整体硬质合金立铣刀角度参数及刀型结构对其切削性能影响的研究
整体硬质合金立铣刀的创新结构
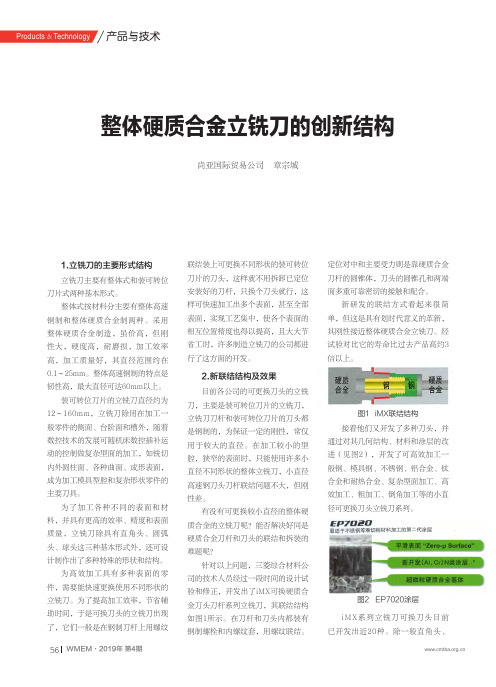
56WMEM·2019年 第4期Products & Technology产品与技术图1 iMX联结结构整体硬质合金立铣刀的创新结构尚亚国际贸易公司 章宗城1.立铣刀的主要形式结构立铣刀主要有整体式和装可转位刀片式两种基本形式。
整体式按材料分主要有整体高速钢制和整体硬质合金制两种。
采用整体硬质合金制造,虽价高,但刚性大,硬度高,耐磨损,加工效率高,加工质量好,其直径范围约在0.1~25mm。
整体高速钢制的特点是韧性高,最大直径可达60mm以上。
装可转位刀片的立铣刀直径约为12~160mm,立铣刀除用在加工一般零件的侧面、台阶面和槽外,随着数控技术的发展可随机床数控插补运动的控制做复杂型面的加工,如铣切内外圆柱面、各种曲面、成形表面,成为加工模具型腔和复杂形状零件的主要刀具。
为了加工各种不同的表面和材料,并具有更高的效率、精度和表面质量,立铣刀除具有直角头、圆弧头、球头这三种基本形式外,还可设计制作出了多种特殊的形状和结构。
为高效加工具有多种表面的零件,需要能快速更换使用不同形状的立铣刀。
为了提高加工效率,节省辅助时间,于是可换刀头的立铣刀出现了,它们一般是在钢制刀杆上用螺纹联结装上可更换不同形状的装可转位刀片的刀头,这样就不用拆卸已定位安装好的刀杆,只换个刀头就行,这样可快速加工出多个表面,甚至全部表面,实现工艺集中,使各个表面的相互位置精度也得以提高,且大大节省工时,许多制造立铣刀的公司都进行了这方面的开发。
2.新联结结构及效果目前各公司的可更换刀头的立铣刀,主要是装可转位刀片的立铣刀,立铣刀刀杆和装可转位刀片的刀头都是钢制的,为保证一定的刚性,常仅用于较大的直径。
在加工较小的型腔,狭窄的表面时,只能使用许多小直径不同形状的整体立铣刀,小直径高速钢刀头刀杆联结问题不大,但刚性差。
有没有可更换较小直径的整体硬质合金的立铣刀呢?能否解决好同是硬质合金刀杆和刀头的联结和拆装的难题呢?针对以上问题,三菱综合材料公司的技术人员经过一段时间的设计试验和修正,开发出了iMX可换硬质合金刀头刀杆系列立铣刀,其联结结构如图1所示。
整体式木工硬质合金立铣刀铣削温度仿真分析

整体式木工硬质合金立铣刀铣削温度仿真分析
贾娜;殷志成;陈肖男;李佳颖
【期刊名称】《林产工业》
【年(卷),期】2024(61)4
【摘要】以整体式木工硬质合金立铣刀铣削刨花板时铣刀温度分布为研究对象,探究铣削深度、前角、及螺旋角对铣刀温度的影响规律,并通过优化参数提升铣削过程的效率和稳定性。
采用动力学仿真分析模拟实际切削工况,对立铣刀铣削温度进行理论分析,得出铣削深度、前角、螺旋角三个主要研究变量。
通过Abaqus软件分析以及试验探究,分析以上三个研究变量对立铣刀铣削刨花板过程中刀刃温度变化的影响,验证了立铣刀铣削温度模型的可行性。
铣削过程中,铣刀的温度经历快速上涨、缓慢上升、趋于稳定三个阶段。
其他条件一定,当切削深度为4.0 mm,前角为17°,螺旋角为22°时,刀刃的平均温度较低。
研究结果对立铣刀铣削加工温度的深入研究具有重要的理论和实践意义。
【总页数】7页(P28-34)
【作者】贾娜;殷志成;陈肖男;李佳颖
【作者单位】东北林业大学机电工程学院;中国航发东安发动机有限公司
【正文语种】中文
【中图分类】TS653;TS396
【相关文献】
1.整体式立铣刀铣削加工中温度场有限元分析
2.切削参数对微铣削加工温度影响的ABAQUS有限元仿真分析
3.硬质合金立铣刀铣削难加工材料的仿真研究
4.直齿圆柱木工铣刀铣削切入过程动力学仿真分析
5.基于温度场仿真分析的整体式驱动电机设计优化
因版权原因,仅展示原文概要,查看原文内容请购买。
硬质合金刀片几何角度选择原则

硬质合金刀片几何角度选择原则硬质合金刀片作为切削加工工具广泛应用于现代生产制造业,作为财富切削利器,株洲三鑫硬质合金生产有限公司荣誉出品硬质合金刀片几何角度的选择以满足最佳使用要求作为原则,主要体现在以下方面。
1.前角前脚大,切削层的塑性变形小,刀-屑摩擦阻力小,切削力和切削热可降低,但前角过大,则切削刃和合金刀头强度降低,散热条件恶化,刀具寿命下降,前角较小,切屑变形增大,断屑容易,前角的大小与其他集合参数一样,应依加工要求合理选择,其选择原则是:a.工件材料的强度、硬度越低,塑性越好,应取较大的前角;加工脆性材料(如铸铁)或刀-屑接触长度短的材料(如钛合金)时,应取较小的前角;加工特硬材料(如淬硬钢、冷硬铸铁)甚至可取负的前角。
b.刀具材料的抗弯强度及韧性越高,可取较大的前角。
c.断续加工或粗加工有硬皮的锻、铸件时,应适当减小前角,但如果此时有较大的负刃倾角配合,可取较大前角,以减小径向切削力。
d.高速切削时,前角对切屑变形及切削力的影响较小,可取较小前角。
e.成形硬质合金刀具的前角,应根据具体加工要求选择。
2.后角/副后角减小刀具的后刀面或副后刀面与工件之间的摩擦。
但后角过大,会减弱切削刃强度,并恶化散热条件,使刀具寿命下降。
其选择原则是:a.精加工时,切削厚度薄,磨损主要发生在后刀面,取较大后角;粗加工时,切削厚度大,负荷重,前、后刀面均要发生磨损,取较小后角。
b.多刃硬质合金刀具切削厚度较薄,应取较大后角。
c.被加工工件刚性差(如细长轴或薄壁工件)时,应取较小后角,以增大后刀面与工件的接触面积,减少或消除振动。
d.工件材料较软、黏,加工硬化倾向大,弹性模量小时,后面摩擦严重,则取较大后角;工件材料硬度高、强度高,为保证刃口强度,取较小后角;但对加工硬材料的负前角刀具,后角应稍微大些,以便刀刃易于切入工件;加工脆性材料,负荷集中在刃口处,直接缺较小后角。
e.尺寸硬质合金刀具(如内拉刀,绞刀)应取较小后角,以免重磨后刀具尺寸变化太大。
整体合金立铣刀的设计
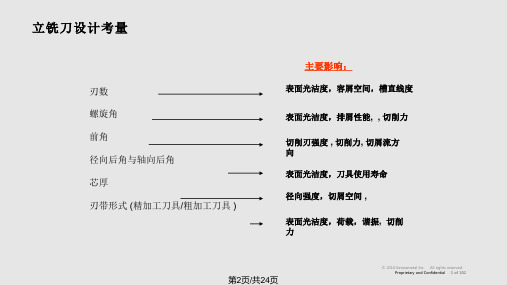
第3页/共24页
刀柄直径
立铣刀设计基本参数
侧视图
端视图
径向前角
主后角
轴向锲角 主后角
次后角
次后角
过中心刃
© 2010 Kennametal Inc. l All rights reserved. l Proprietary and Confidential l 3 of 102
凹角
锲角
第4页/共24页
切削面
次要后角
第10页/共24页
© 2010 Kennametal Inc. l All rights reserved. l Proprietary and Confidential l 9 of 102
前刀面设计
传统前刀面 (一个表面) 接触区大
切屑速度慢 接触区小
快速切屑 前刀面 (两个表面)
刀尖条件
刃数
容屑空间
2刃 过中心切削
3刃 过中心切削
4刃 过中心切削
6刃
8刃
过中心切削 过中心切削
表面光洁度
第5页/共24页
© 2010 Kennametal Inc. l All rights reserved. l Proprietary and Confidential l 4 of 102
齿距
© 2010 Kennametal Inc. l All rights reserved. l Proprietary and Confidential l 12 of 102
粗加工齿形
粗加工刀具
粗齿 铝,非铁材料
深槽铣 主轴荷载少
半精加工刀具
密齿 钢,铸铁 仿形,槽铣 耐磨损性能好
超密齿 不锈钢,钛,高温合金
整体硬质合金刀具

由于硬质合金的硬度高,其耐磨性也相对较 好,能够在长时间加工过程中保持切削刃的 完整性,减少磨损和崩刃现象。
强度与韧性
强度
整体硬质合金刀具具有较高的抗弯强度和抗 压强度,能够在承受较大的切削力和冲击力 的加工过程中保持稳定。
韧性
硬质合金的韧性较好,不易脆化,能够有效 吸收冲击能量,提高刀具的抗破损能力。
切削速度与切削深度
切削速度
整体硬质合金刀具的切削速度较快,能够显著提高加工效率,同时也能减小切削力,降 低切削热。
切削深度
由于硬质合金的硬度高和强度大,整体硬质合金刀具能够承受较大的切削深度,从而在 一次装夹中完成更多的加工步骤。
耐热性与抗氧化性
耐热性
整体硬质合金刀具在高温下仍能保持较好的硬度和强度 ,不易发生热软化和氧化现象,提高了加工过程的稳定 性和刀具寿命。
和排屑效果。
切削参数匹配
根据工件材料和切削要求,选择合适 的切削速度、进给速度和切削深度, 以确保最佳的切削效果。
刀具品牌与质量
选择知名品牌的整体硬质合金刀具, 确保其质量和性能满足加工要求。
使用注意事项
01
02
03
04
刀具安装
确保刀具正确安装于机床上, 特别是切削刃对准工件中心线
。
切削液使用
根据加工要求和刀具材质,选 择合适的切削液,以提高切削
选用高纯度、低氧含量的钨粉作为原料,确保刀具的硬度和 耐磨性。
碳化钨制备
将钨粉与碳化钨粉末按比例混合,通过球磨、喷雾干燥等工 艺制刀具的形状和尺寸设计模具,确保成型过程中尺寸精度和形状稳定性。
压制成型
将混合料放入模具中,通过压制成型工艺制成刀具毛坯。
烧结
烧结温度
整体硬质合金螺旋木工立铣刀的设计及加工工艺
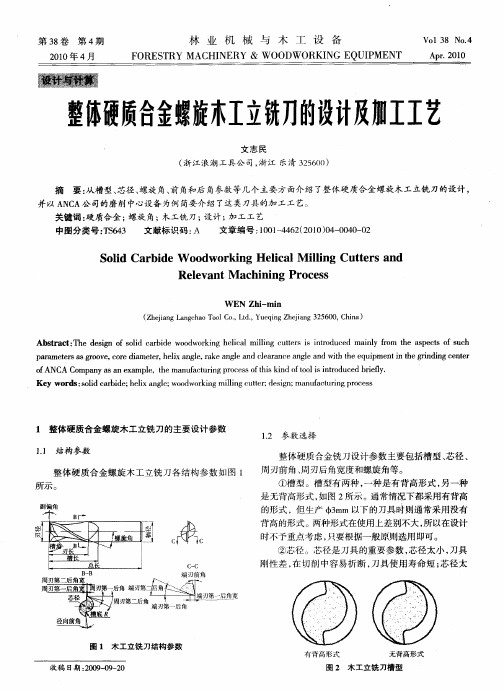
粗加丁相对精加工来说余量大 , 切削抗力 大。因此 在设 计粗加 工铣 削刀具 时应 主要考 虑刀具 的强度 、 容
屑空 间和排 屑 问题 。而设计 精加工铣 削刀具时考虑 的 重点则是加 1 后如何 获得光滑 的切 削表面质量和提 高 二 加二 效率的问题 。具体应注意以下几点 。 r
景 塞 B - B
篓 角蔗 =唇
◎ ◎
有背高形式 无背高形式
收 稿 日期 :0 9 0 — 0 20 — 9 2
图 2 木 工立 铣 刀 槽 型
第4 期
文志 民 : 整体硬质合金螺旋木工立铣 刀的设计及 加工丁艺
明等 , 柄部参数标注示例如 图 3 所示 。
1 精、 . 5 粗铣 刀 在 设 计 上 的 区别
度等影 响都非常大 ,因此 前角 的设计 是刀具设计 的重
要组成部 分之一 。木材是 属于材 质较 软和易 于切削材 料, 因此在设 计时应选择 比较大 的正前角 , 一般在 1 。 7~
2。 间选取 。 5之
①刀具的芯径直接影响刀具整体的刚性 , 在有足够
排 屑空 间 的前 提下 粗 铣 刀应 尽量 增加 刀 具芯 径 的尺
( hj n a g h o o l o Ld, u qn h j n 2 6 0 C ia Z e a gL n c a o C . t.Y e ig ei g3 5 0 , hn ) i T , Z a
Absr c : e d sg fs l abde wo d r ig h l a ln utr s ito u e an y fo te a p cs o u h t a t Th e in o oi c r i o wo kn ei lmi ig c t si nr d c d m il rm h s e t fs c d c l e
精磨硬质合金数控刀片切削与磨损性能的实验研究

第27卷第4期2009年12月 河北建筑工程学院学报J OUR NAL O F HEBEI INSTITUTE OF AR C HITEC TUR E AN D C IVIL ENG INEER INGVol 27No 4Dec.2009收稿日期:20090820作者简介:女,1963年生,教授,张家口市,075024基金项目:河北省科技厅科学技术研究与发展计划项目(05212157)精磨硬质合金数控刀片切削与磨损性能的实验研究郭秀云 梁建明 王占英 刘春东 王少雷河北建筑工程学院摘 要 对YT 14三角形硬质合金数控刀片的切削与磨损性能进行了实验研究.在实验中,针对两种不同精度级的数控刀片进行了切削性能和磨损特性对比实验.实验表明:刀片精度级越高,其磨损速度越低.用高精度级刀片进行切削加工,不仅可以提高工件的加工表面质量,还可延长刀片的使用寿命,从而节省刀片的购置费用,具有可观的经济效益和社会效益.关键词 刀片;磨损;切削中图分类号 TH160 引 言数控机床在我国机械行业应用越来越普遍,数控刀具的制造与使用直接影响着数控机床效率的发挥.目前,在西方工业化国家中,硬质合金已占刀具材料的65%以上,硬质合金可转位刀片产量已达刀片总产量的70%~90%,所以研究硬质合金数控刀片的切削与磨损性能具有现实意义.国外硬质合金刀片产品分为精密级和普通级.精密级硬质合金刀片公差带很小,刀片必须经过精研,从而使刀片表面质量得到改善,但价格十分昂贵.从进口刀具产品外观质量上看,其外观、颜色和纹理明显优于国产刀具.在刀具产品使用性能上,进口刀具加工尺寸精度高、稳定性好、耐用度高、切除率高,刀具及其配件具有良好的互换性,一般装配后即可达到精度要求.在我国随着机械加工技术不断进步,硬质合金可转位刀具在机械行业的使用也越来越广泛.从目前使用情况来看,国产硬质合金可转位刀具的市场占有率低于进口刀具.由于国产硬质合金刀片的数量及品种均不能满足生产的需要,每年不得不花费美元去进口数控刀片.这样,从我国生产实际出发,应立足于国内数控刀片的生产,在产品外观上加以改进,相应增加一些表面处理工艺.国产硬质合金刀片精磨后,尺寸精度与国外的精密级刀片相近,刀片钝圆半径小,刀片表面质量也改善了,因此应用于精加工的场合,刀片的寿命长、可靠性好,而且价格便宜,极限切削深度也可取更小值.本实验分别对常规磨削与经精磨后的YT14三角形数控刀片进行了切削性能对比实验,观察并分析了刀片的磨损情况,探索了提高数控刀片的加工精度和延长刀片使用寿命的途径,为降低刀片的购置费用提供了理论依据和实验验证.1 实验装置本实验采用由无锡市荣盛合金工具有限公司生产的硬质合金切削刀片YT 14三角形可转位数控刀片.常规磨削的三角形数控刀片,表面粗糙度在Ra0 4~0 8甚至更高些.而需精磨的三角形数控刀片,将其固定在自行设计的专用夹具上,利用金刚石砂轮对各个刀面进行磨削.最后将各个加工面在金刚石研磨机上进行研磨,直至达到所需精度为Ra0 014~0 06.切削性能对比实验在沈阳机床厂生产的CAK3665di 型号数控机床进行.利用上海光学仪器五厂生产的型号为4XB 显微镜对三角形可转位数控刀片的主切削刃磨损量VBmax 进行观测.工件材料为45钢,直径为 40的棒料.2 实验条件及结果(1)当切削深度a p =1mm 、工件转速n w =500r/m in 、进给量f =0 2mm/r 时,经同等条件实验五次后,未经磨削与经精磨后的三角形数控刀片后刀面的最大磨损量VBmax (取平均值)与切削时间t 的实验数据见表1,VBmax 与t 的对应关系曲线见图1.表1 VBm ax 与t 的实验数据t(min)6 412 819 225 632 0VBmax(mm)未磨0 1060 1470 1750 1980 215已磨0 0750 1120 1520 183195图1 切削时间与磨损量的对应关系 图2 切削速度与磨损量的对应关系(2)当进给量f =0 2mm/r 、切削深度a p =1mm 、切削长度为640mm 时,经同等条件实验五次后,常规磨削与经精磨后的三角形数控刀片后刀面的最大磨损量VBm ax (取平均值)与切削速度V 的实验数据见表2,VBm ax 与V 的对应关系曲线见图2.表2 VBmax 与V 的实验数据V(m/min)62 8075 3687 92100 48113 04VBmax(mm)未磨0 1060 1330 1630 1970 227已磨0 0750 1110 1430 1630 187(3)当V =113 04m /min 、切削深度a p =1mm 、切削长度为640m m 时,经同等条件实验五次后,未经磨削与经精磨后的三角形数控刀片后刀面的最大磨损量VBmax (取平均值)与进给量f 的实验数据见表3,VBmax 与f 的对应关系曲线见图3.表3 VBm ax 与f 的实验数据f(mm/r)0 100 150 200 250 30VBmax(mm)未磨0 2200 2240 2270 2290 233已磨0 1820 1850 1870 1890 193(4)当V =113 04m/min 、进给量f =0 2mm/r 、切削长度为690mm 时,经同等条件实验五次后,未经磨削与经精磨后的三角形数控刀片后刀面的最大磨损量VBm ax (取平均值)分别与切削深度a p 的实验数据见表4,VBm ax 与ap 的对应关系曲线见图4.77第4期 郭秀云 梁建明 王占英等 精磨硬质合金数控刀片切削与磨损性能的实验研究表4 VBmax 与ap 的实验数据ap(mm)12345VBmax(mm)未磨0 2270 2280 2290 2300 230已磨0 1870 1880 1880 189189图3 进给量与磨损量的对应关系 图4 切削深度与磨损量的对应关系3 实验结果分析从图1~图4我们可以看到:(1)在整个切削过程中,当切削条件相同时,我们进行比较后刀面最大磨损量值.实验结果表明:未磨刀片的磨损量值大于经精磨后刀片的磨损量.(2)刀片在刚开始进行切削时,已磨刀片与未磨刀片的磨损量差值较大,随着切削时间的延长,此差值略有减小的趋势.(3)对刀片磨损量影响最大的是切削速度.在切削过程中,随着切削速度的提高,未磨和已磨刀片的磨损量均剧增,且未磨与已磨刀片磨损量差值处于0 020~0 041mm 的范围内.(4)进给量对未磨和已磨刀片的磨损量也有影响,仅次于切削速度.当改变进给量时,未磨和已磨刀片的磨损量处于0 038~0 040mm 的范围内.(5)切削深度的改变对未磨和已磨刀片的磨损量影响最小,二者的磨损量差值也基本保持稳定状态,处于0 040~0 041mm 之间.4 磨损量的经验公式利用角正回归法,对实验数据进行处理,可得后刀面磨损量的回归方程为:未磨为:VB max =0 00576a p0 1256f 0 7159V0 9866(mm);已磨为:VB max =0 00712a p 0 1523f 0 8976V 1 3116(mm);式中单位为:VB(mm );a p (m m);f(m m/r);V(m/min).5 结 论(1)由于已磨刀片表面精度高且结构密实,提高了表面硬度,能够减小刀片与切屑之间的摩擦系数,降低切削力,使刀片具有较好的耐磨性,促使刀片的抗磨损能力增强,从而其使用寿命也大大提高.(2)利用经精磨后的数控刀片进行切削加工,随切削参数的变化可不同程度地降低刀片的磨损速度,提高刀片的使用寿命.(3)在切削过程中,切削速度对刀片的切削性能及磨损速度影响最大;进给量次之;而切削深度影响最小.78河北建筑工程学院学报 第27卷(4)当改变进给量和切削深度时,已磨和未磨刀片的磨损量差值均略大于改变切削速度时二者的差值,所以大进给量和大切削深度的切削方式更能使刀片的使用寿命相对延长.(5)建议无论在粗加工或精加工时,尽量使用经精磨后的刀片进行切削加工.这样不仅提高了加工精度,而且还能延长刀片的使用寿命,从而节省刀片的购置费用.这一技术若广泛推广,将会产生良好的经济效益和社会效益.参 考 文 献[1]郭秀云.硬质合金磨削力的实验研究.硬质合金,1996,1[2]郭秀云.硬质合金材料磨削机理及磨削温度的实验研究.天津大学研究生毕业论文,1996,8[3]郭秀云.硬质合金磨削温度的实验研究.硬质合金,1997,2[4]于启勋.新型硬质合金 添加稀土元素的硬质合金.现代刀具材料系列讲座(七),2005,11,12[5]周泽华主编.金属切削原理.上海科学技术出版社,1984,12[6]陈章燕.平面、外圆磨削力计算公式的研究和应用.磨床与磨削,1992,4:27~31[7]郭秀云.磨削硬质合金材料去除机理的实验研究.硬质合金,1997,5[8]郭秀云.硬质合金磨削温度场的实验研究.硬质合金,1999,2[9]郭秀云.硬质合金刀片磨损性能的实验研究.新技术新工艺,2000,10The Experimental Study on Cutting and Wear Performance ofFine Grinding Cemented Carbide Numerical Control ToolsGuo Xiuy un ,Lian g Jia nm in g ,Wa ng Zha nyin g ,Liu Chun don g ,Wa ng Sha oleiH ebei Institute o f A rchitectur e and Civil Engineer ingAbstract T he cutting and w ear perform ance of YT 14triang le cemented carbide numerical contro lto ols w ill be studied ex perimentally in this paper.T he ex periment show s that the hig her the too l 's precisio n level is,the m ore slow ly it w ear s.H ig h precision leveled tools are used in the cutting process,w hich can not only im pro ve the surface cutting quantity,but also pr olong the tool's life time,then the purchasing expense of tools is saved and considerable economic and social benefits can be got.Key words tool;w ear;cutting79第4期 郭秀云 梁建明 王占英等 精磨硬质合金数控刀片切削与磨损性能的实验研究。
硬质合金铣刀切削参数表【一览表】

切削速度的选择主要取决于被加工工件的材质;进给速度的选择主要取决于被加工工件的材质及立铣刀的直径。
国外一些刀具生产厂家的刀具样本附有刀具切削参数选用表,可供参考。
但切削参数的选用同时又受机床、刀具系统、被加工工件形状以及装夹方式等多方面因素的影响,应根据实际情况适当调整切削速度和进给速度。
当以刀具寿命为优先考虑因素时,可适当降低切削速度和进给速度;当切屑的离刃状况不好时,则可适当增大切削速度。
高速钢立铣刀的使用范围和使用要求较为宽泛,即使切削条件的选择略有不当,也不至出现太大问题。
而硬质合金立铣刀虽然在高速切削时具有很好的耐磨性,但它的使用范围不及高速钢立铣刀广泛,且切削条件必须严格符合刀具的使用要求。
1 铣削速度V指铣刀旋转时的圆周线速度,单位为m/min。
计算公式;V=兀DN/1000式中D——铣刀直径,mm;N——主轴(铣刀)转速,r/min。
从上式可得到:主轴(铣刀)转速:N=1000V/兀D铣削速度V推荐值2进给量在铣削过程中,工件相对于铣刀的移动速度称为进给量.有三种表示方法:铣刀每转过一个齿,工件沿进.给方向移动的距离, 单位为mm/z。
(1) 每齿进给量af(2) 每转进给量f铣刀每转过一转, 工件沿进.给方向移动的位为距离, 单位为mm/r.。
(3) 每分钟进给量V f铣刀每旋转1min, 工件沿进.给方向移动的位为距离, 单位为mm/ min。
.zn三种进给量的关系为: V f=af式中a——每齿进给量,mm/z。
.fz——铣刀(主轴)转速,r/min。
n——铣刀齿数.。
铣刀每齿进给量, a(mm/z.) 推荐值f3铣削层用量铣刀在一次进给中所切掉工件表面的宽度,单位为mm。
.(1)铣削宽度ae一般立铣刀和端铣刀的铣削宽度约为铣刀直径的50%~60%左右。
(切削深度) 铣刀在一次进给中所切掉工件表面的厚度,即工件的已加(2)背吃刀量ap工表面和待加工表面间的垂直距离,单位为mm。
硬质合金切削工具材料性能研究
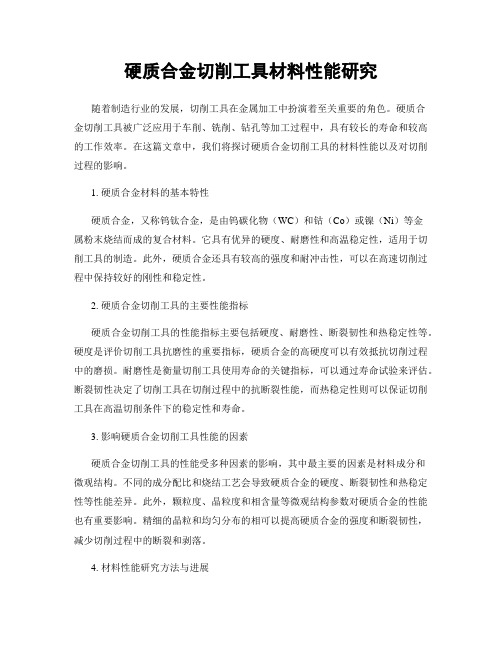
硬质合金切削工具材料性能研究随着制造行业的发展,切削工具在金属加工中扮演着至关重要的角色。
硬质合金切削工具被广泛应用于车削、铣削、钻孔等加工过程中,具有较长的寿命和较高的工作效率。
在这篇文章中,我们将探讨硬质合金切削工具的材料性能以及对切削过程的影响。
1. 硬质合金材料的基本特性硬质合金,又称钨钛合金,是由钨碳化物(WC)和钴(Co)或镍(Ni)等金属粉末烧结而成的复合材料。
它具有优异的硬度、耐磨性和高温稳定性,适用于切削工具的制造。
此外,硬质合金还具有较高的强度和耐冲击性,可以在高速切削过程中保持较好的刚性和稳定性。
2. 硬质合金切削工具的主要性能指标硬质合金切削工具的性能指标主要包括硬度、耐磨性、断裂韧性和热稳定性等。
硬度是评价切削工具抗磨性的重要指标,硬质合金的高硬度可以有效抵抗切削过程中的磨损。
耐磨性是衡量切削工具使用寿命的关键指标,可以通过寿命试验来评估。
断裂韧性决定了切削工具在切削过程中的抗断裂性能,而热稳定性则可以保证切削工具在高温切削条件下的稳定性和寿命。
3. 影响硬质合金切削工具性能的因素硬质合金切削工具的性能受多种因素的影响,其中最主要的因素是材料成分和微观结构。
不同的成分配比和烧结工艺会导致硬质合金的硬度、断裂韧性和热稳定性等性能差异。
此外,颗粒度、晶粒度和相含量等微观结构参数对硬质合金的性能也有重要影响。
精细的晶粒和均匀分布的相可以提高硬质合金的强度和断裂韧性,减少切削过程中的断裂和剥落。
4. 材料性能研究方法与进展研究硬质合金切削工具材料性能的方法主要包括实验测试和数值模拟。
实验测试可以通过切削试验、硬度测试、显微镜观察等手段来获取硬质合金的性能数据。
数值模拟则通过计算机模拟切削过程中的材料应力、变形和热传导等物理过程,预测硬质合金切削工具的性能。
近年来,基于人工智能和机器学习的模型也逐渐应用于硬质合金材料性能研究中,提高了研究效率和准确性。
5. 切削工具性能改善的途径为了改善硬质合金切削工具的性能,研究人员采取了多种途径。
立铣刀螺旋角

立铣刀螺旋角大小对切削性能的影响1螺旋刃立铣刀的基本特性与问题的提出立铣刀的基本刃口形状(螺旋槽形状)有直形和螺旋形两种.由于螺旋刃立铣刀相对于直刃具有切削轻快、平稳、效率高和使用范围广等优点,因此在铣削加工中得到了广泛应用.根据加工设备和加工对象的不同要求,螺旋刃立铣刀有左刃、右刃和左螺旋、右螺旋之分的4种不同组合〔1〕,其中左刃左螺旋和右刃右螺旋在加工中的轴向切削阻力有把立铣刀从刀夹中拔出的趋势,需采用拉紧螺栓克服轴向切削阻力.而左刃右螺旋和右刃左螺旋的轴向切削阻力刚好把立铣刀压向夹头方,故多采用锥柄加扁尾,以适应大功率切削.因为右刃右螺旋立铣刀可让切屑沿排屑槽向柄部排出,易保证切削的平稳进行,符合机床主轴旋向标准,在高性能夹头的支持下装卸方便,所以,其使用范围最广,使用量最大.实际应用中的螺旋刃立铣刀,其螺旋角通常在30°~45°.在刀具原理、设计和应用技术领域,根据工件材料、刀具材料及切削加工诸参数的不同,有关螺旋刃立铣刀的切削力、扭矩、切削功率及前角、后角等主要刀具角度的设计计算公式、实验数据与使用经验等资料很多,但有关螺旋角大小与立铣刀加工性能的讨论和资料介绍很少.一般认为,螺旋刃立铣刀的螺旋角β就是刃倾角λs,但有关刃倾角的介绍和讨论主要以车削加工为主线展开,而铣削和车削毕竟有许多不同之处,因此不可能完全适用.对铣削而言,通常认为较大的螺旋角可以增加同时工作的齿数,减少铣削过程中的冲击和增加其平稳性〔2〕,并使立铣刀刀刃锋利、实际前角增大.除此之外,螺旋角的大小对立铣刀的性能究竟还会产生什么样的影响呢?刀具角度之间是相互联系和影响的.不妨首先通过实验和实际加工例,取得初步认识和相关知识,为进一步的深入探讨做准备.2螺旋角与2刃立铣刀铣槽实验实验在立式加工中心上进行.采用直径 12mm的不同螺旋角的2刃立铣刀,铣宽度×高度为12mm×12mm的槽,并以加工后槽的底面为基准,测量槽的两侧面的垂直度误差(侧面最大变形量ΔX),通过比较误差值的大小来评价螺旋角大小对立铣刀铣槽时加工精度的影响.被切削材料为硬度28HRC的碳素钢.实验中各刀具的切削参数统一为:进给速度50mm/min,切削速度29m/min,吃刀深度12mm.切削中冷却液选用油性.实验结果如图1所示.图1螺旋角与铣槽时的加工精度图2铣侧面时的螺旋角与加工精度从实验结果可以看出:(1)逆铣侧总是出现过切,而与之相反,顺铣侧总是出现漏切,且过切量和漏切量的最大点在立铣刀伸出最远处.这一点符合逆铣、顺铣时的刀具变形规律和刀具伸出长度的变形规律.(2)立铣刀的螺旋角小于30°前,不管是顺铣侧还是逆铣侧,垂直度误差值都随螺旋角的增大而增大.螺旋角大于40°以后,又随螺旋角的增大而变小.因此,可以认为立铣刀有较小的螺旋角或有较大的螺旋角时,其铣槽加工的形状精度高.(3)从加工精度看,在螺旋角为0,即切削刃为直刃时精度最高.但从立铣刀螺旋角的基本特性可知,这时完全呈断续切削,切削冲击力大,对刀具本身的制作精度要求高,加工精度对刀具本身精度的依赖性很强,刀具的使用寿命短.所以,实际应用中应根据具体情况辩证地考虑.3螺旋角与4刃立铣刀铣侧面实验在立式加工中心上,用螺旋角分别为30°和55°度的4刃立铣刀铣侧面,比较两种立铣刀随切削宽度(径向吃刀量)的变化对加工精度的影响.立铣刀直径为 25mm,被切削材料为硬度94HRB的45号钢.切削全部采用顺铣方式和干式切削.切削参数统一为:进给速度100mm/min,切削速度26m/min,切削深度38mm.加工后所测得的垂直度误差、平面度误差和表面粗糙度值如图2所示.可以看出,在切削宽度不是特别大时,55°的大螺旋角立铣刀比30°螺旋角立铣刀的加工精度高.这一点与图1的铣槽实验结果相吻合.分析其原因,可以认为这是由于当切削宽度较小时,螺旋角较大的立铣刀实际前角大,刃口锋利,切入性好;切向切削阻力小,减小能量消耗和刀具变形,切削轻快;切削刃与被切削面的接触点多,使立铣刀切入和切出时比较平稳,切削阻力的波动小,减弱了加工中对立铣刀的振动激励等因素的综合效应所致.4螺旋角特性的归纳(1)螺旋角与切削阻力:切向切削阻力随螺旋角的增大而减小,轴向切削阻力随螺旋角的增大而增大.(2)螺旋角与前角:螺旋角的增大使立铣刀实际前角增大,刃口更加锋利.(3)螺旋角与被加工面精度:一般被加工面的垂直度和平面度公差值随螺旋角的增大而增加,但螺旋角大于40°以后反而随螺旋角的增大而呈减小趋势.(4)螺旋角与刀具寿命:圆周刃刃带的磨损速度与螺旋角大小基本成正比;另一方面,当螺旋角很小时,轻微的刀具磨损也将明显降低刀具的切削性能,引起振动,使刀具无法继续使用.当螺旋角过大时,刀具刚性变差,寿命减低.(5)螺旋角与被切削材料:加工硬度低的软质材料时,用大螺旋角,以增大前角,提高刃口的锋利性;加工硬度高的硬质材料时,用小螺旋角,以减小前角,提高刃口的刚性.5结束语螺旋角是螺旋刃立铣刀的主要参数之一,螺旋角大小的改变对刀具的切削加工性能有很大影响.随着数控加工技术和柔性制造技术的发展,在刀具制造工艺上改变螺旋角的大小已成为可能和非常简便.如果进一步深入研究螺旋角大小对螺旋刃立铣刀切削性能的各种影响,在制造和选用螺旋刃立铣刀时,结合机床和工装卡具的性能,根据被加工材料的性能及加工精度、加工效率以及刀具材料和刀具寿命等因素综合考虑,优化螺旋角的大小,无疑会对促进高效、高精铣削加工起重要作用.。
硬质合金刀具刃口几何参数对工件加工影响研究

硬质合金刀具刃口几何参数对工件加工影响研究发布时间:2021-06-28T06:57:36.548Z 来源:《防护工程》2021年6期作者:林春雨郑伟张恒鑫徐云飞吴学岩宿华龙李冰王剑[导读] 机械加工刀具切削工件时,刀具刃口的几何角度与切削用量、切削力、切削温度及工件质量有重要联系。
适合的角度不仅能使刀具更加耐用,合理的几何角度配合具有良好的散热效果亦可以减小工件残余应力的产生。
林春雨郑伟张恒鑫徐云飞吴学岩宿华龙李冰王剑吉林江机特种工业有限公司吉林省吉林市 132021机械加工刀具切削工件时,刀具刃口的几何角度与切削用量、切削力、切削温度及工件质量有重要联系。
适合的角度不仅能使刀具更加耐用,合理的几何角度配合具有良好的散热效果亦可以减小工件残余应力的产生。
1 切削热零件切削时刀具与工件发生相对运动,切削接触期间摩擦及挤压发生物理形变,并释放切削热,刀具前角γ、后角α及螺旋角β所吸收的热量不尽相同,且呈梯度关系。
前角的温度最高,且主要集中在中下部,该部位是切削接触的主要部位,工件毛坯残屑脱离时带走的热量二次接触再次赋予了热量。
铣削工件时,不仅由温度较高形变区组成,同时包含摩擦问题,[1] 而当毛坯余量低于刀具前角时,温度出现增高的现象,是因为后角成为了主要的切削角,而后角挤压程度大于前角所造成的,挤压加剧了形变的产生从而增加了热量的释放,这时后角成为了主要参加切削的角,它的热量最高,接触部分是热量集中的部分,此状态所释放的热量高于前角成为主要切削刃的温度,因为它对于温度的释放是不利的。
当然,外界因素的制约影响了切削热的产生和释放,如切削深度、切削速度、切削用量的大小及冷却介质的流量。
所述表达的是:切削时后角摩擦接触产生了主要的热量,前角的热量是塑性形变和排除残屑接触的热量叠加。
2 残余应力残余应力是影响加工变形主要因素,亦是影响工件精度稳定的因素。
切削加工不可避免会产生残余应力,刀具几何参数、切削用量、切削热等因素影响残余应力,刀具刃口几何角度对残余应力的分布有很大影响。
硬质合金立铣刀对316L不锈钢的铣削加工研究
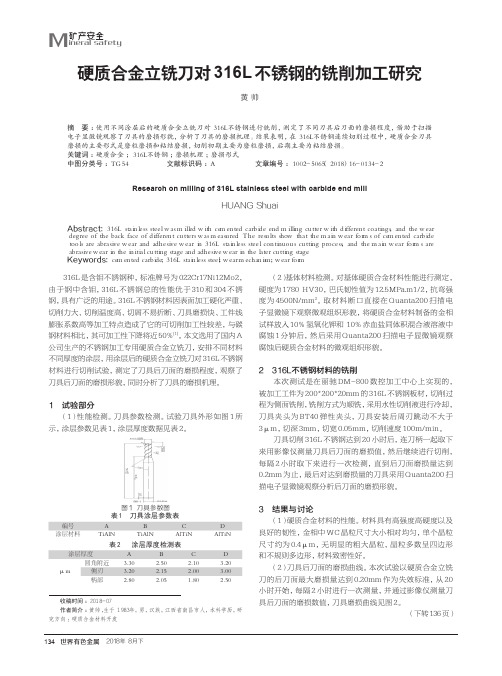
收稿时间:2018-07作者简介:黄帅,生于1983年,男,汉族,江西省南昌市人,本科学历,研究方向:硬质合金材料开发316L 是含钼不锈钢种,标准牌号为022Cr17Ni12Mo2,由于钢中含钼,316L 不锈钢总的性能优于310和304不锈钢,具有广泛的用途。
316L 不锈钢材料因表面加工硬化严重、切削力大、切削温度高、切屑不易折断、刀具磨损快、工件线膨胀系数高等加工特点造成了它的可切削加工性较差,与碳钢材料相比,其可加工性下降将近50%[1]。
本文选用了国内A 公司生产的不锈钢加工专用硬质合金立铣刀,安排不同材料不同厚度的涂层,用涂层后的硬质合金立铣刀对316L 不锈钢材料进行切削试验,测定了刀具后刀面的磨损程度,观察了刀具后刀面的磨损形貌,同时分析了刀具的磨损机理。
1 试验部分(1)性能检测。
刀具参数检测。
试验刀具外形如图1所示,涂层参数见表1,涂层厚度数据见表2。
图1 刀具参数图表1 刀具涂层参数表编号A B C D 涂层材料TiAlNTiAlNAlTiNAlTiN 表2 涂层厚度检测表涂层厚度A B C D μm 圆角附近3.30 2.50 2.10 3.20侧刃3.20 2.15 2.00 3.00柄部2.802.051.802.50(2)基体材料检测。
对基体硬质合金材料性能进行测定,硬度为1780 HV30,巴氏韧性值为12.5MPa.m1/2,抗弯强度为4500N/mm 2。
取材料断口直接在Quanta200扫描电子显微镜下观察微观组织形貌,将硬质合金材料制备的金相试样放入10%氢氧化钾和 10%赤血盐同体积混合液溶液中腐蚀1分钟后,然后采用Quanta200扫描电子显微镜观察腐蚀后硬质合金材料的微观组织形貌。
2 316L不锈钢材料的铣削本次测试是在丽驰DM-800数控加工中心上实现的,被加工工件为200*200*20mm 的316L 不锈钢板材,切削过程为侧面铣削,铣削方式为顺铣,采用水性切削液进行冷却,刀具夹头为BT40弹性夹头,刀具安装后周刃跳动不大于3μm,切深3mm,切宽0.05mm,切削速度100m/min。
硬质合金车刀几何角度选择原则

●硬质合金车刀合理前角、后角的参考值(1)前角的选择增大前角,可减小切削变形,从而减小切削力、切削热,降低切削功率的消耗,还可以抑制积屑瘤和鳞刺的产生,提高加工质量。
但增大前角,会使楔角减小、切削刃与刀头强度降低,容易造成崩刃,还会使刀头的散热面积和容热体积减小,使切削区局部温度上升,易造成刀具的磨损,刀具耐用度下降。
选择合理的前角时,在刀具强度允许的情况下,应尽可能取较大的值,具体选择原则如下:1)加工塑性材料时,为减小切削变形,降低切削力和和切削温度,应选较大的前角,加工脆性材料时,为增加刃口强度,应取较小的前角。
工件的强度低,硬度低,应选较大的前角,反之,应取较小的前角。
用硬质合金刀具切削特硬材料或高强度钢时,应取负前角。
2)刀具材料的抗弯强度和冲击韧性较高时,应取较大的前角。
如高速钢刀具的前角比硬质合金刀具的前角要大;陶瓷刀具的韧性差,其前角应更小。
3)粗加工、断续切削时,为提高切削刃的强度,应选用较小的前角。
精加工时,为使刀具锋利,提高表面加工质量,应选用较大的前角。
当机床的功率不足或工艺系统的刚度较低时,应取较大的前角。
对于成形刀具和在数控机床、自动线上不宜频繁更换的刀具,为了保证工作的稳定性和刀具耐用度,应选较小的前角或零度前角。
(2)后角的选择增大后角,可减小刀具后刀面与已加工表面间的摩擦,减小磨损,还可使切削刃钝圆半径减小,提高刃口锋利程度,改善表面加工质量。
但后角过大,将削弱切削刃的强度,减小散热体积使散热条件恶化,降低刀具耐用度。
实验证明,合理的后角主要取决于切削厚度。
其选择原则如下:1)工件的强度、硬度较高时,为增加切削刃的强度,应选较小后角。
工件材料的塑性、韧性较大时,为减小刀具后刀面的摩擦,可取较大的后角。
加工脆性材料时,切削力集中在刃口附近,应取较小的后角。
2)粗加工或断续切削时,为了强化切削刃,应选较小的后角。
精加工或连续切削时,刀具的磨损主要发生在刀具后刀面,应选用较大的后角。
硬质合金刀具铣削Ti6Al4V时刀具磨损及切削力研究

磨 损及 寿命 有 至关 重 要 的影 响 。因 此 , 用 切 削力 在 利 切削 过程 中 的变 化 来 辅 助 分 析 刀 具 的 磨 损 规 律 及 机
理 , 而 找 出力 、 度 、 削 方 式与 刀具 磨 损 之 间 的关 从 温 切
・
1・ O 2
; Ⅲ等 ; ‘ ■
维普资讯
Th1 d Z艺与检溺 en g n c0y 0a
维普资讯
工艺与检测 nga T 0yn 酬 1 d 0
硬 质 合 金 刀 具 铣 削 T6 4 时刀 具 磨 损 及 切 削 力研 究 iAIV
王 晓 琴① 艾 兴① 赵 军① 李 甜 甜 ① ②
( 山东 大 学机械 工程 学 院 , ① 山东 济 南 206 ; 济南 大学机 械 工程 学院 , 50 1② 山东 济 南 202 ) 502 摘 要: 对硬 质 合金 刀具在 干切 削 状态 下 铣 削 T6 IV 磨 损 机 理和 切 削 力进 行 了试 验 研 究 , 削 速 度分 别 iA4 切
Absr c t a t:Dr l n e tf rwe rme h nim n ut n o c t un se a b d o lh v e o e a ut y mi i g t s o a c a s a d c t g f r e wih t g t n c r i e to a e be n d n tc - l i t p e i s e d 40,8 ng O,1 0,1 0m/mi 2 6 n,t e r lto s i ewe n c ti g f r e a d c ti g s e d,c ti h e ai n h p b t e u tn o c n u tn p e ut ng d sa c sa ay e T o lwe ra d we rme h n c r n e t ae itn e wa n l z d. he to a n a c a iswe e i v si t d.T e r s ls s o t tb n - g h e u t h w ha o d i g a d d f ig a e t e man we rme h n s fc r i e c t ng to s n n if n r h i a c a ims o a b d u t o l. us i Ke ywo d r s:Ti 4V ;Cut n pe d;Cutn o c 6AI t gS e i t g F r e;To lW e r i o a ;W e r Me h nim a c a s
硬质合金刀具在金属切削中的应用研究

硬质合金刀具在金属切削中的应用研究摘要:硬质合金刀具作为一种重要的刀具材料,在金属切削领域中具有广泛的应用。
本文通过分析硬质合金刀具的特性,探讨了其在金属切削中的应用研究现状及面临的挑战,并提出了未来的发展方向。
关键词:硬质合金刀具,金属切削,应用研究引言硬质合金刀具是根据研究人员对金属切削工艺发展的需要而设计的一种高性能切削工具。
它由金属粉末和添加剂经热处理而成,具有高硬度、高强度、耐磨损等优点,适用于对各种金属进行高效切削。
本文旨在通过对硬质合金刀具在金属切削中的应用研究进行系统的探讨,为相关行业的工程师和研究人员提供一定的参考和指导。
硬质合金刀具特性硬质合金刀具是由钴基或镍基合金粉末和一定比例的超硬颗粒(通常是碳化钨)以及其他辅助材料混合制备而成。
其具有以下特性:1. 高硬度:硬质合金刀具的硬度通常在80-95HRA之间,可以切削各种硬度的金属材料。
2. 高强度:硬质合金刀具具有较高的强度和刚性,可以在高速切削过程中保持较好的刚性,减少刀具变形和震动。
3. 耐磨损性:硬质合金刀具的超硬颗粒具有优异的耐磨损性,能够在长时间的切削过程中保持刀具的良好切削性能。
4. 耐热性:硬质合金刀具由于添加了合适的金属粉末,能够有效降低切削过程中的热膨胀和高温脆断现象。
硬质合金刀具在金属切削中的应用研究现状硬质合金刀具在金属切削领域中具有广泛的应用,已经取得了一系列显著的研究成果。
以下是一些典型的应用研究案例:1. 切削性能研究:许多研究人员针对硬质合金刀具的切削性能展开了深入的研究。
他们通过设计不同切削参数和刀具结构,评估了硬质合金刀具的切削力、切削温度、刀具磨损等指标,提出了切削性能优化的方法和策略。
2. 表面质量优化:硬质合金刀具在金属切削中的应用还涉及到对工件表面质量的要求。
一些研究人员通过控制切削参数和采用特殊的刀具结构,成功提高了金属加工的表面光洁度和粗糙度。
3. 刀具寿命评估:硬质合金刀具的使用寿命直接影响到加工成本和工艺效率。
立铣刀讲义

问题 耐热合金切削加工时旳要点?
Ni合金、Co合金、钛合金
耐热合金旳特征
耐热合金旳特征
热传导率低、高温强度高、易加工硬化、与工具材料亲和力大 旳材料.尤其是Ni合金等超耐热合金、钛合金等旳难削材具有 硬、粘旳特征.热传导率低、切削热传导于切屑困难而集中于切 削点、切削刀刃旳热影响大.
不易切 削粒子
把微量旳冷却液加在高压气体中喷到刀具上起到冷却旳效果.对于环境旳污染 也降到最低程度
切削途径对刀具旳影响 ●高速加工首选等高切削
等高切削
仿形切削
为了得到最长旳刀具寿命,在铣削过程中应使切削刃尽量长时间地保持连续切削, 最佳是顺铣.在这方面采用等高线铣削是最佳措施,它能让刀具一直沿着一种方向切削,
受力变化是最小旳.
二.提升刀具旳刚性 尽量选用刃长和伸出长度较短旳立 铣刀,或锥颈型旳铣刀
三.降低切削负荷 经过变化刀具旳刃部形状降低切削 负荷
Ad1 Ad2 Ad3 Ad4
刀具刚性 小
切削载荷 大
F1 F2 F3 F4
刀具刚性 大
切削载荷 小
铣削和车削旳比较 ●切削速度和磨损旳关系
磨损 mm 0.1 0.2 0.3
切削途径对刀具旳影响 ●加工效果不好可尝试变化刀路
等高层铣
侧视图
渐进侧铣
俯视图
有时槽加工使用等高层铣加工效果不好,刀尖易崩(切深小),刀具产生振动.这时可尝试
采用侧面渐进旳措施,加大切削深度,使用刀具旳侧刃铣削,选择多刃型增长刀具旳刚性.
球头刀 圆鼻刀旳优劣区别 ●圆鼻刀 优: 1.效率高,底刃和侧刃都能够用
车削
铣削 最佳切 削区间
200
●排屑比较
600
V mm/min
06整体式硬质合金立铣刀切削参数简表

最小最大<0.25%C 退火125(-)220230≥0.25%C 退火190(11)170190<0.55%C 淬火和回火250(24.5)140150≥0.55%C 退火220(18)140150≥0.55%C 淬火和回火300(32)120130最小最大最小最大退火200(13.8)140150Fz Fz Fz Fz 淬火和回火275(28)10011010.0030.00510.0030.007淬火和回火300(32)1101201.30.0030.01 1.30.0030.012P 非合金钢和铸钢、易切削钢D(mm)铣槽D(mm)方肩铣/仿型铣低合金钢和铸钢(所有合金元素比例低于5%)标准切削条件材 质条件布氏硬度(HB)≈(HRC)Vc (m/min)淬火和回火350(37.9)1201301.50.0030.02 1.50.0030.022退火200(13.8)110130 1.80.0050.025 1.80.0050.028淬火和回火325(34.5)607020.0050.0320.0050.033铁素体/马氏体200(13.8)1001702.30.0050.03 2.30.0050.033马氏体型240(22.8)601502.50.0050.03 2.50.0050.03奥氏体型180(8)701002.80.010.035 2.80.010.038铁素体/珠光体180(8)7022030.010.0430.010.044珠光体260(26.6)1102003.30.0150.04 3.30.010.044铁素体型160(3.2)13023040.0150.04540.0150.049珠光体250(24.5)702304.30.020.045 4.30.0150.049铁素体型130(-)13023050.0250.0550.020.055珠光体230(20.5)11020060.030.0660.0250.066M 不锈钢和铸钢K 球墨铸铁GGG 灰口铸铁GG 可锻铸铁高合金钢、铸钢和工具钢标准切削条件未固化6067070070.030.0770.030.077固化10061069080.030.0880.030.088≤12%Si 未固化7567070090.030.0890.030.088固化90610690100.0350.09100.030.098>12%Si 高温130270280120.040.1120.0350.108>1%Pb 易切削110330350140.050.11140.040.119黄铜90330350160.050.12160.050.13电解铜100230250180.050.13180.050.14---200.050.15200.050.17---250.060.15250.060.18N 变形铝合金铸造铝,铝合金铜合金非金属硬质塑料、纤维塑料硬质橡胶铁基退火200(13.8)2030铁基固化280(29)2020镍基或铜基退火250(24.5)2030镍基或铜基固化350(37.9)2020镍基或铜基铸造320(34.2)3060RM4003060RM10503060淬火55HRC 3040淬火60HRC 3030冷硬铸铁铸铁400(43.1)5060铸铁淬火55HRC 30403、粗铣用ap 最大=1.5D V=1.25×Vc 高速切削高硬度材料(硬度最高HRC60):使用小切深:Vc 为80~160m/min 时,ap 等于0.1~0.3mm 1、铣槽用M 型材料--ap 最大=0.5D S 型材料--ap 最大=0.25D 2、精铣用P 型材料--ap 最大=1.5D S 高温合金钛和钛合金α-β固化合金H 淬火钢。
硬质合金铣刀涂层性能的试验研究
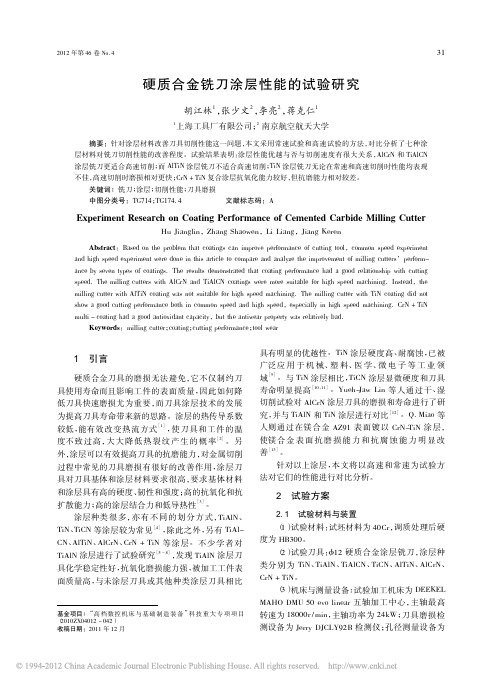
31
硬质合金铣刀涂层性能的试验研究
胡江林1 ,张少文2 ,李亮2 ,蒋克仁1
1上海工具厂有限公司; 2 南京航空航天大学
摘要: 针对涂层材料改善刀具切削性能这一问题,本文采用常速试验和高速试验的方法,对比分析了七种涂
层材料对铣刀切削性能的改善程度。试验结果表明: 涂层性能优越与否与切削速度有很大关系,AlCrN 和 TiAlCN
文献标志码: A
Experiment Research on Coating Performance of Cemented Carbide Milling Cutter
Hu Jianglin,Zhang Shaowen,Li Liang,Jiang Keren
Abstract: Based on the problem that coatings can improve performance of cutting tool,common speed experiment and high speed experiment were done in this article to compare and analyze the improvement of milling cutters’performance by seven types of coatings. The results demonstrated that coating performance had a good relationship with cutting speed. The milling cutters with AlCrN and TiAlCN coatings were more suitable for high speed machining. Instead,the milling cutter with AlTiN coating was not suitable for high speed machining. The milling cutter with TiN coating did not show a good cutting performance both in common speed and high speed,especially in high speed machining. CrN + TiN multi - coating had a good antioxidant capacity,but the antiwear property was relatively bad.
硬质合金刀具的材料特性与切削原理分析

硬质合金刀具的材料特性与切削原理分析硬质合金刀具作为现代切削工具中的重要组成部分,具有优秀的耐磨性、高强度和良好的切削性能,被广泛应用于金属加工行业。
本文将对硬质合金刀具的材料特性和切削原理进行详细分析。
首先,我们来了解硬质合金刀具的主要材料成分。
硬质合金刀具通常由钴基或钨基高硬度合金粉末与金属粉末通过高温烧结而成。
其中,钴基合金刀具的主要成分为碳化钨(WC)和钴(Co)两种物质的混合物,而钨基合金刀具则主要由碳化钨(WC)和碳化钨钎焊合金(WCCo)两种材料构成。
这些材料的合理配比和制造工艺,使得硬质合金刀具具有硬度高、韧性强、耐磨性好等显著特点。
硬质合金刀具的硬度高是由其成分中的碳化钨所决定的。
碳化钨具有极高的硬度,能够抵抗金属切削过程中的高温和高压,使其具备较长的使用寿命。
另外,硬质合金刀具的韧性强则是由所含的钴决定的,钴具有良好的塑性和可加工性,能有效减轻硬质合金刀具的脆性,提高其整体强度和韧性。
钴还能提高硬质合金刀具的抗断裂和抗疲劳性能,使其具有更好的稳定性和切削效率。
在切削原理方面,硬质合金刀具的切削过程主要是通过切削刃与被加工的工件之间的物理作用完成的。
切削刃通过与工件接触并在切削速度和切削力的作用下,将工件上的材料剪切、切削或磨削掉,实现加工目的。
硬质合金刀具的切削原理可以分为两种类型:切削刃切削和磨削刃切削。
切削刃切削适用于金属切削加工,主要通过硬质合金刀具的切削刃与工件的相对运动进行剪切切削。
切削刃切削的切削原理是将工件材料剥离,并且通过一系列连续的块剥、微剥和微小切削粒子的形成来完成切削过程。
而磨削刃切削则适用于非金属材料的加工,如陶瓷、纸张等,其切削原理是通过硬质合金刀具的磨削刃与工件之间的磨削作用,使工件材料发生微小磨削并剥离。
此外,硬质合金刀具还具有一定的刃口几何形状,如刀角、前角、侧倾角等,这些刃口参数的选择关系到切削力的大小和切削质量。
合理的刃口参数能够降低切削力,提高切削效率和切削质量。
硬质合金车刀几何角度选择原则
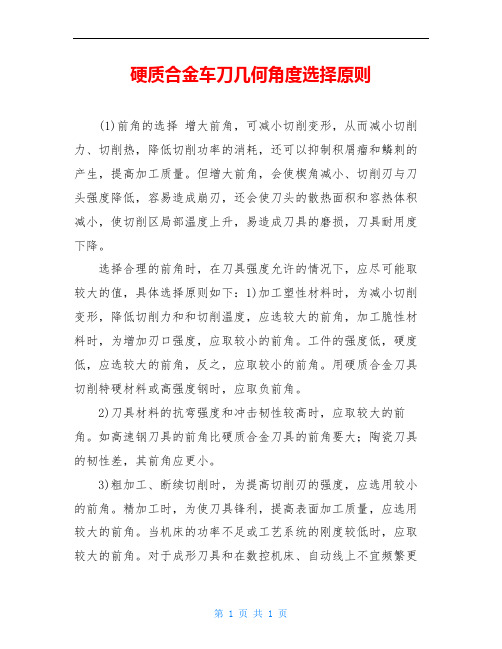
硬质合金车刀几何角度选择原则(1)前角的选择增大前角,可减小切削变形,从而减小切削力、切削热,降低切削功率的消耗,还可以抑制积屑瘤和鳞刺的产生,提高加工质量。
但增大前角,会使楔角减小、切削刃与刀头强度降低,容易造成崩刃,还会使刀头的散热面积和容热体积减小,使切削区局部温度上升,易造成刀具的磨损,刀具耐用度下降。
选择合理的前角时,在刀具强度允许的情况下,应尽可能取较大的值,具体选择原则如下:1)加工塑性材料时,为减小切削变形,降低切削力和和切削温度,应选较大的前角,加工脆性材料时,为增加刃口强度,应取较小的前角。
工件的强度低,硬度低,应选较大的前角,反之,应取较小的前角。
用硬质合金刀具切削特硬材料或高强度钢时,应取负前角。
2)刀具材料的抗弯强度和冲击韧性较高时,应取较大的前角。
如高速钢刀具的前角比硬质合金刀具的前角要大;陶瓷刀具的韧性差,其前角应更小。
3)粗加工、断续切削时,为提高切削刃的强度,应选用较小的前角。
精加工时,为使刀具锋利,提高表面加工质量,应选用较大的前角。
当机床的功率不足或工艺系统的刚度较低时,应取较大的前角。
对于成形刀具和在数控机床、自动线上不宜频繁更换的刀具,为了保证工作的稳定性和刀具耐用度,应选较小的前角或零度前角。
(2)后角的选择增大后角,可减小刀具后刀面与已加工表面间的摩擦,减小磨损,还可使切削刃钝圆半径减小,提高刃口锋利程度,改善表面加工质量。
但后角过大,将削弱切削刃的强度,减小散热体积使散热条件恶化,降低刀具耐用度。
实验证明,合理的后角主要取决于切削厚度。
其选择原则如下:1)工件的强度、硬度较高时,为增加切削刃的强度,应选较小后角。
工件材料的塑性、韧性较大时,为减小刀具后刀面的摩擦,可取较大的后角。
加工脆性材料时,切削力集中在刃口附近,应取较小的后角。
2)粗加工或断续切削时,为了强化切削刃,应选较小的后角。
精加工或连续切削时,刀具的磨损主要发生在刀具后刀面,应选用较大的后角。
- 1、下载文档前请自行甄别文档内容的完整性,平台不提供额外的编辑、内容补充、找答案等附加服务。
- 2、"仅部分预览"的文档,不可在线预览部分如存在完整性等问题,可反馈申请退款(可完整预览的文档不适用该条件!)。
- 3、如文档侵犯您的权益,请联系客服反馈,我们会尽快为您处理(人工客服工作时间:9:00-18:30)。
整体硬质合金立铣刀角度参数及刀型结构对其切削性能影响的研究整体硬质合金立铣刀角度参数及刀型结构对其切削性能影响的研究整体硬质合金立铣刀角度参数及刀型结构对其切削性能影响的研究整体硬质合金立铣刀角度参数及刀型结构对其切削性能影响的研究:2013-5-9 11:58:15毕业论文(科学研究报告)题目整体硬质合金立铣刀角度参数及刀型结构对其切削性能影响的研究院(系)别机电及自动化学院专业机械工程及自动化级别 2008摘要本文阐述了整体硬质合金立铣刀的发展现状与目前国内整体硬质合金刀具的大体水平,并对金鹭公司的整体硬质合金立铣刀做了个简单的介绍。
后面,在角度参数方面对几把金鹭公司的整体硬质合金平头立铣刀的几个重要参数(前角、后角、螺旋角、尖角保护)进行切削性能的研究实验。
其次,在刀型结构上选择金鹭公司铝合金立铣刀与模仿某知名公司的做的铝合金立铣刀做对比切削实验,得出刀具刀型结构对切削性能的影响。
在以上的基础上,对金鹭公司平云系列2刃、3刃平头立铣刀对切高硬材料(HRC?40)易先在底刃与圆周刃交接处先崩刃的现象提出改进方案,并实验分析。
最后通过实验现象数据与切削磨损图片对比分析可以得出以下结论: 1. 前角大,刃口锋利,切屑变小,切削力小,切削轻快。
但易产生崩刃,影响切屑形态,前角小切屑变形大,易折断。
立铣刀的螺旋角越大,工件与刀刃的接触线越长,施加到单位长度的刀刃上的负荷就会越小,从而有利于刀具的寿命。
但另一方面,螺旋角增大,切削抵抗的轴方向分力也增大,使得刀具容易从刀柄中脱落。
对切削高硬材料,减小后角有利于增大刀刃的强度,从而可以提高刀具耐用度。
2. 铣刀切削过程中刀尖最先与切削材料接触并使切削阻力最先作用与刀尖上,容易引起刀具从刀尖最先崩刀,加了尖角保护可以加大切削阻力的承受面积,从而达到保护刀尖的作用提高刀具的耐用度。
3. 刀具的排屑槽的增大使得刀具加工过程排屑顺畅,并且断屑均匀,但另一方面,刀具的排屑槽增大,刀体的芯径变小,从而使得刀具的刚性变差容易引起断刀。
关键词:整体硬质合金立铣刀,磨损量,耐用度,切削性能,切屑Abstract This article describes the currentdevelopment of solid carbide end mills and solid carbidecutting tools in the general level of solid carbide end millsand gold heron made a brief introduction. Behind in terms of the angle parameter of the few gold heron solid carbide head end mills several important parameters (rake angle, clearance angle, helix a first contact with the cutting material and the cutting resistance on thefirst role with the tip, easy to cause the tool to collapse the knife from the tip of the first, plus the sharp corners protection can increase the tolerance of the cutting resistance area, so as to achieve the role of protecting the tip to improve the durability of the tool.3. Tool chip removal slot increase makes the tool processing chip removal and smooth, and the chip breaking even, but on the other hand, theflutes of the tool increases, the core diameter of the cutter body smaller, so that the rigidity of the tool change The difference is easy to cause the cutting knife.Key words: Solid Carbide End MillsAmount of wear Durability Cutting Chip 目录第一章绪论 11.1 中国整体硬质合金刀具的现状和课题研究的意义 11.2 立铣刀的应用与各部分名称 21.3 立铣刀的磨损特征及主要影响因素和切削性能评价 41.4本文研究所针对的问题及研究的思路 5第二章刀具主要角度参数的切削对比实验 62.1 实验方法 62.2 切削实验条件 62.2.1 实验机床 62.2.2 实验材料 72.2.3 实验刀具 72.2.4 切削参数选择 72.3切削实验内容72.4 实验结果与分析 82.4.1螺旋角、圆周刃前角对切削性能的影响 92.4.2圆周刃后角对切削性能的影响 102.4.3尖角保护对切削性能的影响 112.5 本章小结 12第三章铝合金刀具刀型结构的切削对比实验 143.1实验内容 143.2切削实验条件 143.2.1刀具的信息及机床 143.2.2切削参数及实验材料 153.3切削实验结果163.3切削实验结果分析 17第四章刀具改进实验 194.1待改进刀具 194.2 改进方案 194.3实验方案与结果分析 204.3.1 实验机床 204.3.2切削参数及实验材料 204.3.3实验结果214.3.4实验结果分析 23第五章总结与展望 255.1论文内容总结 255.2实习工作总结及展望 25致谢 27参考文献 28 第一章绪论1.1 中国整体硬质合金刀具的现状和课题研究的意义机械制造业是全球经济繁荣最重要的支柱产业。
工具,包括刀具、模具等制约着机械制造业劳动生产力的水平和结构件的质量水平,成为整个行业关注的焦点之一。
发展制造业,就必须发展工具,特别是工具中最基础的刀具。
据有关协会的统计,世界刀具的市场总额约为110亿美元,硬质合金刀具的份额约80%世界模具市场的总量约接近700亿美元。
我国模具产值接近500亿元人民币,约占世界模具销售产值的1/12。
模具和很多结构零件加工的复杂刀具过去多用工具钢、高速钢制造。
但随着材料和制造技术的发展,高速钢刀具不仅效率只有硬质合金刀具的1/3~1/4,而且不能满足普遍推广应用的预硬化模具钢(硬度HRC27~34)等材料加工的需要。
整体硬质合金刀具就因此应运而生。
中国整体刀具行业相对落后,从刀具材料、制造工艺、使用技术方面进行比较,国内刀具行业的整体水平相对落后。
首先,尽管国内有几家大型硬质合金企业可以生产高强度、高硬度的超细合金,但难以满足汽车、航天航空和模具三大制造业对刀具高强度、高耐磨性、高稳定性的要求,在现代制造中,稳定的高效率刀具才是真正实用的刀具,价格因素已退居其后。
现在国内的刀具材料及其制做的刀具,虽然价格比进口产品低,但稳定性相对较差,不仅出口难,而且国内的使用者仍然首选进口刀具。
第二,国内整体刀具制造企业众多,分布广泛,大体分为二类。
一是国有大中型企业,二是民营小型企业。
前者虽然也装备了一些进口的高精度加工设备,但规模不大,配套不很完善,更兼机制影响,市场应变能力较差。
以模具制造业用量最大的非标刀具为例,进口刀具交货期为7~15天,而国产刀具备料霎时间就要7~10天,刀具的总交货期在30天以上,很难在市场上胜出。
民营小企业一般在几种刀具制造上有特色,但整体装备、技术比较落后,配套能力较差,形成不了规模。
二者虽各有特点,但都是在工艺技术、规模和开发能力上与国外先进企业存在较大差距。
迄今为止,国内尚无一家龙头企业能在世界强者之中占有一席重要地位。
第三,刀具使用技术的研究落后,国内对刀具切削数据的研究一直没有大的投入,对刀具切削工艺研究甚少,刀具的设计也多停留在测绘、仿制、替代进口产品的低层次上,在国内外市场竞争中处于极其被动的地位。
造成目前国内刀具现状源于国内刀具产业的各环节断裂,缺乏从材料到刀具应用的整体系统考虑,使刀具的发展落后于制造业的发展。
过去我们的刀具首先没有解决好材料问题,刀具的基体就存在先天不足;其次材料的研究和刀具的设计制造以及应用的研究严重脱节各行其是,各自为战。
刀具应用研究对基体材质的要求不够重视,材料的研究与制造没有紧扣材料的最终用途。
刀具的质量档次得不到提升。
刀具的质量提不上去对于加工效率、加工质量、加工成本以及刀具耐用度影响很大本课题主要从厦门金鹭特种合金有限公司的几种整体硬质合金立铣刀的主要角度参数、刀型结构研究其对切削性能的影响,并学习对比国际上某些知名刀具企业在某些特定刀具的设计上与金鹭公司的不同之处,同时对金鹭公司某些问题刀具学习并提出改进。
1.2 立铣刀的应用与各部分名称立铣刀是数控铣削中最常用的一种铣刀,圆柱面上的切削刃是主切削刃,端面上分布着副切削刃,主切削刃一般为螺旋齿,这样可以增加切削平稳性,提高加工精度。
由于普通立铣刀端面中心处无切削刃,所以立铣刀工作时不能作轴向进给,端面刃主要用来加工与侧面相垂直的底平面。
立铣刀的工作原理是刀具的旋转和工件的进给,将多余的金属切除。
如图1-1所示。
(a) 整体硬质合金立铣刀 (b)立铣刀的应用图1-1立铣刀的加工立铣刀广泛用于机械船舶、工业设备、医疗设备、航天航空等领域,具体应用形式主要为:1. 端面铣削:适用于较小平面范围、较小切削深度的操作要求。
加工后的零件表面相对较为“粗糙不均”。
2. 键槽加工:一般来说,生产一道高质的键槽需要至少两把铣刀。
3. 月牙键槽加工:一般来说,这个过程需要一把铣刀,用全面进给进刀法操作。
4. 特殊切削:包括锥形表面的铣削(比如:“T”形沟槽)以及鸠尾槽的加工。
5. 精细仿形切削:在有平行边壁的工件上完成内表面/ 外表面的轮廓。
6. 模具孔洞加工:大致包括在钢模凹处的俯面加工和精细加工。
凹模加工需要三维方位的处理。
球铣刀比较适合该项操作。
如下图所示。
图1-2立铣刀的应用立铣刀的各部分名称如下图1-3所示,它由刀刃部、安装在机床上的刀柄以及连接刀刃与刀柄的颈部3部分组成。
图1-3立铣刀各部分名称1.3 立铣刀的磨损特征及主要影响因素和切削性能评价刀具磨损是指刀具摩擦面上的刀具材料逐渐损失的现象。