成型技术基础知识
材料成形技术基础 知识点总结

材料成形技术基础知识点总结滑移系:晶体中一个滑移面及该面上的一个华滑移方向的组合。
纤维组织:金属经冷加工变形后,晶粒形状发生改变,其变化趋势大致与金属的宏观变形一致,若变形程度很大,则晶粒呈现一片纤维状的条纹。
拉深:当凸模下降与坯料接触,坯料首先弯曲,于凸模圆角接触的材料发生胀形形变,凸模继续下降,法兰部分坯料在切向压应力,径向拉应力的作用下沿凹模圆角向直壁流动,形成筒部,进行拉深变形。
自发形核:在单一的液相中,通过自身的结构起伏形成新相核心的过程。
非自发形核:在不均匀的液体中,依靠外来杂质和容器壁面提供衬底而进行形核的过程。
焊接热循环:在焊接热源的作用下,焊件上的某一点温度随时间变化的过程。
焊接残余应力:由于焊接过程中的不均匀加热等因素而导致的焊接结构中存在残余应力。
温度场:加热和冷却过程中某一瞬间温度分布。
材料成型过程中的三种流:材料流,能量流,信息流。
液态金属在凝固和冷却到室温时发生:液态,凝固,固态三种收缩。
减小及消除焊接残余应力的措施有:热处理,温差拉伸,拉力载荷,爆炸冲击,振动法等。
液态金属结构:液态金属有许多近程有序的原子集团组成,原子集团内部原子规则排列,其结构与原固体相似;有大的能量起伏,激烈的热运动和大量的空穴;所有原子集团和空穴时聚时散,时小时大,始终处于瞬息万变的状态。
形核剂应具备哪些条件:失配度小,粗糙度大,分散性好,高温稳定性好。
加工硬化:金属经冷塑性变形后,随着变形程度的增加,金属的强度硬度增加,而塑性韧性降低,这种现象叫。
其成因与位错的交互作用有关,随着塑性变形的进行,位错密度不断增加,位错反应和相互交割加剧,结果产生固定割阶,位错缠结等障碍,以致形成胞装亚结构,使位错难以越过这些障碍而被限制在一定范围内运动,这样,要使金属继续变形就需要不断增加外力才能克服位错间强大的交互作用力。
滑移变形时通常把滑移因子u为0.5或接近0.5的取向称为软取向,把u为0或接近0 的取向称为硬取向。
铸造成形技术-基本知识

(1)流动性 (1)流动性
决定合金流动性的因素主要有: 1、合金的种类:合金的流动性与合金的熔点、 热导率、合金液的粘度等物理性能有关。铸 钢熔点高,在铸型中散热快、凝固快,则流 动性差。
(1)流动性 (1)流动性
2、合金的成分:同种合金中,成分不同的铸造 合金具有不同的结晶特点,对流动性的影响 也不相同。
合金的充型能力及影响因素
1、熔融合金的充型能力: 这里有二个基本概念即充型与充型能力。 ★熔化合金填充铸型的过程,简称充型。 , ★熔融合金充满铸型型腔,获得形状完整,轮廓 清晰铸件的能力,称合金的充型能力。
合金的充型能力及影响因素
2、影响合金充型能力的主要因素有: (1)流动性:流动性指熔融金属的流动能力,它是 影响充型能力的主要因素之一。 (2)浇注条件:指的是浇注温度与充型的压力。 (3)铸型条件:熔融合金充型时,铸型的阻铸型 对合金的冷却作用 都将影响合金的充型能力。
(3)铸型条件 (3)铸型条件
4、铸件结构的壁厚 当铸件壁厚过小,壁厚急剧变化、结构复杂 或有大的水平面时,均会使充型困难。因此 在进行铸件结构设计时,铸件的形状应尽量 简单,壁厚应大于规定的最小壁厚。对于形 状复杂、薄壁、散热面大的铸件,应尽量选 择流动性好的合金或采取其它相应措施。
(3)铸型条件 (3)铸型条件
合金的收缩及影响因素
合金的收缩:
铸件在凝固和冷却过程中,其体积减少的现象称为 收缩。
1)收缩过程及影响因素
收缩可分为液态收缩、凝固收缩和固态收缩,液态 收缩和凝固收缩表现为合金的体积缩小,通常以体积 收缩率表示,它们是铸件产生缩孔、缩松缺陷的基本 原因。 合金的固态收缩,尽管也是体积变化,但它只 引起铸件各部分尺寸的变化。因此,通常用线收缩率 来表示。固态收缩是铸件产生内应力、裂纹和变形等 缺陷的主要原因。
材料成型技术基础知识点总结
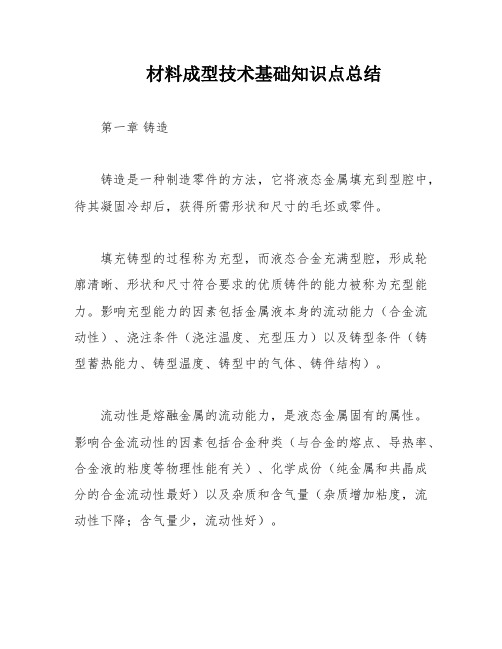
材料成型技术基础知识点总结第一章铸造铸造是一种制造零件的方法,它将液态金属填充到型腔中,待其凝固冷却后,获得所需形状和尺寸的毛坯或零件。
填充铸型的过程称为充型,而液态合金充满型腔,形成轮廓清晰、形状和尺寸符合要求的优质铸件的能力被称为充型能力。
影响充型能力的因素包括金属液本身的流动能力(合金流动性)、浇注条件(浇注温度、充型压力)以及铸型条件(铸型蓄热能力、铸型温度、铸型中的气体、铸件结构)。
流动性是熔融金属的流动能力,是液态金属固有的属性。
影响合金流动性的因素包括合金种类(与合金的熔点、导热率、合金液的粘度等物理性能有关)、化学成份(纯金属和共晶成分的合金流动性最好)以及杂质和含气量(杂质增加粘度,流动性下降;含气量少,流动性好)。
金属的凝固方式包括逐层凝固方式、体积凝固方式或称“糊状凝固方式”以及中间凝固方式。
收缩是液态合金在凝固和冷却过程中,体积和尺寸减小的现象。
收缩能使铸件产生缩孔、缩松、裂纹、变形和内应力等缺陷。
合金的收缩可分为三个阶段:液态收缩、凝固收缩和固态收缩。
液态收缩和凝固收缩通常以体积收缩率表示,是铸件产生缩孔、缩松缺陷的基本原因。
合金的固态收缩通常用线收缩率来表示,是铸件产生内应力、裂纹和变形等缺陷的主要原因。
影响收缩的因素包括化学成分(碳素钢随含碳量增加,凝固收缩增加,而固态收缩略减)、浇注温度(浇注温度愈高,过热度愈大,合金的液态收缩增加)、铸件结构(铸型中的铸件冷却时,因形状和尺寸不同,各部分的冷却速度不同,结果对铸件收缩产生阻碍)以及铸型和型芯对铸件的收缩也产生机械阻力。
缩孔和缩松是铸件凝固结束后常常在某些部位出现孔洞,按照孔洞的大小和分布可分为缩孔和缩松。
缩孔的形成主要出现在金属在恒温或很窄温度范围内结晶,铸件壁呈逐层凝固方式的条件下。
缩松的形成主要出现在呈糊状凝固方式的合金中或断面较大的铸件壁中,是被树枝状晶体分隔开的液体区难以得到补缩所致。
合金的液态收缩和凝固收缩越大,浇注温度越高,铸件的壁越厚,缩孔的容积就越大。
工程材料与成形技术基础总结

工程材料与成形技术基础主要内容1、工程材料的分类工程材料一般可分为金属材料、高分子材料、陶瓷材料和复合材料等几大类。
2、金属材料的主要性能(1)力学性能是金属材料重要的使用性能,主要有:弹性、塑性、刚度、强度、硬度、冲击韧性、疲劳强度、断裂韧性等,要求掌握各种性能的定义。
(2) 常用的力学性能指标有:弹性极限(σe )、屈服强度(σs ,σ0.2 )、抗拉强度(σb )、延伸率(δ)、断面收缩率(φ)、冲击韧性(αk )、硬度(HB ,HRC ,HV )和疲劳强度(σ-1)等。
3、掌握金属材料的物理性能、化学性能和工艺性能的概念。
4、名词解释:(1)、合金(2)组元(3)固溶体(4)相图(5)金属化合物(6)结晶(7)晶体(8)晶格(9)晶面(10)晶胞(11)固溶强化(12)金属热处理(13)退火(14)正火(15)淬火(16)回火(17)调质处理5、铁碳合金的基本组织:铁素体、奥氏体、渗碳体、珠光体和莱氏体。
6、掌握铁碳合金相图中的特性点和特性线的含义,要求默画铁碳合金相图。
7、了解铁碳合金中典型合金的结晶过程分析。
8、掌握铁碳合金的成分、组织和性能的变化规律。
9、掌握金属热处理的定义及作用。
10、重点掌握常用的金属热处理工艺方法的定义、目的、特点及应用。
常用热处理工艺包括退火、正火、淬火、回火及表面热处理和表面化学热处理。
11、了解钢在加热和冷却时的转变过程。
12、掌握常用金属材料的分类。
重点掌握碳钢的分类(按质量、用途、含碳量)、铸铁的分类(两种分类法)和合金钢的分类。
13、掌握碳钢、铸铁、合金钢的编号方法、成分、性能和应用。
能正确选用螺栓、齿轮、轴、床身、箱体、弹簧、模具、刀具等典型零件的相关材料(名称和编号)。
14、了解机械零件选材的一般原则。
第二部分材料成形工艺基础一、铸造1、了解合金的铸造性能及相关影响因素。
2、了解常见铸件缺陷及产生的主要原因。
3、掌握砂型铸造的工艺过程及应用范围。
18粉体成型的基本方法和过程

过程特点: ①随着压制力的继续增大,当压力达到和超过粉末颗粒的强度极限,粉末颗粒 将发生塑形变形(对于脆性粉末来说,不发生碎塑性变形而出现脆性断裂), 直到达到具有一定密度的坯块。 ②由于接近加压端面的部分压力最大,远离加压端面压力逐渐降低,这种压 力分布的不均匀性造成了压坯各个部分粉末致密化不均匀。
3、去除压力,施加脱模压力
现象: ①去除压力后,压坯仍会紧紧的固定在钢压膜内
②压坯中聚集的内应力使压坯产生弹性后效现象
三、影响粉体压制成形的因素
1、粉末本身的特性起关键性作用
压制成形是一个十 分复杂的过程 Nhomakorabea2、 压制力起着决定性的作用
金属材料工程基础知识 一、粉体成型的原理 二、粉体成型的过程 三、影响粉体压制成形的因素
的预成形坯中,底部和顶部的密度有很大差异,这种密 度差随预成形高度的增加而增加,随直径的增大而减小。
解决方法:若使用润滑剂可以减少粉粉末批量与莫蒂之间的摩
擦力,也可以降低沿高度方向的密度不均匀程度
双向压制
浮动凹模压制
轧制成形
二、粉体成型的过程
1、将松散的粉末装在钢压膜内 2、对钢压模中粉末施加压力
金属材料工程第十八讲
胡燕燕
一、粉体成型的原理
粉体成型是指将粉末状的材料制成具有一定形状,尺寸,孔隙 率以及强度的预成形坯体的加工过程。
成型方法
不同材料因其物 理化学特性不同, 所采用的成型方 法与技术并不完 全相同
模压成形 钢模压制成形
等静压成形
单向压制 是指压力施加在粉末配料的上顶部
特点:粉末批料与凹模之间的摩擦,使得在经单向压制所得到
工程材料与成形技术基础的感想

工程材料与成形技术基础的感想
在学习工程材料与成形技术基础的过程中,我收获了很多知识和体会。
首先,我深刻认识到了材料的重要性。
不同的材料具有不同的特点和用途,对于不同的工程项目,需要选用不同的材料。
了解材料的特性和性能,可以帮助我们更好地选择和使用材料,提高工程的质量和效率。
其次,我学习了成形技术的基本原理和方法。
成形技术是制造过程中非常重要的一环,它能够将材料加工成所需的形状和尺寸,为后续的加工和使用奠定基础。
掌握成形技术的基本原理和方法,可以帮助我们更好地理解制造过程,提高工艺的稳定性和效率。
最后,我认识到了实践的重要性。
学习知识不是为了停留在书本上,而是要应用到实际中去。
在课堂上,我们不仅学习了理论知识,还进行了实验和实践练习,这让我更加深入地了解了材料和成形技术的基础知识。
总之,学习工程材料与成形技术基础是我大学学习生涯中的一次宝贵经历。
通过这门课程的学习,我不仅扩展了知识面,还学会了更多的思考和应用能力。
我相信,这些知识和经验将会在我今后的学习和工作中发挥重要作用。
- 1 -。
成形工艺基础--切削工艺知识讲解

成形工艺基础--切削工艺知识讲解切削工艺是指利用刀具与工件之间的相对运动来剥除工件材料的一种加工方法。
它常用于工件形状加工、尺寸精加工以及表面质量要求较高的加工过程中。
切削工艺的应用范围广泛,涵盖了金属加工、塑料加工、木材加工等多个领域。
切削工艺基础主要包括切削原理、切削力、工艺参数及切削液等方面的知识。
首先,切削原理是切削工艺的核心。
切削过程中,刀具与工件之间形成切削速度,刀具对工件施加切削力,工件材料被剥除。
切削时,刀具一般沿着切削方向作直线运动,与工件表面相切,将工件材料切削下来。
切削力是切削工艺中一个重要的参数。
切削力包括切削力的大小和方向。
切削力的大小会直接影响到刀具寿命和加工质量。
大的切削力会导致刀具磨损,降低刀具寿命。
切削力的方向对于刀具的合理设计和工件材料的选择以及加工工艺的确定具有重要的指导意义。
工艺参数是切削工艺中需要关注的另一个重要方面。
工艺参数包括切削速度、进给速度和切削深度等。
切削速度决定了切削过程的快慢,进给速度决定了每根刀齿在单位时间内所切削的长度,切削深度决定了每次切削所剥离的材料量。
合理的工艺参数可以提高生产效率和工件质量。
切削液是一种重要的辅助工艺。
切削液主要用于冷却刀具和工件,减少切削过程中的热量积聚,降低切削温度,防止刀具变形和磨损,提高刀具寿命。
切削液还能够冲洗切屑,减少切削过程中的摩擦和磨损,提高切削质量。
总之,切削工艺是一门重要的制造工艺,在现代工业生产中起着至关重要的作用。
了解切削工艺的基本知识,可以帮助工程师们更好地设计和实施切削工艺,提高生产效率和产品质量。
切削工艺是现代制造工业中最主要的金属加工方法之一,广泛应用于各个领域,如汽车制造、航空航天、电子设备等。
切削工艺的发展与进步在很大程度上推动了现代工业的发展。
本文将进一步介绍切削工艺的相关知识,包括切削原理、切削工具、切削材料及切削方法。
切削原理是切削工艺的核心,它是指刀具对工件施加的力在切削区域产生剪切应力,将工件材料剪断的过程。
电磁成形原理

电磁成形原理电磁成形原理一、引言电磁成形是一种利用电磁力进行金属成形的新型加工技术,它具有高效、高精度、无损等优点。
本文将介绍电磁成形的原理。
二、电磁场与电流在介绍电磁成形原理之前,需要先了解一些基础知识。
电磁场是指存在于空间中的一种物理场,它由带电粒子所激发而产生。
当一个导体通过一个变化的磁场时,会在导体内部产生感应电流。
这个过程就是基于法拉第定律的。
三、电磁成形的基本原理1. 理论基础根据安培定律和洛伦兹力定律可以得出:当通过导体中有一定大小和方向的电流时,会在该导体周围产生一个强大的磁场,并且该导体会受到一个力,这个力就是洛伦兹力。
2. 作用方式利用洛伦兹力可以实现金属板材或管材等金属材料的成形。
具体来说,就是将待加工的金属放置在两个带有线圈的铁芯之间,并通电使其形成磁场,这个磁场会在金属中产生一个感应电流,从而在金属中产生一个洛伦兹力。
这个洛伦兹力会使金属板材或管材等金属材料发生变形。
3. 成形方式根据不同的加工需要,可以设计不同的线圈结构和通电方式。
例如,可以通过改变线圈的布局、大小和方向来控制磁场的分布和强度;也可以通过改变通电方式来控制加工速度和加工形状。
四、电磁成形的优点1. 高效相比传统成形技术,电磁成形具有高效的优点。
它可以在很短的时间内完成金属件的成型,从而提高了生产效率。
2. 高精度由于电磁成形是利用电流产生洛伦兹力进行成型的,因此可以实现高精度的加工。
这种加工方式可以避免传统冲压等加工方式中由于模具损耗等原因带来的误差。
3. 无损传统冲压等加工方式可能会对金属材料造成一定程度上的损伤,而电磁成形则不会对金属材料造成任何损伤。
这就保证了金属材料的质量和性能。
五、电磁成形的应用电磁成形技术可以应用于各种金属材料的成形,例如钢、铝、铜等。
它可以用于制造汽车零部件、航空航天部件等。
此外,电磁成形还可以用于制造微型器件等。
六、总结电磁成形是一种利用电磁力进行金属成形的新型加工技术。
材料成形技术基础知识点总结
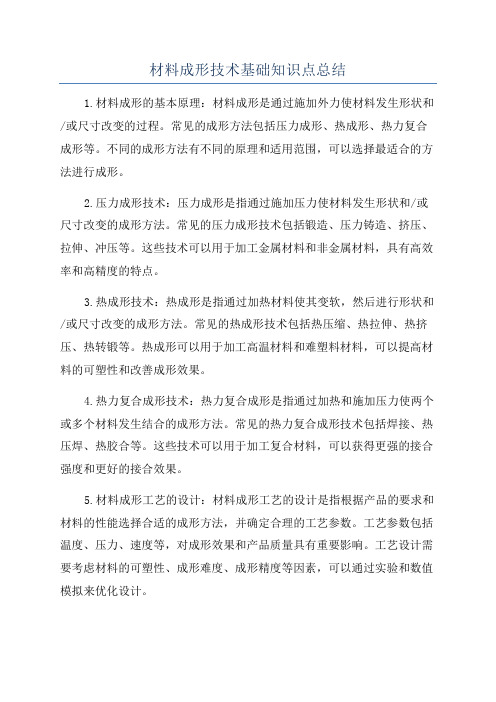
材料成形技术基础知识点总结1.材料成形的基本原理:材料成形是通过施加外力使材料发生形状和/或尺寸改变的过程。
常见的成形方法包括压力成形、热成形、热力复合成形等。
不同的成形方法有不同的原理和适用范围,可以选择最适合的方法进行成形。
2.压力成形技术:压力成形是指通过施加压力使材料发生形状和/或尺寸改变的成形方法。
常见的压力成形技术包括锻造、压力铸造、挤压、拉伸、冲压等。
这些技术可以用于加工金属材料和非金属材料,具有高效率和高精度的特点。
3.热成形技术:热成形是指通过加热材料使其变软,然后进行形状和/或尺寸改变的成形方法。
常见的热成形技术包括热压缩、热拉伸、热挤压、热转锻等。
热成形可以用于加工高温材料和难塑料材料,可以提高材料的可塑性和改善成形效果。
4.热力复合成形技术:热力复合成形是指通过加热和施加压力使两个或多个材料发生结合的成形方法。
常见的热力复合成形技术包括焊接、热压焊、热胶合等。
这些技术可以用于加工复合材料,可以获得更强的接合强度和更好的接合效果。
5.材料成形工艺的设计:材料成形工艺的设计是指根据产品的要求和材料的性能选择合适的成形方法,并确定合理的工艺参数。
工艺参数包括温度、压力、速度等,对成形效果和产品质量具有重要影响。
工艺设计需要考虑材料的可塑性、成形难度、成形精度等因素,可以通过实验和数值模拟来优化设计。
6.材料成形工具的设计与制造:材料成形工具是实现成形过程的重要设备,需要根据产品的形状和尺寸设计相应的工具。
工具设计包括毛坯设计、凸模设计、模具结构设计等。
材料成形工具的制造需要精密的加工工艺和高质量的材料,可以采用数控加工、电火花等先进技术来提高工具的精度和寿命。
7.材料成形过程的监测与控制:材料成形过程需要对温度、压力、力量、速度等进行监测和控制,以确保成形效果和产品质量的稳定。
常用的监测和控制技术包括传感器、自动控制系统等。
这些技术可以实时监测成形过程的参数,并根据需求调整工艺参数,以达到最佳的成形效果。
工程材料及成形技术基础复习重点完整版
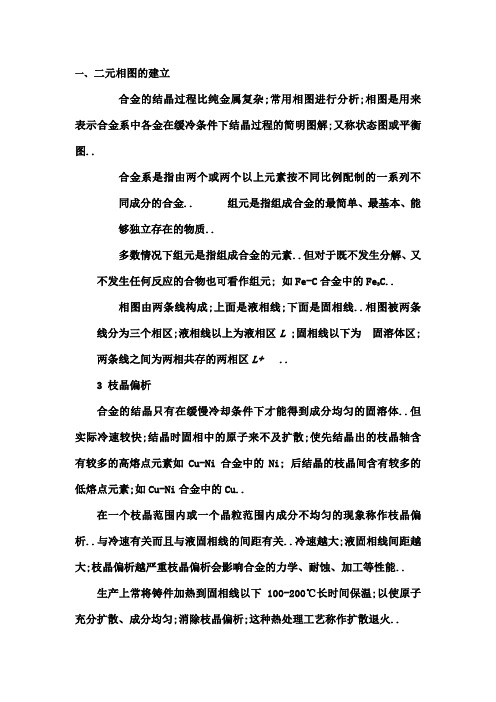
一、二元相图的建立合金的结晶过程比纯金属复杂;常用相图进行分析;相图是用来表示合金系中各金在缓冷条件下结晶过程的简明图解;又称状态图或平衡图..合金系是指由两个或两个以上元素按不同比例配制的一系列不同成分的合金.. 组元是指组成合金的最简单、最基本、能够独立存在的物质..多数情况下组元是指组成合金的元素..但对于既不发生分解、又C..不发生任何反应的合物也可看作组元; 如Fe-C合金中的Fe3相图由两条线构成;上面是液相线;下面是固相线..相图被两条线分为三个相区;液相线以上为液相区L ;固相线以下为固溶体区;两条线之间为两相共存的两相区L+ ..3 枝晶偏析合金的结晶只有在缓慢冷却条件下才能得到成分均匀的固溶体..但实际冷速较快;结晶时固相中的原子来不及扩散;使先结晶出的枝晶轴含有较多的高熔点元素如Cu-Ni合金中的Ni; 后结晶的枝晶间含有较多的低熔点元素;如Cu-Ni合金中的Cu..在一个枝晶范围内或一个晶粒范围内成分不均匀的现象称作枝晶偏析..与冷速有关而且与液固相线的间距有关..冷速越大;液固相线间距越大;枝晶偏析越严重枝晶偏析会影响合金的力学、耐蚀、加工等性能..生产上常将铸件加热到固相线以下100-200℃长时间保温;以使原子充分扩散、成分均匀;消除枝晶偏析;这种热处理工艺称作扩散退火..2、二元共晶相图当两组元在液态下完全互溶;在固态下有限互溶;并发生共晶反应时所构成的相图称作共晶相图..以 Pb-Sn 相图为例进行分析..1 相图分析①相:相图中有L、、三种相; 是溶质Sn在 Pb中的固溶体; 是溶质Pb在Sn中的固溶体..②相区:相图中有三个单相区: L、、;三个两相区: L+ 、L+ 、+ ..③液固相线:液相线AEB;固相线ACEDB..A、B分别为Pb、Sn的熔点..④固溶线: 溶解度点的连线称固溶线..相图中的CF、DG线分别为Sn在 Pb中和 Pb在 Sn中的固溶线..固溶体的溶解度随温度降低而下降..⑤共晶线:水平线CED叫做共晶线..在共晶线对应的温度下183 ℃;E点成分的合金同时结晶出C点成分的固溶体和D点成分的固溶体;形成这两个相的机械混合物LE C+D在一定温度下;由一定成分的液相同时结晶出两个成分和结构都不相同的新固相的转变称作共晶转变或共晶反应..一、铁碳合金的组元和相C1. 组元:Fe、 Fe32. 相⑴铁素体——碳在-Fe中的固溶体称铁素体;用F或表示碳在–Fe中的固溶体用表示;体心立方间隙固溶体..铁素体的溶碳能力很低;在727℃时最大为0.0218%;室温下仅为0.0008%..铁素体的组织为多边形晶粒;性能与纯铁相似..2 奥氏体碳在 -Fe中的固溶体称奥氏体..用A或表示..是面心立方晶格的间隙固溶体..溶碳能力比铁素体大;1148℃时最大为2.11%..组织为不规则多面体晶粒;晶界较直..强度低、塑性好;钢材热加工都在区进行;碳钢室温组织中无奥氏体..3 渗碳体Fe3C含碳6.69%;用Fe3C或Cm表示..Fe3C硬度高、强度低 b35MPa;脆性大;塑性几乎为零..由于碳在 -Fe中的溶解度很小;因而常温下碳在铁碳合金中主要以Fe3C或石墨的形式存在..重要知识点五个重要的成份点: P、S、E、C、F四条重要的线: ECF、PSK、ES、GS三个重要转变: 共晶转变反应式、共析转变反应式、包晶转变本节略二个重要温度: 1148 ℃、727 ℃第一节退火和正火一般零件的工艺路线为:毛坯铸造或锻造→退火或正火→机械粗加工→淬火+回火或表面热处理→机械精加工..退火与正火常作为预备热处理;其目的是为消除毛坯的组织缺陷;或为以后的加工作准备;淬火和回火工艺配合可强化钢材;提高零件使用性能;作为最终热处理..一、退火将工件加热到适当温度;保温一定时间;缓慢冷却热处理工艺目的根据不同情况;退火的作为可归纳为降低硬度;改善钢的成形和切削加工性能;均匀钢的化学成分和组织;消除内应力等..①调整硬度以便进行切削加工;②消除残余内应力;以防止钢件在淬火时产生变形或开裂;③细化晶粒;改善组织;提高力学性能;为最终热处理作准备..1、退火类型1 完全退火完全退火是将工件完全奥氏体化后缓慢冷却;获得接近平衡组织的退火工艺..工艺加热温度为Ac3以上20℃~30℃;保温时间依工件的大小和厚度而定;使工件热透;保证全部得到均匀化的奥氏体;冷却方式可采用随炉缓慢冷却;实际生产时为提高生产率;退火冷却至600℃左右即可出炉空冷..2球化退火工艺球化退火的加热温度为Ac1以上20℃~30℃;采用随炉缓冷;至500℃~600℃后出炉空冷;3去应力退火去除工件塑性变形加工、切削加工或焊接造成的内应力及铸件内存在的残余内应力而进行的退火工艺..工艺去应力退火加热温度较宽;但不超过AC1点;一般在500℃~650℃之间;铸铁件去应力退火温度一般为500℃ ~ 550℃;焊接工件的去应力退火温度一般为500℃ ~600℃..去应力退火的保温时间也要根据工件的截面尺寸和装炉量决定..去应力退火后的冷却应尽量缓慢;以免产生新的应力..4扩散退火为减少铸件或锻坯的化学成分和组织不均匀性;将其加热到略低于固相线固相线以下 100℃~200℃的温度;长时间保温10h~15h;并进行缓慢冷却的热处理工艺;称为扩散退火或均匀化退火..二、正火1、正火的概念工艺正火处理的加热温度通常在Ac3或Accm以上30℃~50℃..对于含有V、Ti、Nb等碳化物形成元素的合金钢;采用更高的加热温度AC3 + 100℃~150℃..正火冷却方式常用的是将钢件从加热炉中取出在空气中自然冷却..对于大件也可采用吹风、喷雾和调节钢件堆放距离等方法控制钢的冷却速度;达到要求的组织和性能..第二节钢的淬火将亚共析钢加热到Ac3以上;共析钢与过共析钢加热到Ac1以上;低于Accm的温度;保温后以大于Vk的速度快速冷却;使奥氏体转变为马氏体或贝氏体的热处理工艺叫淬火..马氏体强化是钢的主要强化手段;因此淬火的目的就是为了获得马氏体;提高钢的机械性能..淬火是钢的最重要的热处理工艺也是热处理中应用最广的工艺之一..1、淬火温度的确定淬火温度即钢的奥氏体化温度;是淬火的主要工艺参数之一..选择淬火温度的原则是获得均匀细小的奥氏体组织..亚共析钢的淬火温度一般为Ac3以上30~50℃;淬火后获得均匀细小的马氏体组织..温度过高;奥氏体晶粒粗大而得到粗大的马氏体组织;而使钢的机械性能恶化;特别是塑性和韧性降低;淬火温度低于Ac3;淬火组织中会保留未溶铁素体;使钢的强度硬度下降..4、钢的淬透性1淬透性与淬硬性的概念钢的淬透性是指奥氏体化后的钢在淬火时获得马氏体的能力也称为淬透层深度;其大小用钢在一定条件下淬火获得的淬硬层深度来表示..淬硬层深度指由工件表面到半马氏体区50%M + 50%P的深度..淬硬性是指钢淬火后所能达到的最高硬度;即硬化能力..淬透性与淬硬层深度的关系同一材料的淬硬层深度与工件尺寸、冷却介质有关..工件尺寸小、介质冷却能力强;淬硬层深.. 淬透性与工件尺寸、冷却介质无关..它只用于不同材料之间的比较;通过尺寸、冷却介质相同时的淬硬层深度来确定的..2淬透性的测定及其表示方法同一材料的淬硬层深度与工件的尺寸;冷却介质有关;工件尺寸小、冷却能力强;淬硬层深;工件尺寸小、介质冷却能力强;淬硬层深;而淬透性与工件尺寸、冷却介质无关;它只用于不同材料之间的比较;是在尺寸、冷却介质相同时;用不同材料的淬硬层深度进行比较的..淬透性常用末端淬火法测定如下图所示;将标准化试样奥氏体化后;对末端进行喷水冷却..然后从水冷段开始;每隔一定距离测量一个硬度值;即可得到试样沿轴向的硬度分布曲线;称为钢的淬透性曲线..即用 表示J 表示末端淬透性;d 表示半马氏体区到水冷端的距离;HRC 为半马氏体区的硬度..3 影响淬透性的因素钢的淬透性取决于临界冷却速度V K ; V K 越小;淬透性越高..V K 取决于C 曲线的位置;C 曲线越靠右;V K 越小..凡是影响C 曲线的因素都是影响淬透性的因素;即除Co 外;凡溶入奥氏体的合金元素都使钢的淬透性提高;奥氏体化温度高、保温时间长也使钢的淬透性提高..影响淬硬层深度的因素淬透性 冷却介质 工件尺寸对于截面承载均匀的重要件;要全部淬透..如连杆、模具等..对HRC J d于承受弯曲、扭转的零件可不必淬透淬硬层深度一般为半径的1/2-1/3;如轴类、齿轮等..淬硬层深度与工件尺寸有关;设计时应注意尺寸效应..第三节钢的回火回火——将淬火钢加热到Ac1以下的某温度保温后冷却的热处理工艺..1、回火的目的消除或减少淬火内应力;防止工件变形或开裂;获得工艺所要求的力学性能;稳定工件尺寸..淬火马氏体和残余奥氏体都是非平衡组织;有自发向平衡组织铁素体加渗碳体转变的倾向..回火可使马氏体和残余奥氏体转变为平衡或接近平衡的组织;防止使用时变形..对于未经淬火的钢;回火是没有意义的;而淬火钢不经回火一般也不能直接使用;为避免淬火件在放置过程中发生变形或开裂;钢件经淬火后应及时回火..3、回火工艺1低温回火<250℃低温回火后得到回火马氏体组织..其目的是降低钢的淬火应力和脆性;回火马氏体具有高的硬度一般为58~64HRC、强度和良好耐磨性..低温回火特别适用于刀具、量具、滚动轴承、渗碳件及高频表面淬火等工求高硬度和耐磨性的工件..2中温回火350-500℃中温回火时发生如下变化;得到T回组织;即为在保持马氏体形态的铁素体基体上分布着细粒状渗碳体的组织..使钢具有高的弹性极限;较高的强度和硬度一般为35 ~ 50HRC;良好的塑性和韧性..中温回火主要用于各种弹性元件及热作模具..3高温回火>500℃高温回火后得到回火索氏体组织;即为在多边性铁素体基体上分布着颗粒状Fe3C的组织 ..工件淬火并高温回火的复合热处理工艺称为调质..高温回火主要适用于中碳结构钢或低合金结构钢制作的曲轴、连杆、螺栓、汽车半轴、等重要的机器零件..4、回火时的性能变化回火时力学性能变化总的趋势是随回火温度提高;钢的强度、硬度下降;塑性、韧性提高..5、回火脆性淬火钢的韧性并不总是随温度升高而提高..在某些温度范围内回火时;会出现冲击韧性下降的现象..1低温回火脆性淬火钢在250℃~350℃范围内回火时出现的脆性叫做低温回火脆性..几乎所有的钢都存在这类脆性..这是一种不可逆回火脆性;目前尚无有效办法完全消除这类回火脆性..所以一般都不在250℃~350℃这个温度范围内回火..2高温回火脆性淬火钢在500℃~650℃范围内回火时出现的脆性称为高温回火脆性;称为第二类回火脆性..这种脆性主要发生在含Cr、Ni、Si、Mn等合金元素的结构钢中..这种脆性与加热、冷却条件有关..加热至600℃以上后;以缓慢的冷却速度通过脆化温度区时;出现脆性;快速通过脆化区时;则不出现脆性..此类回火脆性是可逆的;在出现第二类回火脆性后;重新加热至600℃以上快冷;可消除脆性..第四节钢的表面淬火钢的表面热处理有两大类:一类是表面加热淬火热处理;通过对零件表面快速加热及快速冷却使零件表层获得马氏体组织;从而增强零件的表层硬度;提高其抗磨损性能..另一类是化学热处理;通过改变零件表层的化学成分;从而改变表层的组织;使其表层的机械性能发生变化..1、表面淬火表面具有高的强度、硬度和耐磨性;不易产生疲劳破坏;而心部则要求有足够的塑性和韧性..采用表面淬火可使钢的表面得到强化;满足工件这种“表硬心韧”的性能要求..1 表面淬火目的使表面具有高的硬度、耐磨性和疲劳极限;心部在保持一定的强度、硬度的条件下;具有足够的塑性和韧性..适用于承受弯曲、扭转、摩擦和冲击零件2 表面淬火用材料0.4-0.5%C的中碳钢..含碳量过低;则表面硬度、耐磨性下降含碳量过高;心部韧性下降;铸铁提高其表面耐磨性..3 预备热处理工艺对于结构钢为调质或正火..前者性能高;用于要求高的重要件;后者用于要求不高的普通件..目的①为表面淬火作组织准备②获得最终心部组织..表面淬火后的回火采用低温回火;温度不高于200℃..目的为降低内应力保留淬火高硬度耐磨性..表面淬火+低温回火后的组织:表层组织为M回;心部组织为S回调质或F+S正火..第五节化学热处理化学热处理是将钢件置于一定温度的活性介质中保温;使一种或几种元素渗入它的表面;改变其化学成分和组织;达到改进表面性能;满足技术要求热处理过程..目的1、提高渗层硬度和耐磨性;如渗碳、氮等;2、提高零件接触疲劳强度和提高抗擦伤能力;渗氮等;3、提高零件抗氧化、耐高温性能;如渗入铝、铬等;4、提高零件抗蚀性;如渗入硅、铬等..化学热处理基本过程1介质的分解—即加热时介质中的化合物分子发生分解并释放出活性原子;2工件表面的吸收—即活性原子向固溶体中溶解或与钢中某些元素形成化合物;3原子向内部扩散—即溶入的元素原子在浓度梯度的作用下由表层向钢内部的扩散..1、渗碳原理渗碳是指向钢表面渗入碳原子的过程..渗碳是为了使低碳钢工件含碳量为0.1%~0.25%表面获得高的碳浓度0.85%~1.05%;从而提高工件表面的硬度、耐磨性及疲劳强度;同时保持心部良好的韧性和塑性..若采用中碳以上的钢渗碳;则将降低工件心部的韧性..渗碳主要用于那些对耐磨性要求较高、同时承受较大冲击载荷的零件..2渗碳件用钢一般采用碳质量分数为0.1%~0.25%的低碳钢或低碳合金钢;20、20Cr、20CrMnTi等..可使渗碳件表面高硬度、耐磨;心部高强韧性、承受较大冲击..3渗碳后的热处理及性能渗碳缓冷后组织:表层为P+网状Fe3CⅡ; 心部为F+P;中间为过渡区..渗碳后必须经淬火+低温回火后才能满足使用性能的要求..热处理后使渗碳件表面具有马氏体和碳化物的组织;表面硬度58~64HRC..而心部根据采用钢材淬透性的大小和零件尺寸大小;获得低碳马氏体或其他非马氏体组织;具有心部良好强韧性..常用方法是渗碳缓冷后;重新加热到Ac1+30-50℃淬火+低温回火..表层:M回+颗粒状碳化物+A’少量; 心部:淬透时;M回+F..2、渗氮渗氮是在一定温度下于一定介质中使氮原子渗入工件表层的化学热处理工艺..方法主要有气体渗氮和离子渗氮等..1气体渗氮渗氮温度一般为500~560℃;时间一般为20~50小时;采用氨气NH3 作渗氮介质..氨气在450℃以上温度时即发生分解;产生活性氮原子: 2NH3——3H2+2N2渗氮的特点渗氮件的表面硬度高达;相当于65HRC~72HRC..并可保持到560~600℃而不降低..氮化后钢件不需其他热处理;渗氮件的变形小..渗氮后具有良好的耐腐蚀性能..这是由于渗氮后表面形成致密的氮化物薄膜;气体渗氮所需时间很长;渗氮层也较薄一般为0.3-0.6mm;38CrMoAl钢制压缩机活塞杆为获得0.4-0.6mm的渗氮层深度气体渗氮保温时间需60h左右..氮化缺点工艺复杂;成本高;氮化层薄..用于耐磨性、精度要求高的零件及耐热、耐磨及耐蚀件..第六节铸铁一、铸铁的成分、组织和性能特点1、铸铁的成分特点a. 含碳量理论上含C:2.11%~ 6.69% 的铁碳合金都属于铸铁; 但工业上常用铸铁的含碳量一般在:2.50%~4.00%之间..三、铸铁的分类1、灰口铸铁普通铸铁石墨呈片状;典型灰口铸铁;这类铸铁机械性能不高;但生产工艺简单;价格低廉;工业上所用铸铁几乎全部属于这类铸铁..灰口铸铁又根据第三阶段石墨化程度的不同分为:铁素体灰铁、 F+P灰铁、珠光体灰铁2、白口铸铁炼钢生铁第一、二、三阶段石墨化过程完全被抑制;Fe-C合金完全按照Fe-Fe3CC形式存在组织中存在莱氏体组织;断口呈白亮结晶而得到的铸铁;以Fe3色;故得名白口铸铁..白口铸铁硬脆;主要作为炼钢原料..3、可锻铸铁韧性铸铁;玛钢C分解而得到团石墨呈团絮状;用白口铸铁经长时间高温退火后;Fe3絮状石墨组织的铸铁..由于石墨呈团絮状;对基体的割裂作用比片状石墨小一些;故机械性能尤其冲击韧性高于灰口铸铁..可锻铸铁由于生产工艺复杂;成本较高;应用很少..4、球墨铸铁石墨组织呈球状;这种铸铁强度高;生产工艺比可锻铸铁简单;且可通过热处理进一步提高强度..球墨铸铁既保持了铸铁的特点;又具钢的高强度、高韧性;故应用越来越多..1球化处理与孕育处理Ⅰ球化处理铁水浇铸前;加入一定量的球化剂镁;硅铁-镁;铜-镁系;以促使石墨结晶时生长成为球状的工艺;称为球化处理..Ⅱ孕育处理变质处理球化处理只能在铁水中有石墨核心产生时;才能促使石墨生长成球状;而球化剂都是阻碍石墨化的元素;所以必须进行孕育处理变质处理;往铁水中加入变质剂75% Si-Fe..第七节铝及铝合金1性能特点纯铝银白色金属光泽;密度小2.72;熔点低660.4℃;导电导热性能优良..耐大气腐蚀;易于加工成形 ..具有面心立方晶格..铝合金一般具有有限固溶型共晶相图..可将铝合金分为变形铝合金和铸造铝合金两大类..3形变铝合金的牌号、性能变形铝及铝合金牌号表示方法;国标规定;变形铝及铝合金可直接引用国际四位数字体系牌号或采用国标规定的四位字符牌号..GB 3190-82中的旧牌号表示方法为防锈铝合金:LF +序号硬铝合金: LY +序号超硬铝合金:LC +序号锻铝合金: LD +序号4铸造铝合金牌号、分类Al- Si系:代号为ZL1+两位数字顺序号Al-Cu系:代号为ZL2+两位数字顺序号Al-Mg系:代号为ZL3+两位数字顺序号Al-Zn系:代号为ZL4+两位数字顺序号二、铜及铜合金1性能特点纯铜呈紫红色;又称紫铜;具有面心立方晶格;无同素异构转变;无磁性..纯铜具有优良的导电性和导热性;在大气、淡水和冷凝水中有良好的耐蚀性..塑性好..2黄铜以Zn为主要合金元素的铜合金称为黄铜..黄铜按化学成分可分为普通黄铜和特殊黄铜..按工艺可分为加工黄铜和铸造黄铜..单相黄铜塑性好;常用牌号有H80、H70、H 68..适于制造冷变形零件;如弹壳、冷凝器管等..三七黄铜两相黄铜热塑性好; 强度高..常用牌号有H59、H62..适于制造受力件;如垫圈、弹簧、导管、散热器等..四六黄铜3青铜青铜主要是指Cu-Sn合金..加工青铜的牌号为:Q +主加元素符号及其平均百分含量 + 其他元素平均百分含量.. QSn4-3含4%Sn 3%Zn 常用青铜有锡青铜、铝青铜、铍青铜、硅青铜、铅青铜等..常用牌号有:QSn4-3、QSn6.5-0.4、ZCuSn10Pb1轴承合金制造滑动轴承的轴瓦及其内衬的耐磨合金称为轴承合金..滑动轴承是许多机器设备中对旋转轴起支撑..由轴承体和轴瓦两部分组成..与滚动轴承相比滑动轴承具有承载面积大;工作平稳;无噪音及拆装方便等优点..一、组织性能要求速旋转时;轴瓦与轴颈发生强烈摩擦;承受轴颈施加的交变载荷和冲击力..⑴足够的强韧性;承受交变冲击载荷;⑵较小的热膨胀系数;良好的导热性和耐蚀性;以防止轴与轴瓦之间咬合;⑶较小的摩擦系数;良好的耐磨性和磨合性;以减少轴颈磨损;保证轴与轴瓦良好的跑合..为满足上述性能要求;轴承合金的组织应是软的基体上分布着硬的质点..当轴旋转时;软的基体或质点被磨损而凹陷;减少了轴颈与轴瓦的接触面积;有利于储存润滑油..软基体或质点还能起嵌藏外来硬杂质颗粒的作用;以避免擦伤轴颈..这类组织承受高负荷能力差;属于这类组织的有锡基和铅基轴承合金;又称为巴氏合金babbitt alloy1、锡基轴承合金以锡为主并加入少量锑、铜等元素组成的合金熔点较低;是软基体硬质点组织类型的轴承合金..锡基轴承合金具有较高的耐磨性、导热性、耐蚀性和嵌藏性;摩擦系数和热膨胀系数小;但疲劳强度较低;工作温度不超过150 ℃;价格高..广泛用于重型动力机械;如气轮机、涡轮机和内燃机等大型机器的高速轴瓦..2、铅基轴承合金以铅为主加入少量锑、锡、铜等元素的合金;软基体硬质点型轴承合金;ZChPbSb16Sn16Cu2..铅基轴承合金的强度、硬度、耐蚀性和导热性都不如锡基轴承合金;但其成本低;高温强度好;有自润滑性..常用于低速、低载条件下工作的设备;如汽车、拖拉机曲轴的轴承等..。
材料成形技术基础知识点总结
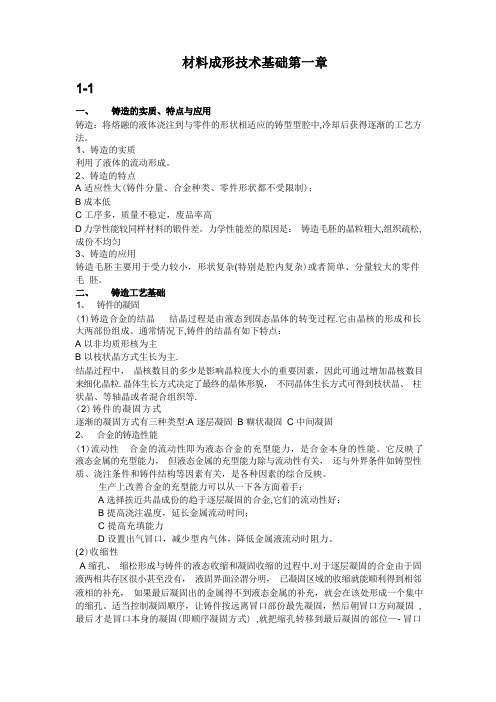
铸造:将熔融的液体浇注到与零件的形状相适应的铸型型腔中,冷却后获得逐渐的工艺方法。
1、铸造的实质利用了液体的流动形成。
2、铸造的特点A 适应性大(铸件分量、合金种类、零件形状都不受限制);B 成本低C 工序多,质量不稳定,废品率高D 力学性能较同样材料的锻件差。
力学性能差的原因是:铸造毛胚的晶粒粗大,组织疏松, 成份不均匀3、铸造的应用铸造毛胚主要用于受力较小,形状复杂(特别是腔内复杂)或者简单、分量较大的零件毛胚。
1、铸件的凝固(1)铸造合金的结晶结晶过程是由液态到固态晶体的转变过程.它由晶核的形成和长大两部份组成。
通常情况下,铸件的结晶有如下特点:A 以非均质形核为主B 以枝状晶方式生长为主.结晶过程中,晶核数目的多少是影响晶粒度大小的重要因素,因此可通过增加晶核数目来细化晶粒. 晶体生长方式决定了最终的晶体形貌,不同晶体生长方式可得到枝状晶、柱状晶、等轴晶或者混合组织等.(2)铸件的凝固方式逐渐的凝固方式有三种类型:A 逐层凝固B 糊状凝固C 中间凝固2、合金的铸造性能(1)流动性合金的流动性即为液态合金的充型能力,是合金本身的性能。
它反映了液态金属的充型能力,但液态金属的充型能力除与流动性有关,还与外界条件如铸型性质、浇注条件和铸件结构等因素有关,是各种因素的综合反映。
生产上改善合金的充型能力可以从一下各方面着手:A 选择挨近共晶成份的趋于逐层凝固的合金,它们的流动性好;B 提高浇注温度,延长金属流动时间;C 提高充填能力D 设置出气冒口,减少型内气体,降低金属液流动时阻力。
(2)收缩性A 缩孔、缩松形成与铸件的液态收缩和凝固收缩的过程中.对于逐层凝固的合金由于固液两相共存区很小甚至没有,液固界面泾渭分明,已凝固区域的收缩就能顺利得到相邻液相的补充,如果最后凝固出的金属得不到液态金属的补充,就会在该处形成一个集中的缩孔。
适当控制凝固顺序,让铸件按远离冒口部份最先凝固,然后朝冒口方向凝固, 最后才是冒口本身的凝固(即顺序凝固方式) ,就把缩孔转移到最后凝固的部位—- 冒口中去,而去除冒口后的铸件则是所要的致密铸件。
材料成型技术基础课件

d. 提高铸型和型芯的退让性;浇注后尽早开型 e. 提高铸型温度 f. 去应力退火
(2)变形 ①变形方向
受拉部位趋于缩短; 受压部位趋于伸长 例如:T形梁 平板件
返 回
②防止措施 a. 反变形法。例如:床身铸件 b. 设置工艺筋
c. 去应力退火或自然时效
反变形量
(3)铸件的裂纹 ①热裂 a. 特征:裂纹短、形状曲折、缝隙宽、缝内呈氧化色 b. 影响因素: 合金性质和铸型阻力
返 回
c. 防止措施 选择结晶温度范围窄、收缩率小的合金 合理设计铸件结构 改善砂型和砂芯的退让性 严格限制钢和铸铁中硫的含量 ②冷裂 a. 特征:裂缝细小,表面光滑,呈连续圆滑曲线或直 线状,有金属光泽或呈轻微氧化色 b. 防止措施
减小铸造应力或降低合金的脆性
严格控制钢和铸铁中磷的质量分数
返 回
由于铸件壁厚不均匀,各部分冷却速度不同,以致 在同一时期内铸件各部分收缩不一致而引起的应力 a. 形成机理 b. 应力分布规律 厚壁或心部—拉应力; 薄壁或表层—压应力
返 回
c. 应力大小 ②机械应力
铸件壁厚差愈大 合金的线收缩率愈高 弹性模量愈大
热应力愈大
上型
铸件因收缩受到铸型、型 芯及浇注系统的机械阻碍而 产生的应力 特点:拉应力或剪切应力; 临时应力 ③减小和消除应力的措施 a. 铸件壁厚尽量均匀 b. 尽量选用线收缩率小、弹性模量小的合金
返 回
糊状(体积)凝固方式; 液态收缩+凝固收缩>固态收缩
(4)缩孔防止措施 ①“定向(顺序)凝固”。安放冒口 定向凝固特点: 有效地消除缩孔、缩松;
铸件易产生内应力、变 形和裂纹;
工艺出品率低;切削费工 应用:用于收缩较大、凝固温度范围较小的合金。 如铸钢、高牌号的灰铸铁、铝青铜等铸件
工程材料及成形技术_电子教材0
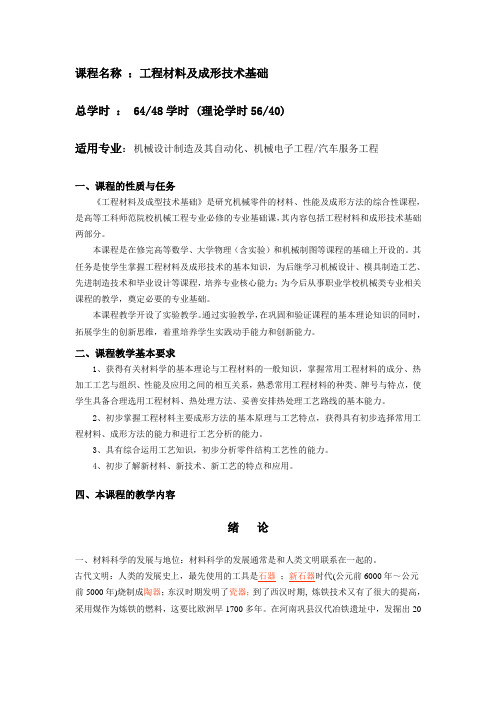
课程名称:工程材料及成形技术基础总学时: 64/48学时 (理论学时56/40)适用专业:机械设计制造及其自动化、机械电子工程/汽车服务工程一、课程的性质与任务《工程材料及成型技术基础》是研究机械零件的材料、性能及成形方法的综合性课程,是高等工科师范院校机械工程专业必修的专业基础课,其内容包括工程材料和成形技术基础两部分。
本课程是在修完高等数学、大学物理(含实验)和机械制图等课程的基础上开设的。
其任务是使学生掌握工程材料及成形技术的基本知识,为后继学习机械设计、模具制造工艺、先进制造技术和毕业设计等课程,培养专业核心能力;为今后从事职业学校机械类专业相关课程的教学,奠定必要的专业基础。
本课程教学开设了实验教学。
通过实验教学,在巩固和验证课程的基本理论知识的同时,拓展学生的创新思维,着重培养学生实践动手能力和创新能力。
二、课程教学基本要求1、获得有关材料学的基本理论与工程材料的一般知识,掌握常用工程材料的成分、热加工工艺与组织、性能及应用之间的相互关系,熟悉常用工程材料的种类、牌号与特点,使学生具备合理选用工程材料、热处理方法、妥善安排热处理工艺路线的基本能力。
2、初步掌握工程材料主要成形方法的基本原理与工艺特点,获得具有初步选择常用工程材料、成形方法的能力和进行工艺分析的能力。
3、具有综合运用工艺知识,初步分析零件结构工艺性的能力。
4、初步了解新材料、新技术、新工艺的特点和应用。
四、本课程的教学内容绪论一、材料科学的发展与地位:材料科学的发展通常是和人类文明联系在一起的。
古代文明:人类的发展史上,最先使用的工具是石器;新石器时代(公元前6000年~公元前5000年)烧制成陶器;东汉时期发明了瓷器;到了西汉时期, 炼铁技术又有了很大的提高,采用煤作为炼铁的燃料,这要比欧洲早1700多年。
在河南巩县汉代冶铁遗址中,发掘出20多座冶铁炉和锻炉。
炉型庞大,结构复杂,并有鼓风装置和铸造坑。
可见当年生产规模之壮观。
合工大材料成型技术基础复习知识点
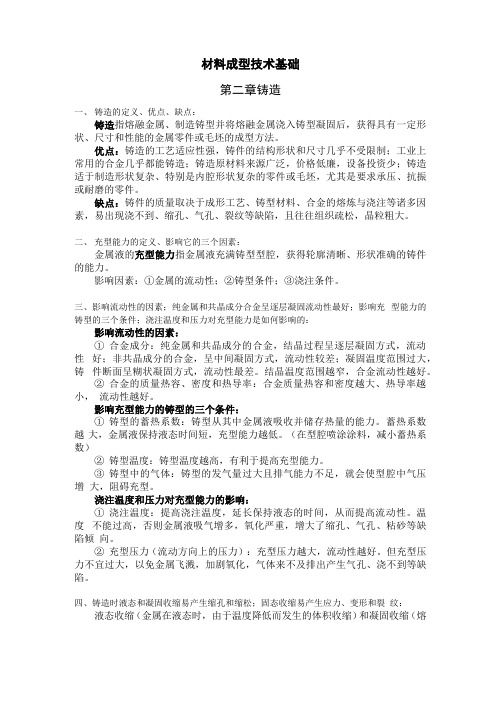
材料成型技术基础第二章铸造一、铸造的定义、优点、缺点:铸造指熔融金属、制造铸型并将熔融金属浇入铸型凝固后,获得具有一定形状、尺寸和性能的金属零件或毛坯的成型方法。
优点:铸造的工艺适应性强,铸件的结构形状和尺寸几乎不受限制;工业上常用的合金几乎都能铸造;铸造原材料来源广泛,价格低廉,设备投资少;铸造适于制造形状复杂、特别是内腔形状复杂的零件或毛坯,尤其是要求承压、抗振或耐磨的零件。
缺点:铸件的质量取决于成形工艺、铸型材料、合金的熔炼与浇注等诸多因素,易出现浇不到、缩孔、气孔、裂纹等缺陷,且往往组织疏松,晶粒粗大。
二、充型能力的定义、影响它的三个因素:金属液的充型能力指金属液充满铸型型腔,获得轮廓清晰、形状准确的铸件的能力。
影响因素:①金属的流动性;②铸型条件;③浇注条件。
三、影响流动性的因素;纯金属和共晶成分合金呈逐层凝固流动性最好;影响充型能力的铸型的三个条件;浇注温度和压力对充型能力是如何影响的:影响流动性的因素:①合金成分:纯金属和共晶成分的合金,结晶过程呈逐层凝固方式,流动性好;非共晶成分的合金,呈中间凝固方式,流动性较差;凝固温度范围过大,铸件断面呈糊状凝固方式,流动性最差。
结晶温度范围越窄,合金流动性越好。
②合金的质量热容、密度和热导率:合金质量热容和密度越大、热导率越小,流动性越好。
影响充型能力的铸型的三个条件:①铸型的蓄热系数:铸型从其中金属液吸收并储存热量的能力。
蓄热系数越大,金属液保持液态时间短,充型能力越低。
(在型腔喷涂涂料,减小蓄热系数)②铸型温度:铸型温度越高,有利于提高充型能力。
③铸型中的气体:铸型的发气量过大且排气能力不足,就会使型腔中气压增大,阻碍充型。
浇注温度和压力对充型能力的影响:①浇注温度:提高浇注温度,延长保持液态的时间,从而提高流动性。
温度不能过高,否则金属液吸气增多,氧化严重,增大了缩孔、气孔、粘砂等缺陷倾向。
②充型压力(流动方向上的压力):充型压力越大,流动性越好。
材料成型基础课件
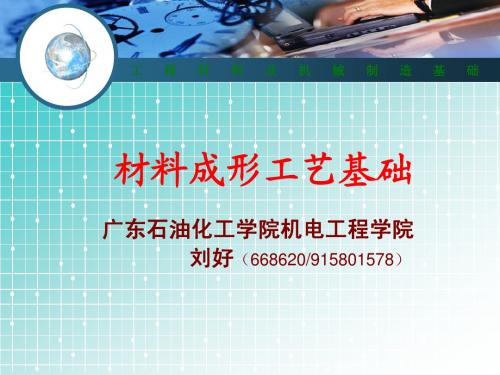
一般合金在凝固过程中都存在液-固两相区,树枝状晶在其中 不断扩大[见图a]。枝晶长到一定程度,枝晶分叉间的熔融 合金被分离成彼此孤立的状态[见图b],它们继续凝固时也 将产生收缩,这种凝固方式称糊状凝固。这时铸件中心虽有液 体存在,但由于树枝晶的阻碍使之无法补缩,在凝固后的枝晶 分叉间就形成许多微小的孔洞(缩松)[见图c]。
2.2 液态成形理论基础
材 料 成 形 工 艺 基 础
总结:具有逐层凝固倾向的合金(如灰 铸铁、铝硅合金等) 易于铸造,应尽量 选用。当必须采用有糊状凝固倾向的合 金(如锡青铜、铝铜合金、球墨铸铁等) 时,需考虑采用适当的工艺措施,例如, 选用金属型铸造等,以减小其凝固区域。
2.2 液态成形理论基础
1.2 材料成型方法及特点
材 料 成 形 工 艺 基 础
1.材料成型方法的分类
1.3 材料成型工艺发展及概况
材 料 成 形 工 艺 基 础
古代、近代及现代的材料成形技术 材料成形技术与材料科学 我国及世界先进国家的差距
1.4 材料成型工艺的发展趋势
材 料 成 形 工 艺 基 础
每项材料成形技术都有各自发展特点,总的趋势可归纳为 : 1、成型技术精密化 2、材料制备与成型一体化 3、复合成型 4、数字化成型 5、材料成型自动化 6、绿色清洁生产
液态合金填满铸型后[见图 a],因铸型吸热,靠近型腔表面 的金属很快就降到凝固温度,凝固成一层外壳[见图b],温 度继续下降,合金逐层凝固,凝固层加厚,内部的剩余的液体, 由于液态收缩和补充凝固层的凝固收缩,体积缩减,液面下降, 铸件内部出现空隙[见图c],直到内部完全凝固,在铸件上 部形成缩孔[见图d]。已经形成缩孔的铸件继续冷却到室温 时,因固态收缩使铸件的外形轮廓尺寸略有缩小[见图e]。 合金的液态收缩和凝固收缩越大,浇注温度越高,铸件的壁越 厚,缩孔的容积就越大。
材料成形技术基础培训
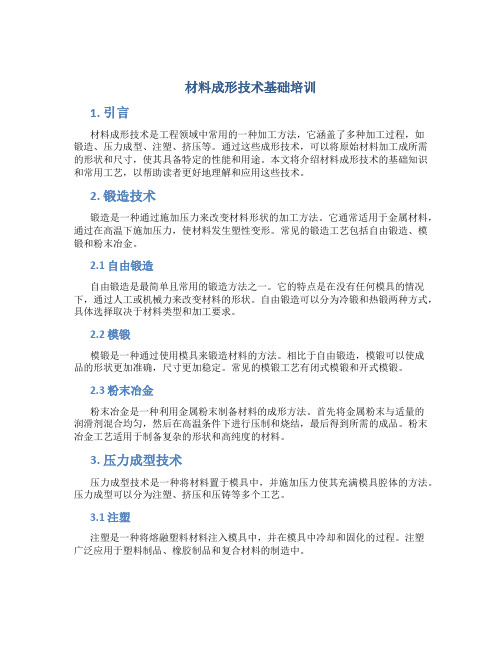
材料成形技术基础培训1. 引言材料成形技术是工程领域中常用的一种加工方法,它涵盖了多种加工过程,如锻造、压力成型、注塑、挤压等。
通过这些成形技术,可以将原始材料加工成所需的形状和尺寸,使其具备特定的性能和用途。
本文将介绍材料成形技术的基础知识和常用工艺,以帮助读者更好地理解和应用这些技术。
2. 锻造技术锻造是一种通过施加压力来改变材料形状的加工方法。
它通常适用于金属材料,通过在高温下施加压力,使材料发生塑性变形。
常见的锻造工艺包括自由锻造、模锻和粉末冶金。
2.1 自由锻造自由锻造是最简单且常用的锻造方法之一。
它的特点是在没有任何模具的情况下,通过人工或机械力来改变材料的形状。
自由锻造可以分为冷锻和热锻两种方式,具体选择取决于材料类型和加工要求。
2.2 模锻模锻是一种通过使用模具来锻造材料的方法。
相比于自由锻造,模锻可以使成品的形状更加准确,尺寸更加稳定。
常见的模锻工艺有闭式模锻和开式模锻。
2.3 粉末冶金粉末冶金是一种利用金属粉末制备材料的成形方法。
首先将金属粉末与适量的润滑剂混合均匀,然后在高温条件下进行压制和烧结,最后得到所需的成品。
粉末冶金工艺适用于制备复杂的形状和高纯度的材料。
3. 压力成型技术压力成型技术是一种将材料置于模具中,并施加压力使其充满模具腔体的方法。
压力成型可以分为注塑、挤压和压铸等多个工艺。
3.1 注塑注塑是一种将熔融塑料材料注入模具中,并在模具中冷却和固化的过程。
注塑广泛应用于塑料制品、橡胶制品和复合材料的制造中。
3.2 挤压挤压是一种将熔融金属或塑料材料通过模具挤压成型的工艺。
挤压常用于制备管材、线材和复杂形状的材料。
3.3 压铸压铸是一种通过使金属或塑料材料在模具中充满腔体,然后在高压下冷却和固化的方法。
压铸常用于制造复杂的零件和产品。
4. 其他成形技术除了锻造和压力成型技术,还有一些其他常用的成形技术,如精密铸造、镦粗和拉伸等。
4.1 精密铸造精密铸造是一种通过在真空或惰性气氛下将熔融金属注入模具中,然后在模具中冷却和固化的方法。
- 1、下载文档前请自行甄别文档内容的完整性,平台不提供额外的编辑、内容补充、找答案等附加服务。
- 2、"仅部分预览"的文档,不可在线预览部分如存在完整性等问题,可反馈申请退款(可完整预览的文档不适用该条件!)。
- 3、如文档侵犯您的权益,请联系客服反馈,我们会尽快为您处理(人工客服工作时间:9:00-18:30)。
2014-12-7
4
1-3射出成型加工
如何選擇合適的射出成型機?
一般而言,從事射出成型行業多年的客戶多半有能力自行判斷並選擇合適的射出機來生產。但是在某些 狀況下,客戶可能需要廠商的協助才能決定採用哪一個規格的射出機,甚至客戶可能只有產品的樣品或 構想,然後詢問廠商的機器是否能生產,或是哪一種機型比較適合。此外,某些特殊產品可能需要搭配 特殊裝置如蓄壓器、閉迴路、射出壓縮等,才能更有效率地生產。由此可見,如何決定合適的射出機來 生產,是一個極為重要的問題。通常影響射出機選擇的重要因素包括模具、產品、塑料、成型要求等, 因此,在進行選擇前必須先收集或具備下列資訊: 模具尺寸(寬度、高度、厚度)、重量、特殊設計等。 使用塑料的種類及數量(單一原料或多種塑料)。 射出成品的外觀尺寸(長、寬、高、厚度)、重量等。 成型要求,如品質條件、生產速度等。
9
1-3射出成型加工---射出機台
2014-12-710Βιβλιοθήκη 1-3射出成型加工---射出機
1.射嘴 2.射嘴法蘭 3.料管 4.射膠螺桿 5.電熱片
6.泠却環 7.固定大螺母 8.定位銷 9.射膠油缸 10.射膠尾板
11.油壓馬達 12.導桿 13.調整螺絲 14.半圓環
2014-12-7
11
1-3射出成型加工---射出機
2014-12-7
12
1-3射出成型加工---射出機名詞解釋
1.鎖模力:關閉模具所須最大壓力值.一般以噸表示…其意義為於成形時成品投影
面積所須之壓力。
當製品厚度薄且深.外型複雜時需將鎖模常數加大20~30%
此時計算方法:鎖模力=(A×B)in2 × 鎖模力常數
2014-12-7
機械鎖模力必須大於模具所須鎖模力..否 則成品將會有毛邊
射出成形機的夾模單元用以承載模具,它提供了關模、鎖模、開模及成品脫 模的動作和所需的力量,而其基本的組成元件包括繫桿、動模板、靜模板、 執行開關模的夾模機構及成品頂出機構。由於射出與保壓期間,融膠壓力會 產生極大的反作用力於模具上因此為了保證模具的閉合,夾模單元必須提供 足夠的鎖模力,以確保成型品品質,而此鎖模力的大小不但是機器的主要規 格,亦是射出機價格的指標
曲肘式:優點-技術教成熟 缺點-真的要作好不容易
2014-12-7
7
1-3射出成型加工---直壓式射出機台
直壓式夾模系統一般的共同特點為利用軸心方向的油壓缸來夾模,在此狀況,油壓缸的 活塞桿直接與動模板牢固。整個直壓式鎖模機構,為節省供油能量,夾模缸的作動乃 利用關模的同時由油槽吸入,,另外動模板的運動可利用速度快、體積小的兩支側邊 或一支中心位置的油壓缸來驅動,而此作動油則直接由油壓泵浦供給。對此直壓式夾 模機構,動模板由於兼有鎖模活塞桿的支撐,較不會傾斜及不平衡的現象,同時動模 板位置直接由油壓缸的行程決定,不需模厚調整機構,此乃直壓是機器的規格僅列出 最大模板間距的原因。
2014-12-7 3
1-3射出成型加工
射出機分多種型式.有卧式/立式---常見射出機以臥式均多。立式多半 應用於需埋入(IN Sert)物件之射出機一般用來說明射出機大小的方式 有二種:
鎖模力:比較正確的區分法為鎖模力..歐美國家也大都採行此法 注塑量:注塑量為射出機一次所能注塑之最大膠料重量.適常以盎司(0Z)為單位。但由 於每種塑料之比重不同.一般都以泛用塑膠PS為準..遇不同塑料則需以其比重系數來決 定其實際射出量。
2014-12-7
四、鎖得住:由產品及塑料決定「鎖模力」噸數。 五、射得飽:由成品重量及模穴數判定所需「射出量」並選擇合適的「螺桿直徑」。
5
1-3射出成型加工
射出機的分類方法非常多,通常可分為下列幾種:
1. 以驅動方式來分:油壓式射出機、全電式射出機、油電複合式射出機。
2. 以鎖模單元的開關方向來分:水平開關模為臥式(水平式)射出機,垂直開 關模則為立式射出機(簡稱直立機)。絕大部分為臥式射出機,立式射出機 適用於小型插件成品。
成型技術基礎知識講座
2014-12-7
1
大綱
1-塑膠各類加工法介紹 2-射出成型機介紹
3-射出加工設備介紹
4-射出加工成型技術 5-不良品發生之原理/原因/對策
2014-12-7 2
1-塑膠各類加工法介紹
1-1射出成型加工 1-2射壓成型 1-3快速射出成型 1-4共射出成型
6. 以鎖模結構來分:曲手式射出機、直壓式射出機、複合直壓式射出機(二板 式),此三種結構各有優劣點,目前仍以曲手式鎖模為最大宗。 7. 以射出結構來分:單色機(一組射出)、多色機(多組射出Multi2014-12-7 Component),絕大部分仍為單色機。
6
1-3射出成型加工---曲肘式射出機台
3. 以適用原料來分:熱塑性塑膠射出機、熱固性塑膠射出機(電木機)、粉末 射出機(金屬、陶瓷、合金)。目前絕大部分為熱塑性塑膠射出機。
4. 以油壓迴路來分:單迴路射出機、多迴路(雙迴路或三迴路)射出機。目前 絕大部分為單迴路射出機。
5. 以油路控制來分:開迴路射出機、閉迴路射出機。一般射出機均為開迴路, 但越來越多採用閉迴路控制,以增加機器穩定性。
2014-12-7
8
1-3射出成型加工---直壓式射出機台
優點
寬闊的模板和特長的頂出行程及開關模行程,對於特殊模具,容量加大。
設計獨特的直壓鎖模機構,摩擦滑動機件極少,只有連接柱需潤滑油,簡潔又方便,機身決不油膩 而且節省潤滑油。 獨特的直壓鎖模系統,更換鋼模只須設定位置距離,生產效率高
2014-12-7
1. 2. 3. 4.
在獲得以上資訊後,即可按照下列步驟來選擇合適的射出機:
一、選對型:由產品及塑料決定機種及系列。 二、放得下:由模具尺寸判定機台的「大柱內距」、「模厚」、「模具最小尺寸」及「模盤尺寸」是否適 當, 以確認模具是否放的下。 三、拿得出:由模具及成品判定「開模行程」及「托模行程」是否足以讓成品取出。
13
1-3射出成型加工---射出機名詞解釋
射出壓力:射出壓力是指在射出螺桿先端射出口部所發生之最大之壓力..一般射出油缸 內發生最大油壓之同時在螺桿先端射出口所發生之壓力即為此時之射出壓力