超声波和射线探伤区别
五大常规无损检测

五大常规无损检测PT=渗透探伤MT=磁粉探伤UT=超声波探伤RT=射线探伤ET=涡流探伤五大常规无损检测:渗透探伤、磁粉探伤、超声波探伤、射线探伤、涡流探伤,1.射线探伤也就是X光拍片简称RT,2.超声波检查简称UT,射线探伤和超声波探伤一般适用于主甲板,外板,横舱壁,内底板,上下边柜斜板等对接的焊缝。
施工者对要求射线探伤的焊缝及热影响区域进行打磨处理,消除焊缝表面的凹凸不平对底片影像显示的影响,确保无油污、无油漆、无飞溅。
射线探伤有一定的杀伤性,船方及各施工部门在X光射线探伤时段、不得靠近X光射线探伤位置半径三十米范围的警示区域,防止射线伤害人员。
3.磁粉探伤又称MT或者MPT(Magnetic Particle Testing),一般适用于对接焊缝,角焊缝,尾轴及锻钢件,铸钢等磁性材料的表面附近进行探伤的检测方法。
利用铁受磁石吸引的原理进行检查。
在进行磁粉探伤检测时,使被测物收到磁力的作用,将磁粉(磁性微型粉末)散布在其表面。
然后,缺陷的部分表面所泄漏出来泄露磁力会将磁粉吸住,形成图案。
指示图案比实际缺陷要大数十倍,因此很容易便能找出缺陷。
磁粉探伤检测一般按照前处理→磁化→喷淋磁粉→观察→后处理的步骤进行4.渗透探伤简称PT,着色一般适用于船体对接焊缝,角焊缝等,螺旋桨叶根部,锻钢件、铸钢件表面。
当机械零部件需磁粉探伤或着色探伤时,则要将被探物件表面的油污清洁干净并摆放整齐,如果焊缝做磁粉探伤或着色探伤时,则需将焊道清洁干净,要求无油污、无油漆、无飞溅。
5.涡流检测(ET)的英文名称是:Eddy Current Testing工业上无损检测的方法之一。
给一个线圈通入交流电,在一定条件下通过的电流是不变的。
如果把线圈靠近被测工件,像船在水中那样,工件内会感应出涡流,受涡流影响,线圈电流会发生变化。
由于涡流的大小随工件内有没有缺陷而不同,所以线圈电流变化的大小能反映有无缺陷。
适用于导电材料..由于导体自身各种因素(如电导率,磁导率,形状,尺寸和缺陷等)的变化,会导致感应电流的变化,利用这种现象而判知导体性质,状态的检测方法叫做涡流检测方法.属于表面探伤法,适用于钢铁、有色金属、石墨等导电体工件,因为并不需要接触工件,所以检测速度很快,但设备昂贵。
钢板探伤标准

钢板探伤标准钢板探伤是指利用探伤技术对钢板进行检测,以发现和评定钢板内部缺陷的一种工艺。
钢板探伤标准是对钢板探伤工艺和方法进行规范和要求的文件,是保证钢板质量和安全的重要依据。
本文将介绍钢板探伤的一般标准和常见方法,以便广大生产和使用钢板的人员了解和掌握相关知识。
一、钢板探伤的一般标准。
1. 钢板探伤的目的。
钢板探伤的目的是为了发现和评定钢板内部的缺陷,包括裂纹、夹杂、气孔等,以保证钢板的质量和安全性。
2. 钢板探伤的要求。
钢板探伤应符合国家相关标准和规定,探伤人员应具备专业的技术知识和操作技能,探伤设备应符合要求,并经过定期检验和校准。
3. 钢板探伤的分类。
钢板探伤可分为常规探伤、超声波探伤、射线探伤等不同方法,具体应根据钢板的材质、厚度和使用要求进行选择。
二、钢板探伤的常见方法。
1. 常规探伤。
常规探伤是指利用目视、触摸和简单工具进行检测,适用于对表面缺陷和局部缺陷的初步检测。
2. 超声波探伤。
超声波探伤是利用超声波的传播和反射规律来检测钢板内部缺陷的方法,具有高灵敏度和精度的优点,适用于对钢板整体和局部的全面检测。
3. 射线探伤。
射线探伤是利用X射线或γ射线对钢板进行透射检测,可以发现钢板内部的细小缺陷,适用于对厚钢板和复杂结构的检测。
三、钢板探伤的注意事项。
1. 保护探伤人员的安全。
在进行钢板探伤时,应做好防护措施,避免辐射和化学品的危害,确保探伤人员的安全。
2. 确保探伤设备的正常使用。
探伤设备应经过定期检验和维护,确保其性能稳定和准确度,避免因设备故障导致探伤结果的不准确。
3. 对探伤结果的评定和记录。
对探伤结果应进行准确的评定和记录,包括缺陷的类型、位置、大小等信息,以便对钢板进行合理的处理和使用。
四、结语。
钢板探伤是保证钢板质量和安全的重要环节,掌握相关知识和技能对于生产和使用钢板的人员至关重要。
希望本文能够为大家提供一些参考和帮助,使钢板探伤工作更加规范和有效。
五大常规探伤方法概述及其特点
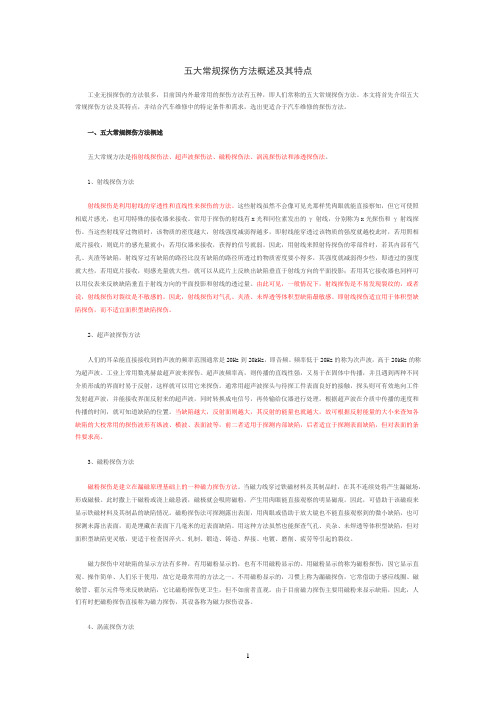
五大常规探伤方法概述及其特点工业无损探伤的方法很多,目前国内外最常用的探伤方法有五种,即人们常称的五大常规探伤方法。
本文将首先介绍五大常规探伤方法及其特点,并结合汽车维修中的特定条件和需求,选出更适合于汽车维修的探伤方法。
一、五大常规探伤方法概述五大常规方法是指射线探伤法、超声波探伤法、磁粉探伤法、涡流探伤法和渗透探伤法。
1、射线探伤方法射线探伤是利用射线的穿透性和直线性来探伤的方法。
这些射线虽然不会像可见光那样凭肉眼就能直接察知,但它可使照相底片感光,也可用特殊的接收器来接收。
常用于探伤的射线有x光和同位素发出的γ射线,分别称为x光探伤和γ射线探伤。
当这些射线穿过物质时,该物质的密度越大,射线强度减弱得越多,即射线能穿透过该物质的强度就越校此时,若用照相底片接收,则底片的感光量就小;若用仪器来接收,获得的信号就弱。
因此,用射线来照射待探伤的零部件时,若其内部有气孔、夹渣等缺陷,射线穿过有缺陷的路径比没有缺陷的路径所透过的物质密度要小得多,其强度就减弱得少些,即透过的强度就大些,若用底片接收,则感光量就大些,就可以从底片上反映出缺陷垂直于射线方向的平面投影;若用其它接收器也同样可以用仪表来反映缺陷垂直于射线方向的平面投影和射线的透过量。
由此可见,一般情况下,射线探伤是不易发现裂纹的,或者说,射线探伤对裂纹是不敏感的。
因此,射线探伤对气孔、夹渣、未焊透等体积型缺陷最敏感。
即射线探伤适宜用于体积型缺陷探伤,而不适宜面积型缺陷探伤。
2、超声波探伤方法人们的耳朵能直接接收到的声波的频率范围通常是20Hz到20kHz,即音频。
频率低于20Hz的称为次声波,高于20kHz的称为超声波。
工业上常用数兆赫兹超声波来探伤。
超声波频率高,则传播的直线性强,又易于在固体中传播,并且遇到两种不同介质形成的界面时易于反射,这样就可以用它来探伤。
通常用超声波探头与待探工件表面良好的接触,探头则可有效地向工件发射超声波,并能接收界面反射来的超声波,同时转换成电信号,再传输给仪器进行处理。
无损检测(射线,超声)
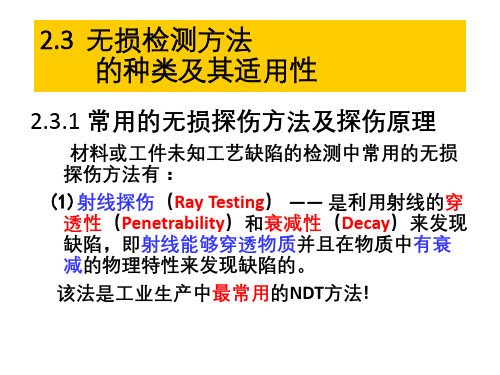
3.1.3 射线的产生
射线的性质,有利、有弊,应该科学地加以利 用和防范!射线学就是研究如何利用与防范射线 的科学。下面介绍产生x射线的主要设备: (1)x光管基本组成: • 阴极部件:灯丝(钨丝)——发射电子; 阴极罩——聚焦电子。 • 阳极部件:阳极靶——接收电子; 冷却介质——散热作用。 • 真空管——玻璃或金属陶瓷制作的真空外罩。
2.3.1 常用的无损探伤方法及探伤原理
(2)超声波探伤(Ultrasonic testing)—— 是利用超声波在 物质中传播(Propagation)、反射(Reflection)和 (Decay)等物理性质来发现缺陷的。 该法与射线探伤法形成优势互补. (3)磁力探伤(Magnetic testing)—— 是通过对铁磁材料 进行磁化所产生的漏磁场(Leakage magnetic field) 来发现其表面及近表面缺陷的。 在黑色金属( ferrous metal )的表面检测中应用广泛.
3.1.2 射线的性质 (1)不可见,直线传播—具有隐蔽性和指向性; (2)不带电,因而不受电磁场影响—电中性; (3)能穿透物质,但有衰减—具有穿透性和衰减性; 对同1种射线而言,功率越大,穿透性越强,衰减越慢; (4)能与某些物质产生光化作用,使荧光物质发光;可 使胶片感光—可成像; (5)能使某些气体电离—即产生电离辐射; (6)与光波一样,有反射、折射、干涉现象; (7)能产生生物效应,伤害和杀死生物细胞 —对人体有害。(此点非常重要)
2.3 无损检测方法 的种类及其适用性
2.3.1 常用的无损探伤方法及探伤原理
材料或工件未知工艺缺陷的检测中常用的无损 探伤方法有: (1)射线探伤(Ray Testing) —— 是利用射线的穿 透性(Penetrability)和衰减性(Decay)来发现 缺陷,即射线能够穿透物质并且在物质中有衰 减的物理特性来发现缺陷的。 该法是工业生产中最常用的NDT方法!
超声波和射线探伤

超声波和射线探伤都是无损检测,什么情况下用超声波,什么情况下用射线是由施工内容对应的施工设计说明和施工及验收规范来确定的。
也有一些情况是双重要求,如在长输管道内设计一般会要求100%的射线检测再用超声波来复验,也有一些规范会用射线或超声波来检验,由业主和施工单位自行确定。
一般情况下由于射线检测具有追溯性而且检测精度高于超声波,所以原则上是不能由超声波替代的。
但超声波对裂纹的敏感性要比射线强,因此对一些高强度的容易出现裂纹的焊缝会增加超声波检验。
1、超声波检测原理:超声波探伤:是利用超声能透入金属材料的深处,并由一截面进入另一截面时,在界面边缘发生反射的特点来检查零件缺陷的一种方法,当超声波束自零件表面由探头通至金属内部,遇到缺陷与零件底面时就分别发生反射波来,在萤光屏上形成脉冲波形,根据这些脉冲波形来判断缺陷位置和大小。
超声波在介质中传播时,在不同质界面上具有反射的特性,如遇到缺陷,缺陷的尺寸等于或大于超声波波长时,则超声波在缺陷上反射回来,探伤仪可将反射波显示出来;如缺陷的尺寸甚至小于波长时,声波将绕过射线而不能反射;波声的方向性好,频率越高,方向性越好,以很窄的波束向介质中辐射,易于确定缺陷的位置。
超声波的传播能量大,如频率为1MHZ(100赫兹)的超生波所传播的能量,相当于振幅相同而频率为1000HZ(赫兹)的声波的100万2、射线检测原理:射线探伤是利用射线的穿透性和直线性来探伤的方法。
这些射线虽然不会像可见光那样凭肉眼就能直接察知,但它可使照相底片感光,也可用特殊的接收器来接收。
常用于探伤的射线有x光和同位素发出的γ射线,分别称为x光探伤和γ射线探伤。
当这些射线穿过(照射)物质时,该物质的密度越大,射线强度减弱得越多,即射线能穿透过该物质的强度就越小。
此时,若用照相底片接收,则底片的感光量就小;若用仪器来接收,获得的信号就弱。
因此,用射线来照射待探伤的零部件时,若其内部有气孔、夹渣等缺陷,射线穿过有缺陷的路径比没有缺陷的路径所透过的物质密度要小得多,其强度就减弱得少些,即透过的强度就大些,若用底片接收,则感光量就大些,就可以从底片上反映出缺陷垂直于射线方向的平面投影;若用其它接收器也同样可以用仪表来反映缺陷垂直于射线方向的平面投影和射线的透过量。
超声波检测讲义
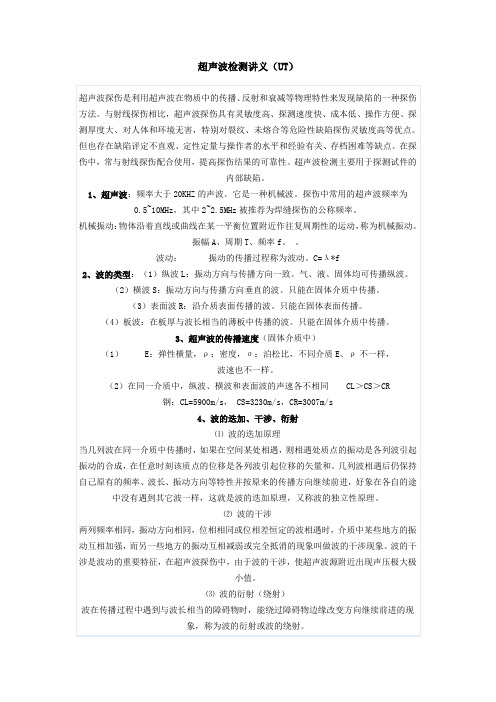
超声波检测讲义(UT)无损检测培训资料--超声波检测通用工艺规程1.主要内容与适用范围本规程规定了焊缝超声检测人员具备的资格、仪器、探头、试块、检测技术方法和质量分级等。
本规程适用于本公司生产的厚度为6mm~30mm钢制承压设备全熔化焊的超声检测。
不适用于铸钢及奥氏体钢焊缝,外径小于159mm的钢管对接焊缝,内径小于或等于250mm或内外径之比小于80%的纵向焊缝检测。
本规程按JB4730的要求编写,符合《容规》和GB150等要求。
检测工艺卡是本规程的补充,由Ⅱ级人员按本规程等要求编制,其检测参数规定的更具体。
2.引用标准、法规JB/T4730-2005《承压设备无损检测》GB150-1998《钢制压力容器》JB/T9214-1999《A型脉冲反射式超声波探伤系统工作性能测试方法》JB/T10061-1999《A型脉冲反射式超声波探伤仪通用技术条件》JB/T10062-1999《超声探伤用探头性能测试方法》3.检测人员3.1检测人员必须经过培训,按《特种设备无损检测人员考核与监督管理规则》的要求。
经理论和实践考试合格,取得相应等级资格证书的人员担任。
3.1.1检测人员每年应检查一次身体,其矫正视力不低于1.0。
4.探伤仪、探头和试块4.1探伤仪采用A型脉冲反射式超声波探伤仪器,其工作频率范围为0.5 MHz~10MHz,仪器至少在荧光屏满刻度的80%范围内呈线性显示。
仪器应具有80dB以上的可调衰减器,步进级每档不大于2Db,其精度为任意相邻12 dB的误差在±1dB 以内,最大累计误差不超过1dB.。
水平线性误差不大于1%,垂直线性误差不大于5%。
4.2探头4.2.1晶片面积一般不应超过500mm2,且任意一边长原则上不大于25 mm 。
4.2.2单斜探头声束轴线水平偏离角不应大于2度,主声束垂直方向不应有明显的双峰。
4.3仪器和探头的系统性能4.3.1在达到所检工件的最大检测声程时,其灵敏度余量应≥10dB。
铸铁探伤标准
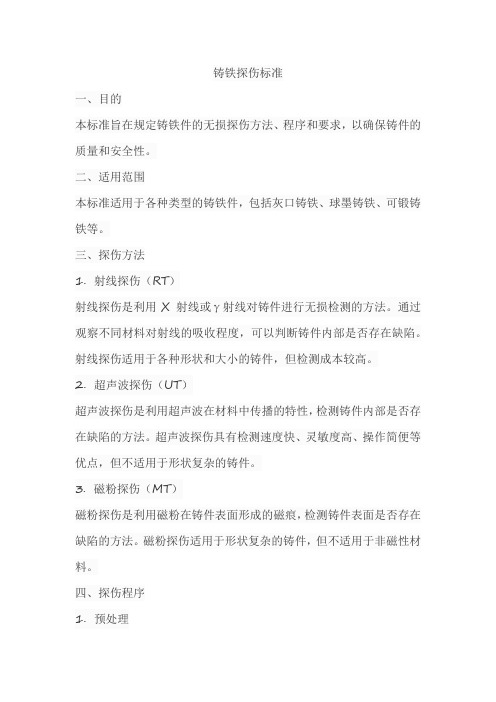
铸铁探伤标准一、目的本标准旨在规定铸铁件的无损探伤方法、程序和要求,以确保铸件的质量和安全性。
二、适用范围本标准适用于各种类型的铸铁件,包括灰口铸铁、球墨铸铁、可锻铸铁等。
三、探伤方法1. 射线探伤(RT)射线探伤是利用X射线或γ射线对铸件进行无损检测的方法。
通过观察不同材料对射线的吸收程度,可以判断铸件内部是否存在缺陷。
射线探伤适用于各种形状和大小的铸件,但检测成本较高。
2. 超声波探伤(UT)超声波探伤是利用超声波在材料中传播的特性,检测铸件内部是否存在缺陷的方法。
超声波探伤具有检测速度快、灵敏度高、操作简便等优点,但不适用于形状复杂的铸件。
3. 磁粉探伤(MT)磁粉探伤是利用磁粉在铸件表面形成的磁痕,检测铸件表面是否存在缺陷的方法。
磁粉探伤适用于形状复杂的铸件,但不适用于非磁性材料。
四、探伤程序1. 预处理对铸件进行清洗、干燥和打磨等处理,以去除表面杂质和氧化层,确保探伤结果的准确性。
2. 探伤操作根据铸件的大小和形状选择合适的探伤方法,按照探伤设备的操作规程进行探伤操作。
在操作过程中应注意以下几点:a) 确定合适的探伤灵敏度;b) 确保探头与铸件表面紧密贴合;c) 合理选择扫描速度和角度;d) 记录探伤过程中的异常现象。
3. 结果判定和处理根据探伤结果进行判断和处理,包括以下几种情况:a) 合格:铸件内部无缺陷或缺陷在允许范围内,可以判定为合格;b) 不合格:铸件内部存在超出允许范围的缺陷,应判定为不合格;c) 让步接收:对于某些小缺陷,在不影响使用和安全性能的情况下,可考虑让步接收;d) 返修或报废:对于不合格的铸件,应进行返修或报废处理。
返修后应重新进行探伤检测。
焊缝内部缺陷的超声波探伤和射线探伤剖析

二.超声波探伤
➢ 直探头及斜探头示意图
Company Logo
二.超声波探伤
Company Logo
2.超声波探伤仪选择
❖ 探伤仪针对不同的检测对象、目的、方法、 速度等需要,其设计制造也不尽相同。按信 号的显示方式不同,可分为A、B、C型三种 探伤仪,即人们通常所说的A超、B超、C超。
二.超声波探伤
未熔合——坡口未熔合在底片上呈直线状的黑色条纹,位置偏离焊缝中心, 靠近坡口边缘一边的密度较大且直;层间未熔合在底片上呈黑色条纹, 但不很长,有时与非金属夹渣相似。
Company Logo
三.射线探伤
3.射线探伤的质量评定 按《钢熔化焊对接接头射线照相和质量分级》
(GB3323)的规定进行。根据缺陷性质和数量、 射线探伤焊缝质量分为四个等级: ①Ⅰ级焊缝内应无裂纹、未焊透、未熔合和条状夹渣; ②Ⅱ级焊缝应无裂纹、未熔合、未焊透; ③Ⅲ级焊缝内应无裂纹、未熔合及双面焊和加垫板的单
一.焊件内常见缺陷
Company Logo
❖4.未熔合:焊接时在焊缝金属与母材之间
或焊道金属和焊道金属之间未完全熔化结合 的部分,其主要类型是按其所在部位可分为坡 口未熔合(侧壁未熔合),层间未熔合(焊 道之间未熔合)和单面焊根部未熔合三种
一.焊件内常见缺陷
Company Logo
❖5.裂纹:主要是在熔焊冷却时因热力盈 利和相变应力而产生的,也有在校正或 疲劳过程中产生的。是危险性最大的一 种缺陷。
面焊中的未焊透; ④Ⅳ级焊缝是缺陷超过Ⅲ级的。
参考文献
Company Logo
➢ 大连理工大学,李孟喜主编.无损检测.机械工业出版 社,2001
二.超声波探伤
➢ 直探头探测钢材缺陷
常用无损探伤及使用原则

工业无损探伤的方法很多,目前国内外最常用的探伤方法有五种,即人们常称的五大常规探伤方法.本文将首先介绍五大常规探伤方法及其特点,并结合电厂管道焊接的特定条件和需求,选出适合探伤方法。
除以上五大常规方法外,近年来又有了红外,声发射等一些新的探伤方法.五大常规方法是指:1、射线探伤法 RT:检测内部有气孔,夹渣、未焊透等体积型缺陷,不易发现裂纹等面积型缺陷。
2、超声波探伤法 UT:纵波,横波适用于探测内部缺陷, 表面波适宜于探测表面缺陷,但对表面的条件要求高.3、磁粉探伤法 MT:能探查气孔, 夹杂,未焊透等体积型缺陷, 但更适于检查因淬火, 轧制, 锻造,铸造,焊接,电镀,磨削,疲劳等引起的裂纹。
4、涡流探伤法 ET:能确定表面及近表面缺陷的位置和相对尺寸5、渗透探伤法 PT。
能确定表面开口缺陷的位置、尺寸和形状。
一、射线探伤方法:射线探伤是利用射线的穿透性和直线性来探伤的方法. 这些射线虽然不会像可见光那样凭肉眼就能直接察知,但它可使照相底片感光,也可用特殊的接收器来接收.常用于探伤的射线有 x 光和同位素发出的γ射线,分别称为x光探伤和γ射线探伤.当这些射线穿过(照射)物质时,该物质的密度越大,射线强度减弱得越多,即射线能穿透过该物质的强度就越小.此时,若用照相底片接收,则底片的感光量就小;若用仪器来接收,获得的信号就弱。
因此,用射线来照射待探伤的零部件时,若其内部有气孔,夹渣等缺陷,射线穿过有缺陷的路径比没有缺陷的路径所透过的物质密度要小得多,其强度就减弱得少些,即透过的强度就大些,若用底片接收,则感光量就大些,就可以从底片上反映出缺陷垂直于射线方向的平面投影; 若用其它接收器也同样可以用仪表来反映缺陷垂直于射线方向的平面投影和射线的透过量。
由此可见,一般情况下,射线探伤是不易发现裂纹的,或者说,射线探伤对裂纹是不敏感的.因此,射线探伤对气孔,夹渣,未焊透等体积型缺陷最敏感.即射线探伤适宜用于体积型缺陷探伤,而不适宜面积型缺陷探伤。
焊缝内部缺陷的超声波探伤和射线探伤

Company Logo
三.射线探伤
气孔—在底片上多呈圆形或椭圆形黑点,其黑度中心处较大并均匀地向边缘 减小。气孔分布特征有单个的,有密集的,有连续的等。 夹渣——在底片上多呈不同形状的点和条状。点状夹渣呈单独黑点,外观不 太规则并带有棱角,黑度较均匀;条状夹渣呈宽而短的粗线条状,长条 状夹渣,线条较宽,宽度不太一致。 未熔合——坡口未熔合在底片上呈直线状的黑色条纹,位置偏离焊缝中心, 靠近坡口边缘一边的密度较大且直;层间未熔合在底片上呈黑色条纹, 但不很长,有时与非金属夹渣相似。
LOGO
焊缝内部缺陷的超声波 探伤和射线探伤
主 讲: 曹 野
指导老师:纪洪广
Company Logo
一.焊件内常见缺陷 1.气孔:气孔是金属中含有气体的孔洞。气
体是由焊接过程中产生的化学和物理反应引 起的。在常规的焊接中,总会产生一定量的 气体,但通常不能被射线照相所发现。当产 生过多的气体时,就会导致被称为“气孔” 的缺陷产生。
二.超声波探伤
A、B、C型探伤仪示意图
Company Logo
二.超声波探伤
3.基本原理 超声波通过钢材上表面、缺陷及底面时,均 有部分超声波反射回来,这些超声波各自往 返的路程不同,回到探头的时间不同,在示 波器上将分别显示出反射脉冲,分别称其为 始脉冲、伤脉冲和底脉冲。当钢材中无缺陷 时,则无伤脉冲。
Company Logo
二.超声波探伤 1.探头选择
①直探头:用来发射和接收纵波,它的波束垂直 于被测工件表面入射。一般用于钢材的探伤。 ②斜探头:通常用直探头加楔块组成,它利用楔 块的不同角度可以进行波型转换,依入射角度 的变化,可以在被测工件中产生纵波、横波和 表面波等。通常所说的斜探头,大多数是特指 横波探头。入射角分为:30°、40°和50°。 斜探头一般用于焊缝的探伤。
锻件探伤标准
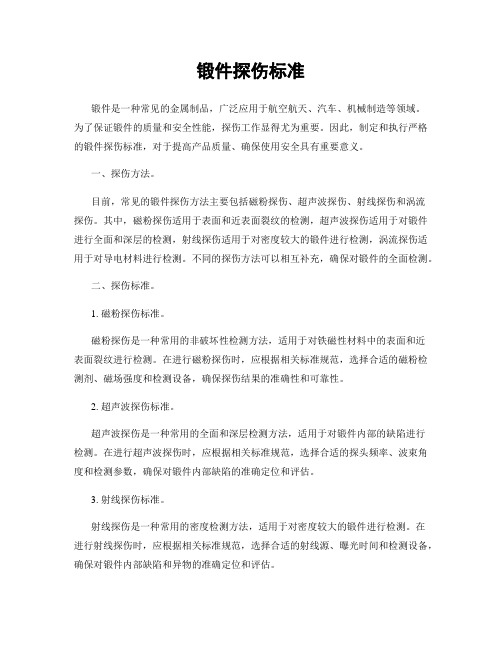
锻件探伤标准锻件是一种常见的金属制品,广泛应用于航空航天、汽车、机械制造等领域。
为了保证锻件的质量和安全性能,探伤工作显得尤为重要。
因此,制定和执行严格的锻件探伤标准,对于提高产品质量、确保使用安全具有重要意义。
一、探伤方法。
目前,常见的锻件探伤方法主要包括磁粉探伤、超声波探伤、射线探伤和涡流探伤。
其中,磁粉探伤适用于表面和近表面裂纹的检测,超声波探伤适用于对锻件进行全面和深层的检测,射线探伤适用于对密度较大的锻件进行检测,涡流探伤适用于对导电材料进行检测。
不同的探伤方法可以相互补充,确保对锻件的全面检测。
二、探伤标准。
1. 磁粉探伤标准。
磁粉探伤是一种常用的非破坏性检测方法,适用于对铁磁性材料中的表面和近表面裂纹进行检测。
在进行磁粉探伤时,应根据相关标准规范,选择合适的磁粉检测剂、磁场强度和检测设备,确保探伤结果的准确性和可靠性。
2. 超声波探伤标准。
超声波探伤是一种常用的全面和深层检测方法,适用于对锻件内部的缺陷进行检测。
在进行超声波探伤时,应根据相关标准规范,选择合适的探头频率、波束角度和检测参数,确保对锻件内部缺陷的准确定位和评估。
3. 射线探伤标准。
射线探伤是一种常用的密度检测方法,适用于对密度较大的锻件进行检测。
在进行射线探伤时,应根据相关标准规范,选择合适的射线源、曝光时间和检测设备,确保对锻件内部缺陷和异物的准确定位和评估。
4. 涡流探伤标准。
涡流探伤是一种常用的导电材料检测方法,适用于对导电材料中的表面和近表面缺陷进行检测。
在进行涡流探伤时,应根据相关标准规范,选择合适的探头频率、电流密度和检测参数,确保对锻件表面缺陷的准确定位和评估。
三、探伤人员资质。
进行锻件探伤工作的人员,应具备相关的资质和技能。
他们需要经过专业的培训和考核,取得相应的探伤人员资格证书,才能进行探伤工作。
只有具备专业技能和丰富经验的探伤人员,才能确保探伤工作的准确性和可靠性。
四、探伤设备管理。
对于探伤设备的选择和管理也是至关重要的。
管道探伤原理

管道探伤原理一、引言管道作为现代工业中不可或缺的设备之一,其安全性和可靠性对于生产运行至关重要。
然而,由于管道长期使用或外界因素的影响,管道可能会出现各种问题,如腐蚀、裂纹、疲劳等。
为了及时发现和解决这些问题,管道探伤技术应运而生。
本文将介绍管道探伤的原理及其应用。
二、管道探伤原理管道探伤是利用物理原理和仪器设备对管道进行无损检测的技术。
其原理是通过对管道内部或外部的物理特性进行检测,从而获取管道的结构和性能信息。
1. 超声探伤原理超声探伤是最常用的管道探伤方法之一。
其原理是利用超声波在物质中传播的特性,通过探头发射超声波并接收反射回来的信号来检测管道内部的缺陷。
当超声波遇到缺陷时,会发生反射、散射或透射,根据反射信号的强弱和时间延迟可以确定缺陷的位置、形状和大小。
2. 磁粉探伤原理磁粉探伤是一种适用于管道表面缺陷检测的方法。
其原理是在管道表面涂覆磁粉,通过施加磁场使磁粉在缺陷处形成磁粉堆,从而可观察到缺陷的存在和形状。
常用的磁粉探伤方法有湿法和干法,其中湿法指的是在磁粉中添加液体使其形成磁悬浮液,干法则是直接将磁粉粘附在管道表面。
3. 射线探伤原理射线探伤是一种利用射线穿透物质并通过检测射线的衰减程度来检测管道内部缺陷的方法。
常用的射线有X射线和γ射线。
通过射线照射管道,不同材料和缺陷对射线的衰减程度不同,从而可以获取缺陷的存在和位置。
射线探伤具有穿透力强、探测范围广的特点,但需要专业人员操作,并且对辐射防护要求严格。
4. 磁性粉末检测原理磁性粉末检测是一种利用磁性粉末在磁场作用下对管道进行检测的方法。
其原理是将磁性粉末喷洒在管道表面,通过施加磁场使粉末在缺陷处形成磁线,从而可观察到缺陷的存在和形状。
磁性粉末检测适用于对表面缺陷进行检测,如裂纹、疲劳等。
三、管道探伤应用管道探伤广泛应用于石油、化工、电力、航空等领域,其主要目的是为了确保管道的安全运行和延长使用寿命。
具体应用包括以下几个方面:1. 缺陷检测和评估:通过管道探伤技术可以及时发现管道内外的缺陷,如腐蚀、裂纹等,从而进行评估和修复,保证管道的安全运行。
超声探伤技术

超声探伤技术3.1无损探伤3.1.1无损探伤种类及特点无损探伤是在不损坏工件或原材料工作状态前提下,对被检验部件的表面和内部质量进行检查一种测试手段。
常用的无损探伤方法有射线探伤、超声探伤、磁粉探伤、渗透探伤和涡流探伤。
下面分别介绍。
(1) 射线探伤射线探伤(RT)是利用电磁波穿透工件,完好部位与缺陷部位透过剂量有差异,其程度与这两部分的材质、射线强度和透过方向与缺陷尺寸有关,从而形成缺陷影像。
射线探伤的主要特点如下:1)图片上有完好部位与缺陷部位的黑度差形成的缺陷平面投影影象,一般无法测量缺陷的深度;2)基本不受焊缝厚度限制;3)要求焊缝双面靠近,检验成本高,时间长;4)对操作人员有射线损伤射线探伤有利于检验出夹渣、气孔等体积形缺陷。
对平行于射线方向的开口性缺陷有检出能力(2) 超声探伤超声探伤是利用弹性波在缺陷部位形成反射或衍射的方法提取缺陷信号,其信号强度与波的类型、探伤频率,缺陷的尺寸、取向及其表面状态以及完好部位和缺陷部位的材质有关。
超声探伤的主要特点如下:1)显示器屏幕上缺陷波的幅度与位置代表缺陷的尺寸与深度,一般较难测量缺陷真实尺寸,只有采用衍射波法可测缺陷高度;2)厚度小于8mm时,要求特殊检验方法;3)焊缝只须单面靠近,检验时间短,成本低;4)对操作人员无损害。
超声探伤有利于检出裂纹类面积形缺陷。
(3)磁粉探伤磁粉探伤是将焊缝磁化利用缺陷部位的漏磁通可吸附磁粉的现象得以形成缺陷痕迹以达到探伤效果的检测手段。
磁粉探伤限于检验铁磁材料,要完全接近与工件表面,缺陷性质容易辨认,油漆与电镀面基本不影响检验灵敏度,但应做层膜厚度对灵敏度影响的试验。
磁粉检测可以用来检表面与近表面缺陷。
(4)渗透探伤渗透探伤的原理是利用毛细作用将带有颜色的渗透液喷涂在焊缝表面上,使其渗入缺陷内,清洗后施加显象剂显示缺陷彩色痕迹。
渗透检测适用于各种金属工件,不要电源,缺陷性质容易辨认,渗透操作到显示缺陷约半小时。
超声波探伤培训资料
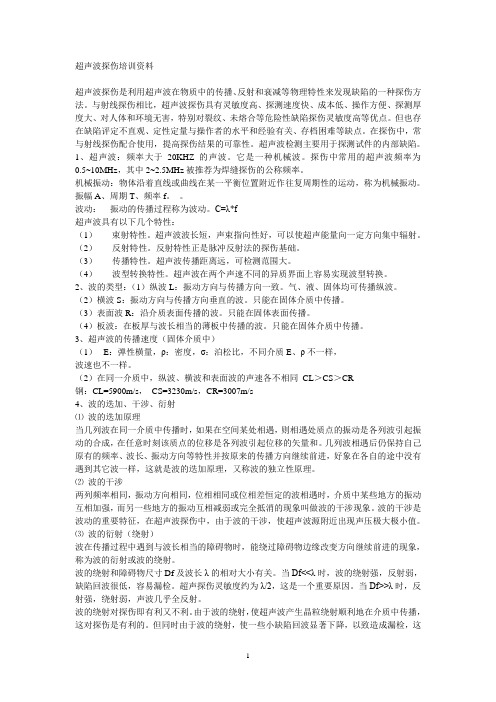
超声波探伤培训资料超声波探伤是利用超声波在物质中的传播、反射和衰减等物理特性来发现缺陷的一种探伤方法。
与射线探伤相比,超声波探伤具有灵敏度高、探测速度快、成本低、操作方便、探测厚度大、对人体和环境无害,特别对裂纹、未熔合等危险性缺陷探伤灵敏度高等优点。
但也存在缺陷评定不直观、定性定量与操作者的水平和经验有关、存档困难等缺点。
在探伤中,常与射线探伤配合使用,提高探伤结果的可靠性。
超声波检测主要用于探测试件的内部缺陷。
1、超声波:频率大于20KHZ的声波。
它是一种机械波。
探伤中常用的超声波频率为0.5~10MHz,其中2~2.5MHz被推荐为焊缝探伤的公称频率。
机械振动:物体沿着直线或曲线在某一平衡位置附近作往复周期性的运动,称为机械振动。
振幅A、周期T、频率f。
波动:振动的传播过程称为波动。
C=λ*f超声波具有以下几个特性:(1)束射特性。
超声波波长短,声束指向性好,可以使超声能量向一定方向集中辐射。
(2)反射特性。
反射特性正是脉冲反射法的探伤基础。
(3)传播特性。
超声波传播距离远,可检测范围大。
(4)波型转换特性。
超声波在两个声速不同的异质界面上容易实现波型转换。
2、波的类型:(1)纵波L:振动方向与传播方向一致。
气、液、固体均可传播纵波。
(2)横波S:振动方向与传播方向垂直的波。
只能在固体介质中传播。
(3)表面波R:沿介质表面传播的波。
只能在固体表面传播。
(4)板波:在板厚与波长相当的薄板中传播的波。
只能在固体介质中传播。
3、超声波的传播速度(固体介质中)(1) E:弹性横量,ρ:密度,σ:泊松比,不同介质E、ρ不一样,波速也不一样。
(2)在同一介质中,纵波、横波和表面波的声速各不相同 CL>CS>CR钢:CL=5900m/s,CS=3230m/s,CR=3007m/s4、波的迭加、干涉、衍射⑴波的迭加原理当几列波在同一介质中传播时,如果在空间某处相遇,则相遇处质点的振动是各列波引起振动的合成,在任意时刻该质点的位移是各列波引起位移的矢量和。
焊接探伤检测有几种方法

焊接探伤检测有几种方法焊接探伤检测是指对焊接接头进行质量检测的过程,其目的是发现焊接接头中的缺陷和问题,以保证焊接接头的质量和安全性。
在实际的焊接生产中,为了保证焊接接头的质量,需要采用不同的方法进行探伤检测。
下面将介绍焊接探伤检测的几种常用方法。
首先,我们来介绍一种常见的焊接探伤检测方法——X射线探伤检测。
X射线探伤检测是利用X射线的穿透能力来检测焊接接头中的缺陷和问题的一种方法。
在X射线探伤检测中,通过X射线管产生的X射线照射到焊接接头上,X射线经过焊接接头后,被感光胶片或探测器接收,形成X射线照片。
通过分析X射线照片,可以发现焊接接头中的缺陷和问题,如气孔、夹杂、裂纹等。
X射线探伤检测具有高灵敏度和准确性的优点,可以发现较小的缺陷,但是设备昂贵,操作复杂,需要专业人员进行操作。
另一种常用的焊接探伤检测方法是超声波探伤检测。
超声波探伤检测是利用超声波在材料中传播的特性来检测焊接接头中的缺陷和问题的一种方法。
在超声波探伤检测中,通过超声波探头向焊接接头发射超声波,当超声波遇到焊接接头中的缺陷时,会发生反射或散射。
通过接收和分析反射或散射的超声波信号,可以发现焊接接头中的缺陷和问题,如气孔、夹杂、裂纹等。
超声波探伤检测具有操作简单、灵敏度高、成本低的优点,但对操作人员的技术要求较高,只能检测表面附近的缺陷。
除了X射线探伤检测和超声波探伤检测外,还有一种常用的焊接探伤检测方法是磁粉探伤检测。
磁粉探伤检测是利用磁粉在磁场中的特性来检测焊接接头中的缺陷和问题的一种方法。
在磁粉探伤检测中,先在焊接接头表面涂覆磁粉,然后在焊接接头周围施加磁场。
当磁粉遇到焊接接头中的缺陷时,会产生磁粉堆积,形成磁粉痕迹。
通过观察和分析磁粉痕迹,可以发现焊接接头中的缺陷和问题,如裂纹、夹杂等。
磁粉探伤检测具有操作简单、成本低的优点,但只能检测表面附近的缺陷,对表面粗糙的焊接接头检测效果较差。
总的来说,焊接探伤检测有多种方法,每种方法都有其特点和适用范围。
术语知识--五大无损检测方法
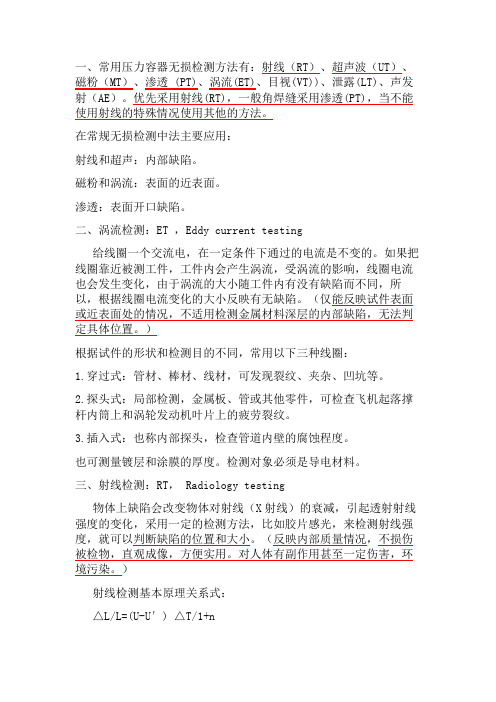
一、常用压力容器无损检测方法有:射线(RT)、超声波(UT)、磁粉(MT)、渗透 (PT)、涡流(ET)、目视(VT))、泄露(LT)、声发射(AE)。
优先采用射线(RT),一般角焊缝采用渗透(PT),当不能使用射线的特殊情况使用其他的方法。
在常规无损检测中法主要应用:射线和超声:内部缺陷。
磁粉和涡流:表面的近表面。
渗透:表面开口缺陷。
二、涡流检测:ET ,Eddy current testing给线圈一个交流电,在一定条件下通过的电流是不变的。
如果把线圈靠近被测工件,工件内会产生涡流,受涡流的影响,线圈电流也会发生变化,由于涡流的大小随工件内有没有缺陷而不同,所以,根据线圈电流变化的大小反映有无缺陷。
(仅能反映试件表面或近表面处的情况,不适用检测金属材料深层的内部缺陷,无法判定具体位置。
)根据试件的形状和检测目的不同,常用以下三种线圈:1.穿过式:管材、棒材、线材,可发现裂纹、夹杂、凹坑等。
2.探头式:局部检测,金属板、管或其他零件,可检查飞机起落撑杆内筒上和涡轮发动机叶片上的疲劳裂纹。
3.插入式:也称内部探头,检查管道内壁的腐蚀程度。
也可测量镀层和涂膜的厚度。
检测对象必须是导电材料。
三、射线检测:RT, Radiology testing物体上缺陷会改变物体对射线(X射线)的衰减,引起透射射线强度的变化,采用一定的检测方法,比如胶片感光,来检测射线强度,就可以判断缺陷的位置和大小。
(反映内部质量情况,不损伤被检物,直观成像,方便实用。
对人体有副作用甚至一定伤害,环境污染。
)射线检测基本原理关系式:△L/L=(U-U′) △T/1+n△L/L:物体对比度,L是射线强度,△L是射线强度增量,U:物质线衰减系数,U′:缺陷线衰减系数,△T:射线照射方向上的厚度差,n:散射比。
按检测技术可以分为:照相、实时成像、层析检测。
按检测方式分:固定、移动式。
分类:胶片成像工艺、数字成像工艺。
四种应用类型:质量检测:铸造、焊接工艺缺陷检测。
无损探伤种类

在探测物件时,探测结果很重要,这样才知道物件有没有损坏,以及损坏的具体部位是哪。
除此之外,无损也很重要,如果检测的过程中,使物件受到了二次损伤,那就得不偿失了。
因此,无损探伤引发关注,无损探伤种类包括哪些呢?常用的无损测试技术有:1、射线探伤利用X射线或γ射线在穿透被检物各部分时强度衰减的不同,检测被检物的缺陷。
若将受到不同程度吸收的射线投射到X射线胶片上,经显影后可获得显示物体厚度变化和内部缺陷情况的照片。
如用荧光屏代替胶片,可直接观察被检物体的内部情况。
2、超声检测利用物体自身或缺陷的声学特性对超声波传播的影响,来检测物体的缺陷或某些物理特性。
在超声检测中常用的超声频率为0.5~5兆赫(MHz)。
常用的超声检测是脉冲探伤。
3、声发射检测通过接收和分析材料的声发射信号来评定材料的性能或结构完整性。
材料中因裂缝扩展、塑性变形或相变等引起应变能快速释放而产生应力波的现象称为声发射。
材料在外部因素作用下产生的声发射,被声传感器接收转换成电信号,经放大后送至信号处理器,从而测量出声发射信号的各种特征参数。
4、渗透探伤利用某些液体对狭窄缝隙的渗透性来探测表面缺陷。
常用的渗透液为含有有色染料或荧光的液体。
5、磁粉探伤通过磁粉在物体缺陷附近漏磁场中的堆积来检测物体表面或近表面处的缺陷,被检测物体需具有铁磁性。
此外,中子射线照相法、激光全息照相法、超声全息照相法、红外检测、微波检测等无损测试新技术也获得了发展和应用。
6、涡流探伤涡流探伤是由交流电流产生的交变磁场作用于待探伤的导电材料,感应出电涡流。
如果材料中有缺陷,它将干扰所产生的电涡流,即形成干扰信号。
用涡流探伤仪检测出其干扰信号,就可知道缺陷的状况。
南京博克纳自动化系统有限公司总部位于美丽的中国古都南京,是国内专业研制无损检测仪器及设备的高科技企业。
公司致力于涡流、漏磁和超声波仪器及各种非标设备的研制,已拥有自主研发的多项国家专利。
产品被广泛应用于航天航空、军工、汽车、电力、铁路、冶金机械等行业。
探伤辐射范围

探伤辐射范围
探伤辐射的范围取决于所使用的具体技术和设备。
以下是几种常见的探伤辐射技术及其范围:
1. X射线探伤:X射线探伤通常使用射线源发出的X射线进
行检测。
其辐射范围大约为几米到十几米范围内。
2. 伽马射线探伤:伽马射线探伤使用伽马射线源进行检测。
其辐射范围一般比X射线探伤更大,可以达到几十米到几百米。
3. 超声波探伤:超声波探伤是通过超声波在被检测物体中传播的特性来检测缺陷。
其辐射范围主要受传播介质的限制,一般为几毫米到几十毫米。
需要注意的是,以上辐射范围是相对于射线或波束在空气中传播的情况下给出的。
具体的范围还受到被检测物体的材料和结构等因素的影响。
同时,为了确保安全,需要采取辐射防护措施,控制辐射范围在可控制的范围内。
四种常用探伤方法特点及区别

四种常规无损检测方法的比较无损检测就是利用声、光、磁和电等特性,在不损害或不影响被检对象使用性能的前提下,检测被检对象中是否存在缺陷或不均匀性,给出缺陷的大小、位置、性质和数量等信息,进而判定被检对象所处技术状态(如合格与否、剩余寿命等)的所有技术手段的总称。
常用的无损检测方法:超声检测(UT)、磁粉检测(MT)、液体渗透检测(PT)及X射线检测(RT).超声波检测(UT)1、超声波检测的定义:通过超声波与试件相互作用,就反射、透射和散射的波进行研究,对试件进行宏观缺陷检测、几何特性测量、组织结构和力学性能变化的检测和表征,并进而对其特定应用性进行评价的技术.2、超声波工作的原理:主要是基于超声波在试件中的传播特性。
声源产生超声波,采用一定的方式使超声波进入试件;超声波在试件中传播并与试件材料以及其中的缺陷相互作用,使其传播方向或特征被改变;改变后的超声波通过检测设备被接收,并可对其进行处理和分析;根据接收的超声波的特征,评估试件本身及其内部是否存在缺陷及缺陷的特性.3、超声波检测的优点:a。
适用于所有金属、非金属和复合材料等多种制件的无损检测;b。
穿透能力强,可对较大厚度范围内的试件内部缺陷进行检测.如对金属材料,可检测厚度为1~2mm的薄壁管材和板材,也可检测几米长的钢锻件;c.缺陷定位较准确;d。
对面积型缺陷的检出率较高;e。
灵敏度高,可检测试件内部尺寸很小的缺陷;f.检测成本低、速度快,设备轻便,对人体及环境无害,使用较方便。
4、超声波检测的局限性a。
对试件中的缺陷进行精确的定性、定量仍须作深入研究;b。
对具有复杂形状或不规则外形的试件进行超声检测有困难;c.缺陷的位置、取向和形状对检测结果有一定影响;d.材质、晶粒度等对检测有较大影响;e。
以常用的手工A型脉冲反射法检测时结果显示不直观,且检测结果无直接见证记录。
5、超声检测的适用范围a.从检测对象的材料来说,可用于金属、非金属和复合材料;b。
- 1、下载文档前请自行甄别文档内容的完整性,平台不提供额外的编辑、内容补充、找答案等附加服务。
- 2、"仅部分预览"的文档,不可在线预览部分如存在完整性等问题,可反馈申请退款(可完整预览的文档不适用该条件!)。
- 3、如文档侵犯您的权益,请联系客服反馈,我们会尽快为您处理(人工客服工作时间:9:00-18:30)。
超声波探伤比X射线探伤具有较高的探伤灵敏度、周期短、成本低、灵活方便、效率高,对人体无害等优点;缺点是对工作表面要求平滑、要求富有经验的检验人员才能辨别缺陷种类、对缺陷没有直观性;
超声波探伤适合于厚度较大的零件检验。
射线对体积型缺陷敏感,但对线状缺陷,特别是厚板中细小的未焊透(熔入不足)或微裂纹等难于发现,而超声波对线状缺陷敏感,却对点状缺陷的定量不容易定准。
综上所述,射线的检测优势在于体积型缺陷的检测,超声波优势在于面缺陷的检测。
体积型缺陷:气孔,夹渣
面积型缺陷:裂纹,未熔合。