启动锅炉冲洗、吹扫、烘炉、煮炉工艺(参考一)
锅炉的烘炉和煮炉操作规程范本

锅炉的烘炉和煮炉操作规程范本第一章总则第一条为了安全、高效地进行锅炉的烘炉和煮炉操作,保障生产过程中的人身安全和设备安全,制定本规程。
第二条本规程适用于各类锅炉的烘炉和煮炉操作。
第三条烘炉和煮炉操作应严格按照本规程的要求执行。
第四条烘炉和煮炉操作人员应经过专业培训和考核,持有相应的操作资格证书。
第五条在煮炉和烘炉操作过程中,应遵守国家有关法律、法规和标准,严禁违规操作。
第六条各级管理人员应定期进行安全检查和操作指导,对违反本规程的行为进行纠正。
第二章烘炉操作规程第一节烘炉前的准备工作第七条烘炉前,应仔细检查烘炉设备及配件是否完好。
第八条烘炉前,应进行烘炉区的安全检查,确保无杂物、无明火等安全隐患。
第九条烘炉前,应检查燃料和热源是否充足。
第十条烘炉前,应清理烘炉底部的灰渣和燃烧器部分的污垢。
第二节烘炉的操作流程第十一条开启烘炉前,应按照操作手册依次操作。
第十二条操作人员在开启烘炉前,应检查电气系统是否正常工作。
第十三条开启烘炉后,应调整热风温度和风量,确保烘炉内温度的控制。
第十四条烘炉运行过程中,应定期检查各部位的温度、压力和流量。
第十五条烘炉停机前,应关闭热源和烘炉内的设备。
第十六条烘炉停机后,应进行烘炉设备的清洁和维护。
第三节烘炉的安全操作要求第十七条在烘炉操作过程中,严禁在烘炉周围堆放易燃物品。
第十八条在烘炉操作过程中,严禁超负荷运行烘炉。
第十九条在烘炉操作过程中,应定期检查烘炉设备的耐火材料。
第二十条在烘炉操作过程中,应设有烘炉报警系统,确保安全报警的及时性。
第二十一条在烘炉操作过程中,应设有应急处理措施和设备,以应对突发情况。
第三十二章煮炉操作规程第一节煮炉前的准备工作第二十三条煮炉前,应仔细检查煮炉设备及配件是否完好。
第二十四条煮炉前,应进行煮炉区的安全检查,确保无杂物、无明火等安全隐患。
第二十五条煮炉前,应确保燃料和水源充足。
第二十六条煮炉前,应清理煮炉底部的污垢和燃烧器部分的杂物。
锅炉的烘炉和煮炉操作规程

锅炉的烘炉和煮炉操作规程第一章总则为保障锅炉的安全运行,提高烘炉和煮炉操作的效率和质量,制定本规程。
第二章责任和权限1. 烘炉和煮炉操作人员应经过培训并持有相应的证书。
操作人员需熟悉锅炉的工作原理和操作要求,并具备应急处理和事故处理能力。
2. 烘炉和煮炉操作人员应按照规程和操作指导书进行操作,严禁擅自修改操作流程和参数。
3. 负责制定并执行煤炭和燃料的供应计划,保证锅炉的正常燃烧。
4. 负责安排锅炉的检修和维护工作,及时清理和更换附件设备。
第三章烘炉操作流程1. 烘炉操作前的准备工作:(1) 检查炉内是否有杂物和残余物,必要时进行清理。
(2) 检查燃烧器和辅助设备的工作状态,确保正常运行。
(3) 检查烘炉的水位、压力和温度,确保在正常范围内。
(4) 检查燃料的供应情况,确保充足并正确配比。
(5) 检查烘炉的进出口阀门和排污阀门,确保正常通畅。
2. 烘炉的操作步骤:(1) 打开炉门,逐层放入燃料,注意保持燃料的均匀分布。
(2) 关闭炉门,并根据燃烧系统的要求,调整燃烧风量和供热参数。
(3) 开启点火装置,点燃燃烧器并观察燃烧情况。
(4) 根据烘炉的使用要求,调节水位和压力,保持在安全范围内。
(5) 监控烘炉的温度和压力,及时采取调节措施。
(6) 定期清理炉灰和排污,保持烘炉的正常工作。
(7) 烘炉停用时,逐步停止燃烧器并关闭炉门和燃气阀门。
第四章煮炉操作流程1. 煮炉操作前的准备工作:(1) 检查锅炉的水位、压力和温度,确保在正常范围内。
(2) 检查燃烧器和辅助设备的工作状态,确保正常运行。
(3) 检查煮炉的水质,必要时进行处理和调整。
(4) 检查燃料的供应情况,确保充足并正确配比。
(5) 检查煮炉的进出口阀门和排污阀门,确保正常通畅。
2. 煮炉的操作步骤:(1) 根据煮炉的使用要求,调节锅炉的水位和压力。
(2) 打开燃烧器的供气阀门,并根据燃烧系统的要求,调整燃烧风量和供热参数。
(3) 点燃燃烧器并观察燃烧情况。
锅炉煮炉工艺规程
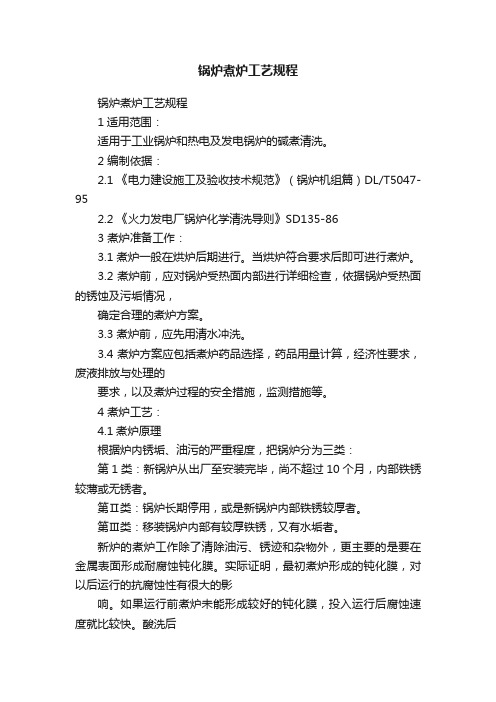
锅炉煮炉工艺规程锅炉煮炉工艺规程1适用范围:适用于工业锅炉和热电及发电锅炉的碱煮清洗。
2 编制依据:2.1 《电力建设施工及验收技术规范》(锅炉机组篇)DL/T5047-952.2 《火力发电厂锅炉化学清洗导则》SD135-863 煮炉准备工作:3.1 煮炉一般在烘炉后期进行。
当烘炉符合要求后即可进行煮炉。
3.2 煮炉前,应对锅炉受热面内部进行详细检查,依据锅炉受热面的锈蚀及污垢情况,确定合理的煮炉方案。
3.3 煮炉前,应先用清水冲洗。
3.4 煮炉方案应包括煮炉药品选择,药品用量计算,经济性要求,废液排放与处理的要求,以及煮炉过程的安全措施,监测措施等。
4 煮炉工艺:4.1煮炉原理根据炉内锈垢、油污的严重程度,把锅炉分为三类:第 1类:新锅炉从出厂至安装完毕,尚不超过10个月,内部铁锈较薄或无锈者。
第Ⅱ类:锅炉长期停用,或是新锅炉内部铁锈较厚者。
第Ⅲ类:移装锅炉内部有较厚铁锈,又有水垢者。
新炉的煮炉工作除了清除油污、锈迹和杂物外,更主要的是要在金属表面形成耐腐蚀钝化膜。
实际证明,最初煮炉形成的钝化膜,对以后运行的抗腐蚀性有很大的影响。
如果运行前煮炉未能形成较好的钝化膜,投入运行后腐蚀速度就比较快。
酸洗后的锅炉,开炉前必须进行煮炉工作,在活性金属表面形成一层钝化膜。
碱煮除垢药剂由烧碱和磷酸三钠组成。
烧碱的主要成分是氢氧化钠 NaOH,它对油污以及硅酸盐垢都有一定的溶解作用,氢氧化钠NaOH与硅酸盐的反应如下:SiO2+2NaOH→Na2SiO3+H2O硅酸钠 Na2SiO3又称水玻璃,它是易溶于水的物质。
磷酸三钠Na3PO4的作用是使坚硬、致密的硫酸钙水垢和碳酸钙水垢转型变成松软的磷酸钙水垢,起反应如下:3CaSO4+2Na3PO4→Ca3(PO4)2↓+3Na2SO43CaSO3+2Na3PO4→Ca3(PO4)2↓+3Na2SO3磷酸钙 Ca3(PO4)2水垢能被盐酸溶解:Ca3(PO4)2+6HCL→3CaCL2+2H3PO4故,硫酸盐水垢或碳酸盐水垢经碱煮转型后生成的磷酸钙水垢Ca3(PO4)2,可以用盐酸清洗剂除去。
3#锅炉启动前的准备(烘炉、煮炉)
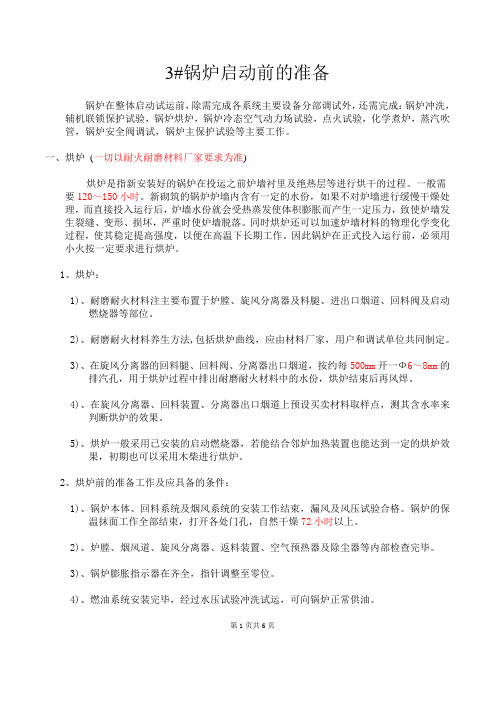
3#锅炉启动前的准备锅炉在整体启动试运前,除需完成各系统主要设备分部调试外,还需完成:锅炉冲洗,辅机联锁保护试验,锅炉烘炉,锅炉冷态空气动力场试验,点火试验,化学煮炉,蒸汽吹管,锅炉安全阀调试,锅炉主保护试验等主要工作。
一、烘炉(一切以耐火耐磨材料厂家要求为准)烘炉是指新安装好的锅炉在投运之前炉墙衬里及绝热层等进行烘干的过程。
一般需要120~150小时。
新砌筑的锅炉炉墙内含有一定的水份,如果不对炉墙进行缓慢干燥处理,而直接投入运行后,炉墙水份就会受热蒸发使体积膨胀而产生一定压力,致使炉墙发生裂缝、变形、损坏,严重时使炉墙脱落。
同时烘炉还可以加速炉墙材料的物理化学变化过程,使其稳定提高强度,以便在高温下长期工作。
因此锅炉在正式投入运行前,必须用小火按一定要求进行烘炉。
1、烘炉:1)、耐磨耐火材料注主要布置于炉膛、旋风分离器及料腿、进出口烟道、回料阀及启动燃烧器等部位。
2)、耐磨耐火材料养生方法,包括烘炉曲线,应由材料厂家,用户和调试单位共同制定。
3)、在旋风分离器的回料腿、回料阀、分离器出口烟道,按约每500mm开一Ф6~8mm的排汽孔,用于烘炉过程中排出耐磨耐火材料中的水份,烘炉结束后再风焊。
4)、在旋风分离器、回料装置、分离器出口烟道上预设买卖材料取样点,测其含水率来判断烘炉的效果。
5)、烘炉一般采用已安装的启动燃烧器,若能结合邻炉加热装置也能达到一定的烘炉效果,初期也可以采用木柴进行烘炉。
2、烘炉前的准备工作及应具备的条件:1)、锅炉本体、回料系统及烟风系统的安装工作结束,漏风及风压试验合格。
锅炉的保温抹面工作全部结束,打开各处门孔,自然干燥72小时以上。
2)、炉膛、烟风道、旋风分离器、返料装置、空气预热器及除尘器等内部检查完毕。
3)、锅炉膨胀指示器在齐全,指针调整至零位。
4)、燃油系统安装完毕,经过水压试验冲洗试运,可向锅炉正常供油。
第1页共6页5)、锅炉有关的热工仪表和电气仪表均已安装和试运完毕,校验结束,可投入使用。
烘炉、洗炉及清炉安全操作规程

烘炉、洗炉及清炉安全操作规程(一)烘炉1、新修的炉子自然干燥时间不得少于1个月。
2、新修或大修后炉子的烘炉操作制度(表一)以及曲线(图一):表一烘炉操作制度序号加热温度(℃)升温时间(小时)保温时间(小时)累计时间(小时)炉门开关状况1室温-120xx7282开2120-18067278开3180-2608120xx8开4260-34087280开5340-480143650关6480-540696102关7540-650114859关8650-800157287关9熔炼炉666保温炉图一新修或大修后炉子的烘炉曲线3、停歇后的炉子烘炉操作制度及烘炉曲线(图二):图二冷启炉加热曲线(二)洗炉在连续生产过程中,洗炉次数越多,生产效率越低,生产成本越高。
因此,在安排合金转换顺序时,应该根据合同科学安排。
一般的原则是:前一炉合金的主要成分不是下一炉合金的杂质;前一炉合金杂质的允许含量低于下一炉合金杂质的允许含量。
1、洗炉原则(1)新修、中修和大修后的炉子在生产前必须洗炉。
(2)高成份合金往低成份合金转组,原则要求必须洗炉,但可以根据具体情况进行合金过渡。
2、洗炉用料的规定(1)向高纯合金或特殊合金转组时,必须用原铝锭洗炉。
(2)新炉(包括大修)开炉、一般合金转组可用原铝锭或纯铝一级废料洗炉,也可以用紧接着需要生产合金的本身一级废料进行洗炉。
(3)中修或长期停炉后的炉子如单纯为清洗炉内脏物,可用纯铝的一级废料洗炉,也可以用紧接着需要生产合金的本身一级废料进行洗炉。
3、洗炉料用量:洗炉料用量必须≥40%炉子容量。
4、洗炉要求(1)装洗炉料前必须彻底放干、大清炉。
(2)洗炉的熔体温度为800~850℃,彻底搅三次,每次间隔时间半小时。
(3)洗炉料不经由深床或管式过滤,经由铸造机铸造出废锭供后续使用。
(4)洗炉料必须彻底放干,之后撒入清炉剂彻底进行大清炉,彻底清理干净炉底、炉壁、炉底的渣子,一定要保证炉子的干净。
余热锅炉煮炉、吹洗方案-最终

余热锅炉煮炉、吹管方案编制:审核:日期:2006年10月24日余热锅炉煮炉、吹洗方案一、概述:本台余热锅炉的型号为Q396/568-77.3(9.9)-6.08(0.3)/483(190),由杭州锅炉集团有限公司生产,锅炉是带烟气旁路系统、凝结水加热器、自除氧、无补燃、自然循环、三压余热锅炉。
受热面采用标准单元模块式结构,由垂直布置的错列开齿螺旋鳍片管和上下集箱组成,以获得最佳的传热效果和最低的烟气压降。
锅炉在安装完毕,并进行水压试验合格办理签证后,同时将炉内存水及时放净。
随后应进行煮炉、冲洗、吹扫工作。
目的是清除锅炉在制造安装过程中留在系统内的油污,铁锈等。
二、编制依据:1.《电力建设施工及验收技术规范》(锅炉篇)(管道篇)2.《火电工程调整试运质量检验及评定标准》3.《火力发电厂汽水管道设计导则》4.《电业工作安全规程》(热力机械)5.《火力发电厂基本建设工程启动及竣工验收规程》6.生产厂家资料及有关设计图纸。
7.《火电机组启动蒸汽吹管导则》.8.杭州锅炉集团有限公司提供的锅炉安装说明书和设计说明书等技术文件。
三、锅炉煮炉:1、煮炉前的准备工作:1.1锅炉正式或临时加药及取样装置能够投入运行。
1.2 供给合格的除盐水。
1.3汽、水分析化验能随时工作。
1.4 准备好煮炉用药品,并做好药品纯度分析。
1.5 准备好加药用的劳保用品及工具。
2、煮炉要求:2.1系统中装有温度测点、取样点、压力表、流量计、监视管段和腐蚀指示片;与清洗的设备、系统相连而又不参加化学清洗的部分应可靠地隔绝。
2.2 锅炉煮炉采用碱煮法,即加NaOH和Na3PO4。
2.3正常运行时系统总的水容积52m3。
每m3水加NaOH和Na3PO4各3~5kg(按100%纯度)。
2.4 加药量为:高压锅炉水容积20m3,NaOH和Na3PO4各加80公斤。
低压锅炉水容积10 m3,NaOH和Na3PO4各加40公斤。
除氧系统水容积22 m3 NaOH和Na3PO4各加44公斤2.5药剂的配制和投加:利用加药系统,接临时上水泵,把药品缓慢加入水箱,并搅拌均匀,将上述两种药剂配制成浓度20%以下的溶液(用80℃~100℃的除盐水溶解)。
开工锅炉烘炉及煮炉方案

开工锅炉烘炉及煮炉方案一、烘炉前应具备下列条件:1、锅炉及其附属装置全部组装完毕和水压试验合格。
2、保温结束3、锅炉的热工仪表应该校验合格,并检查锅炉给水水源的可靠性,同时向锅炉进水至正常水位。
4、烘炉所需的辅机试运转完毕,例如水泵风机等,证实了各部分工作有安全启动的条件,即可开始烘炉。
二、烘炉方法及注意事项1、烘炉应根据现场具体条件采用火焰、蒸汽等法,烘炉前应装设必要的临时措施。
2、采用火焰烘炉时应符合下列要求:•••• 2.1、火焰应在炉膛中央,燃烧均匀,不得时断时续;2。
2、烘炉温度应按炉膛出口处的烟气温度来控制,在正常养护期满后(矾土水泥约为3昼夜)方可开始烘炉,在最高温范围内持续时间内不应少于一昼夜,其温升速度每天不超过80℃,后期烟温不应超过160℃。
三、煮炉1、煮炉的目的锅炉加入NaOH和Na3PO4进行化学处理,采用碱性煮炉,把锅内油污、沉淀物、铁锈除去,以保证锅炉受热均匀,运行正常.2、煮炉方法及注意事项2.1、煮炉最早可在烘炉末期进行。
2。
2、煮炉时的加药量应符合设备技术文件规定,如无规定的,应符合下列表的规定:•••• 煮炉时的加热配方备注:1.药品按100%的纯度计算。
2。
缺乏磷酸三钠时,可用碳酸钠代替,数量为磷酸三钠的1.5倍。
3。
可以单独用碳酸钠煮炉,其数量为6kg/m3水.2。
3、药品应溶化成溶液状加入锅炉内,配制和加入药液时应注意安全。
2.4、加药时,炉水应在低水位.2.5、为保证煮炉效果,在煮炉末期应使工作压力保持在工作压力的75•%左右.煮炉时间一般应为2~3天,如在较低的蒸汽压力下煮炉,则应适当地延长煮炉时间。
2。
6、煮炉时间应定期从锅筒取样,对炉水碱度进行分析。
炉水碱度不应低45mg —eg/L,否则应补充加药.2.7、煮炉完毕,应清理锅筒内的沉淀物。
冲洗锅炉内部和曾与药液接触过的阀门等,检查排污阀有无堵塞。
2。
8、煮炉应符合下列要求:A.锅筒内壁面应无油垢.B.擦去附着物后金属表面应无锈斑.2。
锅炉启用前的工作
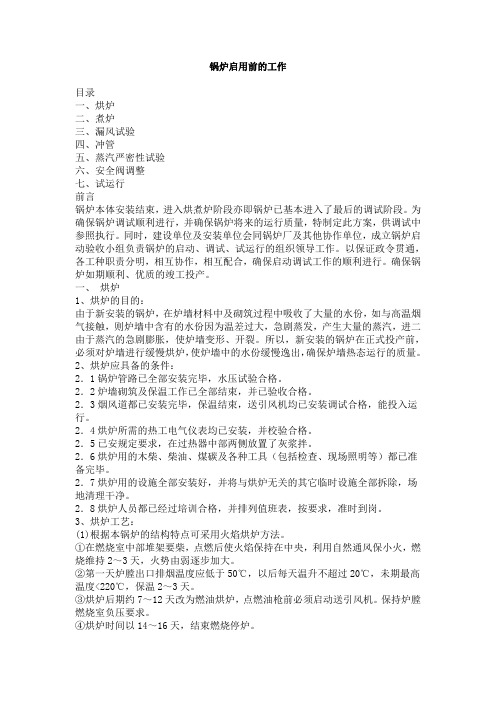
锅炉启用前的工作目录一、烘炉二、煮炉三、漏风试验四、冲管五、蒸汽严密性试验六、安全阀调整七、试运行前言锅炉本体安装结束,进入烘煮炉阶段亦即锅炉已基本进入了最后的调试阶段。
为确保锅炉调试顺利进行,并确保锅炉将来的运行质量,特制定此方案,供调试中参照执行。
同时,建设单位及安装单位会同锅炉厂及其他协作单位,成立锅炉启动验收小组负责锅炉的启动、调试、试运行的组织领导工作。
以保证政令贯通,各工种职责分明,相互协作,相互配合,确保启动调试工作的顺利进行。
确保锅炉如期顺利、优质的竣工投产。
一、烘炉1、烘炉的目的:由于新安装的锅炉,在炉墙材料中及砌筑过程中吸收了大量的水份,如与高温烟气接触,则炉墙中含有的水份因为温差过大,急剧蒸发,产生大量的蒸汽,进二由于蒸汽的急剧膨胀,使炉墙变形、开裂。
所以,新安装的锅炉在正式投产前,必须对炉墙进行缓慢烘炉,使炉墙中的水份缓慢逸出,确保炉墙热态运行的质量。
2、烘炉应具备的条件:2.1锅炉管路已全部安装完毕,水压试验合格。
2.2炉墙砌筑及保温工作已全部结束,并已验收合格。
2.3烟风道都已安装完毕,保温结束,送引风机均已安装调试合格,能投入运行。
2.4烘炉所需的热工电气仪表均已安装,并校验合格。
2.5已安规定要求,在过热器中部两侧放置了灰浆拌。
2.6烘炉用的木柴、柴油、煤碳及各种工具(包括检查、现场照明等)都已准备完毕。
2.7烘炉用的设施全部安装好,并将与烘炉无关的其它临时设施全部拆除,场地清理干净。
2.8烘炉人员都已经过培训合格,并排列值班表,按要求,准时到岗。
3、烘炉工艺:(1)根据本锅炉的结构特点可采用火焰烘炉方法。
①在燃烧室中部堆架要柴,点燃后使火焰保持在中央,利用自然通风保小火,燃烧维持2~3天,火势由弱逐步加大。
②第一天炉膛出口排烟温度应低于50℃,以后每天温升不超过20℃,未期最高温度<220℃,保温2~3天。
③烘炉后期约7~12天改为燃油烘炉,点燃油枪前必须启动送引风机。
启动锅炉冲洗、吹扫、烘炉、煮炉工艺(参考一)
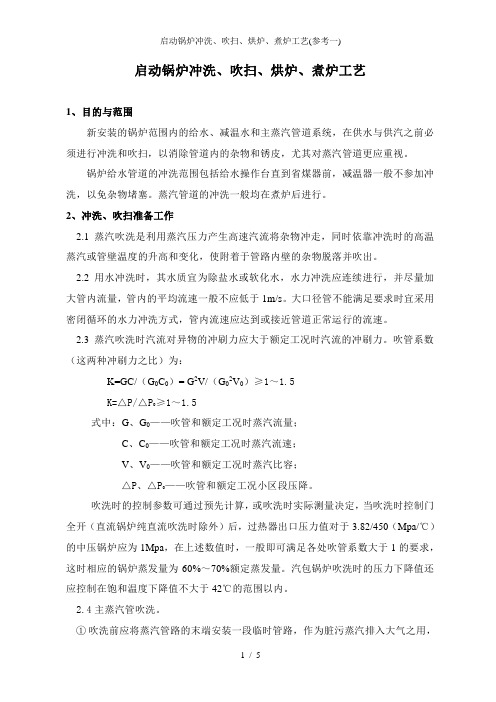
启动锅炉冲洗、吹扫、烘炉、煮炉工艺1、目的与范围新安装的锅炉范围内的给水、减温水和主蒸汽管道系统,在供水与供汽之前必须进行冲洗和吹扫,以消除管道内的杂物和锈皮,尤其对蒸汽管道更应重视。
锅炉给水管道的冲洗范围包括给水操作台直到省煤器前,减温器一般不参加冲洗,以免杂物堵塞。
蒸汽管道的冲洗一般均在煮炉后进行。
2、冲洗、吹扫准备工作2.1蒸汽吹洗是利用蒸汽压力产生高速汽流将杂物冲走,同时依靠冲洗时的高温蒸汽或管壁温度的升高和变化,使附着于管路内壁的杂物脱落并吹出。
2.2用水冲洗时,其水质宜为除盐水或软化水,水力冲洗应连续进行,并尽量加大管内流量,管内的平均流速一般不应低于1m/s。
大口径管不能满足要求时宜采用密闭循环的水力冲洗方式,管内流速应达到或接近管道正常运行的流速。
2.3蒸汽吹洗时汽流对异物的冲刷力应大于额定工况时汽流的冲刷力。
吹管系数(这两种冲刷力之比)为:K=GC/(G0C0)= G2V/(G02V0)≥1~1.5≥1~1.5K=△P/△P式中:G、G0——吹管和额定工况时蒸汽流量;C、C0——吹管和额定工况时蒸汽流速;V、V0——吹管和额定工况时蒸汽比容;——吹管和额定工况小区段压降。
△P、△P吹洗时的控制参数可通过预先计算,或吹洗时实际测量决定,当吹洗时控制门全开(直流锅炉纯直流吹洗时除外)后,过热器出口压力值对于3.82/450(Mpa/℃)的中压锅炉应为1Mpa,在上述数值时,一般即可满足各处吹管系数大于1的要求,这时相应的锅炉蒸发量为60%~70%额定蒸发量。
汽包锅炉吹洗时的压力下降值还应控制在饱和温度下降值不大于42℃的范围以内。
2.4主蒸汽管吹洗。
①吹洗前应将蒸汽管路的末端安装一段临时管路,作为脏污蒸汽排入大气之用,临时管路的截面积应大于或等于被吹管的截面积,否则节流过大或使蒸汽流速降低,不能达到冲洗的效果。
②临时管路应通到室外,并安装牢固,排汽管口应朝上30o~45o向大气排放。
锅炉的烘炉和煮炉操作规程

锅炉的烘炉和煮炉操作规程锅炉是工业生产中不可或缺的设备,它的安全运行是保障生产顺利进行的重要条件之一。
在使用锅炉时,烘炉和煮炉操作是非常重要的步骤,下面就介绍一下锅炉的烘炉和煮炉操作规程。
一、锅炉的烘炉操作1. 烘炉前准备在进行烘炉前,应对锅炉进行清洗,并清除锅炉内残留的水,确保锅炉内干燥。
烘炉时需要注意下列事项:1.关闭进水阀门,排气阀门。
2.打开烟囱排气阀门,让烟囱内空气畅通。
3.在烘炉前,应检查热风门、燃气阀门、吹扫阀门、循环阀门、进风阀门、排渣阀门是否完好无损。
2. 进行烘炉操作烘炉主要是为锅炉内表面或水平面进行烘干操作,具体操作流程如下:1.开启燃煤锅炉的燃气阀门并打开燃气切断阀门。
2.打开吹扫阀门,启动风机,并关闭热风门,使热风进入锅炉内部。
3.把燃烧室温度调节在50℃左右,并逐渐升温,直至设定温度,保持温度两小时以上,使锅炉内表面和水平面干燥。
4.烘炉操作完成后,关闭吹扫阀门、风机燃气切断阀门、燃气阀门、进气阀门和排气阀门。
二、锅炉的煮炉操作煮炉操作是指把水放入锅炉内,烧开并使锅炉产生蒸汽的操作,以下是具体操作流程:1. 煮炉前准备1.进行清洗:煮炉前要对锅炉进行彻底的清洗,清除锅炉内部的污物。
2.加水:在煮炉前,应加足够的水,可根据锅炉的水位标志线加水。
3.排气:倒入水后需进行排气操作,以确保锅炉内的空气被排出,避免锅炉启动后出现爆炸等危险情况。
2. 进行煮炉操作1.点炮:按照锅炉的燃烧方式点炮,使燃烧器点燃煤气或油气,产生火焰。
2.调节煤气量:煮炉过程中,应逐渐调节煤气量,使锅炉产生适当的蒸汽,同时加强煙囪的抽力,让燃烧更加完全。
3.观察水位:在煮炉过程中,应时刻观察水位,保持水平稳定,防止煮干锅炉。
4.关闭煮炉:煮炉完成后,应先关闭燃烧器,停止煮炉操作。
同时,应开启排污管道,释放锅炉内余压和热水,待水温降至常温时,方可停止放水。
结论对于锅炉的烘炉和煮炉操作规程,应遵循操作流程,认真细致地进行操作,确保锅炉安全、高效、稳定地运行。
锅炉烘炉、煮炉的技术要求

锅炉烘炉、煮炉新安装的锅炉、经大修和改造的锅炉在投入运行前都必须进行烘炉、煮炉。
这时对锅炉、辅机安装和制造质量的一次全面检查,也是正式运行前必须进行的一个环节。
一、烘炉(一)烘炉的目的及方法新安装的锅炉在炉墙内、耐火混凝土及磨面层内部都含有大量水份。
烘炉的目的是对新安装的锅炉炉墙进行缓慢烘热,使炉墙中的水份缓慢逸出,达到一定的干燥程度,确保炉墙的热态运行质量。
防止锅炉运行时由于炉墙潮湿,急骤受热后水份大量蒸发,急剧膨胀不均而造成炉墙变形、开裂。
此外,烘炉还可使炉墙的灰缝达到比较好的强度,提高炉墙耐高温的能力。
烘炉的方法目前主要有两种,即火焰烘炉法和蒸汽烘炉法。
烘炉时,应根据各种不同的锅炉型号,是轻型炉墙还是重型炉墙,当时、当地的气候条件等因素确定升温曲线。
按确定好的升温方案进行烘炉。
要注意绘制升温曲线,并将其存入锅炉技术档案。
(二)烘炉应具备的条件1、锅炉本体及工艺管道全部安装完毕,水压试验合格。
炉墙砌筑和管道保温工作全部结束,并检查验收合格。
炉膛、烟、风道都已安装完毕,保温结束,内部清理干净,外部拆除脚手架并将周围场地清扫干净。
2、送风机、引风机、除尘器、制粉、喷油及锅炉附属设备安装完毕,并经单体试车合格。
3、锅炉的热工及电气仪表安装完毕并调试合格,汽包及联箱的膨胀指示器安好并调整到位。
4、按技术文件的要求选好炉墙测温点和取样点,并准备好温度计和取样工具。
5、有旁通烟道的省煤器应关闭主烟道挡板,使用旁通烟道。
无旁通烟道时,省煤器循环管路上阀门应开启。
6、开启锅炉上所有排气阀和过热器集箱上的疏水阀。
7、准备好木材、煤等燃料,用于链条炉排上的燃料中的不得有铁钉、铁器,准备好各种工具、器材及用品(包括检查、现场照明等)。
8、编制烘炉方案及烘炉曲线,对参加烘炉人员进行技术交底,并准备好有关烘炉的记录表。
烘炉人员都已经过培训合格,并排列值班表,按要求,准时到岗。
9、冲洗锅炉,注入处理合格的软水,并上水至正常水位。
锅炉烘炉及吹洗方案

锅炉烘炉及吹洗方案该锅炉除下级省煤器区域采用护板轻型炉墙外,其余均采用敷管式炉墙。
按相关规范(DL/T5047-95锅炉机组篇)要求,一般在达到正常养护期后,可不再单独进行烘炉。
但考虑到该锅炉处在室外环境中以及距正式点火试运行时间较短,故据此具体情况对其进行烘炉。
烘炉合格后即进入蒸汽吹洗工作阶段。
蒸汽吹洗合格后停炉进行蒸汽管道恢复工作以及锅炉消缺工作。
本方案仅对烘炉、吹洗做出要求,锅炉启动试运另行编制。
1、烘炉1.1 方案编制目的及要求烘炉是锅炉投产前的一项重要工作,其主要作用是排出内衬炉墙中的水份。
为防止在锅炉点火升压过程中,因锅膛升温使墙体造成裂纹或塌落,影响锅炉墙体工程质量。
根据《电力建设施工及验收技术规范》锅炉机组篇DL/T5047-95规定,新锅炉正式点火前对敷管式混凝土炉墙需进行锅炉整体烘炉。
1.2 方案编制依据《电力建设施工及验收技术规范》锅炉机组篇DL/T5047-95《锅炉使用说明书》编号03575SM21.3 烘炉方式根据锅炉结构特点及现场具备条件,该1#锅炉采用炉内燃烧器明火烘炉方式。
今后2#炉采用无明火蒸汽烘炉方式。
本方案仅适用于南钢联2×50MW煤气综合利用电厂1#锅炉。
1.4 烘炉前要求具备的条件。
1.4.1 锅炉本体安装、炉墙及保温工程已结束1.4.2 锅炉炉膛及冷风、热风、烟风道漏风试验合格。
1.4.3 为烘炉服务的附属设备安装已结束,且单机调试、冷态试验合格,满足要求随时能够投入使用。
1.4.4 锅炉本体化学清洗已合格。
1.4.5 烘炉所需的热控、电气、仪表已安装和校验,试验调整合格,能正常投入使用。
1.4.6 与锅炉配套的除盐水、燃气、燃烧装置、送引风系统已安装及调试完毕,能随时投入使用。
1.4.7 烘炉用的临时设备及设施已装好,上、下水道畅通,保证满足供水和排水的需要。
1.4.8 烘炉现场具备充足可靠的照明,通讯和消防设施满足使用。
1.4.9 与尚在继续施工的现场及有关系统之间有可靠的隔离措施。
锅炉的烘炉和煮炉操作规程

锅炉的烘炉和煮炉操作规程锅炉是工业和民用领域中常用的热能设备,其烘炉和煮炉操作规程对保证安全生产和提高工作效率具有重要意义。
以下为锅炉的烘炉和煮炉操作规程,共计2000字。
一、烘炉操作规程1. 检查烘炉设备:每次操作前应检查烘炉设备的完整性和正常运行状态,检查电器、燃烧器、风机等设备是否损坏或堵塞。
2. 清洁烘炉内部:开机前应将烘炉内部进行清洁,清除燃烧残留物和灰尘,确保通风畅通。
3. 加燃料:根据生产需要,合理加入适量的燃料,确保火焰的稳定和温度的控制。
4. 开启烘炉:按照正确的启动顺序和程序依次开启烘炉设备,尽量避免突然开启引起大的冲击。
5. 控制温度:运行时应根据生产工艺要求控制烘炉温度,在操作过程中根据生产情况进行调整。
6. 监测烘炉状态:定期监测烘炉的燃烧状态和风机的运行状态,确保设备正常工作。
7. 关闭烘炉:操作结束后,应按照正确的顺序依次关闭烘炉设备,断开电源并清理设备。
8. 记录操作情况:每次操作前后应进行操作记录,包括设备检查、温度调整、燃料加入等情况。
二、煮炉操作规程1. 检查煮炉设备:运行前应对煮炉设备进行检查,包括水位、压力、安全阀等设备的正常工作状态。
2. 加水:根据需要,适量加入清洁的水,确保煮炉水位正常。
3. 燃烧器调整:根据实际情况进行燃烧器的调整,确保燃烧稳定且不产生过多的烟尘。
4. 点火:点火前应确保煮炉的排空已完成,点火时需要注意安全,避免引起火灾。
5. 控制压力:运行时应根据工艺要求控制合适的煮炉压力,注意监测压力表的变化。
6. 定期排污:煮炉运行一段时间后,应定期进行排污操作,清理煮炉内可能堆积的污垢。
7. 关闭煮炉:操作结束后,应按照正确的顺序依次关闭煮炉设备,断开电源并排空煮炉。
8. 记录操作情况:每次操作前后应进行操作记录,包括水位、压力、排污等情况。
三、操作注意事项1. 熟悉设备操作:操作人员应熟悉烘炉和煮炉设备的操作原理和流程,并遵守设备操作指南。
锅炉及管道的清洗流程

锅炉及管道的清洗流程新锅炉在制造、运输及安装过程中,其管道内壁会聚积氧化物或其他污物,使锅炉在初次运行过程出现受热面腐蚀破坏。
已安全运行一段时间的锅炉,在热负荷比较高的区域(如燃烧器区)会发生管道内壁的氧化沉积,造成受热面的超温或爆管事故。
天然水是电解质的水溶液,与金属接触极易产生电化学腐蚀,如果盐垢沉积在蒸汽的阀门处可能引起阀门动作失灵及阀门漏气。
为此,锅炉从安装完毕准备运行时就该采取一系列措施以保证受热面的清洁。
公司建议对新装锅炉在初次启动前进行管道的化学清洗,包括:凝汽器---给水系统的清洗,锅炉汽水系统的清洗,及过热再热系统的冲洗及锅炉酸洗四大部分。
运行一段时间的锅炉,如果管子受热一侧的沉积物达到每平方英寸10--12克(对汽包压力超过2000psig的锅炉),或每平方英寸12---20克(对汽包压力1500---2000psig的锅炉),也该进行化学清洗。
(文章来源:河南永兴锅炉集团 转载请注明!)一、凝汽器—给水系统的清洗1、冲洗凝汽器---给水系统在冲洗之前,凝汽器,热井和除氧器、给水箱应用百分之二的磷酸三钠(Na31PO4.12H20)溶液进行手工清洗,然后用普通水冲洗这些系统。
系统正式冲洗最好使用除盐水,冲洗的循环动力由冷凝水泵提供,凝汽器热井作为存水容器。
为了防止悬浮物质对冷凝水泵造成损坏,在泵的入口处应安装过滤器。
冲洗应从冷凝器井开始,逐步通过冷凝水和给水系统直到锅炉人口,各部分的冲洗要进行至看到废水变清为止,一般在某些排放口收集水样以确认冲洗终点。
对所有含有分叉的回路(如有疏水排放口、放气口、仪表接头等),或有并行路径(如旁通管线)的回路,在作业期间应考虑这些分叉、支线的隔离,确保系统充分清洗。
建议在开始清洗作业之前准备一份检查单,表明各支管和旁通管道的作业顺序,和对应的阀门状态。
2、碱洗凝汽器---给水系统的碱洗使用含有2000ppm磷酸三钠(2000ppm Na3P04或4600ppmNa3PO4.12H20)和1000ppm磷酸二钠(Na2PO4)及相容湿润剂的溶液。
锅炉烘炉、煮炉、漏风试验、冲管等详细知识阐述
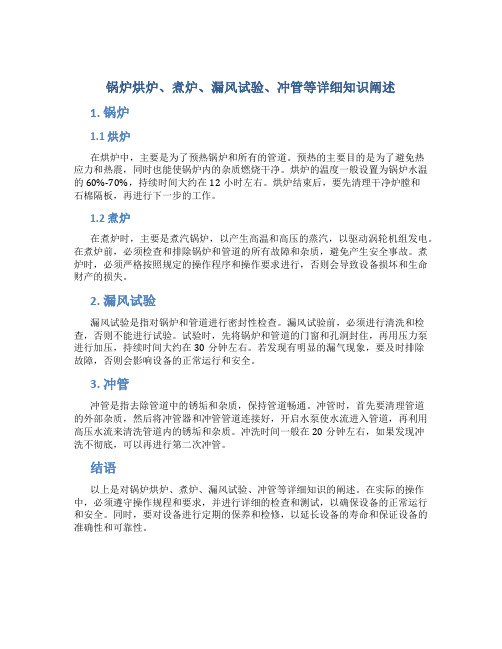
锅炉烘炉、煮炉、漏风试验、冲管等详细知识阐述1. 锅炉1.1 烘炉在烘炉中,主要是为了预热锅炉和所有的管道。
预热的主要目的是为了避免热应力和热震,同时也能使锅炉内的杂质燃烧干净。
烘炉的温度一般设置为锅炉水温的60%-70%,持续时间大约在12小时左右。
烘炉结束后,要先清理干净炉膛和石棉隔板,再进行下一步的工作。
1.2 煮炉在煮炉时,主要是煮汽锅炉,以产生高温和高压的蒸汽,以驱动涡轮机组发电。
在煮炉前,必须检查和排除锅炉和管道的所有故障和杂质,避免产生安全事故。
煮炉时,必须严格按照规定的操作程序和操作要求进行,否则会导致设备损坏和生命财产的损失。
2. 漏风试验漏风试验是指对锅炉和管道进行密封性检查。
漏风试验前,必须进行清洗和检查,否则不能进行试验。
试验时,先将锅炉和管道的门窗和孔洞封住,再用压力泵进行加压,持续时间大约在30分钟左右。
若发现有明显的漏气现象,要及时排除故障,否则会影响设备的正常运行和安全。
3. 冲管冲管是指去除管道中的锈垢和杂质,保持管道畅通。
冲管时,首先要清理管道的外部杂质,然后将冲管器和冲管管道连接好,开启水泵使水流进入管道,再利用高压水流来清洗管道内的锈垢和杂质。
冲洗时间一般在20分钟左右,如果发现冲洗不彻底,可以再进行第二次冲管。
结语以上是对锅炉烘炉、煮炉、漏风试验、冲管等详细知识的阐述。
在实际的操作中,必须遵守操作规程和要求,并进行详细的检查和测试,以确保设备的正常运行和安全。
同时,要对设备进行定期的保养和检修,以延长设备的寿命和保证设备的准确性和可靠性。
PH锅炉水压、煮炉、冲洗、吹扫方案
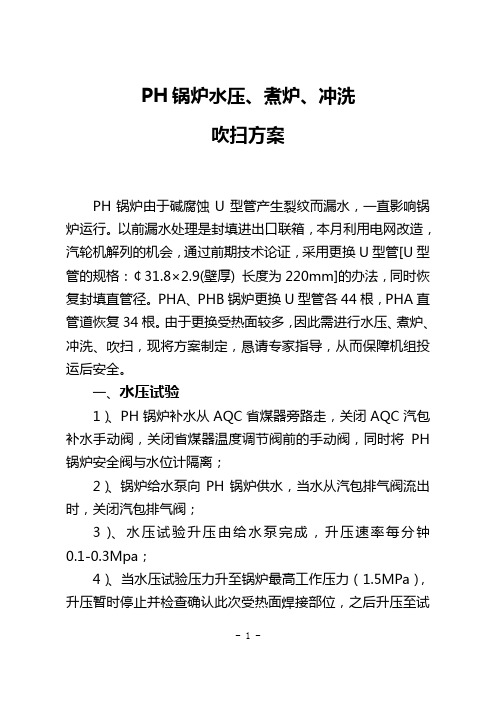
PH锅炉水压、煮炉、冲洗吹扫方案PH锅炉由于碱腐蚀U型管产生裂纹而漏水,一直影响锅炉运行。
以前漏水处理是封填进出口联箱,本月利用电网改造,汽轮机解列的机会,通过前期技术论证,采用更换U型管[U型管的规格:¢31.8×2.9(壁厚) 长度为220mm]的办法,同时恢复封填直管径。
PHA、PHB锅炉更换U型管各44根,PHA直管道恢复34根。
由于更换受热面较多,因此需进行水压、煮炉、冲洗、吹扫,现将方案制定,恳请专家指导,从而保障机组投运后安全。
一、水压试验1)、PH锅炉补水从AQC省煤器旁路走,关闭AQC汽包补水手动阀,关闭省煤器温度调节阀前的手动阀,同时将PH锅炉安全阀与水位计隔离;2)、锅炉给水泵向PH锅炉供水,当水从汽包排气阀流出时,关闭汽包排气阀;3)、水压试验升压由给水泵完成,升压速率每分钟0.1-0.3Mpa;4)、当水压试验压力升至锅炉最高工作压力(1.5MPa),升压暂时停止并检查确认此次受热面焊接部位,之后升压至试验压力(2.3MPa);5)、当水压升至试验压力后,保持20分钟,其间压力下降- 1 -不应超过0.05Mpa,再次降至工作压力下进行检查。
6)、水压试验时,如果发现有泄露的地方,停止补水并修补泄露的地方。
当修补结束后,继续按上述操作进行试验,直至泄露完成停止。
7)、降压速率与升压速率一致。
二、碱煮炉1)、根据PH(A-A)锅炉炉水体积(87m3),NaOH和Na3PO4 比例为4:1,混合物取2Kg/m3。
药品数量如下:NaOH为440Kg(液体,浓度32%)、NA3PO4 为35Kg,联氨为72.5Kg。
2)、将药品溶解成溶液后加入汽包内,加药时锅炉应在低水位。
煮炉时药液不允许进入蒸气、过热气管道内。
3)、缓慢升压0.2-0.3Mpa,额定负荷5%时煮炉12h,升压0.4-0.5Mpa,保压排污8h,升压0.6-0.7 Mpa,保压排污8h4)、碱煮炉过程中通过间断性排污,连续性用纯水进行臵换锅炉用水,定期记录炉水PH值、电导率(电导率在500us/cm 以下),PH值在7-9之间煮炉结束。
烘炉和煮炉工艺规程

烘炉和煮炉工艺规程编制日期审查日期批准日期1.适用范围:本文件适用锅炉安装工程的烘炉和煮炉的施工。
2.烘炉和煮炉施工方案可以是锅炉制造商提供或本公司提供,可在锅炉制造商的技术人员的指导下进行。
3.烘炉3.1烘炉的目的:新装、移装、改造或大修后的锅炉,以及长期停用的锅炉,由于砖墙和灰缝中含有较多水份,如果在投入运行前不进行干燥处理,则在点火受热后,水份大量蒸发形成蒸汽,由于体积膨胀而使砖墙裂缝变形,甚至倒塌。
因此,需要通过烘炉除去水分。
3.2烘炉前的条件3.2.1锅炉及其水处理、汽水、排污、输煤、除渣、送风、除尘、照明、循环冷却水等系统均应安装完毕,并经试运转合格。
3.2.2炉墙砌筑和绝热工程结束,并经炉体漏风检验合格,全部清理好炉膛炉排、灰斗、渣机、烟道等.3.2.3水位表、压力表、测温仪表等烘炉需用的热工和电气仪表均应安装和试验完毕. 3.2.4锅炉给水应符合现行国家标准《低压锅炉水质标准》的规定.3.2.5锅筒和集箱上的膨胀指示器应安装完毕,在冷状态下应调整到零位。
3.2.6炉墙上的测温点或灰浆取样点应设置完毕.3.2.7应有烘炉升温曲线图。
3.2.8管道、风道、烟道、灰道、阀门及挡板均应标明介质流向、开启方向和开度指示。
3.2.9做好烘炉的组织工作,并根据炉型结构制定烘炉的操作程序,在整个烘炉过程中应有专人负责。
3.3烘炉前的检查3.3.1内部检查a).对锅筒、集箱内部检查、有无遗留工具杂物等.检查内壁有无腐蚀、结水垢,并做好记录。
b).检查沦内装置;如汽水分离器、进水管、液面排污管、加药管等是否完好。
c).检查人孔、手孔是否完好。
d).炉膛内部检查;炉墙、拱砖、隔火墙是否平整、无裂纹、炉内受压元件表面是否完好,管子和炉墙、炉墙与炉墙间连接处是否用石棉填装好,留有膨胀位。
3.3.2外部检查a)检查受压元件外部有无损伤、人孔、手孔、检查孔等是否装好。
b)检查外墙质量,炉门、灰门、看火门等是否装好、并应作漏风检查。
锅炉的烘炉和煮炉操作规程

锅炉的烘炉和煮炉操作规程锅炉是一种重要的能源设备,其烘炉和煮炉操作是关乎安全和效率的重要环节。
下面给出一份锅炉烘炉和煮炉操作规程,供参考。
1. 烘炉操作规程1.1 仔细检查烘炉和附件:在操作烘炉之前,首先要对烘炉及其附件进行仔细检查,确保设备正常工作。
检查操作员应仔细检查炉内是否有杂物,检查燃烧器是否正常,检查炉体是否有漏气现象。
1.2 清除炉内杂物:炉内应清除杂物,以免影响炉内烘炉效果和燃烧器正常工作。
同时还要注意清除炉膛内积灰,避免积灰过多影响热交换效果。
1.3 炉体预热:在启动烘炉之前,必须进行炉体预热操作。
首先关闭燃烧器,然后使用辅助燃烧器进行预热,以免炉体温度骤然升高影响炉膛结构。
1.4 点火:预热完成后,可启动燃烧器进行点火。
点火前需检查燃烧器是否正常,燃料是否足够,炉蓄火箱内是否有火。
1.5 控制燃烧:燃烧器点火成功后,需要根据工艺要求调节燃烧器的燃烧强度,以保证炉内温度和湿度符合要求。
此外,还需对燃料供给进行控制,以确保炉内的燃烧效果良好。
1.6 炉内温度调节:在烘炉操作过程中,炉内温度的调节是非常重要的。
操作员需根据工艺要求,调节燃烧器的燃烧强度,以达到所需的温度。
调节过程中需注意监测炉内温度变化,及时采取措施进行调整。
1.7 炉内湿度调节:一些特殊工艺要求需要炉内湿度的调节。
在操作过程中,操作员需根据工艺要求,控制喷水装置,以调节炉内湿度。
1.8 炉内冷却:当烘炉操作完成后,需进行炉内冷却。
关闭燃烧器,打开烟囱风门,以加快炉内热量的散发。
同时,操作员需对炉体进行清洗和检查,以确保下次操作的安全和顺利。
2. 煮炉操作规程2.1 组织人员:煮炉操作需要足够的操作人员,以确保操作的安全和顺利进行。
组织人员时需要考虑到煮炉时间、炉容大小、操作难度等因素。
2.2 安全检查:在煮炉操作之前,需要对炉体及其附件进行安全检查。
检查炉体是否有漏气现象,是否有杂物,检查燃烧器是否正常等。
此外,还需检查水位、水压及安全阀等,确保设备正常工作。
热锅炉操作规程
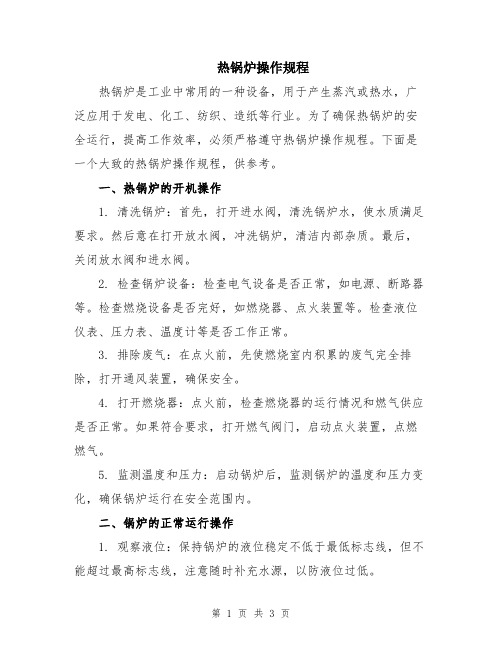
热锅炉操作规程热锅炉是工业中常用的一种设备,用于产生蒸汽或热水,广泛应用于发电、化工、纺织、造纸等行业。
为了确保热锅炉的安全运行,提高工作效率,必须严格遵守热锅炉操作规程。
下面是一个大致的热锅炉操作规程,供参考。
一、热锅炉的开机操作1. 清洗锅炉:首先,打开进水阀,清洗锅炉水,使水质满足要求。
然后意在打开放水阀,冲洗锅炉,清洁内部杂质。
最后,关闭放水阀和进水阀。
2. 检查锅炉设备:检查电气设备是否正常,如电源、断路器等。
检查燃烧设备是否完好,如燃烧器、点火装置等。
检查液位仪表、压力表、温度计等是否工作正常。
3. 排除废气:在点火前,先使燃烧室内积累的废气完全排除,打开通风装置,确保安全。
4. 打开燃烧器:点火前,检查燃烧器的运行情况和燃气供应是否正常。
如果符合要求,打开燃气阀门,启动点火装置,点燃燃气。
5. 监测温度和压力:启动锅炉后,监测锅炉的温度和压力变化,确保锅炉运行在安全范围内。
二、锅炉的正常运行操作1. 观察液位:保持锅炉的液位稳定不低于最低标志线,但不能超过最高标志线,注意随时补充水源,以防液位过低。
2. 观察压力:保持锅炉的压力稳定在规定范围内,如果压力过高或过低,应及时调整。
3. 调整燃烧器:根据锅炉的负荷需求,调整燃烧器的燃烧效率,以保持锅炉的稳定运行。
4. 清洗锅炉:定期清洗锅炉内部的污垢和沉积物,以保证加热效果和安全运行。
5. 维护设备:定期检查锅炉设备的电气和机械部件是否正常,如电源、阀门、泵等,并及时更换磨损和老化的部件。
三、熄火和停机操作1. 熄火操作:首先,关闭燃气阀门,切断燃气供应。
然后,关闭通风装置,停止空气进入。
最后,打开排烟装置,将烟气排出锅炉。
2. 停机操作:在熄火操作后,等待锅炉温度和压力降到安全范围内。
然后,关闭水源,停止供水。
最后,关闭电源,停止锅炉的电力供应。
四、应急处理1. 发生故障或异常情况时,应立即停止锅炉运行,并报告相关人员。
2. 在处理故障或异常时,必须佩戴个人防护装备,严禁单独操作、违规操作。
- 1、下载文档前请自行甄别文档内容的完整性,平台不提供额外的编辑、内容补充、找答案等附加服务。
- 2、"仅部分预览"的文档,不可在线预览部分如存在完整性等问题,可反馈申请退款(可完整预览的文档不适用该条件!)。
- 3、如文档侵犯您的权益,请联系客服反馈,我们会尽快为您处理(人工客服工作时间:9:00-18:30)。
启动锅炉冲洗、吹扫、烘炉、煮炉工艺
1、目的与范围
新安装的锅炉范围内的给水、减温水和主蒸汽管道系统,在供水与供汽之前必须进行冲洗和吹扫,以消除管道内的杂物和锈皮,尤其对蒸汽管道更应重视。
锅炉给水管道的冲洗范围包括给水操作台直到省煤器前,减温器一般不参加冲洗,以免杂物堵塞。
蒸汽管道的冲洗一般均在煮炉后进行。
2、冲洗、吹扫准备工作
2.1蒸汽吹洗是利用蒸汽压力产生高速汽流将杂物冲走,同时依靠冲洗时的高温蒸汽或管壁温度的升高和变化,使附着于管路内壁的杂物脱落并吹出。
2.2用水冲洗时,其水质宜为除盐水或软化水,水力冲洗应连续进行,并尽量加大管内流量,管内的平均流速一般不应低于1m/s。
大口径管不能满足要求时宜采用密闭循环的水力冲洗方式,管内流速应达到或接近管道正常运行的流速。
2.3蒸汽吹洗时汽流对异物的冲刷力应大于额定工况时汽流的冲刷力。
吹管系数(这两种冲刷力之比)为:
K=GC/(G0C0)= G2V/(G02V0)≥1~1.5
≥1~1.5
K=△P/△P
式中:G、G0——吹管和额定工况时蒸汽流量;
C、C0——吹管和额定工况时蒸汽流速;
V、V0——吹管和额定工况时蒸汽比容;
——吹管和额定工况小区段压降。
△P、△P
吹洗时的控制参数可通过预先计算,或吹洗时实际测量决定,当吹洗时控制门全开(直流锅炉纯直流吹洗时除外)后,过热器出口压力值对于3.82/450(Mpa/℃)的中压锅炉应为1Mpa,在上述数值时,一般即可满足各处吹管系数大于1的要求,这时相应的锅炉蒸发量为60%~70%额定蒸发量。
汽包锅炉吹洗时的压力下降值还应控制在饱和温度下降值不大于42℃的范围以内。
2.4主蒸汽管吹洗。
①吹洗前应将蒸汽管路的末端安装一段临时管路,作为脏污蒸汽排入大气之用,
临时管路的截面积应大于或等于被吹管的截面积,否则节流过大或使蒸汽流速降低,不能达到冲洗的效果。
②临时管路应通到室外,并安装牢固,排汽管口应朝上30o~45o向大气排放。
③管路上的流量表(流量孔板)在吹管前不要安装,否则将使吹洗效果降低并损伤孔板。
④吹洗管路与不吹洗管路之间应加以隔绝。
⑤管路安装应牢固,连接方式应正确,除控制阀门外吹洗管路上的阀门应在全开
位置。
3、吹管方法
管道的冲洗和吹扫应参照DL/T5047-95《电力建设施工及验收技术规范(锅炉机组篇)》10.5节管道的冲洗和吹扫、DL5031-94《电力建设施工及验收技术规范(管道篇)》6.2节管道系统的清洗规定中的有关要求进行。
对于一般中小型锅炉,吹洗管路一般采用降压法,利用锅炉工质、金属及炉墙的蓄热短时释放出来,提高吹洗流量的方法。
吹洗时,锅炉升高到一定压力后,保持一定的燃料,尽快全开控制阀(最好采用电动阀)利用压力降产生的附加蒸发量增大冲洗流量,当压力降下降到一定值后,关闭控制阀重新升压,准备再次冲洗。
吹洗过程中,至少应有一次停炉冷却(时间12以上),冷却过热器及其管道,以提高吹洗效果。
4、吹洗质量标准
通过对装在临时排汽管内(或排汽口处)的靶板检查,以判断冲洗质量,靶板一般用铝板制作,宽度为装设靶板处管道内径的10%左右,长度等于管子内径,装设方向应对正汽流冲击方向。
在保证吹管系数至少大于1的前提下,连续两次更换靶板检查,靶板上冲击斑痕粒度不大于0.8mm,且肉眼观察斑痕不多于8点即认为吹洗合格。
管道冲洗和吹扫完后,应整理记录,办理签证。
三、烘炉(暖炉)
新安装锅炉和连续停用3个月以上都应进行烘炉(暖炉);
1、烘炉前的准备工作
编制烘炉方案及烘炉曲线,对参加人员进行技术交底,并准备好有关烘炉记录。
炉墙上布置好测温点或取样点,并准备好温度计或取样工具。
2、烘炉
本锅炉采用火焰烘炉法进行烘炉,其中前期为开火种阀小火烘炉,后期~15%燃烧器负荷烘炉。
前期烘炉阶段(小火):首先开启引风机前调节门1/5到1/6左右,点燃燃烧器小火,根据升温的情况调整火焰的大小,使炉膛保持微负压,烟气缓慢流动,根据各测点显示数据,然后逐渐加大火焰,以过热器后部的烟气温度为监控调节值。
后期烘炉阶段(~12.5%燃烧器负荷):当用小火已不能使过热器后温度再提高的时候(一般为2-3天)应加大燃料投入量烘炉,并启动引风机、逐步增大送风量,加强燃烧,使烟气温度不断提高。
3、烘炉时间的温度控制
烘炉期间,控制温度很重要,升温的速度对烘炉的效果有着直接影响,因此,采用测量过热器后部的烟气温度的办法来控制燃料供给量及送、引风量。
第一天温升不得超过50℃,以后每天升温不得超过30℃,每小时不得超过10℃,烘炉后期,烟温不得超过220℃。
在最高温度范围内,烘炉持续时间不得少于24小时。
如果炉墙特别潮湿应适当减慢温升速度。
4、控制燃烧火焰
烘炉时燃烧要均匀,按时记录温度读数,并且要注意观察炉体膨胀情况和炉墙情况,以便出现异常时及时处理。
5、及时排出水蒸汽
为了及时排出烘炉期间产生的水蒸汽,在烘炉时,应打开上部检查门,当发现炉墙的温度比较大时,还应减缓升温速度并加强通风,以便使炉墙中的水分及时蒸发并顺利排出。
6、烘炉时间
烘炉时间一般为5-7天,究竟多少天数适宜,要根据炉墙的具体情况,当时当地的气候条件等因素具体确定。
7、烘炉的合格标准
7.1 炉墙经烘烤后不应有变形和裂纹,混凝土不得有塌落等缺陷。
7.2 凡达到下列规定中任一种标准时,即认为达到合格。
7.2.1 炉墙灰浆试样法
在过热器位置的炉墙中部、下部位置分别取耐火砖的丁字交叉缝处的灰浆50g,
若其含水率小于2.5%,则为合格。
7.2.2 测温法
在过热器炉墙耐火砖与隔热层接合处设测温点,而当此点的温度达到50℃时,并继续保持48小时。
用测温法烘炉时,要定期观察测点的温度,做好记录,并给出温升曲线,存入锅炉技术档案中。
四、煮炉
煮炉在烘炉结束后进行,煮炉目的就是要清除锅炉受热面内表面的油污及铁锈等杂质,保证锅炉炉水品质,确保锅炉在安全、经济工况下正常运行。
本锅炉的煮
炉采用氢氧化钠(NaOH)和磷酸三钠(Na
3PO
4
.12H
2
O),其加药量均为2-3公斤/
每吨锅水,配制成~20%的均匀溶液加入锅内,不得将药品直接加入锅炉。
1、煮炉前的准备
1.1人员及工器具准备
参加煮炉的人员确定之后,要明确分工,使之熟悉煮炉要点,在煮炉之前,要将胶手套,防护眼镜、口罩等防护用品准备齐全。
操作地点应有清水,急救药品和纱布,以备急用。
1.2药品准备
准备150kg氢氧化钠(NaOH)和200kg磷酸三钠(Na
3PO
4
.12H
2
O),将其中65kg
氢氧化钠(NaOH)和85kg磷酸三钠(Na
3PO
4
.12H
2
O)加400kg水溶解,配制成浓度
为~20%的药液。
2、煮炉的方法及要求
2.1烘炉末期,当炉墙红砖灰浆的含水率降至10%以下,或当过热器耐火砖外侧温度达到50℃时,即可进行煮炉。
2.2 向锅炉内加药
锅炉处在最低水位时,通过上锅筒加药管路系统一次性加入配制成的浓度为~20%的药液。
2.3 煮炉时间及压力要求
2.3.1 加药后升压到0.3-0.4Mpa左右,保持4小时。
2.3.2 在0.3-0.4Mpa的压力下煮炉12小时。
2.3.3 在压力1.3Mpa的下,煮炉12小时。
2.3.4在压力1.9Mpa的下,煮炉12小时。
2.3.5 降压至0.3-0.4Mpa煮炉4小时。
2.4 取样化验
煮炉期间应不断地进行炉水取样试验,如碱度低于45毫克当量/升时应及时补药。
2.5 降压排污
煮炉期间,需要排污,应将压力降低。
2.6 换水、清洗及检查
煮炉结束后,应放掉碱水,凡接触药液的阀门都要清洗,然后打开人孔,手孔进行检查,残留的沉淀物要彻底清除。
3、煮炉合格标准
3.1 锅筒、集箱内壁无油垢。
3.2 擦去附着物后,金属表面应无锈斑。
4、煮炉中应注意的事项
4.1 煮炉期间,锅炉应保持在最高水位,以保证被清洗部分浸满洗液,同时,注意不允许让药液进入过热器,过热器吹洗和主蒸汽管道一起进行,药液在过热器存留时间较长,对其腐蚀较严重。
4.2 在煮炉后期,压力已达工作压力的75%,此时要注意检查各部的变化情况,膨胀情况,特别要注意检查锅筒,受热面管子,膨胀节,支吊架,炉墙与锅筒,集箱的接触部位等。
4.3 煮炉期间,应经常检查,受压元件,管道、风烟道的密封情况。
4.4 煮炉期间,前后、左右应对称地进行排污。
煮炉结束后,各管道系统应按要求进行吹扫冲洗。
具体参照DL/T5047-95《电力建设施工及验收技术规范(锅炉机组篇)》和DL5031-94《电力建设施工及验收技术规范(管道篇)》。
五、总体验收
1、锅炉总体验收时,使用单位应报告当地技术监督部门,消防、环保、安装等有关部门派员参加。
经总体验收合格,领取当地锅炉压力容器安全监察机关核发的使用许可证,方可投入运行。
用户应根据锅炉的数量和对安全性能的要求,设置专门机构和专职人员,加强对锅炉安全技术管理,建立和健全安全管理制度。
2、使用单位对锅炉的运行,必须按照有关规定实行定期检查、保养,并做好其
检查、保养情况的记录。