轧钢一精整工艺流程
轧钢工艺流程
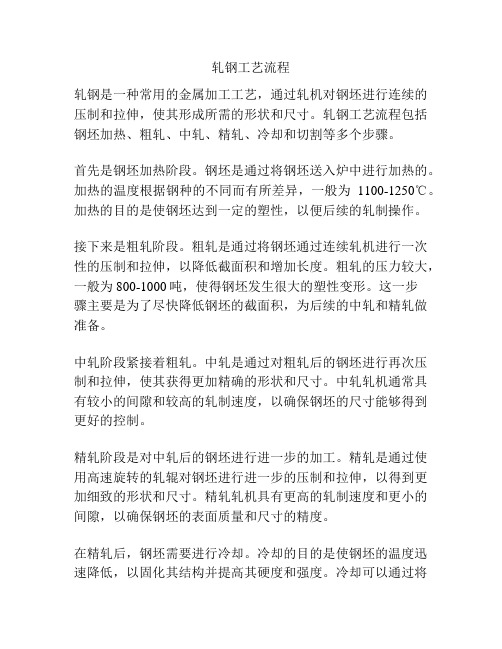
轧钢工艺流程轧钢是一种常用的金属加工工艺,通过轧机对钢坯进行连续的压制和拉伸,使其形成所需的形状和尺寸。
轧钢工艺流程包括钢坯加热、粗轧、中轧、精轧、冷却和切割等多个步骤。
首先是钢坯加热阶段。
钢坯是通过将钢坯送入炉中进行加热的。
加热的温度根据钢种的不同而有所差异,一般为1100-1250℃。
加热的目的是使钢坯达到一定的塑性,以便后续的轧制操作。
接下来是粗轧阶段。
粗轧是通过将钢坯通过连续轧机进行一次性的压制和拉伸,以降低截面积和增加长度。
粗轧的压力较大,一般为800-1000吨,使得钢坯发生很大的塑性变形。
这一步骤主要是为了尽快降低钢坯的截面积,为后续的中轧和精轧做准备。
中轧阶段紧接着粗轧。
中轧是通过对粗轧后的钢坯进行再次压制和拉伸,使其获得更加精确的形状和尺寸。
中轧轧机通常具有较小的间隙和较高的轧制速度,以确保钢坯的尺寸能够得到更好的控制。
精轧阶段是对中轧后的钢坯进行进一步的加工。
精轧是通过使用高速旋转的轧辊对钢坯进行进一步的压制和拉伸,以得到更加细致的形状和尺寸。
精轧轧机具有更高的轧制速度和更小的间隙,以确保钢坯的表面质量和尺寸的精度。
在精轧后,钢坯需要进行冷却。
冷却的目的是使钢坯的温度迅速降低,以固化其结构并提高其硬度和强度。
冷却可以通过将钢坯浸入冷水中或通过冷风吹扫来实现。
冷却的速度和方法根据钢种的不同而有所变化。
最后是切割阶段。
切割是将冷却后的钢坯切割成所需的长度和形状。
切割可以通过机械切割或火焰切割来实现,根据钢坯的尺寸和形状的不同而有所变化。
总结起来,轧钢工艺流程包括钢坯加热、粗轧、中轧、精轧、冷却和切割等多个步骤。
这些步骤的顺序和参数都会根据不同的钢种和需要的成品要求而有所变化。
轧钢工艺的发展使得钢材的生产更加高效和精确,满足了不同行业对钢材质量和性能的需求。
冶金厂轧钢厂工艺流程图
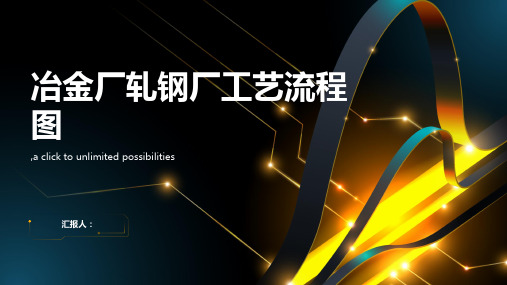
,a click to unlimited possibilities
汇报人:
目录
01 轧 钢 工 艺 流 程 概 述 03 轧 钢 工 艺 流 程 图 应
用
05 轧 钢 工 艺 流 程 图 的
发展趋势
02 轧 钢 工 艺 流 程 图 解 析
04 轧 钢 工 艺 流 程 图 的 绘制与改进
冷却:将轧制后的钢坯进行冷却
添加标题
添加标题
添加标题
添加标题
轧制:将加热后的钢坯送入轧机进 行轧制
切割:将冷却后的钢坯进行切割, 得到所需的钢材
精整阶段
精整目的:提高钢材表面质量,改善钢材性能 精整工艺:包括矫直、剪切、打磨、抛光等 精整设备:矫直机、剪切机、打磨机、抛光机等 精整效果:提高钢材表面光洁度,改善钢材尺寸精度和性能指标
THANKS
汇报人:
降低生产成本
优化工艺流程:减少废品率,提高 生产效率
降低能源消耗:采用节能技术,减 少能源消耗
添加标题
添加标题
添加标题
添加标题
提高设备利用率:合理安排生产计 划,减少设备闲置时间
提高产品质量:减少返工率,降低 废品率,提高产品附加值
Part Four
轧钢工艺流程图的 绘制与改进
绘制轧钢工艺流程图的工具与软件
收集轧钢工 艺流程图所 需的数据和 信息
绘制轧钢工 艺流程图的 草图
修改和完善 轧钢工艺流 程图
审核和确认 轧钢工艺流 程图
发布和实施 轧钢工艺流 程图
轧钢工艺流程图的改进与优化
优化工艺流程:提高生产效率,降 低能耗
优化生产环境:改善工作环境,提 高员工工作效率
添加标题
轧钢一精整工艺流程
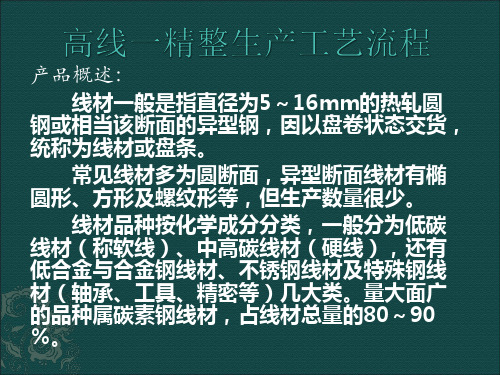
线材一般是指直径为5~16mm的热轧圆 钢或相当该断面的异型钢,因以盘卷状态交货, 统称为线材或盘条。
常见线材多为圆断面,异型断面线材有椭 圆形、方形及螺纹形等,但生产数量很少。
线材品种按化学成分分类,一般分为低碳 线材(称软线)、中高碳线材(硬线),还有 低合金与合金钢线材、不锈钢线材及特殊钢线 材(轴承、工具、精密等)几大类。量大面广 的品种属碳素钢线材,占线材总量的80~90 %。
卸卷
配合行车吊运
把包装合格的钢材从“C”形钩上用卸卷小车卸下,放在 卸卷机上,等待天车吊运。
工艺制度:卸卷过程生产正常时为全自动模式
工艺标准:在卸卷机上对方的钢材必须对齐
工艺技术:成品钢材不允许在P&F输送链上挤的太多
工艺条件:卸卷小车、卸卷机、P&F线运行正常
6特殊操作
1停止器信号失灵,在称重过程中,停止器忽 然打开,应立即拍下P&F链急停,谨防翻称。
特殊操作
1操作时,根据监控设备,对钩子运动情况 进行监控,发生撞钩、滑线、倒钩等故障要 及时通知有关人员处理。
2严禁肓目封点,强行启动,造成事故。
3道岔上严禁打钩。
4遇有歪钩时,必须及时停机进行处理,不 得强行用其它钩带动运行或强行封闭保护开 关。
5当生产中出现局部质量缺陷时,剪切工应 听从精轧热检工的指令,将盘卷缺陷部分切 除,直到盘条符合标准为止。
线材在国民经济中的作用与地位较重要,是不可 或缺的重要品种。
首先,线材产量占钢材总产量的比例很大,一 般线材产量占钢材总产量的8~10%,而我国占20 %以上;
其次,线材用途遍布国民经济各个部门,除直 接用作建筑钢材外,线材的深加工产品用途更为广 泛和重要,例如各类商品钢丝及专用弹簧钢丝、焊 丝、冷激钢丝、镀锌钢丝、通讯线、轮胎钢丝及钢 帘线、高强度钢丝及钢绞线、轴承钢丝、工具钢丝、 不锈钢丝、各种钢丝绳、钢钉、标准件等等。发达 国家线材加工比在70%左右,我国为30%左右。
1轧钢厂工艺操作规程

山西长信工业轧钢厂作业文件工艺操作规程受控状态:编制部门:轧钢厂审核人:***批准人:***2022-7-10 实施CX-ZY-16-001 A/0版 2022-7-2 批准更改状态表轧钢生产线工艺流程图飞剪精轧φ158*8 .☆注:“”关键工序质量把握点轧钢厂作业文件工艺操作规程CX-ZY-16-0011生产工艺流程连铸坯一上料根道一排齐一推钢机推入加热炉一加热一出钢机推出f 出炉辑道f机前辐道f①550×2->Φ 530X3f卡断剪一①400 X4f切头剪一侧活套一①300X8一飞剪f①158×8精轧机组承受45度无扭转摩根轧机一穿水冷却(控轧控冷)一吐丝机一强风冷却一PF钩式输送系统一打包一卸卷->入库堆放。
2原料、产品规格及技术标准2.1产品名称、规格、技术标准2. Ll产品标准名称、规格、国家标准号:钢种2.2原料截面尺寸、长度、技术条件:2. 2.1钢坯截面尺寸及允许偏差:连铸坯技术条件:2. 2.3.1连铸坯外表不得有肉眼可见的裂纹、重皮、翻皮、结疤、夹杂、划痕、擦伤、气孔、皱纹、冷溅、耳子、凹坑、凸块和深度大于2mm的发纹。
连铸坯横截面不得有缩孔和皮下气泡。
2. 2.3.2连铸坯的弯曲度每米不得大于20mm,总弯曲度不得大于总长度的2%o2. 2.3. 3连铸坯不得有明显扭转。
2. 2.3. 4连铸坯端部火焰切割局部保持平坦。
2.2.3. 5连铸坯允许有鼓肚,但高度不得超过连铸坯边长的允许正偏差。
3.2. 3. 6连铸坯端部的斜割不得大于20mm。
坯料规格:150X150X 6000mmo轧钢厂使用钢坯长度范围:5m~6. 2m。
3原料工艺技术操作规程3.1正常生产时,连铸坯由炼钢连铸车间直接运至加热炉尾上料辑道上,热装入炉轧制。
3.2后道工序处理事故时间较长时,连铸钢坯需作冷坯处理,按炉批号堆放整齐,堆垛高度不得超过4m,垛与垛间距不小于0. 5m o3.3对于不符合坯料技术条件的不合格坯料,在投炉时要挑出,按炉批号做好记录,放在指定地点。
轧钢工艺流程(1)
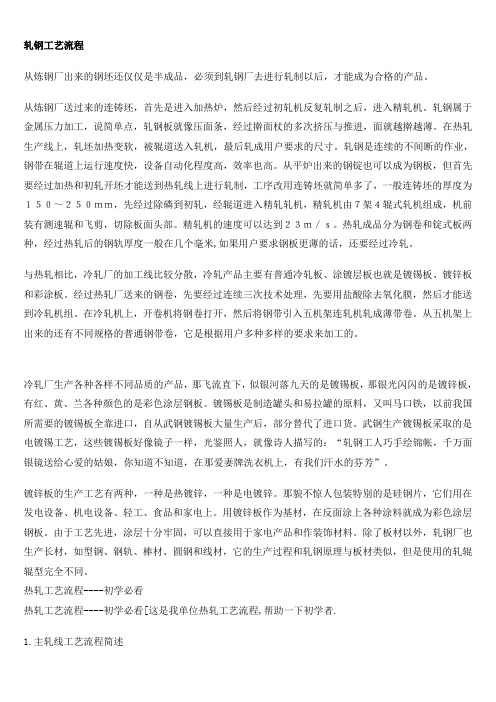
轧钢工艺流程从炼钢厂出来的钢坯还仅仅是半成品,必须到轧钢厂去进行轧制以后,才能成为合格的产品。
从炼钢厂送过来的连铸坯,首先是进入加热炉,然后经过初轧机反复轧制之后,进入精轧机。
轧钢属于金属压力加工,说简单点,轧钢板就像压面条,经过擀面杖的多次挤压与推进,面就越擀越薄。
在热轧生产线上,轧坯加热变软,被辊道送入轧机,最后轧成用户要求的尺寸。
轧钢是连续的不间断的作业,钢带在辊道上运行速度快,设备自动化程度高,效率也高。
从平炉出来的钢锭也可以成为钢板,但首先要经过加热和初轧开坯才能送到热轧线上进行轧制,工序改用连铸坯就简单多了,一般连铸坯的厚度为150~250mm,先经过除磷到初轧,经辊道进入精轧轧机,精轧机由7架4辊式轧机组成,机前装有测速辊和飞剪,切除板面头部。
精轧机的速度可以达到23m/s。
热轧成品分为钢卷和锭式板两种,经过热轧后的钢轨厚度一般在几个毫米,如果用户要求钢板更薄的话,还要经过冷轧。
与热轧相比,冷轧厂的加工线比较分散,冷轧产品主要有普通冷轧板、涂镀层板也就是镀锡板、镀锌板和彩涂板。
经过热轧厂送来的钢卷,先要经过连续三次技术处理,先要用盐酸除去氧化膜,然后才能送到冷轧机组。
在冷轧机上,开卷机将钢卷打开,然后将钢带引入五机架连轧机轧成薄带卷。
从五机架上出来的还有不同规格的普通钢带卷,它是根据用户多种多样的要求来加工的。
冷轧厂生产各种各样不同品质的产品,那飞流直下,似银河落九天的是镀锡板,那银光闪闪的是镀锌板,有红、黄、兰各种颜色的是彩色涂层钢板。
镀锡板是制造罐头和易拉罐的原料,又叫马口铁,以前我国所需要的镀锡板全靠进口,自从武钢镀锡板大量生产后,部分替代了进口货。
武钢生产镀锡板采取的是电镀锡工艺,这些镀锡板好像镜子一样,光鉴照人,就像诗人描写的:“轧钢工人巧手绘锦帐,千万面银镜送给心爱的姑娘,你知道不知道,在那爱妻牌洗衣机上,有我们汗水的芬芳”。
镀锌板的生产工艺有两种,一种是热镀锌,一种是电镀锌。
轧钢生产工艺流程
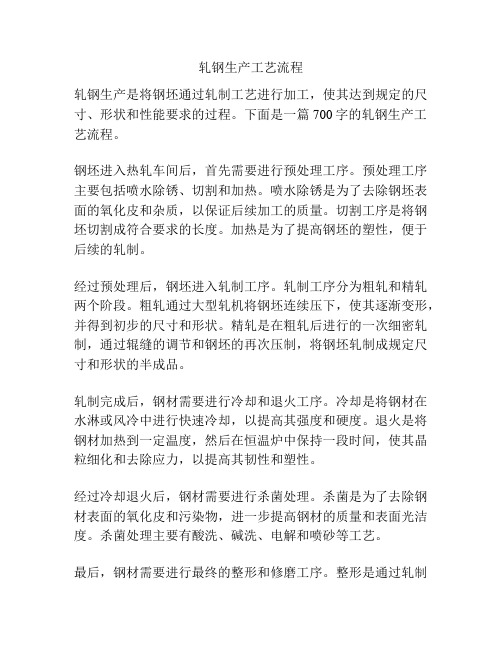
轧钢生产工艺流程轧钢生产是将钢坯通过轧制工艺进行加工,使其达到规定的尺寸、形状和性能要求的过程。
下面是一篇700字的轧钢生产工艺流程。
钢坯进入热轧车间后,首先需要进行预处理工序。
预处理工序主要包括喷水除锈、切割和加热。
喷水除锈是为了去除钢坯表面的氧化皮和杂质,以保证后续加工的质量。
切割工序是将钢坯切割成符合要求的长度。
加热是为了提高钢坯的塑性,便于后续的轧制。
经过预处理后,钢坯进入轧制工序。
轧制工序分为粗轧和精轧两个阶段。
粗轧通过大型轧机将钢坯连续压下,使其逐渐变形,并得到初步的尺寸和形状。
精轧是在粗轧后进行的一次细密轧制,通过辊缝的调节和钢坯的再次压制,将钢坯轧制成规定尺寸和形状的半成品。
轧制完成后,钢材需要进行冷却和退火工序。
冷却是将钢材在水淋或风冷中进行快速冷却,以提高其强度和硬度。
退火是将钢材加热到一定温度,然后在恒温炉中保持一段时间,使其晶粒细化和去除应力,以提高其韧性和塑性。
经过冷却退火后,钢材需要进行杀菌处理。
杀菌是为了去除钢材表面的氧化皮和污染物,进一步提高钢材的质量和表面光洁度。
杀菌处理主要有酸洗、碱洗、电解和喷砂等工艺。
最后,钢材需要进行最终的整形和修磨工序。
整形是通过轧制或冲压等方法将钢材进行完全成型,以满足各种尺寸和形状的要求。
修磨是对钢材表面进行研磨处理,以去除表面的氧化皮、凹凸和划痕,提高表面平整度和光洁度。
整形和修磨完成后,钢材经过质量检验,合格后可以进行包装、储存和出库等工序,最终送到客户手中。
在整个轧钢生产过程中,为保证产品质量,还需要进行各种质量控制和检测,如硬度测试、化学成分分析和尺寸测量等。
以上是一篇关于轧钢生产工艺流程的700字的介绍。
轧钢生产工艺是一个复杂的过程,需要各种设备和工艺的配合,以保证产品的质量和效率。
随着技术的不断发展,轧钢工艺也在不断改进和优化,以满足不断变化的市场需求。
轧钢厂生产工艺流程图及简介
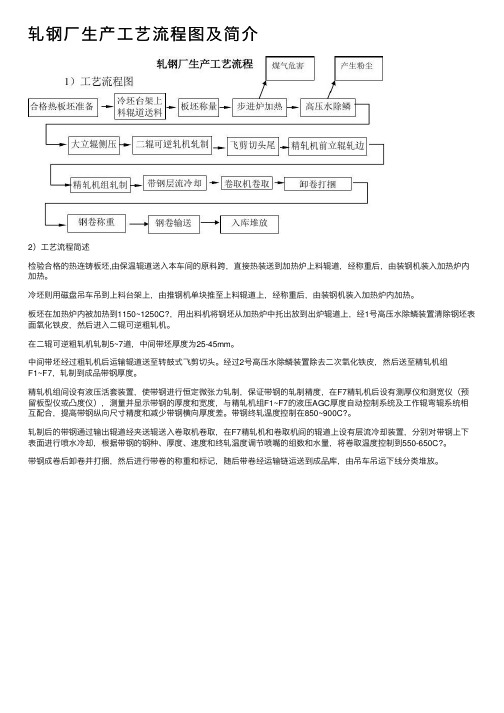
轧钢⼚⽣产⼯艺流程图及简介
2)⼯艺流程简述
检验合格的热连铸板坯,由保温辊道送⼊本车间的原料跨,直接热装送到加热炉上料辊道,经称重后,由装钢机装⼊加热炉内加热。
冷坯则⽤磁盘吊车吊到上料台架上,由推钢机单块推⾄上料辊道上,经称重后,由装钢机装⼊加热炉内加热。
板坯在加热炉内被加热到1150~1250C?,⽤出料机将钢坯从加热炉中托出放到出炉辊道上,经1号⾼压⽔除鳞装置清除钢坯表⾯氧化铁⽪,然后进⼊⼆辊可逆粗轧机。
在⼆辊可逆粗轧机轧制5~7道,中间带坯厚度为25-45mm。
中间带坯经过粗轧机后运输辊道送⾄转⿎式飞剪切头。
经过2号⾼压⽔除鳞装置除去⼆次氧化铁⽪,然后送⾄精轧机组
F1~F7,轧制到成品带钢厚度。
精轧机组间设有液压活套装置,使带钢进⾏恒定微张⼒轧制,保证带钢的轧制精度,在F7精轧机后设有测厚仪和测宽仪(预留板型仪或凸度仪),测量并显⽰带钢的厚度和宽度,与精轧机组F1~F7的液压AGC厚度⾃动控制系统及⼯作辊弯辊系统相互配合,提⾼带钢纵向尺⼨精度和减少带钢横向厚度差。
带钢终轧温度控制在850~900C?。
轧制后的带钢通过输出辊道经夹送辊送⼊卷取机卷取,在F7精轧机和卷取机间的辊道上设有层流冷却装置,分别对带钢上下表⾯进⾏喷⽔冷却,根据带钢的钢种、厚度、速度和终轧温度调节喷嘴的组数和⽔量,将卷取温度控制到550-650C?。
带钢成卷后卸卷并打捆,然后进⾏带卷的称重和标记,随后带卷经运输链运送到成品库,由吊车吊运下线分类堆放。
轧钢工艺操作规程

一、工艺流程:钢坯进场验收——装钢加热——φ550轧机轧制——切头——φ350轧机轧制四道——切尾——φ300轧机轧制六道——飞剪——热检———步进冷床——冷检——剪切——分钢——打捆——检验入库二、原料种类及验收标准1、原料种类:135方 150方2、钢坯执行标准:GB1499—1998 YB/T2011—1983三、基本工艺技术要求及工艺参数1、加热炉技术规程1.1、主要设备参数形式:三段式煤气发生炉外形尺寸:长27 m*宽 5m有效尺寸:长25 m*宽3.7 m1.2、加热炉点火前的准备工作1、工具:钳子、手钳,石棉布及司炉工应用的防护用品。
2、木柴及引火物:φ40—φ100mm,长度为300—500mm.3、司炉工检查煤气间内设备及水、电、汽管线、阀门、开关传动机组,及各密封处(探火孔、人孔门、双钟阀板)的可靠性,并在减速机油箱内加油,试开车运转。
4、点火:用长火点燃木屑,均匀燃烧后,关闭炉门,向炉内投煤。
培养火层至炉出口温度达400'C左右,关闭汽包放散阀,向炉底供蒸汽,取煤气抽样化验含量<0.4%,煤气合格后可供气。
5、日常保养:a 发生炉外部应保持清洁、无积灰、无油垢、无积水。
b 发生炉传动运转是否正常。
c 配套的各种阀门操作时,转动开启是否灵活。
d 各种润滑部位、油路、油液质量是否良好。
6、注意:测钎时,灰盘不能转动,以免发生事故,探火时,先开蒸汽阀,然后开探火孔塞头,方可进行炭火,但不能同时打开3个以上的探火孔,以免大量空气被吸入炉内而发生危险。
1.3、钢坯吊运管理规定1、接收钢坯时,必须执行按炉送钢制度。
2、检验钢坯外观质量。
3、剔除的钢坯要另外堆放,并做出标识。
4、无送钢卡片不得装炉。
5、按送钢卡片顺序吊装。
1.4 钢坯装炉规定1、纪录装炉钢坯根数、重量、装入时间。
2、换坯、换钢号时应按规定做好标记。
3、钢坯入炉不得刮墙落地。
1.5 钢坯加热规定:1、正常生产均热段温度控制在1250—1350'c,窑炉加热不超过1320'C,低合金钢出炉温度1060—1200'C左右,普碳钢出炉温度1050—1150'C。
轧钢工艺流程(1)
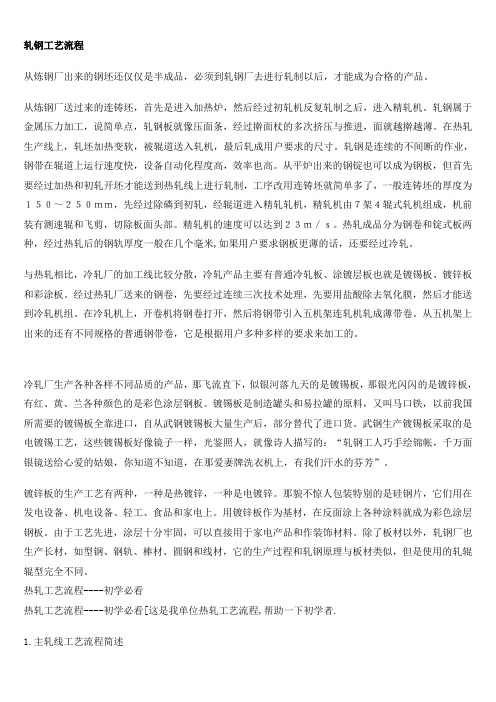
轧钢工艺流程从炼钢厂出来的钢坯还仅仅是半成品,必须到轧钢厂去进行轧制以后,才能成为合格的产品。
从炼钢厂送过来的连铸坯,首先是进入加热炉,然后经过初轧机反复轧制之后,进入精轧机。
轧钢属于金属压力加工,说简单点,轧钢板就像压面条,经过擀面杖的多次挤压与推进,面就越擀越薄。
在热轧生产线上,轧坯加热变软,被辊道送入轧机,最后轧成用户要求的尺寸。
轧钢是连续的不间断的作业,钢带在辊道上运行速度快,设备自动化程度高,效率也高。
从平炉出来的钢锭也可以成为钢板,但首先要经过加热和初轧开坯才能送到热轧线上进行轧制,工序改用连铸坯就简单多了,一般连铸坯的厚度为150~250mm,先经过除磷到初轧,经辊道进入精轧轧机,精轧机由7架4辊式轧机组成,机前装有测速辊和飞剪,切除板面头部。
精轧机的速度可以达到23m/s。
热轧成品分为钢卷和锭式板两种,经过热轧后的钢轨厚度一般在几个毫米,如果用户要求钢板更薄的话,还要经过冷轧。
与热轧相比,冷轧厂的加工线比较分散,冷轧产品主要有普通冷轧板、涂镀层板也就是镀锡板、镀锌板和彩涂板。
经过热轧厂送来的钢卷,先要经过连续三次技术处理,先要用盐酸除去氧化膜,然后才能送到冷轧机组。
在冷轧机上,开卷机将钢卷打开,然后将钢带引入五机架连轧机轧成薄带卷。
从五机架上出来的还有不同规格的普通钢带卷,它是根据用户多种多样的要求来加工的。
冷轧厂生产各种各样不同品质的产品,那飞流直下,似银河落九天的是镀锡板,那银光闪闪的是镀锌板,有红、黄、兰各种颜色的是彩色涂层钢板。
镀锡板是制造罐头和易拉罐的原料,又叫马口铁,以前我国所需要的镀锡板全靠进口,自从武钢镀锡板大量生产后,部分替代了进口货。
武钢生产镀锡板采取的是电镀锡工艺,这些镀锡板好像镜子一样,光鉴照人,就像诗人描写的:“轧钢工人巧手绘锦帐,千万面银镜送给心爱的姑娘,你知道不知道,在那爱妻牌洗衣机上,有我们汗水的芬芳”。
镀锌板的生产工艺有两种,一种是热镀锌,一种是电镀锌。
轧钢工艺过程介绍(介绍的比较详细)

一、钢铁的冶炼流程和主要设备一般来说,钢铁的冶炼大致分为四个过程:炼铁、炼钢、热轧、冷轧。
其中我们着重介绍热轧、冷轧的流程和主要设备。
1.热轧热轧是在钢的再结晶温度以上进行的轧制,轧制过程就是在旋转的轧辊间改变钢坯形状的压力加工过程。
热轧时金属塑性高,变形抗力低,大大减少了金属变形的能量消耗。
所以热轧能显著降低能耗,降低成本。
此外热轧能改善金属及合金的加工工艺性能,即将铸造状态的粗大晶粒破碎,显著裂纹愈合,减少或消除铸造缺陷,将铸态组织转变为变形组织,提高合金的加工性能。
热轧通常采用大铸锭,大压下量轧制,不仅提高了生产效率,而且为提高轧制速度、实现轧制过程的连续化和自动化创造了条件。
一般可在带钢热轧机上生产厚度为1.2~8mm 成卷热轧带钢。
热轧工艺一般是将连铸的钢板板坯进过加热炉加热到一定温度,经过传送辊道到轧机处进行轧制成带钢、型钢或钢管。
带钢还需要经过卷取机卷成钢卷以便运输。
热轧厂主要设备:加热炉、传送辊道、轧机(1)加热炉现在一般采用步进加热炉来加热板坯,以提高自动化程度和生产率。
涉及到的传动产品:链条、轴承、联轴器、电机、减速箱、密封、液压胶管、工业胶管等等。
(2)传送辊道热轧基本是靠辊道来运输钢坯或带钢。
一般有链条传送和棍子传送两种。
涉及到的传动产品:链条、轴承、联轴器、电机、减速箱、密封等等。
(3)轧机轧机是热轧的关键设备,直接决定了产品质量的好坏。
为减少轧辊弹变而影响带钢厚度精度,国内使用的热轧机以四棍或六棍轧机为主。
轧机模型:涉及到的传动产品:轴承、联轴器、电机、减速箱、密封、液压胶管、工业胶管等等。
(4)冷轧冷轧是利用热轧钢卷为原料,经酸洗去除氧化皮后进行轧制。
冷轧通常采用纵轧(轧辊轴线相平行,旋转方向相反,轧件作直线运动的轧制方法)的方式。
冷轧生产的工序一般包括开卷、轧制、脱脂(酸洗)、退火(热处理)、卷取等,生产汽车板还需要镀锌等工艺。
酸洗工艺流程图:镀锌工艺流程图:镀锌厂房布局:冷轧主要设备:开卷机(卷取机)、轧机等。
轧钢生产工艺流程介绍

轧钢生产工艺流程介绍1、棒材生产线工艺流程钢坯验收T加热T轧制T倍尺剪切T冷却T剪切T检验T包装T计量T入库(1)钢坯验收=钢坯质量是关系到成品质量的关键,必须经过检查验收。
①、钢坯验收程序包括:物卡核对、外形尺寸测量、表面质量检查、记录等。
②、钢坯验收依据钢坯技术标准和内控技术条件进行,不合格钢坯不得入炉。
(2)、钢坯加热钢坯加热是热轧生产工艺过程中的重要工序。
①、钢坯加热的目的钢坯加热的目的是提高钢的塑性,降低变形抗力,以便于轧制;正确的加热工艺,还可以消除或减轻钢坯内部组织缺陷。
钢的加热工艺与钢材质量、轧机产量、能量消耗、轧机寿命等各项技术经济指标有直接关系。
②、三段连续式加热炉所谓的三段即:预热段、加热段和均热段。
预热段的作用:利用加热烟气余热对钢坯进行预加热,以节约燃料。
(一般预加热到300〜450C)加热段的作用:对预加热钢坯再加温至1150〜1250 C,它是加热炉的主要供热段,决定炉子的加热生产能力。
均热段的作用:减少钢坯内外温差及消除水冷滑道黑印,稳定均匀加热质量。
③、钢坯加热常见的几种缺陷a、过热钢坯在高温长时间加热时,极易产生过热现象。
钢坯产生过热现象主要表现在钢的组织晶粒过分长大变为粗晶组织,从而降低晶粒间的结合力,降低钢的可塑性。
过热钢在轧制时易产生拉裂,尤其边角部位。
轻微过热时钢材表面产生裂纹,影响钢材表面质量和力学性能。
为了避免产生过热缺陷,必须对加热温度和加热时间进行严格控制。
b、过烧钢坯在高温长时间加热会变成粗大的结晶组织,同时晶粒边界上的低熔点非金属化合物氧化而使结晶组织遭到破坏,使钢失去应有的强度和塑性,这种现象称为过烧。
过烧钢在轧制时会产生严重的破裂。
因此过烧是比过热更为严重的一种加热缺陷。
过烧钢除重新冶炼外无法挽救。
避免过烧的办法:合理控制加热温度和炉内氧化气氛,严格执行正确的加热制度和待轧制度,避免温度过高。
c、温度不均钢坯加热速度过快或轧制机时产量大于加热能力时易产生这种现象。
轧钢工艺流程介绍

轧钢工艺流程介绍轧钢工艺流程介绍从炼钢厂出来的钢坯还仅仅是半成品,必须到轧钢厂去进行轧制以后,才能成为合格的产品。
从炼钢厂送过来的连铸坯,首先是进入加热炉,然后经过初轧机反复轧制之后,进入精轧机。
轧钢属于金属压力加工,说简单点,轧钢板就像压面条,经过擀面杖的多次挤压与推进,面就越擀越薄。
在热轧生产线上,轧坯加热变软,被辊道送入轧机,最后轧成用户要求的尺寸。
轧钢是连续的不间断的作业,钢带在辊道上运行速度快,设备自动化程度高,效率也高。
从平炉出来的钢锭也可以成为钢板,但首先要经过加热和初轧开坯才能送到热轧线上进行轧制,工序改用连铸坯就简单多了,一般连铸坯的厚度为150~250mm,先经过除磷到初轧,经辊道进入精轧轧机,精轧机由7架4辊式轧机组成,机前装有测速辊和飞剪,切除板面头部。
精轧机的速度可以达到23m/s。
热轧成品分为钢卷和锭式板两种,经过热轧后的钢轨厚度一般在几个毫米,如果用户要求钢板更薄的话,还要经过冷轧。
与热轧相比,冷轧厂的加工线比较分散,冷轧产品主要有普通冷轧板、涂镀层板也就是镀锡板、镀锌板和彩涂板。
经过热轧厂送来的钢卷,先要经过连续三次技术处理,先要用盐酸除去氧化膜,然后才能送到冷轧机组。
在冷轧机上,开卷机将钢卷打开,然后将钢带引入五机架连轧机轧成薄带卷。
从五机架上出来的还有不同规格的普通钢带卷,它是根据用户多种多样的要求来加工的。
冷轧厂生产各种各样不同品质的产品,那飞流直下,似银河落九天的是镀锡板,那银光闪闪的是镀锌板,有红、黄、兰各种颜色的是彩色涂层钢板。
镀锡板是制造罐头和易拉罐的原料,又叫马口铁,以前我国所需要的镀锡板全靠进口,自从武钢镀锡板大量生产后,部分替代了进口货。
武钢生产镀锡板采取的是电镀锡工艺,这些镀锡板好像镜子一样,光鉴照人,就像诗人描写的:“轧钢工人巧手绘锦帐,千万面银镜送给心爱的姑娘,你知道不知道,在那爱妻牌洗衣机上,有我们汗水的芬芳”。
镀锌板的生产工艺有两种,一种是热镀锌,一种是电镀锌。
轧钢工艺(完整版)详解

钢工艺(完整版)详解铜陵市富鑫钢铁有限公司编号:FX-08-2011 版本/修订:1/1轧钢工艺技术操作规程起草:审核:批准:受控状态:分发号:二〇一二年六月十六日修订即日起颁布实施铜陵市富鑫钢铁有限公司轧钢工艺技术操作规程1、棒材(钢筋混凝土用热轧带肋钢筋)生产工艺流程2、原料种类及验收标准2.1、原料种类:150*150*3000mm,2.2、钢坯执行标准:GB1499.2—2007 YB/T2011—20043、加热炉基本工艺技术要求及工艺参数3.1、加热炉主要参数形式:双蓄热推钢式连续加热三段式加热炉外形尺寸: 长3200mm 宽500mm有效尺寸: 长2840mm 宽3600mm合 加热 轧 轧 切头尾 热共轧分段剪切 热检 冷却 取力学实验 冷检 包装 定尺剪切 不合格 废钢库 称重 成品库 出厂 用户3.2、加热炉点火前的准备工作点火前应对炉子进行全面的系统地检查和煤气防烛实验,并严格执行公司《煤气系统操作管理规程》,点火前15分钟启动风机,提起烟道闸板,开启所有的仪表控制系统并检查无异后进行加热炉正常操作。
3.3、加热制度为使钢筋产品质量得到控制,加热炉温度应分段控制如下:HRB500、HRB 500E控制温度为:φ12-φ18控制温度为预热段600℃-700℃加热段1180℃-1200℃均热段1150℃-1180℃φ20-φ22控制温度为预热段630℃-750℃加热段1200℃-1230℃均热段1180℃-1200℃φ25控制温度为预热段650℃-800℃加热段1220℃-1250℃均热段1180℃-1230℃φ28 控制温度为预热段750℃-850℃加热段1220℃-1250℃均热段1220℃-1250℃HRB400HRB400E控制温度为:φ12-φ18控制温度为预热段550℃-650℃加热段1150℃-1200℃均热段1150℃-1180℃φ20-φ22控制温度为预热段600℃-700℃加热段1180℃-1220℃均热段1150℃-1180℃φ25控制温度为预热段600℃-750℃加热段1200℃-1230℃均热段1150℃-1220℃φ28控制温度为预热段700℃-850℃加热段1200℃-1250℃均热段1200℃-1250℃为使钢筋终轧温度控制在1000-1100℃,钢坯出炉温度应控制在1150℃-1200℃,即均热段的温度为1150℃-1200℃.头炉炉膛压力应保持微正压,防止冷风吸入。
轧钢生产工艺流程

轧钢生产工艺流程棒、线材是钢铁产品的重要品种之一;广泛应用于工业、农业、交通运输业及建筑业和深加工业。
由于机械和电气控制技术的进步,孔型设计的改进,上游连铸技术的进步,棒、线材轧机的根本性的变革(第三代高刚度短应力线轧机、高速无扭线材精轧机及斯太尔摩控制冷却工艺的问世);把棒、线材的生产技术推到了一个新的阶段:棒材轧制速度提高到18m/s;高线轧制速度提高到120-140m/s,保证速度105 m/s,单重达2500kg;其轧钢工艺生产流程成为标准布置形式。
第一章棒材生产工艺及性能控制1.1棒材生产工艺流程简介1):车间组成轧钢车间由炉子垮、主轧垮、成品垮和主电室组成2):年产82万吨棒材工艺流程图(如下图1-1)3):产品方案①:规模:由生产单位和设计院共同商定(投资决定)我们年产82万吨;②:钢种:低合金钢20Mn2(HRB44和HRB335),碳素结构钢Q235, 优质碳素结构钢45,③:产品规格:带肋钢筋¢10-¢40mm (64万吨)圆钢¢16-¢50mm (18万吨)④:产品质量及标准带肋钢筋精度应符合GB1499-98和GB13041-91的质量标准;圆钢产品直径精度应符合GB702-86;成品定尺要求:长度: 6-12m交货状态: 成捆交货,捆重1-5t4)生产熟练后,成材率可达到97%-98%5):坯料120*120-150*150连铸坯,长度6-12m连铸坯质量符合YB2011-83、YB/T154-1999、图1-11.2:车间工艺布置平面图(见详图)1.3:棒材工艺流程简述轧线设备高架平台布置:优点:利用空间,节省投资,便于检修轧钢生产工艺流程设备布置在+5.0m平台上,轧线标高为+5.8m。
冷、热坯(600℃)生产时,合格的连铸坯以单根方式从连铸坯出坯台架送入热送辊道,坯料在运送过程中由自动测长装置对坯料进行测长(使坯料进入加热炉后能准确对中),合格的单根坯料经提升装置将其提升到+5.0m平台辊道上,通过运送辊道进入入炉辊道,由推钢机推入加热炉,蓄热推钢式加热炉按不同钢种的加热制度,将坯料加热到980-1150℃,加热炉的设计能力为:冷坯160t/h,热坯180t/h。
轧钢生产工艺流程介绍

轧钢生产工艺流程介绍1、棒材生产线工艺流程钢坯验收→加热→轧制→倍尺剪切→冷却→剪切→检验→包装→计量→入库(1)钢坯验收〓钢坯质量是关系到成品质量的关键,必须经过检查验收。
①、钢坯验收程序包括:物卡核对、外形尺寸测量、表面质量检查、记录等。
②、钢坯验收依据钢坯技术标准和内控技术条件进行,不合格钢坯不得入炉。
(2)、钢坯加热钢坯加热是热轧生产工艺过程中的重要工序。
①、钢坯加热的目的钢坯加热的目的是提高钢的塑性,降低变形抗力,以便于轧制;正确的加热工艺,还可以消除或减轻钢坯内部组织缺陷。
钢的加热工艺与钢材质量、轧机产量、能量消耗、轧机寿命等各项技术经济指标有直接关系。
②、三段连续式加热炉所谓的三段即:预热段、加热段和均热段。
预热段的作用:利用加热烟气余热对钢坯进行预加热,以节约燃料。
(一般预加热到300~450℃)加热段的作用:对预加热钢坯再加温至1150~1250℃,它是加热炉的主要供热段,决定炉子的加热生产能力。
均热段的作用:减少钢坯内外温差及消除水冷滑道黑印,稳定均匀加热质量。
③、钢坯加热常见的几种缺陷a、过热钢坯在高温长时间加热时,极易产生过热现象。
钢坯产生过热现象主要表现在钢的组织晶粒过分长大变为粗晶组织,从而降低晶粒间的结合力,降低钢的可塑性。
过热钢在轧制时易产生拉裂,尤其边角部位。
轻微过热时钢材表面产生裂纹,影响钢材表面质量和力学性能。
为了避免产生过热缺陷,必须对加热温度和加热时间进行严格控制。
b、过烧钢坯在高温长时间加热会变成粗大的结晶组织,同时晶粒边界上的低熔点非金属化合物氧化而使结晶组织遭到破坏,使钢失去应有的强度和塑性,这种现象称为过烧。
过烧钢在轧制时会产生严重的破裂。
因此过烧是比过热更为严重的一种加热缺陷。
过烧钢除重新冶炼外无法挽救。
避免过烧的办法:合理控制加热温度和炉内氧化气氛,严格执行正确的加热制度和待轧制度,避免温度过高。
c、温度不均钢坯加热速度过快或轧制机时产量大于加热能力时易产生这种现象。
轧钢厂精整工艺技术操作规程

文件编码:CXZY.030----2016作业文件轧钢厂精整工序作业规程第A/0版编制人:吴硕明审核人:荣鑫批准人:闫建刚2016年1月1日发布 2016年1月5日实施山西长信轧钢有限公司发布文件修改履历轧钢厂精整工序作业规程1. 精整工序操作技术要求1.1 输送冷却与定尺剪切工序1.1.1 执行标准:GB1499.2-2007《钢筋混凝土用热轧带肋钢筋》;集团钢铁公司《钢筋混凝土用热轧带肋钢筋内控制标准》1.1.2 CS4操作工与冷床值守工的工作要求a) CS4操作工接到更换炉(批)号通知后,应将冷床连续步进运行,使上一炉最后一段成品后面至少留有4个齿条空位,以便使之与下一批第一段成品明显分开;b) 成品在冷床上冷却和输送过程中,前后不同批号的成品不能同时摆放在冷床齐头辊和下料装臵上;c) 更换炉批号时,冷床值守工应在下一批的前面几段成品上作上标记,防止与上一批钢混淆;d) 冷床值守工应随时监视成品的运行情况,发现成品在运行过程中产生顶弯受阻或卡钢时,应及时查明原因、排除故障;如果属于轧机或设备方面的原因,应向相关人员反映;、e) CS4操作工应准确控制定尺剪切长度,确保定尺实际长度在标准的允许范围,提高定尺率;f) 剪切时,要切净因轧制变形和分段剪切变形不合格的头部和尾部;g) 定尺剪切中,如果发现分段剪切长度不合理,不能达到定尺剪切的最佳尺寸时,应及时与CS3主操作工联系,调整和修改尾部调整系数或长度补偿值,以提高定尺率,减小头尾剪切长度;h) 定尺剪切时,不能将前后不同批号的成品同时取放在冷床输出辊道上输送和剪切;i) 当一炉(批)成品剪切完毕后,CS4操作工应通知CS5/CS6操作工更换炉(批)号,并将上一炉(批)的所有成品输送到定尺台架上后方能开始剪切下一批成品。
j) 交接班时,上一班CS4操作工应向下一班交接清楚冷床及其下料装臵、输出辊道、定尺剪前后钢材的批号、钢号、数量等,特别交待清楚前后两个不同批号的准确分界位臵,下一班人员应认真检查核实无误后方可接班。
- 1、下载文档前请自行甄别文档内容的完整性,平台不提供额外的编辑、内容补充、找答案等附加服务。
- 2、"仅部分预览"的文档,不可在线预览部分如存在完整性等问题,可反馈申请退款(可完整预览的文档不适用该条件!)。
- 3、如文档侵犯您的权益,请联系客服反馈,我们会尽快为您处理(人工客服工作时间:9:00-18:30)。
线材在国民经济中的作用与地位较重要,是不可 或缺的重要品种。
首先,线材产量占钢材总产量的比例很大,一 般线材产量占钢材总产量的8~10%,而我国占20 %以上;
其次,线材用途遍布国民经济各个部门,除直 接用作建筑钢材外,线材的深加工产品用途更为广 泛和重要,例如各类商品钢丝及专用弹簧钢丝、焊 丝、冷激钢丝、镀锌钢丝、通讯线、轮胎钢丝及钢 帘线、高强度钢丝及钢绞线、轴承钢丝、工具钢丝、 不锈钢丝、各种钢丝绳、钢钉、标准件等等。发达 国家线材加工比在70%左右,我国为30%左右。
开关置于自动位置,出现下列情形之一采用半自动 或手动操作:
(1)自动操作过程中,收集系统某一电气、液压设 备出现故障影响收集时。
(2)处理收集处的乱卷。 (3)测试某一单体设备的动作需手动、半自动操作。
特殊操作
1当收集系统出现故障或收集处出现乱卷、挂 钢时,立即将风冷辊道置于爬行状态,并通知 3C操作台不要来钢。
“人猿相揖别。只几个石头磨过,小儿时节。铜铁 炉中翻火焰,为问何时猜得,不过几千寒热。”轧 钢生产就是将钢坯轧成钢材的过程。其主要包括三 大工序:加热 轧制 精整
吐丝机吐丝后散冷线的剪头剪尾; 风冷到集卷筒收集、运转小车、倾翻机构; PF线自然冷却; 剪除头尾处不合格的线材; 打包机压紧打包; 称重、卸卷小车卸卷; 成品堆放; 精整工段是轧钢厂加热,轧制工艺中的后道工
2一根放一卷,严禁两根或多根放一卷。
3运卷小车处出现卡钢、挂钢时,严禁强行操 作应将故障处理完后才能操作。
4做好收集操作室与其它操作室的联络,协调 工作,做好物料跟踪管理,不得混炉,发现异 常及时向调度反映。
5采用手动、半自动操作时,要与设备周围操 作工密切配合,确保人身、设备安全。
剪除头尾处不合格的线材:
产品概述:
线材一般是指直径为5~16mm的热轧圆 钢或相当该断面的异型钢,因以盘卷状态交货, 统称为线材或盘条。
常见线材多为圆断面,异型断面线材有椭 圆形、方形及螺纹形等,但生产数量很少。
线材品种按化学成分分类,一般分为低碳 线材(称软线)、中高碳线材(硬线),还有 低合金与合金钢线材、不锈钢线材及特殊钢线 材(轴承、工具、精密等)几大类。量大面广 的品种属碳素钢线材,占线材总量的80~90 %。
头尾在线剪切工:将盘卷头尾有缺陷的部分切除;将控冷 轧制的盘卷头尾未穿水部份切除;其表面不得有耳子、折 叠、结疤等。
P&F线送来散卷 → 头尾不合格处剪切 → P&F链输送 和在线热检工搞好联系,严格按照有关要求剪切,保证包
装后的成品无缺陷。
工艺制度:严格执行按炉送钢制度
时通知轧线人员切钢,并报告调度。 5处理辊道内的乱丝和集卷筒卡钢,要对环境确认好,确保人和设
备的安全.
风冷到集卷筒收集、运转小车、倾翻机构:
集卷双芯棒:操作本区域设备把来自散卷运输机 的散状线圈垂直收集成盘卷并水平放到运卷车上, 负责换号的分隔识别;运卷车再将盘卷运至P&F 线钩式运输机的C形钩上。
风冷工工艺条件:散冷辊道、风机、 驱动电机、减速箱等设备运行良好
1开车前的准备工作及检查确认 (1)各联接部件紧固良好,无松动,辊道上无杂物。 (2)链条及各轴承座润滑良好,链条罩完好。 2开车操作程序 (1)启动各组辊道,检查传动是否正常,根据工艺要求调试辊
道速度及风机开启数量及风量。
风冷辊道 → 上集卷 → 双臂芯棒 → 运卷小车 → C形钩
把斯太尔摩风冷线上输送来的散卷通过上集卷站 整理成外形规则的盘卷,有双臂芯棒旋转,把竖 着的盘卷水平放置,用运卷小车把水平放置的盘 卷移送到“C”形勾上,并做好上钩记录。
正常操作1操作前对Fra bibliotek个系统的状态进行确认。 2检查系统各电气元件是否正常、是否接通。 3检查液压系统是否启动并处于正常工作状态。 4根据生产工艺要求调控操作台上的开关进行作业。 5过程操作:一般情况下操作室将收集系统操作选择
整理吐丝机吐出来的散卷,把钢材的 头部和尾部圈形整理好,使钢材顺利的进 入集卷筒。
吐丝机吐出散卷 → 风冷辊道冷却 → 集卷站集卷
风冷工工艺制度:随时注意吐丝机 吐出来的圈形特别是钢的头部和尾 部
风冷工工艺标准:当吐丝机吐得圈 形不太好时必须用钩子把乱了的圈 形整理好防止倒插料
风冷工工艺技术:把吐丝机吐出来 的散卷头尾的圈形用钩子整理好, 为收集工作做好准备
理化性能差距:
差距主要表现在以下方面: (l)化学成分。国外线材波动小且稳定,[C]%一
般波动在3个范围;国内在6~8个范围,头尾偏析更 严重。 (2)表面质量主要表现在脱碳层深度方面,国产 一般为0.023~0.14mm,最深为0.23~0.35mm; 国外一般0.02~0.05mm。 (3)金相组织。进口线材实测奥氏体晶粒度为5~6 级,很均匀,索氏体一般85%以上。国产线材奥氏晶 粒度2~7级,很不均匀,索氏体一般达不到85%, (4)非金属夹杂。国产线材夹杂多且颗粒很大,尤 其是A12O3颗粒最长达133μm,一般为≥50μm,进 口国外线材最大≥30μm,一般8μm左右。 (5)钢中气体含量也普遍比国外线材高,〔H〕、 〔O〕、(N〕一般比国外线材高1~2倍甚至更高。
序,是撑握质量,售后服务的关键因素,是产品形 象的重要窗口。 | 员工的使命感尤为重要。
吐丝机吐丝后散冷线的剪头剪尾:
负责操作运输辊,将成品运送到下一 道工序,以及冷却风机对成品的冷却;对 风冷线内成品出现头尾乱的盘卷进行和对 吐丝机吐丝情况的观察,发现异常不能满足 下道工序的,要及时通知轧线人员进行调整。
(2) 检查链条传动是否正常 (3).电机及电机有否异常振动及杂音 (4)链条是否润滑良好 特殊操作
1临时紧急停机,按下就地操作箱急停按钮,并报告调度。 2正常停机操作须待线卷走过辊道之后才能停机。 3出现吐丝机吐丝不好和卷径不能满足下一工序要及时通知轧线
进行调整,并报告调度。 4当运输辊道出现故障,不能正常运行,以及钢卡在辊道内时,要及