Lean指的是精益管理的精益
精益生产管理思想核心

解析精益生产管理思想核心精益生产管理(LeanProduction,LP),又称精良生产,其中“精”表示精良、精确、精美;“益”表示利益、效益等等。
精益生产管理就是及时制造,消灭故障,消除一切浪费,向零缺陷、零库存进军。
它是美国麻省理工学院在一项名为“国际汽车计划”的研究项目中提出来的。
它们在做了大量的调查和对比后,认为日本丰田汽车公司的生产方式是最适用于现代制造企业的一种生产组织精益生产管理方式,称之为精益生产管理,以针对美国大量生产方式过干臃肿的弊病。
精益生产管理综合了大量生产与单件生产方式的优点,力求在大量生产中实现多品种和高质量产品的低成本生产。
精益生产管理是生产管理中的精锐部分,其核心思想是将生产达到一个巅峰状态,在生产管理中,精益生产管理的要务就是打造最好的生产项目管理。
精益生产一、精益生产管理的产生与推广20世纪初,从美国福特汽车公司创立第一条汽车生产流水线以来,大规模的生产流水线一直是现代工业生产的主要特征。
大规模生产方式是以标准化、大批量生产来降低生产成本,提高生产效率的。
这种方式适应了美国当时的国情,汽车生产流水线的产生,一举把汽车从少数富翁的奢侈品变成了大众化的交通工具,美国汽车工业也由此迅速成长为美国的一大支往产业,并带动和促进了包括钢铁、玻璃、橡胶、机电以至交通服务业等在内的一大批产业的发展。
大规模流水生产在生产技术以及精益生产管理史上具有极为重要的意义。
但是第二次世界大依以后,社会进入了一个市场需求向多样化发展的新阶段,相应地要求工业生产向多品种、小批量的方向发展,单品种、大批量的流水生产方式的弱点就日渐明显了。
为了顺应这样的时代要求,由日本丰田汽车公司首创的精益生产管理,作为多品种、小批量混合生产条件下的高质量、低消耗进行生产的方式在实践中摸索、创造出来了。
1950年,日本的丰田英二考察了美国底持律的福特公司的轿车厂。
当时这个厂每天能生产7000辆轿车,比日本丰田公司一年的产量还要多。
与精益相关的概念

满意作为目标和最终的评价标准。
4)完美无缺:以精益求精的工作精神和态度,利用改进各种资源的效率与效应的无穷机遇,以最低的成本、最高的质量和最短的交货期实现TCS,超越竞争对手,占领更多的市场份额,夺取竞争优势。
4 以消除浪费为中心精益生产是以发现、分析研究和消除存在于工序与操作中的浪费为中心的。
最新的研究与企业实践证明,精益理念中所指的浪费 (损耗)包括:为防万一而过量或提前生产长的安装调整过程不平衡的工作负荷冗余的检测与试验过量的库存与WIP缺乏必要而精练的信息设备出现故障不均衡 (不平顺)的流程排序重复的工程活动过程中的等待加工处理的浪费运输的延迟质量缺陷冗余的动作缺乏多面手,等。
5.消除等待产生等待的根源是:工作负荷不均衡、进行非计划的维护修理、模具与工具安装与调整的时间长、机器或生产线停机、供应不及时或者上游出现质量缺陷或设备故障等。
消除等待的目标是,用工人的工作效率最大化代替机器利用率的最大化。
6.消除兄余的中间库存WIP产生冗余WIP的根源是:产品生产的导人时间长、保护低效率、产品复杂化、不平衡的流程排序、负荷不均衡、缺乏准确的生产预测、供应不可靠、设备故障频发、没有有效地沟通、工作报酬不合理等。
7.处理浪费问题产生处理浪费的根源是,在产品变换后不改变过程、防万一的保险思维作怪、不清楚顾客的需求与要求、缺乏有效地沟通、轻视消除浪费、赞成冗余、进行超量生产而不准时生产、提供给决策者与操的信息爆炸等。
处理浪费问题的目标是,使必须和可能处理浪费问题的流程阶段最少化和过程中的问题最少化。
8.运输确立运输不能创造附加价值的理念,应该使其最少化或者忽略掉。
产生运输浪费的根源是:差的运输路线或工厂的平面布局、不了解生产流程、生产的批量过大、制造的导人时间长、存储区的安排不合理等。
9.动作确立1人、机器与运输的无效动作是浪费的理念,应该改进所有运作作业的空程与冗余。
产生动作浪费的根源是:人与机器的低效率、工作方法不合理或不协调、无法有效利用装备、生产线的布局不合理、工作地的布局不合理、等待时的额外运动等。
精益(Lean)管理工具与方法课件

将经过验证的改进措施标准化和制度化,确保其在组织内部得到长期 执行和推广。
05
精益管理案例分析
案例一:某汽车制造企业的精益转型
总结词
全面转型、持续改进
详细描述
该汽车制造企业通过引入精益管理理念,对生产流程进行全面优化,减少浪费,提高生产效率。通过持续改进, 实现了产品质量、成本和交付期的全面提升。
5S管理有助于提高工作效率,减少浪费,保证安全,并改善 工作环境。通过实施5S管理,企业可以使其工作场所更加有 序、整洁、安全和高效。
快速换模
快速换模是一种生产管理技术,旨在减少设备或生产线更 换模具或夹具的时间和成本。
通过实施快速换模,企业可以提高生产效率,减少生产准 备时间,降低生产成本,并更好地满足客户需求。快速换 模对于多品种、小批量生产的企业尤为重要。
率和客户满意度。
确定目标与指标
目标设定
根据价值流分析结果,设定具体、可衡量的目标,以指导改进措 施的实施。
KPI指标
确定关键绩效指标(KPI),用于评估改进措施的效果和进度。
目标与指标的调整
根据实际情况调整目标与指标,确保其合理性和可行性。
实施改进措施
改进计划制定
根据目标与指标,制定详细的改进计划,包括具体的实施步骤、 责任人、时间表等。
精益(Lean)管理工具 与方法课件
• 精益管理概述 • 精益管理工具 • 精益管理方法 • 精益管理实施步骤 • 精益管理案例分析
01
精益管理概述
定义与特点
定义
精益管理是一种以客户需求为导 向,追求高效、低成本、高品质 的管理理念和方法。
特点
注重客户需求,强调价值流分析, 持续改进,消除浪费,追求卓越。
精益化管理

精益化管理什么是精益化管理精益化管理(Lean Management)是一种以精益思维为核心的管理方法。
它起源于丰田生产系统(Toyota Production System),是一种通过消除浪费、提高效率、改善质量的管理方法。
精益化管理的目标是在提供价值的同时,最大限度地减少资源的浪费。
它通过优化生产流程、改进工作方法、提高员工参与度等手段,实现持续改进和经营绩效的提升。
精益化管理的原则精益化管理遵循一系列的原则,包括:1.价值观导向:将顾客价值放在首位,以满足顾客需求为核心目标,通过消除无价值的活动和浪费来提供最大的价值。
2.流程优化:优化生产流程,实现物料、信息和人员的流畅运转,降低产出时间和成本。
3.质量保证:通过完善的质量管理体系,确保产品和服务的质量符合顾客要求。
4.员工参与:鼓励员工参与和提供改进意见,发挥员工的创造力和潜能,共同推动持续改进。
5.持续改进:通过不断地检查、评估和改善过程,实现持续的增长和改进。
以上原则共同构成了精益化管理的框架,帮助组织实现高效、高质量、高可靠性的运营。
精益化管理的方法和工具精益化管理采用一系列的方法和工具,在实践中帮助组织改善运营效率和质量。
下面介绍几个常用的方法和工具:PDCA循环PDCA循环是持续改进的核心方法,包括四个步骤:计划(Plan)、执行(Do)、检查(Check)、行动(Act)。
通过循环使用这四个步骤,不断改进和优化业务流程。
PDCA循环PDCA循环5S整理法5S整理法是一种通过整理、整顿、清扫、标准化、维护的方式,提高工作场所效率和工作环境的方法。
它通过整理工作区域、标记工具和设备、建立规范等手段,提高工作效率和质量。
Kaizen(改善)Kaizen是一种以持续改进为核心的管理理念和方法。
它强调利用小改进来促使持续的变革和进步。
价值流映射价值流映射是通过绘制整个价值流程图,分析每个环节的价值和浪费,找出改进的机会和方向。
它帮助组织理解和优化价值流程,降低浪费和提高效率。
精益管理方案
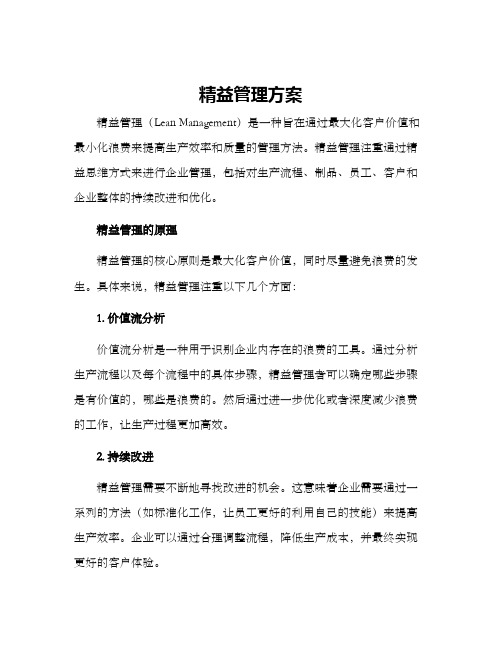
精益管理方案精益管理(Lean Management)是一种旨在通过最大化客户价值和最小化浪费来提高生产效率和质量的管理方法。
精益管理注重通过精益思维方式来进行企业管理,包括对生产流程、制品、员工、客户和企业整体的持续改进和优化。
精益管理的原理精益管理的核心原则是最大化客户价值,同时尽量避免浪费的发生。
具体来说,精益管理注重以下几个方面:1. 价值流分析价值流分析是一种用于识别企业内存在的浪费的工具。
通过分析生产流程以及每个流程中的具体步骤,精益管理者可以确定哪些步骤是有价值的,哪些是浪费的。
然后通过进一步优化或者深度减少浪费的工作,让生产过程更加高效。
2. 持续改进精益管理需要不断地寻找改进的机会。
这意味着企业需要通过一系列的方法(如标准化工作,让员工更好的利用自己的技能)来提高生产效率。
企业可以通过合理调整流程,降低生产成本,并最终实现更好的客户体验。
3. 团队合作精益管理需要团队工作。
员工和管理层需要紧密合作,共同追求最高效率,尽可能的减少浪费。
职员需要负责自己的岗位,同时需要了解其他工作,以便在必要时相互协助。
精益管理的优势采用精益管理的企业可以享受以下几个显著的优势:1. 提高生产效率精益管理的核心是减少浪费,严控生产成本。
企业通过精益管理可以明确发现生产流程中的瓶颈和浪费,能够更加精确地控制生产过程。
在生产过程中,优化生产流程,去除无用的步骤,以便更好的满足客户需求。
2. 降低生产成本在精益管理的生产过程中,企业能够更好地管理和控制成本。
通过深度去除浪费和优化流程,企业能够在不到降低质量的前提下,降低成本,为企业节省大量成本。
3. 提高员工满意度精益管理需要员工充分合作,让各个部门、职能之间深度合作。
员工无须考虑过多工作时间的问题,也不必承受因长时间工作而带来的压力,可以更加充分地发挥自己的技能和能力,同时也可以感受到自己的工作是有价值的,从而大大提升员工满意度。
总结精益管理是一种旨在提高生产效率和质量的管理方法。
精益管理的概念
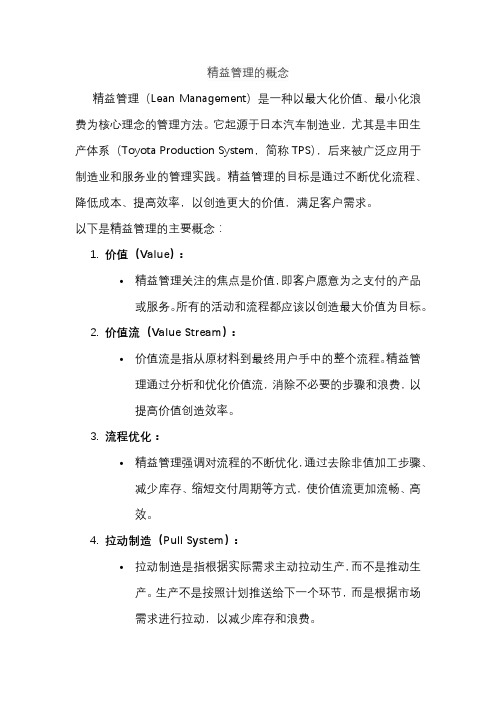
精益管理的概念精益管理(Lean Management)是一种以最大化价值、最小化浪费为核心理念的管理方法。
它起源于日本汽车制造业,尤其是丰田生产体系(Toyota Production System,简称TPS),后来被广泛应用于制造业和服务业的管理实践。
精益管理的目标是通过不断优化流程、降低成本、提高效率,以创造更大的价值,满足客户需求。
以下是精益管理的主要概念:1.价值(Value):•精益管理关注的焦点是价值,即客户愿意为之支付的产品或服务。
所有的活动和流程都应该以创造最大价值为目标。
2.价值流(Value Stream):•价值流是指从原材料到最终用户手中的整个流程。
精益管理通过分析和优化价值流,消除不必要的步骤和浪费,以提高价值创造效率。
3.流程优化:•精益管理强调对流程的不断优化,通过去除非值加工步骤、减少库存、缩短交付周期等方式,使价值流更加流畅、高效。
4.拉动制造(Pull System):•拉动制造是指根据实际需求主动拉动生产,而不是推动生产。
生产不是按照计划推送给下一个环节,而是根据市场需求进行拉动,以减少库存和浪费。
5.精益六大Sigma:•与精益管理密切相关的是“六西格玛”(Six Sigma),它是一种用于改进和控制过程的质量管理方法。
六西格玛强调通过减少变异性来提高质量,与精益管理结合使用,形成了一种强大的管理体系。
6.持续改进(Continuous Improvement):•精益管理是一种持续改进的管理哲学。
团队和组织应该不断地寻找和消除浪费,优化流程,追求卓越。
7.参与和团队合作:•精益管理强调员工的参与和团队合作。
通过激发员工的创造力和积极性,使得改进和优化成为全员参与的过程。
8.质量第一:•精益管理强调质量至上,通过不断提高质量水平,减少缺陷和重工,提高客户满意度。
精益管理不仅在制造业有着丰富的应用经验,而且在服务业、医疗保健、软件开发等领域也得到了广泛应用。
LEAN精益管理.doc

LEAN精益管理精益管理的内涵精益管理要求企业的各项活动都必须运用“精益思维” (Lean Thinking)。
“精益思维”的核心就是以最小资源投入,包括人力、设备、资金、材料、时间和空间,创造出尽可能多的价值,为顾客提供新产品和及时的效劳。
精益管理的目标可以概括为:企业在为顾客提供满意的产品与效劳的同时,把浪费降到最低程度。
企业生产活动中的浪费现象很多,常见的有:错误——提供有缺陷的产品或不满意的效劳;积压——因无需求造成的积压和多余的库存;过度加工——实际上不需要的加工和程序;多余搬运——不必要的物品移动;等候——因生产活动的上游不能按时交货或提供效劳而等候;多余的运动——人员在工作中不必要的动作;提供顾客并不需要的效劳和产品。
努力消除这些浪费现象是精益管理的最重要的内容。
由顾客确定产品价值结构1.产品价值结构的涵义。
产品价值结构即产品价值的组成、比例及其价值流程,即某种产品所提供的各种利益、支出及其比例关系以及价值的实现过程。
产品价值结构就是要确定企业的某一种产品具体提供给顾客那些具体的利益,每种利益的数量;还要确定顾客购置产品的各种支出,各种支出的数量;各种利益、支出之间是一种什么样的联系;各种利益和支出是按照什么样的流程来实现产品价值的。
如对一般顾客,家乐福超市盛物塑料袋,麦德龙的盛物塑料袋却要收费。
这说明家乐福向一般顾客提供盛物塑料袋这一利益,麦德龙不向一般顾客提供该种利益。
其原因是两商家的目标群体不一样,家乐福主要面对一般顾客,而麦德龙主要面对团体顾客。
2.产品价值结构由顾客确定。
在当前信息经济社会的背景下,由于高素质的人才、低本钱的信息,先进的技术、成熟的管理模式、顾客的强势购置力等等外部环境因素,企业已具有了经济的满足顾客多样化需求的社会条件。
企业竞争的焦点是如何利用工业社会的规模优势和信息社会的信息低本钱优势,来满足顾客个性化的需求。
这时候,产品的价值结构就由顾客来确定了。
当然,在目前的社会经济条件下,企业由于经济性的约束,大局部情况是企业提供一个价值组成清单,在清单的范围内,由顾客确定产品价值结构。
精益管理理论、方法

精益管理理论、方法精益管理(Lean management)是一种以优化流程、提高效率和质量为目标的管理理论和方法,以追求客户价值、减少浪费为核心,通过精确计划、持续改进、员工参与和高效团队合作来实现。
精益管理最初源自于丰田汽车公司的生产方式,后逐渐演变为一种全面的管理理念,并在各个行业广泛应用。
精益管理的目标是实现高效率、低成本的生产和服务,以满足客户需求,并在同类产品市场竞争中获得优势。
它通过对价值流进行分析,尽量减少非价值增加的活动,做到零浪费。
同时,精益管理强调以人为本,鼓励每个员工发挥自己的潜力,提供持续的培训和发展机会,使员工成为问题解决者,积极参与到流程改进中。
精益管理的核心方法之一是价值流图(Value Stream Mapping),它是通过绘制生产或服务过程中各项活动的流程图,揭示出非价值增加的环节和浪费,以便针对性地改进。
通过对价值流图的分析,可以找出优化的空间,消除瓶颈和缩短交付周期,提高生产效率。
另一个重要的方法是精益生产(Lean Production),它关注如何在现有资源和时间限制下提高产出效率。
精益生产强调延迟决策和灵活性,以适应需求的变化。
通过实施精益生产,可以有效减少库存、降低生产成本,提高产品质量和交付速度。
精益管理还注重质量管理,强调从源头上控制质量,追求零缺陷。
通过精益管理的方法,可以减少不良品数量,提高客户满意度,提升企业的竞争力。
在实施精益管理的过程中,领导者起到了至关重要的作用。
他们需要树立正确的价值观,倡导质量至上、持续改进的文化,并树立榜样。
同时,他们还需要提供必要的资源和培训,支持员工参与并推动改进。
总而言之,精益管理理论和方法通过优化流程、减少浪费、提高效率和质量,让企业能够更好地满足客户需求,提升竞争力。
它是一种以持续改进和员工参与为核心的管理方式,可以在各个行业中应用,并产生显著的效果。
精益管理理论和方法是一种跨行业、跨功能的管理方式,旨在提升企业的绩效和竞争力。
什么是精益
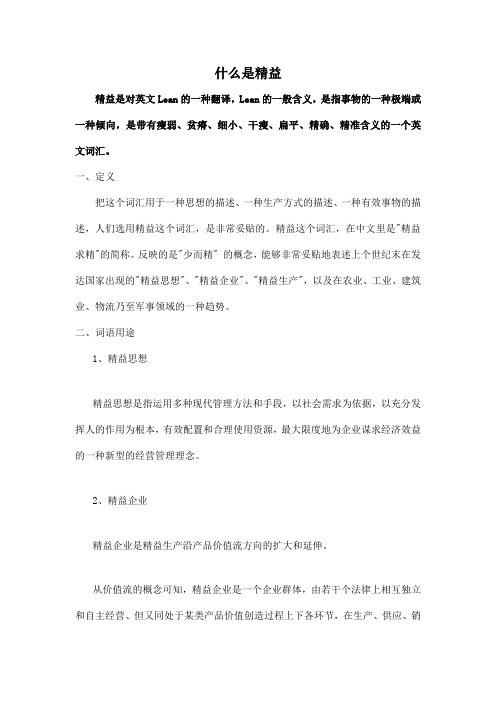
什么是精益精益是对英文Lean的一种翻译,Lean的一般含义,是指事物的一种极端或一种倾向,是带有瘦弱、贫瘠、细小、干瘦、扁平、精确、精准含义的一个英文词汇。
一、定义把这个词汇用于一种思想的描述、一种生产方式的描述、一种有效事物的描述,人们选用精益这个词汇,是非常妥贴的。
精益这个词汇,在中文里是"精益求精"的简称。
反映的是"少而精" 的概念,能够非常妥贴地表述上个世纪末在发达国家出现的"精益思想"、"精益企业"、"精益生产",以及在农业、工业、建筑业、物流乃至军事领域的一种趋势。
二、词语用途1、精益思想精益思想是指运用多种现代管理方法和手段,以社会需求为依据,以充分发挥人的作用为根本,有效配置和合理使用资源,最大限度地为企业谋求经济效益的一种新型的经营管理理念。
2、精益企业精益企业是精益生产沿产品价值流方向的扩大和延伸。
从价值流的概念可知,精益企业是一个企业群体,由若干个法律上相互独立和自主经营、但又同处于某类产品价值创造过程上下各环节,在生产、供应、销售等方面相互联系和相互依赖的不同公司或企业构成。
其使命就是在对产品价值创造过程进行共同分析的基础上,集中致力于产品价值的创造活动。
3、精益生产所谓精益生产,简言之,就是一种以满足用户需求为目标、力求降低成本、提高产品的质量、不断创新的资源节约型的生产方式。
4、精益管理《管理精益》中所描述的一种方式:精益通过提高员工的水平来保证产品开发。
在这个定义的基础上,这篇论文接下来解释了精益是怎样提高人员的水平的:方法就是解决问题。
这一定义揭示了以下管理实践的美妙之处:仔细设计你的工作,让你能够清晰地看见所发生的问题(以及同时出现的学习机会),并在问题出现后以科学的方式解决。
LEAN精益管理
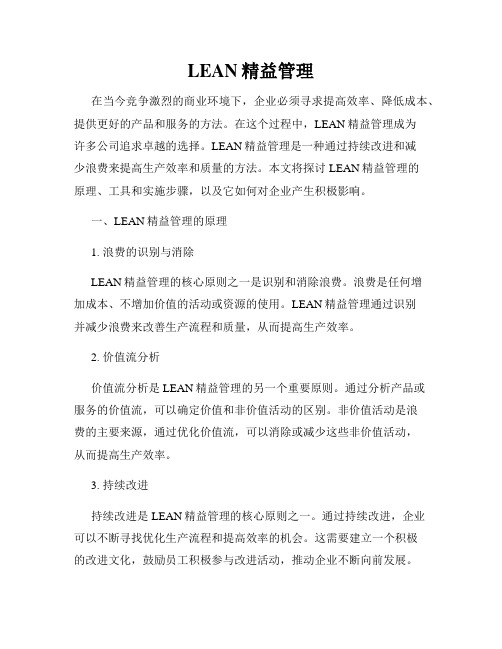
LEAN精益管理在当今竞争激烈的商业环境下,企业必须寻求提高效率、降低成本、提供更好的产品和服务的方法。
在这个过程中,LEAN精益管理成为许多公司追求卓越的选择。
LEAN精益管理是一种通过持续改进和减少浪费来提高生产效率和质量的方法。
本文将探讨LEAN精益管理的原理、工具和实施步骤,以及它如何对企业产生积极影响。
一、LEAN精益管理的原理1. 浪费的识别与消除LEAN精益管理的核心原则之一是识别和消除浪费。
浪费是任何增加成本、不增加价值的活动或资源的使用。
LEAN精益管理通过识别并减少浪费来改善生产流程和质量,从而提高生产效率。
2. 价值流分析价值流分析是LEAN精益管理的另一个重要原则。
通过分析产品或服务的价值流,可以确定价值和非价值活动的区别。
非价值活动是浪费的主要来源,通过优化价值流,可以消除或减少这些非价值活动,从而提高生产效率。
3. 持续改进持续改进是LEAN精益管理的核心原则之一。
通过持续改进,企业可以不断寻找优化生产流程和提高效率的机会。
这需要建立一个积极的改进文化,鼓励员工积极参与改进活动,推动企业不断向前发展。
二、LEAN精益管理的工具和技术1. 5S整理法5S整理法是LEAN精益管理中常用的工具之一。
它包括整理、整顿、清扫、清洁和纪律五个步骤。
通过5S整理法,可以改善工作环境,提高工作效率和品质。
2. 价值流映射价值流映射是一种用于分析和改进价值流的工具。
通过绘制当前状态价值流图和期望状态价值流图,可以识别出改进的机会,并制定相应的措施。
3. Kaizen活动Kaizen是指持续改进的活动。
通过开展Kaizen活动,可以鼓励员工积极参与改进,寻找降低成本、提高效率和品质的机会,并及时采取行动。
三、LEAN精益管理的实施步骤1. 制定战略目标首先,企业应该明确制定与LEAN精益管理相关的战略目标,明确追求卓越的愿景和使命,并设定具体的指标来衡量目标的达成情况。
2. 建立改进文化要成功实施LEAN精益管理,企业需要建立一种积极的改进文化。
实验室管理学精益管理名词解释
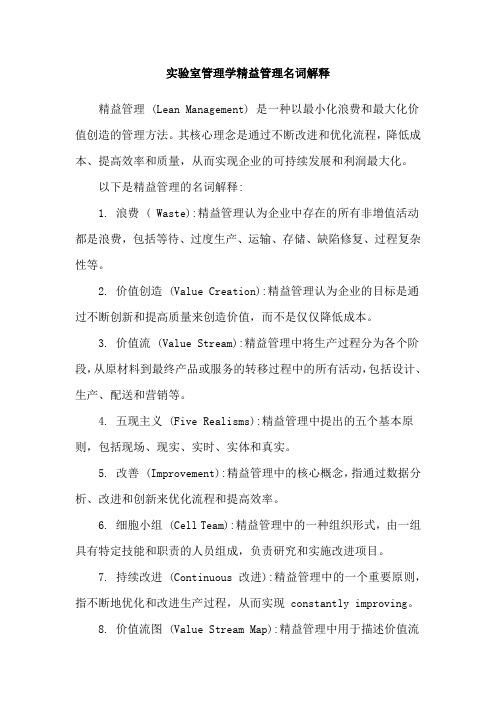
实验室管理学精益管理名词解释精益管理 (Lean Management) 是一种以最小化浪费和最大化价值创造的管理方法。
其核心理念是通过不断改进和优化流程,降低成本、提高效率和质量,从而实现企业的可持续发展和利润最大化。
以下是精益管理的名词解释:1. 浪费 ( Waste):精益管理认为企业中存在的所有非增值活动都是浪费,包括等待、过度生产、运输、存储、缺陷修复、过程复杂性等。
2. 价值创造 (Value Creation):精益管理认为企业的目标是通过不断创新和提高质量来创造价值,而不是仅仅降低成本。
3. 价值流 (Value Stream):精益管理中将生产过程分为各个阶段,从原材料到最终产品或服务的转移过程中的所有活动,包括设计、生产、配送和营销等。
4. 五现主义 (Five Realisms):精益管理中提出的五个基本原则,包括现场、现实、实时、实体和真实。
5. 改善 (Improvement):精益管理中的核心概念,指通过数据分析、改进和创新来优化流程和提高效率。
6. 细胞小组 (Cell Team):精益管理中的一种组织形式,由一组具有特定技能和职责的人员组成,负责研究和实施改进项目。
7. 持续改进 (Continuous 改进):精益管理中的一个重要原则,指不断地优化和改进生产过程,从而实现 constantly improving。
8. 价值流图 (Value Stream Map):精益管理中用于描述价值流的图形化工具,可以帮助企业分析和优化生产过程。
9. 浪费可视化 ( Waste Visualization):精益管理中的一种方法,通过可视化浪费,帮助企业更好地识别和消除浪费。
10. 拉动系统 (Pull System):精益管理中的一种生产组织形式,强调由客户需求来拉动生产,而不是通过堆积和过量生产来响应客户需求。
精益化与精细化的名词解释
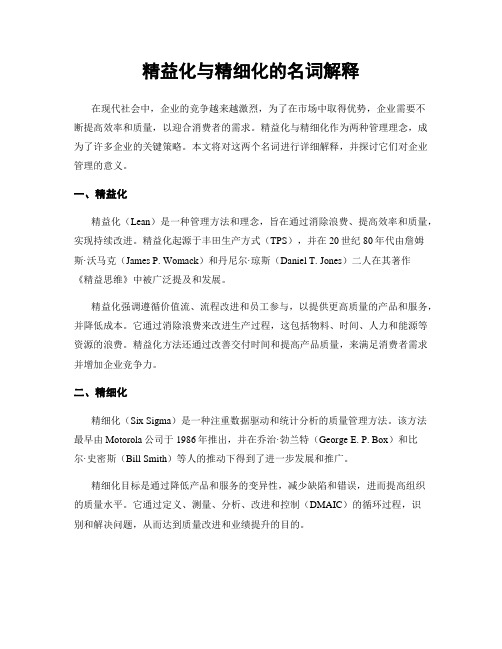
精益化与精细化的名词解释在现代社会中,企业的竞争越来越激烈,为了在市场中取得优势,企业需要不断提高效率和质量,以迎合消费者的需求。
精益化与精细化作为两种管理理念,成为了许多企业的关键策略。
本文将对这两个名词进行详细解释,并探讨它们对企业管理的意义。
一、精益化精益化(Lean)是一种管理方法和理念,旨在通过消除浪费、提高效率和质量,实现持续改进。
精益化起源于丰田生产方式(TPS),并在20世纪80年代由詹姆斯·沃马克(James P. Womack)和丹尼尔·琼斯(Daniel T. Jones)二人在其著作《精益思维》中被广泛提及和发展。
精益化强调遵循价值流、流程改进和员工参与,以提供更高质量的产品和服务,并降低成本。
它通过消除浪费来改进生产过程,这包括物料、时间、人力和能源等资源的浪费。
精益化方法还通过改善交付时间和提高产品质量,来满足消费者需求并增加企业竞争力。
二、精细化精细化(Six Sigma)是一种注重数据驱动和统计分析的质量管理方法。
该方法最早由Motorola公司于1986年推出,并在乔治·勃兰特(George E. P. Box)和比尔·史密斯(Bill Smith)等人的推动下得到了进一步发展和推广。
精细化目标是通过降低产品和服务的变异性,减少缺陷和错误,进而提高组织的质量水平。
它通过定义、测量、分析、改进和控制(DMAIC)的循环过程,识别和解决问题,从而达到质量改进和业绩提升的目的。
精细化方法大量使用统计工具和技术,以识别和量化问题,并通过数据分析找到根本原因。
它注重过程的控制和持续改进,强调团队合作和员工参与,以实现质量目标和满足客户需求。
三、精益化与精细化的联系与区别尽管精益化和精细化都是提高企业效率和质量的管理方法,但它们的侧重点和操作方式略有不同。
精益化侧重于生产和运营过程的持续改进,关注如何消除资源浪费,并通过流程优化来提高效率和质量。
精益管理知识
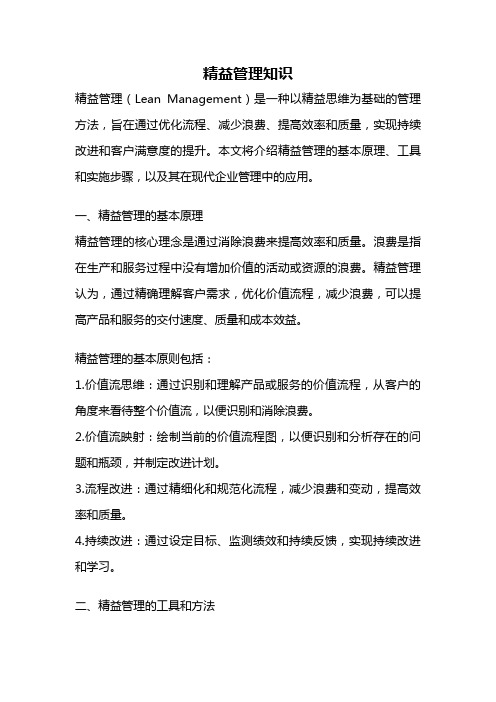
精益管理知识精益管理(Lean Management)是一种以精益思维为基础的管理方法,旨在通过优化流程、减少浪费、提高效率和质量,实现持续改进和客户满意度的提升。
本文将介绍精益管理的基本原理、工具和实施步骤,以及其在现代企业管理中的应用。
一、精益管理的基本原理精益管理的核心理念是通过消除浪费来提高效率和质量。
浪费是指在生产和服务过程中没有增加价值的活动或资源的浪费。
精益管理认为,通过精确理解客户需求,优化价值流程,减少浪费,可以提高产品和服务的交付速度、质量和成本效益。
精益管理的基本原则包括:1.价值流思维:通过识别和理解产品或服务的价值流程,从客户的角度来看待整个价值流,以便识别和消除浪费。
2.价值流映射:绘制当前的价值流程图,以便识别和分析存在的问题和瓶颈,并制定改进计划。
3.流程改进:通过精细化和规范化流程,减少浪费和变动,提高效率和质量。
4.持续改进:通过设定目标、监测绩效和持续反馈,实现持续改进和学习。
二、精益管理的工具和方法精益管理借鉴了许多工业工程和管理学的方法和工具,用以实现流程优化和问题解决。
以下是几个常用的精益管理工具和方法:1. 5S:通过整理、整顿、清扫、标准化和自律,改善工作环境和工作效率。
2. Kaizen:即持续改进,通过小步骤、小改进来不断优化流程和提高绩效。
3. PDCA循环:计划(Plan)、执行(Do)、检查(Check)、行动(Act)的循环,用于问题解决和持续改进。
4. VSM:价值流映射,通过绘制价值流程图,识别和分析存在的问题和瓶颈,并制定改进计划。
5. TPM:全员生产维护,通过设备保养和维护,实现设备稳定性和可靠性的提高。
6. JIT:即时生产,通过按需生产和减少库存,降低成本和提高效率。
7. DMAIC:定义(Define)、测量(Measure)、分析(Analyze)、改进(Improve)、控制(Control)的方法,用于问题解决和过程改进。
精益生产(lean)和准时生产(JIT)的区别.docx
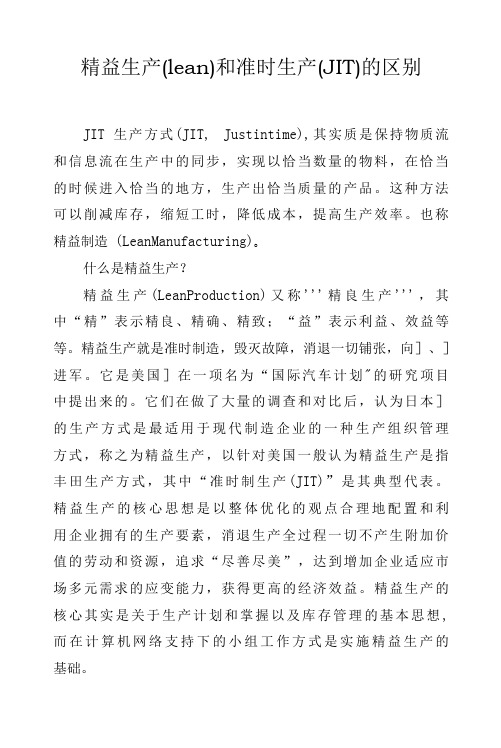
精益生产(lean)和准时生产(JIT)的区别JIT生产方式(JIT, Justintime),其实质是保持物质流和信息流在生产中的同步,实现以恰当数量的物料,在恰当的时候进入恰当的地方,生产出恰当质量的产品。
这种方法可以削减库存,缩短工时,降低成本,提高生产效率。
也称精益制造(LeanManufacturing)o什么是精益生产?精益生产(LeanProduction)又称'''精良生产''',其中“精”表示精良、精确、精致;“益”表示利益、效益等等。
精益生产就是准时制造,毁灭故障,消退一切铺张,向]、]进军。
它是美国]在一项名为“国际汽车计划"的研究项目中提出来的。
它们在做了大量的调查和对比后,认为日本]的生产方式是最适用于现代制造企业的一种生产组织管理方式,称之为精益生产,以针对美国一般认为精益生产是指丰田生产方式,其中“准时制生产(JIT)”是其典型代表。
精益生产的核心思想是以整体优化的观点合理地配置和利用企业拥有的生产要素,消退生产全过程一切不产生附加价值的劳动和资源,追求“尽善尽美”,达到增加企业适应市场多元需求的应变能力,获得更高的经济效益。
精益生产的核心其实是关于生产计划和掌握以及库存管理的基本思想, 而在计算机网络支持下的小组工作方式是实施精益生产的基础。
精益生产要求以少而精的生产要素投入管理和追求效益经济的指导思想,是对传统的“大规模生产模式”的挑战。
它的基本目标是零库存、高柔性、无缺陷。
精益生产的特点是:第一、以销售部门作为生产过程的起点,按订货合同组织多品种小批量生产;第二、在产品开发上有独特的方法,采用类似“项目经理负责制",项目经理被赋予极大的权力去组织人力物力资源并会得到各级领导的支持,以保障开发的顺当进行。
开发过程中采用的是并行工程(简称CE),即在产品设计时,就将其后续的工艺、制造、装配、检测、使用、修理、服务等产品整个生命周期中的相关过程全部考虑并一同设计,以削减反复修改的次数,争取一次成功。
精益

八大浪费
KAIZEN 及进行要点
人, 名词:KAIZEN (改善) --日语,即中文“改善”。“改”即改变,“善”即变的更好; --在精益管理活动中,“KAIZEN改善”表示持续改善,即每一天, 每一 每一处的全员参与的持续改善;最初来源于日本质量管理大师今井正明。
--在持续改善活动中,能够快速进行的小、快、灵的项目被称为“KAIZEN” 项目。此类项目在进行时一般不用额外投入成本,不用花费大量时间和人力 物力,一般1~4周内采用简单的改善工具即可完成; “KAIZEN” 项目进行的要点: 1)没有借口; 2)改变传统观念;
QC 7大手法
工具4:头脑风暴法(Brain Storming) --又称脑力激荡法或自由思考法、畅谈法,集思法等 ,由美国创造学家 A.F.奥斯本于1939年首次提出的一种激发创造性思维的方法。 --作用:联想反应,热情感染,竞争意识,个人欲望。 --方法:自由发言式;轮流发言式;指定发言式;接力发言式。 --原则:各抒己见;自由鸣放;取长补短;追求数量;庭外判决;事后改善。
精益管理
精益及其历史
名词:什么是精益 (Lean)
管理
-- 来源于英语“Lean”的翻译。形容词,原意为“ 瘦的,瘦肉”;精益 一词起源于美国麻省理工学院对丰田生产系统研究的的
总结,最早出现在其
出版的书籍《改变世界的机器》。 --“精”即少,少而精。要少投入、少消耗资源、少花 时间,尤其是要减少不可再生资源的投入和耗费。 --“益”既效益,所有经营活动都要有益有效,具有 经济性多产出经济效益,实现企业升级的目标。 --今天“精益管理”已经成为一种解决问题的方法论 帮助企业投入适当的资源,使效益最大化。
--5W2H即: Where何处,在什么地方,~空间 When何时,在什么时候~时间 What 何者,是什么东西/事~生产对象 Who 何人,是什么人做/生产主体 Why 为何,为什么如此 How如何,怎么做的 How much 成本
LEAN精益生产作用及特点

LEAN精益生产作用及特点LEAN精益生产是一种管理方法,旨在通过优化生产过程和资源利用,提高效率和质量,降低浪费和成本。
它通过不断改进和减少浪费,对企业的生产流程进行改革,以实现最高价值的生产。
首先,LEAN精益生产通过排除浪费来提高企业效率。
浪费是任何不增加价值的活动或资源的使用。
LEAN精益生产方法通过分析生产过程,将其中的非价值增加活动剔除掉,例如:等待时间、运输时间、加工中的破损、生产过程中的缺陷等等。
通过减少和消除这些浪费,企业可以提高生产效率,并最大程度地节省成本。
其次,LEAN精益生产方法强调持续改进。
它提倡员工的积极参与和团队合作,鼓励他们在生产过程中发现问题并提出解决方案。
通过持续的改进措施,不断提高生产效率和质量,LEAN精益生产方法帮助企业实现持续发展和竞争优势。
此外,LEAN精益生产方法注重质量管理。
它通过提早发现并解决生产过程中的问题,确保产品的质量符合标准要求。
通过减少缺陷和提高产品质量,企业可以提高客户满意度,增加市场竞争力。
最后,LEAN精益生产方法也倡导有效的资源利用。
它通过优化生产流程和资源配备,最大限度地利用和优化现有资源,实现生产的最佳结果。
这有助于降低企业的生产成本,并加强企业的经济效益。
总之,LEAN精益生产方法通过排除浪费、持续改进、质量管理和资源利用等手段,帮助企业提高生产效率、质量和经济效益。
它的特点是不断追求卓越,全员参与,注重问题解决和持续改进。
因此,LEAN精益生产方法被广泛应用于许多企业,成为提高竞争力和实现可持续发展的重要工具。
LEAN精益生产是一种广泛应用于制造业和服务业的管理方法。
它起源于丰田汽车公司的生产方式,旨在通过精简流程、减少浪费和优化资源利用来提高企业的效率、质量和竞争力。
LEAN精益生产方法的特点之一是其以客户价值为导向,注重实现产品或服务的最高价值。
LEAN精益生产的核心理念是以客户为中心。
这意味着企业应该全面了解客户的需求和期望,并将其视为指导生产和提供服务的基准。
Lean是什么-入门级必备

Lean 初级必备Lean Production (精益生产)一种管理产品开发、生产运作、供应商、以及客户关系的整个业务的方法。
与大批量生产系统形成对比的是,精益生产强调以更少的人力,更少的空间,更少的投资,和更短的时间,生产符合顾客需求的高质量产品。
精益生产由丰田公司在第二次世界大战之后首创,到1990年的时候,丰田公司只需要用原来一半的人力,一半的制造空间和投入资金,生产相同数量的产品。
在保证质量和提高产量的同时,他们所花费的在产品开发和交货的时间,也远比大批量生产更有效益。
(Womack,Jones和Roos1990, P.13)“精益生产”这个术语由MIT国际机动车辆项目的助理研究员John Krafcik于20世纪80年代最先提出。
Lean Logistics (精益物流)在沿着价值流的各个公司和工厂之间,建立一个能够经常以小批量进行补给的拉动系统。
我们假设A公司(一个零售商)直接向顾客销售产品,而且从B公司(一个制造商)大批量、低频率的补给货物。
精益物流将会在零售商(A公司)安装一个拉动信号,当他售出若干的货物之后,这个信号就会提示制造商,补充相同数量的货物给A,同时制造商会提示他的供应商补充相同数量的原料或半成品,以此一直向价值流的上游追溯。
精益物流需要拉动信号(EDI,看板,网络设备,等等),来保证价值流各工序之间的平衡生产,举个例子,用频繁的小批量装运方法,将零售商、制造商、以及供应商,联成一条“送牛奶”的供应链。
Kanban (看板)看板是拉动系统中,启动下一个生产工序,或搬运在制品到下游工序的一个信号工具。
这个术语在日语中是“信号”或“信号板”的意思。
看板卡片是人们最熟悉的例子。
人们通常使用表面光滑的纸制作看板,有时还会用透明的塑料薄膜来加以保护。
看板上的信息包括:零件名称,零件号,外部供应商,或内部供应工序,单位包装数量,存放地点,以及使用工作站。
卡片上可能还会有条形码以便于跟踪和计价。
- 1、下载文档前请自行甄别文档内容的完整性,平台不提供额外的编辑、内容补充、找答案等附加服务。
- 2、"仅部分预览"的文档,不可在线预览部分如存在完整性等问题,可反馈申请退款(可完整预览的文档不适用该条件!)。
- 3、如文档侵犯您的权益,请联系客服反馈,我们会尽快为您处理(人工客服工作时间:9:00-18:30)。
一、
“Lean”指的是精益管理的“精益”
Healthcare is the next great industry to begin the lean journey. The existing model in which the hospital doctor acting as a skilled craftsperson effectively manages their own waiting list of patients, clinics and operations inside some one else’s mass production general hospital is reaching the end of the road. We need to create a vision of what it means to be a lean doctor, what is involved in running a lean health delivery organization and how the context needs to change to help bring this about.
Recent experience in the UK has shown the problem can not be resolved by spending more money or by increasing capacity and staff. Better outcomes for patients, more satisfying working conditions for staff and lower costs to the tax payer (or members of private healthcare schemes) can only come from fundamentally redesigning the underlying processes for delivering healthcare.
The most important difference between healthcare (and many services) and manufacturing is that the patient is present throughout most of the process, indeed the patient is the product and their problem is the purpose of the activity. If you are a manufacturer just think how different your life would be if your product could experience your process and tell you what it was like!
医疗保健业是接下来开展“求精求益”工作的一个重要行业。
现行该行业中医生如能工巧匠般娴熟地将自己候选名单上的患者,诊所和手术穿插安排在医院的其他事务安排中,而这一现象即将走到尽头。
我们所需要的是一个精益求精的医生形象,一个可以传递“求精求益”健康理念的组织,以及如何改变以求得其实现。
目前英国的经验告诉我们增加投入资金或增加生产力和工作人员并不能使该项问题得到解决。
只有从根本上重置医疗保健业的基础传递过程才能使患者得到更好的实惠,使工作人员对工作环境更满意,使纳税人(私立医疗健康机构成员)少纳税。
医疗保健业(其他许多行业)与制造业最大的不同在于患者差不多存在于整个行业运行过程之中,而且患者实际上就是产品,而他们身上的问题则是该行业运行的目的所在。
如果你是制造商,却是你加工处理完成的产品告知你产品情况,那么试想你的生活将糟糕成什么样。
二、
打印机
Adjustment/settings
How to use the adjustment section
• “Adjustment/Setting” contains detailed information on the adjustment item s and procedures for this machine.
• Throughout this “Adjustment/Setting,” the default settings are indicated by “ ”. Advance checks
• Before attempting to solve the customer problem, the following advance checks must be made. Check to see if:
• The power supply voltage meets the specifications.
• The power supply is properly grounded.
• The machine shares the power supply with any other machine that draws large current intermittently (e.g., elevator and air conditioner that generate electric noise). • The installation site is environmentally appropriate: high temperature, high humidity, direct sunlight, ventilation, etc.; levelness of the installation site.
• The original has a problem that may cause a defective image.
• The density is properly selected.
• The original glass, slit glass, or related part is dirty.
• Correct paper is being used for printing.
• The units, parts, and supplies used for printing (developer, PC drum, etc.) are properly replenished and replaced when they reach the end of their useful service life. • Toner is not running out.
打印机
调整/设置
调整章节使用说明
•“调整/设置”详细地说明了该机器的可调整项及调整程序。
•在“调整/设置”中,默认设置均显示为“”
预查
• 在解决客户问题之前,应做好下列预查。
逐一检查是否:
•电源电压合格。
•电源供电器接地。
• 和其他间歇式需大量电流的机械共享电源。
(例如:会产生电动噪音的电梯和空调)
• 安置环境应为:高温,高湿度,太阳直照,空气流通等等。
水平放置安装。
• 打印原件存在致使打印效果不好的问题。
• 密度选择适当。
• 原片玻璃,玻璃焊接处或相连部分有污迹。
•机内有合格的打印纸张正在打印。
•在打印所需装置,部件和物料(显影剂,光导磁鼓等等)已过期时应及时装满和更换。
•调色剂充足。