点焊剪切强度检验方法
点焊对焊焊接强度快速检验方法
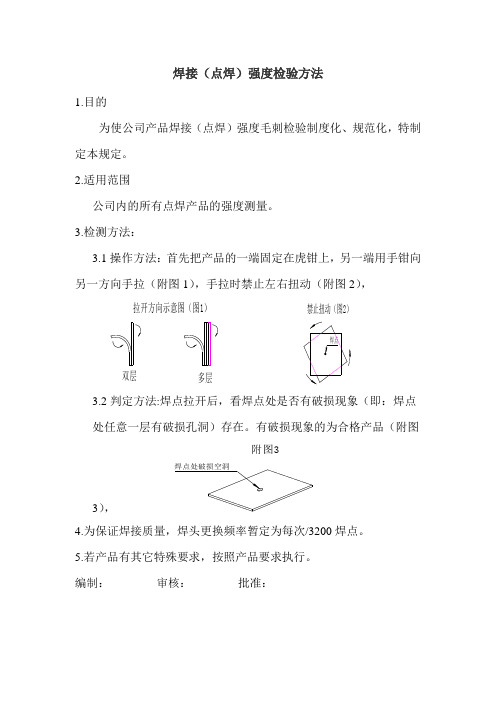
焊接(点焊)强度检验方法
1.目的
为使公司产品焊接(点焊)强度毛刺检验制度化、规范化,特制定本规定。
2.适用范围
公司内的所有点焊产品的强度测量。
3.检测方法:
3.1操作方法:首先把产品的一端固定在虎钳上,另一端用手钳向另一方向手拉(附图1),手拉时禁止左右扭动(附图2),
拉开方向示意图(图1
)双层多层
焊点
禁止扭动(图2)
3.2判定方法:焊点拉开后,看焊点处是否有破损现象(即:焊点处任意一层有破损孔洞)存在。
有破损现象的为合格产品(附图
3),焊点处破损空洞
附图3
4.为保证焊接质量,焊头更换频率暂定为每次/3200焊点。
5.若产品有其它特殊要求,按照产品要求执行。
编制:审核:批准:。
焊接强度试验基准

补充说明 焊接强度等级 (HES A 1018) 焊接方法类别
焊接符号的表示方法
1、基本符号
焊接符号的表示方法
2、辅助符号
焊接符号的表示方法
3、类别符号
焊接符号的表示方法
4、图纸标注方法
a) 电阻点焊的图面示例1
图1
焊接符号的表示方法
图纸标注方法
电阻点焊的图面示例2
图2
焊接符号的表示方法
大纲
一、焊接的分类 1.电阻点焊 2.凸焊 3.缝焊 4.气体保护焊 5.激光焊 6.钎焊 二、焊接符号的表示方法 1.基本符号 2.辅助符号 3.类别符号 4.图纸标注方法 三、焊接强度试验标准 1.电阻点焊焊接强度试验标准 2.焊接螺母焊接强度试验标准 3.焊接螺栓焊接强度试验标准 4.气体保护焊焊接强度试验标准 5.激光焊焊接强度试验标准 6.焊接强度试验标准总结 四、焊接强度检查表
HES E001-4.4.2
工程间检查 初物检查
工程间检查、初 物检查至少各一 次 工程间检查、初 物检查至少各一 次 工程间检查依据 工厂的质量管理 规定量产准备阶 段都做
5
非破坏检查
焊接直径
零件
HES E001-4.5.1
HES E001-4.5.2
工程间检查 初物检查
工程间检查 量产准备阶段(工艺参数确认) (需要提供报告) 初物检查
焊接的分类
气体保护焊
•什么是MIG焊? 使用熔化电极的惰性保护焊,英文简称 MIG焊,见图16。保护气体可采用Ar、 Ar+He或He,电弧燃烧稳定,熔滴过渡平 稳、安定,无激烈飞溅。在整个电弧燃 烧过程中,焊丝连续等速送进,可用来 焊接各种钢材及有色金属。
•什么是TIG焊? 利用纯钨或活化钨(钍钨、铈钨等)作为 电极的惰性气体保护焊称钨极惰性气体保 护焊,其英文简称为TIG焊。它是在惰性 气体的保护下,利用钨电极与焊件间产生 的电弧热熔化母材和填充焊丝的一种焊接 方法,其示意图见图9。
HES焊接强度试验基准
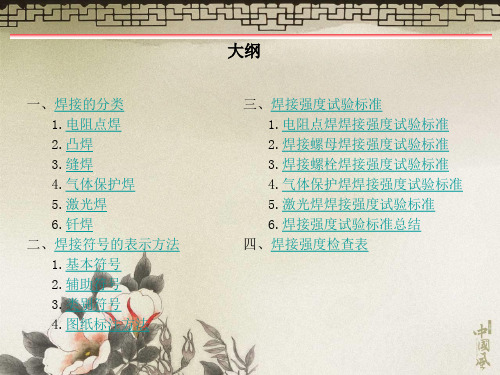
a)材料相同板厚相同﹙材料抗拉强度相同板厚相同﹚——按相应的抗拉剪切强度可作参考。
例 :JSC270E/1.6t和JSC270E/1.6t
选等级270Mpa/1.6t的抗拉剪切强度 7662N作基准。(参照表1 中a)
b)材料相同板厚不同﹙材料抗拉强度相同板厚不同﹚——按较薄板的抗拉剪切强度作基准。
电阻点焊强度试验标准
抗拉剪切强度试验
公称板厚的选取:
1.在板厚和材质不同钢板焊接时,计算钢板抗拉强度与钢板厚 度的积,取积较小的钢板厚度作为公称板厚。
2.三层以上焊接时,试片的形状为图3,尺寸按照表1。这种情 况下的剪切强度试验,如图3a)、b)所示,要在相关部件材质间 进行。
3.三层以上焊接,板厚或材质不同时,试片尺寸,计算不同相 关部件材质的抗拉强度与板厚的积,取较小值的板材的板厚为 公称板厚。
工程间检查、初 物检查至少各一 次
工程间检查 量产准备阶段(工艺参数确认) (需要提供报告) 初物检查
工程间检查依据 工厂的质量管理 规定量产准备阶 段都做
-抗拉剪切强度试验
•试片的形状及尺寸 ——JIS Z 3136 尺寸的选取见表1
图2为两层钢板的焊接
焊接强度试验标准
电阻点焊强度试验标准
抗拉剪切强度试验
焊、软钎焊、闪光焊、凸焊和摩擦焊,符号依据表3。 • 注意:
焊接强度分:A/B/C三个等级; 图面没有标识为B级。
补充说明 焊接强度等级 (HES A 1018) 焊接方法类别
1、基本符号
焊接符号的表示方法
2、辅助符号
焊接符号的表示方法
3、类别符号
焊接符号的表示方法
4、图纸标注方法
焊接符号的表示方法 a) 电阻点焊的图面示例1
焊接强度试验及判定规范

序号1、2、3、4、5、1、2、3、4、5、1、2、3、4、5、1、 编号2、3、敲击破坏试验查焊接作业指导书主要参数一栏,进行调节查焊接作业指导书产品结构一栏,选择最大料厚1、将变形制件恢复到原状,在相邻位置处增焊1点;2、若零件发生开裂,用C02保护焊进行加固,抛光处理3、发生无法修复的情况,申请报废处理不得流转下序或交付修复4、半破坏试验试片破坏性试验若不合格对电极进行俢挫,或重新调节参数破坏用虎钳夹持一端,来回扭转另一端使其脱离 见(图4)判定观察断裂情况,不许再焊点处断裂 见(图5)试片规格30mm×100mm×t若未达到要求,重新进行试验紧固件无发黑、变形等现象若不合格对电极进行俢挫,或重新调节参数用1kg榔头根据(图6)方向进行敲击用錾子紧靠焊点两侧进行剥离,无需撕裂零件简图试焊焊点要求呈圆形或团圆形,无飞溅、毛刺、焊穿等现象 见(图1)操作方法试焊剥离解释说明焊点要求呈圆形或团圆形,无飞溅、毛刺、焊穿等现象 见(图1)先用錾子将两侧分开,再用虎钳夹持一端,剥离另一端 见(图2)试片剥离试验查焊接作业指导书产品结构一栏,选择最大料厚查焊接作业指导书主要参数一栏,进行调节测量判定用卡尺,对剥离后的焊核直径进行测量,D=(X+Y)/2 见(图3)若未达到要求,重新进行试验选择紧固件调节设备参数试焊破坏步骤选择试片料厚调节设备参数选择试片料厚调节设备参数查焊接作业指导书产品结构一栏,选择最大规格紧固件试片规格30mm×100mm×t查焊接作业指导书主要参数一栏,进行调节选取破坏点判定紧固件无脱了或撕裂母材,4焊脚紧固件撕裂3个焊点以上为合格若未达到要求,重新进行试验根据实际情况,选择破坏后易于修复或使用性能不高的点位进行破坏判定6、修复料厚与焊核直径对照表0.7~0.8 >2.0≥5.6≥5.0观察焊点零件处有变白迹象或有发生拉裂的情况即为合格此判定是建立在班前做了试片试验的基础上焊接强度试验及判定规范≥4.0 焊核直径料厚将变形制件恢复到原状,用新的紧固件进行焊接,若不牢靠,在紧固件斜对角处用CO2保护焊进行加固 见(图7)破坏备注若不合格对电极进行俢挫,或重新调节参数试片规格30mm×100mm×t定州至信机械制造有限公司北京焊接车间编制 审核≥4.5 正面:201309100120130910年月日01 第1次批准XXX 操作者正面:年月日+第几次反面:操作者+合格与否1.0~1.2 1.4~1.6 1.8~2.0≥6.3OK反面:XXXOK 例1:2013年9月10日XXX操作者对置物板焊接总成组焊1进行了试片试验第1次判定合格合格提前准备好各种料厚试片,以便使用试片编号原则见(例1)试片至少保存一周,以便追溯NO不合格OK合格虎钳扳手图2图5未生成焊点焊点处断裂咬边断裂拔式断裂图6图4虎钳来回旋转錾子图7图1。
焊接强度检查通用操作规程-201204
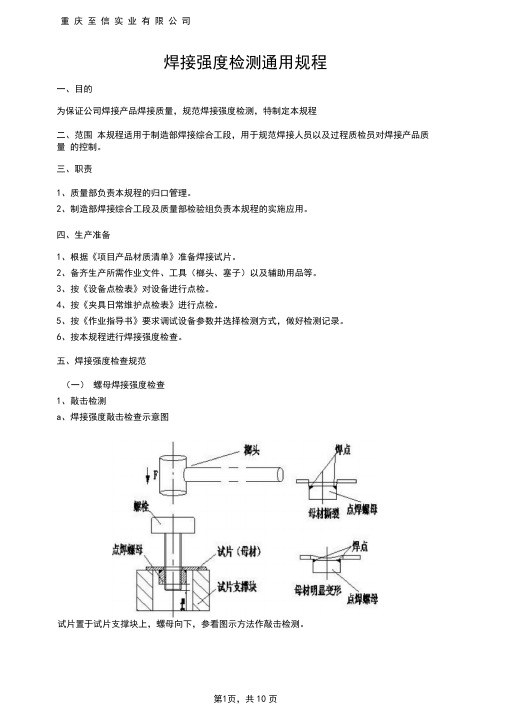
焊接强度检测通用规程一、目的为保证公司焊接产品焊接质量,规范焊接强度检测,特制定本规程二、范围本规程适用于制造部焊接综合工段,用于规范焊接人员以及过程质检员对焊接产品质量的控制。
三、职责1、质量部负责本规程的归口管理。
2、制造部焊接综合工段及质量部检验组负责本规程的实施应用。
四、生产准备1、根据《项目产品材质清单》准备焊接试片。
2、备齐生产所需作业文件、工具(榔头、塞子)以及辅助用品等。
3、按《设备点检表》对设备进行点检。
4、按《夹具日常维护点检表》进行点检。
5、按《作业指导书》要求调试设备参数并选择检测方式,做好检测记录。
6、按本规程进行焊接强度检查。
五、焊接强度检查规范(一)螺母焊接强度检查1、敲击检测a、焊接强度敲击检查示意图试片置于试片支撑块上,螺母向下,参看图示方法作敲击检测。
b、检测时机:日常生产的首中末件;参数调整时;设备大修或更换时;零件设变时;电极或工装变更时;焊接强度可能不够,有必要做检测验证时。
c、判定标准:对于凸点数学3的螺母,允许最多1个凸点不符合要求;对于环状焊脚的螺母,连续的环形焊接区域至少为70%例:①敲击后螺母有三个或三个以上焊点撕缺试片母材,焊接强度合格(如下图左);②敲击后,试片明显变形但螺母未脱焊,焊接强度合格(如下图右);图左图右2、扭矩检测a、焊接强度扭矩检测示意图:扭矩试会示意图b、检测时机:日常生产的首中末件;更换操作者时;更换新的电极时;设备故障维修后;应品质检测临时需要时c、扭力检测对象:原则上采用生产的零件进行检测,检测后需增加保护焊对检测过的螺母进行加固。
d、凸焊螺母扭力检测值对应表:凸焊螺母扭力检测值对应表(单位:N- m)三螺母规格M4 M5 M6 M8 M10 M12 M14 M16 材料厚度0.6 〜0.7 25 25 32 40 55 -- -- --0.8 30 30 40 30 65 70 70 701.0 30 30 45 55 70 80 80 801.2 40 40 50 60 85 95 100 1201.6 40 40 55 70 90 110 120 1302.0 40 40 55 75 105 115 130 1502.3 40 40 55 75 110 130 130 1502.3 〜6.0 40 40 55 75 110 145 130 150 注:当材料厚度介于此表相邻材料厚度之间时,以较大者为检测参考标准。
3.2 点焊检验

第五节 点焊检验电阻焊的问题之一是没有适当的无损检验方法。
因此,在实际生产中,经常采用过程控制、外观和非破坏性的强度检验、焊点破坏性试验等来保证点焊接头的质量。
虽然外观和非破坏性的牢度检验并不可靠,但因其简单易行,也可以发现诸多焊接质量问题,因此在实际生产和质量控制过程中应用最广。
为了比较准确地判断焊接质量是否合格,进行焊接接头的破坏性试验是必要的。
焊接接头的破坏性试验方法,有机械试验法、现场试验法和金相检验法等,前者使用机械性能试验机测定拉剪、拉开、压缩、扭转、冲击等性能,而剥离、压缩、扭转、旋绞等是不使用试验机的现场试验法。
机械试验法的缺点是用适当形状的试件,并要把试件夹持在试验机的一定位置上,其优点是能够显示出性能数值。
与此相反,现场试验法的优点是操作非常简单,快速而成本低,其缺点是只能是定性检验,大部分不能显示性能数值,而且试验条件也不恒定。
金相检验则用来测定熔核尺寸和鉴定焊接缺陷。
一、点焊主要缺陷及可能原因接头外部或内部缺陷是评定点焊接头质量的另一重要指标。
点焊缺陷分表面缺陷及内部缺陷(未焊透、不穿透裂纹、缩孔等)。
表面缺陷可以通过外部观察发现,内部缺陷则较难发现。
点焊最危险的缺陷是未焊透(熔核未形成或尺寸太小),使接头强度剧烈下降。
一般点焊缺陷的类别及其产生原因见表所示2-6。
表2-6 点焊缺陷的类别及其产生原因缺陷类别 简图缺陷对焊接质量的影响缺陷主要产生原因1.未焊透 (1)没有熔核 (2)焊核尺寸很小零件表面烧坏1. 零件清理不好,或者由于过脏 2. 压力太小3. 焊接电流过大、时间过长3.内部飞溅4.烧穿压坑深度∆>0.25时,降低焊接强度零件过热,电极间压力过大和内部喷溅6.缩孔降低强度压力不足,过硬规范二、检验试件点焊的破坏性检验中,在直接使用焊接零件进行检验不合适时,常用检验点焊试件来推断焊件的点焊质量,此时试件的制作主要应注意下面两点:a)焊接条件不变;b)材料取自同一板材或卷材。
焊接拉脱力试验标准

焊接拉脱力试验标准
焊接拉脱力试验标准值分为以下两种:
1.电阻点焊钢接头的最低剪切拉力。
DL为基本金属的抗拉强度
Rm≤360MPa;每个焊点的最低剪切拉力(kN)。
2.电弧焊钢接头的最低剪切拉力。
DL为基本金属的抗拉强度
Rm>360MPa;每个焊点的最低剪切拉力(kN)。
焊接拉脱力试验是一种检测焊接强度的试验方法。
标准中心汽车减振器焊接强度标准内容规定:对于吊环联接式减振器,通常用拉脱力的方法来检测其焊接强度;对于转向联接式减振器的焊接强度通常用熔深的方法来做评价。
无铅焊点检验规范
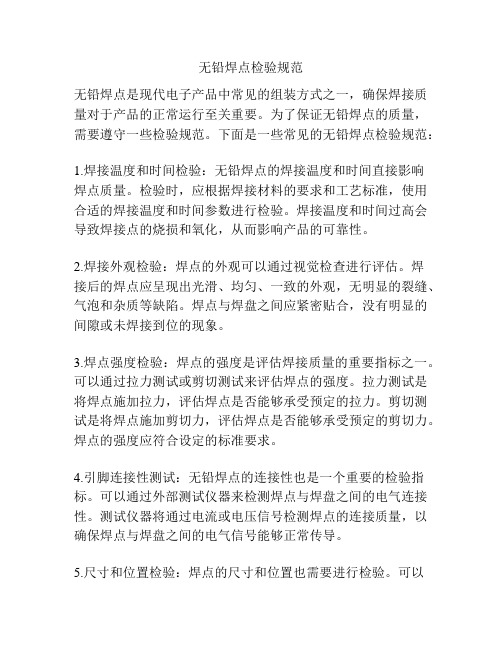
无铅焊点检验规范无铅焊点是现代电子产品中常见的组装方式之一,确保焊接质量对于产品的正常运行至关重要。
为了保证无铅焊点的质量,需要遵守一些检验规范。
下面是一些常见的无铅焊点检验规范:1.焊接温度和时间检验:无铅焊点的焊接温度和时间直接影响焊点质量。
检验时,应根据焊接材料的要求和工艺标准,使用合适的焊接温度和时间参数进行检验。
焊接温度和时间过高会导致焊接点的烧损和氧化,从而影响产品的可靠性。
2.焊接外观检验:焊点的外观可以通过视觉检查进行评估。
焊接后的焊点应呈现出光滑、均匀、一致的外观,无明显的裂缝、气泡和杂质等缺陷。
焊点与焊盘之间应紧密贴合,没有明显的间隙或未焊接到位的现象。
3.焊点强度检验:焊点的强度是评估焊接质量的重要指标之一。
可以通过拉力测试或剪切测试来评估焊点的强度。
拉力测试是将焊点施加拉力,评估焊点是否能够承受预定的拉力。
剪切测试是将焊点施加剪切力,评估焊点是否能够承受预定的剪切力。
焊点的强度应符合设定的标准要求。
4.引脚连接性测试:无铅焊点的连接性也是一个重要的检验指标。
可以通过外部测试仪器来检测焊点与焊盘之间的电气连接性。
测试仪器将通过电流或电压信号检测焊点的连接质量,以确保焊点与焊盘之间的电气信号能够正常传导。
5.尺寸和位置检验:焊点的尺寸和位置也需要进行检验。
可以使用量具或显微镜来测量焊点的尺寸和位置,确保焊点符合设计要求和规范要求。
综上所述,无铅焊点的检验规范包括焊接温度和时间检验、焊接外观检验、焊点强度检验、引脚连接性测试以及尺寸和位置检验等。
通过遵守这些检验规范,能够确保无铅焊点的质量和可靠性,提高产品的使用寿命和性能。
无铅焊点的质量是电子产品的重要保障,因此需要严格遵守相关的检验规范以确保焊点的质量和可靠性。
下面将继续介绍相关的内容:6.焊点表面光洁度检验:焊点的表面光洁度对焊接质量有着重要影响,因为高光洁度的焊点可以提供更好的连接性和稳定性。
检验时,可以使用显微镜或光学仪器来评估焊点表面的光洁度。
JIS_Z_3136-1999电阻点焊及凸焊焊接接头剪切试验的试验片尺寸及试验方法中文版

Z3136: 1999前言本标准是依据工业标准化法,经日本工业标准调查会的审议,由日本通商产业大臣修订的日本工业标准。
因此,JIS Z3136:1989经修改由本标准替代。
本次的修订,为了与国际标准接轨,以ISO/DIS 14273:1989作为基础。
日本工业标准 JISZ 3136:1999电阻点焊及凸焊焊接接头剪切试验的试验片尺寸及试验方法序文本标准是在1989年发行的ISO/DIS 14273 的基础上编制的日本工业标准,其对应部分(试验片、试验装置、试验顺序及记录)等技术方面的内容没作变更,但追加了如下规定内容。
a) 关于试验片尺寸,从前规定的“常规板宽试验片”和ISO/DIS 中规定的“饱和板宽试验片”并用。
b) 关于试验片的个数,以ISO/DIS 中规定的11个为基础,当不需要标准偏差时,可经当事者之间协商后减少之。
c) 对3张重叠以上的焊接接头试验片做了规定。
1 适用范围本标准对金属的点焊及凸焊焊接接头在如下方面做了规定:厚度0.3—5.0mm具有不超过片的试验方法。
2 引用标准本标准引用的标准如下,这些被引用的标准可作为构成本标准的一部分,这些被引用的标准适用最新版本。
JIS Z 2241 金属材料抗拉试验方法 JIS Z 3001 焊接用语JIS Z 8041 数值的归纳方法 3 定义本标准中所使用的主要用语的定义依据JIS Z 3001 及如下规定。
a) b) c)d)饱和板宽试验片当已给出焊接直径、试验片厚度及重叠代时,随着板宽的增加,试验得到的剪切力的值也会增加,直至达到饱和值。
在本标准中,饱和板宽试验片是指这样的试验片:具有与5根号t焊接直径时的饱和值相对应的板宽。
图1 剪切试验时的主要断裂形式和焊接直径上图中的焊接直径均按下面的公式求得D=(d1+d2)/24试验片4.1试验片的形状及尺寸试验片的形状如图2所示。
试验片的尺寸,常规板宽的试验片尺寸见表1,饱和板宽的试验片的尺寸见表2。
电阻焊焊点检测方法及要求

最小板厚/mm 0.60 0.70 0.75 0.80 0.85 0.90 1.00 1.20
最小焊点直径/mm 3.1 3.3 3.5 3.6 3.7 3.8 4.0 4.4
序号 9 10 11 12 13 14 15 16
最小板厚/mm 1.25 1.50 1.75 2.00 2.25 2.50 2.75 3.00
熔核直径≥最小熔核直径,焊核边 缘裂纹<100μm,熔核中心裂纹< 300μm
熔核直径≥最小熔核直径, 300μm≤熔核中心裂纹≤500μm
不合格
熔核直径<最小熔核直径,或熔核 边缘裂纹≥100μm,或熔核中心裂 纹>500μm
注:热影响区、熔核结合线上不允许出现裂纹
气孔评价说明
气孔直径<10%熔核直径,必须保证剥 离实验结果为合格。
最小焊点直径/mm 4.5 4.9 5.3 5.7 6.0 6.3 6.6 6.9
焊点质量要求
熔核尺寸 核直径只能通过测量金相试样来获得。
序号 1 2 3 4 5 6 7 8
最小板厚/mm 0.60 0.70 0.75 0.80 0.85 0.90 1.00 1.20
最小熔核直径/mm 2.7 2.9 3.0 3.1 3.2 3.3 3.5 3.8
电阻焊焊点检测方法及要求
电阻焊焊点常用检验方法 破坏性检验
非破坏性检验
剥离实验 抗剪实验 金相实验 目视检查 凿测实验 超声波检测
常用检验方法说明
目视检查
通过目视检查来初步判别,例如表面裂纹、位置偏差、边缘焊点以及漏焊等
凿测实验
是典型的非破坏性实验,通常用于检查虚焊和熔核过小的焊点,不要求通过这种方法来确定焊点尺寸。 注:凿测实验是将凿子楔入相邻焊点的板材之间(不能对准焊点进行凿测,凿子距离焊点 3~10mm) 剥离实验 是一种典型的破坏性实验,是将焊点从连接板材处分开,通过测量焊点直径大小来评价电阻点焊的质量。 注:对于焊核直径需多次测量,取平均值。 抗剪实验 确定焊点强度是否符合要求,该实验通常使用专用仪器来进行。 注:1、由于取自白车身的试样难以保证合适的装夹尺寸,因此抗剪试样多采用标准试片
金属剪切强度测试方法

金屬剪切強度測試方法一、金属剪切强度测试的重要性。
1.1 金属在我们的生活和工业生产中无处不在,从小小的螺丝钉到庞大的桥梁建筑。
而剪切强度就像是金属的一种“抵抗力”,它关系到金属在承受横向力时会不会被轻易剪断。
比如说,汽车发动机里的一些零部件,在高速运转过程中会受到各种力的作用,如果这些部件的金属剪切强度不够,那就很容易出故障,这可就像一颗定时炸弹,随时可能让汽车抛锚。
1.2 对于建筑行业来说,金属结构的剪切强度更是关乎安全的大事。
像高楼大厦的钢梁,如果剪切强度不过关,在遇到大风或者地震等外力时,就可能像脆弱的树枝一样被折断,那后果不堪设想。
这就好比建房子不打牢地基,是在拿大家的生命安全开玩笑。
二、常见的金属剪切强度测试方法。
2.1 单剪试验。
这种试验方法相对比较直接。
我们把金属试样固定在专门的夹具上,然后施加一个横向的力,就像用剪刀剪纸一样。
这个力要持续增加,直到试样被剪断。
在这个过程中,我们通过测量仪器记录下力的大小等数据。
就像给金属来一场力量的考验,看看它能承受多大的“剪刀力”。
不过呢,这种方法有时候会受到试样形状和夹具的影响,如果试样或者夹具有点小毛病,那测试结果可能就不太准确了,就像厨师做菜,锅不好使,炒出来的菜味道也可能受影响。
2.2 双剪试验。
双剪试验就像是给金属来了个双面夹击。
有两个剪切面同时受力,这样能更全面地测试金属的剪切强度。
它的原理和单剪试验类似,但是在数据处理上可能会稍微复杂一点。
打个比方,单剪试验是一个人单挑,双剪试验就是两个人打配合。
这种方法在测试一些形状规则、对称性较好的金属试样时特别有用。
但是呢,它对夹具的要求也比较高,如果夹具安装得不好,就像两个人配合不默契,那测试结果也会大打折扣。
2.3 扭转剪切试验。
这个试验有点特别,它不是直接横向剪切,而是通过扭转的方式来产生剪切力。
想象一下拧毛巾的动作,只不过我们拧的是金属试样。
这种方法对于一些需要承受扭转力的金属构件的测试很有意义。
焊接强度试验基准
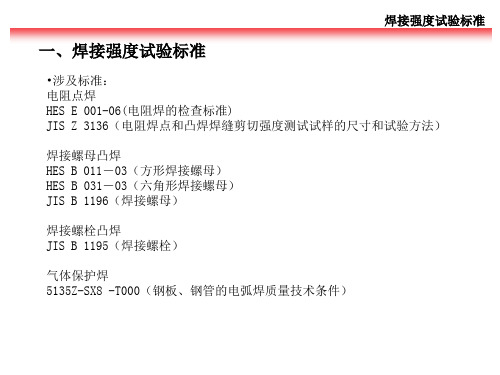
4 螺丝刀检查
5 非破坏检查
6 破坏检查
焊接直径 熔核直径
点焊试验项目
试验状态
试验方法
判定基准
A级
试 片
B级
C级
A级
试 片
B级
C级
A级
50个 20个 5个 5个 - 100个 50个 20个
HES E001-4.1.1 HES E001-4.2.1 HES E001-4.3.1
焊接螺栓凸焊 JIS B 1195(焊接螺栓)
气体保护焊 5135Z-SX8 -T000(钢板、钢管的电弧焊质量技术条件)
焊接强度试验标准
1、电阻点焊强度试验标准
电阻点焊的试验项目依据HES E 001来确定。
NO .
项目
1 抗拉剪切强度
2
断面 检查
3
外观 检查
熔核直径 溶深 内部缺陷 裂纹、飞溅、凹陷 等外部缺陷
检查频率 - -
认可测试 受入检查及工程检查
受入及工程检查 至少每批一次
工程间检查 初物检查
工程间检查、初 物检查至少各一 次
工程间检查 初物检查
工程间检查、初 物检查至少各一 次
工程间检查 量产准备阶段(工艺参数确认) (需要提供报告) 初物检查
工程间检查依据 工厂的质量管理 规定量产准备阶 段都做
判断基准 无裂纹 焊道无破损
凹痕+气孔 长度率28%以下
无裂纹 5135Z-SX8 -T000 2
焊接强度试验标准
一、焊接强度试验标准
•涉及标准: 电阻点焊 HES E 001-06(电阻焊的检查标准) JIS Z 3136(电阻焊点和凸焊焊缝剪切强度测试试样的尺寸和试验方法)
焊接强度试验及判定规范
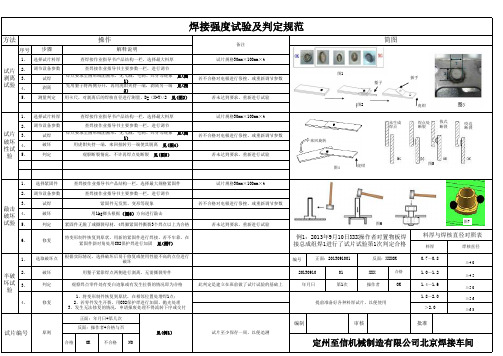
判定
紧固件无脱了或撕裂母材,4焊脚紧固件撕裂3个焊点以上为合格
6、
修复
将变形制件恢复到原状,用新的紧固件进行焊接,若不牢靠,在 紧固件斜对角处用CO2保护焊进行加固 见(图7)
1、
选取破坏点
根据实际情况,选择破坏后易于修复或使用性能不高的点位进行 破坏
半破 2、
破坏
坏试 3、
判定
验
4、
修复
用錾子紧靠焊点两侧进行剥离,无需撕裂零件
见(图 见(图
5、 测量判定 用卡尺,对剥离后的焊核直径进行测量,D=(X+Y)/2 见(图3)
备注 试片规格30mm×100mm×t 若不合格对电极进行俢挫,或重新调节参数 若未达到要求,重新进行试验
简图
图1 錾子
图2
扳手 虎钳
1、 选择试片料厚
查焊接作业指导书产品结构一栏,选择最大料厚
2、 调节设备参数
查焊接作业指导书主要参数一栏,进行调节
试片 3、 破坏 性试 4、
试焊 破坏
焊点要求呈圆形或团圆形,无飞溅、毛刺、焊穿等现象 见(图 1)
用虎钳夹持一端,来回扭转另一端使其脱离 见(图4)
验 5、
判定
观察断裂情况,不许再焊点处断裂 见(图5)
试片规格30mm×100mm×t 若不合格对电极进行俢挫,或重新调节参数
若未达到要求,重新进行试验
来回旋转
图4
虎钳
未生成 焊点
焊点处 断裂
拔式 断裂
咬边 断裂
图5
1、 选择紧固件
查焊接作业指导书产品结构一栏,选择最大规格紧固件
2、 调节设备参数
查焊接作业指导书主要参数一栏,进行调节
3、
焊点质量检测方法

焊点质量检测方法1.1 目视检测目视检测时最常用的一种非破坏性检测方法,可用万能投影仪或10倍放大镜进行检测。
检测速度和精度与检测人员能力有关,评价可按照以下基准进行:(1)湿润状态钎料完全覆盖焊盘及引线的钎焊部位,接触角最好小于20°,通常以小于30°为标准,最大不超过60°。
(2)焊点外观钎料流动性好,表面完整且平滑光亮,无针孔、砂粒、裂纹、桥连和拉尖等微小缺陷。
(3)钎料量钎焊引线时,钎料轮廓薄且引线轮廓明显可见。
1.2 电气检测电气检测是产品在加载条件下通电,以检测是否满足所要求的规范。
它能有效地查出目视检测所不能发现的微小裂纹和桥连等。
检测时可使用各种电气测量仪,检测导通不良及在钎焊过程中引起的元器件热损坏。
前者是由微小裂纹、极细丝的锡蚀和松香粘附等引起,后者是由于过热使元器件失效或助焊剂分解气体引起元器件的腐蚀和变质等。
1.3 X-ray检测X-ray检测是利用X射线可穿透物质并在物质中有衰减的特性来发现缺陷,主要检测焊点内部缺陷,如BGA、CSP和FC焊点等。
目前X射线设备的X光束斑一般在1-5μm范围内,不能用来检测亚微米范围内的焊点微小开裂。
1.4 超声波检测超声波检测利用超声波束能透入金属材料的深处,由一截面进入另一截面时,在界面边缘发生反射的特点来检测焊点的缺陷。
来自焊点表面的超声波进入金属内部,遇到缺陷及焊点底部时就会发生反射现象,将反射波束收集到荧光屏上形成脉冲波形,根据波形的特点来判断缺陷的位置、大小和性质。
超声波检验具有灵敏度高、操作方便、检验速度快、成本低、对人体无害等优点,但是对缺陷进行定性和定量判定尚存在困难。
扫描超声波显微镜(C-SAM)主要利用高频超声(一般为100 MHz以上)在材料不连续的地方界面上反射产生的位相及振幅变化来成像,是用来检测元器件内部的分层、空洞和裂纹等一种有效方法。
采用微声像技术,通过超声换能器把超声脉冲发射到元件封装中,在表面和底板这一深度范围内,超声反馈回波信号以稍微不同的时间间隔到达转化器,经过处理就得到可视的内部图像,再通过选通回波信号,将成像限制在检测区域,得到缺陷图。
HES焊接强度试验基准
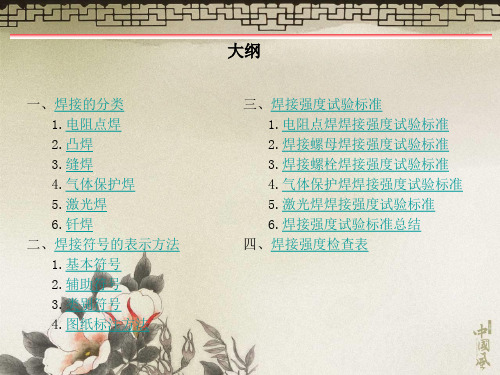
零件
HES E001-4.5.1 HES E001-4.5.2
零件
HES E001-4.6.1 HES E001-4.6.2
适用范围 认可测试
认可测试 (高强度钢板)
检查频率 -
-
认可测试 受入检查及工程检查
受入及工程检查 至少每批一次
工程间检查 初物检查
工程间检查、初 物检查至少各一 次
工程间检查 初物检查
电阻点焊的试验项目依据HES E 001来确定。
NO.
项目
1 抗拉剪切强度
2
断面 检查
3
外观 检查
熔核直径 溶深 内部缺陷 裂纹、飞溅、凹陷 等外部缺陷
压痕
4 螺丝刀检查
5 非破坏检查
6 破坏检查
焊接直径 熔核直径
试验状态
A级
试 片
B级
C级
100个 50个 20个
A级 5个
试 片
B级
5个
C级 -
A级
例: JSC780T 1.1t的抗拉剪切强度
=(780Mpa 1.0t的抗拉剪切强度+780Mpa 1.2t的抗拉剪切强度)/2
= (10724N+13274N)/2
=11999N
结论:11999N就是JSC780T 1.1t的抗拉剪强度的基准值。
-断面检查
•试片的制作 依据抗拉剪切强度的试片的形状及尺寸标准制作试片。 断面——焊点切割线尽可能的贴近焊点中心。 焊点的断面处理——进行研磨,用腐蚀液进行腐蚀。
焊接强度试验标准
•判定标准 依据HES A 1018 中规定,规格值查询表1所示。
板厚
焊接强度试验标准
电阻点焊强度试验标准
抗拉剪切强度试验
点焊破检试验标准-概述说明以及解释

点焊破检试验标准-概述说明以及解释1.引言1.1 概述:点焊破检试验是一种常用的焊接质量检验方法,通过对焊接接头进行破坏性的检验,可以有效评估焊接接头的强度和可靠性。
在工程实践中,点焊破检试验广泛应用于汽车制造、电子设备制造、航空航天等领域。
本文将从点焊破检试验标准的重要性、制定和演变以及应用领域等方面进行探讨,旨在为相关领域的从业者提供参考和指导。
通过深入了解点焊破检试验标准的内容和要求,可以更好地指导焊接工艺的改进和质量控制,提高焊接接头的质量和可靠性。
1.2 文章结构:本文主要分为三个部分来讨论点焊破检试验标准的相关内容。
首先,在引言部分中,将对点焊破检试验标准进行概述,并介绍文章的结构和目的。
接着,在正文部分,将分别探讨点焊破检试验标准的重要性、制定和演变过程以及应用领域。
最后,在结论部分将总结本文的观点,展望未来点焊破检试验标准的发展方向,并给出结束语。
通过这样的结构安排,读者可以全面了解点焊破检试验标准的相关内容,有助于加深对该主题的理解。
1.3 目的点焊破检试验标准旨在规范点焊工艺的检测方法,确保焊接质量和工艺稳定性。
通过明确的测试标准和流程,可以有效地评估点焊接头的质量,提高焊接的可靠性和稳定性。
同时,点焊破检试验标准还可以帮助制定适当的点焊焊接参数,减少生产中的缺陷率,提高产品的质量和可靠性。
通过本文的介绍和分析,旨在加深对点焊破检试验标准的理解,为实际生产中的点焊工艺提供指导和参考,推动点焊工艺的进步和发展。
2.正文2.1 点焊破检试验标准的重要性:在现代制造业中,点焊是一种常见的连接方法,特别是在汽车工业和电子行业中广泛应用。
点焊破检是用来验证点焊接头质量的一项重要测试方法。
准确的点焊破检试验标准可以确保点焊接头的可靠性和耐久性,减少产品出现点焊瑕疵的可能性,提高产品质量和生产效率。
点焊破检试验标准的重要性主要体现在以下几个方面:1. 保证产品质量:通过严格遵守点焊破检试验标准,可以确保点焊接头的质量符合规定的标准,避免因点焊不良而导致的产品质量问题,提高产品的可靠性和耐久性。
质量基础文件之———焊接强度的检查方法(下半部分)

凸焊螺柱焊接强度的检验一.概述1.凸焊螺柱通常为一个供焊接用的预制凸点,螺柱焊(stud welding)焊接过程是:将螺柱一端与板件(或管件)表面接触,螺柱与工件间通电引弧,工件被加热,待接触面熔化后,给螺柱一定压力,螺柱送入工件上的焊接熔池形成焊接接头。
a.将焊接螺柱(或柱状金属)放置于焊接母材上b.提升焊接螺柱,同时导通电流,在焊接螺柱和焊接母材之间激发电弧,c.电弧将焊接螺柱端部和焊接母材表面溶化,并形成焊接熔池;d.焊接螺柱和焊接母材相对运动,焊接螺柱在外力作用下以一定速度受控地插入熔池;e.焊接电流终止,电弧熄灭,同时熔池凝固,焊接过程完成,形成全断面熔合的焊缝2.螺柱焊接优点:①焊接在瞬间完成,提高了焊接工作效率,非常节省时间;②所有螺柱焊的结构不用钻孔,冲孔,标准的螺柱是低成本的,所以非常节省成本③可适应多种金属材料;④热影响区小,焊接母材变形小;⑤焊接损伤很小,母材背面没有或只有很小的焊接损伤;⑥保持中空零件的密闭性;⑦实现单面焊接;⑧操作简便。
正因为上述优点,所以螺柱焊在称身焊接中使用较广泛。
4.(以下内容仅作了解)螺柱根据公称直径的不同,长度的不同,丝牙(螺纹)的不同,凸点种类的不同等分类较多,常见的螺柱类型见下列图片3.对于端面凸焊螺栓来说,其敲检,套管扳检和判定方法与凸焊螺柱相同。
序号项目二.凸焊螺母焊接强度的检查敲检要求敲检时机使用工具内容1 23当螺柱熔融端与钣金的焊接面有间隙时焊接强度不够的可能性较大,建议进行敲检。
①达到工艺或检验文件规定的敲检频次时;②人、机、料、法、环任一因素发生变更时;③焊点外观质量极差,怀疑焊接强度不够时。
螺柱焊接强度检查使用的工具有:榔头(或锤子),对应规格的螺母,螺柱套管(内径7至10mm或比螺柱直径大1.5至5mm),扭力扳手,对应规格的套筒,记号笔,相机。
或序号项目螺柱的半破坏敲检内容4根据使用工具的不同或差异,具体操作有以下三种方式可供选择①橡胶榔头直接敲击:此种方式对螺纹基本无损伤,但操作起来相对费力。
焊缝强度质量测试操作规程

1.检验人员做强度测试过程中应该确定样件是否装夹牢固;
2.破坏性实验过程中,工件左右以及前面不允许有人以免工件飞出砸伤人。
编制
审核
批准
日期2006年12月01日编号GTI-SHG-WT-01-intensity
焊接测试文件WT Test Document
文件编号
WT0207-003
版本
A
文件名称:焊缝强度质量测试操作规程
页码
1/1
生效日期
2006.12.01
样件示意图如下:
编制
审核
批准
三.试验方法
1.首先设定好用于测试的焊机的参数:电流45~70A,电压21~28V,气量10~15,送丝速度0.33~0.75m/10s。
2.组织工人进行焊接。将6mm厚钢板水平放置于平台上,然后将2mm厚钢板150mm长的一边垂直放其上面,先用焊枪将接触面两端点焊固定,然后开始焊接。再两钢板接触端任一面开始焊接,焊缝长度50mm左右,位置尽量靠近中部。每个焊工需要完成两套样品的焊接。
日期2006年12月01日编号GTI-SHG-WT-01-intensity
焊接测试文件WT Test Document
文件编号
WT0207-003
版本
A
文件名称:焊缝强度质量测试操作规程
页码
1/1
生效日期
2006.12.01
一.目的
对焊接产品的焊缝强度质量进行认定
二.所需材料
150×100×2与150×150×6钢板各一块组成一套,每位焊工需要两套;成组焊机若干;台钳;榔头。
3.焊接过程中的目测样件不容许有漏焊、不能有明显的焊透、焊缝表面应均匀平整;焊接收弧应合理,不能有凹坑或者走弧距离不够等缺陷。对目测不合格的,我们需要及时的对其进行纠正,并要求其进行重新焊接试样。目测合格后对每个焊工所焊接的样件做上相应标识,以便实验中的追溯。
HES焊接强度试验基准
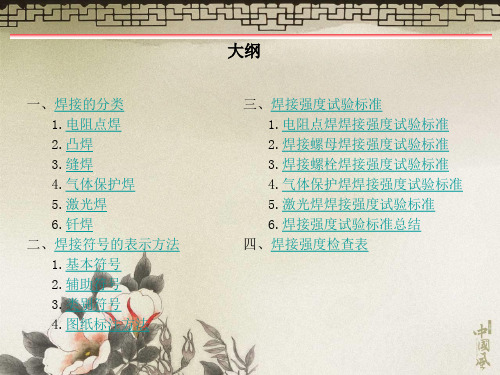
查表:等级780Mpa/1.0t的抗拉剪强度(d)=10724N(参照附表1 中d)
由下列等式得抗拉剪强度(X)
(X)=(f) x t2/ t1=3998N x 2.3t/1.0t=9195N<10724N(d)
比较(X)和(d),用较小值作基准。
结论:9195N就是基准值。
B.当钢板厚度为两个相邻板厚的中间值时,取相邻板厚的抗拉剪强度的平均值。
焊接的分类
4、气体保护焊
•定义: 属于电弧焊类。利用气体在电弧周围形成局部的保护层,保护金属熔滴、焊接 熔池和焊接区高温金属不受空气的氧化作用影响的焊接过程,简称气体保护焊。 常用的保护气体:惰性气体(如氩气、氦气)、还原性气体(如氢气、氮气)、 氧化性气体(如二氧化碳等)。 •特点: 1.气体保护层,防止有害于熔滴和熔池的气体侵入,保证焊接过程的稳定。 2.由于保护气体对弧柱有压缩作用,使电弧热量集中,熔池体积小,因而,其 焊接热影响区和焊接变形都比其他电弧焊和气焊小。
四、焊接强度检查表
一、焊接的分类
焊接的分类
在众多的焊接工艺中,广州本田汽车车身零部件和白车身焊接主要有
电阻点焊、凸焊、缝焊、二氧化碳气体保护焊、氩弧惰性气体保护焊、激 光焊等方式。
1、电阻点焊
•点焊的定义: 连接钢板的一个过程。 钢板放置于电极之 间,热量通过钢板的接口产生,当施加压力 时发生局部焊接。
电阻点焊强度试验标准
抗拉剪切强度试验
公称板厚的选取:
1.在板厚和材质不同钢板焊接时,计算钢板抗拉强度与钢板厚 度的积,取积较小的钢板厚度作为公称板厚。
2.三层以上焊接时,试片的形状为图3,尺寸按照表1。这种情 况下的剪切强度试验,如图3a)、b)所示,要在相关部件材质间 进行。