数控车床对刀操作时容易出现的问题及操作注意事项
项目二数控车床对刀操作课件
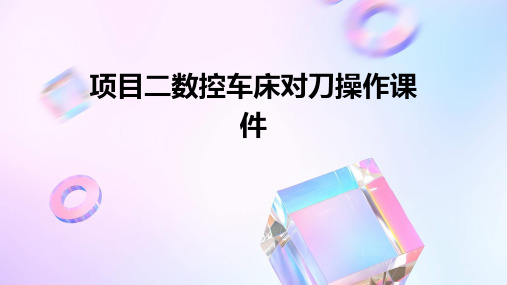
目录
• 对刀操作的基本概念 • 对刀操作的步骤 • 对刀操作的注意事项 • 对刀操作的应用实例 • 对刀操作常见问题及解决方案
01
对刀操作的基本概念
对刀操作的定义
对刀操作是指在数控车床上,通过调整刀具相对于工件的位 置,使刀具的刀位点对准工件坐标系的某一参考点,以确保 加工过程中刀具与工件正确对齐的过程。
2. 使用减震装置或工具夹具等辅助工具 ,减小振动传递;
详细描述:切削振动的原因有多种,如 工件材料硬度过高等。为了解决这一问 题,可以采取以下措施
1. 调整主轴转速和切削深度等参数,以 改变切削力的变化规律,减少振动;
加工精度问题及解决方案
总结词:加工精度问题是对刀操作中的核心问题之一, 它直接影响到工件的质量和性能。 1. 选用高精度刀具和夹具,提高对刀精度;
总结词
异形零件的形状各异,对刀操作需要根据零件的具体形状进行调整。
详细描述
在异形零件的对刀操作中,需要仔细观察工件的形状,并根据需要进行调整。对于某些具有特殊形状的零件,可 能需要采用特殊的对刀方法,以确保加工精度和表面质量。同时,还需要特别注意安全问题,以避免因操作不当 而造成意外事故。
05
对刀操作常见问题及解决 方案
刀具安装
将刀具正确安装在刀架上 ,确保刀具夹紧牢固,不 会松动。
刀具调整
调整刀具的角度、高度和 偏移量,以适应加工需求 。
刀具补偿参数设置
刀具长度补偿
根据刀具的实际长度,设 置刀具长度补偿参数,确 保加工过程中的切深与编 程深度一致。
刀具半径补偿
根据刀具的实际半径,设 置刀具半径补偿参数,确 保加工出的工件轮廓与编 程轮廓一致。
数控车床对刀方法
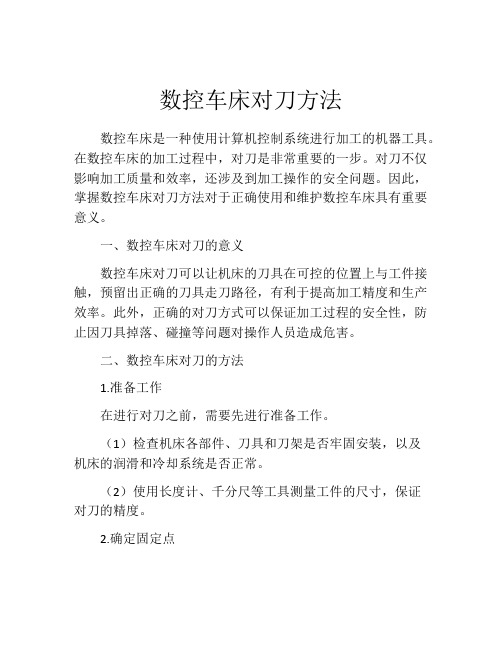
数控车床对刀方法数控车床是一种使用计算机控制系统进行加工的机器工具。
在数控车床的加工过程中,对刀是非常重要的一步。
对刀不仅影响加工质量和效率,还涉及到加工操作的安全问题。
因此,掌握数控车床对刀方法对于正确使用和维护数控车床具有重要意义。
一、数控车床对刀的意义数控车床对刀可以让机床的刀具在可控的位置上与工件接触,预留出正确的刀具走刀路径,有利于提高加工精度和生产效率。
此外,正确的对刀方式可以保证加工过程的安全性,防止因刀具掉落、碰撞等问题对操作人员造成危害。
二、数控车床对刀的方法1.准备工作在进行对刀之前,需要先进行准备工作。
(1)检查机床各部件、刀具和刀架是否牢固安装,以及机床的润滑和冷却系统是否正常。
(2)使用长度计、千分尺等工具测量工件的尺寸,保证对刀的精度。
2.确定固定点固定点是指在数控下处理的零点的位置,即要加工工件的原点。
通常,固定点需要根据手册或数控系统的参数手动输入。
在数控系统中,固定点可以利用修正处理实现校准。
3.选择刀具选择合适的刀具对于加工的质量和效率影响很大。
刀具的选择需要考虑加工件材质、表面形状、线速度、切削用量和切削液条件等。
在选择刀具的时候需要尽量避免出现中心偏差,以保证对刀的准确性。
4.调整刀具位置刀具需要在机床上调整到正确的位置,以保证加工质量和效率。
具体来说,以下两种对刀方式常见:(1)刮刀法:在使用前,需要将刀具调整到靠近工件的位置,打开机床手轮,然后用刀片轻轻的刮掉工件上的涂层。
当涂层刮净后,可以逐渐调整刀具的出刀量,将刀具调整到最佳位置。
(2)对刀仪法:在使用对刀仪的时候,需要在工件和刀具之间放置对刀仪,测量靠近工件的刀具尖端和对刀仪的距离,然后根据测量结果调整刀具的位置。
5.校正刃口补偿值在数控车床加工过程中,刃口补偿值是一个很重要的参数。
为了保证刃口补偿值的准确性,需要根据实际情况和手册要求进行校正。
通常在进行磨刀后需要重新校正刃口补偿值,以确保机床的加工精度。
数控车床常见问题及解决方法

数控车床常见问题及解决方法数控车床是一种通过编写数控程序自动加工零件的机床,其优点在于高精度、高效率和自动化程度高,常用于生产中、小型批量生产以及精密零件加工等领域。
然而,由于数控系统较为复杂,使用不当或者设备老化等原因可能会导致一些常见问题的出现,例如偏差过大、加工粗糙度不满足要求等。
下面,本文将针对数控车床常见问题进行解析,并提供相关的解决方法供读者参考。
1. 偏差过大偏差过大是数控车床加工中常见的问题,可能由于工具磨损、夹具变形、材料质量差等原因所致。
解决方法一般有以下几种:1) 对机床进行维护保养,保证夹具、刀具和加工过程中的材料质量等达到标准。
2) 加强对数控程序编写的规范性和严谨性的要求,避免编写不当或者失误所导致的偏差问题。
3)进行数控系统的校准和调试,保证数控系统的精度和稳定性。
2. 加工粗糙度不满足要求加工粗糙度不满足要求常见于数控车床加工的细节部分,常见原因可能是刀具选型不合适、刀片磨损、夹具变形等问题,解决方法一般有以下几种:1) 进行装夹和调整刀位的操作,保证加工过程中的稳定性和精度。
2) 选择合适的刀具和工艺参数进行加工,避免因为刀具磨损或者加工参数错误所导致的问题。
3)做好设备的检测和维护工作,及时更换磨损的刀片或者进行设备的调整。
3. 其他常见问题除了以上两种问题外,数控车床加工中还存在一些其他问题,例如:1) 程序调错:由于程序编写错误或者使用不当,可能会导致加工失败或者损坏机床等问题。
解决方法:进行编程时要规范严谨,确保编写正确无误;在操作数控设备时要仔细检查程序是否正确并且保证程序更改前做好备份。
2) 模具寿命短:由于模具材质选用不当或者寿命到期等原因,可能会导致模具使用寿命短,影响生产效率。
解决方法:正确选择模具材质;以及经常进行模具的保养维护以保证其有足够的使用寿命。
总之,对于数控车床的使用,除了对设备自身的保养和维护外,还需要保证程序编写的严谨和正确。
同时,针对问题,应该根据具体情况判断,采取相应的解决措施。
简述数控机床对刀的过程和注意哪些方面

数控机床对刀的过程和注意事项一、什么是数控机床对刀在使用数控机床进行加工过程中,正确的对刀操作是非常重要的。
数控机床对刀是指通过一系列的操作和调整,使刀具与工件之间达到理想的对刀状态,以便正常加工工件。
这个过程中还需要注意一些关键事项,以确保加工质量和安全。
二、数控机床对刀的过程数控机床对刀的过程可以分为以下几个步骤:1. 设定参考点首先,需要设定一个参考点作为对刀的基准点。
通常情况下,参考点会选择工件的一个角点或者边缘作为基准。
2. 加工刀具的设定接下来,需要对加工刀具进行设定。
这包括选择合适的切削刃、确定刀具安装位置以及设定刀具的刀尖与刀夹的距离。
3. 对刀工具的设定然后,需要对刀具进行设定。
这包括调整刀具的刀尖高度、刀具的半径补偿以及切削刃的长度设定。
4. 加工路径的设定在对刀过程中,还需要设置加工路径。
这包括确定刀具的进给速度、切削速度以及确定刀具的运动轨迹。
完成设置后,需要对刀具进行检查。
通过测量刀具的位置和角度,确定切削刃是否正确对准工件表面。
如果发现偏差,需要进行微调,直到达到理想的对刀状态。
6. 再次验证和修正最后,对刀完成后,需要再次验证对刀的准确性。
这可以通过测量加工后的工件尺寸和形状来进行验证。
如果出现偏差,需要进行修正,直到达到要求的加工精度。
三、数控机床对刀的注意事项在进行数控机床对刀的过程中,需要注意以下几个方面:1. 安全注意事项•在对刀过程中,必须确保机床处于安全状态,刀具处于停止状态。
避免对刀时发生意外伤害。
•切勿用手直接接触刀具,以免被刀具伤到。
应使用合适的工具进行调整和检查。
2. 刀具的选择和安装•根据加工工件的要求选择合适的切削刃和刀具。
不同的加工材料和工件形状需要选择不同的刀具。
•在安装刀具时,要确保刀具正确安装,不可有松动或倾斜现象。
否则可能导致加工精度下降或刀具偏差。
3. 对刀工具的设定•在对刀工具的设定过程中,应使用合适的测量工具进行测量和调整。
确保对刀工具的准确性和稳定性。
广数控车床对刀操作步骤
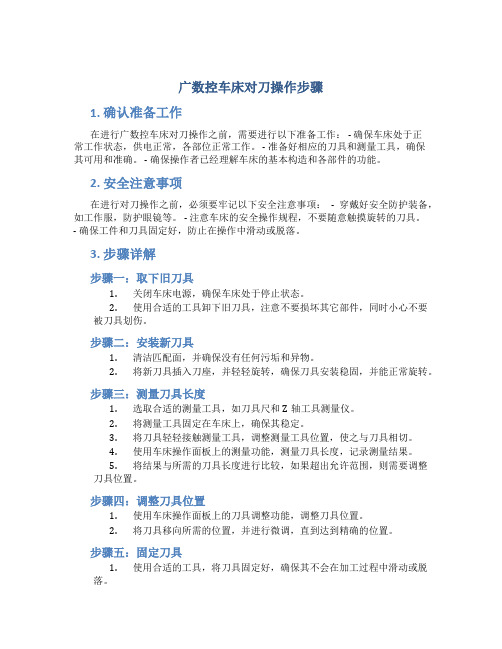
广数控车床对刀操作步骤1. 确认准备工作在进行广数控车床对刀操作之前,需要进行以下准备工作: - 确保车床处于正常工作状态,供电正常,各部位正常工作。
- 准备好相应的刀具和测量工具,确保其可用和准确。
- 确保操作者已经理解车床的基本构造和各部件的功能。
2. 安全注意事项在进行对刀操作之前,必须要牢记以下安全注意事项:- 穿戴好安全防护装备,如工作服,防护眼镜等。
- 注意车床的安全操作规程,不要随意触摸旋转的刀具。
- 确保工件和刀具固定好,防止在操作中滑动或脱落。
3. 步骤详解步骤一:取下旧刀具1.关闭车床电源,确保车床处于停止状态。
2.使用合适的工具卸下旧刀具,注意不要损坏其它部件,同时小心不要被刀具划伤。
步骤二:安装新刀具1.清洁匹配面,并确保没有任何污垢和异物。
2.将新刀具插入刀座,并轻轻旋转,确保刀具安装稳固,并能正常旋转。
步骤三:测量刀具长度1.选取合适的测量工具,如刀具尺和Z轴工具测量仪。
2.将测量工具固定在车床上,确保其稳定。
3.将刀具轻轻接触测量工具,调整测量工具位置,使之与刀具相切。
4.使用车床操作面板上的测量功能,测量刀具长度,记录测量结果。
5.将结果与所需的刀具长度进行比较,如果超出允许范围,则需要调整刀具位置。
步骤四:调整刀具位置1.使用车床操作面板上的刀具调整功能,调整刀具位置。
2.将刀具移向所需的位置,并进行微调,直到达到精确的位置。
步骤五:固定刀具1.使用合适的工具,将刀具固定好,确保其不会在加工过程中滑动或脱落。
2.检查刀具固定情况,确保刀具安全可靠。
步骤六:测试刀具1.打开车床电源,启动车床。
2.测试刀具是否安装正确,并进行必要的微调。
3.确保刀具在旋转过程中不会碰到其它部件。
4.如有需要,对刀具进行进一步的调整。
步骤七:完成对刀操作对刀操作完成后,可以进行加工操作。
确保在加工过程中时刻关注刀具的磨损情况,并根据需要及时更换或调整刀具。
4. 注意事项•在上述步骤中,操作者应根据具体情况进行调整和判断,并注意自身安全。
数控车床对刀操作步骤及主意事项

数控车床对刀操作步骤及主要注意事项引言数控车床是一种常用的自动化机床,它能够通过计算机程序控制切削刀具进行各种精密加工。
对刀操作是数控车床上的一项重要工作,不仅关系到加工质量,还关系到操作人员的安全。
本文将介绍数控车床对刀的操作步骤及一些需要注意的事项。
操作步骤1. 准备工作在进行对刀操作之前,需要进行一些准备工作:- 检查车床设备是否正常运行,确保各项安全保护设施功能正常; - 准备好合适的刀具,并检查刀具的磨损程度;- 确定加工工件的材料和尺寸,并将工件正确装夹在车床上。
2. 测量工件和刀具对刀操作的关键是准确测量工件和刀具的尺寸。
- 使用合适的测量工具(如卡尺、游标卡尺等)测量工件的尺寸,包括直径、长度等。
记录下测量结果; - 使用刀具测量仪(或编程装置)测量刀具的长度、直径等尺寸,并记录下测量结果。
3. 汇编刀具根据测量结果,正确选择刀具,并进行刀具的汇编。
- 根据加工要求选择合适的刀具,并将其正确安装在车床的刀架上; - 使用专用工具对刀具进行调整,确保刀具的位置、夹持力等参数符合要求。
4. 进行对刀操作对刀操作是一项技术性较高的工作,需要仔细操作。
- 打开数控车床的操作界面,选择对刀操作功能; - 根据测量结果输入刀具和工件的尺寸等参数,然后启动对刀操作; - 数控车床会根据输入的参数自动调整刀具的位置和补偿值,确保加工的准确性。
5. 对刀结果检验和调整完成对刀操作后,需要对对刀结果进行检验,确保加工的准确性和质量。
- 使用测量工具对加工后的工件进行检验,与加工要求进行对比,判断偏差是否在允许范围内; - 如果测量结果有偏差,需要根据实际情况进行调整,如重新测量,重新选择刀具等。
注意事项在进行数控车床对刀操作时,需要注意以下事项,以确保操作安全和加工质量:1. 熟悉数控车床的操作规程和安全操作要求,遵守相关的安全操作规定; 2. 选择合适的刀具,并保证其质量和磨损情况符合要求; 3. 对工件进行正确的装夹,保证工件与车床床身之间的配合间隙适当; 4. 准确测量工件和刀具的尺寸,确保测量结果准确无误; 5. 在对刀操作过程中,避免手部接近刀具,以免发生意外伤害;6. 在进行刀具调整时,切勿用力过度,以免损坏刀具和车床设备;7. 对刀完成后,及时清理工作区域和设备,保持车床的清洁和良好的工作环境。
数控车床对刀操作
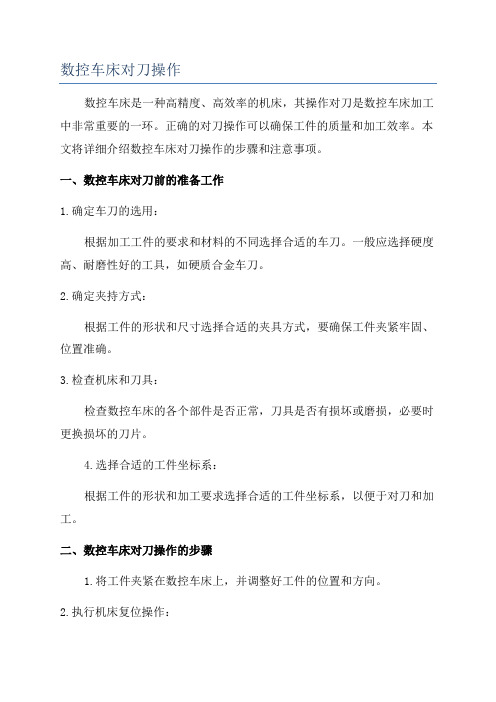
数控车床对刀操作数控车床是一种高精度、高效率的机床,其操作对刀是数控车床加工中非常重要的一环。
正确的对刀操作可以确保工件的质量和加工效率。
本文将详细介绍数控车床对刀操作的步骤和注意事项。
一、数控车床对刀前的准备工作1.确定车刀的选用:根据加工工件的要求和材料的不同选择合适的车刀。
一般应选择硬度高、耐磨性好的工具,如硬质合金车刀。
2.确定夹持方式:根据工件的形状和尺寸选择合适的夹具方式,要确保工件夹紧牢固、位置准确。
3.检查机床和刀具:检查数控车床的各个部件是否正常,刀具是否有损坏或磨损,必要时更换损坏的刀片。
4.选择合适的工件坐标系:根据工件的形状和加工要求选择合适的工件坐标系,以便于对刀和加工。
二、数控车床对刀操作的步骤1.将工件夹紧在数控车床上,并调整好工件的位置和方向。
2.执行机床复位操作:在数控系统中选择“复位”功能,使数控车床回到初始状态。
3.选择对刀方式:有多种对刀方式可供选择,如纵向对刀、横向对刀、刀尖对刀等。
根据具体情况选择合适的对刀方式。
4.第一次对刀:首先,用手摇车床将车刀靠近工件,使其与工件轻微接触,然后通过数控系统的操作将车刀靠近工件,直至工件上出现微弧光斑。
此时,数控系统会自动记录车刀位置。
5.第二次对刀:将车刀离开工件,重新摆放好刀具,再次将车刀靠近工件。
通过数控系统的操作,使车刀与工件轻微接触,并记录下车刀的位置。
6.对刀参数计算:利用数控系统的功能,计算出车刀位置需要调整的数值,并将其输入系统。
7.进行调整:根据计算结果,通过数控系统调整车刀位置,使其达到预期的位置。
8.再次对刀:将车刀重新靠近工件并进行微调,直至车刀与工件轻微接触。
通过数控系统的操作,记录车刀的准确位置。
9.完成对刀:对刀操作完成后,检查车刀位置是否准确,并进行必要的微调。
三、数控车床对刀操作的注意事项1.安全第一:操作人员在进行对刀操作时,必须严格遵守安全操作规程,切勿将手部或身体靠近旋转的刀具。
数控车床常见问题及解决方法

数控车床常见问题及解决方法数控车床是一种高精度、高效率的机床,广泛应用于各种加工领域。
然而,在使用过程中可能会遇到一些常见问题,下面我将就数控车床常见问题及解决方法进行总结。
1. 加工精度不达标:加工精度是数控车床的重要指标,如果出现精度不达标的情况,首先需要检查刀具磨损情况,如果刀具磨损较大,需要更换刀具。
其次,可以检查夹具的精度,如果夹具不稳定,会导致工件的位置不准确。
最后,可以调整数控系统的参数,例如提高伺服电机的控制精度,调整传动件的间隙等。
2. 加工过程中出现振动:振动是数控车床的常见问题,它不仅会降低加工精度,还会影响机床寿命。
首先,需要检查工件夹持情况,如果夹持不稳定,可以更换夹具或调整夹持方式。
其次,可以检查刀具的刃数和刃角,过大或过小的刃数和刃角都会引起振动。
最后,可以调整数控系统的参数,例如降低进给速度、提高切削速度等。
3. 加工出现毛刺或切痕:毛刺和切痕是数控车床加工中常见的表面缺陷问题,主要原因是刀具磨损或刀具的刃角不合适。
解决方法是定期更换刀具,保持刀具的锋利度。
另外,合理选择切削速度和进给速度也可以减少毛刺和切痕的产生。
4. 难以调试刀具位置:数控车床的刀具位置调试是加工中的重要环节,但有时会遇到难以调试的情况。
首先,可以检查刀具夹持的紧固情况,如果夹持不牢固,会导致刀具位置难以精确定位。
其次,可以使用刀具几何参数测量仪对刀具位置进行精确测量,然后根据测量结果进行调整。
最后,可以调整数控系统的参数,例如调整工件坐标系和刀具补偿值等。
5. 数控系统故障:数控系统是数控车床的核心部件,如果出现故障,会影响整个加工过程。
常见的故障包括电路板故障、伺服电机故障等。
解决方法是检查故障代码,并参考数控系统的故障排除手册进行排查。
如果无法解决,需要联系数控系统供应商或维修人员。
以上是数控车床常见问题及解决方法的相关参考内容,希望对使用数控车床的人员能够有所帮助。
在使用数控车床时,需要注意安全操作,定期保养和维护机床,以确保其正常工作和延长使用寿命。
数控车对刀误差怎么样解决
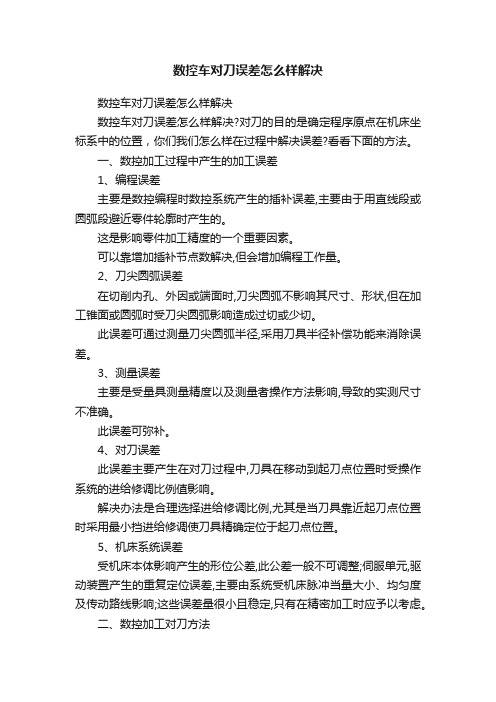
数控车对刀误差怎么样解决数控车对刀误差怎么样解决数控车对刀误差怎么样解决?对刀的目的是确定程序原点在机床坐标系中的位置,你们我们怎么样在过程中解决误差?看看下面的方法。
一、数控加工过程中产生的加工误差1、编程误差主要是数控编程时数控系统产生的插补误差,主要由于用直线段或圆弧段避近零件轮廓时产生的。
这是影响零件加工精度的一个重要因素。
可以靠增加插补节点数解决,但会增加编程工作量。
2、刀尖圆弧误差在切削内孔、外因或端面时,刀尖圆弧不影响其尺寸、形状,但在加工锥面或圆弧时受刀尖圆弧影响造成过切或少切。
此误差可通过测量刀尖圆弧半径,采用刀具半径补偿功能来消除误差。
3、测量误差主要是受量具测量精度以及测量者操作方法影响,导致的实测尺寸不准确。
此误差可弥补。
4、对刀误差此误差主要产生在对刀过程中,刀具在移动到起刀点位置时受操作系统的进给修调比例值影响。
解决办法是合理选择进给修调比例,尤其是当刀具靠近起刀点位置时采用最小挡进给修调使刀具精确定位于起刀点位置。
5、机床系统误差受机床本体影响产生的形位公差,此公差一般不可调整;伺服单元,驱动装置产生的重复定位误差,主要由系统受机床脉冲当量大小、均匀度及传动路线影响;这些误差量很小且稳定,只有在精密加工时应予以考虑。
二、数控加工对刀方法数控加工的对刀,对其处理的好坏直接影响到加工零件的精度,还会影响数控机床的操作。
所谓对刀,就是在工件坐标系中使刀具的刀位点位于起刀点(对刀点)上,使其在数控程序的控制下,由此刀具所切削出的加工表面相对于定位基准有正确的尺寸关系,从而保证零件的加工精度要求。
在数控加工中,对刀的基本方法有试切法、对刀仪对刀、ATC对刀和自动对刀等。
1、试切法根据数控机床所用的位置检测装置不同,试切法分为相对式和绝对式两种。
在相对式试切法对刀中,可采用三种方法:一是用量具(如钢板尺等)直接测量,对准对刀尺寸,这种对刀方法简便但不精确;二是通过刀位点与定位块的工作面对齐后,移开刀具至对刀尺寸,这种方法的对刀准确度取决于刀位点与定位块工作面对齐的精度;三是将工件加工面先光一刀,测出工件尺寸,间接算出对刀尺寸,这种方法最为精确。
数控车床的对刀方法
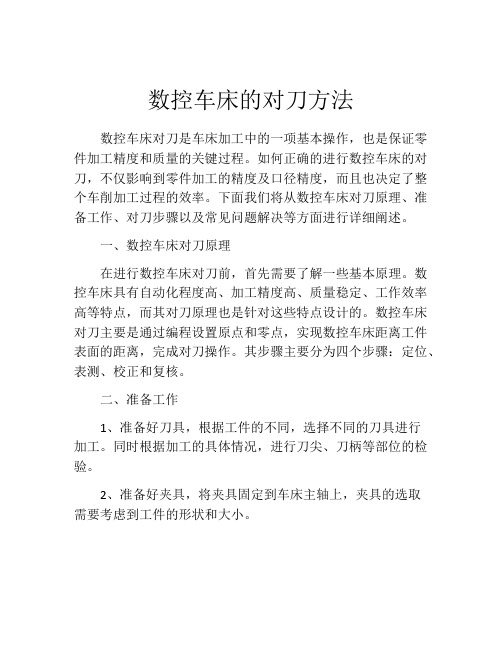
数控车床的对刀方法数控车床对刀是车床加工中的一项基本操作,也是保证零件加工精度和质量的关键过程。
如何正确的进行数控车床的对刀,不仅影响到零件加工的精度及口径精度,而且也决定了整个车削加工过程的效率。
下面我们将从数控车床对刀原理、准备工作、对刀步骤以及常见问题解决等方面进行详细阐述。
一、数控车床对刀原理在进行数控车床对刀前,首先需要了解一些基本原理。
数控车床具有自动化程度高、加工精度高、质量稳定、工作效率高等特点,而其对刀原理也是针对这些特点设计的。
数控车床对刀主要是通过编程设置原点和零点,实现数控车床距离工件表面的距离,完成对刀操作。
其步骤主要分为四个步骤:定位、表测、校正和复核。
二、准备工作1、准备好刀具,根据工件的不同,选择不同的刀具进行加工。
同时根据加工的具体情况,进行刀尖、刀柄等部位的检验。
2、准备好夹具,将夹具固定到车床主轴上,夹具的选取需要考虑到工件的形状和大小。
3、安装好测头,并对其进行校准。
测头的精度直接影响到加工精度,所以在安装测头之前,一定要检查好测头的精度和准确程度,确保其可靠性。
4、指定好原点及零点,原点具有特殊的意义,指的是机床的固定点,所有的测量都是以这个点为基础,而零点则是指刀具离工件表面的距离,即数控车床进行加工时,刀具和工件距离的最小值。
三、对刀步骤1、定位:将夹具握紧工件,确定工件的位置。
这一步是整个对刀过程中十分关键的一步,需要运用专业工具进行定位。
定位具体方法根据工件形状的不同而有所不同。
2、表测:按照正常的夹法夹紧刀具,车床主轴旋转。
将手摇车床主轴进给轮旋转到零位,然后将测头放置到工件表面上,将表头调至位于车床主轴的刀尖、刀柄之中。
这一步是对加工的精度评估,通过测头测量,求出实际加工距离与预设距离之间的距离差值(误差),用于进行下一步的校准。
3、校正:通过调整测头,调整刀尖的位置,使其与实际加工距离相等。
具体方法为:根据表测数据,通过对刀偏差进行计算,并将测量值进行调节,使零点与对刀偏差精确重合。
数控车床对刀操作时容易出现的问题及操作注意事项
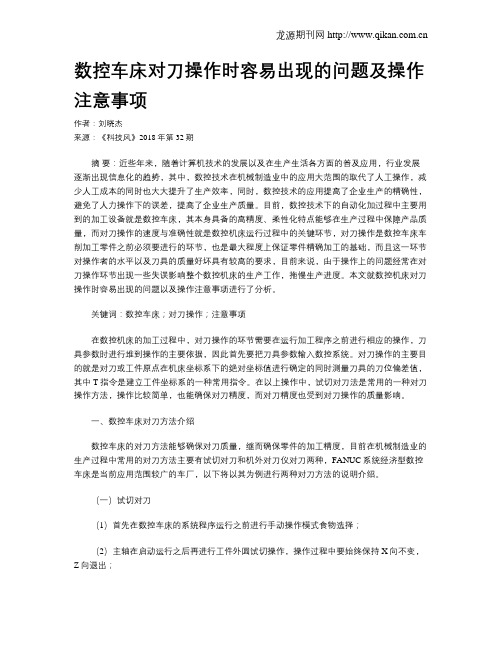
数控车床对刀操作时容易出现的问题及操作注意事项作者:刘晓杰来源:《科技风》2018年第32期摘要:近些年来,随着计算机技术的发展以及在生产生活各方面的普及应用,行业发展逐渐出现信息化的趋势,其中,数控技术在机械制造业中的应用大范围的取代了人工操作,减少人工成本的同时也大大提升了生产效率,同时,数控技术的应用提高了企业生产的精确性,避免了人力操作下的误差,提高了企业生产质量。
目前,数控技术下的自动化加过程中主要用到的加工设备就是数控车床,其本身具备的高精度、柔性化特点能够在生产过程中保障产品质量,而对刀操作的速度与准确性就是数控机床运行过程中的关键环节,对刀操作是数控车床车削加工零件之前必须要进行的环节,也是最大程度上保证零件精确加工的基础,而且这一环节对操作者的水平以及刀具的质量好坏具有较高的要求,目前来说,由于操作上的问题经常在对刀操作环节出现一些失误影响整个数控机床的生产工作,拖慢生产进度。
本文就数控机床对刀操作时容易出现的问题以及操作注意事项进行了分析。
关键词:数控车床;对刀操作;注意事项在数控机床的加工过程中,对刀操作的环节需要在运行加工程序之前进行相应的操作,刀具参数时进行堆到操作的主要依据,因此首先要把刀具参数输入数控系统。
对刀操作的主要目的就是对刀或工件原点在机床坐标系下的绝对坐标值进行确定的同时测量刀具的刀位偏差值,其中T指令是建立工件坐标系的一种常用指令。
在以上操作中,试切对刀法是常用的一种对刀操作方法,操作比较简单,也能确保对刀精度,而对刀精度也受到对刀操作的质量影响。
一、数控车床对刀方法介绍数控车床的对刀方法能够确保对刀质量,继而确保零件的加工精度,目前在机械制造业的生产过程中常用的对刀方法主要有试切对刀和机外对刀仪对刀两种,FANUC系统经济型数控车床是当前应用范围较广的车厂,以下将以其为例进行两种对刀方法的说明介绍。
(一)试切对刀(1)首先在数控车床的系统程序运行之前进行手动操作模式食物选择;(2)主轴在启动运行之后再进行工件外圆试切操作,操作过程中要始终保持X向不变,Z向退出;(3)主轴暂停运行之后将工件的外径值测量出来并进行记录;(4)选择数控车床的MDI操作模式;(5)按下“offsetsitting”按钮;(6)找到屏幕下方的“坐标系”软键之后按下去;(7)可以看见光标会移至“G54”;(8)之后向系统中输入X及测量的直径值;(9)再按下屏幕下方的“测量”软键;(10)启动主轴,试切工件端面,保持Z向不变,X向退出;(11)主轴暂停后,重复以上(4)—(9)步,将第(8)步中的X及测量值改为 Z0。
数车加工中,对刀常见的错误有哪些?

数车加工中,对刀常见的错误有哪些?
对刀对车削加工的重要性不言而喻,对刀数据的准确与否决定了后续的工件试切的安全。
在这里咱们就简单的说下对刀中常见的错误。
1、开机后操作人员没有对机床进行回零操作
开机后操作人员没有对对刀进行回零将导致机床对刀数据准确性降低,导致对刀错误。
部分人员忘记建立机床原点基准坐标也可以在定程度上导致自身的对刀效果降低,造成对刀有误。
2、刀补搞混
例如当前刀具为2号刀具,对刀数据虽然准确,但却输入到1号刀具补偿位置,程序运行时调用2号刀具及2号刀具补偿时,则会出现重大数据错误而引发事故。
除此之外,在刀补的过程中操作人员对MDI手动换刀操作没有进行手动退补,这种状况导致自身的推出刀补效果降低。
在进行刀补数据设置的过程中,刀补人员没有对数据进行准确处理,导致刀补过程中数据出现偏颇,造成对刀错误。
3、手轮摇错方向
使用电子手轮试切后退刀时手轮摇反方向,应该退刀反而进刀切入工件,此时一般是刀具或工件损坏,不会造成较大的损失。
数控车床对刀操作时容易出现的问题及操作注意事项
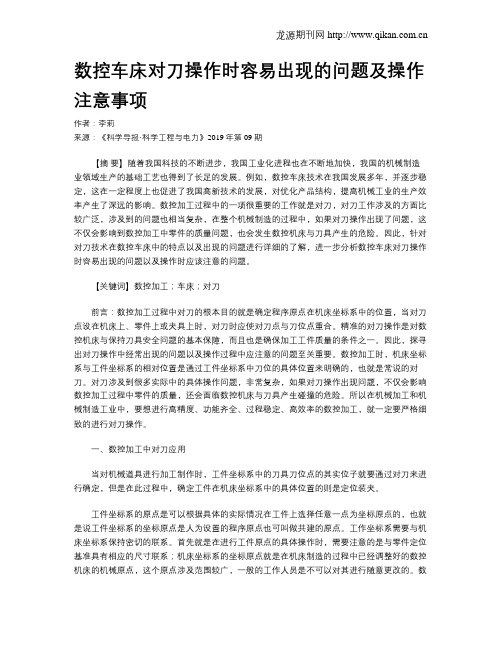
数控车床对刀操作时容易出现的问题及操作注意事项作者:李莉来源:《科学导报·科学工程与电力》2019年第09期【摘要】随着我国科技的不断进步,我国工业化进程也在不断地加快,我国的机械制造业领域生产的基础工艺也得到了长足的发展。
例如,数控车床技术在我国发展多年,并逐步稳定,这在一定程度上也促进了我国高新技术的发展,对优化产品结构,提高机械工业的生产效率产生了深远的影响。
数控加工过程中的一项很重要的工作就是对刀,对刀工作涉及的方面比较广泛,涉及到的问题也相当复杂,在整个机械制造的过程中,如果对刀操作出现了问题,这不仅会影响到数控加工中零件的质量问题,也会发生数控机床与刀具产生的危险。
因此,针对对刀技术在数控车床中的特点以及出现的问题进行详细的了解,进一步分析数控车床对刀操作时容易出现的问题以及操作时应该注意的问题。
【关键词】数控加工;车床;对刀前言:数控加工过程中对刀的根本目的就是确定程序原点在机床坐标系中的位置,当对刀点设在机床上、零件上或夹具上时,对刀时应使对刀点与刀位点重合。
精准的对刀操作是对数控机床与保持刀具安全问题的基本保障,而且也是确保加工工件质量的条件之一。
因此,探寻出对刀操作中经常出现的问题以及操作过程中应注意的问题至关重要。
数控加工时,机床坐标系与工件坐标系的相对位置是通过工件坐标系中刀位的具体位置来明确的,也就是常说的对刀。
对刀涉及到很多实际中的具体操作问题,非常复杂,如果对刀操作出现问题,不仅会影响数控加工过程中零件的质量,还会面临数控机床与刀具产生碰撞的危险。
所以在机械加工和机械制造工业中,要想进行高精度、功能齐全、过程稳定、高效率的数控加工,就一定要严格细致的进行对刀操作。
一、数控加工中对刀应用当对机械道具进行加工制作时,工件坐标系中的刀具刀位点的其实位子就要通过对刀来进行确定,但是在此过程中,确定工件在机床坐标系中的具体位置的则是定位装夹。
工件坐标系的原点是可以根据具体的实际情况在工件上选择任意一点为坐标原点的,也就是说工件坐标系的坐标原点是人为设置的程序原点也可叫做共建的原点。
排刀数控车床对刀方法及常见故障处理
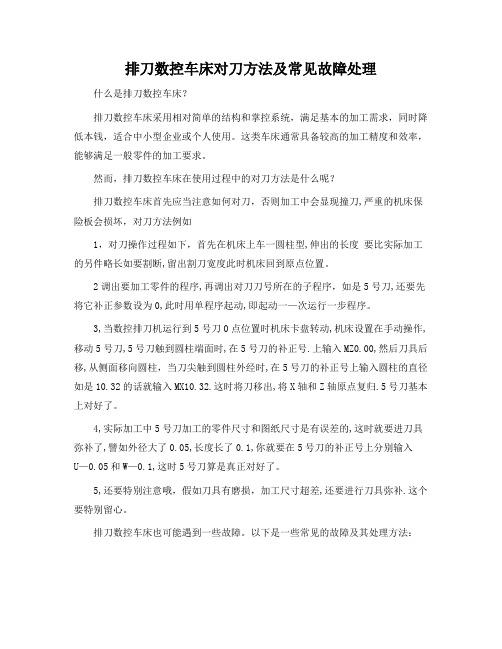
排刀数控车床对刀方法及常见故障处理什么是排刀数控车床?排刀数控车床采用相对简单的结构和掌控系统,满足基本的加工需求,同时降低本钱,适合中小型企业或个人使用。
这类车床通常具备较高的加工精度和效率,能够满足一般零件的加工要求。
然而,排刀数控车床在使用过程中的对刀方法是什么呢?排刀数控车床首先应当注意如何对刀,否则加工中会显现撞刀,严重的机床保险板会损坏,对刀方法例如1,对刀操作过程如下,首先在机床上车一圆柱型,伸出的长度要比实际加工的另件略长如要割断,留出割刀宽度此时机床回到原点位置。
2调出要加工零件的程序,再调出对刀刀号所在的子程序,如是5号刀,还要先将它补正参数设为0,此时用单程序起动,即起动一—次运行一步程序。
3,当数控排刀机运行到5号刀0点位置时机床卡盘转动,机床设置在手动操作,移动5号刀,5号刀触到圆柱端面时,在5号刀的补正号.上输入MZ0.00,然后刀具后移,从侧面移向圆柱,当刀尖触到圆柱外经时,在5号刀的补正号上输入圆柱的直径如是10.32的话就输入MX10.32.这时将刀移出,将X轴和Z轴原点复归.5号刀基本上对好了。
4,实际加工中5号刀加工的零件尺寸和图纸尺寸是有误差的,这时就要进刀具弥补了,譬如外径大了0.05,长度长了0.1,你就要在5号刀的补正号上分别输入U—0.05和W—0.1,这时5号刀算是真正对好了。
5,还要特别注意哦,假如刀具有磨损,加工尺寸超差,还要进行刀具弥补.这个要特别留心。
排刀数控车床也可能遇到一些故障。
以下是一些常见的故障及其处理方法:刀具返回不到零点:这类故障通常是由于掌控系统故障引起的。
可以试验检查并更换开关三极管,由于当开关三极管损坏时,高速回零点的高压电源无法打开,导致步进电机输出转矩不足,从而造成回零丢步。
刀架锁不紧:这可能是由发信盘位置没对正、系统反锁时间不足长或机械锁紧机构故障导致的。
可以通过拆开刀架,调整发信盘位置和系统反锁时间参数,以及检查并修复机械锁紧机构来解决这个问题。
简述数控机床对刀的过程和注意哪些方面
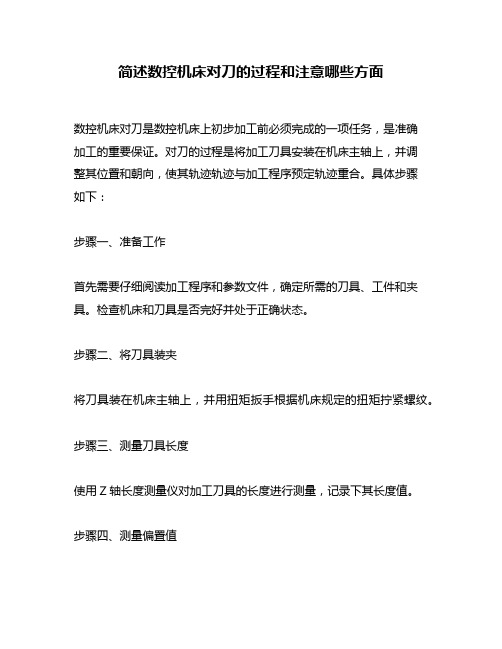
简述数控机床对刀的过程和注意哪些方面数控机床对刀是数控机床上初步加工前必须完成的一项任务,是准确加工的重要保证。
对刀的过程是将加工刀具安装在机床主轴上,并调整其位置和朝向,使其轨迹轨迹与加工程序预定轨迹重合。
具体步骤如下:步骤一、准备工作首先需要仔细阅读加工程序和参数文件,确定所需的刀具、工件和夹具。
检查机床和刀具是否完好并处于正确状态。
步骤二、将刀具装夹将刀具装在机床主轴上,并用扭矩扳手根据机床规定的扭矩拧紧螺纹。
步骤三、测量刀具长度使用Z轴长度测量仪对加工刀具的长度进行测量,记录下其长度值。
步骤四、测量偏置值将加工刀具向工件表面靠近一定距离,并使用刀具偏置仪测量其在X 轴和Z轴的偏置值。
步骤五、编写偏置值将测得的偏置值输入到机床的偏置寄存器中,从而把刀具的实际位置与计算机编制的程序所给位置一致。
步骤六、调整朝向进行刀位校准,判断刀具的朝向是否正确,在X、Z平面上和Y、Z平面上分别测量角度,确保刀具与工件表面的交角满足要求。
步骤七、测试刀具参照机床的相关操作手册对加工刀具进行测试,确认其在加工中没有出现异常情况,并对数控机床进行必要的维护保养。
需要注意的方面有:1. 设备的准备和保养应当充分,必须调节配合工作的关键参数,包括工件、刀具、夹紧装置、机床等选择。
2. 切削刀具的材料应符合切削加工要求,刃口尺寸不得超出精度范围。
3. 数字伺服系统一定要进行检查,机床各项参数、机床磨损和各零部件状态等都需要详细了解,保持最佳工作状态。
4. 加工完成后需要对机床进行充分清洗和维护保养,剩余的金属碎屑和油污都需要处理好,以及代替液压油,维护机床的清洁和起到优化机床工作状态的作用。
数控机床对刀的过程需要经过严格而细致的操作,过程中需要对各个要素进行精确定位和调整。
只有通过严格的操作流程和注意各方面细节,才能确保加工工件的精度和工作效率。
数控加工中易犯的低级错误及预防方法

加工中易犯的低级错误及预防方法1、手轮摇反预防措施:在摇动手轮前,先看一眼手轮的正反方向与应摇出的方向是否存在冲突。
做到看一遍再想一遍,已达到方向准确性,从而避免此问题的出现。
将衣袖扎紧,掌握正确使用手轮姿势,在摇动手轮时尽量做到避免过多动作,防止无意识碰到手轮。
摇动手轮的速度应该是先轻摇1到2格,确认无误后方可由慢到快地摇动。
2、刀补输反预防措施:在我们加工零件过程中因刀补输反导致零件报废的事例屡见不鲜。
在加工中每每需要输入刀补的时候我们都应该保持一个清醒的头脑,多计算。
输入刀补后观察刀补与上一件活的刀补方向是否一致,刀补数值是否相差过大。
3、测量错误预防措施:尺子使用前先校下精度,测量时确定工件所要测量的测量面无毛刺、铁削。
使用内/外径千分尺时最好在测量完后用卡尺卡下,确保读数的准确性。
4、扎刀预防措施:在对刀或校刀过程中由于操作者粗心大意容易发生扎刀。
所以在摇动手轮前一定要先确定好手轮的方向。
退刀时先将手轮打到X10上,摇1格。
如果是对刀在你摇出一个后塞片的与刀具的紧度会变松。
如果在校刀时则应该不会下削。
当刀具摇出工件一定距离后方可快速退刀。
5、看错标准件预防措施:使用标准件前,先校对所使用标准间与图纸尺寸是否一致。
不一致则要看是标准间比图纸尺寸大了还是小了。
测量零件时注意百分表的方向,最好在测量后用手前后扳下板测具,确定其测量值的大小和方向。
6、首件废活预防措施:干首件时注意最好将G00的进给倍率打到最低,并打上单节。
在没车上零件前手时刻放到进给上,直到刀具正常车上零件为止。
走刀前确定所使用的刀杆刀具号与程序是否一致,测量时测杆及标准件是否完好。
测杆测量零件时伸出长度是否合适。
综上所述加工过程中只要能做到认认真真,胆大心细,仔细观察。
此类事故的发生就能降低到最小的程度。
数控操作中对刀的操作方法
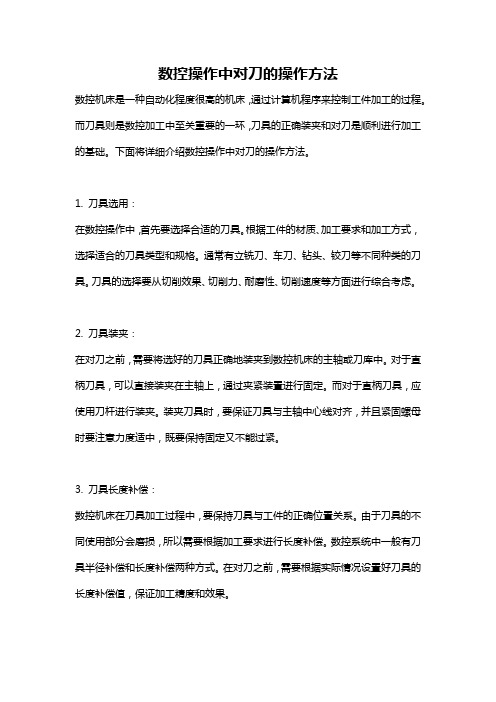
数控操作中对刀的操作方法数控机床是一种自动化程度很高的机床,通过计算机程序来控制工件加工的过程。
而刀具则是数控加工中至关重要的一环,刀具的正确装夹和对刀是顺利进行加工的基础。
下面将详细介绍数控操作中对刀的操作方法。
1. 刀具选用:在数控操作中,首先要选择合适的刀具。
根据工件的材质、加工要求和加工方式,选择适合的刀具类型和规格。
通常有立铣刀、车刀、钻头、铰刀等不同种类的刀具。
刀具的选择要从切削效果、切削力、耐磨性、切削速度等方面进行综合考虑。
2. 刀具装夹:在对刀之前,需要将选好的刀具正确地装夹到数控机床的主轴或刀库中。
对于直柄刀具,可以直接装夹在主轴上,通过夹紧装置进行固定。
而对于直柄刀具,应使用刀杆进行装夹。
装夹刀具时,要保证刀具与主轴中心线对齐,并且紧固螺母时要注意力度适中,既要保持固定又不能过紧。
3. 刀具长度补偿:数控机床在刀具加工过程中,要保持刀具与工件的正确位置关系。
由于刀具的不同使用部分会磨损,所以需要根据加工要求进行长度补偿。
数控系统中一般有刀具半径补偿和长度补偿两种方式。
在对刀之前,需要根据实际情况设置好刀具的长度补偿值,保证加工精度和效果。
4. 工件装夹:对刀之前,还需要将工件正确地装夹在数控机床上。
对于不同形状和尺寸的工件,有不同的装夹方式,可以使用机械夹具、气动夹具、液压夹具等进行固定。
工件装夹时,要注意工件的位置关系,使其与刀具的相对位置能够满足加工要求。
5. 对刀操作:对刀操作的目标是确定刀具与工件表面之间的相对位置关系。
对刀操作通常包括粗对刀和精对刀两个步骤。
(1) 粗对刀:首先使用手动操作,将刀具靠近工件表面,调整刀具位置,使其与工件表面相切或稍微超过。
然后,通过手动操作数控机床的手轮、微调装置或数字控制面板,移动刀具,使刀具呈与工件表面垂直或指定角度。
通过目视检查和测量,调整刀具位置,直到满足加工要求。
(2) 精对刀:在粗对刀的基础上,使用专用的对刀仪器,精确测量刀具与工件表面的相对位置,进行微调。
简述数控车床对刀过程及注意事项
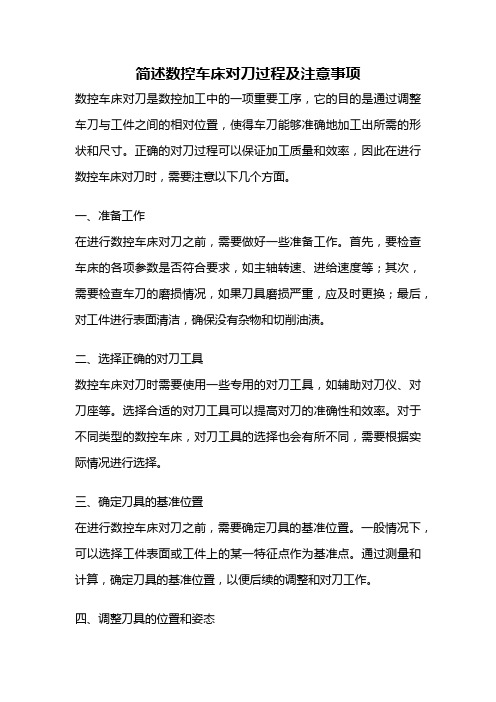
简述数控车床对刀过程及注意事项数控车床对刀是数控加工中的一项重要工序,它的目的是通过调整车刀与工件之间的相对位置,使得车刀能够准确地加工出所需的形状和尺寸。
正确的对刀过程可以保证加工质量和效率,因此在进行数控车床对刀时,需要注意以下几个方面。
一、准备工作在进行数控车床对刀之前,需要做好一些准备工作。
首先,要检查车床的各项参数是否符合要求,如主轴转速、进给速度等;其次,需要检查车刀的磨损情况,如果刀具磨损严重,应及时更换;最后,对工件进行表面清洁,确保没有杂物和切削油渍。
二、选择正确的对刀工具数控车床对刀时需要使用一些专用的对刀工具,如辅助对刀仪、对刀座等。
选择合适的对刀工具可以提高对刀的准确性和效率。
对于不同类型的数控车床,对刀工具的选择也会有所不同,需要根据实际情况进行选择。
三、确定刀具的基准位置在进行数控车床对刀之前,需要确定刀具的基准位置。
一般情况下,可以选择工件表面或工件上的某一特征点作为基准点。
通过测量和计算,确定刀具的基准位置,以便后续的调整和对刀工作。
四、调整刀具的位置和姿态在确定了刀具的基准位置之后,需要调整刀具的位置和姿态,使其与工件的轮廓和要求相吻合。
调整刀具的位置可以通过调整刀具的坐标值来实现,可以通过数控系统的操作界面进行调整。
调整刀具的姿态可以通过调整刀具的角度来实现,可以通过调节刀具座或刀具夹持装置来实现。
五、进行对刀试车在完成了刀具位置和姿态的调整之后,需要进行对刀试车,以检查刀具是否正确对刀。
对刀试车时需要注意以下几个方面:首先,要选择合适的进给速度和主轴转速,以保证加工质量和效率;其次,要观察加工过程中的切削情况,如切削力、切削声音等,以判断刀具是否正确对刀;最后,要对加工后的工件进行检查,检查加工的形状和尺寸是否满足要求。
六、调整和优化对刀结果在对刀试车的过程中,如果发现刀具没有正确对刀,需要及时进行调整和优化。
可以根据试车结果,调整刀具的位置和姿态,再次进行试车,直到达到满意的对刀效果为止。
车床对刀操作方法

车床对刀操作方法车床对刀是车床操作中非常重要的一个环节,它直接关系到车削工件的精度和质量。
对刀的准确与否,将直接影响到工件的加工质量和加工效率。
下面将详细介绍车床对刀的操作方法。
一、准备工作1、选用合适的对刀器具:对刀尺、剃高器、平头螺丝刀、螺纹螺丝刀、平尺等。
不同的车床类型和工件形态,所用的对刀器具也有所不同,因此在对刀之前需要对对刀所用的器具进行适当的选择。
2、选用合适的刀具:根据工件材料和车床的性能要求,选择合适的刀具进行对刀。
刀具的质量和刃磨情况直接影响到工件的加工精度和表面质量,因此需要在对刀之前对刀具进行检查和磨刃。
3、准备对刀的工件:将要加工的工件安装到车床上,紧固好工件夹具,并将工件调整到加工位置,待对刀后即可进行加工。
二、车床对刀的操作步骤1、安装对刀器具:首先,将对刀尺安装在刀架上,并调整好与工件表面相切。
然后,将剃高器安装在车床主轴上,并旋转工件,调整剃高器与工件表面相切,这样可以得到工件的轴线。
最后,将平头螺丝刀和螺纹螺丝刀分别用于调整对刀刀具的位置和高度,使其与工件表面相切。
2、用对刀器具找工件中心:将对刀尺端面沿着工件表面旋转,找到工件的中心位置,并调整对刀尺的位置,使其与工件的中心位置相切,这样可以确定工件的中心轴线。
3、确定对刀参考面:根据加工工件的特点,确定对刀的参考面。
对于圆柱形工件,一般选择工件端面或轴向表面作为参考面;对于非圆柱形工件,一般选择工件的基准面作为参考面。
4、对刀调整:根据对刀参考面来调整对刀刀具的位置和高度,使其与工件表面相切,并通过调整剃高器和螺纹螺丝刀,使刀尖与工件中心轴线重合,这样可以确定对刀刀具的位置和高度。
同时,对刀尺上的刻度可以用来确定对刀刀具的位置和高度,这样可以提高对刀的精度。
5、检查对刀效果:对刀完成后,用平尺检查对刀刀具与工件表面的垂直度和平行度,并用剃高器检查刀尖与工件中心轴线的重合度,以确保对刀的准确性。
三、注意事项1、对刀前要检查车床主轴、导轨和夹紧装置的状况,确保其正常工作。
- 1、下载文档前请自行甄别文档内容的完整性,平台不提供额外的编辑、内容补充、找答案等附加服务。
- 2、"仅部分预览"的文档,不可在线预览部分如存在完整性等问题,可反馈申请退款(可完整预览的文档不适用该条件!)。
- 3、如文档侵犯您的权益,请联系客服反馈,我们会尽快为您处理(人工客服工作时间:9:00-18:30)。
数控车床对刀操作时容易出现的问题及
操作注意事项Array龙永莲
(江西应用技术职业学院,江西赣州341000)摘要:介绍了数控车床对刀操作方法, 叙述了进行数控车
床对刀操作时容易出现的问题,分析了出现问题的原因,说明了避免出现类似问题的方法,提出了在进行数控车床对刀操作时应该注意的事项。
关键词: 对刀; 加工坐标系;刀具补偿值
实际生产中,在数控车床车削加工零件前,必须先进行对
刀操作, 准确的对刀操作是实现零件精确加工的基础。
在进行数控车床对刀操作时,常因操作失误而出现一些问题。
1.数控车床对刀方法介绍
数控车床对刀操作主要有试切对刀和机外对刀仪对刀两种方法, 下面以F ANU C系统经济型数控车床为例来说明其操作方法。
1.1试切对刀
试切对刀用于建立加工坐标系。
当工件装上车床后, 为了加工出所需工件, 必须将编程原点设为加工原点, 建立加工坐标系, 从而确定刀具和工件的相对位置, 使刀具按照编程轨迹运动, 最终加工出所需零件。
其操作步骤为:
(1) 选择机床的手动操作模式;
(2) 启动主轴, 试切工件外圆, 保持X方向不移动;
(3) 停主轴, 测量出工件的外径值;
(4) 选择机床的M D I操作模式;
(5) 按下“of fs et s it ti ng”按钮;
(6) 按下屏幕下方的“坐标系”软键;
(7) 光标移至“G54”;
(8) 输入X及测量的直径值;
(9) 按下屏幕下方的“测量”软键;
(10) 启动主轴,试切工件端面,保持Z方向不移动;
(11) 停主轴,重复以上(4)—(9)步,将第(8) 步中的X及测量值改为Zo。
1.2机外对刀仪对刀
机外对刀仪对刀一般将显微对刀仪固定于车床上, 用于建立刀具之间的补偿值。
因各把刀具尺寸不相同, 刀具在装到刀架后刀位点在机床中的坐标值各不相同,如果不设立刀具之间的补偿值, 运行相同的程序时就不可能加工出相同的尺寸,为使采用不同的刀具在运行相同的程序时能够加工出相同的尺寸,
必须建立刀具间的补偿。
其操作步骤为:
(1) 首先移动基准刀, 使其刀位点对准显微镜的十字线中心;
(2) 将基准刀在该点的相对位置清零, 具体操作是选择相对位置显示, 按X, 按下屏幕下方的“起源”软键;
(3) 将其刀具补偿值清零,具体操作是按下“of fs et
s i tt in g”按钮,按下屏幕下方的“补正”软键,选择“形状”, 在基准刀相对应的刀具补偿号上输入X o、Z o;
(4)选择机床的手动操作模式,移出刀架, 换刀;
(5) 使其刀位点对准显微镜的十字线中心;
(6) 选择机床的M D I操作模式;
(7) 设置刀具补偿值, 具体操作是按下“of fs et s itt i ng”
按钮, 按下屏幕下方的“补正”软键,选择“形状”,在相对应的刀补号上输入X、Z;
(8)移出刀架, 执行自动换刀指令即可。
实际生产中,也通常不采用机外对刀仪, 而直接在工件上
找一个基准点, 用基准点来建立刀具补偿值, 其操作步骤为:
(1) 首先找出工件上的一点(该点一般外露, 使各刀的刀位点容易接触到) 作为基准点,移动基准刀, 使其刀位点接触到该点;
(2) 将基准刀在该点的相对位置清零, 方法同前;
(3) 其它操作和采用机外对刀仪的操作相同。
2.数控车床对刀操作时容易出现的问题及原因
(1) 加工坐标系乱, 出现刀架撞到工件或卡盘上。
分两种情况:一是当第一次运行程序时, 能够正确地运行,
第二次运行同一程序时出现撞刀等加工坐标系乱的现象;另一
种情况是还没有运行程序,开始自动执行程序时加工坐标系就乱。
前一种情况是在程序结尾处使用了一个T××○○指令, 该
指令为取消刀具补偿指令,使用该指令后, 相应的基准坐标系
的X、Z坐标也增加或减少一个刀具补偿值, 从而使坐标系发
生改变而乱; 后一种情况是在程序开头用G50X××Z××指令,
该指令是建立坐标系的指令,使用该指令后, 机床重新以指
定的值建立坐标系,使刀具不是在先前建立的坐标系中运动,
从而出现加工坐标系乱的现象。
(2) 刀具补偿值乱,造成换刀加工时坐标值乱。
在使用基准
刀加工时, 程序能够正常运行, 坐标值也没有问题,但换刀
后, 可能切削不到工件,也有可能撞到工件,严重时出现刀
架、主轴损坏的现象。
其原因有两个:一是在进行刀具补偿的对刀操作时,没有将
原始的刀具补偿值清零, 使新设置的刀具补偿值在原来的基
础上累加,从而导致换刀后刀具偏移,不是实际的刀具补偿值; 二是在进行刀具补偿的对刀操作时,在没有设置刀补值前, 换
非基准刀对刀时使用了自动换刀指令T××××, 而在对基准刀
的位置时, 又没有注意当前刀具的刀补号已不相对应, 在设置
刀具补偿后, 所设置的刀具补偿值已不是相对基准刀的补偿值, 故导致换刀后刀具偏移, 不是实际的刀具补偿值。
3.数控车床对刀操作时注意事项
为了避免对刀操作出现上述类似问题, 除了要熟练掌握对
刀操作步骤外, 操作中应该注意以下几点:
(1) 在进行刀具补偿的对刀操作前,先将所有刀具的刀具补
偿值清零;
(2) 进行刀具补偿的对刀操作时,尚未设置好刀具补偿值的
刀具换刀时最好采用手动换刀;
(3) 程序开头不要使用建立坐标系的G50X××Z××指令;
(4) 程序结尾处不要使用取消刀具补偿的T××○○指令;
(5) 在确定基准刀的位置时要注意其刀具补偿号是否相对应;
(6) 无论是哪种对刀方式,对好刀之后, 要进行验证;
(7) 如果采用上述操作仍会出现刀具之间补偿值乱的现象,
则使用G28X0Z0指令进行机床回零。
4.小结
对刀是车床车削加工前的必要准备工作, 是数控车床操作
的重要内容, 对刀时必须严格按照操作步骤进行, 注意操作事项, 谨慎操作,方可避免实际生产中发生事故。
参考文献
【1】李峰.数控车床的对刀方法和技巧[J].中国科技信息,2006 (2):125.
【2】王忠.数控车床的对刀方法和刀具库的建立与应用
[J]. 机械工人(冷加工),2007 (5):18.
【3】黄文汉.数控车床对刀技巧与应用[J].金属加工
(冷加工), 2008 (5):28.
【4】张颖.如何提高数控机床的使用与管理水平[J].机械工人(冷加工),2005 (3):22.
【5】张涛,陈发东,董建荣.数控机床实训操作常见失误分析[J].机械工程师,2008 (3):91.
【6】夏宝林.经济型数控车床的试切法对刀策略[J].现代制造工程,2004 (10):10.
【7】李炳富.数控车床技能训练探讨[J].装备制造技术,2008 (1):58.
【8】黄华栋.数控车床操作技术常见问题初探[J].苏州工职院,2006 (1):10.
【9】王钧.GS K980T数控车床操作几点说明[J].机械工程
师,2008 (1):24.
【10】陈小红,来建良,杜红文,孟庆波.刀具补偿与数控工艺分析[J].组合机床与自动化加工技术,2008 (3):23.。