固相烧结
烧结的问题和解答

烧结的问题和解答第九章烧结1、解释下列名词(1)烧结:粉料受压成型后在高温作用下而致密化的物理过程。
烧成:坯体经过高温处理成为制品的过程,烧成包括多种物理变化和化学变化。
烧成的含义包括的范围广,烧结只是烧成过程中的一个重要部分。
(2)晶粒生长:无应变的材料在热处理时,平均晶粒尺寸在不改变其分布的情况下,连续增大的过程。
二次再结晶:少数巨大晶粒在细晶消耗时成核长大过程。
(3)固相烧结:固态粉末在适当的温度、压力、气氛和时间条件下,通过物质与气孔之间的传质,变为坚硬、致密烧结体的过程。
液相烧结:有液相参加的烧结过程。
2、详细说明外加剂对烧结的影响?答:(1)外加剂与烧结主体形成固溶体使主晶格畸变,缺陷增加,有利结构基元移动而促进烧结;(2)外加剂与烧结主体形成液相,促进烧结;(3)外加剂与烧结主体形成化合物,促进烧结;(4)外加剂阻止多晶转变,促进烧结;(5)外加剂起扩大烧结范围的作用。
3、简述烧结过程的推动力是什么?答:能量差,压力差,空位差。
4、说明影响烧结的因素?答:(1)粉末的粒度。
细颗粒增加了烧结推动力,缩短原子扩散距离,提高颗粒在液相中的溶解度,从而导致烧结过程的加速;(2)外加剂的作用。
在固相烧结中,有少量外加剂可与主晶相形成固溶体,促进缺陷增加,在液相烧结中,外加剂改变液相的性质(如粘度,组成等),促进烧结。
(3)烧结温度:晶体中晶格能越大,离子结合也越牢固,离子扩散也越困难,烧结温度越高。
(4)保温时间:高温段以体积扩散为主,以短时间为好,低温段为表面扩散为主,低温时间越长,不仅不引起致密化,反而会因表面扩散,改变了气孔的形状而给制品性能带来损害,要尽可能快地从低温升到高温,以创造体积扩散条件。
(5)气氛的影响:氧化,还原,中性。
(6)成形压力影响:一般说成型压力越大颗粒间接触越紧密,对烧结越有利。
5、在扩散传质的烧结过程中,使坯体致密的推动力是什么?哪些方法可促进烧结?说明原因。
固相烧结法 英语
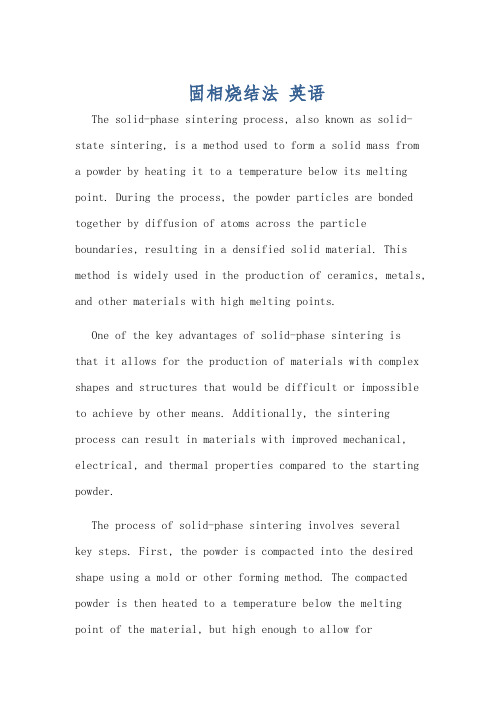
固相烧结法英语The solid-phase sintering process, also known as solid-state sintering, is a method used to form a solid mass from a powder by heating it to a temperature below its melting point. During the process, the powder particles are bonded together by diffusion of atoms across the particle boundaries, resulting in a densified solid material. This method is widely used in the production of ceramics, metals, and other materials with high melting points.One of the key advantages of solid-phase sintering isthat it allows for the production of materials with complex shapes and structures that would be difficult or impossible to achieve by other means. Additionally, the sintering process can result in materials with improved mechanical, electrical, and thermal properties compared to the starting powder.The process of solid-phase sintering involves severalkey steps. First, the powder is compacted into the desired shape using a mold or other forming method. The compacted powder is then heated to a temperature below the melting point of the material, but high enough to allow fordiffusion of atoms across the particle boundaries. As the temperature increases, the particles begin to bond together, forming a solid mass. The sintered material is then cooled and may undergo additional processing steps to achieve the desired properties.Solid-phase sintering can be performed using a varietyof heating methods, including conventional furnace heating, microwave sintering, and spark plasma sintering. Each method has its own advantages and limitations, and the choice of sintering method will depend on the specific material and desired properties.In summary, solid-phase sintering is a versatile and widely used method for producing dense, complex-shaped materials with improved properties. By carefullycontrolling the sintering process, it is possible to tailor the microstructure and properties of the final material to meet specific application requirements.固相烧结法,也称为固态烧结,是一种通过将粉末加热至其熔点以下的温度来形成固体块的方法。
材料科学基础最全名词解释

1.固相烧结:固态粉末在适当的温度,压力,气氛和时间条件下,通过物质与气孔之间的传质,变为坚硬、致密烧结体的过程。
液相烧结:有液相参加的烧结过程。
2.金属键:自由电子与原子核之间静电作用产生的键合力。
3.离子键:金属原子自己最外层的价电子给予非金属原子,使自己成为带正电的正离子,而非金属得到价电子后使自己成为带负电的负离子,这样正负离子靠它们之间的静电引力结合在一起。
共价键:由两个或多个电负性相差不大的原子间通过共用电子对而形成的化学键。
氢键:由氢原子同时与两个电负性相差很大而原子半径较小的原子(O,F,N等)相结合而产生的具有比一般次价键大的键力。
弗兰克缺陷:间隙空位对缺陷肖脱基缺陷:正负离子空位对的奥氏体:γ铁内固溶有碳和(或)其他元素的、晶体结构为面心立方的固溶体。
布拉菲点阵:除考虑晶胞外形外,还考虑阵点位置所构成的点阵。
不全位错:柏氏矢量不等于点阵矢量整数倍的位错称为不全位错。
玻璃化转变温度:过冷液体随着温度的继续下降,过冷液体的黏度迅速增大,原子间的相互运动变得更加困难,所以当温度降至某一临界温度以下时,即固化成玻璃。
这个临界温度称为玻璃化温度Tg。
表面能:表面原子处于不均匀的力场之中,所以其能量大大升高,高出的能量称为表面自由能(或表面能)。
半共格相界:若两相邻晶体在相界面处的晶面间距相差较大,则在相界面上不可能做到完全的一一对应,于是在界面上将产生一些位错,以降低界面的弹性应变能,这时界面上两相原子部分地保持匹配,这样的界面称为半共格界面或部分共格界面。
柏氏矢量:描述位错特征的一个重要矢量,它集中反映了位错区域内畸变总量的大小和方向,也使位错扫过后晶体相对滑动的量。
柏氏矢量物理意义:①从位错的存在使得晶体中局部区域产生点阵畸变来说:一个反映位错性质以及由位错引起的晶格畸变大小的物理量。
②从位错运动引起晶体宏观变形来说:表示该位错运动后能够在晶体中引起的相对位移。
部分位错:柏氏矢量小于点阵矢量的位错包晶转变:在二元相图中,包晶转变就是已结晶的固相与剩余液相反应形成另一固相的恒温转变。
固相烧结法

固相烧结法
固相烧结法是一种制备材料的方法,主要是通过将单元系固相粉末、化合物或均匀固溶体在熔点以下温度进行烧结。
固相烧结过程大致分为低温阶段、中温阶段和高温阶段。
在低温阶段,主要发生金属的回复、吸附气体和水分的挥发、压坯内成形剂的分解和排除。
中温阶段开始发生再结晶、粉末颗粒表面氧化物被完全还原,颗粒接触界面形成烧结颈,烧结体强度明显提高,而密度增加较慢。
在高温阶段,扩散和流动充分进行并接近完成,烧结体内的大量闭孔逐渐缩小,孔隙数量减少,烧结体密度明显增加。
在固相烧结过程中,扩散传质是最重要的,同时颗粒和颈部的形状也会发生变化。
固相烧结法可以根据其组元多少分为单元系固相烧结和多元系固相烧结两类。
单元系固相烧结过程中,只发生粉末颗粒间粘结、致密化和纯金属的组织变化,不存在组织间的溶解,也不出现新的组成物或新相。
该方法适用于制备各种金属材料、陶瓷材料和复合材料等,广泛应用于材料科学和工程领域。
以上信息仅供参考,如有需要,建议查阅相关文献或咨询专业人士。
陶瓷膜的烧结原理
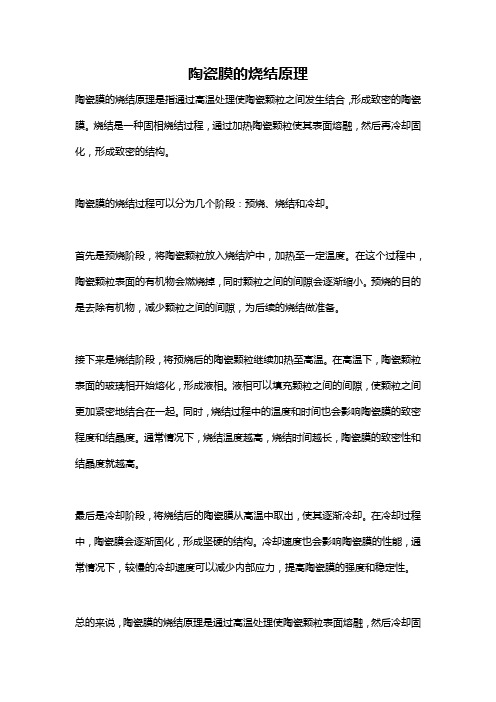
陶瓷膜的烧结原理
陶瓷膜的烧结原理是指通过高温处理使陶瓷颗粒之间发生结合,形成致密的陶瓷膜。
烧结是一种固相烧结过程,通过加热陶瓷颗粒使其表面熔融,然后再冷却固化,形成致密的结构。
陶瓷膜的烧结过程可以分为几个阶段:预烧、烧结和冷却。
首先是预烧阶段,将陶瓷颗粒放入烧结炉中,加热至一定温度。
在这个过程中,陶瓷颗粒表面的有机物会燃烧掉,同时颗粒之间的间隙会逐渐缩小。
预烧的目的是去除有机物,减少颗粒之间的间隙,为后续的烧结做准备。
接下来是烧结阶段,将预烧后的陶瓷颗粒继续加热至高温。
在高温下,陶瓷颗粒表面的玻璃相开始熔化,形成液相。
液相可以填充颗粒之间的间隙,使颗粒之间更加紧密地结合在一起。
同时,烧结过程中的温度和时间也会影响陶瓷膜的致密程度和结晶度。
通常情况下,烧结温度越高,烧结时间越长,陶瓷膜的致密性和结晶度就越高。
最后是冷却阶段,将烧结后的陶瓷膜从高温中取出,使其逐渐冷却。
在冷却过程中,陶瓷膜会逐渐固化,形成坚硬的结构。
冷却速度也会影响陶瓷膜的性能,通常情况下,较慢的冷却速度可以减少内部应力,提高陶瓷膜的强度和稳定性。
总的来说,陶瓷膜的烧结原理是通过高温处理使陶瓷颗粒表面熔融,然后冷却固
化,形成致密的陶瓷膜。
烧结过程中的温度、时间和冷却速度等因素都会影响陶瓷膜的性能。
陶瓷膜的烧结原理在陶瓷材料的制备中具有重要的意义,可以用于制备各种功能性陶瓷膜,如过滤膜、分离膜和传感器等。
固相反应对烧结有什么意义

固相反应对烧结有什么意义?
固相反应一般是固体质点进行扩散迁移并发生化学反应,颗粒与颗粒之间形成固体连接桥(或者连接颈),化合物和固溶体把颗粒连接起来。塔曼学派的观点认为,固相反应开始的温度都比较低,开始反应的温度远低于它们的熔点或它们的低共熔点,该温度与其熔点之间存在一定的规律,对于盐类和氧化物,开始反应的温度T反≈0.57T熔;对于硅酸盐及
3固相反应与烧结详解

离子晶体中的离子在电场的作用下发生迁移 或电解;
在烧结过程中,固体外表积趋于最小,因而 使原子从外表曲率大的地方向曲率小的地方集中。
液相或气相反响的动力学可以表示为 反响物浓度变化的函数,但对固相反响来 说,反响物浓度是没有多大意义的。
2.4 固相反响与烧结 2.4.1 概论
固相反响是指那些有固态物质参与的化学 反响。固相反响不仅包括固---固反响,也包括 有气体或液体参与的反响。
我们只着重介绍固——固反响。 广义的烧结包含固相反响的某些内容,我 们所谈的烧结是通过高温处理,而使晶粒尺寸 变大及材料致密化的过程。
固相反响与烧结也是固态化学的重要争论 内容之一。
2.4.3.2 粉末反响
上面争论了单晶体之间的固一固反响, 这种状况在实际上是很少发生的。
以单晶为对象进展争论,其目的是使 固相反响的初始条件和边界条件尽量简化, 从而易于了解反响的根本机理。其结论对 一般固一固反响仍有指导意义。
事实上,在工业生产和科学争论中常 常遇到的有重要实际意义的是金属或无机 非金属材料细粉之间的反响。
固相反响通常包含以下步骤: 1.固体界面如原子或离子的跨过界面的
集中; 2.原子规模的化学反响; 3.新相成核; 4.通过固体的输运及新相的长大。 打算固相反响性的两个重要因素是成核和集 中速度.
假设产物和反响物之间存在构造类似性, 则成核简洁进展。
集中与固相内部的缺陷、界面形貌、原 子或离子的大小及其集中系数有关。
在完全抱负的晶体中,质点的迁移现象一 般是不行能发生的。因此,在固态材料中发生 的每一种传质现象和反响过程均与晶格的各种 缺陷有关。
陶瓷的传统固相烧结工艺

陶瓷的传统固相烧结工艺陶瓷是指以无机非金属粉末为原料,经过成型、干燥、烧成等工艺制成的坚硬、致密、耐磨、耐腐蚀、耐高温的材料。
固相烧结工艺是陶瓷制造的传统方法之一,也是目前应用最广泛的成型工艺之一。
固相烧结工艺的步骤主要有原料制备、成型、干燥、烧结、密封等工序。
首先是原料的制备。
陶瓷的原料包括粘土、石英、矾土、长石、白云石、氧化铝等无机非金属物质。
制备原料是固相烧结工艺的第一步,原料的质量对最终制成的陶瓷材料的质量影响很大。
因此,对原料的选择和处理要求非常严格。
接下来是成型。
常用的成型方法有压制、注塑、挤出、注浆和液压成型等多种方法。
成型的目的是将原料压制成一定形状的坯体,形状可以是各种几何形状。
成型后的坯体需要进行干燥处理,以免在烧结时出现爆炸或破损等情况。
干燥过程是坯体失去水分的过程,干燥的方法有自然通风干燥、烘干炉干燥等方式。
干燥的温度和时间要视原料不同而定。
烧结是固相烧结工艺的核心步骤。
它是指将干燥后的坯体置于高温环境下,在特定温度和时间内使之烧结成陶瓷材料的过程。
在烧结过程中,原料粒子之间会发生吸附、扩散和重组等现象,使粒子紧密结合,形成致密的陶瓷体。
密封是最后一个必须完成的步骤。
因为陶瓷材料的热膨胀系数很小,若在高温下使用时不能控制热胀冷缩,容易造成烧毁、爆裂等损伤。
因此,在烧结前后对陶瓷器进行密封处理,能有效避免陶瓷材料在高温下的损伤。
总之,陶瓷的固相烧结工艺对原料的精选、成型的精度、烧结的温度控制和密封的处理都有严格的要求。
只有精细的工艺流程和高品质的原材料,才能生产出质量优良、使用寿命长久、安全可靠的优质陶瓷制品。
按照烧结时是否出现液相,可将烧结分为两类固相烧结和液
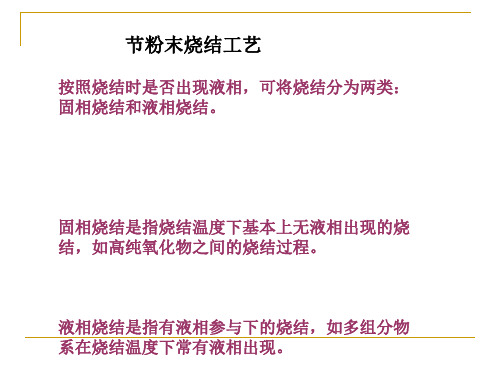
• 合金的收缩主要发生在液相出现之后。液相流动 引起WC颗粒重排与溶解和析出等过程使合金收缩 显著,并且导致WC颗粒长大。
• 保温时间愈长,WC晶粒愈粗并且愈不均匀。
• 烧结保温的后期,还发生WC的聚晶长大,它与通 过液相约重结晶长大不同,是发生在WC固架形成 之后的固相烧结长大。
液相烧结过程
液相烧结不同阶段的示意图(O:熔化;Ⅰ:重排;Ⅱ:溶解-沉淀;及Ⅲ:固相烧结)
(1)颗粒重排(Particles Re-arrangement) 在液相烧结过程中,颗粒间的液相膜起润滑作用。颗粒重 排向减少气孔的方向进行,同时减小系统的表面自由能。 当坯体的密度增加时,由于周围颗粒的紧密接触,颗粒进 一步重排的阻力增加,直至形成紧密堆积结构。
优点: 1)提高烧结驱动力。 2)可制备具有控制的微观结构和优化性能的陶瓷及金属复合材料;
液相烧结能否顺利完成(致密化进行彻底),取决于同 液相性质有关的三个基本条件: 1.润湿性
当液相润湿固相时,在接触点A用杨氏 方程表示平衡的热力学条件为:
完全润湿时,θ=0o;完全不润湿时,θ>90o;部分润湿的状态, 0o<θ<90o
液相烧结是指有液相参与下的烧结,如多组分物 系在烧结温度下常有液相出现。
一、液相烧结
粉末压坯仅通过固相烧结难以获得很高的密度,如果在烧结温 度下,低熔组元熔化或形成低熔共晶物,那么由液相引起的物质迁 移比固相扩散快,而且最终液相将填满烧结体内的孔隙,因此可提 高得密度、增强烧结产品机械性能。
液相烧结(Liquid Phase Sintering,简写为LPS)是指在烧结 包含多种粉末的坯体中,烧结温度至少高于其中的一种粉末的熔融 温度,从而在烧结过程中而出现液相的烧结过程。
材料科学基础最全名词解释

小崔工作室材料科学基础最全名词解释固相烧结:固态粉末在适当的温度,压力,气氛和时间条件下,通过物质与气孔之间的传质,变为坚硬、致密烧结体的过程。
液相烧结:有液相参加的烧结过程。
金属键:自由电子与原子核之间静电作用产生的键合力。
离子键:金属原子自己最外层的价电子给予非金属原子,使自己成为带正电的正离子,而非金属得到价电子后使自己成为带负电的负离子,这样正负离子靠它们之间的静电引力结合在一起。
共价键:由两个或多个电负性相差不大的原子间通过共用电子对而形成的化学键。
氢键:由氢原子同时与两个电负性相差很大而原子半径较小的原子(O,F,N等)相结合而产生的具有比一般次价键大的键力。
弗兰克缺陷:间隙空位对缺陷肖脱基缺陷:正负离子空位对的奥氏体:γ铁内固溶有碳和(或)其他元素的、晶体结构为面心立方的固溶体。
布拉菲点阵:除考虑晶胞外形外,还考虑阵点位置所构成的点阵。
不全位错:柏氏矢量不等于点阵矢量整数倍的位错称为不全位错。
玻璃化转变温度:过冷液体随着温度的继续下降,过冷液体的黏度迅速增大,原子间的相互运动变得更加困难,所以当温度降至某一临界温度以下时,即固化成玻璃。
这个临界温度称为玻璃化温度Tg。
表面能:表面原子处于不均匀的力场之中,所以其能量大大升高,高出的能量称为表面自由能(或表面能)。
半共格相界:若两相邻晶体在相界面处的晶面间距相差较大,则在相界面上不可能做到完全的一一对应,于是在界面上将产生一些位错,以降低界面的弹性应变能,这时界面上两相原子部分地保持匹配,这样的界面称为半共格界面或部分共格界面。
柏氏矢量:描述位错特征的一个重要矢量,它集中反映了位错区域内畸变总量的大小和方向,也使位错扫过后晶体相对滑动的量。
柏氏矢量物理意义:①从位错的存在使得晶体中局部区域产生点阵畸变来说:一个反映位错性质以及由位错引起的晶格畸变大小的物理量。
②从位错运动引起晶体宏观变形来说:表示该位错运动后能够在晶体中引起的相对位移。
5-4_陶瓷材料的烧结

可广泛用于磁性材料、梯度功能材料、纳米陶瓷、纤维增强陶瓷和金 属间化合物等系列新型材料的烧结。
一、放电等离子体烧结的优点 ①烧结温度低(比HP和HIP低200-300℃)、烧结时间短(只需3-10min, 而HP和HIP需要120-300min)、单件能耗低; ②烧结机理特殊,赋予材料新的结构与性能;
2.2 烧结驱动力
烧结的驱动力就是总界面能的减少。粉末坯体的总界面能表示为 γA, 其中γ为界面能;A为总的比表面积。那么总界面能的减少为:
A A A
其中,界面能的变化(Δγ)是因为样品的致密化,比表面积的变化 是由于晶粒的长大。对于固相烧结,Δγ主要是固/固界面取代固/气界面。
(2)保温时间对产品性能的影响 在烧成的最高温度保持一定的时间,一方面使物理化学变化更趋完全,使 坯体具有足够液相量和适当的晶粒尺寸,另一方面组织结构亦趋均一。但保温 时间过长,则晶粒溶解,不利于在坯中形成坚强骨架,而降低机械性能。 (3)烧成气氛对产品性能的影响 ① 气氛对陶瓷坯体过烧膨胀的影响 ② 气氛对坯体的收缩和烧结的影响 ③ 气氛对坯的颜色和透光度以及釉层质量的影响 (4)升温与降温速度对产品性能的影响
(pore drag)和晶粒生长驱动力之间力的平衡作用。
研究表明,较小的颗粒尺寸分布范围是获取高烧结密度的必要条件。
二、影响陶瓷材料烧结的工艺参数 (1)烧成温度对产品性能的影响 烧成温度是指陶瓷坯体烧成时获得最优性质时的相应温度,即操作时的 止火温度。 烧成温度的高低直接影响晶粒尺寸和数量。对固相扩散或液相重结晶来 说,提高烧成温度是有益的。然而过高的烧成温度对特瓷来说,会因总体晶 粒过大或少数晶粒猛增,破坏组织结构的均匀性,因而产品的机电性能变差。
4.3 晶粒生长和粗化
固相烧结

2 3
(
64
1
)6
5
t2
13422
0.1
(
5
)2
/
3
(
2
1
)6
x / r 16 8
x/r 0.0725
0.066
0.112
0.058
9-7 在制造透明Al2O3材料时,原始粉料粒度为2m,烧结至最高 温度保温0.5小时,测得晶粒尺寸为10 m,试问若保温2小时, 晶粒尺寸多大?为抑制晶粒生长加入0.1%MgO,此时若保温 2小时,晶粒尺寸又多大?
传质 蒸 发-凝 聚 扩散传质 流动传质
条件 x/r=0.2 粒度 r=16m 求 t
运 算
x2
/
r2
kr2
2 3
t
2
1 3
x1 / r1
kr1
2 3
1
t1 3
(16
)
3 5
(
64)Βιβλιοθήκη 1 35t2
(16
)
1 2
(
64)
1 2
5
t2
2 1
2 1
16 3 t2 3 5 3163
t(h) 163.8
2097.2
说明:晶粒生长是晶界移动的结果,并不是原子定向向颈部 迁移的传质过程,因而不能促进坯体致密化。晶界移动 可以引起原子跃迁,也可以使气孔移入晶粒内,从而影响 烧结速率。因而晶界移动需进行控制。
补充:1、试就(a) 驱动力的来源,(b) 驱动力大小,(c) 在陶瓷系 统中的重要性,来区分初次再结晶、晶粒长大和二次再结晶。
料烧结速率的影响( )
A、没有影响。 B、延缓烧结速率。 C、促进烧结速率。
固相法 烧结

化学组成、矿物组成
材料性质 结构 显微结构
改变
晶粒尺寸分布 气孔尺寸分布 晶界体积分数
烧结
应用
目的:粉状物料变成致密体。 陶瓷、耐火材料、粉沫冶金、超高温材料…… 现代无机材料 如:功能瓷:热、声、光、电、磁、生物特性。
结构瓷:耐磨、弯曲、湿度、韧性……
• 烧结(sintering)是把粉状物料转变为致密体的工艺过程。 • 烧结的定义: • 1) 宏观定义:粉体原料经过成型、加热到低于熔点的温 度(烧结温度),发生固结、气孔率下降、收缩加大、致密 度提高、晶粒增大,变成坚硬的烧结体,这个现象称为烧 结。 • 2) 微观定义:固态中分子(原子)间存在相互吸引,通过加 热使质点获得足够的能量进行迁移,使粉末体产生颗粒黏 结,产生强度并导致致密化和再结晶的过程称为烧结。 • 烧成 — 烧成是在一定的温度范围内烧成致密体的过程。 • 烧结 — 指粉料经加热而致密化的简单物理过程,不包括 化学反应,烧结仅是烧成过程的一个重要部分。烧结是在 低于固态物质的熔融温度下进行的。
固相法
高温烧结法
烧结过程是一门古老的工艺。现在,烧结过 程在许多工业部门得到广泛应用,如陶瓷、耐火 材料、粉末冶金、超高温材料等生产过程中都含 有烧结过程。烧结的目的是把粉状材料转变为致 密体。 研究物质在烧结过程中的各种物理化学变化。 对指导生产、控制产品质量,研制新型材料显得 特别重要。
烧结(sintering)
固相-烧结
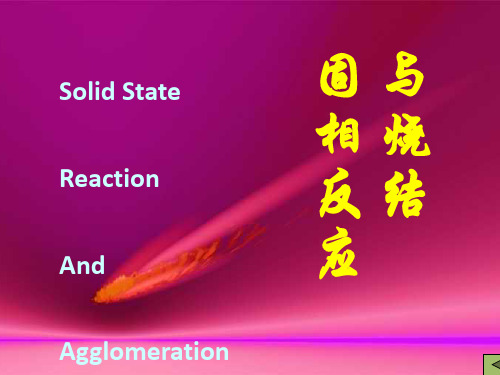
小晶粒生长为大晶粒.使界面面积减小,界面 自由能降低,晶粒尺寸由 1μm 变化到 lcm ,相 应的能量变化为0.1-5Cal/g。
自由焓
△G
*
△G 位置 (a) (b)
图12 晶界结构及原子位能图
50 3 4
10 6
图13 烧结后期晶粒长大示意图
晶粒正常长大时,如果晶界受到第二相杂质的 阻碍,其移动可能出现三种情况:
烧结中期
烧结后期
传质继续进行,粒子长大, 气孔变成孤立闭气孔,密 度达到95%以上,制品强 度提高。
二、烧结推动力
粉体颗料尺寸很小,比表面积大,具有较高的表面能, 即使在加压成型体中,颗料间接面积也很小,总表面积 很大而处于较高能量状态。根据最低能量原理,它将自 发地向最低能量状态变化,使系统的表面能减少。
不同物质泰曼温度与熔点Tm之间的关系:
金属:0.3~0.4Tm 盐类:0.57Tm
硅酸盐:0. 8~0.9Tm
2、广义固相反应的共同特点
(1)固态物质间的反应活性较低、反应速度较慢; (2)固相反应总是发生在两种组分界面上的非均相反应; 固相反应包括两个过程:
相界面上的化学反应
反应物通过产物扩散(物质迁移)
烧结是一个自发的不可逆过程,系统表面 能降低是推动烧结进行的基本动力。
图9 不同烧结机理的传质途径
表面张力能使凹、凸表面处的蒸气压P1分别低于和 高于平面表面处的蒸气压Po,并可以用开尔文本公 式表达:
对于球形表面
P 2M 1 ln P0 dRTr
(1)
对于非球形表面
P M 1 1 1 ln ( ( ) 2) P0 dRT x
可见,作为烧结动力的表面张力可以通 过流动、扩散和液相或气相传递等方式 推动物质的迁移。
固相烧结法步骤

固相烧结法步骤宝子们,今天来给你们唠唠固相烧结法的步骤哦。
固相烧结法呢,一开始得准备原料。
这原料就像是盖房子的砖头一样重要 。
要把那些需要烧结的固体原料按照一定的比例混合好。
这个比例可不能马虎呀,就像做菜放盐放多放少都不行呢。
比如说要烧结陶瓷,就得把陶瓷的各种矿物原料按照配方精确地混合起来。
混合好原料后呀,就到了压制成型这一步啦。
这就像是把松散的面粉压成饼一样的感觉。
把混合好的原料放进模具里,然后用压力机给它施加一定的压力,让原料变成我们想要的形状。
这个形状可以是块状、片状或者其他奇奇怪怪的形状哦,只要符合我们最后的需求就行。
比如说我们想做个陶瓷小杯子,就把原料压制成小杯子的形状。
接着呢,就是烧结过程啦。
这可是固相烧结法的关键步骤呢。
把压制成型的样品放到高温炉子里。
这个高温可不是一般的高哦,可能是几百摄氏度甚至上千摄氏度呢。
在这个高温环境下,固体颗粒之间就开始发生奇妙的变化啦。
它们会相互扩散、融合,就像小伙伴们手拉手一样紧紧地结合在一起。
随着时间的推移,样品的密度会不断增加,性能也会变得越来越好。
烧结完成之后呢,可不能就这么不管啦。
还得进行冷却。
冷却也有讲究哦,不能太快也不能太慢。
太快的话呢,样品可能会因为温度变化太剧烈而产生裂纹,就像玻璃突然遇冷会裂掉一样。
太慢的话呢,又会浪费很多时间。
所以要选择一个合适的冷却速度,让我们的样品能够完美地从高温状态过渡到常温状态。
宝子们,固相烧结法的步骤大概就是这样啦。
是不是还挺有趣的呢?每个步骤都像是一场小小的冒险,一个环节出问题都可能影响最后的结果哦。
不过只要按照正确的步骤来,就能做出很棒的烧结产品啦。
3-5 固相烧结

§3-5 固相烧结—固相传质机理一、固相传质机理固相物质传递,是指在一定的温度作用之下,质点(通常指原子或离子)在固体内部,表面或界面作有向扩散时形成内部表面或界面的物质迁移过程。
对于晶态物质而言,在完整的晶格结构中进行体内扩散传质特别困难,因为正常格点上之原子或离子,其外电子壳层几乎彼此相切,或说电子云有相当程度的重叠,质点要挤进其间隙,并通过这种间隙而不断运动,所需之激活能是很高的。
如果在晶格结构中存在一定的空余格点(有一定缺位浓度),或出现不规则的排列(结构位错)时,将给体内扩散传质带来不少方便。
由于晶粒取向的不同,晶粒界面质点的排列都是不够规则的,至于晶体表面则有一边完全裸露或存在更多缺陷。
规则的,至于晶体表面则有边完全裸露或存在更多缺陷。
在同一温度下,同类晶体的体内,界面和表面进行传质扩散时,其相应的扩散系数D必然存在较大的差别,并具有下列关系:sb V D D D <<其差别往往以数量级计。
和研究气相传质时的情况相似,固体的表面状态,因存在表面张力或表面能不仅影响其表面附该物质的蒸气压表面张力或表面能,不仅影响其表面附近该物质的蒸气压,也会影响该表面内侧物体中的空格点浓度。
¾由于表面张力的作用,凹表面具有力图向外拉平的扩张趋势,这便有利于使其内侧形成较大的空格点浓度。
趋势这便有利于使其内侧形成¾表面张力将促使凸表面向体内拉平、绷紧,出现朝内压的趋势,使其内侧空格点浓度将特别地小。
¾平表面,由于不出现向外张或朝内压的作用,故平表面下的空格点浓度将介乎凹凸两种情况之间。
下的空格点浓度将介乎凹凸两种情况之间倘若将理想完整的晶体看作是空格点的“真空”;将不含质点的空孔比作空格点的“实体”,而把单个格点的空缺比拟为空格点的“气态分子”,因而空格点的浓度就可以类比于蒸气压了,经过如此一番虚、实颠倒之后,就能将固相传质的行为和气相传质很好地对应起来了。
固相烧结法

固相烧结是混合粉末或者样品在高温下物质相互扩散,使微观离散颗粒逐渐形成连续的固态结构,此过程样品整体自由能降低,然而强度提高.固相烧结过程包含了表面扩散、晶界扩散、晶界迁移、颗粒重排等烧结机制的作用.3。
3。
2工艺流程的说明:(1)配料:流程与要求:1)按照化学方程式严格计算配比.2)原料质量要计入纯度。
3)应该尽量采用较光滑的,不吸水的称量用纸。
4)称量完毕的药品直接放入球磨罐,不能与其他介质接触。
5)钥匙在使用之前与每次换料之前必须要严格擦洗干净。
6)称量准确,一般应该精确到小数点后3位,误差不能超过0.5mg。
(2)混合:流程与要求:1)使用球磨机,球磨既使得物料颗粒变细又使得不同组分可以充分混合。
2)方式为湿磨,湿磨可以增大研磨效率,有利于粉料的细化。
3)球磨介质的选取应该不溶解原材料。
使该介质淹没锆球。
4)溶剂的添加必须采用注射器量取,量以磨完后料成浆状为宜.出料时可适宜添加溶剂。
5)球磨罐磨料以30g左右为宜,一般不超过50g。
相应的锆球比例(直径10:6。
5:5)=(质量70:100:120)。
其中,本次试验的球磨介质是无水乙醇,取量为45ml。
另外,采用锆球是防止引起样品的介电性能降低。
将聚酯罐放入行星式球磨机,以225r/min转速球磨12小时,使原料混合均匀。
完成后,将浆状药品放入烘干机中烘干。
(3)预烧:流程与要求:1)采用压块预烧,增大接触面积和结合力,降低预烧温度,方便反应,较少挥发。
2)压片压力为6-8Mpa。
3)预烧温度的选择要求:生成纯相;颗粒均匀,颗粒不能太大,可用XRD 检测。
本次试验是采用的压块预烧,模具的直径为30mm,压片厚度为18mm,压力为8Mpa。
温度为450o C,预烧180min。
(4)粉碎:流程与要求:1)一般先采用研钵粗磨,然后用球磨机精磨。
2)研钵使用过程中要注意:大颗粒要压碎,不能直接磨,导致损伤研钵并引入杂质。
3)粗磨要磨到肉眼看不到颗粒为止。
粉末冶金中烧结分类

书山有路勤为径,学海无涯苦作舟粉末冶金中烧结分类根据致密化机理或烧结工艺条件的不同,烧结可分为液相烧结、固相烧结、活化烧结、反应烧结、瞬时液相烧结、超固相烧结、松装烧结、电阻烧结、电火花烧结、微波烧结和熔浸等。
1 . 固相烧结:按其组元的多少可分为单元系固相烧结和多元系固相烧结两类。
单元系固相烧结纯金属、固定成分的化合物或均匀固溶体的松装粉末或压坯在熔点以下温度(一般为绝对熔点温度的2/3 一4/5)进行的粉末烧结。
单元系固相烧结过程大致分3 个阶段:(1)低温阶段(T 烧毛0.25T 熔)。
主要发生金属的回复、吸附气体和水分的挥发、压坯内成形剂的分解和排除。
由于回复时消除了压制时的弹性应力,粉末颗粒间接触面积反而相对减少,加上挥发物的排除,烧结体收缩不明显,甚至略有膨胀。
此阶段内烧结体密度基本保持不变。
(2)中温阶段(T 烧(0.4~。
.55T 动。
开始发生再结晶、粉末颗粒表面氧化物被完全还原,颗粒接触界面形成烧结颈,烧结体强度明显提高,而密度增加较慢。
(3)高温阶段(T 烧二0.5 一。
.85T 熔)。
这是单元系固相烧结的主要阶段。
扩散和流动充分进行并接近完成,烧结体内的大量闭孔逐渐缩小,孔隙数量减少,烧结体密度明显增加。
保温一定时间后,所有性能均达到稳定不变。
( 2 )多元固相烧结:组成多元系固相烧结两种组元以上的粉末体系在其中低熔组元的熔点以下温度进行的粉末烧结。
多元系固相烧结除发生单元系固相烧结所发生的现象外,还由于组元之间的相互影响和作用,发生一些其他现象。
对于组元不相互固溶的多元系,其烧结行为主要由混合粉末中含量较多的粉末所决定。
如铜一石墨混合粉末的烧。
固相烧结反应的缺陷

固相烧结反应的缺陷
固相烧结反应是一种常用的陶瓷制备方法,但它也存在一些缺陷:
1. 不均匀性:固相烧结反应在烧结过程中容易产生非均匀性。
由于开始时反应速率较低,反应产物在烧结过程中可能会出现不均匀分布的情况,导致烧结体的物理和化学性质不均匀。
2. 收缩差异:由于反应产物的体积变化和烧结体密度的不一致,固相烧结过程中可能出现不同部位的收缩差异。
这种收缩差异可能导致烧结体的形状变化和开裂。
3. 限制形状:固相烧结反应对于制备特定形状的陶瓷制品有一定的限制。
由于固相烧结是在高温下进行的,反应过程中烧结体容易变形或破碎。
这使得制备复杂形状的陶瓷制品变得困难。
4. 高温需求:固相烧结反应需要在高温下进行,通常需要较长的时间来完成反应和烧结过程。
这使得固相烧结方法不适用于一些低熔点材料,或者在烧结过程中易挥发或分解的材料。
5. 能源消耗:由于固相烧结反应需要在高温下进行,所以需要大量的能源来提供烧结的温度。
这导致固相烧结方法的能源消耗相对较高,不太环保。
总的来说,固相烧结反应在陶瓷制备中有一些缺陷,如不均匀性、收缩差异、限制形状、高温需求和能源消耗等。
因此,在实际应用中需要结合具体材料和制备要求来选择合适的制备方法。
- 1、下载文档前请自行甄别文档内容的完整性,平台不提供额外的编辑、内容补充、找答案等附加服务。
- 2、"仅部分预览"的文档,不可在线预览部分如存在完整性等问题,可反馈申请退款(可完整预览的文档不适用该条件!)。
- 3、如文档侵犯您的权益,请联系客服反馈,我们会尽快为您处理(人工客服工作时间:9:00-18:30)。
溶解-沉淀 溶解-
0.1 2 = ( )1 / 6 0.2 t 2
128
0 .1 2 1/ 6 =( ) x/r 8
0.16
0.13
0.2
பைடு நூலகம்
0.126
9-5 如上题粉料粒度改为 m,烧结至 - 如上题粉料粒度改为16 ,烧结至x/r=0.2,各个传质需要多 , 少时间?若烧结8小时时 各个传质过程的颈部增长x/r又是多少 小时时, 又是多少? 少时间?若烧结 小时时,各个传质过程的颈部增长 又是多少? 从两题计算结果,讨论粒度 烧结时间对四种传质过程的影响程度 粒度与 对四种传质过程的影响程度? 从两题计算结果,讨论粒度与烧结时间对四种传质过程的影响程度? 传质 蒸 发-凝 聚 扩散传质 x/r=0.2 条件 粒度 r=16m 运 算 t(h) 条件
K 1 = Aexp(-Q/RT)
D=63 m
加入抑制剂计算式: 加入抑制剂计算式: D 3 D 3 = K t 计算式 0 2
K 2 = Aexp(-Q/RT 2 )
K1=99.75 由K式作比较得K2=998.6 式作比较得 式作比较
D=16 m
9-10 在烧结时,晶粒生长能促进坯体致密化吗?晶粒生长会 - 在烧结时,晶粒生长能促进坯体致密化吗? 影 响烧结速率吗?试说明之。 响烧结速率吗?试说明之。 说明:晶粒生长是晶界移动的结果, 说明:晶粒生长是晶界移动的结果,并不是原子定向向颈部 晶界移动的结果 迁移的传质过程,因而不能促进坯体致密化。 迁移的传质过程,因而不能促进坯体致密化。晶界移动 可以引起原子跃迁,也可以使气孔移入晶粒内, 可以引起原子跃迁,也可以使气孔移入晶粒内,从而影响 烧结速率。因而晶界移动需进行控制。 烧结速率。因而晶界移动需进行控制。
第九章 烧结 习题课
第九章 一、传质机理 固相烧结
蒸发- 蒸发-凝聚 扩散传质 粘性流动
习题课
液相烧结
溶解- 溶解-沉淀
二、晶粒生长和二次再结晶 三、影响烧结的因素
9-4 设有粉料粒度为 m,若经 小时烧结后,x/r=0.1。 如果不 - 设有粉料粒度为5 ,若经2小时烧结后 小时烧结后, 。 考虑晶粒生长,若烧结至x/r=0.2。并分别通过蒸发-凝聚;体积 蒸发- 考虑晶粒生长,若烧结至 。并分别通过蒸发 凝聚; 传质, 各需多少时间?若烧结8小 扩散;粘性流动;溶解-沉淀传质 扩散;粘性流动;溶解-沉淀传质, 各需多少时间?若烧结 小 各个传质过程的颈部增长x/r又是多少 又是多少? 时,各个传质过程的颈部增长 又是多少? x/r 蒸发-凝聚 蒸发- 扩散传质 粘性流动 x / r1 t1 1 / 3 =( ) 运 x / r2 t2 0.1 2 0.1 2 1/ 2 = ( )1 / 5 =( ) 算 0.2 t 2 0.1 2 1/ 3 0.2 t 2 =( ) 0.2 t 2 时间 16 64 8 烧结时间由2小时延长至 小时延长至8小时 烧结时间由 小时延长至 小时 运 算 x/r
气孔率下降
由于大晶粒受到周围晶粒应 力作用或由于本身易产生缺 陷,常在大晶粒内出现隐裂 导致材料机、 纹,导致材料机、电性能恶 化。但在硬磁铁氧体 BaF12O14的烧结中有益。 的烧结中有益。
2、烧结为什么在气孔率达约5%就停止了,烧结为什么达不到理 、烧结为什么在气孔率达约 %就停止了, 论密度?采取哪些措施可使烧结材料接近理论密度,为什么? 论密度?采取哪些措施可使烧结材料接近理论密度,为什么?
1 5 1/ 2 2 2 =( ) ( )
1
16 3 64 6 ( ) =( ) 5 t2
13422
2
1
= 5
2 1 3 16 3
163.8 r=16 m
2 / 3 1 / 3 r1 t1 2 / 3 1 / 3 r2 t2 1 5 2 / 3 2 3 ) ( )
2097.2 t=8小时 小时
1 5 3/ 5 2 5 =( ) ( )
D D0 = Kt
2 2
加入抑制剂晶粒长大计算式: 加入抑制剂晶粒长大计算式: D 3 D 3 = Kt 0 答案: 答案: 约20 m 约15.84 m
9-8 在1500℃Al2O3正常晶粒生长期间,观察到晶体在 小时内从 - 正常晶粒生长期间,观察到晶体在1小时内从 ℃ 0.5 m直径长大到 m。如已知晶界扩散激活能为 直径长大到10 直径长大到 。如已知晶界扩散激活能为335kJ/mol, , 试预测在1700℃下4小时后,晶粒尺寸是多少?你估计加入 ℃ 小时后, 试预测在 小时后 晶粒尺寸是多少? 0.5%MgO杂质对 2O3晶粒生长速率有什么影响?在与上面相同 杂质对Al 晶粒生长速率有什么影响? 杂质对 条件下烧结,会有什么结果,为什么? 条件下烧结,会有什么结果,为什么? 分析:晶粒正常生长计算式: 分析:晶粒正常生长计算式: D 2 D 0 2 = Kt 计算式
补充: 、试就(a) 驱动力的来源, 驱动力大小, 补充:1、试就 驱动力的来源,(b) 驱动力大小,(c) 在陶瓷系 统中的重要性,来区分初次再结晶、晶粒长大和二次再结晶。 统中的重要性,来区分初次再结晶、晶粒长大和二次再结晶。 驱动力来源 驱动力大小 在陶瓷系统中的重要性 初次 在金属中较重要。 硅酸盐 基质塑性形变所增加 0.4~4.2J/g 在金属中较重要。硅酸盐材 在金属中较重要。 在金属中较重要。 再结 的能量。 0.4~4.2J/g 材料热加工时塑性形变较小。 材料热加工时塑性形变较小。 的能量。 ~ 料热加工时塑性形变较小。 料热加工时塑性形变较小。 晶 晶 粒 长 大 二 次 再 结 晶 晶界两侧曲率的差异 界面两边存在 下 界面两边存在G下, 晶界向曲率半径小的 0.4~2J/g ~ 晶粒中心推进, 晶粒中心推进,晶粒 平均生长。 平均生长。 大晶粒晶面与邻近高 表面能和小曲率半径 的晶面相比较有较低 的表面能。 的表面能。
x /r 运 1 1= 算 x2 / r2
0.1 =( x / r 16 x/r 0.0725
0.1 x/ r
16
8
16
8
0.1 x/ r
1 5 2/ 3 2 6 =( ) ( )
16
8
8
0.066
0.112
0.058
9-7 在制造透明 2O3材料时,原始粉料粒度为 m,烧结至最高 - 在制造透明Al 材料时,原始粉料粒度为2 , 温度保温0.5小时 测得晶粒尺寸为10 小时, 小时, 温度保温 小时,测得晶粒尺寸为 m,试问若保温 小时, ,试问若保温2小时 晶粒尺寸多大?为抑制晶粒生长加入0.1%MgO,此时若保温 晶粒尺寸多大?为抑制晶粒生长加入 , 2小时,晶粒尺寸又多大? 小时, 小时 晶粒尺寸又多大? 分析:晶粒正常长大计算式: 分析:晶粒正常长大计算式:
x 2 / r 2 = kr 2 x 1 / r1 = kr 1 16
2 3 1 t2 3 2 1 3 t2 3 1 t1 3 2 3
流动传质 求t
溶解- 溶解-沉淀
1
3 16 5 ( )
5
=
1 64 3 ( )
t2
16 2 64 2 ( ) =( ) 5 t2
25.6 求 x/r 0.1 x/ r
填空题 1、在晶粒尺寸平均增长时,为使气孔与晶界一起移动,可以采 、在晶粒尺寸平均增长时,为使气孔与晶界一起移动, 取的措施是______、_______和________。 取的措施是 、 和 。 2、在扩散传质为主的烧结过程中,进入烧结的中后期时,若温 、在扩散传质为主的烧结过程中,进入烧结的中后期时, 度和晶粒尺寸不变,则气孔率随烧结时间(t)以_____次方关系而 度和晶粒尺寸不变,则气孔率随烧结时间 以 次方关系而 减少。 减少。 3、在烧结中、后期,往往伴随晶粒生长过程。晶粒的长大对物 、在烧结中、后期,往往伴随晶粒生长过程。 料烧结速率的影响( ) 料烧结速率的影响 A、没有影响。 B、延缓烧结速率。 C、促进烧结速率。 、没有影响。 、延缓烧结速率。 、促进烧结速率。 D、开始促进,随着烧结时间的延长而对烧结速率起延缓作用。 、开始促进,随着烧结时间的延长而对烧结速率起延缓作用。 4、某物料粉碎成粒度为 m的物料,经2小时烧结后,其颈部 的物料, 小时烧结后 小时烧结后, 、某物料粉碎成粒度为5 的物料 半径增长率x/r=0.1,为使其达到 不考虑晶粒生长), 半径增长率 ,为使其达到x/r=0.2(不考虑晶粒生长 ,又 不考虑晶粒生长 经过64小时的烧结 这是在( )传质机理条件下进行的烧结的。 小时的烧结。 传质机理条件下进行的烧结的。 经过 小时的烧结。这是在 传质机理条件下进行的烧结的 A、粘性流动 B、溶解-沉淀 、 、溶解- C、蒸发-凝聚 D、体积扩散 、蒸发- 、
A、晶格扩散 、 E、颗粒重排 、
D、流动传质 、
F、蒸发-凝聚 G、非本征扩散 H、溶解-沉淀 、蒸发- 、 、溶解-
7、属于固相烧结的典型传质有_____和_____两种,液相烧结的典型 、属于固相烧结的典型传质有 两种, 和 两种 传质有____和_____。这四种传质颈部增长 与烧结时间关系分别 和 传质有 。这四种传质颈部增长x/r 为_____、_____、______和_____。 、 、 和 。
5、下列过程中, ( 、下列过程中, A、蒸发-凝聚 、蒸发-
)能使烧结产物强度增大而不产生致密化过程。 能使烧结产物强度增大而不产生致密化过程。 能使烧结产物强度增大而不产生致密化过程 B、体积扩散 、 D、表面扩散 、 A、D 、 B、F 、
C、粘性(塑性 扩散 、粘性 塑性 塑性)扩散
6、在烧结过程中,只改变气孔形状而不引起坯体致密化的传质 、在烧结过程中, 方式有( 方式有 ) B、表面扩散 、 C、晶界扩散 、