CAE分析
常用CAE分析简介

常用CAE分析简介1. 有限元分析(FEA):有限元分析是一种将复杂结构分解为简单单元的方法,通过求解这些单元的力学行为,从而得到整个结构的力学性能。
有限元分析广泛应用于结构分析、热分析、流体分析等领域,可以帮助工程师评估设计的强度、刚度、稳定性等性能指标。
2. 计算流体动力学(CFD):计算流体动力学是一种利用数值方法模拟流体流动问题的方法。
通过CFD分析,工程师可以了解流体在特定条件下的速度、压力、温度等参数,从而优化设计,提高设备的性能。
CFD分析广泛应用于航空航天、汽车、化工、建筑等领域。
3. 多体动力学(MBD):多体动力学是一种模拟多个刚体之间相互作用的力学分析方法。
通过MBD分析,工程师可以研究机械系统的运动特性、动力学性能和振动特性,从而优化设计,提高设备的可靠性。
MBD分析广泛应用于汽车、、航天器等领域。
4. 优化设计:优化设计是一种在满足一定约束条件下,寻找最优设计方案的方法。
通过优化设计,工程师可以在保证产品质量的前提下,降低成本、提高性能。
优化设计方法包括线性规划、非线性规划、遗传算法等。
5. 可靠性分析:可靠性分析是一种评估产品在使用过程中发生故障的概率的方法。
通过可靠性分析,工程师可以了解产品的故障模式和故障原因,从而优化设计,提高产品的可靠性。
可靠性分析方法包括故障树分析、故障模式与影响分析等。
CAE分析在工程领域具有广泛的应用,可以帮助工程师在设计阶段发现潜在问题,优化设计,提高产品质量和降低成本。
随着计算机技术的不断发展,CAE分析将在未来发挥越来越重要的作用。
6. 热分析:热分析是一种评估产品在温度变化下的热传导、热对流和热辐射性能的方法。
通过热分析,工程师可以了解产品在不同温度条件下的热性能,从而优化设计,提高产品的热效率和热稳定性。
热分析广泛应用于电子设备、汽车、航空航天等领域。
7. 声学分析:声学分析是一种评估产品在声波作用下的声学性能的方法。
通过声学分析,工程师可以了解产品在不同频率下的声压级、声强级和声功率级等参数,从而优化设计,提高产品的声学性能。
机械设计基础机械设计中的CAE分析方法

机械设计基础机械设计中的CAE分析方法机械设计是工程领域中非常重要的一项任务,它涉及到各种机械设备的设计和制造。
而在现代机械设计中,CAE(计算机辅助工程)分析方法的应用越来越广泛,为设计师提供了强大的工具和技术支持。
本文将介绍机械设计中常用的CAE分析方法,以及它们在设计过程中的应用。
一、有限元分析(Finite Element Analysis,简称FEA)有限元分析是机械设计中最常用的CAE分析方法之一。
它通过将实际的结构分割成有限数量的小元素,然后利用数值计算方法求解每个小元素的应力、变形等物理量。
这样可以在较小的计算范围内,准确预测结构的力学性能。
在机械设计中,有限元分析广泛应用于刚度、强度、稳定性、疲劳寿命等方面的评估。
设计师可以通过有限元分析来验证设计方案的可行性,确定合适的材料和尺寸,并最终优化设计方案。
二、计算流体力学分析(Computational Fluid Dynamics,简称CFD)计算流体力学分析是机械设计中另一个重要的CAE分析方法。
它用数值方法解决流体力学方程,对液态、气态流体的流动、传热、传质等进行模拟和计算。
在机械设计中,计算流体力学分析常用于气动性能、液压性能、热传导等方面的研究。
通过CFD分析,设计师可以预测流体在机械设备中的流动状态和传热效果,为设计方案的改进提供重要的参考。
三、多体动力学分析(Multibody Dynamics Analysis,简称MDA)多体动力学分析是机械设计中用于研究刚体与刚体之间相对运动的CAE分析方法。
它将机械系统视为由多个刚体组成的多体系统,通过求解动力学方程,计算系统中刚体的位移、速度、加速度等运动参数。
在机械设计中,多体动力学分析广泛应用于机构设计、机械振动、运动机理等方面的研究。
通过MDA分析,设计师可以了解机械系统的运动规律和力学性能,优化机构设计,提高系统的工作效率和稳定性。
四、耦合分析(Coupled Analysis)耦合分析是机械设计中将多个CAE分析方法整合起来进行综合分析的方法。
2024年CAE市场前景分析

2024年CAE市场前景分析1. 引言计算机辅助工程(CAE)是一种利用计算机技术对工程领域中的设计、分析和优化进行支持的方法。
随着科技的不断进步和全球市场对高品质产品的不断需求,CAE市场前景变得极为广阔。
本文将对CAE市场未来的发展进行分析,并探讨其市场前景。
2. CAE市场概览CAE市场是一个多元化、竞争激烈的市场。
它包括了众多的子领域,例如:有限元分析(FEA)、计算流体力学(CFD)、多体动力学(MBD)等等。
根据市场研究机构的数据,全球CAE市场规模正在稳步增长,预计未来几年将保持相对稳定的增长趋势。
3. CAE市场驱动因素3.1 技术进步随着计算机硬件和软件技术的不断进步,CAE技术也得到了长足发展。
高性能计算机的出现使得复杂的工程分析和建模成为可能。
同时,新的模拟方法和算法的发展为工程师提供了更准确和高效的工具,促进了CAE市场的增长。
3.2 成本削减传统的物理试验需要巨大的投资和时间,而CAE技术可以通过模拟和仿真快速验证设计方案,减少试验成本和时间。
这在制造业和工程设计领域尤为重要。
3.3 市场需求全球市场对高品质产品的需求正在不断增加。
CAE技术可以帮助设计师提高产品的质量和性能,在常规设计方法中很难达到的要求。
此外,全球竞争的加剧也推动了CAE技术的应用,以提高企业的技术竞争力。
4. CAE市场的挑战4.1 技术复杂性CAE技术要求工程师具备一定的数学、物理和计算机背景知识。
这对于传统工程师来说可能是一个挑战,需要进行持续的专业培训和学习。
4.2 软件和硬件成本高端的CAE软件和计算机硬件是昂贵的投资,对于中小企业来说可能不易承担。
此外,随着技术的不断更新和升级,软件和硬件的维护和更新成本也会增加。
5. CAE市场的发展趋势5.1 云计算与软件即服务(SaaS)云计算和软件即服务(SaaS)的出现为CAE市场带来了新的发展机遇。
云计算能够提供更强大的计算能力,解决了CAE计算过程中的瓶颈问题。
CAE仿真分析流程

CAE仿真分析流程CAE(计算机辅助工程)仿真分析是一种利用计算机实现的工程分析方法,以模拟和预测工程产品和系统的性能。
它通过数值计算和模型来代替传统的试验方法,可以快速、准确地评估产品的设计和性能。
下面是CAE仿真分析的流程及其步骤。
第一步:准备工作在进行CAE仿真分析之前,需要建立分析目标和所需的输入数据、边界条件以及使用的CAD模型。
这包括收集和整理相关数据,制定分析方案和目标。
第二步:建立数值模型在这一步,需要将CAD模型转化为数值模型,以便进行数值计算。
这可以通过网格划分和离散化来实现。
划分网格时,需要考虑模型的几何和结构特征。
第三步:设定物理和数学模型在这一步中,需要选择适当的物理模型(如流体动力学、热传导等)和数学模型(如有限元法、有限差分法等)。
物理模型会影响模拟的准确性和计算效率。
第四步:设定边界条件在这一步中,需要指定问题的边界条件,如约束、加速度和载荷等。
这些条件会直接影响计算结果和仿真分析的准确性。
第五步:进行数值计算在这一步中,使用所选的数值方法和模型进行数值计算。
这包括解方程组、求解数值逼近方程以及处理非线性和非定常问题等。
第六步:分析结果在这一步中,需要对数值计算的结果进行分析和解释。
这可能涉及到图形绘制、数据处理和统计分析等。
通过分析结果,可以评估产品的性能和优化设计。
第七步:验证和验证在这一步中,需要对模拟结果进行验证和验证。
这可以通过将仿真结果与真实试验数据进行比较来实现。
如果两者之间有良好的一致性,那么该模拟可以用于预测实际情况。
第八步:优化设计根据仿真结果和分析,可以对设计进行优化。
可以通过调整材料、几何形状和边界条件等来改善产品的性能。
第九步:迭代在这一步中,如果发现仿真结果与实际情况不一致,可以对模型和分析方法进行调整和迭代。
这可以提高仿真的准确性和可靠性。
总结CAE仿真分析是一种快速、准确和经济实用的工程分析方法。
通过建立数值模型、设定物理和数学模型、进行数值计算和分析结果,可以预测产品性能和优化设计。
CAE分析解读与提升

CAE分析解读与提升1.结果视觉化:CAE分析通常会生成大量的数值数据,为了更好地理解和解释分析结果,通常需要将这些数据可视化成图表、图像或动画。
这样不仅可以更直观地呈现结果,也可以帮助工程师发现其中的规律和问题。
2.结果解释:CAE分析结果需要根据实际情况进行解释,比如验证设计的合理性、确认是否满足规定的要求和标准、评估产品的寿命等等。
解释结果需要综合考虑材料性能、结构特点、加载条件等各种因素,并根据实际需求进行分析和判断。
3.结果评估:CAE分析结果需要进行评估,以确定产品在正常使用条件下的可行性、安全性及其它性能指标。
评估的方法可以包括对比分析、灵敏度分析、优化分析等等。
通过评估分析,可以为产品的设计和改进提供依据和指导。
提高CAE分析的能力和准确性有以下几个方面的方法:1.提高建模能力:合适的建模能力对于CAE分析的结果至关重要。
工程师需要具备良好的理论基础和实践经验,能够准确地将实际产品转换为数学模型,并在模型中考虑各种因素的影响。
2.改进边界条件和加载方式:加载条件和边界条件的设定对于分析结果的准确性和可靠性有很大的影响。
工程师需要对实际产品的使用环境和加载方式进行合理的估计和设定,同时也需要对加载条件进行敏感性分析,以确定其对结果的影响。
3.验证和对比实验:为了验证CAE分析结果的准确性和可靠性,可以进行实验验证和对比。
实验结果可以作为评估和校正CAE模型的参考,同时也可以帮助工程师了解CAE分析的局限性和不确定性。
4.不断学习和更新知识:CAE技术在不断发展和更新,工程师需要时刻保持学习和更新的态度,了解最新的分析方法和技术。
同时也需要关注工程实践中的问题和挑战,探索解决问题的新思路和方法。
总之,CAE分析的解读和提升是提高工程效率和产品质量的关键。
通过合理的结果解读和评估,工程师可以更好地理解产品的性能和行为,并为产品的设计和改进提供有力支持。
同时,不断提高CAE分析的能力和准确性,可以在工程实践中发挥更大的作用,为产品的优化和创新提供可靠的技术支持。
cae分析流程范文

cae分析流程范文1.确定问题和目标:首先,需要明确问题和目标。
工程师需要与设计团队和相关利益相关者沟通,了解产品的需求和性能要求。
同时,需要明确分析的目标,例如验证设计的可行性、优化产品性能等。
2.数据准备:在进行CAE分析之前,需要准备相关的数据。
这包括产品的几何模型、材料性质、边界条件和加载条件等。
通常,工程师可以使用计算机辅助设计(CAD)软件创建产品的几何模型,并导入到CAE软件中。
3.网格生成:在进行CAE分析之前,需要将产品的几何模型离散化为有限元网格。
有限元网格是由许多小的几何单元(例如三角形或四边形)组成的,用于对产品进行数值计算。
网格生成是一个关键步骤,其质量和密度直接影响到分析结果的准确性和计算效率。
4.定义材料和加载条件:在进行CAE分析之前,需要定义产品的材料性质和加载条件。
对于材料性质,可以通过实验或模型进行获取。
加载条件包括外部力、温度、压力等,需要根据实际应用场景进行定义。
5.模型设置:在进行CAE分析之前,需要设置分析模型。
这包括选择适当的分析方法(例如有限元分析、流体动力学分析等)、选择适当的求解器和设置数值参数等。
在设置模型时,需要根据实际问题和目标进行选择和调整。
6.运行分析:在设置好模型后,可以运行分析。
CAE软件会根据所选的分析方法和设置的参数对产品进行模拟和计算。
运行分析的时间取决于问题的复杂性和计算机性能等因素。
7.结果分析和评估:在分析完成后,需要对结果进行分析和评估。
结果可以包括产品的应力、应变、位移、温度等信息。
工程师可以对结果进行可视化和统计分析,评估产品的性能和可靠性。
8.结果解释和优化:根据分析结果,工程师可以对产品进行进一步的优化。
这可能包括调整产品的几何形状、材料选择、加载条件等。
通过CAE分析的结果,可以更好地指导产品设计和制造过程,提高产品性能和质量。
9.文档记录和报告:最后,需要对CAE分析的过程和结果进行文档记录和报告。
这有助于团队内部的沟通和知识共享,也有助于与利益相关者进行沟通和决策。
CAE分析报告流程

CAE分析报告流程CAE分析报告是以有限元分析(CAE)技术为基础的工程分析报告,用于对复杂结构或部件的性能进行深入评估和优化。
本文将详细介绍CAE分析报告的流程,包括前期准备、建模与网格划分、加载和边界条件的定义、求解和后处理等步骤。
一、前期准备阶段在开始CAE分析之前,首先需要明确分析的目标和要求,包括结构的应力、变形、疲劳寿命等指标。
此外,还需收集相关的材料性能参数、工程图纸、边界条件等基础数据,并对其中的约束和假设进行评估。
二、建模与网格划分阶段建模是将真实的结构或部件抽象成数学模型的过程。
在这个阶段,应根据实际情况选择合适的建模方法,如二维平面模型或三维实体模型,并建立相应的几何特征。
此外,还需要根据结构的复杂程度和精度要求选择适当的网格划分方法,如四面体网格、六面体网格或八面体网格等。
三、加载和边界条件的定义阶段加载和边界条件的定义是指对模型施加外部载荷和约束条件,模拟真实工况下的力学行为。
例如,可以通过定义施加载荷的大小、方向和分布方式来模拟实际工作状态下的负荷;同时,还需要定义与其他部件的接触、约束和固定等边界条件。
四、求解阶段在完成加载和边界条件的定义后,即可进行求解过程。
求解是基于有限元法,将结构或部件划分成有限数量的元素,利用数学和力学原理对每个元素进行离散描述,并通过求解相应的线性或非线性方程组得到模型的应力、变形和其他相关结果。
在进行求解之前,还需选择合适的求解器和合理的控制参数,并进行模型的数值稳定性和收敛性分析。
五、后处理阶段求解完成后,需要对计算结果进行后处理和分析。
后处理包括对结果数据的提取、整理和可视化,以便更直观地了解结构的应力、变形分布和其他性能指标。
同时,还可进行数据对比、灵敏度分析和优化设计等后处理工作,从而得到一些有关结构性能和优化可能性的建议。
最后,根据实际情况和需求,可以将最终的结果汇总成CAE分析报告。
该报告将包括前期准备、建模与网格划分、加载和边界条件的定义、求解和后处理等各个阶段的详细过程、结果和分析,以及对结构性能和优化方案的评估和建议。
CAE分析岗位职责
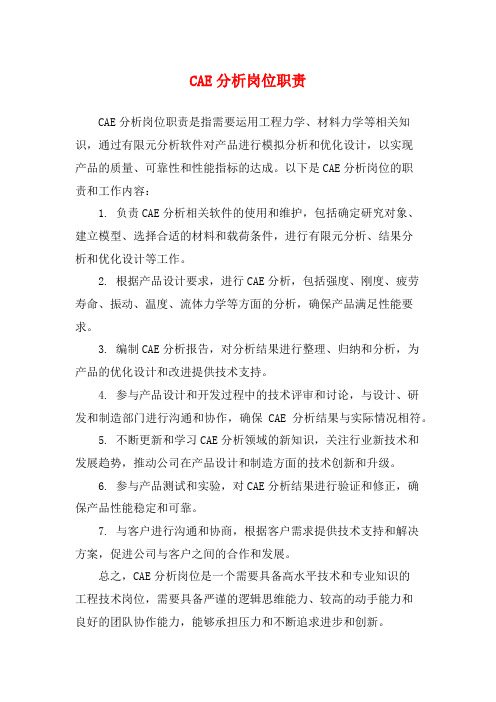
CAE分析岗位职责
CAE分析岗位职责是指需要运用工程力学、材料力学等相关知识,通过有限元分析软件对产品进行模拟分析和优化设计,以实现
产品的质量、可靠性和性能指标的达成。
以下是CAE分析岗位的职
责和工作内容:
1. 负责CAE分析相关软件的使用和维护,包括确定研究对象、
建立模型、选择合适的材料和载荷条件,进行有限元分析、结果分
析和优化设计等工作。
2. 根据产品设计要求,进行CAE分析,包括强度、刚度、疲劳
寿命、振动、温度、流体力学等方面的分析,确保产品满足性能要求。
3. 编制CAE分析报告,对分析结果进行整理、归纳和分析,为
产品的优化设计和改进提供技术支持。
4. 参与产品设计和开发过程中的技术评审和讨论,与设计、研
发和制造部门进行沟通和协作,确保CAE分析结果与实际情况相符。
5. 不断更新和学习CAE分析领域的新知识,关注行业新技术和
发展趋势,推动公司在产品设计和制造方面的技术创新和升级。
6. 参与产品测试和实验,对CAE分析结果进行验证和修正,确
保产品性能稳定和可靠。
7. 与客户进行沟通和协商,根据客户需求提供技术支持和解决
方案,促进公司与客户之间的合作和发展。
总之,CAE分析岗位是一个需要具备高水平技术和专业知识的
工程技术岗位,需要具备严谨的逻辑思维能力、较高的动手能力和
良好的团队协作能力,能够承担压力和不断追求进步和创新。
CAE分析验证流程

CAE分析验证流程医疗设备的CAE(计算机辅助工程)分析验证流程是为了确认设备的设计是否满足一些特定的标准和要求。
以下是一个典型的CAE分析验证流程的概述。
第一步:确定验证标准和目标在进行CAE分析验证之前,首先需要明确验证的标准和目标。
这通常是通过评估和理解设备的功能要求和性能指标来确定的。
例如,可能需要验证设备的耐用性、安全性、性能等方面的标准。
第二步:开展建模和网格化在进行CAE分析验证之前,需要将设备进行建模并生成网格化结构。
建模是将设备几何形状转化为计算机可处理的几何模型的过程,而网格化是将建模结果划分为小的元素(如三角形或四面体)以进行计算的过程。
这一步是分析的基础,因此需要仔细、准确地进行。
第三步:选择适当的CAE工具和方法根据验证的标准和目标,选择适当的CAE工具和方法来进行分析。
常用的CAE工具包括有限元分析(FEA)、计算流体力学(CFD)、多体动力学(MBD)等。
根据设备的特点和需求,选择相应的工具和方法进行分析。
第四步:进行CAE分析在这一步中,使用选择的工具和方法来进行CAE分析。
根据验证的目标,设置适当的边界条件和加载条件,并执行必要的计算。
例如,在进行有限元分析时,需要设置适当的约束条件、加载条件和材料特性等。
第五步:结果评估和解释分析完成后,对计算结果进行评估和解释。
这包括对结果进行可视化和图表化,以便更好地理解和解释分析结果。
如果结果不符合验证的标准和目标,需要对设计进行相应的修改和优化。
第六步:验证结果的可靠性在分析完成后,需要验证结果的可靠性。
这可以通过与实验数据的对比和验证来完成。
如果结果与实验数据一致,则可以认为分析是可靠的。
第七步:撰写验证报告最后一步是撰写验证报告。
报告应包括验证的标准和目标、建模和分析的方法、计算结果和分析的可靠性等内容。
这将有助于将分析结果传达给相关的利益相关者,并作为日后改进设备设计的依据。
总结:CAE分析验证流程是一个系统化的过程,涉及到多个步骤和方法。
CAE分析解读与提升
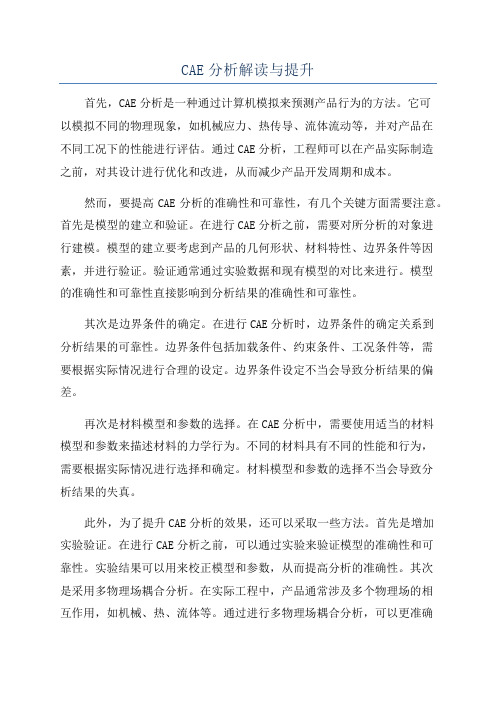
CAE分析解读与提升首先,CAE分析是一种通过计算机模拟来预测产品行为的方法。
它可以模拟不同的物理现象,如机械应力、热传导、流体流动等,并对产品在不同工况下的性能进行评估。
通过CAE分析,工程师可以在产品实际制造之前,对其设计进行优化和改进,从而减少产品开发周期和成本。
然而,要提高CAE分析的准确性和可靠性,有几个关键方面需要注意。
首先是模型的建立和验证。
在进行CAE分析之前,需要对所分析的对象进行建模。
模型的建立要考虑到产品的几何形状、材料特性、边界条件等因素,并进行验证。
验证通常通过实验数据和现有模型的对比来进行。
模型的准确性和可靠性直接影响到分析结果的准确性和可靠性。
其次是边界条件的确定。
在进行CAE分析时,边界条件的确定关系到分析结果的可靠性。
边界条件包括加载条件、约束条件、工况条件等,需要根据实际情况进行合理的设定。
边界条件设定不当会导致分析结果的偏差。
再次是材料模型和参数的选择。
在CAE分析中,需要使用适当的材料模型和参数来描述材料的力学行为。
不同的材料具有不同的性能和行为,需要根据实际情况进行选择和确定。
材料模型和参数的选择不当会导致分析结果的失真。
此外,为了提升CAE分析的效果,还可以采取一些方法。
首先是增加实验验证。
在进行CAE分析之前,可以通过实验来验证模型的准确性和可靠性。
实验结果可以用来校正模型和参数,从而提高分析的准确性。
其次是采用多物理场耦合分析。
在实际工程中,产品通常涉及多个物理场的相互作用,如机械、热、流体等。
通过进行多物理场耦合分析,可以更准确地描述产品的行为。
最后是使用优化算法。
通过使用优化算法,可以对产品的设计进行自动化优化,从而达到最佳的性能和效果。
总而言之,CAE分析是一种重要而有效的工程设计和分析方法。
通过合理选择模型、设定边界条件和材料参数,可以提高分析结果的准确性和可靠性。
同时,通过增加实验验证、多物理场耦合分析和使用优化算法等方法,可以进一步提升CAE分析的效果。
cae分析报告
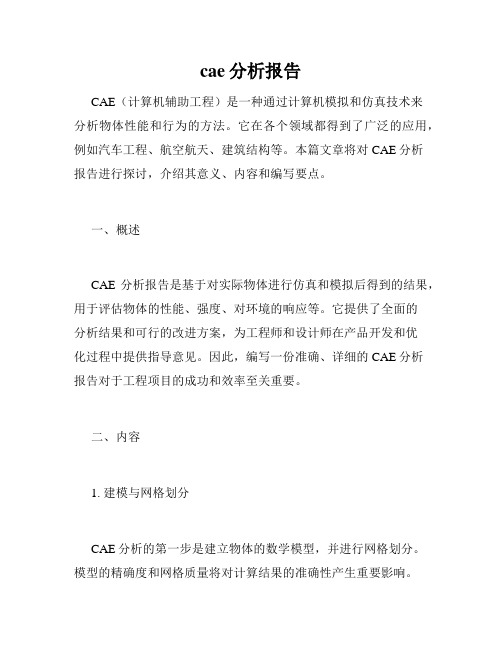
cae分析报告CAE(计算机辅助工程)是一种通过计算机模拟和仿真技术来分析物体性能和行为的方法。
它在各个领域都得到了广泛的应用,例如汽车工程、航空航天、建筑结构等。
本篇文章将对CAE分析报告进行探讨,介绍其意义、内容和编写要点。
一、概述CAE分析报告是基于对实际物体进行仿真和模拟后得到的结果,用于评估物体的性能、强度、对环境的响应等。
它提供了全面的分析结果和可行的改进方案,为工程师和设计师在产品开发和优化过程中提供指导意见。
因此,编写一份准确、详细的CAE分析报告对于工程项目的成功和效率至关重要。
二、内容1. 建模与网格划分CAE分析的第一步是建立物体的数学模型,并进行网格划分。
模型的精确度和网格质量将对计算结果的准确性产生重要影响。
因此,在报告中需要详细描述建模过程,包括采用的软件和方法、模型的几何特征、所选网格类型和质量等。
2. 载荷和约束条件在进行CAE分析前,需要确定物体所受的外部载荷和内部约束条件。
比如,在汽车工程中,载荷可以是行驶在不同路况下的动态载荷,约束条件可以是车轮在地面上的接触条件。
在报告中,需清晰地描述这些载荷和约束条件,并给出计算依据和分析原理。
3. 结果分析CAE分析的核心是得到准确的结果,并进行深入的分析与解释。
在报告中,应包括物体的应力分布、变形情况、疲劳寿命、流体流动轨迹等相关结果。
同时,需要对结果进行分析,解释其原因和影响,并与实验数据进行对比,以验证模型的准确性。
4. 优化方案根据CAE分析的结果,可以提出改进和优化方案,以提高产品的性能和可靠性。
在报告中,需要详细描述这些方案的设计思路和实施步骤。
同时,对于每个方案,应进行CAE分析以评估其效果,并给出具体的指导建议。
三、编写要点1. 语言简洁明了:CAE分析报告通常是给工程师和设计师阅读的,因此要避免使用过于专业或晦涩的术语和定量方法。
尽可能使用简单明了的语言,使读者能够轻松理解和掌握分析结果。
2. 图表展示清晰:在CAE分析报告中,经常使用图表来展示结果和数据。
CAE分析报告(2024)
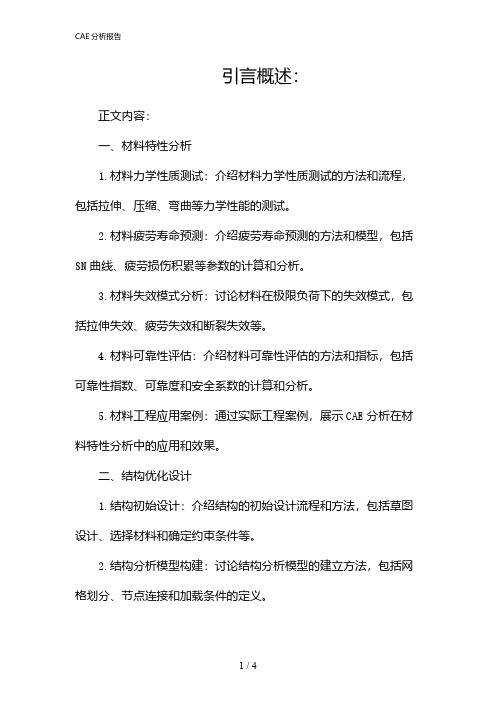
引言概述:正文内容:一、材料特性分析1.材料力学性质测试:介绍材料力学性质测试的方法和流程,包括拉伸、压缩、弯曲等力学性能的测试。
2.材料疲劳寿命预测:介绍疲劳寿命预测的方法和模型,包括SN曲线、疲劳损伤积累等参数的计算和分析。
3.材料失效模式分析:讨论材料在极限负荷下的失效模式,包括拉伸失效、疲劳失效和断裂失效等。
4.材料可靠性评估:介绍材料可靠性评估的方法和指标,包括可靠性指数、可靠度和安全系数的计算和分析。
5.材料工程应用案例:通过实际工程案例,展示CAE分析在材料特性分析中的应用和效果。
二、结构优化设计1.结构初始设计:介绍结构的初始设计流程和方法,包括草图设计、选择材料和确定约束条件等。
2.结构分析模型构建:讨论结构分析模型的建立方法,包括网格划分、节点连接和加载条件的定义。
3.结构优化算法:介绍结构优化算法的原理和分类,包括形状优化、拓扑优化和参数优化等方法。
4.结构优化效果评估:针对不同的优化目标,介绍效果评估指标的选取和考虑因素的分析。
5.结构优化设计案例:通过实际工程案例,展示CAE分析在结构优化设计中的应用和效果。
三、热仿真分析1.热传导分析:介绍热传导分析的原理和计算方法,包括热传导方程和传热边界条件的建立。
2.热应力分析:讨论热应力分析的方法和模型,包括线性热弹性模型和非线性热弹性模型。
3.温度场分布分析:展示CAE分析在温度场分布分析中的应用,包括温度梯度和温度均匀性等指标的计算和评价。
4.热仿真优化设计:介绍热仿真优化设计的原理和流程,包括热网格优化和热传导路径优化等方法。
5.热仿真分析案例:通过实际工程案例,展示CAE分析在热仿真分析中的应用和效果。
四、流体力学分析1.流体流动模拟:介绍流体流动模拟的原理和方法,包括NavierStokes方程和控制方程的求解。
2.流场数值计算:讨论流场数值计算的过程和方法,包括网格划分、边界条件设置和求解器选择等。
3.流场压力分析:分析流体流动中的压力场分布和压力梯度的计算和分析。
cae分析报告
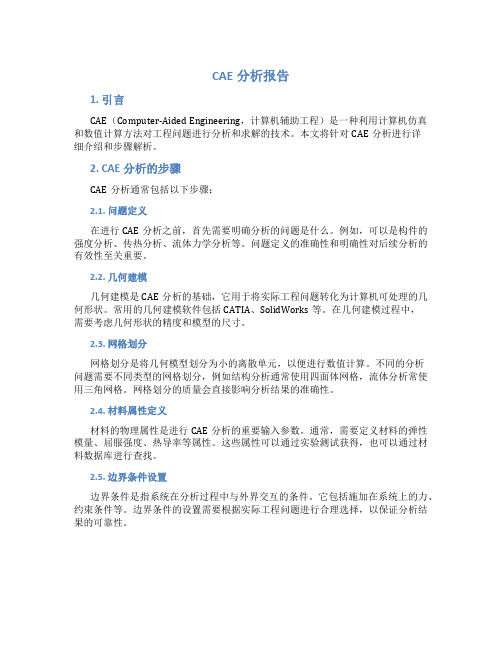
CAE分析报告1. 引言CAE(Computer-Aided Engineering,计算机辅助工程)是一种利用计算机仿真和数值计算方法对工程问题进行分析和求解的技术。
本文将针对CAE分析进行详细介绍和步骤解析。
2. CAE分析的步骤CAE分析通常包括以下步骤:2.1. 问题定义在进行CAE分析之前,首先需要明确分析的问题是什么。
例如,可以是构件的强度分析、传热分析、流体力学分析等。
问题定义的准确性和明确性对后续分析的有效性至关重要。
2.2. 几何建模几何建模是CAE分析的基础,它用于将实际工程问题转化为计算机可处理的几何形状。
常用的几何建模软件包括CATIA、SolidWorks等。
在几何建模过程中,需要考虑几何形状的精度和模型的尺寸。
2.3. 网格划分网格划分是将几何模型划分为小的离散单元,以便进行数值计算。
不同的分析问题需要不同类型的网格划分,例如结构分析通常使用四面体网格,流体分析常使用三角网格。
网格划分的质量会直接影响分析结果的准确性。
2.4. 材料属性定义材料的物理属性是进行CAE分析的重要输入参数。
通常,需要定义材料的弹性模量、屈服强度、热导率等属性。
这些属性可以通过实验测试获得,也可以通过材料数据库进行查找。
2.5. 边界条件设置边界条件是指系统在分析过程中与外界交互的条件。
它包括施加在系统上的力、约束条件等。
边界条件的设置需要根据实际工程问题进行合理选择,以保证分析结果的可靠性。
2.6. 求解模型求解模型是指利用数值方法对系统进行求解,得到系统的响应结果。
常用的数值方法包括有限元法、有限差分法等。
求解模型的准确性和稳定性对分析结果的可信度具有重要影响。
2.7. 结果分析与评估在完成求解后,需要对分析结果进行分析和评估。
这包括对应力、应变、温度等物理量的分析,以及对系统性能和安全性的评估。
分析报告应清晰地呈现分析结果,并提供有效的解决方案。
3. CAE分析的应用领域CAE分析在工程领域有着广泛的应用。
cae分析报告

cae分析报告CAE分析报告。
一、背景介绍。
CAE(Computer-Aided Engineering)即计算机辅助工程,是利用计算机仿真技术对工程问题进行分析和解决的一种方法。
它可以在产品设计的早期阶段就对产品的性能进行评估,从而提高产品的质量和效率。
本报告旨在对某产品的CAE分析结果进行详细报告,以便后续工程师和设计师们对产品进行改进和优化。
二、分析方法。
在本次分析中,我们使用了有限元分析(FEA)和计算流体动力学(CFD)两种主要的CAE分析方法。
有限元分析用于对产品的结构强度、刚度和振动特性进行评估,而计算流体动力学则用于分析产品的流体流动、传热和压力等特性。
通过这两种方法的综合分析,可以全面地了解产品的性能和特性。
三、结构强度分析。
通过有限元分析,我们对产品的结构强度进行了评估。
结果显示,在受力情况下,产品的各个部位都能够承受相应的载荷,不存在明显的应力集中现象。
同时,我们也对产品的刚度进行了分析,发现在受力情况下,产品的变形较小,刚度较高,能够满足设计要求。
四、振动特性分析。
除了结构强度分析,我们还对产品的振动特性进行了评估。
结果显示,在受到外部激励时,产品的振动频率和振幅均在合理范围内,不会对产品的正常使用造成影响。
这对于产品的可靠性和稳定性具有重要意义。
五、流体流动分析。
在计算流体动力学分析中,我们对产品的流体流动特性进行了评估。
通过模拟不同工况下的流体流动情况,我们发现产品的流体流动较为稳定,压力分布均匀,传热效果良好。
这为产品的优化设计提供了重要参考。
六、总结。
综上所述,通过本次CAE分析,我们全面地了解了产品的结构强度、振动特性和流体流动特性。
通过对分析结果的综合评估,我们可以为产品的改进和优化提供重要参考。
在今后的产品设计过程中,CAE分析将继续发挥重要作用,帮助我们不断提升产品的质量和性能。
七、参考文献。
1. Smith, J. (2018). Introduction to Finite Element Analysis. New York: McGraw-Hill.2. Jones, L. (2017). Computational Fluid Dynamics in Engineering. London: Springer.以上为本次CAE分析报告的内容,希望能为产品的改进和优化提供有益的参考。
CAE分析流程范文

CAE分析流程范文1.确定任务目标:首先需要明确CAE分析的目标是什么,是为了验证设计是否满足要求,还是为了改进和优化设计等。
2.获取CAD模型:在进行CAE分析之前,需要获取产品或结构的CAD 模型。
这个模型应该包含几何形状、边界条件和材料属性等基本信息。
3.建立有限元模型:使用CAE软件通过CAD模型建立有限元模型。
这个过程包括网格划分、选择适当的单元类型和节点等。
在建立模型时,需要考虑模型精度和计算效率的平衡。
4.分析设置:根据任务目标和要求,设置分析的类型和参数。
常见的分析类型包括静力学分析、动力学分析、热力学分析等。
还需要确定适当的边界条件、加载方式和材料模型等。
5.模型求解:使用数值解法求解建立的有限元模型,得到计算结果。
这个过程中,需要考虑求解器的选择和计算资源的配置。
6.结果评估:根据任务目标,对计算结果进行评估和分析。
这包括强度、刚度、振动、热分布等方面的评估。
需要与设计要求进行对比,判断设计是否合理或需要优化。
7.结果后处理和可视化:对计算结果进行后处理和可视化。
可以利用CAE软件进行结果的处理和分析,生成报告和图表等。
8.结果验证和校核:进行结果的验证和校核,与实验数据进行对比,判断计算结果的准确性和可靠性。
9.优化设计:如果计算结果不符合要求,需要进行优化设计。
可以通过参数优化、拓扑优化等方法实现。
然后重新进行分析和评估。
10.结果应用:将优化的设计方案应用于实际生产中。
可以将优化方案与原始设计进行比较,评估改进效果和性能提升程度。
总结起来,CAE分析流程包括确定任务目标、获取CAD模型、建立有限元模型、分析设置、模型求解、结果评估、结果后处理和可视化、结果验证和校核、优化设计、结果应用等步骤。
通过这样一系列的分析和优化过程,可以有效地提高产品和结构的设计质量和性能。
CAE分析教程实例精华版
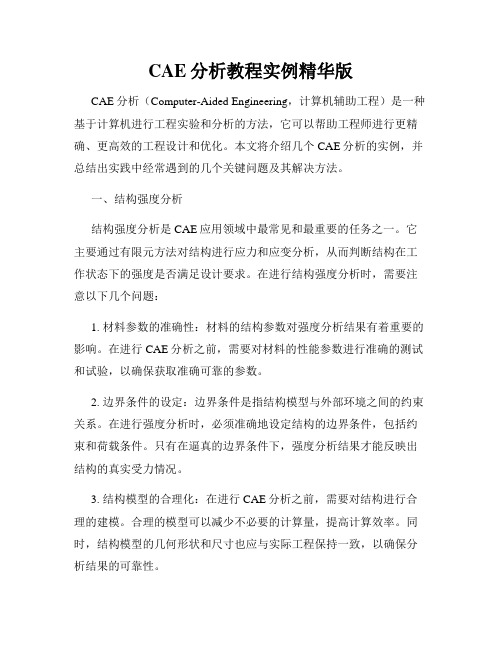
CAE分析教程实例精华版CAE分析(Computer-Aided Engineering,计算机辅助工程)是一种基于计算机进行工程实验和分析的方法,它可以帮助工程师进行更精确、更高效的工程设计和优化。
本文将介绍几个CAE分析的实例,并总结出实践中经常遇到的几个关键问题及其解决方法。
一、结构强度分析结构强度分析是CAE应用领域中最常见和最重要的任务之一。
它主要通过有限元方法对结构进行应力和应变分析,从而判断结构在工作状态下的强度是否满足设计要求。
在进行结构强度分析时,需要注意以下几个问题:1. 材料参数的准确性:材料的结构参数对强度分析结果有着重要的影响。
在进行CAE分析之前,需要对材料的性能参数进行准确的测试和试验,以确保获取准确可靠的参数。
2. 边界条件的设定:边界条件是指结构模型与外部环境之间的约束关系。
在进行强度分析时,必须准确地设定结构的边界条件,包括约束和荷载条件。
只有在逼真的边界条件下,强度分析结果才能反映出结构的真实受力情况。
3. 结构模型的合理化:在进行CAE分析之前,需要对结构进行合理的建模。
合理的模型可以减少不必要的计算量,提高计算效率。
同时,结构模型的几何形状和尺寸也应与实际工程保持一致,以确保分析结果的可靠性。
二、热传导分析热传导分析是指通过CAE方法对物体内部的温度分布和传导过程进行模拟和分析。
在进行热传导分析时,需要注意以下几个问题:1. 材料的热性能参数:热传导分析需要准确的材料热性能参数,包括导热系数、比热容等。
这些参数的准确性直接影响到分析结果的准确性。
因此,在进行热传导分析之前,需要对材料的热性能参数进行准确测试和试验。
2. 初始温度和边界条件:在进行热传导分析时,需要准确设定物体的初始温度和边界条件。
初始温度是指物体在开始分析时的温度状态,而边界条件包括约束和热流条件等。
合理的初始温度和边界条件可以保证分析结果的可靠性。
3. 网格划分和时间步长:在进行热传导分析时,需要对物体进行网格划分,将其离散为一个个小单元,以进行计算。
cae分析报告

cae分析报告CAE分析报告是一种基于数值模拟、力学分析和材料力学等方法,对于产品的性能进行评估和优化的工程分析方法。
本报告将对某个产品的CAE分析结果进行详细介绍和分析。
经过CAE分析,建议在产品的设计和制造过程中采用合适的材料和结构,以确保产品的性能和质量。
首先,对于材料的选择,通过CAE分析发现,目前使用的材料具有较高的强度和刚度,能够满足应力和振动的要求,但是存在一定的开裂和断裂的风险。
因此,建议在材料选择时,考虑使用更具韧性的材料,以增加产品的抗拉伸能力和耐磨性,同时降低开裂和断裂的风险。
其次,在产品设计和制造过程中,需要考虑到产品的结构强度和刚度。
通过CAE分析,发现当前产品在受力部位存在一定的应力集中,可能导致局部的破坏和失效。
因此,建议在产品的设计过程中,增加受力部位的支撑和加强结构,以分散应力和提高产品的强度。
另外,还可以考虑使用增加刚度的结构设计,以降低振动和共振的影响,提高产品的稳定性和寿命。
此外,在产品的制造过程中,需要注意制造工艺和表面处理的影响。
通过CAE分析,发现产品的表面粗糙度对于摩擦和磨损的影响较大。
因此,建议在制造过程中,采用适当的加工工艺,以提高表面的光洁度和平整度,降低表面粗糙度,从而减少摩擦和磨损。
最后,在产品的使用和维护过程中,需要进行适当的检测和修复。
通过CAE分析,发现产品的应力和变形会随着使用时间的增加而逐渐积累,可能导致材料疲劳和失效。
因此,建议在产品的使用过程中,定期进行检测和维修,以及时发现和修复产品的疲劳和损伤。
综上所述,CAE分析报告提供了一种全面的工程分析方法,可以评估产品的性能和质量,并提供优化的建议。
通过合理选择材料和结构设计,控制制造工艺和维护过程,可以提高产品的性能和寿命,降低故障和失效的风险。
因此,在产品的设计和制造过程中,需要充分应用CAE分析方法,以确保产品的安全性和可靠性。
CAE分析概述范文
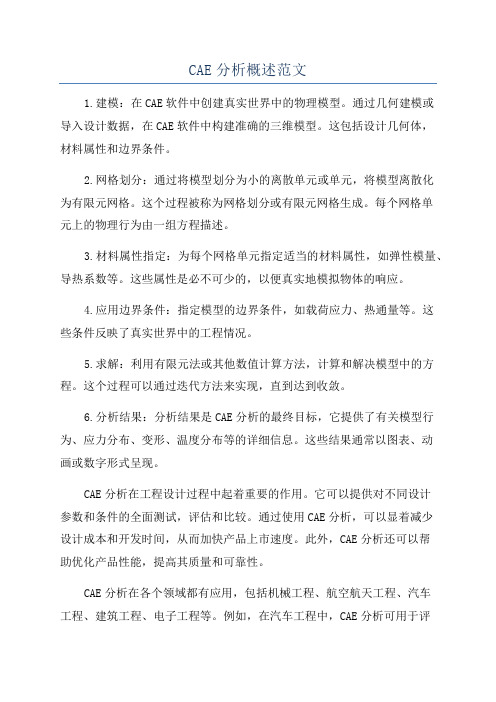
CAE分析概述范文1.建模:在CAE软件中创建真实世界中的物理模型。
通过几何建模或导入设计数据,在CAE软件中构建准确的三维模型。
这包括设计几何体,材料属性和边界条件。
2.网格划分:通过将模型划分为小的离散单元或单元,将模型离散化为有限元网格。
这个过程被称为网格划分或有限元网格生成。
每个网格单元上的物理行为由一组方程描述。
3.材料属性指定:为每个网格单元指定适当的材料属性,如弹性模量、导热系数等。
这些属性是必不可少的,以便真实地模拟物体的响应。
4.应用边界条件:指定模型的边界条件,如载荷应力、热通量等。
这些条件反映了真实世界中的工程情况。
5.求解:利用有限元法或其他数值计算方法,计算和解决模型中的方程。
这个过程可以通过迭代方法来实现,直到达到收敛。
6.分析结果:分析结果是CAE分析的最终目标,它提供了有关模型行为、应力分布、变形、温度分布等的详细信息。
这些结果通常以图表、动画或数字形式呈现。
CAE分析在工程设计过程中起着重要的作用。
它可以提供对不同设计参数和条件的全面测试,评估和比较。
通过使用CAE分析,可以显着减少设计成本和开发时间,从而加快产品上市速度。
此外,CAE分析还可以帮助优化产品性能,提高其质量和可靠性。
CAE分析在各个领域都有应用,包括机械工程、航空航天工程、汽车工程、建筑工程、电子工程等。
例如,在汽车工程中,CAE分析可用于评估车辆碰撞安全性能、车身结构强度等;在电子工程中,CAE分析可用于电路板设计和散热效果评估等等。
总而言之,CAE分析是通过计算机仿真和数值计算技术对工程问题进行分析和解决的过程。
它是现代工程设计的重要工具,可以帮助工程师优化设计、减少成本和提高产品质量。
随着计算机技术的不断发展和CAE软件的不断改进,CAE分析在工程设计中的应用将会越来越广泛。
- 1、下载文档前请自行甄别文档内容的完整性,平台不提供额外的编辑、内容补充、找答案等附加服务。
- 2、"仅部分预览"的文档,不可在线预览部分如存在完整性等问题,可反馈申请退款(可完整预览的文档不适用该条件!)。
- 3、如文档侵犯您的权益,请联系客服反馈,我们会尽快为您处理(人工客服工作时间:9:00-18:30)。
汽车CAE工程分析汽车公司建立高性能的计算机辅助工程分析系统,其专业CAE队伍与产品开发同步地广泛开展CAE应用,在指导设计、提高质量、降低开发成本和缩短开发周期上发挥着日益显著的作用。
CAE应用于车身开发上成熟的方面主要有:刚度、强度、NVH分析、机构运动分析等;而车辆碰撞模拟分析、金属板件冲压成型模拟分析、疲劳分析和空气动力学分析的精度有进一步提高,已投入实际使用,完全可以用于定性分析和改进设计;虚拟试车场整车分析正在着手研究,此外还有焊装模拟分析、喷涂模拟分析等。
汽车公司建立高性能的计算机辅助工程分析系统,其专业CAE队伍与产品开发同步地广泛开展CAE应用,在指导设计、提高质量、降低开发成本和缩短开发周期上发挥着日益显著的作用。
CAE应用于车身开发上成熟的方面主要有:刚度、强度(应用于整车、大小总成与零部件分析,以实现轻量化设计)、NVH分析(各种振动、噪声,包括摩擦噪声、风噪声等)、机构运动分析等;而车辆碰撞模拟分析、金属板件冲压成型模拟分析、疲劳分析和空气动力学分析的精度有进一步提高,已投入实际使用,完全可以用于定性分析和改进设计,大大减少了这些费用高、周期长的试验次数;虚拟试车场整车分析正在着手研究,此外还有焊装模拟分析、喷涂模拟分析等。
一、刚度和强度分析有限元法在机械结构强度和刚度分析方面因具有较高的计算精度而到普遍采用,特别是在材料应力-应变的线性范围内更是如此。
另外,当考虑机械应力与热应力的偶合时,像ANSYS、NASTRAN等大型软件都提供了极为方便的分析手段。
(1)车架和车身的强度和刚度分析:车架和车身是汽车中结构和受力都较复杂的部件,对于全承载式的客车车身更是如此。
车架和车身有限元分析的目的在于提高其承载能力和抗变形能力、减轻其自身重量并节省材料。
另外,就整个汽车而言,当车架和车身重量减轻后,整车重量也随之降低,从而改善整车的动力性和经济性等性能。
(2)齿轮的弯曲应力和接触应力分析:齿轮是汽车发动机和传动系中普遍采用的传动零件。
通过对齿轮齿根弯曲应力和齿面接触应力的分析,优化齿轮结构参数,提高齿轮的承载载力和使用寿命。
(3)发动机零件的应力分析:以发动机的缸盖为例,其工作工程中不仅受到气缸内高压气体的作用,还会产生复杂的热应力。
缸盖开裂事件时有发生。
如果仅采用在开裂处局部加强的办法加以改进,无法从根本上解决问题。
有限元法提供了解决这一问题的根本途径。
二、NVH分析近年来,随着人们环保意识的增强,对汽车提出了更高要求。
为此,国际汽车界制定NVH标准,即噪音(Noise)、振动(Vibration)、平稳(Harshness)三项标准,通俗称为乘坐轿车的“舒适感”。
对NVH标准的一项试验表明,用顾客较喜欢的轿车作试验,在用水泥铺得较平坦的公路上,轿车以时速40公里的速度行驶,如将欧洲产轿车的NVH以100%作标准,日本轿车则为75%,韩国轿车为50%。
欧洲轿车悬架技术较高,所以乘坐舒适,日本轿车设计时将人体工程学考虑在内,对提高乘坐舒适感有很大帮助。
三、机构运动分析机构运动分析就是根据原动件的已知运动规律,求该机构其他构件上某些点的位移、轨迹、速度和加速度,以及这些构件的角位移、角速度和角加速度。
通过对机构进行位移或轨迹的分析,可以确定某机构件在运动时所需得空间,判断当机构运动时各构件之间是否会互相干涉,确定机构中从动件的行程,考察构件上某一点能否实现预定的位置或轨迹要求。
通过对机构进行速度分析,可以了解从动件的速度变化规律能否满足工作要求,了解机构的受力情况。
通过对机构进行加速度分析,可以确定各构件及构件上某些点的加速度,了解机构加速度的变化规律。
机构运动分析的方法很多,主要有图解法和解析法。
四、车辆碰撞模拟分析汽车作为现代化交通工具,在给人们的生活带来便利与乐趣的同时,也因其引起的交通事故给人类的生命和财产带来极大的威胁和伤害。
因此,汽车的安全性是汽车厂商、消费者、政府部门高度关注的问题。
汽车的安全性可划分为主动安全性和被动安全性。
主动安全性是指汽车能够识别潜在的危险自动减速,或当突发的因素出现时,能够在驾驶员的操纵下避免发生交通事故的性能;被动安全性是指汽车发生不可避免的交通事故后,能够对车内乘员或行人进行保护,以免发生伤害或使伤害降低到最小程度。
交通事故原因的统计分析表明,以预防事故发生的主动安全性只能避免5%的事故,因此提高汽车被动安全性日趋重要。
五、金属板冲压成型模拟分析由于冲压成型材料利用率高,产品质量稳定,易于实现自动化生产,故这一工艺方法在汽车生产中得到广泛应用。
在传统的冲压生产过程中,无论是冲压工序的制定、工艺参数的选取,还是冲压模具的设计、制造,都要经过多次修改才能确定。
这种反复的调试过程造成企业人力、物力和财力的大量消耗,导致生产成本高,生产周期难以保证。
冲压成型过程数值模拟技术的出现为改变这种传统模式提供了强有力的工具。
通过对冲压过程模拟分析得到最佳模具结构和工艺条件,并能通过对板材冲压过程数值模拟,在计算机上观察到模具结构、冲压工艺条件(如压边力、冲压方向、摩擦润滑等)和材料性能参数(如皱曲、破裂)的影响,还可以提供最佳钣料形状、合理的压料面形状、最佳冲压方向、以及分析卸载和切边后的回弹量,并补偿模具尺寸以得到尺寸和形状精度良好的冲压件。
该技术使试模时间大大缩短,从而减少制模成本。
六、疲劳分析传统的疲劳技术由许多经验公式组成。
这些经验公式根据一些理论框架,从材料、零件或结构的疲劳试验数据中拟合而成。
验证产品的疲劳性能一般需要进行疲劳试验。
疲劳分析依赖于准确的试验数据,同时也需要得到试验验证。
过去,常规设计定型样机疲劳试验需要几年甚至更多时间来发现设计失误、修改设计。
现代疲劳寿命设计技术是以电子技术(数字信息)和计算机技术(数字仿真)结合进入机械设计领域,将机械强度寿命由定性设计提高到定量设计。
它立足于随机、动态,整个受载过程的每一实时信号都参与设计,而不仅仅是一个最大值。
现代疲劳试验技术只需在计算机上用仿真技术,用载荷谱模拟和加载,预测寿命和反馈优化。
这可把试验时间压缩到原来的十分之一、百分之一,大大降低了开发成本,缩短了开发周期。
根据疲劳理论,疲劳破坏主要由循环载荷引起。
从理论上说,如果汽车的输入载荷相同,那么所引起的疲劳破坏也应该一样。
因此,可以在试车场上按一定的比例混合各种路面及各种事件(如开门、关门、刹车等),重现这一载荷输入。
这一载荷重现通常可能在较短的时间里完成,因此,可以达到试验加速的目的。
七、空气动力学分析汽车空气动力学主要是应用流体力学的知识,研究汽车行驶时,即与空气产生相对运动时,汽车周围的空气流动情况和空气对汽车的作用力(称为空气动力),以及汽车的各种外部形状对空气流动和空气动力的影响。
此外,空气对汽车的作用还表现在汽车发动机的冷却、车厢里的通风换气、车身外表面的清洁、气流噪声、车身表面覆盖件的振动、甚至刮水器的性能等方面的影响。
为了减少空气阻力系数,现代轿车的外形一般用园滑流畅的曲线去消隐车身上的转折线。
前围与侧围、前围、侧围与发动机罩,后围与侧围等地方均采用园滑过渡,发动机罩向前下倾,车尾后箱盖短而高翘,后冀子板向后收缩,挡风玻璃采用大曲面玻璃,且与车顶园滑过渡,前风窗与水平面的夹角一般在25度-33度之间,侧窗与车身相平,前后灯具、门手把嵌入车体内,车身表面尽量光洁平滑,车底用平整的盖板盖住,降低整车高度等等,这些措施有助于减少空气阻力系数。
八、虚拟试车场整车分析CAE技术的飞速发展、软硬件功能的大幅度提高使得整车系统仿真已经成为可能。
美国工程技术合作公司(ETA)在ANSYS/LS-DYAN软件平台上二次开发推出的虚拟试验场技术(virtual proving ground, VPG)就是一个对整车系统性能全面仿真实用软件的代表。
VPG技术是汽车CAE 技术领域中一个很有代表性的进展。
VPG是在NASYS/LS-DYAN软件平台上二次开发推出的,以整车系统为分析对象,考虑系统各类非线性,以标准路面和车速为负荷,对整车系统同时进行结构疲劳、权频率振动噪声分析和数据处理、以及碰撞历程仿真,达到在产品设计前期即可得到样车道路实验结果的“整车性能预测”效果的计算机仿真技术。
九、焊装模拟分析机器人在车身焊装工位上的大量应用提高了车身的焊接质量,缩短了生产加工时间。
但如何能够快速而准确地完成全部焊点的加工,即如何规划机器人焊接路径问题,是目前汽车制造企业迫切需要解决的问题。
传统的机器人焊接路径规划方法是根据设计人员提供的工位上的焊点数量和焊接顺序,由工艺人员根据经验或类似工艺离线编制机器人加工程序,设计加工工艺。
所编写的程序输入到相应设备中,在实验室里预操作,记录下每次偏差位置,重新编程、设计直至满足生产要求。
这不仅耗时、费力,同时对于多机器人加工的碰撞问题无法解决。
一旦涉及多机器人协同加工,则往往在实验室中采用步进式逼近方法配合专家经验加以解决,以免发生碰撞,损坏设备。
为此,现代车身焊装模拟分析结合虚拟制造技术,在仿真环境下,运用相应的优化算法对车身焊装工位的机器人加工路径进行离线规划,并通过仿真加工进行验证,从而达到指导实际生产的目的。
虚拟制造的基础是采用计算机支持的技术,应用数字建模和仿真技术、虚拟现实技术等来模拟生产、加工和装配等过程,在计算机上将产品“制造”出来,实现将工艺过程转为数字化操作,再由数字化操作指导实际生产。
通过建立生产加工的仿真模型研究制造活动,使用户在设计阶段能够了解产品未来制造过程,实现对生产系统性能有效的预测与评价。
在仿真环境下的试运行,有利于进行多工艺方案比较,更有利于多机器人焊接轨迹的选取与优化。