金属成型油起泡的原因及解决方法
铝型材表面出现气泡的原因和解决办法

铝型材表面出现气泡的原因和解决办法铝型材挤压机进行加压的时候,会在铝型材里面残留空气,导致铝型材的内部和表面都出现气泡,产生不能彻底解决的缺陷,使得铝型材变成了废料。
为了避免空气进入铝型材中,一定要找出空气被带入的原因。
下面介绍的是四个挤压铝型材内部残留了空气的主要因素:一、长棒热剪导致空气的残留对于柱棒热剪切的时候形成的剪切面是绝对不会完美、垂直的。
工业铝型材简单的进行长棒热剪切会使得柱棒的弯曲非常严重,导致铝型材出现椭圆形的横截面以及被剪切一头非常巨大的倒圆角。
就算是最新型的长棒热剪,被剪切柱棒的边缘角度总是会产生倒圆,这些倒圆就是空气残留的最好地方。
解决方案:对铝棒进行标准检验,坚决杜绝不合格铝棒。
二、镦粗导致了空气的残留镦粗导致了空气的残留。
只有在盛装铝锭的筒直径比柱棒的直径大的时候,柱棒才能够被放入到盛装铝锭的筒里面。
对于盛装铝锭筒里面的柱棒施加压力导致柱棒扩大到盛锭筒直径之后,一定要排放出去所携带的气体。
气体没有排放出去,残留在铝锭里面最后就会变成气泡。
解决方案:根据挤压筒内衬尺寸的最小值来配置挤压垫片、定期更换挤压筒,对挤压筒、挤压垫蚀洗检查,测量挤压筒,挤压垫内、外径尺寸来配置合适的挤压垫片;每班用清理垫片清理挤压筒一次,定期对挤压筒进行蚀洗。
三、两根铝棒相接导致空气的残留由于两根铝棒相接而导致了空气的残留。
因为两根短柱棒的表层基本上是平的,携带进去空气的概率非常小。
锯切的品质直接干扰到两根短柱棒之间携带的空气数量。
目前具有一种高新技术能够防止两根短柱棒相接,进行消除空气进入的可能性。
解决方案:根据型材单重、出料支数等工艺参数确定合理的棒长的铝棒。
四、挤压铝型材导致空气的残留挤压铝型材的时候一定要避免空气的进入,以免出现空气残留的状况,使得后期处理中产生各种缺陷。
1.涂油不当造成制品气泡。
解决方案:使用正确的涂油方法并减少涂油用量;加强员工岗前的操作技术的培训;2.压余过薄,导致在剪切时把分流孔的金属拉出,使摸具分流孔内留有间隙。
金属化板板面起泡成因及对策探讨
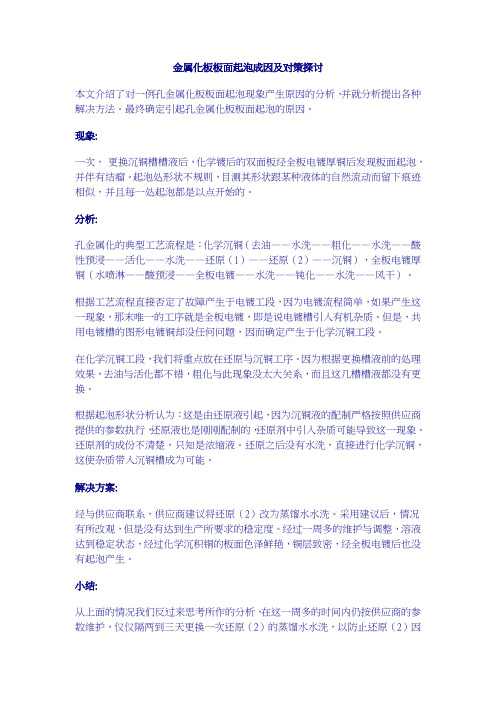
金属化板板面起泡成因及对策探讨本文介绍了对一例孔金属化板板面起泡现象产生原因的分析,并就分析提出各种解决方法。
最终确定引起孔金属化板板面起泡的原因。
现象:一次,更换沉铜槽槽液后,化学镀后的双面板经全板电镀厚铜后发现板面起泡,并伴有结瘤。
起泡处形状不规则,目测其形状跟某种液体的自然流动而留下痕迹相似,并且每一处起泡都是以点开始的。
分析:孔金属化的典型工艺流程是:化学沉铜(去油——水洗——粗化——水洗——酸性预浸——活化——水洗——还原(1)——还原(2)——沉铜),全板电镀厚铜(水喷淋——酸预浸——全板电镀——水洗——钝化——水洗——风干)。
根据工艺流程直接否定了故障产生于电镀工段,因为电镀流程简单,如果产生这一现象,那末唯一的工序就是全板电镀,即是说电镀槽引入有机杂质。
但是,共用电镀槽的图形电镀铜却没任何问题,因而确定产生于化学沉铜工段。
在化学沉铜工段,我们将重点放在还原与沉铜工序。
因为根据更换槽液前的处理效果,去油与活化都不错,粗化与此现象没太大关系,而且这几槽槽液都没有更换。
根据起泡形状分析认为:这是由还原液引起,因为沉铜液的配制严格按照供应商提供的参数执行,还原液也是刚刚配制的,还原剂中引入杂质可能导致这一现象。
还原剂的成份不清楚,只知是浓缩液。
还原之后没有水洗,直接进行化学沉铜,这使杂质带入沉铜槽成为可能。
解决方案:经与供应商联系,供应商建议将还原(2)改为蒸馏水水洗。
采用建议后,情况有所改观,但是没有达到生产所要求的稳定度。
经过一周多的维护与调整,溶液达到稳定状态,经过化学沉积铜的板面色泽鲜艳,铜层致密,经全板电镀后也没有起泡产生。
小结:从上面的情况我们反过来思考所作的分析,在这一周多的时间内仍按供应商的参数维护,仅仅隔两到三天更换一次还原(2)的蒸馏水水洗,以防止还原(2)因还原(1)的残留液的带入而使起浓度上升。
从这一情况看我们认为还原引入杂质的分析有误。
二次分析:既然否定杂质的引入的可能,那么原因何在呢?在控制过程中发现新配溶液的反应很快,起泡是否与活性有关呢?这引起我们的关注,但因为溶液已达到稳定状态,故障无从找起,槽液的更换周期较长,对于起泡的跟踪观察就停止。
铝合金压铸起泡改善方案

铝合金压铸起泡改善方案一、提高模具温度1. 提高模具表面温度适当地提高模具的温度,可以减少铝合金压铸起泡的现象。
通过提高模具的温度,可以使得铝合金材料更容易粘附在模具表面上,从而减少了气泡的形成。
2. 减少热应力铝合金压铸过程中产生的热应力也可能导致起泡。
因此,需要采取措施减少热应力。
比如,优化压铸工艺参数,控制压铸温度和压力等,以减少热应力的产生。
3. 降低料温波动铝合金材料的温度波动也可能导致起泡。
因此,需要控制铝合金材料的温度,减少波动。
可以采用恒温压铸的方法,即在铝合金材料中加入恒温剂,以控制温度波动。
二、优化压铸工艺1. 选择合适的压铸机器及材料选择合适的压铸机器和材料,可以减少铝合金压铸起泡的现象。
比如,选择符合工艺要求的压铸机器和材料,可以使得铝合金材料更容易粘附在模具表面上,从而减少了气泡的形成。
2. 优化压铸工艺参数优化压铸工艺参数,可以减少铝合金压铸起泡的现象。
比如,适当地调整压铸压力、压铸温度、压铸速度等参数,可以使得铝合金材料更容易粘附在模具表面上,从而减少了气泡的形成。
3. 调整压铸温度和压力等工艺参数在铝合金压铸过程中,合理地调整压铸温度和压力等工艺参数,可以减少起泡的现象。
比如,在保证铝合金材料充分凝固的前提下,适当地降低压铸温度和压力等参数,可以减少气泡的形成。
三、加强模具维护1. 定期检查模具磨损情况定期检查模具的磨损情况,可以及时发现模具表面粗糙或凹凸不平的问题。
这些问题会导致铝合金材料难以粘附在模具表面上,从而产生起泡现象。
因此,需要定期检查模具的磨损情况,并及时进行修复和保养。
2. 清洗模具定期清洗模具,可以保持模具表面的清洁度,从而减少铝合金压铸起泡的现象。
清洗模具时,需要使用合适的清洗剂和工具,彻底清除模具表面的污垢和杂质。
3. 涂抹润滑油脂在铝合金压铸过程中,涂抹适量的润滑油脂,可以减少铝合金材料与模具表面的摩擦,从而减少起泡现象的产生。
但是需要注意,涂抹的润滑油脂不能过多,否则可能影响铝合金材料的粘附性。
冷轧铝板带材轧制油起泡的原因及对策
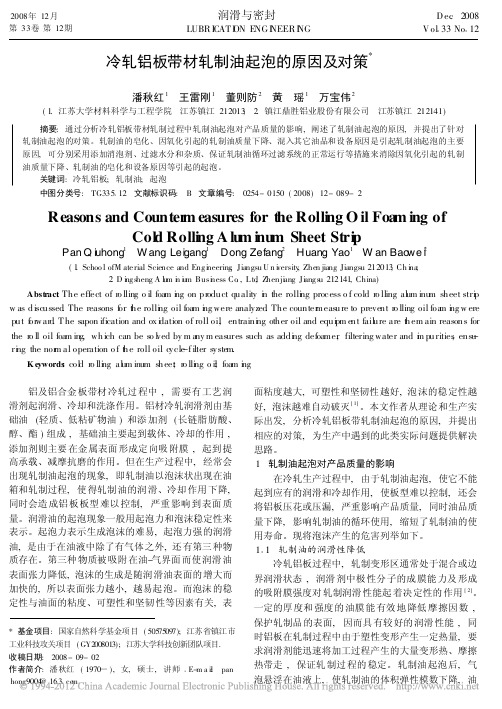
2008年12月第33卷第12期润滑与密封LUBR I CAT I ON ENG I NEER I NGD ec .2008V ol 133No 112*基金项目:国家自然科学基金项目(50575097);江苏省镇江市工业科技攻关项目(GY2008013);江苏大学科技创新团队项目.收稿日期:2008-09-02作者简介:潘秋红(1970)),女,硕士,讲师1E-m a i:l panhong9004@1631co m 1冷轧铝板带材轧制油起泡的原因及对策*潘秋红1 王雷刚1 董则防2 黄 瑶1 万宝伟2(1.江苏大学材料科学与工程学院 江苏镇江212013;2.镇江鼎胜铝业股份有限公司 江苏镇江212141)摘要:通过分析冷轧铝板带材轧制过程中轧制油起泡对产品质量的影响,阐述了轧制油起泡的原因,并提出了针对轧制油起泡的对策。
轧制油的皂化、因氧化引起的轧制油质量下降、混入其它油品和设备原因是引起轧制油起泡的主要原因,可分别采用添加消泡剂、过滤水分和杂质、保证轧制油循环过滤系统的正常运行等措施来消除因氧化引起的轧制油质量下降、轧制油的皂化和设备原因等引起的起泡。
关键词:冷轧铝板;轧制油;起泡中图分类号:TG335112 文献标识码:B 文章编号:0254-0150(2008)12-089-2Reasons and Counter m easures for t he Rolli ng O il Foa m ing ofCol d Rolli ng A lu m i nu m Sheet Stri pPan Q i u hong 1 W ang Lei g ang 1 Dong Zefang 2 Huang Yao 1 W an Bao we i2(1.School ofM aterial Science and Engi neering ,Jiangsu Un i versity ,Zhen jiang Jiangsu 212013,Ch i na ;2.D i ngs heng A l u m i n i u m Busi ness Co .,Ltd ,Zhenji ang Ji angs u 212141,China)Abstract :The effect of r o lling o il foa m i ng on pr oduct quality i n the rolli ng process o f cold r o lling al um inu m sheet stri pw as disc ussed .The reasons f or t he rolli ng oil foa m i ng were analyzed .The counter measure to preve nt r o lling oil foa m i ng w ereput f or war d .T he sapon ification and ox i dation of roll oi,l entraini ng other oil and equi pm e nt fail ure are t hem ain reasons for the r o ll oil foa m ing ,which can be so l ved by m a ny m easures such as addi ng defoa mer ,filtering water and m i purities ,ensu -ri ng the nor m al operation o f t he roll oil c ycle -f ilter syste m.K eywords :col d r o lli ng al um inum sheet ;r o lli ng o i;l foa m i ng铝及铝合金板带材冷轧过程中,需要有工艺润滑剂起润滑、冷却和洗涤作用。
金属件氧化锈蚀后喷漆起泡机理

金属件氧化锈蚀后喷漆起泡机理
金属件氧化锈蚀后喷漆起泡的机理主要涉及以下几个方面:
1. 金属表面含有锈迹:金属件经过氧化锈蚀后表面会形成铁锈,其中包含氧化铁等物质。
如果在喷漆前不彻底清除这些锈迹,铁锈会在喷漆过程中与涂料发生作用,从而引起起泡。
2. 铁锈溶解气体的释放:在喷漆过程中,涂料中的溶剂会与金属表面的铁锈发生化学反应,产生气体,如氢气等。
这些气体会在涂料膜中形成气泡,导致喷漆起泡。
3. 金属表面有油污或其他污染物:如果金属表面存在油污或其他污染物,这些物质会与涂料中的溶剂发生反应,产生气体,引起喷漆起泡。
4. 涂料与金属表面的相容性问题:不同的涂料与金属表面的相容性不同。
如果涂料与金属表面不相容,涂料会无法牢固地附着在金属表面上,从而形成气泡。
为避免喷漆起泡,可以采取以下措施:
1. 在喷漆前彻底清除金属表面的锈迹,可以通过砂纸磨砂或者酸洗等方法去除。
2. 确保金属表面干燥、干净,避免存在油污、水分或其他污染物。
3. 使用相容性良好的涂料,在喷漆前进行充分的涂料配套实验,以确定涂料与金属表面的相容性。
4. 控制涂料的喷涂厚度和施工方式,避免过多涂料积累在金属表面上,导致空气密封和气泡产生。
5. 注意喷漆工艺,避免喷涂时过度摇晃喷枪,引入空气或产生气泡。
总而言之,金属件氧化锈蚀后喷漆起泡是由于锈迹、溶解气体、污染物和涂料相容性等因素综合作用引起的。
为避免起泡,需要彻底清除锈迹,保持金属表面干净和干燥,选择相容性良好的涂料,并控制涂料施工厚度和方式。
冷轧铝板带材轧制油起泡

【9】马前, 刘白成, 王兆昌. Fe2C合金高温保温过程中碳化 物表面的研究[ J ]. 钢铁, 1994, 29 (5) : 47. 【10】马前, 王兆昌. 白口铁热处理对共晶碳化物的溶解与粒 状化的影响[ J ]. 钢铁研究学报, 1990, 2 (1) : 63. 【11】王树奇, 姜启川, 崔向红. 稀土对莱氏体钢共晶碳化物 粒化的影响[ J ]. 中国稀土学报, 1998, 16 (3) : 242 -246.
一.轧制油起泡对产品质量的影响 轧制油起泡对产品质量的影响
在冷轧生产过程中, 由于轧制油起泡, 使它不能起到应有的润滑 冷轧铝板带材轧制油起泡的原 和冷却作用, 使板型难以控制, 还会将铝板压花或压漏, 严重影响产 品质量, 同时油品质量下降, 影响轧制油的循环使用, 缩短了轧制油 因及对策 的使用寿命。现将泡沫产生的危害列举如下。 1.轧制油的润滑性降低 轧制油起泡后, 气泡悬浮在油液上, 使轧制油的体积弹性模数下 降, 油的动力粘度增高, 导致油膜强度降低, 润滑性能下降; 泡沫内 制作人:尤凤霞 混入的空气使轧制油的散热性降低, 使大量的热量滞留, 冷却性能 下降, 变形的热效应使轧制区温度升高, 从而相应会抑制油膜厚度, 使摩擦因数增大, 润滑性能降低。
结束语
对轧制油起泡的原因从理论和实践上进行了系统分析, 并提 出了解决此问题的对策, 可防止铝板带材在冷轧过程中由于轧制 , 油起泡而引起产品质量的波动, 使冷轧生产能够顺利进行。
参考文献 【1】邹先瑞. 润滑油起泡原因、危害和处理[ J ]. 山西机械,2001 (增刊) : 164 - 166. 【2】孙建林. 轧制工艺润滑原理技术与应用[M ]. 北京: 冶金工业出版社, 2004. 【3】袁驰, 刘友良, 孙建林, 等. 冷轧过程中轧制油对铝材表面质量的影 响[ J ]. 轻合金加工技术, 2005, 33 ( 11 ) :24 - 26. 【4】熊绍钧. 液压设备设计和使用中如何预防气泡油问题[ J ]. 液压与气 动, 1999 (2) : 3 【5】吕振林, 周永欣, 时惠英. 破碎机械上易磨损件的材质选择[ J ]. 机械 工程材料, 1997 (5) : 44 - 46. , 【6】李茂林. 我国金属耐磨材料的发展和应用[ J ]. 铸造, 2002 (9) : 525 - 529. 【7】宋绪丁, 蒋志强, 符寒光. 高硼铸钢的制备与应用[ J ]. 铸造技术, 2006, 27 (8) : 805 - 808. 【8】符寒光, 胡开华. 高硼铸造铁基耐磨合金及其热处理方法: 中国, CN1624180 [ P ]. 2004: 12 - 14.
金属蒙皮涂层起泡的原因分析及其控制

金属蒙皮涂层起泡的原因分析及其控制摘要随着涂料工业的发展,涂料的表观效果日益引起人们的关注,涂层气泡的原因是基材表面残存水、氧化物、可溶性盐等污物,使其局部附着不牢、引起水、水汽及腐蚀性物质等的渗透侵入,或涂层表面残留的水、空气、溶剂等在温度变化时膨胀起泡。
可以通过控制生产工艺,调整工艺配方,严格施工操作等手段加以控制。
关键词溶剂型涂料膨胀起泡腐蚀起泡1引言某架飞机出厂1年后机身金属蒙皮涂层出现局部气泡,导致飞机因表面涂层返厂排故。
涂层起泡问题,已不仅影响到涂膜的保护效果,而且也大大影响了涂膜的装饰效果。
涂层起泡现象一直贯穿于涂料生产、储存、施工以及使用的全过程,涉及的问题较多,本文就溶剂型涂料施工及使用中的气泡问题作一分析,提供几点控制方法,以解决涂层起泡的问题。
2气泡的特征及分类气泡是涂层表面出现的细小的肉眼可见的泡,它是不溶性气体在外力作用下进入固体(或液体)之中,并被固体(或液体)互相隔离的一个体系。
涂料中的气泡是气体在涂料液体中的分散形式,它是一种典型的热力学不稳定体系:气泡的存在增加了涂料体系的表面积,即增加了体系的能量:当气泡破灭后,体系的总表面积大大减少,于是能量也相应降低。
所以,存在气泡的涂料体系始终处于热力学的不稳定状态中。
在涂料生产过程中,气泡作为干扰因素出现,使涂料产品在应用时产生表面缺陷,既有损外观,世会影响涂膜的防腐性和耐候性。
气泡通常是涂膜附着力不足的体现,对于防腐涂料而言,它往往是其防腐能力不足的最先外观表征。
气泡有大小,泡内可以含液体、蒸汽、其它气体或结晶物,泡的尺寸多依赖于涂料对基材表面的附着力保持平衡而将涂膜拉伸反向顶起的程度。
按其形态,气泡可以分为泡和泡沫两种。
泡是指气泡会很快上升到液面,形成以少量液体构成的依靠液膜隔开的气泡密集体。
水性涂料起泡多为此类。
3 气泡产生的原因气泡通常是伴随涂层老化过程产生的,从此意义上说,气泡可以分为膨胀气泡和腐蚀气泡两种。
金属加工液消泡剂

金属加工液消泡剂金属加工液起泡的原因和影响(1)水质偏软,度软化的水和含碱的水会增加乳化液的泡沫;(2)流体循环泵密封不严也会增大液体的泡沫。
(3)金属加工液的流速太快,气泡没有时间溢出,越积越多,导致大量泡沫产生;(4)金属加工液液槽容积过小,导致金属加工液静置时间不足。
选择金属加工液消泡剂·还在为以下问题烦恼吗①消泡剂使用过后会影响切削液原有的性能,耐高温,高剪切,防锈,润滑,冷却等等性能。
②消泡剂使用过后会有反效果,担心会有析出(像鼻涕一样液体析出),漂油,破乳等等现象。
③消泡剂使用后的相容性不好,影响产品的透明度。
金属加工液消泡剂介绍金属加工液消泡剂是高效浓缩液,使用时加20倍水冲稀,特种复合型加工液消泡剂直接加入稀溶液能达到良好的消泡性,但使用不方便,应当把它添加到浓缩液中。
此复合消泡剂最好在加工液配制过程中加入,加入量<I%。
分两步加入,第一步在加工液合成中期加入,可使消泡剂与原液反应,抑制反应过程中的泡沫,第二步在反应后期加入。
分阶段加入消泡剂能更好地发挥其效能,同时也能减少加入量。
金属加工液消泡剂特点消泡、抑泡力强,用量少,不影响起泡体系的基本性质。
耐热性好,化学性稳定,适用于多个领域。
具有较好的耐高温性、耐酸碱性、不漂浮、不漂油。
其性能可与进口产品相媲美,而价格更具明显之优势。
金属加工液消泡剂应用金属加工液消泡剂适用于:金属加工、金属加工液、半合成金属加工液、切割液、电解液切割液、切割机、润滑油、全合成润滑油、半合成润滑油、乳化油、乳化液、皂化油、液压液、冲压油、拉丝油、铜拉丝油、拉丝液、淬火液等产品中消泡。
金属加工液消泡剂使用和储存添加:根据不同使用体系,消泡剂的添加量可为0.05%—0.3%,添加量根据具体情况试验决定;包装:本品采用25/50/60/200/1000KG塑料桶装;贮存:密封存放于室内阴凉、通风、干燥处。
未使用完前,使用后容器应严格密封。
25℃左右保质期12个月运输:本品运输中要密封好,防潮、防强碱强酸及防雨水等杂质混入。
解决油起沫的小窍门

解决油起沫的小窍门
1、把油坐到火上,边加热边搅,防止溢出,要有人看,直到油起烟无泡为止,然后就又能用了,以后用的时候先将油烧至冒轻烟,然后再炸就不会有这种现象。
2、油品:有的油起沫重是因为成分复杂,豆油、花生油起沫的情况比较多。
特别是毛油、二级油等含磷脂较高的油脂,遇高温时易起泡沫而影响正常使用。
3、油温:油温长时间停在低温区也容易起沫,等油热后再下锅。
4、油多次使用:油的使用次数也会影响,多次使用的油炸东西的时候会出好多的沫,油很脏,使用过的油里面有很多杂质。
压铸件气泡产生的原因和解决办法

压铸件气泡产生的原因和解决办法锌合金压铸件表面经常出现大小不等的气泡,请问原因是什么,该如何解决?解决压铸件气孔的办法:先分析出是什么原因导致的气孔,再来取相应的措施。
(1)干燥、干净的合金料。
(2)控制熔炼温度,避免过热,进行除气处理。
(3)合理选择压铸工艺参数,特别是压射速度。
调整高速切换起点。
(4)顺序填充有利于型腔气体排出,直浇道和横浇道有足够的长度(>50mm),以利于合金液平稳流动和气体有机会排出。
可改变浇口厚度、浇口方向、在形成气孔的位置设置溢流槽、排气槽。
溢流品截面积总和不能小于内浇口截面积总和的60%,否则排渣效果差。
(5)选择性能好的涂料及控制喷涂量。
-------------------压铸件气孔分析-------------------压铸件缺陷中,出现最多的是气孔:气孔特征:有光滑的表面,表现形式可以在铸件表面、或皮下针孔、也可能在铸件内部。
(铸件壁内气孔)一般呈圆形或椭圆形,具有光滑的表面,一般是发亮的氧化皮,有时呈油黄色。
(表面气孔)气泡可通过喷砂发现,内部气孔气泡可通过X光透视或机械加工发现气孔气泡在X光底片上呈黑色.<<A>>气体来源(1)合金液析出气体—a与原材料有关 b与熔炼工艺有关(2)压铸过程中卷入气体?—a与压铸工艺参数有关 b与模具结构有关(3)脱模剂分解产生气体?—a与涂料本身特性有关 b与喷涂工艺有关<<B>>原材料及熔炼过程产生气体分析铝液中的气体主要是氢,约占了气体总量的85%。
熔炼温度越高,氢在铝液中溶解度越高,但在固态铝中溶解度非常低,因此在凝固过程中,氢析出形成气孔。
氢的来源:(1)大气中水蒸气,金属液从潮湿空气中吸氢。
(2)原材料本身含氢量,合金锭表面潮湿,回炉料脏,油污。
(3)工具、熔剂潮湿。
<<C>>压铸过程产生气体分析由于压室、浇注系统、型腔均与大气相通,而金属液是以高压、高速充填,如果不能实现有序、平稳的流动状态,金属液产生涡流,会把气体卷进去。
7招教你如何应对铸件气泡问题

7招教你如何应对铸件气泡问题气泡可以说是咱们压铸行业中铸件最常见问题之一,而且一旦铸件出现了气泡问题,也等于产品报废了。
为了避免气泡的产生,小编将详细的为您剖析铸件气泡~~教您7招解决铸件气泡问题【缺陷现象】铸件表皮下,聚集气体鼓胀所形成的泡,有时会崩裂,存在贯通和非贯通两种。
别名:鼓泡、起泡【原因分析】•模具温度太高,开模过早。
•填充速度太高,金属流卷入气体过多。
•涂料发气量大,用量过多,浇注前未燃尽,使挥发气体被包在铸件表层,另涂料含水量大。
•型腔内气体没有排出,排气不顺。
•合金熔炼温度过高。
•铝合金液体除气不彻底,吸有较多气体,铸件凝固时析出留在铸件内•填充时产生紊流。
【对应措施】1、测温枪测试模具表面温度,显示数值超过工艺规定范围。
降低模具表面温度,增加保压时间;2、铸件表面内浇口压入的金属流明显比其它部位亮很多。
填充速度高产生原因一方面是设备本身的压射速度高,另一方面可能是内浇口太薄造成。
降低压射速度,适当增加内浇口厚度;判断内浇口薄的方法:是否有浇口易粘现象,降低二快速度看远端是否有严重压不实现象,不给压打件,看是否有多股铝液流;3、喷涂时察看雾的颜色是否呈白色,合模前察看型腔是否还有气体残留。
更换涂料或增大涂料与水的配比;4、在烫模阶段,铸件表面有明显的漩涡和涂料堆积。
判断及解决方法:调开档,人为产生涨模,如果解决,需开排气道;5、铸件表面内浇口压入的金属流特别亮并伴有粘结。
适当降低浇注温度;6、取样块测密度,看是否符合要求。
重新进行除气处理或在保温炉内进行再次精炼;7、烫模阶段铸件表面明显有各流溶接不到一起的痕迹伴有涂料堆积。
判断及解决方法:涂黑油生产,看痕迹是否有堆积,分析堆积部位,解决方法:•a、开设或加大相应部位的集渣包,•b、调整内浇口流向、位置或填充方向。
————————。
金属成型油起泡的原因及解决方法

"泡"是指被固体或液体薄膜包围的气体,当气泡之间被几个厚度的液膜隔开的时候即聚集为泡沫。
泡沫在生活和工业生产过程中经常可见。
一、金属成型油起泡的原因:(1)成型油的抗泡性能不合格。
成型油一般添加了一些表面活性剂类添加剂,当没有添加任何抗泡剂,在受震荡和揽拌等作用时,极易造成涧滑油起泡。
(2)油品黏度不合适。
黏度过大或过小也会导致成型油起泡,应根据不同应用场合和负荷选择不同类型和黏度等级的金属成型油(3)吸油管漏气。
油泵前一段吸油管接头密封不严漏气或油累阀件漏气,会直接导致产生气泡。
(4)回油管的安装位置不合理。
由于回油管安装位置不妥,导致回油管中的金属成型油冲击油面,造成很大的震荡和波动而使油品起泡。
(5)新油使用过程中被污染。
由于油箱进入水分,机械杂质和固体润滑剂等其它物质导致油品乳化和品质恶化而起泡,所以应定期清理油箱内的油泥。
(6)混油。
不同牌号或不同厂家的金属成型油混合使用也会是导致金属成型油起泡的原因之一,所以应避免混油。
换用其他牌号金属成型油前应清洗油箱和输油管路的旧油。
(7) 滤油网不畅通。
若油粟入口粗滤器部分吸油孔被杂质堵死,会因局部真空生成气泡。
(8)抗泡剂失活。
由于抗泡剂被逐步增溶或消耗,导致抑泡和消泡能力减弱。
二、金属成型油起泡产生的危害:(1)涧滑油散热性能变差当油箱表面集中分布着大量的泡沫,泡沫膜形成一道厢热层使油箱内金属成型油散热性能变差,冷却能力降低,最终导致油温升高。
(2)金属成型油氧化变质加剧油箱表面或油箱内产生气泡后,油品与空气的接触面积增大,再加上油温的升高,因此会加剧基础油巧添加剂的氧化变质,导致油箱底部油泥大量齡积。
(3)涧滑油润滑性能降低油品起泡会使金属成型油润滑性能降低,加剧机件的磨损和烧结,减少机械使用寿命。
(4)机件磨损加剧,噪声增加由于泡沫具有可压缩性,当含气泡的金属成型油经油累输送进入液压缸,活塞推动会产生抖动,增加噪声;另外由于润滑性降低导致机械摩擦加剧,也会导致噪声増大。
涂料对金属型铸件表面气泡的影响

涂料对金属型铸件表面气泡的影响摘要:涂料对金属型铸件质量影响很重要,不当的涂料及不正确的使用,会使铸件产生缺陷甚至报废。
某厂金属型铸件易形成表面气泡,通过改进的涂料及涂覆工艺,改善了铸件成型条件,防止了表面气泡的产生,提高铸件表面质量。
关键词:涂料金属型铸造表面气泡某厂后桥套毛坯的外观质量不甚理想,特别是易形成表面气泡,光洁度差,影响了成品的整体外观效果。
后桥套是铝硅合金,使用金属型铸造,原来生产所用涂料为铑粉、氧化锌及水玻璃和适量水,大致配比:氧化锌60%+水玻璃40%+适量水,但不能很好地满足需要,经过分析和试验,改进了涂料配比及涂覆工艺,取得了较好的效果。
1 金属型铸造中涂料的功用金属型铸造在铝合金铸造中运用广泛,其生产率高,铸件尺寸公差小,经济性高,但金属型工作环境恶劣,寿命较短,铸件易产生气泡气孔裂纹等缺陷,常在铸型表面涂覆一层涂料,缓解金属型热疲劳破坏。
涂料层防止金属液与金属型发生粘膜,减少铸型对金属液的激冷作用,合适的涂料配比及涂覆工艺,发气量小,涂层干燥后形成的小空隙有一定的蓄气和排气能力,防止铸件产生缺陷。
2 金属型涂料的组成及施涂工艺国内外很多学者对涂料进行大量的研究开发,铝合金铸件金属型铸造涂料的研究更是不胜枚举,涂料一般由粉状耐火材料、粘结剂、载体和其它附加物组成。
粉状耐火材料一般具有较好的绝热性能,不同合金铸件,所用的耐火材料也不同。
铝、镁合金,常用氧化锌、氧化钛、氧化镁、白垩粉等;铜合金及铸铁可用石墨粉;铸铁及铸钢常用石英粉、粘土及刚玉粉等。
粘结剂通常采用水玻璃,铸钢常用糖浆、纸浆废液等。
载体作用是使涂料各组成物能均匀混为一体,并有良好的涂刷性能,一般用水或醇类。
附加物赋与涂料具有特殊性能的物质。
如石棉粉、硅藻土能有效地提高涂料的绝热性;石墨粉、滑石粉可使涂料有较好的润滑性[1]。
生产铝合金铸件的金属型涂料的制备方法有搅拌法和研磨法,涂覆工艺有低压热空气喷涂法、高压无气喷涂法等。
锌合金压铸件起泡原因分析及解决方案

锌合金压铸件目前广泛用于各种装饰方面,如家具配件、建筑装饰、卫浴配件、灯饰零件、玩具、领带夹、皮带扣、各种金属饰扣等,因此对压铸件表面质量要求较高,同时要求有良好的表面处理性能。
而锌合金压铸件最常见的缺陷就是表面起泡。
一直以来锌合金压铸件的一个重大而且常发性缺陷(起泡)困扰着诸多的压铸从业者和压铸加工企业。
同时也致使大到原料供应商和压铸企业及抛光和电镀企业,小到公司部门之间的扯皮现象时有发生。
锌合金压铸件目前广泛用于各种装饰方面,如家具配件、建筑装饰、卫浴配件、灯饰零件、玩具、领带夹、皮带扣、各种金属饰扣等,因此对压铸件表面质量要求较高,同时要求有良好的表面处理性能。
而锌合金压铸件最常见的缺陷就是表面起泡。
一、缺陷表征:压铸件表面有突起的小泡,压铸出来就发现、抛光或加工后显露出来、喷油或电镀后出现。
二、产生原因:1、孔洞引起:主要是气孔和收缩机制,气孔往往是圆形,而收缩多数是不规则形。
(1)气孔产生的原因:A、金属液在充型、凝固过程中,由于气体侵入,导致铸件表面或内部产生孔洞。
B、涂料挥发出来的气体侵入。
C、合金液含气量过高,凝固时析出。
当型腔中的气体、涂料挥发出来的气体、合金凝固析出的气体,在模具排罐子不良时,最终留在铸件中形成的气孔。
(2)缩孔产生的原因:A、金属液凝固过程中,由于积体缩小或最后凝固部位得不到金属液补缩,而产生缩孔。
B、厚薄不均的铸件或铸件局部过热,造成某部位凝固过慢,体积收缩时表面形成凹位。
由于气孔和缩孔的存在,使铸件在进行表面处理时,孔洞可能会进水,当喷漆和电镀后时宜行烘烤时,孔洞内气体受热膨胀或孔洞内水会变蒸气,体积膨胀,因而导致铸件表面起泡。
2、晶间腐蚀引起:锌合金成分中有害杂质:铅、镉、锡会聚集在晶粒交界处导致晶间腐蚀,金属基体因晶间腐蚀而破碎,而电镀加速了这一祸害,受晶间腐蚀的部位会膨胀而将镀层顶起,造成铸件表面起泡。
特别是在潮湿的环境下晶间腐蚀会使铸件变形、开裂、甚至破碎。
喷射成形7055铝合金试样表面起泡原因分析

喷射成形7055铝合金试样表面起泡原因分析凌阿斌;万蕾;李晶;朱小溪;孙书;杨耀东【摘要】喷射成形7055铝合金拉伸试验件在进行固溶处理的过程中,不同批次的试验件表面均出现了不同程度的起泡现象.通过对起泡试样表面、截面以及拉伸断口起泡区域处进行宏微观观察,以及对起泡试样进行拉伸性能检测、H含量测试以及金相组织分析,结果表明,7055铝合金在进行固溶热处理后表面发生起泡现象是由于热处理炉内湿度过大,发生高温氧化反应所致.建议对已发生起泡的拉伸试验件,采用机械加工的方法消除起泡.【期刊名称】《失效分析与预防》【年(卷),期】2018(013)004【总页数】4页(P243-246)【关键词】喷射成形;7055铝合金;表面起泡;高温氧化【作者】凌阿斌;万蕾;李晶;朱小溪;孙书;杨耀东【作者单位】北京卫星制造厂, 北京100094;北京卫星制造厂, 北京100094;北京卫星制造厂, 北京100094;北京卫星制造厂, 北京100094;北京卫星制造厂, 北京100094;北京卫星制造厂, 北京100094【正文语种】中文【中图分类】TH142.30 引言喷射成形技术是一种在传统快速凝固/粉末冶金(RS/PM)传统工艺基础上发展起来的,直接制备金属材料坯件或半成品的先进制备技术[1-2],其制备的材料具有晶粒细小、组织均匀、氧化少、偏析程度小等优点,广泛应用于制备各种先进材料以及传统材料[3]。
7055铝合金属于Al-Zn-Mg-Cu系超高强铝合金,最先是由美国开发并申请专利的超高锌含量的新型铝合金,具有强度更高、韧性更好、抗应力腐蚀性能更优的特点,广泛应用于航天航空、交通运输及民用工业等领域[4-5]。
表面起泡虽是铝合金热处理后常见缺陷之一,且起泡的外形通常极其相似,但是引起起泡的原因和机理却不相同。
崔景博等[6]对7A04铝合金表面产生起泡的机理、原因、现象进行了详细的研究和分析;安景如[7]对铝合金铸锭均匀化退火表面起泡的原因进行了分析。
金属加工液的泡沫问题

TRIM 是马斯达化学集团的注册商标© 2010 马斯达化学集团 修订10-05-2010由于使用条件不在我们的控制范围之内,因此对该产品的使用情况我们不能完全提供保证和承诺。
在金属加工液中, 泡沫真是一个头痛问题.为了使加工液发挥正常功能, 必须控制泡沫。
泡沫引起下述问题:1. 泡沫不能使润滑功能正常发挥.2. 在很多场合,泡沫象一层隔热层,不能使冷却功能很好的起作用。
3.泡沫使液体体积显著膨胀.4. 泡沫使铁屑和微粒悬浮,影响过滤时对微粒的处理能力.5.泡沫使化学品的气味更易挥发,更易形成气雾 .6. 泡沫吸入进泵中和机床管路,将造成极大危害. 泡沫因下述条件产生。
1.液体被搅动或流动..2.液体中一定含有表面活性剂或乳化剂.3.流动的液体一定暴露在空气中,4.并包裹了一些气体.如果可能,工程技术人员消除上述一些因素,控制泡沫将变得容易些。
所以在应急式的添加消泡剂之前,要努力从机械上提出彻底的解决方案. 在枪钻和喷吸钻的应用中,通常要求高的冷却速度,高压,高流量, 有利于断屑,把铁屑迅速冲离切削部位.现在,适合高压,高流速,高流量的冷却液已经被开发出来,可用于车床和加工中心. 这种冷却液经过优化设计,可以抗泡沫和空气混入,使你能充分发挥机床和所配有的高压冷却系统的能力.金属加工液的泡沫问题有一些典型的例子显示机械原因,导致了加工液的泡沫问题,从设备上着手,发现解决方案是恰当的.1.阀的密封松了,导致漏入空气.2.泵的轴密封松了, 导致漏入空气3,在管路,旋转连接或其它连接处,出现泄漏, 导致漏入空气. 4,软管上的针孔.5. 旁路阀过于靠近,在系统中产生极大的背压.6.超过工作需求的大功率泵,在系统中形成了搅拌的作用.7.儲液箱过于浅,或泵放置的过高,导致泵吸入空气. 8.加工液的泵反向旋转. 9. 过度的喷射在液槽的液面形成冲击.从加工液方面考虑,有一些因素可能导致泡沫问题.1.选择的冷却液和使用浓度是否合适.2.机床漏油的污染.3.清洗液或洗地板的皂液污染.4.水质及其与冷却液混合是否恰当.5.错误使用或超量使用消泡剂.6.从其它工序带来问题,例如拉延或脱模剂粘在零件表面.如果你需要帮助,以解决泡沫问题,联系马思特地区经理或当地马思特代理商,以帮助你选择低泡冷却液产品或适合您应用场合的削泡剂产品.对于消泡请记住,添加的消泡剂,最终均会被带出系统,因此,要控制泡沫,需要不断的,阶段性添加消泡剂.但当冷却液使用时间增长,被杂油污染,冷却液的起泡趋势减弱。
铝合金喷油烘烤后表面起泡预防措施

铝合金喷油烘烤后表面起泡预防措施在铝合金喷油过程中,表面起泡是一个常见的问题。
这可能会对工件的外观和性能产生负面影响。
本文将介绍一些预防措施,以帮助您避免铝合金喷油烘烤后表面起泡的问题。
1. 确保铝合金工件表面清洁在喷油前,确保铝合金工件表面无油污、灰尘等杂质。
这些杂质可能会导致油漆附着力下降,从而引起表面起泡。
在进行喷油前,应使用清洁剂和水彻底清洗工件表面,确保其完全清洁。
2. 喷油前进行磷化处理在进行喷油前,对铝合金工件进行磷化处理可以提高油漆附着力。
磷化处理是一种化学处理方法,通过在工件表面形成一层磷化膜,使油漆更好地附着在工件表面。
选择适当的磷化液或涂层防腐涂料,可以提高工件表面的耐腐蚀性和耐磨性。
3. 烘烤温度控制在100℃以下在烘烤过程中,避免高温引起油泡。
在烘烤时,应将温度控制在100℃以下。
适当延长烘烤时间,但不要过度加热。
建议使用恒温设备来控制烘烤温度,避免温度波动过大。
4. 油漆调配时加入适量的消泡剂在油漆调配过程中,加入适量的消泡剂可以减少泡沫的产生。
消泡剂可以帮助消除泡沫,提高油漆的稳定性。
在添加消泡剂时,应根据油漆的种类和厚度进行适量添加,避免过量使用。
5. 喷油时注意气压,避免油漆过量或不足在喷油时,注意气压,避免油漆过量或不足。
气压过大或过小都可能导致油漆喷涂不均匀,从而引起表面起泡。
适当调整喷嘴孔径大小,保持气压适当,确保油漆均匀喷涂。
6. 烘烤时间根据油漆种类和厚度适当控制不同的油漆种类和厚度需要不同的烘烤时间。
在喷油前,应根据油漆的种类和厚度选择适当的烘烤时间。
烘烤时间过长或过短都可能导致表面起泡。
建议事先进行实验,确定合适的烘烤时间和温度。
7. 定期检查烘烤设备,确保正常运行,避免温度不均匀最后,定期检查烘烤设备,确保其正常运行,避免温度不均匀。
温度不均匀可能导致局部过热或局部过冷,从而导致表面起泡。
定期检查烘烤设备的温度控制系统和加热元件,确保其正常工作,避免出现温度不均匀的情况。
以金属表面产生气泡的快慢为标准
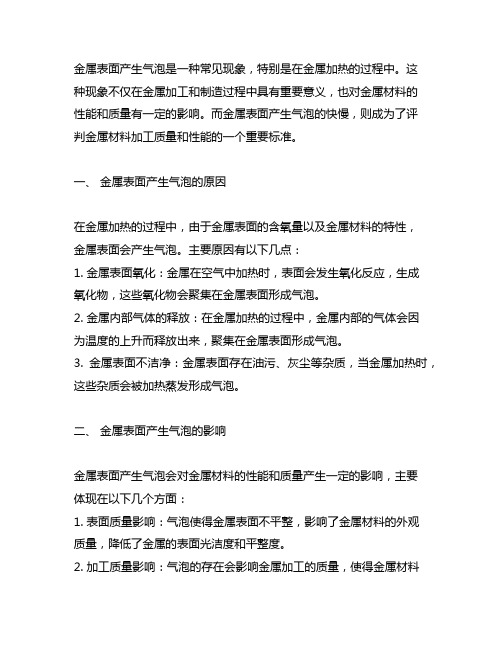
金属表面产生气泡是一种常见现象,特别是在金属加热的过程中。
这种现象不仅在金属加工和制造过程中具有重要意义,也对金属材料的性能和质量有一定的影响。
而金属表面产生气泡的快慢,则成为了评判金属材料加工质量和性能的一个重要标准。
一、金属表面产生气泡的原因在金属加热的过程中,由于金属表面的含氧量以及金属材料的特性,金属表面会产生气泡。
主要原因有以下几点:1. 金属表面氧化:金属在空气中加热时,表面会发生氧化反应,生成氧化物,这些氧化物会聚集在金属表面形成气泡。
2. 金属内部气体的释放:在金属加热的过程中,金属内部的气体会因为温度的上升而释放出来,聚集在金属表面形成气泡。
3. 金属表面不洁净:金属表面存在油污、灰尘等杂质,当金属加热时,这些杂质会被加热蒸发形成气泡。
二、金属表面产生气泡的影响金属表面产生气泡会对金属材料的性能和质量产生一定的影响,主要体现在以下几个方面:1. 表面质量影响:气泡使得金属表面不平整,影响了金属材料的外观质量,降低了金属的表面光洁度和平整度。
2. 加工质量影响:气泡的存在会影响金属加工的质量,使得金属材料在加工时易产生裂纹、气孔等缺陷。
3. 材料性能影响:气泡会对金属材料的强度、韧性、耐腐蚀性等性能产生影响,降低了金属材料的整体性能。
三、控制金属表面产生气泡的方法为了提高金属材料的质量和性能,需要采取一定的控制措施来减少金属表面产生气泡的情况,主要包括以下几种方法:1. 金属表面清洁:在金属加工或制造过程中,要保持金属表面的清洁,避免油污、灰尘等杂质的存在,减少气泡的生成。
2. 控制加热温度:合理控制金属的加热温度,避免金属表面氧化反应的发生,减少氧化物的聚集。
3. 采用保护气体:在金属加热的过程中,可以采用保护气体(如氮气、氩气)来覆盖金属表面,防止氧化反应的发生,减少气泡的产生。
4. 金属表面处理:采用化学处理或物理处理的方法,对金属表面进行改性处理,减少气泡的产生。
四、金属表面产生气泡的检测方法为了确保金属加工制造的质量和性能,需要采取一定的检测方法来检测金属表面是否产生气泡,以便及时发现问题并进行处理。
- 1、下载文档前请自行甄别文档内容的完整性,平台不提供额外的编辑、内容补充、找答案等附加服务。
- 2、"仅部分预览"的文档,不可在线预览部分如存在完整性等问题,可反馈申请退款(可完整预览的文档不适用该条件!)。
- 3、如文档侵犯您的权益,请联系客服反馈,我们会尽快为您处理(人工客服工作时间:9:00-18:30)。
"泡"是指被固体或液体薄膜包围的气体,当气泡之间被几个厚度的液膜隔开的时候即聚集为泡沫。
泡沫在生活和工业生产过程中经常可见。
一、金属成型油起泡的原因:
(1)成型油的抗泡性能不合格。
成型油一般添加了一些表面活性剂类添加剂,当没有添加任何抗泡剂,在受震荡和揽拌等作用时,极易造成涧滑油起泡。
(2)油品黏度不合适。
黏度过大或过小也会导致成型油起泡,应根据不同应用场合和负荷选择不同类型和黏度等级的金属成型油
(3)吸油管漏气。
油泵前一段吸油管接头密封不严漏气或油累阀件漏气,会直接导致产生气泡。
(4)回油管的安装位置不合理。
由于回油管安装位置不妥,导致回油管中的金属成型油冲击油面,造成很大的震荡和波动而使油品起泡。
(5)新油使用过程中被污染。
由于油箱进入水分,机械杂质和固体润滑剂等其它物质导致油品乳化
和品质恶化而起泡,所以应定期清理油箱内的油泥。
(6)混油。
不同牌号或不同厂家的金属成型油混合使用也会是导致金属成型油起泡的原因之一,所以应避免混油。
换用其他牌号金属成型油前应清洗油箱和输油管路的旧油。
(7) 滤油网不畅通。
若油粟入口粗滤器部分吸油孔被杂质堵死,会因局部真空生成气泡。
(8)抗泡剂失活。
由于抗泡剂被逐步增溶或消耗,导致抑泡和消泡能力减弱。
二、金属成型油起泡产生的危害:
(1)涧滑油散热性能变差
当油箱表面集中分布着大量的泡沫,泡沫膜形成一道厢热层使油箱内金属成型油散热性能变差,冷却能力降低,最终导致油温升高。
(2)金属成型油氧化变质加剧
油箱表面或油箱内产生气泡后,油品与空气的接触面积增大,再加上油温的升高,因此会加剧基础油巧添加剂的氧化变质,导致油箱底部油泥大量齡积。
(3)涧滑油润滑性能降低
油品起泡会使金属成型油润滑性能降低,加剧机件的磨损和烧结,减少机械使用寿命。
(4)机件磨损加剧,噪声增加
由于泡沫具有可压缩性,当含气泡的金属成型油经油累输送进入液压缸,活塞推动会产生抖动,增加噪声;另外由于润滑性降低导致机械摩擦加剧,也会导致噪声増大。
(5)影响液力传动系统
大量的泡沫会影响压力的传递和动力的传递,对液力传动机车来说会引起液力传动
(6)油箱内金属成型油溢出
如果油箱内产生大量气泡,不能及时消除。
则会使油的体积增大,
甚至溢出油箱,或使液面高度指示器指示出假油面髙度,不能及时发
(7)缩短换油周期,造成能源浪费
油品起泡会加剧油品的品质下降,涧滑性能变差,引起设备的噪声増大等
综上所述,机械设备的涧滑油箱产生气泡的危害巨大,为解决这些不利的因素需及时补加新油或更换高性能金属成型油。
可选用联诺化工MPS02A成型油。
MPS02A成型油以精制矿物油为基础,复配入极压、油性及防锈等多种特殊添加剂调配而成,具有良好的润滑性、极压抗磨性、防锈性及高温抗氧化安全性等。
能有效地保护模具,满足标准件及非标准件的多工位成型加工工艺。
MPS02A成型加工油优点
●具有良好的润滑性、极压抗磨性、消泡性,优秀的防锈性及高温抗氧化安定性;
●有效保护冲棒(冲针)及模具,延长使用寿命,降低综合成本;高耐温性能好,不易产生油泥,对抵挡磷化处理的线材也有很好的清净沉降性;
●低气味、低烟雾,保护操作环境。
应用介绍
●用于碳钢冷镦,高强度螺栓、套筒、空心及半空心铆钉等的成型加工,也可用于铝铆钉的成型加工。
MPS02A成型油适合所有碳钢冷镦成型加工。
●MPS02为通用型产品;
●MPS02A为加强型产品,适用于加长深度套筒(管)、盲孔螺帽和其它一些难加工非标准的润滑,对模具和冲棒起到最佳保护。
使用说明
●MPS02A分中等黏度(80)和高黏度(120)两种黏度等级;
●Pb值:显示油品润滑性能,Pd值显示油品高温高压下的极压性能,普通润滑剂Pb值280,Pd值1200;
●Pb、Pd值越高显示油品润滑性能越好。
如今,工业4.0时代的加工所需要成型油提出了更高的技术要求。
金属成型油发展到今天,是所有金属加工油当中利润最低的一款,已经不在适合于长途贩卖,各地成型油调和厂都在想方设法攻克技术难题,以期望打破台进口油品的垄断局面,在市场总需求量中分得一杯羹。
因此,金属成型油厂家应更注重产品品质,要想成为行业中的第一,必须要经过千锤百炼,不断提升自己,最终才能练就成“金钟罩铁布衫”。