊点应连续、平滑,无气泡、空洞或 裂缝。
焊点应呈光亮的金属色,无氧化、变 色等现象。
焊点强度
焊点应牢固,能承受一定程度的压力 和振动,不易脱落。
元件位置标准
元件位置准确性
元件应放置在正确的位置,偏差 不超过允许范围。
元件方向正确性
元件的方向应符合电路设计要求, 极性元件方向正确。
焊点外观检测
焊点外观需光滑、连续、无气泡、无杂质。
检测工艺
01
功能检测
对产品进行功能检测,确保满足设 计要求。
尺寸检测
对产品尺寸进行检测,确保符合规 格要求。
03
02
外观检测
对外观进行检测,确保无明显缺陷。
可靠性检测
对产品进行可靠性检测,确保满足 使用要求。
04
SMT贴片质量标准
03
焊点质量标准
贴片材料的表面质量
贴片材料的表面应光滑、无缺陷,以确保良好的贴装效果。
辅助材料标准
1 2
粘合剂材料
用于固定电子元件的粘合剂应具有适当的粘性和 耐温性能。
清洁剂材料
用于清洁贴片表面的清洁剂应无腐蚀性、无残留 物。
3
包装材料
用于包装贴片产品的包装材料应具有保护性、防 潮性和抗震性。
SMT贴片机的性能考核指标

SMT贴片机的性能考核指标SMT贴片机(Surface Mount Technology Placement Machine),是一种用于电子元器件贴装的自动化设备。
其性能考核指标主要包括速度、精度、可靠性、柔性等。
以下将逐一分析这些指标。
速度是衡量SMT贴片机性能的一个重要指标。
它通常指的是SMT贴片机每小时能够完成元器件的贴装数量。
速度的高低与设备的生产效率直接相关。
靠前的SMT贴片机速度通常能达到10万个焊点/小时以上。
高速的设备能够提高生产效率和产能,降低生产成本,适应高强度的生产要求。
精度是衡量SMT贴片机性能的另一个关键指标。
它是指贴装元器件的精确定位能力。
具体来说,精度可分为以下几个方面的考量,包括:坐标定位精度、贴装偏移精度、贴装角度精度和复杂元器件贴装精度。
高精度的设备能够确保元器件的准确位置,保证电路的正常工作。
目前,SMT贴片机的精度一般在几十微米到几百微米之间。
可靠性是指SMT贴片机长时间稳定运行的能力,包括抗干扰能力、抗震动能力、抗磨损能力等。
这些性能指标保证设备在恶劣的环境条件下仍然可以正常运行,减少设备故障对生产的影响,提高设备的稳定性。
柔性是指SMT贴片机适应不同尺寸和类型的元器件的能力。
随着电子产品的不断发展,元器件的类型和尺寸呈多样化趋势。
因此,SMT贴片机需要具备良好的柔性,能够灵活调整和适应不同尺寸、形状和材料的元器件贴装工艺。
除了以上指标,还有一些辅助指标也需要考虑。
例如,设备的故障率是指设备在一定时间内发生故障的概率,高可靠性的设备具有低故障率;设备的易用性包括操作界面友好性、编程简单性等等。
另外,还有一些可选的指标可根据企业的具体需求进行考虑,如软件系统的稳定性、后期维护等。
总而言之,SMT贴片机的性能考核指标主要包括速度、精度、可靠性和柔性等。
正确评估和选择合适的机器是企业提高生产效率、降低成本、提升竞争力的重要一环。
smt各流程工艺要求和品质注意事项

smt各流程工艺要求和品质注意事项嘿,搞SMT的小伙伴们!今天咱们可得好好唠唠SMT各流程工艺要求和品质注意事项啦,这可太重要啦!首先呢,咱们来说说锡膏印刷这个流程。
锡膏就像是SMT的魔法胶水一样,那工艺要求可不能马虎。
锡膏的型号得选对喽,就像给不同的人穿合适的鞋子一样,选错了可不行。
印刷的时候,钢网要保证清洁干净,要是钢网上沾了脏东西,就好比在干净的画布上乱涂乱画,印出来的锡膏肯定不均匀。
压力也要适中呀,压力过大,锡膏就会被挤得到处都是,像调皮的小虫子乱跑;压力过小呢,锡膏又印不完整,这就糟糕啦。
在这个流程里,品质注意事项也很多呢。
要经常检查锡膏的厚度,这厚度要是不对,可能会导致焊接不良,那可就影响整个产品的品质啦,就像盖房子地基没打好,房子能稳吗?接着就是元件贴装啦。
哇,这一步就像是给电路板这个小世界安排居民一样。
贴片机的精度那得超高的,偏差一点点都不行。
元件的吸取和放置位置要精准无误,就像把棋子准确地放在棋盘格子里。
操作人员得时刻关注贴片机的运行状态,要是它出了点小毛病还不知道,那就像火车偏离了轨道一样危险。
对于品质方面,要检查元件有没有贴歪,有没有贴错型号的情况。
这要是贴错了,整个电路板就可能会像个乱了套的小社会,功能肯定不正常啦。
再然后就是回流焊接啦。
这个过程就像是给元件和电路板举办一场融合的派对。
回流焊的温度曲线要严格按照工艺要求来设置,这就像厨师做菜要按照菜谱的火候要求一样。
温度高了,元件可能会被烤坏,就像蛋糕在烤箱里烤焦了;温度低了呢,焊接就不牢固,就像胶水没粘牢东西一样。
在品质上,要检查焊接的效果,有没有虚焊、短路之类的问题。
虚焊就像两个人拉手没握紧,随时可能松开;短路就像电线乱搭,会引发大问题的。
还有检测环节呀。
这就像是给已经组装好的电路板做个体检。
检测设备要定期校准,不然就像秤不准了一样,量出来的数据都不可靠。
检测人员得认真仔细,不能放过任何一个小瑕疵。
对于发现的不良品,要及时标记和处理,可不能让有问题的产品混在好产品里面,这就像在一群健康的人里混进了生病的人一样,会传染的。
SMT制程与设备能力介绍

課程內容
SMT簡介 各工序介紹 波峰焊 SMT周邊設備介紹 ESD防護
SMT簡介
1.SMT定義 表面貼裝技術Surface Mounting Technology簡稱SMT是新一代電子組裝技術,它將傳統的電子元器件壓縮成為體積只有幾十分之一的器件,從而實現了電子產品組裝的高密度、高可靠、小型化﹑低成本﹐以及生產的自動化.這種小型化的元器件稱為:SMD器件(或稱SMC、片式器件).將元件裝配到印刷線路板或其他基板上的工藝方法稱為SMT工藝.相關的組裝設備則稱為SMT設備.
各工序介紹--貼片
3複合式 複合式貼片機從拱架式機器發展而來,集合了轉塔式和拱架式特點,動臂上安裝有轉盤,又稱閃電頭,可實現每小時60000片貼片速度.
各工序介紹--貼片
4大型平行系統 大規模平行系統(又稱模組機),使用一系列單獨小貼裝單元.各單元有獨立絲杆位置系統、安裝有相機和貼裝頭.各貼裝頭可吸取部分的帶式送料,貼裝PCB一定區域,PCB以固定間隔時間在機器內步進.單獨地各個單元機器運行速度較慢,但其連續或平行運行會有很高的效率.
各工序介紹--錫膏印刷
6.重要耗材-錫膏 1.何為錫膏
2.錫膏主要組成成份 錫粉顆粒+助焊膏/劑
各工序介紹--錫膏印刷
3.錫膏的存儲和使用 錫膏是一種化學特性很活躍的物質,因此它對環境的要求是很嚴格的.一般在溫度為0℃-10℃,濕度為20%-21%的條件下有效期為6個月,在使用時要注意幾點: A.保存的溫度 B.使用前應先回溫(一般>4小時) C.使用前應先攪拌3-4分鐘 D.最佳作業環境溫度25+/-3℃濕度為50+/-10%RH E.儘量縮短進入回流焊的等待時間 F.在開瓶24小時內必須使用完,否則做報廢處理
SMT表面贴装工艺设备、PCB线路板制作工艺设备参数
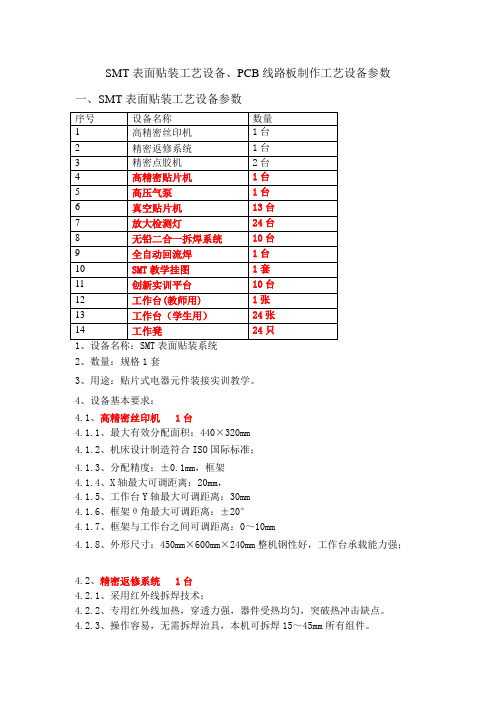
SMT表面贴装工艺设备、PCB线路板制作工艺设备参数一、SMT表面贴装工艺设备参数2、数量:规格1套3、用途:贴片式电器元件装接实训教学。
4、设备基本要求:4.1、高精密丝印机 1台4.1.1、最大有效分配面积:440×320mm4.1.2、机床设计制造符合ISO国际标准;4.1.3、分配精度:±0.1mm,框架4.1.4、X轴最大可调距离:20mm,4.1.5、工作台Y轴最大可调距离:30mm4.1.6、框架θ角最大可调距离:±20°4.1.7、框架与工作台之间可调距离:0~10mm4.1.8、外形尺寸:450mm×600mm×240mm整机钢性好,工作台承载能力强;4.2、精密返修系统 1台4.2.1、采用红外线拆焊技术;4.2.2、专用红外线加热,穿透力强,器件受热均匀,突破热冲击缺点。
4.2.3、操作容易,无需拆焊治具,本机可拆焊15~45mm所有组件。
4.2.4、本机配备0.6KW预热系统,预热范围120×120㎜。
4.2.5、红外线加热无热风流动,不影响周边微小器件,适合BGA组件。
4.2.6、红外线加热拆焊速度比热风枪快一倍,因受热损坏器件率大大降低。
4.2.7、全功能CPU控制,LED数码管显示。
4.2.8、使用电压:AC220V,50Hz。
使用温度范围:100-450℃。
4.3、精密点胶机 2台可手动,自动,半自动、脚动四种控制,可手动轻触控制,由定时器控制每次滴胶时间,定时、定量出胶水,确保每次滴胶一致;可滴胶液体或料,有红胶、黄胶、环氧树脂、锡浆、矽胶、助焊剂等;调节气压,选择适当的时间和针咀,便于改变每次滴胶量和滴胶时间,适合不同需要;微型脚踏控制板;多种规格的塑胶咀适合不同需要。
4.3.1、自动定时:0.01s~30s4.3.2、重复准确性:±0.5%4.3.3、外型尺寸:235x165x60(mm)4.3.4、输入电压:220~240V 50Hz AC4.3.5、内部电压:24V DC4.3.6、最小滴胶量:0.01ml4.3.7、输入气压:2.5~7 bar (35~100psi)4.4、高精密贴片机 1台4.4.1、CCD、液晶视频放大系统,可将图象放大10X;4.4.2、配有真空装置,不需另接气源;4.4.3、工作台面:220X220mm4.4.4、XY向调节范围40mm,Z向移动范围80mm4.4.5、旋转角度可调节正负,内置减压装置,操作快速灵活。
SMT贴片标准及工艺标准

二:印刷得一些不良現象
印刷得主要不良現象有少錫、錫量過多、過厚、 漏銅、短路、錫尖、偏移。
1、少錫,錫量過多,過厚。
此不良現象就是指印刷之錫量低於或高於標準錫 量,錫膏印刷過厚。
一般錫厚就是通過鋼板來決定得。錫厚不能低於 鋼板厚度或高於鋼板厚度得0、03mm。標準鋼板一般 分為:0、13mm,0、15mm,0、18mm。
錫焊應呈弧形。(如圖)
2、具有良好得導電性:即焊錫相互擴散形成合金屬、 3、具有一定得強度:即焊點必須具有一定抗拉強度 和抗衝擊韌性、 4、回焊時盡量使用N2,回焊效果更佳。
三:不良焊點、
生產中由於PCB線路設計,生產中工藝控制以及錫膏 得選擇等因素影響,均會出現不良焊點,所出現得不良時點 主要有以下几種:
SMT贴片标准及工艺标准
目錄
一:錫膏印刷工藝 二:作業貼片工藝 三:錫量回焊工藝
第一章:錫膏印刷工藝
一:簡述錫膏及印刷 錫膏可分為免洗型錫膏,現主流使用。FLUX在10
%以下,成份主要就是錫(Sn),鉛(Pb)組成,另無鉛錫 膏因單價較高還未廣泛使用。
印刷即就是通過鋼板將PCB焊墊(PAD)上印刷錫膏。 因好壞直接關系到生產品質,故有一定之標準。
件加熱至錫膏溶點溫度
恆溫區:使PCB及各種不同之零件有足夠時間吸收熱 量,以達到均溫,同時Flux完全揮發
回焊區:已活化得Flux及完全熔化得錫膏,開始進行焊 接功能
冷卻區:焊接功能完成,已熔化得錫膏快速冷卻完成焊 接
升溫區
恆溫區
預溫區
回焊區
冷卻區
圖七
二:回焊效果 1、回焊後之焊點應光滑,有光澤,吃錫性好,焊點與零
1、短路
現象:兩個直立得接點,因焊錫連通而導致電流跨越, 即不同線路上得焊點連在一起、(如圖)
SMT工艺标准

表面贴装技术(SMT)工艺标准Q/WP1101-20021范围本标准规定了本公司表面贴装生产的设备、器件、生产工艺方法、特点、参数以及产品和半成品的一般工艺要求以及关于表面贴装生产过程防静电方面的特殊要求。
本规范适用于我公司所有采用表面贴装的生产工艺。
2规范性引用文件SJ/T 10670-1995 表面组装工艺通用技术要求SJ/T 10666-1995 表面组装组件的焊点质量评定SJ/T 10668-1995 表面组装技术术语3术语3.1 一般术语a)表面组装技术---- SMT(Surface Mount Technology)。
b)表面组装元器件---SMD/SMC(Surface Mount Devices/ Surface Mount Components)。
c)表面组装组件--- SMA (Surface Mount Assemblys)。
d)表面组装印制板--- SMB (Surface Mount Board)。
e)回流焊(Reflow soldering)--- 通过重新熔化预先印制到印刷板焊盘上的锡膏焊料,实现SMD焊端或引脚与印制板焊盘之间的机械与电气连接的软钎焊。
f)峰焊(Wave soldering)--- 将熔化的软钎焊料,经电动泵或电磁泵喷流成设计要求的焊料波峰,使预先装有电子元器件的印制板通过焊料波峰,实现元器件焊端或引脚与印制板焊盘之间的机械与电气连接的软钎焊。
3.2 元器件术语a)焊端(Terminations)--- 无引线表面组装元器件的金属化外电极。
b)形片状元件(Rectangular chip component)两端无引线,有焊端,外形为薄片矩形的SMD。
c)外形封装 SOP(Small Outline Package)小外形模压塑料封装,两侧有翼形或J形短引脚的一种SMD。
d)小外形晶体管SOT(Small Outline Transistor)采用小外形封装结构的表面组装晶体管。
SMT工艺技术及其质量标准

SMT工艺技术及其质量标准SMT(表面贴装技术)是一种电子制造过程中广泛使用的技术,它通过将电子元件直接焊接到印刷电路板(PCB)的表面,实现了高效、快速和精确的组装过程。
在SMT工艺技术中,需要考虑的质量标准包括焊接质量、封装质量、组装精度等。
焊接质量是SMT工艺中最重要的质量标准之一。
一个良好的焊接质量保证了电子元件的稳定连接,从而确保电路板的正常工作。
焊接质量取决于焊接温度、焊接时间和焊料等因素。
焊接温度应在适当范围内控制,过高或过低的温度都会影响焊接质量。
焊接时间也需合理控制,过长或过短的焊接时间都会导致焊接不良。
此外,选择合适的焊料材料也是确保焊接质量的重要因素,常用的焊料材料包括锡铅合金和无铅焊料等。
封装质量是指对电子元件进行正确和可靠封装的能力。
封装质量直接影响电路板的耐用性和可靠性。
SMT工艺中常用的封装方式包括贴片封装和插件封装。
贴片封装要求组装精度高,确保元件正确放置并与焊盘对齐。
插件封装则要求焊脚与焊盘之间的间距和对齐度符合要求,以确保可靠焊接。
此外,封装过程中的焊接温度、焊接压力等参数也需要精确控制,以避免封装过程中的损伤或质量问题。
组装精度是指在SMT工艺中要求元件正确放置到PCB上的精度。
SMT设备通常通过计算机控制,能够精确定位和放置元件。
组装精度的准确性直接影响电路板的工作性能和稳定性。
组装精度的要求包括元件的位置精度、间距精度等。
在工艺过程中,需要合理设置设备参数,确保元件的正确放置和精确位置。
在SMT工艺中,以上质量标准是确保电子元件正确焊接和封装的关键。
通过合理控制焊接温度、焊接时间和焊料选择等因素,能够提高焊接质量。
同时,适当设置封装过程中的参数和精确控制元件的放置位置,能够保证封装质量和组装精度。
这些质量标准的保证,有助于提高SMT工艺的效率和产品质量。
继续关于SMT工艺技术及其质量标准的内容。
除了焊接质量、封装质量和组装精度,SMT工艺还需要考虑其他一些质量标准,以确保电路板的可靠性和稳定性。
SMT工艺参数介绍

自动化程度高
可靠性高
灵活性高
可以实现自动化生产, 提高生产效率和产品质
量。
焊接可靠性强,可以减 少产品故障和维修成本。
可以快速适应不同产品 种类的生产需求,灵活
度高。
SMT设备与工具
02
贴片机
01
02
03
贴片速度
贴片机的贴片速度是衡量 其性能的重要参数,它决 定了生产效率。
贴片精度
光学放大倍数
指检测系统中的光学放大倍数,通常以“倍数”为单位。
检测光源类型
指检测系统中使用的光源类型,如LED光源、卤素光源等。
SMT工艺材料
04
焊料
焊料是用于将电子元件与 PCB板连接起来的金属材 料。
焊料的熔点是关键参数, 需要根据不同的元件和工 艺要求选择合适的熔点。
ABCD
常见的焊料有锡铅合金、 纯锡、纯铅等,其中锡铅 合金应用最为广泛。
贴片机的贴片精度决定了 元器件贴装的准确性和可 靠性,是保证产品质量的 关键。
吸嘴类型和数量
吸嘴的类型和数量影响贴 片机对不同元器件的适应 性和贴装速度。
印刷机
印刷精度
印刷机的印刷精度决定了 焊锡膏的分布精度,直接 影响到元器件的焊接质量。
印刷速度
印刷机的印刷速度决定了 生产效率,是印刷机性能 的重要指标。
焊料的成分和纯度对焊接 质量有很大影响,杂质过 多或成分不均会导致焊接 不良。
胶水
01
02
03
04
胶水在SMT工艺中主要用于 固定电子元件,防止其移动或
脱落。
常见的胶水有热熔胶、快干胶 、环氧胶等。
胶水的粘度、固化时间和粘附 力是关键参数,需要根据元件 的尺寸和工艺要求选择合适的
SMT设备参数简介

真空烘箱
技术参数 1.真空度范围:0~0.1MPa 2.漏气量:1KPa/小时 3.机器尺寸:L940mm,W830mm, H1250mm 4.工作尺寸:L620mm,W650mm,H610mm 5.机器重量:0.4t 环境要求 1.电压:220VAC(+-10%) 2.频率:50/60 Hz 3.气压要求:0.5Mpa (5kgf/cm2) 4.温度:0℃--40℃ 5.湿度:30%----80%
FUJI NXTⅡ
环境要求 1.电压:110VAC(+-10%), 2.频率:50/60 Hz 3.气压要求:0.5Mpa (5kgf/cm2) 4.温度:15℃--35℃ 5.湿度:30%----80% 技术参数
1.贴片范围:01005-7.5*7.5mm,高度9.5mm以下的零件 2.生产能力:V12:26000cph;H08:10500cph ;H04:6500cph 3.贴片精度:±0.038mm 4.适用基板:最大534x610mm,最小48x48mm, 厚度0.3-4mm 5.料架支持:160个站位 6.机器尺寸:L2590mm,W1900mm,H1474mm(排除信号塔) 7.机器重量:4t
GKG G5
环境要求 1.电压:220VAC(+-10%) 2.频率:50/60 Hz 3.气压要求:0.5Mpa (5kgf/cm2) 4.温度:15℃--35℃ 5.湿度:30%----80% 技术参数 1.印刷范围: 410X489mm 2.印刷速度:2.0-150.0mm/sec 3.印刷精度:±0.025mm 4.适用基板:最大400X310mm 最小50X50mm, 厚度0.4~6.0mm 5.机器尺寸:L1105mm,W1500mm,H1400mm(排除信号塔) 6.机器重量:1t
SMT生产工艺及生产设备分析
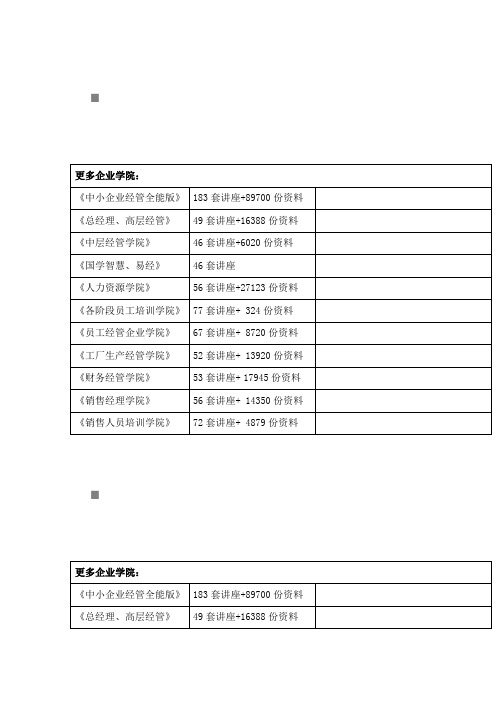
⏹⏹SMT生产设备工作环境要求SMT生产设备是高精度的机电一体化设备,设备和工艺材料对环境的清洁度、湿度、温度都有一定的要求,为了保证设备正常运行和组装质量,对工作环境有以下要求:1:电源:电源电压和功率要符合设备要求电压要稳定,要求:单相AC220(220±10%,50/60 HZ)三相AC380V(220±10%,50/60 HZ)如果达不到要求,需配置稳压电源,电源的功率要大于功耗的一倍以上。
2:温度:环境温度:23±3℃为最佳。
一般为17~28℃。
极限温度为15~35℃(印刷工作间环境温度为23±3℃为最佳)3:湿度:相对湿度:45~70%RH4:工作环境:工作间保持清洁卫生,无尘土、无腐蚀性气体。
空气清洁度为100000级(BGJ73-84);在空调环境下,要有一定的新风量,尽量将CO2含量控制在1000PPM以下,CO含量控制10PPM以下,以保证人体健康。
5:防静电:生产设备必须接地良好,应采用三相五线接地法并独立接地。
生产场所的地面、工作台垫、坐椅等均应符合防静电要求。
6:排风:再流焊和波峰焊设备都有排风要求。
7:照明:厂房内应有良好的照明条件,理想的照度为800LUX×1200LUX,至少不能低于300LUX。
8:SMT生产线人员要求:生产线各设备的操作人员必须经过专业技术培训合格,必须熟练掌握设备的操作规程。
操作人员应严格按"安全技术操作规程"和工艺要求操作。
(一) 片式元器件单面贴装工艺↓说明:步骤1:检查元件、焊盘、焊膏是否有氧化、焊锡成分是否匹配,集成电路引脚及其共面性。
步骤2:通过焊膏印刷机或SMT焊膏印刷台、印刷专用刮板及SMT漏板将SMT焊膏漏印到PCB的焊盘上。
步骤3:检查所印线路板焊膏是否有漏印,粘连、焊膏量是否合适等。
步骤4:由贴片机或真空吸笔、镊子等完成贴装。
步骤5:检查所贴元件是否放偏、放反或漏放,并修复,窄间距元件需用显微镜实体检查。
smt各流程工艺要求和品质注意事项

smt各流程工艺要求和品质注意事项下载温馨提示:该文档是我店铺精心编制而成,希望大家下载以后,能够帮助大家解决实际的问题。
文档下载后可定制随意修改,请根据实际需要进行相应的调整和使用,谢谢!并且,本店铺为大家提供各种各样类型的实用资料,如教育随笔、日记赏析、句子摘抄、古诗大全、经典美文、话题作文、工作总结、词语解析、文案摘录、其他资料等等,如想了解不同资料格式和写法,敬请关注!Download tips: This document is carefully compiled by theeditor. I hope that after you download them,they can help yousolve practical problems. The document can be customized andmodified after downloading,please adjust and use it according toactual needs, thank you!In addition, our shop provides you with various types ofpractical materials,such as educational essays, diaryappreciation,sentence excerpts,ancient poems,classic articles,topic composition,work summary,word parsing,copy excerpts,other materials and so on,want to know different data formats andwriting methods,please pay attention!SMT(Surface Mount Technology,表面贴装技术)是一种电子组装技术,它将无引脚或短引脚的电子元件直接安装在印刷电路板(PCB)的表面,并通过自动化的设备进行焊接。
SMT设备参数简介

设备维护参数
01
02
03
维护周期
指设备需要定期进行维护 保养的时间间隔,如每日、 每周、每月等。
维护内容
描述每次维护保养的具体 内容,如清洁、检查、更 换部件等。
维护工具与备件
列出维护保养所需的工具 和备件,以及其规格和数 量。
03
SMT设备参数对生产的影 响
设备型号对生产的影响
设备型号的选择直接决定了生产效率和产品质量。不同型号的设备具有不同的性 能参数和功能特点,适合不同的生产需求。选择适合产品特点的设备型号可以提 高生产效率、减少废品率。
SMT设备参数简介
目录 CONTENT
• SMT设备概述 • SMT设备参数详解 • SMT设备参数对生产的影响 • SMT设备的未来发展趋势 • SMT设备的选择建议
01
SMT设备概述
SMT设备定义
表面贴装技术(Surface Mount Technology,简称SMT)设备是指用 于实现表面贴装技术工艺的设备,主 要包括贴片机、印刷机、回流焊等。
效率
设备的效率决定了企业的生产效率和产能,选择高效率的设备能够 提高企业的竞争力。
考虑设备的操作便利性
操作性
设备的操作界面和控制系统应简单易用,方便操 作人员快速掌握和操作。
维护性
设备的维护和保养应方便快捷,降低维护成本和 时间成本。
升级性
设备的软件和硬件应具有良好的升级性和扩展性, 满足企业未来发展的需求。
精度要求
描述设备在加工过程中对零件位置、尺寸等精度的控 制能力。
可靠性
指设备在长时间运行过程中保持稳定和准确性能的能 力。
设备操作参数
操作界面
设备的控制面板、显示屏等操作界面,要求易 于理解和操作。
SMT贴片机器标准产能

SMT贴片机器标准产能首先,需要了解SMT贴片机的工作原理。
SMT贴片机主要由供料系统、排料系统、传送系统和贴片头体系组成。
工作时,原料为贴片元件的无源元器件或贴片绕组预贴片元件,以及不同形状的贴片夹具,通过供料系统进行供料,经传送系统将元器件传送至贴片头的接料区,再由贴片头将元器件贴在PCB板的印刷电路上,最后经排料系统排出。
1.设备性能:不同型号的SMT贴片机在设计时就具备不同的生产能力,通常会有最高速度和最高精度的指标。
高性能设备通常具有更高的产能,能够更快速、准确地完成各项工作。
2.贴片元件尺寸:贴片元件的尺寸越小,单个元器件的贴装时间越短,从而提高了生产效率和贴片机的产能。
相反,大尺寸元件则需要更长时间贴装,影响产能。
3.贴装头的数量:SMT贴片机通常配备多个贴装头,能够同时完成多个元器件的贴装任务。
贴装头的数量越多,每个贴装头可以同时进行的贴装任务就越多,产能也就越高。
4.机器的工作模式:SMT贴片机通常有连续工作模式和间歇工作模式两种。
在连续工作模式下,贴片机可以一直运行,不需要停机,相比之下,间歇工作模式下需要每次贴装任务结束后停机,等待下一个任务。
因此,连续工作模式下贴片机的产能更高。
5.设备维护和操作:定期进行设备维护和保养可以保证设备的良好状态,减少故障和停机时间,从而提高产能。
同时,操作人员的操作水平和熟练度也会影响到SMT贴片机的产能。
总结起来,SMT贴片机的标准产能是一个复杂的指标,受多方面因素的影响。
一台高性能、多贴装头、工作模式为连续工作的SMT贴片机,在适当的维护和操作下,可以达到较高的产能水平。
当然,具体产能还需要根据实际工艺参数、元器件类型和大小等因素进行具体的测试和分析。
SMT工艺控制标准
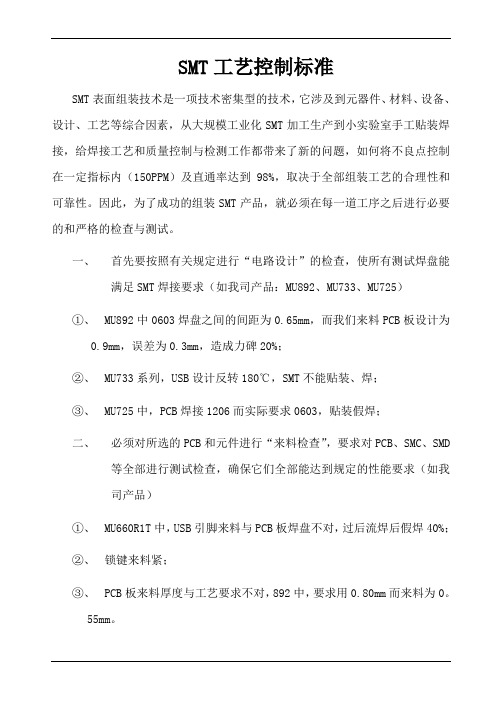
SMT工艺控制标准SMT表面组装技术是一项技术密集型的技术,它涉及到元器件、材料、设备、设计、工艺等综合因素,从大规模工业化SMT加工生产到小实验室手工贴装焊接,给焊接工艺和质量控制与检测工作都带来了新的问题,如何将不良点控制在一定指标内(150PPM)及直通率达到98%,取决于全部组装工艺的合理性和可靠性。
因此,为了成功的组装SMT产品,就必须在每一道工序之后进行必要的和严格的检查与测试。
一、首先要按照有关规定进行“电路设计”的检查,使所有测试焊盘能满足SMT焊接要求(如我司产品:MU892、MU733、MU725)①、MU892中0603焊盘之间的间距为0.65mm,而我们来料PCB板设计为0.9mm,误差为0.3mm,造成力碑20%;②、MU733系列,USB设计反转180℃,SMT不能贴装、焊;③、MU725中,PCB焊接1206而实际要求0603,贴装假焊;二、必须对所选的PCB和元件进行“来料检查”,要求对PCB、SMC、SMD等全部进行测试检查,确保它们全部能达到规定的性能要求(如我司产品)①、MU660R1T中,USB引脚来料与PCB板焊盘不对,过后流焊后假焊40%;②、锁键来料紧;③、PCB板来料厚度与工艺要求不对,892中,要求用0.80mm而来料为0。
55mm。
三、必须在SMT产品生产过程中,自始自终坚持按规定进行工序间及组装结束后的检查和测试,确保SMT产品的质量要求和可靠性。
温度必须在20℃-27℃1.车间环境温度必须在45%/H-65%/H无尘、防静电2、锡膏的使用:平时要把锡膏保存在0-10℃之间的环境中,使用前,提前2H将其取出,置于室温,且使用前应该充分搅拌,以保证锡膏黏度均匀一致。
3、印刷:事实表明,超过半数的焊接不良问题都与印刷部分有关;①、钢网要求:0.6mm-0.4mm间距的IC一般选用0.12mm-0.14mm钢网;②、印刷方式:a、刮刀硬度:60-90HS(金属刮刀式聚胺甲刮刀)b、刮刀角度:45℃-60℃c、印刷压为:(2~4)*10*5pa正紧标准:20-40mm/seld、印刷速度印刷细间距时:15-20mm/sel印刷宽间距时:50-100mm/sel④、印刷时需注意的技术要点:a、印刷前需检查刮刀、钢网等用具;b、将钢网与PCB之间的位置调整到越吸越好;c、开始印刷时所加到钢网上的锡膏要适量,一般A5规格钢网加工200g左右,B5为300g左右,A4为400g左右;d、连续印刷时,每隔一段时间应清洗钢网的上下面;e、不能使锡膏在钢网上停留太久,其印刷性能不黏性边差;f、作业结束前应将钢网上下面彻底清洗干净。
SMT工艺标准
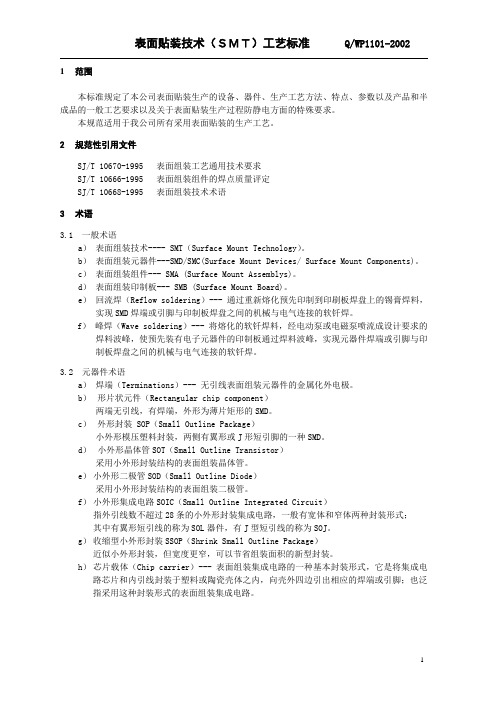
表面贴装技术(SMT)工艺标准Q/WP1101-20021范围本标准规定了本公司表面贴装生产的设备、器件、生产工艺方法、特点、参数以及产品和半成品的一般工艺要求以及关于表面贴装生产过程防静电方面的特殊要求。
本规范适用于我公司所有采用表面贴装的生产工艺。
2规范性引用文件SJ/T 10670-1995 表面组装工艺通用技术要求SJ/T 10666-1995 表面组装组件的焊点质量评定SJ/T 10668-1995 表面组装技术术语3术语3.1 一般术语a)表面组装技术---- SMT(Surface Mount Technology)。
b)表面组装元器件---SMD/SMC(Surface Mount Devices/ Surface Mount Components)。
c)表面组装组件--- SMA (Surface Mount Assemblys)。
d)表面组装印制板--- SMB (Surface Mount Board)。
e)回流焊(Reflow soldering)--- 通过重新熔化预先印制到印刷板焊盘上的锡膏焊料,实现SMD焊端或引脚与印制板焊盘之间的机械与电气连接的软钎焊。
f)峰焊(Wave soldering)--- 将熔化的软钎焊料,经电动泵或电磁泵喷流成设计要求的焊料波峰,使预先装有电子元器件的印制板通过焊料波峰,实现元器件焊端或引脚与印制板焊盘之间的机械与电气连接的软钎焊。
3.2 元器件术语a)焊端(Terminations)--- 无引线表面组装元器件的金属化外电极。
b)形片状元件(Rectangular chip component)两端无引线,有焊端,外形为薄片矩形的SMD。
c)外形封装 SOP(Small Outline Package)小外形模压塑料封装,两侧有翼形或J形短引脚的一种SMD。
d)小外形晶体管SOT(Small Outline Transistor)采用小外形封装结构的表面组装晶体管。
- 1、下载文档前请自行甄别文档内容的完整性,平台不提供额外的编辑、内容补充、找答案等附加服务。
- 2、"仅部分预览"的文档,不可在线预览部分如存在完整性等问题,可反馈申请退款(可完整预览的文档不适用该条件!)。
- 3、如文档侵犯您的权益,请联系客服反馈,我们会尽快为您处理(人工客服工作时间:9:00-18:30)。
SMT设备性能参数对生产基本的工艺要求针对在实际的生产中设备与工艺的可制造性出现的冲突异常,现将一些在实际操作中常使用及注意事项的要求参数整理汇总,同时将经常出现的一些工艺上要求汇总与大家分享一下以便我们共同努力提高制程能力,详细如下:
AI设备参数要求:
SMT设备参数要求:
二:550mm*650mm网框,铝框厚度25.4mm,铝框宽度38.1mm。
三:29*29英寸,网框尺寸736mm*736mm,铝框厚度40.00mm,铝框宽度40.00mm。
制程中不良案例分析及改善措施
一、自动插件时,发现供料的MZ31-04M 400-500Ω热敏电阻出现引脚断裂的不良现象(见附图)。
引脚插件时断裂对自动插件设备造成损坏隐患;且从引脚断裂面分析,部分物料可能存在电性能不良可能
原因:从提供的图片来分析为表面受力,工序周转时个别产品受到撞击,本体所承受的拉力较小,易断;测阻值时没有能对已受到的外力的产品测出。
措施:焊接工序增加外观全检,工序周转时由专人操作避免粗暴作业;控制锡炉的温度每小时做到点检,由QC及生产小组长监督与抽查;阻值测试现调整为全检;对员工培训。
二、发现FR105编带脱胶严重,影响机插:
产生不良的原因有以下两种可能:
1、在后道编带过程中,由于操作人员调试不当,没有将机器的压轮调节到位,从而使该批编带由
于没有压紧,在运输过程中的受到各种力作用使得编带松动、脱胶。
2、该批次的编带粘性不良。
改善控制措施:
1、对于原因一,我们对作业记录及同一机器当天其它批次的产品进行检查,并没有发现任何异常。
2、对于原因二,由于我司IQC对编带粘性没有检验手段,我们已经与供应联系,让其分析产生不
良的原因,并进行整改。
3、针对我司目前对编带粘性没有检验手段这一情况,我司已经组织相关人员进行制定,目前工作
正在进行中。
三、使用过程中发现有一盘二极管存在本体不齐的现象;
原因:主要是胶带粘合不紧密造成。
四、引脚从根部脱焊断裂
在自动插件生产时,发现供料的RY 2W301 J 编带小型电阻在引脚打弯时有引脚从根部断裂的现象,查看引脚断口可以看出引脚端部未形成良好焊点(见附图)。
生产使用10000PCS 电阻有30PCS引脚断裂,不良比率为0.3%。
此现象对自动插件设备会造成损坏隐患且影响生产效率
原因:焊接夹嘴在焊接夹线时没夹紧铜线,造成滑线情形,导致假焊发生人员在自主检验时没有发现此不良。
改正措施:要求设备人员将夹嘴松紧度作为重点对象核查。
五、物料剥离
下述现象会造成元件散落,无法使用SMT设备进行贴装。
六、FPC生产偏移问题:
测量数据
2008年6月2日11时22分8秒星期一(质量部提供测试)
序号名称X坐标Y坐标Z坐标距离半径直径角度
1 线14.379
2 50.2679 3.7415 179.5724
2 圆17.7915 54.8794 4.5046 0.7169 1.4339
3 距离[2-1] 4.6368(偏移焊盘外沿到Mark点的距离)
4 线7.6648 47.9038 3.0159 91.0609
5 圆 2.861
6 47.9042 4.4996 0.7161 1.4323
6 距离[5-4] 4.8023(正常焊盘外沿到Mark点的距离)
7 线 5.0343 47.2064 4.0578 90.1314
8 线10.3392 43.6791 3.6114 89.2617
9 距离[7-8] 5.3242(偏移焊盘两端的距离)
10 线 6.5901 47.4779 3.8160 89.4410
11 线11.9323 43.9971 3.5273 90.0000
12 距离[10-11] 5.3586(正常焊盘两端的距离)
13 线 1.6771 40.0091 3.2848 90.9741
14 圆-4.5013 39.8249 4.4911 0.7148 1.4296
15 距离[14-13] 6.1807(偏移焊盘Mark点到发光管本体外沿的距离)
16 线 3.4939 42.9292 3.2204 90.6623
17 圆-2.6653 42.6490 4.4735 0.7120 1.4240
18 距离[17-16] 6.1620(正常焊盘Mark点到发光管本体外沿的距离) 从上面测试的数据可以看出:两块线路板SMT发光二极管贴装位置正常,但因白油丝印偏移,造成一块线路板其焊盘偏移(焊盘外沿离Mark点较近)。
详细图解如下:
正常测量出的数据:
因此要解决印刷的偏移及焊接的漏铜问题首先要解决白油丝印偏移及FPC板差问题,这是解决所有问题的关键,如果此问题不易解决可以考虑对元件封装进行更改,如果不解决这个问题就会出现上述图示的不良现状及焊接上的一些不良现状。
工艺要求参考
一、SMT贴装元件的封装要求:
如图所示:正常的使用贴装物料在进行编带时料槽的深度与左右上下的误差要求要控制在大于元件实际的尺寸在上下为0.1到0.3MM,左右控制在0.15到0.3MM,深度控制在0.1到0.2MM;
二、SMT生产中贴片机对MARK点的要求:
基准标记(Mark)作用:为了纠正PCB加工、变形引起的误差,在PCB上画出的用于光学定位的一组图形,主要用于全自动印刷机、贴装机和检验设备等工序。
放置要求如下:
另外孔定位的定位孔位置在离PCB各边5MM处,孔径一般取直径4MM与直径5MM;
以上相关的分析均来自实际生产中,期间如有不足之处欢迎提出!资料仅供大家参考!
刘加伟
2009-6-11。