精益生产游戏(Lean Game) 实践案例
精益生产游戏(Lean Game) 实践案例
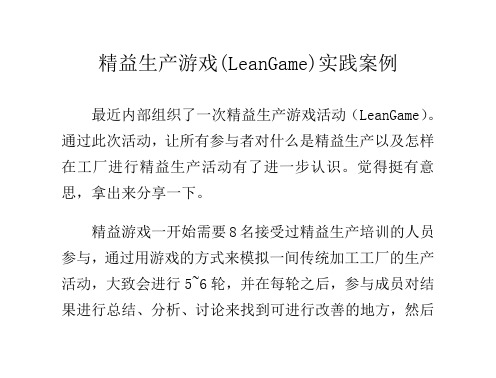
精益生产游戏(LeanGame)实践案例最近内部组织了一次精益生产游戏活动(LeanGame)。
通过此次活动,让所有参与者对什么是精益生产以及怎样在工厂进行精益生产活动有了进一步认识。
觉得挺有意思,拿出来分享一下。
精益游戏一开始需要8名接受过精益生产培训的人员参与,通过用游戏的方式来模拟一间传统加工工厂的生产活动,大致会进行5~6轮,并在每轮之后,参与成员对结果进行总结、分析、讨论来找到可进行改善的地方,然后进行下轮游戏。
精益游戏的规则大致如下:该模拟的传统加工工厂的工序为:计划冲压装配热处理质检库房顾客.每个工序的指导书及规则:计划:小组根据3种主计划选定一组生产计划,计划员按照计划安排产品的生产顺序,确保冲压工按正确顺序进行生产。
(比如计划一:8个红色,2个蓝色,2个黄色)冲压:按照计划生产,冲压完毕的产品(积木)放进容器内,当容器内数量达到6个后,通知物料员送到下工序。
当冲压另一种颜色的产品时,需用秒表计时30秒的换模时间。
薪金由你冲压产品的数量决定。
装配:将两个小零件和两个大零件(小积木和大积木)装配到已冲压的半成品上,放入容器内,当容器内产品为6件后,需运送到下工序。
同样,薪金由生产数量决定。
热处理:将上工序产品放进加热炉加热,产品按批加热,即一同进炉,一同出炉,每批最大容量为8件,需加热60秒。
红色产品只能单独加热,黄色与蓝色可以一起加热。
该工序初始库存为3个未加热红色产品。
装运批量同样为6件产品(不多不少),且红色不可与其他颜色产品混装。
质检:根据废品标准进行检验,合格品放入容器,当达到6个后通知物料员送到下个工序。
仓库:给供应产品并记录供货状况(分迟交货和未交货),游戏开始后每15秒,会要求一种产品,如有就马上送,如没有作好迟交纪录,如在下个订单来前都没有交货,则作未交货纪录。
初始库存为3红,3黄,3蓝。
顾客:有48张卡片作为48个订单(红,黄,蓝三种,红色比例最大),第一个订单在游戏开始后30秒发出,以后间隔15秒一个订单。
企业管理理论的应用实践案例分享
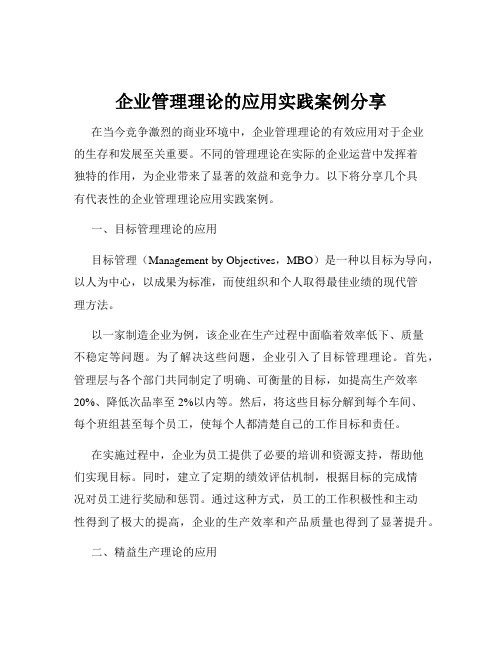
企业管理理论的应用实践案例分享在当今竞争激烈的商业环境中,企业管理理论的有效应用对于企业的生存和发展至关重要。
不同的管理理论在实际的企业运营中发挥着独特的作用,为企业带来了显著的效益和竞争力。
以下将分享几个具有代表性的企业管理理论应用实践案例。
一、目标管理理论的应用目标管理(Management by Objectives,MBO)是一种以目标为导向,以人为中心,以成果为标准,而使组织和个人取得最佳业绩的现代管理方法。
以一家制造企业为例,该企业在生产过程中面临着效率低下、质量不稳定等问题。
为了解决这些问题,企业引入了目标管理理论。
首先,管理层与各个部门共同制定了明确、可衡量的目标,如提高生产效率20%、降低次品率至 2%以内等。
然后,将这些目标分解到每个车间、每个班组甚至每个员工,使每个人都清楚自己的工作目标和责任。
在实施过程中,企业为员工提供了必要的培训和资源支持,帮助他们实现目标。
同时,建立了定期的绩效评估机制,根据目标的完成情况对员工进行奖励和惩罚。
通过这种方式,员工的工作积极性和主动性得到了极大的提高,企业的生产效率和产品质量也得到了显著提升。
二、精益生产理论的应用精益生产(Lean Production)是一种通过消除浪费、优化流程来提高生产效率和质量的管理理念。
一家汽车零部件制造企业在面临生产成本过高、交货期延迟等问题时,决定采用精益生产理论进行管理改革。
企业首先对整个生产流程进行了详细的价值流分析,找出了其中的浪费环节,如库存积压、过度加工、等待时间过长等。
然后,针对这些问题采取了一系列措施,如实施准时制生产(Just in Time,JIT),减少原材料和在制品库存;优化生产布局,减少物料搬运距离和时间;引入自动化设备,提高生产效率和精度。
此外,企业还注重培养员工的精益思维,鼓励他们提出改进建议,并建立了持续改进的机制。
经过一段时间的努力,企业的生产成本大幅降低,交货期明显缩短,产品质量也得到了客户的高度认可。
精益生产案例
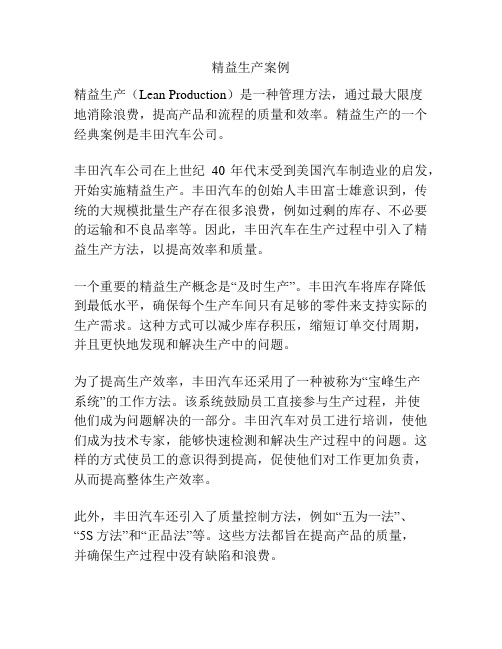
精益生产案例精益生产(Lean Production)是一种管理方法,通过最大限度地消除浪费,提高产品和流程的质量和效率。
精益生产的一个经典案例是丰田汽车公司。
丰田汽车公司在上世纪40年代末受到美国汽车制造业的启发,开始实施精益生产。
丰田汽车的创始人丰田富士雄意识到,传统的大规模批量生产存在很多浪费,例如过剩的库存、不必要的运输和不良品率等。
因此,丰田汽车在生产过程中引入了精益生产方法,以提高效率和质量。
一个重要的精益生产概念是“及时生产”。
丰田汽车将库存降低到最低水平,确保每个生产车间只有足够的零件来支持实际的生产需求。
这种方式可以减少库存积压,缩短订单交付周期,并且更快地发现和解决生产中的问题。
为了提高生产效率,丰田汽车还采用了一种被称为“宝峰生产系统”的工作方法。
该系统鼓励员工直接参与生产过程,并使他们成为问题解决的一部分。
丰田汽车对员工进行培训,使他们成为技术专家,能够快速检测和解决生产过程中的问题。
这样的方式使员工的意识得到提高,促使他们对工作更加负责,从而提高整体生产效率。
此外,丰田汽车还引入了质量控制方法,例如“五为一法”、“5S方法”和“正品法”等。
这些方法都旨在提高产品的质量,并确保生产过程中没有缺陷和浪费。
由于实施了精益生产,丰田汽车取得了巨大的成功。
丰田汽车以其高质量、可靠性和高效率而闻名全球。
丰田车的生产周期非常短,车辆的质量也得到了高度保证。
丰田汽车通过精益生产方法的实施,有效地提高了生产效率,减少了浪费,并提高了产品质量。
这为其他企业提供了一个成功的案例,也促进了全球制造业的转型和发展。
现场管理的卓越实践与标杆案例

现场管理的卓越实践与标杆案例引言现场管理是指对现场工作进行有效控制和监督的一种管理方法。
在各个行业中,现场管理被视为保证生产效率和顺利进行的重要因素之一。
卓越的现场管理实践可以帮助企业有效地提高工作效率、降低成本、提升产品质量以及改善员工安全和满意度。
本文将介绍一些在现场管理方面取得卓越实践的企业,并分析其标杆案例。
案例一:丰田汽车的现场管理实践丰田汽车是全球知名的汽车制造商,其现场管理实践一直被视为行业标杆。
丰田汽车在现场管理方面采用了“精益生产”(Lean Production)的方法,以最大限度地提高生产效率和产品质量。
丰田汽车注重员工参与和持续改进。
他们通过培养员工的创新和质量意识,鼓励员工积极参与现场管理,提出改善建议,并持续优化工作流程。
丰田汽车还实行了“错误防止”(Poka-yoke)的原则,通过在生产过程中引入自动化装置和检测设备,减少了人为错误,提高了产品质量。
另外,丰田汽车在供应链管理方面也取得了卓越的成果。
他们与供应商建立了紧密的合作伙伴关系,通过共享信息和资源,实现供应链的协同管理。
这种合作的方式不仅提高了供应链的敏捷性和灵活性,还降低了库存成本和交货周期。
案例二:沃尔玛的现场管理实践沃尔玛是世界最大的零售商之一,其现场管理实践也备受瞩目。
沃尔玛在现场管理方面注重供应链的协调和优化,以及仓储和物流的高效运作。
沃尔玛利用信息技术和数据分析工具来实现供应链的协同管理。
他们通过实时跟踪和监控销售数据和库存情况,以及与供应商进行紧密的合作,实现了快速响应市场需求和准确配送商品的目标。
沃尔玛还通过优化仓储和物流流程,实现了即时补货和最低库存的管理目标,降低了运营成本,并提升了顾客满意度。
此外,沃尔玛还注重员工的培训和参与。
他们通过提供培训和发展机会,激励和激发员工的工作激情和创造力。
沃尔玛鼓励员工积极参与现场管理,提出改进建议,并采取措施来实施这些改善措施。
以上介绍的丰田汽车和沃尔玛是在现场管理方面取得了卓越实践的企业,并成为行业的标杆。
精益生产游戏

精益生产游戏Lean Game本月7,8号,在公司内部组织了一次精益生产游戏活动(Lean Game)。
通过此次活动,让所有参与者对什么是精益生产以及怎样在工厂进行精益生产活动有了进一步认识。
觉得挺有意思,拿出来分享一下。
精益游戏一开始需要8名接受过精益生产培训的人员参与,通过用游戏的方式来模拟一间传统加工工厂的生产活动,大致会进行5~6轮,并在每轮之后,参与成员对结果进行总结、分析、讨论来找到可进行改善的地方,然后进行下轮游戏。
精益游戏的规则大致如下:该模拟的传统加工工厂的工序为:计划—冲压—装配—热处理—质检—库房—顾客每个工序的工作指导书及规则:计划:小组根据3种主计划选定一组生产计划,计划员按照计划安排产品的生产顺序,确保冲压工按正确顺序进行生产。
(比如计划一:8个红色,2个蓝色,2个黄色)冲压:按照计划生产,冲压完毕的产品(积木)放进容器内,当容器内数量达到6个后,通知物料员送到下工序。
当冲压另一种颜色的产品时,需用秒表计时30秒的换模时间。
薪金由你冲压产品的数量决定。
装配:将两个小零件和两个大零件(小积木和大积木)装配到已冲压的半成品上,放入容器内,当容器内产品为6件后,需运送到下工序。
同样,薪金由生产数量决定。
热处理:将上工序产品放进加热炉加热,产品按批加热,即一同进炉,一同出炉,每批最大容量为8件,需加热60秒。
红色产品只能单独加热,黄色与蓝色可以一起加热。
该工序初始库存为3个未加热红色产品。
装运批量同样为6件产品(不多不少),且红色不可与其他颜色产品混装。
质检:根据废品标准进行检验,合格品放入容器,当达到6个后通知物料员送到下个工序。
仓库:给客户供应产品并记录供货状况(分迟交货和未交货),游戏开始后每15秒,客户会要求一种产品,如有就马上送,如没有作好迟交纪录,如在下个订单来前都没有交货,则作未交货纪录。
初始库存为3红,3黄,3蓝。
顾客:客户有48张卡片作为48个订单(红,黄,蓝三种,红色比例最大),第一个订单在游戏开始后30秒发出,以后间隔15秒一个订单。
精益生产与实际案例

精益生产与实际案例精益生产是一种以减少浪费为核心的管理方法,旨在提高生产效率、降低成本、改善质量和满足客户需求。
下面我将介绍一个实际案例,展示精益生产在制造业中的应用。
这个案例是关于一家传统制造业公司,该公司生产玩具汽车,面临着来自市场竞争对手的压力。
这家公司的生产线效率低下,生产周期长,产品质量也不稳定。
为了改变这个局面,公司决定引入精益生产理念。
首先,公司进行了价值流映射,以了解整个生产过程中的价值流和不必要的浪费。
通过对各个步骤进行分析,公司发现许多步骤是多余的,而且存在大量的等待时间和物料的不必要移动。
接下来,公司实施了一系列的改进措施。
首先,他们重新设计了生产线布局,将各个工作站之间的距离缩短,减少了物料运输的时间和距离。
其次,他们优化了工作流程,减少了无效的操作和重复的工作。
同时,公司也对员工进行了培训,提高了他们的技能和工作效率。
通过这些改进,公司实现了显著效益的提升。
生产周期缩短了一半,产品质量得到了大幅提升,而产品的价格也降低了10%。
公司的生产效率大幅提高,能够满足客户更快的交货需求,同时降低了库存成本。
除此之外,公司还引入了精益生产中的5S和标准化工作等概念。
通过整理和清理工作场所,减少了物料的丢失和遗漏,提高了工作的效率。
通过制定标准化工作程序,公司能够保持一致的生产质量,并且易于培训新员工。
总之,精益生产的应用帮助这家传统制造业公司实现了生产效率的大幅提升,降低了生产成本,并提高了产品质量。
这个案例说明了精益生产在实践中的价值,不仅能够增强企业的竞争力,还能够为顾客提供更好的产品和服务。
精益生产是一种以减少浪费为核心的管理方法,旨在提高生产效率、降低成本、改善质量和满足客户需求。
在现代制造业中,越来越多的公司将精益生产作为一种重要的运营策略,以应对激烈的市场竞争和不断变化的客户需求。
在实际中,许多公司通过引入精益生产概念和方法,成功地改进了业务流程,提高了生产效率和质量水平。
精益生产案例分析
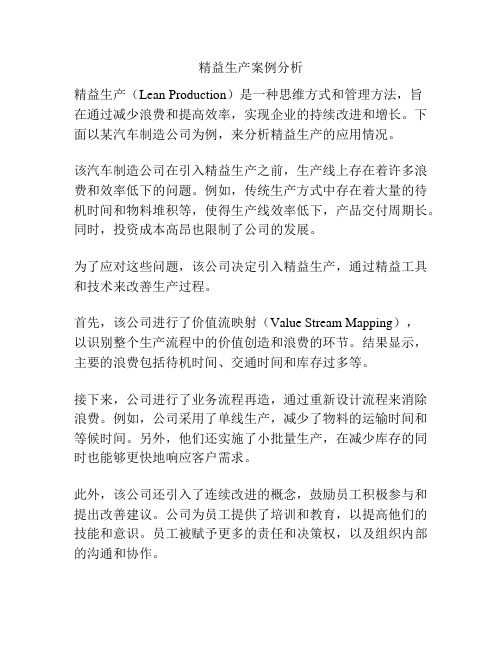
精益生产案例分析精益生产(Lean Production)是一种思维方式和管理方法,旨在通过减少浪费和提高效率,实现企业的持续改进和增长。
下面以某汽车制造公司为例,来分析精益生产的应用情况。
该汽车制造公司在引入精益生产之前,生产线上存在着许多浪费和效率低下的问题。
例如,传统生产方式中存在着大量的待机时间和物料堆积等,使得生产线效率低下,产品交付周期长。
同时,投资成本高昂也限制了公司的发展。
为了应对这些问题,该公司决定引入精益生产,通过精益工具和技术来改善生产过程。
首先,该公司进行了价值流映射(Value Stream Mapping),以识别整个生产流程中的价值创造和浪费的环节。
结果显示,主要的浪费包括待机时间、交通时间和库存过多等。
接下来,公司进行了业务流程再造,通过重新设计流程来消除浪费。
例如,公司采用了单线生产,减少了物料的运输时间和等候时间。
另外,他们还实施了小批量生产,在减少库存的同时也能够更快地响应客户需求。
此外,该公司还引入了连续改进的概念,鼓励员工积极参与和提出改善建议。
公司为员工提供了培训和教育,以提高他们的技能和意识。
员工被赋予更多的责任和决策权,以及组织内部的沟通和协作。
通过精益生产的应用,该汽车制造公司取得了显著的改进和成果。
公司生产效率提高了30%,产品交付时间缩短了50%。
另外,公司库存水平减少了60%,大幅降低了企业的资金占用成本。
除此之外,品质管理也得到了明显的提升。
公司通过实行全员质量管理,强调“Do it right the first time”的原则,减少了缺陷率。
总之,精益生产的应用使得该汽车制造公司在面临激烈竞争的市场中获得了差异化优势。
通过减少浪费和提高效率,公司在成本控制上取得了明显的改善,提高了客户满意度。
此外,精益生产还培养了公司内部的团队合作精神和创新意识,为企业的可持续发展打下了坚实的基础。
继续写相关内容,1500字精益生产(Lean Production)作为一种有效的生产管理方法,不仅可以帮助企业提高效率,降低成本,还能够提高产品质量和客户满意度。
精益生产游戏(Lean Game)
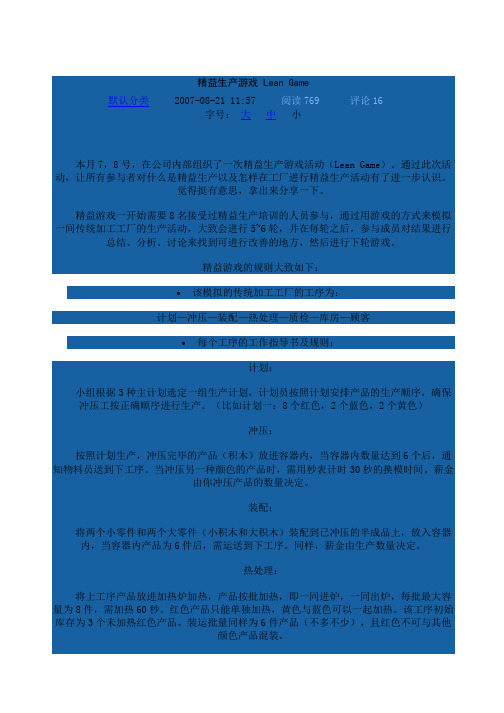
精益生产游戏 Lean Game默认分类2007-08-21 11:57 阅读769 评论16字号:大中小本月7,8号,在公司内部组织了一次精益生产游戏活动(Lean Game)。
通过此次活动,让所有参与者对什么是精益生产以及怎样在工厂进行精益生产活动有了进一步认识。
觉得挺有意思,拿出来分享一下。
精益游戏一开始需要8名接受过精益生产培训的人员参与,通过用游戏的方式来模拟一间传统加工工厂的生产活动,大致会进行5~6轮,并在每轮之后,参与成员对结果进行总结、分析、讨论来找到可进行改善的地方,然后进行下轮游戏。
精益游戏的规则大致如下:•该模拟的传统加工工厂的工序为:计划—冲压—装配—热处理—质检—库房—顾客•每个工序的工作指导书及规则:计划:小组根据3种主计划选定一组生产计划,计划员按照计划安排产品的生产顺序,确保冲压工按正确顺序进行生产。
(比如计划一:8个红色,2个蓝色,2个黄色)冲压:按照计划生产,冲压完毕的产品(积木)放进容器内,当容器内数量达到6个后,通知物料员送到下工序。
当冲压另一种颜色的产品时,需用秒表计时30秒的换模时间。
薪金由你冲压产品的数量决定。
装配:将两个小零件和两个大零件(小积木和大积木)装配到已冲压的半成品上,放入容器内,当容器内产品为6件后,需运送到下工序。
同样,薪金由生产数量决定。
热处理:将上工序产品放进加热炉加热,产品按批加热,即一同进炉,一同出炉,每批最大容量为8件,需加热60秒。
红色产品只能单独加热,黄色与蓝色可以一起加热。
该工序初始库存为3个未加热红色产品。
装运批量同样为6件产品(不多不少),且红色不可与其他颜色产品混装。
质检:根据废品标准进行检验,合格品放入容器,当达到6个后通知物料员送到下个工序。
仓库:给客户供应产品并记录供货状况(分迟交货和未交货),游戏开始后每15秒,客户会要求一种产品,如有就马上送,如没有作好迟交纪录,如在下个订单来前都没有交货,则作未交货纪录。
精益生产案例

精益生产案例精益生产(Lean Production)是一种以精益思维为基础的生产管理方法,旨在通过减少浪费、提高效率和质量,实现生产过程的优化。
下面列举10个精益生产案例,以展示其在不同领域的应用和效果。
1. 丰田生产系统(T oyota Production System,简称TPS)是精益生产的典型案例。
TPS通过标准化流程、零库存、及时生产等手段,实现了生产效率和质量的大幅提升。
丰田汽车以其高效、灵活和质量稳定的生产模式成为全球汽车行业的典范。
2. 亚马逊的仓储和物流管理也是一个成功的精益生产案例。
亚马逊通过使用先进的仓储机器人、优化的物流网络和实时数据分析,实现了高效的订单处理和快速的配送服务,提高了客户满意度。
3. 丹麦乐高公司采用精益生产方法,实现了高效的生产和供应链管理。
乐高通过精细的计划、准确的库存控制和灵活的生产调度,保证了产品的高质量和及时交付,同时降低了库存成本。
4. 耐克公司在生产和供应链管理中采用了精益生产的方法。
耐克通过减少生产过程中的浪费、优化供应链和加强与供应商的合作,提高了生产效率和产品质量,同时缩短了产品上市时间。
5. 日本的富士康科技集团(Foxconn)是全球最大的电子制造服务公司之一,也是精益生产的成功案例。
富士康通过引进先进的生产设备、标准化工作流程和持续的员工培训,实现了高效的生产和质量控制,为客户提供高品质的电子产品。
6. 美国的快餐连锁企业麦当劳通过精益生产的方法,实现了订单处理和服务的高效率。
麦当劳通过优化餐厅布局、标准化工作流程和使用先进的点餐系统,提高了订单处理速度和客户满意度。
7. 日本的丸红公司是一家全球知名的物流和供应链管理公司,也是精益生产的典范。
丸红公司通过优化仓储和运输流程、精细的库存管理和实时数据分析,实现了高效的物流运作和准时交货。
8. 德国汽车制造商奔驰公司采用精益生产方法,实现了高质量和高效率的生产。
奔驰通过持续改进生产流程、优化零部件供应和自动化生产线,提高了生产效率和产品质量。
leanJITgame精益生产游戏
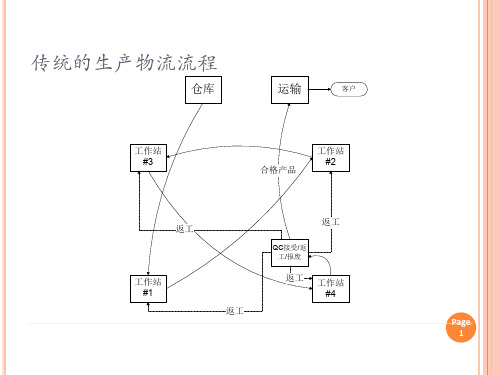
Continue exercise until 10 minutes has elapsed. 10分钟之后结束游戏
Write down key measures on a flipchart. 记录数据
Page 7
练习
JIT生产方式: 5 minutes into exercise introduce a “design change” switching
colors on stations 3 and 4. All product that cannot be “reworked” to the proper color must be scrapped. 5分钟后转换工作站3跟工作站4的颜色,不能返工的在制 品必须报废
Continue exercise until 10 minutes has elapsed. 10分钟之后结束游戏
传统生产方式: 5 minutes into exercise introduce a “design change” switching
colors on stations 3 and 4. All product that cannot be “reworked” to the proper color must be scrapped. 5分钟后转换工作站3跟工作站4的颜色,不能返工的在制 品必须报废
Station 3
Station 4
SUPER SHAPE SUBASSEMBLY,
REV. X
Page 3
人员安排
传统的制造
JIT 生产模式
需要6人(每个工作站1个人, 需要4人(没有物料传输人或者QC) QC1名,物料传输人员1名)
(1) 顾客 (1) 时间记录员 (1) 规则/返工监督者
精益生产之仓库模拟游戏

精益生产之仓库模拟游戏精益生产是一种用于优化生产流程的管理方法,通过最大限度地减少浪费,提高生产效率。
在仓库模拟游戏中,玩家可以扮演仓库经理,管理和优化仓库内的各项工作,以实践精益生产的理念。
游戏开始时,玩家将面对一个初始的仓库布局,其中包括货架、储物箱、搬运设备等。
玩家需要根据不同的产品类型和销售需求来进行合理的仓库布局,以便提高货物的存储和调配效率。
例如,将销量较大的产品放在靠近出口的货架上,以便快速装载。
在仓库模拟游戏中,玩家需要时刻监控库存情况,并根据实际需求进行智能调度。
当库存不足时,玩家需要及时向供应商下订单,以防止产品缺货。
同时,玩家还可以使用精益生产的原则,通过减少非价值增加的活动,来提高货物的周转速度和准确性。
在游戏中,玩家还需面对一系列的挑战和难题。
例如,玩家可能需要应对来自不同地区的订单,需要根据订单的紧急程度和产品的位置,制定有效的货物调度计划。
此外,仓库设备的维护和修理也是一项重要的任务,玩家需要及时安排维修人员进行维护,以保证设备的正常运转。
随着游戏的进行,玩家可以逐步解锁更多的仓库功能和设备,例如智能仓储系统、自动化搬运设备等。
通过合理的设施投资和流程优化,玩家可以逐渐提高仓库的运营效率,降低运营成本,实现更高水平的精益生产。
仓库模拟游戏不仅可以提供娱乐和挑战,还可以让玩家亲身体验和理解精益生产的概念和原则。
通过这种互动的方式,玩家可以在娱乐中学习,并在实践中掌握精益生产的技巧。
这样的模拟游戏有助于培养玩家的管理能力、决策能力和团队协作精神,同时也可以为实际的仓库工作提供一定的参考和启示。
总之,仓库模拟游戏是一种有趣而有益的娱乐方式,通过实践精益生产的理念,可以帮助玩家理解和应用其在实际生产环境中的价值。
这样的游戏不仅可以提供娱乐,还有助于培养思考和解决问题的能力,对于感兴趣或从事相关行业的人来说,更是一种有效的学习和实践平台。
仓库模拟游戏是一种非常有趣和有教育意义的游戏。
Lean Game
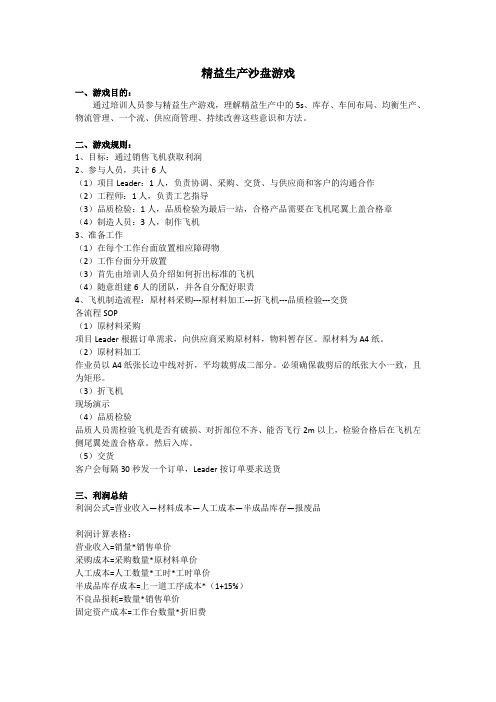
精益生产沙盘游戏一、游戏目的:通过培训人员参与精益生产游戏,理解精益生产中的5s、库存、车间布局、均衡生产、物流管理、一个流、供应商管理、持续改善这些意识和方法。
二、游戏规则:1、目标:通过销售飞机获取利润2、参与人员,共计6人(1)项目Leader:1人,负责协调、采购、交货、与供应商和客户的沟通合作(2)工程师:1人,负责工艺指导(3)品质检验:1人,品质检验为最后一站,合格产品需要在飞机尾翼上盖合格章(4)制造人员:3人,制作飞机3、准备工作(1)在每个工作台面放置相应障碍物(2)工作台面分开放置(3)首先由培训人员介绍如何折出标准的飞机(4)随意组建6人的团队,并各自分配好职责4、飞机制造流程:原材料采购---原材料加工---折飞机---品质检验---交货各流程SOP(1)原材料采购项目Leader根据订单需求,向供应商采购原材料,物料暂存区。
原材料为A4纸。
(2)原材料加工作业员以A4纸张长边中线对折,平均裁剪成二部分。
必须确保裁剪后的纸张大小一致,且为矩形。
(3)折飞机现场演示(4)品质检验品质人员需检验飞机是否有破损、对折部位不齐、能否飞行2m以上,检验合格后在飞机左侧尾翼处盖合格章。
然后入库。
(5)交货客户会每隔30秒发一个订单,Leader按订单要求送货三、利润总结利润公式=营业收入—材料成本—人工成本—半成品库存—报废品利润计算表格:营业收入=销量*销售单价采购成本=采购数量*原材料单价人工成本=人工数量*工时*工时单价半成品库存成本=上一道工序成本*(1+15%)不良品损耗=数量*销售单价固定资产成本=工作台数量*折旧费要求:1、每轮后进行讨论,提出改善方案2、一轮后只能进行3次改善。
Lean Game -v02

Lean Day Preparation
July 11, 2017
22
精益游戏
第二轮问题点及改善点
3 min 小组讨论(可改变布局前提下提出改善点)
Lean Day Preparation
July 11, 2017
23
精益游戏
第二轮问题点及改善点
32 32
Thank you!
Lean Day Preparation
July 11, 2017
26
第三轮
2. 配料站
按照超市信息拉动配料,配送原料至Kanban区。Kanban区初始状态:按照颜 色和工站分别放置原料,共需6个物料盒。
Lean Day Preparation
July 11, 2017
27
第三轮
3. 半成品组装站
July 11, 2017
17
第二轮
2. 配料站
根据生产计划所下订单顺序,利用液压车配料,工单随实物移动。
注:一个液压车只放一个工单物料,无液压车可用时,则处于等待状态
Lean Day Preparation
July 11, 2017
18
第二轮
3. 半成品组装站
装配Line Service送来的原料,不同颜色需要换模10秒(用笔写数字1~10)。
30
第三轮
6. Line Service
用液压车从质检站取走成品和2个工单,入库。同时可辅助有帮助需求的 工站。
生产经理需记录从首次下单到完成9个成品所需总时间。
Lean Day Preparation
July 11, 2017
精益生产管理的成功案例

精益生产管理的成功案例精益生产管理(Lean Production Management)促使企业实现高效运营、降低成本并提升质量。
下面将介绍三个成功应用精益生产管理的案例。
案例一:丰田汽车公司丰田汽车公司是一个广为人知的精益生产管理的成功案例。
该公司在汽车制造业中引入了丰田生产系统(Toyota Production System),凭借其卓越的精益管理理念,有效地提高了效率、质量和利润。
丰田生产系统强调持续改进和减少浪费。
通过精确计划、高效布局和员工参与决策等措施,丰田成功地降低了库存、提高了生产灵活性,同时还能满足客户需求。
案例二:波音公司波音公司是另一个成功应用精益生产管理的案例。
该航空制造企业采用了精益管理的方法来提高生产效率、降低成本并提供高质量的产品。
波音公司运用精益生产管理来优化供应链、改进生产流程、减少制造时间和提高资源利用率。
通过精细制定的生产计划、物料缩短流程和追求卓越质量的理念,波音不断提高产品竞争力,为客户提供满意的解决方案。
案例三:日本服装公司日本一些服装公司通过精益生产管理的方式,实现了生产过程的高效、卓越的质量和最小化的浪费。
这些公司主要通过以下措施来提升业绩。
首先,改善生产流程。
服装企业会合理安排生产线,确保各个生产环节之间的流程顺畅,并减少传统大量存货。
其次,强调员工培训和参与,使每个人都能理解自己的角色和责任,并为精益生产目标贡献力量。
再次,注重质量管理。
这些企业通过引入严格的质量控制措施,确保产品达到最高标准。
结论:以上三个案例展示了精益生产管理在不同行业中的成功应用。
丰田汽车公司、波音公司和日本服装公司通过实施精益管理的策略,优化了生产流程、提高了质量、降低了成本,进而实现了业务的卓越表现。
这些成功案例表明,精益生产管理已经成为许多企业提高竞争力和持续发展的重要工具。
精益生产(Lean Production)
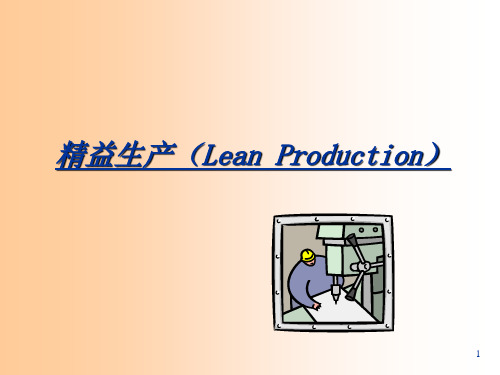
27 h
全面生产系统的浪费
生产要素的5MQS: Man(人) Machine(机器) Material(物料) Method(作业方法) Management(管理) Quality(品质) Safety(安全)
28 h
5
M
Q
S
的 浪 费
分类
浪费
说明
人 的 浪 费
1. 行走的浪费 2. 监视的浪费 3. 寻找的浪费 4. 动作的浪费 5. 职责不清的浪费
25 h
每天都在“烧钱”
以下不良现象或浪费在“烧钱” 仪容不整的工作人员; 机器设备放置不合理; 机器设备保养不当; 原材料、在制品、完成品、待修品、不 良品等随意摆放;
通道不明确或被占; 好心疼啊!
工作场所脏污。
26 h
全面生产系统的浪费
什么是浪费: ✓ 不增加价值的活动,是浪费; ✓ 尽管是增加价值的活动,所用的资源超过了
9 h
精益生产追求的目标
零 7个“
”目标
☆ 零切换浪费 ☆ 零库存 ☆ 零浪费 ☆ 零不良 ☆ 零故障 ☆ 零停滞
☆ 零事故
10 h
精益生产追求的目标
零目标 目的
现状
思考原则与方法
7个“零”目标 零 切换 浪费
多品种 切换时间长, 对应 切换后不稳定
零 库存
发现 真正 问题
大量库存造成成本 高、周转困难,且 看不到真正的问题 在哪里
4 h
何谓精益生产方式
Just In Time
适品 ·适量 ·适时
JIT的基本思想是:只在需要的时候、按需 要 的量、生产所需的产品,故又被称为准时制 生产、适时生产方式、看板生产方式。
精益生产游戏(Lean Game)(doc 8页)

精益生产游戏(Lean Game)(doc 8页)精益生产游戏 Lean Game默认分类 2007-08-21 11:57 阅读769 评论16字号:大中小本月7,8号,在公司内部组织了一次精益生产游戏活动(Lean Game)。
通过此次活动,让所有参与者对什么是精益生产以及怎样在工厂进行精益生产活动有了进一步认识。
觉得挺有意思,拿出来分享一下。
精益游戏一开始需要8名接受过精益生产培训的人员参与,通过用游戏的方式来模拟一间传统加工工厂的生产活动,大致会进行5~6轮,并在每轮之后,参与成员对结果进行总结、分析、讨论来找到可进行改善的地方,然后进行下轮游戏。
精益游戏的规则大致如下:•该模拟的传统加工工厂的工序为:计划—冲压—装配—热处理—质检—库房—顾客•每个工序的工作指导书及规则:计划:小组根据3种主计划选定一组生产计划,计划员按照计划安排产品的生产顺序,确保冲压工按正确顺序进行生产。
(比如计划一:8个红色,2个蓝色,2个黄色)冲压:按照计划生产,冲压完毕的产品(积木)放进容器内,当容器内数量达到6个后,通知物料员送到下工序。
当冲压另一种颜色的产品时,需用秒表计时30秒的换模时间。
薪金由你冲压产品的数量决定。
装配:将两个小零件和两个大零件(小积木和大积木)装配到已冲压的半成品上,放入容器内,当容器内产品为6件后,需运送到下工序。
同样,薪金由生产数量决定。
热处理:将上工序产品放进加热炉加热,产品按批加热,即一同进炉,一同出炉,每批最大容量为8件,需加热60秒。
红色产品只能单独加热,黄色与蓝色可以一起加热。
该工序初始库存为3个未加热红色产品。
装运批量同样为6件产品(不多不少),且红色不可与其他颜色产品混装。
质检:根据废品标准进行检验,合格品放入容器,当达到6个后通知物料员送到下个工序。
仓库:给客户供应产品并记录供货状况(分迟交货和未交货),游戏开始后每15秒,客户会要求一种产品,如有就马上送,如没有作好迟交纪录,如在下个订单来前都没有交货,则作未交货纪录。
- 1、下载文档前请自行甄别文档内容的完整性,平台不提供额外的编辑、内容补充、找答案等附加服务。
- 2、"仅部分预览"的文档,不可在线预览部分如存在完整性等问题,可反馈申请退款(可完整预览的文档不适用该条件!)。
- 3、如文档侵犯您的权益,请联系客服反馈,我们会尽快为您处理(人工客服工作时间:9:00-18:30)。
精益生产游戏(LeanGame)实践案例
最近内部组织了一次精益生产游戏活动(LeanGame)。
通过此次活动,让所有参与者对什么是精益生产以及怎样在工厂进行精益生产活动有了进一步认识。
觉得挺有意思,拿出来分享一下。
精益游戏一开始需要8名接受过精益生产培训的人员参与,通过用游戏的方式来模拟一间传统加工工厂的生产活动,大致会进行5~6轮,并在每轮之后,参与成员对结果进行总结、分析、讨论来找到可进行改善的地方,然后
进行下轮游戏。
精益游戏的规则大致如下:
该模拟的传统加工工厂的工序为:计划冲压装配热处理质检库房顾客.
每个工序的指导书及规则:
计划:小组根据3种主计划选定一组生产计划,计划员按照计划安排产品的生产顺序,确保冲压工按正确顺序进行生产。
(比如计划一:8个红色,2个蓝色,2个黄色)
冲压:按照计划生产,冲压完毕的产品(积木)放进容器内,当容器内数量达到6个后,通知物料员送到下工序。
当冲压另一种颜色的产品时,需用秒表计时30秒的换模时间。
薪金由你冲压产品的数量决定。
装配:将两个小零件和两个大零件(小积木和大积木)装配到已冲压的半成品上,放入容器内,当容器内产品为6件后,需运送到下工序。
同样,薪金由生产数量决定。
热处理:将上工序产品放进加热炉加热,产品按批加热,即一同进炉,一同出炉,每批最大容量为8件,需加热60秒。
红色产品只能单独加热,黄色与蓝色可以一起加热。
该工序初始库存为3个未加热红色产品。
装运批量同样为6件产品(不多不少),且红色不可与其他颜色产品混装。
质检:根据废品标准进行检验,合格品放入容器,当达到6个后通知物料员送到下个工序。
仓库:给供应产品并记录供货状况(分迟交货和未交货),游戏开始后每15秒,会要求一种产品,如有就马上送,如没有作好迟交纪录,如在下个订单来前都没有交货,则作未交货纪录。
初始库存为3红,3黄,3蓝。
顾客:有48张卡片作为48个订单(红,黄,蓝三种,红色比例最大),第一个订单在游戏开始后30秒发出,以
后间隔15秒一个订单。
最后一张订单发出15秒后,该轮游戏结束。
有些特殊订单会随机发出,12倍于普通订单交货时间(3分钟)几倍于普通订单的售价。
物料员:各个站之间搬运成品及半成品,给冲压和装配工位提供零件。
(该零件为顾客处回收的成品拆卸得到)
规则介绍完毕之后游戏正式开始:第一轮:
第一轮布局的安排设置是固定的:
我们故意将每个工序离得较远,物料员在这轮游戏中往返奔波,累得够呛;其他工序也不平衡,有很忙碌的,
也有很闲的。
48个订单很快就生产完了,但结果如何呢游戏结束后,统计了交货情况及在线库存,结果分析如果以利润来判断该轮结束后工厂的盈利状况,那么显然是亏本。
利润=-179单位交货率=71%。
随后,参与成员间进行了分析讨论,认识到现场布局不合理,工序交叉,且工序之间不平衡,于是做出了一些改善:(注:每轮中,只允许选择最多3个改善点)
1.改变布局,按流程顺序首尾相连;makeaflow
2.消除生产瓶颈,装配人员减少两个零件的装配,
由加热工人在空闲时装配;3.移动代表各个工序的桌子靠在一起,减少物料员的走动距离。
第二轮:
那我们先看看第二轮如何呢
首先是布局改变了,我们能清晰地看到流程并且物料员的走动距离变短了。
装配与热处理的配合消除了流程中的瓶颈工序。
那么结果如何呢利润=-156单位交货率=81%
看来它们均有上升,但工厂仍然不赚钱啊,为什么呢在接下来的讨论中有人已经注意到桌子(代表工厂厂房,设备等固定投资)的数量,以及生产结束时大量的半成品
和成品数量是影响利润的一个原因。
该轮讨论后决定如下改善:
1.优化布局,流程,去掉两张桌子(优化流程,节约厂房空间);
2.热处理炉由一个8格60秒加热时间的换为两个4格加热时间为80秒的小加热炉(小批量,生产更具弹性)
3.实行单件流,冲压和装配之间1件传输(一件流)第三轮:
让我们看看经过第二轮改变后效果如何呢
可以看到,流程结合更紧密,物料员已经几乎无事可做,偶尔帮助拆卸成品提供零件(其实在之前讨论时已经有人提出去掉物料员,但一次只能改善3处,就未作优先处理)。
并且在此轮,游戏小组已经敢于接受顾客的特殊订单了。
那么,该轮完后,结果又如何呢利润=-33单位交货率=85%
看上去有很大改善,但还是没赚钱,问题在哪儿呢小组人员又开始了讨论,下面原因被认为是主要的影响:库存仍然很大,废品率升高,有3个特殊订单没能完成。
小组进行分析讨论后决定出新的三个改善点:
1.冲压工序换模具时间从原来的30秒提高为15秒(通过SMED,在工厂可以实现的)2.加热炉换为4个迷你型的,每个2格,加热时间80秒3.省去物料员,流水作业第四轮:物料员没有啦:在该轮中,又增加了3个特殊订单(增加的同时会减掉3个普通订单)。
该轮结束后:利润=169交货率=96%
大家已经开始欢呼了,工厂第一次赚钱了,并且在顾客不断增加特殊订单的情况下,工厂的交货率仍然保持在96%。
但仍然不足够。
这时候需要介入引导参与者了:a.
取消计划员,引入看板方式,采用拉动系统。
每15秒要求一件产品,我们的生产周期是多少看板容量需要设置多少b.那些防呆措施可以采取,用自检代替质检
经过讨论,小组成员决定如下改变:
1.取消计划人员,采用拉动系统,看板容量在库房为5:2:2(红:黄:蓝),加热处看板容量为4:1:1(红:黄:蓝)
2.确定质检标准,每个工序自检,取消专门的质检工序;3.去掉一张桌第五轮:此轮结束,大获全胜:利
润=381交货率=98%
随后进行的一些总结中,大家也都谈了很多,包括我自己在这个过程中也有新的体会和思考:
1.值得一提的是整个过程我都没强调5S,但大家在整个过程中都非常注意零件(不同颜色形状的积木)的整理,整顿,非常自觉的做5S。
但在工厂为什么5S就那么难以推行呢2.很多工厂推行精益生产失败,是不是他们在顺序上出错比如在该游戏中,如果在布局流程改进之前就推行单件流和看板,当然会失败。
3.工厂有多大能力在多长时间里做出改善,这非常需要了解,不然一次性给工厂太多培训,太多改善点,会适得其反。
所以为什么即使在一个游戏中,一次也仅仅允许3个改善。
也许还有很多,会留给我们慢慢去体会。