质量管理05_控制图
统计质量管理第五章 统计过程控制(1)

❖ 这两天的变异原因消除后,失控点会从数据中消除。 ❖ 点的消除改变了过程的平均值和标准差。 ❖ 同时,中心线,上下控制限和各分区都会产生变化。
p15/428000.055
UCL(0p.)05350.0505.9450.123
100
LCL(0p.)0-5350.050.59450.0103.000
100
Number Cracked 的 P 控制图
0.14
0.12
+3SL=0.1234
0.10
+2SL=0.1006
比率
0.08
+1SL=0.0778
0.06
_ P=0.055
0.04 0.02 0.00
-1SL=0.0322
-2SL=0.0094 -3SL=0
❖ 如果一个过程的某个特征值是5%,拥有20个单位 的子组的平均计点数是1。而且每一个子组有一个 整数点,产出比例增加5%,那么中心线是0.05, 控制下限是0,控制上限是0.196。
❖ 子组的比例值只有四种情况(0,0.05,0.1,0.15) 是落在控制限以内。利用之前所述之方法寻找失 控点则是毫无意义的。
1
4
7
10
13 16 19 22 25 28
样本
❖ 通过改变过程,消除失控点,重新计算控制限和 区域界限,此时,最初判断为一般变异的点现在 可能会变成缺乏控制的状态。
❖ 这种现象发生时,需要再次进行评估,并消除变 异点。
❖ 但是,这种做法重复得多会产生两个问题,一是 数据库会因此萎缩,控制图的建立会基于越来越 少的子组,不能很好地描述原来的过程。
现代质量管理学,第四版,韩福荣,机械工业出版社,电子课件。第五章

CP
T
6
TU TL
6
2. 双侧公差分布中心和标准中心不重合的情况下CPK值的计算
当质量特性分布中心µ和标准中心M不重合时,虽然分布标准差σ未 变,但却出现了过程能力不足的现象。令ε=|M-µ|,这里ε为分布中心对 标准中心M的绝对偏移量。把ε对T/2的比值称为相对偏移量或偏移系数, 记作K。
(二)两类错误
第一类错误是将正常的过程判为异常,既生产仍处于统 计控制状态,但由于偶然性原因的影响,使得点子超出控 制限,虚发警报而将生产误判为出现了异常。处于控制状 态的样品有0.27%的可能落在3σ控制界限外,即犯错误的 可能性在 1000 中约有 3 次。犯这类错误的概率称为第Ⅰ 类风险,记作α。 第二类错误是将异常判为正常,生产已经处于非统计控 制状态,但点子没有超出控制限,而将生产误判为正常, 这是漏发警报。把犯这类错误概率称为第Ⅱ类风险,记作β。
准则2(连续9点落在中心线同一侧)
此准则通常是为了补充准则1而设计的,以便改进控制图的灵敏度。选择 9点是为了使其犯第一种错误的概率α与准则1的α0=0.0027大体相仿, 同时也使得本准则采用的点数不致过多于美国格兰特和列文沃斯(Grant and Levenworth)在1980年提出的7点链判异的准则。
CP上
T
/2
3
T /2 CP下 3
CPK C(P 1 K)
三、过程不合格品率的计算
(一) 当分布中心和标准中心重合时的情况
P 1 P(TL x TU ) 2(3CP )
由以上公式可以看出,只要知道CP值就可求出该 过程的不合格品率。
质量管理学控制图课件.ppt

• 计算统计量的中心值和控制界限。
x 图:
中心值CL=
= =x29.86(g)
UCL= =x+ A2 R ≈ 45.69(g)
LCL=
= x—
A2
R
≈
14.03(g)
注:A2为随着样本容量n而变化的系数,可由控制图系数选用表中选取。
第13页,共35页。
R 图:
中心值 CL= R=27.44(g) UCL= D4 R≈ 58.04(g)
• 在质量改进方面,可以用来确认某过程是否得到了改进。
第5页,共35页。
二、应用控制图的步骤
应用步骤如下:
选择控制图拟控制的质量特性,如重量、不合格品数等;
选用合适的控制图种类; 确定样本容量和抽样间隔;
收集并记录至少20~ 25个样本的数据,或使用以前所记录的数据; 计算各个样本的统计量,如样本平均值、样本极差、样本标准差等;
• 在不对该过程做任何调整的同时,继续用同样的方法对 多装量抽样、观察和打点。如果在继续观察时,控制图 显示出存在异常原因,则应进一步分析具体原因,并采 取措施对过程进行调整。
第16页,共35页。
四、控制图的观察与分析
点子没有超出控制线(在控制线上的点子按出超出处理),
控制界限内的点子排列无缺陷,反映工序处于控制状态,生 产过程稳定,不必采取措施。 控制图上的点子出现下列情形之一时,即判断生产过程异常:
34.2
25
24
28
27
22
32
54
163
32.6
32
25
42
34
15
29
21
141
23.2
27
累计
746.6
质量管理05控制图

I—Rs图 计算移动极差Rsi
质量管理05控制图
控制图的绘制(续)
•4.(1)控制图样本参数的计算:
图名称 np图
步骤
计算平均不合格 品率
p 图 计算各组不合格 品率pi
c图 计算各样本的平 均缺陷数
u图 计算各样本的单 位缺陷数ui
计算公式
备注
(np)i——第i样本的 不合格品数(各样本 样本容量皆为n)
质量波动的来源主要有五个方面(简称 5M1E ):
• 操作人员(Man)——人 • 设备(Machine) —— 机 • 原材料(Material)——料 • 操作方法(Method)——法 • 环境(Environment)——环 • 测量(Measurement) ——测
质量管理05控制图
控制对象-质量波动(续)
质量管理05控制图
控制图的由来
•控制图的发展:
20世纪40年代,美国 贝尔电话公司应用统计质量 控制技术取得成效;美国军 方在军需物资供应商中推进 统计质量控制技术的应用; 美国军方制定了战时标准 Z1.1《质量控制指南》、 Z1.2《数据分析用的控制图 法》、 Z1.3《生产中质量管 理用的控制图法》。
质量管理05控制图
均值-极差控制图(续)
极差控制图随生产过程的特点不同 有其不同的作用: •在自动化水平比较高的生产过程中, 产品质量的一致性好。因此,当极差增 大,意味着机器设备出现故障.需要进 行修理或更换; •在非自动化生产过程中,极差反映出 操作者的技术水平,生产熟练程度,故 又称为操作者控制图。
–所谓满足规格要求,并不是指上、下控制线必须在规格上、下限内侧,
即UCL>TU;LCL< TL。而是要看受控工序的工序能力是否满足给定 的Cp值要求。
质量管理-质量控制-老七种工具之七:控制图
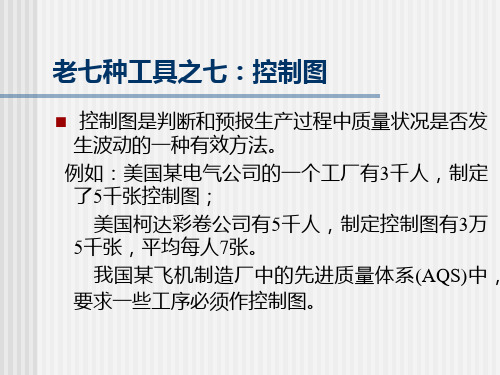
控制图是判断和预报生产过程中质量状况是否发 生波动的一种有效方法。 例如:美国某电气公司的一个工厂有3千人,制定 了5千张控制图; 美国柯达彩卷公司有5千人,制定控制图有3万 5千张,平均每人7张。 我国某飞机制造厂中的先进质量体系(AQS)中, 要求一些工序必须作控制图。
P(连25点,d > 0)=0.0654 (有人建议这一判据应划为稳态)
2) 失控状态的判断
只要控制图上的点子出现下列情况时,就可判断工 序为失控状态: (a) 控制图上的点子超出控制界限外或恰好在在界 限上;(针对判真为假而言,α越小越好) (b) 控制界限内的点子排列方式有缺陷,呈现非随 机排列。 (针对判假为真而言, β越小越好)
所谓控制图的基本思想就是把要控制的质量特性 值用点子描在图上,若点子全部落在上、下控制 界限内,且没有什么异常状况时,就可判断生产 过程是处于控制状态。否则,就应根据异常情况 查明并设法排除。通常,点子越过控制线就是报
警的一种方式。
2.常用控制图的种类
常用质量控制图可分为两大类: (1)计量值控制图包括:
的场合。
计量值控制图对工序中存在的系统性原因反应敏 感,所以具有及时查明并消除异常的明显作用, 其效果比计数值控制图显著。计量值控制图经常 用来预防、分析和控制工序加工质量,特别是几 种控制图的联合使用。
计数值控制图则用于以计数值为控制对象的
场合。离散型的数值,比如,一个产品批量的不 合格品件数。虽然其取值范围是确定的,但取值 具有随机性,只有在检验之后才能确定下来。
小组观察 数目(n)
2 3 4 5 6 7 8 9 10
表4-11 计量值控制图计算公式中的系数值表
A2 1.830 1.023 0.729 0.577 0.483 0.419 0.373 0.337 0.308
质量管理学复习试题及答案
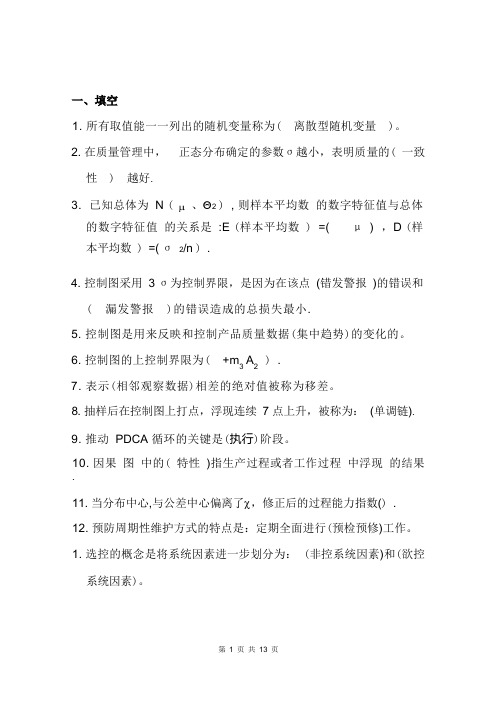
1. 所有取值能一一列出的随机变量称为( 离散型随机变量 )。
2. 在质量管理中,正态分布确定的参数σ越小,表明质量的( 一致性 ) 越好.3. 已知总体为N ( 、Θ2 ) , 则样本平均数的数字特征值与总体的数字特征值的关系是:E (样本平均数 ) =( μ ) ,D (样本平均数 ) =( σ 2/n ) .4. 控制图采用3 σ为控制界限,是因为在该点(错发警报)的错误和( 漏发警报 )的错误造成的总损失最小.5. 控制图是用来反映和控制产品质量数据(集中趋势)的变化的。
6. 控制图的上控制界限为( +m3 A2) .7. 表示(相邻观察数据)相差的绝对值被称为移差。
8. 抽样后在控制图上打点,浮现连续7 点上升,被称为:(单调链).9. 推动PDCA 循环的关键是(执行)阶段。
10. 因果图中的( 特性)指生产过程或者工作过程中浮现的结果.11. 当分布中心,与公差中心偏离了χ,修正后的过程能力指数() .12. 预防周期性维护方式的特点是:定期全面进行(预检预修)工作。
1. 选控的概念是将系统因素进一步划分为: (非控系统因素)和(欲控系统因素)。
2. 质量体系就是为了达到(质量目标)所建立的综合体。
3. 传统质量管理的主要特征是( A ) .A 按照规定的技术要求,对产品进行严格的质量检验B 按照过去的经验进行质量检验C 按照领导的意图进行质量检验4. 2000 年版 ISO9000 族标准将由四项基本标准及若干份支持性技术报告构成。
四项基本标准中—— ISO9001 是:( C )。
A 质量体系审核指南C 质量管理体系—要求B 质量管理体系—指南D 质量管理体系—概念和术语5. 造成产品质量异常波动的原因是( B )。
A 偶然性原因、B 系统性原因、C 不可避免的原因6. 相关系数的取值范围是( D).A 0≤<1B 0≤≤1C − 1≤≤0D − 1≤≤17. 每吨铸件成本(元)和每一工人劳动生产率(吨)之间回归方程为y=270—0.5x。
控制图、排列图、直方图讲义

控制图、排列图和直方图参考书:张智勇(2004),基础质量管理工具,广东科技出版社马逢时等,六西格玛管理统计指南,中国人民大学出版社。
全国质量专业技术人员职业资格考试办公室,质量专业理论与实务,第4章统计过程控制,中国人事出版社。
质量管理工具有七种主要工具:排列图,直方图、质量控制图、散点图、分层法、因果图和检验表(老7种)。
本次重点介绍排列图,直方图和质量控制图的软件画法。
控制图能对过程质量特性统计值进行测定、记录、评估,从而监察过程是否处于控制状态,简言之,控制图用以判断生产过程是否处于统计控制状态(是否存在异因),可以判断生产过程的异常,及时报警。
质量控制图既可以由质量管理人员使用,也可以由第一线工人使用,日本115家中小企业平均每个厂用137张控制图;美国柯达公司5000名职工,共用35000张控制图,可见其重要性。
工厂中使用控制图的数量在某种意义上反映了管理现代化的程度。
控制图是质量管理7个工具的重要组成部分,也是六西格玛管理的重要工具。
质量管理软件分为专用软件与通用软件,后者如MINITAB,JMP、SPSS,SAS-QC等。
许多专用软件ETM(ERP)中也有质量控制部分。
本次只介绍MINITAB15中文版。
MINITAB是美国宾夕法尼亚大学统计系开发,特别适用于质量管理。
主要窗口有数据窗口(工作表)和会话窗口。
可用粘贴等方法将数据填入工作表。
在会话窗口发布命令和收到结果。
Pareto 图是一种条形图,其中水平轴表示所关注的类别(缺陷),而非连续尺度。
类别通常是缺陷。
将每种缺陷按百分比从大到小排列成条形,Pareto 图可帮助您确定哪些缺陷是“少数而关键”的缺陷,哪些缺陷为“多数而琐碎”。
累积百分比线条帮助您判断每种类别所占的比例。
Pareto 图可帮助你,着重改进能获得最大收益的方面。
画排列图可按如下步骤:将数据贴入工作表,为了清楚,在C1,C2下建立变量名“缺陷”和“频数”。
缺陷的值是断裂,檫伤,…等;频数的值是10,42,…。
第五章 工序质量控制工具—控制图
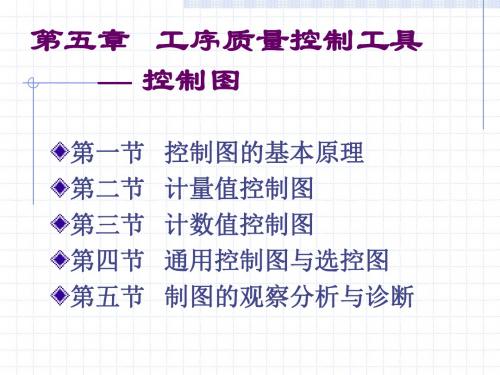
3.控制图的作用:
(1) 判断生产工序质量的稳定性。 (2) 评定生产过程的状态,发现以便及时消除生 产过程的异常现象,预防废、次品的产生。 (3) 确定设备与工艺装备的实际精度,以便正确 的做出技术上的决定。 (4) 为真正地制定工序目标和规格界限确立了可 靠的基础,也为改变未能符合经济性的规格标 准提供了依据。
X
(4)比X单值控制图 敏感性强
2.R控制图的特点
极差R是指一组数据中的最大值与最小值之差:R =Xmax- Xmim 极差R控制图是用样本的极差反映分析和控制总 体的离散程度的。
特点: (1) 极差不会出现负值。 (2) 极差的众数会偏向于数值较小的一边,极差 R很大的情况很少发生。 所以极差的分布是非对称的。
第一种错误 如果产品质量波动服从正态分布,那么产 品质量特性值落在μ±3σ控制界限外的可 能性是0.27%,而落在一侧界限外的概率 仅为0.135%。根据小概率事件在一次实 验中不会发生的原理,若点子出界就可以 判断生产有异常。可是0.27%这个概率数 值虽然很小,但这类事件总还不是绝对不 可能发生的。当生产过程正常时,在纯粹 出于偶然原因使点子出界的场合,我们根 据点子出界而判断生产过程异常,就犯了 错发警报的错误,或称第一种错误。这种 错误将造成虚惊一场,停机检查劳而无功, 延误生产等等损失。
选控图的基本原理当生产过程正常时生产过程中起作用的因素是偶然因素和非控系统因素如业务量引起的波动起作用但非控系统因素通过计算选控值已加以排除实际控制图中只有偶然因素起作用质量特性数据的选控数据形成了某种曲线分布这时选控数据9973落在选控数据平均值3的范围内落在界外的只有027选控数经抽样在控制图上打点不出界表明生产过程正常可以继续生产
一、X单值-移差控制图
控制图在质量管理中的应用

控制图在质量管理中的应用Xx(xx学院数学统计学院,河南 xx 455002)摘要:本文分别介绍了均值-标准差控制图(x s-图)、均值-极差控制图(x R-图)和不合格品率控制图(p图)等控制图的制作过程和使用方法.并且配以相应的例题做详细论述. 关键字:中心线;控制界限;控制;合格;不合格1 引言一个产品总是经过设计、制造与检验才能将合格的产品提供给使用者.抽样检测是判断一批产品是否合格的方法,它通过对不合格的产品分析,发现设计与制造的中的问题,反映给相关部门,以便进行改进,然而这些产品已经生产,并造成了一定的损失,为了避免这一损失,一个自然的想法是进行预防.如果不考虑设计中的问题,大部分质量问题可以在制造过程中给予避免,问题在于及时发现问题.假如在制造过程的每一道工序建立一个简单易行的控制系统,当质量问题一出现就能及时发现,及时纠正,不使不合格的半成品流入下一道工序,加以避免,达到预防的目的.本文所介绍的统计过程控制图就是一个简单易行的控制系统,在一些场合有人称其为统计过程控制图SPC(Statistical Process Control).2 波动及其原因大家知道没有两个完全相同的产品,产品的差异常常用其质量特性(记为X)的差异反映出来.造成波动的原因是由于在生产过程中存在许多的波动源比如:机器的老化、电压的稳定、操作者的情绪的波动、操作场所的湿度、操作场所的光线等都会对产品的质量产生影响.波动又可以分为两大类:一是正常波动,一是异常波动.所谓正常波动,其特点是过程中存在许多波动源,每个波动源对质量特性X的影响都是很微小的,通常X服从正态分布,且其分布不随时间的变化而改变.这时过程为受控状态.所谓异常波动,其特点是过程中存在许多波动源,但有一个或几个对质量特性的影响较大,而其它的影响均很小,由于这些强的波动源的出现,就使X的分布随时间的变化而发生变化,有时是改变的分布的位置,有时是改变分布的标准差,有时会使分布的形状发生变化.这时候过程不处于统计控制状态,也称为失控状态.因此,我们可以根据质量的特性的分布去区分波动的类型,当随时间变化,质量的特性分布为保持不变的正态分布时,这时为正常波动,这是无法避免的.当质量的特性发生变化时,则存在异常波动,需要去识别它,并加以剔除.3 减小波动的对策要消除波动是不可能的,而要尽量减少波动是可能的.如果存在异常波动的话,这时要设法找到他,用技术手段去排除,从而使过程恢复到受控状态.如果过程处于统计控制状态,也不并一定满足产品的质量要求,通常一个产品的特性值总有一个目标值和一定的公差范围,如果波动在公差范围内是允许的,只是不需要去减小波动.如果波动超过公差允许的范围,那么就要设法去减小波动,这往往不是简单的技术手段所能解决的,有时需要对整个生产线做改造,譬如更换设备零件等. 4 控制图的种类过程控制图有多种.由于质量特性通常有两大类,一类是计量的,如温度、长度、电阻等,一类是计数的,如不合格品数、缺陷数等,因此常规控制图也有两大类. 4.1 计量值控制图均值-标准差控制图(x s -图) 均值-极差控制图(x R -图) 中位数-极差控制图(x R -图) 单值-移动极差控制图(s x R -图) 4.2 计数值控制图不合格品率控制图(p 图) 不合格品数控制图(pn 图) 单位缺陷数控制图(u 图) 缺陷数控制图(c 图) 5 控制图的原理与构造尽管有多种控制图,但其基本原理都是一样的,以下以计量值控制图来说明.设过程的质量特性X 是计量的,在过程处于稳定的状态(既统计控制状态)是X 应服从正态分布,记为2(,)N μσ,假如能把此正态分布的两个参数μ(均值)和σ(标准差)控制住,那么质量特性也就得到了控制.为了控制μ与σ,常需要两张控制图,一张用于控制μ,一张用于控制σ.在实际中,常用样本值x 估计μ,而用样本标准差s 或样本的极差R 估计σ.若用x 和s 分别估计μ和σ就形成了x s -图,若用x 与R 分别估计μ与σ就形成x R -图.控制图是根据正态分布的3σ原理[2]而构造出来的.于是就加入了一个统计量12(,T T x x =,…,)n x 服从正态分布或近似服从正态分布,即2(,)T TN μσ其中T μ是T 的均值,T σ是T 的标准差,根据3σ原理,有(33)0.9973T T T T P T μσμσ-<<+=这表明,对统计量的T 做大量的重复的观察,则其中99.73%的T 值是应该落在区间(3,3)T T T T μσμσ-+之间,仅有0.27%在此区间外,若取3T T μσ+为控制上界,记为UCL 3T T μσ-为控制下界,记为LCLT μ为控制中心线,记为CL将这三条水平线画在一张坐标纸上,其横轴为时间或样本序号,纵轴为T 的观察值,这就形成了一张控制图.当把T 的观察值按序点在图上,就可用于过程控制.这些上、下控制界限被用来判断生产过程有无异常,当图上的点越出控制上界或控制下界是就认为生产过程出现异常.因为点越出上、下界是一个小概率事件,通常在一次实验中不应该发生,一旦发生,就认为过程出现异常.综上可知,控制图实际上是生产过程质量的一种记录图形,它提供了判断过程是否处于统计控制状态的一种方法.实际中,T μ与T σ是未知的,人们需要收集一定数量的样本做出估计.T μ常用T 做估计,又记T σ估计为ˆT σ,则中心线以及上、下控制界线分别为 CL T =ˆ3T UCL T σ=+ (1) ˆ3T LCL T σ=- 具体的估计方法将结合每张控制图的特点在做叙述. 6 均值-标准差控制图(x s -图)均值控制图主要用于判断生产过的均值是否处于或保持在所要求的统计控制状态,标准差控制图主要用于判断生产过程标准差是否处于或保持在所要求的统计控制状态,这两张图通常一起用,因此称为均值-标准差控制图,记为(x s -图).下面我们就来叙述制作和使用控制图的一般步骤,并在质量特性服从正分布条件下给出制定控制界限的原理. 6.1 收集预备数据首先根据选定的特性值,按一定时间间隔,抽取一个容量为n 的样本,共抽k 个样本,对每一个样本内的每个样品测定其特性值,将其数值填在数据表中(见例1的表2)一般的要求是25k ≥.例[1]1 某车间生产一种电阻,每隔一小时随机抽四个电阻测定其阻值(单位为k Ω)这就得到一个样本,共抽取了25个样本(数据见表1).标准要求其电阻值在[77.9,86.1]之间为合格.作能用于控制的均值-标准差控制图.RTX质量特性90.9.12 样本容量测量值()i 1i X 2i X 3i X 4i X i x i s1 81.86 81.61 82.98 81.33 81.945 0.7232 82.09 81.06 80.48 80.07 80.925 0.8763 81.21 82.77 79.95 80.72 81.162 1.1914 81.23 80.61 81.68 82.13 81.412 0.6495 83.20 82.50 82.37 80.54 82.152 1.1356 82.68 82.48 82.96 82.12 82.560 0.3537 80.17 81.83 81.12 81.41 81.132 0.7058 80.40 81.60 85.00 83.80 82.700 2.0829 80.69 80.49 82.16 84.29 81.908 1.754 10 82.72 82.12 81.77 81.60 81.052 0.495 11 80.98 81.33 81.60 80.70 81.152 0.394 12 80.42 82.20 80.13 80.24 80.748 0.976 13 82.11 82.13 83.22 82.17 81.408 0.542 14 82.40 81.41 82.93 83.13 82.468 0.769 1581.55 80.91 81.3182.43 81.550 0.64316 81.32 80.12 81.23 80.38 80.762 0.602 17 81.39 80.85 80.60 80.93 80.942 0.330 18 81.37 83.12 80.39 81.81 81.672 1.133 19 80.62 82.06 81.49 80.92 81.772 0.732 20 79.76 81.17 81.24 79.54 80.428 0.903 21 81.06 82.06 82.76 82.46 82.085 0.741 22 82.55 83.53 82.94 81.89 82.728 0.688 23 83.33 80.33 80.36 80.67 81.172 1.447 24 81.17 81.33 82.57 80.87 81.485 0.748 6.2 制作分析用控制图6.2.1计算第一个样本的均值与标准差以ij x 表示i 个样本的第j 次观察值,用i x 与j s 分别表示第i 个样本的均值与标准差,即11,1,2,ij n i i j x x s i n ====∑…,k 例1每一个样本的均值与标准差一起列在表1的最后两列中.6.2.2 计算k 个样本的均值的均值与标准差的均值这两个均值分别记为x 与s 即有11/,/kki i i i x x k s x k ====∑∑这便是控制图的中心线.对于例1来讲,由表1的数据可以求出来,于是得到81.5384x =,0.8608s =.6.2.3 计算x 图与s 图的上、下控制界限根据(1),x 图与s 图的中心线分别是各样本均值x 与标准差的平均值s ,为了计算上、下控制界限需要给出样本均值的标准差与标准差的标准差.根据3σ原则,x 图的上、下控制界为3x x σ±,由于已知2()/Var x n σ=故x σσ=由于σ未知,用其无偏估计*2/s C 代替,则图上、下控制限为*13/(x s C x A s ±=±其中*1A =.s 图的上、下控制限为3s s σ±,由于已知[]222*22()()()1()Var s E s E s C σ⎡⎤=-=-⎣⎦其中*21()/()22n n C -=Γ(()Γ是伽马函数). 故s σ=,同样σ用其无偏估计*2/s C ,则有*22(1)s C s ±=± 记321B =421B =+. 则s 图的上控制限为4B s ,下控制限为3B s .若30B <.则用0代替.以上的*134,,A B B 都是与样本的容量n 有关的常数,具体数值见表2,当30B ≤时不予考虑,以“—”表示.x 样本大小*1A *2C 3B 4B 2 2.659 0.7979 —— 3.267 3 1.954 0.8862 —— 2.568 4 1.628 0.9213 —— 2.266 5 1.427 0.9400 —— 2.089 6 1.287 1.9515 0.029 1.970 7 1.182 0.9594 0.113 1.882 8 1.099 0.9650 0.179 1.815 9 1.032 0.9693 0.232 1.761 10 0.975 0.9727 0.276 1.716 11 0.927 0.9754 0.313 1.679 12 0.886 0.9776 0.346 1.646 13 0.850 0.9794 0.374 1.618 14 0.817 0.9810 0.399 1.594 对例1来讲,4n =由表2可查得1=1.628A ,4 2.266B =表中3B 为“—”则3B 用0来代替.由此可得6.2.4 作分析控制图在坐标纸上分别作x 图和s 图,x 图在上,s 图在下,纵坐标分别为x 与s ,横坐标为样本序号,用实线表示CL ,用虚线表示上、下控制界限UCL 与LCL (见图1)然后把各自的样x s中心线CL xs上控制界限UCL *1x A s + 4B s下控制界限LCL*1x A s -3B sx 图 s 图 中心线CL 81.53840.8608上控制界限UCL 81.5384+1.628×0.8608 =82.93982.266×0.8608 =19.51下控制界限LCL81.5384-1.628×0.8608 0本i x 与i s 的值分别依次点在x 图与s 图上,通常x 图中的点用“·”表示,s 图中的点用“⨯”表示,再用直线将相邻的两点连接成折线.图1 例1 x R -图6.2.5 判断生产过程是否处于生产状态从图1可见,例1中的第8组数据的标准差落在上控制界限外(8s 大于s 图的UCL ),所以认为生产不处在统计控制状态.通常我们可以通过观察控制图上点的分布情况来判断生产过程是否处于统计控制状态,仅当下列条件都满足时,才认为过程处于统计控制状态.(1)连续25点中没有一点在限外或连续35点中最多一点在限外或连100中最多两点在限外.由于在统计控制状态下,每一点落在控制界限以内的概率为0.9973,那么连续25点都在控制界限以内的概率为250.9973,从而得至少有一点在界限之外的概率为: 2510.9973-= 0.065358.这是一个小概率事件,通常一次试验中不应该发生,一旦发生,认为发生了异常.出现这种情况可能性有:测量系统发生了变化,譬如测量员的调换,量具更换等.在s 图上,如果点超出上限,则表示波动在增加,而点超出下限,则波动在减小,质量变好.在x 图上出现这种情况,有可能为某种外界突发原因引起.同样在连续35点都在控制界限以内的概率为350.9973,恰有一点落在控制界限以外的概率为3435(10.9973)0.9973⨯-⨯,同理可以得出来至少有两点在界限之外的概率为:353410.997335(10.9973)0.99730.0040886--⨯-⨯=.同理又可得连续100点至少有三点落在控制界限以外的概率为0.0026177.他们都是小概率事件. (2)控制界限内的点的排列无下列异常现象当数据点都在控制界限以内,生产处控制状态时,数据点应该在中心线上下随机波动,不应该有规律性的排列出现,下列事件的发生都是小概率事件.① 连续7点或更多呈上升或下降趋势.在随机情况下,每一点对前一点来讲,或大或小.发生的可能性为0.5,那么恰好有连续7点呈上升趋势的概率为:720.50.015625⨯=.产生这种情况的可能有:测量系统的变化、量具精度下降造成这种偏移与偏差;在s 图上,如果点呈上升趋势则表明波动在逐渐增大,可能过程的输入有变化,譬如设备故障、原料变化等,如果点呈下降趋势,表明波动在逐渐减小,应及时研究与总结,以改进质量;在x 图上发生,表明过程均值在逐渐增加或减小,有可能是设备老化、器具磨损到需要调换或调整的时候了.② 过多的点落在中心线的同侧:连续7点或更多点在中心线同一侧;连续11点中至少有10点在中心线同一侧;连续点14中至少有12点在中心线同一侧;连续17点中至少有14点在中心线同一侧;连续20点中至少有16点在中心线同一侧.在随机情况下,点落在中心线与控制上限(下限)的概率为0.9973/20.49865=,连续7点在中心线的同侧的概率为:720.498650.015322⨯=.同理可知连续11点中至少有10点在中心线的同侧的概率为0.0113754; 连续14点中至少有12点在中心线的同侧的概率为0.0124656; 连续17点中至少有14点在中心线的同侧的概率为0.0121542; 连续20点中至少有16点在中心线的同侧的概率为0.0108626; 这些都是小概率事件.发生这种情况的原因可能有:如上所述的测量系统的变化;s 图上,若这些点在中心线的上侧,表明波动在增大,可能如上述所述过程输入变化,若这些点在中心线的下侧,表明波动在减小,应及时研究当时的生产条件,进行总结,以改进质量,当然也不排除因测量系统的问题而造成的;在x 图上发生上述现象表明过程的均值有位移,可能是环境造成原因所致.③ 连续3点中至少有2点或连续7点中至少有3点落在二倍与三倍标准差控制界限之间.如果我们把中心线与控制界限之内的区域等分为三个区域,并分别命其为A,B,C ,如图2.那么上面的叙述即为点落在A 区的情况.图2 区域A 、B 、C每一点在中心线与两倍标准的概率为0.9545落在两倍标准差与三倍标准差之间的概率为0.99730.95450.0428-=,那么可以得出来连续3点中恰有两点落在其中的概率为230.04280.9545⨯⨯,三点都落在其中的概率为30.0428.因此连续3点中至少有两点都落在两倍标准差与三倍标准差之间的概率为:2330.04280.95450.04280.00532339⨯⨯+=同理有连续7点中至少有三点落在两倍标标准差与三倍标准差这间的概率0.00238254.由于上述这些变化现象都是小概率事件,所以一旦出现,表明质量发生变化,应该引起注意,以防止降低质量的异常情况出现.6.2.6 当生产过程不处于统计控制状态时,就采取下列措施首先应该寻找产生异常的原因,在找原因时应先从自己着手,或从内部着手,譬如记录、计算、作图等是否有错,测量是否正确,操作有无不当之处,工具是否有缺损,机器是否疲劳,材料有无变化,电压是否有波动等.当异常数据点不多时,在确认原因后,消除降低质量的异常因素,同时去掉异常数据点对应的一组数据,重新计算中心线和控制界限.然而在重新计算时,不应去掉对质量有利的数据,也不能去掉虽使质量降低但不能消除异常原因的数据.重新计算后,如果仍有一点在控制界限之外时,可补充到35个样本后重新计算与考察,此时只允许一点在限外;如果有两点在限外的话;可补充到100个样本后重新计算与考察,如果有两点在限外的,仍属过程受控.当异常数据比例较大时,应改进生产过程,重新计算数据,并重新计算中心线和控制界限.在例1中,对产生第8组数据的生产情况进行了检查,发现是设备发生了故障,所以去掉第8组数据重新计算得81.4900x =, 0.810s =同此求得x s -图是中心线和上、下控制界限分别为x 图s 图 中心线CL81.4900 0.810 上控制界限UCL82.8087 1.835 下控制界限LCL80.1713 0去掉第8点后,例1的分析控制图见图3.此时再考察图上的分布,发现生产过程处于控制状态.图3 例1x R -图6.3 判断生产过程是否满足质量要求当生产过程处统计控制状态时,可以进一步判断生产过程是否满足顾客(包括使用者、下一道程序的加工者等)的质量要求.可以根据产品的质量要求选用适当的公式计算过程能力指数.在例1中质量特性为电阻值,给出了双边规格77.9L T =,86.1u T =,从而可以得出来82,M =x =82.4900M ≠,故用公式2(1)6pk p T C k C sε-=-=计算,σ未知,用其无偏估计*2/s C 代替,现在*24,8.2,0.51,0.810,0.9213U L n T T T s C ε==-====因而过程能力指数为*228.220.511.3616/60.81/0.9213pk T C s C ε--⨯===⨯ 由此可见该生产过程满足质量要求,因此所制定的控制图的中心线与控制界限可用于生产控制.6.4 作控制用控制图当生产过程满足顾客质量要求时,我们便可以用上面获得的中心线与上、下控制界限画控制图,放在生产现场来对质量指标进行控制,这张图便是控制用控制图.在生产现场用控制图时,通常应按收集预备数据同样的样本容量抽取样本,并测定样本中每一个样品的特性值,计算样本的均值x 与标准差s ,并将它们分别描在x 图与s 图上,按上面提到的判断标准去判断生产过程是否处于控制状态.当生产过程无异常时可以继续进行生产,如果发生异常需要及时消除使质量下降的原因.使之不再发生,而对提高质量的有利措施也应及时总结,使之推广.6.5 控制图应随时间和质量的要求不断的修正当控制图使用了一段时间后应根据实际的质量水平,对控制图的中心线和上、下控制线进行修正,使控制水平能够不断提高.其他计数控制图不在做详细介绍,详细介绍可参考相关文献[3]~[8]. 7 不合格品率控制图(p 图)不合格品率控制图用于判断生产过程的不合格品率是否处于或保持在所要要求的水平,记为p 图.制作和使用控制图的一般步骤仍与x s -图类似,这里也要叙述不同之处. 7.1 收集预备数据按事先规定的抽样间隔,抽取k 个样本,这里第一样本的容量可以不完全相同,但要求来讲每个样本至少有一个不合格样品,在这种场合,样本的容量一般比较大,通常在100以上譬如,根据顾客的要求,不合格品率为0.01,那么这个样本的容量至少要100个,甚至更多,因为在100产品可能没有一个不合格品.记录每个样本中不合格品数,将其填在数据表中(见表3),一般要求25k ≥.例[1]2 某电镀件25批产品中的外观质量不合格件数如表3所示,作p 图.序号 i 样本容量i n 不合格数 ()i np 不合格率 (%)p 1 724 48 6.63 2 763 83 10.88 3 748 70 9.36 4 748 85 11.36 5 724 45 6.22 6 727 56 7.70 7 726 48 6.61 8 719 67 9.32 975937 4.8710 745 52 6.98 11 736 47 6.39 12 739 50 6.77 13 723 47 6.50 14 748 57 7.62 15 770 51 6.62 16 756 71 9.39 17 719 53 7.37 18 757 33 4.36 19 760 29 3.82 20 737 49 6.65 21 750 61 8.13 22 752 39 5.19 23 726 50 6.89 24 730 58 7.95 7.2 制作过程控制分析图7.2.1 计算每个样本的不合格品率,以i n 表示第i 个样本的容量,以()i np 表示其中不合格数,由此计算第i 个样本的不合格品率()/,i i i p np n = 1,2,i =…,k例2的每一个样本不合格品率记在表3的最后一列中. 7.2.2 计算k 个样本总不合格率p111(),1,ki i k ii ki i np n p p k ===⎧⎪⎪⎪=⎨⎪⎪⎪⎩∑∑∑样本容量不同时样本容量相同时这便是p 图中心线.在例2中样本容量不同,1()1374ki i np ==∑,118533ki i n ==∑.从而得25样本的总不合格品率p 为1347/185337.27%p ==.7.2.3 计算p 图的上、下界限如果将一个产品中的不合格品数Y 看成随机变量,那它服从二点分布,即(1)P Y p ==,(0)1P Y p ==-则根据中心极限定理[2]可以得出,容量为n 的样本不合格品率近似服从正态分布(,(1)/)N p p p n -,通常p 用p 估计,这样得p 图的中心线及上、下控制界限如下中心线CL p上控制界限UCL 3(1)/i p p p n +-下控制界限LCL 3(1)/i p p p n --其中各i n 最好相同,因为这样的样本容量不同时控制界限将不同.但当样本容量同时满足下列两个不等式时,可以采用近似的控制界限计算公式,即当min max /2,2n n n n ≥≤⨯同时成立时,取近似的控制界限为中心线CL p上控制界限UCL 3(1)/p p p n +-下控制界限LCL 3(1)/p p p n --其中1/ki i n n k ==∑.在例2中p 图的中心线和上、下控制界限可以采用近似计算公式,因为此时有741.32n =,min 719741.32/2n =>,max 7632741.32n =<⨯则得中心线CL 0.072772.7%=上控制界限UCL 0.072730.0727(10.0727)/741.320.101310.13%+⨯-=下控制界限LCL 0.072730.0727(10.0727)/741.320.0441 4.41%-⨯-=7.4 作分析用控制图只要作一个p 图即可,这时纵坐标为p ,横坐标为样本序号,同样用实线表示CL ,用虚线表示上、下控制界限UCL 与LCL .然后把各个样本的i p 的值依次点在p 图上,图中点常用“×”表示,再用直线把相邻的两点连接成折线.例2的p 图见图4.图4 例2的p 图7.5 判断生产过程是否处于统计控制状态判断规则同前.在例2中,从图4可见,第2与第4个样本的i p 值值超过上控制界限,第18与第19个样本的i p 低于下控制界限,说明生产过程未处于统计控制状态.7.6 当生产过程不处于统计控制状态时应采取的措施同前.在例2中,较低的不合格品率对质量是有利的,因此第18第第19两个样本予以保留,第2与第4两个样本有较高的不合格品率,应寻找原因,找出原因后可去掉第2与第4两个样本,重新计算控制图的中心线和上、下控制界限得23k =,1()1179k i i np ==∑,117022ki i n ==∑, 6.93%p =,740.09n =中心线CL 6.93%上控制界限UCL 0.069330.0693(10.0693)/740.090.09739.73%+⨯-=下控制界限LCL 0.069330.0693(10.0693)/740.090.0973 4.13%-⨯-=其p 图见图5,再次检查生产过程已处于统计控制状态.图5 修正后的例2的p 图7.7 判断生产过程是否满足质量的要求在质量特性为不合格品率时,通常规定不合格品率的上限,据此可判断生产过程是否满足质量要求.7.8 作控制用控制图方法同前类似.7.9 对控制线的修正当控制图使用了一段时间后,应根据实际质量水平,对控制图的中心线和上、下控制线进行修正.其他计量控制图不在做详细介绍,详细介绍可参考相关文献[3]~[8].8 结束语本文已经通过方法与例题的结合的方式,对统计过程过程图的种类和如何在不同的情况根据不同的限制选择使用不同的图作出了具体的阐述.不同的情况使用不同的统计过程控制图时,计算的简单和复杂程度也是不一样的,适当的场合选择适当的控制图,可以及时控制生产线,检测是否处于统计控制状态,以及时掌握生产线的信息,对生产及时控制.以避免生产出过多的不合格产品,来减小生产出过多的不合格产品.以达到对生产线进行控制的目的.参考文献[1]周纪芗,茆诗松./质量管理统计方法(第二版)[M].中国统计出版社,2008: 107~124.[2]茆诗松,程依明,濮晓龙.概率论与数理统计(第三版)[M].高等教育出版社,2009:226~237, 315~327.[3]华东师范大学数学系.数学分析 下册(第三版)[M].高等教育出版社,2008: 190~195.[4]罗国勋.质量管理与可靠性[M].高等教育出版社,2005.6: 187~240.[5]王毓芳,肖诗唐.统计过程控制的策划与实施[M].中国统计出版社, 2006.1: 136~240.[6]俞明南,丁正平.质量管理[M].大连理工大学出版社, 2005.4: 183~213 64~107.[7]周纪芗,回归设计[J].上海质量,1996,(11):15~26[8]茆诗松,参数设计[J].上海质量,1995,(10):10~29[9]许守群.超声波换器优化[J]数理统计管理,1996,(12):22~34Applications of Control Chart in Quality ManagementZHANG Shuai(Mathematics & Statistics School, Anyang Normal University, Anyang, Henan 455002)Abstract: This paper respectively introductes the production process and method of use of mean -standard deviation control charts (x s - chart),mean value-range control chart (x R - chart) and percent nonconforming control chart (p chart) and so on. This paper discusses them with appropriate examples in detail.Key word: center line ; control state ; control limits ; qualified ; failure摘 要:本文分别介绍了均值-标准差控制图(x s -图)、均值-极差控制图(x R -图)和不合格品率控制图(p 图)等控制图的制作过程和使用方法.并且配以相应的例题做详细论述.。
质量控制图及其应
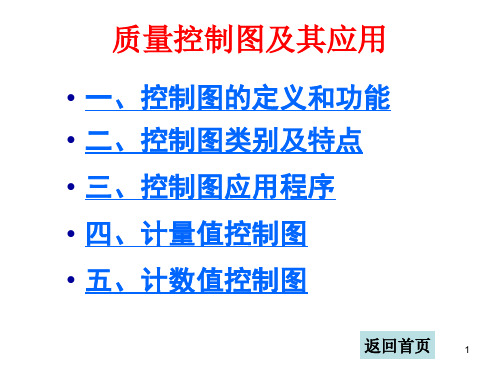
• E( x) n p , ( x) n pq n p(1 p)
• 其控制界限为:
k
ni pi
CL n p i1
k
UCL n p 3 n p n p 3 n p(1 p)
LCL n p 3 n p(1 p)
• 式中 p ——样本不合格品率;
10
0.975 0.308 0.288 1.716 0.223 1.777 0.975 0.36 3.087 0.973 0.797
15
• 典型的 X 控制图,其中 CL X 为控制中心,UCL X 3 为上控制限,LCL X 3 为下控制限。
16
(2) R 图
• 每个组的及的分布也是个连续的分布,但不 是正态分布,而是一个偏态分布。其期望 值 E(R) d2 ;其标准偏差 R d3 。与可 由表10—8查得。
• 于是,其控制界限为:
CL d2 R
UCL D4 R LCL D3 R
• 控制图控制界限计算公式见表10—9。
17
• 注意:
•
在这里,由于 3d3
d2
有时可能大于1,这样LCL就会
出现负值。而极差出现负值就没有意义,此时将
LCL视为零。因此,一般都把“0”线当做及图的
控制下限。但是当样本大小n>6时,极差R就不
CL X
UCL
X
3
X
3
1 d2
Rs
X
E2
Rs
LCL X E2 R s
• 其中,E2 可从表10—8中查到(n=2)。
26
• Rs 图的控制界限为:
《质量统计工具—控制图》PPT课件 44页
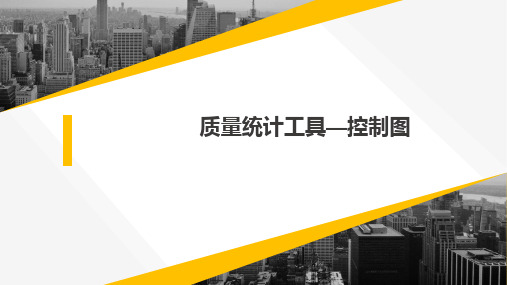
控制图
分门别类
12 3
控制图
基本原理
控制图
常规计量
控制图
制作分析
456
控制图
常规计数
控制图
实战演练
控制图·基本原理
一、控制图的基本原理
实际生产中,影响过程质量的因素有很多。根据其影响大小与作用性质分 类,质量因素大体可分为如下两类:
偶然因素
异常因素
偶然因素又称为随机因素,它具有如下4个特点:
均值偏离正的态正分态布分图布图
μμ -3-σ3σ
++33σσ
UUCCLL
另刚一才种我错们误说方过式,是质质量量特特性性值值分已布偏在离μ已±确3σ定之的外正的态概分率布为,0.但27仍%有。一正部是分因点为落这在0.控27制%限内 的(概如率斜使线得阴控影制)图。有如可果能据出此现判点断位过落程在处控于制统限计以控外制从状而态影,响则判属断于。第这二类错误就“称漏为发警
第1类错误“报虚”发,警出报现”概,率出记现作概β。率记作α。
控制图·分门别类
二、控制图的分类
控制图的种类
12、按控标制准图值应(用标目准的值的即不给同定划的分要求或目标值)是否给定划分 (1)(标1准)值分给析定用的控控制制图图 这种分控制析图用的控目制的图是在为样了本分量析相考同察的过情程况是下否,处确于定统若计干控样制本状的态均,值并、且标可准得差出的CL质、量UC特L性、与LC对L数应的 据标,准为值控之制差用是控否制 显图著提大供于原正始常数质据量。波动的差异。 (2)(标2准)值控未制定用的控控制制图图 这则控制图用的控目制的图是发为现了控制图后上续所的控过制程的。特在性实本际身使有用没时有,明当显分波析动用。控这制种图图表完明全过依程靠无测系量统样因本素, 起只作用用来,发且现过异程常的 因过素程造能成力的满误足差质。量要求时,可以将控制线延伸作为控制用控制图。
质量管理工具“控制图”详解
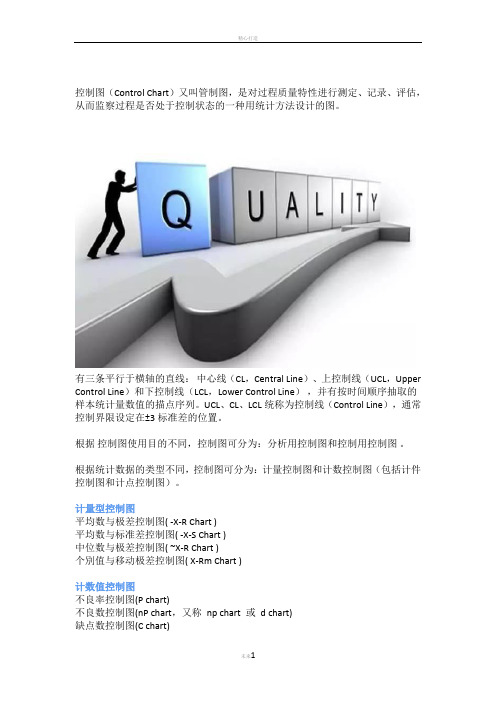
控制图(Control Chart)又叫管制图,是对过程质量特性进行测定、记录、评估,从而监察过程是否处于控制状态的一种用统计方法设计的图。
有三条平行于横轴的直线:中心线(CL,Central Line)、上控制线(UCL,Upper Control Line)和下控制线(LCL,Lower Control Line),并有按时间顺序抽取的样本统计量数值的描点序列。
UCL、CL、LCL统称为控制线(Control Line),通常控制界限设定在±3标准差的位置。
根据控制图使用目的不同,控制图可分为:分析用控制图和控制用控制图。
根据统计数据的类型不同,控制图可分为:计量控制图和计数控制图(包括计件控制图和计点控制图)。
计量型控制图平均数与极差控制图( -X-R Chart )平均数与标准差控制图( -X-S Chart )中位数与极差控制图( ~X-R Chart )个別值与移动极差控制图( X-Rm Chart )计数值控制图不良率控制图(P chart)不良数控制图(nP chart,又称np chart 或d chart)缺点数控制图(C chart)单位缺点数控制图(U chart) 控制图种类及应用场合控制图的分析与判定应用控制图的目的,就是要及时发现过程中出现的异常,判断异常的原则就是出现了“小概率事件”,为此,判断的准则有两类。
第一类:点子越出界限的概率为0.27% 。
准则1属于第一类。
第二类:点子虽在控制界限内,但是排列的形状有缺陷。
准则2-8属于第二类。
控制图八大判异准则(口诀)2/3A (连续3点中有2点在中心线同一侧的B区外<即A区内>)4/5C (连续5点中有4点在中心线同一侧的C区以外)6连串(连续6点递增或递减,即连成一串)8缺C (连续8点在中心线两侧,但没有一点在C区中)9单侧(连续9点落在中心线同一侧)14交替(连续14点相邻点上下交替)15全C (连续15点在C区中心线上下,即全部在C区内1界外(1点落在A区以外)▶ 2/3A (连续3点中有2点在中心线同一侧的B区外<即A区内>)判读:1、控制过严;2、材料品质有差异;3、检验设备或方法之大不相同;4、不同制程之资料绘于同一控制图上;5、不同品质材料混合使用。
质量管理的统计方法--控制图

质量管理的统计方法--控制图控制图是用于确定生产或工作过程是否处于稳定状态的图形,通过它可以发现并及时消除生产和工作过程中的失控情况。
控制图是通过对过程中各特性值进行测定、记录、评估和监察过程是否处于控制状态的一种用统计方法设计的图。
在控制图中有两条平行的上下控制界限和中心线,并有按时间序列排列的样本统计量数值的描点序列。
如果控制图中描点落在控制界限之内,则表明过程正常;若控制图中描点落在控制界限之外或描点序列在界限之间有某一种或几种不正常的趋势,则表明过程异常。
(一)控制图的分类控制图可以分为两类,即计量值控制图和计数值控制图。
计量值控制图所依据的数据均属于由测量工具实际测量出来的数据,如长度、重量等控制特性,具有连续性,它包括:①单值控制图;②平均值与极差控制图;③平均值与标准差控制图;④中位值与极差控制图;⑤个别值与移动极差控制图。
计数值控制图所依据的数据均属于以单位个数或次数计算,如不合格品数、不合格品率等。
它包括:①不合格品数控制图;②不合格品率控制图;③缺陷数控制图;④单位缺陷数控制图。
(二)控制图的应用控制图可用于以下几方面:①预测,通过现有图形的分析和研究可大致预测下一步可能的位置。
②评价与诊断,可以评价过程的变化情况,评估过程的稳定性,并能与其他方法结合,可以找到产生状况的原因。
③控制,可对品质状况及时掌控,决定何时需要调整,何时需要保持原有状态。
④确认,比较后确认某一过程的改进。
[例题8] 控制图可用于()A. 预测,通过现有图形的分析和研究可大致预测下一步可能的位置B. 评价与诊断,可以评价过程的变化情况,可以找到产生状况的原因C. 可以显示波动的状况D. 控制,可对品质状况及时掌控,决定何时需要调整,何时需要保持原有状态1E. 确认,比较后确认某一过程的改进答案:ABDE(三)控制图的作法(1)选择控制特性。
(2)选择合适的控制图。
(3)选取一定数量的数据,在生产过程中,定期抽取试样。
质量管理“控制图”应用详解(干货)

质量管理“控制图”应用详解(干货)导读: 控制图(Control Chart)又叫管制图,是针对过程质量特性进行测定、记录、评估,从而监察过程是否处于控制状态的一种用统计方法设计的图。
有三条平行于横轴的直线:中心线(CL,Central Line)、上控制线(UCL,Upper Control Line)和下控制线(LCL,Lower Control Line),并有按时间顺序抽取的样本统计量数值的描点序列。
UCL、CL、LCL统称为控制线(Control Line),通常控制界限设定在±3标准差的位置。
根据控制图使用目的不同,控制图可分为:分析用控制图和控制用控制图。
根据统计数据的类型不同,控制图可分为:计量控制图和计数控制图(包括计件控制图和计点控制图)。
· 计量型控制图平均数与极差控制图( -X-R Chart )平均数与标准差控制图( -X-S Chart )中位数与极差控制图( ~X-R Chart )个別值与移动极差控制图( X-Rm Chart )· 计数值控制图不良率控制图(P chart)不良数控制图(nP chart,又称 np chart 或 d chart)缺点数控制图(C chart)单位缺点数控制图(U chart)一、控制图种类及应用场合二、控制图的分析与判定应用控制图的目的,就是要及时发现过程中出现的异常,判断异常的原则就是出现了“小概率事件”,为此,判断的准则有两类。
第一类:点子越出界限的概率为0.27% 。
准则1属于第一类。
第二类:点子虽在控制界限内,但是排列的形状有缺陷。
准则2-8属于第二类。
控制图八大判异准则(口诀)2/3A--连续3点有2点在中心线同一侧的B区外<即A区内>4/5C--连续5点中有4点在中心线同一侧的C区以外6连串--连续6点递增或递减,即连成一串8缺C--连续8点在中心线两侧,但没有一点在C区中9单侧--连续9点落在中心线同一侧14交替--连续14点相邻点上下交替15全C --连续15点在C区中心线上下,即全部在C区内1界外--1点落在A区以外012/3A (连续3点中有2点在中心线同一侧的B区外<即A区内>)判读:1、控制过严;2、材料品质有差异;3、检验设备或方法之大不相同;4、不同制程之资料绘于同一控制图上;5、不同品质材料混合使用。
质量控制图的方法
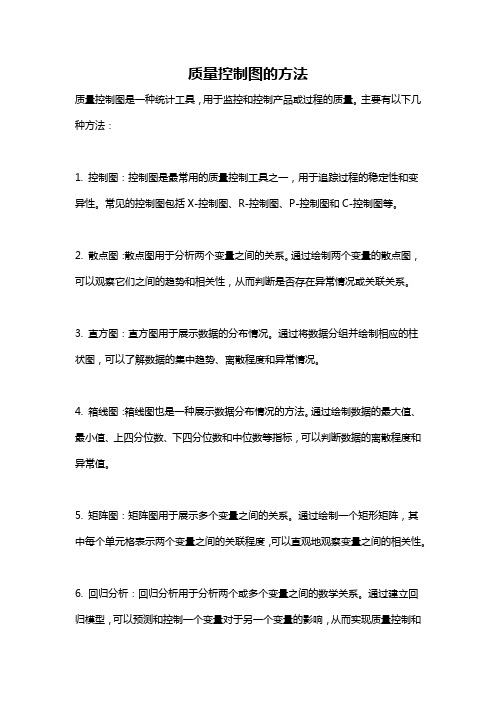
质量控制图的方法
质量控制图是一种统计工具,用于监控和控制产品或过程的质量。
主要有以下几种方法:
1. 控制图:控制图是最常用的质量控制工具之一,用于追踪过程的稳定性和变异性。
常见的控制图包括X-控制图、R-控制图、P-控制图和C-控制图等。
2. 散点图:散点图用于分析两个变量之间的关系。
通过绘制两个变量的散点图,可以观察它们之间的趋势和相关性,从而判断是否存在异常情况或关联关系。
3. 直方图:直方图用于展示数据的分布情况。
通过将数据分组并绘制相应的柱状图,可以了解数据的集中趋势、离散程度和异常情况。
4. 箱线图:箱线图也是一种展示数据分布情况的方法。
通过绘制数据的最大值、最小值、上四分位数、下四分位数和中位数等指标,可以判断数据的离散程度和异常值。
5. 矩阵图:矩阵图用于展示多个变量之间的关系。
通过绘制一个矩形矩阵,其中每个单元格表示两个变量之间的关联程度,可以直观地观察变量之间的相关性。
6. 回归分析:回归分析用于分析两个或多个变量之间的数学关系。
通过建立回归模型,可以预测和控制一个变量对于另一个变量的影响,从而实现质量控制和
优化。
以上方法都是常用的质量控制图方法,根据具体情况选择合适的方法进行质量控制。
QC七大手法培训资料

03
改进措施执行不到位
即便通过散布图分析确定了问题所在, 若后续的改进措施执行不力或监督不到 位,也难以达到预期的改进效果。因此 ,确保每项措施都被有效实施并定期评 估其成效至关重要。
分析方法选择不当
散布图的分析过程中,选择合适的统计 方法和解读图表是关键。错误的方法选 择可能导致误导性的结论,因此必须根 据数据特性和研究目的精心选择分析技 术。
历史背景与发展
01 QC七大手法的起源
QC七大手法起源于日本,由质量管理专家石川馨在20世纪50年 代提出,旨在通过系统化的分析工具,解决生产过程中的质量问 题,提升生产效率与产品质量。
02 发展历程与演变 03 国际影响与推广
自QC七大手法诞生以来,随着科技的进步和管理理念的更新, 这些手法经历了不断的完善与发展,逐渐形成了一套完整的质量 管理工具体系,广泛应用于各行各业。
数据的可视化呈现
将复杂的数据以图表或图形的形式直观展现,可以 大大提高信息的可理解性和传达效率。数据可视化 不仅能够帮助我们快速捕捉关键信息,还能促进团 队间的沟通与协作。
案例分享
01
02
03
调查表法在制造业的 应用
通过一个具体案例,展示如何运 用调查表法对生产线上的问题进 行系统分析和数据收集,进而发 现生产过程中的瓶颈和改进点, 有效提升生产效率和产品质量。
相关性评估
利用散布图可以直观地评估两个变量之间的相关性强度,即它们是否同向 变化或反向变化,以及变化的一致性如何,这对于理解变量间的内在联系 非常有帮助。
典型问题与改进措施
01
数据关联性不明确
在应用散布图时,经常遇到数据间关联 性不明显的问题。这通常是由于数据采 集的样本量不足或者数据本身的变异过 大所导致,进而影响了对问题根源的判 断和分析。
- 1、下载文档前请自行甄别文档内容的完整性,平台不提供额外的编辑、内容补充、找答案等附加服务。
- 2、"仅部分预览"的文档,不可在线预览部分如存在完整性等问题,可反馈申请退款(可完整预览的文档不适用该条件!)。
- 3、如文档侵犯您的权益,请联系客服反馈,我们会尽快为您处理(人工客服工作时间:9:00-18:30)。
控制图的由来
•控制图的发展:
20世纪40年代,美国 贝尔电话公司应用统计质量 控制技术取得成效;美国军 方在军需物资供应商中推进 统计质量控制技术的应用; 美国军方制定了战时标准 Z1.1《质量控制指南》、 Z1.2《数据分析用的控制图 法》、 Z1.3《生产中质量管 理用的控制图法》。
图名称 np图 p图 c图
u图
步骤 计算平均不合格 品率 p
计算各组不合格 品率pi
计算各样本的平
均缺陷数 c
计算各样本的单 位缺陷数ui
计算公式
k
p np
npi
np i1
n
k
备注
(np)i——第i样本的 不合格品数(各样本 样本容量皆为n)
pi
npi
ni
ni——第i样本的样本 容量(各样本样本容
控制对象-质量波动(续)
•随机因素:
始终存在,对质量影 响微小且方向各异,难以 消除的因素;由随机因素 造成的质量波动是正常的 波动,近似正态分布;允 许波动的范围往往以公差 反映,此时的工序处于稳 定状态或受控状态。
机电学院 材料检测及质量管理教研部
控制对象-质量波动(续)
•系统因素:
有时存在,对质量影响 很大,不难消除,是可以避 免的;系统因素造成较大的 质量波动,常常超出了规格 范围或存在超过规格范围的 危险,称作异常波动,此时 生产过程处于非控制状态(或 称非稳定状态)。
质量波动的来源主要有五个方面(简称 5M1E ):
• 操作人员(Man)——人 • 设备(Machine) —— 机 • 原材料(Material)——料 • 操作方法(Method)——法 • 环境(Environment)——环 • 测量(Measurement) ——测
机电学院 材料检测及质量管理教研部
机电学院 材料检测及质量管理教研部
控制图的类型-按用途
一、分析用控制图:
– 过程是否处于统计控制状态--(统计稳态); – 该过程的过程能力指数是否满足要求--(技术
稳态)
二、控制用控制图:
– 当判断工序处于稳定状态后,用于控制工序用 的控制图。
当过程达到了我们所确定的状态后,才能将这 时的控制图的控制线延长作为控制用控制图。
7.与规格比较,确定控制用控制图
•由分析用控制图得知工序处于稳定状态后,还须与规格要求 进行比较。若工序既满足稳定要求,又满足规格要求,则称 工序进入正常状态。 •此时,可将分析用控制图的控制线作为控制用控制图的控制 线;若不能满足规格要求,必须对工序进行调整,直至得到 正常状态下的控制图。
–所谓满足规格要求,并不是指上、下控制线必须在规格上、下限内侧,
6. 判断工序状态是否处于稳定状态
工序质量特性值分布的变化是通过控制图上点子 的分布体现出来的,因此工序是否处于稳定状态要 依据点子的位置和排列来判断。
若判断工序状态不稳定,应查明原因,消除不稳 定因素,重新收集预备数据,直至得到稳定状态下 分析用控制图。
机电学院 材料检测及质量管理教研部
控制图的绘制(续)
控制图的绘制(续)
4.(1)控制图样本参数的计算:
图名称
步骤
(1)计算各样本平
X R图 均值 xi
(2)计算各样本极 差Ri
(1)找出或计算出 X~ R图 各样本的中位数 X~i
(2)计算各样本极 差Ri
计算公式
备注
xi
1 n
n
xij
j 1
Ri max xij min xij
xij——第I样本中的第j个数据 i= 1,2…k;
j=1,2…n;
max(xij)——第i样本中最大值; min(xij)——第i样本中最大值。
~x j
x i
n
1
n为奇数
n为奇数时,第i样本中按大
2
小顺序排列起的数据列中间
~xi
1 2
x i
n 2
x i
n1 2
即UCL>TU;LCL< TL。而是要看受控工序的工序能力是否满足给定 的Cp值要求。
机电学院 材料检测及质量管理教研部
第2节 计量值控制图
机电学院 材料检测及质量管理教研部
计量值控制图的应用
控制图的绘制(续)
控制图上下限计算所需系数:
机电学院 材料检测及质量管理教研部
控制图的类型-按数据类型(续)
几种分布的数学期望和方差
机电学院 材料检测及质量管理教研部
控制图的绘制(续)
类型
X R X~ R
I Rs
p np c u
CL
UCL
LCL
各
x
x A2R
x A2R
控制图的两类错误
•第一类错误:
LCL
CL
当工序正常时,
点子仍有落在控制
界限外面的可能,
此时会发生将正常
波动判断为非正常
波 动的错误——误
发信号的错误,控
α/2
制图犯第一类错误
的概率记为α。
0 k
0
UCL
α/2
0 k x
机电学院 材料检测及质量管理教研部
控制图的两类错误(续)
R的期望值 E(R) d2 R的标准偏差 D(R) d3
x图的控制界限 UCL E(x) 3 D(x) 3 LCL E(x) 3 D(x) 3
CL x
n
x
3 R d2
n
x
A2 R
n
x
3 R d2
n
x
A2 R
机电学院 材料检测及质量管理教研部
的方法是间隔随机抽样。为能反映工序总体状况,数据应在10~15天内
收集 ,并应详细地记录在事先准备好的调查表内。数据收集的个数参见
下表。
控制图的样本与样本容量
控制图名称
XX~
R R
图 图
xs 图
I—Rs图
np图、 p 图
C图、U图
样本数k 一般k=20~25
样本容量n 一般3~6
备注
X~图的样本容
控制图的实质就是区分系统因素与随机因素 的,控制限就是区分正常波动与异常波动的科学 界限。
机电学院 材料检测及质量管理教研部
3σ准则
t
k
k
机电学院 材料检测及质量管理教研部
小概率原理
• 所谓小概率原理,即认为小概率事件一般是 不会发生的。
反证法思想
机电学院 材料检测及质量管理教研部
c 3 c
限
u
u 3
u n
u 3
u n
机电学院 材料检测及质量管理教研部
控制图的绘制(续)
5.绘出分析用控制图
(1)在坐标图上画出三条控制 线,控制中线一般以细实线 表示,控制上下线以虚线表 示; (2)将各样本的参数值在控 制图中打点;
机电学院 材料检测及质量管理教研部
控制图的绘制(续)
量可以不等)
k
ci
c i1 k
ui
ci ni
ci——第i样本的缺陷 数(各样本样本容量 相等)
各样本样本容量不等
机电学院 材料检测及质量管理教研部
控制图的绘制(续)
4.(2)控制界限的计算( 以 x R控制图为例):
x的期望值 E(x) x的标准偏差 Dx
n
量常取3或5
K=20~30 一般k=20~25
1
1/p~5/p
尽可能使样本中缺陷 数C=1~5
机电学院 材料检测及质量管理教研部
控制图的绘制(续)
4.计算控制界限
各种控制图控制界限的计算方法及计算公 式不同,但其计算步骤一般为:
(1)计算各样本参数 (2)计算分析用控制图控制线
机电学院 材料检测及质量管理教研部
R
D4 R
D3 R
类 控
~x
~x m3 A2R ~x m3 A2R
制
R
D4 R
D3 R
图
x
x 2.66 Rs
x 2.66 Rs
的
Rs
D4 Rs
D3 Rs
控
p
np
p3
p(1 p) n
np 3 np(1 p)
p3
p(1 p) n
np 3 np(1 p)
制 界
c
c 3 c
3 t
3
t
机电学院 材料检测及质量管理教研部
什么是控制图
x(或x、R、S等)
控制上线UCL
控
制 控制中线CL 图
的 控制下线LCL
0 1 2 3 4 5 6 7 8 9 10 11 12 13 14 15 16 17 18
样本号(或时间)
结 构
1.以质量特性值或其统计量为纵坐标,以随时间推移而变动着的
X~ R X R
x s I Rs np
p
c
u
控
控
控控 控
控
控
控
制
制
制制 制
制
制
制
图
图
图图 图
图
图
图
机电学院 材料检测及质量管理教研部
控制图的绘制
1确定受控质量特性 2选定控制图种类
机电学院 材料检测及质量管理教研部
控制图的绘制(续)
3. 收集预备数据
收集预备数据的目的只为作分析用控制图以判断工序状态。数据采集