机械加工检验规程
机械加工工艺与检验规范
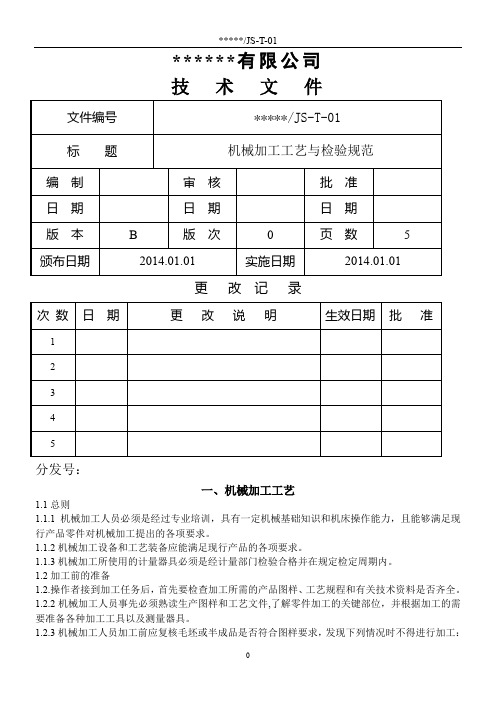
******有限公司技术文件更改记录分发号:一、机械加工工艺1.1总则1.1.1机械加工人员必须是经过专业培训,具有一定机械基础知识和机床操作能力,且能够满足现行产品零件对机械加工提出的各项要求。
1.1.2机械加工设备和工艺装备应能满足现行产品的各项要求。
1.1.3机械加工所使用的计量器具必须是经计量部门检验合格并在规定检定周期内。
1.2加工前的准备1.2.操作者接到加工任务后,首先要检查加工所需的产品图样、工艺规程和有关技术资料是否齐全。
1.2.2机械加工人员事先必须熟读生产图样和工艺文件,了解零件加工的关键部位,并根据加工的需要准备各种加工工具以及测量器具。
1.2.3机械加工人员加工前应复核毛坯或半成品是否符合图样要求,发现下列情况时不得进行加工:a、被加工件存在明显缺陷;b、被加工件与图样尺寸或形状不相符。
1.2.4按工艺规程要求准备好加工所需的全部工艺装备,发现问题及时处理。
对新夹具、模具等,要先熟悉其使用要求和操作方法。
1.3刀具与工件的装夹1.3.1刀具的装夹1.3.1.1在装夹各种刀具前,一定要把刀柄、刀杆、导套等擦试干净。
1.3.1.2刀具装后,应用对刀具装置或试切等检查其正确性。
1.3.2工件的装夹1.3.2.1在机床工作台上安装夹具时,首先要擦净其定位基面,并要找正其与刀具的相对位置。
1.3.2.2工件装夹前应将其定位面、装紧面、垫铁和夹具的定位、平紧面擦试干净,并不得有毛刺。
1.3.2.3按工艺规程中规定的定位基准装夹,若工艺规程中未规定装夹方式,操作者可自行选择定位基准和装夹方法,选择定位基准应按以下原则:a、尽可能使定位基准与设计基准重合;b、尽可能使各加工面采用同一定位基准;粗加工定位基准应尽量选择不加工或加工余量比较小的平整表面,而且只能使用一次;c、精加工定位基准应是已加工表面;d、选择的定位基准必须使工件定位夹方便,加工时稳定可靠。
1.3.2.4对无专用夹具的工件,装夹时应按以下原则进行找正;e、对划线工件应按划线进行找正;f、对不划线工件,在本工序后尚需继续加工的表面,找正精度应保证下工序有足够的加工余量;g、对在本工序加工到成品尺寸的表面,其找正精度应小于尺寸公差的三分之一;h、对在本工序加工到成品尺寸的未注尺寸公差和位置公差的表面,其找正精度应保证GB1804-C级GB1189-10级未注公差和位置公差的要求。
变速箱箱体的机械加工工艺规程

变速箱箱体的机械加工工艺规程变速箱是汽车传动系统的重要组成部分,它通过不同的齿轮组合来实现不同的速度和扭矩输出。
而这些齿轮的运转离不开变速箱箱体的支撑和稳定,因此变速箱箱体的加工质量直接影响着汽车的性能和安全。
本文将介绍变速箱箱体的机械加工工艺规程,包括相关的工艺流程、设备和技术要点。
一、加工流程1、检查箱体毛坯:对毛坯进行外观、尺寸和材质等检查,并根据加工图纸确定加工工艺和加工参数。
2、分号廓、开整体孔:用数控车床对毛坯进行分号廓和开整体孔的加工,确保精度和尺寸配合。
3、铣凹槽、钻螺纹孔:用数控铣床对箱体进行凹槽、倒角和螺纹孔的加工,确保精度和表面质量。
4、车平面、切倒角:用数控车床对箱体进行平面和倒角加工,确保箱体的平整和美观度。
5、排刀台、磨平面:用磨床对箱体的主体结构进行平面的磨削,确保平面精密度和表面光洁度。
6、清洗箱体、质检:对加工好的箱体进行清洗和表面处理,同时进行质量检查和尺寸配合测试。
7、装配齿轮、检验调试:按照设计图纸进行齿轮的装配,进行齿轮间的配合度和转动力的调试。
二、设备要求1、数控机床:包括数控车床、数控铣床、数控磨床等设备,用于箱体的分号廓、开孔、加工凹槽、钻孔、车平面和磨削等加工工序。
2、高压清洗机:用于对加工好的箱体进行清洗和表面处理,确保箱体干净无油污,表面质量良好。
3、品质检测设备:包括示波器、卡尺、针对性量规等检测仪器,用于对箱体质量进行检测和质量保证。
三、技术要点1、机械加工工艺:对箱体进行加工时,需要结合箱体的加工图纸和加工参数进行加工,严格按照工艺流程和技术规范进行加工,确保箱体的尺寸和精度。
2、表面处理:对箱体进行表面处理时,需要选择合适的清洗剂和表面处理剂,同时注意处理时的温度和时间,确保箱体表面光洁度和质量。
3、质量检查:对加工好的箱体进行质量检查时,需要结合检测仪器和装配情况进行测试,其中重点检查加工尺寸和配合度,以确保产品质量。
综上所述,变速箱箱体的机械加工工艺规程是汽车传动系统中非常重要的一环,它直接影响着汽车的性能和安全。
机械加工制程检验规程

机械加工制程检验规程一、目的:根据公司在机械加工中批量生产的特点特制定此检验规程。
二、范围:适用于本公司自制零件各工序的检验。
三、具体检验项目如下:1、落料(数控冲,数控剪,冲床,俗称展开图):⑴确认其材质、板厚是否与图相符,我公司所使用的板材主要有冷轧钢板、镀锌钢板、不锈钢板、热轧钢板、镀锌花纹板、铜板、以及铝板应注意其表面要求是雾面,镜面还是拉丝面,不可搞错。
⑵外观1)有无毛边毛刺,锐角,划碰伤,接刀痕,锈蚀;2)面板类,板材在去除毛边时,要特别注意不可被打磨成斜面(四角);3)如果此产品下道工序须作拉丝处理那么板材表面的划碰伤及毛刺只要不是很明显的手感即可接收,如为镀锌、镀铬等不需喷塑的需保护;4)在下料时还应注意其板材是否平直,不可有明显的波浪状及滚辊印痕。
⑶尺寸检验必须将其四周及孔的毛边毛刺,接刀痕去除于净,并且要产品校平后才能进行测量,否则会影响对产品尺寸的测量及判断。
⑷摆放及保护是否合理此方面主要依据作业指导书上的要求执行检验,要求贴膜保护,用隔板隔离的一定要遵照执行,如果工件摆放过高,四角要用透明打包胶带包好,以免在运输过程中发生倒塌及碰撞,损坏工件表面。
⑸现场有无作自检记录,记录是否真实,写的是否规范等。
⑹上述检验项目不可漏掉任何一项,当全部合格时方可下转。
2、数控折弯,冲床成型。
⑴确认其材质,板厚是否与图相符;⑵外观:表面有无明显之折痕,变形,折斜,划碰伤,接模痕等不良;⑶角度:每一刀的角度依图面清楚进行检测,对于折弯角度较复杂要求较高的工件,可做检具加以控制;⑷方向:在看折弯方向时先弄清楚图面要求的是什么视图方法(第一角,第三角还是机械视图)当发生折弯成型后毛边在正面一定要对折弯方向重新进行确认是否折反。
⑸尺寸:1)依图量测所有折弯尺寸;2)重点尺寸(图纸提示,有特殊标注或标有公差的尺寸)应予以重点控制,特别是那些不易测量,客户有投诉过的重点尺寸一定要设计检具进行控制;3)对不重要的尺寸如加强筋,工艺加强尺寸只要与图纸无太大的差别即可。
机械加工操作规程
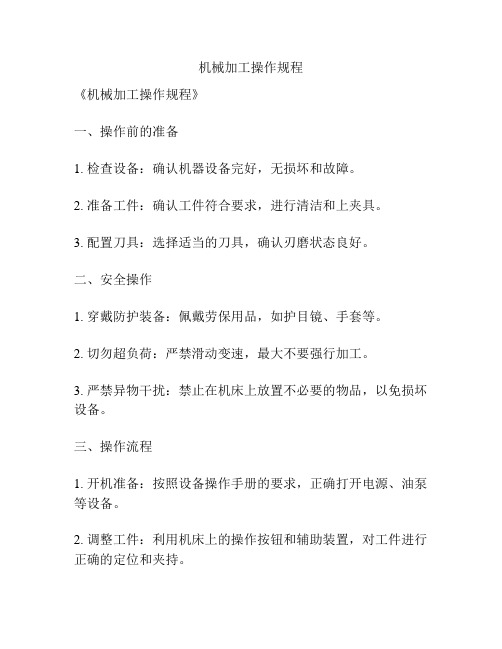
机械加工操作规程
《机械加工操作规程》
一、操作前的准备
1. 检查设备:确认机器设备完好,无损坏和故障。
2. 准备工件:确认工件符合要求,进行清洁和上夹具。
3. 配置刀具:选择适当的刀具,确认刃磨状态良好。
二、安全操作
1. 穿戴防护装备:佩戴劳保用品,如护目镜、手套等。
2. 切勿超负荷:严禁滑动变速,最大不要强行加工。
3. 严禁异物干扰:禁止在机床上放置不必要的物品,以免损坏设备。
三、操作流程
1. 开机准备:按照设备操作手册的要求,正确打开电源、油泵等设备。
2. 调整工件:利用机床上的操作按钮和辅助装置,对工件进行正确的定位和夹持。
3. 进行加工:根据加工要求,逐步进行切削、铣削等加工操作。
4. 测量检验:实时检查工件精度,保证加工的准确性。
四、操作结束
1. 清洁设备:关机后,对机床及操作区域进行清洁和整理。
2. 恢复设备:将设备调整至初始状态,关闭电源。
3. 记录资料:对加工过程进行记录,包括参数设置、工件尺寸等。
通过以上《机械加工操作规程》,操作人员能够按照规程严格操作,确保机械加工的安全性和准确性,提高生产效率。
机械加工检查员安全技术规程范本
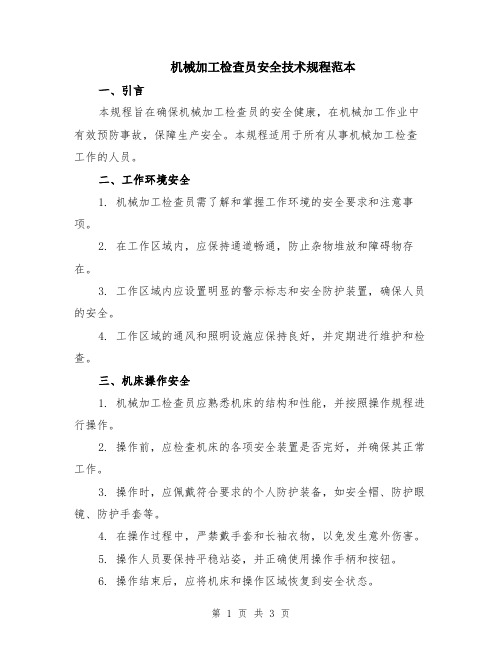
机械加工检查员安全技术规程范本一、引言本规程旨在确保机械加工检查员的安全健康,在机械加工作业中有效预防事故,保障生产安全。
本规程适用于所有从事机械加工检查工作的人员。
二、工作环境安全1. 机械加工检查员需了解和掌握工作环境的安全要求和注意事项。
2. 在工作区域内,应保持通道畅通,防止杂物堆放和障碍物存在。
3. 工作区域内应设置明显的警示标志和安全防护装置,确保人员的安全。
4. 工作区域的通风和照明设施应保持良好,并定期进行维护和检查。
三、机床操作安全1. 机械加工检查员应熟悉机床的结构和性能,并按照操作规程进行操作。
2. 操作前,应检查机床的各项安全装置是否完好,并确保其正常工作。
3. 操作时,应佩戴符合要求的个人防护装备,如安全帽、防护眼镜、防护手套等。
4. 在操作过程中,严禁戴手套和长袖衣物,以免发生意外伤害。
5. 操作人员要保持平稳站姿,并正确使用操作手柄和按钮。
6. 操作结束后,应将机床和操作区域恢复到安全状态。
四、机械设备维护安全1. 机械加工检查员应按照设备维护规程进行机床的定期检查和维护。
2. 维护前,应确保设备停止工作,且断开供电。
3. 维护时,应按照设备制造商提供的操作和维护手册进行维护工作。
4. 维护完毕后,应清理工作现场,将维护工具和材料妥善存放。
五、机械加工作业安全1. 在机械加工作业前,必须了解加工对象的性质和工艺要求,制定操作方案。
2. 加工过程中,应使用适当的切削工具,确保加工质量和安全。
3. 加工时应注意切削速度、进给速度和切削深度的选择,避免超负荷运转。
4. 加工完成后,应及时清理加工区域的切屑和废料,防止堆积和滑倒。
5. 加工液的使用要符合相关的安全标准,并妥善保存和处理。
六、紧急情况处理1. 机械加工检查员应熟悉常见紧急情况的处理方法,并能迅速采取应急措施。
2. 发生意外事故时,要立即停止机械加工作业,确保自身安全。
3. 根据事故情况,进行必要的紧急救护和报警。
机械设备检测管理制度

机械设备检测管理制度一、总则为了规范机械设备检测工作,确保设备的安全性和可靠性,有效地预防事故和提高生产效率,制定本机械设备检测管理制度。
二、适用范围本制度适用于公司内所有机械设备的日常检测。
三、检测责任1.设备管理部门负责组织和协调机械设备的检测工作。
2.设备操作人员负责定期检查设备的运行情况,及时发现和上报问题。
3.检测机构负责对机械设备进行定期检验和检测,并出具检测报告。
四、检测周期1.根据设备的使用频率和工况,设备管理部门确定机械设备的检测周期。
2.高频使用的设备一般需要进行每月检测,中低频使用的设备则可以根据实际情况进行季度或年度检测。
五、检测内容1.外观检查:对设备的外观进行检查,包括设备的表面是否有损伤、锈蚀等。
2.功能检查:对设备的各项功能进行检查,包括设备是否正常运行、各零部件是否完好等。
3.安全检查:对设备的安全措施进行检查,确保设备是否符合相关的安全规定。
4.测试检查:对设备的性能进行测试,包括设备的电气性能、气密性能、压力性能等。
六、检测记录1.设备操作人员应对每次检测进行详细记录,包括检测的时间、地点、具体内容、检测结果等。
2.检测机构应对每次检测结果进行记录,并出具检测报告。
3.设备管理部门应对所有检测记录进行归档管理,并建立相应的数据库。
七、异常处理1.如果在检测过程中发现设备存在问题或隐患,设备操作人员应及时上报设备管理部门,并停止使用该设备。
2.设备管理部门应立即采取相应的措施修复设备,并做好相应的记录和报告。
八、培训教育1.新进员工在入职培训中要接受机械设备检测管理制度的教育培训,了解设备的检测流程和要点。
2.定期组织设备操作人员进行设备检测知识的培训,提高其检测能力和意识。
九、制度评审定期对本机械设备检测管理制度进行评审,根据实际情况进行修订和完善。
十、责任追究对于未按照本制度进行机械设备检测的责任人员,将按照公司相应的纪律规定,给予相应的处罚。
十一、附则本制度自颁布之日起执行,并不时根据实际情况进行修订和完善。
机械制造行业产品质量检验规范
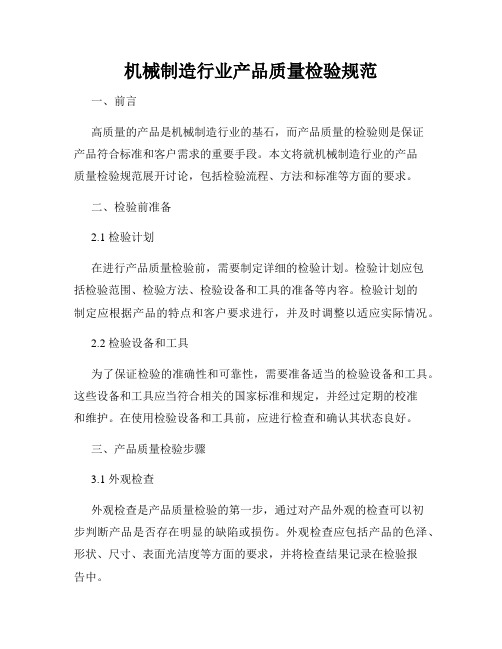
机械制造行业产品质量检验规范一、前言高质量的产品是机械制造行业的基石,而产品质量的检验则是保证产品符合标准和客户需求的重要手段。
本文将就机械制造行业的产品质量检验规范展开讨论,包括检验流程、方法和标准等方面的要求。
二、检验前准备2.1 检验计划在进行产品质量检验前,需要制定详细的检验计划。
检验计划应包括检验范围、检验方法、检验设备和工具的准备等内容。
检验计划的制定应根据产品的特点和客户要求进行,并及时调整以适应实际情况。
2.2 检验设备和工具为了保证检验的准确性和可靠性,需要准备适当的检验设备和工具。
这些设备和工具应当符合相关的国家标准和规定,并经过定期的校准和维护。
在使用检验设备和工具前,应进行检查和确认其状态良好。
三、产品质量检验步骤3.1 外观检查外观检查是产品质量检验的第一步,通过对产品外观的检查可以初步判断产品是否存在明显的缺陷或损伤。
外观检查应包括产品的色泽、形状、尺寸、表面光洁度等方面的要求,并将检查结果记录在检验报告中。
3.2 尺寸检验尺寸检验是产品质量检验的关键环节之一,对产品的关键尺寸进行准确的测量和判定能够直接反映产品的质量水平。
尺寸检验应采用适当的测量工具和方法,比如卡尺、游标卡尺、坐标测量机等,并按照相关的国家标准和规定进行操作和记录。
3.3 功能性能检验功能性能检验是产品质量检验的核心内容,通过检测产品的功能性能能够评估产品是否能够满足客户的需求和使用要求。
功能性能检验应采用适当的测试方法和设备,比如负载试验台、运行试验台等,并按照相关的国家标准和规定进行操作和记录。
3.4 耐久性检验耐久性检验是对产品的使用寿命和耐用性进行评估的重要手段。
耐久性检验应采用适当的试验装置和方法,比如疲劳试验机、振动试验台等,并按照相关的国家标准和规定进行操作和记录。
3.5 环境适应性检验环境适应性检验是对产品在不同环境条件下的适应性进行评估的重要手段。
环境适应性检验应采用适当的试验方法和设备,比如恒温恒湿试验箱、盐雾试验箱等,并按照相关的国家标准和规定进行操作和记录。
特种机械设备检查检测制度模版
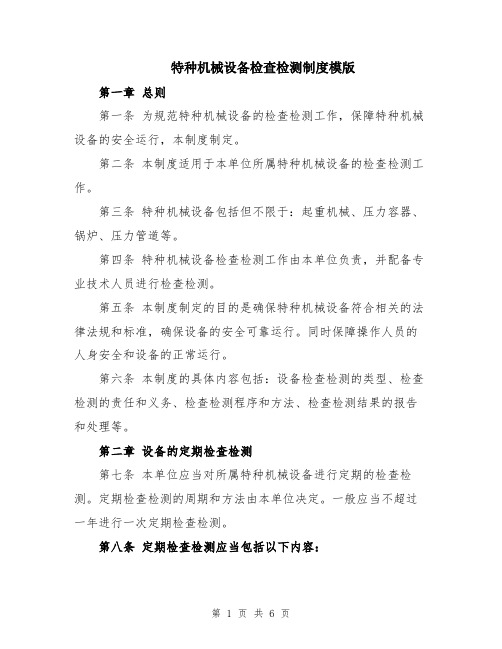
特种机械设备检查检测制度模版第一章总则第一条为规范特种机械设备的检查检测工作,保障特种机械设备的安全运行,本制度制定。
第二条本制度适用于本单位所属特种机械设备的检查检测工作。
第三条特种机械设备包括但不限于:起重机械、压力容器、锅炉、压力管道等。
第四条特种机械设备检查检测工作由本单位负责,并配备专业技术人员进行检查检测。
第五条本制度制定的目的是确保特种机械设备符合相关的法律法规和标准,确保设备的安全可靠运行。
同时保障操作人员的人身安全和设备的正常运行。
第六条本制度的具体内容包括:设备检查检测的类型、检查检测的责任和义务、检查检测程序和方法、检查检测结果的报告和处理等。
第二章设备的定期检查检测第七条本单位应当对所属特种机械设备进行定期的检查检测。
定期检查检测的周期和方法由本单位决定。
一般应当不超过一年进行一次定期检查检测。
第八条定期检查检测应当包括以下内容:(一)设备的外观检查,包括外观有无异常变形、损坏等情况的检查。
(二)设备的工作机构检查,包括工作机构是否有松动、断裂、磨损等现象的检查。
(三)设备的电气系统检查,包括电气线路是否正常,电器设备是否损坏等的检查。
(四)设备的液压系统检查,包括液压油是否正常、液压元件是否损坏等的检查。
(五)设备的传动系统检查,包括传动链条、传动带等是否正常的检查。
(六)设备的安全保护装置检查,包括安全绳、安全阀等是否正常的检查。
(七)设备的性能检查,包括设备的起升能力、工作速度等是否符合要求的检查。
第九条定期检查检测应当由本单位的特种机械设备检查检测人员进行。
检查检测人员应当持有相应的特种设备操作和维护的合格证书。
第十条定期检查检测的结果应当及时记录,并进行保存。
如发现设备有异常情况或不合格情况,应当及时上报,并做出相应的处理。
第三章设备的接管检查检测第十一条新购进或租赁特种机械设备在投入使用之前,应当进行接管检查检测。
接管检查检测应当包括以下内容:(一)设备的规格和型号是否符合要求的检查。
机械零件加工工艺规程方案设计

机械零件加工工艺规程方案设计一、引言本文旨在设计机械零件加工的规程方案,以确保加工过程的准确性、安全性和高效性。
二、工艺流程1.制定加工计划:根据零件的要求和材料特性,确定合适的加工方法和设备。
2.准备加工设备和工具:确保加工设备和工具的良好状态,包括刀具、夹具、机床等。
3.检查工件和材料:检查工件和材料是否符合要求,包括尺寸、材质、硬度等。
4.加工前准备:准备加工液、切削液和冷却液,确保加工过程的顺利进行。
5.加工操作:根据加工工艺要求,进行加工操作,包括车削、铣削、磨削等。
6.质量检查:在加工过程中进行定期检查,确保加工质量的合格性。
7.表面处理:根据要求进行表面处理,包括镀铬、喷涂等。
8.检验和验收:对加工完成的零件进行检验,确保其符合要求。
9.清洗和防锈:对加工完成的零件进行清洗和防锈处理,以延长其使用寿命。
10.包装和交付:根据客户要求进行适当的包装,并按时交付给客户。
三、注意事项1.安全第一:加工过程中必须严格遵守安全操作规程,佩戴必要的个人防护装备。
2.设备保养:定期检查和维护加工设备,确保其正常运转。
3.物料管理:加工过程中要注意对材料的储存和保护,防止受潮、受污等。
4.加工参数控制:严格控制加工参数,如切削速度、进给速度和切削深度,以确保加工质量。
5.过程记录:对加工过程中的关键参数和质量数据进行记录,以便追溯和分析。
四、质量控制1.原材料质量控制:进行必要的材料检测,确保其符合零件要求。
2.首件检查:对首件进行全面检查,确保加工程序和工装的准确性。
3.过程控制:加工过程中进行定期检查和检验,纠正加工中的问题,确保加工质量。
4.最终检验:对加工完成的零件进行全面检验,检查尺寸、表面质量和功能性能。
5.不良品处理:对不良品进行分类和处理,如返修、重新加工或报废。
五、工艺改进1.分析问题:对加工过程中出现的问题进行分析,找出问题的原因。
2.制定改进方案:根据问题的原因,制定具体的改进方案,如更换设备、改进工艺参数等。
拨叉零件的机械加工工艺规程
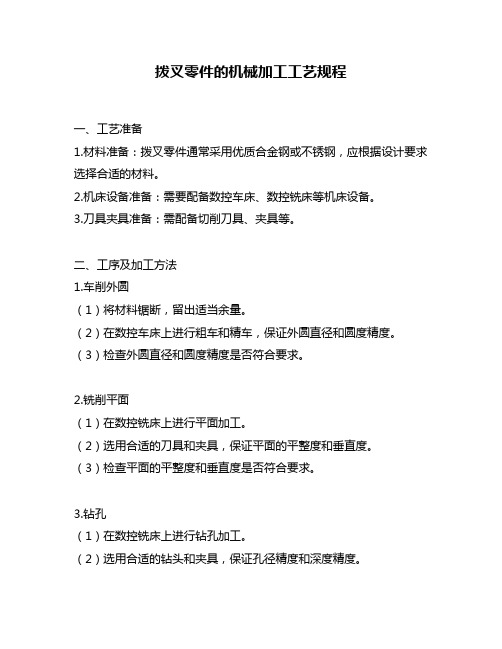
拨叉零件的机械加工工艺规程一、工艺准备1.材料准备:拨叉零件通常采用优质合金钢或不锈钢,应根据设计要求选择合适的材料。
2.机床设备准备:需要配备数控车床、数控铣床等机床设备。
3.刀具夹具准备:需配备切削刀具、夹具等。
二、工序及加工方法1.车削外圆(1)将材料锯断,留出适当余量。
(2)在数控车床上进行粗车和精车,保证外圆直径和圆度精度。
(3)检查外圆直径和圆度精度是否符合要求。
2.铣削平面(1)在数控铣床上进行平面加工。
(2)选用合适的刀具和夹具,保证平面的平整度和垂直度。
(3)检查平面的平整度和垂直度是否符合要求。
3.钻孔(1)在数控铣床上进行钻孔加工。
(2)选用合适的钻头和夹具,保证孔径精度和深度精度。
(3)检查孔径精度和深度精度是否符合要求。
4.切削齿形(1)在数控铣床上进行切削齿形加工。
(2)选用合适的齿轮铣刀和夹具,保证齿形精度和齿距精度。
(3)检查齿形精度和齿距精度是否符合要求。
5.车削内孔(1)在数控车床上进行内孔加工。
(2)选用合适的刀具和夹具,保证孔径精度和深度精度。
(3)检查孔径精度和深度精度是否符合要求。
6.倒角(1)在数控铣床上进行倒角加工。
(2)选用合适的倒角刀具,保证倒角的大小和平整度。
(3)检查倒角的大小和平整度是否符合要求。
7.清洗、除油将拨叉零件进行清洗、除油等表面处理,以便后续的装配使用。
三、质量检验1.外观质量:检查拨叉零件表面是否有裂纹、气泡、毛刺等缺陷。
2.尺寸精度:采用测量仪器进行尺寸测量,保证尺寸精度符合要求。
3.功能性能:进行装配试验,保证拨叉零件的功能性能符合设计要求。
四、工艺文件1.工艺卡:记录拨叉零件的加工工序、加工方法、刀具夹具等信息。
2.检验报告:记录拨叉零件的外观质量、尺寸精度和功能性能等检验结果。
轴零件的机械加工工艺规程及夹具设计

轴零件的机械加工工艺规程及夹具设计一、轴零件的机械加工工艺规程1.材料准备:轴零件的材料通常选择优质的钢材或铸铁材料,需要根据轴零件的使用要求和工艺特点来选择合适的材料。
2.工艺路线确定:根据轴零件的形状、结构和加工要求,确定合适的工艺路线,包括车削、铣削、钻孔等加工工序的顺序和方法。
3.加工设备选择:根据轴零件的尺寸、形状和工艺要求,选择合适的加工设备,包括车床、铣床、钻床等。
4.工艺参数确定:根据轴零件的材料和加工要求,确定合适的切削速度、进给量和切削深度等工艺参数。
5.工艺操作规范:对于每个加工工序,制定相应的工艺操作规范,包括操作顺序、刀具安装、夹具装夹和加工顺序等。
6.质量检验要求:确定轴零件的质量检验要求和方法,包括尺寸偏差、表面粗糙度、硬度等指标的检验。
7.工艺文件编制:将以上所有内容整理成工艺文件,包括工艺路线图、刀具配套表、工艺操作规程和质量检验记录表等。
二、夹具设计夹具是机械加工中用来固定工件、定位和保持工件位置的装置。
在轴零件的机械加工中,夹具设计是非常重要的一环。
夹具的设计应满足以下几个要求:1.夹紧可靠:夹具的设计应保证对轴零件进行可靠的夹紧,以防止在加工过程中因工件松动而引起的加工误差。
2.定位准确:夹具的设计应能够确保轴零件在加工过程中的准确定位,以保证加工精度。
3.易于安装和调整:夹具应设计成易于安装和调整的形式,以方便操作人员进行装夹和调整。
4.加工装卸方便:夹具的设计应便于轴零件的装卸,以提高生产效率。
5.避免干涉:夹具的设计应避免与加工刀具和加工设备的干涉,以保证加工进程的顺利进行。
在夹具设计过程中,需要根据轴零件的形状、尺寸和加工要求,选择合适的夹具类型,包括平面夹具、分度夹具、对心夹具等,并进行夹具的结构设计和强度计算。
总结起来,轴零件的机械加工工艺规程及夹具设计是确保轴零件加工质量和工艺正确性的重要环节,对于提高加工效率和保证加工精度具有重要意义。
机械加工操作规程范本

机械加工操作规程范本第一章总则第一条为了保证机械加工作业的安全和质量,规范操作行为,减少事故的发生,制定本规程。
第二条本规程适用于机械加工作业过程中的操作人员。
第三条机械加工作业过程中,操作人员应严格遵守本规程,保持安全操作、高效工作、良好质量。
第二章安全操作规程第一条操作人员必须穿戴符合要求的劳动防护用具,保护头、面、眼、耳、呼吸道和手部等易受伤处。
严禁穿着松散衣服和珠宝物品。
第二条操作人员应确保加工设备在正常工作状态下,无任何隐患。
如发现设备异常,应立即报告维修。
第三条操作人员在进行机械加工操作前,应对所用设备进行检查,确保其正常运转。
第四条操作人员在操作设备时,应严禁戏言、闲聊、嬉戏,确保专注工作、全神贯注。
第五条操作人员应保持操作区域整洁、干净,禁止在工作区域内乱扔废弃物品。
第三章高效工作规程第一条操作人员应按照工作计划和工艺要求,合理安排工作时间,提高生产效率。
第二条操作人员要熟悉所使用机械设备的工艺流程,准确掌握操作方法。
第三条操作人员要合理安排工作空间,确保材料和工具的合理摆放,方便取用。
第四条操作人员要经常清洁和保养自己所使用的工具和设备,确保操作顺利进行。
第五条操作人员应按照工作计划和工艺要求控制好加工进度,确保按时完成任务。
第四章良好质量规程第一条操作人员要严格按照工艺要求进行操作,确保产品质量。
第二条操作人员要经常检查和维护所使用的工具和设备,确保其良好状态。
第三条操作人员要遵守标准操作规程,确保加工精度和表面质量。
第四条操作人员要严格注意检验过程中的尺寸、角度等要求,确保加工件符合技术要求。
第五条操作人员要协助质检人员进行产品质量检验,及时解决问题。
第五章突发事件处置规程第一条在机械加工过程中,如发生突发事故,操作人员应立即停止操作,采取措施确保人员安全。
第二条操作人员应及时向上级报告突发事件,并按照事故报告流程进行上报。
第三条在突发事件处理过程中,操作人员应积极配合有关部门做好善后工作。
钢筋加工机械设备检查技术规程

钢筋加工机械设备检查技术规程1.1 一般规定1.1.1整机应符合下列规定:1机械的安装应坚实稳固,保持水平位置;2金属结构不应有开焊、裂纹;3零部件应完整,随机附件应齐全;4外观应清洁,不应有油垢和锈蚀;5操作系统应灵敏可靠,各仪表指示数据应准确;6传动系统运转应平稳,不应有异常冲击、振动、爬行、窜动、噪声、超温、超压;7机身不应有破损、断裂及变形;8各部位连接应牢靠,不应松动。
1.1.2电气系统及润滑系统应符合下列规定:1钢筋加工机械的用电应符合国家现行标准《施工现场临时用电安全技术规范》JGJ46的有关规定;2电气系统装置应齐全,线路排列应整齐,卡固应牢靠;3电气设备安装应牢固,电气接触应良好;4电机运行时不应有异常响声、抖动及过热;5电气控制设备和元件应置于柜(箱)内,电气柜(箱)门锁应齐全有效;6油泵工作应有效;油路、油嘴应畅通;油杯、油线、油毡应齐全,不应有破损;油标应醒目,刻线应正确,油质、油量应符合说明书的要求;7润滑系统工作应有效,油路应畅通,润滑应良好;各润滑部位及零件不应严重拉毛、磨损、碰伤;8润滑油型号、油质及油量应符合说明书的要求。
1.1.3安全防护应符合下列规定:1安全防护装置及限位应齐全、灵敏可靠,防护罩、板安装应牢固,不应破损;2接地(接零)应符合用电规定,接地电阻不应大于4Q;3漏电保护器参数应匹配,安装应正确,动作应灵敏可靠;电气保护(短路、过载、失压)应齐全有效。
1.1.4液压系统应符合下列规定:1各液压元件固定应牢固,不应有渗漏;2液压系统应清洁,不应有油垢;3各液压元件的调定压力应符合说明书的要求;4各液压元件应定期校准和检验。
1.2钢筋调直机1.2.1传动系统应符合下列规定:1传动机构运转应平稳,不应有异响,传动齿轮及花键轴不应有断齿、啃齿、裂纹及表面脱落;2传动皮带数量应齐全,不应有破损、断裂,松紧度应适宜。
1.2.2调直系统及牵引和落料机构应符合下列规定:1调直筒、轴不应有弯曲、裂纹和轴销磨损等;2离合器应灵敏可靠,结合时应吻合,不应咬边;调速滑动齿轮滑动应灵活,不应窜动;3自动落料机构开闭应灵活,落料应准确,落料架各部件连接应牢固;4牵引轮工作应有效,调节机构应灵敏,滑块移动不应有卡阻;5调节螺母、回位弹簧及链轮机构应灵敏、可靠。
机械加工工艺规程概述

机械加工工艺规程概述引言机械加工工艺规程是指在机械加工过程中,为了提高生产效率、保证产品质量以及确保工人安全,制定的一系列操作规程和操作方法。
本文将对机械加工工艺规程进行概述,介绍其基本概念、目的以及常见的工艺规程内容。
工艺规程的基本概念工艺规程是指根据产品的特点和加工工艺要求,制定出一系列操作规程和操作方法的文档。
它涵盖了加工工序、加工设备、操作方法、质量要求、安全措施等内容,为加工操作提供了指导和规范。
工艺规程的目的制定工艺规程的目的主要有以下几点:1.提高生产效率:通过规范的操作方法和流程,可以减少加工中的错误和重复工作,提高生产效率。
2.确保产品质量:工艺规程明确了加工中的质量要求和检验方法,可以保证产品的质量稳定和一致性。
3.保障工人安全:工艺规程规定了加工操作中的安全措施和防护措施,确保工人的身体安全和健康。
工艺规程的内容1. 加工工序工艺规程包含了产品的所有加工工序和加工顺序,以及每个工序的具体要求和操作方法。
每个工序的步骤和流程应该清晰明确,指导操作人员正确进行加工。
2. 加工设备工艺规程中需要明确所需的加工设备和其规格要求。
包括机床、刀具、量具、夹具等,以及设备的调整、校验和维护要求。
3. 加工参数工艺规程中应说明每个工艺参数的设定范围和具体数值。
包括切削速度、进给量、切削深度等参数,以及不同材料和加工工艺的参数选择。
4. 加工工具工艺规程应包含对加工工具的使用说明和保养要求。
包括刀具的选择、磨削和更换,以及量具的校准、使用和保养方法。
5. 质量要求工艺规程中应明确产品加工的质量要求和检验方法。
包括尺寸精度、表面质量、装配要求等,以及不同工序的工件检验要求和方法。
6. 安全措施工艺规程中需要规定加工操作中的安全措施和防护措施,以保障工人的安全。
包括作业人员的防护用具、设备的安全操作要求和应急措施等。
编写工艺规程的注意事项在编写工艺规程时,需要注意以下几点:1.精确细致:工艺规程应尽可能详尽,不遗漏任何工序和操作要点,确保操作人员按照规程正确进行加工。
机械加工安全操作规程(3篇)
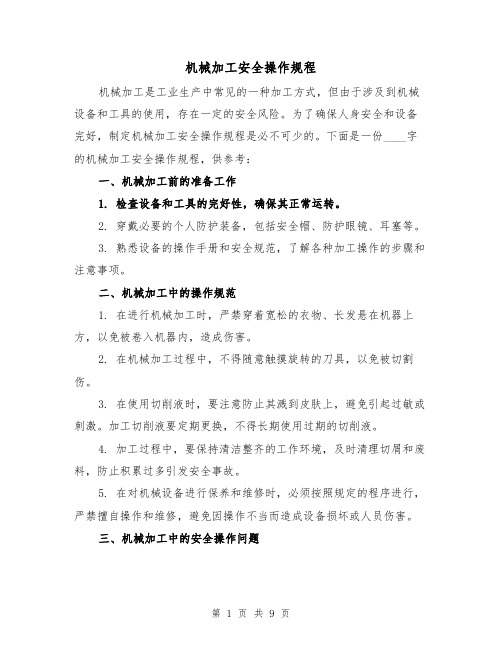
机械加工安全操作规程机械加工是工业生产中常见的一种加工方式,但由于涉及到机械设备和工具的使用,存在一定的安全风险。
为了确保人身安全和设备完好,制定机械加工安全操作规程是必不可少的。
下面是一份____字的机械加工安全操作规程,供参考:一、机械加工前的准备工作1. 检查设备和工具的完好性,确保其正常运转。
2. 穿戴必要的个人防护装备,包括安全帽、防护眼镜、耳塞等。
3. 熟悉设备的操作手册和安全规范,了解各种加工操作的步骤和注意事项。
二、机械加工中的操作规范1. 在进行机械加工时,严禁穿着宽松的衣物、长发悬在机器上方,以免被卷入机器内,造成伤害。
2. 在机械加工过程中,不得随意触摸旋转的刀具,以免被切割伤。
3. 在使用切削液时,要注意防止其溅到皮肤上,避免引起过敏或刺激。
加工切削液要定期更换,不得长期使用过期的切削液。
4. 加工过程中,要保持清洁整齐的工作环境,及时清理切屑和废料,防止积累过多引发安全事故。
5. 在对机械设备进行保养和维修时,必须按照规定的程序进行,严禁擅自操作和维修,避免因操作不当而造成设备损坏或人员伤害。
三、机械加工中的安全操作问题1. 加工大型工件时,要做好固定和支撑工作,避免因工件不稳造成的意外。
2. 加工过程中,不得随意更改加工参数,如切削速度、进给量等,以免导致设备故障或工件损坏。
3. 在加工过程中,如发现异常声音、烟雾等异常情况,应立即停机检查,排除故障后方可继续操作。
4. 加工过程中,不得随意触动电气设备和控制按钮,如需操作,必须按照操作规程进行,避免因误操作引起电气事故。
四、机械加工后的安全处理1. 加工完成后,要及时关闭机械设备的电源和切削液供应,确保设备安全停机。
2. 清洁工作台和机器设备表面的切削屑和废料,保持设备的整洁和通风。
3. 将使用过的工具、测量工具和切削刀具进行分类清理和存储,避免丢失和损坏。
4. 定期对机械设备进行保养和维护,检查设备各部位的磨损和松动,及时进行维修和更换,确保设备的安全运行。
杠杆零件的机械加工工艺规程和夹具设计
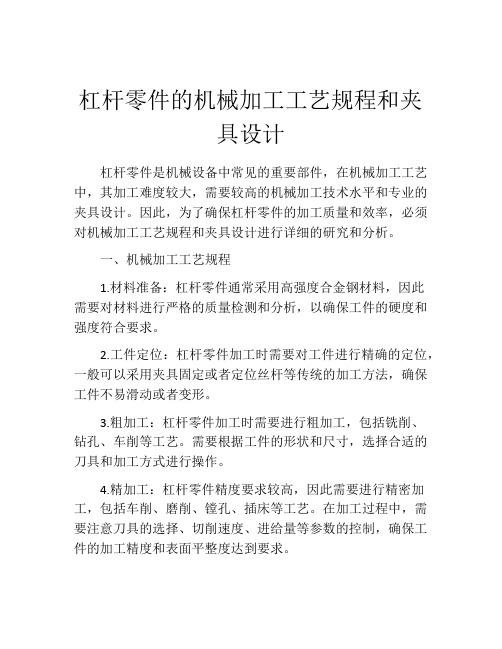
杠杆零件的机械加工工艺规程和夹具设计杠杆零件是机械设备中常见的重要部件,在机械加工工艺中,其加工难度较大,需要较高的机械加工技术水平和专业的夹具设计。
因此,为了确保杠杆零件的加工质量和效率,必须对机械加工工艺规程和夹具设计进行详细的研究和分析。
一、机械加工工艺规程1.材料准备:杠杆零件通常采用高强度合金钢材料,因此需要对材料进行严格的质量检测和分析,以确保工件的硬度和强度符合要求。
2.工件定位:杠杆零件加工时需要对工件进行精确的定位,一般可以采用夹具固定或者定位丝杆等传统的加工方法,确保工件不易滑动或者变形。
3.粗加工:杠杆零件加工时需要进行粗加工,包括铣削、钻孔、车削等工艺。
需要根据工件的形状和尺寸,选择合适的刀具和加工方式进行操作。
4.精加工:杠杆零件精度要求较高,因此需要进行精密加工,包括车削、磨削、镗孔、插床等工艺。
在加工过程中,需要注意刀具的选择、切削速度、进给量等参数的控制,确保工件的加工精度和表面平整度达到要求。
5.测量检验:杠杆零件加工完成后,需要进行废品率控制和质量检验。
一般采用测量仪器进行检测,如温度计、直角尺、卡尺等,确保工件的尺寸和形状符合设计要求。
二、夹具设计1. 表面精密度要求:杠杆零件加工时,对夹具的精度和表面平整度要求较高,需要采用高精度数控加工设备来进行制造,以确保夹具的精确度和稳定性。
2. 夹紧力的设计:夹具的夹紧力要足够大,能够确保工件安全固定和不易变形。
但同时,过大的夹紧力也会导致工件变形和加工精度降低。
因此,需要对夹具的夹紧力进行合理的设计和调整。
3. 直线度和平行度的控制:杠杆零件加工时,需要采用直线和平行夹具对工件进行夹紧,在设计和制造夹具时,需要控制直线度和平行度的精度,确保工件的加工精度。
4. 夹具的耐用性:夹具在加工过程中容易磨损和疲劳,因此需要考虑夹具的材质和表面硬度的选择,合理的加工工艺,能够延长夹具的使用寿命,提高生产效率和经济效益。
总之,在机械加工过程中,杠杆零件的加工难度比较大,需要精细的机械加工技术和专业的夹具设计,才能确保工件的加工质量和效率。
某机械零件的加工工艺规程
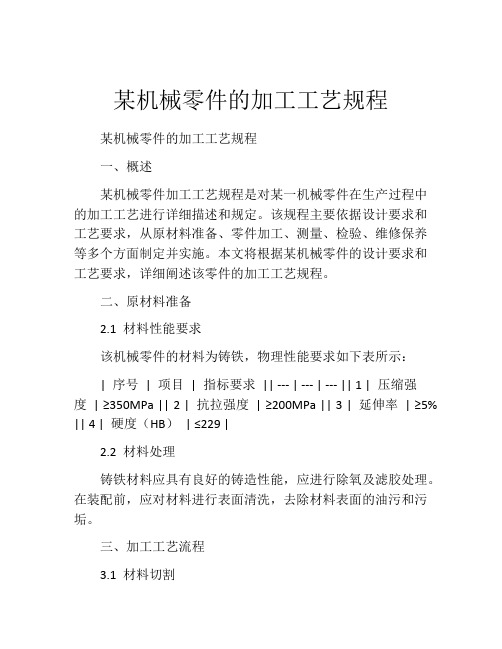
某机械零件的加工工艺规程某机械零件的加工工艺规程一、概述某机械零件加工工艺规程是对某一机械零件在生产过程中的加工工艺进行详细描述和规定。
该规程主要依据设计要求和工艺要求,从原材料准备、零件加工、测量、检验、维修保养等多个方面制定并实施。
本文将根据某机械零件的设计要求和工艺要求,详细阐述该零件的加工工艺规程。
二、原材料准备2.1 材料性能要求该机械零件的材料为铸铁,物理性能要求如下表所示:| 序号| 项目| 指标要求|| --- | --- | --- || 1 | 压缩强度| ≥350MPa || 2 | 抗拉强度| ≥200MPa || 3 | 延伸率| ≥5% || 4 | 硬度(HB)| ≤229 |2.2 材料处理铸铁材料应具有良好的铸造性能,应进行除氧及滤胶处理。
在装配前,应对材料进行表面清洗,去除材料表面的油污和污垢。
三、加工工艺流程3.1 材料切割根据机械零件的设计要求,使用切割机将铸铁材料切割成材料坯。
3.2 粗加工步骤:车床加工→ 铣床加工→ 钻床加工3.2.1 车床加工根据机械零件图纸要求,经过加工准备、装夹工件、校正、精加工等多个步骤,对材料坯进行车削加工,得到下图所示的中间轴套。
(图1:车削加工)3.2.2 铣床加工将车削加工好的中间轴套装夹在铣床上加工,得到下图所示的中间轴套的中空孔。
(图2:铣削加工)3.2.3 钻床加工在铣床中心孔位置处将其上下两端加固,然后在中心孔处进行钻孔。
其加工方法和过程与车床加工类似,得到下图所示的中间轴套螺纹孔。
(图3:钻孔加工)3.3 精加工步骤:磨削加工→ 理石加工3.3.1 磨削加工根据设计要求对中间轴套的内外表面进行磨削加工。
该加工过程具有高精度、良好的表面光洁度和精度维持能力的优点,可得到理想的加工精度和表面质量,下图为加工后的中间轴套。
(图4:磨削加工)3.3.2 理石加工将磨削加工后的中间轴套经过理石加工,使其表面粗糙度能够满足设计的要求,得到下图所示的最终成品。
车削工序检验规程

车削工序检验规程1、范围本规范规定了建筑机械与设备产品切削加工件的检验项目、未注尺寸的极限偏差、未注形状和位置公差本规范适用于建筑机械与设备产品的切削加工零件2、引用标准JG/T5011.10-92 建筑机械与设备切削加工通用技术条件GB/T1184-96 形状和位置公差未注公差的规定3、检验项目3.1外观质量3.2加工质量4、检验方法4.1外观质量a)零部件的已加工表面不得有锈蚀及影响性能寿命和外观的磕碰、划伤。
b) 除特殊要求外,加工后的零部件不得有尖锐的棱角和毛刺。
4.2加工质量4.2.1加工、检验所用的量具,必须是经检验部门检验合格的量具。
4.2.2零部件的切削加工必须符合产品图样,工艺规程的规定。
4.2.3图样上未注明倒角应符合JG/T5011.10-92中图1和表1的规定4.2.4图样上未注尺寸的极限偏差,未注公差尺寸的公差带按JG/T5011.10-92表3规定执行,其极限偏差值按JG/T5011.10-92表4执行4.2.5钻孔直径的极限偏差应符合JG/T5011.10-92表4中H14执行4.2.6盲孔的钻孔深度,其允许偏差规定如下:1) 孔深不大于50mm时,为0-3mm2) 孔深大于50mm时,为0-5mm4.2.7加工面至非加工面的尺寸公差带,其值见JG/T5011.10-92表4中JS174.2.8图样上未注的形状和位置公差4.2.8.1未注形状公差未标注的形状公差公差值应按GB/T1184-96的表1中规定的K级选取未标注的圆度和圆柱度的公差值等于标准的直径公差值,但不能大于0.2mm4.2.8.2未注位置公差未标注的同轴度和对称度应按GB/T1184-96中的第5.2条规定,公差等级为K级为标注的平行度、垂直度、倾斜度、圆跳动的公差值应符合 GB/T1184-96的第5.2条规定,公差等级为K级4.2.9在同一中心线或同一圆周上的任意两螺栓孔中心距的极限偏差,未注明时应符合JG/T5011.10-92中图4和表8的规定4.2.10螺孔德轴线对端面的垂直度公差应符合JG/T5011.10-92中图6和表10的规定5 验收规则5.1 A、B类件应逐件检查几何形状与尺寸精度,有一项不符合第4条规定的,为不合格品。
- 1、下载文档前请自行甄别文档内容的完整性,平台不提供额外的编辑、内容补充、找答案等附加服务。
- 2、"仅部分预览"的文档,不可在线预览部分如存在完整性等问题,可反馈申请退款(可完整预览的文档不适用该条件!)。
- 3、如文档侵犯您的权益,请联系客服反馈,我们会尽快为您处理(人工客服工作时间:9:00-18:30)。
机械加工检验规程
1总则
1.1检验人员必须具有一定的专业知识和实际工作经验,且能满足现行产品对检验工作的各项要
求。
1.2检验人员所用的计量器具必须是经计量部门校验合格并在规定周期内。
1.3检验人员验收产品前应熟读相关图样和技术文件,了解零件的关键尺寸及装配关系要点。
1.4检验人员必须严格按照图样和技术文件所规定的要求对零件进行判定。
1.5检验人员应对车间在制品按规定进行标识。
1.6检验人员必须定期(6个月最长1年)参加专业知识培训,学习和接受先进的检测方法,以提
高自身的业务水平。
2目的和范围
通过严格执行三检,“首件检验”、“巡回检验”、“完工检验”将检验工件与工序控制紧密结合,对每一工序的质量问题或可能出现的质量问题不放过,剔除不合格品,使其不能投入下序或出厂,从而达到工序控制目的。
3检验依据:
过程检验的检测依据按检验工艺卡执行。
4检验类别
4.1首件检验:
4.1.1在下述情况下,必须首件检验后,才能开始加工:
4.1.1.1工作班开始加工的第一个工件;
4.1.1.2调换操作者后加工的第一个工件;
4.1.1.3更换(调整)工艺装备或更换模具后加工的第一个工件;
4.1.1.4更换材料批(炉)号后加工的第一个工件;
4.1.1.5代用材料后加工的第一个工件。
4.1.2首件检验的依据:a)工艺图纸或工艺卡片;b)作业指导书(工艺控制点)。
4.1.3检验内容:
4.1.3.1根据检验工艺规程的要求,核对首件产品的质量特性值是否真正符合要求;对首件检验
合格,批准生产加工,首件检验不合格,进行不合格品的处理,同时分析不合格原因,
采取改进措施后生产,产品继续首件检验,直至合格为止。
4.1.4检验要求:
4.1.4.1对首件,根据加工工艺要求,核实首件产品或工件(毛坯)产品的质量特性是否符合要
求。
对首批检查的工件(毛坯),操作者必须做好自检和标识,在操作者缺乏检测手段
时,也应对工件外观质量自检,合格后送检验员检查。
无论在任何情况下,首件检验未
经检验合格,不得进行批量生产或继续加工作业。
4.1.4.2做好首件检验记录,要求按工件种类分类填写首件检验记录,以便追溯。
4.1.4.3检验状态分为:合格、不合格、待检、检后待定;产品标识要求填写“工件名称、规格、
数量、尺寸、首检合格”要素,并放在产品的最顶端。
4.2巡回检验:
4.2.1由检验人员在生产现场,进行日常工艺纪律巡回监督检查,重点监控工序质量和工艺纪律。
4.2.2根据检验工艺规程和作业指导书的要求、检验、核对巡检产品的质量特性值是否真正符合
要求。
4.2.3若巡检某质量特性值不合格,应按《不合格品控制程序》处理,同时。
立即对本次巡检与
上次巡检(或首检)间隔中生产的产品的不合格质量特性值逐件100%检查,剔除不合格品。
4.2.4对巡检中剔除的不合格品按《不合格品控制程序》进行处理。
4.2.5对投入批量生产的工件某尺寸在机加工过程中有争议时,应立即报告生产技术部进行分析
性检查、仲裁性检测,必要时核实模具或工艺卡片,严禁不合格模具或工艺卡继续生产和
现场毛坯流入下道工序。
4.3完工检验(终检)
4.3.1全部加工活动结束后,对半成品或完工的产品、零件进行综合性的核对工作,核对加工件
的工序是否全部完成,有无漏序、跳序的现象存在,并分析原因,采取措施。
4.3.2完工检验依据:a)工艺卡(图)或零件图;b)产品设计图样及作业指导书;c)合同规定或交
货验收技术条件及标准。
4.3.3完工检验的抽样规定:
4.3.3.1完工批抽样以该批总数量的10%,但不低于5件,如果检测样件全部检测项目(质量特
性)均合格,则判定该完工批为合格批。
4.3.3.2如果检测样件的一个(或一个以上)检测项目(质量特性)不符合,则应对整个完工批
产品该检测项目(质量特性)全数(100%)的检验,剔除所有不合格品,剔除不合格品
后的完工批判定为合格批,并在检验卡上记录。
4.3.4完工检验内容和项目:
4.3.4.1检验加工后的几何尺寸;
4.3.4.2检验形状和位置误差;
4.3.4.3检验外观,对零件的倒角、毛刺、磕碰、划伤应予以特别关注;
4.3.4.4检查应有的标识是否齐全、正确,有无漏序、跳序的现象存在,在批量完工件中有无尚
未完工或不同规格的零件混入,并分析产生的原因,采取纠正措施,必要时提出防止再
发生的措施建议。
5检验方法
5.1外径的测量
5.1.1测量零件外径尺寸时,至少应在轴向两个部位进行测量,并进行记录,两次测量的切点交
角应在60°~120°之间,最大与最小半径之差即为该外径圆度误差。
5.1.2当零件同直径长度大于50mm时,应作直线度检查,利用刀口尺工作面与外径母线接触,
观察漏光度,然后对照标准光隙进行判断。
5.1.3当零件同直径长度大于40mm时,应做圆柱度检查,即在同直径长度方向范围内分别取较
大间隔的三个位置进行外径测量,方法同1.1 a,取其中误差值最大两组作记录并计算圆柱
度误差值。
5.2内径测量
5.2.1测量零件内径尺寸时,至少应在轴向三个部位进行测量,并进行记录,三次测量的接点连
线交角应在50°~70°之间,最大与最小半径之差为该内径圆度误差。
5.2.2当同直径长度大于40mm时,应作圆柱度检查,即在同直径长度方向范围内,分别取较大
间隔两位置进行测量,方法同1.2 a,选取其中误差值较大的两组数据记录,并计算圆柱度
误差。
5.3长度测量
5.3.1考虑到端面与轴线的垂直度误差,在测量零件长度时,至少应在轴向两个不同位置上进行
测量并作记录,两次测量的切点连线交角应在60°~120°之间。
5.3.2验收标准:
图样或技术文件未注尺寸公差,按GB1804-m级,未注形位公差按GB1184-10级规定验收。
5.4螺纹测量
5.4.1外螺纹测量
5.4.1.1外螺纹外径方法同5.1.1、5.1.3。
5.4.1.2外螺纹中经用螺纹环规或三针测量。
5.4.1.3外螺纹小径用螺纹环规(同规)检测。
5.4.2内螺纹测量
5.4.2.1内螺纹外径用螺纹塞规(通规)检测。
5.4.2.2内螺纹内径方法见5.2.1。
5.4.2.3内螺纹中径用螺纹塞规检测。
5.4.3螺纹有效长度
内外螺纹的有效长度,应采用螺纹副旋合的方法进行测量。
5.4.4验收标准
5.4.4.1螺纹的大、中、小径应按图样要求的精度等级进行验收。
5.4.4.2螺纹的有效长度公差,按HY/QT001紧固件验收规范中的要求执行。
5.5表面平面检测
5.5.1表面粗糙度检测:
采用粗糙度样块比较法进行比较判断。
5.5.2平面度的检测:
应采用打表法检测,即平板上放置三个可调支撑,将零件测量面朝上放置于支撑点上,调整支撑点,使三点等高(千分表在三点上的读数均为零),打表所测得峰谷值即为该平面的平面度。
5.5.3验收标准:按图样规定的精度等级进行验收。
5.6位置度检测
5.6.1平行度误差检测
5.6.1.1采用厚薄差法,即用外径千分尺测量被测零件各测量位置的厚度,取最大与最小值厚度
之差,作为该平面度误差。
5.6.2垂直度误差检测
5.6.2.1采用比较法测量零件的垂直度,以平板工作面模拟基准轴线,刀口角尺与平面基准面构
成垂直基准,将被测零件放置于刀口状的V形块上,工件一端与挡板固定,将刀口角尺
的工作面与被测零件的平面相靠,观察两侧之间光隙,用标准光隙或塞尺确定其间隙值。
5.6.2.2将被测件在V形块上转一角度,按照5.6.2.1进行测量,如此重复若干次,取其中最大
值为该零件的垂直度误差。