注射模的热流道技术
热流道模具技术详解

(3)无流道凝料注射模具适用的塑料材料
1)熔融温度范围宽,粘度变化小,热稳定性好。(高温不易分 解, 低温流动性好) 2)熔体粘度对压力敏感。不施压不流动,较低压力就可流动。 3)塑料的比热容低,易于熔融和固化。 4)塑料的热变形温度高,制品能迅速从模具中脱模。 理论上几乎所有的热塑性塑料都可以采用无流道注射成型。 目前应用最多的是:PE、PP、PS和ABS等材料。
(2)使用无流道凝料注射模具的限制
1)模具结构复杂,制造费用高,维护保养较困难;热流道系统 易出故障,运行成本高。不适宜小批量生产。 2)初始生产准备时间长,模具调试要求高。 3)不适宜热敏性和流动性差的塑料及成型周期长的塑件成形。 4)流道板易产生热膨胀,对熔体泄漏及加热元件的故障较敏感。 5)温度控制要求严格,需精密的温度控制元件及系统。
内加热流道与喷嘴 1—冷却水孔;2—加热喷嘴; 3—熔体通道;4—内加热器
• 外加热
外加热的流道板悬装在模具里,常以加热棒或弯曲的加热管配置在流道 的外侧。流道板的绝热用气隙,也有用绝热片。热损失是必须考虑的问题。 流道板的热膨胀需进行补偿,防止泄漏。热喷嘴装在流道板上。外加热可使 模具的压力损失最小,流道一般为圆形大直径。外加热流道板和喷嘴适用于 热敏性和高粘度塑料,流道没有冷皮层,流道流量较大。外加热流道比内加 热的成本高。
分流道板与动模板之间的气隙,为减小接触面积。 图(a) 浇口的始端突入分流道中,使部分直浇口处于分流 道绝热皮层的保温之中。图(b)在直接浇口衬套四周增设了 加热圈,浇口衬套与动模板之间有气隙绝热,与流道板之间 有加热圈。若成型周期长,可在浇口中央插入加热棒加热。
1—主流道衬套; 2—定模固定板; 3—分流道; 4—固化绝热层; 5—分流道板; 6—直接浇口衬套; 7—动模板; 8—型芯; 9—加热圈; 10—冷却水管。
热流道(一)热流道的发展过程注塑模热流道是通过加热的办法来保证...
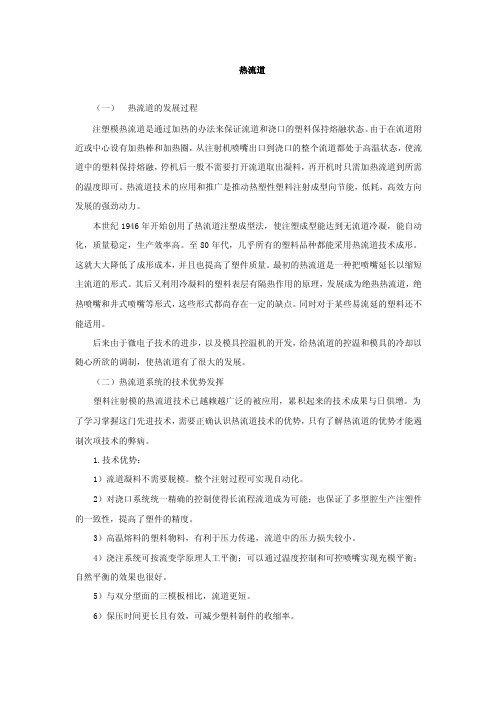
热流道(一)热流道的发展过程注塑模热流道是通过加热的办法来保证流道和浇口的塑料保持熔融状态。
由于在流道附近或中心设有加热棒和加热圈,从注射机喷嘴出口到浇口的整个流道都处于高温状态,使流道中的塑料保持熔融,停机后一般不需要打开流道取出凝料,再开机时只需加热流道到所需的温度即可。
热流道技术的应用和推广是推动热塑性塑料注射成型向节能,低耗,高效方向发展的强劲动力。
本世纪1946年开始创用了热流道注塑成型法,使注塑成型能达到无流道冷凝,能自动化,质量稳定,生产效率高。
至80年代,几乎所有的塑料品种都能采用热流道技术成形。
这就大大降低了成形成本,并且也提高了塑件质量。
最初的热流道是一种把喷嘴延长以缩短主流道的形式。
其后又利用冷凝料的塑料表层有隔热作用的原理,发展成为绝热热流道,绝热喷嘴和井式喷嘴等形式,这些形式都尚存在一定的缺点。
同时对于某些易流延的塑料还不能适用。
后来由于微电子技术的进步,以及模具控温机的开发,给热流道的控温和模具的冷却以随心所欲的调制,使热流道有了很大的发展。
(二)热流道系统的技术优势发挥塑料注射模的热流道技术已越赖越广泛的被应用,累积起来的技术成果与日俱增。
为了学习掌握这门先进技术,需要正确认识热流道技术的优势,只有了解热流道的优势才能遏制次项技术的弊病。
1.技术优势:1)流道凝料不需要脱模。
整个注射过程可实现自动化。
2)对浇口系统统一精确的控制使得长流程流道成为可能;也保证了多型腔生产注塑件的一致性,提高了塑件的精度。
3)高温熔料的塑料物料,有利于压力传递,流道中的压力损失较小。
4)浇注系统可按流变学原理人工平衡;可以通过温度控制和可控喷嘴实现充模平衡;自然平衡的效果也很好。
5)与双分型面的三模板相比,流道更短。
6)保压时间更长且有效,可减少塑料制件的收缩率。
应用热流道技术明显的优点,是原材料损耗减少和易于实现注塑加工的自动化,某些大型的薄壁制件的注射,没有流道技术是困难的,甚至是不可能的。
热流道分类

热流道分类【最新版】目录1.热流道的概念2.热流道的分类3.各类热流道的特点4.热流道在注塑成型中的应用5.热流道的发展趋势正文【热流道的概念】热流道,又称热浇道,是注塑成型机上的一个重要部件,负责将熔融塑料从注射筒输送到模具腔内。
热流道在注射成型过程中扮演着至关重要的角色,能够影响制品的质量、成型周期以及生产效率。
【热流道的分类】热流道根据结构和原理的不同,可以分为以下几类:1.单点热流道:这是最常见的热流道类型,只有一个浇口,熔融塑料通过这个浇口流入模具腔。
2.多点热流道:多点热流道有两个或以上的浇口,可以将熔融塑料从多个方向注入模具腔,以实现更复杂的成型工艺。
3.顺序热流道:顺序热流道是按照一定的顺序依次开启各个浇口,使熔融塑料依次进入模具腔,适用于有特定要求的成型工艺。
4.阀浇口热流道:阀浇口热流道是通过一个或多个阀门来控制熔融塑料的流动,可以实现更精确的控制和更高的生产效率。
【各类热流道的特点】1.单点热流道:结构简单,操作方便,适用于大部分注塑成型工艺。
2.多点热流道:可以实现更复杂的成型工艺,提高制品的质量和外观。
3.顺序热流道:适用于有特定要求的成型工艺,如多色注塑、填充物成型等。
4.阀浇口热流道:可以实现更精确的控制,提高生产效率,但结构相对复杂,操作难度较高。
【热流道在注塑成型中的应用】热流道在注塑成型中的应用非常广泛,几乎涵盖了所有的塑料制品生产领域。
热流道的使用可以提高生产效率,降低生产成本,提高制品的质量和外观。
【热流道的发展趋势】随着注塑成型技术的不断发展,热流道也在不断地进行改进和创新。
未来的发展趋势主要包括以下几个方面:1.结构简化,操作便捷,降低使用成本。
2.提高热流道的精度和稳定性,实现更精确的控制。
3.提高热流道的使用寿命,降低生产成本。
4.研发新型的热流道材料,提高热流道的性能。
热流道侧进胶结构
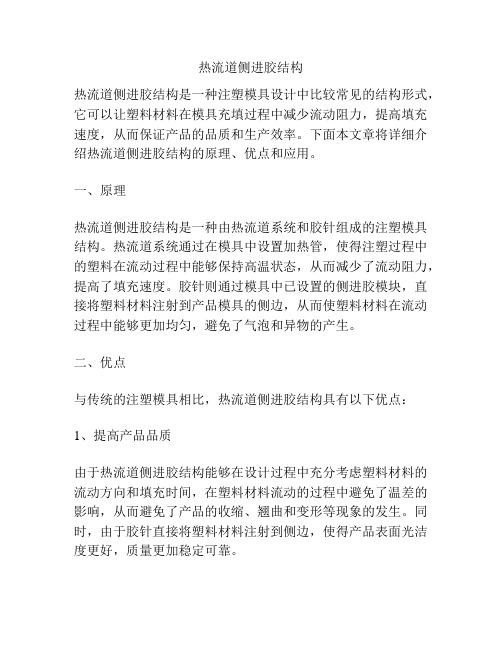
热流道侧进胶结构热流道侧进胶结构是一种注塑模具设计中比较常见的结构形式,它可以让塑料材料在模具充填过程中减少流动阻力,提高填充速度,从而保证产品的品质和生产效率。
下面本文章将详细介绍热流道侧进胶结构的原理、优点和应用。
一、原理热流道侧进胶结构是一种由热流道系统和胶针组成的注塑模具结构。
热流道系统通过在模具中设置加热管,使得注塑过程中的塑料在流动过程中能够保持高温状态,从而减少了流动阻力,提高了填充速度。
胶针则通过模具中已设置的侧进胶模块,直接将塑料材料注射到产品模具的侧边,从而使塑料材料在流动过程中能够更加均匀,避免了气泡和异物的产生。
二、优点与传统的注塑模具相比,热流道侧进胶结构具有以下优点:1、提高产品品质由于热流道侧进胶结构能够在设计过程中充分考虑塑料材料的流动方向和填充时间,在塑料材料流动的过程中避免了温差的影响,从而避免了产品的收缩、翘曲和变形等现象的发生。
同时,由于胶针直接将塑料材料注射到侧边,使得产品表面光洁度更好,质量更加稳定可靠。
2、提高生产效率由于热流道侧进胶结构所需的压力和速度相对较低,可以减少模具的磨损和损伤,同时能够在短的时间内生产出大批量的产品,从而提高了生产效率和降低了生产成本。
3、降低能耗热流道侧进胶结构需要通过加热系统来维持注塑过程中的高温状态,但是由于其采用了先进的加热技术,在加热过程中能够减少能耗和热量损失,并且在工作结束后也能够减少冷却时间和能量消耗。
三、应用热流道侧进胶结构广泛应用于各种高精度和高品质要求的注塑产品的生产中,如手机壳、汽车零部件、电子设备外壳、医疗器械零件等。
其中,由于手机市场的持续增长和消费者对产品品质要求不断提高,热流道侧进胶结构得到了广泛应用。
同时,在汽车零部件、电子设备外壳、医疗器械零件等领域,热流道侧进胶结构也得到了越来越多的应用。
总之,热流道侧进胶结构作为一种先进的注塑模具设计方案,能够提高产品品质和生产效率,降低生产成本和能耗,广泛应用于各种高精度和高要求的注塑产品生产中。
热流道的优势与技术.AMT.
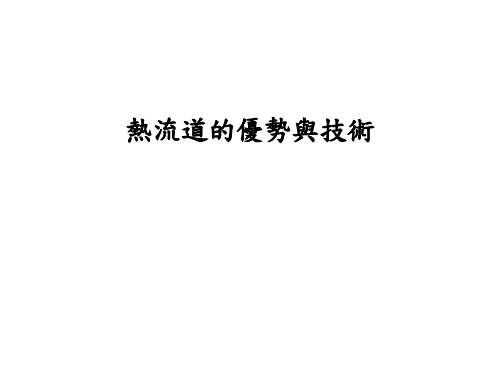
熱流道板的隔熱
目前在熱流道板周圍的模板和模塊中加水孔是為了將熱流道板 散出來的熱帶走, 一方面增加模具的冷凍功率,另一方面又增 加熱流道板的加熱功率,在節能的觀點上是兩面不討好的。 正 本清源之計在於隔絕熱流道板和其周圍的模板和模塊之間的熱 傳 – 主要是熱傳導(Thermal Conduction)和熱輻射(Thermal Radiation)。 熱傳導的減少可從熱流道板和其周圍的模板和模塊的銜接元件 (e.g. 熱嘴、分隔塊、螺釘等)著手,這些元件和熱流道板與其周 圍的模板和模塊的接觸面積在強度剛性符合要求的前題下應儘 量減少,而這些元件可以採用低熱傳導係數的材料。 熱輻射減少的空間較大,是可以特別著墨之處。 請參考後附圖 例 - 在熱流道板的周邊覆以鋁皮(Aluminum Sheet) 是可以採納的有效方法。
熱流道的技術
3. 避免劣解 (Degradation) 應從以下幾點的合理化著手: 1) 塑膠的乾燥、 2) 熔膠的停 留時間(Residence Time)、 3) 熔膠溫度、 4) 剪切速率(She ar Rate)。
42”電漿電視機前框 PC(GE LEXAN HF1110) 問題:黃化、熔接痕
28.48
27.52
流動平衡度 : 9.30/28.48=32.7%
流動平衡度 : 13.74/27.52=49.9%
13.74 9.30
澆口: 澆口: 0.45~0.62
澆口: 澆口: 0.61~0.62
如果將塑流簡化成恆溫(isothermal)、完全發展的層流(fully devel oped laminar flow)的冪律流體(power law fluid),當壓力降相同 時,通過直徑d1澆口的流量Q1與通過直徑d2澆口的流量Q2的比 可以下式表示:
热流道模具 定义

热流道模具定义热流道模具是一种特殊类型的模具,它在塑料注射成型过程中能够有效地控制塑料的流动和冷却,以提高产品的质量和生产效率。
热流道模具的设计和制造要考虑多种因素,如塑料材料的特性、产品的形状和尺寸、注射压力和温度等。
热流道模具具有更高的注塑效率。
相比传统的冷流道模具,热流道模具能够减少塑料的冷却时间,提高注塑速度,从而缩短了生产周期。
热流道模具中的加热系统能够将热能直接传递给塑料,使其保持较高的温度,从而保持较低的粘度,提高了塑料的流动性。
这样一来,塑料在注射过程中能够更加均匀地填充模具腔体,避免了热冷交界线产生的缺陷,提高了产品的质量。
热流道模具能够减少塑料的浪费。
传统的冷流道模具在注塑过程中需要使用大量的冷却水来降低塑料的温度,而这些冷却水会造成大量的水蒸气和废水的产生,对环境造成了一定的污染。
而热流道模具通过加热系统来控制塑料的温度,减少了冷却水的使用,降低了废水的产生。
同时,热流道模具还可以减少塑料的废料产生,提高了材料的利用率,降低了生产成本。
热流道模具还能够提高产品的外观质量。
由于热流道模具能够控制塑料的温度和流动性,使塑料更加均匀地填充模具腔体,从而减少了产品表面的缺陷和气泡的产生。
这样一来,产品的外观质量得到了显著的提高,满足了客户对产品外观的要求。
热流道模具还具有灵活性和多样性。
热流道模具的加热系统可以根据不同的产品要求进行调整,实现不同的温度控制,以适应不同的塑料材料和注塑工艺。
同时,热流道模具还可以应用于复杂的产品结构,如薄壁注塑、多孔注塑等,提高了模具的适用范围和灵活性。
总体而言,热流道模具作为一种先进的注塑模具技术,具有诸多优势。
它能够提高注塑效率、减少塑料浪费、改善产品外观质量,并且具有灵活性和多样性。
随着科技的不断进步和人们对产品质量要求的提高,热流道模具必将在注塑行业中得到更广泛的应用。
通过不断的创新和改进,热流道模具将为塑料制品的生产带来更多的便利和效益。
热流道工作原理

热流道工作原理
热流道工作原理是指通过电加热将热能传导至流道系统,以保持塑料材料在注塑过程中的熔融状态,实现高效、准确的注塑成型。
其工作原理主要包括以下几个步骤:
1. 加热:通过热流道系统中的加热元件(如电热管或热板)向流道传递热能,将塑料原料加热至熔融温度。
2. 保温:热能将传导至整个流道系统,包括模具中的流道和喷嘴。
在注塑过程中,热流道必须保持一定的温度,以确保塑料材料始终处于熔融状态,避免冷却造成流道堵塞。
3. 注射:熔融塑料通过喷嘴进入模具的腔体中。
在注塑过程中,热流道会保持塑料材料的熔融温度,提高塑料流动性,同时避免材料过早冷却导致注塑不良。
4. 冷却:在塑料材料填充腔体后,冷却系统会开始发挥作用,冷却模具温度以使塑料材料凝固成型。
与传统注塑相比,热流道可以通过独立的冷却控制,更精确地调整冷却速度和温度,以提高注塑成型品质和效率。
热流道工作原理通过控制温度进行熔融和冷却的优化,能够有效避免流道堵塞、减少材料损耗和工艺参数调试时间,提高注塑产能和制品质量,成为现代注塑技术中不可或缺的重要工艺手段。
热流道的原理及应用图解
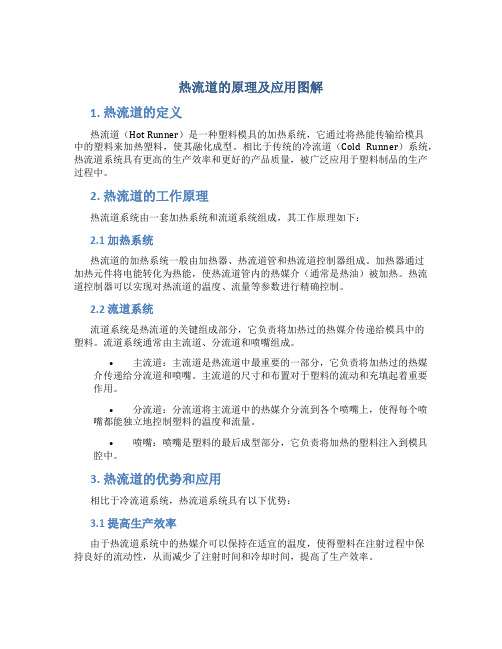
热流道的原理及应用图解1. 热流道的定义热流道(Hot Runner)是一种塑料模具的加热系统,它通过将热能传输给模具中的塑料来加热塑料,使其融化成型。
相比于传统的冷流道(Cold Runner)系统,热流道系统具有更高的生产效率和更好的产品质量,被广泛应用于塑料制品的生产过程中。
2. 热流道的工作原理热流道系统由一套加热系统和流道系统组成,其工作原理如下:2.1 加热系统热流道的加热系统一般由加热器、热流道管和热流道控制器组成。
加热器通过加热元件将电能转化为热能,使热流道管内的热媒介(通常是热油)被加热。
热流道控制器可以实现对热流道的温度、流量等参数进行精确控制。
2.2 流道系统流道系统是热流道的关键组成部分,它负责将加热过的热媒介传递给模具中的塑料。
流道系统通常由主流道、分流道和喷嘴组成。
•主流道:主流道是热流道中最重要的一部分,它负责将加热过的热媒介传递给分流道和喷嘴。
主流道的尺寸和布置对于塑料的流动和充填起着重要作用。
•分流道:分流道将主流道中的热媒介分流到各个喷嘴上,使得每个喷嘴都能独立地控制塑料的温度和流量。
•喷嘴:喷嘴是塑料的最后成型部分,它负责将加热的塑料注入到模具腔中。
3. 热流道的优势和应用相比于冷流道系统,热流道系统具有以下优势:3.1 提高生产效率由于热流道系统中的热媒介可以保持在适宜的温度,使得塑料在注射过程中保持良好的流动性,从而减少了注射时间和冷却时间,提高了生产效率。
3.2 降低生产成本热流道系统减少了冷却时间和废品产生,降低了生产成本。
同时,由于去除了冷道系统,可以减少注塑机的锁模力,降低了设备的投资成本。
3.3 改善产品质量热流道系统可以精确控制塑料的温度和流量,保证了每个喷嘴注入的塑料质量一致,减少了产品的热变形和缺陷。
热流道系统在以下领域有广泛的应用:•医疗器械:热流道系统被广泛应用于制造医疗器械,如注射器、输液器等。
由于产品的精度和质量要求较高,热流道系统能够满足其生产需求。
模具热流道结构原理

模具热流道结构原理热流道技术是现代模具加工技术的一项重要成果,其原理是通过在模具中设置加热通道和热流道,使塑料熔融前进通道的各部分温度基本相同,以保证模具所注射的每一个塑料制件都能够具有相同的品质和尺寸,从而满足工业制造对于高精度的需求。
本文将介绍热流道结构原理的具体内容。
第一部分:热流道结构的分类根据所有元器件的放置位置和熔塑物的流动情况,可以将热流道结构分为三种类型:点式、线式和面式。
点式热流道的主要特点是在模具中设置单个的加热节点,它们通过塑料内部传递热能以实现加热的目的。
这种结构不仅适用于各种大小尺寸的模具,而且具有精度高和低成本的优点,是热流道系统中使用最广泛的一种类型。
与点式热流道类似,线式热流道的结构是通过在模具中设置多个线性的加热通道,更加适合于大型模具。
线式结构能够将热能更加准确地传递至需要加热的部分,避免发生温度分布不均匀的现象。
线式结构需要更多的热元器件、更复杂的控制系统和维护,并且可能会在熔塑物中留下接缝痕迹。
通过在模具中设置一个平面式的加热板,这种结构可以实现塑料从同一个平面上准确流动,并且不会产生接缝或热点。
由于它的制造难度和成本较高,目前应用不是非常广泛。
热流道的工作原理是由控制器中的电子温控模块控制。
在注塑机的加压下,熔塑物被压入模具中。
加热通道中的热器会将热量传输到熔塑物中,使其保持一定的温度。
这样,热力流动能够准确快速地移动到需要热加工的模具内部各个位置,以实现高精度注塑的目的。
热流道系统的控制属于高科技,该系统可以调节模具内的温度控制。
在该过程中,重要的技术参数包括熔塑物的注入速度、时间和热力流动的流动速度。
通过具体的温度检测和控制触发信号,控制器可以及时地响应热能流动的需求,从而更好地控制热流道的温度分布和保持出色的注塑效果。
1. 塑料熔点的特性:不同种类塑料的熔点温度不同,这需要在热流道设计时充分考虑塑料的种类和熔点。
2. 注塑过程的温度和压力:注塑过程的温度和压力必须能够精确地控制,以确保热能能够精确地流动到所需的位置,并达到高精度注塑的目的。
热流道的好处

热流道的好处
热流道是注塑模具中的一种技术,它通过预热注射材料,使其在注射过程中保持较高的温度。
热流道技术具有以下好处:
1. 提高生产效率:热流道技术可以加快注塑周期,减少注射时间,提高生产效率。
因为预热的注射材料更容易流动,填充模具的时间更短,使得生产速度更快。
2. 提高产品质量:热流道技术可以提供更均匀的温度分布,减少料温变化对产品质量的影响。
同时,它可以避免冷凝产生的痕迹,减少或消除焦糊、熔体降解等质量问题,提高产品的外观和机械性能。
3. 降低材料损耗:热流道技术可以减少挤出门的长度,减少冷却时间,降低注塑件的凝固时间。
这样不仅可以节省材料,还可以减少废品率,提高注塑成型效率。
4. 扩大设计自由度:热流道技术可以使得模具设计更加灵活,尤其适用于复杂结构的注塑件。
由于注射材料在模具内保持高温,可以更容易地填充复杂结构,减少或消除热流道痕迹和短流等缺陷。
总的来说,热流道技术在提高生产效率、产品质量、材料利用率和设计自由度等方面都具有明显的优点,是现代注塑模具中广泛采用的一项技术。
热流道技术

热流道技术作者:来源:发表时间:2006-07-08 浏览次数:182 字号:大中小热流道模具与普通流道模具相比,具有注塑效率高、成型塑件质量好和节约原料等优点,随着聚合物工业的发展,热流道技术正不断地发展完善,其应用范围也越来越广泛。
热流道是通过加热的办法来保证流道和浇口的塑料保持熔融状态。
由于在流道附近或中心设有加热棒和加热圈,从注塑机喷嘴出口到浇口的整个流道都处于高温状态,使流道中的塑料保持熔融,停机后一般不需要打开流道取出凝料,再开机时只需加热流道到所需温度即可。
热流道注射成型法于20世纪50年代问世,经历了一段较长时间地推广以后,其市场占有率逐年上升,80年代中期,美国的热流道模具占注射模具总数的15%~17% ,欧洲为12%~15% ,日本约为10% 。
但到了90年代,美国生产的塑料注射模具中热流道模具已占40%以上,在大型制品的注射模具中则占90%以上。
热流道系统的优势节约原料、降低制品成本是热流道模具最显著的特点。
普通浇注系统中要产生大量的料柄,在生产小制品时,浇注系统凝料的重量可能超过制品重量。
由于塑料在热流道模具内一直处于熔融状态,制品不需修剪浇口,基本上是无废料加工,因此可节约大量原材料。
由于不需废料的回收、挑选、粉碎、染色等工序,故省工、省时、节能降耗。
注射料中因不再掺入经过反复加工的浇口料,故产品质量可以得到显著地提高,同时由于浇注系统塑料保持熔融,流动时压力损失小,因而容易实现多浇口、多型腔模具及大型制品的低压注射。
热浇口利于压力传递,在一定程度上能克服塑件由于补料不足而形成的凹陷、缩孔、变形等缺陷。
适用树脂范围广,成型条件设定方便。
由于热流道温控系统技术的完善及发展,现在热流道不仅可以用于熔融温度较宽的聚乙烯、聚丙烯,也能用于加工温度范围窄的热敏性塑料,如聚氯乙烯、聚甲醛(POM)等。
对易产生流涎的聚酰胺(PA),通过选用阀式热喷嘴也能实现热流道成型。
另外,操作简化、缩短成型周期也是热流道模具的一个重要特点。
第5章 热流道注射模具5.3 《塑料成型工艺与模具设计》课件
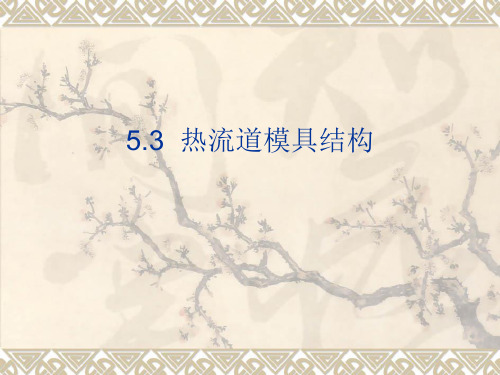
板 12--注塑件 13—动模板
2.流道
❖ 流道的长度和直径及它的体积,在满足注射点的数目和分布 的情况下,还应注意以下两方面的问题。
❖ (1)流道中允许的压力降一般小于35MPa。流道中传输的熔 体应有合理的流动速率和剪切速率。
❖ (2)考虑塑料熔体在流道里允许驻留的时间。校核每次注射的 循环时间,检查型腔注射量与流道容量的比例。熔体在流道 中驻留的时间等于塑料降解时间的10%~20%。
3.流道板的密封和紧固
❖ 要保证流道板无塑料熔体的泄漏,必须考虑流道板的热膨胀 作用。高温的热流道系统,维持了熔体的可流动状态,并不 断地受到注射与保压的短时高压冲击。室温下装配紧固的热 流道系统,在高温下使用时会造成流道板的热变形;生产时 的温度控制不稳定和热变形不均匀;流道板的设计、装配和 加工工艺不当等,都会使流道板中的熔体泄漏。特别是注射 工艺的不当,如超高压的注射和过高的温度冲击。低黏度的 PE和PP等塑料熔体更容易发生泄漏。
2.浇口
❖ 浇口是流道的终点,也是热流道系统中关键功能区。它的形 式有两种,一种是与喷嘴做成
❖ 一个整体;另一种是开设在模具的零件上,再与喷嘴拼合在 一起。浇口调节塑料熔体对型腔的注射充模。浇口通过它的 开闭控制着对型腔内塑料的保压补缩时间,可采用热力闭合 或机械开闭两种方式。
3.喷嘴
❖ 热流道喷嘴是热流道系统的终端,它包括加热器、热电偶和 浇口。它将熔体输送到模具的型腔或冷流道。热流道喷嘴包 括主流道喷嘴和注射点的喷嘴。
❖ 第一,根据塑件结构和使用要求,确定浇口位置。只要塑件 结构允许,在定模镶块内喷嘴和喷嘴头不与成型结构干涉, 热流道系统的浇口可放置在塑件的任何位置上。具体设置方 位与冷流道模具注射成形的浇口位置选择原则相同。对于大 而复杂的异型塑件,注射成形的浇口位置可运用计算机辅助 分析(CAE)模拟熔融状塑料在型腔内的流动情况,分析模具 各部位的冷却效果,确定较合理的浇口位置。
热流道金属粉末注射成形模具设计
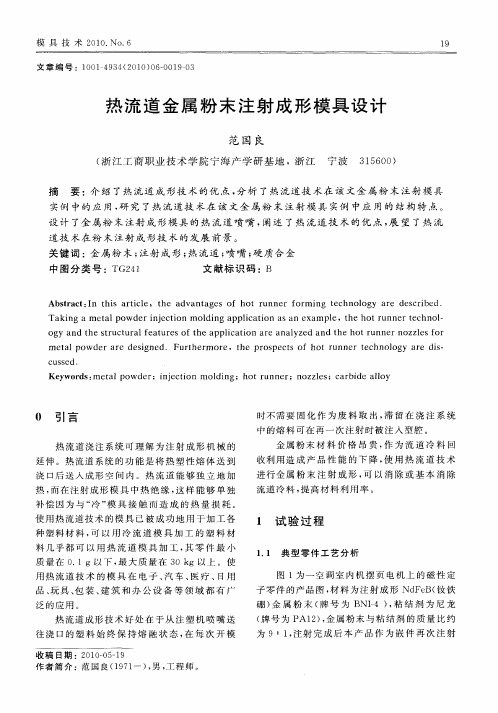
进 行 金 属 粉 末 注 射 成 形 , 以 消 除 或 基 本 消 除 可
流道冷料 , 高材料利用率 。 提
热 , 在 注 射 成 形 模 具 中 热 绝 缘 , 样 能 够 单 独 而 这 补偿 因 为 与 “ ” 具 接 触 而 造 成 的 热 量 损 耗 。 冷 模 使 用 热 流 道 技 术 的模 具 已被 成 功 地 用 于加 工 各
热 流 道 成 形 技 属 粉 末 与粘 结 剂 的质 量 比约 牌 Al ) 金 为 9: , 射 完 成 后 本 产 品 作 为 嵌 件 再 次 注 射 1注
往 浇 口的 塑 料 始 终 保 持 熔 融 状 态 , 每 次 开 模 在
差 范 围 只 有 0 0 . 5 mm , 经 接 近 零 件 的 收 缩 范 已
1 3 模 具 设 计 .
设计 的模 具为一 模 四腔 。考 虑到 模具 成形 零 件 的结 构 以及 出模 方式 , 模具结构 如图 3 所示 。
收 稿 日期 :2 1 — 5 1 0 00 — 9 作者 简介 : 国 良(9 1 )男 , 程师 。 范 17 一 , 工
2 0
Di nd M o d T e h l g o 6 20 0 ea ul c no o y N . 1
后, 经过 充 磁 即 为成 品 。该 产 品形 状 比较 简 单 , 而尺 寸精 度 、 位 公 差 要 求 较 高 . 别 是 尺 寸 公 形 特
Kew rs mea p w e ;ijcin mo dn ;h t u n r o ze ;c r iealy y o d : tl o d r ne t li g o n e ;n z ls a bd l o r o
0 引 言
注射模热流道的技术特点与应用

道取出凝料 ,再开机 时只需 加热流道到所需 温度即 可 。因此 ,热流道 工艺 有 时称 为热集 流管 系统 ,或 者 称 为无 流 道 模 具 … 。在 国外 热 流 道 已 被 广 泛 应 用 ,
如 美 国 I C E公 司 、D E公 司 、西 德 H S O公 司都 NO M AC 有 热流道 产 品 ,在 国内仅有 少数 单位 引进 热流 道加 以 应 用 引。 ,
身与外部形成一绝 热层 ,因而加 热效率高 ,热损失 少 ,节约 能源 。它是 通过 在流 道 内部加 热 的方法 ,使
作者简介 :冯刚 ,男 ,17 年生 ,高级 实验员 ,高级 技师 , 主要从事 机械设 备的维 护和修理 、 量检 验 、教学和研 91 现 质
Z HANG Ja ‘u iny , F NG a g E G n , L i—in ,Z U C i e IJn l g a HO a— n g ( . Z e agIds yP ieh i C l g ,S a ̄ g3 20 ,C ia 1 hj n ut o c n o ee ho n 10 0 hn ; i n r s c l 2 Z e agK iaMahn ol o ,Ld hoi 10 1 hn ) . hjn a ci T o C . t ,S ax g3 24 ,C ia i d e n
Ab t a t h s p p rd s r e t cu a h r ce it s a d a p iai n s o e o o u n r a d d s sr c :T i a e e c i s s u t r lc a a t r i n p l t c p fh tr n e , n i— b r sc c o
注塑热流道工艺流程

注塑热流道工艺流程首先,确定产品设计和模具结构。
根据产品的尺寸、形状和要求确定模具的结构设计,包括模具尺寸、注射系统、热流道系统等。
然后,进行模具加工和组装。
根据设计图纸进行模具零件的加工,包括铣削、刨削、钻孔、车削等工序。
然后将加工好的模具零件进行组装,以得到完整的注塑模具。
接下来,进行热流道系统组装和调试。
根据模具设计,将热流道系统的各个零件进行组装,包括热流道板、热流道嘴、加热管等。
然后进行系统的调试,通过调整温度、压力、流量等参数,确保热流道系统能正常工作。
然后,进行材料预处理。
将塑料原料进行加热和干燥处理,以去除杂质和水分,并使其达到适合注塑加工的熔融状态。
接着,进行注塑机调试。
将已组装好的注塑模具安装到注塑机上,并根据产品要求设置注射参数,如注射压力、注射速度、保压时间等。
通过注塑机的操作界面进行参数设置和调试,以确保注射过程的稳定性。
之后,进行试模和调整。
在注塑机的运行下,进行试模操作,注入塑料熔融料到模具腔内,融合成产品。
根据试模的结果,对注射参数进行调整,以使得产品能够满足设计要求,如尺寸精度、外观质量等。
最后,进行正式生产。
在试模调整完毕后,根据产品批量需求,进行正式生产。
在生产过程中,对注射参数、热流道温度等进行监控和调整,以确保产品质量的稳定性和生产效率的高效性。
总结起来,注塑热流道工艺流程包括产品设计和模具结构确定、模具加工和组装、热流道系统组装和调试、材料预处理、注塑机调试、试模和调整、正式生产等环节。
通过科学的流程和合理的操作,在注塑热流道工艺中可以实现高质量、高效率的生产。
热流道模具设计
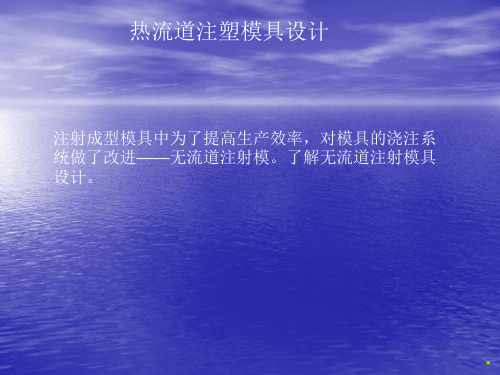
注射压力损失少,可降低熔料温度和注射压力,减少塑料热降解和制 品的内应力。
适用的塑料种类广。
加热流道注射模关键:供热装置、温度调节系统、模具的 绝热措施和防止浇口处凝固和流涎等问题。
2.1.1、单型腔延伸式喷嘴模具 A、塑料绝热式
可用于PE、PP、PS; 密封承压面A面积不宜过大; 绝热层厚度0.5~1.5mm;面积不宜过大; 浇口尺寸约0.75~1.5mm; 不适用于热敏性塑料。
B、有绝热仓的开式喷嘴
铜/钴/铍
侧空气隙、内部塑料绝热,应 用于小制品,加工温度范围较宽 的料(PS、PE),D:L=1:3
绝热仓
3)顶针式喷嘴 特点 无定形和结晶型塑料均可用,热顶针伸至浇口,浇口温度 控制更容易,可用于热敏性塑料注射成型; 浇口尺寸小(0.6~2.5mm),浇口痕迹较小;微小制品浇 口可小至0.3mm; 顶针在浇口中心有助于防止浇口拉丝; 对剪切敏感的塑料(包括含阻燃剂或有机染料的塑料)不 太适合,因环形缝隙较小,易过热分解。
线性温度特征;
对模具热损失小;
体积小,能耗少; 能快速和均匀加热;
维修安全。
线圈加热器:230V加热器通常绕成圆 形、矩形或椭圆形,中部卷绕间距增 大(称对数卷绕)。
加热棒:用来加热鱼雷顶针, 可嵌入鱼雷壳体中或镶入铜套 里。 热管:用来均化沿流道方向的 温度。
内加热式系统
流道外壁冻结层绝热作用好,节电50%; 不存在热绝缘或热膨胀问题,流道板外部温度取决于模温(图1-9),稍高于 模温; 冻结层塑料对系统有良好的密封作用;热流道温度实质上与模具热平衡无关; 内加热式结构不便使用开关式喷嘴。
2.1.4、喷嘴结构 1)喷嘴的种类
A、 开式喷嘴
B、顶针式喷嘴
热流道分类
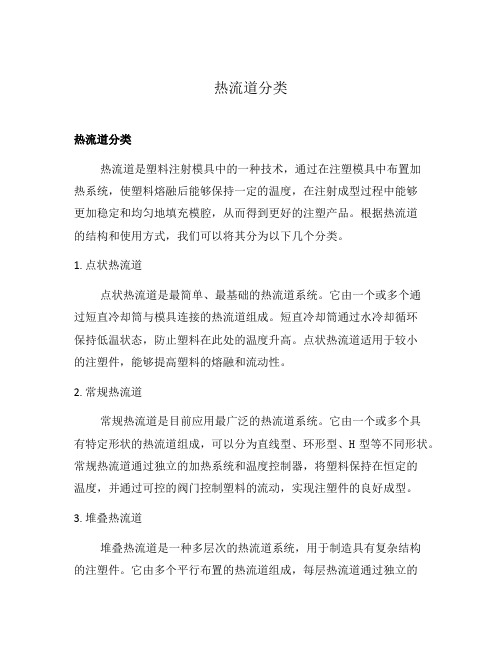
热流道分类热流道分类热流道是塑料注射模具中的一种技术,通过在注塑模具中布置加热系统,使塑料熔融后能够保持一定的温度,在注射成型过程中能够更加稳定和均匀地填充模腔,从而得到更好的注塑产品。
根据热流道的结构和使用方式,我们可以将其分为以下几个分类。
1. 点状热流道点状热流道是最简单、最基础的热流道系统。
它由一个或多个通过短直冷却筒与模具连接的热流道组成。
短直冷却筒通过水冷却循环保持低温状态,防止塑料在此处的温度升高。
点状热流道适用于较小的注塑件,能够提高塑料的熔融和流动性。
2. 常规热流道常规热流道是目前应用最广泛的热流道系统。
它由一个或多个具有特定形状的热流道组成,可以分为直线型、环形型、H型等不同形状。
常规热流道通过独立的加热系统和温度控制器,将塑料保持在恒定的温度,并通过可控的阀门控制塑料的流动,实现注塑件的良好成型。
3. 堆叠热流道堆叠热流道是一种多层次的热流道系统,用于制造具有复杂结构的注塑件。
它由多个平行布置的热流道组成,每层热流道通过独立的加热系统和温度控制器控制。
堆叠热流道可以单独控制每一层塑料的温度和流动情况,使得各层注射成型质量更加稳定。
4. 阀门热流道阀门热流道是一种应用比较广泛的具有多个阀门的热流道系统。
它通过阀门控制塑料的流动和停止,实现注塑件的准确成型。
阀门热流道适用于需要多个注射阶段的注塑件,如多色、多层或嵌入金属件的注塑制品。
5. 多级热流道多级热流道是一种通过多个独立的加热区域控制塑料温度的热流道系统。
它适用于在不同的注射阶段需要不同温度的注塑件。
多级热流道能够更加精确地控制注塑产品的质量,提高产品的一致性。
以上是根据热流道的不同特点和应用场景进行的分类。
每种热流道系统都有其独特的优势和适用范围,在实际应用中可以根据注塑件要求选择合适的热流道分类。
6. 热嘴热流道热嘴热流道是一种将热嘴技术与热流道技术相结合的系统。
热嘴位于模具的前端,用于将塑料熔融并保持在恒定的温度。
大浇口注射模改造热流道技术

e f f i c i e n c y t h a n w i l l b e c a r r i e d o u t i n c o n d i t i o n s a l l o w mo d i ic f a t i o n o f h o t r u n n e r .T h i s p a p e r
热 流 道 的 实用技 术 进行 分 析研 究 , 让 模 具价 值 发挥 到 最 大。 关键字: 注射 模 ; 热流道; 设 计 中图 分类 号 : T Q 3 2 0 . 6 6 文 献标 识 码 : B
Ho t R u n n e r t e c h n o l o g y f o r E d g e Ga t e I n j e c t i o n Mo l d
模 具 技 术 网
h I L p : / / www . s z mo l d s z : o m 模具制造立体传媒电子商务平台
嘉
大 浇 口 注 射 模 改 造 热 流 道 技 术
曾天文 , 陆宇立 河源职 业技 术学院 ( 广 东河源 4 2 7 0 0 0 )
【 摘要 】 热流道技术是 国家“ 十五” 制造业 大力发展 而迫切 需求的一项实用新技术 , 采用该 技术可减 少制 品废料 、 缩短 成型周期 、 提 高制 品精度 。模具行业 热流道的应用越 来越 主 流, 而一些 旧式大浇口模 具为了得到更好效益比 , 将会在条件允许的情况下进行热流道的 改造 。本文解析 了现有 大浇 口注射模 改造 为热流道 注射模 的可行性 以及 工艺步骤 , 并对
热流道结构知识点总结

热流道结构知识点总结热流道结构在塑料注射成型过程中扮演着重要的角色,它可以帮助提高注射成型的效率和质量。
本文将会总结热流道结构的相关知识点,包括热流道系统的基本原理、组成部分、优点和缺点、应用范围等内容。
一、热流道系统的基本原理热流道系统是一种在注射模具中用于传送加热的热载体,保持塑料材料在注射成型过程中的流动状态,以保证产品的成型质量和提高生产效率。
热流道系统的基本原理包括:1. 热载体传导热量:热流道系统中通常采用热载体(如热油、热水)传导热量,将热能传递到模具的热流道中,使塑料材料在注射成型过程中能够始终保持在合适的流动状态。
2. 控制模具温度:通过控制热载体的温度和流量,可以实现对注射模具中的温度进行精确的控制。
这样可以避免塑料材料在成型过程中受温度变化的影响,保证产品的尺寸稳定性和表面质量。
3. 优化成型条件:热流道系统可以根据不同的产品形状和材料特性,灵活调节模具中不同部位的温度,以实现最佳的注射成型效果。
二、热流道系统的组成部分热流道系统由多个组成部分组成,主要包括热流道控制器、加热装置、温度探测器、热流道喉口等。
1. 热流道控制器:负责对热流道系统的温度、压力等参数进行实时监控和调节,以确保注射成型过程中的稳定性和一致性。
2. 加热装置:通常采用电加热或加热用的热管,通过对热载体进行加热,传递热能到热流道系统中。
3. 温度探测器:用于监测热流道系统中的温度变化,反馈给热流道控制器,以实现自动调节和控制。
4. 热流道喉口:负责将加热好的热载体传递到模具的热流道中,为塑料材料提供适宜的加热条件。
三、热流道系统的优点和缺点热流道系统相比传统的冷流道系统具有许多优点,但也存在一些缺点。
1. 优点:(1)节能减耗:热流道系统采用热载体传导热量,可以有效减少注射成型过程中的能耗,提高生产效率。
(2)减少生产环境污染:热流道系统可以降低产品的废料率,提高成型质量,减少生产环境的污染。
(3)提高产品质量:热流道系统可以精确控制模具中不同部位的温度,保证产品的尺寸稳定性和表面质量。
- 1、下载文档前请自行甄别文档内容的完整性,平台不提供额外的编辑、内容补充、找答案等附加服务。
- 2、"仅部分预览"的文档,不可在线预览部分如存在完整性等问题,可反馈申请退款(可完整预览的文档不适用该条件!)。
- 3、如文档侵犯您的权益,请联系客服反馈,我们会尽快为您处理(人工客服工作时间:9:00-18:30)。
封面设计:陈 沛 责任印制:洪汉军 北京瑞德印刷有限公司印刷 2 0 0 6年 1月第 1版第 1次印刷
1 0 0 0 m m× 1 4 0 0 m mB 5 ·7 6 2 5印张·2 9 4千字 00 0 1 - 40 0 0册 定价:2 5 0 0元
本社购书热线电话 ( 0 1 0 )6 8 3 2 6 2 9 4 封面无防伪标均为盗版
w w
w
.g
ol
de
n-
bo
ok
的冲撞和挤压;而且它的里 侧 端 面 承 受 熔 体 高 压。 如 图 1 3 b所 示 衬 套, 需 要 有
.c
om
注射后,为减少注射机喷嘴传热给冷却中的模具,后移注射座将喷嘴撤离模具一
注射模的热流道技术 4 分流道是主流道末端至浇口的整个通道。分流道的功能是将熔体过渡传输和 转向。单型腔模具中分流道是为了缩短流程。多型腔注射模中分流道是为了分配 物料,通常由一级分流道和二级分流道,甚至多级分流道组成。 对于分流道的截面形状,在冷流道系统中常用梯形。因为只需在一块模板上 加工,而且脱模 方 便。 U 形 截 面 与 其 类 似, 也 需 专 用 刀 具 加 工。 在 热 流 道 系 统 中,分流道的截面常用圆形。圆截面与其表面之比最小,有最大的流通截面,压 力传递好,保温效率高。圆截面流道用在冷流道系统的模具上,需在流道分型面 上脱模,必须加工在两块模板上。 分流道截面大小和流道的布置长度,受到浇注系统压力损失和注射机注射能 力的制约。较小的流道截面能减少 浇 注 系 统 用 料, 但 会 增 加 流 道 中 的 压 力 损 失。 注射到型腔的熔料因压力过低而达不到所需的充模速率,将影响制件质量,甚至 使型腔不能充满。对于流道系统,主流道、分流道和浇口通道的压力损失限制在 3 5 MP a 以下。流道尺寸的理论计算能得到流道的最佳尺寸,保证熔体有适当的流 动速率和恰当的压力损失。电子计算机流动充模模拟也能实现浇注系统的优化设 计。 冷流道系统的凝料, 经 粉 碎 和 塑 化 后 再 注 射 制 件。 但 此 回 头 料 的 比 例 须 限 制,它会降低制品的物理质量。热流道圆截面的尺寸愈大,会使流道中保温停留 的塑料熔体量增加。在高温下受热时间过长,会使材料降解,也会引起制品的质 量下降。特别是热敏性的塑料品种,如 P V C和 P O M 等,最为明显。 4 浇口 浇口是分流道末端与模腔入口之间,狭窄且短小的一段通道。它的功能是使 塑料熔体加快流速注入型腔内,有序地填满型腔,且对补缩有控制作用。浇口是 塑料熔体进入型腔的阀门,对塑料制品质量有决定性的影响,因而浇口类型与尺 常用的浇口有十多种,这里介绍三种典型的浇口类型,即直接浇口、侧浇口 直接浇口也称为主流道型浇口或中心浇口,简称直浇口。直接浇口的优点甚 多。注射时以等流程充模,浇注系统流程短,压力损失和热量损失小,且有利于 补缩和排气。因此,注塑件外表无可见的熔合缝,而且浇注系统凝料少。直接浇 口常被用来注射大型厚壁长流程制品,及一些高黏度的塑料。 图1 4所示为直接浇口的设计,可参考前主流道的结构与尺寸。直接浇口与 熔体流动摩擦剧增,产生暗斑和暗纹;如果直径太大,则冷却时间过长,流道凝 料多,易产生缩孔。 直接浇口的缺点是 注 塑 件 上 残 留 痕 迹 过 大, 切 除 困 难, 如 图 1 4 a所 示。 可 塑料件连接处的直径约为塑料件厚度的两倍或略大些。若此处直径不够大,会使 寸、浇口位置与数量是浇注系统设计的关键。
中国科技金书网
图1 2 冷流道系统的组成
1 —主流道 2 —分流道 3 —浇口 4 —注塑件
2 . 主流道 经过的通道,且与注塑机喷嘴在同一轴线。
主流道是指从注射机喷嘴出口到分流道入口的一段流道。它是塑料熔体首先 最常见的直浇口式主流 道 呈 圆 锥 体, 见 图 1 3 。主流道入口直径 d ,应大于 注射机喷嘴直径 1 m m 左右。这 样 便 于 两 者 能 同 轴 对 准,也 使 得 主 流 道 凝 料 能 顺 利脱出。主流道入口 的 凹 坑 球 面 半 径 R , 应 该 大 于 注 射 机 喷 嘴 球 头 半 径 约 2~ 3 m m 。反之, 两 者 不 能 很 好 贴 合 , 会 让 塑 料 熔 体 反 射 , 出 现 溢 边 致 使 脱 模 困难。
w w
凡购本书,如有缺页、倒页、脱页,由本社发行部调换
w
.g
ol
de
n-
bo
ok
责任编辑:陈保华 版式设计:张世琴 责任校对:申春香
.c
机械工业出版社 ( 北京市百万庄大街 2 2号 邮政编码 1 0 0 0 3 7 )
om
中国科技金书网
中国科技金书网
注射模的热流道技术
王建华 徐佩弦 编著
机 械 工 业 出 版 社
w w
w
.g
ol
de
n-
bo
ok
.c
om
中国科技金书网
注射模的热流道技术是塑料注射模塑工程发展的重要方面。本 书 系统全面地介绍了注射模热流道系统的设计、制造、装配、操作 和 维 护技术。内容包括热 流 道 系 统 概 述、 塑 料 材 料 的 影 响、 热 流 道 喷 嘴、 热流道的流道板、温度控制系统、热流道系统设计、热流道的安 装 调 试、热流道注射模的使用和维护、热流道故障及对策等方面。本 书 面 向热流道注射模的设计和生产,实用性强,是我国第一本关于注射 模 热流道技术的专著。 本书可供从事注射模设计和制造的工程技术人员参考,也可作 为 塑料加工工程从业人员和相关专业在校师生的参考书。
第 1章 热流道系统概述
热流道注射模是无流道凝料注射模中最常见的一种。浇注系统凝料的存在不 仅浪费原材料和增大注射机的能耗,而且也增加了流道赘物处理工序。采用无流 道凝料的注射成型方法,可降低生产总成本。 热塑性塑料的无流道凝料注射成型,是对模具的浇注系统采用绝热或加热方 法,使其塑料熔体始终保持熔融状态,从而避免产生浇注系统凝料。热固性塑料 的无流道凝料注射模与热塑性塑料 成 型 相 仿, 也 是 使 浇 注 系 统 塑 料 熔 体 不 固 化, 维持可流动状态,热固性塑料的无流道凝料注射使用温流道注射模。 设置加热器使浇注系统内塑料保持熔融状态的热流道注射模,其热流道装备 有流道板、喷嘴和温度控制器等。由于技术难度高,这些热流道装备都由专业公 司制造和经营。注射模具的生产企业与热流道装备的生产和服务公司合作,共同 完成注射模具的设计和制造,并保证注射成型的生产。
1 1 原理和结构
热流 道 技 术 是 注 射 成 型 技 术 发展 的 新 阶 段, 了 解 热 流 道 系 统 的原 理 和 结 构, 要 从 注 射 的 冷 流 道系统开始。
1 1 1 注射模的冷流道系统
1 注射模的冷流道 注射 成 型 模 具 是 用 闭 合 和 开 启的 型 腔, 成 型 一 定 形 状 和 尺 寸 塑料制品的工具。图 1 1是最基本 的单 分 型 面 注 射 模, 也 是 这 种 两 板模 的 打 开 状 态。 凡 是 注 射 模, 均可 分 为 动 模 和 定 模 两 大 部 件。 注射 充 模 时, 动 模 与 定 模 在 分 型 面上 闭 合, 构 成 型 腔 和 浇 注 系 统
w w
w
冷流道。开 模 时 动 模 与 定 模 分 离,
1 —导柱 2 —主流道杯 3 —型芯 4 —注塑件 5 —流道 6 —主流道 7 —顶杆 8 —回程杆 9 —导套 1 0 —主流道拉杆 1 1 —顶柱 1 2 —顶出板
.g
ol
de
图1 1 单分型面注射模
n-
bo
ok
图书在版编目 ( C I P ) 数据
注射模的热流 道 技 术 / 王 建 华, 徐 佩 弦 编 著 . —北 京: 机 械 工 业 出 版社,2 0 0 7 6 9
Ⅰ.注 Ⅱ Ⅲ . 注 塑—无 流 道 冷 料 模 具 ①王 ②徐 Q 3 2 0 6 6 Ⅳ .T 中国版本图书馆 C I P数据核字 ( 2 0 0 5 )第 1 3 2 0 0 2号
中国科技金书网
w w
w
.g
ol
de
n-
bo
和点浇口。前者也称大浇口,系非限制性浇口。后两者为限制性浇口。
.c
om
注射模的热流道技术 2 取出制件。定模安装在注 射 机 的 固 定 板 上, 动 模 则 安 装 在 注 射 机 的 移 动 模 板 上。 单分型面注射模的主流道设在动模一侧,分流道设在分型面上。开模后注塑 件连同流道凝料一起留在动模一侧。动模上的脱模机构顶出制件和流道凝料。从 打开的动模和定模之间,取走注塑件和流道凝料。在模具重新闭合时,一般有回 程杆使脱模机构复位。 在注射模具中,用于取出塑料制件或浇注系统的面,通称为分型面。常见的 取出注塑件的主分型面,与开模方向垂直。 构成型腔,直接与熔 体 接 触 并 成 型 塑 料 制 件 的 零 件 称 成 型 零 件。 通 常 有 凸 模、型芯、成型杆、凹模、成型环和镶件等零件。在动模和定模闭合后,成型零 件确定了塑料件的内部、外部轮廓和尺寸。 将塑料熔体由注射 机 喷 嘴 引 向 型 腔 的 流 道 称 为 浇 注 系 统, 有 主 流 道、 分 流 道、浇口和冷料井组 成。 相 对 热 流 道 而 言, 不 加 热 也 不 绝 热 的 流 道, 称 为 冷 流 道。其中的冷却凝料在每次开模时必须取走。图 1 2所示模具采用的是一次成型 八个制件的冷流道系统。
w w
w
.g
ol
de
n-
bo
ok
.c
om
第 1章 热流道系统概述 3
中国科技金书网
图1 3 直浇口式主流道
a ) 整体主流道 b ) 组合主流道 1 —定位环 2 —定模垫板 3 —主流道衬套 4 —定模板
主流道锥孔壁面表面粗糙度 R 8 m 。主流道的锥度 α= 2 ° ~ 4 ° 。过大的 ≤0 μ a 锥度会产生湍流或涡流,卷入空气;过小的锥度使凝料脱模困难,还会使充模时 流动阻力增大。主流道的长度,一般按模板厚度确定,但为了减小充模时的压力 降低和减少主流道凝料,以较短为好,小模具控制在 5 0 m m 之内。在出现过长主 流道时,可将主流道衬套挖出深凹坑,让注射机喷嘴伸入模具。也有在主流道的 上游段设置加热喷嘴。热流道系统的主流道喷嘴,有绝热和加热两种,能维持主 流道中塑料的熔融状态。 主流道锥孔的大端直径 D ,要与分流道入口的直径相匹配,保证熔料的转向 和分流的畅通。主流道的出口端,也因此有较大的圆角 R= 1~ 2 m m 。 小型模具可将主流道衬套和定位环制成一体,见图 1 3 a 。定位环与注射机的 定模板上定位孔零间隙地相配,保证注射机喷嘴与模具中心同轴。冷流道模具在 段时间。在下次注射时再撞压主流道衬套。因此,主流道衬套的入口端面受喷嘴 足够硬度和可靠紧固。衬套用 T 8或 T 1 0制造,经淬火硬度为 5 0~ 5 5 H R C 。衬套 里端面与熔体接触面积尽可能小些,并由定位环压紧。 对于单型腔成型模具的冷流道系统,主流道凝料必须顺利地从孔中脱出。同 注塑件一起留在动模一侧。这就要有图 1 1所示的主流道拉杆 1 0 。杆的顶端有勾 子形状结构将主流 道 凝 料 拉 出,有 Z形 和 倒 锥 形 等。这 个 位 置 的 塑 料 也 是 贮 存 冷料的井。由于模具中 的 浇 注 系 统 有 冷 却 过 程, 注 射 充 模 的 熔 料 前 锋 的 温 度 较 前除去。热流道系统注射时,没有这种冷料前锋。热流道注射模具一般不设置冷 料井和拉料杆。 3 . 分流道 低。这部分冷料充填的制品部位,其物理性能很差。冷料必须在进入注塑件型腔