铁路货车车辆用耐候钢的开发
铁路货车用Q450NQR1钢的研制开发

铁 路货车用 Q4 5 0 N QR 1 钢 的研 制开发
乔 松
( 山钢股份济南分公司 宽厚板厂 , 山东 济南 2 5 0 1 0 1 )
摘
要: 采用 合理 的成 分设计 , 通过 钢质纯 净化 、 铌 钛微合金 化和控 轧控冷工 艺 , 济钢开 发生产 了铁路货 车用 Q 4 5 0 N Q R 1
钢 。实物质量 检验表 明, 钢带组织均 匀、 晶粒细小 , 力学性 能 、 耐大气腐蚀性能 、 焊接性能均达 到标准要求 , 现已成功供货铁
路货车制造厂 家。
关键词 : 铁路货 车用钢 ; Q 4 5 0 N Q R 1 ; 微合金化 ; 耐大气腐蚀性能 ; 焊接性 能
中图分类号 : T G 1 4 2 . 4 1 文献标识码 : B 文章编 号: 1 0 0 4 ~ 4 6 2 0 ( 2 0 1 3 ) 0 3 — 0 0 3 1 — 0 2
强化作用 , 实现强度 、 韧性 、 耐疲劳性能等综合性能
的提 高 。焊 接性 能方 面 , 主要从 元 素控 制上 保持 低 的碳 当量和 高的纯净度 。 在 充 分考 虑上 述 因素 的前 提下 , 还 需要 考虑 生
产成 本 。Q 4 5 0 N Q R 1 钢 所 需 的合 金成 本 较 高 , 在 保
加 热
开轧 终轧 卷取
≤0 . 1 2 ≤0 . 7 5 ≤1 . 5 0≤0 . 0 1 5≤0 . 0 1 0 0 . 2 0—0 . 5 0 0 . 3 0~1 . O 0 0 . 1 2~0 . 6 5 适量
≥1 2 0 0 ≥1 0 3 0 ≥8 5 0 6 0 0~6 4 0
步发 展 ; 通过 L F 和R H精 炼提 高钢质 纯净度 , 减
鞍钢铁路货车车体用钢研发历程

鞍钢技术2018 年第 4 期 A N G A N G TEC H N O LO G Y总第 412 期鞍钢铁路货车车体用钢研发历程郭晓宏\刘志伟\张瑞琦\邢津铭2袁金泽宏3袁孙傲1(1.鞍钢集团钢铁研究院,辽宁鞍山114009; 2.鞍钢股份有限公司产品制造部,辽宁鞍山114021曰3.鞍钢股份有限公司市场营销中心,辽宁鞍山114021)摘要:介绍了铁路货车车体用钢在国内外的研究及应用状况,概述了其腐蚀机理及影响 因素,对比分析了耐候钢、不锈钢及铭合金车体材料应用的技术性和经济性,提出了新型耐蚀 钢的设计理念,展望了新型耐蚀钢研究应用方向,详细介绍了鞍钢S450AW关键应用技术研究及效果。
关键词:铁路货车;耐候钢;新型耐蚀钢中图分类号:TG14 文献标识码:A文章编号院1006-4613(2018)04-0009-06Development History of Steel for Freight Train Carriage Body in Ansteel Guo Xiaohong1,Liu Zhiwei1,Zhang Ruiqi1,Xing Jinming2,Jin Zchong3,Sun Ao1(1.Iron&Steel Research Institutes of Ansteel Group Corporation,Anshan 114009, Liaoning,China;2.Product Manufacturing Department of Angang Steel Co.,Ltd.,Anshan 114021, Liaoning,China;3.Marketing Center of Angang Steel Co.,Ltd.,Anshan 114021, Liaoning,China;)Abstract:The development and applications of the steel for freight train carriage body at home and abroad was introduced.The corrosion mechanism and influencing factors were summarized.The design concept on the new corrosion-resistant steel was proposed based on the contrastive analysis over the technical characters and economical efficiency on the applications of these materials for making the carriage body such as weather-resistant steel,stainless steel and aluminum alloy.Meanwhile the development trend and application direction of the new corrosion- resistant steel were prospected.And finally the developments of key applied technologies on S450AW and application results in Ansteel were introduced in detail.Key words:railway freight car;weather-resistant steel;new corrosion-resistant steel根据2017年铁路统计公报,全国铁路货车拥 有量为79.9万辆,机车拥有量为2.1万台,铁路客车 拥有量为7.3万辆,动车组2 935组、23 480辆[1]。
铁道车辆用高强度耐大气腐蚀钢的进展.

铁道车辆用高强度耐大气腐化钢的进展为加快铁路现代化建设和全面建设小康社会的总的要求,同时为适应客货运市场的强烈竞争,知足铁路货运快捷、重载、安全、靠谱、优良、环保的要求,跟着公民经济的发展和技术进步,铁路车辆不论是品种、品位、仍是质量都将会有一个较大的提升。
铁道工业发展的战略要点是加速与重载,要求铁道车辆特别是货车减少车辆自重。
减少车辆自重的门路除了合理的设计参数选择,优化的构造设计,最重要的是钢材的品种、性能和质量。
因为我国地区为加快铁路现代化建设和全面建设小康社会的总的要求,同时为适应客货运市场的强烈竞争,知足铁路货运快捷、重载、安全、靠谱、优良、环保的要求,跟着公民经济的发展和技术进步,铁路车辆不论是品种、品位、仍是质量都将会有一个较大的提升。
铁道工业发展的战略要点是加速与重载,要求铁道车辆特别是货车减少车辆自重。
减少车辆自重的门路除了合理的设计参数选择,优化的构造设计,最重要的是钢材的品种、性能和质量。
因为我国地区广阔,天气条件有较大差别,对资料的腐化问题也应予以足够重视。
因腐化造成报废的金属资料设施相当于金属年产量的 20- 40%,全球因腐化无效的年消耗金属超出一亿吨,由此带来的经济损失占 1-3.5 %GNP。
因为腐化的原由使我国 10- 20%的钢铁构造成为荒弃物。
所以需要从选择合理的设计参数、优化构造设计和提升铁路用钢(板材和型材)的使用性能(品种规格、力学性能、耐蚀性能)几方面结合攻关。
1铁路车辆的现状和新局势下的要求1.1铁路车辆的现状长久以来,我国铁道车辆的技术标准向来源于苏联五、六十年月标准。
铁道车辆的技术进步,必定程度上依靠于我国钢材的品种、性能与质量。
在上世纪 80 年月从前,钢构造基本上采纳普碳钢、 09Mn2等,耐大气腐化钢则向来以折服强度为295MPa 的 09CuPTi Re 和折服强度为 345MPa的 09CuPCrNi为主,而美国等一些国家耐候钢的强度水平已高达 550MPa。
耐候钢及其表面处理技术的开发

— 18 —
镍 、钼 、铝 、钒 、钛等元素也有一定的效果 。
2 耐候钢的耐蚀性
研究表明 [ 2 ] ,在不同地区随着时间的变化 , 碳钢和低合金钢腐蚀速度有很大差异 。它们的耐 蚀性与腐蚀产物的组成及结构密切相关 。与普通 碳钢相比 ,低合金耐候钢具有较好的抗大气腐蚀 性能 ,这主要是由于在碳钢中加入的少量铜 、磷 、 镍 、铬等合金元素所致 。在大气腐蚀条件下 ,钢的 腐蚀主要属于电化学腐蚀 ,腐蚀的第一步是在钢 的表面形成水膜 。如果不考虑空气中二氧化硫和 盐粒子的影响 ,钢的大气腐蚀则主要以水膜下腐 蚀为主 。在腐蚀起始阶段 ,气态的氧首先溶入水
耐候钢的 锈 层 稳 定 化 过 程 与 钢 材 的 化 学 成 分 、使用环境和构造等条件有关 ,若使用不当 ,破 坏了稳定锈层的生成条件 ,耐候钢就会严重锈蚀 。 实践证明 ,海滨地带 、含盐地区及特别潮湿的地区 都不宜使用裸露耐候钢 。因为这些地区大气中腐 蚀性介质浓度过高 ,耐候钢表面的稳定锈层很难 形成 。另外 ,在北方地区的冬季 ,为防止汽车打 滑 ,在道路上使用大量的盐 ,也会影响耐候钢稳定 锈层的生成 。裸露的耐大气腐蚀用钢在使用初期 与普通碳素钢一样会产生红锈 ,污染周围混凝土 结构 。 3. 2 涂装使用
鞍钢技术
2007年第
3期
AN
GAN
G
TECHNOLO G Y 总第
345期
中 , O2 / H2 O 的标准电极电位为 1. 23V ,和铁构成 原电池 ,产生钢的电化学腐蚀 。
钢表面生成的锈层会使其体积产生变化 ,在 锈层和基体的界面生成应力 ,此应力随腐蚀速度 的增加而增大 。铁锈本身变形能力较差 ,在腐蚀 初期生成的锈层中容易产生裂纹 ,一些可与基体 生成无限固溶体的合金元素 (如铜 、铬等 )在大气 腐蚀产物中的溶解度比铁锈小 ,所以易于在锈层 的裂纹和孔洞处析出 ,降低表面能 ,富集在锈层 中 ,而非均匀分布 。铬对改善钢的钝化能力有显 著效果 ;另外在锈层的形成过程中 ,铬部分取代了 α - FeOOH中铁的位置 ,形成了二元合金元素的 羟基氧化物 α - ( Fe1 - x C rx ) OOH[ 3 ] 。这种锈层 稳定性好且组织细小致密 ,除了可以有效地隔离 腐蚀介质与钢基体的接触 ,阻止水和酸根的侵入 外 ,同时因为其具有极高的阻抗 ,极大地减缓了腐 蚀阳极区和阴极区之间的电子迁移 ,从而降低了 电化学反应的速度 ,抑制了内部钢材的腐蚀 。而 普通碳钢表面就不具备这样稳定的保护性锈层 。
鞍钢新型铁路货车用耐候钢受青睐

铁路用耐候钢“独领风骚”的局面被打破。
如何打破技术壁垒,实现产品赶超?鞍钢将 S450EW 在焊接和冷加工成形方面的弊端作为研 发突破口。鞍钢股份耐蚀钢 EVI 研发凭借已有的 技术积累和经验,以全新成分设计体系思路推进
0c07f2c
新产品研发,于 2013 年初成功研发出 S450AW 铁 路车辆用新型耐蚀钢,该钢种具有优异耐腐蚀性 能Байду номын сангаас同时兼顾高强度、高韧性、优异冷成形性能 及焊接性能,自此鞍钢拥有了抢占耐候钢市场的 一枚重要棋子。
0c07f2c
炼和钢坯轧制难度大等困难,于今年 5 月份圆满 完成全部订单任务,得到了铁路车辆厂的好评, 提升了鞍钢耐蚀钢的品牌形象。
作为铁路货车用耐候钢的升级换代产品,鞍 钢新型耐蚀钢 S450AW 凭借着优良的性能和优势, 成功中标中国铁路总 C80E 车型用钢 3.5 万吨, 占全部订单的 70%。6 月 11 日,鞍钢在回访用户 时了解到,这批钢板已顺利应用于3500多台C80E 车型上,各项性能指标良好。
由于受环境气候等因素的影响,铁路货车车 体用钢容易被腐蚀,这会影响车体的运输安全和 维护。上世纪八十年代末,鞍钢在国内率先研制 出第一代耐候钢。然而在第二代和第三代耐候钢 研制生产过程中,国内钢企自主开发出耐候钢 Q450NQR1 和新型高耐蚀性耐候钢 S450EW,鞍钢
新产品研制成功后,市场推介至关重要。鞍 钢领导和耐蚀钢 EVI 多次到铁路总及相关单位进 行推介。去年 3 月份,铁路总同意将 S450AW 在 成形性要求最苛刻的车门上进行试验,试验结果 显示性能指标完全符合要求,并且成形性富裕度 很大,得到了铁路总认可。去年 5 月份,鞍钢新
0c07f2c
型耐蚀钢 S450AW 成功出口莫桑比克,经应用后, 车辆使用寿命大大提高,受到了用户的肯定和信 赖。经过市场的严格考验,鞍钢新型耐蚀钢 S450AW 在行业内的领先优势得到凸显,并且推动 了国内新型耐蚀钢的升级换代。
耐候钢的发展及开发中的关键技术浅析
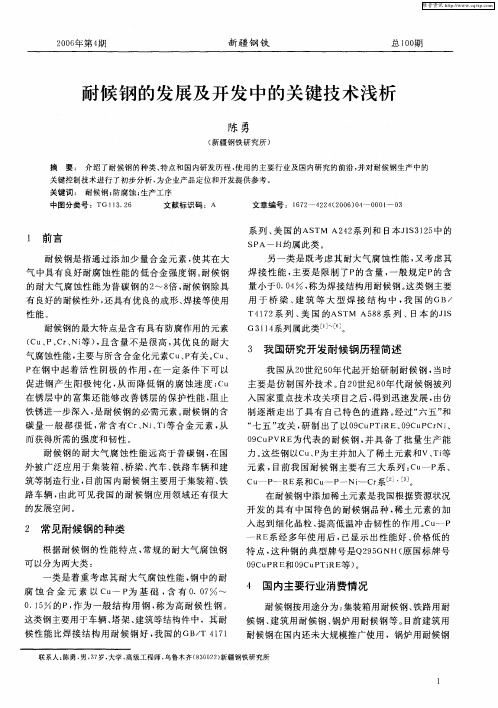
特 点 , 种 钢 的典 型牌 号是 Q 9 GNH( 国标 牌 号 这 25 原
类是 着 重 考虑 其 耐 大 气腐 蚀性 能 , 中 的耐 钢
腐 蚀 合 金 元 素 以 c ~ P 基 础 , 有 0 0 ~ u 为 含 .7
4 国内主要行业消 费情况
耐 候钢 按用途 分为 : 集装 箱用 耐候 钢 、 路用 耐 铁 候钢 、 建筑 用 耐候 钢 、 炉用 耐候 钢 等 。 锅 目前 建 筑 用
联 系人 : 陈勇 、 3 岁 , 男,7 大学 , 高级工程师, 乌鲁木齐( 3 0 2新疆钢铁研究所 802)
维普资讯
2 0 年第 4 06 期
新疆 钢 铁
总 10 期 0
市场 有 限 , 主要 介 绍集装 箱 和铁 路 用 耐候 钢在 国内
主 要是 仿 制 国外 技 术 。 0 纪 8年 代 耐候 钢 被列 自2 世 0 入 国家重 点技 术攻关 项 目之后 , 得到 迅速 发展 , 由仿 制逐 渐 走 出了具 有 自 己特 色 的道路 。 过 “ 五 ” 经 六 和 “ 五 ” 关 , 制 出了 以0C P i 、9 u C NJ 七 攻 研 9 u TRE 0C P r 、
气腐蚀性 能 , 主要 与所 含合 金化 元素 C 、 有关 。 u uP c 、
3 我 国研 究开发耐候钢历程简述
我 国从2 世 纪6 年 代起 开始 研 制 耐候 钢 , 0 0 当时
P 钢 中起 着 活 性 阴 极 的 作 用 , 一 定条 件 下 可 以 在 在 促 进 钢产 生 阳极 钝 化 , 而 降 低 钢 的腐 蚀 速度 ; u 从 C
的发 展空 间 。
元素 , 目前我 国耐 候 钢 主要 有 三 大 系列 : u P 、 c— 系
宝钢高强度铁路车辆用耐候钢的试制及生产实绩
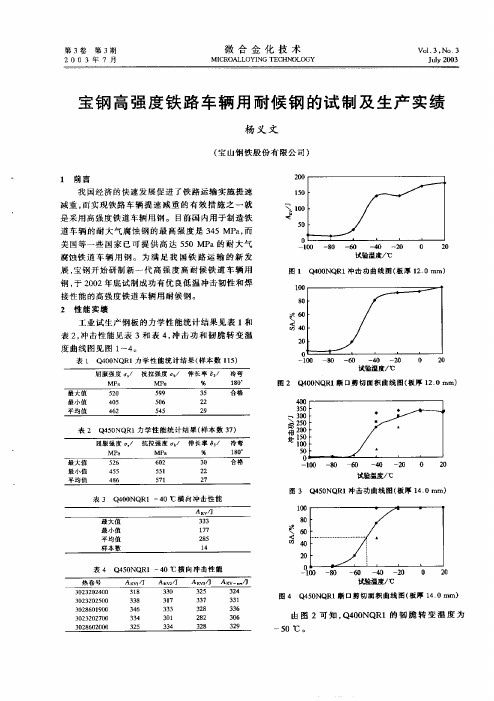
第 3卷
由图 4可知, 40 R Q 5\ 1的韧脆转变温度 为 Q
一5 0℃ 。
80 60 40 20
3 焊接性
用斜 Y坡 口裂纹试验方法和搭接接头( T ) CS 焊接裂纹试验方法评定钢材对焊接冷裂纹的敏感程 度。试验结果表明: 0℃下无论是进行手弧焊还是 气保焊, 宝钢高强度铁道车辆用耐候钢不会产生焊 接冷裂纹, 表现出良好的焊接性。 4 耐腐蚀性能 用室 内加速腐蚀试验方法评价钢的耐腐蚀性 能, 试验结果表明: 宝钢高强度铁路车辆用耐候钢确 实具有优良的耐腐蚀性能, 与普通钢相比, 时间越长, 优势越朋显。室内加速腐蚀试验结果见图5-0 -9
() 1 采用适当的成分和加工工艺可以获得具有 高的强度和韧性以及优 良焊接性能和耐腐蚀性能的 铁道车辆用钢。 () 2 钢板具有高的冲击韧性, 满足铁路车辆服 役的安全性要求。 () 3 钢板具有较高的伸长率, 表现出良好的成 形性能, 满足车辆制造的使用要求。
( 上接第 8页)
表 1 4O Q 1 0 N R 力学性能统计结果( Q 样本数 15 1)
屈服强度 么/ 抗拉强度 。 创
M Pa M Pa
-0 1 0
阅
8 0 -6 0
-4 0 -2 0
0
2 0
伸长率 6/ s
% 一35 2 朋 f\ 俘
试验沮度/ ℃
试脸沮度/ ℃
图 4 4O Q 1 Q 5N R 断口剪切面积曲线图( 板厚 1 . . 40. )
3 2 22 0 03070
3 2 62 0 08000
由图 2可知, 4O Q I的韧脆 转变温度为 Q 0N R
一5 ℃ 。 0
微
合
金
铁路货车用S450EW高耐蚀型耐候钢工艺性能分析

Pr 0 c e s s a bi l i t y a na l y s i s o f S 4 5 0 EW hi g hl y we a t he r— r e s i s t a nt
s t e e l f o r r a i l f r e i g h t c a r s
要是 贝 氏体 、 铁素 体和 珠光体 。
蚀性 能 比 Q 4 5 0 N Q R 1提 高 约 3 0 % ~5 0 % 的 新 型
S 4 5 0 E W 高 耐蚀 型耐 候 钢 。本 文 通过 对 S 4 5 0 E W 钢
根据 运 装 货 车 [ 2 0 1 0 ] 8 4 1号文 技 术 要 求 , 焊 接 材料 选用 牌号 为 T H 6 5 0 E W —H配 套气体 保 护焊 丝 , 直径 为 1 . 2 m m, 其熔覆金属化学成分、 力 学 性 能 分
宝钢高强度铁路车辆用耐候钢的试制及生产实绩

宝钢高强度铁路车辆用耐候钢的试制及生产实绩杨义文宝山钢铁股份有限公司1 前言我国经济的快速发展促进了铁路运输实施提速减重而实现铁路车辆提速减重的有效措施之一就是采用高强度铁道车辆用钢目前国内用于制造铁道车辆的耐大气腐蚀钢的最高强度是345MPa而美国等一些国家已可提供高达550MPa 的耐大气腐蚀铁道车辆用钢为满足我国铁路运输的新发展宝钢开始研制新一代高强度高耐候铁道车辆用钢于2002年底试制成功有优良低温冲击韧性和焊接性能的高强度铁道车辆用耐候钢2 性能实绩工业试生产钢板的力学性能统计结果见表1和表2冲击性能见表3和表4冲击功和韧脆转变温度曲线图见图1图4表1 Q400NQR1力学性能统计结果样本数115屈服强度sMPa 抗拉强度bMPa延伸率5%冷弯180最大值520 599 35最小值405 506 22平均值462 545 29合格表2 Q450NQR1力学性能统计结果样本数37屈服强度sMPa 抗拉强度bMPa延伸率5%冷弯180最大值526 602 30最小值455 551 22平均值486 571 27合格表3 Q400NQR1 -40横向冲击性能冲击试样尺寸mm 101055Akv J最大值333最小值177平均值285样本数14表4 Q450NQR1 -40横向冲击性能冲击试样尺寸mm101055试验温度,图1 Q400NQR1冲击功曲线图板厚12.0mm试验温度,图2 Q400NQR1断口剪切面积曲线图板厚12.0mm由图2可知Q400NQR1的韧脆转变温度为-50试验温度功图3 Q450NQR1冲击功曲线图板厚14.0mm试验温度图 4 Q450NQR1断口剪切面积曲线图板厚14.0mm由图4可知Q450NQR1的韧脆转变温度为-503 焊接性用斜Y 坡口裂纹试验方法和搭接接头CTS焊接裂纹试验方法评定钢材对焊接冷裂纹的敏感程度试验结果表明0下无论是进行手弧焊还是气保焊宝钢高强度铁道车辆用耐候钢不会产生焊接冷裂纹表现出良好的焊接性4 耐腐蚀性能用室内加速腐蚀试验方法评价钢的耐腐蚀性能试验结果表明宝钢高强度铁路车辆用耐候钢确实具有优良的耐腐蚀性能与普通钢相比时间越长优势越明显室内加速腐蚀试验结果见图5图9率图5 240小时湿热试验率图6 480小时湿热试验率图7 96小时盐雾试验率图8 480小时盐雾试验率图9 480小时加速老化试验5 结论宝钢高强度铁道车辆用耐候钢的研制结果表明1采用适当的成份和加工工艺可以获得具有高的强度和韧性以及优良焊接性能和耐腐蚀性能的铁道车辆用钢2钢板具有高的冲击韧性满足铁路车辆服役的安全性要求3钢板具有较高的延伸率表现出良好的成形性能满足车辆制造的使用要求。
含Nb高耐候钢的开发和生产

1 . 成 分设 计
试样表面
l
l l i L ≯
J
擗 叫
辩 辩 : c 暖 羹 《 惭)
鐾 蜷{ ‰}
增强的依次顺序是:N b N、T i C 、N b C 、T i N。 为 了降低钢 中 固溶氨含 量 ,加人微 量钛 .使 钢 中的氮被钛固定 ,从 而 间接提 高 了铌 的强 化作用 。由于加入微合金元素 Nb阻止了晶粒
由于考虑 到该钢种含有 铜, 因此制定加 热 工 艺 时 ,考 虑 避 开铜 的熔 点 1 0 8 3 ℃ 附近 的 裂纹敏感 区,采取高温 快烧 ,均热 段炉温控 制在 1 2 0 0 " C的 加热 炉 ,并 保 温 3 0 mi n 。采 取 在 结 晶 区 和 未 再 结 晶 区 两 阶 段 控 轧 ,终 轧 温 度8 5 0 ℃ ,冷却速度约控制在 2 5 ℃/ s ,终冷温
工 业 技 术
含N b高耐候钢的开发和生产
仇 必宁
南京钢铁联合公司带钢厂 江苏 南京 2 1 0 0 0 0
摘 要:耐候钢主要用于铁道 、车辆、桥梁 、塔架等长期暴露在大气 中使 用的钢 结构 。用于制造集装箱 、铁道车辆、石油井架 、海港建筑 、采油平 台 及化工石油设备 中含硫化氢腐蚀介质的容器等结构件。本文探讨 了含 N b高耐候 钢的开发和 生产 中的成分设计 ,对试生产结果进 行 了分析与评 价。 关键词 :含 N b 高耐候钢 试 生产结果 分析 铌 、钛一般作为 HS L A 的微合金化元素 而 加 入 到 钢 中 , 通 过 晶 粒 细化 和 沉 淀 强 化 影 响钢 的组织与 性能。为有 效发挥铌对抑 制奥 氏体 再结晶 的作用 ,应尽 可能采用低 的碳、 氮含量 , 对耐大气腐蚀钢进行 N b 微合金化后 在较 宽 的温 度 范 围 内可 获得 铁索 体 超 细组 织 。钛可产 生强烈 的沉 淀强化及 中等程度 的 晶粒细化作用 , T i N 可有效阻止奥氏体 晶粒在 加热 过程中的长 大,起到细化 奥氏体 晶粒 的 作用 。 光后 ,用 4 %的硝酸 酒精溶 液浸蚀 ,观察其组 织f 图
铁路货车车体用钢的现状及研究发展趋势

铁路货车车体用钢的现状及研究发展趋势发表时间:2020-08-27T16:57:57.670Z 来源:《基层建设》2020年第9期作者:肖宪锐朱延章[导读] 摘要:对铁路货车种类、使用环境及性能需求进行了概述;总结了国外铁路货车车体用钢发展现状以及国内钢铁企业对铁路货车车体用钢的研究历程,提出了铁路货车车体用钢的主要性能需求,指出了新一代铁路货车车体用钢制造技术的发展趋势。
中车哈尔滨车辆有限公司黑龙江哈尔滨 150056摘要:对铁路货车种类、使用环境及性能需求进行了概述;总结了国外铁路货车车体用钢发展现状以及国内钢铁企业对铁路货车车体用钢的研究历程,提出了铁路货车车体用钢的主要性能需求,指出了新一代铁路货车车体用钢制造技术的发展趋势。
关键词:铁路货车;车体用钢;耐候钢;高强钢 1铁路货车车体用钢的主要性能需求 1.1高耐蚀性能目前国内铁路货车车体用钢的主要采用的钢铁材料为Q450NQR1,但是在实际使用过程中,Q450NQR1还存在诸如耐蚀性差、实际使用寿命低于25年设计寿命的问题,虽然Q450NQR1的耐蚀性能可达到一般的碳素钢的三倍左右,但铁路货车服役过程中会受到大气环境腐蚀和动载荷磨蚀综合影响,Q450NQR1在正常大气环境下的耐腐蚀性能难以满足苛刻运输环境。
我国主要的耐候钢种主要模仿发达国家的技术思路,提高耐腐蚀的思路是采用合金添加的方法而不是采用耐腐蚀相来提高耐候的基体的耐蚀性能,所以需要开发耐腐蚀性能更好的耐候钢,莱钢开发了基于铜磷为主要耐候元素的耐候钢。
国外有些国家在铁道车辆用使用不锈钢代替耐候钢,但是存在制造成本较高应用性较差等问题,合理的思路是采用少量或廉价的合金元素,在不大幅提高成本的基础上获得高耐蚀性是一种比较切实可行的方案。
1.2高强韧性能采用高强度耐候钢来制造铁路货车车体,可有效提高车体强度降低车体用钢厚度,降低整车生产成本,具有提高载重量降低资源消耗等诸多优点,但耐候钢高强化的同时,需考虑刚度问题,并要根据用户的使用要求保证成形性能、焊接性能、低温冲击性能和疲劳性能等。
铁路车辆用V-N-Cr微合金化Q690高强耐候钢组织性能和腐蚀行为

材料工程Journal of Materials Engineering第4 9卷 第4期2021年4月 第111 — 119页Vol. 4 9 No. 4Apr. 202 1pp. 1 11 — 1 1 9铁路车辆用V-N-Cr 微合金化Q690高强耐候钢组织性能和腐蚀行为Microstructureandcorrosionbehaviorof V-N-Cr microalloyed Q690 high strengthweathering steel for railway vehicles刘 悦,吴红艳,杜林秀(东北大学轧制技术及连轧自动化国家重点实验室,沈阳110819)LIU Yue,Wu Hong-yan ,DU LJn-xiu(State Key Laboratory of Rolling and Autoiation, Northeastern University? Shenyang 11 081 9, China)摘要:为开发新一代铁路车辆用高强耐候钢,采用两阶段轧制制备V-N-Cr 微合金化Q690耐候钢,并进行组织观察和力 学性能检测。
采用周期浸润腐蚀实验对V-N-Cr 微合金化Q690耐候钢与Q34 5钢进行腐蚀行为研究。
结果表明:V-N-Cr 微合金化Q690耐候钢的显微组织为多边形铁素体、针状铁素体、板条贝氏体以及少量的M/A 岛,屈服强度及抗拉强度分别为695 MPa 和815 MPa,冲击性能优异,通过大小角度晶界共同作用,有效阻碍裂纹扩展。
两种钢的表面均生成 了明显的锈层,腐蚀产物主要包含aFcOOH ,-FcOOH,y-FcOOH 和FCO i 。
腐蚀360 h 后Q34 5钢的平均腐蚀失重速率为1.83 g/(h ・ci 2) V-N-Cr 耐候钢的腐蚀失重速率为0. 96 g/(h ・ci 2)显著低于Q34 5钢。
关键词:高强度;耐候钢;腐蚀行为;锈层;干/湿循环交替腐蚀实验doi : 10. 11868 j issn 10014381 2019. 000856中图分类号:TG142.4 文献标识码:A文章编号:1001-4381(2021)04-01 1 1-09Abstract : In order to develop a new generation of high strength weathering steel for railway vehicle , V-N-Cr licroalloyed Q690 weathering steel was produced by t.w o-stage rolling , and the micro structuresand lechanical properties were studied. The corrosion behavior of V-N-Cr licroalloyed Q690weathering steel and Q345 steel was studied by cyclic wet./dry corrosion tests. The results show that,the iicrost.ruct.ure of V-N-Cr licroalloyed Q690 weathering steel is polygonal ferrite , acicular ferrite , lath bainite and a few M/A phase. The yield strength and tensile strength are 695 MPa and 815 MPa,respectively , with excellent, impact, perforiance. The crack propagation is effectively hindered by the interactonofgrainboundarieswithlargeandsma l angles.Thesurfacesofbothkindsofsteelshave formed rust, layer, and corrosion products mainly include ct-FeOOH ,-FeOOH,了-FeOOH and Fe ;O 4.After 360 h corrosion , the average corrosion rate of Q345 steel is 1. 83 g/(h ・ ci 2) , and that, of V-N- Cr weathering steel is 0. 96 g/(h • ci 2).Key words : high strength ; weathering steel ; corrosion behavior ; rust layer ; cyclic wet./dry corrosion test.耐候钢是指具有保护锈层并且耐大气腐蚀的低合 金结构钢,它能有效地阻滞腐蚀介质的深度腐蚀[-5],是铁道车辆用钢材用量最大的钢种,在铁路车辆运行 过程中会不断地受到大气环境腐蚀等恶劣应用环境的 影响。
铁路货车车辆用耐候钢的开发

可焊性:
合金元素增加,降低C含量,满足铁道部焊接碳当量≤0.55%的要求
加工工艺:
现有的热连轧工艺: 终轧温度≥840℃,冷却温度范围700~500 ℃,板厚度3~ 20mm(以3~14mm为主) 根据现有工装情况,调整控轧温度区间和水冷温度区间 轧制工艺设计时考虑耐蚀组织设计: 成分和组织均匀化,减少碳化物析出量,提高钢表面电化学的均匀性
谢
谢!
�
3 研究内容和技术路线
研究内容:
1. 车辆用钢失效因素分析 利用现有的Q450NQR1钢及其焊接工艺及 焊接材料, 分别对下述四种损伤类型进行评价试验,探索箱体钢 板及其焊缝失效损伤的主要因素.
大气腐蚀评价试验(周浸,水雾,循环试验等) 煤水腐蚀评价试验(浸泡,周浸) 煤水磨损腐蚀(微动磨损腐蚀,振动磨损腐蚀等) 磨损(煤块磨损,煤粉磨损)
2. 高耐蚀钢种开发
在上述失效因素评价的基础上,针对主要的失效类型,研发耐蚀 钢种. – 材料制备研究:成分设计, 冶炼, 控轧控冷 – 性能评价:腐蚀评价,强度评价,韧性评价,疲劳评价 –材料表面锈层的力学,化学及其与基体结合力评价,抗腐蚀 和磨损损伤能力的评价
3. 焊接材料与焊接工艺研究
在保证现有焊接材料的焊接接头强度韧性水平基础上,开发与母 材相匹配的高耐蚀的焊接材料,并探索相适应的焊接工艺
耐蚀性能评定: 室内模拟实验方法以及铁道部标准方法 耐蚀性能比较:比较新旧钢种耐蚀性能差别 耐蚀成分的优选: 优选出耐蚀性能达到要求的新钢种成分3~5种
焊接技术开发:
焊材成分,焊接工艺的确定: 1,调整焊材成分,提高焊缝金属的耐蚀性能 提高焊材中Ni元素和Cu元素 2,调整焊接工艺,使焊接接头的热影响区的冲击韧性 3,焊接接头腐蚀性能:焊接接头腐蚀性能不低于本体 材料 焊接性能符合铁道部低合金钢焊接技术条件
新一代钢铁材料在铁路货车车辆上的应用探讨

— 。
在 铁路 车 辆用 钢 采 用的 主要 是 普 通 耐候 钢 癣顾 了 我 国铁路 货 车车 辆 用钢 的 发展 及现
状 ,提 出 在高速重载 条 下 铁路 货车 车辆 件 已经 不能 满足 铁路 快速 发展 的要 求 。
SOK TC S
行 了高 强 、耐腐 蚀 、可焊 接 的新一 代钢 铁材
料 的开 发 ,并 已探索 出 工业应 用的 途径 。我 国于 19 年底 启动 了 国家 重大 基础研 究规划 98 项 目(7 9 3项 目) ,即 “ 新一 代钢 铁 材料 的重 大 基础 研 究 ” 。该 项 目的 最 终 目标 是将 占我
增旭 瓤 够
不 同使 用要 求的 各种 类型 的高 强钢 ,钢 材的
复 相化 得 到 了人们 的 重视 。
素 钢 , 因而 抗 大 气 腐 蚀 能 力差 、使 用寿 命 短 ,货车 运 行一 年半 就 要 进行 段修 ,5 要 年 进行 大修 ,这 不仅 耗 费大量 修 理费 用 ,而且 严重影 响车 辆的 周转 ,为此 , 国从 2 世纪 我 0
制和 控制 冷却技 术( M C )的研 究 ,将 微合 T P 金化 术的 效果 发挥到 新 的水平 。 0 2 世纪 9 年 0 代 ,利 用相 变强化 等 手段 ,开 发 出可以满 足
新 一代 钢铁 材料 高强度 耐候钢 ;铁 路货 车
钢 等 ,7 0年代 中期 ~8 0年 代 中期 ,通 用 货
8 年 代着手 耐 候钢 的攻 关 并 投入 批量 生产 , 0 进入 9 0年 代 , 已开发 出一 批钢 号 ,其 中有 C- u P系列和 C — r i 列 ,屈服 强度 u P C N 系 为 2 5 a的 0 P Re和 屈服 强度 为 9 MP 9 Cu Ti 35 a 9 u C Ni 候钢 已在中 国铁 道车 4MP 的0 C P r 耐 辆 上得 到 了广泛 的应 用 。随 着铁 路现 代化 建 设 的发 展 ,高速 、重 载 已成 为 目前 工 作的 当 务之 急 ,选 用高 强度 高 耐 候的 结构 钢以 降 低车 辆 自重 、提高 整车 性 能 问题显 得尤 为突
铁道车辆用高强高耐候钢焊接连续冷却转变规律分析
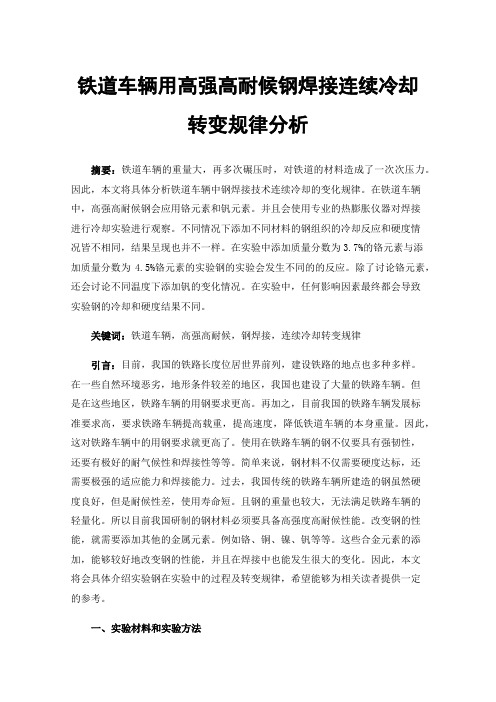
铁道车辆用高强高耐候钢焊接连续冷却转变规律分析摘要:铁道车辆的重量大,再多次碾压时,对铁道的材料造成了一次次压力。
因此,本文将具体分析铁道车辆中钢焊接技术连续冷却的变化规律。
在铁道车辆中,高强高耐候钢会应用铬元素和钒元素。
并且会使用专业的热膨胀仪器对焊接进行冷却实验进行观察。
不同情况下添加不同材料的钢组织的冷却反应和硬度情况皆不相同,结果呈现也并不一样。
在实验中添加质量分数为3.7%的铬元素与添加质量分数为4.5%铬元素的实验钢的实验会发生不同的的反应。
除了讨论铬元素,还会讨论不同温度下添加钒的变化情况。
在实验中,任何影响因素最终都会导致实验钢的冷却和硬度结果不同。
关键词:铁道车辆,高强高耐候,钢焊接,连续冷却转变规律引言:目前,我国的铁路长度位居世界前列,建设铁路的地点也多种多样。
在一些自然环境恶劣,地形条件较差的地区,我国也建设了大量的铁路车辆。
但是在这些地区,铁路车辆的用钢要求更高。
再加之,目前我国的铁路车辆发展标准要求高,要求铁路车辆提高载重,提高速度,降低铁道车辆的本身重量。
因此,这对铁路车辆中的用钢要求就更高了。
使用在铁路车辆的钢不仅要具有强韧性,还要有极好的耐气候性和焊接性等等。
简单来说,钢材料不仅需要硬度达标,还需要极强的适应能力和焊接能力。
过去,我国传统的铁路车辆所建造的钢虽然硬度良好,但是耐候性差,使用寿命短。
且钢的重量也较大,无法满足铁路车辆的轻量化。
所以目前我国研制的钢材料必须要具备高强度高耐候性能。
改变钢的性能,就需要添加其他的金属元素。
例如铬、铜、镍、钒等等。
这些合金元素的添加,能够较好地改变钢的性能,并且在焊接中也能发生很大的变化。
因此,本文将会具体介绍实验钢在实验中的过程及转变规律,希望能够为相关读者提供一定的参考。
一、实验材料和实验方法目前,我们国家在实验中得到的高强度高耐候钢是S450EW。
因为这种钢的使用性能相较其他刚较好,且合金元素在反应中的转变也较为积极。
宝钢铁道车辆用耐候钢研制回顾与展望

相 对 于 普 通 钢 抗 大 气 腐 蚀 的有 效 性 和 相 对 于 不 锈 钢 的 经 济 性 ,耐候 钢 在 世 界 各 国得 到 了迅速 发展 ,在C r T n o— e 系列 基 础 上 ,各 钢 铁 大 国 根 据 资 源 和 使 用 要 求 开 发 了品 种 繁 多 的 耐 候 钢 系 列 。 我 国 开 发 耐 候 钢 品 种 起 步 较 晚 , 1 6 年鞍 钢 91 开 始 研 制 1 Mn u 6 C ,又 结 合 国 内资 源 特 点 研 制 了 一 批 含 铜 、 磷 、 钛 及 稀 土 等 元 素 的耐 候 钢 。 1 6 年 武 汉 钢 铁 公 司 、 铁 99 道 部 科 学 研 究 院 、 齐 齐 哈 尔 车 辆 厂 曾 共 同 研 制 0 Mn u T 9 C Pi 制 造 铁 路 货 车 。 1 7 年 以后 ,开 始 采 用 镍 和 铬 等 元素 仿 制 98 国 外 耐 大 气腐 蚀 钢 。 武 钢 与 有 关 科 研 院所 从 1 6 年 起 选 择 95
了1 9种 含 铜 钢 及 含 稀 土 、钛 、锰 等 元素 的低 合 金 钢 ,在 我
根据 铁道部 对高耐候钢 的需求 ,宝钢在 19 ~ 9 4 9 1 1 9 年
研 制 了 与 美 国C rT n o— e 对 应 的C — — rN 系 的 高 耐 候 A相 u P C— i 钢 ,B 8 GN 4 0 QR就 是 这 一 时 期 的 产 物 。该 钢种 首 先 用 于 要
国 不 同环 境 条 件 下 进 行 了 7 周 期 长 达 1 年 的 大 气 暴 露 试 个 5 验 ,积 累 了一 批 可 靠 的 数据 ,对 进 一 步 发 展 我 国 耐 候 钢 奠 定 了 良好 的 基础 。 铁 道 车辆 的 技 术 进 步 , 一定 程度 上依 赖 于 我 国 钢 材 的 品种 、性 能 与质 量 。在 2 世 纪 8 年 代 以前 ,钢 结 构 基 本 上 O O 采 用 普 碳 钢 等 ,耐 大 气 腐 蚀 钢 则 一 直 以 屈 服 强 度 为 2 5 9 MP a的0 C P ie 屈 服 强 度 为 3 5MP 的 0 C P r i 9 u TR 和 4 a 9 u C N 为 主 ,而 美 国等 一 些 发 达 国 家 耐 候 钢 的 强 度 水 平 已高 达 5 0 5
中国铁路车辆用钢及主要生产厂家简介

中国铁路车辆用钢及主要生产厂家简介截止2008年底,中国铁路营业里程已达8万公里,居世界第三。
中国铁路的运输密度、货物周转量、旅客周转量、货物发送量均居世界第一位。
中国铁路以占世界铁路6%的营业里程完成了世界铁路25%的工作量,运输效率世界第一。
客车方面,继主要干线提速到160km/h之后,在诸多干线和新建的客运专线开行时速200km/h动车组。
国产时速350公里动车组批量生产,已经投入京津城际铁路运营,京沪高速铁路正在紧张建设中。
货车方面,对既有货车实现构造速度120km/h的改造,载重70t的货车研制成功,并全面投产,实现我国铁路货车技术第三次升级换代。
新型通用货车和经过技术改造的货车占货车保有量的83%以上。
到2012年,全国铁路营业里程将达到11万公里,复线率和电气化率分别达到50%以上,客运专线及城际铁路将有1.3万公里。
投入运营的动车组达到800组以上,覆盖整个快速客运网。
空调客车将达到2.5万辆。
货车车辆实现更新换代,全部达到时速120km/h技术标准,并陆续推出载重80吨通用货车、30吨轴重专用货车。
在这种新形势下,铁路行业和冶金行业在铁路车辆用钢方面的技术交流就显得十分必要和迫切。
“铁路车辆用钢材研讨会”于2009年5月26日在北京召开。
会议由中国钢铁工业协会科技与发展部和中国铁道学会车辆委员会主办,北京艾莱咨询有限公司承办。
铁道部运输局装备部,世界轨道交通发展研究会,冷弯型钢协会,北车集团,南车集团,齐齐哈尔、西安、太原轨道交通装备有限责任公司,长江、眉山、北京二七车辆有限公司,包头北方创业股份有限公司,鞍钢、宝钢、武钢、攀钢、太钢、首钢、唐钢、马钢、通钢、南钢、莱钢、武钢集团汉口轧钢厂、宝钢建筑设计院冷弯型钢厂、长春新金享冷弯型钢有限公司等29个单位的68名代表参加了研讨会。
参加会议的主要领导有:中国钢协科技与发展部主任曹真、副主任徐寅、处长姜尚清,铁道部运输局装备部调研员王春山,中国铁道学会秘书处办公室主任吕一力,中国铁道学会车辆委员会秘书长金城、副秘书长张进德、包耀慈,《世界轨道交通》杂志主编董叶青,世界轨道交通发展研究会秘书长贾国平,冷弯型钢协会会长丁国良等。
武钢铁路车辆用耐候钢的开发

武钢铁路车辆用耐候钢的开发
陈吉清;陈邦文;胡敏;宋育来
【期刊名称】《钢铁研究》
【年(卷),期】2003(31)5
【摘要】介绍了武钢生产的铁路车辆用耐候钢的特点 ,分析稀土对Cu -P系列耐候钢的作用机理 ,并介绍武钢正在开发的耐候钢新钢种。
【总页数】3页(P49-51)
【关键词】铁路车辆;耐候钢;稀土;作用机理;开发
【作者】陈吉清;陈邦文;胡敏;宋育来
【作者单位】武汉钢铁集团公司
【正文语种】中文
【中图分类】TG142.7;U270.41
【相关文献】
1.高耐候高强度冷轧结构钢GN310(05CuPCrNi)的开发及在铁路车辆制造上的应用 [J], 张海岭;谢铜;刘家宁
2.武钢成功开发铁路车辆用高耐蚀型耐候钢 [J], 无
3.铁路车辆用高强耐候钢的开发 [J], 胡德勇;高秀华;周海峰;徐立山;安会龙;刘向明;吴红艳
4.铁路车辆用V-N-Cr微合金化Q690高强耐候钢组织性能和腐蚀行为 [J], 刘悦;吴红艳;杜林秀
5.武钢铁路车辆及集装箱用耐候钢的现状及发展 [J], 刘志勇;陈邦文;陈吉清;胡敏;宋育来
因版权原因,仅展示原文概要,查看原文内容请购买。
- 1、下载文档前请自行甄别文档内容的完整性,平台不提供额外的编辑、内容补充、找答案等附加服务。
- 2、"仅部分预览"的文档,不可在线预览部分如存在完整性等问题,可反馈申请退款(可完整预览的文档不适用该条件!)。
- 3、如文档侵犯您的权益,请联系客服反馈,我们会尽快为您处理(人工客服工作时间:9:00-18:30)。
可焊性:
合金元素增加,降低C含量,满足铁道部焊接碳当量≤0.55%的要求
加工工艺:
现有的热连轧工艺: 终轧温度≥840℃,冷却温度范围700~500 ℃,板厚度3~ 20mm(以3~14mm为主) 根据现有工装情况,调整控轧温度区间和水冷温度区间 轧制工艺设计时考虑耐蚀组织设计: 成分和组织均匀化,减少碳化物析出量,提高钢表面电化学的均匀性
强度满足,但是腐蚀速率没有降低,检修周期需要8年 铁道部要求在现有强度水平下,将腐蚀速率降低到60%的 水平,这样壁厚可以进一步降低,而且大修周期可以延长 到12年
箱体腐蚀磨损减薄导致车辆报废
铁道部对耐候车辆箱体损伤减薄的调查结果
耐候钢腐蚀调查结果:
– 腐蚀磨损严重.各个部位的平均减薄速率分布在0.07~ 0.25mm/ a – 局部最大减薄速率则为平均值的2 倍~5 倍 (0.14-1.25mm/ a ) – 下侧门板减薄速率最大,平均减薄速率可达0.25mm/ a. 其局部最大减薄速率可以达到1.25mm/a以上. – 下侧门板减薄速率高的原因可能是受力大,且煤车下部 含
– P 耐蚀元素作用显著,但增加裂纹倾向,尝试少量添加,0.07% – Cu 主要耐蚀并且低碳当量元素,提高冲击韧性,适当提高Cu含量 ,0.55 ~ 0.75% – Ni 主要耐蚀元素,价格高,0.65~0.75% – Cr 提高含量,1.50~1.85%,或者再高 – C 降低含量至0.02% ,降低碳当量,同时提高P元素的耐蚀作用 – Mn和Si含量尽量降低,降低C当量
– 成分设计和焊材开发
– 焊接工艺开发 – 焊接接头性能评定(腐蚀,强度,韧性,疲劳等)
技术路线 钢种开发需要基于其所对应的主要损伤失效的类型来进行开 发.例如,对于大气腐蚀的钢种我们可以按照下述技术 路线进行开发.其它类型的失效形式开发的技术路线相 似. 提高耐蚀性能的成分设计思路:
在现有Q450钢成分和工艺基础上进行耐蚀成分的调整,提 高耐蚀成分的含量及组合作用,提高耐蚀性能,同时结 合TMCP工艺和微合金化技术优化新成分钢种的力学和 焊接性能
新型铁路车辆用耐候钢及其耐 蚀焊接技术开发
北京科技大学 路民旭
2009年9月26日
报告内容
1 2 3 研发背景和现状 研究目标和意义 研究内容和技术路线
1 研发背景和现状
随着我国铁路货车高速化和重载化的迅速发展, 车体减重和高强度储备已成为发展趋势,对高强 度高耐蚀车辆用钢的需求已经非常迫切.
以运煤箱体为例,车辆受到的腐蚀和磨损损伤来自于下述 四个方面:
– 车厢在大气中所受的大气腐蚀 – 车厢煤水浸泡环境中的煤水腐蚀(水来源:雨水和酸雨) – 车厢由于煤的运动摩擦导致的煤水磨损腐蚀 – 车厢由于干煤造成的磨损
上述四种损伤形式那一种对箱体的减薄起主导作用,目前 尚无定论.但目前铁道部标准只利用周浸试验来模拟大气 腐蚀对钢板耐蚀性进行评价,没有考虑到后几种损伤类型 ,所以需要探索能反应真正减薄过程的评价方法
2. 高耐蚀钢种开发
在上述失效因素评价的基础上,针对主要的失效类型,研发耐蚀 钢种. – 材料制备研究:成分设计, 冶炼, 控轧控冷 – 性能评价:腐蚀评价,强度评价,韧性评价,疲劳评价 –材料表面锈层的力学,化学及其与基体结合力评价,抗腐蚀 和磨损损伤能力的评价
3. 焊接材料与焊接工艺研究
在保证现有焊接材料的焊接接头强度韧性水平基础上,开发与母 材相匹配的高耐蚀的焊接材料,并探索相适应的焊接工艺
– 高强度:可以减少满足强度要求的车辆壁厚 – 高耐蚀:可以减少满足腐蚀寿命的壁厚裕量
降低壁厚
但在高强度高耐蚀前提下,具有良好的焊接性能 和足够的性能价格比是另外两个约束条件
典型的抗蚀耐候钢:
– 09CuPTiRE – 09CuPCrNi 及在此基础上改进开发的一些钢种 – 08CuPVRE 系列,09CuPTi 系列,09MnNb, 10CrMoAl ,10CrCuSiV
3 研究内容和技术路线
研究内容:
1. 车辆用钢失效因素分析 利用现有的Q450NQR1钢及其焊接工艺及 焊接材料, 分别对下述四种损伤类型进行评价试验,探索箱体钢 板及其焊缝失效损伤的主要因素.
大气腐蚀评价试验(周浸,水雾,循环试验等) 煤水腐蚀评价试验(浸泡,周浸) 煤水磨损腐蚀(微动磨损腐蚀,振动磨损腐蚀等) 磨损(煤块磨损,煤粉磨损)
耐蚀性能评定: 室内模拟实验方法以及铁道部标准方法 耐蚀性能比较:比较新旧钢种耐蚀性能差别 耐蚀成分的优选: 优选出耐蚀性能达到要求的新钢种成分3~5种
焊接技术开发:
焊材成分,焊接工艺的确定: 1,调整焊材成分,提高焊缝金属的耐蚀性能 提高焊材中Ni元素和Cu元素 2,调整焊接工艺,使焊接接头的热影响区的冲击韧性 3,焊接接头腐蚀性能:焊接接头腐蚀性能不低于本体 材料 焊接性能符合铁道部低合金钢焊接技术条件
耐煤水磨损腐蚀钢的设计思路
钢的耐煤水腐蚀性能: 提高钢中Cr和Ni元素含量,提高基体本身的耐蚀性能; 组织均匀化,减少阴极相的数量,提高电化学性质的均匀性; 钢的耐磨损性能: 提高钢的硬度,同时提高钢中Si和Mn元素的含量,提高钢本体的耐磨 损性能; 提高C含量,增加钢的硬度,提高耐磨损性能,C含量范围 0.12 ~0.3%% 提高钢中Cr元素的含量,Cr含量范围7~10%, 提高钢中Ni元素的含量,Ni含量范围1.5~2% 存在的问题: 强度,冲击韧性,疲劳性能和焊接性能的难度加大,需要调整评价和验 收标准; 焊材成分和焊接工艺的调整
谢
谢!
�
这些钢的强度级别多为295MPa和345MPa
为了应对车辆发展对高强度耐候钢的需求,近些年来发 展出了450MPa级的耐候钢:
– Q450NQR1
Q450NQR1化学成分 C <0.12 S <0.008 Si <0.75 Cu 0.20-0.55 Mn <1.50 Cr 0.30-1.25 P <0.025 Ni 0.12-0.65
其它性能:
符合铁道车辆用耐大气腐蚀钢验收技术条件
耐煤水磨损腐蚀钢的设计思路
钢的耐煤水腐蚀性能: 提高钢中Cr和Ni元素含量,提高基体本身的耐蚀性能; 组织均匀化,减少阴极相的数量,提高电化学性质的均匀性; 钢的耐磨损性能: 提高钢的硬度,同时提高钢中Si和Mn元素的含量,提高钢本体的耐磨损性能; 提高C含量,增加钢的硬度,提高耐磨损性能,C含量范围0.12~0.3%% 提高钢中Cr元素的含量,Cr含量范围7~10%, 提高钢中Ni元素的含量,Ni含量范围1.5~2% 存在的问题: 强度,冲击韧性,疲劳性能和焊接性能的难度加大,需要调整评价和验收标准; 焊材成分和焊接工艺的调整
2 研究目标
研究目标:
1. 利用现有的Q450NQR1钢,针对大气腐蚀,煤水腐蚀,煤 水磨损腐蚀和煤磨损四种损伤类型,进行损伤评价试验,找 出导致箱体减薄的主要损伤与因素,为新钢种设计奠定方向 目标 2. 在四种类型损伤评价试验的基础上,修改铁道部现有标准, 建立能够放映车辆箱体真正损伤过程的评价方法 3. 在现有Q450NQR1钢的基础上,针对主要损伤减薄类型, 进行钢种开发,在维持材料强韧性水平和可焊性的基础之上 ,材料的腐蚀损伤速率降低到现有钢种的60%,成本控制 达到铁道部的要求