宽厚板轧机工作辊断裂原因分析及对策
热轧轧辊剥落或断裂的原因及预防方法探究
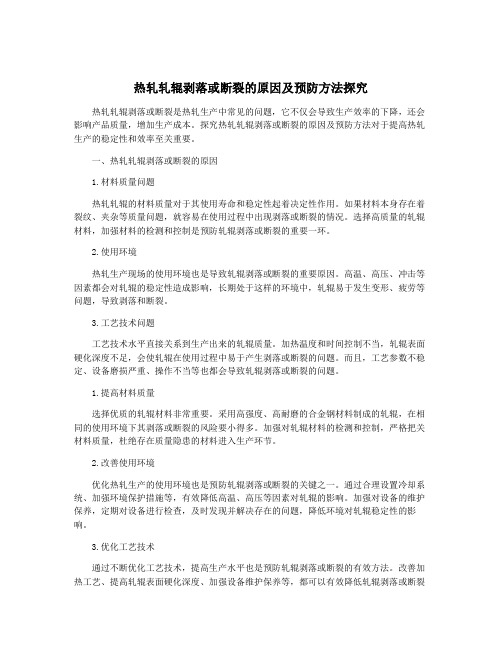
热轧轧辊剥落或断裂的原因及预防方法探究热轧轧辊剥落或断裂是热轧生产中常见的问题,它不仅会导致生产效率的下降,还会影响产品质量,增加生产成本。
探究热轧轧辊剥落或断裂的原因及预防方法对于提高热轧生产的稳定性和效率至关重要。
一、热轧轧辊剥落或断裂的原因1.材料质量问题热轧轧辊的材料质量对于其使用寿命和稳定性起着决定性作用。
如果材料本身存在着裂纹、夹杂等质量问题,就容易在使用过程中出现剥落或断裂的情况。
选择高质量的轧辊材料,加强材料的检测和控制是预防轧辊剥落或断裂的重要一环。
2.使用环境热轧生产现场的使用环境也是导致轧辊剥落或断裂的重要原因。
高温、高压、冲击等因素都会对轧辊的稳定性造成影响,长期处于这样的环境中,轧辊易于发生变形、疲劳等问题,导致剥落和断裂。
3.工艺技术问题工艺技术水平直接关系到生产出来的轧辊质量。
加热温度和时间控制不当,轧辊表面硬化深度不足,会使轧辊在使用过程中易于产生剥落或断裂的问题。
而且,工艺参数不稳定、设备磨损严重、操作不当等也都会导致轧辊剥落或断裂的问题。
1.提高材料质量选择优质的轧辊材料非常重要。
采用高强度、高耐磨的合金钢材料制成的轧辊,在相同的使用环境下其剥落或断裂的风险要小得多。
加强对轧辊材料的检测和控制,严格把关材料质量,杜绝存在质量隐患的材料进入生产环节。
2.改善使用环境优化热轧生产的使用环境也是预防轧辊剥落或断裂的关键之一。
通过合理设置冷却系统、加强环境保护措施等,有效降低高温、高压等因素对轧辊的影响。
加强对设备的维护保养,定期对设备进行检查,及时发现并解决存在的问题,降低环境对轧辊稳定性的影响。
3.优化工艺技术通过不断优化工艺技术,提高生产水平也是预防轧辊剥落或断裂的有效方法。
改善加热工艺、提高轧辊表面硬化深度、加强设备维护保养等,都可以有效降低轧辊剥落或断裂的风险。
培训操作人员,提高其技术水平,增强操作规范性,也是有效预防轧辊剥落或断裂的方法之一。
4.加强监控和管理加强对生产过程的监控和管理,及时发现并处理存在的问题也是预防轧辊剥落或断裂的关键。
轧机勒辊原因分析及控制措施

轧机勒辊原因分析及控制措施发表时间:2017-10-24T17:30:47.767Z 来源:《电力设备》2017年第16期作者:胥洋张跃张翼斌[导读] 摘要:轧机勒辊是冷连生产过程中频繁发生的现象,主要原因是在生产过程中轧辊的辊缝跳动过大,过大的下压力导致带钢生产时发生重叠和跑偏造成的。
在生产过程中勒辊或粘辊不大时,辊体和带钢便面会产生勒印,严重的时候也会发生断带。
(河钢承钢维护检修中心 067102)摘要:轧机勒辊是冷连生产过程中频繁发生的现象,主要原因是在生产过程中轧辊的辊缝跳动过大,过大的下压力导致带钢生产时发生重叠和跑偏造成的。
在生产过程中勒辊或粘辊不大时,辊体和带钢便面会产生勒印,严重的时候也会发生断带。
勒辊是生产冷轧带钢质量控制的重要因素,其影响了带钢的质量的同时还损伤了机械和电气设备,对轧辊进一步的损伤。
本文通过对轧机生产中勒辊现象进行了深度分析,提出合理的改善方案,有效的提高了带钢生产效率。
关键词:轧机;勒辊原因;分析;控制措施一、轧机勒辊的原因在生产过程中,轧机勒辊的原因主要有轧制钢带的原材料控制,产品的动态规格,轧制下压率不同,钢带偏离中心线和辊缝变化等所产生的。
本文以冷轧PL-TCM机组为实例进行勒辊问题详细解析,发生勒辊的主要技术点是在机组第1机架和第4、第5机架上,造成带钢表面勒印、扎漏以致缎带现象。
就此现象我展开太套和研究其原因和解决方案有以下几点: 1、压制过渡模型在市场竞争激烈的环境中,多品种生产增加了车间生产的难度,降低了生产效率,PL-TCM机组主要提供冷硬卷生产,品种多导致品种强度变化较大,在生产过程中,当冷轧钢生产品种变化时,会发生勒辊等现象,如高强度向低强度过度时在4和5机架会发生勒辊,其原因是钢种过度链接,根据统计数据分析,发生勒辊显现是两种钢种焊缝区内应力变化较大,焊缝经过每个机架是都会产生落差,导致张力变化,引起辊缝变化。
当焊缝经过机架时使得钢带失衡,偏离中心线,导致勒辊、断裂,钢带越薄越容易发生此现象。
轧板厂二辊轧机断辊原因及防范措施

轧板厂二辊轧机断辊原因及防范措施付志云(生产部)摘 要 通过对断辊进行分析,查找事故发生的原因,对如何避免此类事故的再次发生,提出了对应的防范措施。
关键词 二辊轧机 断辊事故 防范措施CAUSES TO R OLL BREAKAGE OF TWO HIGH R OLLING MI LL INP LATE MI LL AN D PREVENTATIVE MEASURESFu Zhiyun(The Production Department )Abstract Causes for the accidents are clarified through analysis of the roll breakage andcountermeasures accordingly put forward.K eyw ords tw o high rolling mill roll breakage accident preventative measures付志云,男,工程师1 前 言武钢轧板厂是一座生产中厚板材的轧钢厂,其轧制线的主要设备由一台二辊粗轧机和一台四辊万能精轧机构成。
二辊轧机主要用于原料板坯开坯,可对加热后的板坯进行可逆式轧制,所配备的轧辊主要为铸钢轧辊和少量锻钢轧辊。
2000年3月16日,在正常轧钢生产过程中,二辊轧机的上工作辊突然发生断辊事故,在断辊事故处理完毕,轧机仅生产了25min ,新换上的下工作辊又发生了断辊。
两次断辊共影响生产3h 10min ,并损坏了其它辅助设备。
在同一台轧机上,同个班次,相距很短的时间内,接连发生两起断辊事故,这在轧板厂的生产史上是少有的。
两起断辊引起了各级管理人员和轧辊操作、维护人员的极大重视。
2 断辊事故的调查两支断辊都是来自于同一轧辊制造厂,材质为65CrMnM o 铸钢轧辊,在正常情况下,轧辊的有效使用范围为<1160~1060mm 。
先发生断辊的是上辊,辊号为49号,辊径为1115mm ,已在轧机上使用5次,轧制钢坯约11.3万t ;后断的是下辊,辊号为62号,首次上机使用,仅生产了13块钢,辊径为1160mm 。
热轧轧辊剥落或断裂的原因及预防方法探究
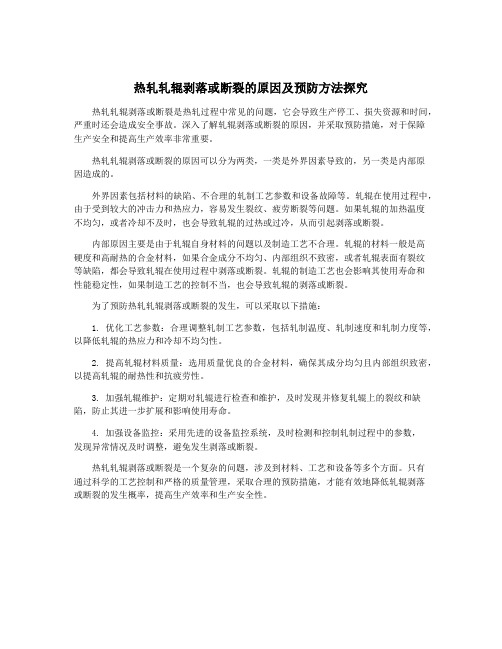
热轧轧辊剥落或断裂的原因及预防方法探究热轧轧辊剥落或断裂是热轧过程中常见的问题,它会导致生产停工、损失资源和时间,严重时还会造成安全事故。
深入了解轧辊剥落或断裂的原因,并采取预防措施,对于保障生产安全和提高生产效率非常重要。
热轧轧辊剥落或断裂的原因可以分为两类,一类是外界因素导致的,另一类是内部原因造成的。
外界因素包括材料的缺陷、不合理的轧制工艺参数和设备故障等。
轧辊在使用过程中,由于受到较大的冲击力和热应力,容易发生裂纹、疲劳断裂等问题。
如果轧辊的加热温度不均匀,或者冷却不及时,也会导致轧辊的过热或过冷,从而引起剥落或断裂。
内部原因主要是由于轧辊自身材料的问题以及制造工艺不合理。
轧辊的材料一般是高硬度和高耐热的合金材料,如果合金成分不均匀、内部组织不致密,或者轧辊表面有裂纹等缺陷,都会导致轧辊在使用过程中剥落或断裂。
轧辊的制造工艺也会影响其使用寿命和性能稳定性,如果制造工艺的控制不当,也会导致轧辊的剥落或断裂。
为了预防热轧轧辊剥落或断裂的发生,可以采取以下措施:1. 优化工艺参数:合理调整轧制工艺参数,包括轧制温度、轧制速度和轧制力度等,以降低轧辊的热应力和冷却不均匀性。
2. 提高轧辊材料质量:选用质量优良的合金材料,确保其成分均匀且内部组织致密,以提高轧辊的耐热性和抗疲劳性。
3. 加强轧辊维护:定期对轧辊进行检查和维护,及时发现并修复轧辊上的裂纹和缺陷,防止其进一步扩展和影响使用寿命。
4. 加强设备监控:采用先进的设备监控系统,及时检测和控制轧制过程中的参数,发现异常情况及时调整,避免发生剥落或断裂。
热轧轧辊剥落或断裂是一个复杂的问题,涉及到材料、工艺和设备等多个方面。
只有通过科学的工艺控制和严格的质量管理,采取合理的预防措施,才能有效地降低轧辊剥落或断裂的发生概率,提高生产效率和生产安全性。
轧辊失效方式及其原因分析

轧辊失效方式及其原因分析摘要:介绍了轧辊存在剥落、断裂、裂纹等几种失效方式,并重点分析了轧辊剥落和断裂产生的机理,为分析生产实践中轧辊失效原因和采取相应改进措施以提高轧辊使用寿命提供了依据。
关键词:轧辊;失效原因;剥落;断裂;裂纹1 前言轧机在轧制生产过程中,轧辊处于复杂的应力状态。
热轧机轧辊的工作环境更为恶劣:轧辊与轧件接触加热、轧辊水冷引起的周期性热应力,轧制负荷引起的接触应力、剪切应力以及残余应力等。
如轧辊的选材、设计、制作工艺等不合理,或轧制时卡钢等造成局部发热引起热冲击等,都易使轧辊失效。
轧辊失效主要有剥落、断裂、裂纹等形式。
任何一种失效形式都会直接导致轧辊使用寿命缩短。
因此有必要结合轧辊的失效形式,探究其产生的原因,找出延长轧辊使用寿命的有效途径。
2 轧辊的失效形式2.1 轧辊剥落轧辊剥落为首要的损坏形式,现场调查亦表明,剥落是轧辊损坏,甚至早期报废的主要原因。
轧制中局部过载和升温,使带钢焊合在轧辊表面,产生于次表层的裂纹沿径向扩展进入硬化层并多方向分枝扩展,该裂纹在逆向轧制条件下即造成剥落。
2.1.1支撑辊辊面剥落支撑辊剥落大多位于轧辊两端,沿圆周方向扩展,在宽度上呈块状或大块片状剥落,剥落坑表面较平整。
支撑辊和工作辊接触可看作两平行圆柱体的接触,在纯滚动情况下,接触处的接触应力为三向压应力,如图1所示。
在离接触表面深度(Z)为0.786b处(b为接触面宽度之半)剪切应力最大,随着表层摩擦力的增大而移向表层。
图1 滚动接触疲劳破坏应力状态疲劳裂纹并不是发生在剪应力最大处,而是更接近于表面,即在Z为0.5b的交变剪应力层处。
该处剪应力平行于轧辊表面,据剪应力互等定理,与表面垂直的方向同样存在大小相等的剪应力。
此力随轧辊的转动而发生大小和方向的改变,是造成接触疲劳的根源。
周期交变的剪切应力是轧辊损坏最常见的致因。
在交变剪切应力作用下,反复变形使材料局部弱化,达到疲劳极限时,出现裂纹。
另外,轧辊制造工艺造成的材质不均匀和微型缺陷的存在,亦有助于裂纹的产生。
引起轧辊发生垂直轧辊轴线断裂断面的主要原因_

引起轧辊发生垂直轧辊轴线断裂断面的主要原因1. 引言1.1 概述在轧钢过程中,轧辊是一种重要的工作部件,其质量和稳定性直接影响到整个轧制过程的效果和产品质量。
然而,在实际生产中,垂直轧辊轴线断裂断面问题时有发生,给生产运行带来了严重的影响和损失。
因此,了解引起这一问题的主要原因,并采取相应措施来预防和解决它们具有重要意义。
1.2 文章结构本文将从三个方面对垂直轧辊轴线断裂断面的主要原因进行探讨:轧辊质量问题、加工工艺问题以及动力系统问题。
每个方面将进一步细分为具体的子问题,并通过深入分析和研究来揭示这些子问题对垂直轧辊轴线断裂造成的影响。
1.3 目的本文旨在全面地研究并概述引起垂直轧辊轴线断裂断面的主要原因。
通过对这些原因进行深入剖析,我们可以更好地理解并找出有效的解决方案,从而提高生产过程中的效率和产品的质量。
给出相关的解决方案和改进建议有助于生产运行更加平稳和可靠地进行。
2. 垂直轧辊轴线断裂断面的主要原因垂直轧辊轴线断裂断面是钢铁工业中常见的问题之一,其主要原因可以归结为轧辊质量问题、加工工艺问题和动力系统问题。
2.1 轧辊质量问题轧辊质量问题是导致垂直轧辊轴线断裂断面的重要原因之一。
首先,材料的质量不合格会直接影响到轧辊的强度和韧性,在工作过程中容易出现疲劳破坏。
其次,热处理过程不当也可能使得轧辊内部存在残余应力或者晶粒生长异常,从而降低了其抗疲劳性能。
此外,加工精度不高也会导致负责分布不均匀以及表面误差增加,使得在工作过程中产生应力集中区域。
2.2 加工工艺问题加工工艺问题也是引起垂直轧辊轴线断裂断面的重要原因之一。
切割过程不正常会导致切口存在毛刺或者微裂纹等缺陷,这些缺陷在后续工作中会发展成裂纹,并最终导致轧辊断裂。
正火过程中温度和时间的控制不合理也会在轧辊内部形成大量的残余应力,使得轴线处于扭转应力状态,容易引发断裂。
此外,精加工磨削不足也可能使得表面存在凸起或者凹陷等缺陷,从而使得轧辊在工作过程中受到额外的摩擦和冲击。
热轧轧辊剥落或断裂的原因及预防方法探究
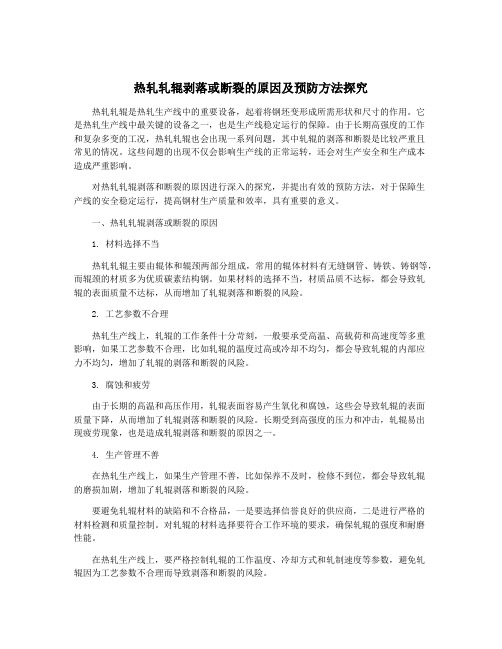
热轧轧辊剥落或断裂的原因及预防方法探究热轧轧辊是热轧生产线中的重要设备,起着将钢坯变形成所需形状和尺寸的作用。
它是热轧生产线中最关键的设备之一,也是生产线稳定运行的保障。
由于长期高强度的工作和复杂多变的工况,热轧轧辊也会出现一系列问题,其中轧辊的剥落和断裂是比较严重且常见的情况。
这些问题的出现不仅会影响生产线的正常运转,还会对生产安全和生产成本造成严重影响。
对热轧轧辊剥落和断裂的原因进行深入的探究,并提出有效的预防方法,对于保障生产线的安全稳定运行,提高钢材生产质量和效率,具有重要的意义。
一、热轧轧辊剥落或断裂的原因1. 材料选择不当热轧轧辊主要由辊体和辊颈两部分组成,常用的辊体材料有无缝钢管、铸铁、铸钢等,而辊颈的材质多为优质碳素结构钢。
如果材料的选择不当,材质品质不达标,都会导致轧辊的表面质量不达标,从而增加了轧辊剥落和断裂的风险。
2. 工艺参数不合理热轧生产线上,轧辊的工作条件十分苛刻,一般要承受高温、高载荷和高速度等多重影响,如果工艺参数不合理,比如轧辊的温度过高或冷却不均匀,都会导致轧辊的内部应力不均匀,增加了轧辊的剥落和断裂的风险。
3. 腐蚀和疲劳由于长期的高温和高压作用,轧辊表面容易产生氧化和腐蚀,这些会导致轧辊的表面质量下降,从而增加了轧辊剥落和断裂的风险。
长期受到高强度的压力和冲击,轧辊易出现疲劳现象,也是造成轧辊剥落和断裂的原因之一。
4. 生产管理不善在热轧生产线上,如果生产管理不善,比如保养不及时,检修不到位,都会导致轧辊的磨损加剧,增加了轧辊剥落和断裂的风险。
要避免轧辊材料的缺陷和不合格品,一是要选择信誉良好的供应商,二是进行严格的材料检测和质量控制。
对轧辊的材料选择要符合工作环境的要求,确保轧辊的强度和耐磨性能。
在热轧生产线上,要严格控制轧辊的工作温度、冷却方式和轧制速度等参数,避免轧辊因为工艺参数不合理而导致剥落和断裂的风险。
要对轧辊的表面进行防腐处理,避免氧化和腐蚀的发生;并对轧辊进行定期的疲劳检测和预防性维护,延长轧辊的使用寿命。
辊子断裂原因分析

辊芯断裂原因分析我司是一家专业生产电镀锡薄钢板(俗称“马口铁”)的公司,在镀锡生产线上有许多的各种材质的辊子。
在生产过程中经常会出现辊芯断裂而造成辊子的报废,给生产经营及设备维护造成了很大的影响。
观察辊芯的断裂位置大都是从卷芯配重块的焊接的焊缝附近位置附近出现的断裂。
本文主要是探讨辊芯断裂的根本原因,本文中有部分是摘自网络,均进行了注明。
下面是辊子断裂原因的分析,主要从三个方面进行分析:1、辊子的受力分析;2、配重块的技术要求及动静平衡对辊子寿命的影响;3、配重块焊接在辊芯内壁上时,焊缝区的机械性能。
一、辊子受力方面的分析。
1、受力分析。
(压辊的重力忽略不计)气缸的规格是180B×45R×100ST,气缸的缸径180mm,活塞杆直径45mm,行程100mm,压缩空气的压力是5kg/cm2。
由此可以计算压缩空气通过活塞杆输出的压力F=л*(18/2)2*5*g=12.7KN。
均布载荷q=(12.7+12.7)/1.4=18.14KN/M2、剪力图3、弯矩图4、强度校核从图中可以看出,最大的弯矩的发生在辊子辊面中间位置,最大的弯矩数值为11.430KN*M。
max max max z M *y =I σ,引用记号z z max I W =y ,也成为抗弯截面系数,max max z M =W σ针对圆形截面的计算3z d W =32π 环形截面抗弯系数()34z πd W =1-α32,其中α=d/D Q275的弯曲许用应力是170MPa. 从辊子的图纸中可以计算()34z πd W =1-α32辊芯两侧距离边部200mm 以内横截面积一样均为环形截面。
最大的弯矩发生在辊芯的重心截面上。
()3max max 34z 3411.430KN *M 11.430*10M ===W πD π*0.2100.1801-α1-32320.210⎛⎞⎛⎞⎜⎟⎜⎟⎜⎟⎝⎠⎝⎠σ=27316070Pa =27.32MPa从上式中可以得出:27.32MPa<170MPa,说明辊芯的强度可以满足其使用要求。
轧机支撑辊断裂.doc

CL0502-轧机支撑辊断裂唐山科技职业技术学院潘韶慧案例简要说明:依据国家职业标准和金属材料及热处理技术、材料成型与控制技术专业教学要求,归纳提炼出所包含的知识和技能点,弱化与教学目标无关的内容,使之与课程学习目标、学习内容一致,成为一个承载了教学目标所要求知识和技能的教学案例。
该案例是轧钢设备使用与维护事故案例,体现轧辊材料的选择、轧辊的失效形式、轧辊的维护使用等知识点和岗位技能,与本专业轧钢机械设备课程轧辊及其维护使用单元的教学目标相对应。
(4)全面复习所学知识,并将知识转化为综合能力。
案例建议的6~8学时教学时间案例的操作现场调研、问题讨论、点评、案例分析、讲授、课堂练习、大作业。
(图片)演示本案例教学可实现现场案例与所学轧辊失效方面的知识有机结合,将书本知识转化为轧案例点评辊的维护使用工作能力,培养了学生的分析问题、解决问题的能力。
轧机支承辊断裂1.背景介绍某集团4300mm特厚板厂,采用高刚度的四辊可逆式轧机,四辊轧机前设置重型立辊轧机,四辊轧机最大轧制力:9600KN。
该轧机采用AGC系统和工作辊弯辊装置。
轧机高刚性有利于轧制宽度大的产品,是发挥厚度自动控制(AGC)功能的基础,同时也是满足控制轧制和板型控制的必要条件。
轧机前后配有除鳞装置,整个轧制阶段要完成成形轧制、宽展轧制和成品轧制。
该厂主要生产低合金、锅炉板、容器板、高建钢板、摸具钢板、船板等。
2.主要内容2.1.事故经过2013年4月15号23:00左右开始进行轧制烫辊,烫辊钢锭27t,材质为235B,烫辊时间45分钟左右,之后开始进行正式轧制第一支钢锭,轧制20道次后,发现下机架位轴承座移位上翘,停机检查发现下机架位支承辊断辊,支承辊断裂后,造成我公司方面支撑辊换辊小车拉头断裂,主传动轴滴油润滑罩子损坏,阶梯垫液压缸损坏。
2.2.事故原因分析(1)轧辊断裂位置分析。
烫辊后正式轧制的钢锭为21t的无冒口钢锭,钢锭尺寸为上端1660×800mm,下端为1620×732mm,材质为Q345B,开轧温度为1250℃,最后道次轧制温度950℃,轧制20道次后,发现下机架位轴承座移位上翘,停机检查发现下机架位支承辊断辊,断裂面整齐且垂直于轴线,断裂位置基本位于中部左右,距辊身操作侧端面长度为2173mm左右。
热轧轧辊剥落或断裂的原因及预防方法探究
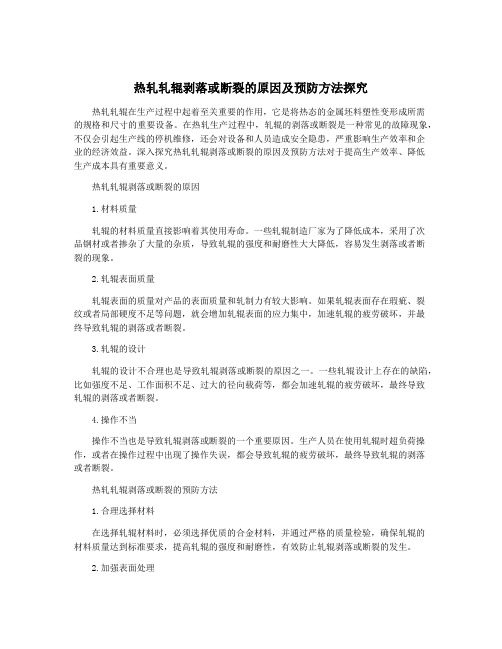
热轧轧辊剥落或断裂的原因及预防方法探究热轧轧辊在生产过程中起着至关重要的作用,它是将热态的金属坯料塑性变形成所需的规格和尺寸的重要设备。
在热轧生产过程中,轧辊的剥落或断裂是一种常见的故障现象,不仅会引起生产线的停机维修,还会对设备和人员造成安全隐患,严重影响生产效率和企业的经济效益。
深入探究热轧轧辊剥落或断裂的原因及预防方法对于提高生产效率、降低生产成本具有重要意义。
热轧轧辊剥落或断裂的原因1.材料质量轧辊的材料质量直接影响着其使用寿命。
一些轧辊制造厂家为了降低成本,采用了次品钢材或者掺杂了大量的杂质,导致轧辊的强度和耐磨性大大降低,容易发生剥落或者断裂的现象。
2.轧辊表面质量轧辊表面的质量对产品的表面质量和轧制力有较大影响。
如果轧辊表面存在瑕疵、裂纹或者局部硬度不足等问题,就会增加轧辊表面的应力集中,加速轧辊的疲劳破坏,并最终导致轧辊的剥落或者断裂。
3.轧辊的设计轧辊的设计不合理也是导致轧辊剥落或断裂的原因之一。
一些轧辊设计上存在的缺陷,比如强度不足、工作面积不足、过大的径向载荷等,都会加速轧辊的疲劳破坏,最终导致轧辊的剥落或者断裂。
4.操作不当操作不当也是导致轧辊剥落或断裂的一个重要原因。
生产人员在使用轧辊时超负荷操作,或者在操作过程中出现了操作失误,都会导致轧辊的疲劳破坏,最终导致轧辊的剥落或者断裂。
热轧轧辊剥落或断裂的预防方法1.合理选择材料在选择轧辊材料时,必须选择优质的合金材料,并通过严格的质量检验,确保轧辊的材料质量达到标准要求,提高轧辊的强度和耐磨性,有效防止轧辊剥落或断裂的发生。
2.加强表面处理对轧辊表面进行加强处理,提高轧辊的表面质量和强度,有效减少轧辊表面的裂纹和瑕疵,降低轧辊的疲劳破坏,延长轧辊的使用寿命,减少剥落或断裂的发生。
3.改善轧辊设计改善轧辊的设计,提高轧辊的强度和刚性,增加轧辊工作面积,合理分配径向载荷,减小轧辊的应力集中,降低轧辊的疲劳损伤,有效预防轧辊剥落或断裂。
宽厚板轧机弯辊系统故障分析与改进

宽厚板轧机弯辊系统故障分析与改进摘要本文描述湘钢3800 mm轧机弯辊系统基本功能、原理,并通过对弯辊系统所出现的问题进行持续跟踪、改进,解决了轧机弯辊系统频繁出现了各类问题,减少了事故,提高生产效率,改善钢板形状。
关键词弯辊缸;伺服阀;承压头;弯辊力;板形中图分类号TG333 文献标识码 A 文章编号1673-9671-(2012)051-0146-02湘钢3800 mm轧机为SEMAC设计,中国一重制造。
其中电控系统、液压系统和部分关键机械设备为进口设备。
弯辊系统是中厚板轧机重要的组成部分,对板型控制起到至关重要作用。
通过低温、大压下量轧制方式从而获得强度更高、性能更全面的现代轧制工艺方法对中厚板轧机弯辊系统提出了更高的要求。
1 系统组成、功能及原理1)组成:3800 mm轧机弯辊系统主要构成:伺服液压站、液压控制回路(伺服阀、液控单向阀、溢流阀)、压力传感器、PLC和16个弯辊缸构成。
液压原理:弯辊缸活塞侧和杆侧分开控制,杆侧是通过一个三通减压阀加切断阀,压力稳定在40bar,从而保证轧钢时活塞与缸头无直接接触;换辊时能自动收回去。
活塞侧液压回路中有平衡功能回路和弯辊功能回路两部分,采用并联连接,两个各自独立的回路上都有插装式切断阀并通过先导控制阀进行控制切断,从而保证检修和事故状况下的回路安全可靠。
2)功能:①紧急平衡功能,下工作辊弯辊缸的活塞侧压力为30 bar,作用是让下工作辊紧贴下支撑辊防止咬钢和抛钢时跳动;上辊油缸活塞侧压力为110 bar,作用:平衡掉上工作辊的重力、使上工作辊紧贴上支撑防止咬钢、抛钢时跳动。
当弯辊功能出现故障时,可切换到紧急平衡功能,保证生产的延续进行。
②弯辊功能:轧制以前,弯辊缸产生比较大的作用力,迫使工作辊产生一定的反向预弯曲,消除掉轧钢时辊系中间变形量,保证钢板厚度均匀和良好的板形。
图13)工作原理:当轧机L2接收到钢板信息后,轧制模型会自动计算出每一道次需要的弯辊力,后将弯辊力自动发给TCS系统(L1),此时PLC根据此期望弯辊力和现场传感器检测到的实际弯辊力进行比较,计算出偏差后,将此偏差信号送到伺服阀上从而达到期望的弯辊力。
轧机支撑辊断裂.doc

CL0502-轧机支撑辊断裂唐山科技职业技术学院潘韶慧案例简要说明:依据国家职业标准和金属材料及热处理技术、材料成型与控制技术专业教学要求,归纳提炼出所包含的知识和技能点,弱化与教学目标无关的内容,使之与课程学习目标、学习内容一致,成为一个承载了教学目标所要求知识和技能的教学案例。
该案例是轧钢设备使用与维护事故案例,体现轧辊材料的选择、轧辊的失效形式、轧辊的维护使用等知识点和岗位技能,与本专业轧钢机械设备课程轧辊及其维护使用单元的教学目标相对应。
(4)全面复习所学知识,并将知识转化为综合能力。
案例建议的6~8学时教学时间案例的操作现场调研、问题讨论、点评、案例分析、讲授、课堂练习、大作业。
(图片)演示本案例教学可实现现场案例与所学轧辊失效方面的知识有机结合,将书本知识转化为轧案例点评辊的维护使用工作能力,培养了学生的分析问题、解决问题的能力。
轧机支承辊断裂1.背景介绍某集团4300mm特厚板厂,采用高刚度的四辊可逆式轧机,四辊轧机前设置重型立辊轧机,四辊轧机最大轧制力:9600KN。
该轧机采用AGC系统和工作辊弯辊装置。
轧机高刚性有利于轧制宽度大的产品,是发挥厚度自动控制(AGC)功能的基础,同时也是满足控制轧制和板型控制的必要条件。
轧机前后配有除鳞装置,整个轧制阶段要完成成形轧制、宽展轧制和成品轧制。
该厂主要生产低合金、锅炉板、容器板、高建钢板、摸具钢板、船板等。
2.主要内容2.1.事故经过2013年4月15号23:00左右开始进行轧制烫辊,烫辊钢锭27t,材质为235B,烫辊时间45分钟左右,之后开始进行正式轧制第一支钢锭,轧制20道次后,发现下机架位轴承座移位上翘,停机检查发现下机架位支承辊断辊,支承辊断裂后,造成我公司方面支撑辊换辊小车拉头断裂,主传动轴滴油润滑罩子损坏,阶梯垫液压缸损坏。
2.2.事故原因分析(1)轧辊断裂位置分析。
烫辊后正式轧制的钢锭为21t的无冒口钢锭,钢锭尺寸为上端1660×800mm,下端为1620×732mm,材质为Q345B,开轧温度为1250℃,最后道次轧制温度950℃,轧制20道次后,发现下机架位轴承座移位上翘,停机检查发现下机架位支承辊断辊,断裂面整齐且垂直于轴线,断裂位置基本位于中部左右,距辊身操作侧端面长度为2173mm左右。
热轧轧辊剥落或断裂的原因及预防方法探究

热轧轧辊剥落或断裂的原因及预防方法探究【摘要】热轧轧辊剥落或断裂是热轧生产中常见的问题,严重影响生产效率和产品质量。
本文从热轧轧辊剥落或断裂现象引起注意和研究目的和意义两个方面展开,然后深入探讨了造成这一问题的原因,包括金属材料的质量问题、外部环境因素和工艺参数设置不当等。
针对这些原因,提出了一些有效的预防方法,如加强材料检验、保持良好的生产环境和合理设置工艺参数。
在研究成果总结和未来研究展望两个方面进行总结,指出今后需要深入研究轧辊剥落或断裂的原因及预防方法,以提高热轧生产的效率和质量。
通过本文的研究,有望为解决热轧轧辊剥落或断裂问题提供一定的参考和借鉴。
【关键词】热轧轧辊、剥落、断裂、金属材料、质量问题、外部环境、工艺参数、预防方法、研究成果、展望。
1. 引言1.1 热轧轧辊剥落或断裂现象引起注意热轧轧辊剥落或断裂是热轧生产中常见的问题,一旦发生会给生产带来严重的影响。
轧辊是热轧生产中不可或缺的重要设备之一,承担着对金属带材进行塑性加工的重要任务。
由于受到多种因素的影响,轧辊往往会出现剥落或断裂的现象,如果不及时处理和预防,将导致生产事故的发生,影响生产效率和产品质量。
热轧轧辊剥落或断裂现象需要引起注意,因为其主要危害包括:一是轧辊剥落或断裂会导致生产线停机,给企业带来直接的经济损失;二是剥落或断裂的轧辊会造成产品表面质量不达标,影响产品的销售和企业的声誉;三是轧辊剥落或断裂会增加生产中的安全隐患,可能导致事故发生,影响员工的生命安全。
对热轧轧辊剥落或断裂现象引起足够的重视,研究其发生的原因以及预防方法,对于提高生产效率、保证产品质量和保障人员安全具有重要意义。
本文旨在探究热轧轧辊剥落或断裂的原因及预防方法,为热轧生产提供一定的参考和指导。
1.2 研究目的和意义研究的目的在于深入探究热轧轧辊剥落或断裂的原因,分析其中可能存在的金属材料质量问题、外部环境因素以及工艺参数设置不当等方面的因素。
通过研究分析,可以为预防热轧轧辊剥落或断裂提供理论依据和技术支持,提高轧辊的使用寿命和生产效率。
宽厚板轧机万向接轴裂纹产生的原因分析及对策
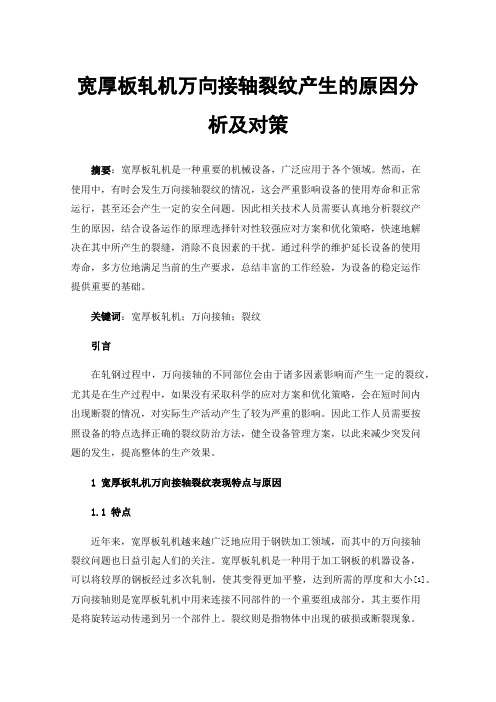
宽厚板轧机万向接轴裂纹产生的原因分析及对策摘要:宽厚板轧机是一种重要的机械设备,广泛应用于各个领域。
然而,在使用中,有时会发生万向接轴裂纹的情况,这会严重影响设备的使用寿命和正常运行,甚至还会产生一定的安全问题。
因此相关技术人员需要认真地分析裂纹产生的原因,结合设备运作的原理选择针对性较强应对方案和优化策略,快速地解决在其中所产生的裂缝,消除不良因素的干扰。
通过科学的维护延长设备的使用寿命,多方位地满足当前的生产要求,总结丰富的工作经验,为设备的稳定运作提供重要的基础。
关键词:宽厚板轧机;万向接轴;裂纹引言在轧钢过程中,万向接轴的不同部位会由于诸多因素影响而产生一定的裂纹,尤其是在生产过程中,如果没有采取科学的应对方案和优化策略,会在短时间内出现断裂的情况,对实际生产活动产生了较为严重的影响。
因此工作人员需要按照设备的特点选择正确的裂纹防治方法,健全设备管理方案,以此来减少突发问题的发生,提高整体的生产效果。
1宽厚板轧机万向接轴裂纹表现特点与原因1.1特点近年来,宽厚板轧机越来越广泛地应用于钢铁加工领域,而其中的万向接轴裂纹问题也日益引起人们的关注。
宽厚板轧机是一种用于加工钢板的机器设备,可以将较厚的钢板经过多次轧制,使其变得更加平整,达到所需的厚度和大小[1]。
万向接轴则是宽厚板轧机中用来连接不同部件的一个重要组成部分,其主要作用是将旋转运动传递到另一个部件上。
裂纹则是指物体中出现的破损或断裂现象。
宽厚板轧机万向接轴裂纹的位置通常不固定,可能出现在不同的部位,如轴承座、轴承支架、万向接头等处。
宽厚板轧机万向接轴裂纹的形状也非常多样化,有些是直线型,有些则呈现出分支或扩展的形态,形状不规则,难以预测。
宽厚板轧机万向接轴裂纹的严重程度也不尽相同,有些只是表面上的薄裂纹,对机器运行影响较小,而有些则是深度较大,经常会导致机器停运甚至事故发生。
宽厚板轧机万向接轴裂纹的成因十分复杂,可能由于材料质量问题、加工工艺不当、运行状态不稳定等多种原因造成。
热轧轧辊剥落或断裂的原因及预防方法探究
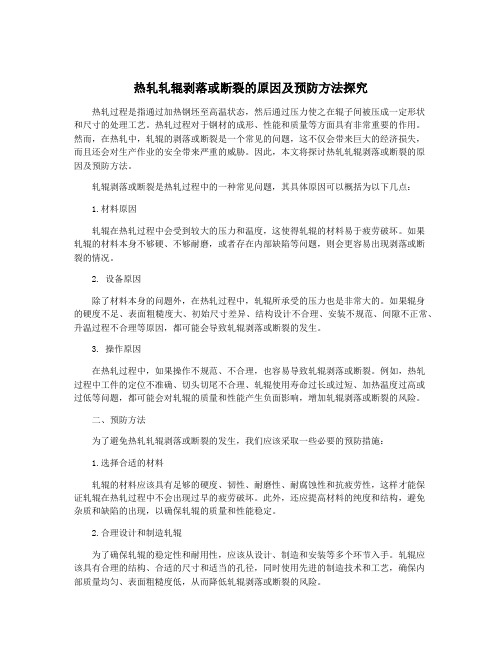
热轧轧辊剥落或断裂的原因及预防方法探究热轧过程是指通过加热钢坯至高温状态,然后通过压力使之在辊子间被压成一定形状和尺寸的处理工艺。
热轧过程对于钢材的成形、性能和质量等方面具有非常重要的作用。
然而,在热轧中,轧辊的剥落或断裂是一个常见的问题,这不仅会带来巨大的经济损失,而且还会对生产作业的安全带来严重的威胁。
因此,本文将探讨热轧轧辊剥落或断裂的原因及预防方法。
轧辊剥落或断裂是热轧过程中的一种常见问题,其具体原因可以概括为以下几点:1.材料原因轧辊在热轧过程中会受到较大的压力和温度,这使得轧辊的材料易于疲劳破坏。
如果轧辊的材料本身不够硬、不够耐磨,或者存在内部缺陷等问题,则会更容易出现剥落或断裂的情况。
2. 设备原因除了材料本身的问题外,在热轧过程中,轧辊所承受的压力也是非常大的。
如果辊身的硬度不足、表面粗糙度大、初始尺寸差异、结构设计不合理、安装不规范、间隙不正常、升温过程不合理等原因,都可能会导致轧辊剥落或断裂的发生。
3. 操作原因在热轧过程中,如果操作不规范、不合理,也容易导致轧辊剥落或断裂。
例如,热轧过程中工件的定位不准确、切头切尾不合理、轧辊使用寿命过长或过短、加热温度过高或过低等问题,都可能会对轧辊的质量和性能产生负面影响,增加轧辊剥落或断裂的风险。
二、预防方法为了避免热轧轧辊剥落或断裂的发生,我们应该采取一些必要的预防措施:1.选择合适的材料轧辊的材料应该具有足够的硬度、韧性、耐磨性、耐腐蚀性和抗疲劳性,这样才能保证轧辊在热轧过程中不会出现过早的疲劳破坏。
此外,还应提高材料的纯度和结构,避免杂质和缺陷的出现,以确保轧辊的质量和性能稳定。
2.合理设计和制造轧辊为了确保轧辊的稳定性和耐用性,应该从设计、制造和安装等多个环节入手。
轧辊应该具有合理的结构、合适的尺寸和适当的孔径,同时使用先进的制造技术和工艺,确保内部质量均匀、表面粗糙度低,从而降低轧辊剥落或断裂的风险。
3.规范操作和维护在热轧过程中,必须确保操作规范严谨。
轧辊破坏常见原因分析及对策.doc

CL0501-轧辊破坏常见原因分析及对策案例简要说明:依据国家职业标准和金属材料及热处理技术、材料成型与控制技术专业教学要求,归纳提炼出所包含的知识和技能点,弱化与教学目标无关的内容,使之与课程学习目标、学习内容一致,成为一个承载了教学目标所要求知识和技能的教学案例。
该案例是轧钢设备使用与维护事故案例,体现了轧辊材质及其力学性能等知识点和轧钢工、设备点检工的岗位操作技能,与本专业轧钢机械设备课程中轧辊部分、金属材料与热处理课程中金属材料的性能部分单元的教学目标对应。
轧辊破坏常见原因分析及对策天津冶金职业技术学院王磊该案例发生在承钢热带厂,该厂自1997年建成投产,生产至今已有10多年,在生产初期经常出现轧辊热裂纹、掉肉、局部破坏、外层剥落、甚至轧辊断裂等事故,轧辊发生故障后一般都需要做换辊处理,不仅增加了岗位作业人员的劳动量,而且降低日历作业率,造成废钢,影响成材率,影响轧机产量,同时更造成巨大的经济损失。
通过几年的摸索,对轧辊常见破坏形式进行归纳总结,并给出相应的解决办法。
该案例在教学过程中辅以图片等多媒体资源对学生进行讲解,让学生能够更好地掌握轧制过程中如何更好地延长轧辊的寿命。
1.背景介绍某厂自1997年建成投产,生产至今已有10多年,在生产初期经常出现轧辊热裂纹、掉肉、局部破坏、外层剥落、甚至轧辊断裂等事故,轧辊发生故障后一般都需要做换辊处理,不仅增加了岗位作业人员的劳动量,而且降低日历作业率,造成废钢,影响成材率,影响轧机产量,同时更造成巨大的经济损失。
通过几年的摸索,对轧辊常见破坏形式进行归纳总结,并给出相应的解决办法。
2.主要内容2.1.热应力断裂一、现象描述此类断裂多发生在粗轧机,一般在粗轧换辊后开轧10块钢以内,寒冷的冬季出现的几率更大一些。
轧辊辊身断层呈径向,起源位于或接近轧辊轴线,断裂面与轧辊轴线垂直,一般发生在辊身中部,如图1所示。
图1 热应力断裂断面形状二、轧辊破坏原因这种热应力断裂与轧辊表面和轴心处的最大温差有关。
热轧轧辊剥落或断裂的原因及预防方法探究
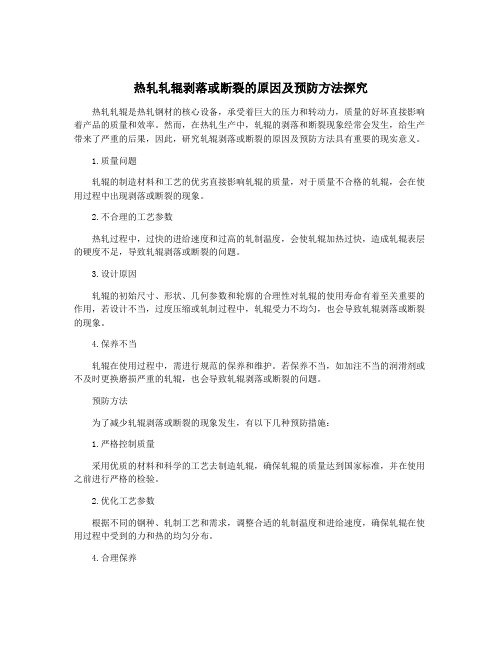
热轧轧辊剥落或断裂的原因及预防方法探究热轧轧辊是热轧钢材的核心设备,承受着巨大的压力和转动力,质量的好坏直接影响着产品的质量和效率。
然而,在热轧生产中,轧辊的剥落和断裂现象经常会发生,给生产带来了严重的后果,因此,研究轧辊剥落或断裂的原因及预防方法具有重要的现实意义。
1.质量问题轧辊的制造材料和工艺的优劣直接影响轧辊的质量,对于质量不合格的轧辊,会在使用过程中出现剥落或断裂的现象。
2.不合理的工艺参数热轧过程中,过快的进给速度和过高的轧制温度,会使轧辊加热过快,造成轧辊表层的硬度不足,导致轧辊剥落或断裂的问题。
3.设计原因轧辊的初始尺寸、形状、几何参数和轮廓的合理性对轧辊的使用寿命有着至关重要的作用,若设计不当,过度压缩或轧制过程中,轧辊受力不均匀,也会导致轧辊剥落或断裂的现象。
4.保养不当轧辊在使用过程中,需进行规范的保养和维护。
若保养不当,如加注不当的润滑剂或不及时更换磨损严重的轧辊,也会导致轧辊剥落或断裂的问题。
预防方法为了减少轧辊剥落或断裂的现象发生,有以下几种预防措施:1.严格控制质量采用优质的材料和科学的工艺去制造轧辊,确保轧辊的质量达到国家标准,并在使用之前进行严格的检验。
2.优化工艺参数根据不同的钢种、轧制工艺和需求,调整合适的轧制温度和进给速度,确保轧辊在使用过程中受到的力和热的均匀分布。
4.合理保养轧辊在使用过程中,应定期进行润滑和维护,并根据实际情况进行轧辊更换和修理,以保证轧辊使用寿命的延长。
总之,热轧轧辊的剥落或断裂问题的解决需要多方面的努力,除了以上预防措施之外,还需要提高工作人员的素质,严格执行操作规程,保证生产环境安全、清洁、整洁,以及进行适当的科技创新和技术改进,以确保轧辊质量及生产效率的提高。
轧机断带原因

轧机断带原因
在金属加工领域,轧制是一种常见的工艺,可以将原材料压制成板材、棒材等形状。
然而,有时候在轧制过程中会出现断带现象,导致生产中断,影响生产效率。
那么,造成轧机断带的原因有哪些呢?
1. 材料问题:材料的硬度、厚度、宽度等因素都会影响轧机的正常运行。
如果材料过硬、过厚或过宽,轧机可能无法将其压制成所需形状,从而产生断带现象。
2. 轧机问题:轧机的质量和性能也会影响加工效果。
如果轧机设备出现故障或使用时间过长,可能导致轧机无法正常工作,从而产生断带现象。
3. 操作问题:操作者的技能水平和操作流程也会影响轧机的运行。
如果操作者技能不够熟练或操作流程不规范,可能会导致轧机产生断带现象。
4. 温度问题:轧制过程中,材料的温度对轧机的运行也有很大影响。
如果温度过高或过低,轧机可能无法正常运作,从而产生断带现象。
综上所述,造成轧机断带的原因有很多,需要从多个方面进行控制和修正。
只有在材料、轧机、操作和温度等各个方面都得到合理的控制,才能有效避免轧机断带的发生,提高生产效率和质量。
- 1 -。
- 1、下载文档前请自行甄别文档内容的完整性,平台不提供额外的编辑、内容补充、找答案等附加服务。
- 2、"仅部分预览"的文档,不可在线预览部分如存在完整性等问题,可反馈申请退款(可完整预览的文档不适用该条件!)。
- 3、如文档侵犯您的权益,请联系客服反馈,我们会尽快为您处理(人工客服工作时间:9:00-18:30)。
从过 程计算 机 记 录 的速 度趋 势 发 现 , 轧 制 在 过程 中 咬钢瞬 间上下辊 速差 达到 7 5rmn 远远 . / i, 超过偏 差 1rmn正 常水平 , 辊辊 速 瞬 间降低 , / i 上 导致 下辊 承担扭 矩 瞬 间增 大 , 下 辊首 先 断 裂 的 是 重要原 因。经查 前一道 次咬入 和抛 出时分 别产 生 了 24 / n和 34 / i .7rmi .8rrn的速 度差 , a 同时 实物
L n n h n ih o iMig a d Z a g L e a
f n a o n t l o L ) dnI nadS e C . t Ha r e d
Ab ta l T i p p rd ti d y a ay e a s s o o k rl b e k g tt e c  ̄ r b t l g a h c e a n - s r c h s a e ea l l n ls s e H e f w r o r a a e a h o a y meal r p i x mi a e l o t n, lrs nc f w d tci n ,s e g h rve o h r k n wo k r l,di e o q e a d p ae f t e s rv asc u e i u t o i a ee t o a l o t n t iw n t e b o e r l r s tr u n l t an s ,e e l a s s r e o v l o o k r l b a a e b n lzn n o ai g t er lv t aa, s b ih ste p e e t eme s r sa a n t h o k fw r o r k g y a ay i g a d c mp r ee a t e t l e r v ni a ue g i s t e w r l e n h n d a s h v r l b a a e,i e ,o t zn h r i a a ss h d l n sa l h n o q e it r c i g p oe t n w e l n o r k g e . . p i ig t e o i n p s c e u e a d e t i ig t r u n e l kn r tci h n r l g mi g l b s o o o i i h p e ft p z i rf e,S s t r v n x e s e r l n o d a d a od a y p o u t n o q i me ta c — ntes e do a eodpo l r i O a o p e te c s i ol g la n v i n r d c i re u p n c i e v i o
Ca s sAn l ssa u t r e s r s o o k Rol u e ay i nd Co n e m a u e fW r l
Br a a e i i e a d He v a e M i e k g n W d n a y Pl t l l
速度 、 制 速度 、 钢速 度 以及选择 3种速 度的合 轧 抛 理切 入 点 , 自动实 现轧 机 低 速咬 钢 、 高速 轧制 、 低
参考 G / 10 B T 54—20 0 8附 录 B: 墨 铸 铁 轧 球
速抛钢的梯形速度轧制功能。这一功能的优点是 既降低 了咬人和抛钢时对轧钢机械设备 的冲击 , 又保障了所需的轧制节奏; 缺点上 、 工 作辊 的 电流 变化 数 据 分 下 析, 上辊电流是逐步增大 , 下辊电流是逐步增大后
i o n
当 日过 程机数 据 轧 制 力 矩 为 24 0k ・ 8 N 153 动 力矩计 算 ..
(.7 3 17×1 )= . 7×1 7P 6 . P 0 66 0 a= 6 7 M a
轧制时采用梯形速度 , 其角加速度设定为每 0 2s . 的加 速 度 29 / , 1. / 计 算 出下 .2rs即 4 6rs,
钢板也存在明显的波浪和扣头现象( 如图 6 。辊 )
速 差导 致上下 辊 产 生过 大 的 阻力 矩 , 造 成此 次 是 从 A C系统 获 得 数 据 显 示 , 七 道 次 压 下 G 第 量 2 . m, 次压 下率达 到 2 .3 。 制 力为 7 5m 道 97 % 轧
4 6 N。 09 4k
传 动扭 矩 Mc + +Md>318k m = 2 N・
传动扭矩 M 超过最大扭矩 3 0 N m是此 c 0k . 0 次 断辊 事故 的直接 原 因。
由此分 析 , 在进 行梯形 轧制 时 , 速产生 动力 升
常 , 巨大震动, 符合疲劳断裂特征 , 有 不 可以排除 轧辊材 质原 因产 生疲 劳断 裂 。
第1 7卷第 5期
・
宽厚板
WI DE AND HE AVY P AT L E
V 11 . . o . 7 No 5
Oco e 2 1 tb r 0 1
3 ’ 21 年 1 0 01 0月
宽厚 板轧 机工 作辊 断裂原 因分析 及对 策
李 明 张 立超
( 邯郸钢铁 有限责任公 司)
de t n.
Ke wo d Mea o r p i x miain, ol g a h p e f r p z i P o l o u n el c i g p oe t n y rs tl g a h c e a n t o R l n t e s e d o a od, r f e tr e it r kn r tci i t t e i q o o
事 故 的重要原 因 。
2 改 进措施
15 2 轧制 力矩 计算 .. 根 据下 辊半 径 R= .9m, 七道 次 压 下 量 0 4 第 z 2 . m, 制力 为 4 6 N。力臂 系数 l 7 5m 轧 h: 094k 取 05 , 算 出下辊 轧制 力矩 : .2 计
=
2 4 N ・I 73 k l l
根据卡环槽靠辊身端辊颈直径 d 06 3I. = . 0 I T 圆弧 r 0 0 m, = . 1 查应力集中系数表 , 得出应力集 中系数为 155 , .8 因此剪切应力值 : 5
r= 1 5 5 5 ・ . 8 =1 5 55 ×l3 6 8 0 . 8 3 6/
辊动 力矩 Md :
M d = FR = mR 3) 11
dt
=
选取 两 支 断 辊 辊 颈 强 度 较 小 值 =4 0 8 M a计算安全系数 : P,
安全 系数 = / 40 6. 72 ^r= 8 /67= . 安 全 系数 大 于 5 因此 辊 颈 强 度 满 足 正 常 轧 , 制要求 。
+朋 =2 4 0+6 8 48=3 2 N ・m 1 8 k
某厂使用新辊直径为 l 5 m, 0m 报废直径为 0
90m 以下 , 故 辊辊 径 90— 8 6 m 事 7 9 0mm, 为使 均 用 后期 , 由于 可逆 轧 制 , 交 变应 力 , 颈 和辊 头 受 辊 处均 可 能存 在疲 劳倾 向。但 若 辊 颈疲 劳 断 裂 , 不 会造 成 下 辊 扁 头 也 同 时 断 裂 。且 断 辊 时 响 声 异
体+ 碳化物 , 级 , 3 碳化物含量 < %。 5
断 口 B点 ( 距外 圆约 10 m 组织 形貌 见 图 0 m)
又减小 , 且上辊电流值远大于下辊电流值, 据此可 判 定下辊 先 断裂 , 上辊 不能 单 独 承 受过 大 的扭 矩
随后扭 断 。
1C , 点石 墨形 态 为 团、 虫 , ( )B 团 3级 , 化 率 球 8 % ; 织 为珠光 体 +碳 化 物 , 0 组 3级 , 化 物 含 量 碳
辊及球芯复合轧辊辊颈组织检验的规则及判定方 法, 对两支 断辊金 相组织进 行 了石墨 形态判 定 、 石
墨球 化评 级 、 碳化物 及铁 素体数 量评级 。 辊颈
1 1 1 上 辊金相 检测 .I
辊颈表面 A点组织形貌见图 1b , ( )A点石墨
形 态为 团 、 团虫 , , 化 率 8 % ; 织 为 珠 光 3级 球 0 组
M =P X ■
2 1 优化 梯形 速度设 计 . 21 00年某 厂 宽 厚 板 线 实施 了梯 形 速 度 轧 制 改造 , 改造过 程 中未 考 虑 升速 过 程 产 生动 力 矩 在
对压下规程的影 响, 要求梯形轧制攻关组首先根
据 设备 能力 和品种 开 发轧 制 的需 要 , 确定 所 需 的
摘
要
从断裂工作辊 的金相检测 、 超声波探伤 、 度校核 、 强 传动扭矩和板型等 方面 , 详细分析 了工作辊辊
头断裂原因 , 针对工作辊断裂原因制定了防范措施一在采 用梯形速 度轧 制时 , 优化原有 压下 规程 、 建立扭矩 联 锁保护 , 避免轧 制负荷过大 , 造成 生产 和设备事故 。 关键词 金相检测 梯形速度轧 制 扭矩联锁保护
<5 %
通 过对工 作 辊辊 头 断 裂原 因分 析 , 制定 改进
第5 期
李 明等: 厚板 宽 轧机 工作辊断裂原因分 析及 对策
・ 3・ 3
W =  ̄d3 6 =3 4 ×0. 4 /1 =3.1 /l .1 553 6 77 × l 。m 0_
: 0 6 05 4 4× .2×V .9× 75× .0 9 o4 2 . 00 1
式 中 : 为下辊 质量 , = 940k。 m 2 5 g
154 传动扭矩计算 .. 已知主机传动 额定扭矩 为 l36k m, 3 N・ 过
载 系数 22 .5倍 , 大传 动扭矩 为 300k ・ 最 0 N m。 不考 虑摩擦 力矩 时 , 动力 矩和静 力矩 合值 为