显示技术制程设备
oled工艺流程

oled工艺流程OLED显示技术(Organic Light Emitting Diode)是一种新型的平面显示技术,其工艺流程主要包括基板准备、有机发光材料的蒸镀、电极制备、封装和测试等步骤。
首先是基板准备。
在OLED显示器的制程中,选择适合的基板材料非常重要,常用的基板材料有玻璃和聚酯薄膜。
基板表面需要进行清洗和涂覆防护层等处理,以确保有机发光材料的附着和性能。
接下来是有机发光材料的蒸镀。
有机发光材料是OLED显示器的核心,通过蒸镀技术将有机分子层层堆积在基板上。
在蒸镀过程中,需要精确控制温度和蒸发速率,以实现红、绿、蓝三原色的有机分子的均匀堆积。
然后是电极制备。
在OLED显示器中,使用透明导电材料作为电极,通常采用氧化铟锡(ITO)薄膜作为阳极,铝或镁银合金作为阴极。
制备电极的方法一般有物理蒸镀和喷墨等技术,这些电极需要具备透明性和导电性。
接下来是封装。
封装是保护OLED显示器的重要步骤,它可以防止水汽和氧气进入显示屏,减少有机发光物质的寿命衰减。
常用的封装方法有真空封装和大气封装两种。
真空封装要求高,但能够有效延长显示器的使用寿命,而大气封装成本较低,但对显示器的使用寿命有一定的影响。
最后是测试。
在OLED显示器的生产过程中,需要对制造的显示器进行严格的测试。
测试内容包括电流-亮度特性、均匀度、色彩均匀度、灰阶等,并对其中的不良品进行剔除。
合格的显示器将进入最终组装和包装环节。
总的来说,OLED显示器的工艺流程包括基板准备、有机发光材料的蒸镀、电极制备、封装和测试等步骤。
这些步骤都需要精确控制各个工艺参数,以确保制造出高质量的OLED显示器。
OLED显示技术的应用前景广阔,未来可望实现更薄、更轻、更柔性的显示设备。
mini led晶圆 制程

mini led晶圆制程摘要:I.前言- 简要介绍mini LED晶圆制程的背景和重要性II.mini LED晶圆制程的概述- 什么是mini LED晶圆制程- mini LED晶圆制程的流程和步骤III.mini LED晶圆制程的关键技术- 介绍mini LED晶圆制程中的关键技术,如芯片设计、制造工艺等IV.mini LED晶圆制程的发展现状和前景- 分析当前mini LED晶圆制程的发展现状- 探讨mini LED晶圆制程的未来发展趋势和前景正文:I.前言随着显示技术的不断发展,mini LED晶圆制程技术逐渐成为人们关注的焦点。
作为一种新兴的显示技术,mini LED晶圆制程不仅可以提供更好的显示效果,还能够实现更低的能耗和更长的使用寿命。
因此,对mini LED晶圆制程的研究和开发具有重要的意义。
II.mini LED晶圆制程的概述mini LED晶圆制程是一种先进的显示技术,它通过在晶圆上制作大量微小的LED灯珠,形成一个阵列,从而实现图像的显示。
与传统LED显示技术相比,mini LED晶圆制程具有更高的分辨率、更快的响应速度和更低的能耗。
mini LED晶圆制程的流程和步骤主要包括:芯片设计、制造工艺、封装和测试等。
其中,芯片设计是关键,需要根据显示需求进行合理的布局和设计;制造工艺则需要通过一系列的工艺步骤,将设计好的芯片制作成实际的晶圆;封装和测试则是为了保证产品的质量和性能。
III.mini LED晶圆制程的关键技术在mini LED晶圆制程中,有很多关键技术,如芯片设计、制造工艺、封装技术等。
其中,芯片设计是关键中的关键,需要根据显示需求进行合理的布局和设计。
此外,制造工艺也是非常重要的一个环节,需要通过一系列的工艺步骤,将设计好的芯片制作成实际的晶圆。
最后,封装技术则是为了保证产品的质量和性能,需要将制作好的晶圆进行封装和测试。
IV.mini LED晶圆制程的发展现状和前景目前,mini LED晶圆制程技术已经取得了很大的进展,很多企业已经开始大量生产mini LED晶圆。
lcd制程简介知识讲稿

02
1990年代,LCD技术开始应用于电视和计算机显示
器等领域,成为主流显示技术之一。
03
随着科技的不断进步,LCD技术不断升级和完善,如
高分辨率、低功耗、柔性化等方向的发展。
lcd制程技术的应用场景
01
LCD技术广泛应用于电视、电 脑、手机、平板等电子产品领 域,成为主流显示技术之一。
02
此外,LCD技术还应用于汽车 、航空航天、医疗等领域,如 车载导航、飞机仪表盘、医疗 影像等。
详细描述:技术创新案例分享将涵盖以下内容
分析该技术创新的应用领域和优势,阐述其对LCD制程 的改进和提升作用
结合数据和图表,展示技术创新带来的效果和效益,包 括生产效率的提高、产品质量的提升以及成本的降低等 方面
市场应用案例分享
• 总结词:LCD制程的产品在市场上有着广泛的应 用,从消费电子到工业设备,再到汽车电子等领 域都有涉及。市场应用案例分享将介绍LCD产品 在各个领域的应用情况和市场前景。
详细描述
液晶灌注不足通常是由于灌注设备或工艺问题,导致液晶无法完全填充液晶盒 。这会导致像素不亮、对比度下降等问题。解决方法包括优化灌注设备和工艺 、控制灌注速度和时间等措施。
05
lcd制程发展趋势和展望
高分辨率lcd制程发展
技术创新
随着显示技术的不断发展,lcd制程在分 辨率上取得了显著的提升。新型的lcd面 板制造技术,如nano-crystal和color filter on array (cfa)等,正在不断涌现, 使得lcd面板的分辨率得到了大幅的提升 ,对于消费者来说,更加细腻的画质无 疑会带来更好的视觉体验。
检查
对注入后的液晶进行质量 检查,确保满足性能要求 。
LED芯片制程资料
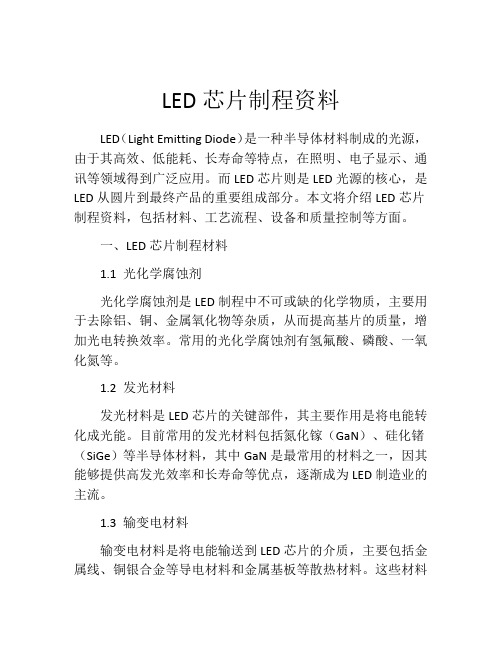
LED芯片制程资料LED(Light Emitting Diode)是一种半导体材料制成的光源,由于其高效、低能耗、长寿命等特点,在照明、电子显示、通讯等领域得到广泛应用。
而LED芯片则是LED光源的核心,是LED从圆片到最终产品的重要组成部分。
本文将介绍LED芯片制程资料,包括材料、工艺流程、设备和质量控制等方面。
一、LED芯片制程材料1.1 光化学腐蚀剂光化学腐蚀剂是LED制程中不可或缺的化学物质,主要用于去除铝、铜、金属氧化物等杂质,从而提高基片的质量,增加光电转换效率。
常用的光化学腐蚀剂有氢氟酸、磷酸、一氧化氮等。
1.2 发光材料发光材料是LED芯片的关键部件,其主要作用是将电能转化成光能。
目前常用的发光材料包括氮化镓(GaN)、硅化锗(SiGe)等半导体材料,其中GaN是最常用的材料之一,因其能够提供高发光效率和长寿命等优点,逐渐成为LED制造业的主流。
1.3 输变电材料输变电材料是将电能输送到LED芯片的介质,主要包括金属线、铜银合金等导电材料和金属基板等散热材料。
这些材料必须具有良好的导电和散热性能,以确保LED芯片的正常工作。
二、LED芯片制程工艺流程LED芯片制程包括原材料准备、基片清洗、晶体生长、芯片制造、打片、电极制造、封装等环节。
2.1 基片清洗为了保证LED芯片的品质,必须先将基片进行清洗,去除表面的污垢和杂质。
清洗过程包括去除油污、酸洗、去胶等,以确保基片表面光滑均匀,有利于晶体生长和芯片制造。
2.2 晶体生长在准备好的基片上,逐渐生长出半导体材料晶体。
这一过程包括衬底降温、沉积物初始附着、稳态生长等步骤。
通过这个步骤可以为LED芯片提供高质量的基板。
2.3 芯片制造在基片上生长晶体后,通过化学腐蚀和打印等工艺制作出各种形状的LED芯片。
2.4 电极制造在LED芯片上制作正、负电极,连接到芯片中心对应的区域。
电极制造的材料和工艺对LED芯片发光效率及稳定性有很大影响,需要进行精细的调整。
LCD模组制程原理
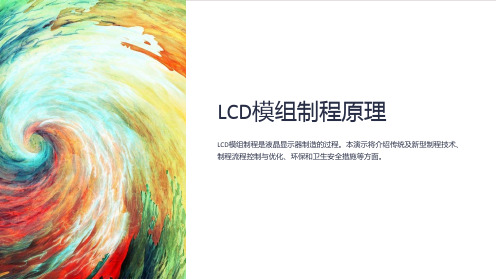
1
液晶面板制作
制作液晶面板,包括玻璃基板清洗、涂布、UV曝光、卤化物蒸发等步骤。
2
液晶面板与基板粘合
将液晶层与基板粘合,确保液晶层与色膜之间的间距均匀。
3
FPC连接步骤
连接灵活线路板(FPC)以操纵液晶面板。
新型LCD模组制程技术介绍
极板喷墨打印
采用喷墨技术在极板上印刷特定图案和字符,提高生产效率和降低成本。
LCD模组制程技术在自动化程度、环保措施、成本效益等方面将不断创新和发展,以满足人们对高质量显示的 需求。
模块封装和测试
对LCD模块进行封装和测试,确保其质量和功能。
模组清洗和质量检测
对模组进行清洗和质量检测,确保无灰尘和良好的显示效果。
LCD模组制程的重要性
LCD模组制程关乎液晶显示器的品质,决定其分辨率、色彩还原度等方面,对 电子产品的视觉体验至关重要。
LCD模制程发展历程
LCD模组制程经历了多年的发展,从传统制程到新型技术的引入,不断提升生 产效率、降低成本,并适应不断变化的市场需求。
LCD模组制程原理
LCD模组制程是液晶显示器制造的过程。本演示将介绍传统及新型制程技术、 制程流程控制与优化、环保和卫生安全措施等方面。
什么是LCD模组制程
LCD模组制程是液晶显示器的制造过程,包括设计外观和功能、透明基板材料 的选择、液晶面板制作、对色膜和透明电极的制备等步骤。
传统LCD模组制程步骤
LCD模组制程产业市场前景
LCD模组制程产业具有广阔的市场前景,随着智能设备的普及和需求的增长,LCD模组制程将持续引领显示技 术领域的发展。
LCD模组制程在电子产品生产 中的应用
LCD模组制程广泛应用于各类电子产品,如智能手机、电视、平板电脑和汽车 显示屏等,为用户提供出色的视觉显示效果。
micro led cog 常规制程
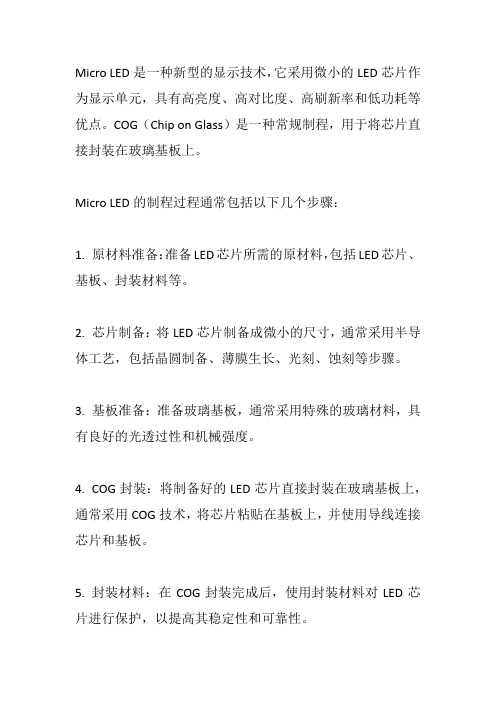
Micro LED是一种新型的显示技术,它采用微小的LED芯片作为显示单元,具有高亮度、高对比度、高刷新率和低功耗等优点。
COG(Chip on Glass)是一种常规制程,用于将芯片直接封装在玻璃基板上。
Micro LED的制程过程通常包括以下几个步骤:
1. 原材料准备:准备LED芯片所需的原材料,包括LED芯片、基板、封装材料等。
2. 芯片制备:将LED芯片制备成微小的尺寸,通常采用半导体工艺,包括晶圆制备、薄膜生长、光刻、蚀刻等步骤。
3. 基板准备:准备玻璃基板,通常采用特殊的玻璃材料,具有良好的光透过性和机械强度。
4. COG封装:将制备好的LED芯片直接封装在玻璃基板上,通常采用COG技术,将芯片粘贴在基板上,并使用导线连接芯片和基板。
5. 封装材料:在COG封装完成后,使用封装材料对LED芯片进行保护,以提高其稳定性和可靠性。
6. 测试和调试:对封装好的Micro LED进行测试和调试,确保其正常工作。
需要注意的是,Micro LED的制程相对复杂,需要高精度的设备和工艺控制,目前仍处于发展阶段,尚未实现大规模商业化生产。
LTPS制程与技术发展

LTPS制程与技术发展简介LTPS(Low Temperature Polysilicon)是指低温多晶硅制程。
它是一种用于制造高分辨率、高灵敏度的主动矩阵液晶显示器(AM-LCD)的技术。
LTPS制程与技术在过去几十年里经历了长足的发展,为现代液晶显示器的高品质和高性能提供了坚实的基础。
本文将重点介绍LTPS制程的原理、工艺步骤以及技术发展。
原理LTPS制程的原理是通过在低温条件下生长多晶硅薄膜来制造晶体管。
与普通的TFT(Thin Film Transistor)技术相比,LTPS制程可以在较低的温度下实现更高的结晶度和更高的电子移动度。
这样可以提高晶体管的开关速度和电流驱动能力,从而实现更高的像素密度和更快的响应时间。
LTPS制程使用的低温多晶硅薄膜通常通过两个步骤来生长:首先是硅薄膜的液相晶化(Liquid Phase Crystallization,LPC)过程,然后是后晶体治理(Post Annealing)过程。
在液相晶化过程中,通过在多晶硅薄膜上加热的同时用激光或其他能量源进行照射,使硅原子重新排列成晶体结构。
而在后晶体治理过程中,通过进一步的加热和退火处理来消除晶粒边界和其它缺陷,使得薄膜具有更好的结晶度和电学特性。
工艺步骤以下是LTPS制程的主要步骤:1.衬底准备:选择适当的衬底材料,通常使用的是玻璃基板或亚克力基板。
2.薄膜堆叠:在衬底上依次生长SiO2、SiNx等薄膜层,以提供电学绝缘和机械支撑。
3.多晶硅生长:在薄膜堆叠的表面上用PECVD(Plasma Enhanced Chemical Vapor Deposition)等方法生长一层非晶硅(a-Si)薄膜。
这是后续多晶硅生长的基础。
4.液相晶化:使用激光或其他能量源进行照射,在退火和加热的作用下,实现多晶硅薄膜的晶体结构生长。
5.后晶体治理:通过进一步的加热和退火处理,消除晶粒边界和其它缺陷,使得薄膜具有更好的结晶度和电学特性。
LCD制程工艺知识培训

LCD制程工艺知识培训概述液晶显示器(Liquid Crystal Display,简称LCD)是一种普遍应用于电子设备中的显示技术。
它由多个液晶分子组成,利用电场的作用来控制光的透过和阻挡,从而实现图像的显示。
LCD制程工艺是指将液晶显示器的各个组件制造和组装到一起的过程。
本文将介绍LCD制程工艺的一些基本知识,包括液晶材料的选择、液晶分子的排列与控制、背光源的制备以及最终的组装过程。
液晶材料的选择液晶材料是制作液晶显示器的关键之一。
根据不同的需求,液晶材料可以分为两种类型:向列型液晶和向行型液晶。
向列型液晶是指液晶分子在电场作用下,沿着电场的方向排列。
这种液晶材料适合于较小的液晶显示器,具有较高的亮度和对比度。
向行型液晶是指液晶分子在电场作用下,垂直于电场的方向排列。
这种液晶材料适用于较大尺寸的液晶显示器,具有更好的视角和更快的响应速度。
根据具体的设计要求和应用场景,制程工艺人员需要选择合适的液晶材料来满足产品的要求。
液晶分子的排列与控制液晶分子的排列和控制是液晶显示器的核心技术之一。
液晶分子的排列状态决定了显示器的图像效果和显示性能。
液晶分子有两种基本的排列状态:平行排列和垂直排列。
在制程过程中,可以通过设计电场的作用方式和液晶分子的配方来控制液晶分子的排列状态,从而达到不同的显示效果。
液晶的排列状态可以通过电极的设计和制备来控制。
通常情况下,液晶显示器需要两组电极,其中一组为透明电极,另一组为反射电极。
电场的作用下,液晶分子在两组电极之间排列,从而实现图像的显示。
背光源的制备LCD显示器的背光源是显示器的另一个重要组成部分。
背光源可以提供显示器所需的光源,使得图像在不同环境下都能够清晰可见。
常见的背光源有冷阴极管(CCFL)和LED背光源。
CCFL是一种传统的背光源技术,使用气态冷阴极管产生的光来提供背光。
LED背光源则是一种新型的背光源技术,使用发光二极管(LED)来提供背光。
制作背光源需要注意功耗和光效的均衡。
OLED制造中比较重要的三个制程

O L E D制造中比较重要的三个制程(总5页)--本页仅作为文档封面,使用时请直接删除即可----内页可以根据需求调整合适字体及大小--OLED制造中比较重要的三个制程的精华资料OLED制造中比较重要的三个制程的精华资料,大家看看,觉得好的给个回复,就是对论坛莫大的支持了!下面是OLED比较重要得三个制程得简短说明!至於材料方面嘛,上网应该可以查到得,目前磷光材料得应用前景要比荧光材料大的多,低分子比高分子的前途也要明朗些!ITO基板前处理制程制造有机EL显示面板所采用的Indium-tin-oxide (ITO) 透明导电玻璃基板,通常厚度为或的钠硷玻璃 (soda lime),在约150mm的ITO导电薄膜及钠硷玻璃基板之间镀上约数十微米的SiO2薄膜,以阻绝钠硷玻璃内金属离子游移的干扰,而ITO薄膜的导电特性则界定在其面电阻 (sheet resistance) 约10Ω/□。
在进入面板制造流程前ITO基板的洗净,则透过湿式及乾式的清洗制程达到高洁净度的ITO表面,在湿式清洗过程反覆地以中性洗剂及纯水超音波清洗後,再搭配有机溶剂以快速地乾燥ITO 基板,经过乾燥的ITO基板表面仍有些许的有机物残留,会影响ITO电极的正电荷 (h ole) 注入效率,UV-O3的处理可以将ITO基板上残留有机物除去,而存在ITO表面的缺陷可利用RF-O2电浆的表面改质处理,以降低正电荷注入的能阶障壁,因此,UV-O3及RF-O2电浆的乾式处理,能有效地降低有机EL元件发光的驱动电压,也广泛地应用在量产的制程中。
多层镀膜制程在发光亮度、耗电量及工作电压的操作条件考量下,多层结构的有机EL显示面板所提供的发光特性和稳定性,始能满足量产化的要求及量产生产时的效益,因此,多腔体的真空镀膜系统及单一镀膜腔体对应一层镀膜处理的设计原则,架构了量产装置的运作方式。
而针对多层镀膜量产系统及制程因应简述如下:1. Mask及ITO基板的对位:由於有机材料及其薄膜对湿式制程及温度的敏感性,使得一般常用於半导体晶圆制造上的微影蚀刻技术,无法被应用於有机EL面板制程中细微化的加工。
CVD制程工艺及设备介绍讲课文档

Plasma产生原理
在气压恒定的条件下,对气体增加能量(热能,电能等),当气体中的温度足够高时, 气体中的分子就会分解为原子气。进一步升高温度,原子就会分解为带电的自由离子( 电子和正离子),此时气体进入等离子体态。
热电离 电晕放电
等离子体产生
气体放电
激光压缩
辉光放电
电弧放电
射线辐照
Particle ① Mura ② Particle
目的 ①特性特性异常 ②成膜区域 ③防止后工程基板裂纹 ④特性异常 点缺陷和线缺陷 ①特性异常 ②点缺陷,线缺陷
① Particle ①特性异常
项目 ①Mura ②成膜区域 ③基板破损,划伤 ④异常放电 ① Mura ② Particle
①点缺陷,线缺陷 ②特性异常
C lc
Cs
第10页,共73页。
CVD工程在TFT流程中的作用
(受入洗净) 成膜前洗净
PVD 成膜(
Physical Vapor Deposition)
CVD 成膜 (Chemical Vapor
Deposition)
光刻(Lithograph)
湿蚀刻 (WET Etch)
干蚀刻 (Dry Etch)
第15页,共73页。
几种常见CVD比较
种类 设备简图
热CVD
AP-CVD (Atmospheric Pressure CVD)
LP-CVD(Low Pressure CVD)
成膜气体
基板
等离子CVD
PE-CVD (Plasma enhanced CVD)
真空腔室
成膜 气体
RF电源
电 极
Plasma
第20页,共73页。
LCD基础知识及制造工艺流程介绍

LCD基础知识及制造工艺流程介绍LCD(液晶显示器)是一种运用液晶技术显示图像的平面显示设备。
它由一系列的液晶层、玻璃基板、导线及亮度调节膜等组成,能够实现高清晰度和低功耗的图像显示。
下面将介绍LCD的基础知识以及制造工艺流程。
一、LCD的基础知识1.液晶层:液晶是一种类似于液体的物质,具有一定的流动性。
液晶分为向列型液晶和向量型液晶两种。
其中,向列型液晶具有电流传输性能,可用于显示器制造。
液晶层通常由两块玻璃基板夹层组成。
2.基板:LCD的基板通常由玻璃或塑料材料制成。
它是液晶显示器的结构支撑物,上面附着有液晶材料,起到固定液晶和导线的作用。
3.导线:液晶显示器中的导线用于传输电信号,驱动液晶层完成图像的显示。
导线通常由透明导电材料(如铟锡氧化物)制成,通过在基板上形成通道和窗口的方法实现。
4.亮度调节膜:亮度调节膜用于控制液晶层的透光度,实现图像亮度的调节。
它通常由聚合物、薄膜材料或金属制成。
二、LCD的制造工艺流程1.基板生产:使用特制的玻璃或塑料材料制造基板,通过磨削、抛光和清洗等步骤形成平整的表面。
2.导线制作:将透明导电材料(如铟锡氧化物)涂布在基板上,然后通过光刻技术制作出导线的图案。
这包括涂覆光刻胶、曝光、显影和洗涤等步骤。
3.形成储存电容:在导线制作完成后,在基板上制作出储存电容的结构。
这通常通过在导线上涂覆并定位特定的电介质材料,然后用导线封装住这种材料。
4.液晶层制作:将液晶材料涂布在基板上,并进行取向处理。
液晶材料的涂布可以通过刮板涂布或滚涂等方法完成。
5.封装背光模块:将背光源(通常是冷阴极荧光灯或LED)和光学片封装在一起,形成背光模块。
6.封装前端制程:在液晶层基板中制造出色彩滤光片、液晶层与色彩滤光板的层间空气封闭结构,同时加工出液晶层之间分隔固体极板和液晶层封装胶。
7.封装:将两块形成互相关系的液晶层基板合并在一起,使用封装剂将其密封。
8.后端制程:液晶显示器的后端制程包括模组组装、封装测试、调试和包装等步骤。
tft 制程工艺

tft 制程工艺标题:理解与探索:TFT制程工艺详解一、引言TFT(Thin Film Transistor)即薄膜晶体管,是液晶显示器(LCD)和有机发光二极管(OLED)显示技术中的关键组件。
TFT制程工艺是制造这些显示器的核心技术,涉及到多个复杂的步骤和精密的工艺流程。
本文将深入探讨TFT制程工艺,帮助读者理解这一高科技领域的奥秘。
二、TFT的基本结构TFT主要由栅极绝缘层、活性层和源/漏极组成。
栅极绝缘层通常由二氧化硅构成,活性层主要使用硅或新型材料如氧化物半导体,源/漏极则由金属材料制成。
这些层通过精细的制程工艺沉积在玻璃基板上,形成一个个微小的晶体管。
三、TFT制程工艺流程1. 基板清洗:首先,玻璃基板需要经过严格的清洗,以去除任何可能影响后续步骤的杂质。
2. 靶材沉积:然后,通过物理气相沉积(PVD)或化学气相沉积(CVD)等方法,在基板上沉积各种材料,形成所需的薄膜层。
3. 光刻:接着,利用光刻技术,将设计好的电路图案转移到薄膜层上。
这个过程需要精确控制,以确保每个晶体管的位置和尺寸准确无误。
4. 蚀刻:光刻后,通过蚀刻工艺,将不需要的部分薄膜去除,留下预定的电路图案。
5. 金属化:在源/漏极位置沉积金属,形成导电路径。
6. 终止和测试:最后,进行封装和测试,确保每个TFT的功能正常。
四、TFT制程工艺的挑战与发展趋势TFT制程工艺面临着精度要求高、环境污染控制严格、成本控制等挑战。
随着科技的进步,新的材料和工艺,如低温多晶硅(LTPS)和铟镓锌氧化物(IGZO)等,正在推动TFT技术向更高分辨率、更低功耗、更小尺寸的方向发展。
五、结论TFT制程工艺是现代显示技术的基础,其复杂性和精确度体现了人类科技的精妙之处。
随着科技的不断进步,我们期待看到更多创新的TFT工艺和技术,为我们的生活带来更优质的显示体验。
LED显示屏关键制程浅析
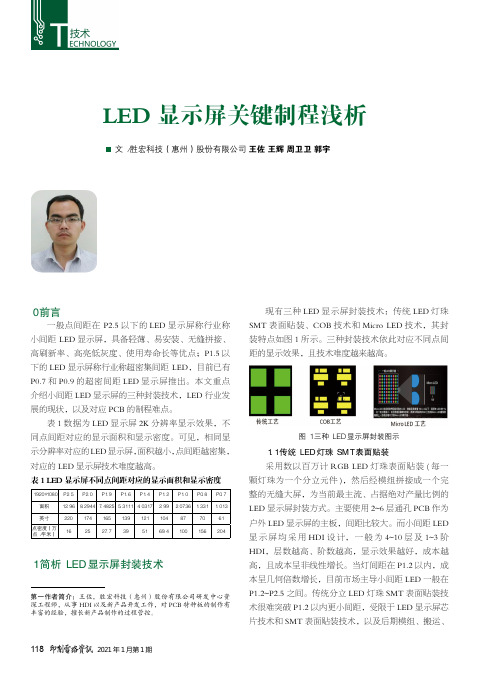
2021年1月第1期118现有三种LED 显示屏封装技术:传统LED 灯珠SMT 表面贴装、COB 技术和Micro LED 技术,其封装特点如图1所示。
三种封装技术依此对应不同点间距的显示效果,且技术难度越来越高。
LED 显示屏关键制程浅析文/胜宏科技(惠州)股份有限公司 王佐 王辉 周卫卫 郭宇一般点间距在 P2.5以下的LED 显示屏称行业称小间距 LED 显示屏,具备轻薄、易安装、无缝拼接、高刷新率、高亮低灰度、使用寿命长等优点;P1.5以下的LED 显示屏称行业称超密集间距 LED,目前已有P0.7和P0.9的超密间距LED 显示屏推出。
本文重点介绍小间距LED 显示屏的三种封装技术,LED 行业发展的现状,以及对应PCB 的制程难点。
表1数据为LED 显示屏2K 分辨率显示效果,不同点间距对应的显示面积和显示密度。
可见,相同显示分辨率对应的LED 显示屏,面积越小,点间距越密集,对应的LED 显示屏技术难度越高。
【摘 要】 广告牌、霓虹灯等广告形式渐渐退出,取而代之的是一块块形状各异的LED显示屏;相对于LCD而言,LED显示屏具备大尺寸无缝拼接、自由灵活组合、亮度高、单点可控、色彩饱满、节能环保、形状多样、显示方式随意切换等优势。
本文重点讨论三种LED显示屏技术和对应的PCB关键制程。
【关键词】COB;Micro LED;PPI(pixels Per inch);光学锣机第一作者简介:王佐,胜宏科技(惠州)股份有限公司研发中心资深工程师,从事HDI 以及新产品开发工作,对PCB 特种板的制作有丰富的经验,擅长新产品制作的过程管控。
1 简析LED显示屏封装技术0前言图1 三种LED显示屏封装图示表1 LED 显示屏不同点间距对应的显示面积和显示密度1.1传统LED灯珠SMT表面贴装采用数以百万计RGB LED 灯珠表面贴装(每一颗灯珠为一个分立元件),然后经模组拼接成一个完整的无缝大屏,为当前最主流、占据绝对产量比例的LED 显示屏封装方式。
cmos oled 制程
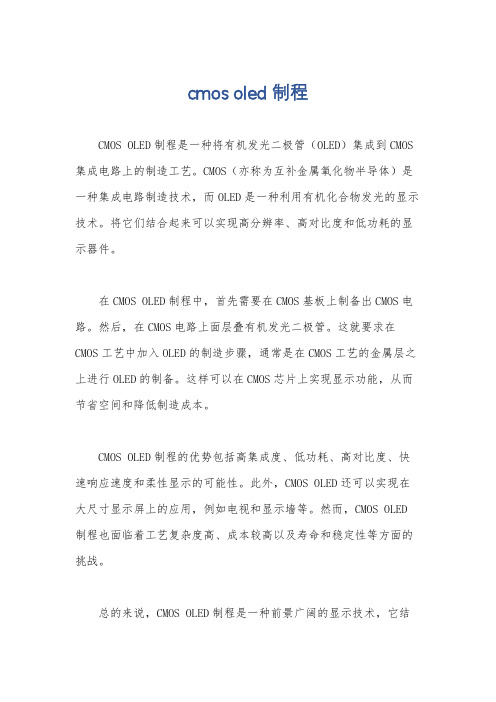
cmos oled 制程
CMOS OLED制程是一种将有机发光二极管(OLED)集成到CMOS 集成电路上的制造工艺。
CMOS(亦称为互补金属氧化物半导体)是一种集成电路制造技术,而OLED是一种利用有机化合物发光的显示技术。
将它们结合起来可以实现高分辨率、高对比度和低功耗的显示器件。
在CMOS OLED制程中,首先需要在CMOS基板上制备出CMOS电路。
然后,在CMOS电路上面层叠有机发光二极管。
这就要求在CMOS工艺中加入OLED的制造步骤,通常是在CMOS工艺的金属层之上进行OLED的制备。
这样可以在CMOS芯片上实现显示功能,从而节省空间和降低制造成本。
CMOS OLED制程的优势包括高集成度、低功耗、高对比度、快速响应速度和柔性显示的可能性。
此外,CMOS OLED还可以实现在大尺寸显示屏上的应用,例如电视和显示墙等。
然而,CMOS OLED 制程也面临着工艺复杂度高、成本较高以及寿命和稳定性等方面的挑战。
总的来说,CMOS OLED制程是一种前景广阔的显示技术,它结
合了CMOS集成电路和OLED显示的优点,可以应用于各种便携式设备和大尺寸显示屏,并有望成为未来显示技术的发展方向之一。
LCD制程简介含ODF-简体

THANKS
感谢观看
04
LCD制程与ODF技术的结合
ODF技术在LCD制程中的应用
液晶显示器的制程中,ODF技术主要用于优化薄膜晶体管(TFT)的制程,以提高 液晶显示器的性能。
ODF技术通过精确控制薄膜晶体管的形状、尺寸和位置,实现了更精细的像素控制, 提高了液晶显示器的分辨率和清晰度。
ODF技术还被用于制造具有更高开关速度和更低功耗的薄膜晶体管,从而提高了液 晶显示器的动态显示性能。
数据更加易于理解和可视化。
ODF技术的应用范围
数据交换
ODF技术可以用于不同系统之间 的数据交换,使得不同系统之间 的数据共享和集成更加方便。
数据可视化
ODF技术可以用于生成高质量的 矢量图形,使得数据更加易于可 视化和展示。
数据处理
ODF技术可以用于处理和分析复 杂的数据结构,使得数据的层次 关系更加清晰,便于理解和使用。
ODF技术的特点
01
可扩展性
ODF技术基于XML和SVG标准,具有良好的可扩展性,可以适应各种
不同类型的数据和业务需求。
02
标准化
ODF技术是一种标准化的技术,遵循国际标准组织(ISO)和开放地理
空间联盟(OGC)的规定,使得不同系统之间的数据交换更加方便。
03
可视化
ODF技术使用SVG标准来表示数据,可以生成高质量的矢量图形,使得
驱动IC
随着技术的不断发展,新型驱动 IC材料和工艺不断涌现,能够提 高LCD的显示效果和稳定性以及 降低生产成本。
04
01
驱动IC是LCD的重要组件之一, 负责控制LCD像素的开关和调节。
OLED制造中比较重要的三个制程
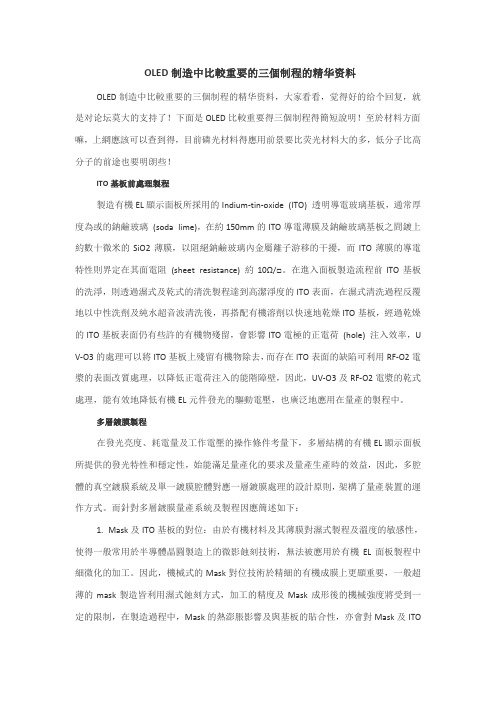
OLED制造中比較重要的三個制程的精华资料OLED制造中比較重要的三個制程的精华资料,大家看看,觉得好的给个回复,就是对论坛莫大的支持了!下面是OLED比較重要得三個制程得簡短說明!至於材料方面嘛,上網應該可以查到得,目前磷光材料得應用前景要比荧光材料大的多,低分子比高分子的前途也要明朗些!ITO基板前處理製程製造有機EL顯示面板所採用的Indium-tin-oxide (ITO) 透明導電玻璃基板,通常厚度為或的鈉鹼玻璃(soda lime),在約150mm的ITO導電薄膜及鈉鹼玻璃基板之間鍍上約數十微米的SiO2薄膜,以阻絕鈉鹼玻璃內金屬離子游移的干擾,而ITO薄膜的導電特性則界定在其面電阻(sheet resistance) 約10Ω/□。
在進入面板製造流程前ITO基板的洗淨,則透過濕式及乾式的清洗製程達到高潔淨度的ITO表面,在濕式清洗過程反覆地以中性洗劑及純水超音波清洗後,再搭配有機溶劑以快速地乾燥ITO基板,經過乾燥的ITO基板表面仍有些許的有機物殘留,會影響ITO電極的正電荷(hole) 注入效率,U V-O3的處理可以將ITO基板上殘留有機物除去,而存在ITO表面的缺陷可利用RF-O2電漿的表面改質處理,以降低正電荷注入的能階障壁,因此,UV-O3及RF-O2電漿的乾式處理,能有效地降低有機EL元件發光的驅動電壓,也廣泛地應用在量產的製程中。
多層鍍膜製程在發光亮度、耗電量及工作電壓的操作條件考量下,多層結構的有機EL顯示面板所提供的發光特性和穩定性,始能滿足量產化的要求及量產生產時的效益,因此,多腔體的真空鍍膜系統及單一鍍膜腔體對應一層鍍膜處理的設計原則,架構了量產裝置的運作方式。
而針對多層鍍膜量產系統及製程因應簡述如下:1. Mask及ITO基板的對位:由於有機材料及其薄膜對濕式製程及溫度的敏感性,使得一般常用於半導體晶圓製造上的微影蝕刻技術,無法被應用於有機EL面板製程中細微化的加工。
lcd 生产工艺 设备

lcd 生产工艺设备1.引言1.1 概述概述:随着科技的不断进步,液晶显示(LCD)技术已成为现代电子产品中最常用的显示技术之一。
无论是智能手机、电视、电脑还是汽车导航系统,LCD都扮演着重要的角色。
LCD的生产工艺和设备在保证产能和质量的同时,也在不断创新和改进。
本文将详细介绍LCD的生产工艺和设备。
我们将首先介绍LCD的生产工艺,包括基本原理、液晶分子排列、色彩显示技术等。
其次,我们将重点关注LCD的生产设备,包括面板制造设备、芯片制造设备、封装设备等。
通过了解LCD的生产工艺和设备,我们可以更深入地了解LCD技术的发展和应用。
本文的目的是为读者提供一个全面了解LCD生产工艺和设备的指南。
通过了解LCD的生产工艺和设备,读者可以更好地理解LCD技术的背后原理和制造过程,为他们在相关领域的研究和工作提供有益的参考。
另外,本文也可以作为LCD生产企业和相关从业人员的培训材料,帮助他们更好地掌握和应用LCD生产工艺和设备。
在接下来的章节中,我们将逐一介绍LCD的生产工艺和设备。
首先,我们将详细介绍LCD的生产工艺,包括液晶分子的排列、电场控制、背光源等。
然后,我们将介绍LCD的生产设备,包括面板制造设备、芯片制造设备和封装设备。
最后,我们将对整个文章进行总结,并展望未来LCD生产工艺和设备的发展趋势。
通过本文的学习,读者将能够全面了解LCD的生产工艺和设备,掌握LCD技术的核心原理和制造过程。
希望本文能够为读者提供有价值的信息,并对LCD行业的发展做出积极贡献。
1.2文章结构文章结构部分的内容可以写成以下方式:在本文中,我们将首先介绍LCD生产工艺,包括其整体的制造流程和各个关键步骤。
随后,我们将详细探讨LCD生产所需的各种设备及其功能。
通过对这些工艺和设备的介绍,我们将能够全面了解LCD的制造过程,并了解如何使用相关设备来实现LCD的生产。
最后,我们将给出文章的结论,总结所述内容,并展望未来LCD生产工艺及设备的发展趋势。
OGS制程工艺讲解

OGS制程工艺讲解1. 什么是OGS制程工艺?OGS制程工艺是一种在触摸屏显示技术中常用的工艺流程,其全称是One Glass Solution,意为“一玻璃解决方案”。
在OGS技术中,触摸感应电路和显示屏幕合为一体,大幅降低了触摸屏幕的复杂度和厚度,提高了显示效果和触控灵敏度。
2. OGS制程工艺的基本原理OGS制程工艺将传统的ITO导电层与玻璃基板融合为一体,通过特殊的工艺将电容式触摸技术结合到显示屏上。
在制程中,首先在一块大型的玻璃基板上涂覆导电膜,然后通过激光切割或化学蚀刻的方式形成电容感应区域。
3. OGS制程工艺的优势•更加轻薄:由于将触控电路整合到显示屏幕中,不需要额外的触摸板,因此产品更加轻薄。
•更高的透光率: OGS工艺中只有一层玻璃,相比传统技术有更高的透光率,提升了显示效果。
•更好的触控体验:由于电容式触摸技术的应用,触控更加灵敏准确。
4. OGS制程工艺的制作流程1.基板准备:选择高质量的玻璃基板,保证表面平整度和透明度。
2.涂覆导电膜:在玻璃基板上涂覆ITO导电膜。
3.光刻和蚀刻:通过光刻和蚀刻工艺制作出电容感应区域。
4.金属化:对电容感应区域进行金属化处理,提高导电性能。
5.封装:将触控电路层封装在另一块玻璃基板中,形成完整的显示屏。
5. OGS制程工艺在行业应用OGS制程工艺在手机、平板电脑、笔记本电脑等电子产品中得到广泛应用。
其轻薄、透光率高、触控灵敏等优势使得触摸屏显示效果更佳,用户体验更好。
6. 结语总的来说,OGS制程工艺通过将触控电路整合到显示面板中,使得产品更加轻薄透光率更高,并提高了触控体验。
在未来,随着科技的发展,OGS制程工艺有望进一步改进和拓展应用领域。
- 1、下载文档前请自行甄别文档内容的完整性,平台不提供额外的编辑、内容补充、找答案等附加服务。
- 2、"仅部分预览"的文档,不可在线预览部分如存在完整性等问题,可反馈申请退款(可完整预览的文档不适用该条件!)。
- 3、如文档侵犯您的权益,请联系客服反馈,我们会尽快为您处理(人工客服工作时间:9:00-18:30)。
6、離子植入裝置 (Ion Implant System)
• 是由重離子加速器及同位素分離器所發展而來 • 應用於不純物質的摻雜處理,進而獲得優良的物理性質 • 一般裝置可分為
– – – – – – – – – – 超低能量型的(Ultra-Low Energy) 中電流型的(Medium Current) 高能量型的(High Energy) 高電流型的(High Current) 植入元素離子化的離子源(一般為Freeman型離子源)及其引出機構 植入離子之質量分離器 高電場離子加速化的加速管 離子束的收斂及偏向處理的偏向機構 基板導入、傳送、掃描和送出等功能的植入處理室 馬達驅動機構、真空系統、電源供應系統及控制系統。
1、液晶胞洗淨裝置
• • • • 分為配向膜印刷前洗淨 面膜後(Lapping)洗淨 液晶注入後洗淨 偏光板貼合前洗淨。
2、配向膜印刷裝置
• 主要目的是為了能形 成配向性液晶。 • 主要配向膜用的材料
– 聚乙醯類樹脂 (Polyimide Resin,PI) , 在溶液狀態將其塗佈 於基板表面;在基版表 面上塗佈聚乙醯溶液 的裝置。
TFT ARRAY製造技術
以通道蝕刻型α –Si TFT array製程為 例—
α –Si TFT array 的製程有洗淨技術、成膜 技術(濺鍍法、化學氣相沉積法)、光微影 技術(光阻劑塗佈、預先烘焙、微影、顯 影、後續烘焙)、蝕刻技術、光阻劑去除 技術及電極蒸鍍技術。
資料來源:顧鴻壽編著,“光電液晶平面顯示器—技術基礎及應用”
3、配向膜烘培裝置
• 目的是利用脫水閉環反應使配向膜聚醯 化,及使配向膜殘存之溶媒得以去除 • 加熱溫度在180~250゚C左右 • 一般常用的有
– 熱風爐方式 – 熱板方式 – 遠紅外線加熱方式
4、面膜裝置(Rubbing System)
• 目的:使配向膜表面之配合導向力增強 • 面磨方式是利用毛布在配向膜表面於一 定方向上進行擦拭,以達到液晶分子的 初期配向處理 • 布材視其用途有使用人造纖維、綿、耐 龍等
資料來源:顧鴻壽編著,“光電液晶平面顯示器—技術基礎及應用”
資料來源:顧鴻壽編著,“光電液晶平面顯示器—技術基礎及應用”
TFT Array 製造設備
玻璃研磨裝置 洗淨裝置 微影曝光裝置 光阻劑旋轉被覆及顯 影裝置 • 光阻劑剝除裝置 • • • • • 乾式蝕刻裝置 • 濕式蝕刻裝置 • 化學氣相沉積鍍膜裝 置 • 濺鍍鍍膜裝置 • 離子植入裝置 • 雷射退火裝置
• 微影製程設備:以曝光用步進機為核心設備, 主要供應商有尼康精機 (Nikon) 、佳能 (Canon) 及ASML公司等三家為主。 • 一般微影製程設備分類有
– – – – – 光微影裝置 電子束微影裝置 雷射束微影裝置 離子束微影裝置 X射線微影裝置。
5、蝕刻製程裝置 (Etching System)
• 蝕刻技術是將不需要的光阻劑部分以物理或化學方式 去除,進而形成所需圖案的一種工程手段。 • 蝕刻製程設備分為:
– 濕式蝕刻(Wet Etching) 裝置:屬等方向性蝕刻,使用HCl、 HNO3、HF等酸性溶液進行蝕刻。 – 乾式蝕刻(Dry Etching裝置:屬異方向性蝕刻
• 化學乾式蝕刻(Chemical Dry Etching,CDE)裝置 • 反應性離子蝕刻(Reactive Ion Etching ,RIE)裝置 • 電漿蝕刻(Plasma Etching ,PE)裝置
2、成膜製程裝置—濺鍍(1) (Thin Film Formation System)
• 濺鍍(Sputtering)成膜法是應用於成長閘電 極、源電極、汲電極、掃描線、儲存電 容電極、信號線以及畫素電極等功能性 金屬薄膜。 • 一般濺鍍裝置基本結構有真空反應室、 排氣機構、放電非活性氣體導入及其壓 力控制系統、放電電力供應控制系統、 濺鍍材料的靶極承接器、基板的傳送搬 運以及保持系統。
2、成膜製程裝置—
化學氣相沉積(Chemical Vapor Deposition, CVD)(2)
• 大氣壓型化學氣相沉積法(Atmospheric Pressure CVD)
– 運用於成長閘電極絕緣膜及層間絕緣膜功能 之SiO2膜。 – 利用熱分解方式,將原料氣體分解反應,促 使薄膜堆積成形。 – 主要機制在於基板表面附近產生反應作用, 使得微小顆粒較少發生,其絕緣性優良。
3、光阻劑塗佈製程裝置 (Photo Resist Coating System)
• 光阻劑塗佈是將光阻劑液滴落於基板的 中央,使其旋轉被覆(Spin Coating),進 而均勻地散布於基板以形成薄膜。 • 旋轉被覆方式的主要缺點:90%以上的 光阻劑液在旋轉被覆中容易流失。
4、微影製程裝置 (Lithography System)
前言
TFT LCD的陣列電路製程可區分為
• 玻璃基板上形成TFT Array Process:控制及調 變光線之各個畫像素電極、時序信號傳送的配 線及開關元件、透明電極等 • Cell Process :TFT Array底層玻璃基板及CF的 上層玻璃基板相互貼合並控制其間的間隙距離, 注入液晶後加以封合 • Assembly Process:將液晶胞面板、提供影像信 號和掃描信號驅動IC及控制IC、週邊的零組件 整合於印刷電路板上,並與背光板貼合
2、成膜製程裝置—
化學氣相沉積(Chemical Vapor Deposition, CVD)(2)
• 電漿增強型化學氣相沉積法(Plasma Enhanced CVD)
– 在真空中導入反應氣體,使用高頻產生電漿 於兩片平行平板電極間,將所產生的反應自 由基(Radical)傳達至基板表面,產生表面反 應堆積成薄膜,使用原料氣體為SiH4、PH3、 NH3、N2O等。
9、裁剪切斷裝置 (Panel Breaking System)
• 目的:將所定之大尺寸液晶胞裁剪切割 • 切斷分割方式和裝置有
– 畫線機(Scriber) – 切割機(Break System)
10、液晶導入裝置 (Liquid crystal Filling and EndSealing System)
• 目的:使截斷後的液晶胞,於其內部導 入或注入液晶分子材料
11、偏光板貼合覆著裝置 (Polarizer Sticking System)
• 目的:在導入液晶材料的液晶胞兩測進 行偏光板附著處理 • 偏光板組成:偏光膜、接著劑、保護膜、 剝離膜等 • 偏光板容易發生靜電效應,造成薄膜電 晶體元件特性的損傷,在處理過程須做 好靜電防止的預防對策
2、成膜製程裝置—
化學氣相沉積(Chemical Vapor Deposition, CVD)(1)
• 使用CVD成長薄膜的製程有
半導體層的氫化,形成非晶矽薄膜(α –Si:H) 高濃度磷摻雜於n型的 α –Si:H層 閘電極絕緣膜 層間絕緣膜或作為保護膜功能之氮化矽 (SiNx) – 氧化矽膜(SiOx)等 – – – –
2、成膜製程裝置—濺鍍(2) (Thin Film Formation System)
• 一般濺鍍製程是使用氬類的非活性氣體, 進行物理式的濺鍍
– 反應性濺鍍法:導入反應性氣體時,伴隨著 產生化學反應,進而達到薄膜的形成。 – 同步式濺鍍法(或稱偏壓式濺鍍法):將數個 不同組成的靶材,置入各別獨立的濺鍍控制 系統,使數個靶材同時進行濺鍍,形成組成 不同化合物或合金的薄膜。
1、洗淨製程裝置 (Cleaning System)
• 洗淨製程作業程序佔整個流程的30%, 對於製程的良率有極大影響 • 使用物理式洗淨技術:毛刷刷洗、超音波
振盪、極超音速振盪、純水噴洗等
• 使用化學式洗淨技術:介面活性劑、酸性
溶液、鹼性溶液、臭氧水溶液等
• 洗淨裝置的種類有:濕式、機械r Spray System)
• 目的:為了使液晶層的厚度均勻化
6、封合材印刷裝置 (Seal Materials Printing System)
• 目的:在兩片玻璃基板上塗佈封合材 • 塗佈方式有
– 網版印刷方式(Screen Printing) – 散布方式(Dispenser)
• 裝置基本結構有
7、光阻劑剝除製程裝置
• 光阻劑剝除方法有
– 藥液剝除法 – 依據氧電漿原理的氧化分解去除的除塵法
• 電漿除塵 • 紫外線除塵 • 臭氧除塵
液晶胞製程/模組設備
• • • • • • • • 洗淨裝置 配向膜塗佈裝置 烘培以及退火爐 面磨裝置 網版印刷裝置 間隔物散布裝置 割線切斷裝置 液晶材料導入裝置 分散器裝置 外接角型構裝裝置 貼合以及硬化裝置 偏光板貼合裝置 帶狀自動接著式及晶 片在玻璃接著式構裝 裝置 • 封合裝置 • • • • •
第2章 顯示技術製程設備
前言
α –Si TFT LCD的應用領域
• • • • 以筆記型電腦的用途為主 小型口袋式的電視機 大型的監視器 液晶電視機
前言
矽半導體材料的製造過程區分為 • 前段工程(Front End Of the Line,FEOL) :基板 上製作電晶體、電阻器以及電容器等電子元件 的工程,亦稱晶圓工程(Wafer Process) , (Wafer • 後段工程(Back End Of the Line,BEOL):在基 板上將電路配線形成的配線工程,亦稱組裝及測 試工程(Assemble &Test Process)
7、基板對準和貼合裝置 (Panel Alignment and Assembly System)
• 目的
– 將兩枚玻璃基板精密地貼合在一起 – 使液晶胞之間隙維持在一定值
8、封合硬化裝置 (Sealing System)
• 主要目的
– 使封合劑產生硬化作用 – 使液晶胞之間隙達到所希望之值而固定之