丝印件检验规范
移印丝印、烫印、热转印产品检验规范

文件编号:
版本/次:A/1 页码:2
文件名称:移印丝印烫印热转印产品检验规范制定日期
1、目的
为确保移印丝印烫印热转印产品的检验与测试得到有效管制
2、范围
适用于公司移印丝印烫印热转印的标志及字样的检验与测试活动。
3、职责
巡检人员按检验规范对产品进行检验与判定,并对检验结果的正确性负责。
4、检验
4.1:检验方式:首件及巡检。
4.2:抽样方案:《MIL-STD-105E 特殊检验水平S-3 级正常检验一次抽样方案》进行
抽样。
4.3:质量允收、放行判定标准参考“抽样方案作业规范”
5.检验结果的记录
5.1:首件检验记在“首件检查记录表”中。
5.2:过程检验结果记在“喷漆车间巡检记录表”中
6、检验标准
6.1:外观检验
参照SI-006 外观检验标准“8.2 喷漆、丝印及热转印外观缺陷判定标准”进行判定
6.2附着力测试:
6.2.1:耐醇性测试
引用标准:《GB19342-2003》 5.1.1 脱色试验
用充分浸透 65%乙醇(酒精)的脱脂棉在产品各部位上往返用力擦拭 100 次,目测观察脱脂棉上是否有颜色。
丝网印刷类产品检验规范

1. 目的:
本标准规定了展示类丝网印刷试验方法、检验规则等要求。
2. 范围:
本标准适用于金属,塑料等材料上的丝网印刷。
3. 外观检验环境、方法:
照明设备
在自然光或光照度在200-300LX的近似自然光下(如40W白色荧光灯距离750mm 视觉方向
检验人员的校正视力不低于
要求验货人员眼睛与部件在要求的距离检验
验货人员视线与所持部件垂直(见图1)
转动部件呈45°角,然后使视线与部件呈夹角(见图1)
检验某部位所在面的视觉持续时间大约10秒
确定任何的判退用一带箭头的标签指示出缺陷位置
光源Light
Hl
4.
5.可靠性检验:
1、2、4为通用标准,3、6为SEB常用标准,5为JARDEN常用标准,7为SOLA(常用标
准,8为澳洲SUNBEA常用
7. 表单记录:
《丝印巡检记录》
8. 说明
本要求自规范发布之日起执行,由品质一科负责修改解释。
丝印产品测试检验规范

制定制定审核审核批准批准丝印产品测试检验规范丝印产品测试检验规范 文件编号文件编号 HSJD-74-07 生效日期生效日期 2014年6月11日版本版本A/1 1.目的目的明确丝印产品测试检验内容、方法以及判定标准,促使生产单位按标准要求生产,有利于检验者对质量进行控制,满足控制,满足客户客户质量要求质量要求. .2.2.适用范围适用范围适用范围2.1我司生产的所有丝印产品的测试,包括外购和外协加工我司生产的所有丝印产品的测试,包括外购和外协加工2.2在进行产品检测时,使用本检查标准的顺序是:《作业检查指导书》、客户图纸要求、BOM 表、表、工艺工艺要求、其它书面文件要求。
其它书面文件要求。
3.3.规范性引用文件规范性引用文件规范性引用文件下列文件中的条款通过本标准的引用而成为本标准的条款。
凡是注日期的引用文件其随后所有的修改单或修订版均不适用于本标准,然而,鼓励根据本标准达成协议的各方研究是否可使用这些文件的最订版均不适用于本标准,然而,鼓励根据本标准达成协议的各方研究是否可使用这些文件的最新版本新版本。
凡是不住日期的引用文件,其最新版本适用于本标准。
日期的引用文件,其最新版本适用于本标准。
MIL-STD-105E MIL-STD-105E 抽样程序和品质检查表抽样程序和品质检查表. .4.4.职责职责职责 丝印部负责产品的生产、周转、产品的标示、隔离、返工、丝印部负责产品的生产、周转、产品的标示、隔离、返工、丝印部负责产品的生产、周转、产品的标示、隔离、返工、异常处理异常处理结果的实施结果的实施品质部负责产品的检验、判定、标示以及品质异常问题的处理追踪结果品质部负责产品的检验、判定、标示以及品质异常问题的处理追踪结果品质部负责产品的检验、判定、标示以及品质异常问题的处理追踪结果. .5.5.检验标准检验标准检验标准5.1丝印性能测试丝印性能测试5.1.1 附着力测试测试 3M610 3M610胶纸胶纸a) a) 待丝印待丝印待丝印字体字体烘干或者在自然环境下冷却48小时后,将丝印表面用无尘布擦拭干净。
丝印检验规范(含表格)

丝印检验规范(IATF16949/ISO9001-2015)1.0 目的为了加强丝印生产现场产品品质的管控,有效地控制和降低潜在的品质风险,确保制程中品质处于受控状态。
2.0 范围适用于本公司所有在丝印生产过程中的半成品、成品的检验。
3.0 职责3.1 生产部负责领料确认、工艺检验、自主检验及不合格的处理记录;3.2 品质部负责巡回检验、移转检验及其记录;3.3 新产品的检验由技术部主导,生产部/品管部配合。
4.0丝印检验标准检验项目检验标准检验方式工具术语和定义:1、标准中W表示宽度、S表示面积、L表示长度、P表示个数、H标示深度2、异物:空气中的灰尘、丝印机污物等夹杂物。
3、凹痕:丝印前基体上的伤痕使涂装后该处出现凹颜色1.按设计图纸,以丝印签样样板或PANTONE丝印色卡为标准,在自然光线下目测如有较明显色差,则为不良全检目测签样样板或色卡附着力1、用透明胶带贴切在丝印文字或图案上,用手指压紧胶带使其与丝印表面紧密接触,3分钟后以与丝印表面成45°方向迅速拉起胶带,文字或图案表面状态有变化为不良。
3件目测透明胶带抗化学溶剂1、将99%酒精倒于白色软布(或脱脂棉)3件目测上。
在产品丝印文字或图案表面上以0.5kg力和1秒钟往返1次的速度摩擦5次(往返),(对按键丝印往返摩擦50次),目测文字或图案试验后的表面状态变化超过表观品质基准中可接受范围为不良。
软布脱脂棉99%酒精陷。
4、划痕:丝印文字或图案表面被坚硬物划伤,可见基体表面。
5、线细:丝印文字或图案线条局部未印刷充满而宽度变小。
6、欠缺:丝印文字或图案线条局部未印刷上而出现残缺。
7、渗透(拖墨):丝印文字或图案线条出现局部凸出或边缘呈锯齿状。
8 油墨飞溅:在印刷时油墨飞溅到丝印表面而形成的斑点。
耐摩擦性1、以直径为6.35mm的圆形橡皮放置于产品丝印文字或图案表面并垂直加载约1.6kg,在25.4mm的行程内以每分30次往返的速度摩擦30次。
丝印产品外观检验规范
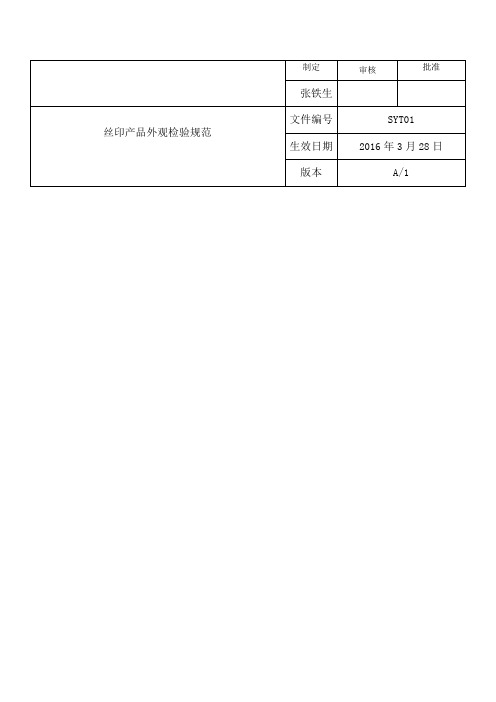
9.相关文件
文件控制程序
产品检验控制程序
10.相关记录
送检通知单
丝印首检检验表
来料送检通知单
IQC日报表
φ
直径mm
L
长度mm
H
深度mm
W
宽度mm
DS
距离mm
S
面积mm2
△E
色差NBS
△d
偏移量mm
8.检验标准
表2 丝印产品件外观要求
缺陷
编号
不良描述
不良
类别
接收标准说明
整个部品
A面
B面
C面
备注
1
走位
Min
L≤50,△d≤;
L>50,△d≤;
/
2
漏光/透底
Maj
不接受
/
3
印刷模糊/拉油/毛边/肥油
Maj
参照限度样板
抽箱方式:每1卡板的每1层至少抽取1箱,每箱至少在上、中、下均匀抽取样板且每个生产日期皆要抽检.
IQC在检查来料时,每次抽取的样本量不能少于5PCS产品,如有1PCS不合格影响装配或功能则判断NG;
IPQC在抽样检查时,每2小时抽取不少于3啤进行外观检查;每2小时抽取不少于2啤进行尺寸检查.
功能测试试装检查
特别说明:
1损坏产品重要的、最终的基本功能的缺陷总是判为不可接受.
2以下标准和客户标准有相异时,最终判定以客户标准优先.
3如有限度样板,优先参照限度样板为准;无限度样板,参照本标准.
4不知怎样判定时,应与相关人员商议或召集会议后判定.
7.缺陷代码对照表
表1 缺陷代码对照表
代码
名称单位
丝印检验标准
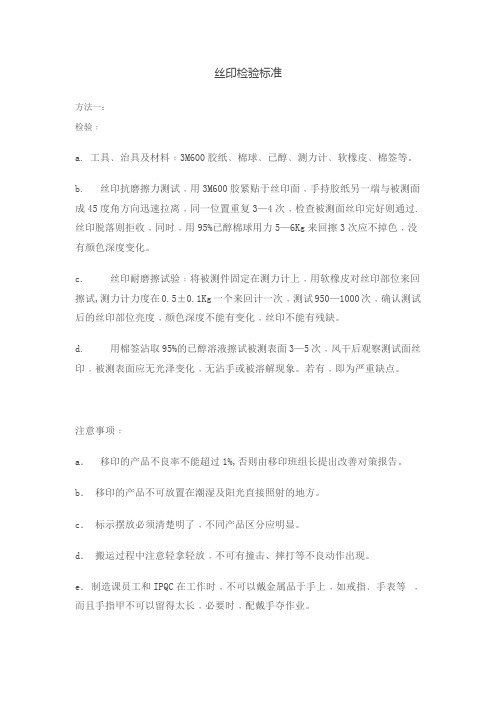
丝印检验标准方法一:检验﹕a. 工具﹑治具及材料﹕3M600胶纸﹑棉球﹑已醇﹑测力计﹑软橡皮﹑棉签等。
b. 丝印抗磨擦力测试﹐用3M600胶紧贴于丝印面﹐手持胶纸另一端与被测面成45度角方向迅速拉离﹐同一位置重复3—4次﹐检查被测面丝印完好则通过.丝印脱落则拒收﹐同时﹐用95%已醇棉球用力5—6Kg来回擦3次应不掉色﹐没有颜色深度变化。
c. 丝印耐磨擦试验﹕将被测件固定在测力计上﹐用软橡皮对丝印部位来回擦试,测力计力度在0.5±0.1Kg一个来回计一次﹐测试950—1000次﹐确认测试后的丝印部位亮度﹐颜色深度不能有变化﹐丝印不能有残缺。
d. 用棉签沾取95%的已醇溶液擦试被测表面3—5次﹐风干后观察测试面丝印﹐被测表面应无光泽变化﹐无沾手或被溶解现象。
若有﹐即为严重缺点。
注意事项﹕a.移印的产品不良率不能超过1%,否则由移印班组长提出改善对策报告。
b.移印的产品不可放置在潮湿及阳光直接照射的地方。
c.标示摆放必须清楚明了﹐不同产品区分应明显。
d.搬运过程中注意轻拿轻放﹐不可有撞击、摔打等不良动作出现。
e.制造课员工和IPQC在工作时﹐不可以戴金属品于手上﹐如戒指﹑手表等﹐而且手指甲不可以留得太长﹐必要时﹐配戴手夺作业。
f.移印的产品包装时要用塑料袋包好才入箱方法二:1.目的1.1规范喷涂/丝印缺陷用语。
1.2明确产品要求,统一检验标准。
2.适用范围适用于本公司所有喷涂/丝印的产品的检验。
3.表面等级3.1 A级表面:能直接正视的外部表面如机柜的正面,以下简称A面。
3.2 B级表面:不明显的外部和开启门后就能正视的内部表面如机柜的后表面,以下简称B 面。
3.3 C级表面;不易察看的内部和外部表面如机柜的底面,以下简称C面。
4.检验环境4.1 光度:200-300LX (相当于40W日光灯距离为750MM)4.2 产品需检验表面与检验者目视方向大约成45°(如下图)(这里的图没有找到),时间约10秒。
喷油.移印.丝印检验规范

三阶文件
XX-SIP-015
品管部
B/0
Page2of4
喷油件缺陷描述及判定
类
别
检验
项目
检验
标准
检验
方式
缺陷描述
缺陷判定
Cri
Maj
Min
喷
油
件
哑色
起沙
工
程
签
办
或
客
签
办
目
视
影响产品外观不明显。
×
影响产品外观明显。
×
气
泡
产品表面1×1CM宽有1个以上大于0.3MM的气泡。
×
产品表面1×1CM宽有1个或面积小于0.3MM的气泡。
5.6由喷油、移印、丝印部返好工的胶件,经QC再检验后,合格了才能入仓.
6.0喷油、移印、丝印件检验缺陷描述及判定:
抽样标准
MIL-STD-105E
单次抽样水准
正常抽样Ⅱ
AQL
CRI
MAJ
MIN
0
1.5
2.5
类
别
检验
项目
检验
标准
检验
方式
缺陷描述
不良品判定
CRI
MAJ
MIN
文件类别
文件编号
制定部门
版本
品管部
B/0
Page3of4
5.3当抽查的不合格品超过AQL值时(严重问题和轻微问题),出不合格验货报告,在产品箱的物料标签上盖上红色QC不合格章,并写不合格报告,通知有关部门进行隔离。
5.4经检验后,没有超出AQL值的箱数上打上QC“PASSED”章,并记录在检验报告上,由货仓人员收货.
5.5当QC人员判定不合格的产品,而生产又急需要的,由QC人员开出<<验货报告>>交由品质部负责人审核后,由经理核准后,通知生产部拣用,才能放行.
丝印检验规范

条件:不得在反光下检验表面、不得使用放大镜检验表面。
检验时间:3-5秒
4.检验要求:
4.1.尺寸检验部位依承认书图纸位置检验
4.2.检验电子料件必须带静电手环/静电手套作业
4.3.检验工具;直尺
5.判退:AQL 6.注意事项 :客户有特殊要求时,以客户特殊要求为准;尺寸与性能参数记录6个数据在《IQC进料检验报告》上
目视
及外箱标识的品名料号与检验验收单中
2.品名(包装 的品名和实物及料号应一致;③任何有
标示)
误,均不可接受。
目视
包装外观 不可有破损及脏污 混料/错料 不可混料﹑错料 出货目视 目视
核准:
审核:
制定:
√
√
√ 3-5PCS
√
√ √
√ √
目视
不可有明显刮伤、划伤、错位、针孔、
产品外观 异物、断线、色差、污渍、油墨厚度不 目视
均等。
丝印附着力测 用水轻擦15S,然后再用己烷或无水乙
试
醇轻擦15S,字迹清晰可辨
棉布 /500g砝
码
1.料号(包装 ①包装袋上应标明数量、品号、品名、
标示)
规格、型号、生产日期及生产厂家;②
与承认样品比较厂商所交实物的料号以
丝印产品进料检验规范
编号:
1.适用范围: 本文件适用于公司內所有产品使用的丝印产品来料检查
2.抽样计划﹕A 一般项目执行MIL-STD-105E Ⅱ 单次抽样
B 带“*”为特殊项目(可靠性检测及破坏性检测)采用MIL-STD-105E S2 抽样
3.外观检验环境:
距离:检验光强度250~500 Lux,眼睛距离被测物45-55CM, 检视偏移范围小于45°角。
丝印检验规范
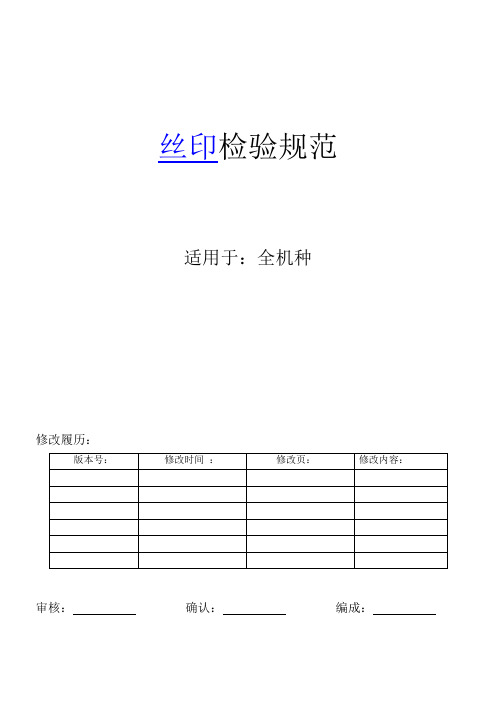
丝印检验规范适用于:全机种修改履历:审核:确认:编成:一、目的:明确产品检验标准,确保产品质量满足公司和客户要求。
二、范围:适用于本公司所有丝印产品。
三、相关文件:参照公司发行的相关产品资料。
四、定义:4.1缺陷定义:4.1.1 CR(Critical):致命缺陷,对产品使用、维修或有关人员身造成危害或不安全的缺陷,抵触安全规格要求的,或妨碍到某些主要的功能的缺陷;4.1.2.MAJ(Major):主要缺陷,即不构成致命的,但可能造成故障,或对单位产品预定的目的使用性能会有严重的降低的缺陷;4.1.3. MIN(Minor):次要缺陷,只对产品的有效使用或使用性能有轻微的影响的,一般为外观或机构组装之差异。
五、检验所需仪器和设备:白棉纱布、75%浓度酒精、95%浓度酒精、3M胶。
六、检验水准:按照MIL-STD-105E一般检验Ⅱ级水准及主要AQL水平进行抽验,允收标准:严重缺陷AQL为:CR=0 ;主要缺陷AQL为:MA=0.65;次要缺陷AQL为:MI=1.5。
七、检验项目:7.1包装检验:外包装以能承受搬运振动的纸箱为主,不允许有受潮或破损现象,每个包装袋须有清晰明显的标贴,标贴内容应包括:供应商、品名规格、包装数量、物料编号、生产日期或批号以便于追溯。
7.2外观检验项目定义:异物:丝印后,涂膜附着飞尘,点状或丝状物。
露底:由于丝印位置丝印太薄露底色。
漏印:要求丝印位置未丝印到位。
模糊/断线:丝印不良导致丝印线条或图案粗细不均,模糊不清,字线局部不相连。
丝印厚薄不均匀:由于丝印操作不当,造成点线或图案的丝印厚薄不均匀。
错位:由于丝印位置不准,丝印偏移。
针孔:涂膜表面能看见针眼状小孔。
擦伤/划痕:丝印后保护不善。
杂色/污渍:非丝印颜色附着在丝印面上。
色差:和标准色板相比颜色有差异。
色错:丝印颜色错误。
7.3可靠性测试:7.4.1.拇指测试:取实验样品5PCS,用拇指放在印刷的字画上,用1.5±0.5Kg·f的力在印刷的字画上往返30个来回(约15SEC)。
电镀、喷涂、丝印检验规范

3.在印刷表面:图案和文字周围20mm的范围内不允许有任何缺陷.
三.性能测试:
1.附着力: (附着强度为10±1N/25mm),3M胶带紧密贴在丝印文字或图案上5分钟后,以60°方向迅速拉起,印刷文字或图案无任何脱落迹象.
2.耐溶剂性:用无水已醇酒精润湿脱脂棉或白色软质棉布,用1kg的力每秒钟往返1次的速度擦同一位置10次,表面无任何变化.
七.光泽: G33 8~12
G34 8~12
G41 55以上
G26 25
G28 5
第1页,共3页
主题:电镀、喷涂、丝印检验规范
适用对象:品保部全体人员
G32 5
电镀
一主视表面零件在装配成完整产品后处于正常视觉范围内的可见表面
二工艺我司使用是挂镀方式电镀五彩锌
三外观
镀层结晶均匀、细致、连续
允许有轻微夹具印
六.涂层硬度:铅笔硬度不低于2H.
允许缺陷:
1.对喷涂之镀锌的钢板或之氧化的铝件允许在内表面深凹处有漏底现象.
2.在零件转弯或边缘部位允许有轻微纹理变平滑现象.
3.在零件内表面深凹处且不易查看处,允许有补漆现象,以消除露底现象,这中区域允许在外观上有差异
4.对于要求局部喷涂的零件,要保证界线清晰、整齐.在不要求上喷涂的区域不能飞上涂料.
不允许缺陷镀层粗糙、麻点、黑点、起泡、剥落和严重条纹镀化膜疏松起粉及严重钝化液痕迹局部无镀层、手印等
允许缺陷不影晌装配效果的轻微水印主视表面不允许
零件状态不同同一零件上有不均匀的颜色和光泽
非主视面有小而少的夹具印小于mm
焊缝搭接交界处不明显的稍暗或发白现象
电镀件一般层放要保持通风干燥保存期限个月电镀日期起超过个月的电镀件必须重检
丝网印刷类产品检验规范

精心整理文件编号 QW/r-16-2012版本状态 A0Page共 4 页丝网印刷类产品查验规范1.目的:本标准规定了展现类丝网印刷试验方法、查验规则等要求。
2.范围:本标准合用于金属,塑料等资料上的丝网印刷。
3.外观查验环境、方法:3.1 照明设施在自然光或光照度在 200-300LX 的近似自然光下(如 40W 白色荧光灯距离 750mm )3.2 视觉方向查验人员的校订视力不低于 1.2 要求验货人员眼睛与零件在要求的距离查验 验货人员视野与所持零件垂直 (见图 1) 转动零件呈 45°角 ,而后使视野与零件呈夹角(见图 1) 查验某部位所在面的视觉连续时间大概 10 秒 确立任何的判退用一带箭头的标签指示出缺点地点光源 LightSourceView40W 荧光灯视角图 14.外观查验:NO注: 600mm 能够用手臂直伸出,指尖至腋窝处为大概距离规格描绘不良项目内容描绘字宽字宽750mm|W1-W2|≤0.2W11文字粗细不均W1W2即对标准 W1同意的表面文字的不平均度为± 40%标准比标准细(粗)Objecta 零件2文字外侧污点h. 如图飞边长度 a ≤1/3h右边的油墨飞边或印刷飞边飞边宽度≤(a: 长度 b: 宽度 )b 1/3W(h: 字高 W:字宽 )45°中心偏移值3X ≤ 1mm 文字偏离中心Y 方向B中心偏移值Y ≤ 1mmYX 方向 XL偏移线4文字倾斜HL ≤450mm 时-2mm ≤H ≤2mm标准线L>450mm 时 -3mm ≤ H ≤ 3mmL :指所有的字长H :指偏离水平线的垂直距离5印刷溅点.溅点的直径 D ≤0.5,N ≤2在应无印刷的地区出现点状油墨精心整理6印刷针孔在应当有印刷的地方出现点状的缺针孔的直径 D≤0.3,N ≤1少油墨连续文字发生断线7文字断线宽度 c不同意cL 如下图8边角漏印边角缺印不同意dd 为缺角长L 为标准长残破部a≤0.1mm9文字残破h 残破宽度 ab≤0.1mm,N≤1残破深度 b10印刷重影二次印刷的整体错位不同意11指纹印刷文字留有指纹不同意12印刷表面异物线屑状异物、印迹等300mm~350mm目视距离不行分辨时同意300mm350mm目视距离不行分辨时13色薄文字的颜色偏浅~同意14印刷文字或颜印刷文字或颜色与图纸、封样规定不符不同意色错误15文字锯齿印刷文字的边体现锯齿参照限度封样品5.靠谱性查验:NO项目测试工具测试方法接受标准高低温箱 / 目储存温度:+66°C印刷表面无起皱、起泡、裂纹、1高温储存试验寄存时间 :48hours视2h 后, 目测察看剥落且颜色光彩无显然变化样板出炉后在室温下搁置高低温箱 / 目储存温度 :- 40°C印刷表面无起皱、起泡、裂纹、2低温试验寄存时间 :48hours视剥落且颜色光彩无显然变化样板出炉后在室温下搁置2h 和后 , 目测察看储存温度 / 湿度:+66°C/85%RH 样板出炉后在室温下搁置 2 小高温高湿储存高低温箱 / 目时后 , 印刷表面无起皱、起泡、3寄存时间: 96hours试验视裂纹、剥落且颜色光彩无显然样板出炉后在室温下搁置2h 后, 目测察看变化储存温度 :- 40°C/+66°C高低温箱 / 目在- 40°C下寄存 1h 而后升温到?+66°C?下存检查零件 : 和印刷表面无起皱、4冷热冲击试验放 1h,为一循环 , 温度间的变换时间不超出起泡、裂纹、剥落且颜色光彩视5min,共 12 循环无显然变化样板出炉后在室温下搁置2h 后, 目测察看3M600透明胶将 3M600透明胶带贴在所要测试的试样的印刷5丝/ 移印附着力带或粘力大字体或图案上,并用手压平,而后拉起胶带尾表面 , 丝 / 移印字体或图案应能测试于 5.3N/18mm部与测试面呈 90 度, 快速撕下胶带,同样部位清楚可辨,没有剥落状况的透明胶带 /重复 3 次精心整理目视将试件固定,用 250kg 的垂直力, 15mm 的行程 表面 , 磨损不可以见底 , 丝/ 移印6 摩擦测试橡皮擦 / 目视 来回摩擦 , 每一单程行程为一次,对丝印字体 应能清楚可辨 或图案 , 连续摩擦 50 次7 抗溶剂测试 - 异 异丙醇 / 白布 取 1ml 异丙醇溶液滴在试样喷涂面或丝 / 移印 丙醇试验 / 目视 表面, 10min 后用白布擦干异丙醇溶液试样表面经擦抹后印刷字体或抗溶剂测试 - 抗 99%的酒精 /用棉团或白布浸润浓度为 99%的酒精溶液 , 然 图案应清楚可见 , 且颜色也不 8 后以 1kg 压力和 1 秒钟来回 1 次的速度在试样 得有失光 , 掉色等现象 酒精测试 目视印刷字体和图案的同一地点,来回擦试 20 次条件:实验样品 5PCS 以上制品印刷图案不行缺口 / 断线 / 9 拇指测试拇指 / 目视 实验程序:取样品,用拇指放在印刷的图片上, 油墨粘附不良等,不然为不合 以 3+0.5-0 kgF 的力来回檫试 15 次。
丝网印刷类产品检验规范
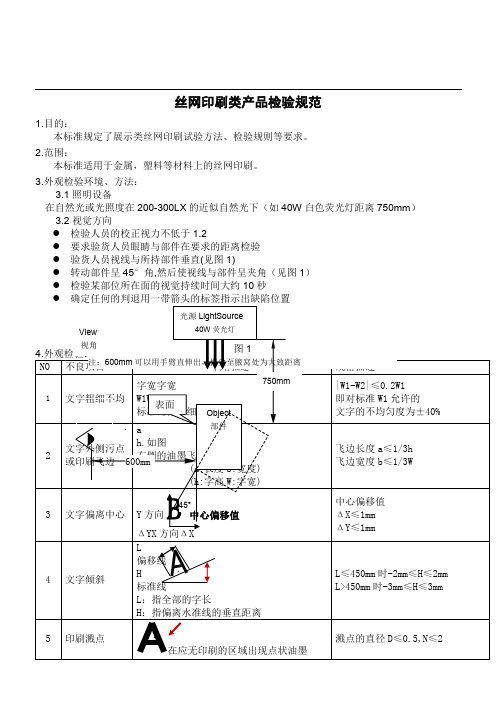
表面,丝/移印字体或图案应能清晰可辨,没有剥落情况
6
摩擦测试
橡皮擦/目视
将试件固定,用250kg的垂直力,15mm的行程来回摩擦,每一单程行程为一次,对丝印字体或图案,连续摩擦50次
L:指全部的字长
H:指偏离水准线的垂直距离
L≤450mm时-2mm≤H≤2mm
L>450mm时-3mm≤H≤3mm
5
印刷溅点
在应无印刷的区域出现点状油墨
溅点的直径D≤0.5,N≤2
6
印刷针孔
在应该有印刷的地方出现点状的缺少油墨
针孔的直径D≤0.3,N≤1
7
文字断线
连续文字发生断线
宽度c
c
不允许
8
边角漏印
批量>500pcs抽5pcs.
低温试验
●
●
高温高湿存储试验
●
●
冷热冲击试验
●
●
丝/移印附着力测试
●
●
摩擦测试
●
●
抗溶剂测试-异丙醇试验
●
●
抗溶剂测试-抗酒精测试
●
●
拇指测试
●
●
75%酒精测试
●
●
95%酒精测试
●
●
810胶带测试
●
●
3M600胶带测试
●
●
250胶带测试
●
●
汽油擦拭测试
正己烷擦试测试
7.表单记录:
L如图所示
边角缺印
dd为缺角长
L为标准长
不允许
塑料件丝印检验规范
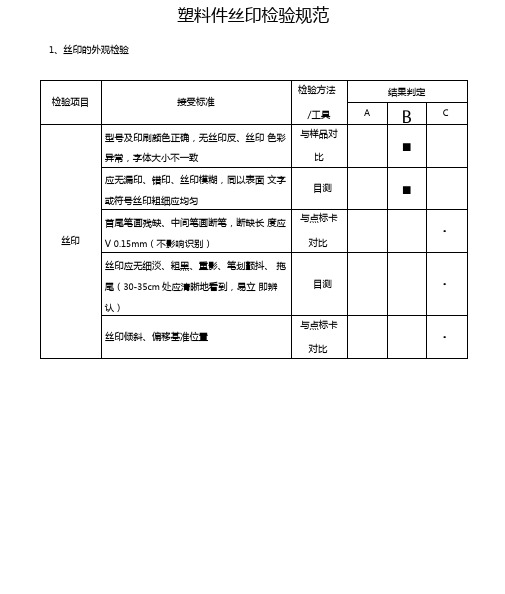
于1条的
明显划痕
2H铅笔
量产
后
2pcs/
批
6
人工
汗液 测试
(酸
性)
将材料放入人汗中,试验持续时间不小于
48小时,在试验温度55(+/-)2 °C、93〜95%相对湿度环境下测试,人汗配方:氯化钠(Nacl)20g/L;氯化氨(NH4CL)17.5g/L;尿 素(CH4N2O)5g/L;醋酸(CH3COOH)2.5g/L;乳酸(C3H6O3)15g/L;再加入氢氧化钠
300 350mm目视 距
离
12
不可分辨时允许
300350mm目视 距
13
色薄
文字的颜色偏浅
离
不可分辨时允许
印刷文字或
印刷文字或颜色与图纸规定不
不允许
3、丝印的特殊检验
序
号
检验
项目
检验内容方法及条件
判定标准
检验工具
抽样
数量
1
附着
力测
试
用百格刀或锋利刀片(刀锋角度为15°〜
30°)在测试样本表面划10X10个
2
••
文字外侧污 点或印刷飞 边
t
字*>如图
*右侧的油墨飞边
W
(a:长度b:宽度)
(h:字高W:字宽)
±20%
飞边长度aWl/3 h飞边宽度bWl/3W
3
文字偏
离中心
G
比照样品或菲林字 体中心位置偏移值:
XWO. 20mm
4ห้องสมุดไป่ตู้
文字 倾斜
偏移线
标准线
L:指全部的字长
H:指偏离水准线的垂直距离
YWO. 20mm
塑料件丝印检验规范.doc

塑料件丝印检验规范1、丝印的外观检验检验项目接受标准检验方法结果判定/工具ABC型号及印刷颜色正确,无丝印反、丝印与样品对●色彩异常,字体大小不一致比应无漏印、错印、丝印模糊,同以表面目测●文字或符号丝印粗细应均匀首尾笔画残缺、中间笔画断笔,断缺长与点标卡●丝印度应< 0.15mm(不影响识别)对比丝印应无细淡、粗黑、重影、笔划颤抖、拖尾( 30-35cm 处应清晰地看到,易立目测●即辨认)丝印倾斜、偏移基准位置与点标卡●对比2、印刷的外观检验缺陷参考表:NO不良项目文字粗1细不均2文字外侧污点或印刷飞边文字偏3离中心4文字倾斜印刷5溅点印刷6针孔7文字断线边角8漏印9文字内容描述字宽字宽W1 W2标准比标准细(粗)ah. 如图w右侧的油墨飞边(a: 长度 b: 宽度 )(h: 字高 W: 字宽 )YXL偏移线H标准线L:指全部的字长H:指偏离水准线的垂直距离.在应无印刷的区域出现点状油漆在应该有印刷的地方出现点状的缺少油墨连续文字发生断线宽度 c如图所示L边角缺印d d为缺角长度L为标准长度残缺部规格描述|W1- W 2| ≤ 0.2W1即对标准 W1允许的文字的不均匀度为±20%飞边长度 a≤1/3 h飞边宽度 b≤1/3 W比照样品或菲林字体中心位置偏移值:X≤0. 20mmY≤0. 20mmL≤3mm时-0.3mm ≤H≤0.3mmL>3mm 时- 0.5mm≤ H≤ 0.5mm溅点的直径D ≤0.2 ,N ≤1针孔的直径D ≤0.2 ,N ≤1c≤0.15mm,N≤1d≤1/10L,N ≤ 1a ≤1/4 h残缺hW 宽度 a深度 b b ≤1/2 W 字高 h字宽 W10 印刷重影二次印刷的整体错位不允许300 ~350mm目视距11 指纹印刷文字留有指纹离不可分辨时允许印刷表面异线屑状异物、印迹等300 ~350mm目视距12 物离不可分辨时允许300 ~350mm目视距13 色薄文字的颜色偏浅离不可分辨时允许印刷文字或印刷文字或颜色与图纸规定不不允许14 颜色错误符15 文字锯齿印刷文字的边呈现锯齿参照限度样品3、丝印的特殊检验序 检验检验内容方法及条件判定标准检验工具抽样号 项目数量用百格刀或锋利刀片(刀锋角度为 15°~30°)在测试样本表面划 10×10个1mm ×1mm小网格, 每一条划线应深及镀层的底材;用 在划线的 毛刷将测试区域的碎片刷干净;用粘附力交叉点处2百格刀或锋利 量产附着 350~400g/cm 的胶带(3M600号胶纸或等同)有小片的牢牢粘住被测试小网格,并用橡皮擦用力擦拭刀片;3M600后1力测 油漆脱落,胶带,以加大胶带与被测区域的接触面积及力 号胶纸或等 2pcs/ 试且脱落总 度;用手抓住胶带一端,在垂直方向 (90 °) 同。
铝外壳丝印喷油通用检验规范(1)

文件编号:版本:A/1制定日期:修订日期:拟案单位:品管部/IQC 发行章:Revision History 修改记录1.0目的明确检验标准,将外观判定标准量化、明确化。
更有利的控制来货、制造过程、出货检验的品质。
指导检验员正确地检查铝外壳来料的品质2.0 范围适用于本公司3335#系列的铝外壳和3339#系列的铝外壳和其它一些新增型号的铝外壳;以及丝印、喷涂、喷油系列表面附着力的检测。
制作图纸上所指定的,应按指定的要求来判定;与客户及纳入厂家之间协商决定的,按协商的结果来判定;客户签有外观限度样板的,按照限度样板来判定;影响安全性能的,本标准不适用。
3.0职责IQC检验员或驻厂QC负责按本检验规范的要求执行检验。
4. 定义公司的铝外壳通常为表面拉纹后再氧化上色;如果有需要也会在表面进行喷涂(烤漆)处理。
5. 抽样计划5.1. 抽检方案一般抽样:依据检验抽样计划ANSI/ASQC Z1.4 抽样计划表/水平Ⅱ级进行抽样,特殊抽样:零部件依S-3水平。
破坏性的测试:不少于3个。
5.2. 样本的抽选应随机、分散抽样。
6.0 检查环境条件6.1温度:常温(5℃~35℃)6.2场所:阳光直射不到的场所,无尘埃飘扬的场所6.3亮度:500Lux~3000Lux,不刺眼。
6.4目视距离:离产品30cm~50cm的距离,但是,判定中有异议时,可用扩散的日光进行检查(从太阳出来3小时后到太阳退去的3小时前这一时段,以避开日光直射入的光)6.5时间:不得在部品上停留,必须以连续的动作进行,在某一位置的停留时间最长不得超过5秒。
.6.6目视方向:与产品成垂直及450角(见图1)7.0 外观等级的定义(一般要求):7.1 A级面:也叫一级面,客户用于光机上的前面、正面。
例如:仪器、设备的面板、顶壳以及有通纸面要求的表面。
7.2 B级面:也叫二级面,客户外装的侧面、背面。
这些表面在基本使用状态下能时常看到的范围。
另外,用户虽然看不见,但会影响机能的零件,也纳入B级面来管理。
外发加工移印件丝印件检验规范

外发加工移印件丝印件检验规范1、外观检验2 、尺寸检测:严格按照文控中心所发放的图纸或样品,用卡尺、工具显微镜或投影仪测量产品的长度、宽度、厚度等关键尺寸,公差按照±0.05进行检验,并记录在检验报告中,当非关键尺寸有特殊要求时也要测量。
3 、附着力测试:用锋得刀片(刀锋角度为15º~30º)在测试样板表面划10X10个1mmX1mm或(5X5个2mmX2mm)小网格,每一条划线应深及油漆层的底材;用毛刷将测试区域的碎片刷干净;用3M 600号胶纸牢牢粘住被测试小网格,并用橡皮擦拭胶带,以加大胶带与测试区域的接触面积及力度;用手抓住胶带的一端,将胶带呈45º角迅速扯下胶纸,粘揭3次,每次使用新的胶带.要求附着力达4B(或3B)为合格.5B-划线边缘光滑,在划线的边缘及交叉点处均无油漆层脱落;4B-在划线的交叉点处有小片的油漆层脱落,且脱落总面积小于5%;3B-在划线边缘及交叉点处有小片的油漆层脱落,且脱落总面积在5%~15之间2B-在划线边缘及交叉点处有成片的油漆层脱落,且脱落总面积在15%~35之间1B-在划线边缘及交叉点处有成片的油漆层脱落,且脱落总面积在35%~65之间0B-在划线的边缘及交叉点处有成片的油漆层脱落,且脱落总面积≥65%注1: 当测试面积较小时,不要求一定要划10X10个小方格,可以根据测试面积的大小确定划格的数目.注2: 当油漆层的厚度小于50µm时,划10X10个1mmX1mm的小方格; 当油漆层的厚度大于50µm时,划5X5个2mmX2mm的小方格.注3: 对于表面光滑的喷油件,表面附着力达4B以上;对于表面有皮纹的油漆层,要求附着力达3B以上.4、耐磨性测试:用专用的RCA耐磨测试仪及专用的纸带,施加175g的载荷,带动纸带在样本表面磨擦200个循环, 油漆层不露底材为合格.(供应商提供测试报告)5 、耐醇测试:用纯棉布蘸满无水酒精(浓度≥99.5%),包在专用的500g砝码头上(包上棉布后测试头的面积为1平方厘米),以40次/分钟~60次/分钟的速度,20mm左右的行程,在样本表面来回擦拭200个循环,试验完成后以油漆层无变色、不露底材为合格.(供应商提供测试报告)。
3.丝印检验标准
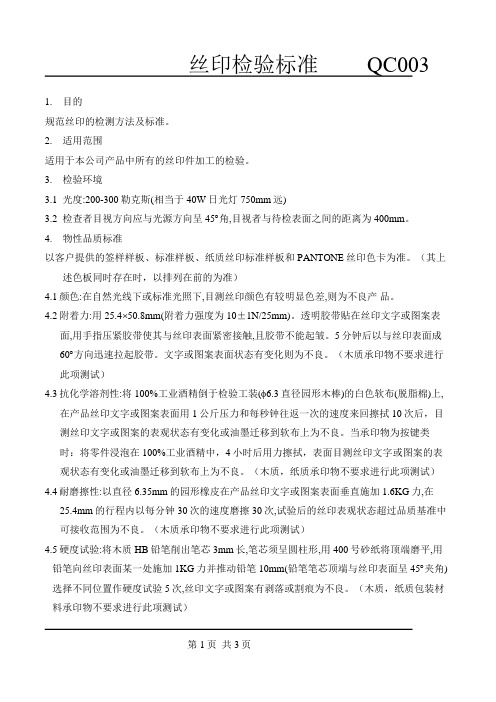
丝印检验标准 QC0031. 目的规范丝印的检测方法及标准。
2. 适用范围适用于本公司产品中所有的丝印件加工的检验。
3. 检验环境3.1 光度:200-300勒克斯(相当于40W日光灯750mm远)3.2 检查者目视方向应与光源方向呈45︒角,目视者与待检表面之间的距离为400mm。
4. 物性品质标准以客户提供的签样样板、标准样板、纸质丝印标准样板和PANTONE丝印色卡为准。
(其上述色板同时存在时,以排列在前的为准)4.1颜色:在自然光线下或标准光照下,目测丝印颜色有较明显色差,则为不良产品。
4.2附着力:用25.4⨯50.8mm(附着力强度为10±1N/25mm)。
透明胶带贴在丝印文字或图案表面,用手指压紧胶带使其与丝印表面紧密接触,且胶带不能起皱。
5分钟后以与丝印表面成60︒方向迅速拉起胶带。
文字或图案表面状态有变化则为不良。
(木质承印物不要求进行此项测试)4.3抗化学溶剂性:将100%工业酒精倒于检验工装(φ6.3直径园形木棒)的白色软布(脱脂棉)上,在产品丝印文字或图案表面用1公斤压力和每秒钟往返一次的速度来回擦拭10次后,目测丝印文字或图案的表观状态有变化或油墨迁移到软布上为不良。
当承印物为按键类时:将零件浸泡在100%工业酒精中,4小时后用力擦拭,表面目测丝印文字或图案的表观状态有变化或油墨迁移到软布上为不良。
(木质,纸质承印物不要求进行此项测试)4.4耐磨擦性:以直径6.35mm的园形橡皮在产品丝印文字或图案表面垂直施加1.6KG力,在25.4mm的行程内以每分钟30次的速度磨擦30次,试验后的丝印表观状态超过品质基准中可接收范围为不良。
(木质承印物不要求进行此项测试)4.5硬度试验:将木质HB铅笔削出笔芯3mm长,笔芯须呈圆柱形,用400号砂纸将顶端磨平,用铅笔向丝印表面某一处施加1KG力并推动铅笔10mm(铅笔笔芯顶端与丝印表面呈45︒夹角)选择不同位置作硬度试验5次,丝印文字或图案有剥落或割痕为不良。
丝印检验标准
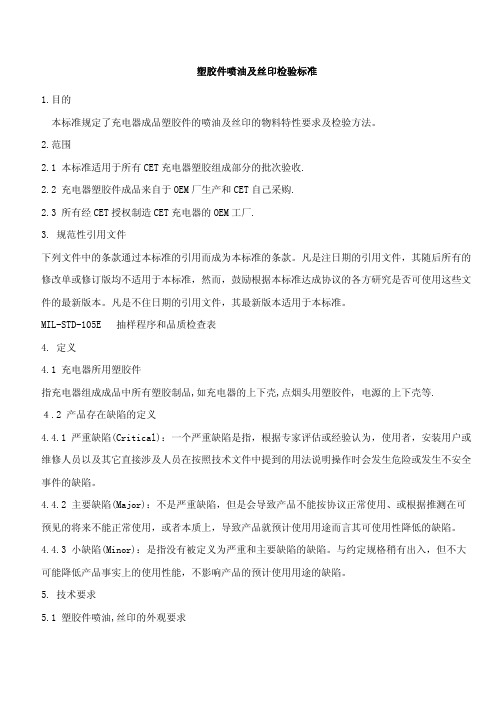
塑胶件喷油及丝印检验标准1.目的本标准规定了充电器成品塑胶件的喷油及丝印的物料特性要求及检验方法。
2.范围2.1 本标准适用于所有CET充电器塑胶组成部分的批次验收.2.2 充电器塑胶件成品来自于OEM厂生产和CET自己采购.2.3 所有经CET授权制造CET充电器的OEM工厂.3. 规范性引用文件下列文件中的条款通过本标准的引用而成为本标准的条款。
凡是注日期的引用文件,其随后所有的修改单或修订版均不适用于本标准,然而,鼓励根据本标准达成协议的各方研究是否可使用这些文件的最新版本。
凡是不住日期的引用文件,其最新版本适用于本标准。
MIL-STD-105E 抽样程序和品质检查表4. 定义4.1 充电器所用塑胶件指充电器组成成品中所有塑胶制品,如充电器的上下壳,点烟头用塑胶件, 电源的上下壳等.4.2 产品存在缺陷的定义4.4.1 严重缺陷(Critical):一个严重缺陷是指,根据专家评估或经验认为,使用者,安装用户或维修人员以及其它直接涉及人员在按照技术文件中提到的用法说明操作时会发生危险或发生不安全事件的缺陷。
4.4.2 主要缺陷(Major):不是严重缺陷,但是会导致产品不能按协议正常使用、或根据推测在可预见的将来不能正常使用,或者本质上,导致产品就预计使用用途而言其可使用性降低的缺陷。
4.4.3 小缺陷(Minor):是指没有被定义为严重和主要缺陷的缺陷。
与约定规格稍有出入,但不大可能降低产品事实上的使用性能,不影响产品的预计使用用途的缺陷。
5. 技术要求5.1 塑胶件喷油,丝印的外观要求5.1.1 塑胶件喷油丝印整体可见表面污点(含簧片表面污渍)面积小于0.5mm2,,数量不多于2个;5.1.2 塑胶件喷油丝印整体可见表面划伤, 直径小于0.2mm,长度小于2mm,数量不多于2个;5.1.3 塑胶件喷油的上下壳无色差;5.1.4 塑胶件整体无变形,缩水,批锋,油渍等不良;;5.1.5 塑胶件的丝印表面位置无偏移, 漏印,错印,杂色等不良现象;5.1.6 在塑胶件中有生产日期的标识。
丝印检验规范

N/A
minor
目视
SOP稽核
开线确认
后续随机稽核
检验各工位及操作人员,油墨丝网,使用工具,干燥箱参数设定是否符合或遵守SOP作业
major
参考SOP
不良品确认
随机
督导产线人员对不良品作好标识及区分,检查有无误判,记录制程不良数
N/A
N/A
异常处理
随机
注:严重缺陷,扣留本批所有成品;轻微缺陷,拒收两平板;重工如发现1PC不良品,连续向前追溯两平板。
major
3M胶带
目视
抗有机溶剂
首件确认开线后,每100PCS检1PC
用白色棉布粘上100%酒精,在丝印线上以1KG的压力,每秒往返一次的频率磨擦20次,棉布上不得沾有油墨
major
白色棉布
100%酒精
目视
硬度
首件确认开线后,每100PCS检1PC
用HB铅笔(磨平芯头)以45度角,施加1KG压力在丝印线五处不同位置划线,文字或图案不得脱落
抽样频率
检验要求
缺陷等级
检验方法
字体位置
首件确认开线后,每50PCS检1PC
将工程菲林和印刷件进行比对
字体偏差不得超过0.5mm
minor
卡尺、目视、菲林
颜色
首件确认开线后,每100PCS检1PC
用标准色板和印刷字体比对,偏差不得超出规格
minor
色板
附着力
首件确认开线后,每100PCS检1PC
用3M胶带粘贴在印刷字体上90S,使附着层不得有汽泡,然后快速反向撕起胶带,胶带上不得有墨迹
版本/修订号
更改内容
生效日期
A/01
初版发行。
2007-07-01
- 1、下载文档前请自行甄别文档内容的完整性,平台不提供额外的编辑、内容补充、找答案等附加服务。
- 2、"仅部分预览"的文档,不可在线预览部分如存在完整性等问题,可反馈申请退款(可完整预览的文档不适用该条件!)。
- 3、如文档侵犯您的权益,请联系客服反馈,我们会尽快为您处理(人工客服工作时间:9:00-18:30)。
丝印件检验规范
目的
规范产品质量检测标准,确保产品质量完全满足相关客户的要求。
规范产品质量缺陷的统一描述,确保内/外部的品质交流和沟通达成共识。
针对相关质量缺陷,分析改进现行生产工艺质量控制方法。
确保生产和检测标准与产品质量标准的一致性。
适用范围
适用于所有丝印车间所有丝印产品的检测。
适用于外购、外加工或客供丝印产品的检测。
丝印件质量缺陷分类
丝印件质量缺陷判定等级:
丝印件质量缺陷产生的原因分析
颜色错误---调制的油墨颜色与工程技术要求的完全不一致;或工程技术要求与客户要求的完全不一致(颜色偏差特别明显,或者根本就是两种不同的
油墨颜色)。
颜色偏差---调制的油墨所丝印出来的颜色与工程技术要求或客户要求有一定的
偏差,通过分光测色计读出的Lab△E值与规定和要求的偏差值在客户接收范围内,或超过了客户的允收标准。
油墨脱落---承印物的表面被化学污染,导致丝印油墨附着不牢固;丝印层干燥条件不足,丝印油墨未彻底干透;油墨本身附着力差;原材料本身无图层;油墨与原材料起化学反应。
丝印偏位---网版拉伸尺寸误差过大;作业员操作方法不当,造成丝印定位(套位)不准;丝印的产品来料定位面边缘变形或呈锯齿状;网版变形;承印物受热胀冷缩的影响明显,导致丝印第二对位或套位不准;定位片破损,造成丝印套位偏位。
补油不良---丝印漏油点,实施人工补油后的视觉效果差,补油局部形成积油或油墨厚度不均、或光泽度不同的现象。
光泽不均---油墨稀稠度不均匀;承印表面不平整造成着墨不均;胶刮有刮痕造成
印刷油墨不均匀。
字体变形---静电过大,造成承印物粘网;承印物表面起皱不平、网板变形。
墨膜龟裂---承印物表面受到其它化学溶剂的污染;油墨干燥温度过高;油墨配方中的溶剂与某种溶剂发生了化学反应。
表面异物---车间防尘控制不足;承印物静电吸附力过大。
飞墨拉丝---油墨研磨不匀,印刷时刮板离版慢,印刷图像周围的余白少,产生静电,导致油墨拉丝;丝印刮板力度过小;油墨浓度高。
表面折痕---作业人员操作方法不当;承印物来料表面折痕。
表面刮花---作业人员操作方法不当;承印物来料表面划痕或刮花。
基材变形---烘烤温度过高,导致承印物来料变形。
表面压痕---存储和转运方式不当,产品受压明显;产品堆放太多,存放时间过长,油墨没有干燥透。
洇(yin)墨---在印刷的线条外侧有油墨溢出并造成线条外侧边缘不整齐;油墨
稀,胶刮纯造成印刷时洇油。
滋墨---承印物图文部分和暗调部分出现斑点状的印迹;印刷速度和油墨干燥过
慢;墨层偏薄;受静电影响,油墨的触性变大;油墨中颜料分散不均。
表面污染---作业人员操作方法不当,导致产品表面指纹;产品表面清洁不足或
清洁方式不当;湿度太低与环境含尘度高。
露底色---压印力过大;网版目数偏高;胶刮刀口太过锋利;油墨流动性过大。
表面针孔---网版上吸附了灰尘或异物;制版时,水洗显影混入了溶胶;承印物
表面清洁不足。
基材色差---承印物来料颜色不一致。
漏丝印---丝印网版堵网;漏(少)丝印工序。
印倒(反)---丝印定位方向错误(印刷方向错误,印错面)。
漏油---丝印网版破裂(网板上有小破洞,网板拖浆);网板堵网。
重影---承印物受热胀冷缩的影响明显,导致丝印第二对位或套位不准。
漏光---丝印层偏薄;压印力过大;网版目数偏高;胶刮刀口太过锋利;油墨流动性过大。
气泡---承印物表面油污;来料油墨本身的气泡;刮印速度快,网距大,由于丝网弹离承印物太快而拉出气泡;油墨与溶剂混溶性差;油墨过期失效。
白点---承印物表面来料白点;网版漏油;丝印生产时飞油;油墨中的颜料有白色颗粒;印刷底色时堵网,盖白底后出现白点。
拖油---油墨未干,作业人员操作不当造成油墨层被破坏;油墨流动性过大;静电过大,造成承印物粘附在网版上。
黑点---承印物表面来料黑点;网版漏油;丝印生产时飞油;油墨中的颜料有黑色颗粒。
积油---网版漏油;油墨流动性过大造成飞油(线条变粗)。
网痕---油墨的流动性差,丝印过程中,当印版抬起后,转移到承印物上的油墨靠自身的流动填平网迹,使墨膜表面光滑平整,如果油墨流动性差,当丝网印刷抬起时,油墨流动性比较小,不能将丝网痕迹填平,就得不到表面光滑平整的墨膜;网纱纹路不均匀。
杂色点---承印物表面来料杂色点;网版漏油;丝印生产时飞油;油墨中的颜料有杂色颗粒。
断字---网版清洁不足,灰尘或异物堵网;油墨流动性差,造成堵网。
丝印层偏薄---压印力过大;网版目数偏高;胶刮刀口太过锋利;油墨流动性过大。
丝印层偏厚---网版目数偏小;胶刮刀口不够锋利;油墨流动性差。
字体粗细不均---油墨流动性过大;压印力大小不一致;网板张力不一致;
字体图案模糊---油墨流动性过大;压印力过大。
丝印内容错误---丝印内容与工程技术要求或客户要求不符;或丝印内容与客户提供的样板不一致;样板与菲林不符。
丝印位置错误---丝印位置与工程技术要求或客户要求不符;或丝印位置与客户提供的样板不一致;菲林排版有误。
着墨不均---印刷台面凹凸不平;刮板前端受损;调油不良导致油墨堵网。
线路氧化---作业人员操作未戴手指套,线路上留有手指印;存储环境温湿度过高;线路上的银油或碳油密封不好。
线路断线---丝印网版堵网;油墨浓度过大(流动性差)。
线路连线---丝印网版漏油;油墨流动性过大。
线路电阻偏高---线路上的银油丝印层偏薄;油墨浓度过稀;压印力度过大;刮板(胶刮)刀口太过锋利。
线路高压击穿---绝缘油绝缘性能差;绝缘油印刷位置堵网;绝缘油印刷层偏薄。
丝印件产品实验测试要求:
丝印层附着力测试。
丝印层耐磨测试。
丝印层膜厚测试。
丝印线路闭合电阻测试。
丝印线路绝缘阻抗测试。
丝印线路耐压测试。
丝印线路短路开路测试。
相关测试要求:
6.8.1参见《产品实验测试标准》进行。
6.8.2批量生产前,相关项目之测试必须列入首件产品确认过程。
6.8.3批量生产中,责任IPQC应于每一丝印机台、每一小时进行一次相关测试,每次测试数量至少不低于10pcs,确保生产工艺过程质量得到控制。
6.8.4。