直拉单晶硅中的杂质PPT课件
晶体硅杂质吸除工艺介绍PPT课件
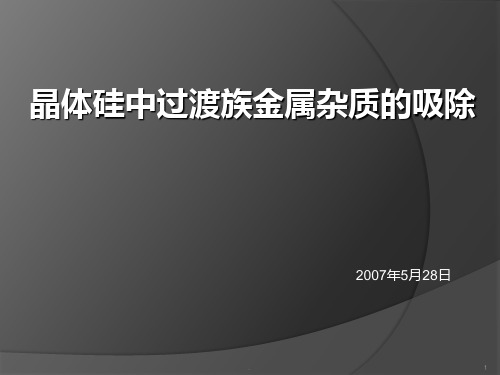
.
4
3. 吸杂:金属杂质从器件内的吸除
不需高额费用操作而对器件区的金属杂质进行有效吸 除,对IC产业而言,一直是个很大的挑战。尽管对于IC 产业,在加工生产过程中金属杂质的引入不可避免,但 针对如何将不期望的金属杂质从器件区去除,人们已发 展了一些工艺,这些工艺一般统称为吸杂工艺。
.
6
根据对杂质的捕获方式,可以将吸杂分为两大类, 即分凝(segregation)和释放(relaxation)。也有一 些学者将自间隙原子注入产生吸杂归为第三种吸杂机制, 但是一般地,人们将这种注入产生吸杂归为分凝吸杂。
而在上述两种机制下衍生的吸杂工艺则有许多,主要 包括:内吸杂,P扩散吸杂,衬底吸杂,Si表面及Si/SiO2 界面吸杂,离子注入吸杂,背表面损伤吸杂,化学吸杂, 铝背场吸杂等。
.
12
b.影响分凝效应的方式
(1)不同的相,如在晶体生长过程中,在晶体硅中 及液相熔体中;
(2)不同元素的影响,如相比于硅,铝对金属杂质 具有更高的溶解能力;
(3)费米能级对金属杂质溶解度的影响,如P掺杂硅 片中Au的影响;
晶体硅中过渡族金属杂质的吸除
2007年5月28日
.
1
第一章: 硅中杂质的吸除工艺
1. 金属杂质对器件的影响 金属杂质的存在会极大地影响半导体器件的产量,
即便在金属杂质的浓度降低到1012cm-3时,这种影响仍然 十分明显。
硅片中的杂质主要会带来以下几个负面作用: a. 过渡族金属杂质形成深能级,增大p-n结的漏导电流,
产生更大的漏导损耗; b. p-n结中的金属杂质降低结的反向击穿电压; c. 金属杂质形成深能级带隙极大地增加结的漏导损耗,甚
直拉单晶硅中的位错
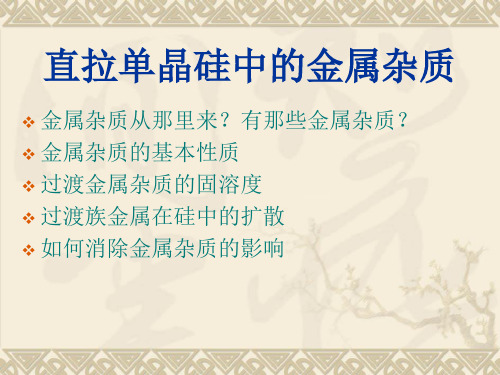
金属杂质的基本性质
1、硅中金属杂质的存在形式 ①和其他杂质一样,硅中金属杂质的存在形式主要取决于固溶度,同时也 受热处理温度、降温速率、扩散速率等因素影响。 ②金属杂质可以以间隙态或替位态形式的单原子存在,也可以以复合体或 沉淀形式存在 2硅中金属杂质对硅器件的影响。 ①原子态的金属杂质主要影响载流子的浓度和少数载流子的寿命。金属杂 质对载流子寿命的影响为τ=1/νσN。 ②沉淀形式的金属杂质会严重影响少数载流子的寿命。
直拉单晶硅中的位错
晶体硅中有哪些位错?哪些途径导致位错?
位错的基本性质 晶体硅中的位错结构 晶体硅中位错的腐蚀和表征 晶体硅中位错对太阳电池的影响
晶体硅中有哪些缺陷?哪些因素导致 缺陷?
按照缺陷的结构分类,直拉单晶硅中主要存在点缺 陷、位错、层错和微缺陷;按照晶体生长和加工过 程分类,可分为晶体原生缺陷和二次诱生缺陷。 直拉单晶硅位错引入途径:①晶体生长时,由于籽 晶的热冲击,会在晶体中引入原生位错。②在晶体 生长的过程中,如果热场不稳定,将会产生热冲击, 也能从固液界面处产生位错,延伸进入晶体硅。③ 热应力引入位错。
位错的基本性质
图示为螺旋位错
螺旋位错是在外力的作用下, 某个原子面沿着一根与其相 垂直的轴线方向螺旋上升, 每旋转一周,原子面便上升 一个原子距离,从而导致部 分晶体的滑移
位错的基本性质
如果要准确的描述位错的性质,就需要用伯氏矢量的概念。伯氏 矢量是指在晶体中围绕某区域任选一点,以逆时针方向做一闭合 回路。如果该区域是完整晶体,回路的起点和终点会重合;如果 区域中含有位错,则起点和终点不能重合,那么从终点指向起点 的连线就是伯氏矢量,同时,该回路称为伯格斯回路。
直拉单晶硅的制备-掺杂讲课讲稿

直拉单晶硅的制备-掺杂直拉单晶硅的制备硅、锗等单晶制备,就是要实现由多晶到单晶的转变,即原子由液相的随机排列直接转变为有序阵列;由不对称结构转变为对称结构。
但这种转变不是整体效应,而是通过固液界面的移动而逐渐完成的。
为实现上述转化过程,多晶硅就要经过由固态到熔融态,然后又由熔融态硅到固态晶体硅的转变。
这就是从熔体硅中生长单晶硅所遵循的途径。
从熔体中生长硅单晶的方法,目前应用最广泛的主要有两种:有坩埚直拉法和无坩埚悬浮区熔法。
在讨论这两种制备方法之前,还应讨论在制备单晶过程中必不可少的一些准备工序。
包括掺杂剂的选择、坩埚的选择、籽晶的制备等,分别介绍如下:一、掺杂在制备硅、锗单晶时,通常要加入一定数量杂质元素(即掺杂)。
加入的杂质元素决定了被掺杂半导体的导电类型、电阻率、少子寿命等电学性能。
掺杂元素的选择必须以掺杂过程方便为准,又能获得良好的电学性能和良好晶体完整性为前提。
1掺杂元素的选择(1)根据导电类型和电阻率的要求选择掺杂元素制备N型硅、锗单晶,必须选择Ⅴ族元素(如P、As、Sb、Bi);制备P型硅、锗单晶必须选择Ⅲ族元素(如B、Al、Ga、In、Ti)。
杂质元素在硅、锗晶体中含量的多少决定了硅、锗单晶的电阻率。
电阻率不仅与杂质浓度有关,而且与载流子的迁移率有关。
当杂质浓度较大时,杂质对载流子的散射作用,可使载流子的迁移率大大降低,从而影响材料的导电能力。
考虑到以上因素,从理论上计算了电阻率与杂质浓度的关系曲线,如图9-5所示。
在生产工艺上按电阻率的高低分档。
掺杂有三档:轻掺杂(适用于大功率整流级单晶)、中掺杂(适用于晶体管级单晶)、重掺杂(适用于外延衬底级单晶)。
(2)根据杂质元素在硅、锗中溶解度选择掺杂元素各种杂质元素在硅、锗中溶解度相差颇大。
例如,采用大溶解度的杂质,可以达到重掺杂的目的,又不会使杂质元素在晶体中析出影响晶体性能。
下表列出了常用掺杂元素在硅、锗单晶生长时掺入量的极限,超过了极限量,单晶生长不能进行。
直拉单晶硅工艺技术PPT课件
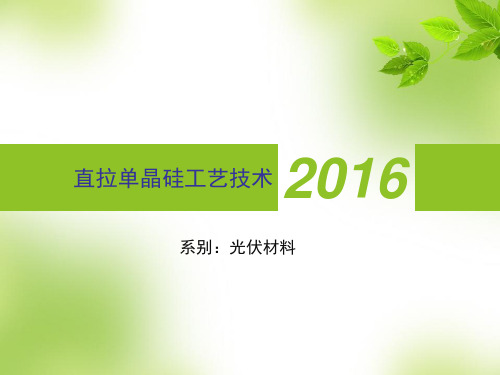
这种周期性规律是晶体结构中最基本的特征。有固定熔点, 各向异性。
Intensity/a.u.
◆ :CuAlO2 ▲:CuO ◆ 1200℃
◆ ▲
◆ ▲◆
1190℃
◆
◆ ▲
◆ ▲◆
1180℃
◆
◆ ▲
◆ ▲◆
1170℃
◆
◆ ▲
◆ ▲◆
1160℃
◆
◆◆ ▲ ▲◆
◆ 1150℃ ◆ ▲◆ ▲◆
20 30 40
◆◆◆
◆ ◆◆ ◆ ◆
◆◆ ◆
◆ ◆◆
◆◆
◆ ◆◆ ◆
◆◆
◆ ◆◆ ◆◆ ◆
◆◆ ◆◆
◆ ◆◆
◆◆ ◆
◆◆
◆ ◆◆
◆◆ ◆ ◆ ◆
50 60 70 80
2()
图1.5 食盐的空间点阵结构图
图1.6 不同烧结温度下通过陶瓷 的XRD图谱
紫锂辉石(Kunzite)
常林钻石 重158.786克拉 图1.7 常见的晶体
1.12晶体的几种晶面
同一个格点可以形成方向不同的晶列,每一个晶列定义了 一个方向,称为晶向。
图1.13 立方晶系中的几个晶面及晶向
1.5晶体的熔化和凝固
晶体的分类: 1.离子晶体 2.分子晶体 3.原子晶体 4.金属晶体
图1.14晶体加热或冷却的理想曲线
1.6结晶过程的宏观特征
1.15冷却曲线
1.7晶核的形成
熔体里存在晶胚,晶胚长到一定的尺寸时,形成晶核。 过冷度越大,临界半径越小。非自发成核要容易多了。
1.8二维晶核的形成
一定数量的液体原子同时落在平滑界面上的临近位置,形 成一个具有单原子厚度并有一定宽度的平面原子集团。
第五章_直拉单晶硅中的杂质和位错
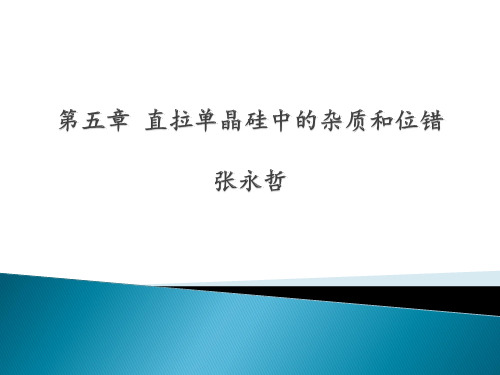
热施主在300-550度范围内产生,450度产生最 大热施主浓度 热施主在550度以上短时间热处理就可以消除, 通常在650度热处理0.5-1h就可以消除 初始形成速率与氧浓度的4次方成正比,其最大 浓度与氧浓度的3次方成正比 能级处于导带下0.06-0.07 eV 和0.13-0.15 eV, 是双施主态,热处理时间增长能级向价带偏移
单晶硅中的杂质: 1.有意引入的电活性杂质:P B 2.其他杂质:氧,碳,氮,氢和金属杂质 对于集成电路用直拉单晶硅来说氧是主要的杂质,碳杂质可 以通过优化工艺降低到1016cm-3 的红外探测极限以下。 氮杂质---用于控制微缺陷和增加机械强度 氢杂质---钝化金属杂质和缺陷 其主要缺陷类型为:点缺陷组成的微缺陷 太阳能级别的直拉单晶硅 杂质较多:氧,碳和金属杂质 1.生长速度快所引起的杂质 2.原材料引入的杂质 3.所用的器械引入的杂质 淀形成驱动 力 过饱和度大,临 界形核半径小 扩散慢 过饱和度较大, 临界形核半径较 大 扩散较快 过饱和度小,临 界形核半径大 扩散快
成核机制
密度高,尺寸小
均质成核为主
750-1050
密度高,尺寸大
均质成核和异质 成核竞争
1050-1250
密度底,尺寸大
异质成核为主
成核期(孕育期)--- 快速生长----接近饱和
氧沉淀形成时,晶体硅中的点缺陷、杂质、掺杂 剂都可能提供氧沉淀的异质核心儿影响氧沉淀的 形成。硼可以促进氧沉淀的形成。 纯氧气氛热处理---抑制作用:氧化时,表面生 成二氧化硅层,大量的自间隙硅原子从表面进入 体内,从而抑制氧沉淀的形成。 氮化气氛—促进作用:硅片氮化产生大量空位扩 散到体内,从而对氧沉淀形成起到促进作用。
单晶硅PPT学习课件PPT学习教案
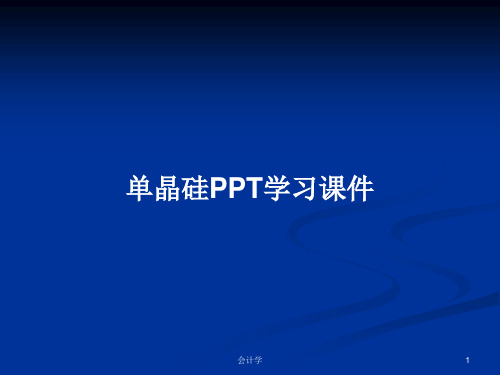
第11页/共49页
12
1.2 硅晶向、晶面和堆积模型
晶向
晶格中原子可看作是处在一 系列方向相同的平行直线系 上,这种直线系称为晶列。 标记晶列方向用晶向, 记为 [m1m2m3] 。用< m1m2m3>表 示等价的晶向.
一晶格中任一格点作为原点,取过原点的三个晶列x,y,z为坐标系 的坐标轴,沿坐标轴方向的单位矢量( x,y,z )称为基矢,任意格 点位置可由下面矢量给出:
金刚石
金刚石
5.43 2.33 11.7 30 1417 10-7(1050℃) 0.70 1.50 0.90 2.5×10-6
5.66 5.32 16.3
8 937 10-7(880℃) 0.31 0.6 0.36 5.8×10-6
2.8×1019 1.0×1019
1.0×1019
6.0×1018
26
刃位错和螺位错
位错主要有刃位错和螺 位错:位错线与滑移矢 量垂直称刃位错;位错 线与滑移矢量平行,称 为螺位错。
硅晶体的双层密排面间 原于价键密度最小,结 合最弱,滑移常沿{111} 面发生,位错线也就常 在{111}晶面之间。该面 称为滑移面。
第26页/共49页
27
刃形位错的运动
攀移
原位
31
1.3 硅中杂质
半导体材料多以掺杂混 合物状态出现,杂质有 故意掺入的和无意掺入 的。
故意掺入Si中的杂质有 ⅢA、VA族,金。故意掺 入杂质具有电活性,能 改变硅晶体的电学特性。
无意掺入Si中的杂质有 氧,碳等。
第31页/共49页
1.45*1010
32
Si中杂质类型
间隙式杂质 主要是ⅠA和ⅧA族元素,有:Na、 K、Li、H等,它们通常无电活性,在硅中以间 隙方式扩散,扩散速率快。 替位式杂质 主要是ⅢA和ⅤA族元素,具有电 活性,在硅中有较高的固浓度。以替位方式扩散 为主,也存在间隙-替位式扩散,扩散速率慢, 称为慢扩散杂质。 间隙—替位式杂质 大多数过渡元素:Au、Fe、 Cu、Pt、Ni、Ag等。都以间隙-替位方式扩散, 约比替位扩散快五六个数量级,最终位于间隙和 替位这两种位置,位于间隙的杂质无电活性,位 于替位的杂质具有电活性。
单晶硅制备 直拉法84页PPT
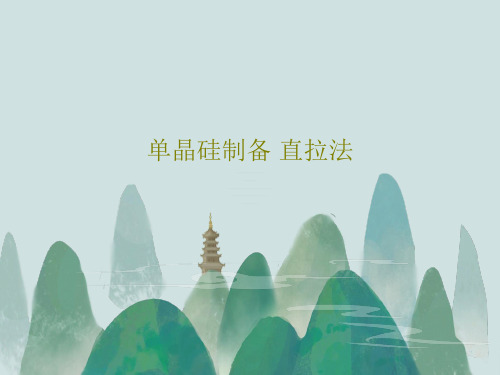
51、没有哪个社会可以制订Fra bibliotek部永远 适用的 宪法, 甚至一 条永远 适用的 法律。 ——杰 斐逊 52、法律源于人的自卫本能。——英 格索尔
53、人们通常会发现,法律就是这样 一种的 网,触 犯法律 的人, 小的可 以穿网 而过, 大的可 以破网 而出, 只有中 等的才 会坠入 网中。 ——申 斯通 54、法律就是法律它是一座雄伟的大 夏,庇 护着我 们大家 ;它的 每一块 砖石都 垒在另 一块砖 石上。 ——高 尔斯华 绥 55、今天的法律未必明天仍是法律。 ——罗·伯顿
谢谢你的阅读
❖ 知识就是财富 ❖ 丰富你的人生
71、既然我已经踏上这条道路,那么,任何东西都不应妨碍我沿着这条路走下去。——康德 72、家庭成为快乐的种子在外也不致成为障碍物但在旅行之际却是夜间的伴侣。——西塞罗 73、坚持意志伟大的事业需要始终不渝的精神。——伏尔泰 74、路漫漫其修道远,吾将上下而求索。——屈原 75、内外相应,言行相称。——韩非
第4章_硅锗中的杂质和缺陷ppt课件

EA EV
25
多子——多数载流子
少子——少数载流子
N型半导体导带电子数由施主决定,半导体 导电的载流子主要是电子。电子为多子,空 穴为少子。
P型半导体价带空穴数由受主决定,半导体导 电的载流子主要是空穴。空穴为多子,电子 为少子。
最新课件
26
3. 杂质半导体
杂质激发
杂质向导带和价带提供电子和空穴的过程(电 子从施主能级向导带的跃迁或空穴从受主能级 向价带的跃迁)称为杂质电离或杂质激发。具 有杂质激发的半导体称为杂质半导体
0.35eV
EA ED
能起到复合中心作用,
0.29eV
Ev
使少数载流子寿命降
低。
Au doped Silicon
最新课件
43
0.35
最新课件
44
化合物半导体中的杂质能级(补充)
Ⅲ-Ⅴ族化合物半导体中的杂质
理想的GaAs晶格
价键结构: 含有离子键成分的 共价键结构
Ga-
As+
Ga
As
Ga
As
Ga
施主向导带提供的载流子 =1016~1017/cm3 》 本征载流子浓度
最新课件
28
上述杂质的特点:
杂质能级在禁带中的位置
施主杂质: ED Eg
受主杂质:
EA Eg
浅能级杂质
杂质的双重作用:
改变半导体的导电性 决定半导体的导电类型
最新课件
29
4. 杂质的补偿作用
半导体中同时存在施主和受主杂质,施主和受 主之间有互相抵消的作用
第4章 硅、锗晶体 中的杂质和缺陷
最新课件
1
理想半导体:
1、原子严格周期性排列,具有完整的晶格 结构。
单晶硅制备直拉法ppt课件
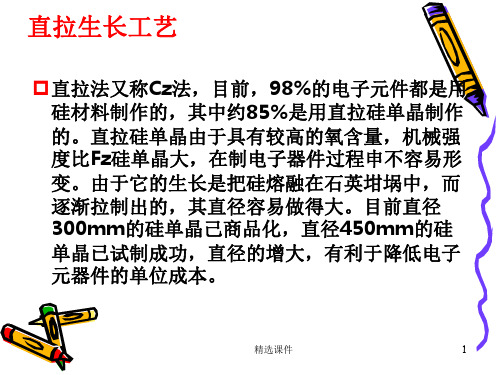
单晶炉结构
1提拉头: 晶升、晶转系统,磁流体系统等;
2上炉筒: 提供晶棒上升空间;
3副室: 提肩装籽晶掺杂等的操作空间;
4炉盖: 主炉室向副室的缩径;
5主炉室: 提供热场和硅熔液的空间;
其经验公式为 d=1.608×10-3DL1/2
d为晶颈直径; D为晶体直径;L为晶体长度,cm。 目前,投料量60~90kg,晶颈直径为4~6mm。 晶颈较理想的形状是:表面平滑,从上至下直径微收
或等径,有利于位错的消除。
直拉生长工艺
⑥放肩 晶颈生长完后,降低温度和拉速,使晶体直径渐渐增
大到所需的大小,称为放肩。 放肩角度必须适当,角度太小,影响生产效率,而且
6下炉室:
提供排气口和电极穿孔等;
8上炉筒提升系统: 液压装置,用于上炉筒提升;
9梯子: 攀登炉顶,检查维修提拉头等;
10观察窗: 观察炉内的实际拉晶状态;
11测温孔: 测量对应的保温筒外的温度;
12排气口: 氩气的出口,连接真空泵;
13坩埚升降系统: 坩埚升降旋转系统等;
14冷却水管组:
提供冷却水的分配。
大小头籽晶: 通过大小头处 变径固定籽晶。
注意事项: Ø 籽晶严禁玷污和磕碰; Ø 晶向一定要符合要求; Ø 安装时一定要装正。
单晶炉拉晶籽晶
规格 直径(mm) 长度(mm) 位错 晶向偏差
方籽晶 圆籽晶
10×10或 12×12
12
100-120 无 100-120 无
<100> ± 1o <100> ± 1o
直拉硅单晶工艺简介PPT.

化料
• 在一定的功率(在规定的时间内从低到高慢慢提升,直到化料要求功率) 和一定的埚位下使硅料熔化
-
中心位置
加热器温度最高点
中心位置
加热器温度最高点
• 在表面硅料全部熔化后,不可将坩埚的位置升的太高,须保证液面至导流 筒的距离有2- 3cm,防止石英坩埚底部硅料翻出时碰到导流筒使导流筒粘 硅。
异常处理
掉棒
产生原因 一、籽晶断
二、籽晶绳
1、籽晶熔接 2、籽晶氧化 3、籽晶夹具 1、籽晶绳氧化 2、籽晶绳毛刺
异常处理
该情况可能会直接导致石英埚破裂引发漏硅事件。 该情况发现应注意以下几点:
一、晶棒过长,停炉处理
角度放大。 • 当放肩直径接近加工要求的直径时,须多次测量,如放肩速度过快,
在直径比预定直径小10mm左右进入转肩状态。如放肩较慢,可在直径 比预定直径小5mm左右进入转肩状目标直径后提高拉速使之纵向生长 • 根据单晶炉性能,转肩可自动或手动,自动单晶炉将晶体生长控制程
等径
1、等径时,晶转、埚转、氩气流量、炉内压及 平均拉速值。 2、等径时,埚跟比随剩余重量变化而变化。
收尾
1、自动收尾时,晶升变化根据收率表来变化 还是根据指数表变化。
2、收尾时,启时拉速是当时的平均拉速还是 设定个拉速。
收尾斜率表,内设定了收尾时的晶升、埚转 、晶转、氩气流量及炉内压力。 2、温度变化根据长度
序启动到“转肩”状态即可。手动单晶炉将晶升速度开到2-3mm/min。 测量并观察晶体生长情况。 • 转肩时根据实际情况可适当提高或降低拉速,同时也可降 低或上升温 度设定点。但拉速不宜调整太快或太高,否则可能会造成转肩掉棱。
直拉硅单晶工艺简介
直拉硅单晶生长工艺流程与原理PPT课件
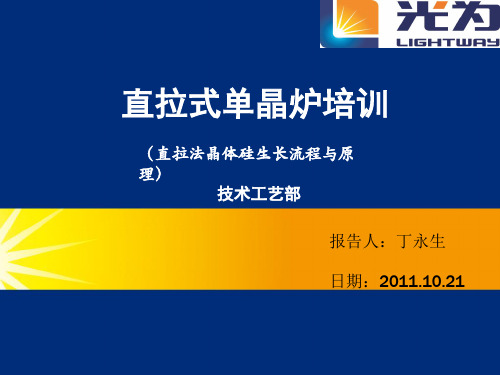
直拉单晶炉下轴(坩埚轴)对环境的要求
1、坩埚通过一根约1m长的硬轴(石墨)支撑并 旋转上升,熔液盛在石英坩埚内;
2、石墨埚杆通过螺丝固定在单晶炉下轴上; (硬轴固定在坩埚提升机构上) 3、坩埚提升机构导轨和丝杠要平顺; 4、带动的硬轴旋转要平稳; 5、冷炉时硬轴上端放一盆水,坩埚提升机构运
行时水面无明显波纹(机械调试时的一个方 法);
单晶炉底座及地基和震源的隔离
外界震源包含: 1、真空泵运行振动 (措施:真空泵下用弹簧座主动隔震真空泵远离炉子) 2、基础所处土壤表层振动 (措施:基础四周挖减震槽隔离) 3、基础所处土壤深层振动 (措施:1、混凝土基础座在实土层2、混凝土基础不宜过高)
二、直拉单晶炉的基本结构
副炉室
隔离阀室 (翻板阀
低压大电流流过加热器产生高温,热量通过辐射加 热石墨坩埚,由石墨坩埚加热石英坩埚和多晶硅料, 达到熔化和结晶所需的温度。调节加热器功率以控 制熔体温度;
直拉单晶炉主炉室及内部热系统概图
单晶炉热场不同系统温度分布对比
直拉单晶炉在气氛下拉晶
1、真空泵不断的对炉子抽气,形成真空; 2、炉子各部件之间都有密封件,其中旋转部件之间 采用磁流体密封; 3、每炉生长之前通过用真空泵对炉子抽极限真空, (抽真空)关闭抽空阀门,测量炉内压力升高速度来 判定炉子是否达到密闭要求;(检漏)
室)
主炉室 坩埚提升 旋转机构
晶体提升 旋转机构
炉盖
控制柜
单晶炉的主要组成部分
1、炉体(基座、炉室、炉盖、液压系统) 2、晶体升降及旋转机构 3、坩埚升降及旋转机构 4、氩气和真空系统 5、加热系统(加热电源、热场) 6、冷却系统 7、控制系统
炉体
炉体(炉体由基座、炉室、炉盖及液压系统组成)
直拉单晶硅中的杂质和位错PPT课件

本征点缺陷对氧沉淀的影响
• 氧沉淀的生成会给硅基体带来很大的应力,只能通过吸收空位以及发射自间隙硅原子,使得应力得到释放。
第18页/共53页
热处理对氧沉淀的影响
• 温度:过饱和度和扩散速率 • 时间:核心在一定的生长速率下的尺寸 • 气氛:硅中引入不同的点缺陷 我们把温度和时间结合在一起考虑为热处理方式,既三个因素简化为 热处理步骤(方式)以及热处理气氛
• 直拉单晶硅中的氧(重点) • 直拉单晶硅中的碳(简要介绍) • 直拉单晶硅中的金属杂质(重点) • 直拉单晶硅中的位错(简要介绍)
目录
第2页/共53页
直拉单晶硅中的氧
• 浓度:1017-1018 cm-1 数量级 • 主要来源:石英坩埚的污染 (1420度),并经过各种温度的热处理 • 存在形式:间隙氧,氧热施主,氧团簇,氧沉淀 • 双刃剑: 内吸杂,破坏器件性能
掺镓的多晶硅
第28页/共53页
第29页/共53页
• 从那里来 • 存在形式 • 基本性质(与氧作用)
直拉单晶硅中的碳
第30页/共53页
从那里来
• 因:原料,直拉单晶炉中存在石墨加热器 • 缘:C + SiO2= SiO + CO CO + Si = SiO + C
第31页/共53页
• 替代位置 • C-O复合体(几个氧有争议) • 间隙位置
第25页/共53页
• 硼浓度 • 氧浓度 • 温度 • 光照强度
硼氧复合体的制约因素(略)
第26页/共53页
如何避免硼氧复合体
• 从氧入手: 区熔单晶硅,磁控直拉单晶硅 • 从硼入手:换成n型单晶硅 • 从硼入手:换成掺镓的单晶硅 • 新的太阳电池工艺,不同升降温工艺和氧化工艺
- 1、下载文档前请自行甄别文档内容的完整性,平台不提供额外的编辑、内容补充、找答案等附加服务。
- 2、"仅部分预览"的文档,不可在线预览部分如存在完整性等问题,可反馈申请退款(可完整预览的文档不适用该条件!)。
- 3、如文档侵犯您的权益,请联系客服反馈,我们会尽快为您处理(人工客服工作时间:9:00-18:30)。
在固溶体体结晶时,如果固相和液相接近 平衡状态,即以无限缓慢的速度从熔体中凝固 出固体,固相中的杂质的浓度为 CS ,液相中
该杂质的浓度为 CL ,则两者的比值为该杂质
在此晶体中的
平衡分凝系数 K 0 CS CL
实际晶体生长时,不可能达到平衡状态,也
就是说固体不可能以无限缓慢的速度从熔体中结
晶,因此,熔体中的杂质不是均匀分布的。例如,
氧以间隙态存在于晶体硅 中,形成Si-O-Si键结合
氧在晶体硅中的浓度要受到固溶度的限制,在硅
的熔点温度附近,氧的平衡固溶度为 2.751018cm ,3随
着晶体硅温度的降低,硅中氧的固溶度会逐渐下降,在 1000℃以上其表达式为
O 91022exp(1.52eV)cm 3
kT
由于在晶体硅的生长过程中存在分凝现象,一般 认为其分凝系数为1.25,因此在实际直拉单晶硅中, 氧浓度表现为头部高、尾部低。
石英
坩埚
单晶
ห้องสมุดไป่ตู้
氧
硅棒
污
熔硅
染
石墨坩埚
石英坩埚溶解 热对流方向
氧进入单晶硅棒内 表面挥发
石墨加 热器
坩埚旋转
①熔硅与石英坩埚作用,生成SiO进入硅熔体
SiSiO22SiO
②通过机械对流、自然对流等方式, SiO传输到熔体 表面,而SiO的蒸气压为12mbar,因此,到达硅熔体 表面的SiO以气体形式挥发。 ③少量的SiO溶解在熔硅中,以氧原子形态存在于液 体硅中,最终进入直拉单晶硅。
②热处理的温度
③热处理的时间 ④碳、氮及其他杂质原子的浓度、 原始晶体硅的生长条件、热处理气 氛、次序等。
①初始氧浓度
初始氧浓度时决定氧沉淀的主要因素 之一。
热处理温度降低、热处理时间延长或碳 浓度增加,能使整个曲线向左移动,氧沉 淀形成的浓度阀值降低,即使是较低的氧 浓度也能形成氧沉淀。反之,则曲线向右 移动,氧沉淀形成的浓度阀值升高。
氧是Cz硅中含量最高杂质,它在硅中行为也很复 杂。总的说来,硅中氧既有益也有害。
(1)增加机械强度 氧在硅晶格中处于间隙位置,对位错有钉扎作用
,因而可增加晶体的机械强度,避免硅片在器件工艺 的热过程中发生型变(如弯曲翘曲等)。这是氧对硅 单晶性能的最大贡献之一,也是Cz硅单晶在集成电路 领域广泛应用的主要原因之一
(2)形成氧热施主
硅中氧以过饱和间隙态存在于硅单晶中。当直拉 单晶硅在300~500℃热处理时,会产生与氧相关的施主 效应,此时,n型晶体硅的电阻率下降, p型晶体硅的 电阻率上升。施主效应严重时,甚至能使p型晶体硅转 化为n型晶体硅,这种与氧相关的施主被称为“热施 主”。研究表明,热施主是双施主,即每个热施主可以 向硅基体提供2个电子,其能级分别位于导带下 0.06~0.07eV和0.13~0.15eV处。因此,当产生的热施 主浓度较高时,会直接影响太阳电池的性能。
另外,晶体硅中的其他杂质也会影响热施 主的生成,研究已经指出,碳、氮会抑制热施 主的生成,而氢会促进热施主的形成。
除热施主外,含氧的直拉单晶硅在550℃~850℃热处 理时,还会形成新的与氧相关的施主,被称为“新施 主”,具有与热施主相近的性质。但是它的生成一般需 要10h左右,甚至更长。对于太阳电池用直拉单晶硅,其 冷却过程虽然要经过该温区,但是要少于10h;另外硅太 阳电池的工艺一般不会长时间热处理,所以,对于太阳 电池用直拉单晶硅而言,新施主的作用和影响一般可以 忽略。
热氧施主可以在300℃~500 ℃范围内生成, 而且在450 ℃是最有效的热施主生成温度。一 旦生成热施主,可以在550 ℃以上用短时间热 处理予以消除,通常利用的热施主消除温度为 650 ℃。
除温度外,单晶硅原生氧浓度是影响热施 主浓度的最大因素。通常认为,热施主浓度主 要取决于单晶硅中的初始氧浓度,其初始形成 速率与氧浓度的4次方成正比,其最大浓度与氧 浓度的3次方成正比。
②热处理的温度
影响氧沉淀的另一个因素是热处理的温度。 因为氧在硅中的固溶度随温度的下降而不断下 降。所以,具有一定浓度的氧在不同温度时的 过饱和度是不同的,这是氧沉淀产生的必要条 件。
研究证明,氧沉淀过程是氧的扩散过程,是受 氧扩散控制的。而温度不仅影响氧的过饱和度
(3)氧成淀
氧在直拉单晶硅中通常是以过饱和间隙态存在, 因此,在合适的热处理条件下,氧在硅中要析出,除 了氧热施主以外,氧析出的另一种形式是氧沉淀。在 晶体生长完成后的冷却过程和硅器件的加工过程中, 单晶硅要经历不同的热处理过程。
在低温热处理时,过饱和的氧一般聚集形成氧施主;
在相对高温热处理或多步热处理循环时,过饱和的氧 就析出形成样氧沉淀。
1 1 CSe
e 为电子电荷, e 1.61019 C
为电子或空穴的迁移率,分别为
1350cm2 / (V s) 和 480cm2 / (V s)
硅熔体中需要掺入的杂质的重量
m W M CS d N0 K0
W 为高纯多晶硅的重量
d 为硅的密度
M为杂质原子量
N0 为阿伏伽德罗常数
CS 为硅晶体头部的杂质浓度
直拉单晶硅中的杂质
标题添加
点击此处输入相 关文本内容
标题添加
点击此处输入相 关文本内容
总体概述
点击此处输入 相关文本内容
点击此处输入 相关文本内容
杂质分凝
由两种或两种以上元素构成的固溶 体,在高温熔化后,随着温度的降低将 重新结晶,形成固溶体。
杂质在固体和熔体中的浓度是不同 的,在结晶的过程中会发生偏析,称为 分凝现象。
氧经高温或多步热处理,会发生析出生成氧成
淀。氧成淀是中性的,主要成分为SiOx,没有学 性能,体积是硅原子的2.25倍。在形成沉淀时,会
从成淀体中向晶体内发射自间隙硅原子,导致硅 晶格中自间隙原子饱和而发生偏析,产生位错、 层错等二次缺陷。
影响单晶硅中氧沉淀形成、结构、分布 和状态的因素: ①初始氧浓度
杂质在熔体中扩散的速度小于晶体结晶的速度的
话,则在固液界面熔体一侧会出现杂质的堆积,
形成一层杂质富集层。此时固液界面处固体一侧
杂质浓度和液体中杂质浓度的比值,称为有效分
凝系数
Ke CS
CL
有效分凝系数和平衡分凝系数遵循 BPS关系(普凡方程)
Ke
K0
f
K0 (1K0)e D
单晶硅的电阻率与掺杂浓度的关系式