压入式曲轴皮带轮总成装配工艺
曲轴减震皮带轮粘附工艺的实验分析与实践

指 标 , 征 了 曲 轴 减 震 皮 带 轮 在 发 动 机 运 表 矩 , 征 曲 轴 减 震 皮 带 轮 在 发 动 机 运 行 过 表 程 中, 带轮抗曲轴角加速度冲击的能力。 皮
s m p e t uc u e a d o i l s r t r n l w c s . le d m p r c a ks f i m a e p f e r i a d h b. o t Pu l y a e r n ha t s d u o g a r ng n u And ub e i ma i g h d mp n e f c r b r s k n t e a i g f e t
1 图 2 、 。
_
2轮 毂和齿环 的连接 强度的实验验证 方案
对 于 曲 轴 减 震 皮 带 轮 而 言 , 估 轮 毂 评
图 1 压 入式 涂 胶工 艺 图 3 轴 向压 脱 实验 示意 图
l髓 _
图 2 硫 化 注入 式涂 胶 工 艺
图 4 滑 移扭 矩测 试 实验 示 意 图
科技资讯 S IN E & T C N L G N O MA I N CE C E H O O Y IF R TO
工 业 技 术
与 齿 环 连 接 强 度 , 要 从 轴 向 压 脱 和 滑 动 轮 的 轮 毂 和 齿 环 分 离 , 时 记 录 压 脱 力与 胶 , 毂 不 涂 胶 , 环 只 涂 底 胶 , 环 只 涂 需 同 轮 齿 齿 扭 矩 两 部 分 来 进 行 评 估 。 于 轴 向 压 脱 力 位 移 的 关 系 。 对 面 胶 和 齿 环 不 涂 胶 六 种 情 况 对 于 最 终 黏 合
工 业 技 术
SIC &T H0OY CNE E NLG E C
发动机主要总成件的装配工艺
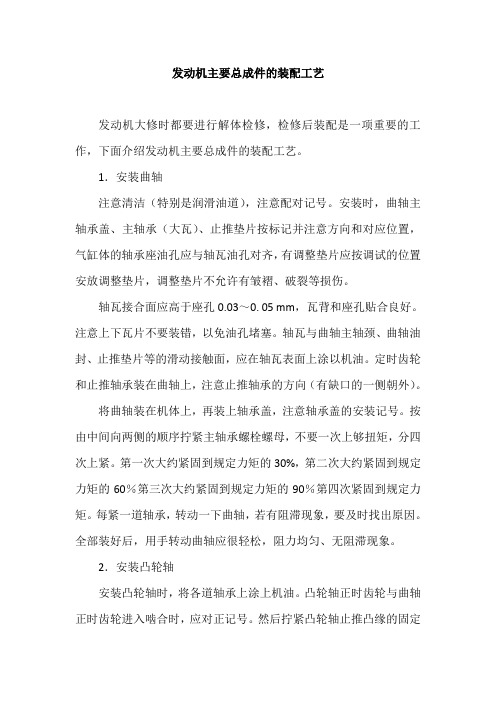
发动机主要总成件的装配工艺发动机大修时都要进行解体检修,检修后装配是一项重要的工作,下面介绍发动机主要总成件的装配工艺。
1.安装曲轴注意清洁(特别是润滑油道),注意配对记号。
安装时,曲轴主轴承盖、主轴承(大瓦)、止推垫片按标记并注意方向和对应位置,气缸体的轴承座油孔应与轴瓦油孔对齐,有调整垫片应按调试的位置安放调整垫片,调整垫片不允许有皱褶、破裂等损伤。
轴瓦接合面应高于座孔0.03~0. 05 mm,瓦背和座孔贴合良好。
注意上下瓦片不要装错,以免油孔堵塞。
轴瓦与曲轴主轴颈、曲轴油封、止推垫片等的滑动接触面,应在轴瓦表面上涂以机油。
定时齿轮和止推轴承装在曲轴上,注意止推轴承的方向(有缺口的一侧朝外)。
将曲轴装在机体上,再装上轴承盖,注意轴承盖的安装记号。
按由中间向两侧的顺序拧紧主轴承螺栓螺母,不要一次上够扭矩,分四次上紧。
第一次大约紧固到规定力矩的30%,第二次大约紧固到规定力矩的60%第三次大约紧固到规定力矩的90%第四次紧固到规定力矩。
每紧一道轴承,转动一下曲轴,若有阻滞现象,要及时找出原因。
全部装好后,用手转动曲轴应很轻松,阻力均匀、无阻滞现象。
2.安装凸轮轴安装凸轮轴时,将各道轴承上涂上机油。
凸轮轴正时齿轮与曲轴正时齿轮进入啮合时,应对正记号。
然后拧紧凸轮轴止推凸缘的固定螺钉,止推凸缘与正时齿轮隔圈的厚度差是限制凸轮轴轴向移动的间隙,应符合技术要求。
3.安装活塞连杆组首先应检查活塞在气缸内的偏斜量。
将没有装活塞环的活塞连杆组装入气缸,按规定扭矩拧紧各道螺栓。
检查连杆小端与活塞座端之间的距离应不小于1 mm。
如偏移,多为气缸中心线偏移所致。
转动曲轴,检查活塞在上、下止点和中间位置时活塞顶在气缸前后方向的间隙,其间隙差值应不大于0. 10 mm,否则应查明偏缸原因,予以排除。
偏缸消除后,将活塞环装入环槽,注意各道环切槽的位置和方向,如有镀铬环应放在第一道环槽内。
环装好后,需彻底清洗,并在环槽内和活塞销上涂一层薄薄的机油。
曲轴压装工艺(装配工序卡)
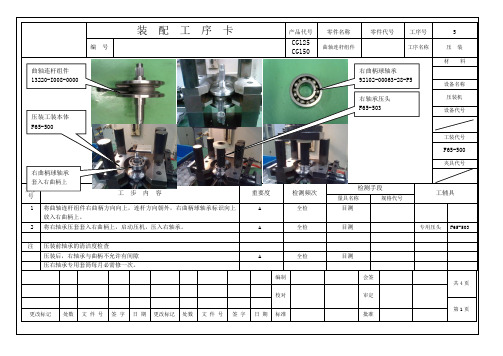
编 号CG125CG150曲轴连杆组件工序名称压 装材 料设备名称 压装机 设备代号工装代号F65-500夹具代号工步号 工 步 内 容重要度检测频次检测手段工辅具量具名称规格代号 1 将曲轴连杆组件右曲柄方向向上,连杆方向朝外,右曲柄球轴承标识向上放入右曲柄上。
A全检目测2 将右轴承压套套入右曲柄上,启动压机,压入右轴承。
A 全检 目测 专用压头 F65-503注压装前轴承的清洁度检查压装后,右轴承与曲柄不允许有间隙 A 全检目测压右轴承专用套筒每月必需修一次。
编制 会签共4页校对审定第1页更改标记处数 文 件 号 签 字 日 期 更改标记 处数文 件 号签 字日 期 标准批准曲轴连杆组件 13220-I008-0000 右曲柄球轴承92102-00063-28-P5 右曲柄球轴承 套入右曲柄上右轴承压头 F65-503压装工装本体 F65-500编 号CG125 CG150曲轴连杆组件工序名称压 装材 料设备名称 压装机设备代号工装代号F65-500夹具代号工步号 工 步 内 容重要度检测频次检测手段工辅具量具名称规格代号 1 将曲轴连杆组件左曲柄方向向上,连杆方向朝外。
B 全检 目测2 将左曲柄球轴承防尘盖向上,轴承专用压套套入左曲柄上,启动压机压入轴承。
A全检目测专用套筒 F65-502注不得碰伤、划伤零部件注意区别左右轴承。
左轴承防尘盖向上。
轴承压装前应转动灵活,无卡滞。
压装后,右轴承与曲柄不允许有间隙,左轴承与曲柄允许有<0.2的间隙。
A20件/次 塞尺0.2压左轴承专用套筒每月必需修一次。
编制 会签 共4页校对审定第2页 更改标记处数 文 件 号 签 字 日 期 更改标记 处数 文 件 号签 字日 期 标准批准左曲柄轴承92102-63-28-RS-P5左曲柄球轴承 套入右曲柄上 防尘盖向上 左轴承压头F65-502编 号CG125 CG150曲轴连杆组件工序名称压正时齿材 料设备名称压装机 设备代号工装代号F65-500夹具代号工步号工 步 内 容重要度检测频次检测手段工辅具量具名称规格代号 1 将正时齿放入压装套,使其O 形标记中心对正半圆键槽中心,调整正时齿使齿轮斜齿与限位套啮合。
发动机曲轴皮带轮正向匹配设计流程

发动机曲轴皮带轮正向匹配设计流程全文共四篇示例,供读者参考第一篇示例:发动机曲轴皮带轮正向匹配设计流程发动机是整个汽车的心脏,而曲轴皮带轮作为发动机的一个重要组成部分,其正向匹配设计是确保发动机运转正常、平稳的关键因素之一。
在设计曲轴皮带轮时,需要考虑到多个因素,并且按照一定的流程进行设计和匹配,以确保其性能和可靠性。
下面将介绍一下发动机曲轴皮带轮正向匹配设计的流程。
一、确定设计需求在进行曲轴皮带轮的正向匹配设计之前,首先需要确定设计的需求。
包括发动机的功率、转速范围、扭矩要求等。
这些需求将直接影响到曲轴皮带轮的设计参数,如直径、齿数、材料等。
二、选取合适的材料曲轴皮带轮一般由铝合金、钢铁等材料制成。
选择合适的材料对于曲轴皮带轮的使用寿命、刚度、轻量化等都有重要影响。
需要根据设计需求和成本考虑选取合适的材料。
三、确定曲轴皮带轮的尺寸和参数根据设计需求和选取的材料,确定曲轴皮带轮的尺寸和参数。
包括外径、内径、长度、齿数、齿距等。
曲轴皮带轮的尺寸和参数必须要与发动机曲轴、皮带等配套部件匹配,确保安装和传动正常。
四、进行强度分析在确定曲轴皮带轮的尺寸和参数后,需要进行强度分析。
主要包括承载能力、抗疲劳性能等。
通过有限元分析等手段,对曲轴皮带轮的强度进行评估,保证其在使用过程中不会出现开裂、变形等问题。
五、进行动力学分析除了强度分析外,还需要进行动力学分析。
主要包括惯性力、动平衡、动态配重等。
通过分析曲轴皮带轮在高速旋转时的动力学性能,可以保证其传动平稳、不产生振动和噪音。
六、优化设计方案根据强度分析和动力学分析的结果,对曲轴皮带轮的设计方案进行优化。
可能需要调整尺寸和参数,改变材料,进行重整设计等。
优化设计方案可以提高曲轴皮带轮的性能和可靠性。
七、进行样机试验在确定最终的设计方案后,需要制作样机进行试验。
通过试验,可以验证设计方案的可行性和稳定性。
根据试验结果对设计进行调整,直至满足设计需求为止。
八、进行生产和测试最终确定好设计方案后,进行生产和测试。
皮带轮加工工艺及精车皮带轮槽工装夹具设计方案
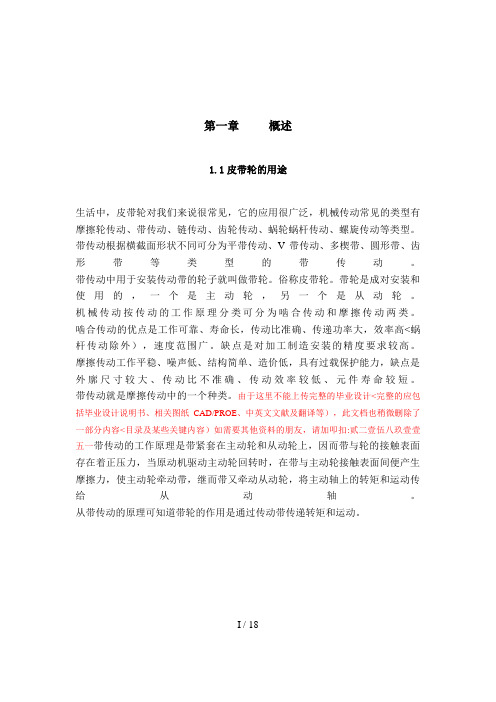
第一章概述1.1皮带轮的用途生活中,皮带轮对我们来说很常见,它的应用很广泛,机械传动常见的类型有摩擦轮传动、带传动、链传动、齿轮传动、蜗轮蜗杆传动、螺旋传动等类型。
带传动根据横截面形状不同可分为平带传动、V带传动、多楔带、圆形带、齿形带等类型的带传动。
带传动中用于安装传动带的轮子就叫做带轮。
俗称皮带轮。
带轮是成对安装和使用的,一个是主动轮,另一个是从动轮。
机械传动按传动的工作原理分类可分为啮合传动和摩擦传动两类。
啮合传动的优点是工作可靠、寿命长,传动比准确、传递功率大,效率高<蜗杆传动除外),速度范围广。
缺点是对加工制造安装的精度要求较高。
摩擦传动工作平稳、噪声低、结构简单、造价低,具有过载保护能力,缺点是外廓尺寸较大、传动比不准确、传动效率较低、元件寿命较短。
带传动就是摩擦传动中的一个种类。
由于这里不能上传完整的毕业设计<完整的应包括毕业设计说明书、相关图纸CAD/PROE、中英文文献及翻译等),此文档也稍微删除了一部分内容<目录及某些关键内容)如需要其他资料的朋友,请加叩扣:贰二壹伍八玖壹壹五一带传动的工作原理是带紧套在主动轮和从动轮上,因而带与轮的接触表面存在着正压力,当原动机驱动主动轮回转时,在带与主动轮接触表面间便产生摩擦力,使主动轮牵动带,继而带又牵动从动轮,将主动轴上的转矩和运动传给从动轴。
从带传动的原理可知道带轮的作用是通过传动带传递转矩和运动。
I / 181.2零件的图样及说明皮带轮的外形图车削是加工中用得最多的加工方法之一。
由于车床具有加工精度高、能作直线和圆弧插补以及在加工过程中能自动变速的特点,因此,其工艺范围较普通机床宽得多。
凡是能在车床上装夹的回转体零件都能在车床上加工。
针对车床的特点,下列几种零件最适合车削加工:1 精度要求较高的回转体零件;2 表面粗糙度要求高的回转体零件;3 表面形状复杂的回转体零件;4 带特殊螺纹的回转体零件;II / 18铣削是机械加工中最常用和最主要的加工方法之一,它除了能铣削普通铣床所能铣削的各种零件表面外,还能铣削普通铣床不能铣削的需2~5坐标联动的各种平面轮廓和立体轮廓。
曲轴减震皮带轮粘附工艺的实验分析与实践
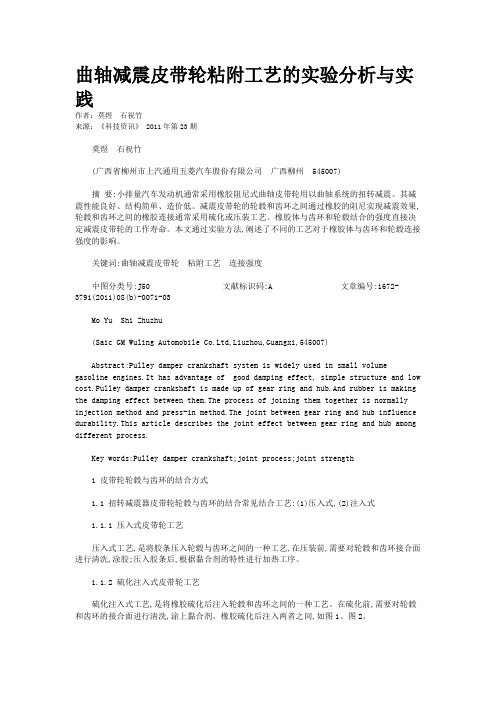
曲轴减震皮带轮粘附工艺的实验分析与实践作者:莫煜石祝竹来源:《科技资讯》 2011年第23期莫煜石祝竹(广西省柳州市上汽通用五菱汽车股份有限公司广西柳州 545007)摘要:小排量汽车发动机通常采用橡胶阻尼式曲轴皮带轮用以曲轴系统的扭转减震。
其减震性能良好、结构简单、造价低。
减震皮带轮的轮毂和齿环之间通过橡胶的阻尼实现减震效果,轮毂和齿环之间的橡胶连接通常采用硫化或压装工艺。
橡胶体与齿环和轮毂结合的强度直接决定减震皮带轮的工作寿命。
本文通过实验方法,阐述了不同的工艺对于橡胶体与齿环和轮毂连接强度的影响。
关键词:曲轴减震皮带轮粘附工艺连接强度中图分类号:J50 文献标识码:A 文章编号:1672-3791(2011)08(b)-0071-03Mo Yu Shi Zhuzhu(Saic GM Wuling Automobile Co.Ltd,Liuzhou,Guangxi,545007)Abstract:Pulley damper crankshaft system is widely used in small volume gasoline engines.It has advantage of good damping effect, simple structure and low cost.Pulley damper crankshaft is made up of gear ring and hub.And rubber is making the damping effect between them.The process of joining them together is normally injection method and press-in method.The joint between gear ring and hub influence durability.This article describes the joint effect between gear ring and hub among different process.Key words:Pulley damper crankshaft;joint process;joint strength1 皮带轮轮毂与齿环的结合方式1.1 扭转减震器皮带轮轮毂与齿环的结合常见结合工艺:(1)压入式,(2)注入式1.1.1 压入式皮带轮工艺压入式工艺,是将胶条压入轮毂与齿环之间的一种工艺,在压装前,需要对轮毂和齿环接合面进行清洗,涂胶;压入胶条后,根据黏合剂的特性进行加热工序。
汽车总装车间工艺流程
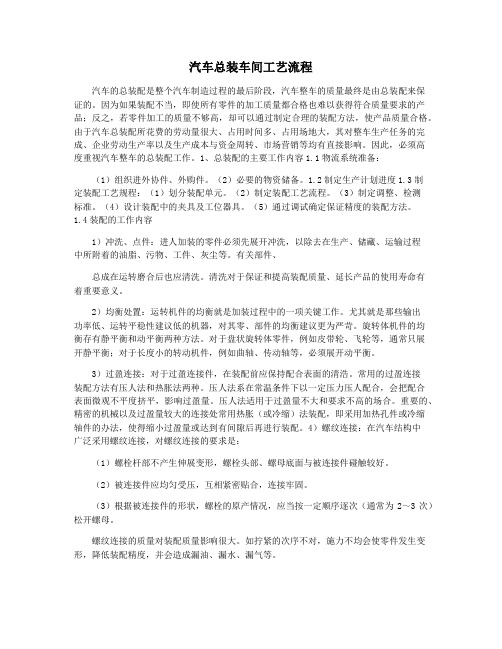
汽车总装车间工艺流程汽车的总装配是整个汽车制造过程的最后阶段,汽车整车的质量最终是由总装配来保证的。
因为如果装配不当,即使所有零件的加工质量都合格也难以获得符合质量要求的产品;反之,若零件加工的质量不够高,却可以通过制定合理的装配方法,使产品质量合格。
由于汽车总装配所花费的劳动量很大、占用时间多、占用场地大,其对整车生产任务的完成、企业劳动生产率以及生产成本与资金周转、市场营销等均有直接影响。
因此,必须高度重视汽车整车的总装配工作。
1、总装配的主要工作内容1.1物流系统准备:(1)组织进外协件、外购件。
(2)必要的物资储备。
1.2制定生产计划进度1.3制定装配工艺规程:(1)划分装配单元。
(2)制定装配工艺流程。
(3)制定调整、检测标准。
(4)设计装配中的夹具及工位器具。
(5)通过调试确定保证精度的装配方法。
1.4装配的工作内容1)冲洗、点件:进人加装的零件必须先展开冲洗,以除去在生产、储藏、运输过程中所附着的油脂、污物、工件、灰尘等。
有关部件、总成在运转磨合后也应清洗。
清洗对于保证和提高装配质量、延长产品的使用寿命有着重要意义。
2)均衡处置:运转机件的均衡就是加装过程中的一项关键工作。
尤其就是那些输出功率低、运转平稳性建议低的机器,对其零、部件的均衡建议更为严苛。
旋转体机件的均衡存有静平衡和动平衡两种方法。
对于盘状旋转体零件,例如皮带轮、飞轮等,通常只展开静平衡;对于长度小的转动机件,例如曲轴、传动轴等,必须展开动平衡。
3)过盈连接:对于过盈连接件,在装配前应保持配合表面的清浩。
常用的过盈连接装配方法有压人法和热胀法两种。
压人法系在常温条件下以一定压力压人配合,会把配合表面微观不平度挤平,影响过盈量。
压人法适用于过盈量不大和要求不高的场合。
重要的、精密的机械以及过盈量较大的连接处常用热胀(或冷缩)法装配,即采用加热孔件或冷缩轴件的办法,使得缩小过盈量或达到有间隙后再进行装配。
4)螺纹连接:在汽车结构中广泛采用螺纹连接,对螺纹连接的要求是:(1)螺栓杆部不产生伸展变形,螺栓头部、螺母底面与被连接件碰触较好。
发动机皮带轮的组装工艺

发动机皮带轮的组装工艺
发动机皮带轮的组装工艺一般包括以下步骤:
1. 准备工作:检查发动机皮带轮的表面是否有损坏或磨损,清洁并检查轮轴轴承的状态。
2. 定位轮轴:将发动机轴的接口与轮轴上的相应接口对准。
确保轮轴和轴承孔对称。
3. 安装皮带轮:将皮带轮放置在轮轴上,确保与轴承孔对齐。
根据轴承的类型,可能需要使用推力轴承或锁紧螺母等固定轮轴。
4. 填充润滑剂:在轮轴和轴承之间涂上适量的润滑剂,以减少摩擦和磨损。
5. 旋转测试:旋转皮带轮,确保其顺畅旋转,没有卡住或阻力。
6. 固定螺栓:使用螺栓将皮带轮固定在发动机上。
根据具体要求,可使用正确的扭矩进行紧固。
7. 检查紧固度:确保螺栓紧固度适当,并检查轮轴是否与轴承保持良好连接。
8. 清洁和调整:清洁皮带轮表面和周围区域,确保没有杂质或污垢。
调整皮带
的松紧度,以确保正常的运行和传动效率。
以上是发动机皮带轮的一般组装工艺步骤,具体的步骤和要求可能因不同发动机型号和厂商而有所不同。
在进行组装前,建议查阅相关的发动机制造商的技术手册或保养指南,以确保正确的操作和组装。
皮带轮装配注意事项
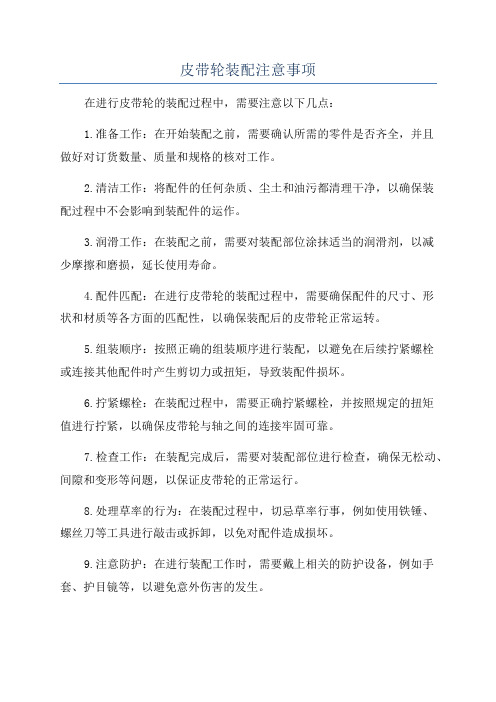
皮带轮装配注意事项
在进行皮带轮的装配过程中,需要注意以下几点:
1.准备工作:在开始装配之前,需要确认所需的零件是否齐全,并且
做好对订货数量、质量和规格的核对工作。
2.清洁工作:将配件的任何杂质、尘土和油污都清理干净,以确保装
配过程中不会影响到装配件的运作。
3.润滑工作:在装配之前,需要对装配部位涂抹适当的润滑剂,以减
少摩擦和磨损,延长使用寿命。
4.配件匹配:在进行皮带轮的装配过程中,需要确保配件的尺寸、形
状和材质等各方面的匹配性,以确保装配后的皮带轮正常运转。
5.组装顺序:按照正确的组装顺序进行装配,以避免在后续拧紧螺栓
或连接其他配件时产生剪切力或扭矩,导致装配件损坏。
6.拧紧螺栓:在装配过程中,需要正确拧紧螺栓,并按照规定的扭矩
值进行拧紧,以确保皮带轮与轴之间的连接牢固可靠。
7.检查工作:在装配完成后,需要对装配部位进行检查,确保无松动、间隙和变形等问题,以保证皮带轮的正常运行。
8.处理草率的行为:在装配过程中,切忌草率行事,例如使用铁锤、
螺丝刀等工具进行敲击或拆卸,以免对配件造成损坏。
9.注意防护:在进行装配工作时,需要戴上相关的防护设备,例如手套、护目镜等,以避免意外伤害的发生。
10.保持记录:在装配过程中,及时记录每个步骤的完成情况、注意事项以及可能存在的问题,以备后续参考和分析。
总之,正确的皮带轮装配过程对于保证设备的正常运行和延长使用寿命至关重要。
因此,在进行装配工作时,需要严格按照相关的操作规程和注意事项进行,确保装配的质量和安全性。
发动机曲轴减震皮带轮装配模具及装配方法[发明专利]
![发动机曲轴减震皮带轮装配模具及装配方法[发明专利]](https://img.taocdn.com/s3/m/1480b2caed630b1c58eeb556.png)
专利名称:发动机曲轴减震皮带轮装配模具及装配方法专利类型:发明专利
发明人:胡先启,陈云明,曾俊来
申请号:CN201510028370.0
申请日:20150120
公开号:CN104551606A
公开日:
20150429
专利内容由知识产权出版社提供
摘要:本发明公开了一种发动机曲轴减震皮带轮装配模具及装配方法,包括上模结构、下模板、用于对所述皮带轮定位的外圈定位块、用于对所述轮毂定位的轮毂定位块和顶胶块,外圈定位块和轮毂定位块设在下模板上,外圈定位块上并具有用于嵌入所述皮带轮上的标记槽内的内凸块,上模结构包括用于压紧皮带轮的外导向块、用于压紧轮毂的内导向块以及用于推动所述橡胶块嵌入皮带轮与轮毂之间的压头。
本发明的发动机曲轴减震皮带轮装配模具,通过设置外圈定位块和轮毂定位块分别对皮带轮和轮毂进行定位,并配合顶胶块和上模结构的压头,使橡胶环压入皮带轮与轮毂之间,完成减震皮带轮的装配工作,提高了装配效率,操作方便简单,而且提高了产品质量。
申请人:芜湖金源机械制造有限公司
地址:241100 安徽省芜湖市芜湖县芜湖机械工业园
国籍:CN
代理机构:芜湖安汇知识产权代理有限公司
代理人:朱顺利
更多信息请下载全文后查看。
简述曲轴皮带轮的拆装步骤
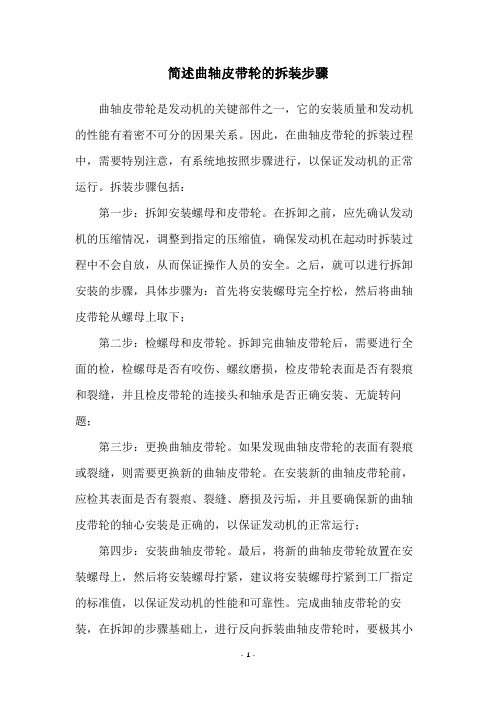
简述曲轴皮带轮的拆装步骤曲轴皮带轮是发动机的关键部件之一,它的安装质量和发动机的性能有着密不可分的因果关系。
因此,在曲轴皮带轮的拆装过程中,需要特别注意,有系统地按照步骤进行,以保证发动机的正常运行。
拆装步骤包括:第一步:拆卸安装螺母和皮带轮。
在拆卸之前,应先确认发动机的压缩情况,调整到指定的压缩值,确保发动机在起动时拆装过程中不会自放,从而保证操作人员的安全。
之后,就可以进行拆卸安装的步骤,具体步骤为:首先将安装螺母完全拧松,然后将曲轴皮带轮从螺母上取下;第二步:检螺母和皮带轮。
拆卸完曲轴皮带轮后,需要进行全面的检,检螺母是否有咬伤、螺纹磨损,检皮带轮表面是否有裂痕和裂缝,并且检皮带轮的连接头和轴承是否正确安装、无旋转问题;第三步:更换曲轴皮带轮。
如果发现曲轴皮带轮的表面有裂痕或裂缝,则需要更换新的曲轴皮带轮。
在安装新的曲轴皮带轮前,应检其表面是否有裂痕、裂缝、磨损及污垢,并且要确保新的曲轴皮带轮的轴心安装是正确的,以保证发动机的正常运行;第四步:安装曲轴皮带轮。
最后,将新的曲轴皮带轮放置在安装螺母上,然后将安装螺母拧紧,建议将安装螺母拧紧到工厂指定的标准值,以保证发动机的性能和可靠性。
完成曲轴皮带轮的安装,在拆卸的步骤基础上,进行反向拆装曲轴皮带轮时,要极其小心,以避免出现拆装错误,从而影响发动机的正常运行。
总结本文,曲轴皮带轮的拆装需系统按照步骤进行,且在拆装过程中需对曲轴皮带轮及安装螺母等进行全面检,以保证曲轴皮带轮的质量及发动机特性。
另外,在安装曲轴皮带轮时,要按照要求正确安装轴心,并将安装螺母拧紧至指定的标准值,以保证发动机的正常运行。
以上就是曲轴皮带轮的拆装步骤,希望能够给大家带来帮助。
发动机曲轴皮带轮装配问题分析与解决
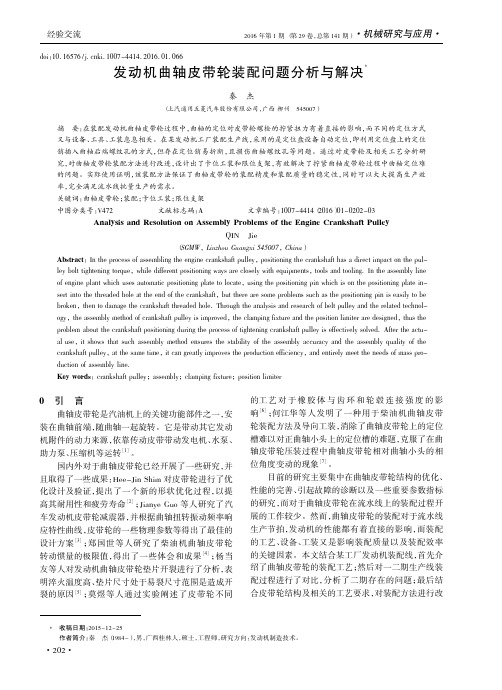
al use,it shows that such assembly method ensures the stability of the assembly accuracy and the assembly quality of the
crankshaft pulley,at the same time,it can greatly improves the production efficiency,and entirely meet the needs of mass pro-
ogy,the assembly method of crankshaft pulley is improved,the clamping fixture and the position limiter are designed,thus the
problem about the crankshaft positioning during the process of tightening crankshaft pulley is effectively solved. After the actu-
ley bolt tightening torque,while different positioning ways are closely with equipments,tools and tooling. In the assembly line
of engine plant which uses automatic positioning plate to locate,using the positioning pin which is on the positioning plate in-
QIN Jie
- 1、下载文档前请自行甄别文档内容的完整性,平台不提供额外的编辑、内容补充、找答案等附加服务。
- 2、"仅部分预览"的文档,不可在线预览部分如存在完整性等问题,可反馈申请退款(可完整预览的文档不适用该条件!)。
- 3、如文档侵犯您的权益,请联系客服反馈,我们会尽快为您处理(人工客服工作时间:9:00-18:30)。
设计说明书题目:皮带轮加工工艺及插键槽(10正负0.018)专用夹具设计班级:姓名:指导教师:前言机械制造工艺学毕业设计是在我们学完了大学的全部基础课、技术基础课以及大部分专业课之后进行的。
这是我们在进行毕业设计之前对所学各课程的一次深入的综合性的链接,也是一次理论联系实际的训练。
因此,它在我们的大学生活中占有十分重要的地位。
就我个人而言,我希望能通过设计对自己未来从事的工作进行一次适应性训练,从中锻炼自己分析问题、解决问题的能力,为今后参加祖国的现代化建设打下一个良好的基础。
一、零件的分析(一)零件的作用皮带轮是回转类零件,主要用于和别的零件进行装配。
所以皮带轮要有一定的配合精度以及表面接触强度,还有要有足够的刚度和耐磨性,以满足使用要求。
(二)零件的工艺分析该零件是轴类零件,形状不太复杂,尺寸精度要求比较高。
零件的主要技术要求分析如下:(1)Φ157 的外圆和Φ45 的内孔,都有很高的尺寸精度要求,主要是为了和其装配件很好的装配。
(2)在Φ45 的内孔插键槽有一定的对称度要求。
(3)在Φ157 的外圆上车 V 形带,要注意他们的相互位置。
二、工艺规程设计(一)确定毛坯的制造形式零件的材料为HT200.考虑到皮带轮在工作过程中会受到一定的载荷,因此选择铸件,以使金属纤维不被切断,保证零件工作可靠.由于零件年产量为 5000 件,已达到大批生产的水平.而且零件的轮廓尺寸不大,故可采用铸造成型,这对于提高生产率,保证加工质量也是有利的。
(二)基面的选择基面的选择是工艺规程设计中的重要工作之一。
基面选择的正确、合理,可以保证加工质量,提高生产效率。
否则,就会使加工工艺过程问题百出,严重的还会造成零件大批报废,使生产无法进行。
1.粗基准的选择对于一般的轴类零件而言,以外圆作为基准是完全合理的。
按照有关粗基准的选择原则(即当零件又不加工表面时,应以这些不加工的表面作为粗基准;若零件有若干个不加工表面时,则应以与加工要求相对位置精度较高的不加工表面作为粗基准),现在应为都要加工就要结合加工工艺来确定粗基准,现取Φ157的外圆作为粗基准,利用三爪卡盘装夹。
利用不完全定位来加工工件。
2.精基准的选择精基准的选择主要考虑基准重合的问题。
当设计基准与工序基准不重合时,应该进行尺寸换算。
(三)工艺路线的制定制定工艺路线的相互发点,应当是使零件的几何形状、尺寸精度及位置精度要求等技术能得到合理的保证.在生产纲领已确定为大批生产的条件下,可以采用万能机床配以专用夹具,并尽量使工序集中来提高生产率.除此以外,还应考虑经济效益,以便降低生产成本。
1.工艺路线方案一:工序 1: 车端面,打中心孔, 车Φ157 的外圆表面,倒角。
工序 2: 调头车另一端面,打中心孔,工序 3: 修研两端中心孔。
工序 4: 钻中心孔。
工序 5: 扩中心孔。
工序 6:铰中心孔工序 7: 插键槽。
工序 8: 粗精车 V 形带。
工序 9:终检。
工序 10:入库。
2.工艺路线方案二:工序 1:铣端面,打中心孔。
工序 2:掉头铣另一端面,打中心孔。
工序 3:车Φ157的外圆,掉头车Φ157 的外圆。
工序 5:钻中心孔、中心孔、铰中心孔。
工序 6: 插键槽。
工序 8: 粗精车 V 形带。
工序 9:终检。
工序 10:入库.3.工艺方案的比较与分析上述两个工艺方案的特点在于:方案一是在车床上用三爪卡盘装夹,车一端面在打中细孔,然后用顶尖顶住来车外圆再掉头加工另一端,以此为基准来完成后面的工序。
方案二则与之不同,是先铣削好两个端面,打中心孔,以此为基准来加工余下的工序。
经比较可见,先加工好一端面和它所在端的外圆,以此为基准来加工后面的工序,这是的位置和尺寸精度较易保证,并且定位也较方便。
在加工螺纹和铣凹槽的时候,方案一中的工序 6、7、8,虽然只是在加工的先后顺序不同,这样的话可能会造成钻孔时的让刀。
故决定将方案二中的工序 5、6、7移入方案一。
具体工艺过程如下:工序 1: 车端面,打中心孔, 车Φ157 的外圆表面,倒角。
工序 2: 调头车另一端面,打中心孔,工序 3: 修研两端中心孔。
工序 4: 钻中心孔。
工序 5: 扩中心孔。
工序 6:铰中心孔工序 7: 插键槽。
工序 8: 粗精车 V 形带。
工序 9:终检。
工序 10:入库。
以上方案大致看来还是合理的。
但通过仔细考虑零件的技术要求以及可能的加工手段之后,发现仍有问题,因此,最后的加工路线确定如下:工序 1: 车端面,打中心孔, 车Φ157 的外圆表面,倒角。
工序 2: 调头车另一端面,打中心孔,工序 3: 修研两端中心孔。
工序 4: 钻中心孔。
工序 5: 扩中心孔。
工序 6:铰中心孔工序 7: 插键槽。
工序 8: 粗精车 V 形带。
工序 9:终检。
工序 10:入库。
以上工艺过程详见附表机械加工工艺过程卡片和附表机械加工工序卡片。
(四)机械加工余量、工序尺寸及毛坯尺寸的确定“皮带轮”零件材料为HT200,生产类型为大批生产,可采用在锻锤上合模铸造毛坯。
根据上述原始资料及加工工艺,分别确定个加工表面的机械加工余量工序尺寸及毛坯尺寸如下:1.外圆表面(Φ157)查《机械制造工艺设计简明手册》(以下简称《工艺手册》)表 2.2-14,其中铸件重量为 4kg,铸件复杂形状系数为 S1,铸件材质系数取 M1,铸件轮廓尺寸(直径方向)>180~315mm,其余量值规定为 1.7~2.2mm,现取 2.0mm。
2.外圆表面沿轴线长度方向的加工余量及公差查《工艺手册》表 2.2-25,其中铸件重量为 4kg,铸件复杂形状系数为 S1,铸件材质系数取 M1,铸件轮廓尺寸(直径方向)>120~180mm,故长度方向偏差为(+1.2;-0.6)mm.长度方向的余量查《工艺手册》表 2.2-25,其余量值规定为 1.7~2.2mm,现取 2.0mm。
(五)确定切削用量及基本工时工序 1:车端面, 打中心孔,车Φ157 的外圆表面,倒角。
本工序采用计算法确定切削用量。
1.加工条件工件材料:HT200,正火,铸造。
加工要求:粗车Φ157 端面及Φ157 的外圆,Φ157 的端面和外圆表面的粗糙度值为 R12.5。
机床:CA6140 卧式车床。
刀具:刀片材料为 YT15,刀杆尺寸为16mmX25mm,kr=90°,γo=15°,αo=8°,r ε=0.5mm2.切削用量计算(1)车Φ157 端面。
1)确定端面最大加工余量:已知毛坯长度方向的加工余量为 2+1.2考虑7° 的铸造拔模斜度,则毛坯长度方向的最大加工余量 Zmax=7mm,故实际端面余量可按Zmax=7mm 考虑,分三次加工,a p=3mm 计。
2)确定进给量 f:根据《机械制造工艺与机床夹具课程设计指导》表 2-19,当刀杆尺寸为 16mmX25mm,a p≦3mm,以及工件直径为Φ81mm 时按CA6140 车床说明书取 f=0.51mm/r(参见表 3-9)3)计算切削速度:按《切削用量简明手册》(第三版)(以下简称《切削手册》)表 1.27,切削速度的计算公式为(寿命选 T=60min)。
v c=(Cv*k v)/(Tm*a p xv*f yv)1. 式中,Cv=242,xv=0.15,yv=0.35,m=0.2。
k v见《切削手册》表28,即k Mv=1.44,k sv=0.8,k kv=1.04,k krv=0.81,k Bv=0.97所以v c=(242X1.44X0.8X1.04X0.81X0.97)/(600.2X30.15X0.510.35)m/min =108.8m/min4)确定机床主轴转速:n s=1000v c/πdw=1000X108.6/πX81=427r/min按机床说明书,与 427r/min 相近的机床转速为 400r/min 及 450r/min。
现选取450r/min。
所以实际切削速度 v=114.45r/min。
5)计算切削工时:按《工艺手册》表 6.2-1,取l=40.5mm,l1=2mm,l2=0,l3=0 t m=(l+l1+l2+l3)*i/n f=3X(40.5+2)/450X0.51=0.556min(2)车Φ157 外圆,同时应校验机床功率及进给机构强度。
1)被吃刀量:单边余量 Z=2mm,可一次切除。
2)进给量:根据《切削手册》表 1.4,选用 f=0.5mm/r。
3)计算切削速度:见《切削手册》表 1.27v c=(Cv*k v)/(Tm*a p xv*f yv)=(242X1.44X0.8X0.81X0.97)/(600.2X20.15X 0.510.35)=110.17m/min4)确定主轴转速:n s=1000 v c/πdw=1000X110.17/πX81=433.16r/min按机床选取 n=450r/min。
所以实际切削速度为V=πdn/1000=πX81X450/1000m/min=114.45m/min5)检验机床功率:主切削力 Fc 按《切削手册》表 1.29 所示工时计算Fc=C a p f v k式中,C =2795,x =1.0, y =0.75, n=-0.15k =(σb/650) =(600/650)0.75=0.94, k =0.89所以Fc=2795X2X0.50.75X114.45-0.15X0.94X0.89N= 1318.9N 切削是消耗功率 Pc 为Pc= Fc*v c/6X104=1318.9X114.45/6X104kW=3.175kW由 CA6140 机床说明书可知,CA6140 主电动机功率为 7.8 kW,当主轴转速为450r/min 时,主轴传递的最大功率为 4.5kW,所以机床功率足够,可以正常加工。
6)校验机床进给系统强度:已知主切削力 Fc=1318.9N,径向切削力 Fp 按,《切削手册》表 1.29 所示公式计算Fp=C a p f v k式中,C =1940,x =0.9, y =0.6 n=-0.3k =(σb/650) =(600/650)1.35=0.897, k =0.5 所以,Fp=1940X20.9X0.50.6X114.45-0.3X0.897X0.5N=258.4N而轴向切削力F f =C a p f v k式中,C =2880,x =1.0, y =0.5, n =-0.4k =(σb/650)= (600/650)1=0.923,k =1.17 于是轴向切削力F f=2880X2X0.50.5X114.45-0.4X0.923X1.17N=601.7N取机床导轨与床鞍之间的摩擦系数μ=0.1,则切削力在纵向进给方向对进给机构的作用力为F= F f+μ(Fc+ Fp)=601.7+0.1X(1318.9+258.4)N=759.43N而机床纵向进给机构可承受的最大纵向力为 3530N(见《切削手册》表1.30),故机床进给系统可正常工作。