主生产计划的功能以及其相关MRP类型参数
MRPⅡERP之第5章主生产计划
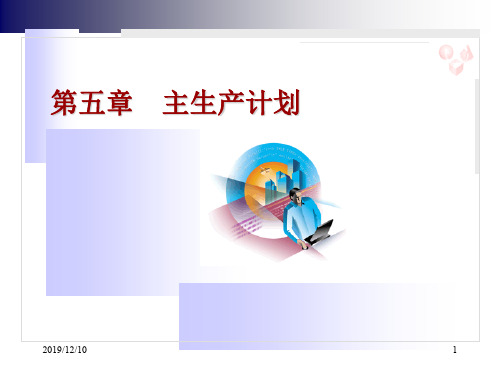
辐条
.II3000
车把
2019/12/10
单位 辆 件 个 件 套 根 套
数量 1 1 2 1 1 42 1
生效日期 20020101 20020101 00000000 20020101 00000000 20020101 00000000
失效日期 20071231 20071231 99999999 20071231 99999999 20071231 99999999
2019/12/10
9
不同形式的产品结构
A型
V型
X型
T型
机电产品
2019/12/10
化工产品 按定单选择装配 冶金材料
10
物料清单的种类
基本物料清单 计划物料清单 模块化物料清单 成本物料清单
2019/12/10
11
标准 BOM
标准物料清单是最通用的清 单类型,并列有组件、每个 组件的要求数量等信息
第五章 主生产计划
2019/12/10
1
5.1 基本概念--物料清单
物料清单
物料清单(BOM—Bill Of Materials)是描述产品结构的管理 文件。
A
零级
B×1
C×3
D×2
一级
EБайду номын сангаас3 F×2
G×1 E×1
H×2 F×1
二级 I×1
2019/12/10
2
自行车物料清单
2019/12/10
计划投入量
根据计划产出量、物料的提前期及物料的成品率等计算 出的投入数量和投入时间
2019/12/10
32
基本概念3
可供销售量
主生产计划主要内容
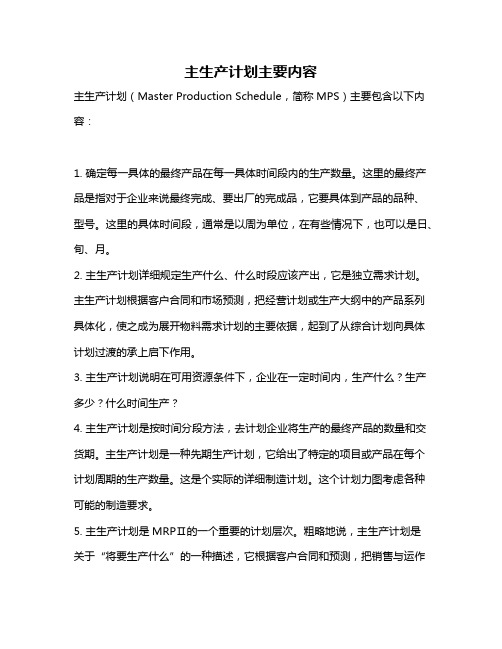
主生产计划主要内容主生产计划(Master Production Schedule,简称MPS)主要包含以下内容:1. 确定每一具体的最终产品在每一具体时间段内的生产数量。
这里的最终产品是指对于企业来说最终完成、要出厂的完成品,它要具体到产品的品种、型号。
这里的具体时间段,通常是以周为单位,在有些情况下,也可以是日、旬、月。
2. 主生产计划详细规定生产什么、什么时段应该产出,它是独立需求计划。
主生产计划根据客户合同和市场预测,把经营计划或生产大纲中的产品系列具体化,使之成为展开物料需求计划的主要依据,起到了从综合计划向具体计划过渡的承上启下作用。
3. 主生产计划说明在可用资源条件下,企业在一定时间内,生产什么?生产多少?什么时间生产?4. 主生产计划是按时间分段方法,去计划企业将生产的最终产品的数量和交货期。
主生产计划是一种先期生产计划,它给出了特定的项目或产品在每个计划周期的生产数量。
这是个实际的详细制造计划。
这个计划力图考虑各种可能的制造要求。
5. 主生产计划是MRPⅡ的一个重要的计划层次。
粗略地说,主生产计划是关于“将要生产什么”的一种描述,它根据客户合同和预测,把销售与运作规划中的产品系列具体化,确定出厂产品,使之成为展开MRP与CRP(细能力计划)运算的主要依据,它起着承上启下,从宏观计划向微观过渡的作用。
6. 主生产计划是计划系统中的关键环节。
一个有效的主生产计划是生产对客户需求的一种承诺,它充分利用企业资源,协调生产与市场,实现生产计划大纲中所表达的企业经营目标。
主生产计划在计划管理中起“龙头”模块作用,它决定了后续的所有计划及制造行为的目标。
以上信息仅供参考,如需获取更多详细信息,建议查阅主生产计划的制定和管理相关书籍或文献。
主生产计划
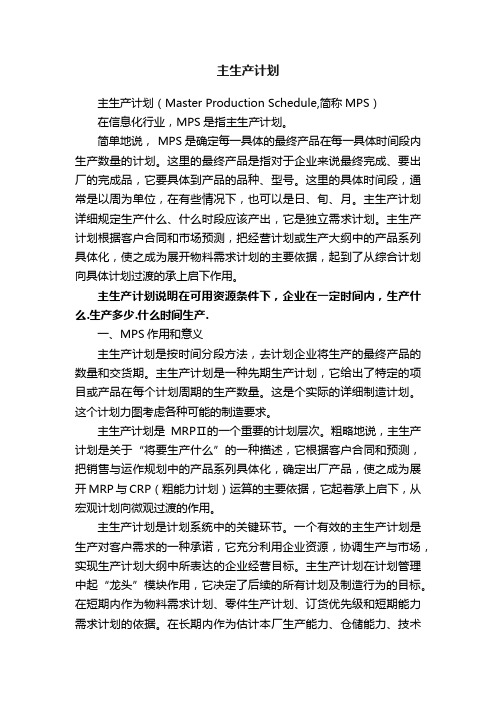
主生产计划主生产计划(Master Production Schedule,简称MPS)在信息化行业,MPS是指主生产计划。
简单地说, MPS是确定每一具体的最终产品在每一具体时间段内生产数量的计划。
这里的最终产品是指对于企业来说最终完成、要出厂的完成品,它要具体到产品的品种、型号。
这里的具体时间段,通常是以周为单位,在有些情况下,也可以是日、旬、月。
主生产计划详细规定生产什么、什么时段应该产出,它是独立需求计划。
主生产计划根据客户合同和市场预测,把经营计划或生产大纲中的产品系列具体化,使之成为展开物料需求计划的主要依据,起到了从综合计划向具体计划过渡的承上启下作用。
主生产计划说明在可用资源条件下,企业在一定时间内,生产什么.生产多少.什么时间生产.一、MPS作用和意义主生产计划是按时间分段方法,去计划企业将生产的最终产品的数量和交货期。
主生产计划是一种先期生产计划,它给出了特定的项目或产品在每个计划周期的生产数量。
这是个实际的详细制造计划。
这个计划力图考虑各种可能的制造要求。
主生产计划是MRPⅡ的一个重要的计划层次。
粗略地说,主生产计划是关于“将要生产什么”的一种描述,它根据客户合同和预测,把销售与运作规划中的产品系列具体化,确定出厂产品,使之成为展开MRP与CRP(粗能力计划)运算的主要依据,它起着承上启下,从宏观计划向微观过渡的作用。
主生产计划是计划系统中的关键环节。
一个有效的主生产计划是生产对客户需求的一种承诺,它充分利用企业资源,协调生产与市场,实现生产计划大纲中所表达的企业经营目标。
主生产计划在计划管理中起“龙头”模块作用,它决定了后续的所有计划及制造行为的目标。
在短期内作为物料需求计划、零件生产计划、订货优先级和短期能力需求计划的依据。
在长期内作为估计本厂生产能力、仓储能力、技术人员、资金等资源需求的依据。
为什么要先有主生产计划,再根据主生产计划制订物料需求计划?直接根据销售预测和客户订单来制订物料需求计划不行吗?产生这样的疑问和想法的原因在于不了解MRP的计划方式。
主生产计划概述

不同生产方式MPS的计划对象
MPS的制定对象:
最终产品
部件/组件
原材料
MTS备货生产
ATO组装生产
MTO订货生产
各种制造环境下MPS计划对象与计划方法
销售环境 现货生产MTS 计划依据 主要根据市场预测 安排生产;产品完 成后入库待销,要 进行促销活动 MPS计划对象 独立需求类型物料 举 例 大批生产的定 型产品 , 如日用 消费品
订单 销售与运作规划 预测
提前期限制
主生产计划 MPS
能力限制
识别生产品种
确定生产数量
安排生产时间
承上启下 ▪ 均衡生产 ▪ 沟通内外
主生产计划在ERP中的层次
ERP共有五个层次: 1. 经营规划—决策层 2. 销售运作规划(生产计划大纲)—决策层 3. 主生产计划与粗能力计划—计划层 4. 物料需求计划与能力需求计划—计划层 5. 采购作业与车间作业计划—执行控制层 主生产计划在以上层次中,具有指导性和过渡性作用。
主生产计划的作用
1.承上启下。 主生产计划是把企业经营战略、生产计划大纲等转化为具体可执行的生 产作业计划和采购作业计划等的工具,是企业物料需求计划的直接来源, 是进行物料需求计划(MRP)运算的前提和基础。 2.均衡、稳定计划。 销售预测和客户订单是不稳定、不均衡的,如果直接用来安排生产,会 出现有时加班加点却不能完成任务,有时则设备闲置、人员闲置的矛, 同时企业的资源和生产能力是有限的,这将给企业带来灾难性后果。通 过制定主生产计划,可以使得主生产计划和销售预测及客户订单在时间
编制主生产计划的对象 策略和原则
主生产计划的对象
主生产计划的计划对象,主要是把生产规划中的产品系列具体化以后的出厂产品, 通称最终项目。但是在不同的生产方式下,对象可以是最终销售的产成品,也可 以是组件或模块化的半成品。由于计划范围和销售环境不同,作为计划对象的最 终项目其含义也不完全相同。 从满足最少项目数的原则出发,下面对3种制造环境分别考虑MPS应选取的计划 对象。 为库存生产的公司(MTS make to stock) :用多种原材料和部件制造出少量品种 的标准产品(消费终端产品),则产品、产品备件等独立需求项目是MPS计划对象 为订单生产的公司(MTO make to order) :最终项目一般就是标准定型产品或按 订货要求设计的产品,如电子行业各种组件。MPS的计划对象可以放在相当于T形 或V形产品结构的低层,以减少计划编制对象的数量。 为订单装配的公司(ATO assemble to order):产品是一个系列,结构相似,表现 为模块化,由若干基本组件和一些通用部件组成。每项基本组件又有多种可选模 块,成品有多种模块搭配选择(如电脑等),形成一系列规格的变型成品。此时 可将主生产计划对象设定为基本组件和通用部件。这时主生产计划就是基本组件 (如发动机、车身等)的生产计划。
主生产计划定义与作用介绍
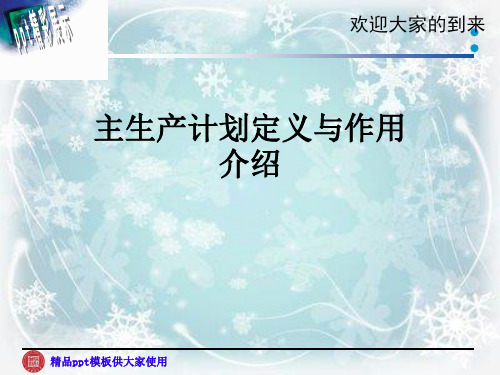
试
试仪器
绝缘电 Z04+绝缘电 小时 1200 1250 500
阻测试 阻测试仪器
能力 超/欠
-150 200 200 50
负荷率
111.11% 83.33% 83.33%
96%
精品ppt模板供大家使用
❖进一步确定某工作中心的各具体时段的负荷 与能力,找出超负荷时段
锤头
偏置时间 锤把
铁锤 时间顺序
精品ppt模板供大家使用
➢ 批准和下达主生产计划
下达部门:生产制造部门、采购部门、工程技术部门、 市场销售部门、财务部门等
➢ 修改MPS的方法
计划的重排和部分修订 ❖全重排法
主生产计划完全重新制定,原有计划被全部删除,计划全部 梳理一遍。重排计划的间隔时间要根据产品结构的复杂程度 ,物料数量的多少,对计划准确度的要求,计划变动影响面 的大小,计算机和服务器的运行速度等因素。
精品ppt模板供大家使用
❖ 时区3,计划以预测为主,或取预测与合同 的最大值。计划允许变动,无代价。系统可 自动更改,计划员即有权可进行更改。
精品ppt模板供大家使用
时区
起点
需求时界
计划时界
总装提前期
累计提前期(加工/采购)
1
2
3
时段 需求依据
12 3 合同
456789 合同及预测的取舍
10 11 12
精品ppt模板供大家使用
➢主生产计划作用
在ERP系统中起着承上启下的作用,实现从 宏观计划到微观计划的过渡与连接 企业的物料需求计划、车间作业计划、采购 计划等均来源于主生产计划
精品ppt模板供大家使用
粗能力计划(Rough-cut Capacity Planning , 简称RCCP)
主生产计划的功能以及其相关MRP类型参数

主生产计划的功能以及其相关MRP类型参数2.MRP运行方式3.MRP运行的先决条件4.客制化MRP参数的优先级别5.MRP的运算逻辑及低阶码的用途6.SAP PP MD02界面参数说明7.mrp操纵参数及未清期间8. SAP PP MRP视图中重要栏位的意义及功能作用主生产计划的功能与其有关MRP类型参数主生产计划实际相当于一个计划调节器,用主生产计划能够合理的调节企业资源配置与需求的矛盾,避免由于需求不稳固造成的产品未能按期交货,产品积压,资源浪费、超负荷运转等现象,提高企业对用户的服务水平。
通常MPS的计划对象为最终产品或者者关键重要部件,有的时候候也会对原材料做计划,比如造船行业。
原料品种比较少而产品品种比较多。
在SAP系统,与MPS有关的MRP类型有:M0 MPS,固定类型 -0-M1 MPS,固定方式 -1-M2 MPS,固定方式 -2-M3 MPS,固定方式 -3-M4 MPS,固定方式 -4-到后台去看这些参数的配置,发现只有确定的类型(Firming Tpyes)一个值不一样0 计划结果未被确认1 自动确定与订购建议被重新计划2 不含订购建议的自动确定3 手工确定与订单建议再计划4 手工确定不含订单建议为了弄清晰上面每个确定类型的含义,需要看下面的图:在时区1、2,某时刻到计划时界这个区间内计划订单是否被确定,新的需求的是否创建与创建的落点在那个区间,由这个确定类型参数确定,下面是它的全面解释。
tpye0 :需求不自动确定,新的需求在需求日期创建,不可能自动确定(计划时界内外都一样)。
tpye1 :需求自动确定,新的需求假如日期在计划时界内,那么在计划时界结束的位置创建需求。
type2 :需求自动确定,计划时界内的新需求不被考虑,缺料。
tpye3 :需求不自动确定,新的需求假如日期在计划时界内,那么在计划时界结束的位置创建需求。
tpye4 :需求不自动确定,计划世界内的新需求不被考虑,缺料。
主生产计划与物料需求计划

主生产计划与物料需求计划摘要主生产计划(Master Production Schedule,简称MPS)和物料需求计划(Material Requirement Planning,简称MRP)是现代企业生产管理中的重要工具。
MPS和MRP能够帮助企业有效地组织生产活动,合理安排材料和资源,实现生产计划的准确执行。
本文将详细介绍主生产计划和物料需求计划的概念、流程以及在企业运作中的作用。
1. 主生产计划主生产计划是企业根据市场需求和生产能力制定的一份计划,用于指导企业的生产活动。
主生产计划通常是以时间段为单位(如月度、季度、年度)进行制定,并根据销售预测、库存状况、生产能力等因素进行调整。
主生产计划的制定需要综合考虑市场需求、生产能力和库存水平,以确保生产计划的准确性和可行性。
主生产计划的制定流程包括以下几个步骤: - 销售预测:根据市场需求和销售数据,预测未来一段时间内的销售情况。
- 库存分析:分析当前库存水平,确定是否存在库存过剩或缺货的情况。
- 生产能力评估:评估企业的生产能力,包括设备、人员和工时等方面的考虑。
- 制定生产计划:根据销售预测、库存分析和生产能力评估,制定合理的生产计划。
主生产计划的制定需要综合考虑多个因素,如市场需求的波动、生产能力的约束以及供应链的稳定性等。
在制定主生产计划时,需要进行综合权衡和调整,以确保生产计划的可行性和效益。
2. 物料需求计划物料需求计划是基于主生产计划,对所需物料进行合理安排和调配的计划。
物料需求计划通过分析主生产计划中所需产品数量和所需物料的关系,以及当前的库存状况和供应链的情况,确定采购和生产物料的时间和数量。
物料需求计划能够帮助企业准确地控制和管理物料的供应,以避免库存过剩或缺货的情况。
物料需求计划的制定流程包括以下几个步骤: - 列出所需物料:根据主生产计划,列出所需物料及其数量。
- 库存分析:分析当前库存水平,确定是否需要采购物料。
主生产计划概述

主生产计划指出生产部门将要生产什么,也指出了将要为客户生产什么。 所以它是联系生产制造和市场销售的桥梁,它还使生产计划和能力计划 符合销售计划要求的优先顺序,并适应不断变化的市场需求。主生产计 划向销售部门提供生产和库存信息,提供可销售量的信息,作为同客户 洽谈的依据。
路漫漫其悠远
•3
路漫漫其悠远
•7
•加工提前期的五种时间
•排队时间 准备时间 加工时间 等待时间
•加 工 提 前 期
传送时间
提前期分类图
•增值作业
•非增值作业
•总 提 前 期 •累计 提 前 期
•排队时间 •准备时间 •加工时间
•等待时间 •传送时间
• 设计 • 采购 •提前期 •提前期
•生产 提 前 期
• 装配 •提前期
•6
加工提前期包含以下几部分: a.排队时间:指一批零件在工作中心前等待的时间。 b.准备时间:包括熟悉图纸及技术条件、工装的准备和调整等时间。 c.加工时间:在工作中心加工或装配的时间,与工作中心的效率、人员
技术水平相关。每批零件加工时间=零件数量×单个零件加工时间。 d.等待时间:加工完成后等待运往下道工序或存储位置的时间。有些软
主生产计划概述
路漫漫其悠远 2020/4/14
主生产计划基本概念和作用
主生产计划的概念(Master Production Schedule MPS)
主生产计划是企业在当前可用资源条件下,要确定生产什么?生产多少? 什么时间交货?是对企业经营运作与销售预测的具体化。 它是确定每一个具体的产品在每一个具体的时间段的生产数量计划。这 里所说的具体产品一般是最终产品,即企业的销售产品,但有时也可能 是组件的MPS计划,然后再下达最终装配计划。
主生产计划

主生产计划(MPS)
• 主生产计划的细节度比生产规划要高。生产规划时基于产 品族,主生产计划则针对每个终端产品,它将生产规划扩 展为对每一个产品族的单个最终产品的需求,以及产品需 求的日期和数量。 • 生产规划控制住生产计划,主生产计划中的产品生产总量 应该等于生产规划中的产品生产总量。例如:如果生产规
某产品单次生产计划在时间上的时区分布关系
MPS的时间基准 • 时区和时界
总提前期 或 计划跨度 累计提前期(采购 + 加工 ) 总装提前期 时区1 时区2 时区3
某时刻
需求时界
计划时界 21
时间顺序
时段:1 2 3 4 5 6 7 8 9 10 11 12 13 14 15 16 17 18 19 20 50台 60台 30台 40台 15台 35台
340 160
预计库存量
545
590
635
680
670
625
主生产计划(MPS) • 计划期为3~18月
经营规划
销售计划
• 计划周期为周或月
生产计划大纲 (PP) 主生产计划 (MPS) 物料需求计划 (MRP)
决 策 层
管理层
主生产计划(MPS) • MPS的概念
– 物料种类: ▪ 独立需求:最终产品、维修件、工厂自用件。(工 厂生产或直接采购),由MPS来处理 ▪ 相关需要:原材料,MRP处理 ▪ 最终项目:=独立需求(主要指最终出厂产品) ▪ MPS件:最终项目,或者重点管理的部件。 ▪ MPS模块输入数据:
把对产品族的 预测分解到产 品族中的每一 项产品
产品C
总预测量
50
160
50
160
50
160
erp 课件 第5章 MRPII原理—主生产计划

(4)毛需求量=预测量+合同量
计划接收S量 ched10u0 le,简称为MPS)是确定每一个
最 PAB初值 终项70目(-10 E40nd70Ite1m0 ,50即-具60 体-10产30品)70 ,10
在 每 预计库存量 PAB
现有 量80
一70
个90具1体40
的70
时11间0
段50
的140生90产1计30
划70
。110
净需求
• 但是由于生产销售环境不同,作为计 划对象的最终项目其含义也不完全相 同。
• 主生产计划中的最终项目可以是最终 产品、主要组件,还可以是产品结构中 最高层次上的单个零件。
不同生产销售环境MPS的计划对象
最终产品
MPS的计划对象
部件、组件
原材料
生产销售环境 MTS/MTO/ETO
产品结构
A型
ATO X型
确认
安全 库存
40105
40123 计划 计划
—
10 2000/02/03 2000/02/10 10 2000/02/17 2000/02/24 10 2000/03/03 2000/03/10 20 2000/03/17 2000/03/24
…
…
…
…
毛需求
12 8 3 2 7 6
…
计划日期: 计 划 员: 需求时界: 计划时界:
2000/01/31 CS 3 8
需求
需用日期 需求追溯
库存 结余
18
2000/02/03 2000/02/10
=合 合同 同
123 134
6 8
2000/02/24 预测
2000/02/24 合同 141 13
主生产计划和MRP计划计算课件

时段 根据需要人为设定
计划期 不低于产品总提前期 计划的预见性强
时段 控制计划稳定性
批量过大,占用流动资金多,加工和采购费用少 批量过小,占用流动资金少,加工和采购费用多
批量规则:计算物品的计划下达数量所使用的规则。批量不等于净需求
净需求量Net Requirement:在任意给定的计划时间段内某需求项目的实际需求量。 安全库存量Safety Stock:库存量最低限,用于抵抗供需波动,缓和产、供、销之间的矛盾。
(1)MPS中净需求量主要针对独立需求而言
净需求量 = 本周期毛需求量-前一周期末可用库存量-本周期计划接收量+安全库存量
02
主生产计划确定以后,生产管理部门下一步要做的事是,保证生产主生产计划所规定的最终产品所需的全部物料(原材料、零件、部件等)以及其他资源能在需要的时候供应上。
01
3、物料需求计划
5.1 主生产计划(MPS)
主生产计划(Master Production Schedule,简称为MPS)是确定每一个具体的产品在每一个具体的时间段的生产计划。计划的对象一般是最终产品,即企业的销售产品,但有时也可能是组件的MPS计划,然后再下达最终装配计划。主生产计划是一个重要的计划层次。
主生产计划(MPS)
企业的三种主要的计划
综合计划 主生产计划 物料需求计划
1、综合计划(生产大纲)
是根据企业所拥有的生产能力和需求预测,对企业未来较长一段时间内的产出内容和产出量、劳动力水平、库存投资所作的(决策)大致性描述。 产品:以系列为单位 自行车分为24型和28型 时间跨度:年、几年 计划时间单位:月、双月、季 人员:分组,加班以及聘用等
第四章主生产计划

5.毛需求量(Gross Requirement)
毛需求量是在任意给定的计划周期内,项目的总需求量。 毛需求量的确定案例表
时区 计划 周期 预测 值 订单 量 毛需 求量 1 需求时区 2 3 4 计划时区 5 6 7 预测时区 8 9 10
60 55 55
80 85 85
75 70 70
75 70 75
3
2.20 1.34 3.35 11.7 9
4
2.20 1.34 3.35 11.7 9
5
2.20 1.34 3.35 11.7 9
6
2.20 1.34 3.35 11.7 9
7
3.30 2.01 5.03 17.6 9
8
3.30 2.01 5.03 17.6 9
9
3.30 2.01 5.03 17.6 9
计划产出量(planned order receipts)是指在计算 预测可用库存时,如果出现负值,表示需求不能被 满足,需要根据批量政策计算得到的供应数量。 计划投入量(planned order releases)是根据计划 产出量、提前期等数据计算得到的计划投入数量。 可供销售量(available to promise,ATP)是指销 售部门可以销售的产品数量。
表8.4 产品A的能力清单
工作中 心 单件加工时间 单件生产准备时间(h) 单件总时间(h)
10 15
0.22 0.54
0.0191 0.0496
0.2391 0.5896
20
25 30 合计
0.14
0.06 0.09 1.05
0.0376
0.0070 0.0200 0.1233
0.1776
主生产计划
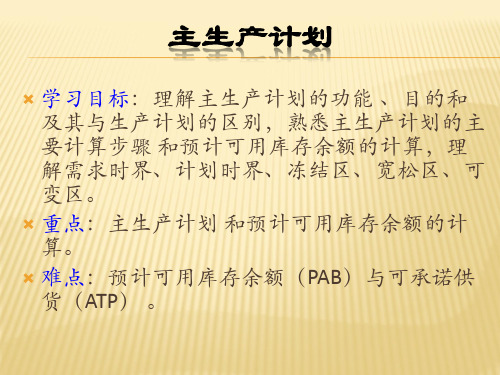
I型主生产计划
周 预测 预计可用库存余额 MPS 300 1 100 2 50 3 200 4 150 总计 500
H型主生产计划
周 预测 预计可用库存余额 MPS 200 1 200 250 250 2 300 200 250 3 100 100 4 100 100 100 总计 700
I型主生产计划
主生产计划
学习目标:理解主生产计划的功能 、目的和 及其与生产计划的区别,熟悉主生产计划的主 要计算步骤 和预计可用库存余额的计算,理 解需求时界、计划时界、冻结区、宽松区、可 变区。 重点:主生产计划 和预计可用库存余额的计 算。 难点:预计可用库存余额(PAB)与可承诺供 货(ATP) 。
MPS 100
45
40
100
50
50
100
5
ATP
生产期
1
2 45
3 40 100 10
4 50
5 50 100 45
6 5
客户订单 80 MPS ATP
100 25
思考:计划人员能否接受第 3周再交付20个单位的订单?
生产期
1
2 45
3
4
5 50 100 45
6 5
客户订单 80 MPS ATP 100 15
3.预计可用库存余额( PAB )
▲预计可用库存余额要考虑预测需求和客户订 单。客户订单有可能大于预测,也有可能小于 预测。 ▲ PAB有两种计算方式 • 需求时界前的生产期 PAB=前期PAB或现有 库存余额+MPS-客户订单 • 需求时界后的生产期 PAB =前期PAB+MPS -客户订单或预测的较大者
MPS与MRP的区别与联系

MPS与MRP的区别和联系一、第一种解释MPS(主生产计划)MPS是产成品的计划表,描述一个特定的产成品的生产时间和生产数量,MPS是一个决定产成品生产排程及可承诺量/可销售签约量(ATP,Available To Promise)的程序。
依据MPS(主生产计划),MRP得以计算在该产成品需求之下,所有组件、零件乃至原材料的所需补充计算。
MPS不是销售预测,不代表需求。
MPS须考虑生产规划、预测、待交订单、关键材料、关键产能及管理目标和政策。
除了材料外,MPS也是其它制造资源的规划基础。
MRP(物料需求计划)MRP利用BOM(物料清单),将MPS运算结果中的产成品需求转换为半成品及原材料需求。
它利用库存状态如OH(在库量)及SR(在途量)等,以及材料主文件中的材料基本资料如LT及SS等,以及厂历,计算出何时需要多少何种材料。
MPS主要是围绕产成品展开生产计划表,MRP主要是依据材料展开采购工作。
根据公司的情况,大型的公司可以一周运行一次,先进行MPS,然后进行MRP,之间有一个时间差;对于小型企业,可以一天运行一次MPS及MRP,正规的MRP会考虑当前的所有变化,如库存、在途等,关键是要及时把变化信息录入ERP中:例如,前一次MRP分解后需要制造A产品100件,但因为某原因,实际只做了90件,就不做了,在ERP中要进行完工入库90件,然后把这个加工命令关闭。
在下一次运行MRP运算时,ERP系统会自动产生下一个制造10件A的任务。
因此,关键是数据的维护工作要及时,系统数据准确,ERP才会发挥作用。
1、MPS是MRP的直接目的,MPS体现的是净需求,MRP运算出来的作业计划和采购计划的目的就是完成MPS提出的任务,从而达到企业外部市场需求的目标2、MPS主要针对有独立需求计划而言,它是整个计划系统的调节器,在充分考虑企业粗能力和资源平衡的基础上平衡外部需求和企业供给能力.有些行业可以没有MPS,直接通过MRP来满足预测和订单的需要3、简单的说:MPS针对的是总装,MRP针对的是总装下的采购及零件4、如果从客户订单或预测过来的需求都需要计划部评估一下这个成品的交期和粗能力,在成品的评审没有完成之前下阶的材料都不允许产生相关需求,这个时候就对成品RUN MPS,当成品评审通过后再对它的一阶材料RUN MRP。
主生产计划详解

主生产计划作用与意义主生产计划在MRPⅡ系统中的位置是一个上下内外交叉的枢纽,地位十分重要。
在运行主生产计划时要相伴运行粗能力计划,只有经过按时段平衡了供应与需求后的主生产计划,才能作为下一个计划层次——物料需求计划的输入信息,主生产计划必须是现实可行的,需求量和需求时间都是符实的。
主生产计划编制和控制是否得当,在相当大的程度上关系到MRPⅡ系统的成败。
这也是它称为“主”生产计划的根本含义,就是因为它在MRPⅡ系统中起着“主控”的作用。
1.1 MPS编制原则●最少项目原则:用最少的项目数进行主生产计划的安排。
如果MPS中的项目数过多,就会使预测和管理都变得困难.因此,要根据不同的制造环境,选取产品结构不同的级,进行主生产计划的编制。
使得在产品结构这一级的制造和装配过程中,产品(或部件)选型的数目最少,以改进管理评审与控制。
●独立具体原则:只列出实际的、具体的可构造项目,而不是一些项目组或计划清单项目。
这些产品可分解成可识别的零件或组件。
●关键项目原则:列出对生产能力、财务指标或关键材料有重大影响的项目.对生产能力有重大影响的项目,是指那些对生产和装配过程起重大影响的项目。
如一些大批量项目,造成生产能力的瓶颈环节的项目或通过关键工作中心的项目。
对财务指标而言,指的是与公司的利润效益最为关键的项目。
如制造费用高,含有贵重部件,昂贵原材料,高费用的生产工艺或有特殊要求的部件项目。
也包括那些作为公司主要利润来源的,相对不贵的项目.而对于关键材料而言,是指那些提前期很长或供应厂商有限的项目。
● 全面代表原则:计划的项目应尽可能全面代表企业的生产产品。
MPS 应覆盖被该MPS 驱动的MRP 程序中尽可能多数组件,反映关于制造设施,特别是瓶颈资源或关键工作中心尽可能多的信息。
● 适当裕量原则:留有适当余地,并考虑预防性维修设备的时间.可把预防性维修作为一个项目安排在MPS 中,也可以按预防性维修的时间,减少工作中心的能力。
第五章、MRP II ERP原理与应用-主生产计划
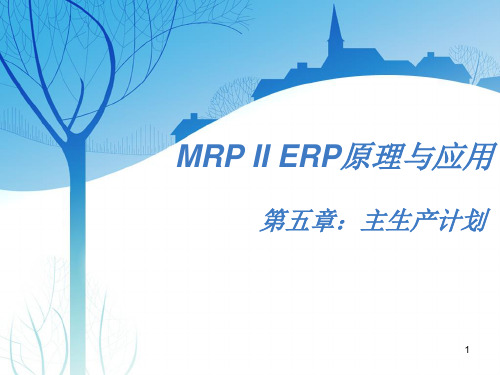
数据来源自销售管理子系统
表体:
系统运算后生成的中间信息
2
18
2.MPS报表——竖式报表
竖式报表对照的现实供给(订单下达状况)和需求(—综合主生产计划
时区 时段 18寸
21寸 25寸 29寸 34寸
需求时区 1 100 100 200 300 2 3 300
14
1.MPS的时间基准
(1)计划展望期 主生产计划的计划展望期一般为3~18个月;对于MPS, 计划展望期应至少等于总的累计提前期或多出3~6个月。 (2)时段 主生产计划的时段可以是按每天、每周、每月或每季 度来表示。当月的生产与装配计划一般是按周来编排, 并且常常按天表示。 时段越细,生产计划越详细。 (3)时界 主生产计划有需求时界和计划时界。 MPS把需求时界设定再最终装配计划的提前期,或者宽 裕一点。计划时界总是大于或等于需求时界的。
宏观计划
承上启下:将宏观 计划转换为微观计划
生产
编制主生产计划的主管计划员是一个极其重要的岗位 (熟悉市场、客户、产品、生产、能力资源)
6
销售
主生产计划 (MPS)
微观计划
2、MPS作用与意义
MPS的意义: 在年度生产规划量的框架下,预先充分考虑了合理的需求预 测量来参与排程,通过人工干预,均衡调节,保证了微观层面的 物料需求计划的均衡性和稳定性。 主计划把企业规划同日常的生产作业计划关联起来,为日常 作业的管理提供一个“控制把手”驱动了一体化的生产计划与库 存控制系统的运作。 经过按时段平衡了供应与需求后的主生产计划,可为物料需 求计划输入信息
200 300
200 200 200
100 200
100 100 100
主生产计划理论与作用
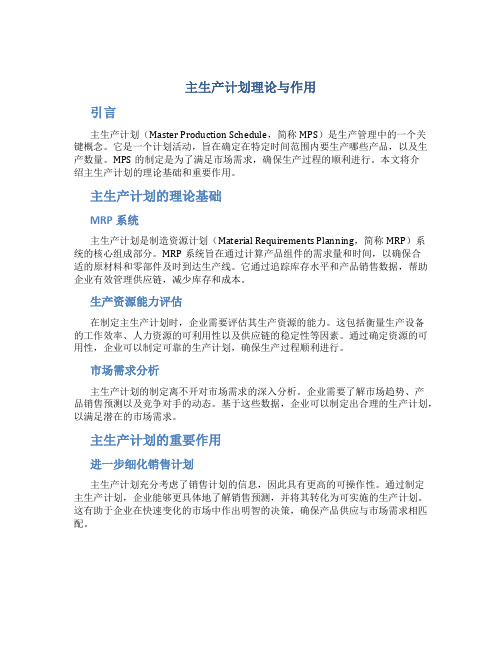
主生产计划理论与作用引言主生产计划(Master Production Schedule,简称MPS)是生产管理中的一个关键概念。
它是一个计划活动,旨在确定在特定时间范围内要生产哪些产品,以及生产数量。
MPS的制定是为了满足市场需求,确保生产过程的顺利进行。
本文将介绍主生产计划的理论基础和重要作用。
主生产计划的理论基础MRP系统主生产计划是制造资源计划(Material Requirements Planning,简称MRP)系统的核心组成部分。
MRP系统旨在通过计算产品组件的需求量和时间,以确保合适的原材料和零部件及时到达生产线。
它通过追踪库存水平和产品销售数据,帮助企业有效管理供应链,减少库存和成本。
生产资源能力评估在制定主生产计划时,企业需要评估其生产资源的能力。
这包括衡量生产设备的工作效率、人力资源的可利用性以及供应链的稳定性等因素。
通过确定资源的可用性,企业可以制定可靠的生产计划,确保生产过程顺利进行。
市场需求分析主生产计划的制定离不开对市场需求的深入分析。
企业需要了解市场趋势、产品销售预测以及竞争对手的动态。
基于这些数据,企业可以制定出合理的生产计划,以满足潜在的市场需求。
主生产计划的重要作用进一步细化销售计划主生产计划充分考虑了销售计划的信息,因此具有更高的可操作性。
通过制定主生产计划,企业能够更具体地了解销售预测,并将其转化为可实施的生产计划。
这有助于企业在快速变化的市场中作出明智的决策,确保产品供应与市场需求相匹配。
提高生产效率通过主生产计划,企业能够更好地组织和安排生产流程。
它可以帮助企业合理分配资源,避免生产过程中的瓶颈和延误。
此外,主生产计划还有助于减少库存和材料浪费,提高生产效率和利润率。
优化供应链管理主生产计划允许企业与供应链合作伙伴更好地协调和沟通。
通过主生产计划,供应商可以更准确地预测其原材料和零部件需求,并做好准备。
这有助于减少供应链中的延迟和错误,并提高整体供应链的效率和可靠性。
主生产计划

2004年3月9日星期二主生产计划Master Production Scheduling上海交通大学工业工程与管理系主要内容基本概念主生产计划计算逻辑主生产计划的评价和维护主生产计划定义主生产计划MPS是以总生产计划、需求预测和客户订单为输入,安排将来各周期中提供的产品种类和数量,将上层生产计划转化为产品计划,它是一个详细的进度计划。
MPS是对最终项目的需求日期(计划时段)和数量的说明。
主生产计划可以用来回答下列问题:(1)生产什么?——计划对象(2)生产多少?——需求量(3)何时生产?——提前期主生产计划的作用主生产计划是计划系统中的关键环节。
它将总生产计划转换成特定产品或特定产品部件的计划,是M R P的主要输入,它驱动M R P及后续的能力需求计划和车间作业计划。
对主生产计划的管理是M R P成功运行的关键。
主生产计划充分利用企业资源,协调生产与市场,实现生产计划大纲中所表达的企业经营计划目标。
主生产计划在三个计划模块中起“龙头”模块作用,它决定了后续所有计划及制造行为的目标APP和MPS的区别综合生产计划只对产品组进行划分,它不确定具体的物料项目。
其下一层是主生产计划。
主生产计划是分时段的计划。
它确定公司计划何时生产、生产多少各种产品。
主生产计划的汇总结果应当等同于总生产计划。
进一步的展开过程是MRP 程序。
APP和MPS的区别MPS计划对象主生产计划(MPS)的计划对象是把总生产计划中的产品进行具体化和系列化,通常称之为最终项目(end item)。
最终项目通常是独立需求件,但是由于销售环境不同,作为计划对象的最终项目其含义也不同。
主生产计划中的最终项目可以是产品、主要组件、虚拟物料单中的组件或者甚至可以是产品结构中最高层次上的单个零件。
时间区间和时间栏按照三级状态,MPS将定单分成三类:制造定单(Manufacturing orders)——冻结状态下达生产的定单,授权制造指定数量的产品确认的计划定单(Firm planned orders)——稳定状态计划定单的数量和时间可以固定下来,计算机不能自动地改变它们,只有计划员可以改变它们,确认计划定单是叙述主生产计划的常用方法计划定单(Planned orders)——灵活状态这些是可以改变的定单时间区间和时间栏时间栏时间区间1 时间区间2 时间区间3周号: 1 2 3 4 5 6 78 9 10 11型号:型号1 48 58 58 58 58 58 58 58型号2 40 50 50 50 50 50 50 50型号3 52 54 54 54 54 54 54 54型号4 82 84 84 84 84 84 84 84型号5 35 40 40 40 40 40 40 40周小计257 286 286 286 286 286 286 286DTF=需求时间栏时间区间和时间栏时间区间1——表明当前生产的制造定单,唯最高层管理人员授权修改时间区间2——表明已安排生产资源进行生产。
主生产计划定义与作用介绍
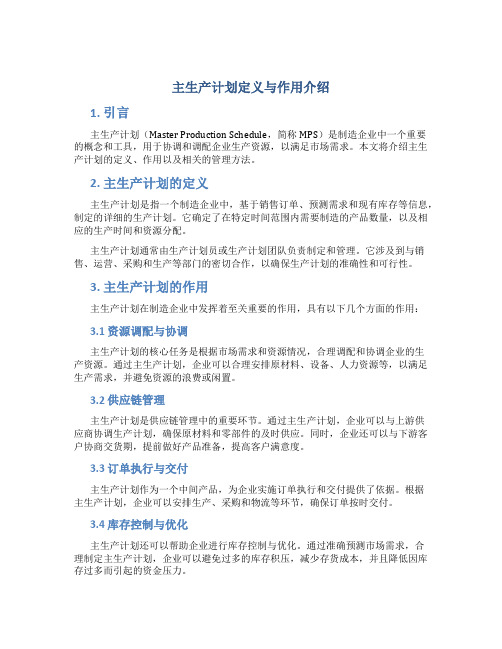
主生产计划定义与作用介绍1. 引言主生产计划(Master Production Schedule,简称MPS)是制造企业中一个重要的概念和工具,用于协调和调配企业生产资源,以满足市场需求。
本文将介绍主生产计划的定义、作用以及相关的管理方法。
2. 主生产计划的定义主生产计划是指一个制造企业中,基于销售订单、预测需求和现有库存等信息,制定的详细的生产计划。
它确定了在特定时间范围内需要制造的产品数量,以及相应的生产时间和资源分配。
主生产计划通常由生产计划员或生产计划团队负责制定和管理。
它涉及到与销售、运营、采购和生产等部门的密切合作,以确保生产计划的准确性和可行性。
3. 主生产计划的作用主生产计划在制造企业中发挥着至关重要的作用,具有以下几个方面的作用:3.1 资源调配与协调主生产计划的核心任务是根据市场需求和资源情况,合理调配和协调企业的生产资源。
通过主生产计划,企业可以合理安排原材料、设备、人力资源等,以满足生产需求,并避免资源的浪费或闲置。
3.2 供应链管理主生产计划是供应链管理中的重要环节。
通过主生产计划,企业可以与上游供应商协调生产计划,确保原材料和零部件的及时供应。
同时,企业还可以与下游客户协商交货期,提前做好产品准备,提高客户满意度。
3.3 订单执行与交付主生产计划作为一个中间产品,为企业实施订单执行和交付提供了依据。
根据主生产计划,企业可以安排生产、采购和物流等环节,确保订单按时交付。
3.4 库存控制与优化主生产计划还可以帮助企业进行库存控制与优化。
通过准确预测市场需求,合理制定主生产计划,企业可以避免过多的库存积压,减少存货成本,并且降低因库存过多而引起的资金压力。
3.5 生产效率与成本控制通过主生产计划,企业可以合理安排生产时间和资源,提高生产效率。
同时,主生产计划也可以帮助企业控制生产成本,避免生产过程中的浪费和损失。
4. 主生产计划的管理方法为了有效制定和管理主生产计划,企业可以采用以下几种管理方法:4.1 信息集成与共享主生产计划要基于大量的信息数据,包括销售订单、预测需求、库存情况等。
- 1、下载文档前请自行甄别文档内容的完整性,平台不提供额外的编辑、内容补充、找答案等附加服务。
- 2、"仅部分预览"的文档,不可在线预览部分如存在完整性等问题,可反馈申请退款(可完整预览的文档不适用该条件!)。
- 3、如文档侵犯您的权益,请联系客服反馈,我们会尽快为您处理(人工客服工作时间:9:00-18:30)。
1.主生产计划的功能以及其相关MRP类型参数2.MRP运行方式3.MRP运行的先决条件4.客制化MRP参数的优先级别5.MRP的运算逻辑及低阶码的用途6.SAP PP MD02界面参数说明7.mrp控制参数及未清期间8. SAP PP MRP视图中重要栏位的意义及功能作用主生产计划的功能以及其相关MRP类型参数主生产计划实际相当于一个计划调节器,用主生产计划可以合理的调节企业资源配置与需求的矛盾,避免由于需求不稳定造成的产品未能按期交货,产品积压,资源浪费、超负荷运转等现象,提高企业对用户的服务水平。
一般MPS的计划对象为最终产品或者关键重要部件,有时候也会对原材料做计划,比如造船行业。
原料品种比较少而产品品种比较多。
在SAP系统,和MPS相关的MRP类型有:M0 MPS,固定类型 -0-M1 MPS,固定方式 -1-M2 MPS,固定方式 -2-M3 MPS,固定方式 -3-M4 MPS,固定方式 -4-到后台去看这些参数的配置,发现只有确定的类型(Firming Tpyes)一个值不一样0 计划结果未被确认1 自动确定和订购建议被重新计划2 不含订购建议的自动确定3 手工确定和订单建议再计划4 手工确定不含订单建议为了弄清楚上面每个确定类型的含义,需要看下面的图:在时区1、2,某时刻到计划时界这个区间内计划订单是否被确定,新的需求的是否创建以及创建的落点在那个区间,由这个确定类型参数确定,下面是它的详细解释。
tpye0 :需求不自动确定,新的需求在需求日期创建,不会自动确定(计划时界内外都一样)。
tpye1 :需求自动确定,新的需求如果日期在计划时界内,那么在计划时界结束的位置创建需求。
type2 :需求自动确定,计划时界内的新需求不被考虑,缺料。
tpye3 :需求不自动确定,新的需求如果日期在计划时界内,那么在计划时界结束的位置创建需求。
tpye4 :需求不自动确定,计划世界内的新需求不被考虑,缺料。
PS:确定的需求,即不能再更改其数量。
MRP运行方式概括的说可以对两个组织层次执行计划运行:1、总的计划 2、单项计划·作为一个特定工厂的总计划运行。
在此,在一个工厂中与计划相关的所有物料被计划。
·作为一个特定物料的单项计划。
在此,计划运行为一个特定的物料在单层或者在多层中执行。
总计划运行的方式又可以细分为两种:A、前台运行 B、后台运行;单项计划又可以细分为单层多层等更为细致的计划,在单层计划中,系统仅计划所选物料的BOM层,在多层计划中,系统计划所选物料的层次加上所有较低的BOM层。
系统对应的路径为:后勤->生产->物料需求计划->计划->总计划->联机/作为后台作业(Logistics->Production->MRP->Planning->Total Planning->Online/As Backgroud)联机就是前台运行整体计划,事物代码为MD01,指程序在客户端运行,如果客户机死机则程序中断。
作为后台作业即是后台运行程序,事物代码为MDBT,程序在服务器端运行,客户端最终读取结果即可,不受客户端影响。
单项计划的路径:后勤->生产->物料需求计划->计划->单项多层/单项单层/单项交互/单项销售订单/单项项目(Logistics->Production->MRP->Planning->Single-ItemMulti-level/Single-Item Single-level/Single-Item Interactive/Single-Item Sales order/Single-Item Project)它们的事物码分别为:单项多层MD02 单项单层MD03 单项交互MD43 单项销售订单MD50 单项项目MD51MRP运行的先决条件对于工厂是否跑MRP取决两个条件:1、工厂MRP状态是否激活。
2、计划文件是否创建。
工厂MRP状态激活和计划文件创建可以通过路径SAP用户化实施指南->生产->物料需求计划->计划文件条目->激活MRP和建立计划相关文件(SAP Customizing ImplementationGuide->Production->Material Requirement Plannning->Planning File Entries->Activate MRP and Set Up Planning File)进入如下画面选择material requirements planning 勾选相应的工厂即激活此工厂MRP状态选择Set up planning file 创建计划文件,计划文件除了后台可以设置外,在MRP运行时选择处理码NEPUL,系统可自动创建计划文件。
对于物料是否跑MRP,取决于物料选择的MRP类型参数,以及物料的状态是否有效。
客制化MRP参数的优先级别MRP运行时数据读取顺序是首先读物料主数据的MPR参数,然后读取MRP组的参数,最后读取工厂参数。
通过这样一种有层次的架构,满足差异化的计划方法,以及方便数据维护。
MRP的运算逻辑及低阶码的用途一般MRP的运算逻辑为由最终产品的毛需求减去当前库存,得到净需求,由净需求、提前期、安全库存等信息推算出实际投产日期和实际数量(净需求);由本级物料的净需求及BOM结构的数量比关系计算出下一级物料的毛需求,再由毛需求和当前库存信息,计算得到净需求⋯⋯依次循环,直到不再有下层物料为止.但是这样一种逻辑当遇到共用件的时候会出现问题。
比如甲产品有组件A(1)、B(2)、C(1);乙产品有组件A(1)、D(2),D的组件为B如果甲和乙各有独立需求100,那么按照甲展开,B的毛需求应该为200,减去库存值50(假设),得到净需求为150;按照乙展开,假设D的毛需求等于净需求,那么可以计算出B的毛需求的为200,但是这个时候还需要再减去库存值50吗,很显然不应该减,但是按照上述逻辑可能计算出乙中B组件的净需求为150,那么总的净需求就为300,而实际的净需求应该是350。
为了避免这种错误在BOM存在共用件的时候发生,引入了阶层码和低阶码的概念。
从最终产品到原材料,给BOM结构的每一个层次分配一个阶层码,MRP运算的顺序为上图箭头顺序,当物料阶层码为最低的时候,再累加毛需求,计算净需求。
比如物料B有两个阶层码,当运算到阶层码002,B的最低阶层码时,累加毛需求再计算净需求。
运算过程如下表:只有当物料的阶层码为最低阶层码的时候,系统才扣除当前库存,计算物料的净需求。
PS:为了避免人为分配错误导致MRP运算无法运行,阶层码由SAP系统在创建BOM时自动检索分配,数位为3位,所以BOM的最高层次也只能为999层。
SAP PP MD02界面参数说明处理代码:NETCH -净变化计划,即只计划上次计划以后计划相关内容发生变动的物料(注意,某些物料的参数发生变动了,系统也认为计划内容没有发生变动)。
NETPL –计划周期内的净变化计划,即只在计划周期内执行净变化计划,周期外将不进行计划。
跟mrp相关的变化在planing horizon中,即由物料主档的MRP1视图的计划的时界,超出计划时界的将不进行计划。
NEUPL –重新计划,所有的物料不管有没有变动都再次计划。
只要速度可以,建议每次都选NEUPL(注意某些单项计划不能选择NEUPL),其次选NETCH。
说明情况:有的物料在用MD01时的NETCH的物料计划单不会重新产生那是因为NETCH只运算物料计划发生变化了的物料,因此要用MD01让所有物料的计划单重新产生,一定要用参数NEUPL;而用MD02时的NETCH 会重新产生物料计划单。
创建采购申请:1-计划结果直接生成采购申请;2-只在未清期间内生成采购申请,未清期间外生成计划订单;3-全部生成计划订单;交货计划表:如果MM模块启用了计划行,则MRP运行的结果如下处理:1-不生成计划行;2-只有在未清期间内生成计划行; 3 –全部生成计划行;创建MRP清单:设置MRP运算是否更新MRP清单;1-不生成/更新;2-根据例外信息决定;3-全部更新/生成MRP清单;计划模式:1-不清空原先的计划订单;2-不清空,但是要重新展开他们的Bom和工艺路线(即按照最新的Bom和工艺路线计划);3-全部清空未确认的计划订单,重新生成。
调度:1-按物料主数据的提前期进行排产;2- 按工艺路线进行排产;这是运算MRP时的参数选择描述,在创建采购申请项目中选择1就可以了,不用到后台.Ps: 未清期间:简单的说就是为计划员提供了一个提前处理的缓冲期。
在逆推排产的逻辑下,比如MRP创建的计划订单开始日期是5日,未清期间是3天,那么假如当前日期是1日,就还没有进入未清期间,此时计划员就没必要这么早处理计划订单,而如果当前日期是3日,就在未清期间里了,此时在MD04中会有一个例外消息05产生,用来提示计划员可以去将这张计划订单转换成生产订单或者采购申请了,这样就可以给计划员充分的时间来处理订单。
如果没有未清期间,直到5日都不会有任何提醒,到时候再来处理就有可能来不及了。
mrp控制参数及未清期间MRP Control Parameters & Opening Period——–mrp控制参数及未清期间经常有人对MRP/MPS运行界面上的参数选择迷糊, 特整理说明如下.Processing key :NETCH (净变化计划):即只计划上次计划以后计划相关内容发生变动的物料(注意,某些物料的参数发生变动了,系统也认为计划内容没有发生变动)NETPL(计划周期内的净变化计划):即只在计划周期内执行净变化计划,周期外将不进行计划.NEUPL(重新计划)所有的物料不管有没有变动都再次计划. 如果没有Performance的考量,建议每次都选NEUPL(注意某些单项计划不能选择NEUPL),其次选NETCH.Create Purchase req.(创建采购申请):1:计划结果直接生成采购申请(PR);2:只在未清期间内生成采购申请(PR),未清期间外生成计划订单(Planned Order);3:全部生成计划订单(Planned Order).Delivery Schedule(交货计划表):如果MM模块启用了计划行(Schedule Line),则MRP结果如下处理: 1:不生成计划行(Schedule Line);2:只有在未清期间内生成计划行(Schedule Line);3:全部生成计划行(Schedule Line);Create MRP List(创建MRP清单):设置MRP运算是否更新MRP清单(MRP List):1:不生成/更新2:根据例外信息决定3:全部更新/生成MRP清单(MRP List)Planning Mode(计划模式):1:不清空原先的计划订单(Planned Order);2:不清空,但是要重新展开他们的BOM和Routing(即按照最新的BOM和Routing);3:全部清空未确认的计划订单(Planned Order),重新生成.Scheduling(调度):1:按物料主数据的提前期(Lead Time)进行排产2:按工艺路线(Routing)进行排产==================================================上面有提到Opening Period(未清期间) , 所以就再转个帖子说明.跑MRP的时候,就“创建采购申请”有三种选择,1全为采购申请,2未清期间的采购申请,3全为计划订单.“未清期间”在“计划边际码”中设定(Sched Margin key, IMG:Production -> MRP -> Plan -> 计划和生产参数 -> 定义浮点),其解释为:The number of working days between the date that the order is created and the planned start date. This time is available for the MRP controller to convert a planned order into a purchase requisition or a production order.也就是计划订单转采购申请/生产订单的提前时间.以下是个例子,今天是2006/06/13,物料A的需求日期2006/07/02,计划交货时间12天,收货处理时间1天.当未清期间设为5天的时候,如图:注意到订单收货开始日期到完成日期,共12天(不含本日).计划转换日期2006/06/14,正好跟订单开始日期相隔5天(也不含本日),这就是“未清期间”.如果未清期间设为6天,由于计划转换日期为当天(或者说运行MRP的日期,落在计划订单的未清期间内),因此计划订单已经自动转化为采购申请.未清期间的作用在于:在计划和采购申请/生产订单间提供一个缓冲的时间.这跟下达时间作用相仿,因此它们都在计划边际码中维护.计划员可以对落在未清期间的计划订单进行批量转换(MD15/CO41)SAP PP MRP视图中重要栏位的意义及功能作用1.MRP4视图中的独立/集中:1--独立,就是已经制定成本分配对象的,尤其是挂靠在销售订单上的,如果是make-to-order。