(φ)3.6m×10m回转阳极炉出烟口水冷烟罩设计
某燃煤采暖锅炉烟气除尘系统设计 计算书

大气污染控制工程课程设计计算书设计题目:某燃煤采暖锅炉烟气除尘系统设计学院:环境与市政工程学院专业班级:学号:学生姓名:指导教师:2013年01月02日目录目录 (1)一、燃煤锅炉排烟量及烟尘和二氧化硫浓度的计算 (3)1.1.理论空气量 (3)1.2.理论烟气量(设空气含湿量12.93g/m3) (3)1.3.实际烟气量 (3)1.4.烟气含尘浓度 (4)1.5.烟气中二氧化硫浓度的计算 (4)二、除尘器的比较和选择 (5)2.1.除尘效率 (5)2.2.二氧化硫的去除率 (5)三、确定除尘器、风机、烟囱的位置及管道布置。
并计算各管段的管径、长度、烟囱高度和出口内径以及系统总阻力 (7)3.1.各装置及管道布置的原则 (7)四、烟囱的设计 (8)4.1.烟囱高度的确定 (8)4.2.烟囱直径的计算 (8)4.3.烟囱的抽力 (9)五、系统阻力的计算 (10)5.1.摩擦压力损失 (10)5.2.局部压力损失 (11)六、风机和电动机选择及计算 (14)6.1.风机风量的计算 (14)6.2.风机风压的计算 (14)6.3.电动机功率的计算 (15)七、通风除尘系统布置图 (16)参考文献 (17)一、 燃煤锅炉排烟量及烟尘和二氧化硫浓度的计算1.1. 理论空气量()Y Y Y Y aO S H C Q 7.07.056.5867.178.4-++=' /kg)(m 3 式中:Y C 、Y H 、Y S 、Y O 分别为煤中各元素所含的质量百分数。
)/(69.6)023.07.0017.07.0032.056.5657.0867.1(78.4'3kg m Q a =⨯-⨯+⨯+⨯⨯=1.2. 理论烟气量(设空气含湿量12.93g/m 3)Y a a Y Y Y Y sN Q Q W H S C Q 8.0791.0016.024.12.11)375.0(867.1+'+'++++=' (m 3/kg )式中:aQ '—理论空气量(m 3/kg ) Y W —煤中水分所占质量百分数;Y N —N 元素在煤中所占质量百分数/kg)(m 11.769.6791.069.6016.009.024.1032.02.11)017.0375.0657.0(867.1'3=⨯+⨯+⨯+⨯+⨯+⨯=s Q1.3. 实际烟气量a ss Q Q Q '-+'=)1(016.1α (m 3N /kg ) 式中:α —空气过量系数。
燃煤采暖锅炉烟气处理系统设计-环境工程课程设计(大气)[优秀]
![燃煤采暖锅炉烟气处理系统设计-环境工程课程设计(大气)[优秀]](https://img.taocdn.com/s3/m/ae32d26449649b6649d7476e.png)
前言据统计,我国目前约有30万台中小型燃煤工业锅炉,耗煤量占全国原煤产量的1/3.而这些锅炉中,大部分没有安装脱硫设备,致使许多地区酸雨频频发生,严重危害了工农业生产和人体健康.因此,烟气脱硫是当前环境保护的一项重要工作.能用于烟气脱硫和除尘的设备很多,但要满足运转稳定可靠、不影响生产同时去除且压力降较小等要求,以袋式除尘器和旋流板为宜.1.设计任务书1.1.课程设计题目燃煤采暖锅炉烟气处理系统设计1.2.设计原始材料锅炉型号:SZL4-13型(额定热功率2.8米W),共3台设计耗煤量:600 千克/h·台烟气温度:160℃脱硫塔出口烟温:60℃标准状态下烟气密度:1.34千克/米3空气过剩系数:α=1.4锅炉外形尺寸:4866×3660×2550锅炉烟囱尺寸:Φ600排烟中飞灰占煤中不可燃成分的比例:16%烟气在锅炉出口前阻力:800Pa当地大气压力:97.86kPa冬季室外空气温度:5℃标准状态下空气含水:0.01293千克/米3烟气其他性质按空气计算煤的工业分析值:C=68% H=4% S=1% O=5%N=1% W=6% A=15% V=13%锅炉大气污染物排放标准(GB 13271-2001)二类标准:标准状态下烟尘浓度排放标准:200米g/米3标准状态下二氧化硫排放标准:900米g/米32.设计概况2.1.设计内容某燃煤采暖锅炉,烟气排放最大量Q=18450米3/h,烟气最高温度160℃,烟气含尘量2340米g/米3,烟气中二氧化硫含量1950米g/米3.2.2.设计依据《锅炉大气污染物排放标准》 GB13271-2001《袋式除尘器技术要求》 GB/T6719-2009《袋式除尘器性能测试方法》 GB12138-89《袋式除尘器安装技术要求与验收规范》 JB/T8471-1996《环境空气质量标准》 GB3095-19962.3.设计要求2.3.1.排放标准锅炉大气污染物排放标准(GB 13271-2001)二类标准:标准状态下烟尘浓度排放标准:200米g/米3标准状态下二氧化硫排放标准:900米g/米33.处理工艺设计3.1.除尘工艺设计3.1.1.各除尘器的简述离心式除尘器离心分离除尘器的工作原理是,利用烟气作旋转运动,依靠离心作用将烟气中粉尘分离出来.这种离心力要比单独靠中立获得的分离大得多,因而除尘较有效.它的结构简单,运行操作方便,可以分离捕集较细的粉粒,但除尘效率不高,约85%左右,阻力一般不大于1000Pa,因此,它被广泛应用于独立的除尘装置,也可作其他除尘器的预处理装置.洗涤式除尘器洗涤式除尘器是用液滴、液膜、气泡等洗涤含尘气体,使含烟气相互凝集,从而使尘粒得到分离的装置.其中应用最多的是文丘里洗涤除尘器,它的主要部件是文丘里管.压力水从文丘里管的喉口的小孔进入,高速的含尘烟气流通过喉口将水雾化成无数水滴,同时使尘粒粘附在所生产的水滴上.将这种气液混合物引入分离器,使水滴与尘粒分离,烟气得到净化.文丘里洗涤器的除尘效率一般在95%以上,它随液滴直径、喉管气速的增加而增加.当液滴直径比尘粒大50倍时,其除尘效率最高.这种除尘器结构简单,除尘效率高,水滴还能吸收烟气中的二氧化硫的三氧化硫.其缺点是阻力大,需要有污水处理装置.袋式除尘器袋式除尘器是使含尘气体通过过滤材料将粉尘分离捕集的装置,采用玻璃纤维作滤料的空气过滤器,主要可用于通风及空气调节的气体净化.袋式除尘器的除尘机理如下:含尘气体进入滤袋,在通过滤料的孔隙时,粉尘被捕集于滤料上,透过滤料的清洁气体从排出口排出,沉积在滤料上的粉尘可在机械振动的作用下从滤料表面脱落,落入灰斗中.粉尘因截留、惯性碰撞、静电和扩散等作用,逐渐在滤袋表面形成粉尘初层.初层形成后,它成为袋式除尘器的主要过滤层,提高了除尘效率,滤布起形成粉尘初层和支撑它的骨架作用,但随着粉尘在滤袋上的积聚,滤袋两侧的压力增大,会把有些已附在滤料上的细小粉粒挤压过去,使除尘效率下降.袋除尘器的阻力一般为1000-2000Pa.另外,若除尘器阻力过高,还会使除尘系统的处理气体量下降,影响生产系统的排风效果.因此,除尘器阻力达到一定数值后要及时清灰,清灰不能过分,即不应破坏粉尘初层,否则会引起除尘效率显著降低.电除尘器电除尘器是利用静电力实现尘粒与烟气流分离的一种除尘装置.电除尘器是在放电极与平板状集尘极之间加以较高的直流电压,使电晕极发生电晕放电.当含尘烟气低速流过放电极与集尘极之间时,首先烟气中的气体分子发生电离,由于含尘烟气中大部分气体(氮气、氢气、二氧化碳)与电无亲和力,故会带负电荷成为负离子,它在向正极移动中遇到随烟气流动的大部分粉尘会使粉尘取得负电荷而转向阳极板上,使粉尘所带的电荷得到中和.集尘板上粉尘到一定厚度时,可用机械振打的方法使之落入灰斗.电除尘器的除尘效率与电场强度、集尘板面积、烟气流量、粉尘趋进速度,尤其是粉尘的导电性有关,电除尘器具有很高的除尘效率(可达99.99%),可捕集到0.1μ米以上的尘粒.它阻力小,运行费用低,处理烟气量的能力大,运行操作方便,可完全实现自动化.缺点是设备庞大,投资费用高.旋风除尘器旋风除尘器是利用旋转的含尘气体所产生的离心力,将粉尘从气流中分离出来的一种干式气-固分离装置.旋风除尘器用于工业生产以来,已有百余年历史.对于捕集5-10μ米以上的粉尘效率较高,其除尘效率可达90%以上,被广泛地应用于化工、石油、冶金、建筑、矿山、机械、轻纺等工业部门.旋风除尘器结构简单,除尘器本身无运动部件,不需特殊的附件设备,占地面积小,制造、安装投资较少.操作、维护简单,压力损失中等,动力消耗不大,运转、维护费用较低.操作弹性较大,性能稳定,不受含尘气体的浓度、温度限制.对于粉尘的物理性质无特殊要求,同时可根据化工生产的不同要求,选用不同材料制成,或内衬各种不同的耐磨、耐热材料,以提高使用寿命.3.1.2.主要除尘器的选用在选择除尘技术时,应充分考虑经济性、可靠性、适用性和社会性等方面的影响.除尘技术的确定受到当地条件、现场条件、燃烧煤种特性、排放标准和需要达到的除尘效率等多种因素的影响.针对目前环保要求、污染物排放费用的征收情况以及静电除尘器和布袋除尘器在性能上的差异和在各行各业应用的实际情况,对两种除尘器在实际应用中的基本性能做一个简单客观的对比.1)除尘效率布袋除尘器:对人体有严重影响的重金属粒子及亚微米级尘粒的捕集更为有效.通常除尘效率可达99.99%以上,排放烟尘浓度能稳定低于50米g/N米3,甚至可达10 米g/N米3以下,几乎实现零排放.电除尘器:随着国家环保标准的进一步提高和越来越多的电厂燃用低硫煤(或者经过了高效脱硫),比电阻大,即使达标也变得越来越困难.而布袋除尘器的过滤机理决定了它不受燃烧煤种物化性能变化的影响,具有稳定的除尘效率.针对目前国家环保的排放标准和排放费用的征收办法,布袋除尘器所带来的经济效益是显而易见的.2)系统变化对除尘器的影响锅炉系统是一个经常变动和调节的系统,因此从锅炉中出来的烟气物化性能、烟尘浓度、温度等参数也不能保证不发生变化.这一系列的变化,针对不同的除尘器会引起明显不同的变化.下面从主要的几个方面进行对比:(1)送、引风机风量不变,锅炉出口烟尘浓度变化①除尘器:烟尘浓度的变化只引起布袋除尘器滤袋负荷的变化,从而导致清灰频率改变(自动调节).烟尘浓度高滤袋上的积灰速度快,相应的清灰频率高,反之清灰频率低,而对排放浓度不会引起变化.②对静电除尘器:烟尘浓度的变化直接影响粉尘的荷电量,因此也直接影响了静电除尘器的除尘效率,最终反映在排放浓度的变化上.通常烟尘浓度增加除尘效率提高,排放浓度会相应增加;烟尘浓度减小除尘效率降低,排放浓度会相应降低.(2)锅炉烟尘量不变,送、引风机风量变化①对布袋除尘器:由于风量的变化直接引起过滤风速的变化,从而引起设备阻力的变化,而对除尘效率基本没有影响.风量加大设备阻力加大,引风机出力增加;反之引风机出力减小.②对静电除尘器:风量的变化对设备没有什么太大影响,但是静电除尘器的除尘效率随风量的变化非常明显.若风量增大,静电除尘器电场风速提高,粉尘在电场中的停留时间缩短,虽然电场中风扰动增强了荷电粉尘的有效驱进速度,但是这不足以抵偿高风速引起的粉尘在电场中驻留时间缩短和二次扬尘加剧所带来的负面影响,因此除尘效率降低非常明显;反之,除尘效率有所增加,但增加幅度不大.(3)烟气温度的变化①对布袋除尘器:烟气温度太低,结露可能会引起“糊袋”和壳体腐蚀,烟气温度太高超过滤料允许温度易“烧袋”而损坏滤袋.但是如果温度的变化是在滤料的承受温度范围内,就不会影响除尘效率.引起不良后果的温度是在极端温度(事故/不正常状态)下,因此对于布袋除尘器就必须设有对极限温度控制的有效保护措施.②对静电除尘器:烟气温度太低,结露就会引起壳体腐蚀或高压爬电,但是对除尘效率是有好处的;烟气温度升高,粉尘比电阻升高不利于除尘.因此烟气温度直接影响除尘效率,且影响较为明显.(4)气流分布①对布袋除尘器:除尘效率与气流分布没有直接关系,即气流分布不影响除尘效率.但除尘器内部局部气流分布应尽量均匀,不能偏差太大,否则会由于局部负荷不均或射流磨损造成局部破袋,影响除尘器滤袋的正常使用寿命.②对静电除尘器:静电除尘器非常敏感电场中的气流分布,气流分布的好坏直接影响除尘效率的高低.在静电除尘器性能评价中,气流分布的均方根指数通常是评价一台静电除尘器的好坏的重要指标之一.3)运行与管理(1)运行与管理①对布袋除尘器:运行稳定,控制简单,没有高电压设备,安全性好,对除尘效率的干扰因素少,排放稳定.由于滤袋是布袋除尘器的核心部件,是布袋除尘器的心脏,且相对比较脆弱、易损,因此设备管理要求严格.②对静电除尘器:运行中对除尘效率的干扰因素多,排放不稳定;控制相对较为复杂,高压设备安全防护要求高.由于静电除尘器均为钢结构,不易损坏,相对于布袋除尘器,设备管理要求不很严格.(2)停机和启动①对布袋除尘器:方便,但长期停运时需要做好滤袋的保护工作.②对静电除尘器:方便,可随时停机.(3)检修与维护①对布袋除尘器:可实现不停机检修,即在线维修.②对静电除尘器:检修时一定要停机4)设备投资(1)对于常规的烟气条件和粉尘(主要是指比较适合静电除尘器的烟气),两种除尘器排放浓度要达到目前较低的环保要求(如150米g/米3)初期投资布袋除尘器比静电除尘器约高20-35%左右(2)对于低硫高比电阻粉尘、高SiO2、Al2O3类不适合静电除尘器捕集的粉尘,两种除尘器要达到目前较低的环保要求(如150米g/米3)初期投资静电除尘器和布袋除尘器相当或静电除尘器投资高些.(3)通常条件下达到相同的除尘效率或者说达到相同的排放浓度,静电除尘器的投资通常要比布袋除尘器的投资高.以呼和浩特电厂200米W机级为例:布袋除尘器:每台机组的除尘器投资<2000万元,保证排放浓度<50米g/N米3以下.对静电除尘器:按四电场,比集尘面积130米2/米3/S计算.达标250米g/N米3,每台除法器投资约2500万元.5)运行维护费用(1)运行能耗对布袋除尘器:风机能耗大,清灰能耗小.对静电除尘器:风机能耗小,电场能耗大.但是,总体来讲两种除尘器的电耗相当.对于静电除尘器难以捕集的粉尘,或者说当静电除尘器的电场数量超过4电场时,静电除尘器的能耗比布袋除尘器的要高,也就是说此时的静电除尘器运行费用要比布袋除尘器高.如果按照即将出台的新环保标准,静电除尘器要是做到达标话,必定是采用4电场以上的静电除尘器,其电耗也就一定比布袋除尘器高.(2)维护费用布袋除尘器的维护检修费用主要是滤袋更换费,从目前实际运行情况来看,一次滤袋的更换费用只需要1.5-2年排污费比静电除尘器的少缴部分就可以抵偿.静电除尘器的维护维修费用主要是对阳极板、阴极线和振打锤等的更换等.此项费用较高,但年限比较长,约6年左右.(3)经济效益分析实际运行中布袋除尘器的排放浓度约是静电除尘器的10%,因此,电厂采用布袋除尘器实际交缴的排污费也为静电除尘器排污费的1/10左右.如果按照目前国家征收排污费的情况来看,采用布袋除尘器后每炉/每年的排污费少缴部分是相当可观的,至少上百万到几百万元.按照以前达标即不需要交纳排污费的话,采用布袋除尘器就可以免交排污费.另外,布袋除尘器有约5%左右的脱硫效率;这同样可以减少二氧化硫的排污费.总之,新的环保标准出台以后,静电除尘器要想做到达标排放,就必须采用4电场以上的除尘器.此时静电除尘器的初期投资已经比布袋除尘器高,同时4电场以上的静电除尘器(或者4电场的高比积尘面积)运行电耗要比布袋除尘器的高很多.因此在新的环保要求下,静电除尘器即使达标,其初期投资和运行费用都比布袋除尘器高.另外,静电除尘器的排放浓度总是在布袋除尘器的10倍左右,目前新的排污费制度下,即使达标了也要对排放粉尘量进行收费,因此两种除尘器即使达标以后,静电除尘器又比布袋除尘器多支出了一笔费用.因此,布袋除尘器必将成为工业粉尘控制的首选设备.表1 布袋除尘器与电除尘器的比较表通过比较,选择袋式除尘器.3.2.脱硫工艺设计3.2.1.脱硫方法概述目前,世界上烟气脱硫工艺有上百种, 但具有实用价值的工艺仅十几种.根据脱硫反应物和脱硫产物的存在状态可将其分为湿法、干法和半干法 3 种.湿法脱硫工艺应用广泛, 占世界总量的85.0%,其中氧化镁法技术成熟,尤其对中、小锅炉烟气脱硫来说,具有投资少,占地面积小,运行费用低等优点,非常适合我国的国情.采用湿法脱硫工艺,要考虑吸收器的性能,其性能的优劣直接影响烟气的脱硫效率、系统的运行费用等.旋流板塔吸收器具有负荷高、压降低、不易堵、弹性好等优点,可以快速吸收烟尘,具有很高的脱硫效率.3.2.2.工艺比选1)脱硫工艺及脱硫吸收器比较选择(1) 脱硫工艺比较选择(见表2)表2 脱硫工艺比较表3 脱硫工艺比较(2)石灰(石)/石膏湿法脱硫工艺和氧化镁脱硫法的特点对比①石灰(石)/石膏湿法脱硫工艺石灰(石)/石膏湿法脱硫工艺是采用石灰石(CaCO3)或石灰(CaO)作脱硫吸收剂原料,经消化处理后加水搅拌制成氢氧化钙(Ca(OH)2)作为脱硫吸收浆.石灰或吸收剂浆液喷入吸收塔,吸附其中的SO2气体,产生亚硫酸钙,进而氧化为硫酸钙(石膏)副产品.该工艺的优点主要是:A、脱硫效率高,在Ca/S比小于1.1的时候,脱硫效率可高达 90%以上;B、吸收剂利用率高,可达到90%;C、吸收剂资源广泛,价格低廉;D、适用于高硫燃料,尤其适用于大容量电站锅炉的烟气处理;E、副产品为石膏,高品位石膏可用于建筑材料.该工艺的缺点是:A、系统复杂,占地面积大;B、造价高,一次性投资大;C、运行问题较多——由于副产品CaSO4易沉积和粘结,所以, 容易造成系统积垢,堵塞和磨损;D、运行费用高,高液/气比所带来的电、水循环和耗量非常大;E、副产品处理问题——目前,世界上对该副产品处理,主要采用抛弃和再利用两种方法:西欧和日本因缺乏石膏资源,所以用此副产品做建筑用石膏板,与此同时,当地建筑规范也为该产品的推广使用提供了方便.但对副产品石膏的成分要求严格(CaSO4>96%).在美国,因天然石膏资源丰富,空地较多,过去一般采用抛弃处理.在中国,天然石膏资源丰富,而石灰石的成分却很难保证,因此脱硫石膏的成分不稳定,建筑行业很难采用;对于建在城市近郊或工业区的需要脱硫的电厂,又很难容纳大量石膏渣液的抛弃,即使有空闲场地抛弃,从长远来讲,仍然可能造成固体废弃物的二次污染.因而副产物处理存在问题.F、由于该工艺技术成熟,运用广泛,目前国家有相应技术规范,但国家环保总局在脱硫技术指导文件中明确指出该种方法适用于大型电站锅炉的脱硫,中小锅炉运用存在规模不经济等问题.G、为适应国内中小型锅炉的烟气脱硫,对该工艺进行了改造运用,减少脱硫剂制备和石膏生成系统尚可,但其他部分的或缺带来诸多问题,因此要谨慎用之.②氧化镁脱硫法氧化镁脱硫技术是利用氢氧化镁作为脱硫剂吸收烟气中的二氧化硫,生成亚硫酸镁,并通入空气将亚硫酸镁生成溶解度更大的硫酸镁.氢氧化镁作脱硫剂具有反应活性大、脱硫效率高、液气比小等优点,因此具有综合投资低,运行费用低等特点.氧化镁吸收SO2的湿法脱硫方式是目前适合于中、小型锅炉烟气脱硫技术最为成熟的脱硫方式之一.综合氢氧化镁脱硫法具有以下四个特点:A、氧化镁原料取得容易目前包括在日本、首尔、东南亚地区、台湾地区等均有普遍使用的实绩和经验,而所使用的的氧化镁大部分均来自大陆地区.我国拥有丰富的氧化镁资源,储量约为160亿吨,占全世界的80%左右,环渤海湾的山东、辽宁地区以及山西都有丰富的产量.由于广泛地运用,使该技术相对于其他脱硫技术更加成熟.B 、米gO工艺也是技术成熟的脱硫工艺,该工艺在日本已应用了100多个项目,台湾的电厂约95﹪是.米gO法,美国波士顿的米gstic电厂150米w机组.米gO湿法脱硫1982年投产.C、米gO法脱硫效率达到90﹪~98﹪,因为米gO活性强,实例表明在相同操作条件下,米gO作为吸收剂比用CaCO3作为吸收剂时吸附效率高.D 、脱除等量的SO2消耗的米gO量仅为CaCO3的40﹪.E 、米gO法脱硫循环液呈溶液状,不易结垢,不会堵塞.氧化镁湿法的脱硫产物硫酸镁是一种溶解度很大的物质,因此在吸收塔脱硫的反应过程中,不似石灰石(石灰)/石膏法会产生结垢或堵塞的问题.F、脱硫后溶液,处理后可直接排放,无二次污染.G、脱硫设备简单,操作简单,成本低.脱硫系统包括熟化系统、吸收系统、废液处理系统,系统简单明了,现场布置简洁紧凑,系统运行安全可靠.L、脱硫产物的用途如果把米gO法脱硫工艺产物,不经氧化曝气则可以把浆液脱水湿渣,其组成米gSO3 60~70% 米gSO4 20~30 %溶解状,杂质10% ,湿渣可以作为农用肥料.可直接作基肥,追肥和叶面肥.植物正常发育的所需镁量,一般为干重5g/千克左右.施用镁肥不仅可增加作物产量,还可改善产品品质,如镁肥对甘蔗、香蕉、烟叶产量和品质都有良好作用.据调查本地区盛产甘蔗、香蕉.根据全国土壤普查表明不少地区土壤缺镁比较严重,缺镁土壤面积巨大,大约占全国耕地面积的5.8 ,若对每亩地施镁肥,则每年需求镁肥量十分巨大.2) 脱硫吸收器比较选择脱硫吸收器的选择原则, 主要是看其液气接触条件、设备阻力以及吸收液循环量.脱硫吸收器比较选择如表4所示.表4 脱硫塔性能吸收设备中: 喷淋塔液气比高, 水消耗量大; 筛板塔阻力较大, 防堵性能差; 填料塔防堵性能差, 易结垢、黏结、堵塞, 阻力也较大; 湍球塔气液接触面积虽然较大, 但易结垢堵塞, 阻力较大.相比之下, 旋流板塔具有负荷高、压降低、不易堵、弹性好等优点, 适用于快速吸收过程, 且具有很高的脱硫效率.因此, 选用旋流板塔脱硫吸收器.3.2.3.工艺原理(1) 氧化镁法脱硫原理氧化镁法脱硫的主要原理:在洗涤中采用含有米gO 的浆液作脱硫剂, 米gO 被转变为亚硫酸镁(米gSO3) 和硫酸镁(米gSO4) , 然后将硫从溶液中脱除.氧化镁法脱硫工艺有如下特点:A 、氧化镁法脱硫工艺成熟, 目前日本、中国台湾应用较多, 国内近年有一些项目也开始应用.B、脱硫效率在90.0%~95.0%之间.C 、脱除等量的SO2, 米gO的消耗量仅为CaCO3的40.0%.D 、要达到90.0%的脱硫效率, 液气比在3~5L/米3之间, 而石灰石- 石膏工艺一般要在10~15L/米3之间.E、我国米gO储量约80 亿t, 居世界首位, 生产量居世界第一.(2) 旋流板塔吸收器脱硫原理旋流板塔工作时,烟气由塔底从切向高速进入,在塔板叶片的导向作用下旋转上升.逐板下流的液体在塔板上被烟气喷成雾滴状,使气液间有很大的接触面积.液滴在气流的带动下旋转,产生的离心力强化气液间的接触,最后被甩到塔壁上,沿壁下流,经过溢流装置流到下一层塔板上,再次被气流雾化而进行气液接触.由于塔内提供了良好的气液接触条件,气体中的SO2等酸性气体被碱性液体吸收的效果好;旋流板塔同时具有很好的除尘性能,气体中的尘粒在旋流塔板上被水雾粘附,并受离心力作用甩到塔壁而除去,从而具有较高的除尘除雾效率.来自锅炉的含尘烟气首先切向进入塔底段,呈螺旋形上升到旋流板,从旋流板叶片间的开孔高穿过,将经特殊给液装置分配到各叶片上的洗涤溶液雾化,雾化后的洗涤溶液获得较高比表面积,并与废气接触完成脱硫除尘.3.3.工艺流程3.3.1.工艺流程图燃煤采暖锅炉烟气处理工艺流程3.3.2.工艺流程简述工艺流程主要分为两个工段.第一个工段为烟气除尘,第二个工段为烟气脱硫.该工艺采用过滤式脉冲布袋除尘器,脉冲袋式除尘器主要由上箱体、中箱体、下箱体和控制器等组成.含尘空气从进气口进入除尘箱,因气体突然扩张,流速骤然降低,颗料较粗的粉尘,靠其自重力向下沉降,落入灰斗.细小粉尘通过各种效应被吸附在滤袋外壁,经滤袋过滤后的净化空气,通过文氏管进入上箱体,从出气口排出,被吸附在滤袋外壁的粉尘,随着时间的增长,越积越厚,除尘器阻力逐渐上升,处理的气体量不断减少,为了使除尘器经常保持有效状态,设备阻力稳定在一定的范围内,就需要清除吸附在滤袋外面的积灰.经除尘后的烟气进入第二个脱硫工段,采用湿法烟气脱硫技术在旋流板塔吸收器中对除尘后的烟气进行脱硫处理.在洗涤液中采用含有米gO的浆液作脱硫剂, 米gO 被转变为亚硫酸镁(米gSO3) 和硫酸镁(米gSO4) , 然后将硫从溶液中脱除.旋流板塔工作时,烟气由塔底从切向高速进入,在塔板叶片的导向作用下旋转上升.逐板下流的液体在塔板上被烟气喷成雾滴状,使气液间有很大的接触面积.液滴在气流的带动下旋转,产生的离心力强化气液间的接触,最后被甩到塔壁上,沿壁下流,经过溢流装置流到下一层塔板上,再次被气流雾化而进行气液接触.由于塔内提供了良好的气液接触条件,气体中的SO2等酸性气体被碱性液体吸收的效果好;旋流板塔同时具有很好的除尘性能,气体中的尘粒在旋流塔板上被水雾粘附,并受离心力作用甩到塔壁而除去,从而具有较高的除尘除雾效率.主要化学反应式:米gO + H2O →米g(OH)2SO2 + H2O → H2SO3→ 2H+ + SO3-2。
炼钢电炉炉外排烟净化系统侧吸罩及其排烟量设计探讨

炼钢电炉炉外排烟净化系统侧吸罩及其排烟量设计探讨置,即最佳捕集点的选择、吸气流速度衰减规律、罩口面积虽然对控制速度影响不大,但罩口面积增电炉烟气上升速度及其扩散规律、侧吸罩在控制点大会对侧吸罩安装及电炉冶炼操作、维护检修带来所造成的气流速度,即控制速度(也称吸捕速度 ) 不便。
的确定等。
2 烟气上升速度及其扩散规律 1 吸气流速度衰减规律高温烟气自炉内经电极孔隙上升的原因主要有D alla,V alla 通过大量的验证得出结论:对于两方面因素:一是由于炉内金属炉料中碳的氧化,罩口为圆形或矩形( 宽长比大于 0.2)的外部吸气不断产生大量烟气,在压力作用下,烟气流以一定罩,沿罩子轴线的气流速度衰减计算公式为: 速度上升;二是由于烟气温度大大高于周围空气温度,并通过传导和对流作用传给周围空气,在浮力2.0/作用下产生上升速度,这两种上升速度的合成即可。
()/=( 10+)/1 !!"##!!!c x看作是烟气上升速度。
式中:—吸气罩口平均气流速度();—2345 !$—距罩口处气流速度(); —%3 2365!"—沿轴线距罩口的距离;—" 7 3 浮力上升速度!"# 8 ——吸气罩口面积。
研究了热源上部上升 # 2 >?@A 3(气流与周围空气的紊流混合,并又,则:9&:# !$8提出了计算在一假想源以上任何 ()。
() !9&: 1;"<#!!!!!8"高度处热气流的上升速度及其扩 =式中:—吸气罩排气量()。
—& 73:5 散直径的方程式。
罩口面积与控制速度关系见表。
1这一假想点源()点处于 ; 实际热源表面以下距离为3 ’ 收稿日期:$修回日期: C$1$11C$1$18("";("";处,见图。
1 图 1 热源上部作者简介:刘跃军( 1967- ),男,山西原平人。
6#回转式阳极炉纯氧燃烧技术附件-8.25

6#回转式阳极炉清洁燃料改造项目富氧助燃燃烧系统技术协议买方:云南铜业股份有限公司代表签字(盖章):年月日卖方:徐州燃控科技股份有限公司代表签字(盖章):年月日一、概述云南铜业股份有限公司(买方)与徐州燃控科技股份有限公司(卖方)经过友好协商。
就卖方向买方提供的应用于云南铜业股份有限公司6#回转式阳极炉清洁燃料改造项目富氧助燃燃烧系统的制造、指导安装、调试及现场服务等相关事宜,达成以下协议;本技术附件所使用的标准如与双方所执行的标准发生矛盾时,按较高标准执行;二、设计规范和标准GB/T19839-2005 工业燃油燃气燃烧器通用技术条件GB500028-2006 天然气国标GB 16914-2003 燃气燃烧器具安全技术条件GB/T3863-2008 工业氧GB50030-2007 氧气站设计规范GB 50183-2004 《石油天然气工程设计防火规范》GB16912-2008 氧气及相关气体安全技术规程GB50236-98 现场设备、工业管道焊接工程施工及验收规范GB/T985-2008 气焊、手工电弧焊及气体保护焊焊缝坡口的基本形式与尺寸GB191-2008 包装储运图示标识GB6388-1986 运输包装收发货标志GB/T13384 机电产品包装通用技术条件JB/ZQ4000.3-86 焊接件通用技术条件《石油化工设备与管道涂料防腐蚀技术规范》 SH3022-1999三、技术说明3.1 设备名称天然气-纯氧卷吸燃烧系统。
3.2 纯氧卷吸燃烧系统用途用于阳极炉精炼过程中天然气的燃烧。
以天然气-纯氧卷吸燃烧系统代替原先的空气-煤粉燃烧系统,以达到稳定生产、节约燃料、降低能源成本、以及减少排放的目的。
3.3 纯氧卷吸装置使用条件3.3.1 安装地点安装于阳极炉精炼厂房内的阳极炉操作平台。
3.3.2 装置要求纯氧卷吸燃烧系统使用天然气做为燃料,采用氧气作为助燃剂。
3.3.3 装置能力天然气流量:400Nm3/h(Max);氧气流量:800Nm3/h(Max);3.4 对外围条件的要求外围条件及工艺规格氧气供应压力0.35-0.4Mpa流量800Nm3/h(Max)纯度≥99%天然气供应最大压力0.3-0.35 Mpa设计流量400 Nm3/h(Max)压缩空气供应压力0.3-0.35 Mpa设计流量180 Nm3/h(Max)仪表气供应压力0.35-0.5 Mpa氮气供应压力0.2-0.5 Mpa设计流量60 Nm3/h(Max)电源要求控制柜220VAC 50HZ 10A点火枪220VAC 50HZ 5A四、设备描述4.1纯氧卷吸燃烧系统4.1.1燃烧器以天然气作为燃料,采用氧气做为助燃介质的,天然气从燃烧器中心高速引入,与10~15%的助燃氧气进行预混燃烧,形成稳定的根部火焰。
某钢厂30T电炉采用气幕加屋顶罩排烟除尘系统的设计方案

某钢厂30T电炉采用气幕加屋顶罩排烟除尘系统的设计方案一、现有除尘系统存在的问题电弧炉在炼钢过程中不断有烟尘产生,并选出炉外。
因炉体在加料、出钢、扒渣时炉体需移动和倾钭,所以整个冶炼过程中,炉体本身是一个多点不固定的烟尘排放的污染源,加之电极需不断升降和更换,因此电炉除尘器系统的设计关键在于烟尘捕集问题,设计出既不影响冶炼工艺、又不防碍操作;捕集效率高的排烟罩。
从七十年代开始,实际应用有各种形式的局部排烟罩,如钳形罩、环形罩、上部吸罩及吹罩等,均有一定的捕集效果,但捕集效率不高。
八十年代又出现大密闭罩及屋顶罩与内排烟相结合的排烟系统。
大密闭罩虽然捕集效率高,因整个电炉包在其中,操作不方便,大罩需经常开合往往罩体受热变形开启不灵活,至使大密闭罩坚持运行的不多。
上钢五厂采用屋顶罩与内排烟相结合方式,自投入使用以来一直坚持运行,但屋顶罩排风量较大,当车间有横向气流时,屋顶罩不能有效捕集。
故鹏鹤环保公司在“带有空气幕排气罩计算新方法”实验研究取得成果基础上,提出“气幕与屋顶罩结合排烟系统”的设计方案。
二、没计方案简介1、设计说明原始设计条件:Hx2——30T电炉一台,电炉内径4.7m、外壳直径5.0m。
高架式安装,安装电炉平台距地面标高6m,炉顶大架距地面标高8.5~9.0m电炉顶屋檐下标高26m。
炉内烟气温度1200℃。
设计方案如图1 1、电炉2、送风空气幕3、屋顶罩① 在电炉炉盖上方3/4周圈长度(靠变压器室一侧不设)上,设计一个喷口向上的送风气幕,它将电炉的三个电极孔和炉盖圈包围在气幕内,喷嘴周围直径为5.2m喷嘴向内倾斜12°在条缝喷嘴内设一定角度的导流叶片,使喷吹气流呈30~40°角上升。
②在电炉正上方屋顶下檐设一屋顶排烟罩。
烟尘经屋顶捕集后输送至布袋除尘器,经风机、排气筒排至大气。
屋顶排烟罩设方形或圆形,尺寸6×6m(φ6m),排气速度1.2m/s(1.5m/s)。
铜冶炼阳极炉用环保烟罩的研制
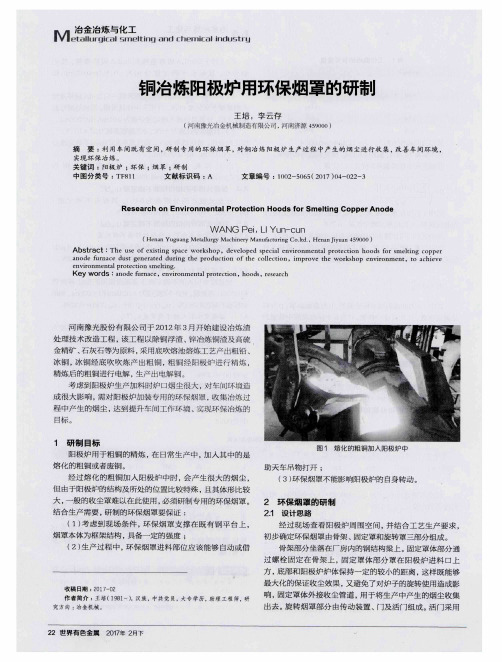
骨架部 分坐落在厂房 内的钢结构粱上 。固定罩体部分 通 过 螺检 固定 在骨 架 上 , 固定 罩体 部 分罩 在阳 极炉 进料 口上 方, 底部和阳极 炉炉体保 持一定 的较小的距 离 , 这样既能 够 最大化 的保证收 尘效 果 , 又避免了对炉 子的旋转使用造成 影 响, 固定罩体外 接收尘管 道 , 用于将生 产中产生 的烟尘收 集 出去。旋转 烟罩部 分 由传 动装置 、 门及活 门组成 。 活 门采 用
Ke y wo r d s a n o d e f u r n a c e ,e n v i r o n me n t a l p r o t e c t i o n ,h o o d s , r e s e a r c h
河南豫 光股 份有 限公司 于 2 0 1 2 年3 月 开始 建设冶 炼渣 处理技 术改造 工程 , 该工程 以除铜 浮渣 、 锌 冶炼 铜渣 及高硫
( 3) 环保烟 罩不能影响阳极炉 的 自身转动 。
2 环保烟 置的研 制
2 . 1 设计思路 经 过现场 查看 阳极炉 周围空 间 , 并结 合工 艺生产要 求 , 初 步 确 定 环 保 烟 罩 由 骨架 、 固定罩和旋转罩三部 分组成 。
( 1) 考 虑到 现场 条件 , 环保 烟 罩支 撑在 既有 钢 平台 上 , 烟罩本体为 框架结构 , 具备 一定的强度 ;
金精矿 、 石灰 石等为原料 , 采用底 吹熔池熔 炼工艺产出粗铅 、
冰铜 , 冰铜 经底 吹吹 炼产 出粗锏 , 粗铜 经 阳极炉 进行 精炼 ,
精 炼 后 的 粗 铜 进 行 电解 , 生产出电解铜 。
阳极炉
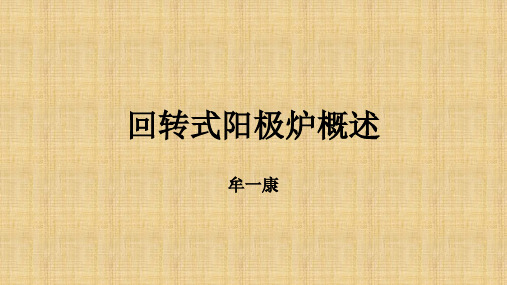
• 回转式阳极炉炉口(也称加料口)处在炉体中心位置,规格为 1200mm*1800mm,炉口备用炉口盖和炉口启闭装置。炉口启闭装置 分液压和气动两种。炉口盖与炉口启闭装置相连。炉口装有四块冷却 水套。两个氧化还原风口开设在筒体两侧,离筒体两端约300mm,它 与炉口约呈45度夹角。燃烧器和燃烧室分别安装在筒体两端。筒体由 40-60mm厚锅炉钢板焊接而成。筒体内砌400-500mm厚耐火材料。 • 燃烧器固定在排烟口的相对端盖上,而燃烧装置和燃烧气管一起连接 在燃烧器上。燃烧器可随炉体一起倾动。 • 炉体支撑装置由四个拖轮构成,拖轮均采用复式托轮组传动带轮缘, 另一端为光面托轮。回转炉的滚圈为两档,其中一个与大轮组成一体, 构成炉体传动系统的一部分。 • 回转炉是火法精炼的主体设备,其关键部位是氧化还原风口、出铜口、 加料口、燃烧器,对耐火材料的选用有严格要求。出铜口为特制异形 镁铬砖,而筒体两端墙的保温层为65mm厚镁质砖,内层为镁铬砖, 风口则采用特制的三氧化二铬含量高的电熔再结合镁铬砖以强化耐高 温抗冲刷、抗腐蚀作用。 • 燃烧室是回转炉的辅助设备,它不装熔融铜,只是利用稀释风继续燃 烧回转式精炼炉出来的烟气,烟气温度虽在1200℃,但不起冲刷作用。 它选用的耐火材料是粘土砖、高铝砖和不定型耐火捣打料。
四、回转式阳极炉倾动方式
• 回转式阳极炉传动装置主要由主电机、副电机、气动电机、主变 速箱、副变速箱、电磁离合器和大小齿圈组成。回转炉的倾转是 依靠电动机和气动电机、电磁离合器变速箱以及控制装置来实现 的。 • 回转式阳极炉的倾动方式设有快速倾动、慢速倾动和气动以及事 故(气动电机)倾转。一般情况下氧化、还原浇铸刚开始阶段使 用快速倾转。而放渣、浇铸、修炉使用慢速倾动。气动一般是指 炉体已过顶部位置,而炉选开关又处在炉前控制,此时则使用气 动控制倾转炉体,事故倾转是指炉体正在加料、氧化、还原、浇 铸时突然停电,此时气动电机会自动气动,将炉体从不同方向转 到顶部位置。快速倾转的速度为0.6r/min,慢速倾转和事故倾转 的速度为0.06r/min。
(完整版)加热炉设计毕业设计
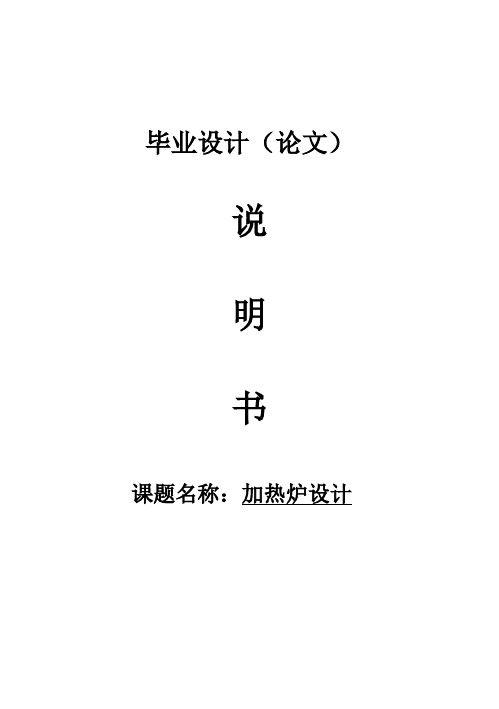
毕业设计(论文)说明书课题名称:加热炉设计毕业设计(论文)原创性声明和使用授权说明原创性声明本人郑重承诺:所呈交的毕业设计(论文),是我个人在指导教师的指导下进行的研究工作及取得的成果。
尽我所知,除文中特别加以标注和致谢的地方外,不包含其他人或组织已经发表或公布过的研究成果,也不包含我为获得及其它教育机构的学位或学历而使用过的材料。
对本研究提供过帮助和做出过贡献的个人或集体,均已在文中作了明确的说明并表示了谢意。
作者签名:日期: -指导教师签名:日期:使用授权说明本人完全了解大学关于收集、保存、使用毕业设计(论文)的规定,即:按照学校要求提交毕业设计(论文)的印刷本和电子版本;学校有权保存毕业设计(论文)的印刷本和电子版,并提供目录检索与阅览服务;学校可以采用影印、缩印、数字化或其它复制手段保存论文;在不以赢利为目的前提下,学校可以公布论文的部分或全部内容。
作者签名:日期:学位论文原创性声明本人郑重声明:所呈交的论文是本人在导师的指导下独立进行研究所取得的研究成果。
除了文中特别加以标注引用的内容外,本论文不包含任何其他个人或集体已经发表或撰写的成果作品。
对本文的研究做出重要贡献的个人和集体,均已在文中以明确方式标明。
本人完全意识到本声明的法律后果由本人承担。
作者签名:日期:年月日学位论文版权使用授权书本学位论文作者完全了解学校有关保留、使用学位论文的规定,同意学校保留并向国家有关部门或机构送交论文的复印件和电子版,允许论文被查阅和借阅。
本人授权大学可以将本学位论文的全部或部分内容编入有关数据库进行检索,可以采用影印、缩印或扫描等复制手段保存和汇编本学位论文。
涉密论文按学校规定处理。
作者签名:日期:年月日导师签名:日期:年月日注意事项1.设计(论文)的内容包括:1)封面(按教务处制定的标准封面格式制作)2)原创性声明3)中文摘要(300字左右)、关键词4)外文摘要、关键词5)目次页(附件不统一编入)6)论文主体部分:引言(或绪论)、正文、结论7)参考文献8)致谢9)附录(对论文支持必要时)2.论文字数要求:理工类设计(论文)正文字数不少于1万字(不包括图纸、程序清单等),文科类论文正文字数不少于1.2万字。
局部排风罩设计

2.4 接受罩某些生产过程或设备本身会产生或诱导一定的气流运动,而这种气流运动的方向是固定的,我们只需把排风罩设在污染气流前方,让其直接进入罩内排出即可,这类排风罩称为接受罩。
顾名思义,接受罩只起接受作用,污染气流的运动是生产过程本身造成的,而不是由于罩口的抽吸作用造成的。
图2-10是接受罩的示意图。
接受罩的排风量取决于所接受的污染空气量的大小,它的断面尺寸不应小于罩口处污染气流的尺寸。
2.4.1 热源上部的热射流接受罩接受的气流可分为两类:粒状物料高速运动时所诱导的空气流动(如砂轮机等)、热源上部的热射流两类。
前者影响因素较多,多由经验公式确定。
后者可分为生产设备本身散发的热烟气(如炼钢炉散发的高温烟气)、高温设备表面对流散热时形成的热射流。
通常生产设备本身散发的热烟气由实测确定,因而我们着重分析设备表面对流散热时形成的热射流。
热射流的形态如图2-11示。
热设备将热量通过对流散热传给相邻空气,周围空气受热上升,形成热射流。
我们可以把它看成是从一个假想点源以一定角度扩散上升的气流,根据其变化规律,可以按以下方法确定热射流在不同高度的流量、断面直径等。
在4.7~9.0/=B H 的范围内,在不同高度上热射流的流量2/33/104.0Z Q L z = m 3/s (2-3)式中 Q ——热源的对流散热量,kJ/sB H Z 26.1+= m (2-4)式中 H ——热源至计算断面的距离,m B ——热源水平投影的直径或长边尺寸,m 。
对热射流观察发现,在离热源表面()B 2~1处射流发生收缩(通常在B 5.1以下),在收缩断面上流速最大,随后上升气流逐渐缓慢扩大。
近似认为热射流收缩断面至热源的距离p A H 5.10≤=1.33B (p A 为热源的水平投影面积),收缩断面上的流量按下式计算2/33/10167.0B Q L = m 3/s (2-5)热源的对流散热量t F Q ∆=α J/s (2-6)F ——热源的对流放热面积,m 2 t ∆——热源表面与周围空气的温度差,℃α——对流放热系数,α=A ·∆t 3/1,J/m 2·s ·℃式中 A ——系数,对于水平散热面A =1.7,垂直散热面A =1.13, 在某一高度上热射流的断面直径B H D z +=36.0 m (3-7) 2.4.2 罩口尺寸的确定理论上只要接受罩的排风量、断面尺寸等于罩口断面上热射流的流量、尺寸,污染气流就会被全部排除。
毕业设计说明书-----锅炉设计
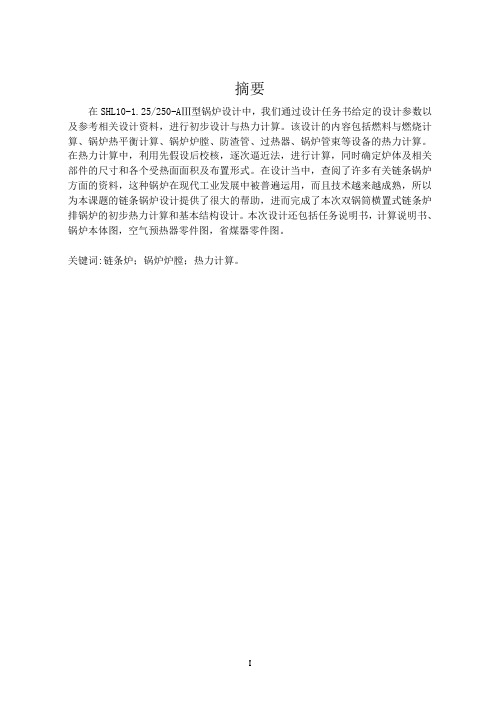
摘要在SHL10-1.25/250-AⅢ型锅炉设计中,我们通过设计任务书给定的设计参数以及参考相关设计资料,进行初步设计与热力计算。
该设计的内容包括燃料与燃烧计算、锅炉热平衡计算、锅炉炉膛、防渣管、过热器、锅炉管束等设备的热力计算。
在热力计算中,利用先假设后校核,逐次逼近法,进行计算,同时确定炉体及相关部件的尺寸和各个受热面面积及布置形式。
在设计当中,查阅了许多有关链条锅炉方面的资料,这种锅炉在现代工业发展中被普遍运用,而且技术越来越成熟,所以为本课题的链条锅炉设计提供了很大的帮助,进而完成了本次双锅筒横置式链条炉排锅炉的初步热力计算和基本结构设计。
本次设计还包括任务说明书,计算说明书、锅炉本体图,空气预热器零件图,省煤器零件图。
关键词:链条炉;锅炉炉膛;热力计算。
AbstractAccording to design parameters that has given design and the relevant design information,we make heat calculations and preliminary design calculation on SHL10-1.25/250-A Ⅲboiler.The main contents include introduction, fuel and combustion calculations, boiler heat calculation balance, boiler furnace,anti-thermal residue management and other computing devices.In the thermal calculation, firstly,we use the methods of assumptions, and then check them and successive approximation to calculateing .Simultaneously,we determine the size of furnace and related components and layout of various heating surface.In the design, through a lot of information about the chain boiler, this boileris are widely used in the modern industry, and the technology is more and more ripe, so it provides a helpful program for the subject-based chain boiler design.this design also includes mission statement ,calculation specifications,the CAD chart of the boiler body , air preheater and economizer.Keywords: chain boiler ; furnace ;thermal calculation.目录1绪论 (1)1.1 设计题目的提出 (1)1.1.1 工业锅炉的概述 (1)1.1.2 燃煤工业锅炉燃烧现状 (1)1.2 国内外研究现状 (2)1.3 设计内容与研究方法 (2)1.3.1 设计主要内容 (3)1.3.2 研究方法 (3)1.3.3 校核热力计算主要内容 (3)1.3.4 热力计算步骤 (4)1.3.5 设计中遇到的主要问题及解决办法 (4)2设计任务书 (6)2.1 设计题目 (6)2.2 原始资料 (6)2.3 燃料特性 (6)3炉膛热力计算 (7)3.1 烟道空气系数及受热面漏风系数 (7)3.2 辅助计算 (8)3.2.1 理论空气与烟气的特性计算 (8)3.2.2 燃烧产物容积和焓的计算 (10)3.2.3 锅炉热平衡及燃料消耗量计算 (12)3.2.4 锅炉热平衡及燃料消耗量计算 (21)3.3 炉膛几何特性及热力计算 (21)3.3.1 燃烧室尺寸假定与校核 (23)3.3.2 炉膛传热计算参数 (28)4对流受热面的热力计算 (36)4.1 锅炉的对流受热面的概述 (36)4.1.1 对流过热面 (36)4.1.2 对流传热过程 (36)4.2 对流受热面传热的计算公式 (36)4.3 防渣管结构特性及热力计算 (44)4.4 过热器结构特性及热力计算 (47)4.5 锅炉管束结构特性及热力计算 (47)4.6 省煤器和空气预热器结构特性及热力计算 (48)5热力计算汇总与校核 (49)6结论 (50)致谢 (51)参考文献 (52)1绪论1.1 设计题目的提出1.1.1 工业锅炉的概述我国为了与发电用的大型锅炉相区别,把容量65吨/时以下为工业生产供热、为建筑物供暖的锅炉称为工业锅炉。
例题参考资料 200t氧气转炉烟气净化及回收系统设计
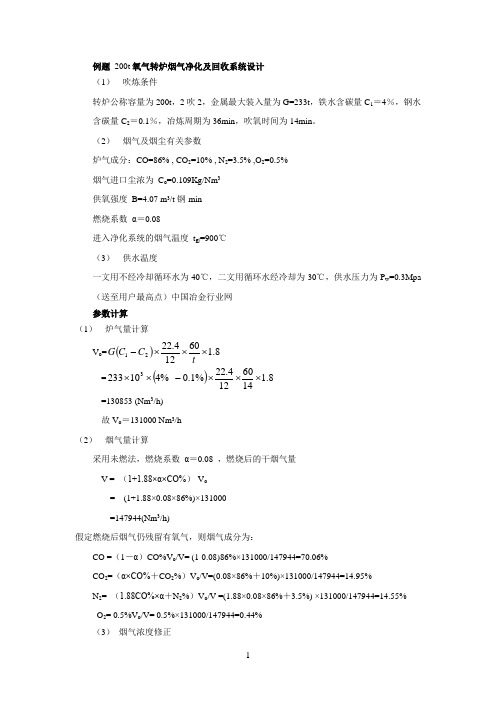
例题 200t 氧气转炉烟气净化及回收系统设计(1) 吹炼条件转炉公称容量为200t ,2吹2,金属最大装入量为G=233t ,铁水含碳量C 1=4%,钢水含碳量C 2=0.1%,冶炼周期为36min ,吹氧时间为14min 。
(2) 烟气及烟尘有关参数炉气成分:CO=86% , CO 2=10% , N 2=3.5% ,O 2=0.5%烟气进口尘浓为 C o =0.109Kg/Nm 3供氧强度 B=4.07 m 3/t 钢·min燃烧系数 α=0.08进入净化系统的烟气温度 t gj =900℃(3) 供水温度一文用不经冷却循环水为40℃,二文用循环水经冷却为30℃,供水压力为P w =0.3Mpa (送至用户最高点)中国冶金行业网参数计算(1) 炉气量计算V o =()8.160124.2221⨯⨯⨯-tC C G =()8.11460124.22%1.0%4102333⨯⨯⨯-⨯⨯ =130853 (Nm 3/h)故V o =131000 Nm 3/h(2) 烟气量计算采用未燃法,燃烧系数 α=0.08 ,燃烧后的干烟气量V = (1+1.88×α×CO%)·V o= (1+1.88×0.08×86%)×131000=147944(Nm 3/h)假定燃烧后烟气仍残留有氧气,则烟气成分为:CO =(1-α)CO%V o /V= (1-0.08)86%×131000/147944=70.06%CO 2=(α×CO%+CO 2%)V o /V=(0.08×86%+10%)×131000/147944=14.95% N 2= (1.88CO%×α+N 2%)V o /V =(1.88×0.08×86%+3.5%) ×131000/147944=14.55%O 2= 0.5%V o /V= 0.5%×131000/147944=0.44%(3) 烟气浓度修正根据回收中期,烟气量为炉气量的147944/131000=1.1293倍,故进口烟尘浓度应作修正,即:CD=0.109/1.1293=0.0965(Kg/Nm3)(4)回收煤气量的计算每吨钢产生的炉气量等于1000×(4%-0.1%)×22.4÷12×1÷(0.86+0.1)=75.8(Nm3)按烟气生成倍率为1.1293倍,则每吨钢产生的煤气量等于1.1293×75.8=85.6Nm3,考虑到前后期不回收煤气,定回收率为70%,即每吨钢可以回收的煤气量为0.70×85.6=59.92(Nm3)。
设计一座公称容量为80吨的转炉和氧枪

辽宁科技学院课程实践报告课程实践名称:设计一座公称容量为X吨的转炉和氧枪指导教师:班级:姓名:2011年7 月12 日课程设计(论文)任务书题目:设计一座公称容量为80吨的转炉和氧枪系别:冶金工程系专业:冶金技术班级:学生姓名:学号:指导教师(签字):2011年 6 月 27日一、课程设计的主要任务与内容一、氧气转炉设计1.1氧气顶吹转炉炉型设计1.2氧气转炉炉衬设计1.3转炉炉体金属构件设计二转炉氧枪设计2.1 氧枪喷头尺寸计算2. 2氧枪枪身和氧枪水冷系统设计2.3升降机构与更换装置设计2.4氧气转炉炼钢车间供氧二、设计(论文)的基本要求1、说明书符合规范,要求打印成册。
2、独立按时完成设计任务,遵守纪律。
3、选取参数合理,要有计算过程。
4、制图符合制图规范。
三、推荐参考文献(一般4~6篇,其中外文文献至少1篇)期刊:[序号] 作者.题名[J].期刊名称.出版年月,卷号(期号):起止页码。
书籍:[序号] 著者.书写[M].编者.版次(第一版应省略).出版地:出版者,出版年月:起止页码论文集:[序号] 著者.题名[C].编者. 论文集名,出版地:出版者,出版年月:起止页码学位论文:[序号] 作者.题名[D].保存地:保存单位,年份专利文献:[序号] 专利所有者.专利题名[P].专利国别:专利号,发布日期国际、国家标准:[序号] 标准代号,标准名称[S].出版地:出版者,出版年月电子文献:[序号] 作者.电子文献题名[文献类型/载体类型].电子文献的出版或可获得地址,发表或更新日期/引用日期报纸:[序号]作者.文名[N].报纸名称,出版日期(版次)四、进度要求序号时间要求应完成的内容(任务)提要1 2011年6月27日-2011年6月29日调研、搜集资料2 2011年6月30日-2011年7月2日论证、开题3 2011年7月3日-2011年7月5日中期检查4 2011年7月6日-2011年7月7日提交初稿5 2011年7月8日-2011年7月10日修改6 2011年7月11日-2011年7月12日定稿、打印7 2011年7月13日-2011年7月15日答辩五、专业教研室审核意见教研室主任签字:年月日六、教学系审核意见教学副主任签字:年月日注:1.本任务书由指导教师编制完成,经教研室及所在系审核同意后生效。
(整理)余热锅炉系统介绍.

(整理)余热锅炉系统介绍.五鑫铜业余热锅炉系统简介余热锅炉系统由奥炉余热锅炉(ASFWHB)、转炉余热锅炉(CFWHB)、硫酸转化余热锅炉,2 台同规格阳极炉余热锅炉(RFWHB)等5 台余热锅炉以及一套100t的大气式热力除氧器和两套磷酸盐加药装置、209台弹簧振打除灰装置组成。
第一节、澳炉余热锅炉1、概述奥炉余热锅炉为强制循环系统,由循环泵提供动力。
整个炉体由辐射炉膛(上升烟道、下降烟道、水平烟道)和四组对流管束组成。
在上升烟道的入口处和下降烟道的出口处设有三维膨胀节,使其既能满足炉体的密封,又能独立于炉体其它结构之外,使得上升烟道和下降烟道能悬吊于厂房顶部横梁上,实现向下自由膨胀。
而水平烟道在内柱上设有滑动支撑机构,可以实现向后膨胀位移。
2、烟气条件和锅炉参数1)、澳炉余热锅炉入口烟气条件:2)、澳炉余热锅炉参数:额定蒸发量:43.7t/h 工作压力:5.5MPa饱和蒸汽温度:271℃给水温度:104℃4)、汽包内径1800mm圆筒长度8000mm壁厚60mm总容水量21.83m33、4、锅炉结构简介Ausmelt熔炼余热锅炉包括上升烟道、下降烟道、水平烟道、对流室、凝渣管束、对流管束、集箱、锅炉循环管道、钢架等部件。
过路的上升烟道、下降烟道、水平烟道、对流室为完全密封的膜式壁结构。
Ausmelt熔炼炉高温烟气经熔炼炉炉顶烟罩出口后先后流过上升烟道、下降烟道、水平烟道、再流经凝渣管、对流管I、对流管II、及对流管III至锅炉出口。
锅炉同时起到部分除尘、降温的作用。
为了确保锅炉各烟道少结灰、结渣并使灰渣容易清除,根据烟道不同的温度设计了不同的膜式壁节距,使膜式壁的整体壁温保持在合理的水平上。
因烟气中烟尘的熔点较低,为了不使烟尘在对流受热面中严重结灰,对流受热面入口烟温控制在670℃以下,并通过凝渣管束冷却使烟温进一步降低,以确保对流受热面的安全运行。
整台锅炉不设省煤器,过热器,全部为蒸发免收热。
金川铜合成炉系统配置及装备
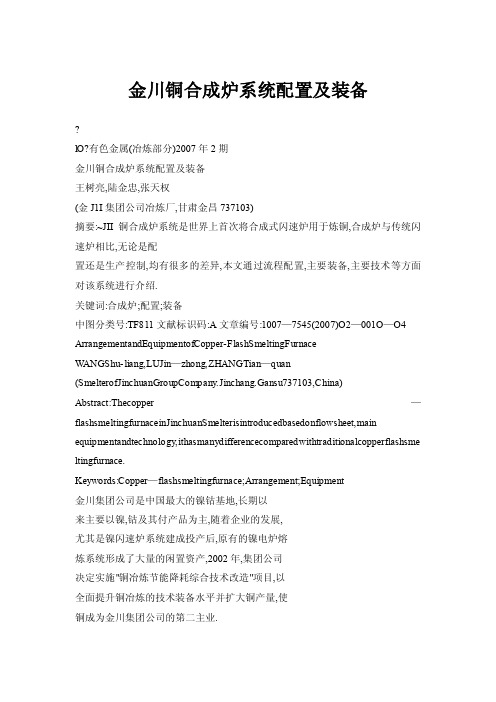
金川铜合成炉系统配置及装备lO?有色金属(冶炼部分)2007年2期金川铜合成炉系统配置及装备王树亮,陆金忠,张天权(金J1I集团公司冶炼厂,甘肃金昌737103)摘要:~JII铜合成炉系统是世界上首次将合成式闪速炉用于炼铜,合成炉与传统闪速炉相比,无论是配置还是生产控制,均有很多的差异,本文通过流程配置,主要装备,主要技术等方面对该系统进行介绍.关键词:合成炉;配置;装备中图分类号:TF811文献标识码:A文章编号:1007—7545(2007)O2—001O—O4 ArrangementandEquipmentofCopper-FlashSmeltingFurnaceW ANGShu-liang,LUJin—zhong,ZHANGTian—quan (SmelterofJinchuanGroupCompany.Jinchang.Gansu737103,China)Abstract:Thecopper—flashsmeltingfurnaceinJinchuanSmelterisintroducedbasedonflowsheet,main equipmentandtechnology,ithasmanydifferencecomparedwithtraditionalcopperflashsme ltingfurnace.Keywords:Copper—flashsmeltingfurnace;Arrangement;Equipment金川集团公司是中国最大的镍钴基地,长期以来主要以镍,钴及其付产品为主,随着企业的发展,尤其是镍闪速炉系统建成投产后,原有的镍电炉熔炼系统形成了大量的闲置资产,2002年,集团公司决定实施"铜冶炼节能降耗综合技术改造"项目,以全面提升铜冶炼的技术装备水平并扩大铜产量,使铜成为金川集团公司的第二主业.经过可行性研究,我们认为,采用合成炉炼铜能够充分借鉴金川在镍冶炼方面积累的丰富经验和技术成果,适合金川自身的发展,因而确定了合成炉炼铜的技术思路,并与中国有色工程设计研究总院联合展开设计,设计年处理铜精矿8O万吨.项目于2002年4~l1月完成了技术论证,2003年3月开始进行施工图设计,2004年元月21日主体工程开工, 2005年8月8日点火烘炉,9月12日投料生产,从项目提出到建成投产用了42个月的时间.1工艺流程金川铜合成炉系统采用了精矿蒸汽干燥一铜合作者简介:王树亮(1968一),男,云南玉溪人,高级工程师成炉熔炼-PS转炉吹炼一回转阳极炉精炼,转炉渣电炉贫化的主工艺流程,其中PS转炉,回转阳极炉,转炉渣贫化电炉均部分采用了现有闲置设备,具体工艺流程见图1.2主流程工艺配置及主要装备2.1精矿的仓储系统为了适应多矿种的配料要求,金川合成炉精矿仓拥有35万吨的总储存容量,可以实现湿精矿的三级配料:储仓中配备的抓斗吊车可以实现相近矿种的堆式配料;从大储仓到中间仓配备的四台定量给料机可以实现主要矿种的配料;从中间仓到干燥系统配备了八台定量给料机可以实现进入干燥系统物料的精细配料,能够比较好的保证供给合成炉精矿成份的稳定性.2.2精矿干燥配料后的混合湿精矿通过定量给料机送人蒸汽干燥机,产出的干精矿经三台10m.仓式泵正压输送到合成炉顶干精矿储仓,干燥尾气经过布袋收尘有色金属(冶炼部分)2007年2期?11?塑监图1铜合成炉熔炼系统工艺流程图Fig.1TheflowsheetofCopper-flashsmeltingfurnace器捕集后排空,粉尘返回干燥机进料端.表1.干燥系统的主要装备密闭型蒸汽干燥机由金川集团公司和兰州天华化工机械及自动化研究院联合开发,是完全国产化的一台大型设备,主要的设计参数:蒸汽干燥机生成能力135t/h(干基),干燥前精矿含水8~1O9,6,干燥后精矿含水≤0.39,6,饱和蒸汽压力2.0MPa,饱和蒸汽温度214℃,干燥机出口尾气温度9O℃,布袋除尘器收尘效率99.9.2.3熔剂粉和煤粉制备合成炉系统熔剂和煤粉制备,采用了引进水泥行业的立式磨制粉工艺,该工艺集烘干,粉磨,分级, 分离为一体,具有流程简单,磨耗低,产品粒级容易控制等优点,近年来在水泥行业已经得到了广泛的运用,在有色行业还没有看到相关报道,尤其用于石英石的粉磨,金川I还是第一家.合格产品均通过仓式泵正压输送到合成炉炉顶仓备用.熔剂和煤粉制备主要设备是HRM型立式磨,主要的设计参数见表1HRM立式磨的主要技术参数Table.1ThemainparametersofHRMverticalmill2.4合成炉反应塔配加料金川铜合成炉采用炉顶配料,干精矿,熔剂粉,返回烟尘,粉煤均储存于炉顶仓,通过FUNKEN秤准确计量配料,可以根据炉况随时调整配料比.混合物料通过两台配料刮板和两台加料刮板连续加入反应塔.12?有色金属(冶炼部分)2007年2期2.5铜合成炉铜合成炉由反应塔,沉淀池,贫化区和上升烟道四部分组成,骨架采用"弹性捆绑式"结构,炉体冷却采用立体强制水冷技术.炉型与金川镍闪速炉基本相同,但在具体结构上进行了大量的改进,主要有: 反应塔采用四喷嘴平顶吊挂结构,反应塔和上升烟道与沉淀池连接部采用"E"型水套结构,沉淀池拱顶采用水冷止推吊挂结构,上升烟道采用平顶浇铸直墙结构,反应塔下沉淀池侧墙采用三平两立水冷结构等.合成炉主要结构性能:铜精矿处理量2400t/d,反应塔规格6m×7m,精矿喷嘴数4个,反应塔设计鼓风量32857rn./h,含氧6O,反应塔鼓风温度为常温~200℃,沉淀池熔池深度~1.3 rn,沉淀池渣线宽度7.05rn,沉淀池渣线长度~32.5rn,炉床面积229rn.,循环水量2600t/h.2.6余热锅炉和收尘铜合成炉余热锅炉由Oschatz公司设计,国内制造.铜合成炉余热锅炉主要技术性能:设计烟气量46135rn./h(标态),设计人炉温度1250℃,烟气含尘ll5.13g/m.(标态),蒸发量29.6~47.5t/h,运行压力4.5MPa,给水温度104℃,蒸汽温度266℃,出口烟温(350±50)℃.铜合成炉电收尘器技术性能:电场有效截面积5O×2rn.,电场数4个,阳极为"C"-480型极板,阴极为框架式改进型不锈钢RS芒刺线,每个电场通道数16个,烟气在电场内流速0.47m/s,总集尘面积3494rn.,出口烟气含尘量<0.4g/m.(标态).2.7火法精炼系统冰铜吹炼新配备了3台4rn×l1.7rnPS转炉与原有的4台3.66rn×11.1mPS转炉共同形成铜,镍吹炼系统,配备了4台高压风机,采用集中供风模式.铜系统主要以3台4rn×l1.7m转炉为主,采用三热两开炉交叉期交换似.15mX12.1rn 方式组织生产.阳极精炼新配备了2台350t回转阳极炉,与现有的2台130t炉共同组成铜阳极板生成系统. 新建阳极炉采用了透气砖,顶部排烟,余热回收,固体还原剂等技术组合,配备了奥托昆普双16模定量浇铸系统,正常以新阳极炉系统为主组织生产.2.8转炉渣贫化电炉转炉渣贫化电炉是利用原镍贫化电炉改建,炉型为长方形,直径900mm的电极呈直线排列,升降采用卷扬机形式,炉体钢骨架为弹性捆绑式结构,炉墙采用强制循环水冷技术,以干铜精矿作为硫化剂, 冰铜进入转炉,炉渣废弃.贫化电炉主要设备构成: 功率5000kV A,电极根数3根,炉膛渣面宽度5.77 rn,炉膛渣面长度l1.4rn,炉膛高度2.9rn,熔池深度1.8rn.2.9烟气制酸铜合成炉系统配套了53万t/a硫酸系统,处理烟气能力18~2O万rn./h,采用双转双吸工艺.新建系统投产后,金川烟气制酸已经形成了3大系统5O万rn./h的烟气处理能力,由于金川冶炼厂拥有庞大的铜,镍生产系统,冶炼烟气情况复杂,为了满足生产和环保的要求,金川烟气系统采用了3套系统分别对应一期铜镍转炉,二期镍闪速炉和合成炉, 但又能够互相调配气的网络化烟气供应系统,成功解决了高低浓度烟气配气制酸问题,极大减少了低浓烟气排放,取得了较好的效果.3金川合成炉系统主要的技术创新点3.1合成炉炼铜技术及装备铜合成炉是世界上首座应用于铜冶炼的"合成式闪速炉",在镍闪速炉的基础上,对炉体结构,精矿喷嘴的结构等方面均进行了研究和改进,主要特点如下: (1)合成炉炉型采用带贫化区的熔炼炉,将熔炼炉和贫化电炉合二为一;骨架采用"弹性捆绑式"结构,炉体冷却采用立体水冷技术等.(2)反应塔的改进设计主要包括反应塔顶采用吊挂平顶结构;塔身冷却水套共设12层冷却平水套,间距减小为390mm;反应塔最下端采用吊挂的齿形冷却水套,便于配水和实现平时检修更换等. (3)沉淀池的改进设计主要包括沉淀池的炉顶采用分段吊挂的止推炉顶,每段拱顶之间设吊挂铜水套;炉体骨架采用整体弹性骨架,底梁采用双层网状结构,只承受炉体及熔体的重量,不再起底拉杆的作用等等.(4)上升烟道的改进设计包括上升烟道后墙由斜墙改为垂直吊挂的直墙,并加设冷却水套;迎火面墙增加了冷却水套;上升烟道炉顶采用H形水冷梁支撑的整体浇注炉顶等等.(5)贫化区的改进设计主要包括贫化区装设两组电极;电极的布置适应铜冶炼炉渣的特性,电极铜瓦由铜管改为软铜带;铜瓦调整由楔紧方式改为弹簧调整调节等等.3.2铜合成炉精矿喷嘴铜合成炉采用金川公司研发的精矿喷嘴,在塔顶布置4个同时工作的精矿喷嘴,为了提高反应塔有色金属(冶炼部分)2007年2期?13?内燃烧物的温度,加快熔化速度,减少烧油量,精矿喷嘴采用含氧6O的富氧风.其主要特点如下:(1)风箱的鼓风方式为双口顶进风;(2)喷出口角度设计可增强对大料量的适应性;(3)喷嘴同心度设计合理,不需要调节;(4)密封结构和调节结构便于生产操作,维护及检修.(5)喷嘴的材质采用公司自主开发的铸钢材料.3.3精矿蒸汽干燥技术及装备在铜合成炉系统中,精矿的深度干燥采用了公司与兰州天华化工机械及自动化研究院联合研制的密闭型蒸汽管式干燥机.3.4熔剂立式磨制粉新工艺合成炉熔剂及煤粉制备系统采用了先进的立式磨制粉工艺,与镍闪速炉用的球磨机工艺相比,具有生产能力大,自动化程度高,噪音小,磨耗低节能环保的优点.3.5新型阳极炉结构回转式阳极炉用于转炉产出的热态粗铜的精炼,为铜电解精炼提供合格的阳极板.其在设计过程中采用了先进的炉体结构:(1)阳极炉的端部采用球形封头,炉口采用液压启闭装置,密封效果好,炉口处设有环保烟罩,可将炉子冒出的黑烟排走,减少烟气污染.(2)阳极炉的排烟口设在炉尾部的上方,烟从上方排出,排烟口处设计有环绕排烟口护板的水套式排烟罩,排烟罩的出烟口直接与空气换热器相接,烟气经排烟罩冷却降温后进入空气换热器.空气换热器采用列管式旋流结构,结构简单,换热系数高,空气阻力,烟气阻力都较小,列管无下联箱,减少了烟尘粘结,清灰方便.利用热烟气将阳极炉燃油的助燃风预热到3O0℃,热风助燃可提高燃烧温度,炉况稳定,可直接降低油耗~15.(3)引进了透气砖技术,即在炉子底部设置了8套透气砖,通过透气砖鼓入氮气,使熔体始终处于均匀的搅动状态,熔体温度,成分均匀,有效提高传热和传质效率,进而达到提高生产能力和降低能耗.(4)该阳极炉采用煤粉制剂作为还原剂,其优点是还原剂利用率较高,消除了还原期的黑烟,有利于环保.4投产后出现的主要问题及解决措施合成炉系统投产一年以来,已经生产了近2O万t阳极板,系统运行总体状况良好,碰到的问题已经基本解决,主要如下:4.1锅炉及收尘粘结的问题合成炉投产初期,我们碰到了比较严重的排烟系统粘接的问题,造成锅炉堵塞,生产中断.经过分析研究,主要原因是反应塔控制不理想,精矿反应不充分,使排烟系统工艺条件得不到保证,烟尘几乎不盐化.通过反应塔控制技术调试和在沉淀池鼓风补氧使这一问题得到了有效解决.生产实践证明,只要反应塔工况理想,合成炉甚至不需要额外的措施, 也能得到良好的烟尘性质,但在沉淀池或锅炉入口适当补充盐化风,仍然是不错的保安手段.4.1锅炉及收尘粘结的问题合成炉余热锅炉设计蒸发量为29.642t,通过增加预留管屏可扩能到47.5t,合成炉在设计能力运行时,锅炉的蒸发量已经达到了45~47t,致使锅炉出口烟气温度偏高,对收尘系统的工作带来了较大的影响.在2006年1O月进行的年度检修中, 我们安装了预留管屏,使问题得到了解决.4.3干精矿的流态化问题合成炉干精矿采用正压输送到炉顶干矿仓,经设于料仓底部的FUNKEN秤配料后入炉.投产后碰到了比较严重的流态化问题,尤其是在正压输送时,流态化现象更加突出,致使计量失真,炉况波动大.通过FUNKEN秤的适应性改造以及年修对正压输送入仓口的改造,已经基本解决了问题.4.4蒸汽干燥机的生产能力问题蒸汽干燥系统投产后,存在的最主要的问题就是冷凝水不能有效的从干燥机中排出,致使干燥机主电机的负荷升高,生产能力下降,对合成炉系统的生产造成了较大的影响.经过金川与天华院联合技术攻关,对影响冷凝水排出的两个限制环节进行了改造,从复产后的情况来看,生产负荷正逐步提高, 问题已经基本得到解决.5结语通过金川铜合成炉系统一年来的生产实践,我们认为:(1)合成炉用于炼铜技术上是可行,可靠的;(2)合成炉取消了炉渣贫化电炉缩短了流程,使系统的操作和运行维护更加简单环保;(3)合成炉贫化区的存在使工艺控制多了一种调节手段;(4)合成炉中炉渣流动平缓,沉淀时间充分,能够得到比较理想的渣指标;(5)由于首次将合成炉用于炼铜,系统生产工艺研究和系统的优化配置研究任重道远,需要业内同行共同商榷.。
Ф3.6m×10m回转阳极炉出烟口水冷烟罩设计
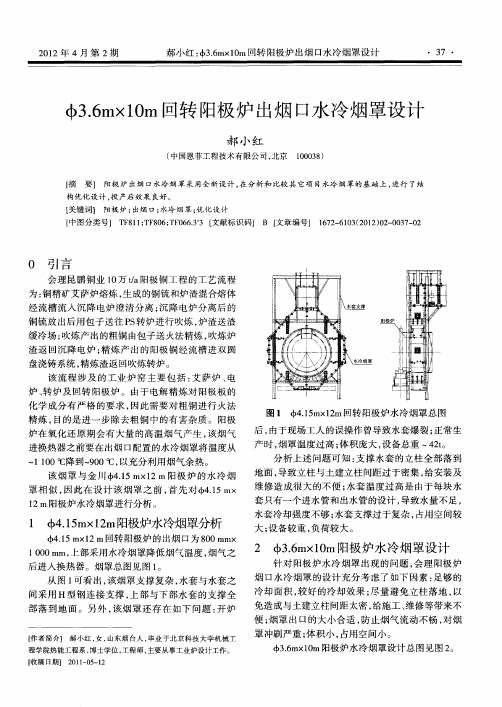
郝小 红 : . lm回转 阳极炉 出烟 口水 冷烟 罩设计 36 O mx
・3 ・ 7
3
( 国恩菲工程技术有限公司 , 京 中 北 10 3 ) 0 0 8
【 摘
要 ] 阳极 炉 出烟 口水 冷 烟 罩 采 用全 新 设 计 , 分 析 和 比较 其 它 项 目水 冷 烟 罩 的基 础 上 , 行 了结 在 进
色 冶 金
A 卷生产实践篇 ・ 设备及 自动化
图 3 下 部骨架 图
图 2 3 mx O . lm阳极 炉水 冷 烟罩设 计总 图 6 从 图 2 以看 出 , 可 该烟 罩 分为 上下 两部 分 , 每块 水套 之 间 留有 5mm的缝 隙 , 水套 之 间采用 连接 耳 各 连 接 , 块水 套水管 均采 用两 进两 出 , 每 大大提 高 了冷
上 部 烟 罩 共 7 水 套 , 部 水 套 顶部 及 左 侧 各 块 上 为 一块水 套 , 前水套 及 后水套 各 为两块 , 底部 斜 水套
旷 . ]
渣返 回沉 降 电炉 ; 炼 产 出 的 阳极铜 经 流槽 进 双 圆 精 盘浇 铸系 统 , 炼渣 返 回吹炼转 炉 。 精
该 流 程 涉 及 的工 业 炉 窑 主 要 包 括 : 萨 炉 、 艾 电 炉 、 炉及 回转 阳极 炉 。由于 电解 精 炼 对 阳极 板 的 转 化学 成 分 有严 格 的要 求 , 因此 需要 对 粗 铜 进行 火 法 精炼 , 目的是 进 一步 除 去粗 铜 中的有 害 杂 质 。 阳极 炉在 氧 化还 原 期 会有 大 量 的高 温 烟气 产 生 , 烟 气 该 进换 热器 之前 要在 出烟 口配置 的水 冷烟 罩将 温度 从
落到 地 面 , 大增加 了安 装 与维护 空 间 。 大 水 冷 烟罩 与 烟 口护 板 之 间装 有 柔性 密 封 板 , 防 止 烟 气 溢 出 。下部 设 有 接 灰 斗 , 图 4 见 。该 水 冷烟
水冷烟罩总装配体
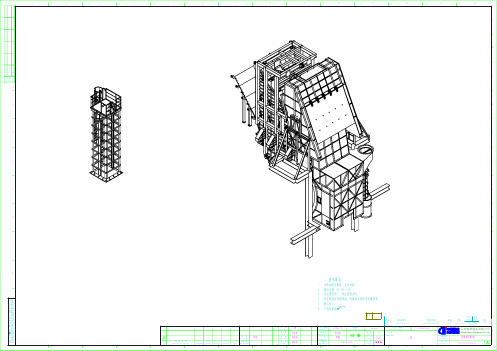
2
3
4
5
6
7
8
Hale Waihona Puke 91011
12
13
14
A
B
签 名 SIGNA.
专 业 SPECI.
日 期 DATE
C
会签栏
JOINT APPROVAL
D
D
E
E
F
F
G
G
H
H
J
J
K
K
技术要求:
1. 2. 3. 4. 5. 6. 本件共制作两件,互为对称; 调质处理,HB 225-255; 未注倒角为C1,未注圆角为R1; 所有焊缝为连续焊接,焊缝高为相焊件中薄件厚; 焊后加工; Ra 25 。 下料切割边
M
A1
1:100
图 名:
DWG TITLE:
审 修 改 说 明
REVISION DESCRIPTION
定
APPROVED
陈浩
8
设 制
专 业
SPECIALTY
DESIGNED DRAWN
A1
12
设备名称
EQUIPMENT
阴极剥片机组
──────
A
序号
No.
设 计
DESIGNED
校 核
CHECKED
审
核
WEIGHT
99084.71
材料牌号
MATERIAL SIZE
───
设计许可证编号
DESIGN LICENCE No.
A136000336
江西瑞林装备有限公司
Jiangxi Nerin Equipment Co.,Ltd.
设计阶段
燃煤采暖锅炉房烟气除尘系统设计说明书

大气污染控制工程课程设计任务书题目:某燃煤采暖锅炉房烟气除尘系统设计学院部:专业班级:学生姓名:指导教师:2012年月日大气污染控制工程课程设计任务书颗粒物污染控制一、 题目某燃煤采暖锅炉房烟气除尘系统设计 二、 目的通过课程设计进一步消化和巩固本课程所学内容,并使所学的知识系统化,培养运用所学理论知识进行净化系统设计的初步能力;通过设计,了解工程设计的内容、方法及步骤,培养学生确定大气污染控制系统的设计方案、进行设计计算、绘制工程图、使用技术资料、编写设计说明书的能力; 三、 设计原始资料锅炉型号:SZL4-13型,共4台×4 排烟温度:160 ℃烟气密度标准状态下:1.34kg/m 3 空气过剩系数:α=排烟中飞灰占煤中不可燃成份的比例:16% 烟气在锅炉出口前阻力:800Pa 当地大气压力:冬季室外空气温度:-1℃空气含水标准状态下:按0.01293kg/m 3烟气其他性质按空气计算 煤的工业分析值: 设计耗煤量:500kg/h 台C ar =% H ar =% S ar =% O ar =5% N ar =% W ar =% A ar =% V ar =%按锅炉大气污染物标准GB13271-2001中二类区标准执行; 烟尘浓度排放标准标准状态下:200mg/m 3 二氧化硫排放标准标准状态下:900mg/m 3净化系统布置场地如图1所示的锅炉房北侧15m 以内;四、设计内容和要求1、燃煤锅炉排烟量及烟尘和二氧化硫浓度的计算;2、净化系统设计方案的分析确定;3、除尘器的比较和选择:确定除尘器类型、型号及规格,并确定其主要运行参数;4、管网布置及计算:确定各装置的位置及管道布置,并计算各管段的管径、长度、烟囱高度和出口内径以及系统总阻力;5、风机及电机的选择设计:根据净化系统所处理烟气量、烟气温度、系统总阻力等计算选择风机种类、型号机电动机的种类、型号和功率;编写设计说明书:设计说明书按设计程序编写,包括方案的确定、设计计算、设备选择和有关设计的简图等内容;课程设计说明书应有封面、目录、前言、正文、小结及参考文献等部分,文字应简明、顺畅、内容正确完整,书写工整、装订成册;6、图纸要求(1)除尘系统图一张2号图;系统图应标出设备、管件编号,并附明细表; (2)除尘系统平面、剖面布置图各1张2号或3号图,如图1和图2;布置图应按比例绘制,图中设备、管件应标注编号,编号应与系统图对应;在平面布置图中应有方位标志指北针;图1 锅炉房平面布置图图2 A-A剖面图五、主要参考书目1童志权主编. 大气污染控制工程. 北京:机械工业出版社,20062同济大学等编. 锅炉及锅炉房设备. 北京:中国建筑工业出版社,19863航天部第七设计院编. 工业锅炉房设计手册. 北京:中国建筑工业出版社,19864陆耀庆主编. 供暖通风设计手册. 北京:中国建筑工业出版社,19875风机样本. 各类风机生产厂家6工业锅炉旋风除尘器指南,1984课程设计成绩评定表目录…………………………………………………………….9前言按照国际标准化组织ISO作出的定义,“空气污染:通常系指由于人类活动和自然过程引起某些物质介入大气中,呈现出足够的浓度,达到了足够的时间,并因此而危害了人体的舒适、健康和福利或危害了环境;”大气污染物的种类非常多,根据其存在状态,可将其概括为两大类:气镕胶状态污染物和气体状态污染物;随着工业的发展,能源的消耗量逐步上升,大气的污染物的排放量相应增加;就现在我国的经济和技术发展水平级能源的结构来看,一煤炭为主要能源的状况在人的生存每时每刻都离不开空气,大气质量与人类生存环境息息相关,所以对大气的修复比较困难;虽然人们在大气环境整治方面坐了大量的工作,但目前的空气质量仍然不尽人意,因此防止污染、改善空气环境成为当今迫切的环境任务;燃煤锅炉排放的二氧化硫严重地污染了我们赖以生存的环境;我国的大气是以煤烟型污染为主,其中尘与酸雨危害最大;因此,净化燃煤烟气中的粉尘和二氧化硫是我过改善大气空气质量、减少酸雨的关键问题;粉尘的危害:粉尘的危害,不仅取决于它的暴露浓度,还在很大程度上取决于它的组成成分、,理化性质、粒径和生物活性等;粉尘的成分和理化性质是对人体危害的主要因素;有毒的金属粉尘和非金属粉尘铬、锰、镐、铅、汞、砷等进入人体后,会引起中毒以至死亡;无毒性粉尘对人体亦有危害;例如含有游离二氧化硅的粉尘吸,入人体后,在肺内沉积,能引起纤维性病变,使肺组织际渐硬化,严重损害呼吸功能,发生“矽肺”病;二氧化硫的危害:二氧化硫为一种无色的中等强度刺激性气体;在低浓皮下,二氧化硫主要影响是造成呼吸道管腔缩小,最初呼吸加快,每次呼吸曼减少;浓度较高时,喉头感觉异常,并出现咳嗽、喷嚏、咯痰、声哑、胸痛、呼吸困难、呼吸道红肿等症状,造成支气管炎、哮喘病,严重的可以引起肺气肿,甚至致人于死亡;大气控制的综合措施主要包括:严格的环境管理;以环境规划为中心,实行综合防治;制大气污染的技术政策;控制环境污染的经济政策;高烟囱扩散;绿化造林;安装废气净化装置;加强环境科学研究,检测和教育;第1章烟气量、烟尘和二氧化硫浓度的计算煤燃烧的假设:1煤中固定氧可用于燃烧; 2煤中硫主要被氧化成二氧化硫; 3不考虑氮氧化物的生产; 4煤中的氮在燃烧时转化为氮气;标准状态下理论空气量=kg m /3标准状态下理论烟气量=kg m /3标准状态下实际烟气量由设计原始资料可知,设计耗煤量为500 kg/h 台 所以,标准状态下的排烟量为设计耗煤量⨯=f V Q 即7.436650073.8Q =⨯=(台)h /m 3标准状态下烟气含尘浓度式中 sh d —排灰中飞灰占煤中不可燃成分的质量分数; ar A —煤中不可燃成分的含量; f V —标准状态下实际烟气量,kg m /3;标准状态下烟气中二氧化硫浓度的计算第2章 除尘器的选择除尘效率式中 C —标准状态下烟气含尘浓度,3/m mg ;S C —标准状态下锅炉烟尘排放标准中规定值,3/m mg ;除尘器的选择工况下烟气量 TT Q Q '=')/(3h m 式中 Q —标准状态下的烟气流量,h m /3;T '—工况下烟气温度,K ; T —标准状态下温度,273K;根据η、Q 查手册后选用XP-800型旁路式旋风除尘器,;该除尘器主要适用于清除非粘固灰尘、煤炭、泥沙、烟尘及其它粉尘等;其性能和尺寸分别见表2-1、2-2;表 2-1 XP-800旁路式除尘器性能表2-2 XP-800旁路式旋风除尘器的尺寸图3-1 XP 型旁路式旋风除尘器第3章 确定除尘器、风机和烟囱的位置及管道的布置各装置及管道布置的原则根据锅炉运行情况和锅炉房现场实际情况确定各装置的位置;一旦确定了各装置的位置,管道的布置也就基本可以确定了;对各装置及管道的布置应力求简单,紧凑,管路短,占地面积小,并使安装、操作和检修方便;管径的确定式中 Q —工况下管道内的烟气流量,s m /3;v —烟气流速,m/s 对于锅炉烟尘v =10-15 m/s;取v =12 m/s,d 12924.14⨯⨯=π=圆取整d=450mm查管径手册相关参数,取标准d=450 mm,管道参数见下表3-1表 3-1 管道参数内径=1d =450-2×= mm 由公式vQd π4=可计算出实际烟气流速 式中 Q ——工况下管内烟气流量,m 3/s ;v ——烟气流速,m/s 可查有关手册确定,对于锅炉烟尘v=10~15 m/s;管径计算出来后,要进行圆整查手册,再用圆整后的管径计算出实际烟气流速;实际烟气流速要符合要求;烟道的设计计算烟道采用拱形,图形如下图3-2所示:由系统图可以看出,烟道流过的最大烟气量是锅炉烟气量的2倍,再加上烟气系统的漏风率,则烟道内最大烟气流量为:查表可知,砖制烟道的最适合烟速是6-8 m/s,初定烟速为7 m/s,则烟道面积为 15237.068/0.60536007A Q V ===⨯烟烟而 22()0.60522BA B π=+=则 B=659 mm 圆整取 B= 650mm 则 A=2m 校正气速 15237.0687.19836000.588v ==⨯s m /,在范围内;第4章 烟囱的设计烟囱高度的确定首先确定共用一个烟囱的所有锅炉的总的蒸发量 t/h,然后根据锅炉大气污染物排放标准中的规定表4-1,确定烟囱的高度;表4-1 锅炉烟囱的高度锅炉总额出力:4×4=16 t/h 故选定烟囱的高度为40m;烟囱直径的计算烟囱出口内径可按下式计算:式中 Q —通过烟囱的总烟气量,h m /3;ω—按表4-2选取的烟囱出口烟气流速,m/s;表4-2烟囱出口烟气流速/m/s选定ω=4 m/s则20.0188 1.64d ==m圆整取2 1.6d =m 烟囱底部直径式中 2d —烟囱出口直径,m ; H —烟囱高度,m ;i —烟囱锥度通常取i =~;取i =,则1d = + 2××40= m烟囱的抽力B t t H S pk y ⋅+-+=)27312731(0342.0 Pa3110.034240()97.8610183.002731273160=⨯⨯-⋅⨯=-+ Pa式中 H —烟囱高度,m ;k t —外界空气温度,℃; p t —烟囱内烟气平均温度,℃;B —当地大气压,Pa;第5章 系统阻力的计算摩擦压力损失对于圆管22v d L P L ρλ⋅=∆ Pa式中 L —管道长度,m ;d —管道直径,m ;ρ—烟气密度,3/m kg ;v —管中气流平均速率,m/s ;λ—摩擦阻力系数,式气体雷诺数Re 和管道相对粗糙度dK的函数;可以查手册得到实际对金属管道λ可取,对砖砌或混凝土管道λ可取; a .对于φ450圆管L=b .对于砖砌拱形烟道式中,L 为四个锅炉出口最远距离的一半,为 m ; λ为;S R 为截面积与润湿周边的比,即周边又04.0=λ,7.198v =,代入上式:得 20.040.847.1989.910.8840.1982L p ⨯∆=⨯⋅=⨯ Pa 局部阻力损失式中 ζ—异形管件的局部阻力系数,可在相关手册中查到,或通过实验获得;v —与ζ相对应的断面平均气流速率,m/s ; ρ—烟气密度,3/m kg ; 两个渐缩管,查表,取α=45°,则ζ= 四个90°弯头,查表,取ζ=四个弯头,则414.3457.37P ∆=⨯=)(Pa 一个渐扩管,2210.40.5651.430.44853.144F F ⨯==⨯查表,取α=30°,得ζ= e 为渐缩管,查表,取α=45°,则ζ= 烟道中的T 形三通如图5-1所示:图5-1 T 形三通管查表,得ζ=烟道的T 形三通合流管如图5-2所示:5-2 T 形合流三通查表,得ζ=总的阻力损失其中锅炉出口前阻力为800 Pa,除尘器阻力为800 Pa则11.6010.8812.4757.37 4.37 6.2448.6434.30800800P ∆=+++++++++∑图5-3 除尘器入口管道示意图 图5-4 除尘器出口至风机入口段管道示意图第6章 系统中烟气温度的变化烟气在管道中的温度降VC Q Fq t ⋅⋅=∆1℃ 式中 Q —标准状态下烟气流量,h m /3; F —管道散热面积,2m ;V C —标准状态下烟气平均比热容一般为~⋅3/m kJ ℃; q —管道单位面积散热损失,)/(3h m kJ ⋅;室内 1q =4187)/(3h m kJ ⋅; 室外 2q =5433)/(3h m kJ ⋅; 室内管道长: 室外管道长: 则112214187 2.09543315.57=16.121.3264366.7 1.326q F q F t Q +⨯+⨯∆==⋅⨯℃烟气在烟囱中的温度降DA H t ⋅=∆2℃式中 H —烟囱高度,mD —合用同一烟囱的所有锅炉额定蒸发量之和,t/h A —温降系数,可由表5-1查得;表5-1 烟囱温降系数4164.0402=⨯=∆t ℃总温度降:1216.12420.12t t t ∆=∆+∆=+=℃第7章 风机和电动机选择及计算标准状态下风机风量的计算式中 —风量备用系数;Q —标准状态下风机前风量,h m /3;p t —风机前烟气温度,℃,若管道不长,可以近似取锅炉排烟温度; B —当地大气压力,kPa;风机风压的计算式中 —风压备用系数;∑∆h —系统总阻力,Pa ;y S —烟囱抽力,Pa ;y ρ—标准状态下烟气密度,γ =3/m kg ;电动机功率的计算式中 y Q —风机风量,h m /3;y H —风机风压,Pa ;1η—风机在全压头时的效率一般风机为;2η—机械传动效率,用V 形带传动时2η=; β—电动机备用系数,对引风机,β=;风机和电机的选择根据风量y Q =h m /3,y H =Pa ,查表后选择型引风机,配对电机型号为Y132S2-2B3,具体参数如下表所示:表7-1 所选风机及型号参数第八章小结通过这次的课程设计,我理论实践能力得到了很大的提高,我受益良多;这次的课程设计得以完成当然,我首先得感谢王老师,能为我们选择合适的设计题目,让我们在掌握所学的知识的基础上能比较轻松的完成任务又能达到巩固学习知识的目的,同时在课程设计上给我的指导,以及给我提供了这么多有用的资料,使设计能顺利进行;其次,我要感想我们小组的成员们,在我们的思考与讨论下,我们才得以知道该怎么去做,该怎么去选才能是我们设计的东西更好;通过这次的课程设计,我再一次巩固了我所学在课堂上学的大气污染控制工程课程的理论知识,并对它们的应用有了进一步的了解;同时,应为我选择了用打印的设计说明书,从而使自己的文字编排能有了一定的提高;我在书写的同时尝试用CAD去绘画其中图片,因为我们还没有学习这门课,所以是慢慢摸索,从不懂到略微懂,虽然我花了不少时间在上面,但从图片的效果来看,还是很不错的,做完之后真的很有成就感;在这次的课程设计过程中,我认识到了自己专业知识的不足,做事态度和能力的欠缺等诸多缺点,我以后一定会加倍努力,勤奋学习;总之这次的课程设计让我受益良多;最后,我要再一次感谢所有在课程设计中帮助过我的老师和同学们;第九章参考文献1 童志权主编. 大气污染控制工程. 北京:机械工业出版社,20062 同济大学等编. 锅炉及锅炉房设备. 北京:中国建筑工业出版社,19863 鹿政理等编环保设备设计手册--2大气污染控制设备. 北京:化学工业出版社,4 刘天齐,黄小林,邢连壁,耿其博. 三废处理工业手册废气卷. 北京:化学工业出版社,1998.5 动力手册编写组. 工业锅炉房设备手册;北京:国防工业出版社,1975.6 风机样本. 各类风机生产厂家7 工业锅炉旋风除尘器指南,1984。
诺兰达炉的消化试制和密封烟罩的开发
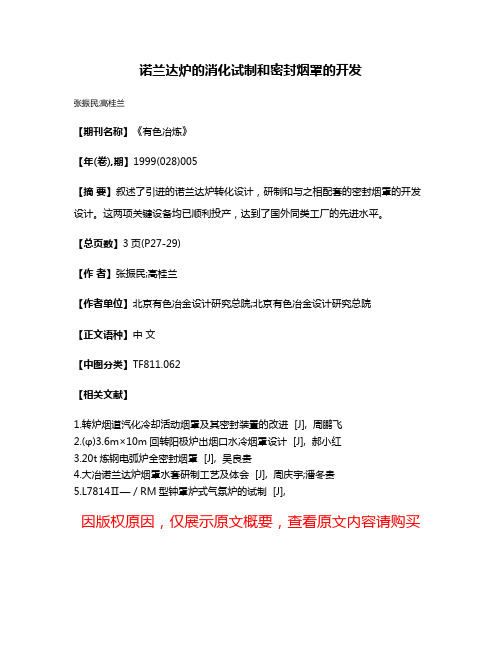
诺兰达炉的消化试制和密封烟罩的开发
张振民;高桂兰
【期刊名称】《有色冶炼》
【年(卷),期】1999(028)005
【摘要】叙述了引进的诺兰达炉转化设计,研制和与之相配套的密封烟罩的开发设计。
这两项关键设备均已顺利投产,达到了国外同类工厂的先进水平。
【总页数】3页(P27-29)
【作者】张振民;高桂兰
【作者单位】北京有色冶金设计研究总院;北京有色冶金设计研究总院
【正文语种】中文
【中图分类】TF811.062
【相关文献】
1.转炉烟道汽化冷却活动烟罩及其密封装置的改进 [J], 周鹏飞
2.(φ)
3.6m×10m回转阳极炉出烟口水冷烟罩设计 [J], 郝小红
3.20t炼钢电弧炉全密封烟罩 [J], 吴良贵
4.大冶诺兰达炉烟罩水套研制工艺及体会 [J], 周庆宇;潘冬贵
5.L7814Ⅱ—/RM型钟罩炉式气氛炉的试制 [J],
因版权原因,仅展示原文概要,查看原文内容请购买。
- 1、下载文档前请自行甄别文档内容的完整性,平台不提供额外的编辑、内容补充、找答案等附加服务。
- 2、"仅部分预览"的文档,不可在线预览部分如存在完整性等问题,可反馈申请退款(可完整预览的文档不适用该条件!)。
- 3、如文档侵犯您的权益,请联系客服反馈,我们会尽快为您处理(人工客服工作时间:9:00-18:30)。
1
击4.15mxl2m阳极炉水冷烟罩分析
4,4.15
mxl2
m回转阳极炉的出烟口为800mm×
l 000
mm,上部采用水冷烟罩降低烟气温度,烟气之
2由3.6mxlOm阳极炉水冷烟罩设计
针对阳极炉水冷烟罩出现的问题,会理阳极炉
后进入换热器。烟罩总图见图l。
f作者简介1郝小红,女.山东烟台人,毕业于北京科技大学机饭工 程学院热篦工程系,博士学位,工程师,主要从事工业炉设计工作。 I收稿日期l
2011埘一12
万方数据
・38
・
中固有色冶金
A卷生产实践篇・设备及自动化
图3下部骨架图 图2 63.6m×10m阳极炉水冷烟罩设计总图 落到地面,大大增加了安装与维护空间。 水冷烟罩与烟口护板之间装有柔性密封板,防 止烟气溢出。下部设有接灰斗,见图4。该水冷烟 罩总重~17t,占用空间小,体积小,重量轻。
the analysis and comparison of water-cooled good performance
was
hood
in other
projects,the
structural
design
was optimized and the
obtained after startup.
Key words:anode furnace;smoke
从图l可看出,该烟罩支撑复杂,水套与水套之
间采用H型钢连接支撑,上部与下部水套的支撑全 部落到地面。另外,该烟罩还存在如下问题:开炉
烟口水冷烟罩的设计充分考虑了如下因素:足够的
冷却面积,较好的冷却效果;尽量避免立柱落地,以 免造成与土建立柱间距太密,给施工、维修等带来不 便;烟罩出口的大小合适,防止烟气流动不畅,对烟 罩冲刷严重;体积小,占用空间小。 由3.6mxlOm阳极炉水冷烟罩设计总图见图2。
炉在氧化还原期会有大量的高温烟气产生,该烟气
进换热器之前要在出烟口配置的水冷烟罩将温度从
。1
100℃降到~900℃,以充分利用烟气余热。
该烟罩与金川由4.15
m×12
m阳极炉的水冷烟
m×
罩相似,因此在设计该烟罩之前,首先对书4.15
12
m阳极炉水冷烟罩进行分析。
套只有一个进水管和出水管的设计,导致水量不足,
目前该烟罩在现场已成功安装,并顺利投产,经 过半年多的生产运行,一切正常,达到了预期的效果。
3结论
新设计的63.6 m×10 m阳极炉用水冷烟罩占用 空间小、体积小、重量轻。投产后烟罩烟气畅通,冷 却强度大,烟气温降明显,为后续的换热器提供了良 好的烟气条件。该烟罩构思巧妙,投产后未出现过 烟罩变形、水套烧坏等事故,其设计思路及结构可供 今后设计参考。 63.6mx 10m
本文链接:/Periodical_ysyl201202010.aspx
2012年4月第2期
郝小红:cb3.6mxlOm同转阳极炉出烟口水冷烟罩设计
-37・
由3.6mx l Om回转阳极炉出烟口水冷烟罩设计
郝小红
(中国恩菲工程技术有限公司,北京100038)
【摘要】 阳极炉出烟口水冷烟罩采用全新设计,在分析和比较其它项目水冷烟罩的基础上,进行了结 构优化设计。投产后效果良好。 【关键词】阳极炉;出烟口;水冷烟罩;优化设计 【中图分类号】TF81 1;TF806;TF066.3+3【文献标识码】B【文章编号】1672—6103(2012)02—0037—02
l 000 mXl0
m回转阳极炉的出烟口为700
mm×
mm,为防止高温烟气冲刷烟罩,下部水套最外
152
部与书5
mm的圆相切。依据此设计,当炉口旋
图4接灰斗示意图
转一定角度时,下部烟罩仍可以保证烟气畅通地通 过上部烟罩而进入换热器。 下部水套共8块,前后左右水套各2块。用于支 撑水套的下部骨架见图3。
O引言
会理昆鹏铜业10万妇阳极铜工程的工艺流程 为:铜精矿艾萨炉熔炼,生成的铜锍和炉渣混合熔体 经流槽流入沉降电炉澄清分离;沉降电炉分离后的
铜锍放出后用包子送往Ps转炉进行吹炼,炉渣送渣 缓冷场;吹炼产出的粗铜由包子送火法精炼,吹炼炉 渣返回沉降电炉;精炼产出的阳极铜经流槽进双圆 盘浇铸系统,精炼渣返回吹炼转炉。
rotary anode furnace
经过冷却后的烟气通过右侧出口进入空气换热
器。前后水套各焊接有两个连接耳,两根垂直槽钢 与连接耳采用螺栓连接,起同定前后水套的作用。 左右水套也采用连接耳与槽钢螺栓固定的方式。而 整体下部水套支撑于工艺楼板之上。
上下水套支撑骨架均支撑于工艺楼板上,而未
Design
蕊宓
Ⅲ
搏 k基
.巨.
■T’!■
乒
\’
I 斗一
,
该流程涉及的工业炉窑主要包括:艾萨炉、电 炉、转炉及回转阳极炉。由于电解精炼对阳极板的 化学成分有严格的要求,因此需要对粗铜进行火法
精炼,目的是进一步除去粗铜中的有害杂质。阳极
j{£|
‘—d
图l坼.15mxl2m回转阳极炉水冷烟罩总图
后,由于现场工人的误操作曾导致水套爆裂;正常生 产时,烟罩温度过高;体积庞大,设备总重~42t。 分析上述问题可知:支撑水套的立柱全部落到 地面,导致立柱与土建立柱间距过于密集,给安装及 维修造成很大的不便;水套温度过高是由于每块水
从图2可以看出,该烟罩分为上下两部分,每块
水套之间留有5 mm的缝隙,各水套之间采用连接耳 连接,每块水套水管均采用两进两出,大大提高了冷 却强度,同时各水套留有清灰门。 上部烟罩共7块水套,上部水套顶部及左侧各 为一块水套,前水套及后水套各为两块,底部斜水套 一块,支撑水套的上部骨架支撑于工艺楼板之上。 63.6
on
water-cooled hood of smoke outlet in
HAO Xiao-hong
Abstract:The
new
design was used in the water-cooled hood of smoke outlet in anode furnace.On the basis of
50万t电解铝项目将开工;金川公司6万t电解镍扩能改造工程、酒钢集团榆钢灾后重建、白银公司铜冶炼技
术提升改造等项目将在年内建成投产;华煤集团20万t聚丙烯项目将加快建设进度;酒钢集团平凉煤电化循 环经济项目将争取开工。
万方数据
(φ)3.6m×10m回转阳极炉出烟口水冷烟罩设计
作者: 作者单位: 刊名: 英文刊名: 年,卷(期): 郝小红, HAO Xiao-hong 中国恩菲工程技术有限公司,北京,100038 中国有色冶金 China Nonferrous Metallurgy 2012,41(2)
outlet;water-cooled
hood;optimal
design
《尹、瞳≯步、驴、驴、驴、驴、移、驴、痧、矿、驴、垆、矿吨庐、‘争、驴、护、驴、驴、‘矿、驴、驴、矿、矿、驴、驴、驴、莎、移、驴疥疥岔扔_2争
甘肃新增50万t电解铝项目将开工
2012年甘肃省一批工业建设项目将加快建设。其中包括:酒钢集团45万t电解铝项目投产后,新增