金创公司精益培训教材七大浪费
车间班组长7大浪费培训教材

七大浪费
浪费的种类
浪费的种类 制造过多的浪费 等待的浪费 搬运的浪费 加工的浪费 库存的浪费 动作的浪费 制作不良的浪费
七大浪费
1.制造过多的浪费
无法保证可卖出的产品做了太多
表现形式:
物流阻塞 库存、在制品增加 产品积压造成不良发生 资金回转率低 材料、零件过早取得 影响计划弹性及生产系统的适应能力
1.制造过多的浪费
1.制造过多的浪费
前提: 6月份金客订单由原先5980台降到5500台,公司的生产稼动偏低,近期又决定6月23日~6月30日停产休假,造成我公司库存品积压过多,生产能力过剩。
生产的调配方案: 窗框班每班借出5人至硬包边班, 由13人生产窗框,标时30pcs/hr 前桥线抽调两人至滑道线,12hr 生产
是浪费的源头
3.“七大浪费”之详介
适时的生产
J IT生产方式
七大浪费
1.制造过多的浪费
制造过多是一种浪费的原因:
只是提前用掉了费用(材料费、人工费)而已,并 无其它好处 会把等待的浪费隐藏起来,掩盖稼动不够的问题 会使制程间积压在制品,制程时间变长,现场工作 空间变大 会产生搬运、堆积的浪费 使先进先出的工作产生困难 会造成库存空间的浪费
4.消除浪费的做法
五原则:
三现:
现场 现物 现状
现场浪费的案例
浪费的实例
DW1114生产线布局
消除“七大浪费”
单击此处添加副标题
管理基础
引言
动作改善、作业流程改善、物流改善、设备模夹治具改善、品质改善、管理改善等
七大浪费、三无工程等
动作标准化、作业流程标准化、操作流程标准化、包装运输标准化等
整理、整顿、清扫、清洁、素养等
精益生产管理中的7大浪费

生产管理中的“七大浪费”定义与说明生产管理中的“七大浪费”,懂精益生产的人都知道,就是不良品,超量生产,库存,搬运,多余的工序,不必要的调动,等待。
一、库存浪费◆精益生产认为:“库存是万恶之源”,所有改善行动皆会与直接或间接地和消除库存有关①产生不必要的搬运、堆积、放置、防护处理、找寻等浪费②使先进先出的作业困难③损失利息及管理费用④物品的价值会减低,变成呆滞品⑤占用厂房空间、造成多余工场、仓库建设等⑥设备能力及人员需求的误判◆因库存造成无形损失,绝不亚于上述有形损失,精益生产者认为库存会隐藏问题,而“问题”在精益生产者被认为是宝藏,问题如果能不断地被发现解决,则利益便会不断地产生1、没有管理的紧张感,阻碍改进2、库存量一多,因机械故障、不良产品所带来的不利后果不能马上显现出来,因而也不会产生对策3、由于有了充足的库存,出现问题时可以用库存先顶上,问题就可以慢慢解决甚至不用解决,最起码是被掩盖住了,不急迫了,不会被上级追究了,于是乎本部门的工作成绩就出来了二、过渡生产(制造过多或过早浪费)◆TPS强调的是“适时生产”◆多做能提高效率,提早做好能减少产能损失(不做白不做,机器还不是一样停着?)1、提早用掉了材料费、人工费而已,并不能得到什么好处2、把“等待浪费”隐藏,使管理人员漠视等待的发生和存在3、积压在制品,使生产周期L/T变长(无形的),而且会使现场工作空间变大,不知不觉吞蚀我们的利润4、产生搬运、堆积浪费,先进先出变得困难三、品质缺陷(不良品浪费)◆任何的不良品产生,皆会造成材料、机器、人工等的浪费◆及早发现不良品,容易确定不良来源,进而减少不良品的产生◆关键是第一次要把事情做对,“零缺陷”四、运输(搬运浪费)◆大部分人皆认同搬运是一种无效的动作,也有人认为搬运是必须的◆用“输送带”的方式来克服,行吗?1、取放浪费;2、等待浪费;3、在制品过多浪费;4、空间浪费◆搬运浪费又包含放置、堆积、移动、整理等动作的浪费五、处理(加工浪费)◆定义:指的是与工程进度及加工精度无关的不必要的加工◆有一些加工程序是可以省略、替代、重组或合并◆很多时候会习惯并认为现在的做法较好六、动作浪费12种动作浪费:◆两手空闲◆单手空闲◆不连贯停顿◆幅度太大◆左右手交换◆步行多◆转身角度大◆移动中变换状态◆不明技巧◆伸背动作◆弯腰动作◆重复不必要动作七、等待浪费◆生产线的品种切换◆工作量少时,便无所事事◆时常缺料,设备闲置◆上工序延误,下游无事可做◆设备发生故障◆生产线工序不平衡◆有劳逸不均的现象◆制造通知或设计图未送达。
精益生产的七大浪费概述

精益生产的七大浪费概述精益生产是一种管理哲学和方法论,旨在通过消除浪费来提高生产效率和质量。
在精益生产中,有七大浪费被广泛认可,包括:1. 运动:指的是任何不必要的移动或行动,例如工人需要频繁移动到不同的工作区域以完成任务。
精益生产鼓励将工作站布置得合理,以减少不必要的运动,从而提高效率。
2. 待料:指的是生产过程中等待原材料、工具或设备供应的时间。
这种等待会导致生产线停滞,降低生产效率。
精益生产鼓励将供应链优化,以减少待料时间。
3. 过产量:指的是生产超过需求的产品,或者在产品的某个阶段生产过多的零件。
过产量会导致库存积压、成本上升,甚至可能导致产品过期。
精益生产鼓励按需生产,以避免过产量的浪费。
4. 等待:指的是生产过程中因为等待其他任务完成而导致的停滞时间。
这种等待会导致生产线的延迟和低效。
精益生产鼓励优化工艺流程,减少等待时间。
5. 过度加工:指的是对产品进行超出需求或规格要求的加工步骤。
过度加工会增加生产成本和时间。
精益生产鼓励消除不必要的加工步骤,以提高效率和降低成本。
6. 错误:指的是在生产过程中出现的错误或瑕疵,例如产品缺陷或错误装配。
这些错误会导致废品产生和重工成本增加。
精益生产鼓励通过质量控制和错误预防来减少错误的发生。
7. 运输:指的是产品或物料在生产过程中频繁移动或运输的浪费。
这种浪费会增加时间和成本,同时也增加了损坏产品的风险。
精益生产鼓励优化布局和流程,减少不必要的运输。
通过有效地识别和消除这七大浪费,精益生产能够提高生产效率、降低成本,并提供更高质量的产品。
精益生产鼓励组织和管理层始终关注价值流,并持续改进以实现更高的效率和竞争力。
精益生产是一种以消除浪费为核心的管理哲学和方法论,旨在提高生产效率和质量。
在精益生产中,有七大浪费被广泛认可,并成为了改善生产流程的重要依据。
这七大浪费是运动、待料、过产量、等待、过度加工、错误和运输。
首先,运动是指不必要的移动或行动。
在生产过程中,员工频繁移动到不同的工作区域以完成任务会增加生产时间和劳动成本。
一文带你了解精益生产管理的七大浪费及七大对策
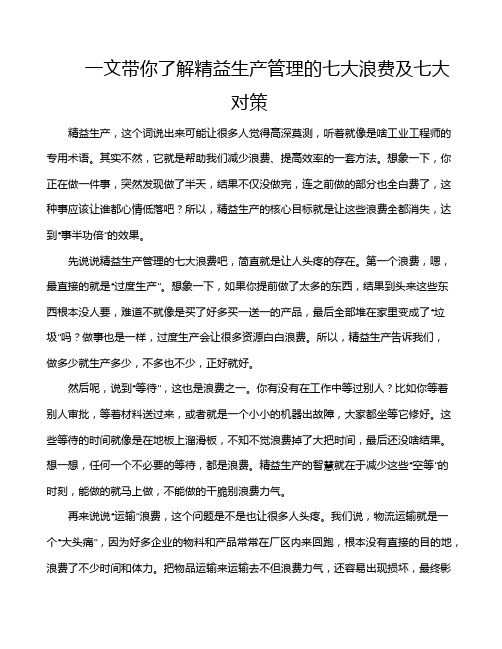
一文带你了解精益生产管理的七大浪费及七大对策精益生产,这个词说出来可能让很多人觉得高深莫测,听着就像是啥工业工程师的专用术语。
其实不然,它就是帮助我们减少浪费、提高效率的一套方法。
想象一下,你正在做一件事,突然发现做了半天,结果不仅没做完,连之前做的部分也全白费了,这种事应该让谁都心情低落吧?所以,精益生产的核心目标就是让这些浪费全都消失,达到“事半功倍”的效果。
先说说精益生产管理的七大浪费吧,简直就是让人头疼的存在。
第一个浪费,嗯,最直接的就是“过度生产”。
想象一下,如果你提前做了太多的东西,结果到头来这些东西根本没人要,难道不就像是买了好多买一送一的产品,最后全部堆在家里变成了“垃圾”吗?做事也是一样,过度生产会让很多资源白白浪费。
所以,精益生产告诉我们,做多少就生产多少,不多也不少,正好就好。
然后呢,说到“等待”,这也是浪费之一。
你有没有在工作中等过别人?比如你等着别人审批,等着材料送过来,或者就是一个小小的机器出故障,大家都坐等它修好。
这些等待的时间就像是在地板上溜滑板,不知不觉浪费掉了大把时间,最后还没啥结果。
想一想,任何一个不必要的等待,都是浪费。
精益生产的智慧就在于减少这些“空等”的时刻,能做的就马上做,不能做的干脆别浪费力气。
再来说说“运输”浪费,这个问题是不是也让很多人头疼。
我们说,物流运输就是一个“大头痛”,因为好多企业的物料和产品常常在厂区内来回跑,根本没有直接的目的地,浪费了不少时间和体力。
把物品运输来运输去不但浪费力气,还容易出现损坏,最终影响产品质量。
谁都知道,一旦物料堆得满满当当,反而什么都做不成。
精益生产告诉我们,越短的运输路径越好,避免无效搬运,这样才能事半功倍。
接下来是“加工”浪费。
这个就很容易理解了,不是每个生产过程都可以做到100%完美,很多时候因为操作失误、设备不合适或者设计缺陷,做出来的东西还得重做或者调整。
比如你做饭,搞了半天,结果菜烧焦了,不得不重新开始,是不是心情瞬间崩塌?精益生产教我们,要精益求精,避免不必要的“返工”,做到一次到位,减少无用功。
精益生产中的七大浪费及改善方法
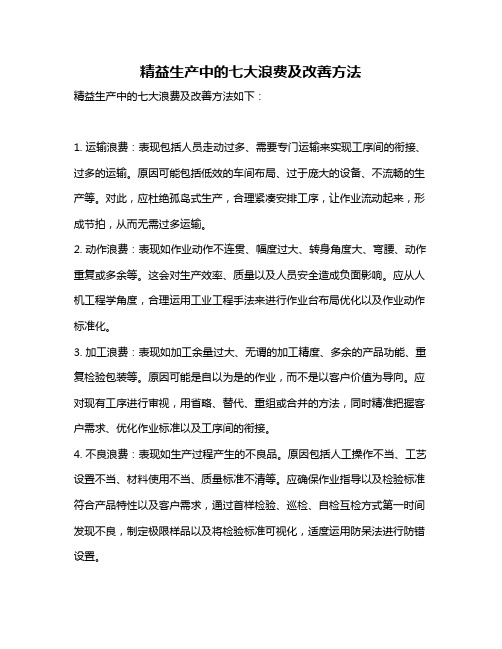
精益生产中的七大浪费及改善方法精益生产中的七大浪费及改善方法如下:1. 运输浪费:表现包括人员走动过多、需要专门运输来实现工序间的衔接、过多的运输。
原因可能包括低效的车间布局、过于庞大的设备、不流畅的生产等。
对此,应杜绝孤岛式生产,合理紧凑安排工序,让作业流动起来,形成节拍,从而无需过多运输。
2. 动作浪费:表现如作业动作不连贯、幅度过大、转身角度大、弯腰、动作重复或多余等。
这会对生产效率、质量以及人员安全造成负面影响。
应从人机工程学角度,合理运用工业工程手法来进行作业台布局优化以及作业动作标准化。
3. 加工浪费:表现如加工余量过大、无谓的加工精度、多余的产品功能、重复检验包装等。
原因可能是自以为是的作业,而不是以客户价值为导向。
应对现有工序进行审视,用省略、替代、重组或合并的方法,同时精准把握客户需求、优化作业标准以及工序间的衔接。
4. 不良浪费:表现如生产过程产生的不良品。
原因包括人工操作不当、工艺设置不当、材料使用不当、质量标准不清等。
应确保作业指导以及检验标准符合产品特性以及客户需求,通过首样检验、巡检、自检互检方式第一时间发现不良,制定极限样品以及将检验标准可视化,适度运用防呆法进行防错设置。
5. 等待浪费:表现如人员(以及设备)在等待,或者有时忙、有时闲的不均衡现象。
原因如生产线品种切换、工作量少、时常缺料、设备闲置等。
应实施生产均衡化,快速换模技术的运用,全员生产性防护,多技能工,消除不良浪费,提升供应商水准。
6. 过量生产:这是常被视为最大的浪费。
其结果导致库存、资金的占用以及潜在的报废风险。
应形成一个流、节拍化生产。
“一个流生产”是指从毛坯投入成品产出的整个制造加工过程,零件始终处于不停滞、不堆积、不超越的状态。
每道工序加工完一个制件后立即流到下一工序;工序间的在制品数量不超过前工序的装夹数量。
零件的运动不间断、不超越、不落地。
只有合格的产品才允许往下一道工序流。
节拍化生产要求是需求节拍与生产节拍平衡。
精益生产认识之七大浪费培训
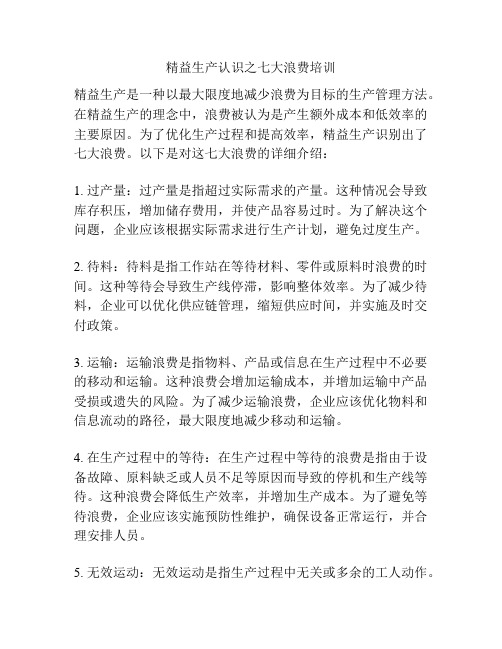
精益生产认识之七大浪费培训精益生产是一种以最大限度地减少浪费为目标的生产管理方法。
在精益生产的理念中,浪费被认为是产生额外成本和低效率的主要原因。
为了优化生产过程和提高效率,精益生产识别出了七大浪费。
以下是对这七大浪费的详细介绍:1. 过产量:过产量是指超过实际需求的产量。
这种情况会导致库存积压,增加储存费用,并使产品容易过时。
为了解决这个问题,企业应该根据实际需求进行生产计划,避免过度生产。
2. 待料:待料是指工作站在等待材料、零件或原料时浪费的时间。
这种等待会导致生产线停滞,影响整体效率。
为了减少待料,企业可以优化供应链管理,缩短供应时间,并实施及时交付政策。
3. 运输:运输浪费是指物料、产品或信息在生产过程中不必要的移动和运输。
这种浪费会增加运输成本,并增加运输中产品受损或遗失的风险。
为了减少运输浪费,企业应该优化物料和信息流动的路径,最大限度地减少移动和运输。
4. 在生产过程中的等待:在生产过程中等待的浪费是指由于设备故障、原料缺乏或人员不足等原因而导致的停机和生产线等待。
这种浪费会降低生产效率,并增加生产成本。
为了避免等待浪费,企业应该实施预防性维护,确保设备正常运行,并合理安排人员。
5. 无效运动:无效运动是指生产过程中无关或多余的工人动作。
这种浪费会造成不必要的体力消耗和生产时间延长。
为了减少无效运动浪费,企业应该优化工作站布局和工作流程,确保工人只进行必要的动作。
6. 过度加工:过度加工是指对产品进行超出要求的处理或处理步骤。
这种浪费会增加生产成本,同时也会延长生产周期。
为了避免过度加工浪费,企业应该对产品和工艺进行分析,找出不必要的加工步骤,并进行精简。
7. 库存:库存浪费是指过多或无用的库存。
这种浪费会增加资金占用和储存成本,并增加产品过时或损坏的风险。
为了减少库存浪费,企业应该实施准时生产和准时交付政策,并优化库存管理。
通过认识和理解这七大浪费,企业可以发现潜在的问题并采取相应的措施来减少浪费,提高生产效率和质量。
精益生产七大浪费

精益生产七大浪费在生产制造过程中,精益生产理论认为,存在着许多的浪费以及不必要的消耗,这些都会导致生产成本的增加,同时也使得生产效率得不到发挥,生产出来的产品也不能够达到最佳品质。
因此,精益生产理论提出了七大浪费,企业在生产制造过程中要尽力消除这些浪费,以提高效率和降低成本。
一、运输浪费:运输浪费指在物料运输过程中出现的不必要的搬运、装卸等环节。
企业应该尽量使用物料直接从生产线到达下一个工作站,从而避免因为不必要的运输而浪费时间和人力成本。
二、库存浪费:库存浪费指生产过程中存在的多余的材料、零部件或者产成品的储存问题。
因为多余的库存不仅浪费资金,而且会使得库存产品过期损坏或者占用大量的仓库空间,从而影响生产的顺畅。
三、动作浪费:动作浪费指在生产过程中存在的不必要的动作、分步操作等问题。
企业应该尽可能地精简工艺流程,避免重复的动作过程,从而减少不必要的动作浪费。
四、等待浪费:等待浪费指在生产过程中因为暂时没有物料、设备或者人员需要等待的时间浪费。
企业应该及时安排生产计划,避免不必要的等待时间,从而有效降低等待浪费。
五、加工浪费:加工浪费指因为产品设计或者操作问题造成的不必要的加工步骤、加工时间等问题。
企业需要加强与设计方面的沟通,避免因为设计问题造成生产加工浪费。
六、过度加工浪费:过度加工浪费指在生产过程中过度加工的产品或者组件,这会导致生产成本和加工周期的增加。
企业应该确保生产出的产品满足设计规范以及客户的需求,从而避免过度加工浪费。
七、废品浪费:废品浪费指在生产过程中出现的废品或者不良品,这会导致原材料以及制造成本的增加,同时也影响了产品的质量和信誉。
企业应该加强品质管理的力度,尽可能降低废品率,从而避免废品浪费的出现。
综上所述,精益生产理论的七大浪费都是可以避免的,企业在生产制造过程中应该加强对于生产环节的管理,尽量减少不必要的浪费,从而提高生产效率和产品质量,实现企业的可持续发展。
精益管理七大浪费

03
激励机制:设立持续 改进的激励机制,鼓 励员工参与
04
持续沟通:建立持续 改进的沟通渠道,及 时反馈问题和建议
05
持续改进计划:制定 持续改进的计划,明 确目标和方法
06
持续改进成果展示: 展示持续改进的成果, 激发员工积极性
持续改进的方法和工具
持续改进的方法:PDCA循环、六西格玛、 精益生产、持续改进计划
05
跟踪评估:对实施计划进行 跟踪和评估,确保消除浪费 的效果得到持续改善
02
制定目标:设定消除浪费的 目标和期限
04
实施计划:按照制定的方案, 分阶段、分步骤实施消除浪 费的计划
实施消除浪费的措施
01
识别浪费: 识别并记录 生产过程中 的浪费现象
02
制定计划: 制定消除浪 费的具体计
划和措施
03
培训员工: 对员工进行 消除浪费的 培训和教育
04
持续改进: 持续改进生 跟踪评估消 除浪费的效 果,并进行 调整和优化
评估消除浪费的效果
设定明确的目标:明确消除 浪费的目标和预期效果
01
收集数据:收集与消除浪费
相关的数据,如时间、成本、 03
质量等
持续改进:根据分析结果,
生产过剩:生产过多或过早, 导致库存积压
等待浪费:等待材料、设备 或人员,导致时间浪费
运输浪费:不必要的运输, 导致时间和成本的浪费
过度加工:不必要的加工, 导致时间和成本的浪费
库存浪费:过多的库存,导 致时间和空间的浪费
动作浪费:不规范的操作, 导致时间和效率的浪费
管理浪费:不合理的管理制 度,导致时间和资源的浪费
浪费的负面影响
增加成本:浪费导致 生产成本上升,降低
精益生产概述之七大浪费

精益生产概述之七大浪费精益生产是一种以消除浪费为核心的生产管理方法,旨在提高生产效率和质量。
七大浪费是精益生产的基本概念之一,它们是指在生产过程中存在的七种浪费现象,并且这些浪费都可以避免或减少。
以下是对七大浪费的简要概述。
1. 运输浪费:指在生产过程中不必要的物料运输或移动,例如将产品从一个车间搬到另一个车间,或者将材料从仓库搬到生产线。
运输浪费会增加生产时间和成本,并容易引起损坏或丢失。
2. 库存浪费:指生产过程中积压的过多原材料、半成品或成品库存。
库存浪费会增加库房和仓储成本,还可能导致过期、损坏或过时的物料。
3. 过程中的等待浪费:指在生产过程中由于机器故障、零部件不足或工人等待等原因导致的停工或非生产时间。
等待浪费会降低生产效率,增加生产周期,并导致交货延迟。
4. 过度加工浪费:指在生产过程中对产品进行过多或不必要的加工。
过度加工浪费会增加生产成本,并可能导致质量问题或产品过度精细化。
5. 度量浪费:指在生产过程中由于测量、追踪或监控不足导致的效率低下或质量问题。
度量浪费会增加错误率和修复成本,并且可能导致产品不符合客户要求。
6. 过剩生产浪费:指生产过程中超出客户需求的产品或数量。
过剩生产浪费会增加库存和仓储成本,并降低资金周转率。
7. 动作浪费:指生产过程中不必要的动作或无效的动作,包括重复、走动、等待、纠正错误等。
动作浪费会降低工人的效率和舒适度,增加生产时间和成本。
精益生产的目标是通过识别和消除这些浪费,提高生产效率和质量,实现产品的快速交付和客户满意度的提升。
通过精益生产的实施,企业可以提高生产线的流程,优化生产方式,减少生产成本,并最大限度地提高企业的竞争力和盈利能力。
精益生产的实施需要从各个方面入手,包括流程优化、员工参与和培训、设备改进等。
下面将进一步探讨精益生产的相关内容,以及其对企业的影响和益处。
首先,要实施精益生产,必须对生产流程进行优化。
通过识别和消除七大浪费,可以简化生产流程,降低生产周期,并提高产品的质量和交货效率。
精益生产七大浪费

1.直接的财务问题。说明库存和在制品增加,资金周转率低,制造时间变长,资金和利息被占用, 会造成库存空间的浪费,这在现金流量表中是很明显的。
2.产生次要问题。搬运和堆积会产生废物;先进先出的工作造成困难;产品积压导致不良品的发生, 物流阻断过程时间变长,现场工作空间变小,存在滞留仓库的风险和不良品的风险。
1. 优化工艺流程,对生产流程进行全面分析,找出其中的瓶颈和不必要的环节,进行优化和改进。 采用更高效的加工方法和设备,减少加工时间和工序。 2. 减少调整时间,通过标准化作业、快速换模等技术手段,减少设备调整和准备时间,提高设备的 利用率。 3. 提高加工精度,采用先进的加工技术和设备,提高加工精度,减少废品和返工,降低加工成本。 4. 引入自动化和智能化,利用自动化设备和智能化系统,提高生产的自动化水平,减少人工干预, 降低加工误差和浪费。 5. 加强质量控制,建立严格的质量控制体系,对原材料、半成品和成品进行严格检测,确保产品质 量符合标准,减少因质量问题导致的加工浪费。 6. 培训员工,加强员工培训,提高员工的技能水平和质量意识,使他们能够熟练掌握加工工艺和操 作方法,减少因操作不当导致的浪费。 7. 持续改进,建立持续改进的机制,鼓励员工提出改进建议,不断优化加工过程,提高生产效率和
5.建立持续改进文化
建立持续改进文化是实现精益生产的关键之一。通过建立持续改进文化,可以使员工充分认识到 浪费的危害和价值,从而积极参与到消除浪费的行动中来。例如,可以定期组织员工进行交流和 分享经验,以提高员工对精益生产的认识和实践水平。
(三)不良品的浪费
(1)不良品浪费对企业生产经营产生了诸多不利影响: (2)成本增加:不良品的产生会增加原材料、人力、设备等资源的浪费,导致生产成本的 增加。 (3)产能降低:不良品的产生会导致生产线停机、返工时间增加,进而降低了企业的产能。 (4)产品质量下降:不良品的产生会影响产品的质量,降低了产品的市场竞争力。 (5)顾客满意度下降:不良品的产生会导致交货延迟、产品质量问题等,降低了顾客的满 意度。
消除七大浪费培训资料

消除七大浪费培训资料在企业的生产与运营过程中,往往存在着各种形式的浪费,这些浪费不仅增加了成本,降低了效率,还影响了产品质量和企业的竞争力。
为了实现精益生产,提高企业的效益,我们有必要深入了解并消除“七大浪费”。
一、什么是七大浪费1、过量生产的浪费过量生产是指生产出比需求更多的产品,导致库存积压。
这不仅占用了资金和空间,还增加了管理成本和质量风险。
例如,某工厂为了提高设备利用率,不顾市场需求,大量生产某种产品,结果造成库存积压,产品滞销。
2、等待的浪费等待的浪费包括人员等待、设备等待、物料等待等。
比如,在生产线上,前一道工序未完成,导致后一道工序的工人和设备处于等待状态;或者设备故障维修时,整个生产线停滞。
3、运输的浪费运输的浪费是指不必要的物料搬运和产品运输。
例如,工厂布局不合理,导致物料在车间内频繁搬运;或者为了将产品从一个仓库转移到另一个仓库,进行了不必要的运输。
4、过度加工的浪费过度加工是指对产品进行超出客户需求或标准的加工,增加了生产成本但并未带来价值的提升。
比如,为产品增加一些不必要的装饰或功能,导致加工时间和成本增加。
5、库存的浪费库存不仅包括成品库存,还包括原材料库存、在制品库存等。
大量库存会掩盖生产过程中的问题,如质量缺陷、设备故障等,同时也增加了资金占用和库存管理成本。
6、动作的浪费动作的浪费是指员工在工作中不必要的动作,如弯腰、转身、寻找工具等。
这些动作不仅浪费时间和体力,还可能导致疲劳和错误。
7、不良品的浪费不良品的产生意味着原材料、人工和设备等资源的浪费。
而且,不良品还可能需要返工或报废,进一步增加了成本。
二、七大浪费产生的原因1、生产计划不合理不准确的市场预测、不合理的生产排程,导致过量生产或生产不足。
2、流程不完善生产流程存在缺陷,工序之间不协调,容易出现等待和运输的浪费。
3、设备维护不当设备故障频繁,维修时间长,影响生产效率,造成等待浪费。
4、员工培训不足员工技能水平低,操作不熟练,容易出现动作浪费和不良品浪费。
详解精益生产的七大浪费

详解精益生产的七大浪费①物料供应不及或前一道工序的能力不足,导致停工待料;②检验作业的过程中,虽然能够管控产品的品质,但是检验时,造成后道工序作业停顿;③因设备故障造成生产停顿、因发现品质问题造成停工待料;④生产型号切换造成生产停顿。
比如一个生产鞋子的工厂,在生产线的传送带上画一个网格。
正常生产时,每格要放一双鞋。
假设生产时中间有很多网格,说明之前的生产过程肯定有问题。
这时候生产线的主管要尽早处理,减少等待浪费。
2.搬运浪费在搬运过程中产生过多的放置、堆积、移动、整理,不仅费时费力,同时会造成搬运上的浪费。
例如:一间公司生产线的布置.从铸造到磨床,磨床之后到铣床,铣床之后到钻床,接着到焊接,最后到涂装部,完成之后进行检验,检验合格之后才送到包装部进行包装,最后入库。
在这些过程中,移动的次数高达八次之多,所以,在整个流程中,我们应该思考如何减少搬运次数,如何缩短搬运距离,其中,工厂的布置就显得尤为重要。
3.不良浪费在生产过程中,不可避免地会出现产品质量差的情况,而这些差的情况又会造成额外的成本,比如材料的损耗、设备的折旧、劳动力的损耗等。
这时候产品的价格也会受到影响,也许订单会流失,甚至公司的声誉也会受损。
这时候就要利用一系列的检验,比如进货检验、过程检验、产品检验(出货检验),把不良品降到最低,减少不良浪费。
4.动作浪费多余的动作会增加我们的工作强度,降低生产效率。
常见的12个浪费动作是:两只手闲着,一只手闲着,作业停止,动作幅度过大,左右手互换,走路过多,转弯角度过大,边走边换动作,作业技巧没有掌握,背伸动作,弯腰动作,重复或不必要的动作。
有些公司在生产线组装的时候,每道工序的移转都必须要借助一个用手按按键的动作,让每道工序的完成品得以转移到下一个工序,所以,“用手按按键”这个动作就是浪费。
假如今天不用手,改用脚来按按键,就能够移转到下一道工序,这时双手还能持续进行组装的动作,这样就不会造成动作的浪费。
精益生产之七大浪费及5S管理
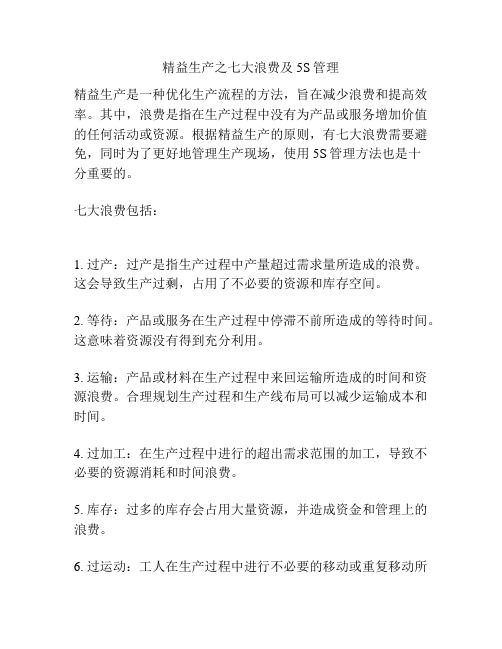
精益生产之七大浪费及5S管理精益生产是一种优化生产流程的方法,旨在减少浪费和提高效率。
其中,浪费是指在生产过程中没有为产品或服务增加价值的任何活动或资源。
根据精益生产的原则,有七大浪费需要避免,同时为了更好地管理生产现场,使用5S管理方法也是十分重要的。
七大浪费包括:1. 过产:过产是指生产过程中产量超过需求量所造成的浪费。
这会导致生产过剩,占用了不必要的资源和库存空间。
2. 等待:产品或服务在生产过程中停滞不前所造成的等待时间。
这意味着资源没有得到充分利用。
3. 运输:产品或材料在生产过程中来回运输所造成的时间和资源浪费。
合理规划生产过程和生产线布局可以减少运输成本和时间。
4. 过加工:在生产过程中进行的超出需求范围的加工,导致不必要的资源消耗和时间浪费。
5. 库存:过多的库存会占用大量资源,并造成资金和管理上的浪费。
6. 过运动:工人在生产过程中进行不必要的移动或重复移动所造成的浪费。
此外,工作场所的布局也可能导致不必要的运动。
7. 失效:产品或设备因为质量问题或故障导致不能正常使用所带来的浪费。
这包括废品、次品和修理等。
为了管理生产现场,5S管理方法可以帮助提高工作效率和质量。
5S分别代表整理、整顿、清扫、清洁和遵守。
1. 整理:整理工作场地,确定需要的物品和设备并清除不需要的物品。
2. 整顿:确定合理的工作流程和布局,确保工作区域的物品和设备放置得井井有条。
3. 清扫:保持工作区域的清洁和整洁,确保工作环境安全和舒适。
4. 清洁:定期进行清洁工作,包括设备和机器的保养和维护,以确保其正常运行。
5. 遵守:遵守标准和规定,执行工作流程,并及时纠正和改进。
精益生产的目标是通过减少浪费和提高效率来提供更高质量的产品和服务。
而5S管理方法可以帮助企业管理生产现场,提高工作效率和质量。
通过合理应用这些原则和方法,企业可以提升竞争力,并更好地满足客户需求。
精益生产的目标是通过减少浪费和提高效率来提供更高质量的产品和服务。
精益生产之七大浪费及5S管理
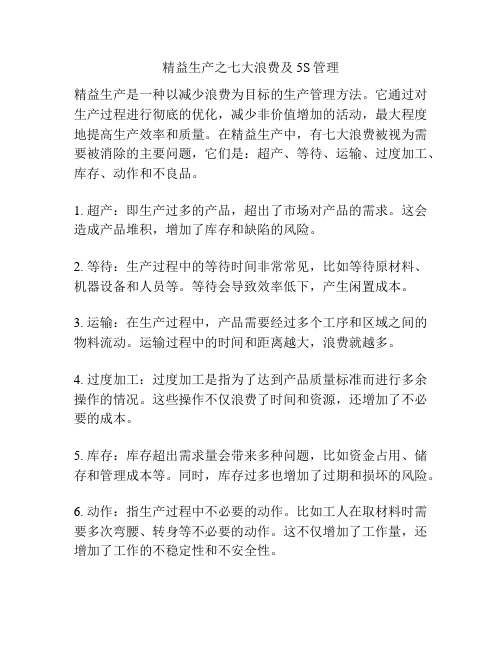
精益生产之七大浪费及5S管理精益生产是一种以减少浪费为目标的生产管理方法。
它通过对生产过程进行彻底的优化,减少非价值增加的活动,最大程度地提高生产效率和质量。
在精益生产中,有七大浪费被视为需要被消除的主要问题,它们是:超产、等待、运输、过度加工、库存、动作和不良品。
1. 超产:即生产过多的产品,超出了市场对产品的需求。
这会造成产品堆积,增加了库存和缺陷的风险。
2. 等待:生产过程中的等待时间非常常见,比如等待原材料、机器设备和人员等。
等待会导致效率低下,产生闲置成本。
3. 运输:在生产过程中,产品需要经过多个工序和区域之间的物料流动。
运输过程中的时间和距离越大,浪费就越多。
4. 过度加工:过度加工是指为了达到产品质量标准而进行多余操作的情况。
这些操作不仅浪费了时间和资源,还增加了不必要的成本。
5. 库存:库存超出需求量会带来多种问题,比如资金占用、储存和管理成本等。
同时,库存过多也增加了过期和损坏的风险。
6. 动作:指生产过程中不必要的动作。
比如工人在取材料时需要多次弯腰、转身等不必要的动作。
这不仅增加了工作量,还增加了工作的不稳定性和不安全性。
7. 不良品:生产出的不良产品无法被销售,这会导致浪费资源和劳动力。
为了减少这些浪费,精益生产倡导使用5S管理方法。
5S是指整理(Seiri)、整顿(Seiton)、清扫(Seiso)、清洁(Seiketsu)和素养(Shitsuke)。
- 整理:将工作场所中无用的东西清除出去,只保留必要的物品。
- 整顿:将工作场所中的物品有序地摆放,方便取用。
为每个物品设立明确的标识。
- 清扫:保持工作场所的清洁,清除尘土和垃圾。
维持一个良好的工作环境。
- 清洁:对设备、工具和工作区域进行定期的清洁和维护,确保其正常运行。
- 素养:让员工养成良好的工作习惯和态度,培养责任心和自我管理能力。
通过5S管理,可以降低生产过程中的浪费,提高工作效率和质量。
它强调提高工作环境和员工意识,促进生产过程的规范化、标准化和自律化。
精益生产七大浪费口诀
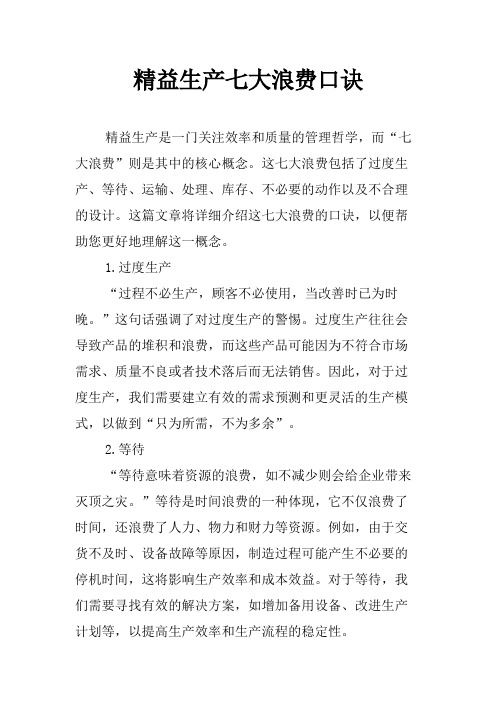
精益生产七大浪费口诀精益生产是一门关注效率和质量的管理哲学,而“七大浪费”则是其中的核心概念。
这七大浪费包括了过度生产、等待、运输、处理、库存、不必要的动作以及不合理的设计。
这篇文章将详细介绍这七大浪费的口诀,以便帮助您更好地理解这一概念。
1.过度生产“过程不必生产,顾客不必使用,当改善时已为时晚。
”这句话强调了对过度生产的警惕。
过度生产往往会导致产品的堆积和浪费,而这些产品可能因为不符合市场需求、质量不良或者技术落后而无法销售。
因此,对于过度生产,我们需要建立有效的需求预测和更灵活的生产模式,以做到“只为所需,不为多余”。
2.等待“等待意味着资源的浪费,如不减少则会给企业带来灭顶之灾。
”等待是时间浪费的一种体现,它不仅浪费了时间,还浪费了人力、物力和财力等资源。
例如,由于交货不及时、设备故障等原因,制造过程可能产生不必要的停机时间,这将影响生产效率和成本效益。
对于等待,我们需要寻找有效的解决方案,如增加备用设备、改进生产计划等,以提高生产效率和生产流程的稳定性。
3.运输“不必要的运输是现代生产的大敌。
”运输是生产过程中的必要环节,但也可能带来不必要的浪费。
例如,因为原材料和产品的运输而导致的等待和停机,以及运输过程中可能产生的损耗和质量问题。
因此,我们需要优化物流系统,缩短运输距离并降低运输成本,以提高生产效率和产品质量。
4.处理“在制造过程中避免处理,欢迎设备运行。
”处理是指在生产过程中需要对产品进行加工、检验、修复等处理,但这些处理可能会浪费时间、资源和质量。
处理不必要的问题通常是因为设计不足或者设备过时。
因此,我们需要改进生产流程并采用现代化的设备和工具,以减少处理次数和提高处理质量。
5.库存“库存过多,等待必定。
”库存是为满足客户需求而存储的产品和原材料,在库存管理不当的情况下,可能会带来许多成本和质量问题。
例如,库存过多会增加物料和产品的损耗、质量问题和过期等问题,同时也会占用企业的物流和仓储资源,增加成本。
精益生产之七种浪费培训

精益生产之七种浪费培训精益生产是一种管理方法,旨在通过减少浪费来提高生产效率和质量。
在精益生产中,有七种被认为是浪费的元素,被称为七种浪费。
这些浪费分别是:1. 运输浪费:指产品或材料在生产过程中的不必要的运输。
这种浪费会消耗时间和资源,并增加出错的可能性。
例如,将原材料从一个生产线运输到另一个生产线,或者将成品从一个仓库运输到另一个仓库。
2. 库存浪费:指过多的库存,不仅占用了宝贵的空间,还需要额外的成本来维护和管理。
过多的库存也意味着产品无法及时交付给客户,增加了交货延迟和过度备货的风险。
3. 过程浪费:指不必要的生产步骤、繁琐的操作和不必要的等待时间。
这些浪费会增加生产周期,并使生产过程变得低效。
4. 超生产浪费:指生产出了超过需求的产品数量。
这种浪费会导致产品堆积在仓库中,没有销售出去,并占用宝贵的资源和资金。
5. 劳动力浪费:指员工的不必要的等待、无效的运动和重复的工作。
这些浪费会降低员工的效率,同时也会对员工的士气和工作满意度产生负面影响。
6. 缺陷浪费:指产品在生产过程中出现的缺陷或错误。
缺陷会导致产品返工或废品产生,增加了成本和生产周期。
7. 不必要的处理浪费:指在生产过程中进行的不必要的操作和处理。
这些操作可能是由于过度设计、不正确的工艺或无效的工作方法引起的,会增加生产成本和工作时间。
通过了解和识别这七种浪费,企业可以采取相应的措施来降低或消除浪费,提高生产效率和质量。
这可能包括改善生产流程、优化库存管理、培训员工以提高技能和意识,以及推动持续改进的文化和实践。
精益生产的目标是实现高效率、高质量、高价值的生产,从而提高企业的竞争力和持续发展能力。
通过消除浪费,企业能够更好地满足客户需求,提供更好的产品和服务,同时也能够降低成本、提高利润和创造更可持续的发展。
在精益生产中,减少浪费是一项重要的任务。
通过减少浪费,企业可以提高生产效率、降低成本,并提供更优质的产品和服务。
下面我们来详细介绍如何应对这七种浪费。
精益生产之七大浪费培训资料

精益生产之七大浪费培训资料1. 引言精益生产是一种以尽量减少浪费为目标的生产管理方法,通过优化流程、降低成本和提高质量,使企业在现有资源的基础上实现最大化价值创造。
其中,七大浪费是指造成资源浪费的七种常见情况,包括过度生产、库存过多、运输过程中的浪费、等待时间、不必要的动作、生产过程中的瑕疵、不合理的处理。
本文档将详细介绍七大浪费的概念、影响以及如何通过精益生产的方法来减少浪费。
2. 七大浪费的定义和影响2.1 过度生产过度生产是指超过实际需求生产产品的现象,导致产品积压、资金占用过多等问题。
这不仅浪费了人力、物力和财力资源,还会增加库存成本和废品损失。
通过精益生产的方式,可以合理预测和控制产品需求,以及优化生产计划,减少过度生产的情况。
2.2 库存过多库存过多是指在生产过程中或者生产完成后,产品的库存量超出正常范围的现象。
过多的库存不仅会造成资金占用,还可能导致产品质量下降、过期损失等问题。
通过精益生产的方法,可以通过精确的需求预测、合理的生产计划以及及时的供应链管理来降低库存过多的情况。
2.3 运输过程中的浪费运输过程中的浪费主要指的是物料在运输过程中因为不必要的移动、重复搬运等问题而造成的资源浪费。
精益生产的方法可以通过优化物流流程、减少不必要的运输环节来降低运输过程中的浪费。
2.4 等待时间等待时间是指产品或者物料在生产过程中由于资源不足、任务排队等原因而产生的不必要的停顿时间。
这不仅会浪费生产时间,还会导致生产效率低下、资源利用率低、成本增加等问题。
通过精益生产的方法,可以通过优化生产计划、提高任务分配的效率来减少等待时间。
2.5 不必要的动作不必要的动作指的是在生产过程中出现的重复操作、无用的工艺步骤等情况。
这不仅增加了生产过程的复杂度,还会增加不必要的时间和能源消耗。
通过精益生产的方法,可以通过流程改进、精简工艺等方式来减少不必要的动作。
2.6 生产过程中的瑕疵生产过程中的瑕疵是指产品在生产过程中发生的不合格或者次品的情况。
- 1、下载文档前请自行甄别文档内容的完整性,平台不提供额外的编辑、内容补充、找答案等附加服务。
- 2、"仅部分预览"的文档,不可在线预览部分如存在完整性等问题,可反馈申请退款(可完整预览的文档不适用该条件!)。
- 3、如文档侵犯您的权益,请联系客服反馈,我们会尽快为您处理(人工客服工作时间:9:00-18:30)。
关键设备的停机成本太昂贵…… 工人有空闲就是一种浪费…… 超天标生产有奖金(错误的绩效指标)……
为什么会生产过早?
担心工人没活干/担心各种人算不如天算的事情会发生(计划跟不上变化) → 提前投产→占用工艺和物料的准备时间→引发生产乱流→陷入恶性循环→ 产生生产过早的浪费
〝莫菲定律〞(Merphy`s Law):愈害怕会发生的事情,它偏偏就要发生!
在以上原理的基础上,丰田公司进一步将浪费定义为:“凡是超过生 产产品所绝对必要的最少量的设备、材料、零件和工作时间的部分,都是 浪费”。
由此提出JIT (Just in time) 准时生产观念,即:只有在顾客需要的 时候,才生产顾客所需质量和数量的产品。
JIT的三要素:正确的时间(顾客需要的)、正确的数量(顾客需要的)、 正确的产品(顾客需要的)。
反之,违反这个原则就会产生:多余的库存、多余的搬运、多余的等 待…等等各种浪费。
物资浪费(Material)
➢没有的浪费 ➢库存的浪费 ➢搬运的浪费 ➢拿、放的浪费 ➢等待的浪费 ➢困难工序的浪费
作业方法浪费(Method)
➢Lot的浪费 ➢库存的浪费 ➢搬运的浪费 ➢拿、放的浪费 ➢困难工序的浪费
个问题也就是企业通常所描述的“计划永远跟不上变化”的情况。
第二节 机器位置固定不动
在传统的制造型企业中,一般在设备安装完毕后,其位置 就基本不会发生变化,这已经成为一种普遍观念,如此会导致 企业生产出现如下问题:
1、生产工序跳跃前进和等待; 2、生产型号混乱生产; 3、企业总体效率降低。
机器位置固定不动所引发的问题…
第六节 动作的浪费
定义:由于在生产过程中企业的生产部门没有采用相应的标准和规范来约 束员工的动作行为而产生的员工非必要的重复动作。
结果: 降低工作愿望; 因反复弯腰而疲劳; 使用多种工具; 作业不稳定而产生不良。
动作浪费包含了三个内容: 这些动作不产生价值; 这些动作违反动作经济原则; 这些动作有办法可以避免;
离岛式车间布局
(B车间:打磨)
(C车间:加工)
(D车间:清洗)
投
单
生
3
产
2
7 8 13 14 6 9 12 15
产
品
18
交
付
17
5
11
1
4
10
16
19 20
离岛式车间所引发的问题…
协 调
加工地点分 散各地
因批量返工而变 更生产计划
质量事故频生
能 力
计划难
经常停工待料 愈急愈草率
很
A车间不知B车间
以控制
• 工作区域之间距离太长, 如工作站零件盒距离
• 操作人员等待系统运行完毕 • 显示一条不均衡的生产线 • 待料停工
• 经常使用的文件未定点定位,以致花费时间寻找 • 办公桌椅不符合人体工程学,导致员工腰酸背痛身心俱疲
• 等待主管签核的延误 • 无法今日事今日毕,积到以后 • 本末倒置,先完成下周的工作,本周工作反而推迟
因此造成了七大浪费!
第二章 识别七大浪费
传统的概念中,浪费指材料丢失、产品受损等。 现代的浪费指企业各项经营环节中所存在的非增值环节。 对应的增值环节,指的是能够直接给企业带来利润的环节,在加工制 造环节则指企业通过有形的物理变化或化学变化,将原材料转变为具有使 用价值商品的过程,那些无法给企业带来创效的环节则是非增值环节。 说明:非增值环节虽然不能够直接给企业创收,但并不意味着它没有 存在的必要,相反要采取措施,使增值环节强化,非增值环节优化。
无附加价值的 时间与工作
必须的 时间与 工作
产生附加价值的行为
不产生附加价值的行为
第一次 浪费 (能即时消除)
• 等待 • 寻找 • 保管 • 重新整理 • 打开包装
常见的无价值作业!
作
业
无附加价值的作业
第二次 浪费 (作业本身)
第三次 浪费 (设备的浪费)
• 复位作业 • 调整作业 • 去除毛刺 • 修正作业 • 喷 除锈剂
第四节 等待的浪费
定义:操作或事件之间的闲置时间,指断料、作业不平衡,计划不当造成 无事可作的等待。
结果: 增加人工成本,工作量变动大,工作量少时无所事事; 因缺料导致机械闲置; 因上游工序延误,导致下游工序无事可做; 生产线未能取得平衡; 生产安排不当的人员等待; 自动作业过程,人员“闲视”的等待; 作业充实度的等待。
陷入事后管理的漩涡……
事后管理就是等事情 发生之后再处理
习惯先 追究责任
挤在一起发生 只好忙于救火
怕后遗症扩大 只好采取围堵措施
没空/不愿追查 发生的原因
同样问题 一再重复发生
惩罚扣款 多于奖励
关闭心门 消极抵抗
救火/ 善后 变成家常便饭
垃圾流程丛生 只治标不治本
经常产生一人错误 百人忙的连锁反应
挤占工艺
强
的生产计划
挤占物料整 整备时间
的
半成品库存
备时间
生
前后进度难实
产
时衔接
管
理
一大堆
等来等去拉长生 产周期时间
只好靠提前 投产来保证
交期
部
只好先进中转仓
门
库储存等待
注定要 搬来搬去
为了搬运效率只好 大批量搬运
从图中可以看到,离岛式车间布局“加工地点分散各地”的特点在一连串
的连锁反应后,最终会引发制造型企业“生产计划难以控制”的严重问题,这
机器位置 固定不变
乱流生产
质量责任 难追溯
扯皮容易 蒙混过关
派活时由现场主管视各 岗位忙闲情况见缝插针
每一批次的加工路线 (经手人)都不一样
花金钱时间精力 去追查或控制
问题被隐藏
注定要 搬来搬去
拉长生 产周期 时间
陷入事后管 理的漩涡
同样问题 一再重复发生
救火/ 善后 变成家常便饭
第三节 事后管理
前言
浪费普遍存在于企业生产经营的全部过程,是造成成本增 加的主要原因,应该被彻底消除,是企业生产经营效益提升 的万恶之源。
金创公司由于技术和管理水平仍然处于较低水平,资源利 用率不如国内外优秀企业,甚至不如玉柴集团的其他子公司 ,在此基础下,发现浪费和消除浪费是金创公司全体员工为 实现精益生产又一重要里程碑,具有巨大的现实意义。
竞争力提升
品质提升 合理化成本降低 形象提升
标准化 改善
消除浪费 现场5S
动作标准化、作业流程标准化、操作流程 标准化、包装运输标准化等
动作改善、作业流程改善、物流改善、设 备模夹治具改善、品质改善、管理改善等
七大浪费
整理、整顿、清扫、清洁、素养等
第一章 制造业常见的管理误区
为了能够运用一些精益的手法排除企业车间现场的七大浪 费,首先需要对传统制造企业中长期存在的一些布局特点有所 认识,从而了解它们可能对企业整个生产效益产生的影响。
库存水平 例子: 过多的设备维修备品库存
人手不够 设备故障
物料未到
质量不良 技能不足 订单变更
第三节 搬运的浪费
定义:搬移零组件产品,过程仅属一种临时需要的搬运活动。 结果:搬运的动作会直接造成时间、空间、容器、载具、人力等浪费,并
间接造成库存、管理上的浪费,更严重的是,搬运过程还经常发生物 品的损伤,也会造成许多质量性和不可预测性的连锁浪费。
质量浪费(Quality)
➢做出不良品的浪费 ➢维修不良品的浪费 ➢犯错误的浪费 ➢检查的浪费 ➢质量管理的浪费
第一节 制造过多/过早的浪费(过量生产)
定义:生产超过需求或生产超过规定速度,即无论是生产过多还是过早, 其结果都是在一定的时间内产品的生产速度超过了商品的销售速度,从而 造成了浪费(过量生产也是所有企业中最大的浪费源)。
动作经济原则——工业工程(IE)把动作划分为六个等级: 等级一 手指头动 等级二 手指头和手腕动 等级三 整个拳头动 等级四 整个手臂在动,在手臂范围内做事情或完成作业; 等级五 活动扩展到腰和上身,活动范围更大 等级六 身体重心产生上下或左右移动 经验统计,动作每降低一级,劳动强度降低1/3,时间缩短1/2。
造成不必要的库存; 提早用掉资金; 占用生产车间,空间不足; 需要搬运,增加栈板,周转箱(纸箱容器); 生产员工工资支付,管理工时增加,利息负担增加。
为什么会生产过多?
追求生产局部效率/未进行生产管理→盲目超量生产/多放一些库存→生产过 多无法销售→(计划式生产最容易产生的)生产过多的浪费
追求局部效率牺牲总体效益的例子: 换模时间长→多生产一点比较好→产生大量库存、搬运、其它等待的
由于生産方法或设备难以改变而预先生産出大 批量的零组件
• 过量的影印、附件、存档等 • 型录宣传品过量印刷 • 简报超过时间未能精简扼要
• 在顾客从来不会看到的内部零组件上涂刷油漆 • 与工作无关的多余的资料收集、文件制作、报告等作业 • 流程中须签核的作业过多,未标准化
事后管理是传统制造型企业中管理人员所养成的一种习惯,在这种习 惯的驱使下他们只会在问题发生之后再采取相应的反映措施:
1、车间开工后,生产管理者根据员工忙闲情况见缝插针、机动派工, 员工亦不管后续工序消化能力全力赶工,做完就立即往下道工序传递,遇 到阻塞就在一旁等待或再次见缝插针;
2、当质量、急件等问题出现时,只能停产、换型并重新安排生产; 3、等待拉长了生产周期,换型增加了搬运浪费,提高了管理者生产压 力,增加了库存,占用了生产空间,导致了寻找、误用、脏污、碰伤等问 题。
害怕发生批量性的质量事故会影响生产进度→提前投产→挤占工艺准备时 间/挤占进料检验时间→遇急就愈草率→所以就……
第二节 库存的浪费
定义:存贮产品、材料、零组件等,所有的库存都是浪费。
增加成本、占用资金、次品隐藏在良品中 掩饰无效率、停工时间过长、生产计划欠妥等管理短板 员工操作不一致 不必要的入库、出库、盘点、防护、寻找和搬运等