安定化生产:品质的安定
安定化生产人员的安定课件

解决方案
提高员工福利待遇,建立激 励机制,提供职业发展机会 ,加强企业文化建设,提高 员工归属感和忠诚度。
生产效率问题
生产效率低下
由于设备老化、工艺落后、操作 不规范等原因,导致生产效率低 下,影响企业盈利能力和市场竞
争力。
成本压力大
在竞争激烈的市场环境下,低生产 效率可能导致企业成本压力增大, 难以保持竞争优势。
制定完善的福利制度,包括五险一金、带 薪年假、节日福利等,提高员工的工作满 意度和生活质量。
员工关怀
激励效果的评估
关注员工的身心健康和家庭状况,提供必 要的关怀和支持,增强员工的归属感和忠 诚度。
对激励和福利制度的效果进行评估,及时 调整和完善制度,确保其合理性和有效性 。
人员沟通与协调
沟通渠道建立
02
人员安定管理
人员招聘与培训
招聘标准
制定明确的招聘标准,确保招 聘到的人员具备必要的技能和
素质,能够胜任工作。
培训计划
根据员工的岗位需求和职业发 展规划,制定个性化的培训计 划,提升员工的专业技能和知 识水平。
培训实施
定期组织内部培训、外部培训 和在线培训,确保员工能够及 时获取最新的知识和技能。
VS
详细描述
实施安定化生产需要从以下几个方面入手 :1. 人员培训:加强员工的安全意识和 技能培训,提高员工的素质和能力;2. 设备维护:建立完善的设备维护和保养制 度,确保设备的正常运行;3. 工艺优化 :不断优化生产工艺,提高生产效率和产 品质量;4. 环境管理:加强环境管理, 减少生产过程中的环境污染;5. 质量管 理:建立完善的质量管理体系,确保产品 质量符合要求。
培训评估
对培训效果进行评估,及时调 整培训计划,确保培训的有效
2-2.163 精益知识——精益生产的四化管理

53、精益知识——精益生产的四化管理精益生产是一个永无止境的精益求精的过程,它致力于改进生产流程和流程中的每一道工序,尽最大可能消除价值链中一切不能增加价值的活动,提高劳动利用率,消灭浪费,按照顾客订单生产的同时也最大限度的降低库存。
精益生产求精的方法可以总结为四化管理。
那么什么是四化管理呢,下面精益生产咨询专家为大家介绍如下:一、精益生产之流线化生产1流线化生产的意义2流线化生产与批量生产的差异3流线化生产的八个条件4流线化生产的步骤5流线化生产的设计原则6流线化生产的设计要点二、精益生产之安定化生产1、人员的安定(1)标准化作业(2)多技能工训练技巧(3)动作经济原则2、设备的安定(1)可动率才重要(2)自主保全与零故障(3)TPM的几大步骤(4)TPM推进的关键点(5)TPM案例讲解与讨论:3、品质的安定(1)现场品质的意识和三不政策(2)品质管理的八条原则和五项战术(3)六西格玛品质改善技术4、物量的安定(1)突破传统思维,经济批量不经济(2)快速切换的基本方法和原则5、管理的安定(1)现场管理的安定法则,人定胜天(2)如何形成现场改善自律机制(3)对日常管理病开药方,5S(4)目视管理,让问题看得出来三、精益生产之平稳化生产(1.5H)1、什么是平稳化生产2、平稳化生产的技巧3、混流生产是平稳化生产的最高境界4、运用约束理论突破流程瓶颈四、精益生产之超市化生产(4H)1、JIT交货与JIT生产2、生产节拍的计算方法3、推系统与拉系统,前推后拉方式如何实现4、如何应对订单波动,平衡生产5、如何预测市场需求,掌握生产主动权。
精益生产实务四安定化生产

精益生产实务四安定化生产什么是精益生产实务四安定化生产?精益生产实务四安定化生产是精益生产方法的一种实践方法,旨在实现生产过程的持续改进和稳定性。
它涉及到四个关键方面的安定化措施,分别是:人员安定化、设备安定化、工艺安定化和品质安定化。
通过实施这些措施,企业可以达到高效、高质量、高稳定性的生产流程,提高生产效率和产品质量。
人员安定化人员安定化是指保持员工队伍的稳定性和连续性。
实现人员安定化的关键是重视人才培养、员工满意度和员工关系管理。
企业需要提供良好的工作环境和福利待遇,关注员工的职业发展和提升,并鼓励员工参与持续改进的活动。
人员安定化可以带来以下益处:•减少员工离职率:稳定的员工队伍可以减少员工离职率,降低员工流动带来的培训成本和时间成本。
•提高工作效率:稳定的员工队伍熟悉工作流程和工作要求,可以提高工作效率和生产能力。
•增强员工责任感:员工安定化可以增加员工对企业的归属感和责任感,从而提升工作积极性和工作质量。
设备安定化设备安定化是指保证设备的稳定性和可靠性。
为实现设备安定化,企业需要进行设备维护和保养,并建立相应的维护计划和流程。
同时,还需要对设备进行定期检查和故障排除,确保设备能够正常运行。
设备安定化的好处包括:•减少设备故障率:通过设备的维护和保养,可以减少设备故障的发生率,降低生产线停机的时间。
•提高生产效率:设备的稳定性能够提高生产效率,减少生产中的等待时间和不良品率。
•降低生产成本:稳定的设备能够减少损耗和浪费,降低生产成本。
工艺安定化工艺安定化是指保证生产工艺的稳定性和一致性。
实现工艺安定化需要建立标准工艺流程和工艺控制点,并进行监测和调整。
同时,还需要培训员工,使其掌握正确的操作方法和工艺要求。
工艺安定化的好处包括:•稳定的产品质量:工艺的稳定性能够确保产品具有一致的质量水平,降低不良品率。
•提高生产效率:稳定的工艺可以减少等待时间和生产中的浪费,提高生产效率和产能。
•更好的产品一致性:稳定的工艺能够保证产品的一致性,满足客户需求,提高客户满意度。
精益生产实务安定化生产
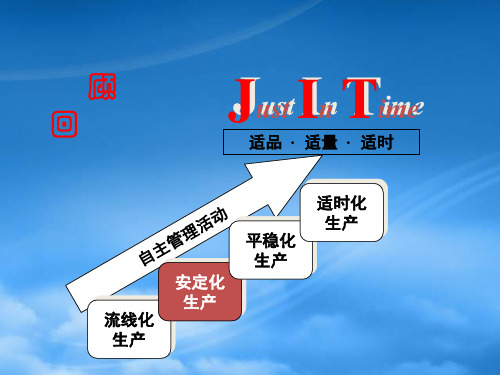
通过机械化和工序改善, 减少操作者体力消耗。 通过多工序作业,减少操作人员。
省力化+省人化+消除动作浪费, 用最少的人仅生产市场需要的数量。
劳动生产效率=
例
上月:需求 1000台/日 本月:需求 800台/日
工序 10个
工序 10个
人员 10人
人员 8个
问题点:1个工序1个操作者,减员不可能
着眼点:抛弃单一工序操作、定岗定员观念 实行多岗位操作、非定员制观念
— 业绩辅导——建立伙伴关系的有效途径 —
业务教导
(O)了解部下 (一)学习准备 (二)工作传授 (三)试做 (四)检验
(一)学习准备
1、使他平心静气 2、告诉他将做何种工作 3、掌握他对该项工作的了解程度 4、创造使之乐园学习的气氛 5、使他进入正确的位置
— 业绩辅导——建立伙伴关系的有效途径 —
表扬、巩固员工行为
例:某员工销售额上升
Step1 指出其业绩大幅上升 % Step2 询问员工通过什么方式使销售额上升
(让员工有表达成绩、感受成就的机会) Step3 征求员工意见,
听取其成功之道 Step4 探讨将来怎么办
— 业绩辅导——建立伙伴关系的有效途径 —
业绩面谈
(一)面谈前准备
主管:1、员工做得如何; 2、是否达到当初目标; 3、回顾工作,如参加的培训; 4、初步业绩评估; 5、员工可能出现的分歧; 6、考虑员工发展。
考虑工序作业性质及质量要求,设计容 器的标准容量、尺寸大小和形状。
设计“水蜘蛛”作业用的台车车型,并 相应考虑仓库的物品配置。
确定“水蜘蛛”作业场所、准备货架及 仓库。原则上作业场所尽可能靠近相关工序, 货架分上下两层,做到不用弯腰即可作业。
第八章 安定化生产 机械的安定

阶段四:总体点检 • 总体点检是要操作者学习自行发觉不良部
位.以及具有设备的基本知识.在完成前述三 个阶段之后.就可以学习自己设备的机能.构 造.具体活动内容是要依据点检手册实施点 检技能教育.实施总体点检找出设备的缺陷 并加以复原.重点如下: .学习对自己设备的机能.构造彻底了解 .先作测验.再实际到设备是做点检 .新发现的不良部位要改正过来 .彻底进行实施目视管理
(四)事后保全
• 设备因故障而停止.或性能退化而必须停止
下来修理.就是事后保全.
五.自主保全 • 自主保全.故名思义就是自己使用的设备要
自以手护.是自己去做设备的日常点检.给油. 备品更换.异常的早期发现及精度的检查等 工作. • 全员生产保全市要依据每日与设备街处的 作业原来消除故障不良.所以设备的守护是 作业员工作的一部份. • 自主保全可分为七个阶段来进行.每一个阶 段要确实做好.主管要每一个阶段亲自诊断 确认.合格之后才能往下一个阶段进行.
第八章 第二招式---安定 化生产 机器的安定
一.不要为设备而生产
• NPS的观念中特别强调不过量生产.不过早
生产.不生产库存品.生产数量要以下订单的 量来做.所以NPS的稼动率.是以市场的需要 量除以机器设备在没有故障.调整.换模.换刀 具等损失时间的最大负荷时间的产量而得 • 可动率要百分之百.而稼动率就不一定要百 分之百
二.可动率最重要 • 可动率是以减少机器设备的损失时间来达
成的.要提高可动率之前.首先要认识一般造 成机械设备损失时间的现象.分为六大类 (一)故障的损失 a.突发性:一但发生能立即知晓的故障 b.慢性故障:由于发生频繁.使维修人员修 不胜修最后弃之不管 (二)换模调整的损失 (三)瞬间停机的损失
培训课件精益生产安定化生产
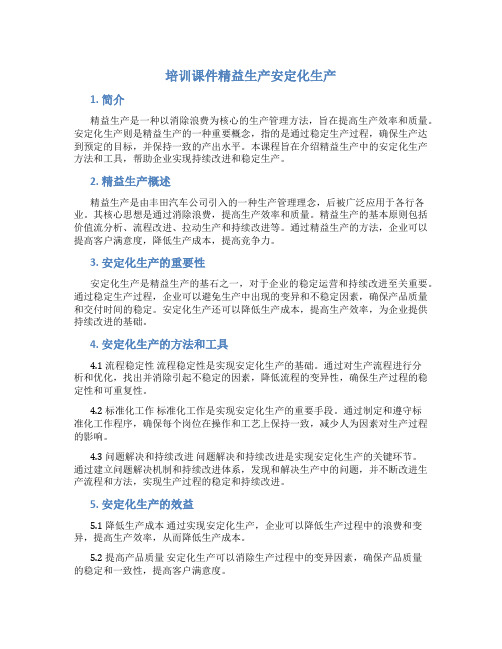
培训课件精益生产安定化生产1. 简介精益生产是一种以消除浪费为核心的生产管理方法,旨在提高生产效率和质量。
安定化生产则是精益生产的一种重要概念,指的是通过稳定生产过程,确保生产达到预定的目标,并保持一致的产出水平。
本课程旨在介绍精益生产中的安定化生产方法和工具,帮助企业实现持续改进和稳定生产。
2. 精益生产概述精益生产是由丰田汽车公司引入的一种生产管理理念,后被广泛应用于各行各业。
其核心思想是通过消除浪费,提高生产效率和质量。
精益生产的基本原则包括价值流分析、流程改进、拉动生产和持续改进等。
通过精益生产的方法,企业可以提高客户满意度,降低生产成本,提高竞争力。
3. 安定化生产的重要性安定化生产是精益生产的基石之一,对于企业的稳定运营和持续改进至关重要。
通过稳定生产过程,企业可以避免生产中出现的变异和不稳定因素,确保产品质量和交付时间的稳定。
安定化生产还可以降低生产成本,提高生产效率,为企业提供持续改进的基础。
4. 安定化生产的方法和工具4.1 流程稳定性流程稳定性是实现安定化生产的基础。
通过对生产流程进行分析和优化,找出并消除引起不稳定的因素,降低流程的变异性,确保生产过程的稳定性和可重复性。
4.2 标准化工作标准化工作是实现安定化生产的重要手段。
通过制定和遵守标准化工作程序,确保每个岗位在操作和工艺上保持一致,减少人为因素对生产过程的影响。
4.3 问题解决和持续改进问题解决和持续改进是实现安定化生产的关键环节。
通过建立问题解决机制和持续改进体系,发现和解决生产中的问题,并不断改进生产流程和方法,实现生产过程的稳定和持续改进。
5. 安定化生产的效益5.1 降低生产成本通过实现安定化生产,企业可以降低生产过程中的浪费和变异,提高生产效率,从而降低生产成本。
5.2 提高产品质量安定化生产可以消除生产过程中的变异因素,确保产品质量的稳定和一致性,提高客户满意度。
5.3 提高交付效率通过稳定生产过程,减少生产中的延误和不确定性,加快产品交付时间,提高交付效率。
之四安定化生产

之四安定化生产安定化生产是指为了提高产品质量和稳定性,采取一系列控制措施来确保生产过程的可靠性和稳定性。
在各行各业中,安定化生产都是至关重要的,特别是在制造业和化工业领域,因为产品的质量和稳定性对企业的长期发展至关重要。
在本文中,我们将讨论安定化生产的重要性、实施安定化生产的步骤以及在实践中可能遇到的挑战。
同时,我们还将探讨一些常见的安定化生产措施,以帮助企业提高产品质量和生产效率。
1. 安定化生产的重要性安定化生产是确保产品质量和生产过程稳定性的关键手段。
通过采取适当的控制措施,可以降低产品变异性,提高产品合格率,减少不良产品的产生。
这不仅有助于提高企业的声誉和竞争力,还可以降低成本,提高生产效率。
在制造业和化工行业中,安定化生产更是必不可少的。
这些行业生产的产品往往需要满足严格的质量标准和要求。
任何质量问题都可能导致产品不合格,进而影响企业的声誉和市场地位。
因此,实施安定化生产是确保产品质量和企业可持续发展的关键。
2. 实施安定化生产的步骤要实施安定化生产,企业需要采取一系列步骤并制定相应的计划。
以下是实施安定化生产的关键步骤:2.1 设定指标和目标首先,企业需要明确产品质量指标和生产目标。
这些指标可以是产品尺寸、强度、重量、外观等方面的要求。
对于化工行业,还可能包括化学成分和纯度等要求。
设定明确的指标和目标是实施安定化生产的基础。
2.2 建立可靠的生产工艺在设定指标和目标后,企业需要建立可靠的生产工艺。
这包括确定生产工艺的每个步骤和操作要点,确保每个步骤都能够稳定地进行。
同时,还需要建立相应的检测和监控体系,以确保生产过程的可控性和稳定性。
2.3 制定标准作业程序标准作业程序是确保生产过程稳定性的重要工具。
通过确定每个步骤的操作方法、工艺参数和品质要求,可以使操作人员按照统一的标准进行工作,减少不确定性和操作错误。
标准作业程序应该包括所有操作步骤、注意事项和质量控制要求。
2.4 建立质量管理体系质量管理体系是实施安定化生产的一个重要组成部分。
安定化生产—人员安定化管理

安定化生产—人员安定化管理1. 引言在现代企业管理中,人员安定化管理是一项极为重要的工作。
通过保障员工的工作稳定和满足其个人需求,可以有效提高员工的工作积极性和生产效率,从而实现企业的可持续发展。
本文将详细介绍人员安定化管理的概念、目的和关键措施,帮助企业管理者理解人员安定化管理的重要性并掌握有效的实施方法。
2. 人员安定化管理的概念人员安定化管理是指企业通过一系列措施,以满足员工的需求、提高员工的工作积极性和减少员工的流动率,从而保持生产稳定并提高生产效率的管理方法。
其核心理念是将员工视为企业最重要的资源,关注员工的职业发展、薪酬福利、工作环境和人际关系等方面的需求,回报员工的贡献和忠诚。
3. 人员安定化管理的目的人员安定化管理的主要目的是实现生产的安定和提高生产效率。
通过保障员工的工作稳定和满足其个人需求,可以达到以下几个具体目标:3.1 提高员工满意度和忠诚度通过合理的薪酬福利、培训发展和良好的工作环境,使员工感到对企业的归属感和认同感,从而增加员工的工作满意度和忠诚度。
满意度和忠诚度高的员工更加愿意为企业付出额外努力,并能在脱离群体的情况下保持稳定的工作状态。
3.2 减少员工流动率人员流动会给企业带来高额的成本和管理压力。
通过提供良好的发展机会、工作环境和工作待遇,吸引员工留在企业,减少员工的流动率。
稳定的员工团队能够形成默契配合和良好的工作氛围,提高生产效率。
3.3 提高生产效率和品质稳定的员工团队能够积累丰富的经验,提高各项工作的效率和品质。
员工的稳定性和熟练度能够减少生产中的错误和失误,提高工作效率和产品质量。
4. 人员安定化管理的关键措施为了实现人员安定化管理的目标,企业可以采取以下关键措施:4.1 提供良好的薪酬福利合理的薪酬体系和福利待遇是留住员工的重要因素之一。
企业应该根据员工的能力和贡献合理制定薪酬结构,并提供有吸引力的福利待遇,如健康保险、带薪假期和提供员工发展的培训机会。
JIT精益生产之安定化生产
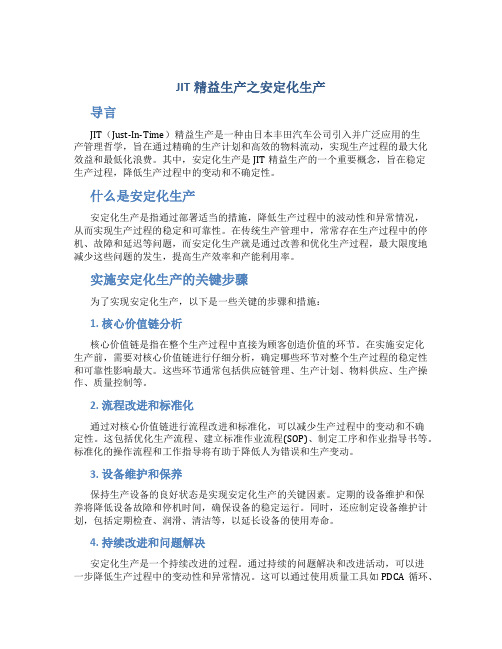
JIT精益生产之安定化生产导言JIT(Just-In-Time)精益生产是一种由日本丰田汽车公司引入并广泛应用的生产管理哲学,旨在通过精确的生产计划和高效的物料流动,实现生产过程的最大化效益和最低化浪费。
其中,安定化生产是JIT精益生产的一个重要概念,旨在稳定生产过程,降低生产过程中的变动和不确定性。
什么是安定化生产安定化生产是指通过部署适当的措施,降低生产过程中的波动性和异常情况,从而实现生产过程的稳定和可靠性。
在传统生产管理中,常常存在生产过程中的停机、故障和延迟等问题,而安定化生产就是通过改善和优化生产过程,最大限度地减少这些问题的发生,提高生产效率和产能利用率。
实施安定化生产的关键步骤为了实现安定化生产,以下是一些关键的步骤和措施:1. 核心价值链分析核心价值链是指在整个生产过程中直接为顾客创造价值的环节。
在实施安定化生产前,需要对核心价值链进行仔细分析,确定哪些环节对整个生产过程的稳定性和可靠性影响最大。
这些环节通常包括供应链管理、生产计划、物料供应、生产操作、质量控制等。
2. 流程改进和标准化通过对核心价值链进行流程改进和标准化,可以减少生产过程中的变动和不确定性。
这包括优化生产流程、建立标准作业流程(SOP)、制定工序和作业指导书等。
标准化的操作流程和工作指导将有助于降低人为错误和生产变动。
3. 设备维护和保养保持生产设备的良好状态是实现安定化生产的关键因素。
定期的设备维护和保养将降低设备故障和停机时间,确保设备的稳定运行。
同时,还应制定设备维护计划,包括定期检查、润滑、清洁等,以延长设备的使用寿命。
4. 持续改进和问题解决安定化生产是一个持续改进的过程。
通过持续的问题解决和改进活动,可以进一步降低生产过程中的变动性和异常情况。
这可以通过使用质量工具如PDCA循环、5W2H等来识别和解决问题,以及通过员工培训和意识提升来增加生产过程的稳定性。
安定化生产的优势和益处实施安定化生产可以带来许多优势和益处:1.提高生产效率:通过减少停机、故障和延迟等问题,提高生产过程的稳定性和可靠性,进而提高生产效率和产能利用率。
第九章 安定化生产 品质的安定
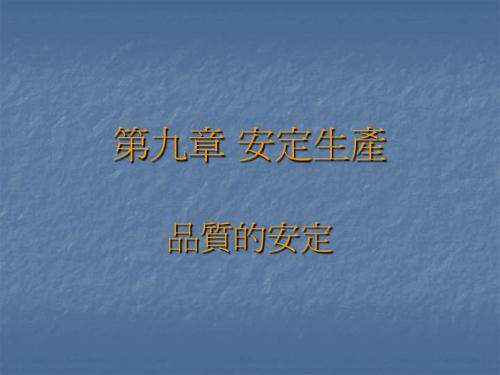
第九章 安定生產
品質的安定
一.追求零不良
企業的品質目標就是零不良. 80%的不良.皆屬於管理上的問題所造成. 以源流管理的方式來達成零不良的目標.
二.品質的三不政策
(一)不製造不良品:針對材料.設備不佳因素. 事先防止或改善.以及找出避免作業人員疏 忽的方法.才能達到零不良的境界. (二)不流出不良品:製造者必須要自主全數 檢查.既自主檢查. (三)不接受不良品:要建立「不良品是誰製 造出來的.就必須由其自己修正」的觀念.
(八)N=2的檢查原則. (九)防錯裝置的原則. (十)檢查的任務原則. (十一)沒有抱怨的原則. (十二)單件流動的原則. (十三)目視管理的原則. (十四)任務明確的原則.
五.零不良源流管理的戰術
戰術一:生產平均化.平準化… 戰術二:標準作業…. 戰術三:自己檢查…. 戰術四:全數檢查…. 戰術五:防錯裝置…. 戰術六:自働化….
三.不良有三種
企業經營的致命傷就是不良太多.品質不佳. 甚麼才是不良呢.簡單的說.不良就是指不符 合要求.可分為三大類…. (一)消費者的不良… (二)管理的不良…… (三)製程的不良……
四.零不良的原則
源自(一)全數檢查的原則. (二)在製程內檢查的原則. (三)責任的原則. (四)現行犯逮捕的原則. (五)徹底實施標準作業的原則. (六)殊途同歸的原則. (七)停線的原則.
精益生产实务安定化生产

精益生产实务安定化生产引言随着市场竞争的不断加剧,企业追求卓越的生产效率和质量管理已成为一项重要的竞争策略。
精益生产作为一种管理理念和方法论,通过优化生产流程和消除浪费,实现了生产效率和质量的双提升。
然而,精益生产的应用并非一蹴而就,需要持续改进和不断调整,以确保生产的安定性。
本文将探讨精益生产实务中如何实现安定化生产的方法和策略。
精益生产概述精益生产,又称为精益制造或精确制造,是日本企业丰田汽车公司首次提出的一种管理理念和方法论。
其核心目标是通过优化价值流程和消除各种浪费,实现生产效率和质量的提升。
精益生产的核心原则包括价值流映射、流程平衡、拉动生产、持续改进等,旨在实现客户价值最大化。
安定化生产的重要性在实施精益生产的过程中,安定化生产是一个关键的环节。
安定化生产指的是通过有效的管理和控制,使生产流程达到稳定的状态,以确保产品质量和生产效率的稳定性。
安定化生产的重要性包括以下几个方面:1.提高生产效率:安定的生产流程能够减少因生产中断和故障引起的停机时间,提高生产效率和产能利用率。
2.降低生产成本:稳定的生产流程能够减少废品和次品率,降低生产成本。
3.提高产品质量:稳定的生产流程有利于发现和解决质量问题,提高产品质量。
4.提高员工满意度:稳定的生产流程能够提高员工工作的稳定性和积极性,增加员工的满意度。
实现安定化生产的方法和策略1. 制定清晰的生产计划和排程制定清晰的生产计划和排程是实现安定化生产的基础。
生产计划应该根据市场需求和生产能力确定合理的生产批次和周期。
排程要考虑原材料供应、生产线平衡和工序间的协调,确保生产流程的稳定性。
2. 优化物料管理物料管理是实现安定化生产的关键环节。
通过建立供应链合作伙伴关系,确保原材料供应的稳定性和及时性。
同时,要采用合理的物料管理方法,如:先进先出(FIFO)原则、定期盘点等,避免物料过期、短缺或堆积的情况。
3. 建立稳定的生产流程稳定的生产流程是实现安定化生产的基础。
第七章第二式安定化生产人员的安定

第七章:第二招式—安定化生产:人员的安定7.1流线化生产线为改善活动之始NPS实施的第二个技法,就是安定化的生产方式,前文中所介绍的将传统的批量生产方式及水平布置,改变为单件流线的生产方式,严格来说,还不上是改善的活动.只是修正的活动.因为,我们只是将旧的生产线,重新再作安排.将物流批量变少,以及人员配置的观念修正过来而已,而对影响整个生产活动的人员动作品质,机器设备的可动率,产品的品质保证等等尚未具体加以改善.如果认为只要将传统的生产线转变为流线生产线后,就是整个改善活动的结束,那苦头就马上会跟着来临.其实,将传统的生产方式改为流线化生产线只是改善活动的开始,为什么呢?我们不妨结合一般生产现场常见的现象加以说明.首先,就机器设备来说,机器会有故障,故障一旦发生,生产活动当然必须跟着停下来,在传统生产方式的观念里,都是以在制品库存的方式,来减少对后制程的影响.维修的人员可以慢慢地修理.短则数十分钟,长则数小时甚至数天.然而,在流线化的生产方式里,机器设备改为依制程顺序衔接在一起,中间的在制品只有一个故障,整条生产线必然跟着全部停下来,设备连接越多,整条生产线停线的机会也越多,停线时间越长,这种状况如果不加以改善,很可能整条生产,线一天将做不到几个小时,许多人也就因为顾虑到这种问题,而认为无法实施流线化的生产,但这是失败者的想法,因为他是以在制品库存的方式来隐藏机器设备故障率的问题.表面上看挺合理.停机期间用库存在制品维持后续制程的生产,而实际上的代价却是故障率的居高不下,NPS的观念就是要以降低库存量的方式,将潜在的问题暴露出来,促使问题暴露,就必然要全心来降低设备的故障率.其次,就是人员的动作品质,人的工作是很有弹性的,不像机器设备仅能固定做某一种动作.但是,人的动作时间不稳定,时长时短,不像机器那样固定,这种不稳定,除了人与人之间的熟练度差异之外,同一个作业员,每一次作业时间也不会完全一样.造成这种不稳定的原因及改善的方法,将在后文中谈到,人员作业时间不稳定也会影响整个生产流线生产的安定性.只要其中一个作业员不能在生产的周期时间内完成其工作,整条生产线也会踊着停下来.第三,不良品的发生也会影响流线生产线的安定.生产线中,一旦发生不良品而且继续流到下一制程,去则下一个制程,也就无法继续加工下去,必须做换模或换线的动作,如果这些动作的时间过长,则在制品库存也要增加,而且也要使整条生产线停下来.总而然之,流线生产线建立之后,并非整条生产线就自然而然地会稳定地生产下去,相反却会暴露出更多潜在的问题点,,需要继续改善.而改善的主要目的就是要使生产线安定下来.如何使生产线安定下来,将在后文中,依照下列的顺序来介绍:(1)人员的安定;(2)机器的安定;(3)品质的安定;(4)物量的安定;(5)管理的安定.7.2人员安定取决于”标准作业”安定化生产的第一个需要安定的内容就是作业人员的工作的安定化,人员安定的主要目的,除了使生产线的速度稳定下来之外,还可以减少作业人员.NPS 以”标准作业”的方法来达到上述两上目的.“标准作业”的意义,在NPS的领域内,有不同的含义存在,一般工厂谈到标准作业,马上就联想到生产线上的每一个制程或每一部机器的操作顺序说明书,这种说明在NPS内,称之为作业标准指导书,还不能视作”标准作业”.NPS所谈到的标准作业涵盖的范围较为广泛,是包含整条生产线机器设备的布置,制程加工的顺序,物流的过程,标准在制品的设定,作业人员的配置,作业人员的动动等.以具体内容来说它包含了”标准作业票””标准作业组合票”,”产品加工能力表”,”作业指导书”,以及”作业要领书”等文件,这些文件表格的说明,将在往后介绍.流线化生产线的是否稳定,首先,要观察生产线是否在做”标准作业”.有没有在做”标准作业”主要不是看生产线有没有做上述表格,而是要看现场作业人员的\操作是否有规律及重复性.所以,”标准作业”又称为”规律作业”.生产线上的人员要安定下来,首先要做的就是要区别出””标准作业”与”非标准作业”.”非标准作业”顾名思义就是与”标准作业”相反,也就是没有规律性,没有重复性的作业,例如说,在装配线中,零部件突然用完了,作业员必须去补充,这个补充的动作发生的频率就没有规律,视每次放置的数量而异,其动作是不确定的,只是随机变动,任何一台机器做完了就立即去处理,没有重复性可言,这些动作,都称为”非标准\作业”.生产不稳定的主要原因就是没有将作业人员的作业动作中的”标准作业”与”非标准作业”区分出来,让一个作业人员同时负责这两种作业,作业人员如果一直都做”标准作业”的动作,生产当然稳定,可是,如果作业员同时必须做”非标准作业”,生产的动作就会被迫停顿下来,整条生产线当然也会受到影响而停下来.因此,人员的安定首先就是要分离”标准作业”与”非标准作业”,并且各指定专人负责,一般是以线上的作业人员来担任”标准作业”,另外准备一个人,专门在线外负责”非标准作业”的工作内容,这一个在线外专门负责”非标准作业”的人员称为”水蜘蛛”,就是指这个人的动作必须像在池塘中、浮在水面上游走的水蜘蛛一样地迅速、灵活.重要的是原来分散在线内作业人员身上的”非标准作业”,全部集中在一个”水蜘蛛”的身上,就形成了”水蜘蛛”的标准作业,从而使得整个生产线所有的作业人员都是在做”标准作业”,自然而然整个生产线就安定下来了.7.3产距时间--宛若指挥棒的节拍NPS的标准作业强调的是,要使生产现场的作业规律化,达到生产活动的稳定.所以,标准作业也是现场生产效率改善及主管管理的依据,因此可以说没有标准作业就没有改善.所有的改善都是从标准作业开始的.前文也谈到,NPS的标准作业,与一般公司使用的操作程序书等以个别制程为说明对象的标准化文件是不同的.后者在NPS的体系内,称之为作业标准.标准作业是为了将作业人员、制程设备的布置及物流过程等问题作最适当的组合,以有效地达成生产目标,而设立的标准化文件,标准作业的应用,可以说是NPS的一大特征.标准作业的制定是生产线上现场主管的职责,这与一般由办公室文秘人员起草的文件是不同的,标准作业是现场管理者自行制定,用来作为指导作业人员用的.由于是自己制定.因而执行标准作业的积极性也较高,同时也随时准备根据市场情况的变化对它进行改进,因为,NPS的标准作业,并不是一成不变的,而是必须依照市场需要量的,变化,经常作改变及改善,来达成目标.标准作业的设立要先掌握三个要素:产距时间、作业顺序、标准手持品,缺一不可.标准作业的第一个要素----产距时间,是一般和平理念中所没有的.产距时间的定义,是以市场一天或一个月有确定订单的需要数,除了作业人员一天或一个月的有效工作数而得.所谓有效工作时数是指作业员上班一天的时间扣除每天班胶会休息.,吃饭及打扫现场时间后的实际工作时数,举例来说,从上午8点上班到下午5点下班,上班时间共为9小时,若每天班前会5分钟,上午休息一次10分钟,中午午餐30分钟,下午休息10分钟,最后打扫5分钟,那么一天的有效工时就是8小时,又假设现在市场每天的需要量是1000台,每台为28.8秒,也就是,生产线应当要每隔28.8秒生产一台结束之后就可以达到市场的需要量了.产距时间从定义上来看,完全受到市场需要量及有效工时变化的影响,是一种目标时间,也是人为制定的,假设现在每需求量降为500台,那么产距时间就变为每57.6秒生产一台产`品,由此呆见,产距时间与工厂内现场实际的产出周期时间及有多大生产能力,多少作业人数一点关联都没有.一般人很[容易将产距时间与实际的生产周期时间混为一谈,这是错误的.聪明的读者,若能明了产距时间的定义,也就可以了解产距时间的重要性.NPS的理念就是不过量生产,在不建立库存.许多人都能够明了这个理念,但是,在生产现场实际操作,到底该如何做才能达到这个要求呢?关键就在于产距时间,因为产距时间就是以市场有订单能够卖得出去的量计算出来的,因此,现场里每一个生产单位,都必须依照此产距时间来安排生产,不可有生产越多越好的观念.否则,整个工厂的生产步调就全部乱了,在制品库存大,以及搬运,等待种种浪费也会因此而生.产距时间就像是交响乐团指挥的指挥棒节拍一样,整个乐团的乐手都必须依照指挥的节拍演奏,才能奏出完美的曲子.如果各奏各的调子,那不是变成的曲子.如果各奏各的调子,那不是变是噪音了吗?所以,生产现场也是要按产距时间来组织,才能达到完美的程度.7.4”标准作业”的其它两大要素-------------作业顺序,标准手持品标准作业的第二个要素是作业顺序,所谓作业顺序是指产品在生产加工中,从材料开始到成品为止依次变化的过程,包括加工物品的传送,机械的上料,下料,及作业员作业顺序的时间流向.作业员的作业顺序,不是物流的顺序,作业员的动作顺序在标准作业中有重要的意义,假若,作业员的作业动作不明确的话,各人依据各自的喜好顺序工作,就会破坏整个生产线操作的规律性.而成为没有标准的作业,而且,作业员若不遵守作业顺序的话,也会产生种种的弊病.例如:误把未加工完毕的物传入后制程因而导致机械损坏或装配线停线等等.在设定作业顺序时,也要具体地考虑工作分配是否合理,是否均衡,以及作业量再分配的可行性,双手的使用方式,双脚的站立位置等,如此一一适当地作出明确规定之后,作业,员就能安全地,有效地,有自信的地依照这样的作业\顺序生产出良好的产品.标准作业的第三个要素素是标准手持品,标准手持品是指为了使生产活动能够重复地持续下去,而必须的生产制程内的在制品,正在机械内加工物`品,也是属于标准手持品的一部分,生产线上若缺少一标准手待品的话,生产就会中断,形成停线.标准手持品虽然是必须的在制品,但也要设法降低,标准手持品的数量与机械配置的方法及作业作业顺序有密切的关联,一般来说,作业员的作业顺序动线若与机械加工物流的顺序同向的话,制程间就必须要有一个手持品,若逆向的话,则制程间的手持品就不需要了.除了这种顺序的关联外,有时为了品质检查的必要,也必须设立一定数量的手持品,必须等待温度下降到某一个程度,或者必须等待干燥几分钟后,才能传送到下一个制程继续加工的产品,也必须设立标准手持品.标准作业一般是以”标准作业票”、”标准作业组合票”及”产品加工能力表”、”作业标准指导书”、”作业要领书”等表现出来,.常用的是前三者,此三者也是一般生产理念所没有的,在此略作介绍.后两者是常见的文件因此不再表述.“标准作业票”包含整个生产线机器配置、加工物流的顺序,作业人员作业顺序的规定及人员配置,标准手持品的旋转位置及数量,品质检查,安全注意事项以及产距时间等内容,而非单纯的机械布置图而已.“标准作业组合票”主要用来观察,分析,记录一个作业员的作业顺序过程,.所以,必须依照该作业顺序记录,并记上作业内容,作业时间及产距时间等内容.从作业组合票可以看出作业员的作业时间是很合理,如果所分配作业量的组合时间刚好等于产距时间,那就是理想的,如果大于产距时间,就表示无法生产出必要的数量,必须以加班的方式来完成.如果少于产距时间,就表示会生产过量或者有等待现象发生,不管太长或太短都需加以改善.“产品加工能力”主要是按不同产品分析,掌握每一制程的生产能力,要分析出人的时间,机械的时间,换模,换线的时间,以及设备的可动时间.设备的生产能力若无法达到目标能力,首先必须设法减少换模,换线时间,以及提高可动率,最后,再考虑改善人的动作品质及机械的动作品质,以突破瓶颈.7.5由”水蜘蛛”来做”非标准作业”标准作业明重复性,规律性的作业,无庸讳言,生产现场一定还会存在一些偶发性没有规律性的事情,这些事情就统称为”非标准作业”.为了使生产线安定下来,同一个作业员不可以同时从事”标准作业”与”非标准作业”.而必须将两者分离开来,让作业员专心从事”标准作业”这个人就称为”水蜘蛛”.精确地说,”水蜘蛛”的工作就是要将这些”非标准作业”变成他的”标准作业”,以超多回供料且在复数的生产线中,以每次供应一套均衡供料的方式来保证生产线的持续作业.实行”水蜘蛛”供料的主要目的是要让生产线的管理者通过供料与产距时间的差异,发现生产线上的问题点,以便迅速,顺利地进行改善,而不是指搬运的合理化.在”水蜘蛛”的作业用下生产得到了巨大的改善.首先是使生产联机操作员的动作品质提高,不但作业时间缩短,而且速度也稳定,使生产线可持续进行作业,不会因为偶然事情干扰,不稳定而造成停线.其次,水蜘蛛以成套的方式供应物料,可以消除拿取零件的选择动作,使作业员仅需拿取零件,即可装置于工作物上,作业员就可以从”装配工”变成”装置工”,有助于多能工化及新人的训练,,以成套的方式\装置可以避免误装或漏装零件的错误,减少不良品,此外,生产线的生产迟误或超前,也都可以立即知道,因此,”水蜘蛛”的供料速度是要配合生产线的产距时间进行的,若两者顺序不配合就表示有问题产生.最后,作业员如作业动作较快,应付有等待的现象出现,也能立即反映出来.要做到”水蜘蛛”方式供料,可依下列的步骤来准备:步骤一确定实施”水蜘蛛”供料的产品及制程,要求做到按产距时间准备一套,供应一套的均衡供料方式为改进的目标,并且做出检料单.步骤二所需的容器大小,形状,以及标准容量的设计要考虑到制程的作业性质及品质要求.步骤三设计使用的车型和仓库的物品配列,使”水蜘蛛”容易检取.步骤四确定场所,准备棚架及仓库.原则上选定的场所,应尽可能靠近对象制程的地方,棚架分为上下两层,做到不用弯腰,只需肩膀倾下即可检料为佳.步骤五确定在生产线旁的供料点,设置供料台.物料从台台上移动至供应台应方便容易,便于作业拿取,原则上,每次只供一台.步骤六设计并制作”水蜘蛛”所需的检料台,台车要设计成手推式,具有前后左右自在转向的车轮,一部台车放置一套物品为佳,并且做到使”水蜘蛛”可一面推车,一面读取”检料单”,拿取物品及消去”检料单”上已完成项目的方便程度.步骤七确定”水蜘蛛”的人选.”水蜘蛛”不但动作要迅速,同时头脑也要清晰灵活,能够掌握生产线上的瞬息变化,懂得采取因应措施,所以,人选非常重要,一般都是由作为下一任的基层管理者的后备人选来担任”水蜘蛛”.7.6”少人化”有利于于人员的安定笔者在工厂现场指导NPS改善活动时,常碰到的一个问题就是:” 我们劳力不足,产量上不去. ” 但是,经过现场巡视后, 笔者所给出的答案都是”人太多了, 所以产量上不去. ” 咋听之下, 一般人都反应不过来, 以为我是在开玩笑. 其实不然, 主要的原应就是传统生产方式在搬运, 找寻, 取放的动作上浪费了太多人力.根据实极经验, 每一家传统式工厂, 在这一方面所浪费的人力, 至少有30%以上. 另外1一点, 就是对“ 少人化“的认知不足, 当然也就不知该如何做到“ 少人化“了当然, 所说的“人太多所以产量上不去“ , 是有所指的, 那是指劳动生产率太低. 劳动生产率的定义是指一个工人平均一天的生产量, 或是类似的表示方法. 在数学上的表现方式就是分子是每天的总生产数量, 分母是生产纤上的人员总数. 工厂要进步, 要能持续支付员工的薪资, 要能永久生产下去, 生产率的提高是一个必须持续追求的目标.在以往物资缺乏, 生产什幺都能卖得出去的“ 卖方市场“ 时代, 只要将生产量尽量做得多和快, 就是提高生产率的最佳方法. 作业的方式也刻意地细分化, 机械式地重复做一小项工作内容, 以提高作业员的熟练程度, 进任而提高产量. 作业人员的配置也十分固定, 这就是“ 大量生产“ 的时代.而现在同样的物品大家都需求的时代已经过去了, 取而代之的是多品种, 少数量, 短交货期的时代的到来, 也就是消费市场导向的时代. 在市场导向的时代, 生产的数量完全要由市场的需求来决定, 换句话说, 生产的数量不能再像以往一样漫无止境地越多越好, 而是受市场订货的限制.在条件生单数量有限制的条件下, 生产率的提升就必须以减少分母上的人数来获得---------- 一般人所想到的减少人数的方法, 大都是斥资机械化或自动化, 这种花大钱的自动化或机械化, 并不是最好的方式, 有时还可能增加了太多的产量, 超出了市场的需要量.少人化是指要以顾客的需要量, 用最少的人数, 最经济的成本来生产产品. 举例来说, 莫产品有10个制程配置10个人成产1000台, 理论上来说, 仅须安排8个人生产就足够了. 但是, 实际生产中作业细分的结果导致每个制程都需1个人来生产, 要减掉2个人, 就变成没有可能了.为了实现对应于生产量的少人化, 必须要拋弃单一制程操作, 非定员制的配置方法. 即必须先拋弃大量的生产时代的“固定观念“省力化及省人化是区于少人化的另外两个概念. 三者的意义是不同的, 顺便作一些说明.省力化只是减少了人的体力, 但是人数仍然没有减少. 比方说, 鉆床原先要人操作鉆孔, 現在改為人僅須上, 下料, 機器可以自動進刀. 這就減少了人的體力, 但是作業員仍然沒有省掉.省人化只是減少了人員,但是浪費的動作並沒有消除掉,比方說,上述的鑽床,可以變成一個人操作兩臺機器,就是利用第一部機器加工的時間,去做第二部的上、下料動作,可以減少一個人,但是,整個機械動作及人員動作的浪費並沒有消除掉.而少人化是要消除掉動作的浪費,用最少的作業人員僅生產市場需要量.7.7生產流線化有助員工”多制程操作”NPS生產率提昇的觀念,是以減少分母的人數,為主要的出發點,此即少人化的意義所在,實施少人化的基礎條件,就是生產線要先流線化,然後使作業員能夠從事多項制程的工作,拋棄傳統的一個制程一個人操作的固定化觀念.在以往大量生產的時代,為追求高產量,所以就將作業徹底地細分化,例如擰螺絲的作業員,每天的工作就是固定在擰那幾個螺絲,貼標簽的作業員,每天就是在貼那幾個標籤,做鞋子工廠的某個工人,每天僅做右邊的鞋子,做了十年,可是有一天要他去做左邊的鞋子,卻不會做,類似這种機械式單純化的工作,連續做了五年,十年之后,每一個人都是重復在做同樣的工作,難道不會感到厭倦嗎?可是,套上一句流行的話:”人在江湖,身不由已”,為了一家的生活,雖然不滿意但也不得不做下去,可以說是失去了人性的尊嚴.相反地,如果過分尊重人性的尊嚴,讓每一位作業員都隨心所欲去做他喜歡的工作,按照他自己喜歡的模式去工作,不但生產率低落,同時又會增長個人主義的氣氛,破壞團隊合作的精神,使整個工廠的管理困難增加,從而使公司失去競爭力,走向倒閉之路.所以,提昇生產率和尊重人性的尊嚴,似乎是一個兩難的問題,難以同時滿足這兩方面的需求,然而,NPS多制程操作的方法,卻使這一難題得以解決.多制程操作,顧名思義就是一個作業人員能夠操作兩個以上的不同制程.實施多制程操作除了建立流線生產(U字型布置,廢止離島作業,專用型的小型設備,安全的作業環境)之外,尚須考慮下列各點:7.7.1離人化離人化就是將機器設備的”人的工作”及”機械的工作”分離開來,使作業人員在機器動作時,能夠離開機器設備,生產成本包含人的成本及機器設備的成本,如果機器在動作中,人員無法離開,那麼這一個制程的成本就必須包含人的成本及機器的成本.反之,在機器設備運作時,人員可以離開,那麼人的成本就可以節省下來.所以,機器設備必須設法能夠”離人化”7.7.2走動作業一般家電產品或電子產品的裝配作業,作業人員都是坐在輸送帶旁邊作業,這种坐姿方式長久下來,容易使足部功能退化,多制程操作要求一個作業員能夠操作多個制程,不能僅在一個固定的工作,而必須走動操作不同的制程,走動作業,其實也不是什麼新觀念,例如,家庭主婦每天在廚房做菜就是一种走動作業的方式.7.7.3多能工的培養如果生產線已經改成要求采用多制程操作了,但是作業員仍然只會一种制程的操作技能,那也無法實現多制程操作.所以,必須培養多能工.7.8”多能工”實施要點多能工就是一個作業員能夠操作兩种以上不同制程的作業技能,培養多能工的主要目的,不是為哪一天有人請假時,有替代的作業員可以使用,而是為了達到”少人化”、來提高生產率、並使生產而是為達到”少人化”來提高生產率,並使生產的物資流動順暢的目的.有些工廠作業人員雖然已經培養訓練成具有多項從事某一固定制程的工作.這种具備多能技能,但僅應用一种技能的情形,稱之為”復能工”.”復能工”並不能達到”少人化”的目的,也無法操作多制程作業,與”少人化”的多能工是有很大的差別的.工廠要培養多能工,必須注意以下各要點:7.8.1作業簡單制程中一定有些必須花費長時間才能學會的技能,特別是更換,調整的作業,像這种作業,對多能工的培養是一大阻礙.制程的操作應趨向於單純化,盡可能做到簡單易於掌握,機械設備也要徹底地標準化.7.8.2適當指導工廠內多能工化的推廣,各個制程主管干部的適當指導是不可或缺的條件,對生產整體每一制程的關鍵,最了解的人不是作業員,而是現場第一線的管理者,如班長,領班之類,多能工的培養是現場干部的重要工作事項之一.7.8.3標準作業對新手的培訓,應著重作業的順序及內容,而且要以書面的方式表現出來,使任何人一看都能充分明白.因此,有關標準作業的作業指導書及作業要領書要準備妥當.7.8.4整體推廣多能工的培養,如果僅在某一個單位內實施,有時會引起不平之鳴,為了避免這种困擾,最好整個工廠一起實施.由總經理或廠長先發佈通告,使全員知道公司的政策方針.此外,每天班前班後會時向作業員灌輸多能工的觀念.定期舉辦多能工競賽,並且表揚優秀的多能工及實施單位.7.8.5制定計劃多能工的培養不是一朝一夕就能完成的,必須要有耐心持續做下去,此外為了掌握實施的進度,實施計劃的制定也是很重要的.可以制定”多能工技能訓練計劃表”.”多能工技能統計表”等等,對個人及單位整體做定期的追蹤考核.7.8.6改良設備設備的改良應以容易操作,達到”離人化”程度、使作業員只做取放的動作。
安定化生产

什么是安定化生产
字体大小:大中小 2010-10-13 15:03:18 来源:智库百科
安定化生产是追求使生产线能够稳定生产。
流线化生产只能算是修正活动,真正改善活动应该从安定化生产开始。
安定化生产的内容
安定化生产包括:
1、人员的安定:
是通过标准作业使生产线的生产速度稳定下来并达到减少作业人员的效果,同时保持人员稳定,员工流动不会太频繁。
2、设备的安定:
现场经常出现在生产过程中因机器故障而浪费很多时间的情况,所以,我们需要使机器也安定运转,可动率达到100%,那么,这就需要全员生产保全了。
全员生产保全包括:预防保全:预防机器故障的发生;改良保全:把机器改良成为没有故障或容易保全的;保全预防:一开始即导入不需保全的设备设计;事后保全:一有故障发生马上修理。
3、品质的安定:
单件流追求的是零不良,执行品质“三不”政策(不制造不良品;不传递不良品;不接受不良品)只要做好“三不”政策,品质自然也就安定下来了。
4、物量的安定:
要求生产线上减少在制品,保持单件流并且做到无缝转款,使生产线保持平稳的状态,确保生产线货源充足不间断。
5、管理的安定:
单件流要对原有的传统观念进行改善,管理是一个重要的因素。
管理者首先应把意识观念理解好,以具备能洞察、发掘问题的能力,其次就是要借助如电子看板、警示灯、瓶颈工序灯等辅助工具将生产现场做成容易显现问题及生产活动能够透明化,使现场一有异常现象出现就能立即察觉并加以改善。
品质的安定

安定化生产:品质的安定1、追求零不良在新生产技术法的基本生产理念是依据客户的需要量,在必要的时候,仅生产必要数量的必要产品,能够这样做的话,就能彻底地将生产线存在的各种问题暴露出来,以达到消除浪费的目的。
为了达到这个目的,生产线安定化的第三个影响因素就是品质的安定,也就是对制造品质零不良的追求。
为什么要以零不良为追求的目标?企业的主要生产活动就是制造商品,由于生产的数量非常多,为了经济的原因或者某些条件的限制,自然就会认为不能全数检查。
所以,下意识就接受了“多少总有些不良品存在吧”这种错误的想法。
比方说,生产汽车的工厂每年生产数十万辆车,假设其中发现一台不良,以不良率来说只是十万分之一,或数百万分之一而已,品质可说是非常好了。
然而,具体到某一消费者来说,一生中或许就只买这一部恰好是不良的车子,那岂不是遗憾终生并会一辈子对这家公司留下恶劣的印象。
所以,对任何一个消费者来说,是不会接受任何一个不良品的。
此外,就制造工厂来说,任何一个不良品的发生,除了造成成本增加外,也会使整个生产计划及管理控制活动发生混乱,而衍生的问题及额外的成本负担更是难以细算。
所以,企业的品质目标就应该是零不良。
当然,许多人或许会认为品质零不良只是理想、口号而已,或者认为必须投入更多的检查人力或仪器设备才能达到。
然而,新生产技术法却认为它是可以实现的目标,而达成的方式是源流管理。
换句话说,要达到零不良的境界,必须改变传统的品质保证做法。
在制程中用传统的统计品质控制图,或抽样检查的做法是无法达到零不良境界的。
这样的说法,相信许多人会持相反的意见,或者说那么该如何做才能达到呢?为源流管理的方式是达成零不良的目标的有效途径。
开始一直认为数理统计品管(如控制图及抽样计划)是一种最经济而且又能保证品质的科学方法,然而,这些手法在实际操作中有其困难的地方,不是很难被普及使用就是有许多应用错误的地方。
最近几年来,在现场的改善实例中,有许多原先改善的对象并不是有关品质方面的,然而从最后的成果中却发现品质方面也跟着有显著提高的例子,于是再加以深入了解,才恍然大悟,原来品质不良的原因中生产流程安排不佳、管理上的问题以及管理者观念上错误所占的比例很大。
如何进行现场生产改善

四、超市化生产
也可叫作“后拉式”生产法。它是根据后单位的需求 进行补货,主要利用传票作为现场生产活动的工具。
通过各种改善活动消除隐藏在企业内的各种浪费。
而在改善活动中最大的问题就是人的观念难以改变,
只有改变人的观念之后,才能改变人的做法、物的做
法、机器的做法,才能获得成果 。
的动作浪费时间。
③清扫:就是指现场没有垃圾、保持干净的状态。 ④清洁:对上述3S彻底化、持续化。
⑤素养:就是让所有人对上述4S养成一种习惯。
三、平稳化生产
就是平坦稳定的生产。它的重点在于生产要有计划性,
它除了月计划、周计划、日计划外,重要的是要有平稳
生产计划即平均化和稳定化的生产计划形态,包括一日
如何进行生产现场改善
讲师:改传统的批量生产为流线化生 安定化生产平稳化生产
超市化生产
一、改传统的批量生产为流线化生产 流线化生产为改善活动之始,它建立的八个条件: 1、单件流动
2、按制程顺序布置设备
3、生成速度的同步化 4、多制程操作的作业
5、作业员的多能工化
6、边走边做的走动作业 7、机器设备的小型化
2.4 物量的安定
2.5 管理的安定 :人的管理、目视管理、5S
5S和全员生产保全是实现安定化的两大关键。5S是一套实现车间组织 化和标准化的系统,其目的在于支持目视管理。它包括:
①整理:清理出现场要与不要的物品,现场只能放置要的物品。不要的物品
要移出现场并加以处置。 ②整顿:就是将需要的物品放置到立即并容易取回的状态,以减少找寻物品
●预防保全:预防故障的发生 ●改良保全:没有故障,或改良成容易保全 ●保全预防:一开始就导入不需保全的设备设计 ●事后保全:一有故障发生,即刻修理
安定化生产(质量的安定)

安定化生产(质量的安定)安定化生产:质量的安定一、为什么以零不良为追求的目标呢?企业生产商品数量多经济考量或条件限制不可能全数检查「总有不良品存在吧」。
生产者的1/10000 比消费者的100/100 消费者的不满、不良印象立场为「不会接受任何一个不良品的」。
生产者任何一个不良品的发生成本上升生产计划加管制混乱衍生的问题加额外的成本负担难估计1/10000的问题疫苗。
零不良质量只是理想口号或需要投入更多人力仪器、设备认为是可以实现的目标达成方式「源流管理」。
「达到零不良中境界」改变传统。
传统用(品质管制制图),(抽样检验)那么应该怎么做?原先抱着不放一二十年的经验结果发现,原先的目的不是为品质,结果是品质受惠!原来品质不良都是生产流程安排不佳,管理上的问题,以及管理者观念上的错误所占的比例较大。
80%属于管理上面20%属于统计品管的应用问题,或者是技术层面上的问题。
二、质量的三不政策品质的问题追根究底首先=管理问题其次=技术问题,一般公司谈到「质量问题」很自然联想到从技术层面先下手,技术上面有突破……这些问题就应刃而解,技术层面——化费一段长时间「研究开发」则成败未知,缓不济急。
但是,从管理层面去寻求改善,不必用时间投资,而能够获得显著的改善。
只是谈到管理,我想会有很多人就退避三舍,为什么呢?因为管理必须与同事面对面地沟通,要做教育训练,以会容易引起反弹,所以常常令人却步。
这就是不敢管理,或者管理技巧不够,得下管理功夫。
当然一个公司管理方面做法较弱,任由员工个别去自我发挥,就很难产生「共识,力量不能整合发挥,当然不容易长久生存下去」。
人是会犯错的动物,会造成很多的失误,公司经营的基本主体是人,所以公司里也必定有误失的现象存在。
而误失发行就是造成「不良」的原始原因。
「性善说」,「性恶说」,可恶!「人总是会犯错,发生,正常现象,没大小」。
「犯错是件可恶的事,或许会犯,但减少,消除是可办到的,处理方式不一,自然会影响到整个品质水准」。
JIT精益生产实务四--安定化生产

前日内容复习 课程四 安定花生产 (三)质量安定化 课程四 安定花生产 (四)切换安定化
中餐
练习:空中耐力
课程四 安定化生产 (五)现场安定化 练习:空中蜕变
自由交流 培训总结、课程调查
JIT精益生产实务四--安定化生产
•CWMC 国慧顾问
4 •第 日
PPT文档演模板
9:00~ 9:10 9:10~11:10 11:10~12:00 12:00~13:30 13:30~14:30 14:30~15:00 15:00~16:00 16:00~16:40 16:40~17:10 17:10~17:30
•CWMC 国慧顾问
•1、标准作业
PPT文档演模板
•标准作业
•非标准作业
• 有规律的重复 性作业,如:组装工 序的螺栓紧固。
• 没有规律的非 重复性作业,如:补 充螺栓。
• 如果操作者在作业中同时需要进行 标准作业和非标准作业,必然造成生产动 作的停顿,从而使生产不稳定。
JIT精益生产实务四--安定化生产
课程四 安定化生产 (二)设备安定化 练习:中国一号
自由交流 培训总结、课程调查
JIT精益生产实务四--安定化生产
•CWMC 国慧顾问
3 •第 日
PPT文档演模板
9:00~ 9:10 9:10~10:40
10:40~12:00
12:00~13:30 13:30~14:10 14:10~16:10
16:10~16:40 16:40~17:10 17:10~17:30
• 有时为了质量检查或下工序加工条件的需要,也必 须设定一定数量的在制品。 • 如:降温或干燥之后进行下工序加工等。
PPT文档演模板
JIT精益生产实务四--安定化生产
- 1、下载文档前请自行甄别文档内容的完整性,平台不提供额外的编辑、内容补充、找答案等附加服务。
- 2、"仅部分预览"的文档,不可在线预览部分如存在完整性等问题,可反馈申请退款(可完整预览的文档不适用该条件!)。
- 3、如文档侵犯您的权益,请联系客服反馈,我们会尽快为您处理(人工客服工作时间:9:00-18:30)。
5
8.N=2的檢查原則:制程中若以自動機器批量為生產方式,則每一批的第一個產 品及最後一個產品(N=2)的檢查就是等於全數檢查的原則,此一原則,在標準 化徹底實施及制程安定的生產線也適用。 9.防錯裝置的原則:要防止不良的發生,不能完全依賴作業人員的注意力,而必 須以防錯裝置來防止人為的疏忽及錯誤。 10.檢查的任務原則:不是在選別,而是要以排除不良原因為努力的對象 11.設有抱怨的原則:要全員徹底地經營品質,以零不良為目標,提供零不良的商 品給客戶。 12.單件流動的原則:做完一個製品,即刻進行下一個制程,即是單件流動之意, 這是早期發現不良的基本方法,而且因為減少搬運儲存等待,所以不良發生 的機會也就減少了。 13.目視管理的原則:生產線不要編得太長,而且要以產品別編成生產線;使生產 上一有異常狀況發生時,就能立即明瞭何處發生了什麼異常現象,此即為目 視管理。 14.任務明確的原則:每一條生產線的生產目標 品質及產量,都要明確地表示出 來,做為改善及維持的依據。
(5)象螺釘螺帽之類的小零件忘記上鎖或是沒有鎖緊所造成的不良。
(6)混入異種物料或零組件等造成的不良。
(7)出貨包裝時的標籤 尺寸烙板等的錯誤或遺失等不良。
4
四、零不良的原則
所謂零不良就是要做到連一個不良品都沒有,要實現“零不良”的境界 ,基本原則如下:
1.全數檢查的原則:所有零件及製品非做到全數檢查不可。 2.在制程內檢查的原則:品質是製造出來的,所以必須在制程內實施檢查。 3.停線的原則:在制程中一旦發現不良,發現的人就需即刻將生產線停頓下來, 並且著手採取排除不良發生原因的對策。 4.責任的原則:發生不良制程的作業者,必須立即做現場的修理或補工,要確 定每一個人的責任範圍。 5.現行逮捕的原則:一旦發現不良,在什麼時後由誰做出來,在那一台機器做 出來,用那種材料做出來,要能夠立即確認,不能用想像嫌疑犯的心態。 6.徹底實行標準作業的原則 7.特殊同歸的原則:降低作業工時,使潛在不良能夠顯現,進而減少不良品, 同時可以提高生產力及品質水準。
1
二、
品質的三不政策
1.不製造不良品: 不可有的錯誤觀念“不良品的發生是正常的現象”。 2.不流出不良品: 製造者必須要自主檢查,不可以有“製造的是一個人,檢查 的又是另一個人”的做法。 3. 不接受不良品: 要建立“不良品是誰做出來的,就必須由其自己修正”的觀 ,這樣員工才知
補充說明:
加上人字邊的“自動化”與傳統的沒有人字邊的“自動化”的意義是完全不 同的。人字邊的“自動化”強調要使機器設備,在有異常狀況發生時,能自動停 止下來,以避免不良品持續發生。因此,也可以說是零不良的品質保證最 佳的方法。此外,人字邊的"自動化"強調要能以"低成本"、"適速化"、"小型化“ 、“專用化”的觀念來達成減少人員的需求,以及縮短生產交期時間的效果。因 此,在“自動化”機器設備的設計觀念上,也有許多與傳統的自動化設備的設計 理念,大有不同見解的地方,是從事自動化機器設備設計製作的人員必需思考 的地方。
3
一般制程不良發生的類別:
(1)加工物在加工時,忘記未加工,或是逆加工,或是過度加工的不良。 (2)在加工時,產品尺寸的大小發生偏差,或是位置對稱的不良。 (3)在安裝治具或機器時,因某些零件忘記裝上,或左右或正反方向安裝錯誤, 或是安裝不完全,而發生外觀不良未加工,逆加工等不良。
(4)制程在裝配時,取用錯誤的零件,或忘記裝配零件,或是左右方向裝置錯誤 ,或是裝配不完全的不良。
安定化生產-品質的安定
安定化生產:品質的安定 一、追求零不良
錯誤的想法:“多少總有些不良品存在吧!” 企業的品質目標就是零不良 以源流管理的方式來達成零不良的目 品質不良都是生產流程安排不佳,管理上的問題以及管理者觀念上 的錯誤所占的比例較大,一般來說約有80%是屬於管理上的問題所 造成的,剩餘20%才是屬於統計品管的應用問題或是技術層面上的 問題因此,現在才逐漸從傳統的品質保證讓方法脫離出來,而走向 NPS零不良的源流管理方式。
6
五、
零不良緣流管理的戰術
1.生產平衡化,平準化 意義:使不同的產品每天內都能平均生產,以及使同一製品有二次以上的反 復生產。 生產平均化及平準化之後可使制程間的在製品大幅降低,產品在各種制程間 的流量少而快,這樣對不良的減少及品質的提升大有裨益。
補充說明: 生產平衡化 : 豐田所謂平衡化指的是“取量均值性”。假如後工程生產作業取量變化大,則前作 業工程必須準備最高量因而產生高庫存的浪費。所以豐田要求各生產工程取量儘可能 達到平均值,也就是前後一致,為的是將需求與供應達成平衡,降低庫存與生產浪費。 平準化: 除了主動配合客戶以降低需求之波動﹐也在製程中建立必要的超市庫存﹐以平衡 製程間週期時間﹑換模(或換線)時間的差異﹐此處所謂的超市庫存與一般的庫存或 暫存庫不同﹐超市庫存有自動補充之機制﹐庫存建立之時即定義其庫存之上下限﹐低 於下限即自動生產加以補充﹐達到上限就停線(或換線)生產他種產品。
1.消費者的不良: 消費者首先感受的就是商品的不良,再次就是交期不準的不良,這些都 是屬於可量化,可具體指出的不良。此外尚有屬於感性的或人文科學領域的 所謂魅力的品質,都是難以用具體的尺度來衡量,這些就稱之為“消費者滿 意度”,滿意低落或是此競爭對手來得差,也稱是不良。 2.管理的不良: 從營業部接單錯誤開始,設計圖面不良與上下游工廠的關系不佳等都屬 於管理不良工廠,內部的不良就更多了,出勤率不良作業不良設備不良 生產 計劃不良-----等。 3.制程的不良: 就是無法達到制程標準而產生的不良品。
7
2.標準作業: 是指徹底消除浪費,使作業者的生產作業活動規律化 定期化;標準 作業是使現場不產生不良品的起點,也是改善的出發點及維持點。 3.自己檢查: 是將後制程當作是客戶的想法,不良品絕對不可往下制程流,要立即找出真 正的原因及改善對策。若是屬於前制程的責任不要自己去判斷修補或選別,要 立即送回前制程,徹底把不良制程的原因發掘出來。 4.全數檢查:(作業員全數檢查) 全數檢查的著手點首先是要朝不要檢的目標前入,要有“品質是製造出來的而 不是檢查出來的”的監定信念。無論採用抽樣檢查,全數檢查或稽查製品的好壞 都是在製造時就決定了,所以製品的品質是由制程左右的,而不是依賴檢查就 決定的。 5.防錯裝置:(例:警報器/蜂鳴器/治具/防呆機構/感應式偵測設備等) 6.人字邊的自動化: 對零不良而言,自動化是指可自動檢查控制而且當品質產生異常時會立刻停 止的設備及生產線,特別是在製品公差很嚴格,而且設備能力不足的場合,這 種自動檢查停止的做法是很重要的。
9
Thanks!