副产蒸汽氯化氢合成炉系统技术方案
一种氯化氢合成炉副产蒸汽装置[发明专利]
![一种氯化氢合成炉副产蒸汽装置[发明专利]](https://img.taocdn.com/s3/m/475482334531b90d6c85ec3a87c24028915f8520.png)
专利名称:一种氯化氢合成炉副产蒸汽装置专利类型:发明专利
发明人:刘红军,邱素芹,宋丹,党传刚
申请号:CN202210568669.5
申请日:20220524
公开号:CN114673980A
公开日:
20220628
专利内容由知识产权出版社提供
摘要:本发明适用于化工设备领域,提供了一种氯化氢合成炉副产蒸汽装置,包括具有从下到上依次设置的燃烧段、蒸发段和冷却段;蒸发段上设置有夹套,夹套的顶部通过蒸汽连通管与汽包相连,夹套的一侧壁上还设置有与所述夹套相通的供水机构;供水机构包括固定设置在夹套一侧外壁上的软水供给箱,所述软水供给箱顶部与汽包之间通过第一导管相通;软水供给箱与软水罐之间通过循环管相连,循环管上具有流速控制阀。
本发明可通过流动腔内的水进行临时补充至供水腔内,来维系该副产蒸汽装置使用更久;而且本发明还可以实时根据供水腔内的水位高度,自动调整流速控制阀的流速大小,自动调节流动腔向供水腔内溢出供水的速率。
申请人:东营市赫邦化工有限公司
地址:257000 山东省东营市东营港经济开发区东港路以西、港北一路以北
国籍:CN
代理机构:北京卓特专利代理事务所(普通合伙)
代理人:段宇
更多信息请下载全文后查看。
副产蒸汽氯化氢合成炉系统技术方案

专业资料山东东营拓宇化工技术有限公司副产蒸汽HCL合成炉系统方案设计江苏苏宇化工设备有限公司2014-2-16目录一、项目要求及报价二、副产蒸汽氯化氢合成炉行业发展情况1、氯化氢合成系统副产中低压蒸汽基本原理2、国内氯化氢合成炉副产蒸汽现状及特点3、新型副产蒸汽氯化氢合成炉的特点三、副产蒸汽氯化氢合成炉主要设备及工艺流程Ⅰ、合成炉主要设备1、副产蒸汽氯化氢合成炉主体2、汽包3、预热器Ⅲ、副产蒸汽氯化氢合成炉系统工艺流程:1、氯化氢合成及冷却流程。
2、副产蒸汽流程。
3、循环水流程。
四、自动控制系统1、自动点火系统2、自动联锁保护系统3、氢气、氯气自动配比控制4、汽包部分的自动控制五、节能减排及经济效益以及安全分析六、主要性能指标七、副产蒸汽HCL合成炉主要设备。
1、副产蒸汽HCL合成炉系统主要设备一览表2、提供的备品备件及易耗品包括灯头、防爆膜、四氟密封材料等一、项目要求及报价根据贵公司的要求:按合成炉每天产60吨HCl的采购条件,要求设计副产蒸汽的HCL合成炉,其副产蒸汽压力达到0.4-1.4MPa。
装置操作操作弹性为:50%~110%;装置操作时间:8000小时/年。
副产蒸汽氯化氢合成炉系统单套含税价228万元(详见副产蒸汽HCL合成炉系统主要设备一览表)。
二、副产蒸汽氯化氢合成炉行业发展情况1、氯化氢合成系统副产中低压蒸汽基本原理氯气与氢气反应生成氯化氢时伴随释放出大量反应热:0.5H2十0.5Cl2=HCL+22.063Kca1/mol,即每合成1千克气态氯化氢放出605.11 Kcal热量。
氯气与氢气在合成炉内以燃烧形式反应生成氯化氢,火焰中心区温度达到2500℃以上,生成的氯化氢气体温度在2000℃以上,这些热量相当可观,完全可以用来副产蒸汽。
2、国内氯化氢合成炉副产蒸汽现状及特点对于氯化氢合成中的热能利用,国内经历了以下阶段。
第一代是使用钢制水夹套氯化氢合成炉副产热水。
这种钢合成炉在炉顶部和底部容易受腐蚀,使用寿命短,副产的热水应用范围有限,目前已经基本被淘汰。
副产低压蒸汽氯化氢石墨合成炉开车方案(自动点火)

副产低压蒸汽二、三合一氯化氢石墨合成炉开车方案(自动点火工艺)南通星球石墨设备有限公司开车前的准备工作一、设备、管道安装工艺确认。
(已确认)二、工艺设备、管道清洗及吹扫。
(已吹扫)三、合成炉夹套进水试压、试漏。
(已完成)四、控制程序、仪表、阀门现场调试确认。
(已完成)五、氯气、氢气及辅助管道试压、试漏。
(已完成)六、合成系统(炉内、连接管道)气密性试漏。
(已完成)七、岗位操作人员工艺培训。
(已完成)开车准备工作一、按照操作规程进行进行各项准备、检查工作。
循环水、锅炉给水、原料气纯度、连锁试验、炉内真空度等。
二、具备开车条件后,拆下炉内点火枪放置在炉外,按点火枪的点火程序点火。
调整点火枪的氢气、空气流量,保证火焰的长度符合条件,然后关闭点火枪,将点火枪装入炉内。
(注:第一次开车的要求)正常开车1、解除该合成炉的所有连锁。
2、在班长指挥下方可进行开车。
3、现场点火人员打开炉前氮气手动阀,关闭炉门,通知DCS控制人员准备点火;确认后启动燃烧器吹扫程序,吹扫(10~15分钟)完成并分析合成炉内含氢是否合格后。
4、打开合成炉空气补充口(炉门),空气置换5~10分钟;DCS控制人员确认后启动点火枪点火程序,观察炉内是否有小火,并确认火焰长度。
5、确认后,缓慢打开氢气手动阀,DCS操作人员远传手动开氢气连锁安全阀、点小火阀,观察炉内是否点着。
6、确认燃烧器点着后,缓慢打开氯气手动阀,DCS操作人员远传手动开氯气连锁安全阀、点小火阀,观察炉内火焰颜色及大小。
确认正常后,关闭炉前空气补充阀(炉门)。
7、DCS控制人员逐步远程手动缓慢开启氢气、氯气调节阀,观察炉内火焰是否正常,按照操作规程要求逐步加大氯、氢流量。
8、合成炉点着后,关闭点火枪,闪蒸罐随过热水温度的上升液位缓慢上升,至70%时,必需手动打开闪蒸罐底部排污阀,将液位降至40%左右。
热水温度升至100度以上时,有蒸汽产出。
9、点炉正常后,将部分连锁投入。
建议:火焰探测器、循环水连锁在正常运行一周后投入。
新型副产中压蒸汽全石墨氯化氢合成炉的研发与应用

TO1 - CORROSI AL ON NTROL CO
VO 26 NO。 L_ 5 MA 2 2 01
生产 实践
Pr oduc i ton Pr tce ac i
圈 圆
灯 头 为 株 洲 产石 英 玻 璃 ,采 用 两 套 式 梅 花 孔 蒸 汽 合成炉基 础上研 发的 第四代 产品 ,结构合 理 , 石 英灯管 ( 鉴 国外先进 技术 ,星球 专利 ),氢气 有 国家 专 利 。 目前 国 内运 行 的 国 产 的副 产 蒸 汽 在 借
2 工艺控制简便 ,实现自动控制 , 操作方便
本 系统 主 要 设 备 :副 产 中 压 蒸汽 二 合 一 氯 化
氢 石墨合 成炉 ( 包括 副产 中压蒸汽 三合一盐 酸合成
12 耐 高温 .
该 炉采用进 口配方改性树脂浸渍 ,经过6 个小时 0
高温、高压下碳化 处理 ,增加 了树脂的耐温性能 ,缩 炉 )、蒸汽 闪发罐 。 工 艺流程 简述 :由氢气处 理工序 来的氢 气经氢 小 了石墨与树脂两 种不 同物体的膨胀系数 ,消除了在
仪 表 控 制 部 分 根 据 用 户要 求 ,可 以 全 自动控
制 ,也可以手动操作 。 工艺流程见 图1 。
3经济效益与社会效益
每合 成 l g 态氯化 氢放 出约6 5 cl k气 0 k a热量 ,相
当于00 6 k 标 准 煤热值 ,能 回收7 %的 热能副 产 .8 5 g 0
小于4 度 。 5
在灯头上燃烧 ,生成 的HC 气体从石 墨合成 炉顶部 经 1 冷却器冷却至 常温后进氯化氢分配台,经 自动阀控制
送下游产 品使用或去吸收系统生产盐酸 。
氯化 氢合成 热大部 分被夹 套锅炉 给水吸 收产生
副产蒸汽氯化氢合成炉运行探讨

Ru nn i n g o f h y dr o g e n c hl o r i de s y nt he s i s f u r n a c e wi t h by - pr o duc t s t e a m
ZHANG Xi o n gt a n g, LI U Y a n' a n, WANG Gu i z h e n
产生 9 2 k J热量 ) 被 系 统 的循环 水 带 走 , 既 浪费 了热
( 3 ) 合成炉的燃烧 区在合成炉的下部 , 为低温 区, 配置有点火 口、 视镜 ; 而高温 区在合成炉的中部 , 高温区用纯水 , 解决了用循环水冷却时结垢 的问题 。 ( 4 ) 采用两层套筒式石英灯头 , 充分燃 烧 , 点火
中 间为纯水 , 石 墨炉 内为 HC 1 。
1 0 万t / a ) , 2 0 0 4年 1 1 月投产 。由于均为敞开式合 成炉 , 且冷却水采用的循环水水质较差 , 结垢较为严
重, 影 响 了合 成炉 的传 热效 果 , 合成 炉 高温 区过 度受
热, 频繁损坏 , 造成检修频率高 、 检修费用高 ; 氢气和 氯气 的化学反应热… ( 每生产 1 m o l 氯化氢气体约
Ab s t r a c t :Th e s t r uc t u r e,c h a r a c t e r i s t i c s a n d t e c h n o l o g i c a l pr o c e s s o f h y dr o g e n c hl o id r e s y nt he s i s f u r — n a c e wi t h b y - p r o d uc t s t e a m a r e i n t r o d u c e d . Th e ma t t e r s n e e d i n g a t t e n t i o n o n s a f e o p e r a t i o n a r e s umma — r i z e d.T he e c o n o mi c b e n e it f s br o u g ht by he t s y n he t s i s f u r n a c e a r e a n a l y z e d.
副产蒸汽氯化氢合成炉运行研究
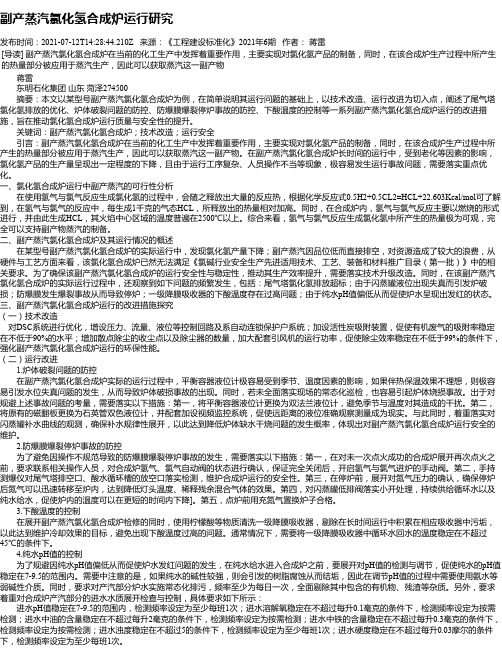
副产蒸汽氯化氢合成炉运行研究发布时间:2021-07-12T14:28:44.210Z 来源:《工程建设标准化》2021年6期作者:蒋雷[导读] 副产蒸汽氯化氢合成炉在当前的化工生产中发挥着重要作用,主要实现对氯化氢产品的制备,同时,在该合成炉生产过程中所产生的热量部分被应用于蒸汽生产,因此可以获取蒸汽这一副产物蒋雷东明石化集团山东菏泽274500摘要:本文以某型号副产蒸汽氯化氢合成炉为例,在简单说明其运行问题的基础上,以技术改造、运行改进为切入点,阐述了尾气塔氯化氢排放的优化、炉体破裂问题的防控、防爆膜爆裂停炉事故的防控、下酸温度的控制等一系列副产蒸汽氯化氢合成炉运行的改进措施,旨在推动氯化氢合成炉运行质量与安全性的提升。
关键词:副产蒸汽氯化氢合成炉;技术改造;运行安全引言:副产蒸汽氯化氢合成炉在当前的化工生产中发挥着重要作用,主要实现对氯化氢产品的制备,同时,在该合成炉生产过程中所产生的热量部分被应用于蒸汽生产,因此可以获取蒸汽这一副产物。
在副产蒸汽氯化氢合成炉长时间的运行中,受到老化等因素的影响,氯化氢产品的生产量呈现出一定程度的下降,且由于运行工序复杂、人员操作不当等现象,极容易发生运行事故问题,需要落实重点优化。
一、氯化氢合成炉运行中副产蒸汽的可行性分析在使用氢气与氯气反应生成氯化氢的过程中,会随之释放出大量的反应热,根据化学反应式0.5H2+0.5CL2=HCL+22.603Kcal/mol可了解到,在氢气与氯气的反应中,每生成1千克的气态HCL,所释放出的热量相对加高。
同时,在合成炉内,氢气与氯气反应主要以燃烧的形式进行,并由此生成HCL,其火焰中心区域的温度普遍在2500℃以上。
综合来看,氢气与氯气反应生成氯化氢中所产生的热量极为可观,完全可以支持副产物蒸汽的制备。
二、副产蒸汽氯化氢合成炉及其运行情况的概述在某型号副产蒸汽氯化氢合成炉的实际运行中,发现氯化氢产量下降;副产蒸汽因品位低而直接排空,对资源造成了较大的浪费,从硬件与工艺方面来看,该氯化氢合成炉已然无法满足《氯碱行业安全生产先进适用技术、工艺、装备和材料推广目录(第一批)》中的相关要求。
副产0.20MPa蒸汽氯化氢合成炉运行总结—金泰氯碱
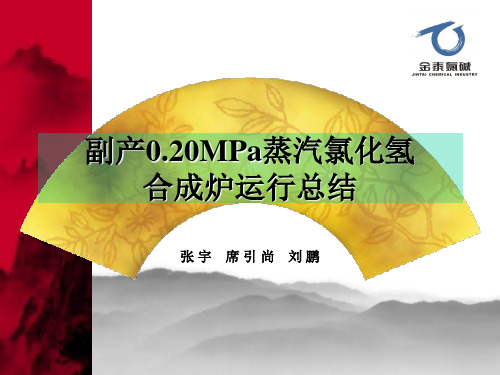
氯化氢(t) 蒸汽(t)
实际累计数据:
氯化氢 40,831 t
蒸汽
30,309 t
实际合成每吨氯化氢的产汽量为: 30309/40831=0.74 t/t
理论合成每吨氯化氢的产汽量为: 44700/50000=0.89 t/t
产率为: 0.74/0.89=83%
四
利用合成炉副产的蒸汽
反
卤水和盐水的加热
每摩尔HCl的合成反应热
92.048 kJ
每小时产生的反应热 12,609,315 kJ/h
氯化氢带出的热量
902,250 kJ/h
蒸汽带走的热量(不考虑热损失)
11,707,065 kJ/h
理论产汽量
4.47t/h
三
表:2006年合成炉运行数据
8000
运
6000
行
数
4000
据
2000
分
0
析
5月 6月 7月 8月 9月 10月 11月 12月
应
热
冬季的取暖
的
二期时计划采用低压蒸汽制冷机组
利
进行液氯冷冻及聚合的软水升温
用
低压蒸汽年产值
216万元
五
循环水费用年节约 纯水补充年花费
22.38万元 24万元
经
经济效益计算
济
216+22.38-24=214.38万元/年
效
益
工艺安装总造价约320万元
约1.49年就可收回合成炉全部投资
一 设计
二 装置介绍
三 运行数据分析
目
四 反应热的利用
录
五 经济效益
六 运行效果
七 改进建议
八 技术进展
氯化氢合成炉工作原理

氯化氢合成炉工作原理1.催化剂床:氯化氢合成炉内通常使用催化剂来催化反应。
催化剂能够提高反应速率,降低反应温度,并提高选择性。
常见的催化剂包括氯化铁、氯化铜和活性炭等。
2.加热系统:合成炉内需要维持一定的反应温度。
加热系统通常采用燃料燃烧产生的高温烟气,通过换热器将烟气的热量传递给反应器中的催化剂床,使其达到所需的反应温度。
燃烧产生的烟气通常含有大量的氮气,可以起到稀释反应物、调节反应温度的作用。
3.控制系统:合成炉内氯化氢的产量和质量需要严格控制,因此通常需要采用先进的自动控制系统。
控制系统可以实时监测和调整反应压力、温度、进料比例等参数,以保证合成炉的稳定运行和高产出。
4.反应器:氯化氢合成炉的反应器通常采用垂直管状结构。
反应器内部装有催化剂床,催化剂床通过与流动的氢气和氯气接触,催化产生氯化氢。
由于反应为放热反应,反应器内需要设置合适的冷却方案,将反应产生的热量迅速带走,以防止过热。
在氯化氢合成过程中,还需要考虑以下几个因素:1.反应温度:合成炉内的反应温度对于反应速率和产物质量有着重要影响。
一般来说,较高的反应温度能够提高反应速率,但过高的温度可能导致副反应的发生。
因此,需要选取适当的反应温度。
2.反应压力:反应压力是控制氯化氢产量的重要因素。
较高的反应压力可以提高气相组分的浓度,从而促进氯化氢的生成。
但过高的压力会增加设备投资和运行成本,需要在经济性和实际操作能力之间做出取舍。
3.催化剂选择:合适的催化剂选择可以显著提高氯化氢合成反应的效率和选择性。
常用的催化剂如氯化铁、氯化铜等都具有良好的催化活性。
正确的催化剂选择可以提高反应转化率和氯化氢纯度。
总之,氯化氢合成炉的工作原理是通过催化剂将氢气和氯气直接反应生成氯化氢。
合成炉通过加热系统和控制系统来维持反应所需的温度和压力,以及实现自动化的操作控制。
正确的参数控制和催化剂选择可以提高氯化氢的产量和质量。
氯化氢石墨副产蒸汽合成炉的应用与出现的问题

氯化氢石墨副产蒸汽合成炉的应用与出现的问题介绍了氯化氢二合一副产蒸汽合成炉装置的生产工艺,运行中出现的一些问题和解决方法。
根据装置的实际运行情况表明,氯化氢副产蒸汽合成炉具有明显的经济效益和社会效益。
标签:副产蒸汽;氯化氢石墨合成炉;利用能源我公司从1986年引进第一套一万吨/年产离子膜烧碱开始,氯化氢工段的合成炉经历了普通不带夹套冷却器的碳钢合成炉、带夹套冷却器的碳钢合成炉以及带冷却夹套的石墨合成炉过程。
单台带夹套碳钢合成炉生产能力比较低,在合成炉内氯气和氢气的燃烧时,反应热传递给合成炉夹套中的循环水,增加了循环水温度,在夏季由于循环水温度的增高,影响了整個装置的满负荷生产。
2009年我公司扩产购进了六台二合一氯化氢石墨副产蒸汽合成炉,并于2010年11月顺利投产,经过近三年来使用,六台氯化氢石墨副产蒸汽合成炉生产运行较好,并且合成炉副产出的蒸汽已经应用到其他工段。
1 氯化氢二合一副产蒸汽合成炉的生产工艺主要包含氯化氢合成气的生产;同时又能生产出低压蒸汽。
首先,氢气经过氢气过滤器脱出氢气中夹带的部分水蒸气,送到氯化氢合成炉的氢气入口调节阀;氯气经过氯处理的五个玻璃钢塔的干燥脱水处理后,送到氯化氢合成炉氯气调节阀;通入的氯气和氢气经过调节阀按一定的比例在蒸汽合成炉炉底灯头处充分混合后燃烧,炉膛内产生的氯化氢气经过炉顶部的块孔式石墨初步冷却,再经过合成炉外部的一级、二级石墨冷却器的二次冷却后,直接送聚氯乙烯合成工段生产氯乙烯,或送降膜吸收器中生产盐酸。
副产蒸汽是在合成炉的夹套层中产生的。
夹套中的无离子水吸收氢气、氯气的燃烧反应热,使夹套中无离子水逐渐沸腾蒸发,产生的蒸汽在夹套层顶部排出,用于烧碱装置一次盐水化盐和聚氯乙烯装置聚合工段汽提塔使用;在冬天一部分副产蒸汽还用于生产厂房采暖。
2 生产运行情况新上的六台氯化氢二合一副产蒸汽合成炉运行近3年的时间,生产运行平稳,蒸汽合成炉的氯化氢合成气质量较好,能满足后续生产要求,副产蒸汽也能够被有效的利用。
副产蒸汽氯化氢合成炉的改进与应用

第4 1 卷第 6期
2 0 1 3年 3月
广
Hale Waihona Puke 州化工 Vo 1 . 4 1 No . 6
Ma r c h .2 01 3
Gu a n g z h o u Ch e mi c a l I n d u s t r y
副 产 蒸 汽 氯 化 氢 合 成 炉 的 改进 与 应 用
Ke y wo r d s :b y—p r o d u c t s t e a m ;h y d r o g e n c h l o r i d e;s y n t h e t i c f u na r c e;e c o n o mi c b e n e i f t s
氢气和氯气的燃烧反应是一个剧烈的放热反应 ,放 出的热量 非常巨大,每生成 1 m o l 的氯化氢 ( H C 1 )气体就会放出9 2 . 3 k J 的 热量 。传统二合一合成炉采用 钢制水 夹套形式 ,热量直接 由冷 却水带走 ,不仅需 要消耗大量的冷却水还造成 了资源浪 费 J ,运 行成本较高。为贯彻 国家推行的 “ 节能减排”方针 ,2 O O 6年起我
- 1、下载文档前请自行甄别文档内容的完整性,平台不提供额外的编辑、内容补充、找答案等附加服务。
- 2、"仅部分预览"的文档,不可在线预览部分如存在完整性等问题,可反馈申请退款(可完整预览的文档不适用该条件!)。
- 3、如文档侵犯您的权益,请联系客服反馈,我们会尽快为您处理(人工客服工作时间:9:00-18:30)。
1、氯化氢合成系统副产中低压蒸汽基本原理 氯 气 与 氢 气 反 应 生 成 氯 化 氢 时 伴 随 释 放 出 大 量 反 应 热 : 0.5H2 十 0.5Cl2=HCL+22.063Kca1/mol,即每合成 1 千克气态氯化氢放出 605.11 Kcal 热 量。氯气与氢气在合成炉内以燃烧形式反应生成氯化氢,火焰中心区温度达到 2500℃以上,生成的氯化氢气体温度在 2000℃以上,这些热量相当可观,完全 可以用来副产蒸汽。 2、 国内氯化氢合成炉副产蒸汽现状及特点 对于氯化氢合成中的热能利用,国内经历了以下阶段。 第一代是使用钢制水夹套氯化氢合成炉副产热水。这种钢合成炉在炉顶部 和底部容易受腐蚀,使用寿命短,副产的热水应用范围有限,目前已经基本被淘 汰。 第二代是使用石墨制的氯化氢合成炉副产热水,主要原理是通过承压石墨 内筒和钢制外筒之间水吸热,产出大于 85 度的热水,是目前国内一些氯碱企业 较多采用的合成炉。但由于其合成炉的结构特点所限,其内部热水不能自循环, 需要通过外循环泵强制循环。这就导致热水吸热不稳定,造成合成炉出口的 HCL 温度变化大,有时会出现 HCL 出口温度过高,达不到工艺要求。另外,由于吸 热的石墨内筒温度一般低于 100 度,会导致在石墨内筒上出现大量冷凝酸,客 观的造成合成炉产生冷凝酸过多。特别是一旦由于受热不均易引起石墨内筒出 现渗漏,导致 HCL 气体进入热水中,使热水的 PH 值降低,腐蚀钢制外筒和热 水循环管道,严重的导致更换。这就导致副产热水 HCL 合成炉系统运行的不稳 定,出现频繁的检修和更换,对企业的安全和连续性生产造成重大的损失和影 响。
七、副产蒸汽 HCL 合成炉主要设备及报价。 1、副产蒸汽 HCL 合成炉系统主要设备一览表
5
三、副产蒸汽氯化氢合成炉主要设备及工艺流程 Ⅰ、本系统主要设备包括副产蒸汽氯化氢合成炉、汽包、预热器。 1、副产蒸汽氯化氢合成炉 与常规的氯化氢合成炉相比,本系统合成炉的炉筒部分采用钢制水冷壁炉
筒替代原来石墨炉筒的结构,自下而上分为氯化氢合成段、蒸汽发生段(第一 冷却段)、氯化氢冷却段(第二冷却段)三部分。原料氯气、氢气从炉底进入, 在石英制的燃烧器内(即氯化氢合成段)混合反应燃烧,反应后的高温氯化氢 气体向上经过二段冷却至 45℃以下后输出。蒸汽发生段为钢制水冷壁炉筒,其 结构是由鳍片锅炉钢管焊接成的封闭圆筒,上下有环形集水箱,水冷壁炉筒与 汽包通过管道连接,组成热水自循环系统,水冷壁炉筒钢管内软水吸收氯化氢 气体的反应热后上升,经上端环形集水箱汇集进入汽包,部分水汽化成蒸汽产 出,部分水与补充软水一道循环回流。
3
一、项目要求及报价 根据贵公司的要求:按合成炉每天产 60 吨 HCl 的采购条件,要求设计副产 蒸汽的 HCL 合成炉,其副产蒸汽压力达到 0.4-1.4MPa。装置操作操作弹性为: 50%~110%;装置操作时间:8000 小时/年。
副产蒸汽氯化氢合成炉系统单套含税价 228 万元(详见副产蒸汽 HCL 合成 炉系统主要设备一览表)。 二、副产蒸汽氯化氢合成炉行业发展情况
1、自动点火系统 自动点火系统由在线火焰检测、自动切断阀、高压点火装置和程序控制组 成。在工艺允许点火条件满足的前提下启动点火程序,装置自动进行以下操作: 首先是进行系统置换,然后通过点火专用的氢气、压缩空气点燃小火,最后引 燃石墨炉主灯头。此后操作人员可以根据生产负荷的需要逐步提升负荷,即安 全又便捷。 2、自动联锁保护系统 该装置设有:氢气压力低、氯气压力低、仪用气压力低、冷却水流量低、 汽包液位、火焰在线监测等多个连锁保护,当任何一个联锁条件满足时,系统 立即自动执行停车保护程序,并进行自动充氮保护,同时还设置了 DCS 及现场 紧急停车按扭,以备特殊情况下使用,确保装置的安全。 3、氢气、氯气自动配比控制 根据生产控制中 HCI 的纯度分析来设定氢气、氯气适合的比值,该系统 可以通过精确的氢气、氯气流量测量与调节实现氢气与氯气的自动配比控制。 若生产中氢气、氯气的纯度发生较大的变动时,则要及时修正氢气与氯气的比 值。并且通过对出口的高纯盐酸中游离氯的检测来控制调节氢气与氯气的比值。 4、汽包部分的自动控制 蒸汽分离的控制包括汽包液位的自动控制、蒸汽压力自动控制。即通过调 节进软水调节阀的开度来控制汽包液位,对出口蒸汽阀的调节来控制产出蒸汽 的压力。另外,为保护合成炉产蒸汽设备的安全,我们做了汽包液位低和的联 锁保护以及对蒸汽压力高后的排放泄压。 五、节能减排及经济效益以及安全效益分析
2、汽包为蒸汽发生分离装置。由钢制炉筒过来的过热水在汽包内闪蒸出蒸 汽输出。汽包上设置有水位检测控制仪表,运行时通过自动补加软水保证汽包 内维持一定液位。
3、预热器是一台列管式换热器,设置在汽包回水管与炉筒进水管之间,开 车时用采预热系统内软水,停车期间用来保持钢制炉筒温度维持在 90 度以上, 防止产生冷凝酸腐蚀。
副产蒸汽氯化氢合成炉系统技 术方案
山东东营拓宇化工技术有限公司 副产蒸汽 HCL 合成炉系统 方案设计
江苏苏宇化工设备有限公司 2014-2-16
目录
一、项目要求及报价 二、副产蒸汽氯化氢合成炉行业发展情况
1、氯化氢合成系统副产中低压蒸汽基本原理 2、 国内氯化氢合成炉副产蒸汽现状及特点 3、新型副产蒸汽氯化氢合成炉的特点 三、副产蒸汽氯化氢合成炉主要设备及工艺流程 Ⅰ、合成炉主要设备
4
第三代的副产低压蒸汽 HCL 合成炉是国内合成炉厂家通过改进副产热水 的石墨内筒材质,提高承压能力,副产出 0.2~0.3Mpa 压力的蒸汽。
但由于石墨是非金属脆性材料,受强度和使用温度的限制,在副产蒸汽 时石墨炉筒作为产汽的受压部件,安全上存在一定隐患,而且热能的利用率只 能达到 30%~40%,采用该方法副产低压蒸汽应用范围同样有限。而通过改进 石墨材质,也只能在一定程度上提高产出蒸汽压力,其提高程度有限,而且大 幅提高了制造成本,并在使用过程中对工艺操作有更加高的要求,增加了操作 的复杂性。另外,由于本身石墨材料的原因,为防止石墨炉筒受热升温过快导 致爆裂,合成炉点火开车后,要小负荷运行约 2 个小时后才能提升负荷,这对 生产负荷的调整带来了不便。
在安全上,由于该合成炉系统采用了先进的设备制造技术、完善的的工艺 水平和高度的自动化控制。比以往的老式合成炉相比大大提高了装置的本质安 全。 六、主要性能指标
8
1.氯化氢合成系统(以日产 60t 氯化氢为例) ①氯化氢质量达到以下要求:
纯度 95% 氯化氢出口温度≤45℃ ②满负荷生产时单套副产 1.4MPa 蒸汽≥1.75t/小时; ○3 自动控制系统实现 DCS 集中控制,现场无人值守。
6
止其过热),再通过连接工艺管进入上部的氯化氢冷却段内(用于冷却氯化氢气 体),经出口输出。 四、自动控制系统
在自动化控制方面,针对该合成炉的结构特点,本公司开发了可靠的远程 自动点火、完善的过程自动控制及安全的连锁保护系统,实现了从点火开车、 过程控制到停车的全过程的 DCS 操作,大大提高了装置的自动化控制水平及本 质安全。控制系统由以下五部分组成。
1、副产蒸汽氯化氢合成炉主体 2、汽包 3、预热器 Ⅲ、副产蒸汽氯化氢合成炉系统工艺流程: 1、氯化氢合成及冷却流程。 2、副产蒸汽流程。 3、循环水流程。 四、自动控制系统 1、自动点火系统 2、自动联锁保护系统 3、氢气、氯气自动配比控制 4、汽包部分的自动控制 五、节能减排及经济效益以及安全分析 六、主要性能指标 七、副产蒸汽 HCL 合成炉主要设备。 1、副产蒸汽 HCL 合成炉系统主要设备一览表 2、提供的备品备件及易耗品 包括灯头、防爆膜、四氟密封材料等
7
1.热能利用率高。每合成 1t 氯化氢气体可副产低压或中压蒸汽 0.7~ 0.8t。以日产 60t 氯化氢为例,氯化氢合成系统装置满负荷生产时日产蒸汽约 42 吨,蒸汽单价以 200.00 元/吨计,年开车 8000 小时,年创效益约 280 万元。
2.由于氯化氢合成放热大部分用来发生蒸汽,与常规炉型相比,循环冷却 水用量大幅减少。以 60t/d 氯化氢合成炉来计算,每小时产出的热量为 1.8*106 kcal/h,这部分热量 68%左右以副产蒸汽的形式带走,若以循环冷却水的方式 移热,则需消耗 210t/h 的冷却水量(循环冷却水温升按 6℃计),按一般循环水 装置配置需约 60kW 动力电,电价按 0.5 元/度计,每年可节约动力电费用约 10.5 万元。
5、由于该副产蒸汽合成炉在保证正常工艺操作条件的情况下,能保持长时 间稳定的运行,企业可以按正常的检修计划作业,避免了非正常的停车检失。