RTM工艺
RTM成型工艺及分类介绍

RTM成型工艺及分类介绍1、RTM成型工艺与分类RTM是指低粘度树脂在闭合模具中流动、浸润增强材料并固化成形的一种工艺技术,属于复合材料的液体成形或结构液体成形技术范畴。
其具体方法是在设计好的模具中,预先放入经合理设计、剪裁或经机械化预成形的增强材料,模具需有周边密封和紧固,并保证树脂流动顺畅;闭模后注入定量树脂,待树脂固化后即可脱模得到所期望产品。
SMC、BMC模压、注射成型、RTM、VEC技术都属闭模成型工艺。
由于环境法的制定和对产品要求的提高使敞模成型复合材料日益受到限制,促使了闭模成型技术的应用,近年来尤其促进了RTM技术的革新和发展。
2、RTM的类型RTM工艺起始于上世纪50年代,目前,RTM成型工艺己广泛应用于建筑、交通、电讯、卫生、航天航空等领域。
下面介绍几种RTM技术。
01、RTM,树脂传递模塑。
该技术源自聚氨酯技术,成型时关闭模具,向预制件中注入树脂,玻纤含量低,约20-45%。
02、VARIT,真空辅助树脂传递注塑。
该技术利用真空把树脂吸入预制件中,同时也可压入树脂,真空度约10-28英寸汞柱。
03、VARTM,真空辅助树脂传递注塑。
制品孔隙一般较少,玻纤含量可增高。
04、VRTM,真空树脂传递模塑。
05、VIP,真空浸渍法。
06、VIMP,可变浸渍塑法。
树脂借助真空或自重移动,压实浸渍。
07、TERTM,热膨胀RTM。
在预制件中插入芯材,让树脂浸渍并对模具与成形品加热。
芯材受热膨胀,压实铺层。
利用这种压实作用,结合表面加压成型。
08、RARTM,橡胶辅助RTM。
在TERTM方法中不用芯材而用橡胶代之。
橡胶模具压紧成型品,使孔隙大大减少,玻纤含量可高达60-70%。
09、RIRM,树脂注射循环模塑。
真空与加压结合,向多个模具交替注入树脂,使树脂循环,直至预制件被充分浸透。
10、CIRTM,Co-Injection RTM。
共注射RTM,可注入几种不同的树脂,也可使用几种预制件,可利用真空袋和柔性表面的模具。
RTM技术工艺详解
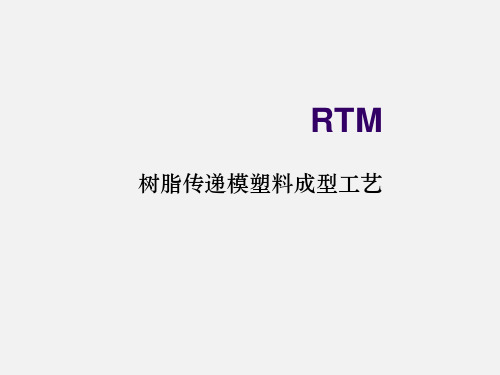
增强材料
由于在RTM成型过程中,增强材料在模具型腔 中要经过带压树脂流动充模过程,会带动或充 散纤维,造成制品出现“冲浪”或“跑道”现 象。因此,为保证制品质量,RTM工艺适用于 采用长纤维和连续纤维织物作为增强材料
工艺因素
影响RTM工艺的因素
VARTM(真空辅助RTM)工艺
一般RTM工艺在树脂注入时,模具型腔内可积起几吨压力。 通过使用了真空,模具内形成这种压力的趋势得到了减少, 因而增加了使用更轻模具的可能性,真空的使用也可提高 玻璃纤维的含量,而且有助于树脂对纤维的浸渍。纤维含 量可达65%以上,空隙率小于2%。
VARTM工艺过程
ห้องสมุดไป่ตู้合模
注射树脂
RTM – 脱模
RTM的优点
无需胶衣涂层即可为 构件提供光滑表面, 能制造出具有良好表 面的高精度复杂制品
模具制造及选材灵 活性大,设备及模 具投资小,产品只 需做小的修边
产品铺层过程中 可加入嵌件及对 局部进行加强
制品纤维含量高, 空隙率低(<0.2%)
成型过程中挥发物少, 车间环境及气味较好
在制作高质量RTM制品时,会让出口流出一定 量的树脂以后才结束充模。
目的是改善树脂对纤维的浸渍程度及排出微观 气泡。即改善了纤维与树脂的物理结合强度, 又改善了制品的密实程度。
一般浪费树脂量可达模制品重量的1/3~2/3。
注胶压力
压力的高低决定模具的材料要求和结构设计, 高压力需要高强度、高刚度和大的合模力。
基体树脂
室温或工作温度下具有低的粘度(小于1.0Pas) 及一定长的适用期
树脂对增强材料具有良好的浸润性、匹配性、 粘附性
树脂在固化温度下具有良好的反应性且后处理 温度不应过高
RTM工艺及模具

轻质RTM工艺及模具制作一.轻质RTM成型工艺原理及技术特点1.工艺原理轻质RTM就是真空辅助带压低粘度树脂在闭合模具中流动浸润增强材料并固化成型的一种工艺技术,其成型压力不足1kg/cm2。
树脂和固化剂通过注射机计量泵按配比输出带压液体在静态混合器中混合均匀,然后在真空辅助下注入已合理铺放好的纤维增强体的闭合模中,模具用真空对周边进行密封和合模,并保证树脂流动顺畅,然后进行固化。
该工艺需要二级真空,第一级真空(真空度为667毫米汞柱)完成上下模的闭合动作,第二级真空(真空度为376毫米汞柱)在树脂注射过程中辅助树脂的流动和对增强材料的浸润。
2.技术特点轻质RTM具有很多传统RTM相似的优点,比如生产效率和产品质量可以得以提高;可以得到两面光,大尺寸的产品;减少树脂有害成份对人体和环境的毒害。
由于轻质RTM是低压真空辅助成型工艺,所以与传统RTM相比,模具制作工艺大大简化,既方便又快捷。
模具无需如传统RTM那样进行钢结构的加强,下模为三明治夹芯结构,具有较高的刚度以防止树脂在注射过程中模具产生任何变形,同时三明治夹芯结构可以有效保存产品固化时产生的热量,有利于后续产品的快速固化,缩短生产周期。
而上模更为简单,可作成轻质、半刚性的结构,这样非常有利于频繁的脱模、合模的操作。
二.模具的制作1.模具制作环境的要求以及原料的选择a.环境环境温度:理想的范围为25±3℃。
相对湿度:不能大于60%。
制作车间:应保持比产品生产区更高的清洁度与日常维护。
b.材料对于该工艺所需要的材料我们推荐如下:①主要材料胶衣:ccp-071(具有优良的耐热能力,HDT为160-173℃)模具树脂:RM2000(快速固化,快速制造模具,低收缩,降低模具成本)F-010(环氧改性乙烯基树脂,良好的强度和耐热性,以及低收缩率)表面毡:300g/m2无碱短切毡:450g/m2轻木:用于提高模具的刚性并减轻重量蜡片:用于控制模腔的厚度,良好的厚度均匀性。
试介绍树脂传递法(rtm)及该工艺过程的特点

试介绍树脂传递法(rtm)及该工艺过程的特点下载提示:该文档是本店铺精心编制而成的,希望大家下载后,能够帮助大家解决实际问题。
文档下载后可定制修改,请根据实际需要进行调整和使用,谢谢!本店铺为大家提供各种类型的实用资料,如教育随笔、日记赏析、句子摘抄、古诗大全、经典美文、话题作文、工作总结、词语解析、文案摘录、其他资料等等,想了解不同资料格式和写法,敬请关注!Download tips: This document is carefully compiled by this editor. I hope that after you download it, it can help you solve practical problems. The document can be customized and modified after downloading, please adjust and use it according to actual needs, thank you! In addition, this shop provides you with various types of practical materials, such as educational essays, diary appreciation, sentence excerpts, ancient poems, classic articles, topic composition, work summary, word parsing, copy excerpts, other materials and so on, want to know different data formats and writing methods, please pay attention!树脂传递法(RTM)是一种常用于复杂结构的树脂浸渍工艺。
rtm工艺技术
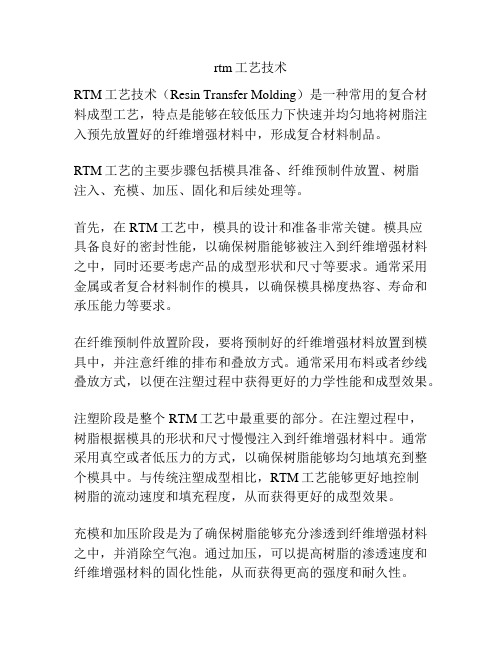
rtm工艺技术RTM工艺技术(Resin Transfer Molding)是一种常用的复合材料成型工艺,特点是能够在较低压力下快速并均匀地将树脂注入预先放置好的纤维增强材料中,形成复合材料制品。
RTM工艺的主要步骤包括模具准备、纤维预制件放置、树脂注入、充模、加压、固化和后续处理等。
首先,在RTM工艺中,模具的设计和准备非常关键。
模具应具备良好的密封性能,以确保树脂能够被注入到纤维增强材料之中,同时还要考虑产品的成型形状和尺寸等要求。
通常采用金属或者复合材料制作的模具,以确保模具梯度热容、寿命和承压能力等要求。
在纤维预制件放置阶段,要将预制好的纤维增强材料放置到模具中,并注意纤维的排布和叠放方式。
通常采用布料或者纱线叠放方式,以便在注塑过程中获得更好的力学性能和成型效果。
注塑阶段是整个RTM工艺中最重要的部分。
在注塑过程中,树脂根据模具的形状和尺寸慢慢注入到纤维增强材料中。
通常采用真空或者低压力的方式,以确保树脂能够均匀地填充到整个模具中。
与传统注塑成型相比,RTM工艺能够更好地控制树脂的流动速度和填充程度,从而获得更好的成型效果。
充模和加压阶段是为了确保树脂能够充分渗透到纤维增强材料之中,并消除空气泡。
通过加压,可以提高树脂的渗透速度和纤维增强材料的固化性能,从而获得更高的强度和耐久性。
固化阶段是将树脂完全固化,使纤维增强材料和树脂成为一个整体。
通常采用热固化或者光固化的方式,通过加热或者紫外线照射等方法,使树脂固化并与纤维增强材料牢固地结合在一起。
固化后的制品具有较高的强度、刚度和耐腐蚀性能,适用于各种工程应用。
最后,进行后续处理,如切割、修整、表面处理和涂装等,以获得符合要求的最终产品。
总之,RTM工艺技术是一种先进的复合材料成型工艺,具有成型效果好、成本低、产量高的优点。
通过合理选择纤维增强材料和树脂、优化模具设计、精确控制注塑和固化参数等,可以生产出符合要求的复合材料制品。
随着科学技术的不断发展,RTM工艺技术也将在航空航天、汽车工业、建筑业和体育用品等领域得到广泛应用。
RTM相关资料

RTM相关资料1.前言所谓闭模成型工艺就是在阴、阳模闭合的情况下成型复合材料构件的工艺方法。
SMC、BMC模压、注射成型、RTM、VEC技术都属闭模成型工艺。
由于环境法的制定和对产品要求的提高使敞模成型复合材料日益受到限制,促使了闭模成型技术的应用,近年来尤其促进了RTM技术的革新和发展。
2.RTM的类型RTM工艺,即树脂传递模塑工艺,是一种新型的模压成型方法。
它具有模具造价低、生产周期短、劳动力成本低、环境污染少、制造尺寸精确、外形光滑、可制造复杂产品等优点。
40年代来,该工艺是为适应飞机雷达罩成型而发展起来的。
目前,RTM成型工艺己广泛应用于建筑、交通、电讯、卫生、航天航空等领域。
下面介绍几种RTM技术。
1)TM,树脂传递模塑。
该技术源自聚氨酯技术,成型时关闭模具,向预制件中注入树脂,玻纤含量低,约20-45%。
2)VARIT,真空辅助树脂传递注塑。
该技术利用真空把树脂吸入预制件中,同时也可压入树脂,真空度约10-28英寸汞柱。
3)VARTM,真空辅助树脂传递注塑。
制品孔隙一般较少,玻纤含量可增高。
4)VRTM,真空树脂传递模塑。
5)VIP,真空浸渍法。
6)VIMP,可变浸渍塑法。
树脂借助真空或自重移动,压实浸渍。
7)TERTM,热膨胀RTM。
在预制件中插入世材,让树脂浸渍并对模具与成形品加热。
芯材受热膨胀,压实铺层。
利用这种压实作用,结合表面加压成型。
8)RARTM,橡胶辅助RTM。
在TERTM方法中不用芯材而用橡胶代之。
橡胶模具压紧成型品,使孔隙大大减少,玻纤含量可高达60-70%。
9)RIRM,树脂注射循环模塑。
真空与加压结合,向多个模具交替注入树脂,使树脂循环,直至预制件被充分浸透。
10)CIRTM,Co-Injection RTM。
共注射RTM,可注入几种不同的树脂,也可使用几种预制件,可利用真空袋和柔性表面的模具。
11)RLI,树脂液体浸(渗)渍。
在下模内注入树脂,入入预制件后覆盖上模,加热并用热压釜的成型压力成型。
rtm工艺流程
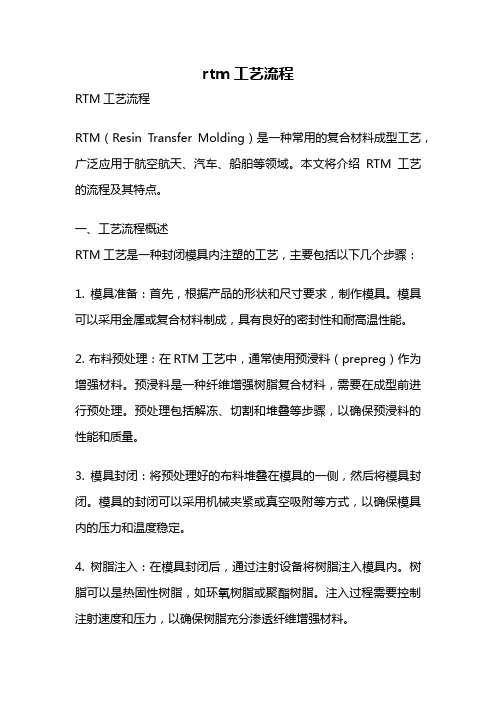
rtm工艺流程RTM工艺流程RTM(Resin Transfer Molding)是一种常用的复合材料成型工艺,广泛应用于航空航天、汽车、船舶等领域。
本文将介绍RTM工艺的流程及其特点。
一、工艺流程概述RTM工艺是一种封闭模具内注塑的工艺,主要包括以下几个步骤:1. 模具准备:首先,根据产品的形状和尺寸要求,制作模具。
模具可以采用金属或复合材料制成,具有良好的密封性和耐高温性能。
2. 布料预处理:在RTM工艺中,通常使用预浸料(prepreg)作为增强材料。
预浸料是一种纤维增强树脂复合材料,需要在成型前进行预处理。
预处理包括解冻、切割和堆叠等步骤,以确保预浸料的性能和质量。
3. 模具封闭:将预处理好的布料堆叠在模具的一侧,然后将模具封闭。
模具的封闭可以采用机械夹紧或真空吸附等方式,以确保模具内的压力和温度稳定。
4. 树脂注入:在模具封闭后,通过注射设备将树脂注入模具内。
树脂可以是热固性树脂,如环氧树脂或聚酯树脂。
注入过程需要控制注射速度和压力,以确保树脂充分渗透纤维增强材料。
5. 固化成型:树脂注入后,需要进行固化过程。
固化可以通过热固化或光固化等方式进行。
固化时间和温度需要根据树脂的性质和产品要求进行控制。
6. 模具开启:在树脂固化后,打开模具,取出成型件。
成型件具有优良的力学性能和表面质量。
二、RTM工艺的特点RTM工艺相比其他成型工艺具有以下特点:1. 成型件质量高:由于RTM工艺采用封闭模具,可以有效控制树脂的渗透和固化过程,从而获得高质量的成型件。
2. 复杂形状成型:RTM工艺适用于复杂形状的产品制造,可以满足各种工程要求。
3. 纤维含量高:RTM工艺可以实现高纤维含量的复合材料制造,提高产品的强度和刚度。
4. 自动化程度高:RTM工艺可以实现自动化生产,提高生产效率和一致性。
5. 环保节能:RTM工艺中的树脂可以回收再利用,减少了废料的产生,符合环保要求。
总结:RTM工艺是一种先进的复合材料成型工艺,具有高质量、适用于复杂形状、高纤维含量、自动化程度高和环保节能等特点。
rtm成型工艺技术

rtm成型工艺技术RTM(Resin Transfer Molding)成型工艺技术是一种在复合材料制造中常用的工艺技术,通过将预浸料注入模具中,使其在高压下固化成型。
以下是关于RTM成型工艺技术的详细介绍。
RTM成型工艺技术是一种集注塑成型和压缩成型为一体的复合材料成型工艺。
该工艺以模具为基础,通过将环氧树脂及其增强材料预浸料注入模具中,并施加一定的压力,使预浸料在模具内部充分浸透并固化。
与传统成型工艺相比,RTM成型具有高成型质量、高成型效率、低成本和环保等优点。
RTM成型工艺技术可以应用于各种复合材料制品的生产,特别是结构性和高强度要求的制品。
例如,飞机、汽车、船舶、建筑等领域的复合材料零部件都可以采用RTM成型工艺进行制造。
此外,RTM工艺还可以灵活地生产各种复材件,如复材齿轮、复材托架等。
RTM成型工艺的关键是模具的设计和制造。
模具必须具备良好的密封性和耐压性能,以确保预浸料在注入过程中不会泄漏。
此外,模具的开关设计也很重要,以确保成品能够顺利脱模。
因此,模具的制造需要高精度的加工和高耐磨的材料。
RTM成型工艺的关键步骤包括预浸料的配料、模具的准备、预热和注射、压力施加和固化等。
在制造过程中,预浸料需要在一定的温度下预热,以改善流动性并减少预浸料中的空气。
然后,预热的预浸料通过注射设备注入到模具中,同时施加一定的压力以保证预浸料充分浸透。
最后,固化过程中,通过加热或其他方法使预浸料固化,并获得最终产品。
RTM成型工艺技术具有许多优点。
首先,由于采用了大型模具和注射设备,RTM工艺可以高效地进行大规模生产,提高生产效率。
其次,由于预浸料中的树脂是事先注入的,可以较好地控制纤维的含量和取向,从而使得制品具有更高的强度和刚度。
此外,由于预浸料中的树脂经过事先预热,因此也能在注入过程中更好地充满空气孔隙,减少产品的缺陷率。
然而,RTM成型工艺也存在一些挑战和限制。
首先,由于需要大型模具和注射设备,设备投资和生产成本相对较高。
rtm成型工艺过程

rtm成型工艺过程
RTM(Resin Transfer Molding)是一种常用的复合材料成型工艺,主要用于生产复材零部件。
RTM成型工艺包含以下几个步骤:
1.模具制备:根据产品的设计要求,制作适用于RTM成型的模具。
通常使用金属或者复合材料制造的模具。
2.面层制备:将预浸料(prepreg)或者无纺布等面层材料剪裁成所需形状和尺寸。
3.模具装备:将面层材料放置在模具的一侧,保持模具清洁。
4.预制:将需要使用的纤维束定位在模具中,并按照设计要求进行预配置,通常采用预定位工具如夹具等,以确保纤维束的定位精准。
5.闭模:将两半模具闭合,并确保模具密封。
通常采用安全和可控的方法进行模具闭合,以防止树脂泄漏。
6.树脂注入:在成型开始前,通过开启充注阀门,将树脂注入模具中。
注入时使用低压或者真空吸引树脂进入纤维束,以确保树脂充分浸润纤维。
7.充注:树脂在模具内浸润纤维的过程中,需要保持一定的注入压力和速度,以确保树脂充分填充整个模具。
8.固化:树脂在充注完成后开始固化。
根据树脂的性质和设计要求,可以通过提高温度、加热模具或者添加固化剂等方法来促进树脂的固化。
9.开模:待树脂完全固化后,打开模具,取出成型件。
10.修整:对成型件进行修整,如去除多余的材料、修整边缘等。
预浸料模压成型工艺

预浸料模压成型工艺预浸料模压成型工艺(RTM)是一种常用于复合材料制造的生产工艺,通常应用于制造高性能的复合材料零部件。
这种工艺结合了预浸料技术和模压工艺,能够实现复杂形状的零部件制造,同时确保材料的均匀性和强度。
在RTM工艺中,首先需要准备预浸料。
预浸料是指预先浸渍了树脂的纤维增强材料,通常使用碳纤维、玻璃纤维等作为增强材料,再将其浸渍在树脂中。
这种预浸料在搅拌和真空处理之后,可用于模压成型。
预浸料的质量和性能对成品的质量至关重要,因此制备过程需严格控制,以确保材料的均匀性和一致性。
在实际生产中,RTM工艺通常分为几个步骤。
首先,将预浸料放置在放置在模具中,并施加压力以确保材料填充模具。
随后,将模具置入加热压力机中,树脂在高温和高压的环境下固化。
在固化过程中,树脂会流动并填充整个模具空间,确保最终成品的均匀性。
RTM工艺具有许多优势。
首先,由于预浸料预先浸渍了树脂,因此可以精确控制树脂含量,从而确保成品的性能。
其次,RTM工艺适用于大批量生产,能够快速且有效地制造复合材料零部件。
此外,由于模具可以被重复使用,因此RTM工艺也具有较低的模具成本。
但与此同时,RTM工艺也存在一些挑战。
例如,由于需要加热和加压,工艺周期较长,生产效率不如其他成型工艺。
此外,对于复杂形状的零部件,可能需要设计复杂的模具,增加了制造成本和复杂性。
因此,在选择制造工艺时,需要综合考虑产品要求、成本和生产效率等因素。
总的来说,预浸料模压成型工艺是一种广泛应用于复合材料制造领域的高性能成型工艺,能够实现复杂形状零部件的制造,同时确保产品的质量和性能。
随着材料和工艺的不断进步,预浸料模压成型工艺将在未来得到更广泛的应用,并为复合材料制造带来更多可能性。
1。
rtm工艺技术要求

rtm工艺技术要求RTM(Resin Transfer Molding)工艺是一种在复合材料制造过程中常用的注塑工艺。
它适用于大量生产高性能复合材料制品的情况,如航空航天、汽车和船舶等领域。
RTM工艺的主要目标是生产出具有优良性能和质量稳定性的复合材料制品。
为了实现这一目标,RTM工艺有以下几个重要的技术要求。
首先,RTM工艺要求完善的模具设计和制造。
模具是RTM工艺成型的关键,它直接决定了制品的形状、尺寸和表面质量。
为了避免制品出现缺陷,如气泡、翘曲等问题,模具必须具备高度的精度和平面度。
此外,还需要具备良好的磨损性能和抗腐蚀性能,以保证模具的使用寿命和稳定性。
其次,RTM工艺要求精确的材料选型和预制。
在RTM工艺中,通常使用环氧树脂、聚酰胺树脂等作为基体材料,同时添加玻璃纤维、碳纤维等作为增强材料。
为了保证制品具有优异的机械性能和低拉伸率,需要精确控制材料的比例和配比。
此外,还需要对材料进行预制,如预浸料或预浸润,以保证材料的自由流动性和粘接性。
第三,RTM工艺要求严格的生产过程控制。
生产过程控制包括温度、压力和流量等参数的控制。
温度控制是非常重要的,因为它直接影响材料的硬化速度和粘接性能。
压力控制可以有效地避免气泡和空隙的形成。
流量控制是为了确保材料可以均匀地填充到模具中,以避免制品出现凝胶线等问题。
最后,RTM工艺要求严格的检验和质量控制。
在制品成型后,需要进行各项性能测试和外观检查,以确保其符合设计要求和产品规格。
常见的测试包括强度测试、硬度测试和耐热性测试等。
此外,还需要进行外观检查,如表面平整度、色差和气泡等。
只有通过严格的检验和质量控制,才能保证RTM工艺生产出的复合材料制品具有稳定性和可靠性。
综上所述,RTM工艺的技术要求包括完善的模具设计和制造、精确的材料选型和预制、严格的生产过程控制以及严格的检验和质量控制。
只有满足这些要求,才能生产出高性能和高质量的复合材料制品,满足客户的需求和市场的竞争。
rtm工艺和模压法

rtm工艺和模压法
RTM工艺是指树脂传输模塑工艺(Resin Transfer Molding),是一种用于复合材料制造的成型工艺。
在RTM工艺中,预先铺设好
的纤维增强材料(如玻璃纤维、碳纤维等)被放置在模具中,然后
通过负压将树脂注入到模具中,使得树脂浸透纤维增强材料,最终
形成所需的零件或构件。
RTM工艺通常用于制造复杂形状的零件,
具有成本低、生产周期短、成型精度高等优点。
而模压法是一种常见的塑料成型工艺,也被称为压缩成型。
在
模压法中,塑料颗粒被加热至熔化状态后,被注入到模具中,然后
施加压力使其充分填充模具并冷却固化,最终得到所需的塑料制品。
模压法适用于生产各种尺寸和形状的塑料制品,具有成本低、生产
效率高、制品密度均匀等优点。
从工艺原理来看,RTM工艺注重树脂的浸透和充填,适用于复
合材料的生产;而模压法则是通过加热塑料颗粒使其熔化后填充模具,适用于塑料制品的生产。
从应用领域来看,RTM工艺主要应用
于航空航天、汽车、船舶等领域,而模压法则广泛应用于塑料制品
制造行业。
总的来说,RTM工艺和模压法都是常见的成型工艺,它们各自适用于不同的材料和产品领域,具有各自独特的优点和适用范围。
rtm成型工艺流程

rtm成型工艺流程
RTM(Resin Transfer Molding)成型工艺流程是一种通过成型
覆膜技术,使用压力将预浸层纤维材料浸渍于合适的树脂中来制造复合材料制品的工艺。
RTM成型工艺流程一般包括以下几个步骤:
1. 制备模具:根据产品设计要求,制作出适合的模具。
模具可以包括一个或者多个腔室,根据产品的复杂程度决定。
2. 准备纤维预浸料:将纤维材料与树脂进行匹配,并将其浸泡在树脂中,以获取预浸层纤维材料。
3. 关闭模具:将两个模具部分合拢,确保密封。
4. 注入树脂:通过在模具中施加压力,将树脂从预先确定的入口注入模具中。
5. 充填纤维:随着树脂的注入,树脂会在模具中渗透纤维材料,充填整个模腔。
6. 固化树脂:当树脂注入完毕后,施加固化条件,例如温度和压力等,使树脂固化。
7. 模具开启:固化完毕后,打开模具,取出模具中的复合材料制品。
8. 整理和加工:对取出的复合材料制品进行必要的整理和加工,例如去除闪烁,修整边缘等。
RTM成型工艺可以生产具有较高性能和复杂形状的复合材料
制品。
由于该工艺的成本较低,制造周期较短,并且适用于大批量生产,因此在航空航天、汽车、建筑等领域得到了广泛应用。
rtm 工艺技术
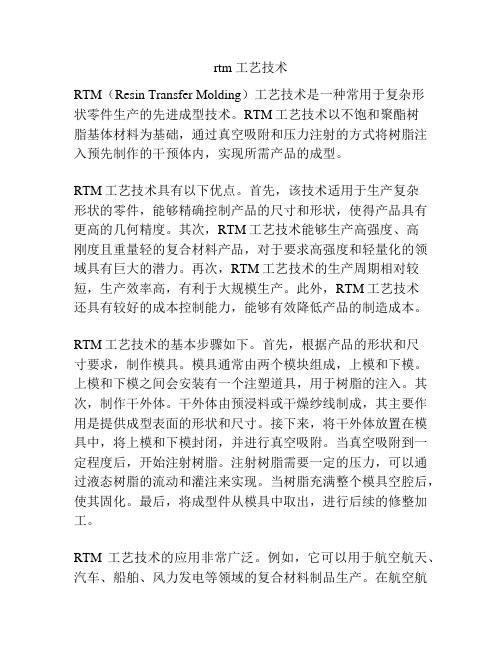
rtm 工艺技术RTM(Resin Transfer Molding)工艺技术是一种常用于复杂形状零件生产的先进成型技术。
RTM工艺技术以不饱和聚酯树脂基体材料为基础,通过真空吸附和压力注射的方式将树脂注入预先制作的干预体内,实现所需产品的成型。
RTM工艺技术具有以下优点。
首先,该技术适用于生产复杂形状的零件,能够精确控制产品的尺寸和形状,使得产品具有更高的几何精度。
其次,RTM工艺技术能够生产高强度、高刚度且重量轻的复合材料产品,对于要求高强度和轻量化的领域具有巨大的潜力。
再次,RTM工艺技术的生产周期相对较短,生产效率高,有利于大规模生产。
此外,RTM工艺技术还具有较好的成本控制能力,能够有效降低产品的制造成本。
RTM工艺技术的基本步骤如下。
首先,根据产品的形状和尺寸要求,制作模具。
模具通常由两个模块组成,上模和下模。
上模和下模之间会安装有一个注塑道具,用于树脂的注入。
其次,制作干外体。
干外体由预浸料或干燥纱线制成,其主要作用是提供成型表面的形状和尺寸。
接下来,将干外体放置在模具中,将上模和下模封闭,并进行真空吸附。
当真空吸附到一定程度后,开始注射树脂。
注射树脂需要一定的压力,可以通过液态树脂的流动和灌注来实现。
当树脂充满整个模具空腔后,使其固化。
最后,将成型件从模具中取出,进行后续的修整加工。
RTM工艺技术的应用非常广泛。
例如,它可以用于航空航天、汽车、船舶、风力发电等领域的复合材料制品生产。
在航空航天领域,复合材料产品具有高强度、高刚度、耐高温等特点,能够满足飞机零件对于性能要求的同时,减轻飞机自身的重量,提高燃油经济性和航空器的使用寿命。
在汽车领域,RTM工艺技术可以用于制作车身、底盘等零部件,使得汽车更轻、更稳定、更节能。
在船舶领域,RTM工艺技术可以制作船体、罩壳等结构件,提高船舶的承载能力和耐候性。
在风力发电领域,RTM工艺技术可以制作复合材料叶片,提高风力发电机组的效率。
总之,RTM工艺技术是一种先进的复合材料成型技术,通过树脂的注入和固化,可以生产出具有复杂形状、高强度、高刚度的复合材料产品。
rtm工艺国内发展现状和市场应用前景

低,能获很好的力学性能,相对于手糊,能节省一半的作业时间,另外还
可以在纤维中加放夹芯材,并且可制作一次成型极厚的制品,如果叶片的
叶根,一次灌注130多层的产品大约有30公分厚度,但是,小型的制
品侧更合适用模传统的RTM工艺和其它的RTM衍化工艺,因为做小型产品
时,耗材的的成本会担高产品的制造成本,而体型中等的产品则适合用轻
6、冷压成型
冷压成型是指先把纤维或预型体放放模腔内,然后把加入固化剂的树脂倒入维纤上 面,然后用压机把模具合模压紧,然后树脂在模腔内流动并充满模腔,然后固化后脱 模的一种工艺,该工艺成型的速度快,且质量好,大约10分钟左右,可生产一个产品,
三、 RTM工艺发展的机遇
RTM从上世纪九十年代引入我国以来,由于多种条件的限制,一直未能得到大规 模的推广应用,直到近几年,由于风电行业,游艇行业,汽车零配行业的带动,RTM工 艺特别是L-RTM得到了迅速的发展,基下以下几个原因,可以预见,该工艺将取代手糊
艺制作产品时,可达十几分钟一个水箱板,一个十几个人的小厂,一天能
生产160多片水箱板,)而多多嵌入面模RTM 工艺则把工艺中最费时
的的铺毡工艺和胶衣喷涂工艺放在主模的嵌入面模上进行,而主模承担的
只是灌注和加热固化的部份,因此能极大的提高生产的效率,因些也适合
大批量的产品制作。
4
1、传统RTM
树脂传递模塑成型简称RTM,起始于50、60年代,是手糊成型工艺改进的一种闭模成型技术, 可以生产出两面光的制品。RTM的基本原理是将玻璃纤维增强材料铺放到闭模的模腔内,用 专用压力设备将树脂胶液注入模腔,浸透玻纤增强材料,然后固化,脱模成型制品。RTM成 型技术的特点:1、可以制造两面光的制品;2、成型效率高,适合于中等规模的玻璃钢产品 生产(20000件/年);3、RTM为闭模操作,不污染环境,不损害工人健康;4、增强材料可 以任意方向铺放,容易实现按制品受力状况例题铺放增强材料;5、原材料及能源消耗少;6、 建厂投资相对少,项目容易上马。 RTM技术适用范围很广,目前已广泛用于建筑、交通、电 讯、卫浴、航空航天等工业领域。已开发的产品有:汽车壳体及部件、娱乐车构件、天线罩、 机器罩、浴盆、沐浴间、游泳池板、座椅、水箱、电话亭、小型游艇等。(RTM模具有制作时,,
rtm成型工艺过程
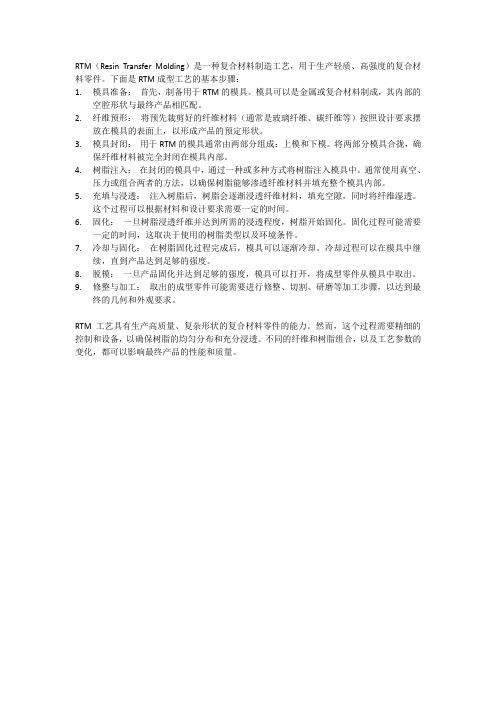
RTM(Resin Transfer Molding)是一种复合材料制造工艺,用于生产轻质、高强度的复合材料零件。
下面是RTM成型工艺的基本步骤:1.模具准备:首先,制备用于RTM的模具。
模具可以是金属或复合材料制成,其内部的空腔形状与最终产品相匹配。
2.纤维预形:将预先裁剪好的纤维材料(通常是玻璃纤维、碳纤维等)按照设计要求摆放在模具的表面上,以形成产品的预定形状。
3.模具封闭:用于RTM的模具通常由两部分组成:上模和下模。
将两部分模具合拢,确保纤维材料被完全封闭在模具内部。
4.树脂注入:在封闭的模具中,通过一种或多种方式将树脂注入模具中。
通常使用真空、压力或组合两者的方法,以确保树脂能够渗透纤维材料并填充整个模具内部。
5.充填与浸透:注入树脂后,树脂会逐渐浸透纤维材料,填充空隙,同时将纤维湿透。
这个过程可以根据材料和设计要求需要一定的时间。
6.固化:一旦树脂浸透纤维并达到所需的浸透程度,树脂开始固化。
固化过程可能需要一定的时间,这取决于使用的树脂类型以及环境条件。
7.冷却与固化:在树脂固化过程完成后,模具可以逐渐冷却。
冷却过程可以在模具中继续,直到产品达到足够的强度。
8.脱模:一旦产品固化并达到足够的强度,模具可以打开,将成型零件从模具中取出。
9.修整与加工:取出的成型零件可能需要进行修整、切割、研磨等加工步骤,以达到最终的几何和外观要求。
RTM工艺具有生产高质量、复杂形状的复合材料零件的能力。
然而,这个过程需要精细的控制和设备,以确保树脂的均匀分布和充分浸透。
不同的纤维和树脂组合,以及工艺参数的变化,都可以影响最终产品的性能和质量。
rtm工艺技术缺点

rtm工艺技术缺点RTM(Resin Transfer Molding)是一种常用的复合材料成型工艺技术,通过在模具中注射树脂将纤维增强材料浸泡在树脂中,然后在高压下固化形成最终产品。
尽管RTM工艺技术具有许多优势,但也存在一些缺点。
首先,RTM工艺技术的成本较高。
相对于传统的手工层叠和注塑成型工艺,RTM工艺需要更多的设备和材料来实现。
在RTM工艺中,需要使用专门的模具和胶片,同时还需要使用高压注射设备来注射树脂。
这些设备和材料的采购和维护成本都较高,从而导致了总体的成本上升。
其次,RTM工艺技术对模具的要求较高。
由于RTM工艺需要将树脂注入模具中,在模具中形成完整的纤维增强复合材料,因此模具的密封性能和耐压性能要求较高。
如果模具的密封性能不足,树脂会泄漏出去,导致产品质量下降。
而且,模具需要能够承受高压注射时带来的压力,如果模具的耐压性能不够强,会导致模具破裂甚至损坏。
此外,RTM工艺技术的生产周期较长。
由于RTM工艺要求将树脂完全浸润纤维增强材料,这个过程需要一定的时间,而且注塑压力较高,导致注塑时间更长。
同时,由于RTM工艺技术的复杂性,需要经过多个工序才能完成,例如模具准备、材料准备、注塑和固化等。
这些工序需要逐一进行,总体来说就需要较长的时间才能完成。
最后,RTM工艺技术在产品设计方面的灵活性较差。
由于RTM工艺要求使用模具生产复合材料产品,因此产品的形状和尺寸主要受到模具的限制。
如果需要更改产品的形状或尺寸,需要重新设计和制造新的模具,这会增加额外的成本和时间。
而且,由于树脂注塑需要一定的压力来实现,对于一些细小、薄壁或者复杂形状的产品,可能无法很好地实现树脂的注塑,导致产品质量受到影响。
综上所述,RTM工艺技术虽然有许多优势,但也存在一些缺点,如成本较高、对模具的要求较高、生产周期较长以及产品设计灵活性较差等。
因此,在选择使用RTM工艺技术时需要权衡其优点和缺点,选择适合的工艺来满足产品的要求。
RTM工艺
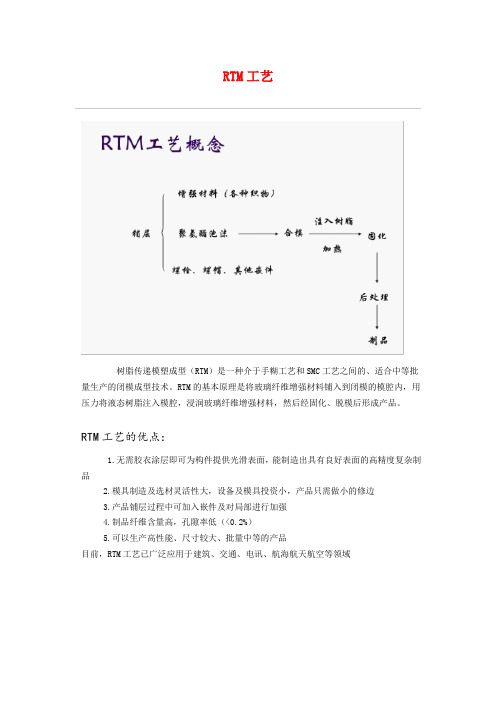
RTM工艺
树脂传递模塑成型(RTM)是一种介于手糊工艺和SMC工艺之间的、适合中等批量生产的闭模成型技术。
RTM的基本原理是将玻璃纤维增强材料铺入到闭模的模腔内,用压力将液态树脂注入模腔,浸润玻璃纤维增强材料,然后经固化、脱模后形成产品。
RTM工艺的优点:
1.无需胶衣涂层即可为构件提供光滑表面,能制造出具有良好表面的高精度复杂制品
2.模具制造及选材灵活性大,设备及模具投资小,产品只需做小的修边
3.产品铺层过程中可加入嵌件及对局部进行加强
4.制品纤维含量高,孔隙率低(<0.2%)
5.可以生产高性能、尺寸较大、批量中等的产品
目前,RTM工艺已广泛应用于建筑、交通、电讯、航海航天航空等领域
RTM模具、制品(高铁VIP座椅模具、制品):
高铁VIP座椅(扶手)上模高铁VIP座椅(扶手)下模
高铁VIP座椅高铁VIP座椅
地铁高压接线盒模具、制品:
地铁高压接线盒(盖板)模具地铁高压接线盒(底座)模具
地铁高压接线盒(防弧罩)模具
地铁高压接线盒制品
地铁高压接线盒制品
地铁高压接线盒制品。
- 1、下载文档前请自行甄别文档内容的完整性,平台不提供额外的编辑、内容补充、找答案等附加服务。
- 2、"仅部分预览"的文档,不可在线预览部分如存在完整性等问题,可反馈申请退款(可完整预览的文档不适用该条件!)。
- 3、如文档侵犯您的权益,请联系客服反馈,我们会尽快为您处理(人工客服工作时间:9:00-18:30)。
树脂传递模塑成型工艺RTM工艺的主要原理是在模腔中铺放按性能和结构要求设计的增强材料预成形体,采用注射设备将专用树脂体系注入闭合模腔,模具具有周边密封和紧固以及注射及排气系统,以保证树脂流动流畅并排出模腔中的全部气体和彻底浸润纤维,还具有加热系统,可加热固化成形复合材料构件。
它是一种不采用预浸料,也不采用热压罐的成形方法。
因此,具有效率高、投资、绿色等优点,是未来新一代飞机机体有发展潜力的制造技术。
该方法的优点是环保、形成的层合板性能好且双面质量好,在航空中应用不仅能够减少本身劳动量,而且由于能够成形大型整体件,使装配工作量减少。
但是树脂通过压力注射进入模腔形成的零件存在着孔隙含量较大、纤维含量较低、树脂在纤维中分布不匀、树脂对纤维浸渍不充分等缺陷,因此该技术还有改进潜力。
该工艺还能帮助生产尺寸精确,表面工艺精湛的复杂零件。
树脂传递模塑工艺还有一个特点是,能够允许闭模前在预成型体中放入芯模填充材料,避免预成型体在合模过程中被挤压。
芯模在整个预成型体中所占的比重较低,大约在0-2%之间。
下表是一些常见RTM成型产品的缺陷问题和解决办法。
粗纱、硬度大再选牌号邹折玻璃纤维流动错位用对预成型坯粘结剂有效的粘结剂,减慢注入速度玻璃纤维类型质量不好选择质量好的玻纤挠曲变形脱模时固化不完全促进树脂固化,用补强材料提高刚度使用矫正夹具树脂固化收缩使用低收缩剂,使用填料RTM工艺成功事例:图:ASC – II桨叶通过美国联邦航空局的认证,成功运用于派珀飞机上(Piper Matrixaircraft),ASC – II桨叶同样适用于Cirrus的SR - 22和其他通用航空飞机。
来源:派珀飞机公司Hartzell公司使用自有设计软件--PROP Code和ANSYS公司开发的有限元分析(FEA)软件对桨叶上应力的分配进行分析和设计,然后用另一个内部开发程序来生成ASC - II复合层压结构。
汉克将这种泡沫夹芯三明治结构设计描述为单体横造结构。
制备原理是通过湿法手糊将碳纤维及芳纶纤维(单向或混编)与环氧树脂复合成型,然后在中间插入闭孔泡沫夹芯材料,形成一个桁条形状的完整复合材料桨叶。
碳纤维能保证桨叶具备高模量和高弯曲强度,而芳纶纤维则能有效提高整个桨叶的阻尼性能和增加其扭曲强度。
机翼外蒙皮是由玻璃纤维制造,表面附有一层铝材避雷网。
值得一提的是,该桨叶结构上不同位置所采用的层压材的层数及其纤维取向各有不同,因此产生了厚度分布的差异化。
虽然汉克没有透露过多的设计细节,比如桨叶是如何通过闭模不锈钢柄的复合材料界面连接到集线器上的?他只是说:“我们借助有限元分析软件,将复合材料桨叶连接到不锈钢柄上,实现了飞行阻力最小化。
”关于具体的材料和供应商是商业秘密,但汉克表示,选定的材料都是航天级的,桨叶上不同位置的厚度的差异化是专门针对不同负载而设计的。
桨叶的前三分之二部分是整个部分旋转速度最快的位置,因此设计上充分考虑这点,采用了高度耐用、易于拆卸和抗损坏材料---镍蚀条制造。
靠近集线器的三分之一则是采用聚氨酯条。
完成设计草图之后,Hartzell开始转向模塑成型工艺。
迪布罗回忆说:“原先的预浸料螺旋桨同样是一个优秀的解决方案,但预浸料的成本对于大多数一般的航空应用来说太昂贵了。
而降低成本正是我们设计ASC – II桨叶的初衷,我们需要的是一款既能让用户负担得起,又拥有最先进技术,同时还不能丧失原始设计的精华的一款复合材料螺旋桨叶。
”在制备工艺上,我们最终诉诸于树脂传递模塑(RTM)工艺认证包括一系列严格的地面试验,和雷击试验(20万安培);循环疲劳试验;和离心力拔出测试(该测试模拟引擎超速飞行条件,利用一个测试夹具试图将桨叶从集线器上拔出来)。
其次是仪器的飞行测试。
Design decisions with digital helpTo achieve these goals, the company used its own proprietary design software called PROP Code. This aerodynamic program, notes Hanke, interfaces seamlessly with ANSYS finite element analysis (FEA) software from ANSYS Inc. (Canonsburg, Pa.) for determination of stresses and their distribution in the blades. Hartzell designers then used another internally developed program to generate the ASC-II's laminate architecture.The result was a foam-cored sandwich design that Hanke describes as a monocoque structure. A combination of carbon and aramid fibers (in both woven hybrid and unidirectional forms) wet out with epoxy enclose a closed-cell foam insert to form an integral composite spar that runs the length of the blade. A second, shaped foam insert fills the trailing edge. Carbon fiber provides the spar's high modulus and high bending strength, while aramid supplies excellent torsion and damping performance through the whole blade. The continuous outer skin is formed from fiberglass and an aluminum lightning protection mesh. The number of plies and their orientation varies throughout the blade span, resulting in a variable-thickness part.Although Hanke won't reveal how the composite interfaces with the comolded stainless steel shank that connects the blade to the hub, he does say, "We connected thecomposite material to the shank in such a way as to minimize stresses, a result we achieved through FEA analysis." Specific materials and suppliers are trade secrets, but Hanke revealed that the materials selected were aerospace-grade and that the laminate thickness was optimized at different locations along the blade span, to meet varying loads. Along the outer two-thirds of the blade's leading edge — the segment that travels at the highest speed — a highly durable, removable nickel erosion strip provides damage protection. Urethane tape protects the third closest to the hub.A revised design in hand, Hartzell turned to the molding process. "The legacy prepreg propeller was an excellent solution, but the prepreg and layup costs made it too expensive for most general aviation applications," Disbrow recalls. "The design goal for the ASC-II was to make an affordable advanced propeller that didn’t sacrifice any of the benefits of the earlier designs." This led to the adoption of resin transfer molding (RTM).The company produces its own lay-up kits, which contain the appropriate number of dry composite materials and metal parts, permitting quick layup in two-part steel molds, designed in-house. The blade parts are comolded and infused with epoxy resin at multiple workstations, each equipped with an automated RTM cell. Part production is fast and overall labor costs are lower as well, the company says.Because Hartzell chose to market the ASC-II to FAA-certified piston aircraft, like those built by Cirrus and Piper, rather than limit it to uncertified experimental planes, the blade had to be type-certified, which is "a huge, demanding task," Disbrow stresses. A series of stringent ground tests included a 4-lb/1.8 kg bird strike at the critical flight regime of full power at take-off rotation; lightning strike trials (200,000 amps); cyclic fatigue tests; and pull-out tests, in which a test fixture tried to pull the blade from the hub, simulating an engine overspeed condition. These were followed by instrumented flight testing. Disbrow points out that the expense and time required by FAA's test regime is one big reason "why there are so few composite propellers on the market for certified aircraft." Yet, overall, he says, "We determined it was worth the effort."Lower weight, longer life, less costWorth the effort, it was: The ASC-II blade saves 16 lb/7.3 kg in three-blade configuration on the Cirrus SR-22, over a comparable aluminum-bladed prop. Beyond weight savings, Hanke and Disbrow explain that the ASC-II has the potential to last 50,000 flight hours — unheard of for a metal blade — because of its repairability.When a metal blade is damaged (usually by gravel or debris), repair involves grinding down the surface to remove potential stress risers and restore the damaged area. Over time, repeated grinding results in an undersized propeller. In contrast, the ASC-II's erosion strip can be removed and replaced, and if the composite itself is damaged, material can be replaced at the damage site, so undersizing isn't an issue. Other advantages include a shank design geometrically similar to that used for aluminum blades, so that composite blades can be substituted readily for metal blades on a propeller. De-icing systems also are compatible, for aircraft so equipped.ASC-II is marketed to piston aircraft with 180- to 350-hp engines, and to turbine aircraft that generate between 400 and 1,800 hp. One arena in which the propeller excels, Hanke reports, is the diesel-powered aircraft niche. Diesel compression ratios are very high, resulting in large excitation pulses. Aluminum props fatigue too quickly, but the ASC-II blades have successfully managed the extreme fatigue regime.More than 500 propellers have been manufactured and shipped so far. The company is currently adapting the two- and three-blade design to additional aircraft and is working on a four-blade ASC-II design. Concludes Disbrow: "The ASC-II gives us a competitive advantage, since the composite materials allow us to balance weight, durability, performance and cost."。