芳构化反应系统工艺流程
芳构化装置工艺介绍

芳构化装置一、装置简介芳构化装置,主要原料混合碳四液化气,产品有轻芳烃、重芳烃,民用液化气等。
原料混合碳四液化气,通过原料加热炉加热后,在反应器内与催化剂接触,经过低聚、环化,脱氢芳构化反应生成粗芳烃混合物,经过吸收稳定系统分离成合格的民用液化气和混合芳烃,再通过分馏分离成轻芳和碳9以上重芳烃。
装置区共有油、气罐16台,水储罐2台,其中地下密闭排放罐1台,机泵20台套。
为了防止污染环境和对操作人员造成损害,装置区所有排放的有机液体均排往密闭排放罐,然后根据情况再进行处理和排放。
二、工艺原理反应部分:轻烃芳构化的机理十分复杂。
一般认为,轻烃在分子筛的酸中心上芳构化反应时经历下列步骤:a)通过在酸中心上发生化学吸附生成正碳离子得到活化;b)正碳离子进一步脱氢和裂解生成乙烯、丙烯、丁烯和戊烯。
这些小烯烃是芳烃分子的建筑单元。
这步反应属于吸热反应;c)小烯烃分子在B酸中心上低聚(二聚、三聚)生成C6-C8烯烃,后者再通过异构化和环化生成芳烃前体(带6元环的前体)。
这步反应属于强放热反应;d)芳烃前体在L酸中心上通过脱氢生成苯、甲苯和C8芳烃等。
这步反应属于吸热反应。
在上述反应中,原料在酸中心上生成正碳离子的步骤最为关键。
它决定了芳构化反应的活性和选择性。
C3-C8之间的轻烃分子都可以在催化剂的酸中心上通过脱氢和裂解生成乙烯、丙烯、丁烯和戊烯。
当反应温度和催化剂的酸度相同时,从不同碳数的轻烃原料出发,可以得到具有同样热力学平衡分布的乙烯、丙烯、丁烯和戊烯。
由于基本建筑单元的种类和浓度分布相近,所以从不同碳数的轻烃原料出发都可以得到苯、甲苯和C8芳烃等产物,并且原料对芳烃产物的分布影响不大。
但是,若两种芳构化原料的碳数不同(如C3、C4、C5、C6、C7、C8)、结构不同(如直链烃、支链烃和环烷烃)和碳-碳键饱和程度不同(如烷烃、单烯烃、二烯烃),则其芳构化的活性、热效应和芳烃产率会有一定差别。
一般来说,碳数越小的原料在酸中心上生成正碳离子越困难,其芳构化活性越低;在同碳数下,烯烃比烷烃更容易生成正碳离子,因而其活性较高;另外,异构烷烃因可以生成相对稳定的叔碳正碳离子,因此其芳构化活性高于正构烷烃。
芳构化停工步骤
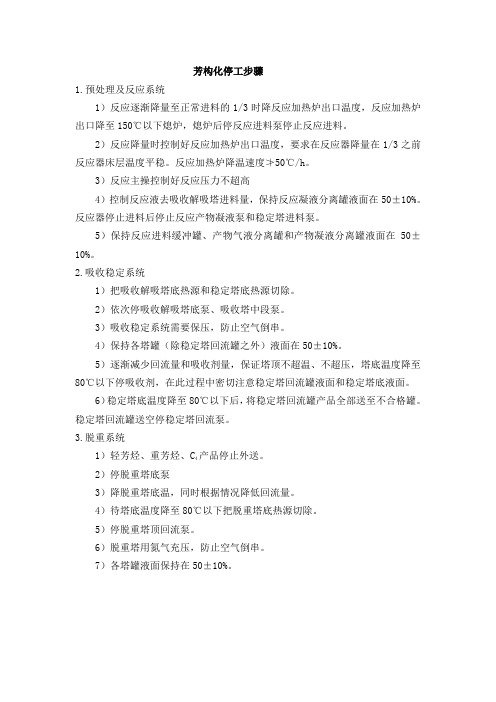
芳构化停工步骤
1.预处理及反应系统
1)反应逐渐降量至正常进料的1/3时降反应加热炉出口温度,反应加热炉出口降至150℃以下熄炉,熄炉后停反应进料泵停止反应进料。
2)反应降量时控制好反应加热炉出口温度,要求在反应器降量在1/3之前反应器床层温度平稳。
反应加热炉降温速度≯50℃/h。
3)反应主操控制好反应压力不超高
4)控制反应液去吸收解吸塔进料量,保持反应凝液分离罐液面在50±10%。
反应器停止进料后停止反应产物凝液泵和稳定塔进料泵。
5)保持反应进料缓冲罐、产物气液分离罐和产物凝液分离罐液面在50±10%。
2.吸收稳定系统
1)把吸收解吸塔底热源和稳定塔底热源切除。
2)依次停吸收解吸塔底泵、吸收塔中段泵。
3)吸收稳定系统需要保压,防止空气倒串。
4)保持各塔罐(除稳定塔回流罐之外)液面在50±10%。
5)逐渐减少回流量和吸收剂量,保证塔顶不超温、不超压,塔底温度降至80℃以下停吸收剂,在此过程中密切注意稳定塔回流罐液面和稳定塔底液面。
6)稳定塔底温度降至80℃以下后,将稳定塔回流罐产品全部送至不合格罐。
稳定塔回流罐送空停稳定塔回流泵。
3.脱重系统
产品停止外送。
1)轻芳烃、重芳烃、C
4
2)停脱重塔底泵
3)降脱重塔底温,同时根据情况降低回流量。
4)待塔底温度降至80℃以下把脱重塔底热源切除。
5)停脱重塔顶回流泵。
6)脱重塔用氮气充压,防止空气倒串。
7)各塔罐液面保持在50±10%。
bergman芳构化反应 -回复
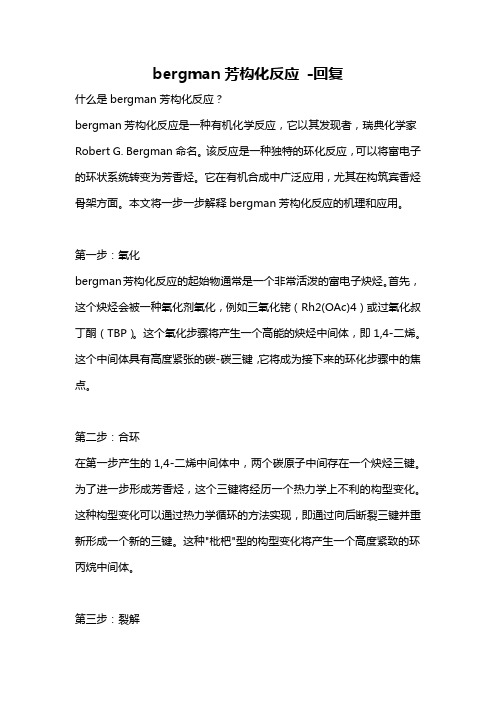
bergman芳构化反应-回复什么是bergman芳构化反应?bergman芳构化反应是一种有机化学反应,它以其发现者,瑞典化学家Robert G. Bergman命名。
该反应是一种独特的环化反应,可以将富电子的环状系统转变为芳香烃。
它在有机合成中广泛应用,尤其在构筑宾香烃骨架方面。
本文将一步一步解释bergman芳构化反应的机理和应用。
第一步:氧化bergman芳构化反应的起始物通常是一个非常活泼的富电子炔烃。
首先,这个炔烃会被一种氧化剂氧化,例如三氧化铑(Rh2(OAc)4)或过氧化叔丁酮(TBP)。
这个氧化步骤将产生一个高能的炔烃中间体,即1,4-二烯。
这个中间体具有高度紧张的碳-碳三键,它将成为接下来的环化步骤中的焦点。
第二步:合环在第一步产生的1,4-二烯中间体中,两个碳原子中间存在一个炔烃三键。
为了进一步形成芳香烃,这个三键将经历一个热力学上不利的构型变化。
这种构型变化可以通过热力学循环的方法实现,即通过向后断裂三键并重新形成一个新的三键。
这种"枇杷"型的构型变化将产生一个高度紧致的环丙烷中间体。
第三步:裂解在合环步骤之后,环丙烷中间体需要进一步转化为芳香烃。
为了实现这一目标,环丙烷中间体将经历一次热裂解。
这个裂解过程会打破环丙烷,并重新组装为一个具有新的碳-碳三键的芳香烃。
这个芳香烃化合物是bergman芳构化反应的最终产物。
第四步:产物稳定性得到的芳香烃产物具有高度稳定的芳香性,因为它的热力学和动力学稳定性都比原先的炔烃更高。
这是因为芳香化合物中的π电子被循环共轭的碳骨架捕获,并以更低的能级稳定下来。
而在炔烃中,这些π电子位于双键中,容易与氧化剂发生反应。
bergman芳构化反应的应用bergman芳构化反应非常灵活,可用于构建复杂的有机分子。
由于芳香烃在生物活性分子中的广泛存在,因此bergman芳构化反应在药物和天然产物研究领域得到了广泛的应用。
这个反应可以用于修饰天然产物,合成有生物活性的小分子工具,以及开发新的药物治疗策略。
bergman芳构化反应 -回复
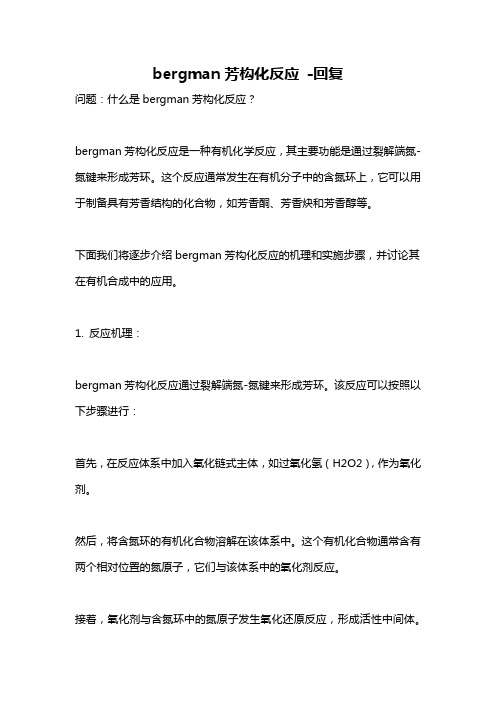
bergman芳构化反应-回复问题:什么是bergman芳构化反应?bergman芳构化反应是一种有机化学反应,其主要功能是通过裂解端氮-氮键来形成芳环。
这个反应通常发生在有机分子中的含氮环上,它可以用于制备具有芳香结构的化合物,如芳香酮、芳香炔和芳香醇等。
下面我们将逐步介绍bergman芳构化反应的机理和实施步骤,并讨论其在有机合成中的应用。
1. 反应机理:bergman芳构化反应通过裂解端氮-氮键来形成芳环。
该反应可以按照以下步骤进行:首先,在反应体系中加入氧化链式主体,如过氧化氢(H2O2),作为氧化剂。
然后,将含氮环的有机化合物溶解在该体系中。
这个有机化合物通常含有两个相对位置的氮原子,它们与该体系中的氧化剂反应。
接着,氧化剂与含氮环中的氮原子发生氧化还原反应,形成活性中间体。
最后,该中间体发生分子内反应,裂解端氮-氮键并形成芳环。
2. 实施步骤:bergman芳构化反应的实施步骤如下:首先,准备含氮环的有机化合物。
这些化合物可以通过合成化学方法或从天然产物中分离获得。
然后,在反应体系中加入氧化剂,如H2O2。
该氧化剂的浓度和用量应根据具体实验要求进行调整。
接下来,将含氮环的有机化合物溶解在该体系中,并进行反应。
反应的时间和反应温度也是关键因素,需要根据具体实验条件进行优化。
随后,使用合适的方法对反应产物进行分离和纯化。
这可以包括柱层析、液液萃取、结晶等技术。
最后,在实验过程中收集和分析所得产物,使用各种分析技术(如核磁共振、质谱等)来验证其结构和纯度。
3. 应用:bergman芳构化反应在有机合成中具有广泛的应用。
其应用领域包括药物合成、天然产物合成和材料科学等。
例如,该反应可用于合成具有独特芳香性质的化合物,如芳香酮、芳香炔和芳香醇等。
此外,bergman芳构化反应还可以用于制备具有特定结构的材料,如功能高分子和石墨炔等。
总之,bergman芳构化反应是一种重要的有机合成方法,其通过裂解端氮-氮键来形成芳环。
芳构化的系统升温和调整操作

芳构化的系统升温和调整操作1)反应系统a 在醚后液化气和石脑油进入反应器之后,逐渐调整F201炉出口温度从150℃至200℃之间,观察有无温升发生,如果没有温升,则继续升温直至有温升,反应被引发。
注意观察反应器R201床层各点温度变化情况,当温升逐渐变小时,说明反应减弱,则继续提高炉出口温度,让R201温度达到300℃以上。
继续观察R201床层温度分布。
当R201上部温度达到350℃时,小量给反应中间进料,观察R201床层温度分布。
须知在反应中间进料开始进入反应器时,各换热器还没有热源,反应中间进料的温度很低而且呈液态,故在开始给反应中间进料时,要控制小流量,以防反应被“扑灭”。
当反应逐渐正常,反应器温度控制在300-350℃。
在此过程中须时刻注意反应进料量和反应中间进料量的调节,使反应器床层温度达到平衡。
b 观察反应产物凝液分离罐V204液位,当其达到预先设定的控制范围时,即开启去吸收解吸塔T201的反应液泵P204,并建立反应产物凝液分离罐V204液位自动控制。
2) 吸收稳定系统a 观察吸收解吸塔T201底液位和温度,当其达到预先设定的控制范围时,即开启去稳定塔T202的吸收解吸塔底泵P205和稳定塔进料泵P203,并建立T201底液位和产物气液分离罐V203液位自动控制。
b 观察稳定塔T202底液位和温度,当其达到预先设定的控制范围时,即开启去吸收解吸塔T201顶的吸收剂泵P207,并按要求实施吸收剂流量的自动控制。
随后开启P206吸收解吸塔中段循环泵,同时开启塔T202底去脱重塔T203的调节阀,并实施T202底液位自动控制。
c 按工艺要求建立稳定塔T202顶压力控制。
观察稳定塔回流罐V205液位,当其达到预先设定的控制范围时,即开启稳定塔顶回流泵P208,并建立稳定塔顶温度自动控制。
同时建立稳定塔回流罐V205液位自动控制,将稳定塔顶产物由稳定塔回流罐V205经稳定塔顶回流泵P208一部分送去V-212,一部分作为稳定塔回流,另一部分去反应。
液化气芳构化
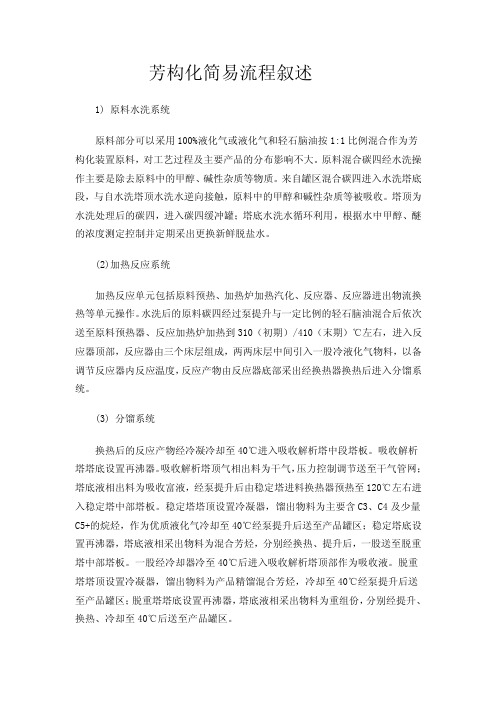
芳构化简易流程叙述1) 原料水洗系统原料部分可以采用100%液化气或液化气和轻石脑油按1:1比例混合作为芳构化装置原料,对工艺过程及主要产品的分布影响不大。
原料混合碳四经水洗操作主要是除去原料中的甲醇、碱性杂质等物质。
来自罐区混合碳四进入水洗塔底段,与自水洗塔顶水洗水逆向接触,原料中的甲醇和碱性杂质等被吸收。
塔顶为水洗处理后的碳四,进入碳四缓冲罐;塔底水洗水循环利用,根据水中甲醇、醚的浓度测定控制并定期采出更换新鲜脱盐水。
(2)加热反应系统加热反应单元包括原料预热、加热炉加热汽化、反应器、反应器进出物流换热等单元操作。
水洗后的原料碳四经过泵提升与一定比例的轻石脑油混合后依次送至原料预热器、反应加热炉加热到310(初期)/410(末期)℃左右,进入反应器顶部,反应器由三个床层组成,两两床层中间引入一股冷液化气物料,以备调节反应器内反应温度,反应产物由反应器底部采出经换热器换热后进入分馏系统。
(3) 分馏系统换热后的反应产物经冷凝冷却至40℃进入吸收解析塔中段塔板。
吸收解析塔塔底设置再沸器。
吸收解析塔顶气相出料为干气,压力控制调节送至干气管网;塔底液相出料为吸收富液,经泵提升后由稳定塔进料换热器预热至120℃左右进入稳定塔中部塔板。
稳定塔塔顶设置冷凝器,馏出物料为主要含C3、C4及少量C5+的烷烃,作为优质液化气冷却至40℃经泵提升后送至产品罐区;稳定塔底设置再沸器,塔底液相采出物料为混合芳烃,分别经换热、提升后,一股送至脱重塔中部塔板。
一股经冷却器冷至40℃后进入吸收解析塔顶部作为吸收液。
脱重塔塔顶设置冷凝器,馏出物料为产品精馏混合芳烃,冷却至40℃经泵提升后送至产品罐区;脱重塔塔底设置再沸器,塔底液相采出物料为重组份,分别经提升、换热、冷却至40℃后送至产品罐区。
(4) 再生系统反应进行一段时间后,随着反应器中催化剂表面结焦量的增加,催化剂表面活性降低,当检测到产品质量不能满足要求时,需将反应器切换出反应系统进行催化剂烧焦再生处理。
芳构化技术、工艺情况说明
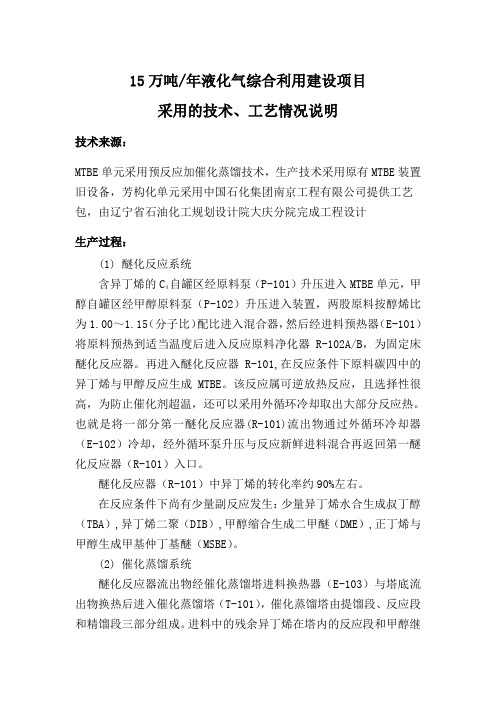
15万吨/年液化气综合利用建设项目采用的技术、工艺情况说明技术来源:MTBE单元采用预反应加催化蒸馏技术,生产技术采用原有MTBE装置旧设备,芳构化单元采用中国石化集团南京工程有限公司提供工艺包,由辽宁省石油化工规划设计院大庆分院完成工程设计生产过程:(1) 醚化反应系统含异丁烯的C4自罐区经原料泵(P-101)升压进入MTBE单元,甲醇自罐区经甲醇原料泵(P-102)升压进入装置,两股原料按醇烯比为1.00~1.15(分子比)配比进入混合器,然后经进料预热器(E-101)将原料预热到适当温度后进入反应原料净化器R-102A/B,为固定床醚化反应器。
再进入醚化反应器R-101,在反应条件下原料碳四中的异丁烯与甲醇反应生成MTBE。
该反应属可逆放热反应,且选择性很高,为防止催化剂超温,还可以采用外循环冷却取出大部分反应热。
也就是将一部分第一醚化反应器(R-101)流出物通过外循环冷却器(E-102)冷却,经外循环泵升压与反应新鲜进料混合再返回第一醚化反应器(R-101)入口。
醚化反应器(R-101)中异丁烯的转化率约90%左右。
在反应条件下尚有少量副反应发生:少量异丁烯水合生成叔丁醇(TBA),异丁烯二聚(DIB),甲醇缩合生成二甲醚(DME),正丁烯与甲醇生成甲基仲丁基醚(MSBE)。
(2) 催化蒸馏系统醚化反应器流出物经催化蒸馏塔进料换热器(E-103)与塔底流出物换热后进入催化蒸馏塔(T-101),催化蒸馏塔由提馏段、反应段和精馏段三部分组成。
进料中的残余异丁烯在塔内的反应段和甲醇继续反应,生成的MTBE随时分离,为保持深度转化需不断往反应段内注入净化甲醇,从而使合成MTBE的反应持续进行,可达到异丁烯的深度转化(≥95%)。
催化蒸馏塔具有产品分离的作用,甲醇和剩余C4所形成的低沸点共沸物从塔顶馏出,馏出物经催化蒸馏塔顶冷凝器(E-104)冷凝后进入催化蒸馏塔回流罐(V-103),凝液经催化蒸馏塔回流泵(P-104)一部分作塔的回流打入塔顶,另一部分经冷却后作为甲醇萃取塔(T-102)进料。
bergman芳构化反应

bergman芳构化反应Bergman芳构化反应是一种重要的有机化学反应,它是指在特定的反应条件下,芳香化合物中的酰胺键(C=O)被断裂,生成两个芳香环的反应。
以下是从多个角度全面完整回答关于Bergman芳构化反应的问题。
1. 反应机理:Bergman芳构化反应的机理涉及到一个中间体,即环丁炔酮。
首先,芳香化合物中的酰胺键被加热或通过光照等外部激发条件断裂,生成环丁炔酮。
然后,环丁炔酮通过一个类似于Diels-Alder 反应的过程,发生一个[2+2]环加成反应,生成两个新的芳香环。
最后,环丁炔酮经历一个脱氢步骤,形成两个芳香环。
2. 反应条件:Bergman芳构化反应通常在高温下进行,一般在200-300摄氏度范围内。
此外,还需要一些外部激发条件,如光照或者加热等,以促进酰胺键的断裂。
3. 反应适用性:Bergman芳构化反应适用于具有合适的结构和功能团的芳香化合物。
常见的反应底物包括芳香酮、芳香酰胺和芳香酸等。
此外,反应的产物通常是两个芳香环,具有较高的环境稳定性和生物活性。
4. 反应应用:Bergman芳构化反应在有机合成中具有广泛的应用。
它可以用于合成具有特定结构和功能的化合物,如天然产物、药物分子和材料科学中的有机材料等。
此外,该反应还可以用于构建具有特定的空间构型和立体化学活性的化合物。
5. 反应优势和局限性:Bergman芳构化反应具有高效、高选择性和原子经济性等优势。
它可以在温和的条件下实现复杂分子的构建。
然而,该反应也存在一些局限性,如需要较高的温度和特定的反应条件,以及对底物结构的一定限制等。
总结起来,Bergman芳构化反应是一种重要的有机化学反应,通过断裂酰胺键和环加成反应的过程,可以合成具有两个芳香环的化合物。
它在有机合成中具有广泛的应用前景,但也需要考虑其反应条件和适用性的限制。
2万吨甲醇芳构化工段工艺设计

2万吨甲醇芳构化工段工艺设计2万吨甲醇芳构化工段工艺设计一、工艺概述甲醇芳构化是将甲醇与催化剂反应,生成苯、二甲苯等芳香烃的过程。
本工艺设计旨在实现每年产出2万吨的芳香烃产品。
主要包括原料处理、反应系统、分离系统和产品处理四个部分。
二、原料处理1. 甲醇净化从甲醇储罐中取出的甲醇经过净化处理,包括脱水、脱硫和脱氯等步骤,以提高反应的纯度和催化剂的稳定性。
2. 催化剂制备选择合适的催化剂制备方法,如浸渍法或沉淀法,将活性组分与载体混合,并进行干燥和活化处理,以获得高效的催化剂。
三、反应系统1. 反应器选择选择适合芳构化反应的反应器,常用的有固定床反应器和流动床反应器。
根据产能要求和经济性考虑,确定合适尺寸和数量。
2. 反应条件控制控制反应温度、压力和催化剂的投料速率,以实现高效的反应转化率和选择性。
通常反应温度为350-450℃,压力为0.1-0.5MPa。
3. 反应过程控制建立稳定可靠的自动控制系统,监测和调节反应温度、压力和催化剂投料速率等参数,以确保反应过程的安全性和稳定性。
四、分离系统1. 气体分离将反应器出口气体经过冷却、减压、冷凝等步骤进行分离,得到芳香烃气体产品。
其中包括苯、二甲苯等组分。
2. 液体分离将反应器出口液体经过冷却、闪蒸等步骤进行分离,得到芳香烃液体产品。
其中包括苯、二甲苯等组分。
五、产品处理1. 产品储存将芳香烃气体和液体产品分别储存在相应的储罐中,并对储罐进行密封和防爆处理,确保产品质量和安全。
2. 产品检测与质量控制对芳香烃产品进行物理性质、化学成分和杂质含量等方面的检测,以确保产品达到相关标准要求。
3. 产品包装与出库将芳香烃产品按照规定的包装要求进行包装,并进行记录和标识,以便于出库和销售。
六、安全环保措施1. 设立安全阀、压力传感器等安全设备,确保反应系统的安全运行。
2. 定期对催化剂进行检测和更换,以维持反应的高效性和稳定性。
3. 对废气进行处理,采用吸附剂或催化剂等方法进行净化,以减少对环境的污染。
轻烃芳构化生产芳烃

6
纯利润
2043.15
六、结论
1、轻烃经改质后,改质后液体收率为51%,液 化气产率为30%。 2、轻烃经改质后,芳烃中三苯含量大于95%。 3 、芳构化改质装置总投资约为 4050 万元,每 年可实现利税1413.01万元,每年可实现利润约 2043.15万元。
换 热 器 稳 定 塔
稳定塔 回流罐
芳构化汽油
图2吸收稳定系统
非芳 产品 排气 抽 提 塔 进 料 缓 冲 罐 水 过 滤 器 真空 系统 非芳 水洗 塔 抽 提 产 抽提 品 中间 罐
汽 提 塔
回 收 塔
溶剂再生 再沸器
水汽提
图3芳烃抽提系统
蒸汽发 生器
蒸汽
甲苯 拔顶苯 苯 混合芳烃 二甲苯
脱氧水
4934.22
3904.62 1029.6 369.72 ――
3 4 5
增值税 消费税 城建及教 育附加 10% 369.72
36.97
税金合计
406.69
表7芳构化改质损益计算
序号 项目 金额(万元)
1
2
销售收入
流转税及附加
30888.36
406.69
3
4 5
总成本
销售利润 所得税
27432.2
表6芳构化装置流转税及附加计算
序号 1 项目 进项税 原料 催化剂 修理费 17% 17% 17% 17% 13% 税率 金额(万元) 26828 26400 288 162 税额(万元) 4564.50 4488.00 48.96 27.54
2
销项税
芳烃 液化气
30888.36
22968.36 7920
十万吨芳构化操作规程

目录十万吨操作规程 (2)1 概述 (2)1.1原料规格 (2)1.2催化剂组分及性质 (2)1.3反应条件及反应结果 (2)2 分析项目及方法 (2)3正常开工和停工 (3)3.1.工艺过程描述及操作条件 (3)3.2开工方案及步骤 (4)3.3长时间停工步骤 (6)3.4短暂停工步骤 (7)4 事故处理 (7)4.1事故处理原则 (7)4.2紧急停工 (7)4.3反应器温度迅速上升、出现飞温现象 (8)4.4停循环水 (8)4.5短暂(晃电)停电 (8)4.6停净化风 (9)4.7燃气不足或燃气中断 (9)5附:工艺流程图 (9)十万吨操作规程1 概述本次开工是用装有南通扬子催化剂有限公司催化剂的大反应器进行轻油芳构化,进料量最大10t/h轻油及3t/h液化气。
1.1原料规格山东仕通芳构化原料为外购轻油跟内部油,内部油先切除轻、重组分,保留C6~C9馏程段组分作为芳构化原料。
外采轻油指标如下表表1-1 原料要求备注:建议采购饱和烃含量高的轻油。
1.2催化剂组分及性质表1-2 催化剂物化性质1.3反应条件及反应结果1.3.1反应条件表1-3 反应条件表2 分析项目及方法表2-1 分析项目及频次3正常开工和停工3.1.工艺过程描述及操作条件3.1.1工艺过程描述本装置由反应系统、稳定系统和分馏系统组成。
原料轻油通过原料罐,由泵送出,经换热器E601A/B、E602、E603 A/B、E611(导热油预热)、E604换热后去加热炉F601加热至所需的反应温度,然后送入反应器R602顶部进料。
由R602出来的反应产物温度较高,先送到分馏塔作为塔底再沸器E608热源,跨过E606再去E604作为原料的最后一段换热,从E604出来的反应产物经E603A/B进一步换热后,经稳定塔进料水冷换热器E610去稳定塔T-601作为该塔进料。
稳定塔顶产物为液化气和少量不凝气,经换热器E601A/B与原料液化气换热,再进入冷却器E605A/B、E612A/B冷凝冷却,然后进入V601进行气液分离,液化气经P-602泵一部分作为T-601回流,另一部分作为产品液化气出装置进入罐区。
醋酸芳构化

醋酸芳构化醋酸芳构化是一种有机化学反应,通过该反应可以将醋酸酯转化为芳香醇或芳香酮。
在此过程中,醋酸酯分子中的酯基被取代,形成具有芳香性质的化合物。
这种反应在有机合成中具有广泛的应用。
在醋酸芳构化反应中,通常使用碱性条件下的催化剂。
常见的催化剂包括碱金属如钠、钾或碱土金属如钙、镁等。
此外,还可以使用碱性溶剂如氢氧化钠或碳酸钠来促进反应的进行。
反应过程中,醋酸酯首先与碱性溶剂中的氢氧根离子发生酰氧根亲核取代反应,生成相应的酰氧根盐。
然后,酰氧根盐再与醋酸酯分子内的羟基发生亲核取代反应,形成中间产物。
最后,中间产物经过脱水作用,生成芳香醇或芳香酮。
醋酸芳构化反应的机理可以分为两步。
首先是酰氧根亲核取代反应,该反应是一个速率决定步骤。
酰氧根离子与醋酸酯发生亲核取代反应,形成酰氧根盐。
然后,酰氧根盐与醋酸酯分子内的羟基发生亲核取代反应,生成中间产物。
中间产物经过脱水反应,生成芳香醇或芳香酮。
醋酸芳构化反应具有以下几个特点。
首先,该反应可以在温和的条件下进行,不需要高温或高压。
其次,反应底物种类丰富,可以适用于不同结构的醋酸酯。
此外,该反应产率较高,且容易控制反应条件,具有较好的可重复性。
醋酸芳构化反应在有机合成中有广泛的应用。
一方面,该反应可以用于合成具有芳香性质的化合物,如香精、香料等。
另一方面,该反应还可以用于合成药物、染料等有机化合物。
总结起来,醋酸芳构化是一种重要的有机化学反应,通过该反应可以将醋酸酯转化为芳香醇或芳香酮。
该反应在有机合成中具有广泛的应用,可以合成具有芳香性质的化合物。
醋酸芳构化反应的机理包括酰氧根亲核取代反应和脱水反应。
该反应具有温和的条件、丰富的底物种类和较高的产率等特点。
通过合理控制反应条件,可以实现对目标化合物的选择性合成。
芳构化反应系统工艺流程
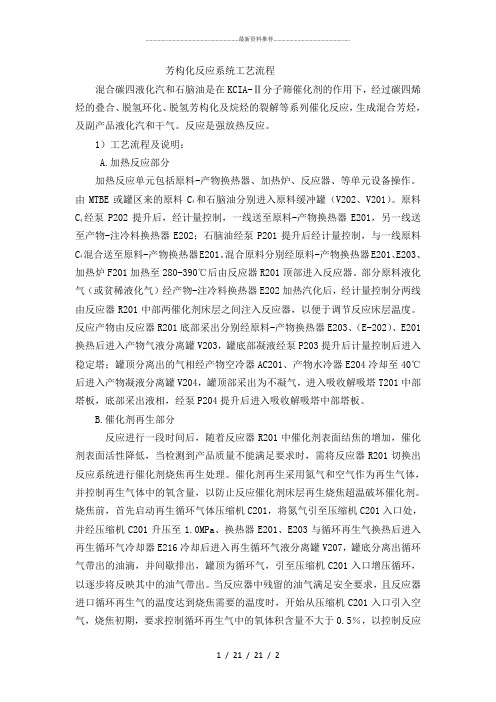
芳构化反应系统工艺流程混合碳四液化汽和石脑油是在KCIA-Ⅱ分子筛催化剂的作用下,经过碳四烯烃的叠合、脱氢环化、脱氢芳构化及烷烃的裂解等系列催化反应,生成混合芳烃,及副产品液化汽和干气。
反应是强放热反应。
1)工艺流程及说明:A.加热反应部分加热反应单元包括原料-产物换热器、加热炉、反应器、等单元设备操作。
和石脑油分别进入原料缓冲罐(V202、V201)。
原料由MTBE或罐区来的原料C4C经泵P202提升后,经计量控制,一线送至原料-产物换热器E201,另一线送4至产物-注冷料换热器E202;石脑油经泵P201提升后经计量控制,与一线原料C混合送至原料-产物换热器E201。
混合原料分别经原料-产物换热器E201、E203、4加热炉F201加热至280-390℃后由反应器R201顶部进入反应器。
部分原料液化气(或贫稀液化气)经产物-注冷料换热器E202加热汽化后,经计量控制分两线由反应器R201中部两催化剂床层之间注入反应器,以便于调节反应床层温度。
反应产物由反应器R201底部采出分别经原料-产物换热器E203、(E-202)、E201换热后进入产物气液分离罐V203,罐底部凝液经泵P203提升后计量控制后进入稳定塔;罐顶分离出的气相经产物空冷器AC201、产物水冷器E204冷却至40℃后进入产物凝液分离罐V204,罐顶部采出为不凝气,进入吸收解吸塔T201中部塔板,底部采出液相,经泵P204提升后进入吸收解吸塔中部塔板。
B.催化剂再生部分反应进行一段时间后,随着反应器R201中催化剂表面结焦的增加,催化剂表面活性降低,当检测到产品质量不能满足要求时,需将反应器R201切换出反应系统进行催化剂烧焦再生处理。
催化剂再生采用氮气和空气作为再生气体,并控制再生气体中的氧含量,以防止反应催化剂床层再生烧焦超温破坏催化剂。
烧焦前,首先启动再生循环气体压缩机C201,将氮气引至压缩机C201入口处,并经压缩机C201升压至1.0MPa、换热器E201、E203与循环再生气换热后进入再生循环气冷却器E216冷却后进入再生循环气液分离罐V207,罐底分离出循环气带出的油滴,并间歇排出,罐顶为循环气,引至压缩机C201入口增压循环,以逐步将反映其中的油气带出。
芳构化
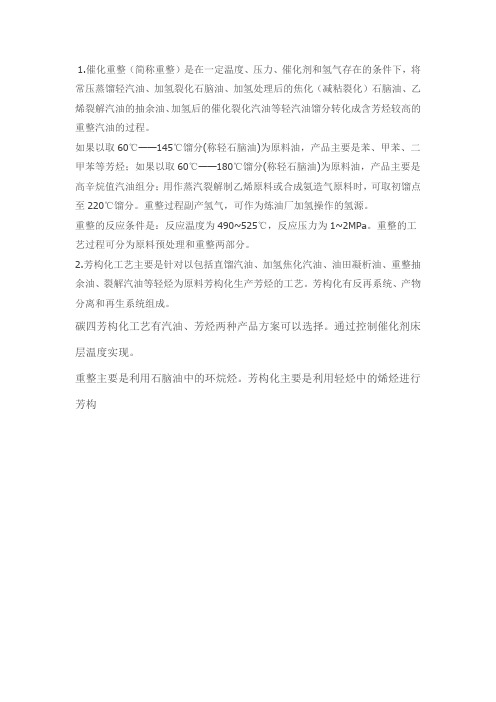
1.催化重整(简称重整)是在一定温度、压力、催化剂和氢气存在的条件下,将常压蒸馏轻汽油、加氢裂化石脑油、加氢处理后的焦化(减粘裂化)石脑油、乙烯裂解汽油的抽余油、加氢后的催化裂化汽油等轻汽油馏分转化成含芳烃较高的重整汽油的过程。
如果以取60℃——145℃馏分(称轻石脑油)为原料油,产品主要是苯、甲苯、二甲苯等芳烃;如果以取60℃——180℃馏分(称轻石脑油)为原料油,产品主要是高辛烷值汽油组分;用作蒸汽裂解制乙烯原料或合成氨造气原料时,可取初馏点至220℃馏分。
重整过程副产氢气,可作为炼油厂加氢操作的氢源。
重整的反应条件是:反应温度为490~525℃,反应压力为1~2MPa。
重整的工艺过程可分为原料预处理和重整两部分。
2.芳构化工艺主要是针对以包括直馏汽油、加氢焦化汽油、油田凝析油、重整抽余油、裂解汽油等轻烃为原料芳构化生产芳烃的工艺。
芳构化有反再系统、产物分离和再生系统组成。
碳四芳构化工艺有汽油、芳烃两种产品方案可以选择。
通过控制催化剂床层温度实现。
重整主要是利用石脑油中的环烷烃。
芳构化主要是利用轻烃中的烯烃进行芳构。
芳构化操作规程(终结版)
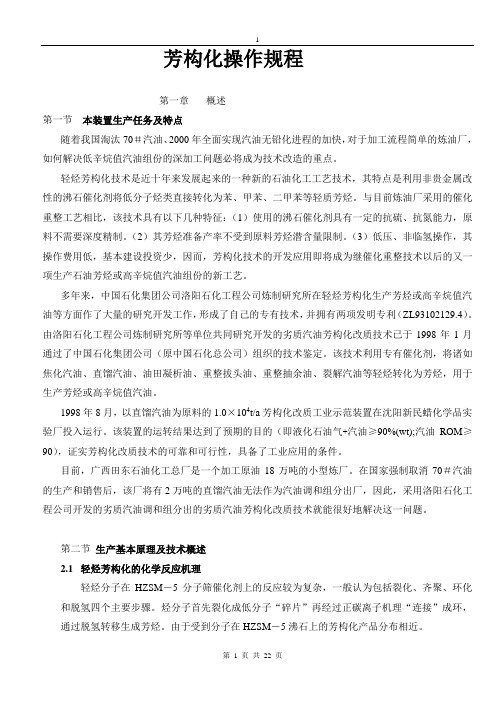
芳构化操作规程第一章概述第一节本装置生产任务及特点随着我国淘汰70#汽油、2000年全面实现汽油无铅化进程的加快,对于加工流程简单的炼油厂,如何解决低辛烷值汽油组份的深加工问题必将成为技术改造的重点。
轻烃芳构化技术是近十年来发展起来的一种新的石油化工工艺技术,其特点是利用非贵金属改性的沸石催化剂将低分子烃类直接转化为苯、甲苯、二甲苯等轻质芳烃。
与目前炼油厂采用的催化重整工艺相比,该技术具有以下几种特征:(1)使用的沸石催化剂具有一定的抗硫、抗氮能力,原料不需要深度精制。
(2)其芳烃准备产率不受到原料芳烃潜含量限制。
(3)低压、非临氢操作,其操作费用低,基本建设投资少,因而,芳构化技术的开发应用即将成为继催化重整技术以后的又一项生产石油芳烃或高辛烷值汽油组份的新工艺。
多年来,中国石化集团公司洛阳石化工程公司炼制研究所在轻烃芳构化生产芳烃或高辛烷值汽油等方面作了大量的研究开发工作,形成了自己的专有技术,并拥有两项发明专利(ZL93102129.4)。
由洛阳石化工程公司炼制研究所等单位共同研究开发的劣质汽油芳构化改质技术已于1998年1月通过了中国石化集团公司(原中国石化总公司)组织的技术鉴定。
该技术利用专有催化剂,将诸如焦化汽油、直馏汽油、油田凝析油、重整拔头油、重整抽余油、裂解汽油等轻烃转化为芳烃,用于生产芳烃或高辛烷值汽油。
1998年8月,以直馏汽油为原料的1.0×104t/a芳构化改质工业示范装置在沈阳新民蜡化学品实验厂投入运行。
该装置的运转结果达到了预期的目的(即液化石油气+汽油≥90%(wt);汽油ROM≥90),证实芳构化改质技术的可靠和可行性,具备了工业应用的条件。
目前,广西田东石油化工总厂是一个加工原油18万吨的小型炼厂。
在国家强制取消70#汽油的生产和销售后,该厂将有2万吨的直馏汽油无法作为汽油调和组分出厂,因此,采用洛阳石化工程公司开发的劣质汽油调和组分出的劣质汽油芳构化改质技术就能很好地解决这一问题。
液化气芳构化简单原理
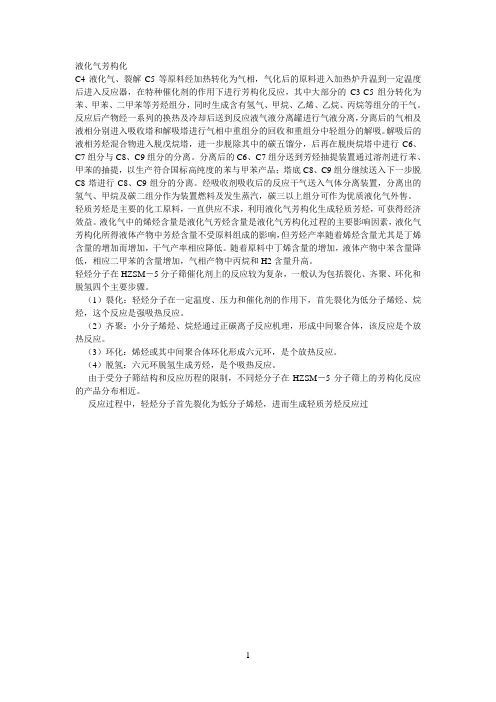
液化气芳构化C4液化气、裂解C5等原料经加热转化为气相,气化后的原料进入加热炉升温到一定温度后进入反应器,在特种催化剂的作用下进行芳构化反应,其中大部分的C3-C5组分转化为苯、甲苯、二甲苯等芳烃组分,同时生成含有氢气、甲烷、乙烯、乙烷、丙烷等组分的干气。
反应后产物经一系列的换热及冷却后送到反应液气液分离罐进行气液分离,分离后的气相及液相分别进入吸收塔和解吸塔进行气相中重组分的回收和重组分中轻组分的解吸。
解吸后的液相芳烃混合物进入脱戊烷塔,进一步脱除其中的碳五馏分,后再在脱庚烷塔中进行C6、C7组分与C8、C9组分的分离。
分离后的C6、C7组分送到芳烃抽提装置通过溶剂进行苯、甲苯的抽提,以生产符合国标高纯度的苯与甲苯产品;塔底C8、C9组分继续送入下一步脱C8塔进行C8、C9组分的分离。
经吸收剂吸收后的反应干气送入气体分离装置,分离出的氢气、甲烷及碳二组分作为装置燃料及发生蒸汽,碳三以上组分可作为优质液化气外售。
轻质芳烃是主要的化工原料,一直供应不求,利用液化气芳构化生成轻质芳烃,可获得经济效益。
液化气中的烯烃含量是液化气芳烃含量是液化气芳构化过程的主要影响因素,液化气芳构化所得液体产物中芳烃含量不受原料组成的影响,但芳烃产率随着烯烃含量尤其是丁烯含量的增加而增加,干气产率相应降低。
随着原料中丁烯含量的增加,液体产物中苯含量降低,相应二甲苯的含量增加,气相产物中丙烷和H2含量升高。
轻烃分子在HZSM-5分子筛催化剂上的反应较为复杂,一般认为包括裂化、齐聚、环化和脱氢四个主要步骤。
(1)裂化:轻烃分子在一定温度、压力和催化剂的作用下,首先裂化为低分子烯烃、烷烃,这个反应是强吸热反应。
(2)齐聚:小分子烯烃、烷烃通过正碳离子反应机理,形成中间聚合体,该反应是个放热反应。
(3)环化:烯烃或其中间聚合体环化形成六元环,是个放热反应。
(4)脱氢:六元环脱氢生成芳烃,是个吸热反应。
由于受分子筛结构和反应历程的限制,不同烃分子在HZSM-5分子筛上的芳构化反应的产品分布相近。
工艺知识芳构化
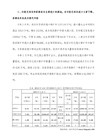
原料中的丁烯含量是液化气芳构化过程的主要影响因素,液化气芳构化所得液体产物中芳烃含量不受原料性质的影响,随着烯烃含量尤其是丁烯含量的增加芳烃产率增加,干气产率相应降低;原料中丁烯含量影响液体产物中苯和气相产物中丙烷和氢气含量。
3、反应温度
随着床层温度的升高,催化剂的活性略有提高,所以在后期不断的提高床层温度。最好的液收率温度为370-420℃;随温度的升高,结焦速度增快,易失活。
4、反应压力
压力越高,脱氢反应速率下降。
反应器:固定床 轴向反应器
在进行多相过程的设备中,若有固相参与,且处于静止状态时,则设备内的固体颗粒物料层,称为固定床。
7、 P301、P302外送合在一起;P303外送与P305合在一起,P304外送与P306合在一起
8、 仪表风分净化风与非净化风两条线,烧焦用非净化风
9、 V101加放空调节阀
10、 V106向V101压油流程
11、 脱色塔进料的分布器堵,改用脱己烷塔当脱色塔使用
液化气芳构化的理论知识:
球阀的公称压力等级(PN),可表明阀在正常温度状态下的最大工作压力。(例如:PN4.0,表明其操作温度在-290C~380C时的最大工作压力为4.0MPa)。
工业专用蝶阀的特点能耐高温,适用压力范围也较高,阀门公称通径大。
执行器按其能源形式分为气动,电动和液动三大类。气动执行器的执行机构有薄膜式、活塞式和齿轮齿条式。活塞式行程长,适用于要求有较大推力的场合,应用于大口径高压降蝶阀;而薄膜式行程较小,只能直接带动阀杆。
球阀特点是本身结构紧凑,密封可靠,结构简单,维修方便,密封面与球面常在闭合状态,不易被介质冲蚀,易于操作和维修,适用于水、溶剂、酸和天然气等一般工作介质,而且还适用于工作条件恶劣的介质,如氧气、过氧化氢、甲烷和乙烯等。球阀在启闭过程中有擦拭性,可用于带悬浮固体颗粒的介质中。
轻烃的芳构化工艺

轻烃的芳构化工艺
轻烃的芳构化工艺是一种将石油中的轻质烷烃转化为芳香烃的过程。
芳构化是一种重要的石油化工反应,可以用于生产苯、甲苯、二甲苯等有机化合物。
常见的轻烃芳构化工艺包括:
1. 热裂解芳构化工艺:在高温下,将烷烃通过裂解反应生成反应物,然后通过催化芳烃生成反应得到芳香烃。
该工艺常用的催化剂有分子筛、磷酸等。
2. 溶剂法芳构化工艺:在选择性溶剂的作用下,利用溶剂促进催化剂对烷烃的活化,产生芳香烃。
该工艺常用的溶剂有苯、甲苯等。
3. 催化重整芳构化工艺:在催化剂的作用下,通过氧化重整反应将烷烃转化为苯和甲苯。
该工艺常用的催化剂有铂、钼等。
这些芳构化工艺需要适当的反应温度和催化剂,以及控制反应的压力、物料的进料速度等因素,以提高反应的转化率和选择性。
芳构化是一种重要的石油化工反应,可以应用于石油精炼和化工工业中,产生各种有机化合物。
- 1、下载文档前请自行甄别文档内容的完整性,平台不提供额外的编辑、内容补充、找答案等附加服务。
- 2、"仅部分预览"的文档,不可在线预览部分如存在完整性等问题,可反馈申请退款(可完整预览的文档不适用该条件!)。
- 3、如文档侵犯您的权益,请联系客服反馈,我们会尽快为您处理(人工客服工作时间:9:00-18:30)。
芳构化反应系统工艺流程-标准化文件发布号:(9456-EUATWK-MWUB-WUNN-INNUL-DDQTY-KII
芳构化反应系统工艺流程
混合碳四液化汽和石脑油是在KCIA-Ⅱ分子筛催化剂的作用下,经过碳四烯烃的叠合、脱氢环化、脱氢芳构化及烷烃的裂解等系列催化反应,生成混合芳烃,及副产品液化汽和干气。
反应是强放热反应。
1)工艺流程及说明:
A.加热反应部分
加热反应单元包括原料-产物换热器、加热炉、反应器、等单元设备操作。
由MTBE或罐区来的原料C4和石脑油分别进入原料缓冲罐(V202、V201)。
原料C4经泵P202提升后,经计量控制,一线送至原料-产物换热器E201,另一线送至产物-注冷料换热器E202;石脑油经泵P201提升后经计量控制,与一线原料C4混合送至原料-产物换热器E201。
混合原料分别经原料-产物换热器E201、E203、加热炉F201加热至280-390℃后由反应器R201顶部进入反应器。
部分原料液化气(或贫稀液化气)经产物-注冷料换热器E202加热汽化后,经计量控制分两线由反应器R201中部两催化剂床层之间注入反应器,以便于调节反应床层温度。
反应产物由反应器R201底部采出分别经原料-产物换热器E203、(E-202)、E201换热后进入产物气液分离罐V203,罐底部凝液经泵P203提升后计量控制后进入稳定塔;罐顶分离出的气相经产物空冷器AC201、产物水冷器E204冷却至40℃后进入产物凝液分离罐V204,罐顶部采出为不凝气,进入吸收解吸塔T201中部塔板,底部采出液相,经泵P204提升后进入吸收解吸塔中部塔板。
B.催化剂再生部分
反应进行一段时间后,随着反应器R201中催化剂表面结焦的增加,催化剂表面活性降低,当检测到产品质量不能满足要求时,需将反应器R201切换出反应系统进行催化剂烧焦再生处理。
催化剂再生采用氮气和空气作为再生气体,并控制再生气体中的氧含量,以防止反应催化剂床层再生烧焦超温破坏催化剂。
烧焦前,首先启动再生循环气体压缩机C201,将氮气引至压缩机C201入口处,并经压缩机C201升压至1.0MPa、换热器E201、E203与循环再生气换热后进入再生循环气冷却器E216冷却后进入再生循环气液分离罐V207,罐底分离出循环气带出的油滴,并间歇排出,罐顶为循环气,引至压缩机C201入口增压循环,以逐步将反映其中的油气带出。
当反应器中残留的油气满足安全要求,且反应器进口循环再生气的温度达到烧焦需要的温度时,开始从压缩机
C201入口引入空气,烧焦初期,要求控制循环再生气中的氧体积含量不大于0.5%,以控制反应器再生时的温升不超过50℃。
根据反应器烧焦情况(关注升温),逐步缓慢地提高循环气中氧含量和反应器入口温度,当反应器入口温度达到450℃,且循环再生气中氧含量到达空气中的氧浓度时,观察反应器中温升情况。
当反应器中不再有升温时,烧焦结束。
烧焦气由再生循环气液分离罐顶部安全排放,并用氮气对系统进行彻底的吹扫置换。
当系统中的氧含量低于0.5%合格后,方可进行下一周期的正常生产。
一般情况下,催化剂的再生烧焦过程大约需要10天,依据结焦程度的不同有所调整。
C.产物分馏部分
产物分馏部分包括三个塔系:吸收解吸塔(T201)、稳定塔(T202)、及脱重塔(T203)。
进入吸收解吸塔T201中段塔板的不凝气和凝液,与塔顶吸收油逆向接触吸收,塔顶分离出不凝气;吸收解吸塔吸收中段设置循环取热系统,降低吸收操作温度,以维持较好的吸收效果;塔底设置再沸器E207,塔底液相出料为吸收富液,经泵P205提升后与V203底部凝液混合后分别经富液-芳烃换热器
E211、稳定塔进出物料换热器E208换热后,进入稳定塔T202中部塔板;稳定塔塔顶设置空冷器AC202、水冷器L209,塔顶出料冷却至40℃进入稳定塔顶回流罐V205 。
流出物料主要含有C3、C4及少量C5+的烷烃混合物,作为贫稀液化气经泵P208提升后一部分回流至稳定塔顶,一部分送至产品罐区、一部分返回反应单元作为催化剂床层降温剂。
稳定塔底设置再沸器E210,塔底液相采出物料为芳构化油,经稳定塔进出物料换热器E208换热后,一部分经泵P207提升并经吸收液水冷器L205冷却至40℃后返回吸收解吸塔T201塔顶作为吸收液,一部分经稳定塔塔底液位、计量控制后送入脱重塔T203中部塔盘。
脱重塔塔顶设置富液-芳烃换热器E211,以回收部分热能。
换热器的混合芳烃馏分进入脱重塔顶水冷器L212冷却至40℃进入脱重塔顶回流罐V206。
脱重塔T203塔顶流出物料为产品轻芳构化油,塔底液相采出物料为少量的重芳构化油,经混合重芳烃冷却器L213冷却至40℃后,由泵P210提升送出。