曲轴连杆轴颈的铣削
曲轴连杆轴颈的粗加工工序安排

4D型曲轴连杆轴颈的粗加工工序安排
通过对曲轴连杆轴颈的车削、内铣和车拉三种粗加工方式的研究,这三种粗加工方式都有各自的优缺点,为了找出适合4D型曲轴连杆轴颈粗加工的加工方式,我通过综合比较分析,制定了合理的加工方案。
表一:车削、内铣和车拉加工工艺的精度对比分析
从上表中的数据分析来看,车削加工和车拉加工的精度要比内铣加工的精度要高,但是对于曲轴的粗加工的工艺要求来说,这三种加工方式都可以满足。
表二:车削、内铣和车拉加工工艺的工作循环平均时间对比分析
从上表中的数据分析来看,内铣和车拉加工的工作循环平均时间要少于车削加工,具有更快的工作效率。
表三:车削、内铣和车拉加工工艺的生产设备价格的对比分析
从上表中的数据分析来看,内铣和车拉加工的生产设备的价格比率要远高于车削加工,车削加工设备成本最低。
表四:车削、内铣和车拉加工工艺适用的连杆轴颈类型的对比分析
从上表中的数据分析来看,内铣不适用于加工有沉割槽的曲轴连杆轴颈,车拉适用于加工有沉割槽的曲轴连杆轴颈。
从上述五个表的分析结果来看,由于4D型曲轴的连杆轴颈需要加工沉割槽,而且从加工精度、工作循环平均时间、省去半精加工过程等方面来看,车拉加工方式都比较适合4D型曲轴连杆轴颈的加工,虽然车拉加工方式在生产设备的投资方面相对高一些,但是从综合效益方面来看我们在4D型曲轴的连杆轴颈的粗加工方面采用了车拉加工方式。
1-主轴颈和连杆轴颈的粗加工工艺分析

cNc车拉 f"=150一175m/min)
±O.05
O.008~0.015
±O.05
±O.05
±O.05
±0.05
CNC高速外铣 (口=350m/min)
±0.08
0.035~O.05
±0.08
±0.05
±O.08
±0.08
cBN高速磨削 f口=200rn/s1
±0.025
0.012
±0.013
±0.015
1.1
≈O.75
/ 1.66(1,2,3,4)
O.80(I.4) 0.80(2.3)
平衡块侧面需加工
///// 1.38
/ 3.66(1,2,3.4)
1.80(1.4) 1.80(2.3)
5
O.8
(正体多刀糯)
cNc车一车拉 6
(双刀盘)O.97源自3.071.20(1,2.3.4)
0.57(1.4) O.57(2.3)
(1)日本汽车发动机厂对曲轴的粗加工,一般都推 荐采用:
一主轴颈加工采用CNC车削。 一连杆轴颈加工采用CNC内铣。 根据表5可知: ①主轴颈加工只有在年产纲领为150000件以下时, 以及平衡块侧面不加工的情况下采用CNc车削才是合 理的方案。但这里尚需说明一下,表5中在平衡块侧面要 加工及轴颈无沉割槽的情况下,年生产纲领为150000 件,采用CNC车削的设备价格与CNC内铣(双刀盘)的 设备价格很接近,所以在这种情况下采用cNc车削工艺 亦可以的。 ②连杆轴颈加工只有在平衡块侧面要加工及轴颈无 沉割槽的情况下采用cNc内铣才是合理的方案。根据我 们分析的结果,证明日本汽车发动机厂对曲轴所推荐的 粗加工工艺需要改进。 (2)国内很多从事曲轴制造的技术人员,对曲轴的 粗加工比较喜欢采用车拉工艺方案。这是一种新工艺, 精度高这点是可以理解的。但是必须指出当曲轴平衡块 侧面要加工,且轴颈无沉割槽的情况下,CNc内铣加工 工艺方案比cNc车拉(含车一车拉)更加经济。 (3)当曲轴平衡块侧面不要加工,且轴颈有沉割槽 的情况下,CNC车拉(含车一车拉)加工工艺方案比CNC 内铣更为经济。
曲轴连杆颈及过渡圆角磨削不良的解决方案

曲轴连杆颈及过渡圆角磨削不良的解决方案徐兵杰北京现代汽车有限公司摘要:在大批量曲轴自动加工过程中机床的工装夹具的刚性及精度决定了产品的稳定性,产品质量的稳定对于节约企业生产成本是极为有利的。
本文着重介绍了利用工业工程方法对于小松内铣机床的工装改进方案。
关键词:WORKREST 产品质量生产成本引言:2009年北汽控股公司制定了产销汽车100万辆、销售收入1000亿元的“百万千亿”目标。
作为北汽控股的重要支柱企业,北京现代的作用非同寻常。
在这样的大背景下就要求了我们的生产准时化,有序化,规范化。
在整个生产运营体系中,同样的要求也出现在发动机厂曲轴生产上。
在曲轴的整条工艺体系中,连杆颈加工是最为复杂的工艺,因而生产质量事故最为频发。
小松内铣的连杆颈粗加工是连杆颈精加工之前重要工序,控制好曲轴连杆颈的粗加工质量就可以极大的降低曲轴不良品的产生。
1.北京现代曲轴连杆颈加工简介:1.11.2 小松内铣工艺简介:小松内铣技术是日本小松的全球专利技术,它通过成型铣刀盘在固定的工件上进行圆弧插补运动,完成一次性铣削加工。
就北京现代的小松连杆颈内铣机床而言其优点有:加工效率高,生产节拍短。
使用成型刀盘生产加工,连杆颈宽度加工尺寸稳定。
机械结构简单,人工调整拆卸简便。
表面粗糙度及圆度参数控制稳定。
1.3 加工尺寸技术要求:2. 在生产过程中,遇到的实际问题在实际的生产实践中,我们并没有发现60序、与100序这两个工位的加工数据有较大的波动,相反,它们的后道工序150序有着明显的加工质量事故发生:2.1 GC30-150序曲轴连杆颈未磨削完全,也就是说在360°的曲轴连杆颈圆周上有一段圆弧面未被磨削到(如图3-1)图2-1此问题产生之后,使我们第一个想到的原因就是查找150序本身是否有工装夹具定位不准的情况或者整个夹具体是否出现了相位偏移,但使我们感到疑惑的是并不是每一根曲轴都存在磨削不良的状况,并且在加工合格的曲轴中进行抽样检测后,结果显示曲轴的相位与1/2行程都处于合格范围内。
曲轴连杆颈磨削的精细化控制
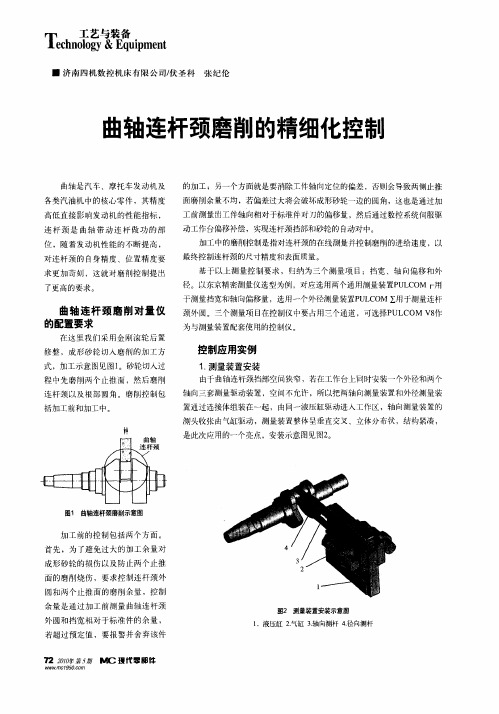
佃
轴 向三套测量驱动装置 ,空 间不 允许 ,所以把两轴 向测量装 置和外径测量装 置通过连接体组装在一起 ,由同一液压缸驱动进入工作 区,轴 向测量装置的 测头收张 由气缸驱动 ,测量装置整体 呈垂直交叉 、立体分布状 ,结构 紧凑 ,
是此次应用的一个亮点,安装示意图见图2 。
I广] 广
l
\ /
图1 曲轴连杆颈磨削示意图
加 工前的控 制包括 两个方 面。 首先 ,为 了避 免过大 的加工 余量对
成形 砂轮的损 伤以及 防止两个 止推
面的 磨削烧 伤 ,要 求控 制连杆 颈外
圆和 两个止推 面的 磨削余量 ,控制
余量 是通过加 工前测 量 曲轴连 杆颈 外 圆和挡宽相 对于标 准件的 余量 ,
位 ,随着 发动机性 能的 不断提高 ,
对连杆颈 的 自身精 度 、位 置精度要
求更加苛 刻 ,这就 对磨 削控 制提 出 了更高 的要求 。
曲轴连杆 颈磨 削对量仪 颈外 圆。三个测量项 目在控制仪 中要 占用三个通道 ,可选择P L OM 8 U C V 作 的配置要 求 为与测量装置配套使用的控制仪 。
各类汽油机 中的核 心零件 ,其精度 高低直接 影响发动 机的性 能指标 ,
连杆 颈 是 曲轴 带动 连 杆 做 功 的 部
工前测量 出工件轴 向相对于标准件对 刀的偏移量 ,然后通过数控 系统伺服驱
动工作台偏移补偿 ,实现连杆颈 挡部和砂轮的 自动对中。 加 工中的磨削控制是指对连杆颈 的在线测量并控制磨削的进给速度 ,以 最终控制连杆颈的尺寸精 度和表面 质量 。 基于以上测 量控制要 求 ,归纳为 三个测量 项 目:挡宽 、轴 向偏移和 外 径。以东京精 密测 量仪选型为例 ,对应选用两个通用测量装 置P C UL OM 广 用 于测量档宽和轴向偏移 量,选用 一个外径测量装置P L M ∑用于测量连杆 U CO
曲轴连杆颈磨削用液压偏心夹具

满液 压油 ,不考虑 油路压 力损失的情 况下 ,此 时 液 压油 的压力为 系统 压 力 ,此 压力仅 能使薄壁 套
筒 产 生 可 以 忽 略 不 计 的 变 形 ,以 确 保 曲 轴 能 够 非
产生往复运动 ,并将旋转运动转为直 线运动 ,其主
要 作 用是 传 递 转矩 ,是 连 杆获 得 动 力 的动 力 源 。 曲 轴 连 杆颈 磨 削 质量 的重 要性 不 言 而喻 。
2 . 车用 空压机 曲轴磨 削工艺流程
车 用空 压 机 曲轴连 杆 颈 的 设 计基 准 是 3 5 k 6 9 1 , 圆 与 3 0 g 6  ̄ 1 , 圆 ,螺 纹 M 1 6 —6 g 与 两 基 准 外 圆 同 轴 ,并 且 螺 纹M 1 6 —6 g 大 径是 距离 曲轴连 杆 颈 最 大 的夹 持 力 臂 ,可 以 确保 偏 心 夹具 夹 持 曲轴 的 刚性 和
( 2 )曲轴偏心夹具的结构 曲轴偏心夹具 ( 见 图5 )依靠联接盘 8 固定在头架主轴前端 ,联接盘8
上 有 一 个 定 位 槽 ,夹具 体 6 可在联接盘的定位槽 中
常轻松地装 入弹性 套筒 ( 见图3 )的内孔 ,单 向阀
4 H ‘ e ‘ 够 确 保该 处 液 压 油 不 产 生 回流 。第 一 次 进 油 时 整 个 油 路 中 充满 了 气体 ,这 时 应 将 两 排 气螺 塞 3 拧 松 从 而 把 气体 排 出 油路 ,然 后 拧 紧两 排 气螺 塞 3 以 确保油路的密闭。
曲轴连杆颈磨削用液压偏心夹具
济南 四机数控机 床有 限公 司 ( 山东 2 5 0 1 0 1 ) 董传军
曲轴连杆轴颈的铣削

4D型曲轴连杆轴颈的铣削曲轴连杆轴颈的铣削是机械加工中效率相对较高的一种基础加工方法,通过多刃刀具的高速旋转运动和进给运动对所加工的工件进行切削操作,根据实际的要求加工的工件可以固定,也可以做进给运动,经过刀具在工件表面进行切削去去屑后逐渐铣出粗加工后的表面。
铣削一般具有以下三个特征:①刀具的每个刀齿在进行切削加工过程中的切削厚度是随时变化的。
②在加工过程中,用每齿进给量af(mm/齿)来表示工件在铣削刀具每次转过一个刀齿的时间内所经过的相对位移量。
③铣刀的各个刀齿在加工的过程中会周期性地进行间断切削。
铣削可以适用于沟槽、平面和螺纹等的加工,一般在镗床或铣床上进行加工操作,加工机床一般有立式的铣床和卧式的铣床,可以是普通或者数控机床。
铣削加工相对于车削加工来说具有较高的生产效率,一般为车削加工生产效率的3倍左右,所以铣削加工的采用可以达到降低生产设备的投资的目的。
车削加工的稳定性在现实生产中也不如铣削加工,同时车削工件在进行车削加工时需要高速的回转,这样对生产机床就不可避免地产生较大的离心力,长期进行的车削加工操作的机床相对发生的故障率也要比铣床多一些。
根据铣削刀具的不同,铣削一般可分为外铣和内铣两种,下面我们通过对两种不同的铣削方式来研究适用于4D型曲轴连杆轴颈加工的具体操作方式。
1、4D型曲轴连杆轴颈的外铣加工曲轴的外铣加工方式主要适用于小排量的车辆,对曲轴的主轴颈和曲轴的连杆轴颈去除毛坯余量不大的加工处理。
按曲轴外铣加工的铣床铣的数量可以分为双头铣加工和单头铣加工两种。
曲轴的外铣加工示意图曲轴在外铣加工时,在机床上将曲轴两端的主轴颈要进行位置和角度定位并夹紧,通过止推面进行轴向定位,在加工的过程中铣刀高速旋转在径向进给到曲轴连杆轴颈所规定的直径尺寸后,外铣刀具进行跟踪曲轴连杆轴颈作仿行铣削运动(这个过程也可称为数控),同时曲轴需要围绕曲轴主轴颈的中心低速旋转三百六十度,这样一个完整的工序就可以将曲轴连杆轴颈的各面加工出来了。
曲轴连杆颈侧壁加工粗糙度问题解决

曲轴连杆颈侧壁加工粗糙度问题解决杨武;邓晓晓【摘要】本文介绍了如何采用外铣刀具来解决曲轴连杆颈侧壁粗糙度的加工方案。
在刀盘上增加修光刀片并合理布置刀片位置,试验最优的切削参数并进行加工验证,通过分析加工数据和测量图形对刀具结构做进一步改进,最终解决了生产中遇到的粗糙度问题。
【期刊名称】《汽车制造业》【年(卷),期】2016(000)004【总页数】2页(P46-47)【关键词】曲轴连杆颈;加工数据;粗糙度;侧壁;题解;刀具结构;合理布置;切削参数【作者】杨武;邓晓晓【作者单位】上汽通用五菱汽车股份有限公司【正文语种】中文【中图分类】U262.11本文介绍了如何采用外铣刀具来解决曲轴连杆颈侧壁粗糙度的加工方案。
在刀盘上增加修光刀片并合理布置刀片位置,试验最优的切削参数并进行加工验证,通过分析加工数据和测量图形对刀具结构做进一步改进,最终解决了生产中遇到的粗糙度问题。
传统的自然吸气发动机曲轴连杆颈侧壁的粗糙度要求一般为Rz16 μm,外铣或内铣机床采用普通不可调的盘式铣刀加工就能满足要求。
增压发动机的曲轴连杆颈侧壁的粗糙度要求一般为Rz6 μm,通常采用磨削或者带一个修光刀片的内铣刀具加工。
内铣加工效率低、换刀频繁,而且必须与内铣机床匹配使用,使用范围大大受到限制。
所以,研究采用外铣机床和外铣刀具加工连杆颈侧壁,来保证粗糙度具有一定的现实意义和推广性。
我公司发动机四期增压改造项目中曲轴线要求增压曲轴与非增压曲轴共线生产,目前采用外铣机床和外铣刀具来加工曲轴连杆颈侧壁。
增压曲轴连杆颈侧壁的粗糙度要求为不大于Rz6 μm。
当外铣机床采用不可调的外铣刀具加工时,连杆颈侧壁表面存在交叉网纹的接刀痕(见图1),该接刀痕的台阶高度直接影响侧壁的粗糙度。
由于外铣刀具上的刀片不可调,刀片间的高度差、刀片的轴向跳动等因素造成接刀痕高度不可控。
无论如何调整切削参数,粗糙度测量结果基本上都在Rz4~9 μm之间,且数值波动大,个别值在Rz10 μm以上,无法满足要求。
LANDIS 6400 曲轴颈磨床..

曲轴连杆颈磨床功能分析图
曲轴连杆颈磨床功能分析形态学矩阵图
分元素 砂轮材质 工件装夹形式 控制形式 伺服形式 各旋转轴支承形式 各旋转轴驱动形式 各轴滑台形式 各轴滑台驱动形式 各轴位置反馈形式 磨削尺寸控制方式 安全控制 人机交互 信息流功能 可能的解法 CBN烧结砂轮 双卡盘+顶尖 PC + CNC NC + PC 交流伺服电动机 直流伺服电动机 静压轴承 滑动轴承 滚动轴承 内置电机 外置电机+联轴器 外置电机+同步带 静压导轨 直线导轨 普通导轨 直线电机 静压丝杠 滚珠丝杠 光栅尺 编码器 旋转变压器 在线测量 控制定程磨削+离线测量 门安全开关 光幕 触摸屏 指示灯 远程控制 故障自诊断 维修指示
LOGO
机电一体化系统的设计域与四视图
复
习
LOGO
机电一体化案例分析 曲轴连杆颈随动磨削磨床
问题的提出
曲轴的特点和磨削方法
问题的提出
1.1 传统曲轴磨削方法 由两道工序完成:在曲轴主轴颈磨床上,以中心孔定位, 以主轴颈中心连线为回转中心加工主轴颈;在曲轴连杆颈磨床 上,以调偏心法磨削连杆颈,即以主轴颈定位,以被加工连杆 颈的轴心线为回转中心加工连杆颈。曲轴连杆颈磨床因涉及到 偏心装夹、曲拐分度,以及由此导致的离心惯性力的平衡,故 结构较复杂。 1.2 数控随动曲轴磨削方法 随动磨削是近年来随着磨削技术和数控技术等的发展而 出现的一种新型工序集中式的曲轴类零件的磨削加工方法。以 曲轴主轴颈中心连线为回转中心,一次装夹依次磨出所有连杆 颈。磨削连杆轴颈的实现方式为:通过采用数控技术,根据建 立的连杆轴颈磨削运动的数学模型,控制砂轮的横向进给(X 轴) 和工件回转运动(C轴)联动插补,以保证连杆颈的磨削精度和表 面质量。
精密曲轴连杆颈磨削加工技术的研究

精密曲轴连杆颈磨削加工技术的研究作者:文/ 张慎明来源:《时代汽车》 2020年第20期张慎明上汽通用五菱汽车股份有限公司广西柳州市 545007摘要:内燃机与发动机作为汽车的心脏,曲轴作为心脏的血管,所以加强曲轴的设计与加工就显得尤为重要,加上曲轴类型多样,加工精度将直接关乎到发动机性能,进而对汽车质量带来影响。
因此,市面上对于曲轴精度的要求也越发苛刻。
本文对以精密曲轴连杆颈磨削加工技术作为研究对象,对其工艺要点和相关误差因素进行了探究,旨于为企业带来更好的经济效应。
关键词:加工技术连杆轴颈摩削曲轴连杆颈Research on Grinding Technology of Precision Crankshaft Connecting Rod NeckZhang ShenmingAbstract:The internal combustion engine and the engine are the heart of the car, and the crankshaft is the blood vessel of the heart. Therefore, it is particularly important to strengthen the design and processing of the crankshaft. With the various types of crankshafts, the machining accuracy will directly affect the performance of the engine, which will affect the quality of the car. Therefore, the requirements for crankshaft accuracy on the market are becoming more stringent. This article takes the precision crankshaft connecting rod neck grinding processing technology as the research object, and explores its process points and relatederror factors, aiming to bring better economic effects to the enterprise.Key words:machining technology, connecting rod journal rubbing, crankshaft connecting rod journal1 引言曲轴的作用是承受连杆传来的力,并将这份力转变为转矩输出并驱动发动机上附件来支持附件的工作。
机车柴油机曲轴连杆颈随动磨削工艺研究

机车柴油机曲轴连杆颈随动磨削工艺研究刘德岭【摘要】以机车柴油机曲轴连杆颈随动磨削为例,结合传统磨床生产过程中的经验,对随动磨削方案优化设计,保证了磨削质量和效率,取得了较为满意的效果.介绍了曲轴随动磨削的优势,进一步阐明了随动磨削技术的先进性.【期刊名称】《机械研究与应用》【年(卷),期】2016(029)005【总页数】3页(P173-175)【关键词】机车;曲轴;连杆颈;随动磨削【作者】刘德岭【作者单位】中车戚墅堰机车有限公司,江苏常州 213011【正文语种】中文【中图分类】U260在机械加工中,传统的曲轴连杆颈磨削时,是以主轴颈外圆定位,采用偏心装夹的方式,让连杆颈中心位于机床主轴的回转中心,采用类似主轴颈磨削的方式进行磨削。
为了实现偏心装夹,磨床设备需要配备及其复杂的机械夹紧系统,且头架和尾架还需配备平衡块,以补偿因偏心装夹带来的动不平衡问题。
因连杆颈所在角度不同,一根曲轴需多次装夹才能完成所有连杆颈的磨削,该磨削工艺繁琐费时,而且要求工人具备极好的素质和丰富的经验[1]。
随着数控技术日新月异的发展,随动磨削方式逐渐被应用到生产现场,可以说给曲轴磨削加工带来了一场革命。
但同时,新工艺的推广总会存在一个摸索的过程,针对生产现场调试过程中发现的问题,总结了一些加工经验,希望能为新工艺的推广起到借鉴作用,帮助大家少走弯路。
随动磨削是建立在数控技术和检测技术的基础上发展起来的,采用砂轮跟随连杆颈的方式进行磨削,也称切点跟踪磨削[2]。
曲轴以两端中心孔定位,以主轴颈轴线为回转中心,砂轮同时进行周期性的往复直线运动,确保始终与连杆颈外圆相切,最终完成对连杆颈外圆的磨削。
曲轴定位方式的改变是其最大的变化。
中车戚墅堰机车有限公司采用的设备为德国埃马克集团生产的的NAXOS-UNION PM460随动曲轴磨床,如图1所示。
磨床的X轴和Z轴均配置了直线电机和静压导轨,动态性能卓越。
其头架和尾架配备有同步驱动扭矩电机,扭矩大,传动平稳。
曲轴连杆颈复合跟随车削原理分析

曲轴连杆颈复合跟随车削原理分析曲轴连杆颈复合跟随车削是一种在大型柴油发动机零件加工中广泛使用的高精度加工技术,它是通过复合跟随车床、曲轴顶端四轴卡盘和特殊的刀架结构组成的。
本文将对曲轴连杆颈复合跟随车削的原理进行分析。
1.曲轴连杆颈复合跟随车削的概念曲轴连杆颈复合跟随车削是一种高精度的加工技术,是通过复合跟随车床、曲轴顶端四轴卡盘和特殊的刀架结构,实现曲轴连杆颈的高精度加工。
曲轴连杆颈复合跟随车削相较于传统车削方式,具有切削效率高、加工精度高、能适应不同工艺要求等优点。
2.曲轴连杆颈复合跟随车削原理首先,在加工曲轴连杆颈时,需要采用复合跟随车床,这种车床可以同时对曲轴和连杆颈进行加工,通过配备两个不同的工作台实现,其中一张工作台用于加工连杆,另一张工作台用于加工曲轴。
其次,车削时需要采用曲轴顶端四轴卡盘,将曲轴固定在车床上,保证曲轴不会出现移位或者前后偏差。
最后,为了保证加工精度,曲轴连杆颈复合跟随车削需要采取特殊的刀架结构,即采用V形夹头进行加工。
这种结构可以保证V形夹头始终紧贴连杆颈表面,确保加工精度。
3.曲轴连杆颈复合跟随车削的优点曲轴连杆颈复合跟随车削相较于传统车削方式,具有以下优点:(1)切削效率高。
采用复合跟随车床,在同一时间内完成曲轴和连杆颈的加工,可有效提高加工效率。
(2)加工精度高。
采用曲轴顶端四轴卡盘和特殊的刀架结构,能够保证加工精度。
(3)适应不同工艺要求。
曲轴连杆颈复合跟随车削可根据工艺要求进行加工,灵活性高。
4.结论曲轴连杆颈复合跟随车削是一种高精度、切削效率高、能适应不同工艺要求的加工技术。
通过采用复合跟随车床、曲轴顶端四轴卡盘和特殊的刀架结构,能够在柴油发动机的制造中起到重要的作用。
为了更好地理解和评价某个问题或现象,常常需要收集和分析相关数据。
以下以“全球男女比例”的数据为例,进行数据分析。
数据来源:根据联合国2019年统计数据,全球男性人口占总人口比例为50.4%,女性人口占比49.6%。
柴油机曲轴连杆轴颈滚切铣床总体和夹具设计

柴油机曲轴连杆轴颈滚切铣床总体和夹具设计毕业设计任务书课题:柴油机曲轴连杆轴颈滚切铣床总体和夹具设计专业机械设计制造及其自动化学生姓名班级学号指导教师专业系主任发放日期协助完成各种机械类课程设计、毕业设计等。
有需求请联系本人,价格优惠,有意向E-mail 或者QQ留言,晚上6点准时答复。
QQ:1084949428 E-mail:1084949428@ 一、设计内容设计一台可加工曲轴中两连杆轴颈的滚切组合机床,具体进行总体设计和夹具设计。
主要内容有:1.总体设计1)制定工艺方案,确定机床配置型式及结构方案。
2)三图一卡设计,包括:(a)被加工零件工序图,(b) 加工示意图,(c) 机床联系尺寸图,(d) 生产率计算卡,(e) 有关设计计算、校核。
2.夹具设计(a) 夹具总装图,(b) 夹具体零件图,(c) 其它零件图,(d) 有关计算、校核等。
二、设计依据1.课题来源:江苏恒力组合机床有限公司2.产品名称:495B-05004A 3.被加工零件:曲轴4.工件材料:QT800-2 硬度HB240-300 5.加工内容:滚切两连杆轴颈φ62,两端圆角,保证轴向尺寸、、和。
6. 生产纲领:大批大量。
7. 批量:本机床设计、制造一台。
三、设计要求1.机床应能满足加工要求,保证加工精度;2.机床应运转平稳,工作可靠,结构简单,装卸方便,便于维修、调整;3.机床尽量能用通用件以便降低制造成本;4.机床各动力部件用电液控制。
5.设计图样总量:折合成A0幅面在3张以上;工具要求:应用计算机软件绘图,要应有三维软件设计的零件。
过程要求:装配图需提供手工草图。
6.毕业设计说明书见相关要求7.查阅文献资料10篇以上,并有不少于3000汉字的外文资料翻译;8.到相关单位进行毕业实习,撰写不少于3000字实习报告;9.撰写开题报告四、毕业设计物化成果的具体内容及要求1、毕业设计说明书要求:按教务处毕业设计格式规范统一编排、打印,字数不少于2万字。
曲轴连杆颈正交车铣加工工艺的研究

曲轴连杆颈正交车铣加工工艺的研究周建江;夏焕金;陆忠民;蒋文伟【摘要】The paper proposes a rmthematical model of orthogonal trim-milling for crankshaft pin. It studies and analyzes the selecting prhacipia of ram-milling tool, the eccentricity of between tool axis and workpiece axis,a cut-in and cut-out position. The practice proves it' s effective and applicable.%对曲轴连杆颈正交车铣加工路径的数学模型作出了分析,根据数学模型对车铣加工曲轴连杆颈时的进、出刀点位置,刀具及刀具与曲轴之间的偏心量等工艺参数进行了一定的研究和分析并给出了选择原则。
实践证明该方法有效可行。
【期刊名称】《常州信息职业技术学院学报》【年(卷),期】2012(011)006【总页数】3页(P17-19)【关键词】曲轴连杆颈;正交车铣;数学模型;偏心量【作者】周建江;夏焕金;陆忠民;蒋文伟【作者单位】中国南车戚墅堰机车有限公司,江苏常州213011;中国南车戚墅堰机车有限公司,江苏常州213011;中国南车戚墅堰机车有限公司,江苏常州213011;中国南车戚墅堰机车有限公司,江苏常州213011【正文语种】中文【中图分类】TG51;TG54引言车铣加工是近十年来发展起来的新型、高效及高质量的切削加工方式,它是利用铣刀旋转和工件旋转的合成运动来实现对工件的切削加工。
按照刀具旋转轴线与工件旋转轴线相对位置不同,车铣加工主要可分为轴向车铣(即刀具的旋转轴线与工件的旋转轴线相平行)和正交车铣(即刀具的旋转轴线与工件的旋转轴线相垂直)[1-2]。
- 1、下载文档前请自行甄别文档内容的完整性,平台不提供额外的编辑、内容补充、找答案等附加服务。
- 2、"仅部分预览"的文档,不可在线预览部分如存在完整性等问题,可反馈申请退款(可完整预览的文档不适用该条件!)。
- 3、如文档侵犯您的权益,请联系客服反馈,我们会尽快为您处理(人工客服工作时间:9:00-18:30)。
4D型曲轴连杆轴颈的铣削
曲轴连杆轴颈的铣削是机械加工中效率相对较高的一种基础加工方法,通过多刃刀具的高速旋转运动和进给运动对所加工的工件进行切削操作,根据实际的要求加工的工件可以固定,也可以做进给运动,经过刀具在工件表面进行切削去去屑后逐渐铣出粗加工后的表面。
铣削一般具有以下三个特征:
①刀具的每个刀齿在进行切削加工过程中的切削厚度是随时变化的。
②在加工过程中,用每齿进给量af(mm/齿)来表示工件在铣削刀具每次转过一个刀齿的时间内所经过的相对位移量。
③铣刀的各个刀齿在加工的过程中会周期性地进行间断切削。
铣削可以适用于沟槽、平面和螺纹等的加工,一般在镗床或铣床上进行加工操作,加工机床一般有立式的铣床和卧式的铣床,可以是普通或者数控机床。
铣削加工相对于车削加工来说具有较高的生产效率,一般为车削加工生产效率的3倍左右,所以铣削加工的采用可以达到降低生产设备的投资的目的。
车削加工的稳定性在现实生产中也不如铣削加工,同时车削工件在进行车削加工时需要高速的回转,这样对生产机床就不可避免地产生较大的离心力,长期进行的车削加工操作的机床相对发生的故障率也要比铣床多一些。
根据铣削刀具的不同,铣削一般可分为外铣和内铣两种,下面我们通过对两种不同的铣削方式来研究适用于4D型曲轴连杆轴颈加工的具体操作方式。
1、4D型曲轴连杆轴颈的外铣加工
曲轴的外铣加工方式主要适用于小排量的车辆,对曲轴的主轴颈和曲轴的连杆轴颈去除毛坯余量不大的加工处理。
按曲轴外铣加工的铣床铣的数量可以分为双头铣加工和单头铣加工两种。
曲轴的外铣加工示意图
曲轴在外铣加工时,在机床上将曲轴两端的主轴颈要进行位置和角度定位并夹紧,通过止推面进行轴向定位,在加工的过程中铣刀高速旋转在径向进给到曲轴连杆轴颈所规定的直径尺寸后,外铣刀具进行跟踪曲轴连杆轴颈作仿行铣削运动(这个过程也可称为数控),同时曲轴需要围绕曲轴主轴颈的中心低速旋转三百六十度,这样一个完整的工序就可以将曲轴连杆轴颈的各面加工出来了。
由于普通的曲轴外铣加工在性能上存在有许多的缺陷,基本上已经被曲轴的内铣加工所取代,所以4D型曲轴连杆轴颈在现实生产中不采用外铣加工。
2、4D型曲轴连杆轴颈的内铣加工
曲轴的内铣加工示意图
曲轴的连杆轴颈的内铣加工根据实际情况可以分为加工工件不旋转和加工
工件旋转两类,两种加工方式在生产的机床结构和所用加工原理都有所不同。
当不旋转工件时,对连杆轴颈内铣加工的铣刀在围绕自己的中心轴线进行自转,同时也要以连杆轴颈为中心进行公转,铣刀围绕连杆轴颈公转一周后完成内铣加工过程。
当旋转工件时,内铣加工与外铣加工过程时的定位和夹紧方式基本相同,曲轴两端的主轴颈分别在铣床左右两边的两个卡盘固定夹紧,进行位置定位和角度定位后,内铣刀具在高速旋转的同时径向进给到曲轴连杆轴颈的规定尺寸后,曲轴低速以主轴颈为中心旋转一圈,内铣刀具进行跟踪曲轴连杆轴颈作切向进给的仿行铣削运动,这是一个完整的连杆轴颈内铣加工周期。
鉴于4D型曲轴连杆轴颈复杂的结构,我们在内铣加工过程时采用了旋转工件的加工方式。
和其他的连杆轴颈加工方式相比,内铣加工有以下特点:
①内铣加工方式具有较高的生产效率,可在一台内铣机床上,可以通过曲轴的一次装夹来完成对连杆轴颈、主轴颈、止推面、轴肩、曲柄臂侧面、沉割槽等部位的集中加工,节省了工序、占地面积和辅助时间,毛坯的去除余量大。
②内铣机床具有转好的柔性,不需另外特制夹具,在加工的过程中只要更换一下刀具就可以对不同型号曲轴进行加工,并且粗铣和精铣加工过程可以在一台机床上得以实现。
③内铣加工的具有良好的断屑性能,特别是在对大功率的锻钢曲轴进行加工时,断屑效果极为明显,同时内铣的吃刀量大,切削的速度较高。
④内铣加工的缺点是在加工过程对刀复杂,切削的速度不高(一般为160m/min以下),工序循环时间过长,不能对轴向沉割槽进行加工,内铣加工后的轴颈表面有明显棱边,需要后期光整的过程相对复杂,机床造价相对较高。
在上个世纪的八十年代中期数控内铣加工工艺开始出现,曲轴的数控内铣加工工艺目前普遍应用于国内外的曲轴连杆轴戏颈的粗加工生产上,是一种较先进的粗加工方法,在大功率的锻钢曲轴的粗加工生产过程中应用更为广泛。