五原则表填写实例
五原则分析表(模板)

确认
部品确认结果:
序 项目 号
1 2 3 4 5 6 7
生产品质状况:
改进措施 备注
要因分析: 完成数量 未完成原因
设备
法 异常问题长
序号 1 2 3
日期
人 番号 项目 1 2 3 4 人 设备 环境 材料 方法
料 要因分析
环 判定
五W综合分析、确认: 5
总结:
3.查明的原因(发生现象、在检现象、分析原因)
ppt模板简历模板个人简历模板名片模板ae模板简历模板下载ppt模板下载网站模板四项基本原则swot分析
题目 编号 部品名 1.发生状况(时间、地点、涉及不良、现象描述、
解决问题的五原则表
2.把握的事实(部品确认、要因分析、生产品质状况等,根据需要更改)
作 成 部 门
年 承认
月
日 确认 作成
报课 告 责任者 书
4.切实的对策(对策内容 1.发生对策:
预测效果PPA) 推进者
日期
5.确认对策效果(效果
实绩)
2.流出对策:
体系: 体系:系统的反映内容
区
分
现象说明
问题1
问题2
问题3
问题4
问题5
内 容
发生不良 流出不良
问题解决5原则表的作成和运用指南

■不良现象的要因调查
・「什么时间、在哪个工序、发生了 什么?」
⇒锁定对象工程和对象批量 ・一般的记入内容
・工程的确认 ・每次确认的时候有无引起相关 不良的可能性 ・工程调查结果
工程履历、数据、作业记录 调查作业者的结果
5原则表的作成 (2)原因の究明
实施2种原因的究明!
別紙デ-タ10参照
○:マツダ様にて確認結果、 接点部導通しっぱなしなし
○:メカでの強制 O FF構造であ
接点溶着
り接点溶着なし
別紙デ-タ11参照
組み付け手順 間違い
○:マツダ様にて確認結果、 組付け手順に問題なし
スイッチ内部ズレ
バネ 不良
×:現象確認
別紙デ-タ3,4参照
下ケース
摺動体
接点
ランプ 接点組成
第2阶段 <对象扩大>
出荷
顾客
顾客索赔
必须! 第1阶段
5原则表的作成运用要点
①首先要优先于开始活动! 不要对策后才报告 ⇒中途经过也可以要向顾客迅速报告!
②不能只有QC担当者作成! 由主要因部门作成、QC协助、承认是基本的途径。 ⇒若是生产的要因那就是制造、设计的要因是技术… 当然要用CFT作成讨论
通过对问题进行4个合理的思考过程分析,从而得出正确的结论。
自然人的思考过程=从以下4个角度进行反复提问,对其结论进行持续考虑。 ①什么课题?(WHAT) ②为什么会那样?(WHY) ③怎样入手解决?(HOW) ④若什么的话会不会引起什么?(IF)
◎状况把握过程(略称SA=Situation Appraisal) 引起什么?→课题是什么?
要点:「目前的处置怎么办?」 首先要检讨不能扩大顾客困惑的处置方法。
五项原则报告解析2.7
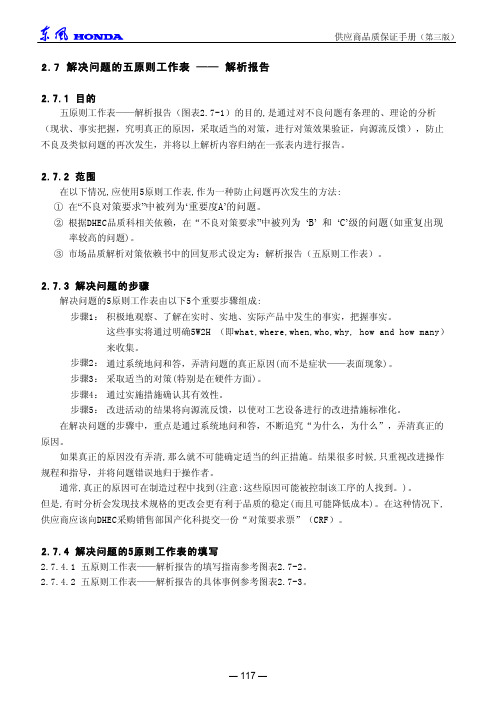
保存期限: 年
供应商品质保证手册(第三版) 图表2.7-3
— 120 —
主题 零件号 零件名
止瓦槽(切槽)位置反向加工
1112*-P**-O***
No.1主轴承盖
具体事例
五原则工作表〔解 析 报 告〕
管理NO: 20041129-001
编
***** 有限公司
2004年12月10日
【目标】 1.证明品质、成本、日程都是最合适的,以防止出现的情 况再次发生。
【填写内容】 1.引起问题零件/部位的硬件(设备、夹工具等)的恒久对策, 以及对策日程、责任人。 2.防止问题零件/部位流出的硬件(QA机、防止错误装置等)的 恒久对策,以及对策日程、责任人。 3.维持上述内容的FMEA、QA矩阵表、作业标准等的对策内容 和管理实施日程和责任人。 4.其它采取对策的机号和机型。 5.出货件的处理判断(预见性、发生的预测和条件、零件和
编制部门的名称
⑦由编制部门的相关人员签
【目的】 1.下次行动时锁定目标。 2.真实填写发生的原因和状况,以便使不良零部件、部位 更清晰
【填写内容】 1.机种、机型 2.车身号码、发动机号码、批号。 3.发生地点。 4.发生年月日。 5.(发生后在销售店)登记年月日。 6.行使路程/时间。 7.事象内容。 8.处置方法和结果。 ※注:上述以外如果有必要的信息请记录。
Ⅴ . 向 源 流 的 反 馈 (反映在体制・组织上的内容)
为什么 ·为什么分析
步骤
1
2
3
4
5
内 发生
容 流出
EQ F1701 M01 D02
保存期限: 年
供应商品质保证手册(第三版) 图表2.7-2
三现五原则-品保部
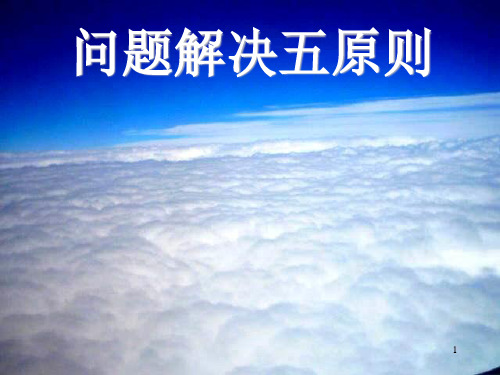
发现单位确认 签核
核准
审核
发现人
核准
责任单位确认 审核
负责人
核准
品质单位确认 稽核
确认
备注
保存年限:5年
17
版本: 2014.03.23 第5版
测试题: 1.三现五原则指哪三现、哪五原则? 2.用三现五原则分析对策时应注意那些问题?
3.制定适当的对策时应注意哪些方面?
4.再现性试验有哪几种方法,分别如何进行? 5.案例分析:结合实际工作中的某一问题点,采用三现五原则 的方法进行分析。
11
八、解析对策应依据三现(现物、现场、现状)
疑问点:有至现场去看吗?是否实车确认、实物、实地确认? 说明: 1.未三现,可能会得到错误的讯息,或疏略重点信息。 2.选择性事实:三现的目的,在于针对问题,全盘掌握事实,
而未三现,可能仅知道部份事实。
3.有三现,才能相信自己,说服别人。
解析对策必须遵守三现主义
13
十、解析对策应五层分析内容连贯
意义:五层分析是一个形容词,代表追根究底的意思,其目
的在寻找真正的原因,并不是一次要作五次为什么分 析,可以比五次少,也可以比五次多。 实例:不良现象:踩剎车时BrakePedal有上、下作动感觉
1 為什 麼之 Drum 內徑黑 五層 皮產生 分析 2 3 4 5 無檢查基準 目視檢查時 鑄造時 Drum 未檢查 加熱變形 Drum 內徑 模具與 Drum 尺寸 NG 間隙過大
4
一、解析对策应有科学的数据依据
疑问点:常发生的直觉判断 1.焊接强度不足→对策:焊道加长2mm,正确吗?
2.模温不足变形→对策:模温提高10℃,没问题吗?
思考:加长2mm、提高10℃如何得到的? 直觉+经验≠事实 100个直觉或经验不如1个数据 分析方法: 1.科学的根据=实验数据 2.有实验的数据才能决定新的标准 3.要去试验出焊道加长2mm及模温提高10℃是最好的条 件作业。
广本5原则培训资料

☆集体创造性思考 ☆特性要因图
• 调查结果总结、变化点和推断原因总结
4、现在的対応状况(緊急処置後的)
• 用X-R管理图 、矩形图、CP值等
可以说问题一定源于变化点(人、物、设备等,4M1E)
1、老七种工具: 调查表 分层法 排列图 因果图 直方图 控制图 散布图 2、新七种工具 亲和图 树图 关联图 矩阵图 箭条图 PDPC法(过程决策程序图法) 矩阵数据分析法
・可用于解决开发、生产、销售、供应、管理等 所有领域发生的问题。
来自顾客的意见、投诉产品、服务不好 设备、机械、机器的问题 精确度与效率不高的工作
解决问题、防止再发
五原则工作表
重要度的决定及处置判断
• 重要度、麻烦度、重要保安部品判断
零件品质科
重要度
麻烦度
重要保安部品
A 不良时判断为危害人身安 A 已进行整车的检测、修理 HS
17 240±5 +7 +8 +9
P21
10 270 SET SET SET
(工序概要) No 工程名 1 来料仓库 2 端末加工 3 弯管加工 4 最終検査 5 出荷
加工機種名 起因 西岛端末加工机 T型弯管机 ★ -
*根据现品确认,弯管形状有同样倾向
■ 5原则工作表(解析报告)
是指从发生问题的初期对应到彻底解决问题,防止再发的问题解 决手法。是本田特有的问题解决手法。
目的:通过对不良问题进行有条理的、理论性的分析(三现主 义) ,查找真正的原因,采取适当的对策,防止问题再发。
・解析报告要将解决问题流程的结果用1张纸(A3)总结后进行报告。
■ 使用范围
集、整理)
• 工序中现正生产的零部件的品质状况、良品批次确认(根据X-R管理图、工程
三现五原则表
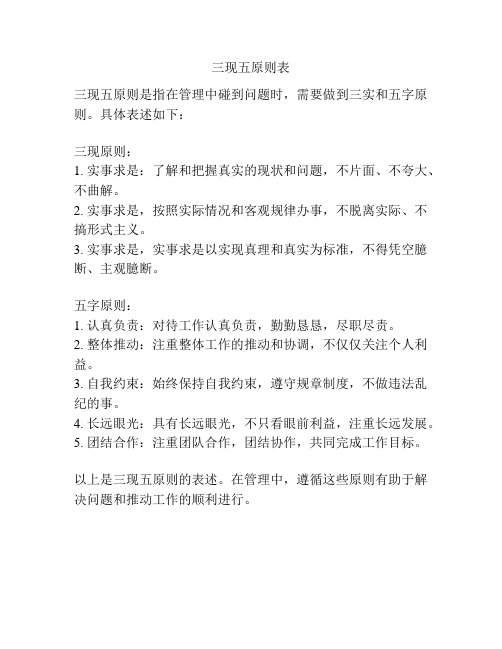
三现五原则表
三现五原则是指在管理中碰到问题时,需要做到三实和五字原则。
具体表述如下:
三现原则:
1. 实事求是:了解和把握真实的现状和问题,不片面、不夸大、不曲解。
2. 实事求是,按照实际情况和客观规律办事,不脱离实际、不搞形式主义。
3. 实事求是,实事求是以实现真理和真实为标准,不得凭空臆断、主观臆断。
五字原则:
1. 认真负责:对待工作认真负责,勤勤恳恳,尽职尽责。
2. 整体推动:注重整体工作的推动和协调,不仅仅关注个人利益。
3. 自我约束:始终保持自我约束,遵守规章制度,不做违法乱纪的事。
4. 长远眼光:具有长远眼光,不只看眼前利益,注重长远发展。
5. 团结合作:注重团队合作,团结协作,共同完成工作目标。
以上是三现五原则的表述。
在管理中,遵循这些原则有助于解决问题和推动工作的顺利进行。
质量五原则表

发放至:就如下的零部件/产品/货物出现的质量问题通知贵单位,请按 5个为什么分析表调查产生不良的原因并填写本表的2-4项。
1.问题的情况和紧急处置方法※3.发生原因调查和对策1.1 问题的描述发生日期: 年 月 日2011.04.20发现地点:□进货检验 □本公司生产线 □中间库 ■顾客生产线 □市场抱怨 □其他( )车型/系统号: 长城/TZ0905 零件名称 / 图号:●进货时间:●不良品生产日期:11.3.24/11.1.28各一件●批号:C0202011-1103240089/C0202011-110128034●检查数:●不良数:2●不良率:发放部门: 1.2 紧急(临时)处置方法(包括实施部门/人员、实施方法<检查/挑选/其它>、完成日期)在库品100%检查,对发现的不良品全部更换或修理。
QM 保留原始记录2-1不良品的调查※5.对策有效性的确认1、上海奉天现有库存398PCS ,经100%开盖检查,合格率100%; 2、天津三电库存2000件,正在复查中;防错:无标准化:有2-2 过程的调查(实际规定)/原因分析6.1 展开应用2-3 其它6.2 标准化防错:有/无标准化:有/无QSR-34-05/09保存部门/保存期:品质管理部门/10年1.因焊锡未完全搭在引脚上,也就是MOS管引脚未完全短路,工序检验和成品检测无法检出;2.生产部工艺更改没有进行相关部门评审和工艺有效性验证;3.对焊点的自检要求不明确。
QM 部门部长担当科长实际实际期限担当科长部长品质异常联络书主题:TZ0905调速模块不能调速管理编号:QM110422-01对策内容认可焊接温度过高、焊接时间过长、上锡过多使多余的焊锡搭在MOS管G、D引脚间导致MOS 引脚出现间隙性短路。
问题对策调速模块/C1540-40090原因对策不合格内容描述:4月20日接到天津三电电话投诉,在长城汽车厂出现2件TZ0905调速模块不调速。
解决问题的五原则
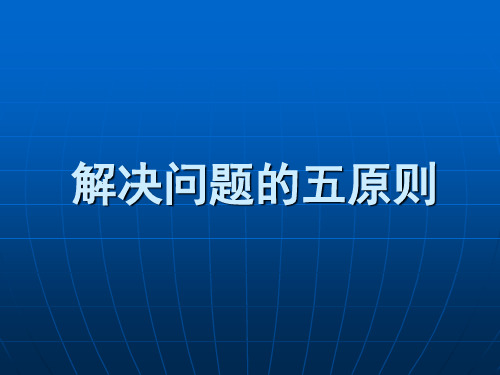
写好五原则表的关键:运用五原则手法分析、解决问题
五原则表的表达要求
要用简单、具体、准确的表述语言填写事实,不要 使用抽象性、否定性(确实、正确、避免、不要、 可能等)的语言。 要求插入示意图、照片、路线图、表格等,这样, 在传递过程时,就可以使你表达的意思和阅读的人 理解内容的一致。 ①.尽量使用短句写 ②.用小学六年的孩子能理解的话写
解决问题的五原则
五原则的定义
“五原则”是指从“三现主义”出发,分五个步骤解决问题
充分把握事实 查明的真正原因 实施切实的对策 确认对策的有效性 反馈到问题的源头
1
五 个 步 骤
2
3 4 5
三现主义
不但适用于制 造现场,也适 用于广泛的其 它工作。
亲自接触实物
亲自到现场
(现物)
总是以事 实为基础 而行动
异常对应难以预测的现象: 临时调休 突发的产品质量问题 突发的设备故障 到货材料、零件异常 停电、地震、洪灾、台风等
工厂是避免不了变化 点的,问题是对变化 点有没有制定正确的 对应方法
三、充分把握事实—2
<要因变化点的确定>
4M变化点
人 变化点的具体事例
(批次追踪及变化点调查)
对预测的变化点,没有进行 正确的管控时也会发生问题
③.用小学六年之前学过的汉字写
④.尽量不要使用专业性很强的文字和西洋文字 (英 、日文)写
五原则表填写要领
01.标题
发生状况 现状把握
02.发生状况
1-1 不良品确认 结果
合适 的 对 策
1-2 批次跟踪 变化点调查
1-3 原因分析
查 明的原 因
检查对 策 的效 果
2-1.查明的原因 发生机理 再现试验
5原则表填写说明

作业要领书的修改
□要 □否
条件表的修改 其他
□要 □否 □要 □否
18/23
19/23
通过对标准类(QC工程图、检查基准书、作业指示书)的 完善,明确再发防止策、对策实施效果的继续・维持方法。 ①判断需要对哪些文书进行修改。
作业标准类:PQC、检查基准书、作业指导书、包装 类指导书、作业要领书,条件表等
①取得正确的事实. ②针对发生及流出原因,用分析图明确表示 ③明确不具合发生基本原因. ④反复为什么为什么找到真正发生的原因. (更进一步使用春风分析图分析原因) ⑤进行适当对策并实施. ⑥反映到标准类、体系中. ⑦确认效果及数值.
1 3
6/23
2
5 4
6
1.发生状况(现实)
7/23
①.现象·投诉内容
□要 □否
担当
纳期
检查基准书的修改
□要 □否
作业指导书的修改 手顺书的修改
□要 □否 □要 □否
PIR记录项目变更
□要 □否
日常/定期点检项目变更
□要 □否
保养项目变更 异常处理方法变更
□要 □否 □要 □否
图面(治工具/金型/制品)的修改 □要 □否
FMEA的修改 包装类指导书的修改
□要 □否 □要 □否
发 生
内
容
流 出
探明原因[采用系统图法进行分析。] 从各个角度反复重复为什么为什么,抓住根本性真 正原因明确填写认为是最受影响的项目。
现象
为何发生
为什么
为什么
为何流出
为什么
为什么 为什么
为什么 为什么 为什么 为什么
为什么 为什么 为什么 为什么 为什么 为什么 为什么 为什么
解决问题的五原则分析

解决问题的五原则
五 原 则 的 定 义
“五原则”是指从“三现主义”(现场、现物、现 实)出发,分五个步骤解决问题。
2
1
充分掌握事实情况
2 查明真正的原因
五个步骤是:
4
3 实施切实的对策 确认所采取的对策是否有效
5 反馈到发生问题的源流
三现主义的定义
不但适用于制造现场,也适用 于广泛的其它工作 。
五原则的填写说明-Байду номын сангаас
8
事 实 的 把 握(部品的确认结果、原因分析、生产品的品质状况)
目标 1、为探明部品、部位的原因; 2、变化(工序与用户的使用方法)产生不良, 为了一针见血找到变化和限定批次。 见下页
五原则的填写说明-
填入内容:
9
事 实 的 把 握(部品的确认结果、原因分析、生产品的品质状况)
◆等待生产现场的联系或生产现场对于技术、品质、资材等部门服务、指导、指示、供应的等待。等待下级 的汇报,任务虽已布置,但是没有检查,没有监督。不主动去深入实际调查研究,掌握第一手资料,只是被动 地听下级的汇报,没有核实,然后作决定或向上级汇报,瞒天过海没有可信度,出了问题,责任往下级身上 一推。“三现主义”的缺乏是等待中的最致命原因之一,严重影响生产现场工作的及时解决。
三现主义在中国用得很早:远点,“捉贼捉脏, 捉奸捉双”;近点,毛主席的“没有调查研究 就没有发言权”;再近点,;新闻工作者不也是 天天在掌握第一手材料么?谁和谁有拍拖之 嫌呀,哪个和哪个出现在某酒店啊,这都是三 现主义的运用,可是中国的三现主义只用于 政治或只用于整人,很少用于品质管理。
三现主义的定义
①不良品 制造工序条件 ②不良品 制造年月日 ③不良品 发生个数、概率 …等,用工序系列、时间系列整理。
三现五原则与8D
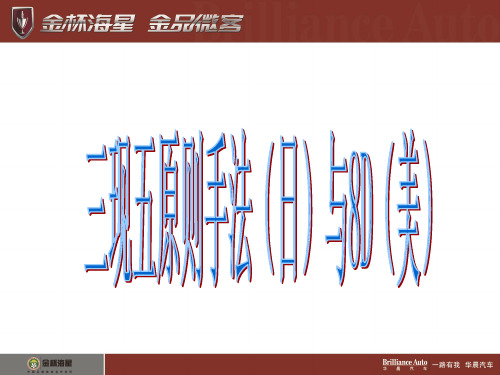
把握现况
5、利用绘图、图表、柱状图使问
题明确化。 6、将可能想到的原因、内容,详 尽的进行整理,在记录上明确 的记载。 7、在特性要因图中,将所有的要 因全部记入。
4M分析 5W分析法 查明原因 特性要因图 查明原因 再现试验 不良原因 查明原因 问题 要因 真因 流出原因 (流出面) NG再现 OK再现 不良再现 (制造面)
十:五层分析
意义:为什么--五层分析是一个形容词, 代表追根究底的意思,其目的在 寻求真正的原因,并不是一次要 作五次为什么分析,可以比五次 少,也可以比五次多,只要能寻 求出真正的原因。
十:五层分析
实例说明: 不良现象:踩刹车时Brake Pedal有上、下作 动感觉。
1 2 3 4 无检查基准 铸造时Drum 加热变形 模具与Drum 间隙过大 5 温度过高加 热不均匀 (500↑℃) 模具磨损 6 无温度 控制 (180200℃) 无标准 规定 目视检查 为什 Drum内 未检查 么之 径黑皮 Drum内径 五层 产生 尺寸NG 分析
查明原因
Q&A 、WHY WHY分析 1、通过WHY、WHY的反复5次进行分析找 出真因。 2、WHY、WHY的疑问必须使之与问题现 象相关联,建立系统来进行。
五原则表(内部培训081113)
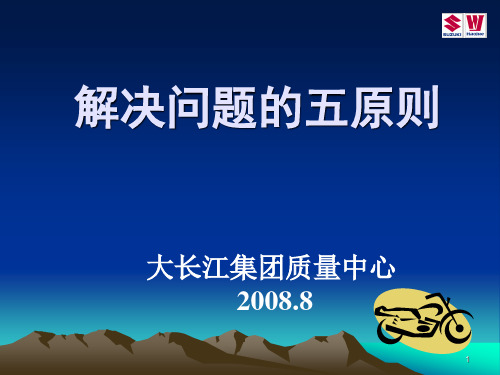
写好五原则表的关键:运用五原则手法分析、 写好五原则表的关键:运用五原则手法分析、解决问题
5
五原则表填写要领
01.标题 标题
发生状况 现状把握
02.发生状况 发生状况
1-1 不良品确认 结果
合适 的 对 策
1-2 批次跟踪 化点、 变化点、 异常点调查
1-3 原因分析
查 明原 因
检查对 策 效 果
其三 问题如果提出来了 决不能说: 决不能说: “这是不可能的”
其四 再现试验成功的 重要的因素是 现场的真实的数据』 『现场的真实的数据』和 决不能放弃的执着』 『决不能放弃的执着』
8
1
充分把握事实
五 个 步 骤
3 4 5
2
2 实 实
三现主义
不但适用于制 造现场, 造现场,也适 用于广泛的其 它工作。 它工作。
亲自接触实物
亲自到现场
(现物) 现物)
总是以事 实为基础 而行动
(现场) 现场)
亲自了解实际情况
(现实) 现实)
3
三现主义
• 现场:不要只坐在办公室决定,而是要立即赶 现场:不要只坐在办公室决定,
到现场。现场每天都在变化, 到现场。现场每天都在变化,不具备正确的观察 方法,你就没法感觉它的变化,包括异常。 方法,你就没法感觉它的变化,包括异常。
• 现物:不能脱离实物凭空推测,只有仔细接触 现物:不能脱离实物凭空推测,
实物并客观地观察其过程,掌握第一手资料( 实物并客观地观察其过程,掌握第一手资料(包 括人的因素),才能找到隐藏的原因。 ),才能找到隐藏的原因 括人的因素),才能找到隐藏的原因。
• 现实:解决问题需要你面对现实,把握事实真 现实:解决问题需要你面对现实,
五原则工作表〔EPB杯托橡胶垫混装异常〕2017-4-27
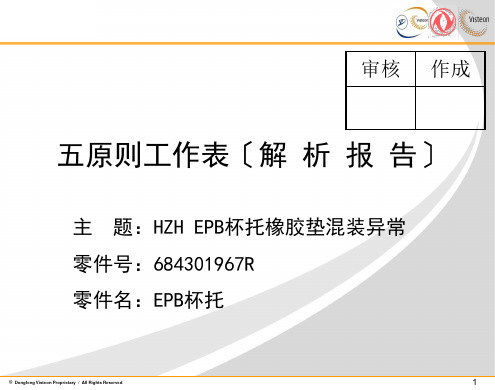
13
© Dongfeng Visteon Proprietary / All Rights Reserved
14
2、要因分析及检证结果
4M
人 机 料
判断 有:× 可能:△ 无:○
管理项目
操作工技能 设备运行
管理基准
熟练操作 设备无异常
检证结果
操作工技能满足要求 注塑机无维修记录 新零件号EPB杯托橡 胶垫一边混装了旧材 料橡胶垫 作业指导书和检验指 导书书中并未定义此 处要求
可能性
○ ○
来料
来料合格
用手进行触摸检查 橡胶垫硬度
© Dongfeng Visteon Proprietary / All Rights Reserved
10
Ⅲ.适当的对策(对策内容・效果预测・PPA) 2、流出原因对策 (1)现GP12检验站现场悬挂质量警示卡,检验员对EPB杯托产品进行全检, 重点检验两边橡胶垫的软硬度,及时识别出新旧材料,避免材料混用,混 装。
×
×
法
检查方法 新旧材料的橡胶垫 避免混用
橡胶垫新旧材料无法 进行单体识别,且新 旧材料产品放置区域 未进行定置区分
×
© Dongfeng Visteon Proprietary / All 确认结果・要因分析・生产品的品质状况)
发生工序
注塑制程
发生工序
组装线
成品检查
流出工序
包装、入库
交付客户
© Dongfeng Visteon Proprietary / All Rights Reserved
7
Ⅱ.原因的究明(发生的途径、再现测试、为什么・为什么分析)
1、 原因分析
步骤 1 2 3 4
【20140104】广汽本田五原则工作表记入要领3

把握事实查明原因(采取)适当的对策确认(对策)效果对(问题)源头的反馈以下是广州本田(1998年)版5原则表的精粹·对于解决问题5原则表,各位同事需要理解以下的事项.5原则需按顺序可以记录.了解5原则各程序的目的.了解应该由谁使用5原则表.了解应该在何时使用5原则表·创立解决问题5原则表的目的.在广州本田内,使解决问题的方法标准化.使为解决问题所进行的全部活动,都能汇总成"キ干'总结到1页纸上.根据上面所做的工作,可以容易地了解到按各步骤所采取的行动有无遗漏.可以容易地评价针对每一步所采取的行动是否是最妥切的.将为解决问题所开展的活动内容作为技术诀窍记录下来,不断地积累技术经验.减少问题再次发生的次数·谁来使用5原则表.所有的广州本田员工都需要了解5原则表,要作到全体人员都能使用·应该在何时使用5原则表.在问题发生的真正原因不明确的时候.为了查明问题发生原因需要进行解析的时候.特别是在问题再一次发生时,一定要使用5原则表的各个流程.<广州本田版5原则表的展开步骤和内容>如果发生了问题,将问题(题目)记入,按照5条原则进行展开5原则1·(发生状况 1-A)·使用5W2H法收集尽可能多的信息..5W: (WHO)谁(什么)-,类型,种类,受影响的部分等(WHAT)什么-问题的症状,尽可能地使用图表等工具将问题表达清楚.(WHEN)何时-记入问题发生的日期(WHERE)何地-记入问题发生的场所(WHY)为什么-具体的内容.2H: (HOW)怎么样-(问题)是怎么样被发现的(HOW MANY)什么程度-(问题)发生的量、程度.问题点的概要(信息的收集、整理) 例如:针对部品或是工程.问题再现试验的结果.现行品的品质状况.发生的对象范围.利用绘图、图表、柱状图使问题明确化·集体创造性思考 1-C.将可能想得到的原因在集体创造性思考会上全部阐述、总结出来.而后将上面的内容尽可能地进行整理,在别的栏里明确地记入·特性要素图 1-D.在特性要素图中,将所有的要素全部记入.为了查找到真正的原因,作为一种工具要尽可能地使用特性要素图5原则2 查明原因、验证·Q&A (WHY WHY分析 2-A).通过WHY WHY的反覆(=)5次进行分析来找出真正的原因.WHY WHY的疑问必须使之与问题现象带关联性、建立起系统来进行.WHY WHY的分析要从问题的发生原因(或者叫硬件方面的原因)和流出原因(又叫软件方面原因)两方面来进行.WHY WHY分析的信息来源,基本上是以特性要素图为基础·<查明原因、验证、总结 2-B>.找到了真正的原因,要将连同可以证实它的内容一起记载在这里.还有,为了说明真正的原因,可以加入插图5原则3 (采取)适当的对策.(针对发生的问题)采取暂定对策与恒久对策.还需要发生对策、流出对策(或叫硬件对策、软件对策).因为可能由对策带来新的问题,需要对这些潜在的问题进行分析(P.P.A)、评价(预测).查明可能会演变成问题的潜在的要素.制订作为预防手段的计划5原则4 确认(对策)效果.对于实行的对策、实施追踪.在为确认效果进行检查时,取样数量可参考实际问题发生率、数据方面可以灵活使用统计手法5原则5 对(问题)向前反馈和向后反馈.针对类似的工程、相似的问题可以采取同样的修正对策.为了更好地实施对策内容和遏制住不良的发生,需要将对策内容落实到组织和管理体制中5原则表 使用特性要素图的目的和好处(要素分析在广州本田版查明原因这一工作中始终作为一项重要手段)重要点是使用特性要素图完整地实施Q&A之所以如此,是因为Q&A在5原则中起着关键作用,在这里大家需要了解作为主要工具的特性要素图的使用方法.我们在进行Q&A时,最重要是提出正确的问题.如果错误地提问,就会得出错误的答案,这时就不能抓住真正的原因在进行Q&A时经验会成为帮助,而最重要的还是理解Q&A的做法.即使是经验少的人,如果能正确实行Q&A,也能够发现真的原因使用特性要素图的好处.对于已完成的5原则表,(使用者)本人自不用说,评价者或者是第三者在看这个表的时候,以下的事情就容易明白.知道遗漏和不恰当的项目.Q&A的每一步的内容可以进行评价.在特性要素图中被列举出来的众多要素与特性有无关系容易判断.如果有谁想掌握具体的5原则的内容,即使没有文字、语言的说明只要有作为基干的特性要素图就可以弄懂.为了使5原则表更容易理解,特性要素图原则上是必须要的作成特性要素图的5个要点1.问题(特性)要尽可能详尽具体地表现出来.要牢牢地把握现状,正确抓住问题点.特性要尽可能地用具体的数字来表示例:服务不好服务的对应太慢在使用5原则表决定标题时使用这种手法服务的对应需要1个小时2.集体创造性思考的实施.把各部分的人集中到一起,作出特性要素图.据此找出真正原因的机会就会增加.这时候由一个人将众人提出的想法记入特性要素图3.汇集事实情报.在用'3现主义'制定对策前将事实和数据汇总起来4.确认全部的要素是否都已经提了出来.重复WHY WHY这一程序.根据需要从熟手那里求得帮助(光罗列现象无法解决问题)5.经常地进行研究、不断改良加以完善.特性要因图需要重复不断地加以修正.根据需要,如果有新的发现要加以追记.在最后总结时可能要将特性要素重写追记:实际上在研究讨论阶段,无拘束地、自由地将想法全部记下来的方法则更好好的特性要素图的确认卡·确认是否全部的要素都已经提炼出来了.可根据需要利用"4M"法或是插图等来防止遗漏.·确认最末端的要素(最小骨)是否已经挖掘,明确到可以采取具体的行动(加以对策)的程度..直到(挖掘出来的)要素细到可以采取具体的行动(加以对策)时为止,要不断地重复'WHY WHY"这一程序(据说5次较为妥当)·确认要素是否有条理地被整理出来了.特性是否保持了和大骨,中骨,小骨及最小骨的关联.确认全部的要素是否都和特性有关系(有无没有关系的要素)·确认要素中有没有意思不明确的东西.多次举行集体性创造会议.因为依据不同的人对选出来的要素的阐述可能不一样..在这里有必要确认全体人员对于各种要素的理解是否相同·确认针对各个要素所采取的解析等活动是否排定了先后顺序要按重要指向将各个要素依重要度排序,按先后顺序采取行动.。
本田五原则报告的作成

五原则的填写说明-
13
对 策 效 果 的 确 认(效果实绩)
填写目标: 为定量证明防止再发 见下页
五原则的填写说明-
14
对 策 效 果 的 确 认(效果实绩)
在工序上或客户处对对策实施效果进行跟踪(注明确认人及 确认日期,效果可以通过品质数据/测量对策前后的变化来确认, 充分活用统计手法) 1、用品质数据对对策效果进行前后比较; 2、偶发不良品时,制造条件的比较数据; 3、制品无法体现变化时,制造条件的比较数据; 在数值上无法对 4、适用方面包括到客户处确认。 比的对策不是真 正的对策 说明 定量进行效果的检证和结果的检查。 这些效果检证属: · 在客户条件下的确认 · 限度值的确认 · 试验等的确认 · 依照质量情况监视 要点: 1、确认数据的取样数量,最终确 认需要的时间也很重要 2、确认所实施对策对正常作业程 序有无不良影响 (确认工程熟练度) 3、确认人的熟练程度(确认对人有 无风险)
例:为什么机器停了?
真正的原因
课题是 构筑购买设备的体系
没有制定购买 设备时的 规则 · 渠道 在购买设备时 没有进行 充分的确认
20
最初的问题 (表象的)
为什么 机器停了
为什么-1
是因为过载造成 保险丝 断开
<防患于未然> ~管理水平~
购买了不带 过滤器的设备
为什么-2
轴承部位的 润滑 不充分
为什么-3
——依工序流程与时序,以变化为中心进行填写 3、不良发生要因调查(尽量使用图、表等来表达) ﹡ QC手法在发生要因分析中有效,利用特性要因图、FMEA进 行分析
﹡对发生要因、流出要因和事实的验证,不产生问题的条件的
特征与变化的比较,相对于集中找准的工序的不良点要因分析与 其结果 4、调查结果总结、变化点和推断原因总结 ——一针见血!变化与原因?
- 1、下载文档前请自行甄别文档内容的完整性,平台不提供额外的编辑、内容补充、找答案等附加服务。
- 2、"仅部分预览"的文档,不可在线预览部分如存在完整性等问题,可反馈申请退款(可完整预览的文档不适用该条件!)。
- 3、如文档侵犯您的权益,请联系客服反馈,我们会尽快为您处理(人工客服工作时间:9:00-18:30)。
6月29日
注:恒久公司正在试验吹气成型工艺。如 果成功可有效避改免成此:故每生障产。完一卷原材料后更换高温胶布。(一
“SLF125-7H更换高温胶布后产品确认记录” 之前的没有文件支持,员工操作没有标准。没有依据。
向源流的反馈(体制、构造的反映) 水平展 开,
○流没出有原采因取
删除不要 追加:如发现不良品,
改成:高温胶 布使用时间太 长
为什么(5)
改成:高温胶 布更换没有定 期管理
1.TDK返 品 2.在后现续品第 注一:批后正续常恒 久公司知会一 TDK,TDK批
改成:会让客户觉得你想变更或不想 一直全检,所以删除。
判定
TO:广汽 ATTN: CC: FM:东方骏
防止缺陷再发生对策报告书
(五原则表) 事
报告单位:深圳东方骏实业有限公司
承认 确认 作成 作成日 岑南松 岑南松 2014年4
发生状况
顾客名 (纯正品番) 品番 品名 发生日 发生场所 生产日期 发生数 连络书发生NO
○
广汽
不
中央面板 2广0汽14品年质4月零2件0日 科 2014年4月20日 1PCS 2014.4.20
当 ○ 发 · 每 如有磨
损马上
实施日 6月29日
果生产的2确0 卷产品
改成:制定“TDK产品成型作业指导书"规定每生产完一卷原材料 后更换高温胶布(即定期更换高温胶布)效果确认见附页
改成:材料受热不均匀,而导致材料拉伸过度,产 生穿孔。耐高温胶布的更换没有进行管理。 之前的原因分析不够明确。
· 更 重点检
当面的处置(对象品番、层别方法、在库选别结果)
疑 步骤 问 分 析 穿孔
为什么(1) 高温胶布磨损
为什么(2)
材成型时铝制模具与PC 料
恒久电子包 装材料厂
改成:材料拉 伸不平衡而引 起空孔
改成:材料受 热不均匀
为什么(3) PC材料物性不同
改成:高温胶 布磨损
1.对高为温什么(4) 胶时布监进控行同 时2.采加取快全吹 气成型的
之前生产的要重新重
点检查
○
之前描述的不清楚。 流 ·
卷原材料可生产27卷产品) 之前的对策无法实施,检查高温胶布是否磨损是很 难检查的。有无磨损一般是目视难以检查出来。
改成:全数检查,并作成全数检查作业指导书。修订 《新产品试作控制程序》追加生产必备文件确认表。
全数检查
采
6月29日
改成:出货仕样书没有派发,相关部门不知道要全检。只有出荷抽检,没有实施全数检查。
顾客发来 的不良写 真
○实
·现 外· 从 1.穿孔
位2.置有不时 一卷当
适
○工程的检证
○要因分析
(社内不良发生工程的明确化) 载带来料 (生O产K加)工 (QAN检G)验 (出N货G)
治具无异常
作业员无异常
改成:QA抽检
(OK)
QA检验,是不准确的描 述,没有体现是全检还 是抽检
没有进行全数检方法无异常 查
对策效
生产时模具异常
穿 孔
材料无不良
改成
NO
工程名
1
来料检查
2 材料入库出库
3
成型
4 工程内定时抽检5Fra bibliotek包装入库
6 出荷尺寸抽检
7
出荷
工程验证 没有发现材料穿孔的现象
不会产生穿孔 会产生穿孔
工程内抽检没有发现穿孔 不会产生穿孔
出荷抽检没有发现穿孔 不会产生穿孔
判定 O O X O O X O
原因的究明 ○发生原因 (根据对顾