丰田方式精益生产培训课程
精益生产(丰田管理模式TPS)培训资料
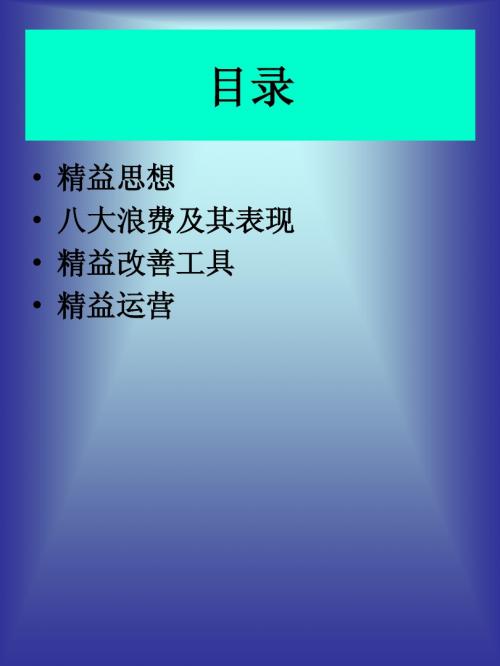
丰田生产方式的演进
全世界学习丰生 产方式
全世界学习丰生 产方式源自精益思想什么是“精益”?
• Lean Production • ——“Lean”是由瘦肉组成的肌肉(没有肥 肉)。
精益思想 --可以好似目标朝着剔除浪费(肥 肉)以承载整个系统的良性运营
精益思想
奉献顾客物美价廉产品 --价格、品质、交货期,符合变化的需求
■ 创造价值的过程 √设计满足市场 √按订单生产 √优质服务 ■没有浪费的过程
目录
• • • • 精益思想 八大浪费及其表现 精益改善工具 精益运营
精益思想
• • • • • • • • • • • • 1什么是“精益” 2精益思想 3精益思想的来源——IMVP 4精益着眼点 5精益思想的五大原则 6基于制造现场的浪费 7精益运营的八大浪费 8八大浪费的原因 9精益模式的核心(L/T) 10识别价值流及其目的 11精益生产的目标 12精益流
丰田精益生产管理培训课件

质量改进
对质量目标进行分解和制定实施措施.有质量审核计划,定期对体系、过程、产品进行内部审核确保体系运行有效性和适宜性.各类质量记录有专人收集保存、存档,对不良品、质量指标、用户抱怨、内外部故障成本等运用统计技术定期统计和分析,未达到标准有确实预防和分析纠正措施和评价
28
全员设备维护保养工作TPM
13
典型的工序看板
前工序部件1-3线出口位置POS.12-2
部件号A232-605C箱号:003箱内数量:100看板编号:2/5
使用工序总装1-3入口位置POS.12-8
14均衡Biblioteka 同步同节拍生产同步化节拍生产是按照生产工艺规定和物流顺序确定生产提前期条件下和产品总装配线保持同步地进行生产一个流的生产,前工序加工一结束即立即转到下一工序,尽量使工序间在制品接近于零一个流的生产,必须将设备的布局进行调正,不是按类型而是按工序形成相互衔接的生产线U形、T形等
17
过剩生产是最严重浪费
为什么会过剩是平衡生产和次废品需求,过剩生产说明由于人员和设备过多. 表面效率和实际效率 原来某工序生产100个,现通过努力增产到120个,表面效率得到提高,但实际祗需求或生产线工艺节拍100个,这就是浪费.实际效率没提高,所以整体效率重于个人效率
18
缩短作业切换时间
31
开展5S活动-现场管理基础
整理 停滞物的管理,是区分要与不要,不要的清除出现场.整顿 对整理后需要物品的整顿,重点是合理定置、方便使用.清扫 就是弄干净,核心是自已动手,创造一个优质、高效、安全、明快舒畅 它包含照明 的工作现场.清洁 坚持整理、整顿、清扫的结果就是清洁,它包括粉尘、噪音、有毒气体等环境要求.素养 就是行为规则,自觉执行制度、标准,不断地提高自身的修养.
丰田方式精益生产PPT教案

❖工序间几乎没有搬运距离,也没有在制品; ❖不良品一旦发生,就可立即发现(哪一台,
哪一作业者)。
第21页/共105页
安灯 制
含义:在生产机器方面,我们在机器里设 有可探测异常状况,并在探测异常时自 动停止机器运转的装置;在人员方面, 授权他们可以按下按钮或拉动绳索---称 为“安灯绳”,以使整条组装线停止作 业。
第22页/共105页
工作标准化
标准:衡量事物的准则。 标准化:
为适应科学发展和管理组织生产的 需要在产品质量,品种规格,零部件通 用等方面的技术标准 。
第23页/共105页
目视管 理定义:
是指用于工作场所,让人们一眼即可看
出应该做什么,以及是否有异于标准的情 况发生的任何沟通机制。是指所有种类的 实时信息显示设计,以确保作业与流程的 快速且正确执行。如看板,各类目视化制度 ,文件,视觉信号系统等。
第二,生产第三。核心思想是: 有消费者才有销售者,有销售 者才有生产者;
第35页/共105页
第三篇:丰田营销
第36页/共105页
丰田的汽车营销
1
2
3
低价制胜
赢在分销
绝妙促销
第37页/共105页
一、低价制胜
价格是市场最重要的信息,价格战略是企业市 场策略的重要组成部分,从丰田的销售史可以
看出,丰田的价格策略就是以低的不能再低的 价格维护市场和排挤竞争者。
1933年,丰田喜一郎设立汽车部,开始了丰田制造汽车 的历史;
1935年,设立汽车制造委员会,AA型轿车开始投产; 1937年8月27日,“丰田汽车工业株式会社”成立,世界
经济危机使其刚成立便面临倒闭,这时侵华战争成了丰 田公司发展的一个重要转折点; 1945年10月,丰田喜一郎制定“公司改进方针”,对经 营体制进行根本性的改革; 1958年,丰田汽车首次出口美国,受挫,研究福特汽车 大批量生产方式后,实施精益生产方式,开始了其快速 的成长;
丰田方式精益生产 ppt课件
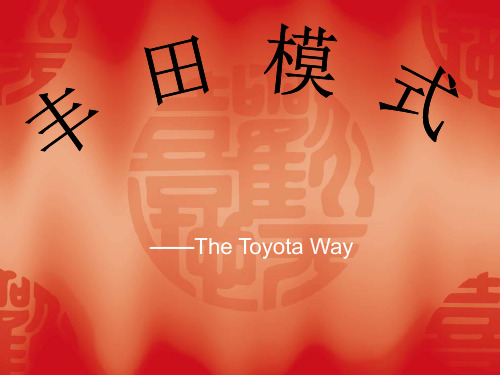
全向沟通
LT(Learning Team)活动流程图
现状调查
确定目标
分析原因
分头调研 集中汇总
总结反思
互查互纠 集中通报
各抒己见 多方论证
沟通交流 辩论趋同
安排对策
各施己长 各负其责
固化巩固
监测评估
实施对策
5W
大野耐一问:“5个为什么”的事情:
问:“机器为什么停了?” 答:“机器超负荷,保险丝断了。” 问:“为什么会超负荷?” 答:“因为轴承润滑不充分。” 问:“为什么没充分地润滑呢?” 答:“因为润滑泵供油不足。” 问:“为什么会供油不足?” 答:“因为泵轴磨损已经摇晃了。” 问:“为什么会磨损了呢?” 答:“因为没加过滤器进去了粉屑。”
丰田的企业文化
丰 田 宪 法
追求创新
丰田企业文化
愈战愈勇
关 注 人 性
一、追求创新
改进福特的
福特的“大
生产体制
规模生产模式”
不适用于日本 设计制度,
鼓励员工创新
JIT生产模 式
如今,备受瞩目的“流程再造”,本质上就是本着“精益生产模式”重塑企业组 织结构,可以说“JIT生产方式”相对于“大规模生产模式”是原创性和革命性的 创新。
了解情况
真正的问题
3.找出问题所在区 域/找出原因点
调查原因
为什么?
为什么? 为什么?
为什么? 为什么?
找出原 因点 (POC) 直接原因 原因 原因 原因 原因
根本原因
基本因果调查
4 .5个为什么? 调查根本原因
5.对 策
6.评估对策成效
7.把新流程方法标准化
四、活用“看板”
看板,是一种传递信号的载体,指各现场的 负责人将各自的作业内容写在现成的纸张等 上面,挂在工作场地,使每一个作业者都能 一目了然。
丰田精益生产方式完整培训资料(PDF 200页)
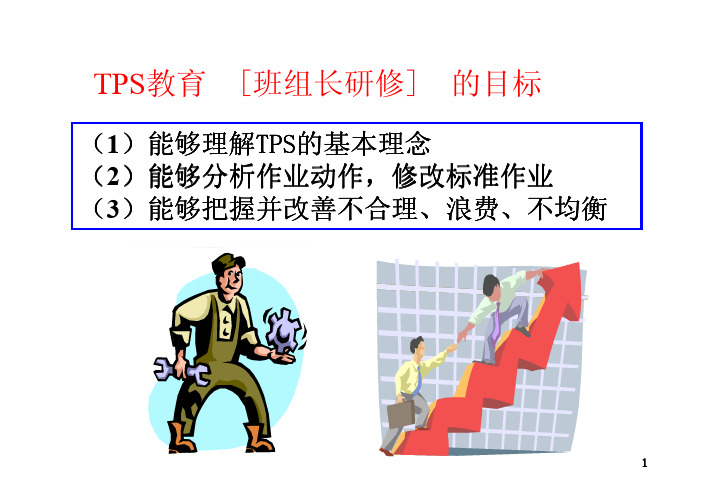
必要量: 100个/日
实际生产性
10人 120个/日 20个是过剩产品
8人 100个/日=改善
12
77.. 稼稼动动率率与与可可动动率率的的区区别别
稼动率 需求数量与班内时间的生产能力之比 →可能大于或小于100%
可动率 表示某机器能正常运转状态的百分比 →保持100%是理想状态
13
88.. 整整体体效效率率高高于于局局部部效效率率
过剩生产,库存增加, 导致问题被掩盖。应该 改善的课题就不明确
(2) 允许生产过剩就会产生新的浪费
・货架、货物箱的增加 ・搬运车、叉车的增加 ・新建仓库
产生新的浪费
成本无法降低
11
66.. 表表面面生生产产性性与与实实际际生生产产性性的的区区别别
表面生产性
10人 100个/日 10人 120个/日
17
『工程的流程化』 模拟游戏 ①
①理解制造方法改变成本的事实 ②体验流程化、逐个生产制造方法
18
Ⅱ.丰田生产方式的源流(Video)
19
Ⅲ. 丰田生产方式
如何将“顾客第一” 具体化
2大支柱
J.I.T
适时地
适时地、低成本地 生产高品质产品
资金短缺时 如何快速回收
彻底消除 “不合理、浪费、不均衡”
赛艇
14
轴承工厂的例子
超大型轴承
B Dd
内轮 1个 50万日元
内轮加工生产线
外轮加工生产线
15
99.. 提提高高劳劳动动生生产产性性与与强强化化劳劳动动的的区区别别
提高劳动生产性 将“動”转化为“働”
浪费 動 働
强化劳动
不改善而加强劳动强度
浪费
動 働
NPS丰田生产实务培训
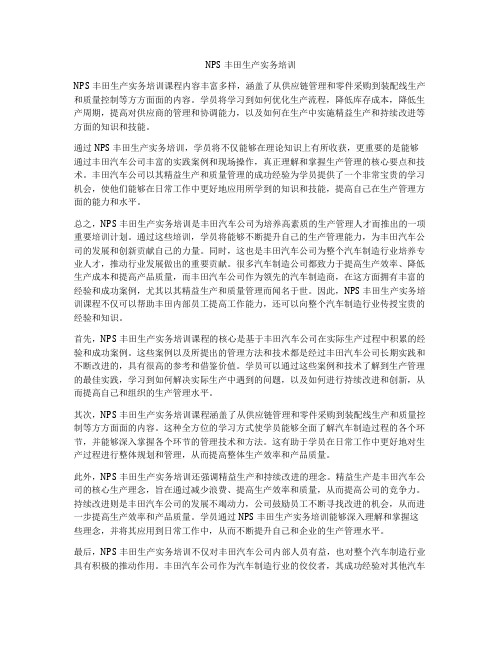
NPS丰田生产实务培训NPS丰田生产实务培训课程内容丰富多样,涵盖了从供应链管理和零件采购到装配线生产和质量控制等方方面面的内容。
学员将学习到如何优化生产流程,降低库存成本,降低生产周期,提高对供应商的管理和协调能力,以及如何在生产中实施精益生产和持续改进等方面的知识和技能。
通过NPS丰田生产实务培训,学员将不仅能够在理论知识上有所收获,更重要的是能够通过丰田汽车公司丰富的实践案例和现场操作,真正理解和掌握生产管理的核心要点和技术。
丰田汽车公司以其精益生产和质量管理的成功经验为学员提供了一个非常宝贵的学习机会,使他们能够在日常工作中更好地应用所学到的知识和技能,提高自己在生产管理方面的能力和水平。
总之,NPS丰田生产实务培训是丰田汽车公司为培养高素质的生产管理人才而推出的一项重要培训计划。
通过这些培训,学员将能够不断提升自己的生产管理能力,为丰田汽车公司的发展和创新贡献自己的力量。
同时,这也是丰田汽车公司为整个汽车制造行业培养专业人才,推动行业发展做出的重要贡献。
很多汽车制造公司都致力于提高生产效率、降低生产成本和提高产品质量,而丰田汽车公司作为领先的汽车制造商,在这方面拥有丰富的经验和成功案例,尤其以其精益生产和质量管理而闻名于世。
因此,NPS丰田生产实务培训课程不仅可以帮助丰田内部员工提高工作能力,还可以向整个汽车制造行业传授宝贵的经验和知识。
首先,NPS丰田生产实务培训课程的核心是基于丰田汽车公司在实际生产过程中积累的经验和成功案例。
这些案例以及所提出的管理方法和技术都是经过丰田汽车公司长期实践和不断改进的,具有很高的参考和借鉴价值。
学员可以通过这些案例和技术了解到生产管理的最佳实践,学习到如何解决实际生产中遇到的问题,以及如何进行持续改进和创新,从而提高自己和组织的生产管理水平。
其次,NPS丰田生产实务培训课程涵盖了从供应链管理和零件采购到装配线生产和质量控制等方方面面的内容。
这种全方位的学习方式使学员能够全面了解汽车制造过程的各个环节,并能够深入掌握各个环节的管理技术和方法。
丰田精益生产内部培训资料
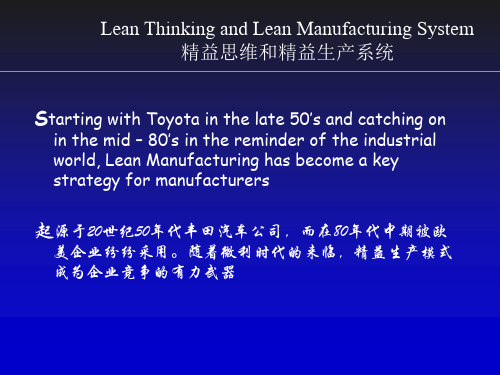
Synchronous 同步生产 • Focused on total elimination of waste • Ongoing efforts to improve Quality, Productivity, and Responsiveness • Attention to detail • Recognition of employee abilities • 消除浪费 • 不断改进 • 员工参与
What is Lean Manufacturing 什么是精益生产-五个原则
Value 价值
Perfect 完美
站在客户 的立场上
Value Stream 价值流
没有任何事物 是完美的 不断改进
Lean Manufacturing 精益生产
从接单到发货 过程的一切活动
Demand Pull 需求拉动
-精益思维, Womack & Jones
Best Plant?最好工厂?
按时交货 - 98% 交付周期时间 - 10 天 缩短交付周期时间 (5年) - 56% 缩短生产周期时间 (5年) - 60% 生产周期时间 - 3 天 执行比率 - 3/10 = .30 库存周转 - 12.0 库存减少 (5年) - 35% 在制品周转 - 80 使用精益生产的工厂 - 96%
Lean 精益生产
组织
Agile 敏捷生产
组织
• 低产量 • 个性化
• Builds on • Remove constraints to synchronous respond to customer manufacturing demand through the • Emphasize on lead entire supply pipeline time reduction (supplier-customer) • Improve asset • Capable plants linked to utilization lean concepts • Built to customer demand • 改善整个价值链 • 节点上连着精益工厂 • 在同步生产的基 础上,强调缩短 生产周期 • 提高资源利用率 • 需求驱动
精益生产系列培训--丰田八步法A3报告

实现彻底的沟通
⑨ WHO——所有的客户或相关人员(不能有遗漏) HOWMUCH——想尽一切办法使对方理解、达成共识。
全员参与
问题、方法、信息、成果等都属于全员的,个人体现不同的贡献和价值。
⑩ 每个人都可以参与任何事;每件事都需要全员参与 集思广益,以达到效果和效率的最大化。 工作分工仅是赋予个人的使命不同
▼ 如果在把握了「 要着手解决的问题点」 后设定「 目标」 , 那么之后的「要因分析」 的步骤中寻找到的「真因」 是否是真正的「 根本原因」 ,就可以根据 「如果消除了这个根本原因、 是否可以达成这个目标」 来进行检查了。 ____无法判定
不能根据要因设定目标__为什么? 应根据问题点设定目标
STEP3.设定目标
■问题解决的「 出发点」
必须强烈地意识到这是——问题解决的第一步
■关键在于“ 具体化” ( 5W2H)
总结
一般情况下 技术问题比 较直观, 管理问题比 较模糊
STEP2.分解问题
STEP2.分解问题
1.将大而模糊的问题逐步分解,整理成自己能够着手处理的具体的问题。 2.决定问题解决的优先顺序、 并现地现物地观察产生问题的具体环节, 收集定量·定性的事实,确定问题点
①寻找要因分析的切入点
为进行要因分析・・・对事情「 考虑构成要素」 有代表性的切入点
资源问题 ⇒ 人、 物品、 资金、 信息 产品问题(QCD) ⇒Quality质量、 Cost成本、 Delivery交货期 生产现场(4M) ⇒Man:人、 Machine: 设备、 Material: 材料、 Method: 方法 人的能力⇒思想・技术・体能 销售问题( 4P) ⇒商品、 价格、 销售渠道、 促销政策
・针对「 培训的效果不好」 的问题; 可以设定「 内容的理解度」、「 期待值的达成度」 等指标、 向听课人进行问卷调查。 对「 内容的理解度」 ,还可以通过测试的形式,用测试得分来 进行评价。
丰田精益生产内部培训资料演示课件(ppt100张)
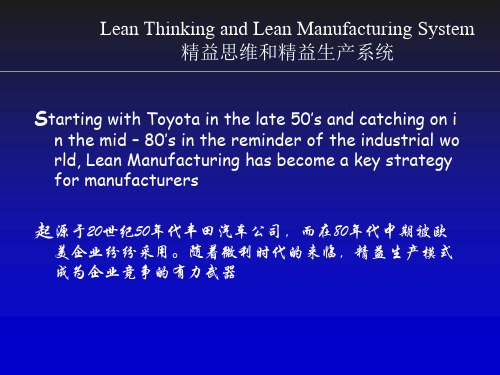
灵巧的双手
全自动
Life Cycle Cost In Different System 不同系统中的成本
大规模生产模式下的 产品生命周期成本
精益生产系统之产品 生命周期成本
$/ piece $/piece
销售价格
销售价格
V 产量
V
产量
Manufacturing Evolution 制造系统演化史
• Ongoing efforts to improve Quality, P roductivity, and Re sponsiveness
• Attention to detail • Recognition of em
ployee abilities
• 消除浪费 • 不断改进 • 员工参与
精益 / 同步型
在价格,成本和利润的关系中,有两种不同的思考方法:
1。传统的方法 销售价格 = 成本 + 利润
2。新的方法 利润 =销售价格 – 成本
The Cost / Lean Relationship 精益生产与成本的关系
直接员工
产品生命周期成本
C
o
质 间接员工
s
量
LEAN
t 精益的通俗定义
投资 间接质员量工
Henry Ford • Assembly line mass production • Produce in high volume with low variety • Single skill
福特首创的装配线是大规模低品种生产方式的代表, 工人被当成工作的机器
Toyota Production System (TPS) • Just-In-Time Production (produce only what is needed) • Pull System • Produce enough volume to meet customers needs • High variety to meet customers wants
精益生产经典课程1--防错法
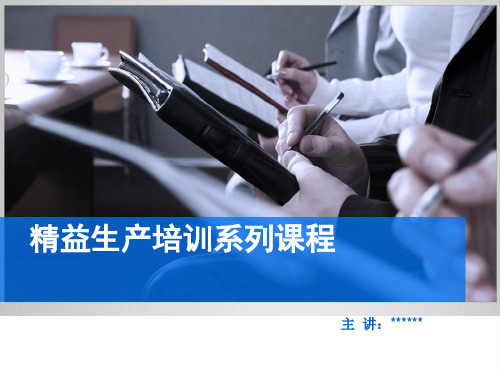
21
防错法(Poka-Yoke)
产生失误的其他原因:
➢ 误导产生的错觉 ➢ 过分关注产生的幻觉 ➢ 观察的细致程度 ➢ 观察的不同角度 ➢ 悖论 ➢ 惯性思维 ➢ 盲点
丰田生产模式TPS学习
14
防错法(Poka-Yoke)
防错法的作用: 图示:
作业失误
丰田生产模式TPS学习
防错法
品质缺陷 比例很大
库存、返工、 报废
成本增加
一次就做好 品质水平提高
没有返工
不需要检查
消除浪费
作业效率提高
降低成本 增加利润
15
防错法(Poka-Yoke)
丰田生产模式TPS学习
认识失误与缺陷:
失误是由于作业者疏忽等原因造成的。 而缺陷是失误所产生的结果,比如由于作业者疏漏而产生的 结果,如,由于作业者疏漏而产生装螺丝作业失误,而导致汽 车轮胎漏装一颗螺丝的缺陷。 缺陷与失误举例如下表:
在最后一段流水线增加了一个称重装置,并能自动将重 量超出设定公差的包装盒剥离流水线,经过一段时间的监视 使用,最后成功关闭了该问题,并做了Success story在整个 集团中分享。
9
防错法(Poka-Yoke)
丰田生产模式TPS学习
防错法的精髓:
同时另一个做肥皂的乡镇企业也发生了同样的问题,空 包装盒流入包装箱,私人老板立马命令生产线班长解决此问 题。
12
防错法(Poka-Yoke)
丰田生产模式TPS学习
防错法的定义:
狭义:如何设计一个东西,使错误绝不会发生。 广义:如何设计一个东西,而使错误发生的机会减至最低的 程度。 因此,更具体的说“防错法”是: 1.具有即使有人为疏忽也不会发生错误的构造──不需要注 意力。 2.具有外行人来做也不会错的构造──不需要经验与直觉。 3.具有不管是谁或在何时工作都不会出差错的构造──不需 要专门知识与高度的技能。