管道焊缝射线探伤数量和合格级别
管道焊缝射线探伤数量和合格级别
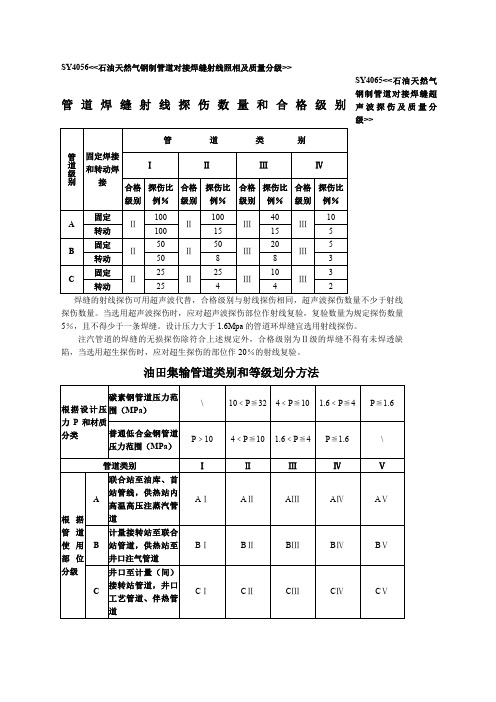
SY4056<<石油天然气钢制管道对接焊缝射线照相及质量分级>>
SY4065<<石油天然气钢制管道对接焊缝超
声波探伤及质量分
级>>
焊缝的射线探伤可用超声波代替,合格级别与射线探伤相同,超声波探伤数量不少于射线探伤数量。
当选用超声波探伤时,应对超声波探伤部位作射线复验,复验数量为规定探伤数量5%,且不得少于一条焊缝。
设计压力大于1.6Mpa 的管道环焊缝宜选用射线探伤。
注汽管道的焊缝的无损探伤除符合上述规定外,合格级别为Ⅱ级的焊缝不得有未焊透缺陷,当选用超生探伤时,应对超生探伤的部位作20%的射线复验。
油田集输管道类别和等级划分方法
管道焊缝射线探伤数量和合格级别
焊接层数及焊条直径
焊道焊接应采用多层焊,焊道熔渣应清除干净,并进行外观检查,合格后可进行下道焊接。
低氢焊条在常温下4h应重新烘干,重复烘干次数不得超过两次。
焊缝质量标准及等级

管道类别Ⅰ(1)毒性程度为极度危害的流体管道;(2)设计压力大于或等于10MPa的可燃流体、有毒流体的管道;(3)设计压力大于或等于4MPa、小于10MPa,且设计温度大于等于400℃的可燃流体、有毒流体的管道;(4)设计压力大于或等于10MPa,且设计温度大于或等于400℃的非可燃流体、无毒流体的管道;(5)设计文件注明为剧烈循环工况的管道;(6)设计温度低于-20℃的所有流体管道;(7)夹套管的内管;(8)按本规范第8。
5。
6条规定做替代性试验的管道;(9)设计文件要求进行焊缝100%无损检测的其他管道.Ⅱ(1)设计压力大于或等于4MPa、小于10MPa,设计温度低于400℃,毒性程度为高度危害的流体管道;(2)设计压力小于4MPa,毒性程度为高度危害的流体管道;(3)设计压力大于或等于4MPa、小于10MPa,设计温度低于400℃的甲、乙类可燃气体和甲类可燃液体的管道;(4)设计压力大于或等于10MPa,且设计温度小于400℃的非可燃流体、无毒流体的管道;(5)设计压力大于或等于4MPa、小于10MPa,且设计温度大于等于400℃的非可燃流体、无毒流体的管道;(6)设计文件要求进行焊缝20%无损检测的其他管道。
Ⅲ(1)设计压力大于或等于4MPa、小于10MPa,设计温度低于400℃,毒性程度为中毒和轻度危害的流体管道;(2)设计压力小于4MPa的甲、乙类可燃气体和甲类可燃液体管道;(3)设计压力大于或等于4MPa、小于10MPa,设计温度低于400℃的乙、丙类可燃液体管道;(4)设计压力大于或等于4MPa、小于10MPa,设计温度低于400℃的非可燃流体、无毒流体的管道;(5)设计压力大于1MPa小于4MPa,设计温度高于或等于400℃的非可燃流体、无毒流体的管道;(6)设计文件要求进行焊缝10%无损检测的其他管道。
Ⅳ(1)设计压力小于4MPa,毒性程度为中毒和轻度危害的流体管道;(2)设计压力小于4MPa的乙、丙类可燃液体管道;(3)设计压力大于1MPa小于4MPa,设计温度低于400℃的非可燃流体、无毒流体的管道;(4)设计压力小于或等于1MPa,且设计温度大于185℃的非可燃流体、无毒流体的管道;(5)设计文件要求进行焊缝5%无损检测的其他管道。
管道焊缝无损探伤拍片数量的确定
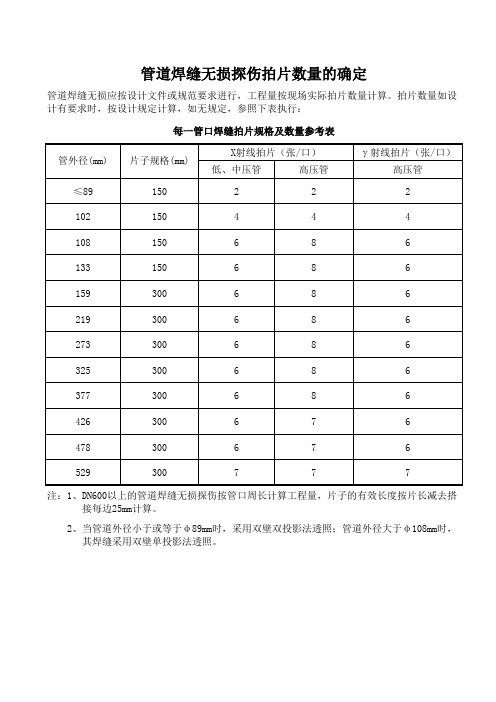
片数量如设
管道焊缝无损探伤拍片数量的确定
管道焊缝无损应按设计文件或规范要求进行,工程量按现场实际拍片数量计算。拍片数量如设 计有要求时,按设计规定计算,如无规定,参照下表执行:
每一管口焊缝拍片规格及数量参考表
管外径(mm)
片子规格(mm)
X射线拍片(张/口)
低、中压管
高压管
γ 射线拍片(张/口) 高压管
≤89
150
2
2
2
102
150
4
4
4
108
150
6
8
6
133
150
6
8
6
159
300
6
8
6
219
30068 Nhomakorabea6
273
300
6
8
6
325
300
6
8
6
377
300
6
8
6
426
300
6
7
6
478
300
6
7
6
529
300
7
7
7
注:1、DN600以上的管道焊缝无损探伤按管口周长计算工程量,片子的有效长度按片长减去搭 接每边25mm计算。
燃气无损探伤
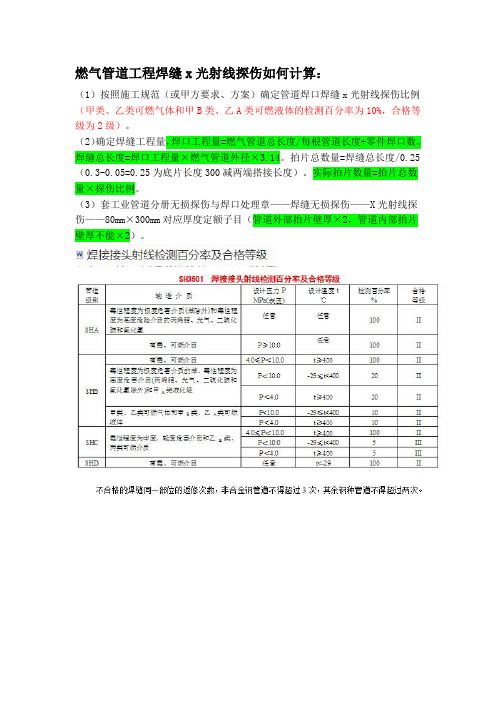
燃气管道工程焊缝x光射线探伤如何计算:
(1)按照施工规范(或甲方要求、方案)确定管道焊口焊缝x光射线探伤比例(甲类、乙类可燃气体和甲B类、乙A类可燃液体的检测百分率为10%,合格等级为2级)。
(2)确定焊缝工程量,焊口工程量=燃气管道总长度/每根管道长度+零件焊口数。
焊缝总长度=焊口工程量×燃气管道外径×3.14。
拍片总数量=焊缝总长度/0.25(0.3-0.05=0.25为底片长度300减两端搭接长度)。
实际拍片数量=拍片总数量×探伤比例。
(3)套工业管道分册无损探伤与焊口处理章——焊缝无损探伤——X光射线探伤——80mm×300mm对应厚度定额子目(管道外部拍片壁厚×2,管道内部拍片壁厚不能×2)。
压力管道安装施工有关无损检测的规定
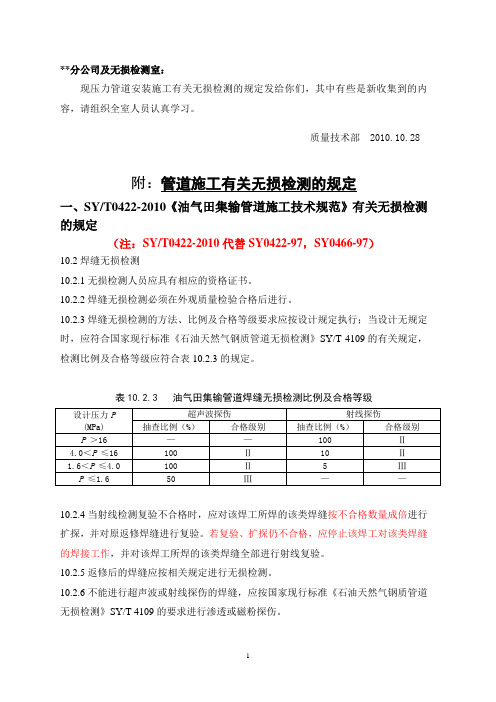
**分公司及无损检测室:现压力管道安装施工有关无损检测的规定发给你们,其中有些是新收集到的内容,请组织全室人员认真学习。
质量技术部 2010.10.28附:管道施工有关无损检测的规定一、SY/T0422-2010《油气田集输管道施工技术规范》有关无损检测的规定(注:SY/T0422-2010代替SY0422-97,SY0466-97)10.2焊缝无损检测10.2.1无损检测人员应具有相应的资格证书。
10.2.2焊缝无损检测必须在外观质量检验合格后进行。
10.2.3焊缝无损检测的方法、比例及合格等级要求应按设计规定执行;当设计无规定时,应符合国家现行标准《石油天然气钢质管道无损检测》SY/T 4109的有关规定,检测比例及合格等级应符合表10.2.3的规定。
表10.2.3 油气田集输管道焊缝无损检测比例及合格等级10.2.4当射线检测复验不合格时,应对该焊工所焊的该类焊缝按不合格数量成倍进行扩探,并对原返修焊缝进行复验。
若复验、扩探仍不合格,应停止该焊工对该类焊缝的焊接工作,并对该焊工所焊的该类焊缝全部进行射线复验。
10.2.5返修后的焊缝应按相关规定进行无损检测。
10.2.6不能进行超声波或射线探伤的焊缝,应按国家现行标准《石油天然气钢质管道无损检测》SY/T 4109的要求进行渗透或磁粉探伤。
二、《石油天然气建设工程施工质量验收规范站内工艺管道工程》SY/T 4203-2007有关无损检测的规定8.1.27 焊缝无损检测应由GB/T9445考试合格并取得相应资格证书的检测人员承担,评片应由取得Ⅱ级资格证书及以上的检测人员承担。
8.1.28 焊缝外观检查合格后应对其进行无损检测。
无损检测应按SY/T4109的管道执行。
8.1.29无损检测的比例及验收合格等级应符合设计要求。
如没有规定时,应按下列管道执行:a) 管道对接焊缝无损检测数量及合格等级应符合表8的规定。
b) 穿越站场道路的管道焊缝、试压后连头的焊缝应进行100%射线照相检查。
NO.21 管道焊缝外观检查报告

观 最 大 焊 缝(mm余) 高 质 (mm) 量 返修后检查合
格的焊口数
(个)
质量评定
1、按 CJJ33—2005 规定,外观质量合格级别:100%射线探伤的焊缝不低于Ⅱ级,抽查射线探伤的焊缝不低于Ⅲ级。
2、GB50683-2011 第 8.1.2 条管道焊缝Ⅱ级、Ⅲ级外观质量:
①不允许有(裂纹、气孔、夹渣、未焊透、未熔合、未焊满)。 ②咬边:深度:纵缝不允许。其他焊缝≤0.05T 且≤0.5mm;连续长度≤100 mm,两侧总长度≤10%焊缝全长。 ③余高:T≤6mm,δ≤1. 5mm;T≤6~13mm,δ≤3. 0 ④根部凹陷:Ⅱ级深度≤0.2+0.02T 且≤0.5mm;长度不限。Ⅲ级≤0.2+0.02T 且≤1mm。 其中:T—母材厚度;t—焊缝设计厚度;δ—焊缝余高。
管道焊缝外观检查报告
工程名称
执行标准 CJJ33-2005、GB50683-2011
焊接方法 □手工电弧焊;√ 氩弧焊+手工电弧焊
桩号 管子Байду номын сангаас格
焊 口 总 数(个)
检查比例
返 修 焊 口 数(个)
表面缺陷(裂纹、气
孔、夹渣、未焊透、 未熔合、未焊满)
管 根部 道 凹陷
深度 长度
焊
咬
缝边 外
深度
最大连 续长度
施工单位技术人员:
监理单位监理工程师:
建设单位现场代表:
年月日
年月日
年月日
焊缝合格标准

焊缝合格级别及无损检测要点一、长输管道:1.SY0410—98《输油输气管道线路工程施工及验收规范》第7.3.2条:RT执行SY4056—93;UT执行SY4065—93合格级别:输油:P设≤6.4MPa Ⅲ级P设>6.4MPa Ⅱ级输气:P设≤4MPa 一、二级地区Ⅲ级;三、四级地区Ⅱ级P设>4MPa Ⅱ级第7.3.4条:输油管道的探伤比例可任选下面其中之一:100%UT后,对每个焊工或机组每天完成数量的5%作射线复验只进行RT抽查,抽查比例为每个焊工或作业机组每天完成数量的15% 。
第7.3.5条:输气管道的探伤比例:100%UT后,对每个焊工或作业机组每天完成数量的抽查比例:一级地区5%二级地区10%三级地区15%四级地区20%只进行RT抽查,对每个焊工或作业机组每天完成数量的抽查比例:一级地区10%二级地区15%三级地区40%四级地区75%第7.3.6条:抽查时,如每天的焊口数量比例达不到比例要求时,可以每公里为一个检验段,并按规定的比例数随焊随查,均匀的复验、抽查。
第7.3.7条:射线探伤复验,抽查中,有一个焊口不合格,应对该焊工或机组段焊接焊口加倍检查,再不合格,则其余焊口逐个RT探伤第7.3.8条:穿越焊口,钢管与弯头连接的焊口,试压后连头的碰口应进行100%RT。
第7.3.9条:×60及以上级别管材,返修后应按《常压钢制焊接储罐及管道渗透检测技术标准》SY/T0443进行渗透检查。
第7.3.10条:探伤人员应取得相关主管部门颁发的证书。
2.SY0470—2000《石油天然气跨越工程施工及验收规范》第5.3.2条:焊缝外观检查合格之后,应进行无损探伤。
焊缝无损探伤应符合下列规定:跨越管道环向焊缝应进行100%射线探伤。
对射线探伤难度大的个别环向焊缝部位,经有关部门共同商定可用超声波探伤代替射线探伤,但其数量不准超过总数10%。
RT符合SY4056 Ⅱ级合格;UT符合SY4065 Ⅱ级合格二、集输管道:1.SY0466—97《天然气集输管道施工及验收规范》第5.2条无损探伤:第5.2.1条:无损探伤人员必须具备劳动部门颁发的Ⅰ级以上资格证,评片人员具有Ⅱ级及其以上资格;第5.2.2条:焊缝无损探伤必须在外观质量检验合格后进行;第5.2.3条:设计无规定时,管道环缝100%UT,每个焊工所焊的各类焊缝应第5.2.5条:当RT复验不合格,应对该焊工所焊该类焊缝按原射线探伤复验数量补充探伤,仍不合格,停止其工作,并对其于焊工所焊焊缝进行100%RT 复验。
管道焊缝射线探伤数量和合格年级别
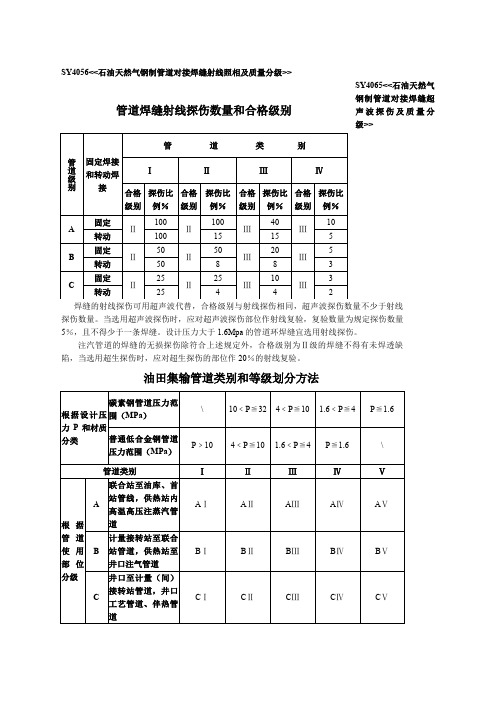
SY4056<<石油天然气钢制管道对接焊缝射线照相及质量分级>>
SY4065<<石油天然气钢制管道对接焊缝超
声波探伤及质量分级>>
焊缝的射线探伤可用超声波代替,合格级别与射线探伤相同,超声波探伤数量不少于射线探伤数量。
当选用超声波探伤时,应对超声波探伤部位作射线复验,复验数量为规定探伤数量5%,且不得少于一条焊缝。
设计压力大于1.6Mpa 的管道环焊缝宜选用射线探伤。
注汽管道的焊缝的无损探伤除符合上述规定外,合格级别为Ⅱ级的焊缝不得有未焊透缺陷,当选用超生探伤时,应对超生探伤的部位作20%的射线复验。
油田集输管道类别和等级划分方法
管道焊缝射线探伤数量和合格级别
焊接层数及焊条直径
焊道焊接应采用多层焊,焊道熔渣应清除干净,并进行外观检查,合格后可进行下道焊接。
低氢焊条在常温下4h应重新烘干,重复烘干次数不得超过两次。
射线探伤标准

射线探伤标准5.1.1 范围本条规定适用于厚度为2mm至400mm的碳素钢、低合金钢、奥氏体不锈钢、镍及镍合金制承压设备,以及厚度为2mm至80mm的铜及铜合金制承压设备的熔化焊对接焊接接头射线检测的质量分级。
管子和压力管道环向对接焊接接头射线检测质量分级按照第6章规定执行。
5.1.2 缺陷类型对接焊接接头中的缺陷按性质可分为裂纹、未熔合、未焊透、条形缺陷和圆形缺陷共五类。
5.1.3 质量分级依据根据对接接头中存在的缺陷性质、数量和密集程度,其质量等级可划分为Ⅰ、Ⅱ、Ⅲ、Ⅳ级。
5.1.4 质量分级一般规定5.1.4.1 I级对接焊接接头内不允许存在裂纹、未熔合、未焊透和条形缺陷。
5.1.4.2Ⅱ级和Ⅲ级对接焊接接头内不允许存在裂纹、未熔合和未焊透。
5.1.4.3对接焊接接头中缺陷超过Ⅲ级者为Ⅳ级。
5.1.4.4当各类缺陷评定的质量级别不同时,以质量最差的级别作为对接焊接接头的质量级别。
5.1.5 圆形缺陷的质量分级5.1.5.1圆形缺陷用圆形缺陷评定区进行质量分级评定,圆形缺陷评定区为一个与焊缝平行的矩形,其尺寸见表8.圆形缺陷评定区应选在缺陷最严重的区域。
表8 缺陷评定区(mm)母材公称厚度T 评定区尺寸25 10×1025~100 10×20100 10×305.1.5.2在圆形缺陷评定区内或与圆形缺陷评定区边界线相割的缺陷均应划入评定区内。
将评定区内的缺陷按表9的规定换算为点数,按表10的规定评定对接焊接接头的质量级别。
表9 缺陷点数换算表缺陷长径,mm 缺陷点数1 l1~2 22~3 33~4 64~6 106~8 158 25表10 各级别允许的圆形缺陷点数评定区(mm×mm) 母材公称厚度T,mmI级 II级 UI级10 1 3 610~15 2 6 1215~25 3 9 1825~50 4 12 2450~100 5 15 3010×30 6 18 36100 6 18 36 Ⅳ级注:当母材公称厚度不同时,取较薄板的厚度。
管道焊缝无损探伤拍片数量的确定

管道焊缝无损应按设计文件或规范要求进行,工程量按现场实际拍片数量计算。拍片数量如设 计有要求时,按设计规定计算,如无规定,参照下表执行: 每一管口焊缝拍片规格及数量参考表 管外径(mm) ≤89 102 108 133 159 219 273 325 377 426 478 529 片子规格(mm) 150 150 150 150 300 300 300 300 300 300 300 300 X射线拍片(张/口) 低、中压管 2 4 6 6 6 6 6 6 6 6 6 7 高压管 2 4 8 8 8 8 8 8 8 7 7 7 γ 射线拍片(张/口) 高压管 2 4 6 6 6 6 6 6 6 6 6 7
注:1、DN600以上的管道焊缝无损探伤按管口周长计算工程量,片子的有效长度按片长减去搭 接每边25mm计算。 2、当管道外径小于或等于φ 89mm时,采用双壁双投影法透照;管道外径大于φ 108mm时, 其焊缝采用双壁单投影法透照。
片数量如设ຫໍສະໝຸດ
管道焊接探伤比例
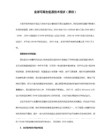
100%和5%就两种
规范是这样规定的:
7.4.2管道焊缝的射线照相检验或超声波检验应及时进行。当抽样检验
时,应对每质检人员共同确定。
7.4.3管道焊缝的射线照相检验数量应符合下列规定:
7.4.3.1下列管道焊缝应进行100%射线照相检验,其质量不得低于
(5)设计文件要求进行100%射线照相检验的其他管道。
7.4.3.2输送设计压力小于等于1MPa且设计温度小于400℃的非可燃流体管道、无毒流体管道的焊缝,可不进行射线照相检验。
7.4.3.3其他管道应进行抽样射线照相检验,抽检比例不得低于5%,
其质量不得低于III级。抽检比例和质量等级应符合设计文件的要求。
II级:
(1)输送剧毒流体的管道;
( 2 )输送设计压力大于等于 10MPa 或设计压力大于等于 4MPa
且设计温度大于等于400℃的可燃流体、有毒流体的管道;
( 3 )输送设计压力大于等于 10MPa 且设计温度大于等于 400 ℃
的非可燃流体、无毒流体的管道;
(4)设计温度小于-29℃的低温管道。
射线探伤标准

5.1.1范围
本条规定适用于厚度为2mm~400mm的碳素钢、低合金钢、奥氏体不锈钢、镍及镍合金制承压设
备,以及厚度为2mm~80mm的铜及铜合金制承压设备的熔化焊对接焊接接头射线检测的质量分级。
管子和压力管道环向对接焊接接头射线检测质量分级按照第6章规定执行。
5.1.2缺陷类型
对接焊接接头中的缺陷按性质可分为裂纹、未熔合、未焊透、条形缺陷和圆形缺陷共五类。
5.1.3质量分级依据
根据对接接头中存在的缺陷性质、数量和密集程度,其质量等级可划分为Ⅰ、Ⅱ、Ⅲ、Ⅳ级。
5.1.4 质量分级一般规定
5.1.4.1 I级对接焊接接头内不允许存在裂纹、未熔合、未焊透和条形缺陷。
5.1.4.2Ⅱ级和Ⅲ级对接焊接接头内不允许存在裂纹、未熔合和未焊透。
5.1.4.3对接焊接接头中缺陷超过Ⅲ级者为Ⅳ级。
5.1.4.4 当各类缺陷评定的质量级别不同时,以质量最差的级别作为对接焊接接头的质量级别。
5.1.5圆形缺陷的质量分级
5.1.5.1 圆形缺陷用圆形缺陷评定区进行质量分级评定,圆形缺陷评定区为一个与焊缝平行的矩形,其尺寸见表8。
圆形缺陷评定区应选在缺陷最严重的区域。
表8 缺陷评定区 mm
5.1.5.2 在圆形缺陷评定区内或与圆形缺陷评定区边界线相割的缺陷均应划入评定区内。
将评定区内的缺陷按表9的规定换算为点数,按表10的规定评定对接焊接接头的质量级别。
表9 缺陷点数换算表
表10 各级别允许的圆形缺陷点数。
工业管道的焊接

工业管道的焊接第一节材料要求第1.1.1 条管道组成件必须具有制造厂的合格证明书,否则应补所缺项目的检验。
第 1.1.2 条焊接工程中所用的母材和焊接材料应具备出厂质量合格证明书或质量复验报告。
第 1.1.3 条焊接工程中应优先选用已列入国家标准或部颁标准的母材和焊接材料。
第 1.1.4 条如设计选用未列入标准的母材和焊接材料,应说明该材料的可焊性,并提出满足设计要求的焊接工艺试验资料。
第二节主要机具第1.2.1 条焊接设备:包括交流电焊机、直流电焊机、氩弧焊机。
第 1.2.2 条机具包括:坡口加工机、切割机、角向磨光机、台式钻诃、等离子弧切割机、焊矩。
第 1.2.3 条计量器具包括:柜式水平仪、焊接检验尺,内外径千分尺、内外径卡尺、深度游标尺、高度游标尺、万能角度尺、光学水准仪、光学经纬仪。
第1.2.4 条液压千斤顶、液压式万能材料试验机、热处理设备、微控电子式拉力试验机、便携式数显里氏硬度计、光谱分析仪。
第1.2.5 条探伤设备及其它:X 射线擦伤机、超声波探伤仪、梯粉探伤机、智能化X 射线探伤机、远红外线干燥机。
第三节作业条件第1.3.1 条与管道有关的土建工程、金属结构工程检验合格,满足管道安装要求。
第1.3.2 条与管道连接的机械设备,容器已找正固定,或已确定管口方位及标高。
第1.3.3 条管道组成件已清理完毕,并满足设计规定的特殊清理要求。
第1.3.4 条管道加工及预制完成,并编号。
第1.3.5 条焊接平台按工程要求制作完成。
第四节操作工艺第 1.4.1 条工艺流程:备料→焊工资格认可→坡口制备→焊接工艺评定→夹具准备→装配定位→施焊→焊后处理→焊接检验第 1.4.2 条焊工1.压力管道所用焊工必须取得由长沙市技术监督局批准颁发的《锅炉压力容器焊工合格证》,且只限于焊接《合格证》内规定的项目。
2.“压力容器焊工合格证”有效期为三年,超过有效期后必须重新办理,否则视为无效。
3.焊工累计合格项目满足GB235-82 中表4.4.1 规定的所有材质的焊接。
管道的焊接与探伤的相关要求规范要求

管道的焊接与探伤的相关要求规范要求管道的焊接与探伤的相关规范要求《压力管道规范工业管道》GB/T20801-2006是基础性标准。
规定了工业金属压力管道设计、制作、安装、检验和安全防护的基本要求。
GB/T 20801《压力管道规范工业管道》由六个部分组成:——第1部分:总则;——第2部分:材料;——第3部分:设计和计算;——第4部分:制作与安装;——第5部分:检验与试验;——第6部分:安全防护。
适用于《特种设备安全监察条例》规定的“压力管道”中金属工业管道的设计和建造。
基础标准只是最低标准。
所以应在满足基础标准的前提下,通过其他“标准规范”或“工程规定”纳入其他需要采纳的材料、管道元件、设计、施工、检验试验和验收及其附加要求。
GB/T20801.4-2006 压力管道规范—工业管道第4部分:制作与安装对焊接作了基础性规定7 焊接7.1 焊接工艺评定和焊工技能评定7.2 焊接材料7.3 焊接环境7.4 焊前准备7.5 焊接的基本要求7.6 焊缝设置等作了详细可操作的规定。
TSG D0001-2009《压力管道安全技术监察规程-工业管道》第六十七条对应当采用氩弧焊焊接的金属管道作了规定,GC1 级管道的单面对接焊接接头,设计温度低于或者等于-200C 的管道,淬硬倾向较大的合金钢管道,不锈钢以及有色金属管道应当采用氩弧焊进行根部焊接,且表面不得有电弧擦伤。
GB/T20801.5-2006 压力管道规范—工业管道第5 部分检验与试验对检验与试验作了基础性规定6.1.1一般规定 a)压力管道的检查等级分为Ⅰ、Ⅱ、Ⅲ、Ⅳ、Ⅴ五个等级,其中Ⅰ级最高,Ⅴ级最低;6.1.2按管道级别和剧烈循环工况确定管道检查等级:a) GC3 级管道的检查等级应不低于Ⅴ级;b) GC2 级管道的检查等级应不低于Ⅳ级;c) GC1 级管道的检查等级应不低于Ⅱ级;d) 剧烈循环工况管道的检查等级应不低于Ⅰ级。
6.1.3 按材料类别和公称压力确定管道检查等级:a)除GC3 级管道外,公称压力不大于PN50 的碳钢管道(本规范无冲击试验要求)的检查等级应不低于Ⅳ级;b) 除GC3 级管道外,下列管道的检查等级应不低于Ⅲ级:1)公称压力不大于PN50 的碳钢(本规范要求冲击试验)管道;2) 公称压力不大于PN110 的奥氏体不锈钢管道。
工艺管线焊缝探伤等级及合格标准

工程直径大于等于500mm
25
注解:
1、P=设计压力(Mpa) T=设计温度(℃) δ=主管厚度(mm) δb=支管厚度(mm) NPS=工程直径
2、VT=外观检测 RT=X射线检测 MT=磁粉检测 PT=着色渗透检测 UT=超声波检测
3、焊接接头的无损检测应执行JB4730-94 RT检测时: ①、检测比例大于5% Ⅱ级合格 ②、检测比例5% Ⅲ级合格
UT检测时: ①、检测比例100% Ⅰ级合格 ②、检测比例为局部 Ⅱ级合格
MT/PT检测时:Ⅰ级合格
4、在被检测的焊接接头中,固定焊的焊接接头不得少于40%,且不少于1个焊接接头。
5、焊接接头的抽样检测,如有不合格时,应按该焊工的不合格数加倍检验,若仍有不合格,则应全部检验。
6、按照GMAW或FCAW工艺进行的环缝焊接应按照5%的比例进行100%RT或UT检验。
7、无损检测时:①当设计文件规定采用超声波检测,应按设计文件规定执行;
②当设计文件规定采用射线检测但由于条件限制需改用超声波检测代替,应书面方式提请采用超声波检测方法,以获得赛科的批准并征得设计单位同意。
25。
环氧乙烷管道焊缝检查等级
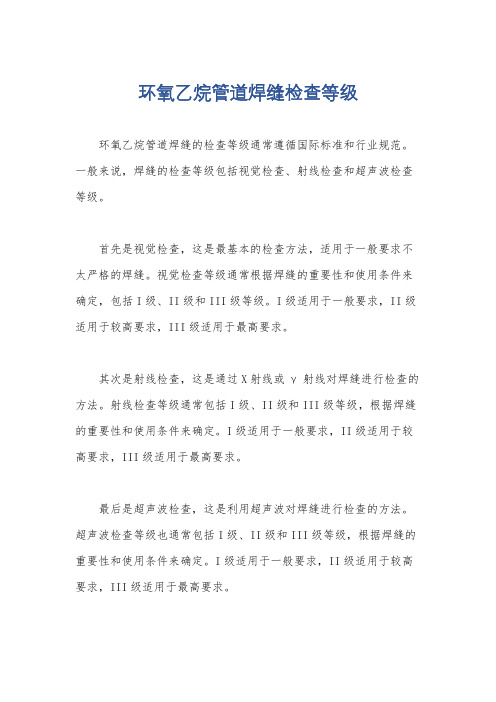
环氧乙烷管道焊缝检查等级
环氧乙烷管道焊缝的检查等级通常遵循国际标准和行业规范。
一般来说,焊缝的检查等级包括视觉检查、射线检查和超声波检查等级。
首先是视觉检查,这是最基本的检查方法,适用于一般要求不太严格的焊缝。
视觉检查等级通常根据焊缝的重要性和使用条件来确定,包括I级、II级和III级等级。
I级适用于一般要求,II级适用于较高要求,III级适用于最高要求。
其次是射线检查,这是通过X射线或γ射线对焊缝进行检查的方法。
射线检查等级通常包括I级、II级和III级等级,根据焊缝的重要性和使用条件来确定。
I级适用于一般要求,II级适用于较高要求,III级适用于最高要求。
最后是超声波检查,这是利用超声波对焊缝进行检查的方法。
超声波检查等级也通常包括I级、II级和III级等级,根据焊缝的重要性和使用条件来确定。
I级适用于一般要求,II级适用于较高要求,III级适用于最高要求。
总的来说,环氧乙烷管道焊缝的检查等级应根据具体的工程要求和相关标准来确定,以确保焊缝的质量和安全性。
同时,在进行焊缝检查时,还需要考虑管道的材质、厚度、工作压力等因素,以选择合适的检查方法和等级。
管道探伤焊口计算表
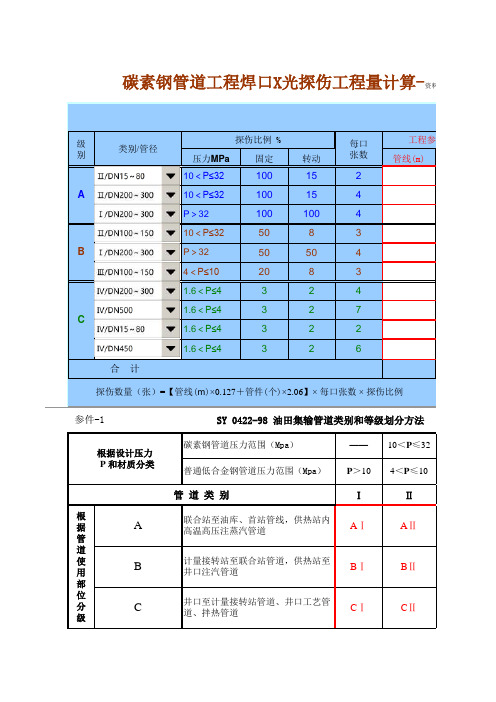
合
计
探伤数量(张)=【管线(m)× 0.127+管件(个)× 2.06】× 每口张数 × 探伤比例
参件-1
根据设计压力 P 和材质分类
SY 0422-98 油田集输管道类别和等级划分方法
碳素钢管道压力范围(Mpa) 普通低合金钢管道压力范围(Mpa) —— P>10 Ⅰ 10<P≤32 4<P≤10 Ⅱ
14 10 14 13 21 14 10 9 21 22 C B A
100 100 100 50 50 20 3 3 3 3
15 15 100 8 50 8 2 2 2 2
2 4 4 3 4 3 4 7 2 6
Ⅱ/DN200~300 Ⅰ/DN200~300 Ⅱ/DN100~150 Ⅰ/DN200~300 Ⅲ/DN100~150 Ⅳ/DN200~300 Ⅳ/DN500 Ⅳ/DN15~80 Ⅳ/DN450
碳素钢管道工程焊口X光探伤工程量计算- 资料来源筑龙网
级 别
类别/管径
Ⅱ/DN15~80
探伤比例 % 压力MPa 10<P≤32 10<P≤32 P>32 10<P≤32 P>32 4<P≤10 1.6<P≤4 1.6<P≤4 1.6<P≤4 1.6<P≤4 固定 转动
每口 张数
工程参数录入 管线(m)
管 道 类 别
根 据 管 道 使 用 部 位 分 级
A B C
联合站至油库、首站管线,供热站内 高温高压注蒸汽管道 计量接转站至联合站管道,供热站至 井口注汽管道 井口至计量接转站管道、井口工艺管 道、拌热管道
AⅠ
AⅡ
BⅠ
BⅡ
CⅠ
CⅡ
参件-2 管 道 级 别 A B C 固定焊接 或 转动焊接 固 转 固 转 固 转 定 动 定 动 定 动
管道环焊缝射线检测工艺规程(修改版)

管道环焊缝射线检测工艺规程(修改版)管道环焊缝射线检测工艺规程ZJ/GC 01-031.范围本规程规定了射线检测人员资格、所用设备、器材、检测工艺和质量分级等。
本规程适用X射线照相方法和AB级质量要求检查壁厚为2-30mm的低碳钢和低合金钢质石油天然气长输、集输管道及其它石油管线的环向对接焊缝。
2. 规范性引用文件下列文件的条款通过本规程引用而成为本规程的条款。
凡其是注日期的引用文件,其随后所有的修改单(不包括勘误的内容)或修订不适用于本规程。
凡是不注日期的引用文件,其最新版本适用于本规程。
SY4056 石油天然气钢质管道对接焊缝射线照相及质量分级GB4792 放射线卫生防护基本标准GB561 线型象质计GB/T12605 钢管环焊缝熔化焊对接接头射线照相工艺及质量分级ZJ/GD03 现场射线检测安全规定3.检测人员3.1从事射线探伤人员必须经专业技术培训,掌握一定的探伤基础知识和操作技能及安全、卫生防护知识,并持有相关部门颁发的相应资格证书。
3.2 评片人员具备校正视力≦1.0,具能判别出400mm距离处高0.5mm、间距0.5mm的一组印刷字母。
3.3 进行射线检测时,检测人员必须严格遵守国家标准GB4792《放射线卫生防护基本标准》和ZJ/GD03 《现场射线检测安全规定》中的有关规定。
当工作环境不符合本规范工艺要求和安全规定时,检测人员有权拒绝探伤。
4. 设备和器材4.1 公司现有设备及其透照厚度范围见表1。
表14.2 在满足射线穿透力的前提下,宜使用较低管电压,曝光量不低于15mAmin,以提高射线照相灵敏度,如管径小于或等于114mm的对接环缝采用双壁双影法时,可适当提高管电压,以减少曝光时间和增大宽容度。
4.3 胶片和增感屏4.3.1 在满足灵敏度要求的情况下,X射线一般选用J2型胶片,如天津III型、上海A、乐凯等。
4.3.2 射线透照采用铅箔增感屏,不得采用荧光增感屏和荧光金属增感屏。
- 1、下载文档前请自行甄别文档内容的完整性,平台不提供额外的编辑、内容补充、找答案等附加服务。
- 2、"仅部分预览"的文档,不可在线预览部分如存在完整性等问题,可反馈申请退款(可完整预览的文档不适用该条件!)。
- 3、如文档侵犯您的权益,请联系客服反馈,我们会尽快为您处理(人工客服工作时间:9:00-18:30)。
SY4056<<石油天然
气钢制管道对接焊缝射线照相及质量
分级>>
SY4065<<石油天然
气钢制管道对接焊缝超声波探伤及质量分级>>
焊缝的射线探伤可用超声波代替,合格级别与射线探伤相同,超声波探伤数量不少于射线探伤数量。
当选用超声波探伤时,应对超声波探伤部位作射线复验,复验数量为规定探伤数量5%,且不得少于一条焊缝。
设计压力大于1.6Mpa 的管道环焊缝宜选用射线探伤。
注汽管道的焊缝的无损探伤除符合上述规定外,合格级别为Ⅱ级的焊缝不得有未焊透缺陷,当选用超生探伤时,应对超生探伤的部位作20%的射线复验。
油田集输管道类别和等级划分方法
管道焊缝射线探伤数量和合格级别
焊接层数及焊条直径
焊道焊接应采用多层焊,焊道熔渣应清除干净,并进行外观检查,合格后可进行下道焊接。
低氢焊条在常温下4h应重新烘干,重复烘干次数不得超过两次。