SPC统计过程分析ppt课件
合集下载
SPC统计过程控制及CPK分析[优质PPT]
![SPC统计过程控制及CPK分析[优质PPT]](https://img.taocdn.com/s3/m/9f995c023c1ec5da50e270e2.png)
8
0.136
1.864
9
0.184
1.816
10
0.223
1.777
• 平均值控制图控制界限: • x = S x i /k • • UCL x = µ + A2 R • • LCL x = µ- A2 R(系数都是A2) • 注:µ= x = 所有抽样组平均值的平均值(实际是全部数据的平均) •_ • X i = 第i个抽样组的平均值 • k = 样本个数 • UCL x = 平均值的上控制界限 • LCL x = 平均值的下控制界限 • 全距控制图:控制精密度,或离散程度 • 平均值控制图:控制准确度,或偏离目标值的程度
过程中存在许多波动源,但有一个或几个对质量特性的 影响较大,而其它的影响均很小。 这些强的波动源使X的分布会随时间的变化而发生改变 ,改变分布的位置、或分布的标准差,有时又会使分布 的形状发生变化。 偶然波动是偶然因素引起的,是过程固有的异常波动是 异常因素引起的,非过程所固有。
一个成熟的过程是工厂 的财富
•简单的统计分析可以发现 •采取局部措施 •由制程人员直接加以消除、改善 •大约可以解决15%之制程问题
管制图异常处理步骤
管制图异常 波动来自
首先:排除测量误差
•测量系统原因 测量的重复性
测量的准确度
加工规格偏离
四:加工设定规格正确?
夹具精度
夹具磨损 夹具
夹具位置
•产品原因 二:产品确实不合规格
设备
•5% •22.5% •25% •35% •12.5%
22.5%+25%+12.5%= 60%
59.5
89.5
49.5
成绩出现在这个范围的概率是
99.5
SPC过程能力分析ppt课件

满足要求 可接受 不可接受
受控 1类 2类
不受控 3类 4类
特殊原因变差
普通原因变差
普通原因和特殊原因变差
最新课件
10 10
3、过程能力及过程能力指数概念
过程能力:指过程要素(人、机、料、法、环)已充分标准化,也 就是在受控状态下,实现过程目标的能力。
过程能力指数:是过程能力与过程目标相比较,定量描绘的数值。 过程能力指数表示的方法: Cp:过程均值 与规范中值一致时的过程能力指数。 Cpk:过程均值 与规范中值不一致时的过程能力指数。
最新课件
31 31
2.5.4、过程能力分析:
数据正态,过程不受控,无法直接分析Cp、Cpk;过 程性能指数Pp=0.57,Ppk=0.44,过程能力不足,且趋中 性存在偏差;导致过程性能指数低的主要原因是铝含量控 制偏高,波动大以及特殊原因的波动较多。
导致波动的原因:班组差异性及其他。
最新课件
32 32
判断原则:
一般对于关键产品性能,要求Cpk≥1.67; 一般产品性能,要求Cpk≥1.33; 关键过程特性Cpk≥1.33; 一般过程特性,要求Cpk≥1.0。 分析过程:数据正态且过程受控,同时分析Cp、Cpk;数据不 正态或不受控,同时分析Pp和Ppk;Cp与Cpk,或Pp与Ppk两者相差 大,说明过程趋中性不好。对趋中性不良的过程建议优先改进参 数均值位置,然后从减少波动采取措施。
例如钢包的包龄,连浇炉数,铸坯
最新课件 合格率等。
26
26
2.3.2、与规范界限的比较分析
当直方图的形状呈正常性时,即工序在此时刻处于稳 定状态时,还需要进一步将直方图同规范界限(即公差) 进行比较,以分析判断 工序满足公差的程度。
SPC统计过程控制教材ppt(37张)

– 5、确定各组的频数 – 6、作直方图 – 7、对直方图的观察: 特点, 中间高、两头低、左右对称
7
SPC
3、基础知识
(2)、正态分布 (Normal Distribution) 当抽取的数据个数趋于无穷大而区间宽度趋向于0时,外形轮廓的折线就趋向于光滑的曲
线,即:概率密度曲线。 特点:面积之和等于1。
11
SPC统计过程控制教材(PPT37页)
SPC
• (4)、使用控制图应考虑的问题
– a、控制图用于何处? – b、如何选择控制对象? – c、怎样选择控制图? – d、如何分析控制图? – e、点出界或违反其他准则的处理。 – f、控制图的重新制定。 – g、控制图的保管问题。
SPC统计过程控制教材(PPT37页)
– 1、找出最大值和最小值,确定数据分散宽度 数据分散宽度=(最大值 最小值)
– 2、确定组数 k n
– 3、确定组距 h=(最大值最小值)/组数
– 4、确定各组的边界 第一组的组下限=最小值 最小测量单位的一半 第一组的组上限=第一组的组下限+组距=第二组的组下限 第二组的组上限=第二组的组下限+组距=第三组的组下限,依此类推。
2
SPC
3、为什么要学习SPC(二)?
• 3控制方式与6控制方式的比较:
3
SPC
4、开展SPC工程的步骤
• 培训SPC
– 正态分布等统计基础知识 – 品管七工具:调查表、分层法、散布图、排列图、直方图、因果图、控制图 – 过程控制网图的做法 – 过程控制标准的做法
• 确定关键质量因素
– 对每道工序,用因果图进行分析,造出所有关键质量因素,再用排列图找出 最终产品影响最大的因素,即关键质量因素;
7
SPC
3、基础知识
(2)、正态分布 (Normal Distribution) 当抽取的数据个数趋于无穷大而区间宽度趋向于0时,外形轮廓的折线就趋向于光滑的曲
线,即:概率密度曲线。 特点:面积之和等于1。
11
SPC统计过程控制教材(PPT37页)
SPC
• (4)、使用控制图应考虑的问题
– a、控制图用于何处? – b、如何选择控制对象? – c、怎样选择控制图? – d、如何分析控制图? – e、点出界或违反其他准则的处理。 – f、控制图的重新制定。 – g、控制图的保管问题。
SPC统计过程控制教材(PPT37页)
– 1、找出最大值和最小值,确定数据分散宽度 数据分散宽度=(最大值 最小值)
– 2、确定组数 k n
– 3、确定组距 h=(最大值最小值)/组数
– 4、确定各组的边界 第一组的组下限=最小值 最小测量单位的一半 第一组的组上限=第一组的组下限+组距=第二组的组下限 第二组的组上限=第二组的组下限+组距=第三组的组下限,依此类推。
2
SPC
3、为什么要学习SPC(二)?
• 3控制方式与6控制方式的比较:
3
SPC
4、开展SPC工程的步骤
• 培训SPC
– 正态分布等统计基础知识 – 品管七工具:调查表、分层法、散布图、排列图、直方图、因果图、控制图 – 过程控制网图的做法 – 过程控制标准的做法
• 确定关键质量因素
– 对每道工序,用因果图进行分析,造出所有关键质量因素,再用排列图找出 最终产品影响最大的因素,即关键质量因素;
SPC过程能力分析 ppt课件
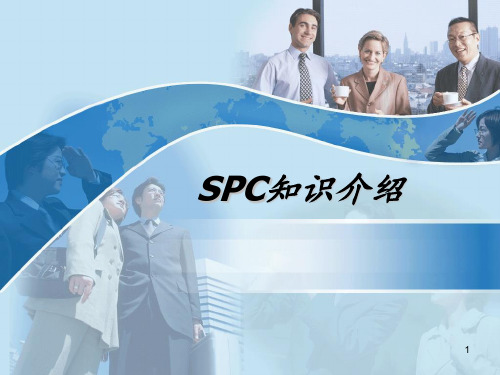
25
2.3 SPC的控制原理
SPC主要是指应用统计分析技术对生产过程进行实时监控, 科学的区分出生产过程中产品质量的偶然波动与异常 波动,从而对生产过程中的异常趋势提出预警,以便 生产管理人员及时采取措施,消除异常,恢复过程的 稳定,从而达到提高和控制质量的目的。
因子 特性
例子
特殊原因(异常波动)
1.机器老化 2.产品设计不良 3.环境不良 4.生产排程不当 5.物料的变异 6.机器的轻微抖动
26
2.3 SPC的控制原理
• 局部措施
• 通常用来消除变异的特殊原因 • 通常由与过程直接相关的人员实施 • 通常可纠正大约15%的过程问题
• 对系统采取措施
• 通常用来消除变异的普通原因 • 几乎总是要求管理措施,以便纠正 • 大约可纠正85%的过程问题
注意点
车胎是否漏气 车胎固定情形如何?
钥匙正确插入钥匙孔
离合器的踩踏感觉如何? 刹车的踩踏感觉如何?
排挡是否在空档?
后视镜、侧镜是否适当? 紧上安全带
核查点
走一圈看车子有否异常?
检核车内配线异常 检核车内异常音 启开引擎盖试试看 是否设定时限装置等 领带歪斜? 头发散乱? 脸不洁 周围有无他人。
19
1
废品率 (%)
1234567 2000
2001
5
2000年7月 连续3个月废品率上升
总经理想要收回他的奖励
废品率 (%)
不但没有保持已有的成绩, 废品率却直线倒退
3
总经理反思: “奖励适得其反.这群人需要强硬的管理!”
2
经理想收回奖励.
1
1234 5 6 7 2000
2001
6
废品率 (%)
2.3 SPC的控制原理
SPC主要是指应用统计分析技术对生产过程进行实时监控, 科学的区分出生产过程中产品质量的偶然波动与异常 波动,从而对生产过程中的异常趋势提出预警,以便 生产管理人员及时采取措施,消除异常,恢复过程的 稳定,从而达到提高和控制质量的目的。
因子 特性
例子
特殊原因(异常波动)
1.机器老化 2.产品设计不良 3.环境不良 4.生产排程不当 5.物料的变异 6.机器的轻微抖动
26
2.3 SPC的控制原理
• 局部措施
• 通常用来消除变异的特殊原因 • 通常由与过程直接相关的人员实施 • 通常可纠正大约15%的过程问题
• 对系统采取措施
• 通常用来消除变异的普通原因 • 几乎总是要求管理措施,以便纠正 • 大约可纠正85%的过程问题
注意点
车胎是否漏气 车胎固定情形如何?
钥匙正确插入钥匙孔
离合器的踩踏感觉如何? 刹车的踩踏感觉如何?
排挡是否在空档?
后视镜、侧镜是否适当? 紧上安全带
核查点
走一圈看车子有否异常?
检核车内配线异常 检核车内异常音 启开引擎盖试试看 是否设定时限装置等 领带歪斜? 头发散乱? 脸不洁 周围有无他人。
19
1
废品率 (%)
1234567 2000
2001
5
2000年7月 连续3个月废品率上升
总经理想要收回他的奖励
废品率 (%)
不但没有保持已有的成绩, 废品率却直线倒退
3
总经理反思: “奖励适得其反.这群人需要强硬的管理!”
2
经理想收回奖励.
1
1234 5 6 7 2000
2001
6
废品率 (%)
统计过程分析(SPC)基础(ppt 33)
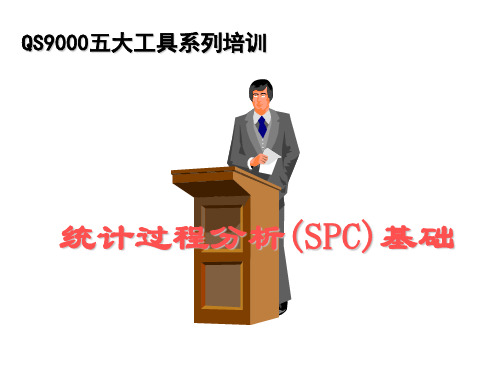
●中位极差图 X~R图, X ~ 表示中位值。现在由于 计算机应用普及,故已淘汰,被均值-标准差图替代。
关注两种错误
一.第一种错误:虚发警报(false alarm)
UCL β α
LCL
二.第二种错误:漏发警报(alarm missing)
三、减少两种错误所造成的损失: ●UCL、LCL距离间隔大,α减小 β增大 ●UCL、LCL距离间隔小,α增大 β减小 ●UCL、LCL距离间隔3σ,α=0.27%
特点: 1、分析过程是否为统计控制状态,调至稳定。 2、过程能力指数是否满足要求?
控制用控制图
等过程调整到稳态后,延长控制图的控制线作为控制用控 制图。应用过程参数判断
工序能力指数的判断
Cp或Cpk
值的大小
判
断
1≤ Cp(Cpk) <1.33 能力尚可,但当Cp接近1时,则可能 产生超差危险,应加以控制
---对每件产品都必须检验,如采用自动化检查和测量的 场合;
---取样费时、昂贵的场合; ---如化工等气体与液体流程式过程,产品均匀,多抽样
无意义;
---特点:灵敏度差
● p控制图:用于控制对象为不合格品率或合格品率的
计件质量指标的场合;
----例如:不合格品率、交货延迟率、缺勤率、邮电的差 错率等;
UCL A
B
CL
C C
B
LCL A
5.连续5点中有4点落在中心线同一侧的C区以外
UCL A
B
CL
C C
B
LCL A
6.连续15点在C区中心线上下
UCL A
B
CL
C C
B
LCL A
7.连续8点在中心线两侧,但无一点在C区中
关注两种错误
一.第一种错误:虚发警报(false alarm)
UCL β α
LCL
二.第二种错误:漏发警报(alarm missing)
三、减少两种错误所造成的损失: ●UCL、LCL距离间隔大,α减小 β增大 ●UCL、LCL距离间隔小,α增大 β减小 ●UCL、LCL距离间隔3σ,α=0.27%
特点: 1、分析过程是否为统计控制状态,调至稳定。 2、过程能力指数是否满足要求?
控制用控制图
等过程调整到稳态后,延长控制图的控制线作为控制用控 制图。应用过程参数判断
工序能力指数的判断
Cp或Cpk
值的大小
判
断
1≤ Cp(Cpk) <1.33 能力尚可,但当Cp接近1时,则可能 产生超差危险,应加以控制
---对每件产品都必须检验,如采用自动化检查和测量的 场合;
---取样费时、昂贵的场合; ---如化工等气体与液体流程式过程,产品均匀,多抽样
无意义;
---特点:灵敏度差
● p控制图:用于控制对象为不合格品率或合格品率的
计件质量指标的场合;
----例如:不合格品率、交货延迟率、缺勤率、邮电的差 错率等;
UCL A
B
CL
C C
B
LCL A
5.连续5点中有4点落在中心线同一侧的C区以外
UCL A
B
CL
C C
B
LCL A
6.连续15点在C区中心线上下
UCL A
B
CL
C C
B
LCL A
7.连续8点在中心线两侧,但无一点在C区中
SPC过程能力分析ppt

绘制控制图
选择合适的控制图类型
根据控制对象和数据特点,选择合适的控制图类型,如均值-极差控制图、单值控制图等。
绘制控制图
将处理后的数据绘制成控制图,并标注中心线、控制限和警告限等。
解读控制图
根据控制图的图形特征和数据指标,对过程能力进行分析和评估,如判断过程的稳定性、识别异常等。
04
SPC结果解读
案例二:SPC在服务业的应用
总结词
服务业是SPC应用的新兴领域之一,SPC在服务业的应用主要 集中在服务流程和客户满意度方面。
详细描述
在服务业中,SPC通过对服务流程的数据统计分析,可以有 效地发现和解决服务中的瓶颈和问题。同时,SPC还可以用 于客户满意度的监测和分析,以了解客户需求和意见,提高 服务质量。
案例三:SPC在其他领域的应用
总结词
SPC还可以应用于其他非制造和非服务业领域,如农业、能源、环保、医疗等。
详细描述
在农业领域,SPC可以用于土壤和水质的分析,以提高农作物的产量和质量。在能源领域,SPC可以用于能源 消耗的监测和分析,以实现能源的优化利用。在环保领域,SPC可以用于环境监测和分析,以保护环境的质量 。在医疗领域,SPC可以用于医疗设备和服务的监测和分析,以提高医疗质量和效率。
减少异常点
针对发现的异常点,需要查明原因并 进行处理。可以采取更换设备、调整 工艺参数、加强原材料管理等措施来 减少异常点。
05
SPC实践案例
案例一:SPC在制造业的应用
总结词
制造业是SPC应用最为广泛和成熟的领域 之一,通过应用SPC可以有效地提高制造 过程的质量和效率。
VS
详细描述
在制造业中,SPC被广泛应用于生产线上 各个环节的质量控制,通过对生产过程中 的数据进行统计分析,可以有效地发现和 解决潜在的质量问题。同时,SPC还可以 用于生产设备的监测和维护,以延长设备 的使用寿命和提高设备的可靠性。
SPC统计方法分析60张课件
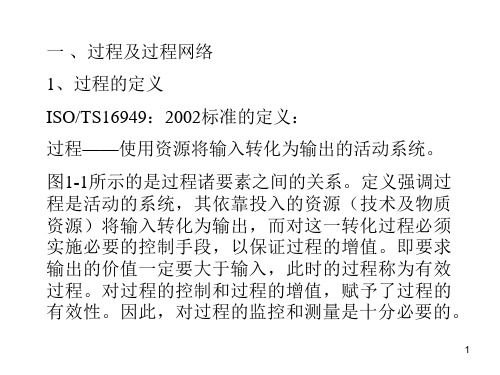
201)首选 途等式是减小偏移量ε
在实际生产过程中采取调整
2)减小质量特性值分布的标准偏差s
标准差s表征质量特性值的离散(质量不一致性)的程度,在实际生产过程中减小标准偏差s往往是困难的,需要通过技术改造、质量改进等措施来实现。
212)减小质量特性值分布的标准偏差s
标准差s表征质量特性
3)放宽公差范围
式中:K为偏移系数,
16b)望目值质量特性且 ,有质量特性值的
表1-1计量值数据过程能力指数计算公式及示例
Tu
Tl
M
TL
TU
M
X
X
17表1-1计量值数据过程能力指数计算公式及示例
M为质量特性的目标值,
19
*注:公式在实际生产过程中,具有普遍的代表性。在大多数
1)首选 途等式是减小偏移量ε
在实际生产过程中采取调整工艺参数的手段,尽可能使质量特性值的分布中心(样本分布的平均值 ) = M 时,计算公式即为
在测量系统中,测量数据的分布中心值与真值的差异(偏移量)称为系统偏差,可以采用线性插补的手段消除。
为不合格品率二项分布的标准偏差。
计点值数据的过程能力指数
式中:CU为允许的缺陷数上限;
为产品的平均缺陷数;
为缺陷数泊松分布的标准偏差。
32b)最佳过程能力
在传统的过程能力等级评价中认定
33
②产品——过程综合能力等级评价
表1-3提出的产品——过程综合能力等评价方法,弥补了传统的过程能力等级评价的不足,使评价更趋向于合理。表1-4给出不同重要度质量特性的过程能力评价及措施。
③非定量工作过程能力指数的计算
27式中:PU为允许的过程不合格品率上限;为过程不合格品率的
在实际生产过程中采取调整
2)减小质量特性值分布的标准偏差s
标准差s表征质量特性值的离散(质量不一致性)的程度,在实际生产过程中减小标准偏差s往往是困难的,需要通过技术改造、质量改进等措施来实现。
212)减小质量特性值分布的标准偏差s
标准差s表征质量特性
3)放宽公差范围
式中:K为偏移系数,
16b)望目值质量特性且 ,有质量特性值的
表1-1计量值数据过程能力指数计算公式及示例
Tu
Tl
M
TL
TU
M
X
X
17表1-1计量值数据过程能力指数计算公式及示例
M为质量特性的目标值,
19
*注:公式在实际生产过程中,具有普遍的代表性。在大多数
1)首选 途等式是减小偏移量ε
在实际生产过程中采取调整工艺参数的手段,尽可能使质量特性值的分布中心(样本分布的平均值 ) = M 时,计算公式即为
在测量系统中,测量数据的分布中心值与真值的差异(偏移量)称为系统偏差,可以采用线性插补的手段消除。
为不合格品率二项分布的标准偏差。
计点值数据的过程能力指数
式中:CU为允许的缺陷数上限;
为产品的平均缺陷数;
为缺陷数泊松分布的标准偏差。
32b)最佳过程能力
在传统的过程能力等级评价中认定
33
②产品——过程综合能力等级评价
表1-3提出的产品——过程综合能力等评价方法,弥补了传统的过程能力等级评价的不足,使评价更趋向于合理。表1-4给出不同重要度质量特性的过程能力评价及措施。
③非定量工作过程能力指数的计算
27式中:PU为允许的过程不合格品率上限;为过程不合格品率的
统计过程控制(SPC)(PPT58页)
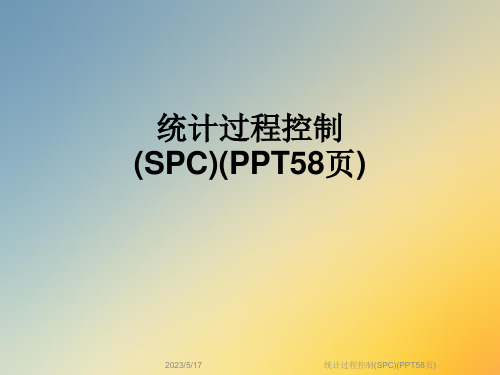
➢ 普通原因 ➢ 特殊原因
江铃汽车股份有限公司
统计过程控制(SPC)(PPT58页)
普通原因 普通原因造成变差的一个原因,它影响被研究过程的所
有单值。(处于统计控制状态;在统计上受控;受控) 造成随着时间的推移具有稳定的且可重复的分布过程中
的许多变差的原因 特点
过程分布将不发生变化 过程的输出是可预测的 过程是稳定、可控的。 采取系统的措施,由管理人员解决问题
江铃汽车股份有限公司
统计过程控制(SPC)(PPT58页)
2.3局部措施和系统措施
措施 对比
对象
系统措施
通常用来消除变差的普 通原因
局部措施
通常用来消除变 差的特殊原因
实施人员
几乎总是要求管理措施, 以便纠正
通常由与过程直 接相关的人员实 施
效果
大约可纠正85%的过程 问题
通常可纠正大约 15%的过程问题
一个可接受的过程必须是处于受控统计控制 状态的且其固有变差(能力)必须小于图纸 的公差
应通过检查并消除变差的特殊原因使过程处 于受统计控制状态,那么性能是可预测的, 变可评定其满足顾客期望的能力。这是持续 改进的基础
江铃汽车股份有限公司
统计过程控制(SPC)(PPT58页)
3.4过程改进循环
2.1过程的理解及过程控制
1.过程—所谓过程是指共同作用以产出输出的供方、生产 者、人、设备、输入材料、方法和环境及使用输出的顾 客的集合。
过程性能取决于:
供方与顾客之间的沟通
过程设计及实施的方式
运作和管理的方式
2.过程的信息
通过分析过程输出可以获得许多与过程性能有关的信息。如过程 是否稳定,过程能力如何。
4.1控制图应用说明
江铃汽车股份有限公司
统计过程控制(SPC)(PPT58页)
普通原因 普通原因造成变差的一个原因,它影响被研究过程的所
有单值。(处于统计控制状态;在统计上受控;受控) 造成随着时间的推移具有稳定的且可重复的分布过程中
的许多变差的原因 特点
过程分布将不发生变化 过程的输出是可预测的 过程是稳定、可控的。 采取系统的措施,由管理人员解决问题
江铃汽车股份有限公司
统计过程控制(SPC)(PPT58页)
2.3局部措施和系统措施
措施 对比
对象
系统措施
通常用来消除变差的普 通原因
局部措施
通常用来消除变 差的特殊原因
实施人员
几乎总是要求管理措施, 以便纠正
通常由与过程直 接相关的人员实 施
效果
大约可纠正85%的过程 问题
通常可纠正大约 15%的过程问题
一个可接受的过程必须是处于受控统计控制 状态的且其固有变差(能力)必须小于图纸 的公差
应通过检查并消除变差的特殊原因使过程处 于受统计控制状态,那么性能是可预测的, 变可评定其满足顾客期望的能力。这是持续 改进的基础
江铃汽车股份有限公司
统计过程控制(SPC)(PPT58页)
3.4过程改进循环
2.1过程的理解及过程控制
1.过程—所谓过程是指共同作用以产出输出的供方、生产 者、人、设备、输入材料、方法和环境及使用输出的顾 客的集合。
过程性能取决于:
供方与顾客之间的沟通
过程设计及实施的方式
运作和管理的方式
2.过程的信息
通过分析过程输出可以获得许多与过程性能有关的信息。如过程 是否稳定,过程能力如何。
4.1控制图应用说明
SPC-统计方法分析(PPT 60张)
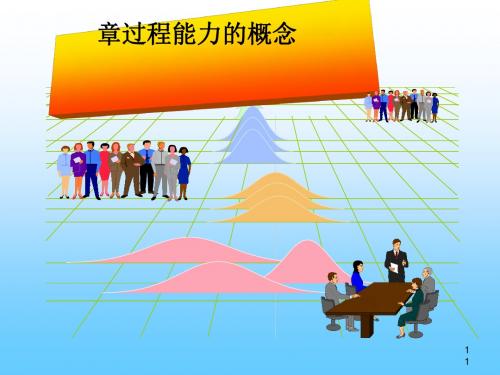
围来提高过程能力必须持非常慎重的态度,轻易
不可采用。只有在通过科学方法验证,确认原设 计的公差范围过严的情况下方可采取。放宽公差 范围属于设计更改的工作内容,必须按业企业质 量体系文件所规定的程序进行。
22
C)望小值质量特性时
c pu TU X 3s
d)望大值质量特性时
c pu
X TL 3s
27
a)在质量指标为望小值时 工作要求的质量标准 Cp 工作实际达到的质量水 平 b)在质量指标为望大值时
工作实际达到的质量水 平 Cp 工作要求的质量
(3)过程能力的等级评定 根据过程能力指数的实际水平评价过程能力,是 普遍采用的评价方式。
28
①传统的过程能力等级评价 在相当长的时间内,无意采用表1-2所示的传统的 过程能力等级评价方式。该评价方式具有以下两点 不足之处: 表1-2 传统的过程能力等级评价表 等级 特级
途径公式的结构为分式,欲提高计算结果应采取增大
分子或减小分母的方法。公式右侧的分式中有三个变
量,因此提高过程力将有三个途径
19
1)首选 途等式是减小偏移量ε 在实际生产过程中采取调整工艺参数的手段, 尽可能使质量特性值的分布中心(样本分布的
平均值 ) = M 时,计算公式即为
T Cp 6S
X
在测量系统中,测量数据的分布中心值与 真值的差异(偏移量)称为系统偏差,可 以采用线性插补的手段消除。
23
表1-1概括总结了以上四种情况的过程能力指数的计算
并给出相关案例。
*注:望目值质量特性:给定双向公差TU和TL,有目标
值
M
与目标值相等为最佳状态。大多数质量特性均属于望 目值质量特性。 望小值质量特性:给定单向公差TU,要求产品质量特
SPC统计分析.pptx
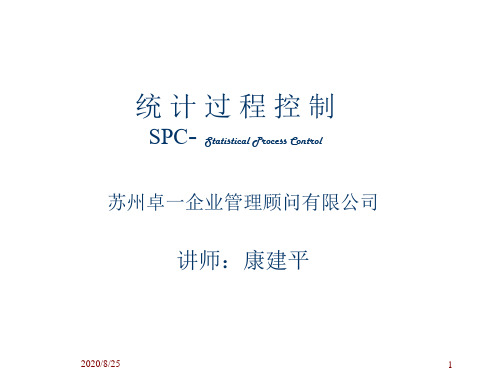
1984年日本名古屋工业大学调查了115家日 本各行各业的中小型工厂,结果发现平均 每家工厂采用137张控制图;
美国柯达彩色胶卷公司有5000多名职工,一 共应用了35000张控制图,平均每名职工 做七张控制图
2020/8/25
9
SPC&SQC
针对过程的重要控制 参数所做的才是SPC
原料
PROCESS
測量 結果
针对产品所做的 仍只是在做SQC
2020/8/25
10
SPC概要说明
目的:寻找有效的方法来提供产品和服务, 并不断在价值上得以改进;
目标:是达到顾客满意(包括内部和外部 顾客);
对象:从事统计方法应用的管理人员;
范围:基本统计方法包括与统计过程控制 及过程能力分析有关的方法,但不是全 部
2020/8/25
3
控制图的历史
控制图是1924年由美国品管大师W.A. Shewhart博 士发明。因其用法简单且效果显著,人人能用, 到处可用,遂成为实施质量管理时不可缺少的 主要工具,当时称为(Statistical Quality Control)。
2020/8/25
4
控制图的历史
休哈特在20世纪20年代提出了过程控制理论 以及监视和控制过程的工具--控制图;
单值(Individual) 一个单个的单位产品或一个特性的一次测量,通 常用符号 X 表示。
2020/8/25
14
SPC常用术语解释
中心线(Central Line)
控制图上的一条线,代表所给数据平均值。
过程均值(Process 一个特定过程特性的测量值分布的位置即为过程均
Average)
值,通常用 X 来表示。
统计过程控制 SPC- Statistical Process Control
美国柯达彩色胶卷公司有5000多名职工,一 共应用了35000张控制图,平均每名职工 做七张控制图
2020/8/25
9
SPC&SQC
针对过程的重要控制 参数所做的才是SPC
原料
PROCESS
測量 結果
针对产品所做的 仍只是在做SQC
2020/8/25
10
SPC概要说明
目的:寻找有效的方法来提供产品和服务, 并不断在价值上得以改进;
目标:是达到顾客满意(包括内部和外部 顾客);
对象:从事统计方法应用的管理人员;
范围:基本统计方法包括与统计过程控制 及过程能力分析有关的方法,但不是全 部
2020/8/25
3
控制图的历史
控制图是1924年由美国品管大师W.A. Shewhart博 士发明。因其用法简单且效果显著,人人能用, 到处可用,遂成为实施质量管理时不可缺少的 主要工具,当时称为(Statistical Quality Control)。
2020/8/25
4
控制图的历史
休哈特在20世纪20年代提出了过程控制理论 以及监视和控制过程的工具--控制图;
单值(Individual) 一个单个的单位产品或一个特性的一次测量,通 常用符号 X 表示。
2020/8/25
14
SPC常用术语解释
中心线(Central Line)
控制图上的一条线,代表所给数据平均值。
过程均值(Process 一个特定过程特性的测量值分布的位置即为过程均
Average)
值,通常用 X 来表示。
统计过程控制 SPC- Statistical Process Control
统计过程分析(SPC).ppt
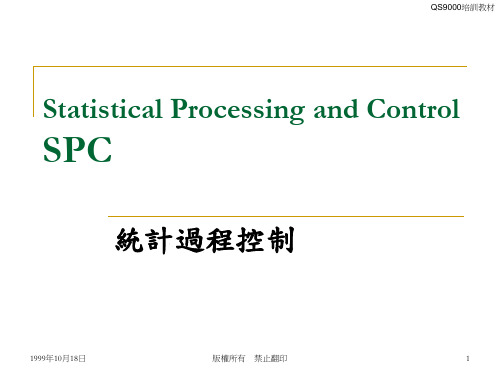
1.收集 收集數據并畫在圖上 UCL 2.控制 根據過程數據計算試驗控制限
識別變差的特殊原因并采取措施
3.分析及改進
LCL
確定普通原因變差的大小并采取減少它的措 施
1999年10月18日
版權所有 禁止翻印
9
統計過程控制概述
控制圖的益處
合理使用控制圖能﹕ 供正在進行過程控制的操作者使用。
有助于過程在質量上和成本上能持續地﹐可預測地保持下去。 使過程達到﹕更高的質量﹑更低的單件成本﹑更高的有效能力。
1999年10月18日
版權所有 禁止翻印
3
統計過程控制概述
控制
兩種過程控制模型和控制策略﹕ 缺陷檢測過程模型﹑具有反饋的過程控制模型
缺陷檢測過程模型
4M1E
過程
產品 /服 務
檢驗
報廢或返工
是否合格
控制策略﹕控制輸出﹐事后把關
顧客
1999年10月18日
版權所有 禁止翻印
4
統計過程控制概述
控制
蹤几個過程流。
☆ :連續三點之中有兩點落在A區或甚至於A區以外者 (在中心線之同側三個連
續點中有兩點出現在兩個標準差之外者).
+3
. . . . UCL
A區
+2 +1
. B區
C區
. CL
1999年10月18日
版權所有 禁止翻印
17
統計過程控制―控制圖
控制圖的制作及應用
(以X―R圖為例)
☆. :連續五點之中有四點落在B區或甚至於B區以外者 (在中心線之同側五個
過程控制要點
屬于系統的問題不要去責難現場人員﹐要由系統采取措施(理解什么是”控制不足”)。 考慮經濟因素﹐做出合理的決定。 過程控制系統應能提供正確的統計信息。 有用的特殊原因變差﹐應該保留。
SPC统计过程控制入门分析(ppt 42页)
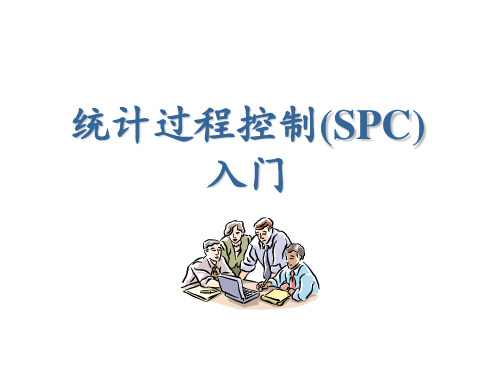
如果在X上做得很好,那么产品的过程能力提高,成本下降,投诉减少。
正态分布简介
波动总是存在的,波动是对称的钟形结构。
对称的钟形结构,统计语言称之为正态分布。
生产过程中产品质量特性服从正态分布。
1.20
1.40
1.70
正态分布的形状不变,则合格品率稳定,过程受控。
举例:Nikon 1.5AS 厚度 (1.4mm, +0.3 -0.2)
统计过程控制(SPC) 入门
课程大纲
• 什么是SPC • 为什么要进行过程控制 • 正态分布简介 • 过程能力指数 • 常见的直方图形态 • 控制图介绍 • Xbar-R控制图的制作 • 控制图的判读 • 使用控制图的注意事项
什么是SPC?
SPC(Statistical Process Control)统计过程控制,就是利用统计 技术对生产过程进行监控,通过检测数据的收集和分析,从而对生 产过程的异常及时告警,以便采取措施及时消除异常,恢复过程的 稳定,达到,达到保证和提高质量的目的。
过程能力-Cp
过程能力指数Cp: 过程的加工质量满足技术标准的能力
。
• 双侧规格
LSL
T UCL LCL
UCL
标准差
CP
T 6S
SU SL 6S
(上限规格)—(下限规格) 6×(标准偏差)
X 平均数
过程能力指数-Cp
单侧规格
• 上限规格
CPU
UCL X 3S
(上限规格)—(平均值) 3×(标准偏差)
正态分布简介
规格之上下限
LSL
USL
相对于目标规范发生变差的频率
SIGMA (s ) 是对离目
标值偏离程度的度量
统计过程分析(SPC)基础(ppt33)

工序能力指数的判断
Cp或Cpk
值的大小
判
断
1≤ Cp(Cpk) <1.33 能力尚可,但当Cp接近1时,则可能 产生超差危险,应加以控制
Cp(Cpk)=1.33 理想状态
Cp(Cpk)≥1.33 能力充足
Cp(Cpk) <1
尺寸分布不能满足公差要求,应立即 采取措施,改变工艺条件或严格进行 全数检查,也可考虑放宽标准
数据的统计分析
示例:
组数 数据1 数据2 数据3 数据4 均值 极差 标准差 第一组 48 48 52 52 50 4 2.3 第二组 48 50 50 52 50 4 1.6 第三组 45 46 54 55 50 10 5.2
分布 控制图代号 控制图名称
备注
正态
分布
(计 量值)
X R
均值—极差控制 图
无意义;
---特点:灵敏度差
● p控制图:用于控制对象为不合格品率或合格品率的
计件质量指标的场合;
----例如:不合格品率、交货延迟率、缺勤率、邮电的差 错率等;
●计量控制图:
由于计算机的应用普及,X s 控制图的计算机毫无困难,而 且无论样本是否大于10,X s 图计算的结果都是精确的,故 均值标准差图完全可以代替均值极差图。
关注两种错误
一.第一种错误:虚发警报(false alarm)
UCL β α
LCL
二.第二种错误:漏发警报(alarm missing)
三、减少两种错误所造成的损失: ●UCL、LCL距离间隔大,α减小 β增大 ●UCL、LCL距离间隔小,α增大 β减小 ●UCL、LCL距离间隔3σ,α=0.27%
-----连续25个点,界外点数d=0 -----连续35个点,界外点数d≤1 -----连续100个点,界外点数d≤2 ●分析判稳原则
- 1、下载文档前请自行甄别文档内容的完整性,平台不提供额外的编辑、内容补充、找答案等附加服务。
- 2、"仅部分预览"的文档,不可在线预览部分如存在完整性等问题,可反馈申请退款(可完整预览的文档不适用该条件!)。
- 3、如文档侵犯您的权益,请联系客服反馈,我们会尽快为您处理(人工客服工作时间:9:00-18:30)。
系统抽样:将20箱零件倒在一起,混合均匀,并将零件从1~ 1000编号,然后用查随机数表或抽签的办法先决定 起始编号,按相同的尾数抽取100个零件组成样 本。
分层抽样:20箱零件,每箱都随机抽取5个零件,共100个组成 样本。
整群抽样:先从20箱零件随机抽出2箱,该2箱零件组成样本。
7
一、集中量数:一群数据之代表值,表示数据的集中位置。
3
什么是SPC?
■ Statistical:(统计)
以概率统计学为基础,用科学的方法分析数据,得出结论;
■ Process: (过程)有输入-输出的一系列的活动; ■ Control: (控制)事物的发展和变化是可预测的;
抽
样
生产过程
检
验
样本
数据
在管制图中发现不正常状态
管制图
调整品质
UCL CL
LCL
10
Process:(过程)
制程控制系统 -- 有反馈的过程控制系统模型
过程的呼声
人员 设备 材料 方法 环境
输入
统计方法
我们工作 的方式/资 源的融合
过程/系统
产品或服务
顾客
识别不断变化的需 求量和期望
输出
顾客的呼声
11
过程的稳定性:
■稳定过程:产品质量 质量特性的变异是在 可预测的统计控制 范围之内;
什么。 • 3. 按时间序列展示过程的个性/表现。 • 4. 设计用来区分信号与噪音。 • 5. 侦测均值及/或标准差的变化。 • 6. 用于决定过程是稳定的(可预测的)或 失控的
(不可预测的)。
19
控制图不是
• 1. 不是能力分析的替代工具。 • 2. 在来料检验的过程中很难用到 • 4. 不应与运行图或预控制图混淆。
Statistical Process control
统计过程控制 SPC
1
课程目标
了解统计基本概念 了解控制图原理 计量型与计数型控制图的作法与适用范围 控制图的选用原则 过程的特性及过程能力 Ppk 和 Cpk 之间的区别以及了解如何计算这些指
数。
2
课程重点
Statistical Process
总体-N
样本-n
μ 总体平均值
X- bar 样本平均值
规格 过程
USL
UCL
SL
CL
LSL
LCL
Ca Cp Cpk
Control
计量值: 均值-极差控制图 中位数-极差控制图 单值-移动极差控制图 均值-标准差控制图 计数值 不合格品率控制图(P图) 不合格品数控制图(Pn图) 缺陷数控制图(c图) 单位缺陷数控制图( µ图)
过程受控
■不稳定过程:产品质量质 量特性的变异无法以统计 方法来预测;
过程失控
12
过程变差:包含普通原因和特殊原因
13
14
15
控制 Control
16
一、 控制图概述
控制图(Control chart)就是对生产过程的 关键质量特性值进行测定、记录、评估并监测过 程是否处于控制状态的一种图形方法。 根据假设 检验的原理构造一种图,用于监测生产过程是否 处于控制状态。它是统计质量管理的一种重要手 段和工具。
?
9
1.极差(Range)-R:度量样本数据分散范围的量, 公式:R=Xmax-Xmin(样本或总体中的最大值减最小值)。 2.标准差(σ.S):样本数据离散程度的统计量,利用每个样本数据偏离其中心位置 的大小来表示离散程度,较精确。
国际标准化组织规定,把样本方差的正平方根作为样本标准偏差,用符号S 来表示。其计算公式:
二、样本(子样):是指从总体中随机抽取出来并且要对它进行详细 研究分析的一部分个体(产品);
1.样本是由1个或若干个样品组成的。 2.样本容量(样本大小):样本中所含的样品数目,常用n表示。
N
n
抽样:是指从总体中随机 抽取样品组成样本
μ
的活动过程。
σ
x s
5
数据、样本和总体的关系
目的
总体
对工序进行分析
意义:1.次数分配中心的位置,又称位置量数。 2.计算法由【平均方式】而得。 3.各种结果皆向其中心集中,也称集中趋势量数。
种类:平均数、中位数、众数
8
3.众数(Mode):-Mo
一群数据中,出现次数最多次的数值。若二相邻两数值均为出现次数最多的数值, 则取平均值。
频数最大的数量,用以消除极大及极小值的影响。
20
三、控制图目的
• 运用控制图的目的之一就是,通过观察控制图上产品质 量特性值的分布状况,分析和判断生产过程是否发生了异 常,一旦发现异常就要及时采取必要的措施加以消除,使 生产过程恢复稳定状态。也可以应用控制图来使生产过程 达到统计控制的状态。产品质量特性值的分布是一种统计 分布.因此,绘制控制图需要应用概率论的相关理论和知 识。
无 限
工序
控制
总 体
对一批产品质量进 有 一批
行判断,确定是否
限 总
产品
合格
体
样本
一批 半成品
样本
判断
数据
数据
样本 判断
数据
6
案例
某种成品零件分装在20个零件箱装,每箱各装50个,总共是 1000个。如果想从中取100个零件作为样本进行测试研究。
简单随机抽样:将20箱零件倒在一起,混合均匀,并将零件从 1~ 1000编号,然后用查随机数表或抽签的办 法从中抽出编号毫无规律的100个零件组成样 本。
二、差异量数:以一个数字来代表一群统计数据内差异或离散程度。离散趋 势指标。
目的:若一群数据差异量大,则平均数代表性小,反之则大,因此为 了了解一群数据之特性,除了计算平均数外,还必须计算差异量数的 大小。
种类:极差、标准差 案例说明:
组别 1
2
3
4
结果
A 50 50 50 50
?
B 0 100 0 100
4
统计分析的基本概念
一、总体(母体):是指在某一次统计分析中研究对象的全体。 1.有限总体:被研究对象是有限的,如一批产品的总数; 2.无限总体:被研究对象是无限的,如某个企业、某个生产过程 从前、现在、将来生产的全部产品。 3.个体:组成总体的每个单元(产品)叫做个体 4.总体含量(总体大小):总体中所含的个体数,常用N表示。
17
二、控制图诞生
1. 美国W. A. Shewhart博士于1924年5月16日发明了第一 张管制图,开启了统计品管的新时代.
• 区分过程中的正常变异或异常变异,并判断过程是否处 于控制状态的一种工具.
18
控制图是:
• 1. 实时图表化反馈过程的工具。 • 2. 设计的目的是告诉操作者什么时候做什么或不做
分层抽样:20箱零件,每箱都随机抽取5个零件,共100个组成 样本。
整群抽样:先从20箱零件随机抽出2箱,该2箱零件组成样本。
7
一、集中量数:一群数据之代表值,表示数据的集中位置。
3
什么是SPC?
■ Statistical:(统计)
以概率统计学为基础,用科学的方法分析数据,得出结论;
■ Process: (过程)有输入-输出的一系列的活动; ■ Control: (控制)事物的发展和变化是可预测的;
抽
样
生产过程
检
验
样本
数据
在管制图中发现不正常状态
管制图
调整品质
UCL CL
LCL
10
Process:(过程)
制程控制系统 -- 有反馈的过程控制系统模型
过程的呼声
人员 设备 材料 方法 环境
输入
统计方法
我们工作 的方式/资 源的融合
过程/系统
产品或服务
顾客
识别不断变化的需 求量和期望
输出
顾客的呼声
11
过程的稳定性:
■稳定过程:产品质量 质量特性的变异是在 可预测的统计控制 范围之内;
什么。 • 3. 按时间序列展示过程的个性/表现。 • 4. 设计用来区分信号与噪音。 • 5. 侦测均值及/或标准差的变化。 • 6. 用于决定过程是稳定的(可预测的)或 失控的
(不可预测的)。
19
控制图不是
• 1. 不是能力分析的替代工具。 • 2. 在来料检验的过程中很难用到 • 4. 不应与运行图或预控制图混淆。
Statistical Process control
统计过程控制 SPC
1
课程目标
了解统计基本概念 了解控制图原理 计量型与计数型控制图的作法与适用范围 控制图的选用原则 过程的特性及过程能力 Ppk 和 Cpk 之间的区别以及了解如何计算这些指
数。
2
课程重点
Statistical Process
总体-N
样本-n
μ 总体平均值
X- bar 样本平均值
规格 过程
USL
UCL
SL
CL
LSL
LCL
Ca Cp Cpk
Control
计量值: 均值-极差控制图 中位数-极差控制图 单值-移动极差控制图 均值-标准差控制图 计数值 不合格品率控制图(P图) 不合格品数控制图(Pn图) 缺陷数控制图(c图) 单位缺陷数控制图( µ图)
过程受控
■不稳定过程:产品质量质 量特性的变异无法以统计 方法来预测;
过程失控
12
过程变差:包含普通原因和特殊原因
13
14
15
控制 Control
16
一、 控制图概述
控制图(Control chart)就是对生产过程的 关键质量特性值进行测定、记录、评估并监测过 程是否处于控制状态的一种图形方法。 根据假设 检验的原理构造一种图,用于监测生产过程是否 处于控制状态。它是统计质量管理的一种重要手 段和工具。
?
9
1.极差(Range)-R:度量样本数据分散范围的量, 公式:R=Xmax-Xmin(样本或总体中的最大值减最小值)。 2.标准差(σ.S):样本数据离散程度的统计量,利用每个样本数据偏离其中心位置 的大小来表示离散程度,较精确。
国际标准化组织规定,把样本方差的正平方根作为样本标准偏差,用符号S 来表示。其计算公式:
二、样本(子样):是指从总体中随机抽取出来并且要对它进行详细 研究分析的一部分个体(产品);
1.样本是由1个或若干个样品组成的。 2.样本容量(样本大小):样本中所含的样品数目,常用n表示。
N
n
抽样:是指从总体中随机 抽取样品组成样本
μ
的活动过程。
σ
x s
5
数据、样本和总体的关系
目的
总体
对工序进行分析
意义:1.次数分配中心的位置,又称位置量数。 2.计算法由【平均方式】而得。 3.各种结果皆向其中心集中,也称集中趋势量数。
种类:平均数、中位数、众数
8
3.众数(Mode):-Mo
一群数据中,出现次数最多次的数值。若二相邻两数值均为出现次数最多的数值, 则取平均值。
频数最大的数量,用以消除极大及极小值的影响。
20
三、控制图目的
• 运用控制图的目的之一就是,通过观察控制图上产品质 量特性值的分布状况,分析和判断生产过程是否发生了异 常,一旦发现异常就要及时采取必要的措施加以消除,使 生产过程恢复稳定状态。也可以应用控制图来使生产过程 达到统计控制的状态。产品质量特性值的分布是一种统计 分布.因此,绘制控制图需要应用概率论的相关理论和知 识。
无 限
工序
控制
总 体
对一批产品质量进 有 一批
行判断,确定是否
限 总
产品
合格
体
样本
一批 半成品
样本
判断
数据
数据
样本 判断
数据
6
案例
某种成品零件分装在20个零件箱装,每箱各装50个,总共是 1000个。如果想从中取100个零件作为样本进行测试研究。
简单随机抽样:将20箱零件倒在一起,混合均匀,并将零件从 1~ 1000编号,然后用查随机数表或抽签的办 法从中抽出编号毫无规律的100个零件组成样 本。
二、差异量数:以一个数字来代表一群统计数据内差异或离散程度。离散趋 势指标。
目的:若一群数据差异量大,则平均数代表性小,反之则大,因此为 了了解一群数据之特性,除了计算平均数外,还必须计算差异量数的 大小。
种类:极差、标准差 案例说明:
组别 1
2
3
4
结果
A 50 50 50 50
?
B 0 100 0 100
4
统计分析的基本概念
一、总体(母体):是指在某一次统计分析中研究对象的全体。 1.有限总体:被研究对象是有限的,如一批产品的总数; 2.无限总体:被研究对象是无限的,如某个企业、某个生产过程 从前、现在、将来生产的全部产品。 3.个体:组成总体的每个单元(产品)叫做个体 4.总体含量(总体大小):总体中所含的个体数,常用N表示。
17
二、控制图诞生
1. 美国W. A. Shewhart博士于1924年5月16日发明了第一 张管制图,开启了统计品管的新时代.
• 区分过程中的正常变异或异常变异,并判断过程是否处 于控制状态的一种工具.
18
控制图是:
• 1. 实时图表化反馈过程的工具。 • 2. 设计的目的是告诉操作者什么时候做什么或不做