组合夹具
组合夹具.

组合夹具
一、组合夹具的概念:
组合夹具由一套预先制造好的不同形状、不同规格、不同尺寸的标准元件及部件组装而成。
二、分类:
组合夹具分为槽系和孔系两大类
三、组合夹具的元件
①基础件②支承件③定位件④导向件⑤夹紧件⑥紧固件⑦夹紧件⑧合件⑨其他新元件和合件
图1
基础件:1-长方形基础件;支承件:2-长方形垫板,3-长方形支承座,4-方形支承座;定位件:6-圆形定位销,7-圆形定位盘,8-菱形定位销;导向件:5-钻模板,9-快换钻套;紧固件:10-钻套螺钉,11-圆螺母,12-槽用螺栓,13-厚螺母,14-特殊螺母,16-埋头螺钉,17-定位螺钉,18-U形垫圈;连接元件:15-定位键。
图2 组合夹具组装示意图
图2是一个钻转向臂侧孔的组合夹具,工件以孔及端面在圆形定位销6、圆形定位盘7上定位共限制五个自由度,另一个自由度由菱形定位销8限制;工件用螺旋夹紧机构夹紧,夹紧机构由U形垫圈18、槽用螺栓12和厚螺母13组成。
快换钻套9用钻套螺钉10紧固在钻模板5上,钻模板用螺帽14、槽用螺栓12
紧固在长方形支承座3上。
支承座3用槽用螺栓12和螺帽14紧固在长方形垫板2和长方形基础板1上。
图2中未标全的件号参见图1。
组合夹具是机床夹具中标准化、系列化、通用化程度最高的一种夹具,其基本特点是:结构灵活多变,元件能长期重复使用,设计和组装周期短。
组合夹具的缺点是:体积较大,刚性较差,购置元件和合件一次性投资大。
组合夹具适于在单件小批生产中加工那些位置精度要求较高的工件,常在新产品试制和完成临时突击任务中使用。
组合夹具基本知识介绍
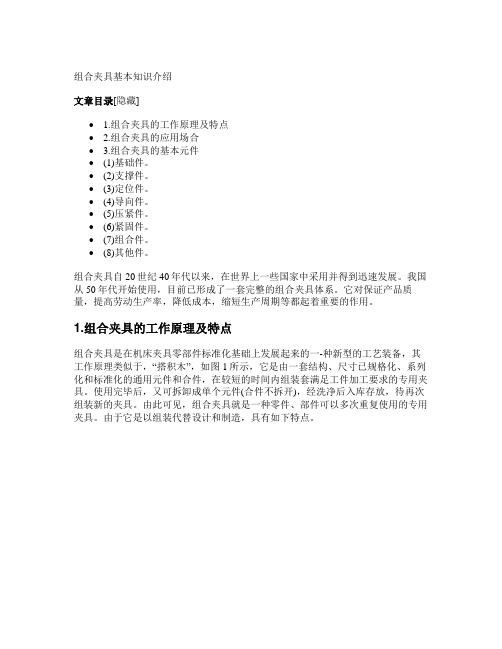
组合夹具基本知识介绍文章目录[隐藏]• 1.组合夹具的工作原理及特点• 2.组合夹具的应用场合• 3.组合夹具的基本元件•(1)基础件。
•(2)支撑件。
•(3)定位件。
•(4)导向件。
•(5)压紧件。
•(6)紧固件。
•(7)组合件。
•(8)其他件。
组合夹具自20世纪40年代以来,在世界上一些国家中采用并得到迅速发展。
我国从50年代开始使用,目前已形成了一套完整的组合夹具体系。
它对保证产品质量,提高劳动生产率,降低成本,缩短生产周期等都起着重要的作用。
1.组合夹具的工作原理及特点组合夹具是在机床夹具零部件标准化基础上发展起来的一-种新型的工艺装备,其工作原理类似于,“搭积木”,如图1所示,它是由一套结构、尺寸已规格化、系列化和标准化的通用元件和合件,在较短的时间内组装套满足工件加工要求的专用夹具。
使用完毕后,又可拆卸成单个元件(合件不拆开),经洗净后入库存放,待再次组装新的夹具。
由此可见,组合夹具就是一种零件、部件可以多次重复使用的专用夹具。
由于它是以组装代替设计和制造,具有如下特点。
图1槽系组合钻模元件分解图1-其他件; 2-基础件; 3-合件; 4-定位件; 5-紧固件; 6-压紧件; 7-支撑件; 8-导向件(1)灵活多变,适应范围广,可大大缩短生产准备周期。
(2) 可节省大量人力物力,减少金属材料的消耗。
(3)可大大减少存放专用夹具的库房面积,简化了管理工作。
其不足之处是外形尺寸较大、笨重,且刚性较差;此外,由于所需元件的储备量大,故一次性投资费用高。
2.组合夹具的应用场合组合夹具使用上的临时性、组合性和多变适应性,使得组合夹具特别适用于生产准备周期很短的临时突击性生产任务,以及新产品的试制、产品的品种多变或单件小批量生产的情况。
但由于组合夹具应用的初始投资较大,其正常循环应用需要一定的生产规模相配合,所以在小企业中往往难以推广,一般多在固定行业的大中型企业得到较快的推广,并取得较好的长期经济效益。
典型的柔性夹具有哪些
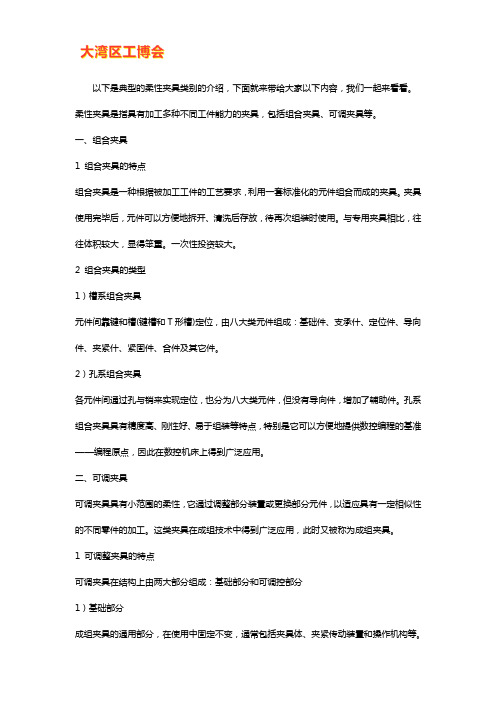
以下是典型的柔性夹具类别的介绍,下面就来带给大家以下内容,我们一起来看看。
柔性夹具是指具有加工多种不同工件能力的夹具,包括组合夹具、可调夹具等。
一、组合夹具1 组合夹具的特点组合夹具是一种根据被加工工件的工艺要求,利用一套标准化的元件组合而成的夹具。
夹具使用完毕后,元件可以方便地拆开、清洗后存放,待再次组装时使用。
与专用夹具相比,往往体积较大,显得笨重。
一次性投资较大。
2 组合夹具的类型1)槽系组合夹具元件间靠键和槽(键槽和T形槽)定位,由八大类元件组成:基础件、支承什、定位件、导向件、夹紧什、紧固件、合件及其它件。
2)孔系组合夹具各元件间通过孔与销来实现定位,也分为八大类元件,但没有导向件,增加了辅助件。
孔系组合夹具具有精度高、刚性好、易于组装等特点,特别是它可以方便地提供数控编程的基准——编程原点,因此在数控机床上得到广泛应用。
二、可调夹具可调夹具具有小范围的柔性,它通过调整部分装置或更换部分元件,以适应具有一定相似性的不同零件的加工。
这类夹具在成组技术中得到广泛应用,此时又被称为成组夹具。
1 可调整夹具的特点可调夹具在结构上由两大部分组成:基础部分和可调控部分1)基础部分成组夹具的通用部分,在使用中固定不变,通常包括夹具体、夹紧传动装置和操作机构等。
2)可调整部分包括定位元件,夹紧元件和刀具引导元件等。
更换工件品种,只需对该部分进行调整或更换元件,即可进行新的加工。
2 可调夹具的调整方式调整方式:更换式、调节式、综合式和组成式。
一种柔性夹具,其特征在于,包括若干板状挡板,各所述挡板上均覆盖有柔性气囊,所述挡板上开设有与柔性气囊连通的进气孔和出气孔,所述进气孔与充气泵连接,所述出气孔与出气调节阀连接,所述柔性气囊与工件相接触的工作面上设有压力感应片,所述压力感应片、充气泵和出气调节阀分别与控制器无线信号连接;控制器根据压力感应片传输的信号判断被夹持件是否被夹紧,通过调节充气泵和出气调节阀控制夹紧度。
简述组合夹具的特点
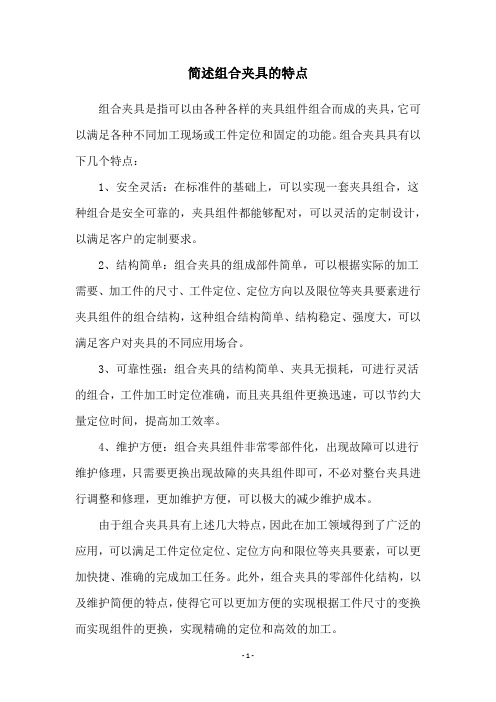
简述组合夹具的特点
组合夹具是指可以由各种各样的夹具组件组合而成的夹具,它可以满足各种不同加工现场或工件定位和固定的功能。
组合夹具具有以下几个特点:
1、安全灵活:在标准件的基础上,可以实现一套夹具组合,这种组合是安全可靠的,夹具组件都能够配对,可以灵活的定制设计,以满足客户的定制要求。
2、结构简单:组合夹具的组成部件简单,可以根据实际的加工需要、加工件的尺寸、工件定位、定位方向以及限位等夹具要素进行夹具组件的组合结构,这种组合结构简单、结构稳定、强度大,可以满足客户对夹具的不同应用场合。
3、可靠性强:组合夹具的结构简单、夹具无损耗,可进行灵活的组合,工件加工时定位准确,而且夹具组件更换迅速,可以节约大量定位时间,提高加工效率。
4、维护方便:组合夹具组件非常零部件化,出现故障可以进行维护修理,只需要更换出现故障的夹具组件即可,不必对整台夹具进行调整和修理,更加维护方便,可以极大的减少维护成本。
由于组合夹具具有上述几大特点,因此在加工领域得到了广泛的应用,可以满足工件定位定位、定位方向和限位等夹具要素,可以更加快捷、准确的完成加工任务。
此外,组合夹具的零部件化结构,以及维护简便的特点,使得它可以更加方便的实现根据工件尺寸的变换而实现组件的更换,实现精确的定位和高效的加工。
综上所述,组合夹具具有安全灵活、结构简单、可靠性强以及维护方便的特点,使得它在加工领域广泛应用,可以满足工件定位、定位方向和限位等夹具要素,实现精准定位、有效加工。
组合夹具的原理和应用
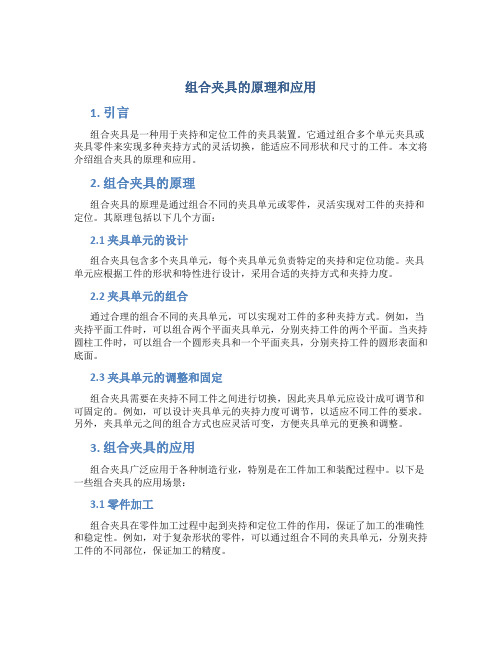
组合夹具的原理和应用1. 引言组合夹具是一种用于夹持和定位工件的夹具装置。
它通过组合多个单元夹具或夹具零件来实现多种夹持方式的灵活切换,能适应不同形状和尺寸的工件。
本文将介绍组合夹具的原理和应用。
2. 组合夹具的原理组合夹具的原理是通过组合不同的夹具单元或零件,灵活实现对工件的夹持和定位。
其原理包括以下几个方面:2.1 夹具单元的设计组合夹具包含多个夹具单元,每个夹具单元负责特定的夹持和定位功能。
夹具单元应根据工件的形状和特性进行设计,采用合适的夹持方式和夹持力度。
2.2 夹具单元的组合通过合理的组合不同的夹具单元,可以实现对工件的多种夹持方式。
例如,当夹持平面工件时,可以组合两个平面夹具单元,分别夹持工件的两个平面。
当夹持圆柱工件时,可以组合一个圆形夹具和一个平面夹具,分别夹持工件的圆形表面和底面。
2.3 夹具单元的调整和固定组合夹具需要在夹持不同工件之间进行切换,因此夹具单元应设计成可调节和可固定的。
例如,可以设计夹具单元的夹持力度可调节,以适应不同工件的要求。
另外,夹具单元之间的组合方式也应灵活可变,方便夹具单元的更换和调整。
3. 组合夹具的应用组合夹具广泛应用于各种制造行业,特别是在工件加工和装配过程中。
以下是一些组合夹具的应用场景:3.1 零件加工组合夹具在零件加工过程中起到夹持和定位工件的作用,保证了加工的准确性和稳定性。
例如,对于复杂形状的零件,可以通过组合不同的夹具单元,分别夹持工件的不同部位,保证加工的精度。
3.2 组装生产线在组装生产线中,组合夹具可以实现对不同组件的夹持和定位。
例如,在手机组装生产线中,可以通过组合不同夹具单元,夹持和定位手机的不同部件,提高组装效率和质量。
3.3 检测与测量组合夹具还可以应用于工件的检测和测量过程中。
通过组合不同的夹具单元,可以夹持工件并将其固定在检测设备上,方便进行精确的测量和检测。
3.4 自动化生产随着自动化生产的发展,组合夹具在自动化生产线上的应用越来越广泛。
组合夹具元件标准及选用
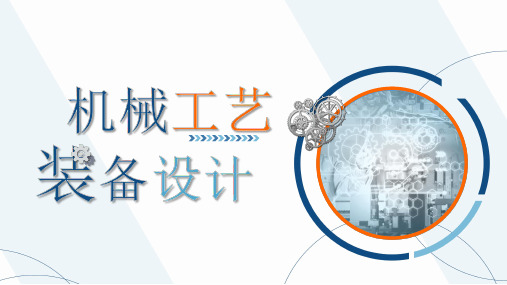
准及选用规 格槽 宽/㎜槽 距/㎜连接螺栓/(㎜·㎜)键用螺钉/㎜支承件截面 /㎜2最大载荷/ N 工件最大尺寸/(㎜·㎜·㎜)大型75±0.01M16×1.5M575×7590×902000002500×2500×1000中型60±0.01M12×1.5M560×601000001500×1000×500小型30±0.01M8、M6M3M3、M2.530×305×22.550000500×250×25008.0016+08.0012+015.008+015.006+ (1) 槽系组合夹具的规格 为了适应不同产品大小的需要,槽系组合夹具分大、中、小型三种规格,其主要参数见表1所示(JB2814-1979)。
表1 槽系组合夹具的主要结构要素及性能机械工业部标准(JB2814-1979)规定如下:①编号D---大(Da)型组合夹具元件,即16mm槽系列;Z---中(Zhong)型组合夹具元件,即12mm槽系列;X---小(Xiao)型组合夹具元件,即8mm或6mm槽系列。
第一位数字表示元件的“类”,用1~9表示。
1---基础件;2---支承件;3---定位件;4---导向件;5---压紧件;6---紧固件;7---其它件;8---合件;9---组装用工具和辅具。
第二位数字表示元件类中的“组”,用0~9表示。
第三位数字表示“组”中的“品种”,用数字0~9表示。
②规格特征尺寸,一般用L×B×H 表示规格尺寸。
【例】型别(中型),亦称12mm槽系列类别,支承件类组别,支承件中的5号组180×90×30Z 2 5 4③元件的分类组合夹具元件的分类,主要根据元件的结构、形状和用途而划分的。
组合夹具设计与组装技术

组合夹具设计与组装技术组合夹具啊,就像是机械世界里的乐高积木,不过是超级专业、超级精密的那种。
它的设计和组装,就像一场精心策划的魔术表演。
你看那夹具的设计图,就像一份神秘的藏宝图。
每个线条、每个标注都是宝藏的线索。
设计师就像一个寻宝船长,在图纸的海洋里寻找最佳的方案。
那些尺寸啊,精度要求啊,就像是海盗设下的重重机关,一不小心就会让整个夹具“沉船”。
当开始组装的时候,那一个个夹具元件就像一群性格各异的小怪兽。
螺栓就像它们的锁链,把这些小怪兽乖乖地锁在一起。
而螺母呢,就像是魔法扣子,一拧上去,就把小怪兽们的力量都整合起来了。
组装工人就像是超级英雄,他们手里的工具就是武器。
电动螺丝刀就像一把光剑,“嗡嗡”地挥舞着,把螺栓迅速拧紧。
有时候,遇到难搞的元件,就像遇到了顽固的大怪兽,怎么都摆不对位置,这时候工人就得像驯兽师一样,耐心地调整,哄着这些“怪兽”就范。
那些定位元件就像导航仪,准确地告诉其他元件应该待在哪里。
如果定位错了,那整个夹具就像迷路的旅人,完全找不到方向,最后生产出来的零件也会像歪瓜裂枣一样难看又不实用。
而且啊,组合夹具的组装过程中,对精度的要求就像走钢丝一样,差一丁点儿都不行。
就好比厨师做菜,盐多一丢丢,整个菜就毁了。
在夹具组装里,一微米的误差可能就导致整个夹具成为一个“残次品”。
组装好的夹具看起来就像一个严阵以待的军队方阵,每个元件都有自己的岗位,各司其职。
它就像一个坚强的堡垒,守护着被加工零件的形状和精度。
有时候,为了找到最合适的组合夹具方案,设计师和工程师们就像一群疯狂的科学家,在实验室里(其实就是设计室啦)头脑风暴。
各种奇思妙想就像烟花一样在空中绽放,直到找到那个最完美的组合方式。
这组合夹具设计与组装技术啊,虽然充满了挑战,但也像是一场充满乐趣的冒险。
每成功组装一个夹具,就像攻克了一个魔法城堡,那种成就感简直要冲破天际,让所有参与其中的人都感觉自己像是机械世界里的王者。
组合夹具设计与组装技术
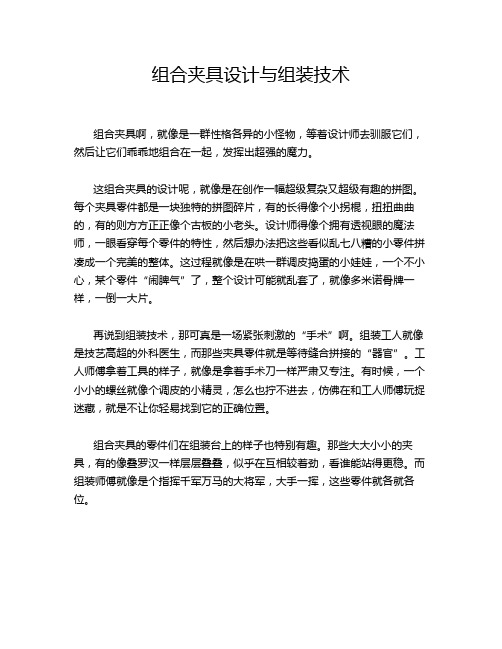
组合夹具设计与组装技术组合夹具啊,就像是一群性格各异的小怪物,等着设计师去驯服它们,然后让它们乖乖地组合在一起,发挥出超强的魔力。
这组合夹具的设计呢,就像是在创作一幅超级复杂又超级有趣的拼图。
每个夹具零件都是一块独特的拼图碎片,有的长得像个小拐棍,扭扭曲曲的,有的则方方正正像个古板的小老头。
设计师得像个拥有透视眼的魔法师,一眼看穿每个零件的特性,然后想办法把这些看似乱七八糟的小零件拼凑成一个完美的整体。
这过程就像是在哄一群调皮捣蛋的小娃娃,一个不小心,某个零件“闹脾气”了,整个设计可能就乱套了,就像多米诺骨牌一样,一倒一大片。
再说到组装技术,那可真是一场紧张刺激的“手术”啊。
组装工人就像是技艺高超的外科医生,而那些夹具零件就是等待缝合拼接的“器官”。
工人师傅拿着工具的样子,就像是拿着手术刀一样严肃又专注。
有时候,一个小小的螺丝就像个调皮的小精灵,怎么也拧不进去,仿佛在和工人师傅玩捉迷藏,就是不让你轻易找到它的正确位置。
组合夹具的零件们在组装台上的样子也特别有趣。
那些大大小小的夹具,有的像叠罗汉一样层层叠叠,似乎在互相较着劲,看谁能站得更稳。
而组装师傅就像是个指挥千军万马的大将军,大手一挥,这些零件就各就各位。
要是把组合夹具的设计和组装比喻成一场音乐会,那每个零件都是一个独特的音符。
设计师负责谱写美妙的乐章,告诉每个音符该在什么位置,而组装工人就是演奏者,把这些音符精准地弹奏出来。
要是哪个音符出了错,那可就会像破了音的歌手一样,整个夹具的性能就会变得非常“难听”。
在这个奇妙的组合夹具世界里,公差就像是个严格的监工。
稍微超出一点,就像越过了雷池一样,整个夹具的精度就会大打折扣。
就好比做菜时盐放多了一点,整道菜的味道就全变了。
每一次成功的组合夹具设计与组装,就像是一场盛大的魔法秀。
那些原本毫无生气的零件,一下子就变成了一个充满活力、功能强大的夹具。
这时候,设计师和组装工人就像魔法世界里的英雄,创造出了令人惊叹的奇迹。
成组夹具

(4)组合式
将一组零件的有关定位或导向元件同 时组合在一个夹具体上,以适应不同零件 加工的需要。
(3)可调整夹具设计
成组夹具的设计方法与专用夹具大体 相同,主要区别在于成组夹具的使用对象 不是一个零件而是一组零件。因此设计时 需对一组零件的图纸、工艺要求和加工条 件进行全面分析,以确定最优的工件装夹 方案和夹具调整形式。
三、其它柔性夹具
大量实验表明:目前组合夹具的刚度主 要取决于组合夹具元件本身的刚度,而 与所用元件的数量关系不大。
二、可调整夹具
具有小范围柔性,通过调整部分 装置或更环部分零件,以适应具有一 定相似性的不同零件的加工。
1.可调整夹具的特点
结构组成:基础部分、可调整部分。 基础部分:夹具的通用部分,在使用中固定 不变,通常包括夹具体、夹紧传动装置和操作机 构等。此部分结构主要依据零件组内各零件的轮 廓尺寸、夹紧方式及加工要求等因素确定。 可调整部分通常包括定位元件、夹紧元件和 刀具引导元件等。更换工件品种时,只需对该部 分进行调整或更换元件,即可进行新的加工。
类型:槽系组合夹具、孔系组合夹具 槽系组合夹具元件间靠键和槽(键槽和
T形槽)定位; 孔系组合夹具则通过孔与销来实现元
件间的定位。
(三)组合夹具的组装
组装过程: 1.熟悉原始材料 2.构思夹具结构方案 3.组装计算 4.试装 5.组装 6.检验
(四)组合夹具的精度与刚度
首先,组合夹具的最终精度大都通过调 整和选择装配来达到,因而可避免误差 累积的问题。经过精心的组装与调整, 组合夹具的组装精度完全可以达到专用Байду номын сангаас夹具所能达到的精度。
2.可调整夹具的调整方式
(1)更换式 采用更换夹具可调整部分元件的方法,
组合夹具的名词解释

组合夹具的名词解释组合夹具是一种广泛应用于制造业的工具,用于固定、定位和加工工件。
它由多个部件组成,可以根据工件的形状和尺寸进行调整,以确保精确而有效的加工过程。
本文将对组合夹具的定义、应用领域以及其在制造业中的重要性进行探讨。
一、定义组合夹具是一种用于固定工件的装置,通常由多个部件组成。
这些部件可以灵活组合,以适应不同形状和尺寸的工件。
组合夹具通常由夹具床、夹具块、夹具夹持系统、定位装置以及调整装置等组成。
通过合理配置这些部件,可以实现夹紧、定位和加工工件的目的。
二、应用领域组合夹具广泛应用于各个制造行业,包括汽车制造、机械制造、航空航天、电子设备等。
在这些行业中,工件的形状和尺寸各异,因此需要根据具体情况设计和使用组合夹具。
无论是汽车车身的焊接,还是电子设备的装配,组合夹具都扮演着至关重要的角色。
三、优势和重要性组合夹具的使用具有多重优势和重要性。
首先,组合夹具能够提高生产效率。
通过合理设计和使用夹具,可以减少工艺时间和劳动力成本。
夹具中的定位装置和夹持系统可以使工件快速、准确地定位,从而加快加工速度和提高加工精度。
其次,组合夹具有助于实现批量生产。
在制造业中,往往需要大量生产相同或类似的工件。
使用组合夹具可以确保每个工件都具有统一的定位和夹持方式,从而保证产品质量的一致性。
此外,组合夹具还能够提高工作安全性。
工件在加工过程中通常需要固定和夹持,以防止意外事故的发生。
组合夹具能够牢固地固定工件,减少操作人员的操作风险和受伤可能性。
最后,组合夹具还在一定程度上减少了人为因素对加工质量的影响。
通过使用夹具,可以减少操作人员对工件定位的依赖,从而减少由于操作不当而引起的加工误差。
四、发展趋势随着制造技术的不断发展和进步,组合夹具也在不断创新和改进。
首先,组合夹具的自动化程度不断提高。
随着自动化技术的应用,传感器和执行器可以集成到夹具中,实现夹紧和定位的自动化控制。
这不仅提高了生产效率,还减少了人为因素的干预。
组合夹具
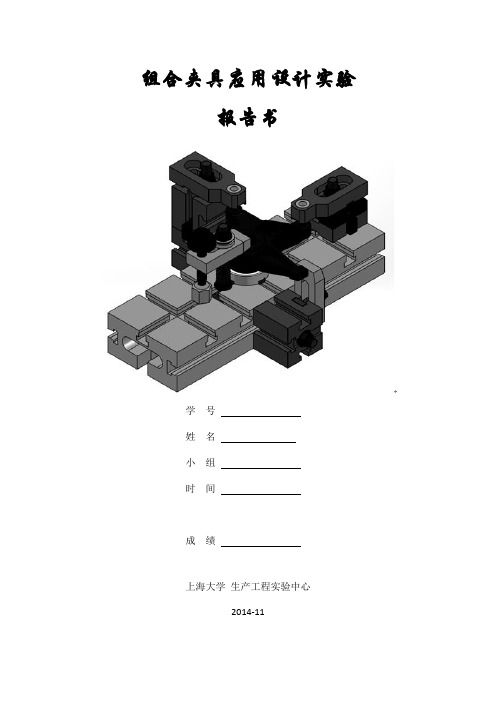
组合夹具应用设计实验报告书学号姓名小组时间成绩上海大学生产工程实验中心2014-11一、实验目的……二、实验要求……三、实验内容……四、实验设备……五、实验报告(双曲柄工件钻a、b孔组合夹具设计)1. 组合夹具组装步骤……2. 组合夹具组装方法……3. 组合夹具虚拟装配效果图……4. 组合夹具组成元件爆炸图……5. 组合夹具组成元件明细表……附录组合夹具应用设计实验指导书一、实验目的通过组合夹具应用设计实验,加深同学了解组合夹具特点,熟悉元件组装方法,掌握组合夹具设计一般步骤,提高组合夹具应用设计能力。
二、实验要求1、熟悉组合夹具的各种元件的基本功能和组装方法。
2、掌握组合夹具设计一般步骤。
3、根据指定零件的加工要求,完成组合夹具设计和虚拟装配。
三、实验内容1、掌握组合夹具的基本概念,熟悉六点定位原理和零件定位方法。
2、根据所指定的工件零件图,针对零件的某一工序的工艺要求设计定位与夹紧方案。
3、根据定位与夹紧方案选择相应系列组合元件进行组装。
4、使用Solidworks等CAD软件进行组合夹具虚拟装配设计,完成组合夹具设计工作。
四、实验设备1、12毫米槽系组合夹具模型库2、计算机及其CAD软件多台套3、虚拟组装实验平台多台套五、实验报告根据实验内容,编写指定零件组合夹具设计与虚拟组装实验报告,内容包括:1. 组合夹具组装步骤2. 组合夹具组装方法3. 组合夹具虚拟装配效果图4. 组合夹具组成元件爆炸图5. 组合夹具组成元件明细表六、实验指导(一)组合夹具现代的组合夹具是伴随着大批大量生产的发展而出现的,早期的夹具为专用夹具。
随着近代工业的不断发展,产品不断的更新换代,零件的结构和尺寸参数亦发生变化,原有的专用夹具就要报废,必须设计新的专用夹具,显然,在经济上和生产周期上是非常不合理的。
为解决这个问题,从上世纪四十年代开始,科技人员就着手研制能够适合单件小批量和成批生产的可多次重复使用的夹具,即组合夹具。
组合夹具的定位原理和方式
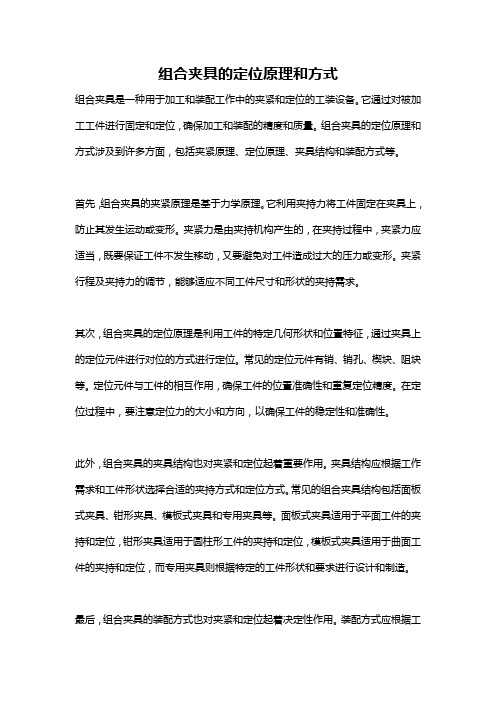
组合夹具的定位原理和方式组合夹具是一种用于加工和装配工作中的夹紧和定位的工装设备。
它通过对被加工工件进行固定和定位,确保加工和装配的精度和质量。
组合夹具的定位原理和方式涉及到许多方面,包括夹紧原理、定位原理、夹具结构和装配方式等。
首先,组合夹具的夹紧原理是基于力学原理。
它利用夹持力将工件固定在夹具上,防止其发生运动或变形。
夹紧力是由夹持机构产生的,在夹持过程中,夹紧力应适当,既要保证工件不发生移动,又要避免对工件造成过大的压力或变形。
夹紧行程及夹持力的调节,能够适应不同工件尺寸和形状的夹持需求。
其次,组合夹具的定位原理是利用工件的特定几何形状和位置特征,通过夹具上的定位元件进行对位的方式进行定位。
常见的定位元件有销、销孔、楔块、阻块等。
定位元件与工件的相互作用,确保工件的位置准确性和重复定位精度。
在定位过程中,要注意定位力的大小和方向,以确保工件的稳定性和准确性。
此外,组合夹具的夹具结构也对夹紧和定位起着重要作用。
夹具结构应根据工作需求和工件形状选择合适的夹持方式和定位方式。
常见的组合夹具结构包括面板式夹具、钳形夹具、模板式夹具和专用夹具等。
面板式夹具适用于平面工件的夹持和定位,钳形夹具适用于圆柱形工件的夹持和定位,模板式夹具适用于曲面工件的夹持和定位,而专用夹具则根据特定的工件形状和要求进行设计和制造。
最后,组合夹具的装配方式也对夹紧和定位起着决定性作用。
装配方式应根据工件的尺寸、材料、形状和工艺要求等因素进行选择。
常见的装配方式包括手动装配、液压装配和气动装配等。
手动装配适用于小型工件和简单工艺的装配;液压装配适用于对夹紧力和定位精度要求较高的工件装配;气动装配适用于大型工件和需要快速定位的装配。
综上所述,组合夹具的定位原理和方式包括夹紧原理、定位原理、夹具结构和装配方式等方面。
通过合理选择夹紧力、定位元件、夹具结构和装配方式,能够实现工件的夹持和定位要求,确保加工和装配的精度和质量。
随着制造技术的不断发展,组合夹具的定位原理和方式也在不断改进和创新,以满足更加复杂和精密的加工和装配需求。
组合式密封夹具设计及使用

组合式密封夹具设计及使用组合式密封夹具是指利用一定的技术,将两个部件或更多部件用紧固件结合在一起,形成一种结构,使这些部件具有密封性能的结构方法。
组合式密封夹具是一种封闭结构,具有高效的密封性能,可以满足各种紧急使用的要求。
二、组合式密封夹具的优点1、结构灵活:夹具可以在不同的环境中使用,它可以根据需要改变形状或属性,以更好地满足工程的安装需求。
2、密封效果好:密封夹具的结构比较紧凑,能够有效地防止空气、液体、气体等介质的逸出,从而实现密封的效果。
3、安装简单:相比于传统的密封方式,组合式密封夹具更简单,使用更加便捷,不需要复杂的安装步骤,可以节省安装时间,提高工作效率。
三、组合式密封夹具的应用1、工程机械:组合式密封夹具在工程机械中的应用非常广泛,可以用来固定和防止运动零部件之间的摩擦,从而提高工作效率。
2、汽车制造:由于轿车和货车的发动机与底盘联系起来,并且要求有良好的紧固性,在这种情况下,组合式密封夹具可以起到很好的密封作用,降低发动机和底盘之间的摩擦损耗。
3、船舶制造:组合式密封夹具在船舶装配中用于固定和防止船体,甲板,底座以及其他部分之间的移动,从而达到防沉和节省能源的目的。
四、组合式密封夹具的设计要点1、考虑夹具的使用环境:在设计夹具的时候,应充分考虑夹具的使用环境,比如温度,湿度,污染水平等,以确保夹具的使用效果。
2、考虑夹具的制造工艺:夹具的制造要实现精度和高效率,制造工艺包括机械加工,抛光,检查,涂装等,这些工艺必须满足夹具的正常使用要求。
3、考虑使用寿命:夹具使用寿命为其密封性能提供了保证,因此,在设计夹具的时候,应考虑其使用寿命,以确保其使用效果。
4、考虑夹具的材料:组合式密封夹具的材料必须考虑其使用环境,确保其结构稳定,耐腐蚀,耐温等特性,以确保夹具的正常使用。
五、组合式密封夹具的使用注意事项1、首先,应进行全面的检查,确保夹具的性能和外观无缺陷,以确保其正常使用。
2、安装前,应充分考虑并计算夹具的安装位置,以确保其安装正确。
对组合夹具的认识

对组合夹具的认识一、组合夹具的定义和作用组合夹具是由多个单元夹具组合而成的一种夹具,它可以在同一工作台上完成多道工序加工,提高生产效率,减少生产成本。
组合夹具可以根据不同的工件形状和加工要求进行设计和制造,适用于各种机械加工行业。
二、组合夹具的结构和特点1.结构:组合夹具由基座、定位元件、支撑元件、夹紧元件等多个部分组成。
其中,基座是整个夹具的基础部分,定位元件用于确保工件在正确位置上进行加工,支撑元件用于固定和支撑工件,夹紧元件则是将工件固定在正确位置上。
2.特点:组合夹具可以根据不同的加工要求进行灵活的设计和制造,能适应各种形状和尺寸的工件;同时,在同一台机床上完成多道工序加工,大大提高了生产效率。
三、组合夹具的优缺点1.优点:(1)适应性强:可以针对不同形状和尺寸的工件进行设计和制造;(2)生产效率高:能在同一台机床上完成多道工序加工,大大提高了生产效率;(3)精度高:定位元件和夹紧元件的设计和制造,保证了加工精度。
2.缺点:(1)制造成本高:组合夹具由多个单元夹具组合而成,制造成本相对较高;(2)维护难度大:由于组合夹具结构复杂,维护难度较大。
四、组合夹具的应用领域组合夹具广泛应用于各种机械加工行业,如汽车零部件、机床零部件、航空零部件等。
在这些行业中,工件形状和尺寸多样化,需要进行多道工序加工,因此使用组合夹具可以大大提高生产效率和生产质量。
五、组合夹具的设计和制造流程1.原理设计:根据工件形状和加工要求确定定位元件、支撑元件和夹紧元件的数量、位置和结构形式。
2.结构设计:根据原理设计确定各个部分的详细尺寸和结构形式,并绘制出详细图纸。
3.加工制造:根据图纸进行各个部分的加工制造,并进行组装和调试。
4.测试验收:对制造好的组合夹具进行测试验收,检查是否满足设计要求,并进行必要的调整和改进。
六、组合夹具的维护和保养1.定期检查:定期对组合夹具进行检查,发现问题及时处理。
2.清洁保养:对组合夹具进行清洁保养,保持其正常使用状态。
组合夹具名词解释

组合夹具名词解释
嘿,朋友!你知道啥是组合夹具不?组合夹具啊,就像是一套神奇
的积木!你玩过积木吧?(就像我们小时候玩积木那样,可以用不同
的积木块拼搭出各种各样的形状和结构。
)组合夹具也是这样,可以
通过不同的组件灵活组合,来满足各种不同的加工需求。
比如说在工厂里,工人们要加工一个形状特别复杂的零件。
这时候,组合夹具就派上大用场啦!(它就像一个超级英雄,随时准备拯救加
工难题。
)工人可以挑选合适的夹具组件,把它们巧妙地组合在一起,就像搭积木一样,一下子就把零件稳稳地固定住了,让加工过程变得
轻松又高效。
想象一下,要是没有组合夹具,那得多麻烦呀!(难道要靠工人一
直拿手扶着零件加工吗?那可太不靠谱啦!)组合夹具的出现,真的
是给制造业带来了巨大的便利呢!它就像是一把万能钥匙,能打开各
种加工难题的锁。
而且哦,组合夹具还很灵活多变呢!今天加工这种零件用一套组合,明天加工另一种零件又可以换一套组合。
(这不就跟我们换衣服一样嘛,根据不同的场合穿不同的衣服。
)多方便呀!它让生产变得更加
灵活,能够快速适应各种不同的需求。
我觉得组合夹具真的是太了不起啦!它是制造业的好帮手,让加工过程变得更加简单、高效、可靠。
(没有它,好多工作可都不好开展呢!)所以呀,我们可千万不能小瞧了组合夹具的作用哦!。
组合夹具参数

组合夹具概述一、组合夹具性质及特点(一)组合夹具性质组合夹具是在机床夹具元件通用化、标准化、系列化的基础上发展起来的新型夹具。
它是由预先制造好的标准化组合夹具元件,根据被加工工件的工序要求组装而成的。
因此组合夹具具有通用性和专用性双重性质,即组成夹具的元件是通用性的元件,而一但组装成成套夹具即为专用夹具。
组合夹具结构灵活多变,元件长期重复使用。
因此。
其主要元件比其它型式的夹具零件具有高精度、高强度、高硬度、耐磨性高的特点,单个元件功能多样,并有完全互换性。
组合夹具元件周而复始循环使用的特点与专用夹具使用规律形成明显差异:专用夹具:设计------制造------使用-----报废组合夹具:元件库------组装------使用------拆卸-------清洗油封-------元件库(二)组合夹具特点根据组合夹具是由能重复使用的标准化元件组装而成的夹具特点,故元件之间的联接要求应定位准确、联接可靠、装拆方便。
槽系组合夹具元件之间定位联接是采用高精度的槽、键定位、螺栓紧固。
GB2804-81《组合夹具元件结构要素》中规定,我国槽系组合夹具的键槽和T型槽的定位尺寸有三种:8H7、12H7和16H7;螺栓采用M6、M8、M12*1.5T和M16*1.5构成微型、小型、中型、大型四个系列的槽系组合夹具元件系列。
采用组合夹具可在以下几个方面取得明显的技术经济效果:a.加速新产品试制,缩短生产周期;b.节约夹具设计、制造工时和材料,从而降低了产品的制造成本;c.保证产品的加工质量,提高新产品试制和小批量生产中工艺装备系数;d.可以大量替代工装生产中的二类工具;e.为复杂的专用夹具结构设计提供模拟试验夹具;f.节约夹具存放的库存面积。
(三)组合夹具的适用范围组合夹具适用于各个机械制造部门。
其广泛性在机械加工中已无所不及,在机床工具、纺织、石油、化工、矿山、冶金、农业、医疗、食品、造纸等机械以及汽车、铁路机车、船舶等制造行业中,特别是在军工航空航天产品施工中应用组合夹具均取得了很好的技术经济效果。
组合夹具拼装实验报告(3篇)
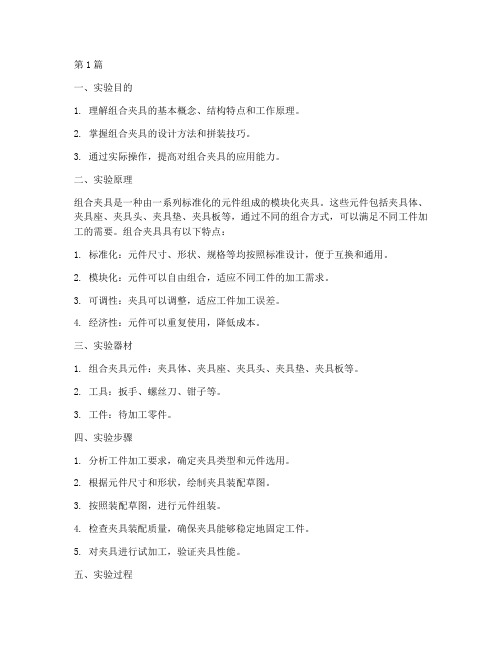
第1篇一、实验目的1. 理解组合夹具的基本概念、结构特点和工作原理。
2. 掌握组合夹具的设计方法和拼装技巧。
3. 通过实际操作,提高对组合夹具的应用能力。
二、实验原理组合夹具是一种由一系列标准化的元件组成的模块化夹具。
这些元件包括夹具体、夹具座、夹具头、夹具垫、夹具板等,通过不同的组合方式,可以满足不同工件加工的需要。
组合夹具具有以下特点:1. 标准化:元件尺寸、形状、规格等均按照标准设计,便于互换和通用。
2. 模块化:元件可以自由组合,适应不同工件的加工需求。
3. 可调性:夹具可以调整,适应工件加工误差。
4. 经济性:元件可以重复使用,降低成本。
三、实验器材1. 组合夹具元件:夹具体、夹具座、夹具头、夹具垫、夹具板等。
2. 工具:扳手、螺丝刀、钳子等。
3. 工件:待加工零件。
四、实验步骤1. 分析工件加工要求,确定夹具类型和元件选用。
2. 根据元件尺寸和形状,绘制夹具装配草图。
3. 按照装配草图,进行元件组装。
4. 检查夹具装配质量,确保夹具能够稳定地固定工件。
5. 对夹具进行试加工,验证夹具性能。
五、实验过程1. 分析工件加工要求,确定夹具类型为三爪卡盘夹具。
2. 根据元件尺寸和形状,绘制夹具装配草图,包括夹具体、夹具座、夹具头、夹具垫、夹具板等。
3. 按照装配草图,进行元件组装。
首先将夹具体安装在夹具座上,然后将夹具头安装在夹具体上,接着将夹具垫安装在夹具头上,最后将夹具板安装在夹具垫上。
4. 检查夹具装配质量,确保夹具能够稳定地固定工件。
观察夹具的紧固情况,确保夹具无松动现象。
5. 对夹具进行试加工,验证夹具性能。
将工件放置在夹具中,进行切削加工。
观察夹具的稳定性,确保工件加工质量。
六、实验结果与分析1. 夹具装配质量良好,能够稳定地固定工件。
2. 试加工过程中,夹具性能稳定,工件加工质量满足要求。
七、实验总结通过本次实验,我们掌握了组合夹具的基本概念、结构特点和工作原理,熟悉了组合夹具的设计方法和拼装技巧。
对组合夹具的认识

对组合夹具的认识组合夹具是一种非常重要的夹具类型,其主要特点是由多个小型夹具组合而成,可以在加工过程中完成多种不同工件的夹持,提高了生产效率和加工精度。
下面就对组合夹具的认识进行详细介绍。
一、组合夹具的结构和功能组合夹具是由多个小型夹具组合而成的,通常由基座、夹持刀架、调节装置、夹紧装置等组成。
在加工过程中,可以根据不同的工件大小、形状和加工要求,选择合适的夹具组合,实现快速高效的夹持,并保证加工精度。
组合夹具具有以下几个主要功能:1.实现多种不同型号、不同形状工件的夹持,提高了通用性和适用范围。
2.可以灵活调节夹持力和夹持位置,以适应不同工件的要求,提高了加工效率和加工精度。
3.在短时间内更换夹具组合,实现不同工件的夹持,提高了生产效率和加工质量。
二、组合夹具的种类和分类组合夹具按照不同的夹紧方法可以分为如下几种:1.机械式组合夹具机械式组合夹具是利用钩爪、螺纹、压板等夹紧装置,通过手动或机械的方式来夹紧工件。
这种夹具的主要优点是结构简单,使用方便,适合夹持形状较简单的工件。
2.气动式组合夹具气动式组合夹具是利用气动缸或气动夹紧器来夹紧工件,通过气动控制来实现夹持装置的开合。
这种夹具的优点是操作简便,夹持力大,夹具刚性好,适合夹持形状复杂、要求高精度的工件。
3.液压式组合夹具液压式组合夹具是利用液压缸或液压夹紧器来夹紧工件,通过液压控制来实现夹持装置的开合。
这种夹具的优点是夹持力大、可调性好、适合夹持大型、重型工件。
三、组合夹具的优点和应用范围组合夹具具有以下几个显著的优点:1.通用性好,可以夹持多种不同的工件。
2.夹紧力大,夹持稳定,对工件的影响小。
3.可调节性好,可以根据不同的工件要求进行调整。
4.易于更换夹具组合,适应生产需求。
组合夹具在机械制造、航空航天、汽车制造、电子制造等领域都有广泛的应用。
特别是在汽车制造和电子制造领域,由于产品更新速度较快,要求生产工艺和设备的快速调整,组合夹具的优势得到了更好的体现,可以适应各种生产需求。
- 1、下载文档前请自行甄别文档内容的完整性,平台不提供额外的编辑、内容补充、找答案等附加服务。
- 2、"仅部分预览"的文档,不可在线预览部分如存在完整性等问题,可反馈申请退款(可完整预览的文档不适用该条件!)。
- 3、如文档侵犯您的权益,请联系客服反馈,我们会尽快为您处理(人工客服工作时间:9:00-18:30)。
目录一、实践目的与要求 (1)1. 实践目的 (1)2. 实践要求 (1)二、车偏心用组合夹具组装 (1)1. 偏心轴零件的简图 (1)2. 工艺分析(毛坯→成品过程) (2)3. 定位方法和定位元件的选用 (2)4. 定位误差的计算 (2)5. 基础件和支承件的选用和组装 (3)6. 夹紧件的选用和组装 (3)7. 偏心距的调整 (3)8. 重点考虑的问题 (3)三、铣槽用组合夹具组装 (3)1. 传动轴零件的简图 (3)2. 工艺分析(工艺路线) (3)3. 定位方法和定位元件的选用 (4)4. 基础件和支承件的选用和组装 (4)5. 手动夹紧件的选用和组装 (5)6. 导向件的选用和组装 (6)7. 对刀尺寸的调整 (6)8. 气动夹紧件的选用和组装 (6)9. 重点考虑的问题 (6)四、钻孔用组合夹具组装 (7)1. 端盖零件的简图 (7)2. 工艺分析(工艺路线) (7)3. 定位方法和定位元件的选用 (8)4. 定位误差的计算 (8)5. 基础件和支承件的选用和组装 (9)6. 夹紧件的选用和组装 (9)7. 导向件的选用和组装 (10)8. 对刀尺寸的调整 (10)9. 重点考虑的问题 (10)五、加工中心上镗孔用组合夹具组装 (11)1. 支座零件的简图 (11)2. 工艺分析(工艺路线) (11)3. 定位方法和定位元件的选用 (11)4. 定位误差的计算 (11)5. 基础件和支承件的选用和组装 (12)6. 夹紧件的选用和组装 (13)7. 尺寸的调整 (13)8. 重点考虑的问题 (13)组合夹具实践一、实践目的与要求1.实践目的(1)熟悉组合夹具的应用场合和各种元件;(2)巩固夹具设计方面的基础知识;(3)掌握组合夹具的设计方法;(4)锻炼组合夹具的组装技能;(5)培养综合运用工艺规程设计、组合夹具设计等方面知识的能力。
2.实践要求(1)根据指定零件图中需加工的表面及技术要求,确定合理的工件表面加工方法;(2)根据选定的表面加工方法,确定合理的工件定位和夹紧方案;(3)根据选定的夹紧方案,设计并组装出符合要求的组合夹具;(4)根据组装出的组合夹具,分析其特点并画出夹具装配草图。
二、车偏心用组合夹具组装1. 偏心轴零件的简图要加工工件的工序简图如图2-1所示图2-1 偏心轴零件图本工序要求加工偏心轴零件的右边偏心圆柱φ48mm和不偏心圆柱φ35mm及右端面,要求以中间圆柱φ35mm和左端面为定位基准,圆柱φ35mm与圆柱φ48mm 有偏心4.8mm,中间圆柱φ35mm与左面圆柱φ35mm无偏心。
2.工艺分析(毛坯→成品过程)工序Ⅰ:毛坯铸造工序Ⅱ:时效处理工序Ⅲ:车φ35mm的外圆和右端面(粗车→半精车)工序Ⅳ:以φ35mm的外圆为基准,粗车其余的外圆和端面工序Ⅴ:夹紧工件车削并钻孔夹紧右端面精车左端面工序Ⅵ:调质处理工序Ⅶ:以左端面为定位基准精车使其他外圆和端面达到所需精度工序Ⅷ:车偏心圆柱:V形支承定位夹紧左Ф35mm圆柱,销定位左端面和工艺孔,工件偏移4.8mm,对φ48mm的外圆粗车,半精车和精车工序Ⅸ:检验3.定位方法和定位元件的选用使用V形支撑板与工件中间圆柱φ35mm构成4点定位,使用支承钉与工件左端面构成1点定位(见车偏心组合夹具简图2-2),在工艺孔上插入一根长销构成一点定位。
图2-2 车偏心组合夹具简图4.定位误差的计算此定位属于工件以外圆柱φ35k6mm为定位基准面,定位元件采用V形块,工序基准在圆柱中心,偏心距定位误差Δ的计算如下。
(1)5.基础件和支承件的选用和组装使用圆形基础板作为基础件,使用方形支承连接基础件和定位件(见图2-3)6. 夹紧件的选用和组装 使用V 形支承板及压板、螺栓、螺钉及螺母构成夹紧件(见图2-3)图2-3车偏心组合夹具元件爆炸图1-螺钉、螺母 2—连接板 3-螺栓 垫圈 4-圆形基础板5-定位键、螺钉 6-V 形支承板 7—螺母8—工件9—方形支承 10—螺栓、垫圈 11—方形垫板7. 偏心距的调整车削φ48mm 圆柱时,要求偏心4.8mm ,此时先应将右边V 形支撑板与压板之间距离从初始13mm 粗调到13+5.6=18.6mm ,应将作为定位的V 形支承板与压板之间距离从初始13mm 粗调到13-4.8=8.2mm ,然后精调V 形支承板与压板之间距离以满足偏心4.8mm 的要求。
8. 重点考虑的问题如何保证偏心距为4.8mm ?答:车削φ48mm 圆柱时,要求偏心4.8mm ,此时先应将右边V 形支撑板与压板之间距离从初始13mm 粗调到13+5.6=18.6mm ,应将作为定位的V 形支承板与压板之间距离从初始13mm 粗调到13-4.8=8.2mm ,然后精调V 形支承板与压板之间距离以满足偏心4.8mm 的要求。
三、铣槽用组合夹具组装1. 传动轴零件的简图要加工工件的工序简图如图3-1所示mm D 011.045sin 2016.02sin 2=⨯==∆ αδ图3-1 传动轴零件简图本工序要求加工传动轴零件上二个键槽14mm和12mm和1个孔φ10,要求以左右两个φ45mm的轴段和右端面为定位基准。
2. 工艺分析(工艺路线)工序Ⅰ:铸造工序Ⅱ:时效处理工序Ⅲ:车外圆(粗车→半精车→精车)工序Ⅳ:上铣床,钻出φ10mm的工艺孔工序Ⅴ:在铣床上,翻转φ10mm孔90度,根据工艺孔定位装夹,铣键槽工序Ⅵ:检验3. 定位方法和定位元件的选用使用两个V形角铁和一个支承钉为定位元件,每个V形角铁与工件φ45mm 的轴段构成2点定位,支承钉与工件右端面构成1点定位(见铣传动轴上键槽组合夹具简图3-2)图3-2 铣传动轴上键槽组合夹具工程简图4. 定位误差的计算此定位属于工件以外圆柱φ45k6mm 为定位基准面,定位元件采用V 形块,工序基准在圆柱的最低处,键槽底部至圆柱最低处定位误差Δ的计算如下。
(2)5. 基础件和支承件的选用和组装使用方形基础板作为基础件,其与V 形角铁和支承钉的组装方式见图3-3、3-4。
图3-3铣传动轴上键槽组合夹具轴测图mm D D 003.02016.045sin 2016.022sin 2=-⨯=-=∆ δαδ图3-4 铣传动轴上键槽组合夹具元件爆炸图6. 手动夹紧件的选用和组装使用压板、螺栓、螺钉及螺母构成夹紧件,其组装方式见图3-3、3-4。
7. 导向件的选用和组装使用方形支承钉构成对刀件、其组装方式见图3-3、3-4。
8. 对刀尺寸的调整铣键槽时将铣刀中心调整到相应夹具定位键槽的中心。
钻孔时将钻头中心调整到相应夹具定位键槽的中心。
9. 气动夹紧件的选用和组装使用气缸、连接板、压板、螺栓、螺钉及螺母构成夹紧件,其组装方式见3-5图3-5 铣传动轴上键槽组合夹具三维轴测图(气动夹紧)10. 重点考虑的问题(1)如何保证键槽和孔成90°位置?在铣床上装夹好已加工完外圆和端面的传动轴,不控制轴向的旋转的自由度,用铣床对φ10mm的孔进行加工,加工完成后,翻转φ10mm的孔90度,使用定位销定位,使孔的轴线水平于铣床平台,然后再使用铣刀加工键槽。
(2)如何调整对刀尺寸?具体问题具体分析如:铣键槽时将铣刀中心调整到相应夹具定位键槽的中心。
钻孔时将钻头中心调整到相应夹具定位键槽的中心。
四、钻孔用组合夹具组装1. 端盖零件的简图要加工工件的工序简图如图4-1所示。
图4-1 端盖零件简图2. 工艺分析(工艺路线)工序Ⅰ:铸造工序Ⅱ:时效处理工序Ⅲ:以外圆为基准粗车左端面和镗中心孔工序Ⅳ:精加工左端面和中心孔工序Ⅴ:以左端面和中心孔为定位基准六个钻孔(使用专用夹具)工序Ⅵ:检验3. 定位方法和定位元件的选用使用定位接头为定位元件,定位接头的顶面与工件左端面构成3点定位,定位接头销与工件中心孔构成2点定位(见钻端盖上分布孔组合夹具工程简图4-2、钻端盖上分布孔组合夹具三维轴测图4-3和钻端盖上分布组合夹具元件爆炸图4-4)图4-2 钻端盖上分布孔组合夹具工程简图4. 定位误差的计算此定位属于工件以内孔φ21H7mm为定位基准面,定位元件采用短销,轴线垂直放置,孔中心距的定位误差Δ的计算如下,其中孔的公差0.021mm,轴的公差0.013mm(组合夹具元件的精度为6级),最小间距为0.007(H7/g6)。
δ+=+∆δmin=++∆021.0dmm.0D041007013.0.05. 基础件和支承件的选用和组装使用长方形基础板和上抬式端齿分度台作为基础件,其与定位接头的组装方式见图4-3和图4-4。
图4-3钻端盖上分布孔组合夹具三维轴测图图4-4钻端盖上分布组合夹具元件爆炸图6. 夹紧件的选用和组装使用开口压板、螺栓、螺钉和螺母构成夹紧件,其组装方式见图4-3和图4-4。
7. 导向件的选用和组装使用钻模板、钻模、压板、螺栓、螺钉及螺母构成导向件,使用方形垫板、连接板、空心长方形支承为连接件,其组装方式见图4-3和图4-4。
8. 对刀尺寸的调整径向尺寸的调整:用螺钉调整钻模板与连接板之间的距离12.5mm(上抬式端齿分度台60mm,再加上方形垫板厚度20mm,减去工件孔中心距36mm,减去钻模中心至边缘距离139mm)。
角度尺寸的调整:先将上抬式端齿分度台的定位刻度对准0度,逆时针方向旋转分度台,使定位刻度对准18度,钻第1个孔,逆时针方向旋转分度台,使定位刻度对准71度,钻第2个孔,逆时针方向旋转分度台,使定位刻度对准180-51=129度,钻第3个孔,逆时针方向选族分度台,使定位刻度对准180度,钻第4个孔,逆时针方向旋转分度台,使定位刻度对准180+53=233度,钻第5个孔,逆时针方向旋转分度台,使定位刻度对准360-36=324度,钻第6个孔。
9. 重点考虑的问题(1)选用哪一个孔作为基准?为了减少装夹次数,应该尽量少的选择定位基准,选择所有孔中位于最外边的孔作为基准,减少分度台的移动,在一次定位装夹好后,只用每次调整分度台的角度,使其达到加工要求的角度,再加工其他孔。
(2)如何方便工加工后取出?设计一个可以上升和下降的装置,装夹好工件后,上升到一个位置则不再产生移动,再加工好后,按一下下降开关,可以下降到初始位置,初始位置的搞的应是一个方便工件取出的高度。
五、加工中心上镗孔用组合夹具组装1. 支座零件的简图要加工工件的工序简图如图5-1所示。
图5-1 支座零件简图2. 工艺分析(工艺路线)基面的选择:从零件图中可知基本的尺寸都是以下端面为设计基准,因此,根据“基准重合”和“基准统一”的原则必须首先加工出下端面,作为后续工序的精基准。
根据粗基准的保证相互位置的原则,选择铸件毛坯定位点作为粗基准来加工下端面,然后由下端面为基准加工定位孔,再以下端面和定位孔加工左右端面的孔。