FEMA失效模式分析 ppt课件
合集下载
FMEA失效模式及后果分析(PPT 148页)

MEA
进行FMEA必须了解失效链:
水箱支架断裂(起初原因)→水箱后倾→水箱 与风扇碰撞→水箱冷却水管被风扇刮伤→水箱 冷却液泄漏→冷却系统过热→发动机气缸损坏 →汽车停驶(最终结果)
MEA
在APQP或项目管理中,有不同的阶段,各阶段分别如下: DFMEA与PFMEA是输出也是输入
概念 项目批准 提出/批准
样件
试生产
投产
策划 产品设计和开发 过程设计和开发
策划
D-FMEA产品设计与开发的输出 是过程设计的输入
产品与过程确认 P-FMEA过程设计与开发的输出 是产品和过程确认的输入
起因是什么?
有可能被预防和 探测吗?
可以做些什么?
A设计变更? B过程变更? C特别的控制? D使变更标准化或
成为指导方针?
部分/全部的 功能降低
探测的方法有多好?
功能间隔工作
非预期的功能
MEA
FMEA共同的因素:
功能框图或过程流程图(用于PFMEA) 产品或过程要执行的功能是什么?
结合
产品或过程功能失效的表现是怎样的? 顾客如何确认失效? 失效产生的后果多严重? 什么引起失效?
潜在 失效 后果
严重度分类
潜在失效
起因/机 理
现行过程控制
频 度
预防 探测
探 R 建议
测P 度N
措施
责任 和目 标完 成日 期
措施执行结果
采取 措施
严 频 探R
重 度
度
测P 度N
功能 特性或 要求是 什么
有多严重? 影响是什么?
发生的机率 有多高?
可以做些什么?
A设计变更? B过程变更? C特别的控制? D使变更标准化或
FMEA失效模式及后果分析PPT课件
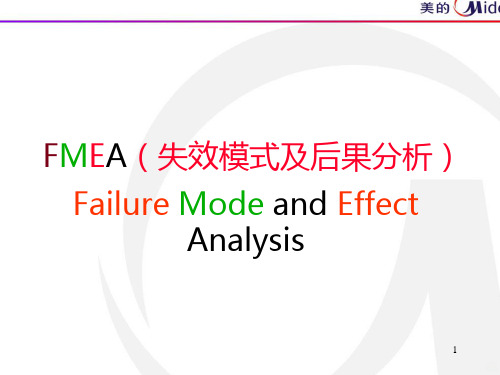
弯曲 断裂 脏污 短路 表面粗糙
毛刺 转运损坏 变形 开路 开孔太深
孔错位 漏开孔 表面太光滑
失效模式应以规范化技术术语描述, 不同于顾客察觉的现象
32
潜在失效的后果
对最终 使用者
噪音 粗糙 费力 工作不正常 异味
渗漏 不能工作 报废 外观不良
对下道 工序
无法紧固 不能配合 不能连接 无法安装 损坏设备 危害操作者
•1960’s-70’s第一次被注意和使用在工程可 靠性 •多方小组准备对产品/过程潜在失效模式和产 品性能影响的文件化体系 •评定产品或过程潜在失效模式的文件,采取 相应措施来消除或降低潜在失效的影响
7
典型的FMEAs
系统
设计
过程
部件 子系统 主系统
部件 子系统 主系统
注意:将系统的 失效模式降为最小
-后果到底有多糟? •O=Likelihood of Occurrence 频 度
-经常发生吗? •D=Likelihood of Detection 探测 度
18
RPN 流程
来自经验和数据
来自预测
DFMEA
项目/功能
潜在 失效模式
潜在 失效后果
严 重级 度别
潜在失效 的起因/机理
频 度
现行 设计控制
10
FMEA 小组
小组 • 为完成同一任务或目标的两个或更多的共同
行动的个体 集体讨论 • 发现许多可能存在和可能发生情况需要小组
的集体讨论
11
成功的FMEA 小组
•控制方向和焦点 •建立自身的统一性 •负责并使用测量方 法 •有全体的支持 •是横向多功能小组
12
FMEA 小组的守则
• 决定前召开小组会议 • 决定谁将参加 • 预先准备议题 • 主张进行会议笔记或记录 • 建立基本准则 • 遵守事先的议程 • 评价会议 • 不允许中断
潜在失效模式分析FMEA第五版教材ppt课件
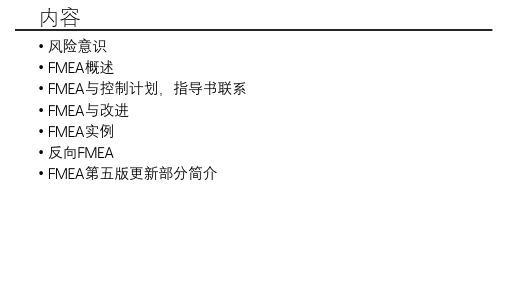
内容
• 风险意识 • FMEA概述 • FMEA与控制计划,指导书联系 • FMEA与改进 • FMEA实例 • 反向FMEA • FMEA第五版更新部分简介
P1/30
做任何事都可能失败,所以你必须提前做好预防! 生活中:做饭糊,起晚,迟到,丢东西,感冒。。。 工作中:算错账,发错货,忙到忘记重要的工作。。。 设备:跳闸,断电,未知原因的停止工作。。。 教育训练:内容不合适,讲解不到位,学员跑神。。。
Baby拿个杯子8--更容易掉
P15/30
FMEA概述
频度(O)
P16/30
FMEA概述
探测度(D)
杯子碎了我听不见也看不见
P17/30
FMEA概述
探测度(D)
P18/30
FMEA概述
风险顺序数(RPN)
综合的考虑三要素 严重度、频度、探测度 RPN=S×O×D
P19/30
FMEA概述
替代
用
系统分析
功能分析
• 定义功能 • 转化要求 • 顾客语言转化未技
术术语
失效分析
• 识别失效及其结构 • 识别变差源(原因) • 定义风险优先级
风险分析
• 预防及探测控制 • SOD打分 • 定义风险优先级
改进措施
• 基于风险优先级确 定该叫你措施
• 风险降低 • 持续改进
失效分析及风险降低
第五版取消RPN风险顺序数,增加了AP
验证所有失效模式之 后,考虑创造和发现 PFMEA中为考虑到的 新的失效模式
是
所有的失
否
效模式都
验证了吗?
P26/30
FMEA内容(第五版)
格式变更(六步法)
范围定义:确认项目
• 风险意识 • FMEA概述 • FMEA与控制计划,指导书联系 • FMEA与改进 • FMEA实例 • 反向FMEA • FMEA第五版更新部分简介
P1/30
做任何事都可能失败,所以你必须提前做好预防! 生活中:做饭糊,起晚,迟到,丢东西,感冒。。。 工作中:算错账,发错货,忙到忘记重要的工作。。。 设备:跳闸,断电,未知原因的停止工作。。。 教育训练:内容不合适,讲解不到位,学员跑神。。。
Baby拿个杯子8--更容易掉
P15/30
FMEA概述
频度(O)
P16/30
FMEA概述
探测度(D)
杯子碎了我听不见也看不见
P17/30
FMEA概述
探测度(D)
P18/30
FMEA概述
风险顺序数(RPN)
综合的考虑三要素 严重度、频度、探测度 RPN=S×O×D
P19/30
FMEA概述
替代
用
系统分析
功能分析
• 定义功能 • 转化要求 • 顾客语言转化未技
术术语
失效分析
• 识别失效及其结构 • 识别变差源(原因) • 定义风险优先级
风险分析
• 预防及探测控制 • SOD打分 • 定义风险优先级
改进措施
• 基于风险优先级确 定该叫你措施
• 风险降低 • 持续改进
失效分析及风险降低
第五版取消RPN风险顺序数,增加了AP
验证所有失效模式之 后,考虑创造和发现 PFMEA中为考虑到的 新的失效模式
是
所有的失
否
效模式都
验证了吗?
P26/30
FMEA内容(第五版)
格式变更(六步法)
范围定义:确认项目
过程FMEA失效模式及后果分析PPT培训课件

评估失效模式的 后果
确定失效模式的 严重程度…
制定预防和探测 措施
食品加工过程,包括原料 采购、加工、包装和储存 等环节。
例如,原料可能存在农药 残留、微生物污染等问题 ;加工过程中可能出现烘 烤不均匀、切割尺寸不对 等;包装过程中可能出现 标签错误、密封不严等。
例如,农药残留可能导致 消费者健康问题;烘烤不 均匀可能导致食品口感和 质量下降;标签错误可能 导致消费者对产品的误解 。
THANKS FOR WATCHING
感谢您的观看
跟踪实施效果
对改进措施的实施情况进行跟 踪和效果评估,持续改进。
02 过程FMEA的实施过程
确定分析范围和边界
确定分析对象
明确过程FMEA的分析对象,如产品、服务或系统 等,并定义其边界和范围。
确定分析阶段
确定失效模式可能发生的阶段,如设计、制造、 运输、安装等。
确定分析重点
根据分析对象和阶段,确定失效模式分析的重点 和关注点。
如何制定有效的改进措施和行动计划?
制定改进措施和行动计划是FMEA分析的最终目的。
根据风险优先级,选择具有最大潜在改进的失效模式进行改进。这可能包括设计更改、工艺改进、过 程控制强化等。制定行动计划时,应明确责任人、完成时间和检查点,以确保改进措施的有效实施。
如何持续改进FMEA分析?
持续改进FMEA分析可以提高其有效性和可靠性。
明确分析的对象,包括产品、系统、过程等,并对其进行 定义和描述。
列出所有可能的失效模式
全面考虑可能出现的失效模式,并对其进行分类和归纳。
评估失效模式的后果
分析失效模式可能导致的影响和后果,包括对产品、系统 、过程的影响以及对顾客的影响。
确定失效模式的严重程度、发生频率…
FMEA讲义课件
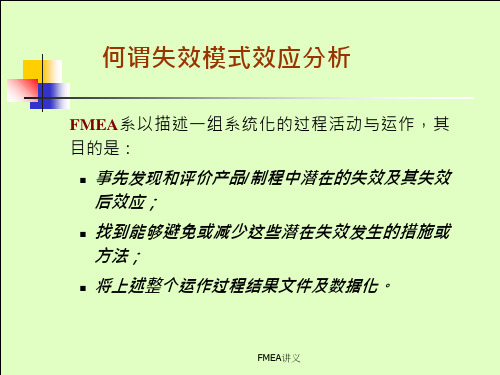
设计FMEA流程图
流 程
说 明
设计工程师应负责确认各项改正行动均经完成或均经通知负责人确实执行。
对RPN之项目应最优先采取必要措施,其目的在降低严重性、发生性及侦测性之分数。若不采有效之改正措施则制程FMEA之成效将受局限。
将风险领先指数做成柏拉图并决定建议之措施
将已采取之改正行动之内容及其完成日期填入记录,重新预估并记录改正后之严重性、发生性及侦测性之结果;计算新的RPN值。如果必要时,采取适当行动以降低RPN值。
9
很高
产品功能不能运作,丧失基本功能
8
高
产品功能能运作,但功能降低,顾客严重不满
7
中等
功能可运作,但舒适性及方便性降低,顾客使用时不满意
6
低
功能能运作,但舒适性及方便性降低,顾客使用时有些不满意
5
很低
如功能性、外观及结构等不合要求,大多数顾客注意到的了缺陷
4
微小
如功能性、外观等不合要求,一般顾客可注意到的缺陷
4
高
设计控制将会侦测出潜在原因/机制和随后的失效模式
3
非常高
设计控制有很高的机会侦测出潜在原因/机制和随后的失效模式
2
几乎肯定
设计控制几乎会侦测出潜在原因/机制和随后的失效模式
1
D-FMEA导入时机与展开
IN PUT
OUT PUT
产品主要功能
.
发生性系指预测该不良模式发生之频
度,不
良之
预防必须加以考虑
.
侦
测性系对该零件或装配件送交生产前,其可
能
存在之设计弱点是否能经设计
验证而查出之能
力
.
设计工程师应负责确认各项改正行动均经完成
FMEA失效模式与效应分析课件(PPT 40张)

經由 FMEA 分析後 的風險 值有多 大? RPN= S*O*D
功能、 特性或 要求是 什麼?
會有什麼問題? 無功能 部份功能/ 功能過強/ 功能降低 功能間歇 非預期功能
可能起 因是什 麼?
發生 的頻 率如 何?
能做些什 麼? 設計更改 過程更改 特殊控制 或規格的 更改
目前的 管制方 式為何?
FailureModeand EffectsAnalysis (FMEA)
失效模式效應分析及填寫
1
講授內容
一.FMEA基本概念 二.FMEA之演變
三.國際間採用FMEA之狀況
四.FMEA表填寫說明 五.FMEA結果之應用
2
FMEA的基本概念.
發生源>> 1.失效分析在找出零組件或系統的潛在弱 點,提供設計、製造、品保等單位採取 可行之對策。
關鍵的—符號以“▲”表示之;PPK或CPK管制—符號以“●”表示之 重要的—符號以“▓”表示之;客戶要求的—符號以“★”表示之
24
Hale Waihona Puke MEA填寫說明.(14)潛在原因/設備失效 1.潛在原因
錯誤的原物料規格。 不適當的的設計壽命假設。 潤滑或加油能力不足。 不適當的維護作業。 缺乏環境保護。 錯誤的算法。 超過壓力。
(1) FMEA編號:填入FMEA文件編號,以便可以追蹤使用。 (2) 系統、子系統及零組件:指示合適的分析等級,並填入系統 、子系統或零件名稱或零件名稱和編號。
(3) 設計責任者:填入OEM、部門和小組,也包括供應商名稱。
(4) 準備者:填入準備FMEA責任工程師的姓名、電話號碼、公司。 A.系統FMEA範圍: -底盤系統;-點火系統;-內部系統
2.設備失效
生產不良。 原物料材質不穩定。 磨損。 金屬疲勞。 裝備欠流暢。 腐蝕。
功能、 特性或 要求是 什麼?
會有什麼問題? 無功能 部份功能/ 功能過強/ 功能降低 功能間歇 非預期功能
可能起 因是什 麼?
發生 的頻 率如 何?
能做些什 麼? 設計更改 過程更改 特殊控制 或規格的 更改
目前的 管制方 式為何?
FailureModeand EffectsAnalysis (FMEA)
失效模式效應分析及填寫
1
講授內容
一.FMEA基本概念 二.FMEA之演變
三.國際間採用FMEA之狀況
四.FMEA表填寫說明 五.FMEA結果之應用
2
FMEA的基本概念.
發生源>> 1.失效分析在找出零組件或系統的潛在弱 點,提供設計、製造、品保等單位採取 可行之對策。
關鍵的—符號以“▲”表示之;PPK或CPK管制—符號以“●”表示之 重要的—符號以“▓”表示之;客戶要求的—符號以“★”表示之
24
Hale Waihona Puke MEA填寫說明.(14)潛在原因/設備失效 1.潛在原因
錯誤的原物料規格。 不適當的的設計壽命假設。 潤滑或加油能力不足。 不適當的維護作業。 缺乏環境保護。 錯誤的算法。 超過壓力。
(1) FMEA編號:填入FMEA文件編號,以便可以追蹤使用。 (2) 系統、子系統及零組件:指示合適的分析等級,並填入系統 、子系統或零件名稱或零件名稱和編號。
(3) 設計責任者:填入OEM、部門和小組,也包括供應商名稱。
(4) 準備者:填入準備FMEA責任工程師的姓名、電話號碼、公司。 A.系統FMEA範圍: -底盤系統;-點火系統;-內部系統
2.設備失效
生產不良。 原物料材質不穩定。 磨損。 金屬疲勞。 裝備欠流暢。 腐蝕。
FMEA失效模式及其影响分析(ppt 63页)
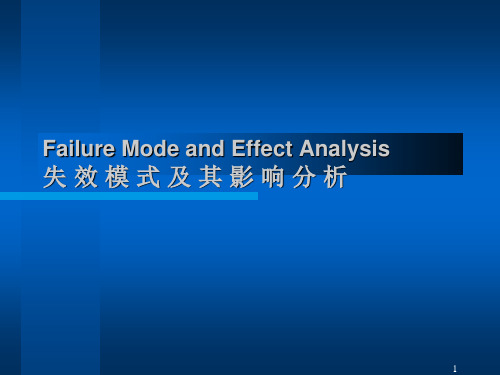
FMEA通常应用在工艺及产品设计的初期,自由讨论决定潜在失效的模式、原因、严重度及发 生的可能性。在6S中,我们应用FMEA去了解失效的模式。我们主要感兴趣的是原因及发生的 可能性。
FMEA is also a valuable tool for managing tasks during defect/failure reduction projects. FMEA也是一个在失效缩小的管理任务的有价值的工具。
When existing designs and processes are being changed
When carry-over designs or processes will be used in new applications or environments
After completing a Problem Solving Study, to prevent recurrence of a problem
Used sporadically throughout industry during 1980’s.
Adopted by MSI in ? Six Sigma is the catalyst.
NASA used FMEA to identify Single Point Failures on Apollo project (SPF = no redundancy & loss of mission). How many
FMEA is a systematic approach used to examine potential failures and prevent their
occurrence. It enhances our ability to predict problems and provides a system of ranking, or
FMEA is also a valuable tool for managing tasks during defect/failure reduction projects. FMEA也是一个在失效缩小的管理任务的有价值的工具。
When existing designs and processes are being changed
When carry-over designs or processes will be used in new applications or environments
After completing a Problem Solving Study, to prevent recurrence of a problem
Used sporadically throughout industry during 1980’s.
Adopted by MSI in ? Six Sigma is the catalyst.
NASA used FMEA to identify Single Point Failures on Apollo project (SPF = no redundancy & loss of mission). How many
FMEA is a systematic approach used to examine potential failures and prevent their
occurrence. It enhances our ability to predict problems and provides a system of ranking, or
FMEA失效模式和后果分析课件
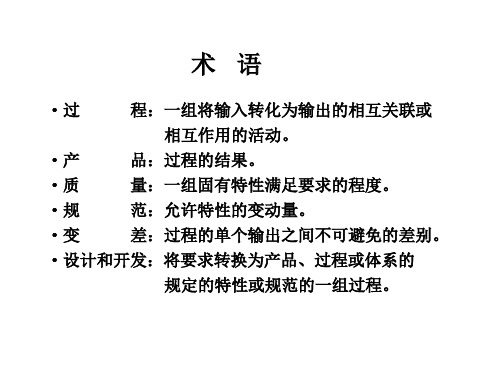
带来的知识增长 · 这一点本身就足够说明为什么要使用FMEA
FMEA小组
· 为什么?
- 经验共享 - 掌握知识 - 头脑风暴 - 有助于问题解决 - 理解上的共享 - 决策的一致
FMEA小组
· 技能和工具
- 小组成员理解赛程管理中使用的工具 - 有技巧的小组辅助人员 - 熟悉防错技术的小组成员 - 熟悉产品和过程相互关系的小组成员 - 建立、控制和维护输出的记录员和文档管理员
·设计FMEA:在产品正式生产发布之前分析潜在失效
- 关注于产品由于设计造成的和功能相关的潜在失效
·过程FMEA:用于分析制造和装配过程
- 专注于过程由于设计和操作造成的和功能相关的潜在失效模式
何时使用FMEA
·情况一:新设计,新技术或新过程
- FMEA的范围包括完整的设计,技术和过程
·情况二:现有设计和过程的更改(假设现有的设计和过程 FMEA已存在)
FMEA小组成功要点
· 管理层知识 · 有效培训 · 和任务相关的小组规模 · 范围不要太大 · 目标明确 · 过程明确 · 目标相关并且作用明显 · 确定小组绩效评估方法 · 充分的时间用于分析和改进 · 和企业的开发过程集成 · 输入的信息和数据易于获得
管理层职责
最终管理层拥有FMEA的开发和维护的权限和责任
什么是FMEA?
·FMEA是严密的分析过程有助一小组预测失效并防 止在设计和制造中发生
概念
识别产品和过程可能失效的方式,阐明后果 然后作出计划预防失效
顾客满意意味着——
Customer satisfaction means: Never having to say you’re sorry!
顾客满意意味着:决不要说对不起!
FMEA小组
· 为什么?
- 经验共享 - 掌握知识 - 头脑风暴 - 有助于问题解决 - 理解上的共享 - 决策的一致
FMEA小组
· 技能和工具
- 小组成员理解赛程管理中使用的工具 - 有技巧的小组辅助人员 - 熟悉防错技术的小组成员 - 熟悉产品和过程相互关系的小组成员 - 建立、控制和维护输出的记录员和文档管理员
·设计FMEA:在产品正式生产发布之前分析潜在失效
- 关注于产品由于设计造成的和功能相关的潜在失效
·过程FMEA:用于分析制造和装配过程
- 专注于过程由于设计和操作造成的和功能相关的潜在失效模式
何时使用FMEA
·情况一:新设计,新技术或新过程
- FMEA的范围包括完整的设计,技术和过程
·情况二:现有设计和过程的更改(假设现有的设计和过程 FMEA已存在)
FMEA小组成功要点
· 管理层知识 · 有效培训 · 和任务相关的小组规模 · 范围不要太大 · 目标明确 · 过程明确 · 目标相关并且作用明显 · 确定小组绩效评估方法 · 充分的时间用于分析和改进 · 和企业的开发过程集成 · 输入的信息和数据易于获得
管理层职责
最终管理层拥有FMEA的开发和维护的权限和责任
什么是FMEA?
·FMEA是严密的分析过程有助一小组预测失效并防 止在设计和制造中发生
概念
识别产品和过程可能失效的方式,阐明后果 然后作出计划预防失效
顾客满意意味着——
Customer satisfaction means: Never having to say you’re sorry!
顾客满意意味着:决不要说对不起!
FMEA-失效模式分析PPT课件
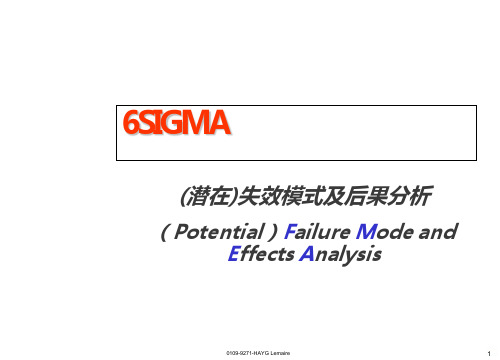
FMEA应用的必要性
外部压力:
• 技术进步与复杂化;
不只考虑正向 好处,应考虑
负向后果
• 产品的功能失效的后期探测难度大;
• 产品功能失效发生的后果灾难性严重;
• 客户对组织 控制、解决产品问题能力的信心需要。
FMEA应用的必要性
内部动力:
工程师知识 转化为公司
知识
• 预知缺陷、主动改善,减小风险和损失,降低成本;
6SIGMA
(潜在)失效模式及后果分析
(Potential)Failure Mode and Effects Analysis
0109-9271-HAYG Lemaire
1
(潜在)失效模式及后果分析
FMEA 为什么?
问题:
1、某机型计划在下个月导入一种新光驱,不知走目前的 导入流程/测试项目是否能保证其导入后不出现质量波动?
主要在于一种产品,这可能是一个系统,子系统或部件。 例:PC机、电源、硬盘
流程----P FMEA
这里的重点是一组程序(一系列步骤以达到确定的产出目标)。产 出通常是一种产品。 例:装配线、订单的输入
FMEA简介
例
FMEA简介
什么是FMEA?
可以应用FMEA的场合? (可针对改进项目)
课程内容
概念提出 和批准
1
QS9000-----APQP过程
图
项目批准
样件
试生产
投产
设计
策划
FMEA
2 产品设计和开发
过程 FMEA
3 过程设计和开发
4 产品和过程确认
5 生产
计划和确定 项目
产品设计和开 发验证
过程设计和 开发验证
FMEA完整教材潜在失效模式及后果分析ppt课件

初始 FMEA
修正 FMEA1
DFMEA必须在计划的 生产设计发布前
PFMEA必须在计划的 试生产日期前
各项未考虑的失效 模式的发现、评审 和更新
修正 FMEA2
时间
各项未考虑的失效 模式的发现、评审 和更新
20
一、FMEA的基本概念
FMEA表及开发顺序:
子系 统
潜在 失效 模式
功能
要求
潜在 失效 后果
有效运用 FMEA 可减少事后追悔
3
一、FMEA的基本概念
及时性是成功实施FMEA的最重要因素之一。 它是“事前的预防”而不是“事后的追悔”。 事先花时间进行FMEA分析,能够容易且低成本地对产品设计或 制程进行修改,从而减轻事后修改的危机。 FMEA能够减少或消除因修改而带来更大损失的机会,它是一个 相互作用的过程,永无止境的改善活动。
6
一、FMEA的基本概念
物品直接表现失效的形式如下:
1、实体破坏:硬式失效 2、操作功能终止 3、功能退化 4、功能不稳定
软式失效
2~4项物品机能因老化(Aging)、退化(Degradation)或不稳定 (Unstable)而不能满足原设定的要求标准,所以失效现象及研 判准则必须量化。
7
一、FMEA的基本概念
一、FMEA的基本概念
FMEA的跟踪:
• 采取有效的预防/纠正措施并对这些措施加以适当的跟踪,对这 方面的要求无论怎样强调也不算过分。措施应传递到所有受影响 的部门。一个经过彻底思考、周密开发的FMEA,如果没有积极 有效的预防/纠正措施,其价值将是非常有限的。
• 责任工程师负责确保所有的建议措施都得到实施或充分的强调。 FMEA是动态文件,应始终反映最新水平以及最近的相关措施, 包括开始生产以后发生的。
FMEA讲义失效模式效应分析课件
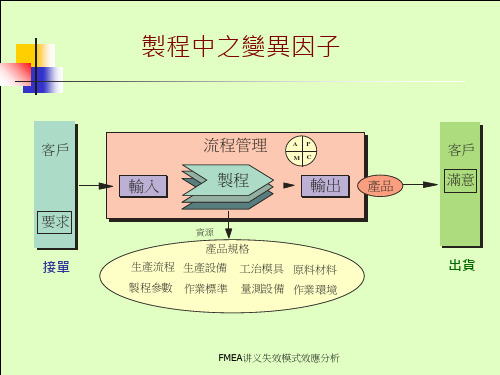
值。如果必要
時,採取適當行動以降低
RPN
值
‧對
RPN
之項目應最優先採取必要措施,其目的在
降低嚴重性、發生性及偵測性之分數。若不採
有
效之改正措施則製程
FMEA
之成效將受局限
‧嚴重性×發生性×偵測性
不良模式舉例:變
型、破裂、
影像模
糊
、
訊號不清
失效效應影響範例:
收訊不
穩定,操作不
靈,
當機
原因範例:
機殼
f
軟板
d
電池
座
b
面板
a
1
5
4
5
4
3
2
零件
a
.
面板
b
.
電池
座
c
.
按鍵
d
.
軟板
原型品管制計劃
製造流程圖 作業流程 作業內容 作業功能 驗明及研訂
製程監測及量產管制計劃定稿
量試
檢驗標準書研定
量試管制計劃
初期製程能力分析
量試檢討Process FMEA 對策驗證及修訂
量具、檢具、夾治 具、測試設備及相關生產設備規劃
量產
量、檢、測試設備變異分析及對策
FMEA 對策
原型品驗證 產品規格確認
度,不
良之
預防必須加以考慮
‧
偵
測性係對該零件或裝配件送交生產前,其可
能
存在之設計弱點是否能經設計
驗證而查出之能
力
‧
設計工程師應負責確認各項改正行動均經完成
或均經通知負責人確實執行
‧
將已採取之改正行動之內容及其完成日期填入
記錄,重新預估並記錄改正後之嚴重性、發生性
時,採取適當行動以降低
RPN
值
‧對
RPN
之項目應最優先採取必要措施,其目的在
降低嚴重性、發生性及偵測性之分數。若不採
有
效之改正措施則製程
FMEA
之成效將受局限
‧嚴重性×發生性×偵測性
不良模式舉例:變
型、破裂、
影像模
糊
、
訊號不清
失效效應影響範例:
收訊不
穩定,操作不
靈,
當機
原因範例:
機殼
f
軟板
d
電池
座
b
面板
a
1
5
4
5
4
3
2
零件
a
.
面板
b
.
電池
座
c
.
按鍵
d
.
軟板
原型品管制計劃
製造流程圖 作業流程 作業內容 作業功能 驗明及研訂
製程監測及量產管制計劃定稿
量試
檢驗標準書研定
量試管制計劃
初期製程能力分析
量試檢討Process FMEA 對策驗證及修訂
量具、檢具、夾治 具、測試設備及相關生產設備規劃
量產
量、檢、測試設備變異分析及對策
FMEA 對策
原型品驗證 產品規格確認
度,不
良之
預防必須加以考慮
‧
偵
測性係對該零件或裝配件送交生產前,其可
能
存在之設計弱點是否能經設計
驗證而查出之能
力
‧
設計工程師應負責確認各項改正行動均經完成
或均經通知負責人確實執行
‧
將已採取之改正行動之內容及其完成日期填入
記錄,重新預估並記錄改正後之嚴重性、發生性
- 1、下载文档前请自行甄别文档内容的完整性,平台不提供额外的编辑、内容补充、找答案等附加服务。
- 2、"仅部分预览"的文档,不可在线预览部分如存在完整性等问题,可反馈申请退款(可完整预览的文档不适用该条件!)。
- 3、如文档侵犯您的权益,请联系客服反馈,我们会尽快为您处理(人工客服工作时间:9:00-18:30)。
有多好?
34
6
跟催
采取有效的预防及矫正措施,以及针对这些行动的跟催是需要的,但不用过分 强求。应该和所有被影响的单位沟通措施行动。一个彻底周详考虑和充分开发 的FMEA如果没有实际有效的预防和矫正措施,其价值将有限。 担当职责的工程师是负责确保所有的建议措施都已经实施或适当的对策。 FMEA是一分份动态文件,应该始终反映出最终的评估,以及最终的适切措施, 包括那些在开始量产之后所发生的措施。 A.审查设计、过程和图样,确保建议措施已经被实施, B.确认该项变更编入设计/组装/制造文件中, C.审查设计/过程FMEAs、特别的FMEA应用和控制计划
5
圖一 潛 在 失 效 模 式 與 效 應 分 析 作 業 序 列
項 目 /失 效
潛在 失效模式
失效 潛在效應
嚴 重 度
等 級
潛在原因/ 失效機制
發 生 度
現行的 設計管制
預防 檢測
難R
檢P 度N
建議措施
責任與 目標
完成日期
行動結果
嚴難檢 R
採行措施 重 檢 驗 P
度度度 N
效應為可能出现问题的项目的分析)。这种系统化的方法体现
了一个工程师在任何设计过程中正常经历的思维过程,并使之规范化、
文件化。
8
设计FMEA能够透过以下几方面支持设计过程,以降低失效风险: .有助于对设计要求和设计方案进行客观评价; .有助于对制造和装配要求的最初设计; .提高在设计/开发过程中,考虑潜在失效模式及其对系统和运行冲击
当FMEAs被展开,会有三种基本的个案。每个案例都有不同的领域和重点: 个案1:新设计、新技术或新过程。该FMEA的领域是完成设计、技术或过 程。 个案2:修改现有的设计或过程(假设现有的设计或过程已经有一个FMEA)。该
FMEA的领域应该在于修改设计或过程,有可能因为某修改和市场历史 反映而有交互影响。 个案3:在一个新的环境、地点或应用上,利用的现有的设计或过程(假设现有 的设计或过程已经有一个FMEA)。该FMEA的领域是对现有设计或过 程新的环境或地点上的影响分析。
7
設 計FMEA
簡
介
设计FMEA主要是由负责设计的工程师/小组采用的一种分析技术,用
来保证在可能的范围内已充分地考虑到,并指明各种潜在的失效模式及
其相关的起因/机理。应该评估最终的产品以及每个与之相关的系统、
子系统和零组件。FMEA以其最严密的形式总结了设计一个零部件、子
系统或系统时,一个工程师和设计小组的设计思想(包括:根据以往的
POTENTIAL FAILURE MODE AND EFFECTS ANALYSIS
(FMEA)
失效模式分析
1
FMEA概要
何谓FMEA: 是描述为一组系统化的活动,其目的是: A:发现和评价产品/过程中潜在的失效及其失效效应 B:找到能够避免或减少这些潜在失效发生的措施 C:将上述整个过程文件化 它是对设计过程的更完善化,明确必须做何种设计和过程 才能满足顾客的需要。
9
顧客的定義
设计FMEA中“顾客”的定义,仅仅是指“最终使用者”,还包括负责车型设计 更高 一级装配过程设计的工程师/小姐,以及在生产过程中负责制造、装配和售后服 务的工程师。 FMEA全面实施要求对所有新的部件、更改的部件以及应用或环境有变化的沿用 零件进行设计FMEA。FMEA始于负责设计工作的工程师,但对有专有权的设计 来说,可能始于其供货商。
10
小組努力
在最初的设计FMEA过程中,负责设计的工程师被预期能够直接地、 主动地从所有有关部门来代表。这些专家和负责的领域应该包括, 但不限于:装配、制造、设计、分析/测试、可靠度、材料、质量、 服务和供货商,以及负责下一个较高阶或低阶的组装、系统、子系 统或零组件的设计部门。FMEA应该成为促进相关部门间充分交换意 见的催化剂,从而提高整个集体的工作水平。 除了负责工程师对FMEA具有经验和小组协助之外,在活动中拥有一 位有经验的FMEA专家以协助该小组是有一定帮助的。
4
在FMEA的编制工作中,必须明确的指派每个人的职责,但是FMEA的输入 还是应该依靠小组努力。小组应该由知识丰富的人员组成(如:对设计、分析 、测试、制造、装配、服务、回收再利用、质量及可靠度等方面的工程人员) FMEA由相关负责组织中的工程师所组成,其可以是OEM如:生产最终产 品、供货商,或是分包商。 如果去比较一个小组的FMEA评价和另一个小组的FMEA评价是不适当,既 使该产品或过程呈现了相同的状况;由于每个小组的所在环境是独一无二的 ,因此各自将会个别的评价(如:评价是主观的)。
模 式被无意地纳入产品或过程之前进行。事先花时间适当地完成FMEA分析,能 够更容易、低成本地对产品过程进行修改,从而减轻事后修改危机。
FMEA能够减少或消除原因进行预防和矫正而带来更大损失的机会。
FMEA小组应该有充分的沟通和整合。
3
图一描述了一个FMEA应该被执行的程序,它并不是简单的把表格填满的案 例,而是进一步理解FMEA的程序,以消除风险和计划能确保顾客满意 的适当控制。
2
FMEA的實施
由于尽可能的持续改进产品和过程是企业的趋势,所以使用FMEA作为专门技 术应用,以识别并帮助减少潜在的隐忧一直是非常重要的。对于产品抱怨的研 究结果表明,全面实施FMEA能够避免许多抱怨事件的发生。
适时性是成功实施FMEA的最重要因素之一,它是一个“事发前”的行为,
而不
是“后见之明”的行动。为打达到最佳效益,FMEA必须在设计或过程失效
的可能性; .为全面、有效的设计试验和开发项目的规划,提供更多的信息; .根据潜在失效模式对“顾客”的冲击,对其进行分级列表,进而建立 一
套设计改进、开发和查证的优先控制系统; .为建议和跟踪降低风险的措施,提供一个公开的讨论形式; .为将来分析研究售后巿场关切情况、评价设计更改及展开更先进的设
计提供参考。
什麼會錯誤? -- 無 功 能 -- 部 分 /過 多 /
降低功能 -- 間 歇 功 能 -- 不 預 期 功 能
原因為何?
其發生 頻率為何?
能夠做什麼? -- 設 計 變 更 -- 製 程 變 更 -- 特 別 管 制 -- 標 準 , 程 序 書
或指引變更
如何能 預防及發現
這種 原因及錯誤?
這種方法 發現這種問題
34
6
跟催
采取有效的预防及矫正措施,以及针对这些行动的跟催是需要的,但不用过分 强求。应该和所有被影响的单位沟通措施行动。一个彻底周详考虑和充分开发 的FMEA如果没有实际有效的预防和矫正措施,其价值将有限。 担当职责的工程师是负责确保所有的建议措施都已经实施或适当的对策。 FMEA是一分份动态文件,应该始终反映出最终的评估,以及最终的适切措施, 包括那些在开始量产之后所发生的措施。 A.审查设计、过程和图样,确保建议措施已经被实施, B.确认该项变更编入设计/组装/制造文件中, C.审查设计/过程FMEAs、特别的FMEA应用和控制计划
5
圖一 潛 在 失 效 模 式 與 效 應 分 析 作 業 序 列
項 目 /失 效
潛在 失效模式
失效 潛在效應
嚴 重 度
等 級
潛在原因/ 失效機制
發 生 度
現行的 設計管制
預防 檢測
難R
檢P 度N
建議措施
責任與 目標
完成日期
行動結果
嚴難檢 R
採行措施 重 檢 驗 P
度度度 N
效應為可能出现问题的项目的分析)。这种系统化的方法体现
了一个工程师在任何设计过程中正常经历的思维过程,并使之规范化、
文件化。
8
设计FMEA能够透过以下几方面支持设计过程,以降低失效风险: .有助于对设计要求和设计方案进行客观评价; .有助于对制造和装配要求的最初设计; .提高在设计/开发过程中,考虑潜在失效模式及其对系统和运行冲击
当FMEAs被展开,会有三种基本的个案。每个案例都有不同的领域和重点: 个案1:新设计、新技术或新过程。该FMEA的领域是完成设计、技术或过 程。 个案2:修改现有的设计或过程(假设现有的设计或过程已经有一个FMEA)。该
FMEA的领域应该在于修改设计或过程,有可能因为某修改和市场历史 反映而有交互影响。 个案3:在一个新的环境、地点或应用上,利用的现有的设计或过程(假设现有 的设计或过程已经有一个FMEA)。该FMEA的领域是对现有设计或过 程新的环境或地点上的影响分析。
7
設 計FMEA
簡
介
设计FMEA主要是由负责设计的工程师/小组采用的一种分析技术,用
来保证在可能的范围内已充分地考虑到,并指明各种潜在的失效模式及
其相关的起因/机理。应该评估最终的产品以及每个与之相关的系统、
子系统和零组件。FMEA以其最严密的形式总结了设计一个零部件、子
系统或系统时,一个工程师和设计小组的设计思想(包括:根据以往的
POTENTIAL FAILURE MODE AND EFFECTS ANALYSIS
(FMEA)
失效模式分析
1
FMEA概要
何谓FMEA: 是描述为一组系统化的活动,其目的是: A:发现和评价产品/过程中潜在的失效及其失效效应 B:找到能够避免或减少这些潜在失效发生的措施 C:将上述整个过程文件化 它是对设计过程的更完善化,明确必须做何种设计和过程 才能满足顾客的需要。
9
顧客的定義
设计FMEA中“顾客”的定义,仅仅是指“最终使用者”,还包括负责车型设计 更高 一级装配过程设计的工程师/小姐,以及在生产过程中负责制造、装配和售后服 务的工程师。 FMEA全面实施要求对所有新的部件、更改的部件以及应用或环境有变化的沿用 零件进行设计FMEA。FMEA始于负责设计工作的工程师,但对有专有权的设计 来说,可能始于其供货商。
10
小組努力
在最初的设计FMEA过程中,负责设计的工程师被预期能够直接地、 主动地从所有有关部门来代表。这些专家和负责的领域应该包括, 但不限于:装配、制造、设计、分析/测试、可靠度、材料、质量、 服务和供货商,以及负责下一个较高阶或低阶的组装、系统、子系 统或零组件的设计部门。FMEA应该成为促进相关部门间充分交换意 见的催化剂,从而提高整个集体的工作水平。 除了负责工程师对FMEA具有经验和小组协助之外,在活动中拥有一 位有经验的FMEA专家以协助该小组是有一定帮助的。
4
在FMEA的编制工作中,必须明确的指派每个人的职责,但是FMEA的输入 还是应该依靠小组努力。小组应该由知识丰富的人员组成(如:对设计、分析 、测试、制造、装配、服务、回收再利用、质量及可靠度等方面的工程人员) FMEA由相关负责组织中的工程师所组成,其可以是OEM如:生产最终产 品、供货商,或是分包商。 如果去比较一个小组的FMEA评价和另一个小组的FMEA评价是不适当,既 使该产品或过程呈现了相同的状况;由于每个小组的所在环境是独一无二的 ,因此各自将会个别的评价(如:评价是主观的)。
模 式被无意地纳入产品或过程之前进行。事先花时间适当地完成FMEA分析,能 够更容易、低成本地对产品过程进行修改,从而减轻事后修改危机。
FMEA能够减少或消除原因进行预防和矫正而带来更大损失的机会。
FMEA小组应该有充分的沟通和整合。
3
图一描述了一个FMEA应该被执行的程序,它并不是简单的把表格填满的案 例,而是进一步理解FMEA的程序,以消除风险和计划能确保顾客满意 的适当控制。
2
FMEA的實施
由于尽可能的持续改进产品和过程是企业的趋势,所以使用FMEA作为专门技 术应用,以识别并帮助减少潜在的隐忧一直是非常重要的。对于产品抱怨的研 究结果表明,全面实施FMEA能够避免许多抱怨事件的发生。
适时性是成功实施FMEA的最重要因素之一,它是一个“事发前”的行为,
而不
是“后见之明”的行动。为打达到最佳效益,FMEA必须在设计或过程失效
的可能性; .为全面、有效的设计试验和开发项目的规划,提供更多的信息; .根据潜在失效模式对“顾客”的冲击,对其进行分级列表,进而建立 一
套设计改进、开发和查证的优先控制系统; .为建议和跟踪降低风险的措施,提供一个公开的讨论形式; .为将来分析研究售后巿场关切情况、评价设计更改及展开更先进的设
计提供参考。
什麼會錯誤? -- 無 功 能 -- 部 分 /過 多 /
降低功能 -- 間 歇 功 能 -- 不 預 期 功 能
原因為何?
其發生 頻率為何?
能夠做什麼? -- 設 計 變 更 -- 製 程 變 更 -- 特 別 管 制 -- 標 準 , 程 序 書
或指引變更
如何能 預防及發現
這種 原因及錯誤?
這種方法 發現這種問題