催化油浆净化处理方法及其化工利用建议
催化裂化油浆系统运行分析及优化措施
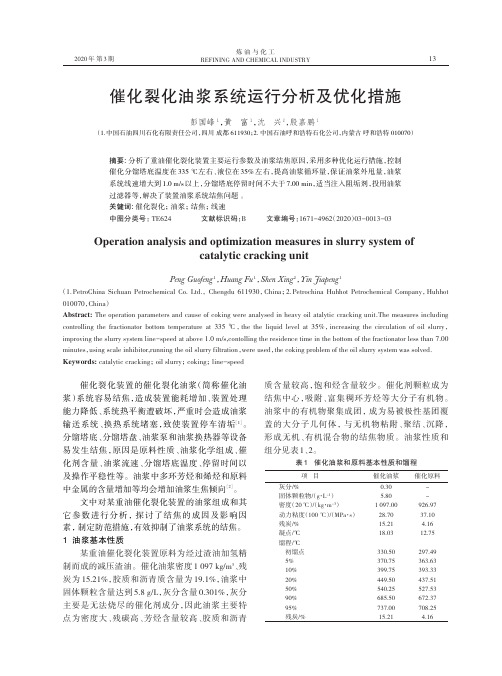
催化裂化油浆系统运行分析及优化措施彭国峰1,黄富1,沈兴2,殷嘉鹏1(1.中国石油四川石化有限责任公司,四川成都611930;2.中国石油呼和浩特石化公司,内蒙古呼和浩特010070)摘要:分析了重油催化裂化装置主要运行参数及油浆结焦原因,采用多种优化运行措施,控制催化分馏塔底温度在335℃左右、液位在35%左右,提高油浆循环量,保证油浆外甩量,油浆系统线速增大到1.0m/s以上,分馏塔底停留时间不大于7.00min,适当注入阻垢剂,投用油浆过滤器等,解决了装置油浆系统结焦问题。
关键词:催化裂化;油浆;结焦;线速中图分类号:TE624文献标识码:B文章编号:1671-4962(2020)03-0013-03Operation analysis and optimization measures in slurry system ofcatalytic cracking unitPeng Guofeng1,Huang Fu1,Shen Xing2,Yin Jiapeng1(1.PetroChina Sichuan Petrochemical Co.Ltd.,Chengdu611930,China;2.Petrochina Huhhot Petrochemical Company,Huhhot 010070,China)Abstract:The operation parameters and cause of coking were analysed in heavy oil atalytic cracking unit.The measures including controlling the fractionator bottom temperature at335℃,the the liquid level at35%,increasing the circulation of oil slurry,improving the slurry system line-speed at above1.0m/s,contolling the residence time in the bottom of the fractionator less than7.00 minutes,using scale inhibitor,running the oil slurry filtration,were used,the coking problem of the oil slurry system was solved. Keywords:catalytic cracking;oil slurry;coking;line-speed催化裂化装置的催化裂化油浆(简称催化油浆)系统容易结焦,造成装置能耗增加、装置处理能力降低、系统热平衡遭破坏,严重时会造成油浆输送系统、换热系统堵塞,致使装置停车清垢[1]。
催化油浆综合利用的技术措施

状焦 、 炭黑 , 作 为橡胶 软化 剂和 填充油 等 。本文 对催 化 油浆 综合 利用 方 面 的技 术 措 施 进 行 了综 述 , 同 时 对 催 化油浆 的综 合利 用前 景进 行 了展 望 。
催 化 油 浆 综 合 利 用 的 技 术 措 施
李 林, 徐 海清
( 中 国石 兰 州 石 化 公 司 炼 油 厂 , 甘肃兰州 7 3 0 0 6 0 )
摘要 : 综述 了催化油浆利用技术方 面的研究进展 , 包括炼 油装 置掺 炼 , 生产道路沥青 、 针状焦 、 炭黑 , 作为橡胶软化剂和填充油等 , 对催 化油浆 的综合利用前景进行 了展望 。 关键词 : 催 化油 浆 芳烃 利用 掺炼 道 路沥青
一
胶 质沥青 质 和残炭 的含量 低 。根据 催化 油浆 的特殊
性质 , 可 将 其 送 往 炼 油 装 置掺 炼 , 以增 加 轻 质 油 收 率; 还 可作 为生产 道路 沥青 、 针状 焦 、 炭黑 、 橡胶 软化
种副 产 品 , 由于 密度 较 大 、 相 对 分 子 质量 大 、 黏 度
第3 4卷 第 1 期 2 0 1 3年 2月
化 学 工 业 与 工 程 技 术
J o u r n a l o f C h e mi c a l I n d u s t r y& E n g i n e e r i n g
Vo 1 . 3 4 No. 1 Fe b ., 2 01 3
s o f t e n e r a n d e x t e n d e r o i l , t h e c o mp r e h e n s i v e u t i l i z a t i o n p r o s p e c t o f c a t a l y t i c c r a c k i n g s l u r r y o i l i s p r o s p e c t e d .
催化裂化油浆处理方法

催化裂化是炼油行业的一个重要的二次加工手段,是生产液化石油气和高辛烷值汽油的主要装置,我国到1998年底炼油能力已达24455万吨/年,催化裂化能力已达8429万吨(含催化裂解167万吨/年),约占原油加工量的34.4%,传统的蜡油原料明显不足,为扩大原料来源,提高炼油行业的加工深度,向深加工要效益,故在原料中掺入一定量的常压渣油、焦化蜡油,减压渣油,导致原料越来越重,质量越来越差。
原料中烷烃最容易裂化,环烷烃类次之,芳烃类化合物最难裂化,故反应产物中稠环芳烃和胶质等越来越多,生焦越来越多,导致再生温度提高,装置处理能力下降。
国内炼厂都采取减少油浆回炼比,外甩部分油浆的措施,像南京炼油厂从1986年开始甩油浆,FCC进料150吨/时,有10吨油浆返回进料,外甩油浆8吨左右,约占进料的5%,结果再生器温度降低15℃左右,装置处理能力约提高10%,当然各炼厂情况不完全相同,外甩油浆量在5—10%,我国每年排放油浆总量达750万吨左右。
油浆中大约50%的饱和烃,40%的芳烃和稠环芳烃,10%的胶质和沥青质,若将其有效地分离,进行深度加工,可以发挥巨大的经济效益.饱和烃是优质的催化裂化原料,芳烃、胶质、沥青质等是生产炭黑、针状焦、重质道路沥青、橡胶填充油、塑料增塑剂、导热油、碳纤维等的优质原料,国内众多科技工作者在这方面做过大量的工作,原南京炼油厂研究所肖振东等人做过较为系统的研究,现简述如下:* A, p/ a4 M7 _/ A3 l q$ N2 x一、糠醛抽提分离及利用1 B" d& z$ u4 \7 z' d/ ~5 H6 b1、分离条件用糠醛做抽提分离的溶剂,在抽提塔中逆向操作,溶剂体积比为0.8:1—1:1,抽提温度50℃—70℃,接触时间大于0.5小时。
2、分离效果:6 G) G9 x- }, e" b& j' P抽余油中饱和烃含量大于98%,残炭小于0.04%,酸值小于0.02,总N小于10PPM,S含量0.3%左右,C/H为5.83,是优质的催化裂化原料可以扩大催化裂化的原料来源,改善催化裂化原料质量。
石油催化剂废料怎么处理
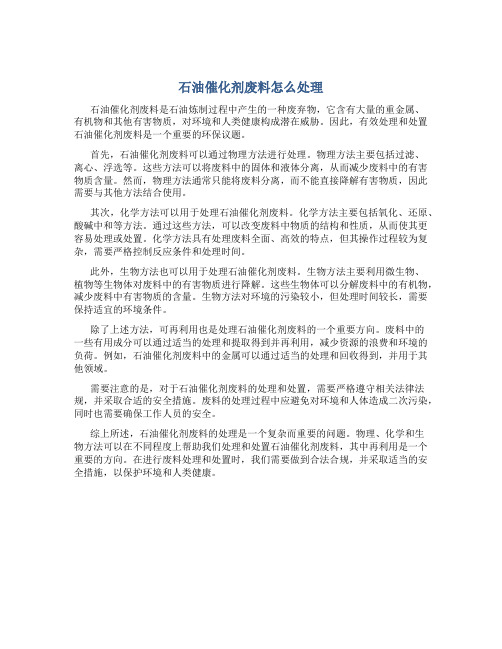
石油催化剂废料怎么处理石油催化剂废料是石油炼制过程中产生的一种废弃物,它含有大量的重金属、有机物和其他有害物质,对环境和人类健康构成潜在威胁。
因此,有效处理和处置石油催化剂废料是一个重要的环保议题。
首先,石油催化剂废料可以通过物理方法进行处理。
物理方法主要包括过滤、离心、浮选等。
这些方法可以将废料中的固体和液体分离,从而减少废料中的有害物质含量。
然而,物理方法通常只能将废料分离,而不能直接降解有害物质,因此需要与其他方法结合使用。
其次,化学方法可以用于处理石油催化剂废料。
化学方法主要包括氧化、还原、酸碱中和等方法。
通过这些方法,可以改变废料中物质的结构和性质,从而使其更容易处理或处置。
化学方法具有处理废料全面、高效的特点,但其操作过程较为复杂,需要严格控制反应条件和处理时间。
此外,生物方法也可以用于处理石油催化剂废料。
生物方法主要利用微生物、植物等生物体对废料中的有害物质进行降解。
这些生物体可以分解废料中的有机物,减少废料中有害物质的含量。
生物方法对环境的污染较小,但处理时间较长,需要保持适宜的环境条件。
除了上述方法,可再利用也是处理石油催化剂废料的一个重要方向。
废料中的一些有用成分可以通过适当的处理和提取得到并再利用,减少资源的浪费和环境的负荷。
例如,石油催化剂废料中的金属可以通过适当的处理和回收得到,并用于其他领域。
需要注意的是,对于石油催化剂废料的处理和处置,需要严格遵守相关法律法规,并采取合适的安全措施。
废料的处理过程中应避免对环境和人体造成二次污染,同时也需要确保工作人员的安全。
综上所述,石油催化剂废料的处理是一个复杂而重要的问题。
物理、化学和生物方法可以在不同程度上帮助我们处理和处置石油催化剂废料,其中再利用是一个重要的方向。
在进行废料处理和处置时,我们需要做到合法合规,并采取适当的安全措施,以保护环境和人类健康。
催化油浆的综合利用情况及催化-常减压工艺的探究

方案 。当然 ,从催化 油浆本 身性 质进行分析对 于整个加 工方 案 h,汽油减少 0.84 ,柴油减少 0.92 t/}l,但全厂石 脑油 、尾油量大
的选择和 确立具有决定性 意义 。
幅 度 增加 ,其 中送 化 工重 石脑 油增 加 1.12,加 裂尾 油 付乙 烯增
1催化裂化油浆的组成及性 质
一 步 推崇 ,将 催化 油浆 回炼 至减 压塔 ,不 仅可 以消 化炼 油企 业
从 以上 三种 催化 油浆 的利 用方式 上来 看 ,催 化裂 化一溶 剂 多余 的重 油 ,还可 以大 幅度 拓展 催化油 浆 的使用 范 围 ,提 高炼
脱沥 青 、催化裂化一溶剂抽 提组合 工艺有一定 的先进性 ,但 对于 油的经济效 益 ,充分发 挥催化油浆 的社会价值 。
进 程不断 加剧 ,催化 裂化装 置外甩油 浆量呈不 断增 多状 态 。近 大 部分 催化 油浆组 分 以及提 高拔 出率 的蜡 油组分 经过 减 压塔
年来 ,不少 专家对催 化油浆性 质及其 合理利 用技术进 行 了大 量 的减 压分离后 ,进入 l#Dn氢 裂化装置加 工生产。
的研究 ,主要涉及将 催化 油浆与炼 油工艺组 合以合理 利用催 化
(2)全厂效益测算
油浆 ,或是 根据催化 裂化油浆 的组成 上的特性 进行生 产化工 产
利 用 R—SIM软 件对 催化油 浆进入 2{!】}常减压 装置 进行 模拟
品的 利用研 究 ,以取得 催化 油浆 高附加 值产 品 ,确 定油 浆加 工 测算 ,全厂主要产 品变化值及效 益情况如 下 :液 化气减少 O.09 t/
艺 、催 化裂 化一延 迟 焦化组 合工 艺以 及直接 作 为燃 料 油调和 组 的地位 在不断提 高 ,多个企 业通过大量 试验和生 产数据 对催化
炼油催化剂废料怎么处理干净
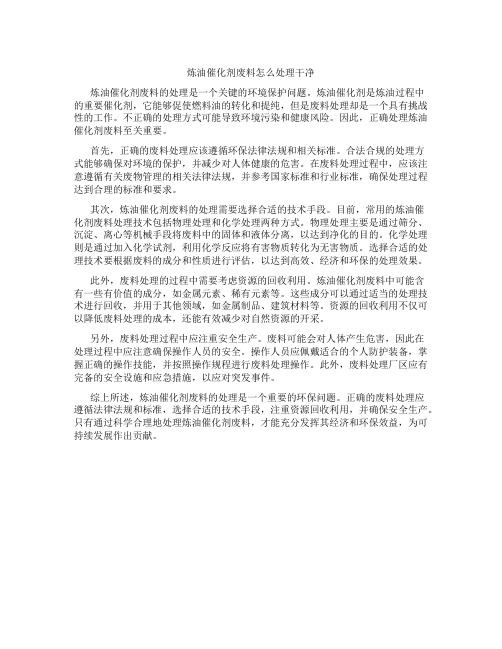
炼油催化剂废料怎么处理干净炼油催化剂废料的处理是一个关键的环境保护问题。
炼油催化剂是炼油过程中的重要催化剂,它能够促使燃料油的转化和提纯,但是废料处理却是一个具有挑战性的工作。
不正确的处理方式可能导致环境污染和健康风险。
因此,正确处理炼油催化剂废料至关重要。
首先,正确的废料处理应该遵循环保法律法规和相关标准。
合法合规的处理方式能够确保对环境的保护,并减少对人体健康的危害。
在废料处理过程中,应该注意遵循有关废物管理的相关法律法规,并参考国家标准和行业标准,确保处理过程达到合理的标准和要求。
其次,炼油催化剂废料的处理需要选择合适的技术手段。
目前,常用的炼油催化剂废料处理技术包括物理处理和化学处理两种方式。
物理处理主要是通过筛分、沉淀、离心等机械手段将废料中的固体和液体分离,以达到净化的目的。
化学处理则是通过加入化学试剂,利用化学反应将有害物质转化为无害物质。
选择合适的处理技术要根据废料的成分和性质进行评估,以达到高效、经济和环保的处理效果。
此外,废料处理的过程中需要考虑资源的回收利用。
炼油催化剂废料中可能含有一些有价值的成分,如金属元素、稀有元素等。
这些成分可以通过适当的处理技术进行回收,并用于其他领域,如金属制品、建筑材料等。
资源的回收利用不仅可以降低废料处理的成本,还能有效减少对自然资源的开采。
另外,废料处理过程中应注重安全生产。
废料可能会对人体产生危害,因此在处理过程中应注意确保操作人员的安全。
操作人员应佩戴适合的个人防护装备,掌握正确的操作技能,并按照操作规程进行废料处理操作。
此外,废料处理厂区应有完备的安全设施和应急措施,以应对突发事件。
综上所述,炼油催化剂废料的处理是一个重要的环保问题。
正确的废料处理应遵循法律法规和标准,选择合适的技术手段,注重资源回收利用,并确保安全生产。
只有通过科学合理地处理炼油催化剂废料,才能充分发挥其经济和环保效益,为可持续发展作出贡献。
催化油浆净化技术的应用及比较

催化油浆净化技术的应用及比较0 引言重油催化裂化(RFCC)装置是石油化工生产中重要的二次加工装置之一。
随着世界原油重质化的不断加大及催化加工工艺的多元化,对催化裂化的发展提出了更高的要求,为保证催化装置的最大生产负荷和长周期运转,通常采用外甩油浆的操作方式。
据有关资料统计我国外甩油浆量占装置处理量的5%~10%,每年排放油浆达7.5Mt。
油浆中含有大量重芳烃等有价值的化工原料,但因其中含有0.3%~2%以上的催化剂粉尘,使其成为催化裂化产品中利用价值最低的馏分,严重影响其深加工产品的质量。
油浆中大量带短侧链稠环(3~5环)的芳烃是生产炭黑、针状焦、碳纤维、橡胶软化剂及填充油、塑料增塑剂、重交通道路沥青及导热油等高附加值产品的优质原料,但对其固体含量有严格要求。
普通炭黑和针状焦原料油对灰份要求油浆中固粒含量小于500×10-6(500mg/kg),优极品指标则为0.03%~0.02%,;电极沥青要求固粒含量不大于100×10-6(100mg/kg);生产碳纤维要求固粒含量为10~20×10-6 (10mg/kg~20mg/kg),过高的固粒含量,限制了油浆的利用。
当前国内大多数炼油厂的油浆被用作7#燃料油的调和油,但催化剂微粒会导致喷嘴磨损、堵塞等问题,同时因烟气中催化剂细粉沉积在加热炉管表面,热效率下降,能耗增加。
因此,催化裂化装置外甩油浆的净化对于调和燃料重油产品质量的改善和外甩油浆深加工技术的发展均有重要的技术经济意义。
1 目前国内油浆净化的应用技术关于重油催化油浆中催化剂的净化,目前在国内外影响较大,技术上比较成熟,并已得到工业应用的分离技术主要有两类:一类是沉降技术,包括离心沉降、重力沉降、静电沉降和沉降助剂法脱固等。
传统的自然沉降法由于沉降周期长、净化效果差,已经逐渐被淘汰;早期由美国公司开发的油浆静电分离技术,在国内已经有20多年工业应用的成功经验,但在国内一直未得到推广,主要原因是其分离效果受油浆性质和操作条件的影响较大,特别对胶沥质含量较高的重油催化裂化的适应性不好,我国镇海、乌石化、锦州石化和金陵石化公司曾各引进一套,其使用效果均不十分理想;采用化学药剂助沉降的方法是对传统自然沉降法的改良,国外于20世纪80年代初始完成开发,该方法投资少,方法简单,有一定的效果,但在运行中也存在一定的问题,我国大连西太平洋石油化工有限公司、抚顺石化公司石油三厂等厂家运用此工艺。
炼油催化剂废料怎么处理
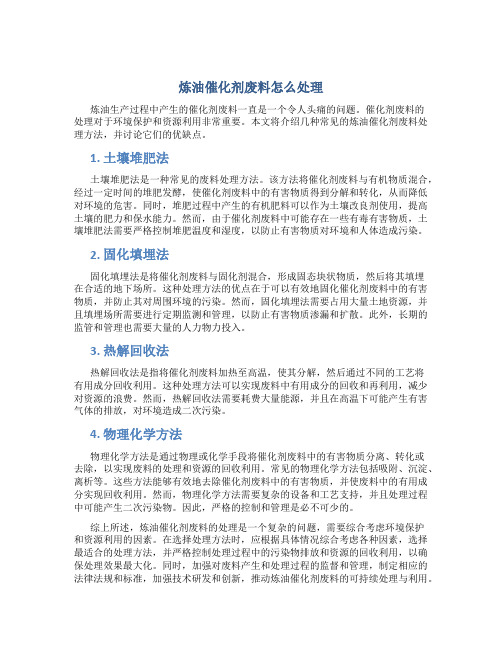
炼油催化剂废料怎么处理炼油生产过程中产生的催化剂废料一直是一个令人头痛的问题。
催化剂废料的处理对于环境保护和资源利用非常重要。
本文将介绍几种常见的炼油催化剂废料处理方法,并讨论它们的优缺点。
1. 土壤堆肥法土壤堆肥法是一种常见的废料处理方法。
该方法将催化剂废料与有机物质混合,经过一定时间的堆肥发酵,使催化剂废料中的有害物质得到分解和转化,从而降低对环境的危害。
同时,堆肥过程中产生的有机肥料可以作为土壤改良剂使用,提高土壤的肥力和保水能力。
然而,由于催化剂废料中可能存在一些有毒有害物质,土壤堆肥法需要严格控制堆肥温度和湿度,以防止有害物质对环境和人体造成污染。
2. 固化填埋法固化填埋法是将催化剂废料与固化剂混合,形成固态块状物质,然后将其填埋在合适的地下场所。
这种处理方法的优点在于可以有效地固化催化剂废料中的有害物质,并防止其对周围环境的污染。
然而,固化填埋法需要占用大量土地资源,并且填埋场所需要进行定期监测和管理,以防止有害物质渗漏和扩散。
此外,长期的监管和管理也需要大量的人力物力投入。
3. 热解回收法热解回收法是指将催化剂废料加热至高温,使其分解,然后通过不同的工艺将有用成分回收利用。
这种处理方法可以实现废料中有用成分的回收和再利用,减少对资源的浪费。
然而,热解回收法需要耗费大量能源,并且在高温下可能产生有害气体的排放,对环境造成二次污染。
4. 物理化学方法物理化学方法是通过物理或化学手段将催化剂废料中的有害物质分离、转化或去除,以实现废料的处理和资源的回收利用。
常见的物理化学方法包括吸附、沉淀、离析等。
这些方法能够有效地去除催化剂废料中的有害物质,并使废料中的有用成分实现回收利用。
然而,物理化学方法需要复杂的设备和工艺支持,并且处理过程中可能产生二次污染物。
因此,严格的控制和管理是必不可少的。
综上所述,炼油催化剂废料的处理是一个复杂的问题,需要综合考虑环境保护和资源利用的因素。
在选择处理方法时,应根据具体情况综合考虑各种因素,选择最适合的处理方法,并严格控制处理过程中的污染物排放和资源的回收利用,以确保处理效果最大化。
催化裂化油浆的综合利用

催化裂化油浆的综合利用谢立国广东石油化工学院,广东茂名摘要:目前,催化油浆主要作为廉价的燃料油出厂,造成了这一宝贵资源的浪费。
催化油浆作为催化裂化过程的副产物,其组成上的特点使之在某些特定的情况下具有较高的利用价值。
对其进行开发利用,提高附加值,可以给炼油厂带来良好的经济效益。
本文就催化裂化油浆的特点,分离,加工组合技术,以及其综合利用方式进行简单的阐述。
关键词:催化裂化油浆,分离,加工组合,应用At present, the catalytic slurry oil mainly as a cheap fuel oil factory, cause the waste of valuable resources. Catalytic slurry oil as a catalytic cracking process by-products, the composition of the characteristics in some specific cases has high value in use. The development and utilization, improve the added value, can give oil refinery to bring good economic benefits. In this paper the characteristics of catalytic cracking slurry oil, separation, processing combination technology, and its comprehensive utilization ways of simple paper.Keywords: catalytic cracking slurry oil, separation, processing combination, application引言国外催化裂化装置主要用于生产汽油和液化气,一般不生产柴油,柴油和比柴油重的馏分都作为燃料油出装置。
催化裂化油浆利用有哪些招数

催化裂化油浆利些■金文催化裂化油浆中含有催化剂粉末,过滤后的澄清油在化学组成上与渣油相比有很大变化。
催化油浆密度大,氢碳原子比低,芳烃含量高,胶质、沥青质含量低,残炭值低。
就其芳香烃而言,单、双环芳烃含量相对较少,三、四环芳烃含量较多,将这些重质芳烃加以分离,可制成高附加值的化工产品。
用作渣油或原料沥青的改性剂国外优质沥青含芳香烃一般为40%~55%,蜡含量小于3.0%。
道路沥青的需求约占沥青总量的80%。
当沥青的沥青质高、硬度大、延伸度大时,加入适量的芳烃久性。
我国原油80%以上为石蜡基原油,不宜生产高等级沥青。
利用炼厂催化裂化油浆这一贫蜡富芳组分作改性剂,生产高等级道路沥青的研究很活跃。
油浆的初馏点一般较低,不能直接用作改善沥青质量的组分。
有研究指出,利用强化蒸馏将油浆(强化剂)加入沥青或渣油中,再进行减压蒸馏,使饱和的、对沥青质量不利的组分蒸出,而对沥青有利的组分留在沥青中,从而改善了沥青质量,生产出优质的沥青。
将新疆混合原油丙烷脱油沥青与催化裂化油浆等改性剂调和,可生产出符合国标GB/T15180-94要求的各种牌号重交沥青。
锦西炼油厂将油浆减压蒸馏,除去小于400℃的馏分,得到富芳、能改善沥青质量的有效组分,与辽河减渣调合,生产出质量符合GB/T15180-94的高等级道路沥青。
该工艺全年可处理油浆4万吨,得到有效组分2.56万吨,可调合高等级道路沥青13.2万吨,年增效500多万元。
用作丙烷脱沥青的强化剂与减压渣油相比,催化裂化油浆密度大、闪点低。
丙烷脱沥青的萃取过程掺炼催化裂化油浆后,使萃取塔的进料密度变大,粘度变小。
进料密度变大,使进料与丙烷的密度差变大;进料粘度减小,使萃取阻力降低,这都有利于萃取过程的进行,提高脱沥青油的收率。
将催化油浆掺兑用有哪招数和胶质,可改善延伸度和耐压渣油相比,催化裂化油与减压渣油闪点低。
丙烷脱沥青的萃浆密度大、闪点低。
化裂化油浆后,使萃取取过程掺炼催化裂化油,粘度变小。
催化油浆在石油化工方面的利用

催化油浆在石油化工方面的利用摘要:近年来,随着重油催化裂化加工能力的不断增加,在催化、裂化的过程中所生成的油浆的产量得到了不断地提高。
目前,油浆的产量大约占据了催化、裂化的处理总量的百分之五至百分之十之间,大约为4Mt/a。
目现如今,油浆俨然已经为了燃料油的主要调和油。
我们知道,这种利用油浆所进行的燃烧方式其效益是比较低下的。
除此之外,在油浆之中还含有着较为少量的类似于固体颗粒状的残留物质,他们及其容易对炉嘴造成一定的结焦。
为了能够提高炼厂工作的效益,能够充分利用石油的资源,对于催化裂化轻重两头的生产高附加值的化工产品能够成为广大石油化工工作者们所共同努力,为了能够早日实现这一目标。
关键词:油浆;石油化工;油浆催化1.催化油浆的利用我们知道,催化油浆的密度相对来说比较大,而,相反,氢碳原子相对来说所占的密度却比较小,主要由几种芳烃组成,这种芳烃均带有短侧链。
至于那些通过几种催化裂化的原料所生产出来的便带有了浓重的油浆性质的特色。
目前,在其他国家,我们对于这种研究所形成的成果通过研究猜测对其进行了进一步的说明。
此外,专家还进行大胆猜测,认为它们对于一些化工产品的研究原料极为吻合,由此可以猜测它们可能是形成这些化工产品的种种原材料。
诸如橡胶软化剂、塑料增塑剂以及表面活性剂和炭素材料等等都有可能是这些化工产品的生产原料。
直到现如今,我国也在对于油浆利用方面的问题有了一定的研究与注重。
1.1增塑剂早在上个世纪七十年代末末期的时候,我国就已经做了大量关于芳烃增塑剂应用于聚氯乙烯上所起到的作用以及它的适应程度方面的实验。
其中发现聚氯乙烯在对增加增塑剂对石油芳烃的要求可以列出以下几点关键点:芳烃的质量分数一般控制在百分之五十到百分之一百之间,尽管一般只要达到了百分之五十以上就可以达到质量浓度的要求,但为了追求更高的质量结果,我们最好可以将其浓度控制达到百分之九十以上。
烯烃质量的分数可以是在百分之二左右,按照法国对于苯胺点的测算标准来说,我们在测定苯胺点时对其的分数点的控制最好控制在零下五度以下,粘贴粘度最好能够控制在01004~0.02kg/(m?s)(99℃),我们知道,这些馏份分别都可以将各种原油、煤作为原材料再经过数道加工程序之后得到。
催化油浆在石油化工方面的利用
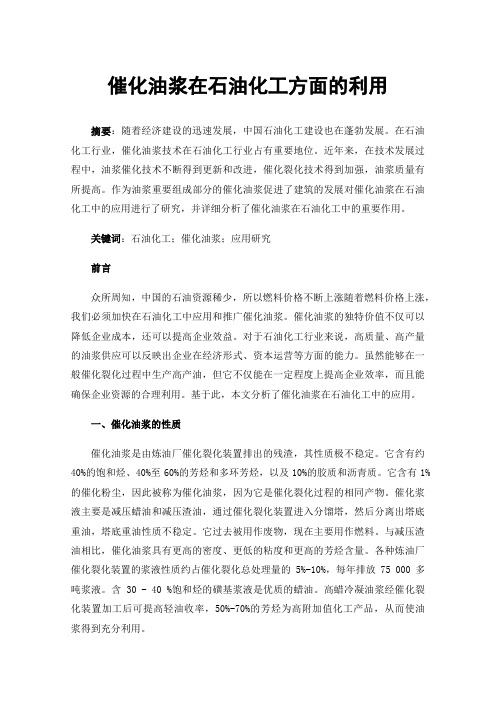
催化油浆在石油化工方面的利用摘要:随着经济建设的迅速发展,中国石油化工建设也在蓬勃发展。
在石油化工行业,催化油浆技术在石油化工行业占有重要地位。
近年来,在技术发展过程中,油浆催化技术不断得到更新和改进,催化裂化技术得到加强,油浆质量有所提高。
作为油浆重要组成部分的催化油浆促进了建筑的发展对催化油浆在石油化工中的应用进行了研究,并详细分析了催化油浆在石油化工中的重要作用。
关键词:石油化工;催化油浆;应用研究前言众所周知,中国的石油资源稀少,所以燃料价格不断上涨随着燃料价格上涨,我们必须加快在石油化工中应用和推广催化油浆。
催化油浆的独特价值不仅可以降低企业成本,还可以提高企业效益。
对于石油化工行业来说,高质量、高产量的油浆供应可以反映出企业在经济形式、资本运营等方面的能力。
虽然能够在一般催化裂化过程中生产高产油,但它不仅能在一定程度上提高企业效率,而且能确保企业资源的合理利用。
基于此,本文分析了催化油浆在石油化工中的应用。
一、催化油浆的性质催化油浆是由炼油厂催化裂化装置排出的残渣,其性质极不稳定。
它含有约40%的饱和烃、40%至60%的芳烃和多环芳烃,以及10%的胶质和沥青质。
它含有1%的催化粉尘,因此被称为催化油浆,因为它是催化裂化过程的相同产物。
催化浆液主要是减压蜡油和减压渣油,通过催化裂化装置进入分馏塔,然后分离出塔底重油,塔底重油性质不稳定。
它过去被用作废物,现在主要用作燃料。
与减压渣油相比,催化油浆具有更高的密度、更低的粘度和更高的芳烃含量。
各种炼油厂催化裂化装置的浆液性质约占催化裂化总处理量的5%-10%,每年排放75 000多吨浆液。
含30 - 40 %饱和烃的磺基浆液是优质的蜡油。
高蜡冷凝油浆经催化裂化装置加工后可提高轻油收率,50%-70%的芳烃为高附加值化工产品,从而使油浆得到充分利用。
我国炼油企业催化裂化比重较大。
催化油浆年产量大,催化油浆原料和芳烃含量高。
芳烃是一种非常珍贵的资源。
催化油浆在石油化工的利用
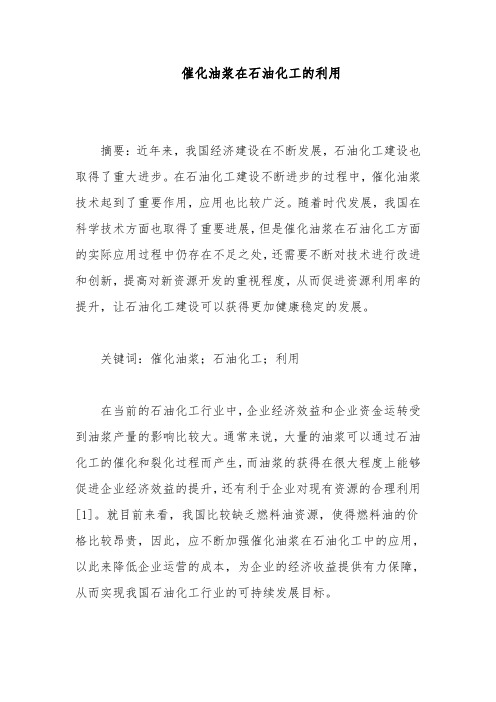
催化油浆在石油化工的利用摘要:近年来,我国经济建设在不断发展,石油化工建设也取得了重大进步。
在石油化工建设不断进步的过程中,催化油浆技术起到了重要作用,应用也比较广泛。
随着时代发展,我国在科学技术方面也取得了重要进展,但是催化油浆在石油化工方面的实际应用过程中仍存在不足之处,还需要不断对技术进行改进和创新,提高对新资源开发的重视程度,从而促进资源利用率的提升,让石油化工建设可以获得更加健康稳定的发展。
关键词:催化油浆;石油化工;利用在当前的石油化工行业中,企业经济效益和企业资金运转受到油浆产量的影响比较大。
通常来说,大量的油浆可以通过石油化工的催化和裂化过程而产生,而油浆的获得在很大程度上能够促进企业经济效益的提升,还有利于企业对现有资源的合理利用[1]。
就目前来看,我国比较缺乏燃料油资源,使得燃料油的价格比较昂贵,因此,应不断加强催化油浆在石油化工中的应用,以此来降低企业运营的成本,为企业的经济收益提供有力保障,从而实现我国石油化工行业的可持续发展目标。
1催化油浆加工技术分析1.1加氢处理技术加氢处理技术需要在高压的环境中使用,使用此技术能够产生高品质的化工原料,还可以得到高芳烃石脑油,有利于产品分布情况的改善。
由于传统的加氢处理技术存在诸多问题,所以石科院有针对性的对传统技术进行了改进和创新,从而研发出了RICP工艺技术,这种技术的优点是让渣油变为轻质油的效率得到很大程度的提升,对炼厂的产品结构进行了大规模的改变,从而使得产品的质量得到大幅度提高。
1.2延迟焦化技术延迟焦化技术的顺利使用离不开油浆,油浆作为一种原材料,里面包含着大量的饱和烃,此外还有一部分的芳烃,重芳烃组在延迟焦化技术的作用下就可以产生出高品质的焦煤。
延迟焦化技术的优点有多种,它能够灵活的调整炼厂的生产行为,提高原材料的转化率,从而使渣油产生的情况得以避免,并在很大程度上对资源的有效利用率进行提升,这也就使得延迟焦化技术在大部分石油化工企业中得到广泛应用。
催化裂化油浆的净化及综合利用

催化裂化油浆的净化及综合利用催化裂化油浆的净化及综合利用徐宁(辽河油田经济贸易置业总公司,盘锦124010)摘要:介绍了催化裂化油浆的性质和组成特点,油浆中脱除催化剂颗粒的常用分离技术与现状,着重对油浆的加工组合工艺和综合利用进行了综述。
最后对催化裂化油浆的综合利用进行展望。
关键词:催化裂化;油浆;分离;组合;利用;Clarification and integrated utilization of fluid catalytic crackingslurryXu Ning(Economic Trade Real Estate Corporation of Liaohe Oilfield,Liaoning Panjin 124010)Abstract:The characteristics of the composition and properties of fluid catalytic cracking (FCC) slurry and the com-mon separation technology for removal of catalyst particles were introduced.In this paper, the combination of slurry oil processing process and comprehensive utilization were eminently reviewed, and the developing prospect of integrated utilization of fluid catalyticcracking slurry was finally discussed.Keywords:fluid catalytic cracking;slurry;separation;combination;utilization 催化裂化是当今重质油轻质化最重要的加工手段之一,然而随着原油重质化不断加大,催化裂化副产品油浆产量逐年增加,加工这些劣质油浆给装置带来许多不利因素,例如结焦和结垢使装置不能正常运行;同时也影响了其产品分布及质量。
化工废旧催化剂回收再生利用技术与工艺优化详解
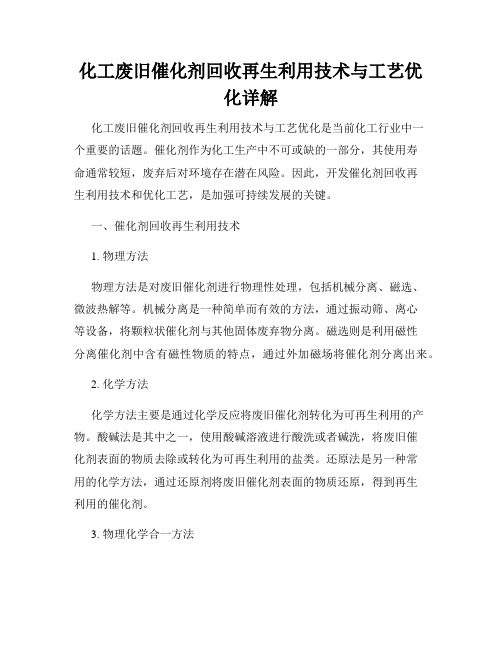
化工废旧催化剂回收再生利用技术与工艺优化详解化工废旧催化剂回收再生利用技术与工艺优化是当前化工行业中一个重要的话题。
催化剂作为化工生产中不可或缺的一部分,其使用寿命通常较短,废弃后对环境存在潜在风险。
因此,开发催化剂回收再生利用技术和优化工艺,是加强可持续发展的关键。
一、催化剂回收再生利用技术1. 物理方法物理方法是对废旧催化剂进行物理性处理,包括机械分离、磁选、微波热解等。
机械分离是一种简单而有效的方法,通过振动筛、离心等设备,将颗粒状催化剂与其他固体废弃物分离。
磁选则是利用磁性分离催化剂中含有磁性物质的特点,通过外加磁场将催化剂分离出来。
2. 化学方法化学方法主要是通过化学反应将废旧催化剂转化为可再生利用的产物。
酸碱法是其中之一,使用酸碱溶液进行酸洗或者碱洗,将废旧催化剂表面的物质去除或转化为可再生利用的盐类。
还原法是另一种常用的化学方法,通过还原剂将废旧催化剂表面的物质还原,得到再生利用的催化剂。
3. 物理化学合一方法物理化学合一方法综合了物理和化学两种方法,具有更高的废旧催化剂回收再生利用效果。
其中一种常用的方法是热解,通过高温处理废旧催化剂,使其发生物理和化学变化,得到可再生的催化剂。
催化过程中产生的废气和废液可以进行处理和回收利用,实现资源的最大化利用。
二、工艺优化1. 废旧催化剂收集与分类废旧催化剂的收集与分类是进行回收再生利用的第一步。
在化工生产过程中,应建立完善的废旧催化剂管理制度,将废旧催化剂进行分类储存,避免混合带来的难以处理问题,减少废旧催化剂的交叉污染。
2. 催化剂回收技术的选择针对不同类型的废旧催化剂,应选择合适的回收技术。
如通过物理方法回收催化剂颗粒状物质,通过化学方法回收含有有害物质的催化剂。
在选择回收技术时,考虑技术成本、回收效果和环境安全等因素。
3. 催化剂再生工艺的优化在催化剂再生过程中,工艺的优化是关键。
通过优化反应条件、控制催化剂的处理时间和温度等因素,可以提高催化剂再生利用效率,减少资源消耗和废弃物产生。
化工废旧催化剂回收再生利用技术与工艺优化解析
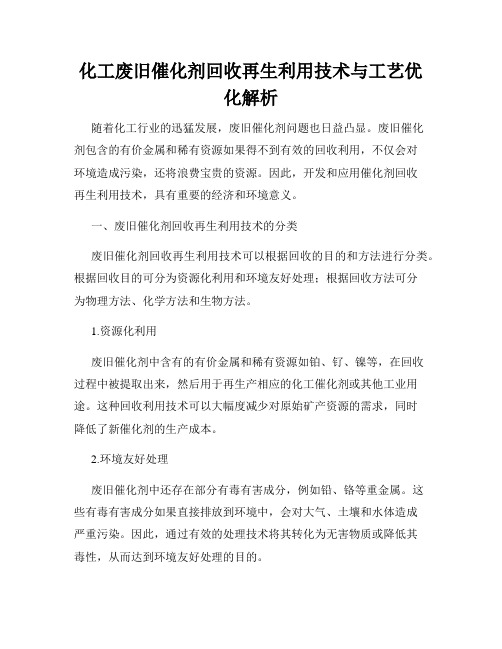
化工废旧催化剂回收再生利用技术与工艺优化解析随着化工行业的迅猛发展,废旧催化剂问题也日益凸显。
废旧催化剂包含的有价金属和稀有资源如果得不到有效的回收利用,不仅会对环境造成污染,还将浪费宝贵的资源。
因此,开发和应用催化剂回收再生利用技术,具有重要的经济和环境意义。
一、废旧催化剂回收再生利用技术的分类废旧催化剂回收再生利用技术可以根据回收的目的和方法进行分类。
根据回收目的可分为资源化利用和环境友好处理;根据回收方法可分为物理方法、化学方法和生物方法。
1.资源化利用废旧催化剂中含有的有价金属和稀有资源如铂、钌、镍等,在回收过程中被提取出来,然后用于再生产相应的化工催化剂或其他工业用途。
这种回收利用技术可以大幅度减少对原始矿产资源的需求,同时降低了新催化剂的生产成本。
2.环境友好处理废旧催化剂中还存在部分有毒有害成分,例如铅、铬等重金属。
这些有毒有害成分如果直接排放到环境中,会对大气、土壤和水体造成严重污染。
因此,通过有效的处理技术将其转化为无害物质或降低其毒性,从而达到环境友好处理的目的。
二、废旧催化剂回收再生利用工艺优化的方法与措施废旧催化剂回收再生利用的工艺优化是提高回收效果和降低成本的关键。
下面将从工艺参数优化、新技术应用和工艺流程改进等方面进行探讨。
1.工艺参数优化在废旧催化剂的回收再生过程中,合理调整工艺参数对提高回收率具有重要意义。
例如,在物理方法中,合适的温度和压力可以提高溶剂的萃取效果;在化学方法中,适当的酸碱度可以促进金属的溶解和分离;在生物方法中,调控菌株的培养条件和废旧催化剂的反应条件,可以提高废旧催化剂的降解效果。
2.新技术应用随着科技的进步,新的催化剂回收再生利用技术不断涌现。
例如,超临界流体技术能在较低温度下高效地提取废旧催化剂中的有价金属;纳米材料技术能够提高催化剂的分散性和活性,从而提高再生利用效果。
这些新技术的应用可以进一步改进废旧催化剂回收再生利用的工艺流程,提高回收效率。
炼油催化剂废料怎么处理的
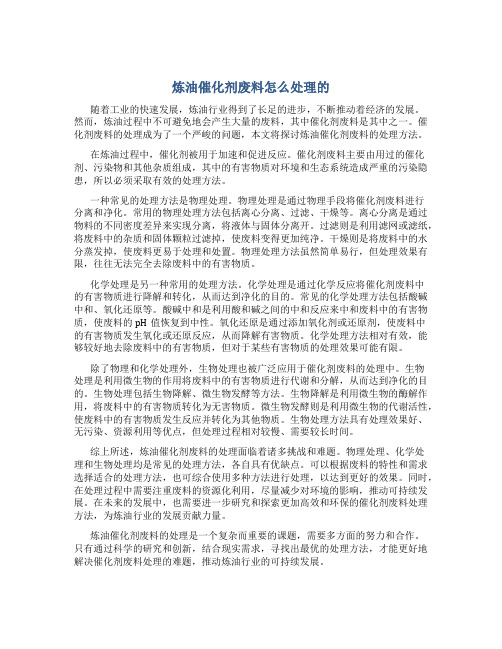
炼油催化剂废料怎么处理的随着工业的快速发展,炼油行业得到了长足的进步,不断推动着经济的发展。
然而,炼油过程中不可避免地会产生大量的废料,其中催化剂废料是其中之一。
催化剂废料的处理成为了一个严峻的问题,本文将探讨炼油催化剂废料的处理方法。
在炼油过程中,催化剂被用于加速和促进反应。
催化剂废料主要由用过的催化剂、污染物和其他杂质组成,其中的有害物质对环境和生态系统造成严重的污染隐患,所以必须采取有效的处理方法。
一种常见的处理方法是物理处理。
物理处理是通过物理手段将催化剂废料进行分离和净化。
常用的物理处理方法包括离心分离、过滤、干燥等。
离心分离是通过物料的不同密度差异来实现分离,将液体与固体分离开。
过滤则是利用滤网或滤纸,将废料中的杂质和固体颗粒过滤掉,使废料变得更加纯净。
干燥则是将废料中的水分蒸发掉,使废料更易于处理和处置。
物理处理方法虽然简单易行,但处理效果有限,往往无法完全去除废料中的有害物质。
化学处理是另一种常用的处理方法。
化学处理是通过化学反应将催化剂废料中的有害物质进行降解和转化,从而达到净化的目的。
常见的化学处理方法包括酸碱中和、氧化还原等。
酸碱中和是利用酸和碱之间的中和反应来中和废料中的有害物质,使废料的pH值恢复到中性。
氧化还原是通过添加氧化剂或还原剂,使废料中的有害物质发生氧化或还原反应,从而降解有害物质。
化学处理方法相对有效,能够较好地去除废料中的有害物质,但对于某些有害物质的处理效果可能有限。
除了物理和化学处理外,生物处理也被广泛应用于催化剂废料的处理中。
生物处理是利用微生物的作用将废料中的有害物质进行代谢和分解,从而达到净化的目的。
生物处理包括生物降解、微生物发酵等方法。
生物降解是利用微生物的酶解作用,将废料中的有害物质转化为无害物质。
微生物发酵则是利用微生物的代谢活性,使废料中的有害物质发生反应并转化为其他物质。
生物处理方法具有处理效果好、无污染、资源利用等优点,但处理过程相对较慢、需要较长时间。
- 1、下载文档前请自行甄别文档内容的完整性,平台不提供额外的编辑、内容补充、找答案等附加服务。
- 2、"仅部分预览"的文档,不可在线预览部分如存在完整性等问题,可反馈申请退款(可完整预览的文档不适用该条件!)。
- 3、如文档侵犯您的权益,请联系客服反馈,我们会尽快为您处理(人工客服工作时间:9:00-18:30)。
催化油浆净化处理方法及其化工利用建议
摘要:催化油浆富含大量短侧链的重芳烃,是极具价值的化工原料,由于其含有许多催化剂固体颗粒,严重制约了其深加工应用。
文章详细阐述了催化油浆脱除催化剂固体颗粒的技术
方法及进展,并在此基础上介绍了催化油浆在化工方面的应用。
关键词:催化油浆净化化工利用重芳烃
1 前言
催化油浆是重油催化裂化工艺过程中所产生的一种性质极为特殊的副产品,因其比重大、分了量大、粘度高并含有较多的催化剂固体颗粒,使其利用率受到限制。
随着催化裂化加工原料重质化,催化油浆产率越来越大,如何解决外排油浆问题显得尤为重要。
催化油浆中含有大量重芳烃,是有价值的化工原料,由于其中含有2g/l以上的催化剂固体颗粒,严重影响其深加工产品的质量。
目前催化油浆普遍作为重质燃料油的调合组分出厂,不仅利用价值低,而且油浆中的固体催化剂粉末会使加热炉火嘴磨损,造成加热炉管表面严重积灰、热效率下降、能耗增加。
据报道,由于催化油浆中大量的带短侧链稠环(3~5环)芳烃,可以作为生产炭黑、针状焦、碳纤维、橡胶软化剂及填充油、塑料增塑剂、重交通道路沥青及导热油等高附加值产品的优质原料,但对其固体含量有严格要求。
因此,进行油浆的开发利用必须分离除掉其中的固体催化剂粉末,有效地降低灰份含量,以满足不同用途的质量要求。
2 催化油浆净化处理技术进展
近年来,国内外对催化油浆脱除催化剂颗粒物技术进行了大量研究,目前文献报道的方法有:自然沉降、过滤、离心分离、静电分离、沉降剂脱除法。
这些脱除方法不是脱固分离效率差就是脱除费用太高。
中国专利报道采用破乳一絮凝法脱除油浆中的固体粒子,但没有给出具体工艺条件对催化裂化油浆中固体粒子脱除的影响,同时存在沉降时间过长的问题。
2.1 自然沉降法
油浆中固体催化剂粉末的粒径范围约0~80μm,其中20μm以下微粒占相当比重。
早期的油浆净化主要采用自然沉降法。
沉降过程通常在沉降器内进行,固体颗粒在沉降器内的沉降速度与颗粒大小、颗粒密度、油浆粘度和密度等因素有关。
一定温度条件下,颗粒尺寸越大,其沉降速度越快。
但是,由于在催化油浆—颗粒分散体系中,一方面催化剂颗粒十分微小,另一方面油浆含有的胶质、沥青质具有阻碍催化剂微粒沉降的分散作用,所以靠重力沉降的净化分离效果较差,一般对直径于20μm的微粒靠重力沉降的方法很难脱除。
所以传统的自然沉降法已经被淘汰。
2.2 过滤分离法
精密的过滤分离能保证过滤后的油浆质量满足深加工的要求,其关键技术是选择适宜的过滤材料和有效的反冲洗方式。
油浆过滤器的滤芯材质通常为不锈钢粉末或丝网烧结的多孔金属,过滤孔径在0.2~20 微米范围,这种滤芯具有较高的强度,能在高温下操作并可承受
较高的压差。
自20世纪80年代始,美国的Mott和Pall公司分别将各自的过滤技术应用于催化裂化油浆分离催化剂粉末,现已有不同规模的工业化装置在世界各地运行(见表1)。
表1 油浆过滤技术工业化应用实例
应用厂家技术来源处理量/t.h-1
美国Ohio TOLEDO,BP公司炼厂MOTT Hy Pulse®LSI系统20
苏格兰GRANGEMOUTH,BP公司炼厂MOTT Hy Pulse®LSI系统12.5
美国Ohio LIMA,BP公司MOTT Hy Pulse®LSI系统20
美国Texa MOTIVA炼厂Pall过滤技术40
日本NPRC横滨根岸炼厂RFCC Pall过滤技术30
印度尼西亚Exor-1 Pall过滤技术70
长岭炼厂RFCC Pall过滤技术10
华北油田第一炼油厂MOTT Hy Pulse®LSI系统3~6
胜利石化总厂MOTT Hy Pulse®LSI系统 4.5
九江炼油厂石油大学7
前郭炼油厂石油大学3~6
大连石化厂安泰科技公司(北京)8
福建炼油厂安泰科技公司10~15
以MOTT公司的高效脉冲过滤器(Hy Pulse®LSI型)为例,它是一种管式滤芯过滤器(结构如图1所示),滤芯材质为316LSS不锈钢粉末烧结的多孔金属。
油浆从过滤器壳体底部进入后向上流至滤芯,油浆透过滤芯被净化后从过滤器上部排出,固体催化剂被拦截,在滤芯外壁形成滤饼,当过滤器的压降超过允许值后,切换进行反冲洗。
反向冲洗采用高压脉冲气体或液体,反向通过滤芯,并卸除滤饼。
一套标准的Hy Pulse®LSI型过滤系统由三个过滤器组成,一台在线过滤,一台反冲洗,第三台备用。
图1 高效脉冲反冲洗过滤器示意图
从技术可靠性和工业应用等方面来看,过滤技术应用比较多,国内许多炼厂都有引进的过滤装置,但过滤效果不理想(滤后的油浆中催化剂粉末含量在几百μg/g以上),系统操作复杂,过滤器切换频繁(1~2小时就需要切换进行反冲洗),且存在滤芯易堵塞、清洗再生困难(需经常更换滤芯,维护费用高)、不能够稳定运行等诸多亟待解决的问题。
国内炼厂的油浆过滤装置有的因效果不好而废弃,有的建成后因为种种原因而未开成。
目前催化油浆中催化剂的分离主要采用不锈钢金属丝网滤芯过滤,滤芯以进口为主;过滤精度不高,滤后的油浆中催化剂粉末含量在几百μg/g以上;过滤运行1~2小时出现堵塞,需要频繁的进行清洗;清洗再生性能差,需要经常更换,目前国内的油浆过滤器大都不能正常运行。
2.3 静电分离法
这是美国海湾公司开发的技术,1979年实现工业化,其原理是含颗粒的液流流经电场作用下的填料床层时,颗粒在高压电场中极化并吸附在填料上,从而使流体得以分离。
从国外工业化的运行状况来看,该技术的主要特点是分离效率高、处理量大、压降小、易冲洗再生,其缺点是设备投资大,运行费用高,静电分离技术脱除油浆中固体的效果受油浆的理化性质影响较大。
1988年南京炼油厂在重油催化装置上引进了一套美国GA公司的专利技术和成套静电分离设备,3组6单元,设计处理能力为10500kg/h,油浆固体含量可从1000μg/g 降到100μg/g以下。
该装置经过几年运行,分离效率变化较大,高时脱固率为80%以上,低时一点效果也没有,固体含量在6000μg/g以上时效果更差,经常超电流、跳停,有时分离后固体含量还超过6000μg/g,无法继续使用。
2.4 高温离心分离技术
高温离心分离法:该技术是抚顺石油二厂张洪林等人发明的专利:将油浆经换热器换热至150℃~300℃,进入高温离心分离机进行离心分离,离心时间约2~10min,离心转速为3000~5000转/min,脱固率为92%~98%,得到固含量为0.02%的脱固油。
此法为经典的固液分离方法,简单易行,效果好,但催化油浆的数量较大,操作费用高,故难以工业化。
旋液分离法:旋液分离法采用的设备为旋流器,其原理是,液—固非均相混合物在旋流器内以较高流速作螺旋运动,固体颗粒在离心力的作用下与液相分离。
理论上旋流器可分离的颗粒尺寸为3~500μm,进料浓度可高达30wt%。
旋流器具有结构简单、操作方便、设备费用低、占地面积小、无转动部件等优点,在许多工业领域得到广泛应用。
对催化油浆,当操作温度在300℃以上、油浆的粘度较低时,设计良好的旋流器的分离效率可以达70%以上。
但是,实际上影响旋流器分离过程的因素很多,有设备结构方面:旋流器直径、进料口尺寸和溢流口直径等;有工艺操作方面:进料压力、流量、颗粒密度和浓度、液相粘度和密度等,而且各种因素之间相互影响、制约,目前还不能用数学解析的方法进行准确描述。
如果设计或操作不当,旋流器的分离效果则可能很差,一般难以满足油浆最终过滤的要求。
不过,由于旋流器具有结构简单以及占地面积小等特点,在实践中有时被用作预处理设备,以减轻下游分离单元如过滤操作的负荷。
例如,九江炼油厂的油浆过滤系统即应用了旋流器预处理单元。
2.5 高温陶瓷膜错流过滤法
北京中天元环境工程有限责任公司一直致力于特种陶瓷膜及其应用研究,2008年与中石化长岭分公司联合开展FCC油浆过滤技术开发工作,开发了针对催化油浆过滤处理的耐高温特种陶瓷膜及其错流过滤处理成套技术,2010年8月完成了放大实验,试验结果表明处理后催化油浆中固含量为零(见表2),催化油浆的品质得到了大幅度提升,为催化油浆的综合利用创造了条件。