面向装配的设计检查表
DFMA

质疑每个零件独立存在的理由
确定设计效率
突出可能导致成本增加和质量 问题的装配困难
Hale Waihona Puke DFMA——集成部件没有适用于所有产品的固定设计准则。上述的 检查表是为了使部件设计致力于减少零部件的 数量,如果不能,就集成零件提高装配效率并 使它们和当前制造工艺相兼容。
DFMA——低成本紧固件设计
尽可能地一次采用钩扣固件,按压固件,槽、接头、螺丝及粘接、 焊接 钩扣固件: 按压固件:过一段时间会失效 槽、接头:采用两个互锁部件,如槽和接头,或弯曲接头 螺丝。使用需注意:
dfma的设计规则设计规则包含内容效益减少零件数量使产品或部件包含尽可能少的零件减少装配工作量降低在制品库存便于管理提高可靠性易于维护使用标准件和通用件尽量使用标准件和通用件采用成组技术简历生产单元减少设计制造时间降低设计制造成本易于保证质量易于维护模块化设计采用模块化设计方法每个模块包含的零件数不宜过多减少最终产品装配时间减少库存缩短交货期易于保证质量易于维护装配结构工艺性?所有零件从一个方向进行装配?尽量在垂直方向进行装配?减少装配工作面?在外部进行装配?零件进入端设计倒角和锥度?避免错误装配减少装配工作量便于装配易于保证装配质量降低装配成本易于维护dfma的设计规则设计规则包含内容效益减少螺纹连接?尽量少用螺纹连接?采用卡扣粘接等快速连接方法减少装配工作量便于实现自动装配设计多功能零件如紧固件和密封件合二为一减少装配工作量减少调整环节尽量减少装配时的调整环节减少装配工作量便于装配少用柔性零件尽量少用橡胶件皮带电缆等在装配中难于处理的柔性零件减少装配工作量便于装配注
20% DFMA 设计 过程 •尝试更多的设 计变更 •早期设计的定 量评价 •DFMA工具
15% •CAD数据 •CAM/CAE分 析 •改变更容易
面向制造和装配的产品设计 - 第一部分

2.避免运动件运动过程干涉
为辅助工具提供空间
为重要零部件提供装配止位
宽松的零件公关要求
1.合理设计零件间隙
2.为关键尺寸缩短尺寸链
3.使用定位特征
四、DFMA的实施
DFMA检查表
DFMA检查表
装配工序面向装配的设计检查
面向制造和装配的产品设计总论
培 训 目 的
目录
一、设计的重要性二、DFMA概念三、DFMA的价值宏观、微观方面的价值;减少设计修改缩短产品开发周期降低产品成本提高产品质量四、DFMA的实施实施DFMA的关键步骤DFMA与传统开发流程对比DFMA检查表DFMA实施DFX附1:产品生命周期管理实例附2:参考文献
装配中的人机工程学
1.避免视线受阻的装配
2.避免装配操作受阻
3.避免操作人员受到伤害
4.减少工具的种类和特殊工具
5.设计特征辅助装配
线缆布局
1.合理的线缆布局
2.为线缆提供保护
可靠性测试
1.防水/防尘IP65/跌落
2.散热设计 (芯片温度)
工程安装设计
其他
总分
设计更改建议
四、DFMA的实施
DFMA检查表
在设计阶段进行成本分析,满足功能的前提下,选择合适的材料和最经济的制造工艺,降低成本;减少设计修改,降低成本。在开发周期里,设计修改的灵活性随着时间的推移越来越低,修改所导致的费用呈10倍增长;简化零件设计、减少零件数量,降低制造复杂度,降低成本;选择合适的装配工序、保证产品的可装配性,使装配简答、有效率、人性化,减少装配工序和装配时间,降低装配成本;降低产品不良率,减少成本浪费。
二、DFMA概念
乐高积木
斯堪尼亚卡车
装配式结构工程综合检查表

砼养护
养护方法、时长及效果
11
地下室外墙带模养护
12
高强及大体积混凝土保温、保湿
13
砼观感
断面尺寸偏差、垂直度、平整度、色差
14
缺陷:烂根(地下室等)、过振、漏振、冷缝、裂缝(屋面保护层等)、气泡、蜂窝、麻面、孔洞等现象漏浆(现浇节点和叠合板现浇板)
15
其他
防水工程质量控制(蓄水实验等)
16
降板位置混凝土质量控制
序号
检查项目(子项)
检 查 情 况
1
钢筋检验批质量验收及原始记录
2
模板检验批质量验收及原始记录
3
混凝土检验批质量验收及原始记录
4
装配式检验批质量验收及原始记录
5
其他分项工程检验批验收及原始记录
6
结构实体混凝土强度检验记录
7
钢筋保护层厚度检测报告
8
混凝土结构实体位置与尺寸偏差检验记录
9
分项工程质量验收记录
附件二
装配式结构工程综合检查表
检查时间:
工程名称
施工单位
建筑面积
层数
地下地上
地基基础、主体结构类型
预制构件名称及装配率
检查部位
序号
项 目
分值
精
良
一般
实得分值
1
施工管理
20
20~18
17.9~16
15.9以下
2
工程资料
20
20~18
17.9~16
15.9以下
3
模板
10
10~9
8.9~8
7.9以下
4
钢筋
梁、柱箍筋加密区(间距控制)
6
装配工艺检查表格

10
90°弯管
在桩头板处安装时,先穿线再固定盖板
11
紧定螺孔
拧紧定螺钉时先用工业吸尘器将铁屑吸除,在螺纹上涂603密封胶
12
吊环安装
装吊环时每个吊环必须拧紧到位。
13
拧螺丝
对角拧螺丝,一次不要拧太紧(并依次进行)
14
轴承加热
轴承加热时,温度应适宜(90~98℃),保温时间不少于30分钟,不大于2小时
15
轴承安装
轴承安装在轴承档上(有字朝外),安装到位,加入1/2~2/3的油脂。
16
按工艺要求加注润滑脂
1.加润滑脂必须用刮刀加注,并控制好轴承内盖的油量,
2.2极加1/3的油脂,4极加1/3~1/2的油脂,6极加1/2~2/3的油脂。
17
塞转子
1.使用塞转子的专用工具不能磕碰到端部线圈
2.转子尽量保持水平,和定子同心
如有粘线先加热电吹风粘融化粘漆瘤再把漆瘤清理干净分开引出线长引接线在端部和根部各扎一个扎带再打个结引接线不散落1090弯管在桩头板处安装时先穿线再固定盖板11拧紧定螺钉时先用工业吸尘器将铁屑吸除在螺纹上涂603密封胶12吊环安装装吊环时每个吊环必须拧紧到位
装配车间工艺纪律检查表
序号
抽查内容
工艺要求
抽查现状
操作者
日期
整改完成时间
1
三检卡
定子压装车间三检卡及时准确填写。
2
定子吊装
1.用专用涨胎吊装
2.H280以上的用专用铁架翻转
3
定子压装
1.保持上压头与机座接触面相互平行
2.符合定位尺寸
3.用专用工装进行压装
4
DFMA检查表
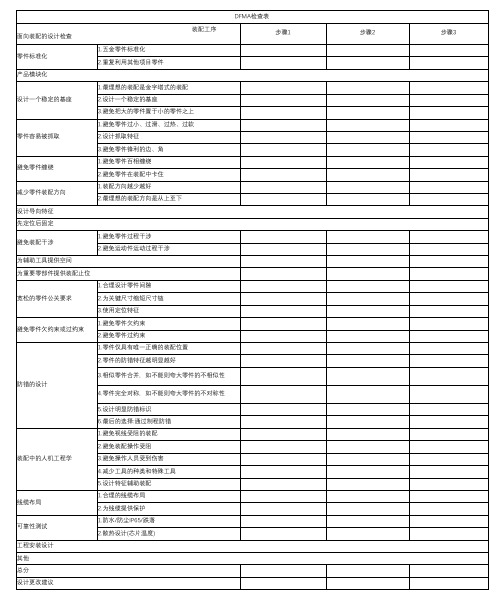
减少零件装配方向
1.装配方向越少越好 2.最理想的装配方向是从上至下
设计导向特征
先定位后固定
避免装配干涉
1.避免零件过程干涉 2.避免运动件运动过程干涉
为辅助工具提供空间
零件间隙
宽松的零件公关要求
2.为关键尺寸缩短尺寸链
3.使用定位特征
避免零件欠约束或过约束
1.避免零件欠约束 2.避免零件过约束
步骤2
步骤3
1.零件仅具有唯一正确的装配位置
2.零件的防错特征越明显越好
DFMA检查表 步骤1
防错的设计
3.相似零件合并,如不能则夸大零件的不相似性 4.零件完全对称,如不能则夸大零件的不对称性
装配中的人机工程学
线缆布局
可靠性测试 工程安装设计 其他 总分 设计更改建议
5.设计明显防错标识 6.最后的选择:通过制程防错 1.避免视线受阻的装配 2.避免装配操作受阻 3.避免操作人员受到伤害 4.减少工具的种类和特殊工具 5.设计特征辅助装配 1.合理的线缆布局 2.为线缆提供保护 1.防水/防尘IP65/跌落 2.散热设计(芯片温度)
面向装配的设计检查
装配工序
零件标准化
1.五金零件标准化 2.重复利用其他项目零件
产品模块化
1.最理想的装配是金字塔式的装配
设计一个稳定的基座
2.设计一个稳定的基座
3.避免把大的零件置于小的零件之上
1.避免零件过小、过滑、过热、过软
零件容易被抓取
2.设计抓取特征
3.避免零件锋利的边、角
避免零件缠绕
1.避免零件百相缠绕 2.避免零件在装配中卡住
装配过程审核检查表

8.6 量具清洁,无明显油污、杂质等。
2
6.7 质量检验人员熟悉产品检验要求,检验规范;
6.8 质量检验人员对测量工具、设施熟悉并掌握,接受过MSA分析确认
6.9 所有检验工具有明确的合格标识,并定期进行了校准;
6.10 检验记录数据完整、有效,真实;放行产品有检验人员签字;
6.11 对不合格进行了专门的记录,并进行了处理;
ห้องสมุดไป่ตู้
6.12 对维修、返工的产品进行了重新检验,并能提供记录;
1
装配过程审核检查表
审核员: 日期: 陪同人员:
评分标准:10---完全符合要求;8---绝大部分符合要求,有少量偏差;6---部分符合要求,有较大偏差;4----少部分符合要求,偏差严重;0---完全不符合要求; ★对每
一大项全部满分(10),或每一小项(6分)以下,要陈述情况,并说明证据(照片);
2.3
工艺参数(压力、温度等)是否有效监控,设备能否防错(自动报 警、停机等)?并有措施保证其有效性?
3 物料:运输/搬运/贮存/包装
3.1 物料清洁度防护控制手段有效,符合工艺要求;
3.2 物料是否按要求贮存?运输器具/包装方法是否按物料的特性而定?
3.3
废品、返修件和不合格件以及车间内的剩余料是否分别贮存与并标 识,可追溯?
6.2 测量工具是否有校验标识,测量工具完好、准确,是否在有效期?
6.3 作业员\检查员是否按规定频率和样本数量使用指定工具检查?
6.4 测量记录完整,准确、有效?(无涂改、数值错误等) 6.5 产品流转卡完整,各工序记录清晰,与产品要求相符,签名、记录 6.6 质量检验点标识明确,清楚,检验样板、文件、资料、记录齐全;
4.6 足要求; 变更是否符合制造过程变更流程,是否经过批准。过程变更记录齐
结构设计检查表

1如果是塑胶件过高的螺钉柱要加Rib
2塑胶件片状的螺钉过孔柱一定要加Rib。加强其强度。
卡勾检查
外观倒角
倒C角:定位柱螺钉柱卡勾便于零件安装
按键行程是否足够
是否会出现熔接痕。
翘翘板式按键按的时候会不会碰到侧壁。
4.零件模具问题
在产品的结构设计过程中,应充分考虑模具的成本和寿命.尽量
装配尽量简单,要保证各个零件之间装配快速完成
2.干涉问题
机构件之间的干涉检查
电子件之间的干涉检查
机构件和电子件之间的干涉检查(注意运动过程中的干涉)
3.单个零件结构的合理性
减少装配零件,设计要简单化
进行壁厚分析检查
1壁厚是否均匀,是否平缓过度(倒C角或者R角)
2钣金折弯角是否一致,过小是否不容易加工
1减少模具的复杂性
2减少斜顶
3减少滑块
4尖角利边
5对插位
斜顶问题:
1有没有斜顶,是否可以通过切割塑胶材料来取消斜顶
2斜顶是否有足够的退出空间
3斜顶是否会干涉其他特征
有没有倒扣,切除倒扣部分
对平板及透明件的设计应充分考虑模具的浇口.
5.成本问题
尽量降低成本
6.共用问题
能共用其他机种零件的尽量共用,以降低成本。
7.外观问题
R角是否能完美的做成。
分模线是否影响外观
是否需要美工线ห้องสมุดไป่ตู้
8.其它问题
3D文件必须重生
外发文件必须删除supress特征。
运动机构件一定要把他的运动全过程都画出来,以减少错误。
结构
检查项目
问题点
1.装配问题
模拟实际组装检查零件固定和干涉(PROE建立简化模型):
设计信息检查表(1.0版)

系统测试是否符合产品要求,验证结果是否符合要求
151
性能测试是否符合设计要求,测试结果是否符合设计要求
编制:审核:复核:批准:
设计信息检查表(表五)
顾客或厂内零件号□手工样件□工程样件□小批量编号:BG-QR-06-06/1
问题
是
否
所要求的意见/措施
负责人
备注
E.测试/验证类
152
使用现有的检验技术,是否有些规定要求不能被评价?
问题
是
否
所要求的意见/措施
负责人
备注
48
先遣的材料供方是否在顾客批准的名单中?
49
是否要求材料供方对每一批货提供检验证明?
50
是否已明确材料特性所要求的检验?如果是,则:
51
·特性将在厂内进行检验吗?
52
·具备试验设备吗?
53
·为保证准确结果,需要培训吗?
54
将使用外部试验室吗?
55
所有被使用的试验室得到认可吗(如要求)?
81
将使用外部试验室吗?
82
所有被使用的试验室得到认可吗(如要求)?
83
是否解决了实验室发现问题和用户反馈问题?
84
是否已考虑以下材料要求
85
对于影响配合、功能和耐久性的尺寸是否已明确?(与结构)
86
可制造性,工艺是否合理?是否满足批量生产?
87
此板卡与外部设备连接是否可通用
88
相关程序是否与软件系统兼容性
9
如果是,是由横向职能小组完成的吗?
10
是否对所有规定的试验、方法、设备和接受准则有一个清楚的定义和了解?
11
是否已选择特殊特性?
编号4-6 DFMA面向制造和装配的产品设计
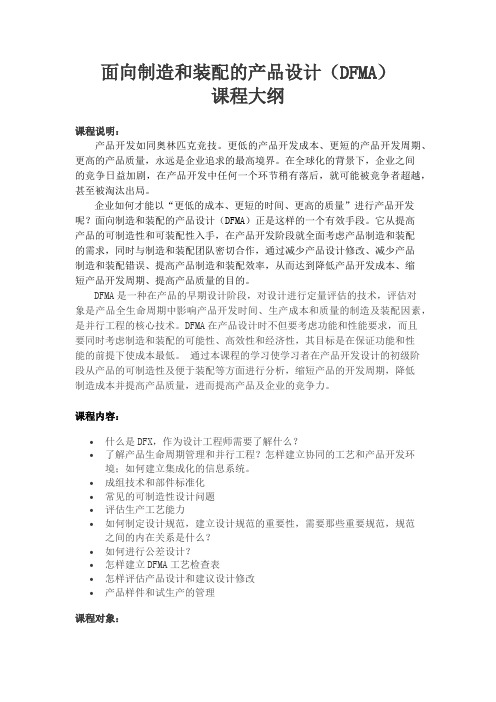
面向制造和装配的产品设计(DFMA)课程大纲课程说明:产品开发如同奥林匹克竞技。
更低的产品开发成本、更短的产品开发周期、更高的产品质量,永远是企业追求的最高境界。
在全球化的背景下,企业之间的竞争日益加剧,在产品开发中任何一个环节稍有落后,就可能被竞争者超越,甚至被淘汰出局。
企业如何才能以“更低的成本、更短的时间、更高的质量”进行产品开发呢?面向制造和装配的产品设计(DFMA)正是这样的一个有效手段。
它从提高产品的可制造性和可装配性入手,在产品开发阶段就全面考虑产品制造和装配的需求,同时与制造和装配团队密切合作,通过减少产品设计修改、减少产品制造和装配错误、提高产品制造和装配效率,从而达到降低产品开发成本、缩短产品开发周期、提高产品质量的目的。
DFMA是一种在产品的早期设计阶段,对设计进行定量评估的技术,评估对象是产品全生命周期中影响产品开发时间、生产成本和质量的制造及装配因素,是并行工程的核心技术。
DFMA在产品设计时不但要考虑功能和性能要求,而且要同时考虑制造和装配的可能性、高效性和经济性,其目标是在保证功能和性能的前提下使成本最低。
通过本课程的学习使学习者在产品开发设计的初级阶段从产品的可制造性及便于装配等方面进行分析,缩短产品的开发周期,降低制造成本并提高产品质量,进而提高产品及企业的竞争力。
课程内容:•什么是DFX,作为设计工程师需要了解什么?•了解产品生命周期管理和并行工程?怎样建立协同的工艺和产品开发环境;如何建立集成化的信息系统。
•成组技术和部件标准化•常见的可制造性设计问题•评估生产工艺能力•如何制定设计规范,建立设计规范的重要性,需要那些重要规范,规范之间的内在关系是什么?•如何进行公差设计?•怎样建立DFMA工艺检查表•怎样评估产品设计和建议设计修改•产品样件和试生产的管理课程对象:本培训适合研发经理、工程师及希望了解设计质量工具作为附加能力的参与产品开发项目的技术人员。
课程大纲:第1章:面向制造和装配的产品设计1.1 产品设计的重要性1.2 Design for X1.3 DFMA的介绍1.4 DFMA的价值1.5 DFMA的实施第2章:面向装配的设计指南2.1面向装配的设计2.1.1装配的定义2.1.2最好和最差的装配工序2.1.3面向装配的设计的定义2.1.4面向装配的设计的目的2.1.5面向装配的设计的历史2.2设计指南——18个原则2.2.1使装配变得最容易(DFA)的8个规则1) 模块化设计2) 使用最少的零件3) 多用标准件4) 减少紧固件5) 采用复合多用途零件6) 增加柔性和可调机构,减少装配中的调整时间7) 减少装配方向和装配面。
产品结构设计检查表

产品结构设计检查表产品结构设计检查表1.目的为了使结构工程师在设计过程及设计完成后,对产品的结构进行自我评审,完善产品的生产工艺,减少后续加工的问题和修改,提高产品成功率和客户满意度。
2.内容检查过程应遵循先整体后局部,先外观后内部结构的原则。
检查项目问题点1.外观问题±外观是否符合客户要求以及效果图要求(包括外形,尺寸,零件布局,表面特征和效果);±R角是否能完美的做成;±分模线是否影响外观;±是否需要美工线。
2.装配问题±模拟实际组装检查零件固定和干涉:①装配的方式和工艺(采用螺钉、焊接、卡扣、粘接等);②唇或止口结构;③零件装配的定位和装拆顺序;④零件组装的时候会不会干涉其他零件。
±螺钉问题:①螺钉选用和螺丝台结构是否符合结构评审标准要求;②所用的螺钉应该画出;③机械牙锁合的长度,一般不少于2-3mm;④自攻牙锁合的长度,要注意螺钉尾端的影响;⑤螺钉头是否干涉其他件。
±对产品生产时的效率的考虑,如生产线的装配人数需尽量少,且每个工位的装配尽量简单;±装配尽量简单。
3.干涉问题±机构件之间的干涉检查;±电子件之间的干涉检查;±机构件和电子件之间的干涉检查(电子件的限高);±运动的干涉。
4.单个零件结构的合理性±拔模检查:①零件的特征是否根据出模的方向进行拔模处理;②拔模面的表面情况是否考虑不同的拔模斜度(光面和晒纹面);③零件是否进行了拔模检测。
±进行壁厚分析检查:①看壁厚是否过厚引起缩水②壁厚是否均匀,是否平缓过度(倒C角或者R角)③螺丝柱是否太过靠近零件侧面;④加强筋拔模后底部是否过厚;⑤壁厚是否过薄。
过薄的壁厚不容易打满。
±零件结构强度是否足够。
结构强度能强一定让它强。
①过高的螺钉柱加Rib;②零件强度比较弱的加Rib(Rib尽量做薄防止缩水);③易变形的位置是否加筋。
面向制造和装配的设计

Thank You !
面向制造和装配的设计
原则3:零件标准化 1.零件标准化的好处 1)零件标准化能够减少定制零件所带来的新零件开发时间和精力的浪费,缩短产品开 发周期. 2)降低成本.标准化零件因为规模性往往成本较低.对于塑胶、钣金等需要通过模具进 行制造的零件,使用标准化的零件能够节省模具的成本,零件成本优势更加明显.在成 本上,定制零件就如同定制衣服一样,通常都会比较贵. 3)避免出现零件质量问题的风险.标准化的零件已经被广泛使用,并证明质量可靠.相反 ,定制的零件需要通过严格的质量和功能验证,否则容易出现质量问题. 2.实现零件标准化的实现 1)制订常用零件的标准库和零件优先选用表,并在企业内部不同产品之间实行标准化 策略 2)五金零件,例如螺钉、螺母、导电泡棉等选用供应商的标准零件,五金零件的定制会 带来成本和时间的增加
面向制造和装配的设计
原则4:模块化产品设计 模块化产品设计是指把产品中多个相邻的零件合并成一个子组件或模块,一个产品由多 个子组件或模块组成.应用模块化设计复杂产品被分解为多个功能模块,从而简化产品 结构和减少产品总装配时的装配工序,同时,模块化的子组件能够在产品总装配之前进 行质量检验,装配质量问题能够更早、更容易被发现,避免不合格的产品流入到产品总 装配线上,从而提高产品装配效率和提高装配质量
面向制造和装配的设计
原则14:防止零件欠约束和过约束
面向制造和装配的设计
原则15:宽松的零件公差要求 1.设计合理的 2.简化产品装配关系 3使用定位特征 4.使用点或线与平面配合
面向制造和装配的设计
原则17:防呆设计 1.零件具有唯一的正确装配位置 零件对称度越 零件完全 2.零件的防呆设计特征越明显越 高,防呆级别 对称,不必 好 不必 越高 防呆 3.放大零件的不对称性或不相似 防呆 性 1.阻止特征越明显 零件仅有唯一的 4.设计明显的防呆标识 2.零件不相似性越明显 阻止 正确装配位置 5.最后的选择:通过制程来防呆 3.零件不对称性越明显 防呆级别越高 6.完美的防呆:不必防呆 制程防呆: 使用明 1.改变或增加工具、治具 标识越明显, 显的防 标识 2.改变装配顺序 防呆级别越高 呆标识 3.增加使用清单、模板或测量仪 4.执行控制图表 防呆级别金字塔
solidworks面向制造和装配的产品设计说明

与金属材料对比,塑胶材料优缺点见下表3-1
3.1.3 注射成型
3.2 塑胶材料选择
• 3.2.1 塑胶材料的分类 • 3.2.2 常用塑胶材料性能 • 3.2.3 塑胶材料选择原则
3.2.1 塑胶材料的分类
按照塑胶材料的力学性能,可分为7大类:
1. 通用塑料:综合力学性能较低,不能作为结构件,但成型性好、 价格便宜、用途广、产量大的塑料,包括PE、PP、EEA、PVC,广 泛应用于薄膜、管材、鞋材、盆子、桶和包装材料类。
2.避免孔与钣金折弯边或成型特 征距离太近钣金冲裁孔与钣金折 弯边或成型特征的距离最小为钣 金厚度的1.5倍加上折弯半径或成 型半径,即E>=1.5T+R,否则冲裁 孔极易在折弯或成型时发生扭曲 变形。
3.避免钣金折弯高度过低而引起的变形扭曲,折弯高度至少为钣 金厚度的2倍加上折弯钣金。
4.钣金折弯时需要保证折弯强度。长而窄的折弯强度低,短而宽 的折弯强度高,因此钣金折弯应尽量附着在比较长的边上。
酸洗、电镀及各种后处理制程后,即成为电镀锌产品。 3) 热浸镀锌钢板:将热轧酸洗或冷轧后的半成品,经过清洗、退火,
浸入温度约为460℃的熔融镀锌槽中,而使钢片镀上锌层,再经调 质整平及化学处理而成。 4) 不锈钢SUS304:最常用的不锈钢板。 5) 不锈钢SUS301:Cr的含量较SUS304低,耐腐蚀较差。
4.1.2 冲压简介
冲压是将冲压模具安装在压力机等设备上,对板材、带材、管 材和型材等施加外力,使之产生塑性变形或分离,从而获得所需 形状和尺寸的钣金件的一种成型加工方法。
4.1.3 常用钣金材料介绍
1) 普通冷轧板:钢锭经过冷轧机连续轧制成要求厚度的钢板卷料。 2) 镀锌钢板:底材为一般的冷轧钢板,在连续电镀生产线经过脱脂
装配式项目检查表(全套)

附件1装配式建筑安全质量专项检查表装配整体式混凝土结构工程施工安全检查表(管理)检查人:检查时间:填表说明:1、依据《装配整体式混凝土结构施工及质量验收规范》DGJ08-2117-2012;《装配整体式混凝土结构建筑施工质量安全监管要点(试行)》沪建安质监【2015】8号;2、检查表中未列检查内容,如起重机械、临时用电参见其他相关规范标准及规定执行;3、检查发现表中“*”内容及方案编制审批,预制构件堆放、驳运、吊装、现场防护及构件连接等关键环节,存在安全生产条件缺陷的,应立即责令局部暂缓施工整改,必要时全面停工整改,并对相关责任单位和个人依法进行处理。
装配整体式混凝土结构工程施工安全检查表(现场实体)检查人:检查时间:填表说明:1、依据《装配整体式混凝土结构施工及质量验收规范》DGJ08-2117-2012;《装配整体式混凝土结构建筑施工质量安全监管要点(试行)》沪建安质监【2015】8号;2、检查表中未列检查内容,如起重机械、临时用电参见其他相关规范标准及规定执行;3、检查发现表中“*”内容及方案编制审批,预制构件堆放、驳运、塔机选型、吊装、现场防护及构件连接等关键环节,存在安全生产条件缺陷的,应立即责令局部暂缓施工整改,必要时全面停工整改,并对相关责任单位和个人依法进行处理。
装配整体式混凝土结构工程施工质量检查表备注:本次重点检查内容为:1、涉及结构安全的连接件及钢筋工程质量2、涉及结构安全的质量检测3、涉及使用功能的防水构造4、涉及结构安全及使用功能的监督抽检检查表中相对应为打“★”标注内容。
检查组成员签字:检查日期:建设工地建筑起重机械检查表检查人:检查时间:附件2: 预制构件成品质量检测表预制构件制作过程检测表预制构件编号:。
模具装配检查表
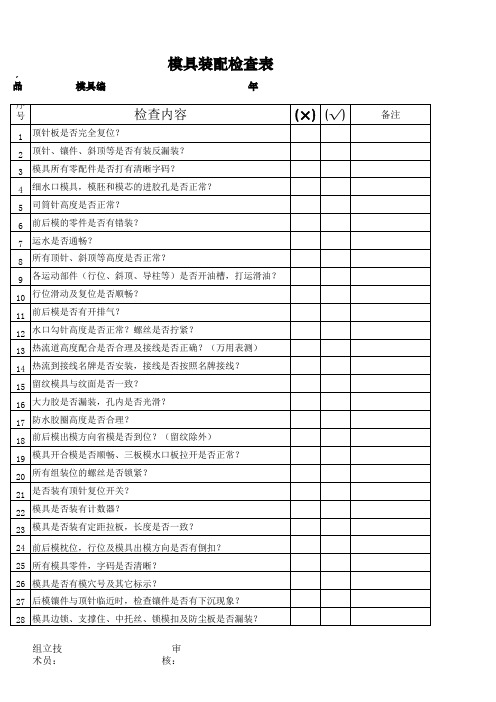
品
模具编
模具装配检查表
年
序
号
检查内容
1 顶针板是否完全复位? 2 顶针、镶件、斜顶等是否有装反漏装? 3 模具所有零配件是否打有清晰字码? 4 细水口模具,模胚和模芯的进胶孔是否正常? 5 司筒针高度是否正常? 6 前后模的零件是否有错装? 7 运水是否通畅? 8 所有顶针、斜顶等高度是否正常? 9 各运动部件(行位、斜顶、导柱等)是否开油槽,打运滑油? 10 行位滑动及复位是否顺畅? 11 前后模是否有开排气? 12 水口勾针高度是否正常?螺丝是否拧紧? 13 热流道高度配合是否合理及接线是否正确?(万用表测) 14 热流到接线名牌是否安装,接线是否按照名牌接线? 15 留纹模具与纹面是否一致? 16 大力胶是否漏装,孔内是否光滑? 17 防水胶圈高度是否合理? 18 前后模出模方向省模是否到位?(留纹除外) 19 模具开合模是否顺畅、三板模水口板拉开是否正常? 20 所有组装位的螺丝是否锁紧? 21 是否装有顶针复位开关? 22 模具是否装有计数器? 23 模具是否装有定距拉板,长度是否一致?
24 前后模枕位,行位及模具出模方向是否有倒扣?
25 所有模具零件,字码是否清晰?
26 模具是否有模穴号及其它标示?
27 后模镶件与顶针临近时,检查镶件是否有下沉现象?
28 模具边锁、支撑住、中托丝、锁模扣及防尘板是否漏装?
否是 (×) (√)
组立技 术员:
审 核:
备注
设计室2D装配图检查表

设计室2D装配图检查表2D Assembly Drawing Checklist项目名称:产品名称:模具编号: Project Name: Component Name: Tool Number:Component Name: Tool Number:Component Name: Tool Number:Component Name: Tool Number:检查工程师:日期:项目负责人:日期:Designer: Date: Project Leader: Date:说明:1、此表旨在加强设计人员在装配图完成后达到自检作用,也可作为设计室一般性设计指导文件参考;This form is made for designers to check their design after assembly drawings are finished, and can also be used as a general guida2、所有的设计依据必须以客供设计资料为先;Customer's specification or requirements enjoy first priority.3、装配图发出前完成此表并签署,交与项目负责人确认;This checklist must be filled and signed by designers and confirmed by leader before assembly drawings are sent for ap4、所有检查项目须认真填写。
Designer must be very careful when filling all of these items.5、所有检查须与装配图相吻合,若没有此项请空白不填写。
All items must be consistent with assembly drawings. Leave items blank, if they do not exist.。
IATF16949设计信息检查表 (A2)
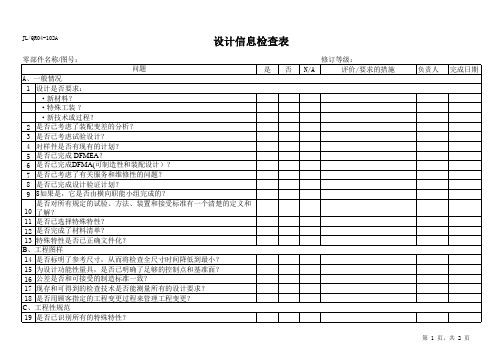
设计信息检查表
零部件名称/图号:
修订等级:
问题
是 否 N/A
要求:
·新材料?
·特殊工装 ?
·新技术或过程?
2 是否已考虑了装配变差的分析?
3 是否已考虑试验设计?
4 对样件是否有现有的计划?
5 是否已完成 DFMEA?
6 是否已完成DFMA(可制造性和装配设计)?
·特性将在厂内进行检验吗?
·如在厂内进行检验,具备试验装置吗?
·如在厂内进行检验,是否具备有能力的人员以确保试验准确性?
31 是否会使用外部试验室?
公司是否有一个可以保证试验室能力(比如认可)的过程?注意,不
论公司与该试验室是何种关系,试验室能力都需要得到保证。
32 是否已考虑以下材料要求:
·搬运,是否包括环境方面?
15 为设计功能性量具,是否已明确了足够的控制点和基准面?
16 公差是否和可接受的制造标准一致?
17 现存和可得到的检查技术是否能测量所有的设计要求?
18 是否用顾客指定的工程变更过程来管理工程变更? C、工程性规范
19 是否已识别所有的特殊特性?
负责人 完成日期
第 1 页,共 2 页
JL/QR04-102A
7 是否已考虑了有关服务和维修性的问题?
8 是否已完成设计验证计划? 9 8如果是,它是否由横向职能小组完成的?
是否对所有规定的试验、方法、装置和接受标准有一个清楚的定义和 10 了解?
11 是否已选择特殊特性?
12 是否完成了材料清单?
13 特殊特性是否已正确文件化? B、工程图样
14 是否标明了参考尺寸,从而将检查全尺寸时间降低到最小?
设计信息检查表
- 1、下载文档前请自行甄别文档内容的完整性,平台不提供额外的编辑、内容补充、找答案等附加服务。
- 2、"仅部分预览"的文档,不可在线预览部分如存在完整性等问题,可反馈申请退款(可完整预览的文档不适用该条件!)。
- 3、如文档侵犯您的权益,请联系客服反馈,我们会尽快为您处理(人工客服工作时间:9:00-18:30)。
防错的设计
防错的设计
6.最后的选择,通过制程防错 1.避免视线受阻的装配 装配中的人机 2.避免装配操作受阻 工程学 3.避免操作人员受到伤害 4.设计特征辅助装配 线缆布局 其他 总分 1.合理的线缆布局 2.为线缆提供保护
2 0 0 0 0 1 0 0 11 增加防错 结构
0 0 0 0 0 0 0 0 5
面向装配的设计指南
零件标准化 产品模块化 1.最理想的装配是金字塔式的装 配 设计一个稳定 2.设计一个稳定的基座 的基座 3.避免把大的零件置于小的零件 之上 避免零件缠绕 1.避免零件相互缠绕 2.避免零件在装配中卡住 1.五金件标准化 2.重复利用其他项目零件 0 0 0 0 0 0 0 0 0 0 0 0 1.避免零件装配过程干涉 2.避免运动件运动干涉 0 0 0 0 0 0 0 1 0 1 3 0 0 3
面向装配设计的检查
项目名称 设计信息 设计工程师 -----
装配工序
护套母端 橡胶垫 0 1 1 0 0 0 0 2 0 0 0 0 1 0 0 0 0 0 0 0 0 0 0 0 0 0 钣金 1 1 0 0 0 0 0 0 0 1 0 0 0 0 0 0 2 0 0 1 0 0 0 0 0 2 护套公端 0 0 0 0 0 0 0 0 0 1 0 0 0 0 0 0 0 0 0 0 1 0 2 0 0 2
0 1 1 0 0 0 0 0 10
0 0 0 0 0 0 0 0 6
设计更改建议
上盖 0 0 0 0 0 0 0 0 0 1 0 0 0 0 0 0 0
0 0 0 0 0 0 0 0
0 0 0 0 0 0 0 0 1
ቤተ መጻሕፍቲ ባይዱ
减少零件装配 1.装配方向越少越好 方向 2.最理想的装配方向是从上而下 设计导向特征 先定位后固定 避免装配干涉
为辅助工具提供空间 为重要零部件提供装配止位 1.合理设计零件间隙 宽松的零件公 2.为关键尺寸缩短尺寸链 差要求 3.使用定位特征 避免零件欠约 1.避免零件欠约束 束和过约束 2.避免零件过约束 1.零件仅具有唯一正确的装配位 置 2.零件的防错特征越明显越好 3.相似零件合并,如不能则夸大 零件的不相似性 4.零件完全对称,如不能则夸大 零件的对称性 5.设计明显防错标识